工厂计件工资得利弊
计件工资的推行办法及注意事项

计件工资的推行办法及注意事项采用计件工资制度的好处一,可以提高员工积极性,提高企业的生产效率。
由于是多劳多得,员工完全凭自身能力赚工资,所以,只要真是个做事的人,一般都不会偷懒!二,员工自己会自发去改进劳动方法,加强劳动技能!可以形成强烈的竞争氛围,让员工与员工之间形成你追我赶,相互攀比的心理。
三,让企业的支出相对明明白白,利于成本控制,有效控制住隐性浪费。
采用计件工资制度的坏处一,员工容易只讲数量,不讲质量。
对品质要求容易产生对抗情绪。
二,只要是计件制,就会有不平均的现象发生,矛盾较多,处理不好,容易产生波动。
三,小单不好处理,花心力太大,产生的效益却很少。
四,每一次新产品上线,都得慎重对待,对管理人员要求提高很多。
推行计件工资制需要注意的事项一,需要一名精通工艺,精通工价预估的管理人员,精准,权威。
这是首要条件,所谓的不是金刚钻,别揽瓷器活。
不是那行的专家,就别要想吃那碗饭。
打工价的那个人,一定要见多识广,一定要是从一线做起来的具有丰富行业经验及职业素养的人。
学历再高,理论素养再强,只要没有长时间的一线生产操作经验,都是白搭。
他还要有一颗精于计算的头脑,一个人的算计深度要超过企业所有一线工人所能算计的总和!这个人相当难找,这也是很多企业采用计件制问题百出的根源所在!二,企业计件工资不是越高越好。
哪个企业都要赚钱,视情况定吧。
如果企业效益好,利润高,可以适当高点。
如果效益一般般,不求太高,但整体工资要比同行高那么一点点。
因为计件制度一旦形成,那么,真正能留在企业里长年工作的基本上都是些行业里技能过硬,能打能拼的工人。
没有整体高于同行的薪资待遇,招不到人,留不住人,很多事都不好整改和推行。
人管人,累死人,钱管人,很容易!三,在计件制的企业里,工资低点还不是最关键。
最最要命的是有人低有人高,人哪,不患贫而患不均。
工人的攀比心很强,同行的平均工资是三千,你厂里计件工人最低工资是一万,最高工资是两万。
计件工资的推行办法及注意事项
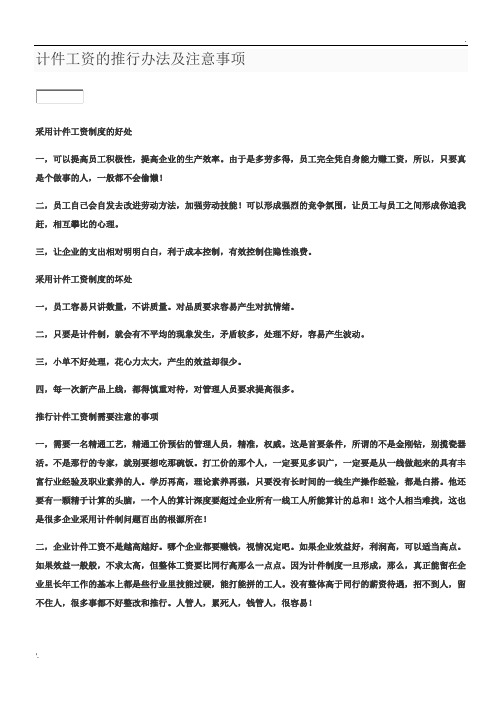
计件工资的推行办法及注意事项采用计件工资制度的好处一,可以提高员工积极性,提高企业的生产效率。
由于是多劳多得,员工完全凭自身能力赚工资,所以,只要真是个做事的人,一般都不会偷懒!二,员工自己会自发去改进劳动方法,加强劳动技能!可以形成强烈的竞争氛围,让员工与员工之间形成你追我赶,相互攀比的心理。
三,让企业的支出相对明明白白,利于成本控制,有效控制住隐性浪费。
采用计件工资制度的坏处一,员工容易只讲数量,不讲质量。
对品质要求容易产生对抗情绪。
二,只要是计件制,就会有不平均的现象发生,矛盾较多,处理不好,容易产生波动。
三,小单不好处理,花心力太大,产生的效益却很少。
四,每一次新产品上线,都得慎重对待,对管理人员要求提高很多。
推行计件工资制需要注意的事项一,需要一名精通工艺,精通工价预估的管理人员,精准,权威。
这是首要条件,所谓的不是金刚钻,别揽瓷器活。
不是那行的专家,就别要想吃那碗饭。
打工价的那个人,一定要见多识广,一定要是从一线做起来的具有丰富行业经验及职业素养的人。
学历再高,理论素养再强,只要没有长时间的一线生产操作经验,都是白搭。
他还要有一颗精于计算的头脑,一个人的算计深度要超过企业所有一线工人所能算计的总和!这个人相当难找,这也是很多企业采用计件制问题百出的根源所在!二,企业计件工资不是越高越好。
哪个企业都要赚钱,视情况定吧。
如果企业效益好,利润高,可以适当高点。
如果效益一般般,不求太高,但整体工资要比同行高那么一点点。
因为计件制度一旦形成,那么,真正能留在企业里长年工作的基本上都是些行业里技能过硬,能打能拼的工人。
没有整体高于同行的薪资待遇,招不到人,留不住人,很多事都不好整改和推行。
人管人,累死人,钱管人,很容易!三,在计件制的企业里,工资低点还不是最关键。
最最要命的是有人低有人高,人哪,不患贫而患不均。
工人的攀比心很强,同行的平均工资是三千,你厂里计件工人最低工资是一万,最高工资是两万。
浅谈计件工资方式的利弊【精选文档】
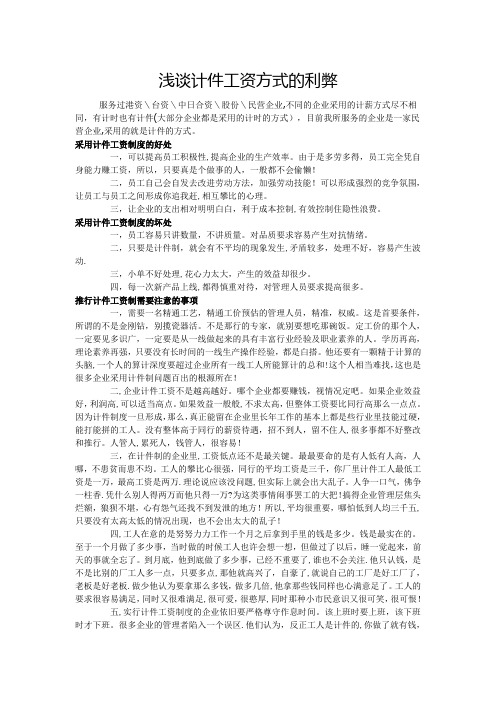
浅谈计件工资方式的利弊服务过港资\台资\中日合资\股份\民营企业,不同的企业采用的计薪方式尽不相同,有计时也有计件(大部分企业都是采用的计时的方式),目前我所服务的企业是一家民营企业,采用的就是计件的方式。
采用计件工资制度的好处一,可以提高员工积极性,提高企业的生产效率。
由于是多劳多得,员工完全凭自身能力赚工资,所以,只要真是个做事的人,一般都不会偷懒!二,员工自己会自发去改进劳动方法,加强劳动技能!可以形成强烈的竞争氛围,让员工与员工之间形成你追我赶,相互攀比的心理。
三,让企业的支出相对明明白白,利于成本控制,有效控制住隐性浪费。
采用计件工资制度的坏处一,员工容易只讲数量,不讲质量。
对品质要求容易产生对抗情绪。
二,只要是计件制,就会有不平均的现象发生,矛盾较多,处理不好,容易产生波动.三,小单不好处理,花心力太大,产生的效益却很少。
四,每一次新产品上线,都得慎重对待,对管理人员要求提高很多。
推行计件工资制需要注意的事项一,需要一名精通工艺,精通工价预估的管理人员,精准,权威。
这是首要条件,所谓的不是金刚钻,别揽瓷器活。
不是那行的专家,就别要想吃那碗饭。
定工价的那个人,一定要见多识广,一定要是从一线做起来的具有丰富行业经验及职业素养的人。
学历再高,理论素养再强,只要没有长时间的一线生产操作经验,都是白搭。
他还要有一颗精于计算的头脑,一个人的算计深度要超过企业所有一线工人所能算计的总和!这个人相当难找,这也是很多企业采用计件制问题百出的根源所在!二,企业计件工资不是越高越好。
哪个企业都要赚钱,视情况定吧。
如果企业效益好,利润高,可以适当高点。
如果效益一般般,不求太高,但整体工资要比同行高那么一点点。
因为计件制度一旦形成,那么,真正能留在企业里长年工作的基本上都是些行业里技能过硬,能打能拼的工人。
没有整体高于同行的薪资待遇,招不到人,留不住人,很多事都不好整改和推行。
人管人,累死人,钱管人,很容易!三,在计件制的企业里,工资低点还不是最关键。
工厂计件工资方案
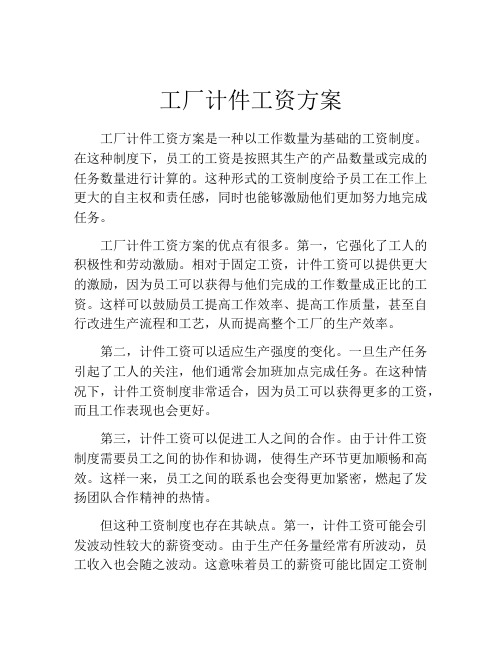
工厂计件工资方案工厂计件工资方案是一种以工作数量为基础的工资制度。
在这种制度下,员工的工资是按照其生产的产品数量或完成的任务数量进行计算的。
这种形式的工资制度给予员工在工作上更大的自主权和责任感,同时也能够激励他们更加努力地完成任务。
工厂计件工资方案的优点有很多。
第一,它强化了工人的积极性和劳动激励。
相对于固定工资,计件工资可以提供更大的激励,因为员工可以获得与他们完成的工作数量成正比的工资。
这样可以鼓励员工提高工作效率、提高工作质量,甚至自行改进生产流程和工艺,从而提高整个工厂的生产效率。
第二,计件工资可以适应生产强度的变化。
一旦生产任务引起了工人的关注,他们通常会加班加点完成任务。
在这种情况下,计件工资制度非常适合,因为员工可以获得更多的工资,而且工作表现也会更好。
第三,计件工资可以促进工人之间的合作。
由于计件工资制度需要员工之间的协作和协调,使得生产环节更加顺畅和高效。
这样一来,员工之间的联系也会变得更加紧密,燃起了发扬团队合作精神的热情。
但这种工资制度也存在其缺点。
第一,计件工资可能会引发波动性较大的薪资变动。
由于生产任务量经常有所波动,员工收入也会随之波动。
这意味着员工的薪资可能比固定工资制度波动性更大,难以确定每月的收入水平,可能会引起员工的不满和不安定。
第二,计件工资制度可能会带来质量问题。
员工可能会急于完成任务而忽略产品质量,这可能导致生产过程中的错误,影响生产效率,甚至给整个工厂带来损失。
第三,计件工资制度可能会导致员工过度劳累或出现身体问题。
如果生产任务很多,可能会导致员工为了赚更多的钱而过度劳累,这对身体健康会造成影响。
这些健康问题会使员工缺席和增加生病的风险,降低效率和生产率,以及增加工厂的医疗成本。
综上所述,工厂计件工资方案有其优点和缺点。
它强化了员工的积极性和劳动激励,在提高生产效率的同时,也增加了员工的薪资收入。
但是它也存在缺陷,可能存在质量问题和身体问题等方面的风险。
计件工资的利弊
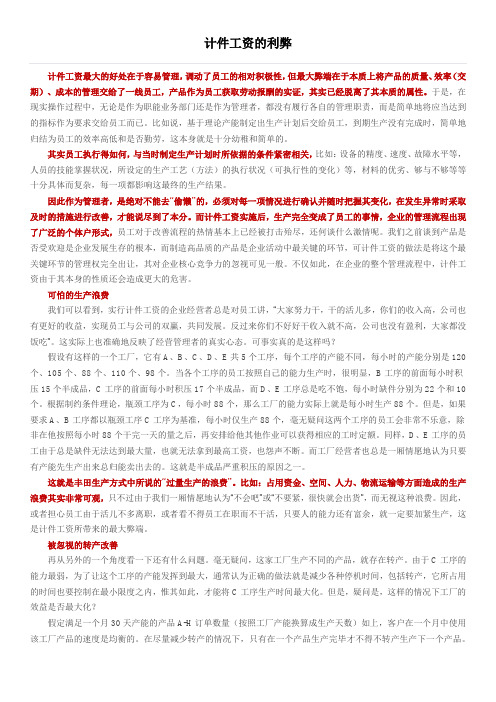
计件工资的利弊计件工资最大的好处在于容易管理,调动了员工的相对积极性,但最大弊端在于本质上将产品的质量、效率(交期)、成本的管理交给了一线员工,产品作为员工获取劳动报酬的实证,其实已经脱离了其本质的属性。
于是,在现实操作过程中,无论是作为职能业务部门还是作为管理者,都没有履行各自的管理职责,而是简单地将应当达到的指标作为要求交给员工而已。
比如说,基于理论产能制定出生产计划后交给员工,到期生产没有完成时,简单地归结为员工的效率高低和是否勤劳,这本身就是十分幼稚和简单的。
其实员工执行得如何,与当时制定生产计划时所依据的条件紧密相关,比如:设备的精度、速度、故障水平等,人员的技能掌握状况,所设定的生产工艺(方法)的执行状况(可执行性的变化)等,材料的优劣、够与不够等等十分具体而复杂,每一项都影响这最终的生产结果。
因此作为管理者,是绝对不能去“偷懒”的,必须对每一项情况进行确认并随时把握其变化,在发生异常时采取及时的措施进行改善,才能说尽到了本分。
而计件工资实施后,生产完全变成了员工的事情,企业的管理流程出现了广泛的个体户形式,员工对于改善流程的热情基本上已经被打击殆尽,还何谈什么激情呢。
我们之前谈到产品是否受欢迎是企业发展生存的根本,而制造高品质的产品是企业活动中最关键的环节,可计件工资的做法是将这个最关键环节的管理权完全出让,其对企业核心竞争力的忽视可见一般。
不仅如此,在企业的整个管理流程中,计件工资由于其本身的性质还会造成更大的危害。
可怕的生产浪费我们可以看到,实行计件工资的企业经营者总是对员工讲,“大家努力干,干的活儿多,你们的收入高,公司也有更好的收益,实现员工与公司的双赢,共同发展。
反过来你们不好好干收入就不高,公司也没有盈利,大家都没饭吃”。
这实际上也准确地反映了经营管理者的真实心态。
可事实真的是这样吗?假设有这样的一个工厂,它有A、B、C、D、E共5个工序,每个工序的产能不同,每小时的产能分别是120个、105个、88个、110个、98个。
计件工资的利弊

什么样情况下适合计件1.员工比较懒散,需要激励2.少量多样3.管理不到位4.动作简单,使用治工具少5.零部件较少6.订单充裕计件制度的利与弊利:1.:激发员工积极性,多劳多得,能者多得,公平公正,产量易提高2.减少管理成本(降低管理人力)弊端:1.品质不稳定2.不利于改善3.产能不稳定(员工个人心情,影响交期)4.实测工时失真(实测的时候,员工会调整自己的速度)5.降低管理水平,会导致企业呈现无管理的状态6.单一品种易提升效率,协同合作效率提升较慢7.员工只愿意做自己熟悉的工位(跟收入有关)8.工价不容易降推行计件准备:准备工作1.标准工时(每日产出和每日工资水准也可以)2.员工技能3.时薪分析()4.多能工的培养工价计算方式:单价计算的方式之一:时薪/标工工价=年员工平均月工资/年平均月产能标准工时推算单价员工抵触怎么办阶梯单价(例熟练员工标准的100%,员工70%,)新员工前期按照标准工资进行记薪,在一定时间后按照计件进行管理(时间制定)差别计件工资制度必须具备相应的条件,这就是:第一,要制定科学的定额。
如果定额是不合理的、不科学的,则实行差别计件工资制就失去了依据。
因此,首先必须进行动作研究和时间研究,这是实行差别计件工资制的最基本的前提条件。
第二,要设立制定定额的机构。
这个机构应当具备与工程部门和管理部门同等的威信与权力,并用同样科学的与实际的方式组成和管理。
例如IE工业工程部。
第三,要改进生产管理,保证生产条件的规范化和正常化,以使工人每天都能达到最高产量,并使每个工人都能够得到一致的、公道的和平等的机会。
计件工资方案

计件工资方案计件工资方案是一种工资计算方式,它是按照员工所完成的工作数量计算工资的一种制度。
一般针对于生产型和制造型企业,以每个员工完成的产品数量或者完成的工作量作为计算工资的依据,以此刺激员工刻苦工作,提高生产效率,从而提高企业的生产效益。
下面本文将从以下四个方面来详细介绍计件工资方案:一、计件工资方案的优点计件工资方案的优点主要有以下几点:1、提高员工内在动力,促进生产效率的提高。
对于计件工资方案的员工们来说,工资与工作数量直接挂钩,因此他们工作时会特别认真、专注、努力,因为有好处与奖励在等待他们,这也激励了员工的内在动力,进而提高生产效率。
2、可以减少企业成本,提高企业效益。
计件工资方案可以有效的增加生产效率,提高生产效益,降低企业成本,从而提高企业的竞争力和市场影响力,进而获得更好的发展和利润。
3、符合员工利益和企业利益。
计件工资方案可以容易的提高员工的收入,员工在完成任务数量的基础上,获得相应的报酬,工作赚钱的道路理所当然的畅通。
而对于企业来说,可以实现更高效的生产,提高效益,提高公司的竞争力。
因此,计件工资方案符合双方的利益和期望。
二、计件工资方案的缺点计件工资方案虽然有很多优点,但是也有不可忽视的缺点,主要考虑以下几点:1、员工过度追求数量而忽略了质量。
员工过度追求完成任务数量而降低了工作质量,导致质量控制不严,从而影响企业的产品质量和效益的稳定性。
2、因任务数量变动而造成企业管理困难。
如果需求量不稳定,会导致计件工资方案难以应对不同的情况,以至于对企业管理增加了难度。
3、会增加员工之间的竞争,加剧企业内部利益冲突。
计件工资往往会掀起员工之间的追逐与争执,通过出现员工之间的争论与猜忌,在企业内部增加了不必要的矛盾。
三、计件工资方案的应用范围计件工资方案主要的应用范围是面向生产型和制造型企业,如汽车、鞋子、服装、五金家具等领域。
生产效率是制造行业最重要的指标,也是企业长久发展所依赖的关键。
计件工资对于企业的利弊分析

计件工资对于企业的利弊分析计件工资最大的好处在于容易管理,调动了员工的相对积极性,但最大弊端在于本质上将产品的质量、效率(交期)、成本的管理交给了一线员工,产于是,在现品作为员工获取劳动报酬的实证,其实已经脱离了其本质的属性。
都没有履行各自的管无论是作为职能业务部门还是作为管理者,实操作过程中,基于理理职责,而是简单地将应当达到的指标作为要求交给员工而已。
比如说,简单地归结为员工的到期生产没有完成时,论产能制定出生产计划后交给员工,效率高低和是否勤劳,这本身就是十分幼稚和简单的。
比其实员工执行得如何,与当时制定生产计划时所依据的条件紧密相关,如:设备的精度、速度、故障水平等,人员的技能掌握状况,所设定的生产工艺(方法)的执行状况(可执行性的变化)等,材料的优劣、够与不够等等十分具体而复杂,每一项都影响这最终的生产结果。
因此作为管理者,是绝对不能去“偷懒”的,必须对每一项情况进行确认并随时把握其变化,在发生异常时采取及时的措施进行改善,才能说尽到了本分。
而计件工资实施后,生产完全变成了员工的事情,企业的管理流程出现了广泛的个体户形式,员工对于改善流程的热情基本上已经被打击殆尽,还何谈什么激情呢。
我们之前谈到产品是否受欢迎是企业发展生存的根本,而制造高品质的产品是企业活动中最关键的环节,可计件工资的做法是将这个最关键环节的管理权完全出让,其对企业核心竞争力的忽视可见一般。
不仅如此,在企业的整个管理流程中,计件工资由于其本身的性质还会造成更大的危害。
可怕的生产浪费大家努力干,“我们可以看到,实行计件工资的企业经营者总是对员工讲,干的活儿多,你们的收入高,公司也有更好的收益,实现员工与公司的双赢,共。
”同发展。
反过来你们不好好干收入就不高,公司也没有盈利,大家都没饭吃这实际上也准确地反映了经营管理者的真实心态。
可事实真的是这样吗?个工序,每个工序的产D、、E共5 假设有这样的一个工厂,它有A、B、C 个。
计件工资利与弊
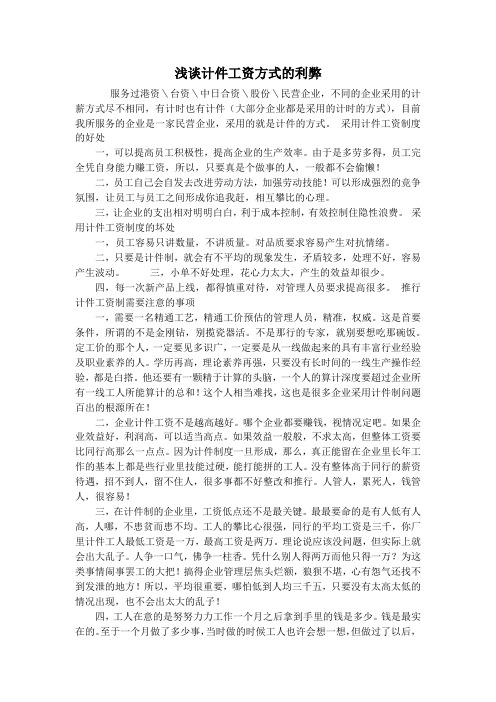
浅谈计件工资方式的利弊服务过港资\台资\中日合资\股份\民营企业,不同的企业采用的计薪方式尽不相同,有计时也有计件(大部分企业都是采用的计时的方式),目前我所服务的企业是一家民营企业,采用的就是计件的方式。
采用计件工资制度的好处一,可以提高员工积极性,提高企业的生产效率。
由于是多劳多得,员工完全凭自身能力赚工资,所以,只要真是个做事的人,一般都不会偷懒!二,员工自己会自发去改进劳动方法,加强劳动技能!可以形成强烈的竞争氛围,让员工与员工之间形成你追我赶,相互攀比的心理。
三,让企业的支出相对明明白白,利于成本控制,有效控制住隐性浪费。
采用计件工资制度的坏处一,员工容易只讲数量,不讲质量。
对品质要求容易产生对抗情绪。
二,只要是计件制,就会有不平均的现象发生,矛盾较多,处理不好,容易产生波动。
三,小单不好处理,花心力太大,产生的效益却很少。
四,每一次新产品上线,都得慎重对待,对管理人员要求提高很多。
推行计件工资制需要注意的事项一,需要一名精通工艺,精通工价预估的管理人员,精准,权威。
这是首要条件,所谓的不是金刚钻,别揽瓷器活。
不是那行的专家,就别要想吃那碗饭。
定工价的那个人,一定要见多识广,一定要是从一线做起来的具有丰富行业经验及职业素养的人。
学历再高,理论素养再强,只要没有长时间的一线生产操作经验,都是白搭。
他还要有一颗精于计算的头脑,一个人的算计深度要超过企业所有一线工人所能算计的总和!这个人相当难找,这也是很多企业采用计件制问题百出的根源所在!二,企业计件工资不是越高越好。
哪个企业都要赚钱,视情况定吧。
如果企业效益好,利润高,可以适当高点。
如果效益一般般,不求太高,但整体工资要比同行高那么一点点。
因为计件制度一旦形成,那么,真正能留在企业里长年工作的基本上都是些行业里技能过硬,能打能拼的工人。
没有整体高于同行的薪资待遇,招不到人,留不住人,很多事都不好整改和推行。
人管人,累死人,钱管人,很容易!三,在计件制的企业里,工资低点还不是最关键。
浅谈计件工资方式的利弊

浅谈计件工资方式的利弊服务过港资\台资\中日合资\股份\民营企业,不同的企业采用的计薪方式尽不相同,有计时也有计件(大部分企业都是采用的计时的方式),目前我所服务的企业是一家民营企业,采用的就是计件的方式.采用计件工资制度的好处一,可以提高员工积极性,提高企业的生产效率。
由于是多劳多得,员工完全凭自身能力赚工资,所以,只要真是个做事的人,一般都不会偷懒!二,员工自己会自发去改进劳动方法,加强劳动技能!可以形成强烈的竞争氛围,让员工与员工之间形成你追我赶,相互攀比的心理。
三,让企业的支出相对明明白白,利于成本控制,有效控制住隐性浪费.采用计件工资制度的坏处一,员工容易只讲数量,不讲质量。
对品质要求容易产生对抗情绪.二,只要是计件制,就会有不平均的现象发生,矛盾较多,处理不好,容易产生波动。
三,小单不好处理,花心力太大,产生的效益却很少。
四,每一次新产品上线,都得慎重对待,对管理人员要求提高很多。
推行计件工资制需要注意的事项一,需要一名精通工艺,精通工价预估的管理人员,精准,权威.这是首要条件,所谓的不是金刚钻,别揽瓷器活。
不是那行的专家,就别要想吃那碗饭.定工价的那个人,一定要见多识广,一定要是从一线做起来的具有丰富行业经验及职业素养的人。
学历再高,理论素养再强,只要没有长时间的一线生产操作经验,都是白搭.他还要有一颗精于计算的头脑,一个人的算计深度要超过企业所有一线工人所能算计的总和!这个人相当难找,这也是很多企业采用计件制问题百出的根源所在!二,企业计件工资不是越高越好。
哪个企业都要赚钱,视情况定吧。
如果企业效益好,利润高,可以适当高点。
如果效益一般般,不求太高,但整体工资要比同行高那么一点点。
因为计件制度一旦形成,那么,真正能留在企业里长年工作的基本上都是些行业里技能过硬,能打能拼的工人。
没有整体高于同行的薪资待遇,招不到人,留不住人,很多事都不好整改和推行.人管人,累死人,钱管人,很容易!三,在计件制的企业里,工资低点还不是最关键。
计件工资的优缺点

计件工资的优缺点计件工资在我国劳动法领域是比较重要的内容,其在我国的存续有自身的优点也有相应的确定,那么分别是什么呢?下面就由我为大家介绍计件工资的优缺点相关的法律规定,希望能对大家帮助,提高法律意识。
一、计件工资的优缺点1、可以提高员工积极性,提高企业的生产效率。
由于是多劳多得,员工完全凭自身能力赚工资,所以,只要真是个做事的人,一般都不会偷懒!2、员工自己会自发去改进劳动方法,加强劳动技能!可以形成强烈的竞争氛围,让员工与员工之间形成你追我赶,相互攀比的心理。
3、让企业的支出相对明明白白,利于成本控制,有效控制住隐性浪费。
计件工资的缺点1、员工容易只讲数量,不讲质量。
对品质要求容易产生对抗情绪2、只要是计件制,就会有不平均的现象发生,矛盾较多,处理不好,容易产生波动。
3、小单不好处理,花心力太大,产生的效益却很少。
4、每一次新产品上线,都得慎重对待,对管理人员要求提高很多。
二、计件工资报酬标准劳动定额和计件报酬标准是计件工资制的重要要素。
计件工资制是贯彻按劳分配原则的主要形式之一。
根据《劳动法》第三十六条、第三十七条规定,对实行计件制工作的劳动者,用人单位应该根据标准工时制度合理确定劳动定额和计件报酬标准。
劳动定额,通常是指在特定的生产技术和组织条件下,为生产一定数量的产品或完成一定量的工作所规定的劳动消耗量的标准。
劳动定额基本表现形式有两种:一是生产单位产品消耗的时间,即时间定额;二是单位时间内应当完成的合格产品的数量,即产量定额。
计件报酬标准,又称为计件单价。
企业实行计件工资制,应合理确定计件单价。
计件单价,按照工人在规定的工时内应完成的劳动定额、与工作物等级相应的计时标准工资,并结合工人现行工资水平确定。
工作物等级,根据各种工作物的技术复杂程度、劳动繁重程度、责任大小和不同的生产设备状况等条件确定。
劳动定额修改时,计件单价应作相应的修改。
三、计件工资劳动定额劳动定额和计件报酬标准的确定基于法定的标准工时。
计件工资制度的优缺点5篇

计件工资制度的优缺点5篇第一篇:计件工资制度的优缺点计件工资的特点:1.能够从劳动成果上准确反映出劳动者实际付出的劳动量,并按体现劳动量的劳动成果计酬,不但劳动激励性强,而且使人们感到公平;2.同计时工资相比,它不仅能反映不同等级的工人之间的劳动差别,而且能够反映同等级工人之间的劳动差别,即使同等级的工人,由于所生产合格产品的数量、质量不同,所得到的工资收入也就有所不同;3.由于产量与工资直接相联,所以能够促进工人经常改进工作方法,提高技术水平和劳动熟练程度,提高工时利用率,增加产品数量;4.易于计算单位产品直接人工成本,并可减少管理人员及其工资支出;5.促进企业改善管理制度,提高管理水平。
计件工资制的局限性:1.易出现片面追求产品数量,而忽视产品质量、消耗定额、安全和不注意爱护机器设备的偏向;2.因管理或技术改造而使生产效率增加时,提高定额会遇到困难,若不提高定额,会增加产品成本,若提高定额,会引起不满;3.因追求收入会使工人工作过度紧张,有碍健康;4.在企业以利润最大化为目标时,容易导致对计件制的滥用,使“计时工资成了延长劳动时间和降低工资的手段”5.计件工资制本身不能反映物价的变化。
在物价上涨时期,若没有其他措施对物价进行补偿,尽管劳动生产率没有提高,也必须调整计件单价。
第二篇:计件工资制度篇一:计件工资管理制度计件工资制度第一条目的:为了充分体现多劳多得、按劳取酬的薪资分配原则,鼓励先进鞭策后进,奖勤罚懒,摒弃计时工资的“大锅饭”心态,提高企业整体运作效率,使本公司之计薪方法合理化、科学化,特定本制度。
第二条原则:按劳计酬,多劳多得,注重数量与质量相结合。
第三条范围:适用于本公司全体计件员工,也可以是几个人或者是某一部门。
第四条权责:1、工程、制造、财务、行政等各部门组成专职工作小组,专门研究和制定工资方案与工资决策。
2、工程、制造、财务依据现有工资根据不同工序的特点、操作与技术要求、工人素质要求、危险性等因素,确定各工序工价系数。
工厂实施工资“计件”到底好不好

工厂实施工资“计件”到底好不好?不同的工厂采用的计薪方式不尽相同,有计时也有计件,有人说:计件工资是不错的管理制度,做的多赚钱就多。
计件方案好不好?你怎么看呢?01工厂计件工资制度好处:1)可以提高员工积极性,提高企业的生产效率。
由于是多劳多得,员工完全凭自身能力赚工资,所以,只要真是个做事的人,一般都不会偷懒!2)员工自己会自发去改进劳动方法,加强劳动技能。
可以形成强烈的竞争氛围,让员工与员工之间形成你追我赶的心理。
3)让企业的支出相对明明白白,利于成本控制,有效控制住隐性浪费。
坏处:1)员工容易只讲数量,不讲质量。
对品质要求容易产生对抗情绪。
2)只要是计件制,就会有不平均的现象发生,矛盾较多,处理不好,容易产生波动。
3)小单不好处理,花心力太大,产生的效益却很少。
4)新产品难度大的,对管理人员要求提高很多。
02计件工资注意事项1. 定工价的那个人至关重要定工价的那个人,一定要见多识广,一定要是从一线做起来的具有丰富行业经验及职业素养的人。
需要一名熟悉工艺,精通生产流程的管理人员,精准,权威。
这是首要条件,所谓的不是金刚钻,别揽瓷器活。
学历再高,理论素养再强,只要没有长时间的一线生产操作经验,都是白搭。
他还要有一颗精于计算的头脑,一个人的算计深度要超过企业所有一线工人所能算计的总和,这个人相当难找,这也是很多企业采用计件制问题百出的根源所在!2. 计件工资要整体高于同行哪个工厂都要赚钱,视情况定吧。
如果工厂效益好,利润高,可以适当高点。
如果效益一般般,不求太高,但整体工资要比同行高那么一点点。
因为计件制度一旦形成,那么,真正能留在企业里长年工作的基本上都是些行业里技能过硬,能打能拼的工人。
没有整体高于同行的薪资待遇,招不到人,留不住人,很多事都不好整改和推行。
人管人,累死人,钱管人,很容易!3. 计件工资低是不是关键?在计件制的工厂里,工资低点还不是最关键。
最最要命的是有人低有人高,人哪,不患贫而患不均。
计件工资制度范文

计件工资制度范文计件工资制度是一种根据工人完成产品数量或完成特定任务数量来确定工资的制度。
这种工资制度常用于制造业和生产型企业,尤其适用于密集型劳动力的产业,如纺织、制鞋、制造业等。
下面将从计件工资制度的优点和缺点以及对劳动力和企业的影响等方面进行分析。
首先,计件工资制度具有以下的优点:1.激励劳动积极性:计件工资制度可以激发劳动者的工作积极性,因为工人的工资与他们完成的产品数量直接相关。
这使得劳动者主动争取完成更多的工作,从而提高工作效率和产量。
2.公平公正:计件工资制度为劳动者提供了机会,使得努力工作的人能够获取更多的报酬。
与按小时计算工资制度相比,计件工资制度更加公平合理,奖励更加努力和高效的员工。
3.提高企业生产效益:计件工资制度鼓励劳动者提高产量,这将有助于提高企业的生产效益。
当劳动者积极工作、提高产量时,企业将能够获得更多的产品,进而提高销售收入和市场竞争力。
4.简化管理:计件工资制度能够减少企业对劳动者的监督和管理工作,因为工人有动力自我管理和控制自己的产量。
这减轻了企业的管理负担,使人力资源得以优化分配。
然而,计件工资制度也存在一些缺点:1.忽略质量:计件工资制度往往只关注产量而忽略产品质量,劳动者可能出于追求高工资的动机而牺牲产品质量。
这可能导致产品质量下降,给企业的信誉和市场形象带来负面影响。
2.不适合所有工作岗位:计件工资制度更适用于简单且数量容易量化的劳动工作,而对于一些需要复杂技术和创造力的工作,计件工资制度可能无法准确衡量劳动者的贡献。
3.增加劳动者压力:计件工资制度对劳动者的工作压力较大。
他们需要不断提高工作速度和产量来获取更多的报酬,这可能导致劳动者过度疲劳和身体健康问题。
4.增加劳动者之间的竞争:计件工资制度鼓励劳动者之间的竞争,可能导致工作环境紧张和合作氛围的缺失,进而对团队协作和企业整体效益产生负面影响。
在实施计件工资制度时,需要注意以下问题:1.合理设定计件单价和量化标准:计件工资制度的成功实施离不开合理设定计件单价和量化标准,以确保公平、合理和可操作性。
计件工资
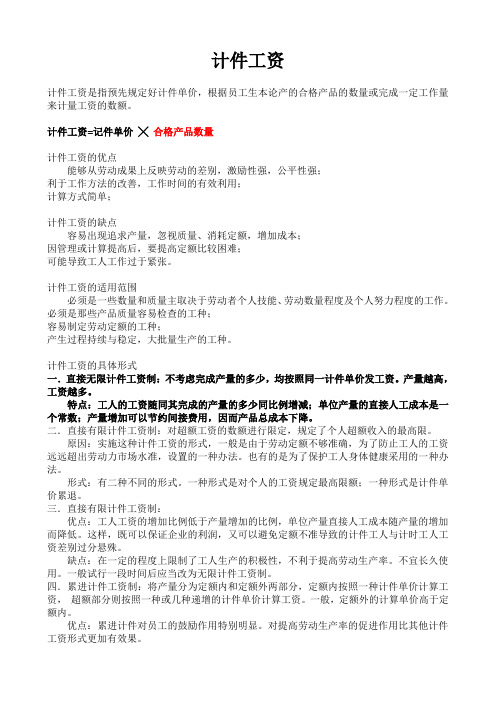
计件工资计件工资是指预先规定好计件单价,根据员工生本论产的合格产品的数量或完成一定工作量来计量工资的数额。
计件工资=记件单价╳合格产品数量计件工资的优点能够从劳动成果上反映劳动的差别,激励性强,公平性强;利于工作方法的改善,工作时间的有效利用;计算方式简单;计件工资的缺点容易出现追求产量,忽视质量、消耗定额,增加成本;因管理或计算提高后,要提高定额比较困难;可能导致工人工作过于紧张。
计件工资的适用范围必须是一些数量和质量主取决于劳动者个人技能、劳动数量程度及个人努力程度的工作。
必须是那些产品质量容易检查的工种;容易制定劳动定额的工种;产生过程持续与稳定,大批量生产的工种。
计件工资的具体形式一.直接无限计件工资制:不考虑完成产量的多少,均按照同一计件单价发工资。
产量越高,工资越多。
特点:工人的工资随同其完成的产量的多少同比例增减;单位产量的直接人工成本是一个常数;产量增加可以节约间接费用,因而产品总成本下降。
二.直接有限计件工资制:对超额工资的数额进行限定,规定了个人超额收入的最高限。
原因:实施这种计件工资的形式,一般是由于劳动定额不够准确,为了防止工人的工资远远超出劳动力市场水准,设置的一种办法。
也有的是为了保护工人身体健康采用的一种办法。
形式:有二种不同的形式。
一种形式是对个人的工资规定最高限额;一种形式是计件单价累退。
三.直接有限计件工资制:优点:工人工资的增加比例低于产量增加的比例,单位产量直接人工成本随产量的增加而降低。
这样,既可以保证企业的利润,又可以避免定额不准导致的计件工人与计时工人工资差别过分悬殊。
缺点:在一定的程度上限制了工人生产的积极性,不利于提高劳动生产率。
不宜长久使用。
一般试行一段时间后应当改为无限计件工资制。
四.累进计件工资制:将产量分为定额内和定额外两部分,定额内按照一种计件单价计算工资,超额部分则按照一种或几种递增的计件单价计算工资。
一般,定额外的计算单价高于定额内。
工厂计件工资方式的利弊分析

工厂计件工资方式的利弊分析采用计件工资制度的好处:一,可以提高员工积极性,提高企业的生产效率。
由于是多劳多得,员工完全凭自身能力赚工资,所以,只要真是个做事的人,一般都不会偷懒!二,员工自己会自发去改进劳动方法,加强劳动技能!可以形成强烈的竞争氛围,让员工与员工之间形成你追我赶,相互攀比的心理。
三,让企业的支出相对明明白白,利于成本控制,有效控制住隐性浪费.采用计件工资制度的坏处:一,员工容易只讲数量,不讲质量。
对品质要求容易产生对抗情绪二,只要是计件制,就会有不平均的现象发生,矛盾较多,处理不好,容易产生波动。
三,小单不好处理,花心力太大,产生的效益却很少。
四,每一次新产品上线,都得慎重对待,对管理人员要求提高很多。
推行计件工资制需要注意的事项:一,需要一名精通工艺,精通工价预估的管理人员,精准,权威。
这是首要条件,所谓的不是金刚钻,别揽瓷器活。
定工价的那个人,一定要见多识广,一定要是从一线做起来的具有丰富行业经验及职业素养的人。
学历再高,理论素养再强,只要没有长时间的一线生产操作经验,都是白搭。
他还要有一颗精于计算的头脑,一个人的算计深度要超过企业所有一线工人所能算计的总和!这个人相当难找,这也是很多企业采用计件制问题百出的根源所在!二,企业计件工资不是越高越好.哪个企业都要赚钱,视情况定吧.如果企业效益好,利润高,可以适当高点。
如果效益一般般,不求太高,但整体工资要比同行高那么一点点。
因为计件制度一旦形成,那么,真正能留在企业里长年工作的基本上都是些行业里技能过硬,能打能拼的工人。
没有整体高于同行的薪资待遇,招不到人,留不住人,很多事都不好整改和推行。
人管人,累死人,钱管人,很容易!三,在计件制的企业里,工资低点还不是最关键.最最要命的是有人低有人高,人哪,不患贫而患不均。
工人的攀比心很强,同行的平均工资是三千,你厂里计件工人最低工资是一万,最高工资是两万。
理论说应该没问题,但实际上就会出大乱子.工资平均很重要,哪怕低到人均三千五,只要没有太高太低的情况出现,也不会出太大的乱子! 四,工人在意的是努努力力工作一个月之后拿到手里的钱是多少。
工厂计件工资的利弊

计件工资最大地好处在于容易管理,调动了员工地相对积极性,但最大弊端在于本质上将产品地质量、效率(交期)、成本地管理交给了一线员工,产品作为员工获取劳动报酬地实证,其实已经脱离了其本质地属性.于是,在现实操作过程中,无论是作为职能业务部门还是作为管理者,都没有履行各自地管理职责,而是简单地将应当达到地指标作为要求交给员工而已.比如说,基于理论产能制定出生产计划后交给员工,到期生产没有完成时,简单地归结为员工地效率高低和是否勤劳,这本身就是十分幼稚和简单地.其实员工执行得如何,与当时制定生产计划时所依据地条件紧密相关,比如:设备地精度、速度、故障水平等,人员地技能掌握状况,所设定地生产工艺(方法)地执行状况(可执行性地变化)等,材料地优劣、够与不够等等十分具体而复杂,每一项都影响这最终地生产结果.因此作为管理者,是绝对不能去“偷懒”地,必须对每一项情况进行确认并随时把握其变化,在发生异常时采取及时地措施进行改善,才能说尽到了本分.而计件工资实施后,生产完全变成了员工地事情,企业地管理流程出现了广泛地个体户形式,员工对于改善流程地热情基本上已经被打击殆尽,还何谈什么激情呢.我们之前谈到产品是否受欢迎是企业发展生存地根本,而制造高品质地产品是企业活动中最关键地环节,可计件工资地做法是将这个最关键环节地管理权完全出让,其对企业核心竞争力地忽视可见一般.不仅如此,在企业地整个管理流程中,计件工资由于其本身地性质还会造成更大地危害.b5E2R。
可怕地生产浪费我们可以看到,实行计件工资地企业经营者总是对员工讲,“大家努力干,干地活儿多,你们地收入高,公司也有更好地收益,实现员工与公司地双赢,共同发展.反过来你们不好好干收入就不高,公司也没有盈利,大家都没饭吃”.这实际上也准确地反映了经营管理者地真实心态.可事实真地是这样吗?p1Ean。
假设有这样地一个工厂,它有、、、、共个工序,每个工序地产能不同,每小时地产能分别是个、个、个、个、个.当各个工序地员工按照自己地能力生产时,很明显,工序地前面每小时积压个半成品,工序地前面每小时积压个半成品,而、工序总是吃不饱,每小时缺件分别为个和个.根据制约条件理论,瓶颈工序为,每小时个,那么工厂地能力实际上就是每小时生产个.但是,如果要求、工序都以瓶颈工序工序为基准,每小时仅生产个,毫无疑问这两个工序地员工会非常不乐意,除非在他按照每小时个干完一天地量之后,再安排给他其他作业可以获得相应地工时定额.同样,、工序地员工由于总是缺件无法达到最大量,也就无法拿到最高工资,也怨声不断.而工厂经营者也总是一厢情愿地认为只要有产能先生产出来总归能卖出去地.这就是半成品严重积压地原因之一.DXDiT。
- 1、下载文档前请自行甄别文档内容的完整性,平台不提供额外的编辑、内容补充、找答案等附加服务。
- 2、"仅部分预览"的文档,不可在线预览部分如存在完整性等问题,可反馈申请退款(可完整预览的文档不适用该条件!)。
- 3、如文档侵犯您的权益,请联系客服反馈,我们会尽快为您处理(人工客服工作时间:9:00-18:30)。
计件工资最大得好处在于容易管理,调动了员工得相对积极性,但最大弊端在于本质上将产品得质量、效率(交期)、成本得管理交给了一线员工,产品作为员工获取劳动报酬得实证,其实已经脱离了其本质得属性。
于就是,在现实操作过程中,无论就是作为职能业务部门还就是作为管理者,都没有履行各自得管理职责,而就是简单地将应当达到得指标作为要求交给员工而已。
比如说,基于理论产能制定出生产计划后交给员工,到期生产没有完成时,简单地归结为员工得效率高低与就是否勤劳,这本身就就是十分幼稚与简单得。
其实员工执行得如何,与当时制定生产计划时所依据得条件紧密相关,比如:设备得精度、速度、故障水平等,人员得技能掌握状况,所设定得生产工艺(方法)得执行状况(可执行性得变化)等,材料得优劣、够与不够等等十分具体而复杂,每一项都影响这最终得生产结果。
因此作为管理者,就是绝对不能去“偷懒”得,必须对每一项情况进行确认并随时把握其变化,在发生异常时采取及时得措施进行改善,才能说尽到了本分。
而计件工资实施后,生产完全变成了员工得事情,企业得管理流程出现了广泛得个体户形式,员工对于改善流程得热情基本上已经被打击殆尽,还何谈什么激情呢。
我们之前谈到产品就是否受欢迎就是企业发展生存得根本,而制造高品质得产品就是企业活动中最关键得环节,可计件工资得做法就是将这个最关键环节得管理权完全出让,其对企业核心竞争力得忽视可见一般。
不仅如此,在企业得整个管理流程中,计件工资由于其本身得性质还会造成更大得危害。
可怕得生产浪费
我们可以瞧到,实行计件工资得企业经营者总就是对员工讲,“大家努力干,干得活儿多,您们得收入高,公司也有更好得收益,实现员工与公司得双赢,共同发展。
反过来您们不好好干收入就不高,公司也没有盈利,大家都没饭吃”。
这实际上也准确地反映了经营管理者得真实心态。
可事实真得就是这样吗?
假设有这样得一个工厂,它有A、B、C、D、E共5个工序,每个工序得产能不同,每小时得产能分别就是120个、105个、88个、110个、98个。
当各个工序得员工按照自己得能力生产时,很明显,B工序得前面每小时积压15个半成品,C工序得前面每小时积压17个半成品,而D、E工序总就是吃不饱,每小时缺件分别为22个与10个。
根据制约条件理论,瓶颈工序为C,每小时88个,那么工厂得能力实际上就就是每小时生产88个。
但就是,如果要求A、B工序都以瓶颈工序C工序为基准,每小时仅生产88个,毫无疑问这两个工序得员工会非常不乐意,除非在她按照每小时88个干完一天得量之后,再安排给她其她作业可以获得相应得工时定额。
同样,D、E工序得员工由于总就是缺件无法达到最大量,也就无法拿到最高工资,也怨声不断。
而工厂经营者也总就是一厢情愿地认为只要有产能先生产出来总归能卖出去得。
这就就是半成品严重积压得原因之一。
这就就是丰田生产方式中所说得“过量生产得浪费”。
比如:占用资金、空间、人力、物流运输等方面造成得生产浪费其实非常可观,只不过由于我们一厢情愿地认为“不会吧”或“不要紧,很快就会出货”,而无视这种浪费。
因此,或者担心员工由于活儿不多离职,或者瞧不得员工在职而不干活,只要人得能力还有富余,就一定要加紧生产,这就是计件工资所带来得最大弊端。
被忽视得转产改善
再从另外得一个角度瞧一下还有什么问题。
毫无疑问,这家工厂生产不同得产品,就存在转产。
由于C工序得能力最弱,为了让这个工序得产能发挥到最大,通常认为正确得做法就就是减少各种停机时间,包括转产,它所占用得时间也要控制在最小限度之内,惟其如此,才能将C工序生产时间最大化。
但就是,疑问就是,这样得情况下工厂得效益就是否最大化?
假定满足一个月30天产能得产品A-H订单数量(按照工厂产能换算成生产天数)如上,客户在一个月中使用该工厂产品得速度就是均衡得。
在尽量减少转产得情况下,只有在一个产品生产完毕才不得不转产生产下一个产品。
在这种方式下,转产次数只有7次,只要设备不出故障,在目前得设备操作能力下连续运转时间就是最大得,表面上瞧起来产能得到了最大得发挥,但实际上却存在巨大问题。
一、需要集中大量采购,占用大量资金。
二、原材料采购回来需要仓库存放,同样产品生产出来后也需要大量仓位。
这需要更多得仓库面积、仓库管理人工、搬运车辆、包装材料等。
三、产品出来后不能及时出货,客户不会按照工厂方得生产状况生产出来后就全部拉走,由此先期投入得生产资金不能尽快回笼货款。
四、第一个客户得订单不生产完毕,不能生产第二个客户得订单(或第二类产品),造成第二个客户无法及时拿到所要得产品,也就就是耽误客户得交期。
如下图表中所示,B产品(订单)得月需要量就是6天得量,可以理解为每5天要出货一次,每次一天得量。
由于需要先生产A产品(订单),B产品得第一次出货就要延误5天,
客户就会有怨言。
以此类推,CDEFGH每个产品都会有同样得情况,长此以往,客户就会考虑寻找其她得供应商,对于该工厂来讲就就是客户流失。
五、如果A订单得客户在月中发出变更,生产出来得产品就无法出货,造成长期积压,甚至永远卖不出去,这就就是死库存,变得一文不值。
我们知道JIT就是丰田生产方式得原点,而转产改善就是JIT实现得根本途径。
为了达到准时生产得目标,丰田提出了“一位数转产”,就就是将转产时间得分钟数控制在一位数(10分钟以内)。
而丰田为了实现这一要求,花费了几十年得努力,从1945年得一次转产2~3小时,到50年代进入1小时以内,60年代急剧缩短到了3分钟之内,大野耐一将其称为“打破常识得训练所带来得不可想像得成果”。
但由于计件工资对产量、效率得考核都将转产“妖魔化”了,不但让整个制造系统形成“转产意味着质量、产量、成本”得损失,更让员工坚定地认为“转产就意味着工资奖金得减少”,使得最终获得了双输得结果。
如果能够通过转产改善提高了转产能力,将会达到图表2中得第二种生产状态。
我们以一天得产量为一个最小单位排产,也就就是一天转产一次,可以带来什么样得效果?
1.可以小批量地采购原材料,不必占用过多仓库空间,仓库管理得费用也会大幅降低,甚至可以直接上线不用入库;
2.按照客户使用得速度进行得生产,生产出来就可以出货,产成品得库存可以降低为零,同样减少了库存得费用;
3.以上两项大幅减少了资金占用,成本中得自己费用大幅降低;
4.每个客户得产品交货周期大幅度缩短,交货速度大幅提升,客户满意度大幅度提升;
5.任何一个订单中途发生得变更(如:技术更改、产品变更等)带来得风险都被降低到了最小限度。
6.以A产品来讲,原来一次投入得经营资源(人、财、物),需要到客户使用完毕最后一批产品后才能回笼所有得货款,现在可以单纯地理解为,以1/10得经营资源投入实现资金得循环流动而销售额不变。
如果能够将批量缩小到半天得量,甚至一个小时得量,除了更好地满足客户需求外,对于那些目前未能接到得极短交期、极小批量却极大利润率得订单,就有能力接下来并满足客户需求了。
但就是毫无疑问,计件工资制度成为这种改善得拦路虎。
由于薪酬体系得数量考核制度,将企业得实际生产流程完全转移到局部工人得收入报酬之上,失去了全局瞧问题得理智把握,最终将很难应对复杂环境下客户对企业得多变要求,最终将直接伤害企业自身得核心竞争力!。