车身匹配设计要点101028
汽车车身设计重点
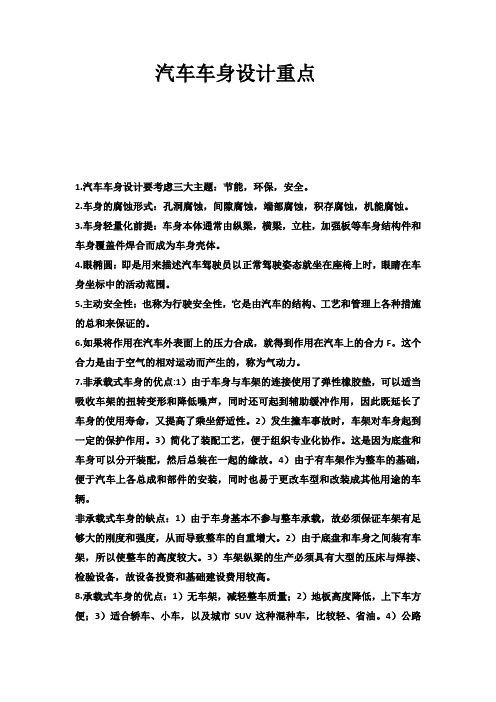
汽车车身设计重点1.汽车车身设计要考虑三大主题:节能,环保,安全。
2.车身的腐蚀形式:孔洞腐蚀,间隙腐蚀,端部腐蚀,积存腐蚀,机能腐蚀。
3.车身轻量化前提:车身本体通常由纵梁,横梁,立柱,加强板等车身结构件和车身覆盖件焊合而成为车身壳体。
4.眼椭圆:即是用来描述汽车驾驶员以正常驾驶姿态就坐在座椅上时,眼睛在车身坐标中的活动范围。
5.主动安全性:也称为行驶安全性,它是由汽车的结构、工艺和管理上各种措施的总和来保证的。
6.如果将作用在汽车外表面上的压力合成,就得到作用在汽车上的合力F。
这个合力是由于空气的相对运动而产生的,称为气动力。
7.非承载式车身的优点:1)由于车身与车架的连接使用了弹性橡胶垫,可以适当吸收车架的扭转变形和降低噪声,同时还可起到辅助缓冲作用,因此既延长了车身的使用寿命,又提高了乘坐舒适性。
2)发生撞车事故时,车架对车身起到一定的保护作用。
3)简化了装配工艺,便于组织专业化协作。
这是因为底盘和车身可以分开装配,然后总装在一起的缘故。
4)由于有车架作为整车的基础,便于汽车上各总成和部件的安装,同时也易于更改车型和改装成其他用途的车辆。
非承载式车身的缺点:1)由于车身基本不参与整车承载,故必须保证车架有足够大的刚度和强度,从而导致整车的自重增大。
2)由于底盘和车身之间装有车架,所以使整车的高度较大。
3)车架纵梁的生产必须具有大型的压床与焊接、检验设备,故设备投资和基础建设费用较高。
8.承载式车身的优点:1)无车架,减轻整车质量;2)地板高度降低,上下车方便;3)适合轿车、小车,以及城市SUV这种混种车,比较轻、省油。
4)公路行驶平稳,整体式车身比较安全。
承载式车身的缺点:1)传动系统和悬架的震动和噪音会直接传入车内,需采取防震和隔声措施;2)底盘强度远不如大梁结构的车身,当四个车轮受力不均匀时,车身会发生变形;3)制造成本偏高。
9.车身总体布置设计的性能要求:1)乘坐舒适性,2)车身的密封、隔热和隔声性能,3)安全性,4)视野性,5)上下车方便性,6)操纵方便性。
车身设计文档
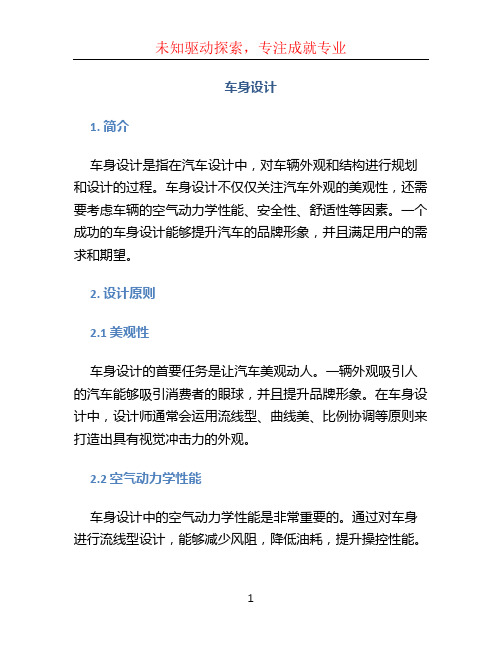
车身设计1. 简介车身设计是指在汽车设计中,对车辆外观和结构进行规划和设计的过程。
车身设计不仅仅关注汽车外观的美观性,还需要考虑车辆的空气动力学性能、安全性、舒适性等因素。
一个成功的车身设计能够提升汽车的品牌形象,并且满足用户的需求和期望。
2. 设计原则2.1 美观性车身设计的首要任务是让汽车美观动人。
一辆外观吸引人的汽车能够吸引消费者的眼球,并且提升品牌形象。
在车身设计中,设计师通常会运用流线型、曲线美、比例协调等原则来打造出具有视觉冲击力的外观。
2.2 空气动力学性能车身设计中的空气动力学性能是非常重要的。
通过对车身进行流线型设计,能够减少风阻,降低油耗,提升操控性能。
此外,合理的车身设计还能够减少风噪和飘移现象,提高汽车的稳定性和舒适性。
2.3 安全性在车身设计中,安全性是一个不可忽视的因素。
合理的车身结构和材料选择能够提供更好的碰撞保护,保障乘车人员的生命安全。
例如,采用高强度钢材料来构建车身能够提高车辆的抗碰撞能力。
2.4 实用性车身设计需要满足用户的实际需求和使用习惯。
设计师要注重车门开启角度、车身高度、车厢宽度等细节,以提升乘坐空间和使用便利性。
此外,车身设计还需要考虑到用户对于储物空间、行李箱容量等方面的需求。
3. 设计流程3.1 概念设计概念设计是车身设计的第一步。
在这个阶段,设计师会收集市场调研和用户需求,并且进行创意构思。
通过手绘或计算机辅助设计工具,设计师将自己的想法转化为初步的车身设计方案。
3.2 三维建模在确定了初步设计方案后,设计师会使用CAD软件进行车身的三维建模。
通过将设计方案转化为三维模型,设计师能够更加直观地观察和修改设计细节。
三维建模还能够帮助工程师进行工艺分析和生产准备。
3.3 动态仿真动态仿真是车身设计的重要环节之一。
通过运用流体力学和结构分析原理,设计师能够预测并优化汽车的空气动力学性能、悬挂系统、刹车系统等方面。
动态仿真可以帮助设计师找出设计中存在的问题,并进行改进。
汽车车身覆盖件检具设计技术要求
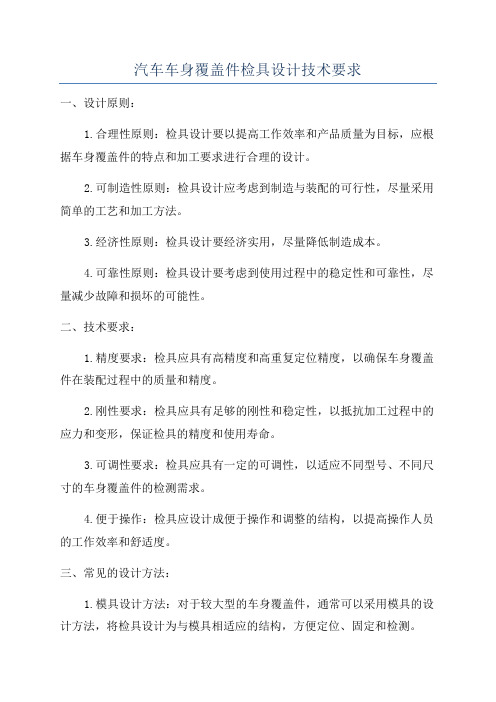
汽车车身覆盖件检具设计技术要求一、设计原则:1.合理性原则:检具设计要以提高工作效率和产品质量为目标,应根据车身覆盖件的特点和加工要求进行合理的设计。
2.可制造性原则:检具设计应考虑到制造与装配的可行性,尽量采用简单的工艺和加工方法。
3.经济性原则:检具设计要经济实用,尽量降低制造成本。
4.可靠性原则:检具设计要考虑到使用过程中的稳定性和可靠性,尽量减少故障和损坏的可能性。
二、技术要求:1.精度要求:检具应具有高精度和高重复定位精度,以确保车身覆盖件在装配过程中的质量和精度。
2.刚性要求:检具应具有足够的刚性和稳定性,以抵抗加工过程中的应力和变形,保证检具的精度和使用寿命。
3.可调性要求:检具应具有一定的可调性,以适应不同型号、不同尺寸的车身覆盖件的检测需求。
4.便于操作:检具应设计成便于操作和调整的结构,以提高操作人员的工作效率和舒适度。
三、常见的设计方法:1.模具设计方法:对于较大型的车身覆盖件,通常可以采用模具的设计方法,将检具设计为与模具相适应的结构,方便定位、固定和检测。
2.多级设计方法:对于较复杂的车身覆盖件,可以采用多级设计方法,通过分级检测,逐步确定检具的形状和尺寸。
3.模块化设计方法:对于常用的零部件和组件,可以采用模块化的设计方法,通过组合和调整模块,实现车身覆盖件的检测需求。
四、常见的检具种类:1.夹具:用于夹紧和固定车身覆盖件,保证尺寸的稳定和一致性。
2.测试仪器:用于测量和检测车身覆盖件的尺寸、形状和质量等指标。
3.定位工具:用于确定车身覆盖件的准确位置,保证装配的精度和质量。
4.校验工具:用于校验和调整检具的精度和定位精度,保证检具的准确性和一致性。
总结:汽车车身覆盖件检具设计是汽车制造中的一个重要环节。
设计时需要考虑合理性、可制造性、经济性和可靠性原则。
技术要求包括精度、刚性、可调性和便于操作等。
常见的设计方法有模具设计、多级设计和模块化设计等,常见的检具种类有夹具、测试仪器、定位工具和校验工具等。
白车身匹配技术
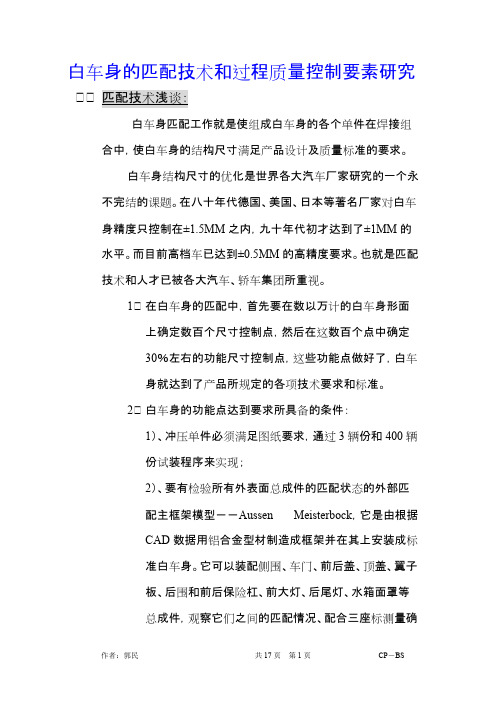
白车身的匹配技术和过程质量控制要素研究、、白车身匹配工作就是使组成白车身的各个单件在焊接组合中,使白车身的结构尺寸满足产品设计及质量标准的要求。
白车身结构尺寸的优化是世界各大汽车厂家研究的一个永不完结的课题。
在八十年代德国、美国、日本等著名厂家对白车身精度只控制在±1.5MM之内,九十年代初才达到了±1MM的水平。
而目前高档车已达到±0.5MM的高精度要求。
也就是匹配技术和人才已被各大汽车、轿车集团所重视。
1、在白车身的匹配中,首先要在数以万计的白车身形面上确定数百个尺寸控制点,然后在这数百个点中确定30%左右的功能尺寸控制点,这些功能点做好了,白车身就达到了产品所规定的各项技术要求和标准。
2、白车身的功能点达到要求所具备的条件:1)、冲压单件必须满足图纸要求,通过3辆份和400辆份试装程序来实现;2)、要有检验所有外表面总成件的匹配状态的外部匹配主框架模型--Aussen Meisterbock,它是由根据CAD数据用铝合金型材制造成框架并在其上安装成标准白车身。
它可以装配侧围、车门、前后盖、顶盖、翼子板、后围和前后保险杠、前大灯、后尾灯、水箱面罩等总成件,观察它们之间的匹配情况、配合三座标测量确定零件的更改数据。
(Aussen Meisterbock示意图)3)、要有检查内饰件与白车身匹配关系的内匹配主框架模型--Innen Meisterbock;它是借助外部框架用合格焊接分总成组装的标准车身,来检查内饰件是否符合匹配要求的工具。
4)、要有正确反映车身下部,即前后轮罩、前后底板、仪表板之间匹配关系的标准车身下部主框架--Fuegen Meisterbock。
它的定位点和夹紧点与生产夹具的定位点完全一致,能实际反映出各总成之间的干涉点和贴合程度,从而确定焊接总成结构尺寸的正确性。
3、匹配过程中对夹具定位、夹紧和工艺的合理性进行验证。
(Inne Meisterbock示意图)1)、基准点系统是否合理、定位点是否与设计基准重合、是满足六点定位原则、定位点尺寸是否正确等;2)、零件的装配顺序是否合理、是否影响尺寸精度;3)、夹具的点定工位点定点是否正确、焊接点定后,到下一工位补焊时,能否保证尺寸稳定;4)、补焊点的顺序对尺寸的稳定性是否有利;5)、夹紧点是否正确,能否保证零件在夹具位置的准确性;6)、夹具顺序是否合理,关键定位点是否首先夹紧;7)、确定能反映零件状态的测量点和功能尺寸;4、单件或总成在匹配过程中的具体步骤1)、首先将满足图纸尺寸的单件按工艺要求顺利放入夹具中,检查零件在夹具上是否贴合,并且无应力。
车身工程设计指南
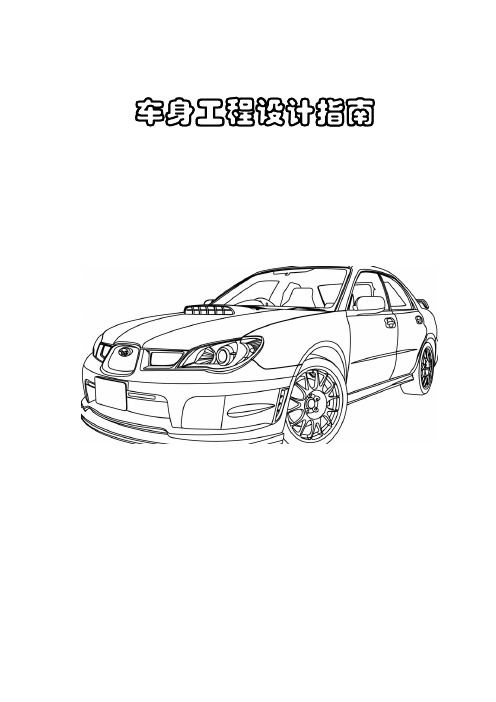
车身工程设计指南前言车身是整车的重要组成部分,开发整车是一项很复杂的工程,车身也一样,它主要包括车身本体、外饰件、内饰及附件,由于它是轿车上载人的容器,因此要求轿车车身应具有良好的舒适性和安全性。
此外,轿车车身又是包容整车的壳体,能够最直观地反映轿车外观形象等特点,所以,轿车车身设计应非常注重外形造型,以足人们对轿车外形地审美要求,取得较好的市场。
而汽车人体工程学、汽车空气动力学、汽车造型及审美艺术、汽车车身新材料的研究及开发、汽车车身结构强度分析、汽车车身设计方法及技术等方面的研究和应用,正是设计出具有良好性能的轿车车身的必要基础。
目录1轿车车身设计要素 (1)1.1车身外形设计方面 (1)1.2车身室内布置设计方面 (1)1.3车身结构设计方面 (1)1.4产品开发方面 (1)2整车开发流程 (1)2.1项目开发流程图(时间) (1)2.2项目开发流程图(节点) (2)3项目开发流程 (3)3.1项目策划阶段 (3)3.2概念设计阶段 (3)3.3技术设计阶段(B认可阶段)及确认 (4)3.4生产准备阶段(D阶段)及确认 (4)4可行性分析阶段 (5)4.1初步可行性分析阶段 (5)4.2详细可行性分析阶段 (5)5车身相关间隙设计规范 (5)5.1车门间隙的标准 (6)5.2车身外间隙设计规范 (8)5.2.1前翼子板和前门处间隙 (8)5.2.2前门和后门处间隙 (8)5.2.3车门下端与门槛处间隙 (9)5.2.4车门的上端与侧围上部配合处 (9)5.2.5后门后端与后翼子板处 (10)5.2.6顶盖与后盖处 (10)5.2.7油箱口盖与侧围的配合 (10)5.2.8后盖与后保险杠处 (11)5.3钣金金过孔的问题 (11)6密封条的截面沿用规范 (12)6.1门洞密封条截面 (12)6.2四门窗框处密封条截面 (13)6.3门上段外侧密封条截面 (13)6.4门上段B柱处密封条截面 (14)6.5门内板上密封条截面 (14)7铰链的结构设计 (14)7.1发动机盖铰链 (15)8门盖系统校核规范 (15)8.1目的 (15)8.2主题内容与适用范围 (15)8.3参考资料 (15)8.4内容 (15)8.4.1门的开启校核 (15)8.5四门需要校核的几个典型截面 (16)9CATIA制图标准/CATIA drawing specification (19)9.1Topic connect/主要内容Tab bar/标题栏 (19)9.1.1总成图纸上各分总成及单件的表示表格清单 (19)9.1.2Tab bar/明细栏 (19)9.2绘图的具体说明 (19)9.2.1设计规范 (19)9.2.2view(视图) (19)9.2.3Layer (层) (19)9.3尺寸标注 (20)9.4字体设置 (22)9.5视图比例选择 (22)10工艺知识 (22)10.1钣金冲压件冲压,焊接,和电镀的工艺性检查 (22)10.1.1弯曲 (22)10.1.2扩孔 (22)10.1.3锥形孔 (22)10.1.4小卷边 (22)10.1.5凹点 (22)10.1.6凸座 (22)10.1.7挤压孔 (22)10.1.8翻边 (22)10.1.9角撑钣 (23)10.1.10压边 (23)10.1.11孔 (23)10.1.12切压缝 (23)10.1.13缺口 (23)10.1.14肋筋(加强筋) (23)10.1.15半冲孔 (24)10.1.16槽(方孔) (24)10.1.17接头 (24)10.1.18焊接 (24)10.1.19电(泳)镀 (24)10.2车身工艺性检查 (24)10.2.1车身工艺性的定义 (24)10.2.2冲压的可加工性 (25)10.2.3冲压的易加工工艺性 (25)10.2.4焊装可加工性 (25)10.2.5焊装易加工工艺性 (25)10.3检查项目 (25)10.3.1与同类车总体比较 (25)10.3.2逐件检查每个零件 (25)10.3.3检查定位点设定合理性 (25)10.3.4检查焊点的合理设定 (26)10.3.5检查测点的合理设定 (26)11汽车车身设计规范 (27)11.1范围 (27)11.2基本原则 (27)11.3冲压工艺要求 (27)11.3.1板件最小弯曲半径 (27)11.3.2正冲孔孔径与最大倾斜角 (28)11.3.3拉深件或弯曲件冲孔的合适位置 (28)11.3.4穿破件的构型原则 (28)11.3.5最小冲孔直径及最小边长 (28)11.3.6最小孔边距和孔间距 (29)11.4冲切件的构型原则 (30)11.5焊接工艺要求 (30)11.6装配工艺要求 (31)11.7涂装工艺要求 (31)11.8轻量化设计要求 (32)11.9结构复杂化,以求最大强度、刚度设计要求 (32)11.10节约成本-对称性设计要求 (32)11.11节约成本-同一件设计要求 (32)11.12密封性要求 (32)11.13美观与缝隙均匀性要求 (33)11.14白车身组成 (33)11.14.1外覆盖件设计 (33)11.14.2内板件结构设计 (33)11.14.3前围设计注意 (34)11.14.4地板焊接总成设计 (34)11.14.5前纵梁的设计 (35)11.14.6地板设计注意事项 (35)12NVH (36)12.1减振沥青毡 (36)12.2孔位EPDM胶堵 (36)12.3焊缝涂胶 (36)12.3.1BIW&Trim公差制定的基本考虑因素 (36)13汽车车身内部布置设计方法 (36)13.1从内到外法 (36)13.2从外到内法 (37)1轿车车身设计要素轿车车身设计要素,亦是从事车身设计工作时,设计人员所必须考虑的方面和重点解决的关键技术,是提高车身设计质量的关键内容。
车身设计重要知识点总结

车身设计重要知识点总结一、设计原则1、空气动力学原理:车身设计中的一个重要方面就是空气动力学,它涉及到车身的气流分析、气动风洞试验以及降低风阻的设计等方面。
这些知识点对于汽车的燃油经济性和性能有着重要的影响。
2、结构设计原则:车身的结构设计是非常重要的,它直接关系到了车身的强度、稳定性和安全性。
因此,在车身设计中需要考虑到各种受力情况,以及选用合适的材料和结构形式。
3、美学原则:车身设计中的美学原则是至关重要的,因为一个好的外形设计可以提高车辆的吸引力和辨识度。
因此,在车身设计中需要注重对比度、曲线美学和比例等方面的设计原则。
4、人机工程学原则:车身设计需要考虑到人机工程学,以保证驾驶员的舒适性和便利性。
这包括对座椅、操纵件和仪表板等方面的设计。
二、设计流程1、概念设计:车身设计的第一步是概念设计,这包括对外形、尺寸和结构等方面的初步设想。
在这一阶段需要考虑到市场需求和设计趋势。
2、方案设计:在概念设计确定后,需要进行方案设计阶段,这包括对车身线条、面板和细节设计的深入研究和反复修改。
3、模型制作:设计师需要根据方案设计来制作车身模型,以便进行视觉和实物检验。
4、评估和修改:制作车身模型后,需要进行评估和修改,以保证车身设计符合产品要求。
5、工程设计:在车身设计确定后,需要进行工程设计,这包括对车身结构和材料等方面的细节设计。
6、工艺设计:最后需要进行工艺设计,以保证车身设计的可生产性和可维护性。
三、材料选择1、钢材:钢材是汽车车身中最主要的材料之一,它的强度和成型性能都比较好,而且成本较低。
2、铝合金:铝合金是轻量化材料的首选,它的密度比钢材小,但强度却很高,而且具有优异的耐腐蚀性和成型性能。
3、碳纤维复合材料:碳纤维复合材料是新型的轻量化材料,它具有密度小、强度高和刚性好的特点,但成本较高。
4、塑料材料:塑料材料适用于车身零部件的生产,它具有成型性好、重量轻和耐腐蚀性强的特点。
四、制造工艺1、冲压成型:冲压是车身成形中常用的工艺,它可以有效地提高产能和成本效益,而且成形精度较高。
车身设计方案

车身设计方案1. 引言车身设计是汽车设计过程中的重要环节之一,它直接关系到汽车的外观美学、空气动力学性能、结构强度等方面。
本文将针对车身设计方案进行分析和探讨,旨在提供一些基本的设计原则和流程,帮助设计师在设计过程中做出科学合理的决策。
2. 设计原则车身设计的核心是要体现品牌风格与车型特点,同时要满足实际需求和市场需求。
以下是一些常用的设计原则,供参考:2.1 流线型设计流线型车身设计可以降低风阻,提高汽车的燃油经济性和行驶稳定性。
通过合理的线条和曲面设计,使车身在空气流动中产生尽可能少的阻力,从而提高整车的性能。
2.2 比例协调车身的比例对于整体美观十分重要。
设计师需要保持车头、车身和车尾的比例协调,使整体呈现出一种动态平衡感。
2.3 简洁与流畅简洁与流畅是现代汽车设计的重要原则之一。
车身线条应尽量简洁、流畅,不过分夸张,使车辆看起来精致又稳重。
2.4 结构强度车身的结构强度直接关系到乘客的安全性。
设计师需要通过优化结构布局和材料选择,以确保车身具有足够的刚度和抗冲击能力。
车身设计的流程包括概念设计、仿真分析和细节设计三个阶段。
下面将对每个阶段进行详细介绍:3.1 概念设计概念设计是车身设计的起点,它基于品牌定位和市场需求,通过手绘草图和数字化建模等方式,形成初步的设计方案。
在这个阶段,设计师需要考虑车身的整体形状、线条和曲面,以及车门、车窗、前后灯等细节部分的设计。
3.2 仿真分析在概念设计确定后,设计师需要进行各种仿真分析,以验证车身设计的可行性和优化方向。
常用的仿真分析包括空气动力学分析、结构强度分析和碰撞模拟等。
通过仿真分析,设计师可以找出设计中的问题并进行针对性的改进。
在完成概念设计和仿真分析后,设计师进入到细节设计阶段。
这个阶段主要涉及到车身各个细节的处理,如车门的开启方式、车窗的设计、车顶的造型等。
设计师需要考虑细节部分与整体的协调性和美感,同时还需要考虑生产制造的可行性和成本控制。
车身匹配总结

车身匹配总结1. 简介车身匹配是一项重要的技术,它的主要作用是根据车辆颜色、车牌号码等信息,将车辆与其所有者或相关的数据库进行匹配。
这项技术广泛应用于交通管理、停车场管理、追踪盗车等领域。
本文将对车身匹配技术进行总结和分析,包括其原理、应用和未来发展趋势。
2. 车身匹配原理车身匹配的核心原理是基于计算机视觉和图像处理技术。
它主要包括以下几个步骤:2.1 图像采集与预处理首先,需要通过摄像头或其他图像采集设备获取车辆的图像。
然后,对图像进行预处理,包括去噪、图像增强等操作,以提高匹配的准确性。
2.2 特征提取在车身匹配中,主要提取的特征有车辆的颜色、车牌号码等。
通过计算车辆图像中的像素值和颜色分布等特征,可以对车辆进行描述和区分。
2.3 数据库匹配通过将提取到的特征与事先建立好的车辆特征数据库进行匹配,可以找到与目标车辆最相似的记录。
匹配算法可以根据实际需求选择,如K近邻算法、支持向量机算法等。
2.4 匹配结果输出最后,根据匹配结果,可以输出匹配的车辆信息,如车主信息、车辆状态等。
3. 车身匹配应用车身匹配技术有广泛的应用场景,下面将介绍其中几个典型的应用。
3.1 交通管理在交通管理中,车身匹配可以用于追踪违法停车、逆向行驶等交通违法行为,并对相应的车辆进行处罚。
通过将车辆图像与交通管理数据库进行匹配,可以快速准确地找到相关车辆和驾驶员。
3.2 停车场管理车身匹配在停车场管理中也有重要作用。
通过车辆图像的匹配,可以实现自动车牌识别和车辆进出记录的管理。
这样可以提高停车场的安全性和管理效率。
3.3 盗车追踪车身匹配可以应用在车辆盗窃案件的调查中。
通过对盗窃车辆的图像进行匹配,可以追踪其行踪和定位,为相关部门提供有力的证据和线索。
4. 车身匹配的挑战与未来发展车身匹配技术在实际应用中仍然面临一些挑战。
首先,车辆图像的质量和角度变化可能会对匹配结果产生影响。
因此,如何提高图像质量和处理角度变化是值得研究的。
汽车车身设计培训教程

汽车车身设计培训教程
车身设计是汽车设计中一个至关重要的方面,它不仅要考
虑到外观的美观与吸引力,还需要关注车身的结构强度、空气动力学性能以及乘客安全等方面。
下面将介绍汽车车身设计的一些基本原则和技巧。
汽车车身设计需要考虑到整体的比例和流线型。
比例是指
车身各个部分之间的尺寸关系,而流线型则是指车身外形的流畅和动感。
好的比例和流线型设计可以赋予汽车一种动感和美感,使其在路上具有更好的视觉冲击力。
车身设计也需要考虑到空气动力学性能。
合理的空气动力
学设计可以降低风阻,提升汽车的稳定性和燃油经济性能。
在车身设计中,一些细节处理,如车身凹槽和空气导流板的设置,可以帮助车辆更好地穿越空气,减少阻力。
车身结构强度也是车身设计中的重要考虑因素。
好的车身
设计应该能够提供足够的刚性和安全性,以保护车内乘客免受碰撞和意外事故的伤害。
合理的材料选择和结构设计可以提高车身的强度和刚性,确保车辆在不同情况下都能保持稳定和安全。
人性化设计也是汽车车身设计的重要内容之一。
车身设计
应该考虑到乘客的需求和舒适性,提供舒适的乘坐空间和方便的操作控制。
例如,合理的座椅设计和车门开关位置的设置都可以提高乘客的舒适度和便利性。
总结而言,汽车车身设计需要考虑到比例和流线型、空气
动力学性能、车身结构强度以及人性化设计等方面。
只有在这些方面都兼顾到位的情况下,才能设计出既美观又实用、安全可靠的汽车车身。
通过系统的培训教程,学习者可以掌握车身设计的基本原则和技巧,提高自己的设计能力。
车身设计重要知识点汇总

车身设计重要知识点汇总车身设计是汽车设计过程中至关重要的一环。
在这篇文章中,我们将讨论一些车身设计的重要知识点。
无论是外观设计还是结构设计,这些知识点都对汽车的性能和安全性起着重要的作用。
第一步:车身设计的目标和原则车身设计的目标是为了在满足外观要求的同时,提供良好的空气动力学特性、优化的车内空间和出色的安全性能。
在设计过程中,应该遵循以下原则:1.空气动力学原理:通过优化车身外形,减少空气阻力,提高燃油效率和稳定性。
2.结构强度和刚度:确保车身足够强度和刚度,以提供良好的碰撞保护和车辆稳定性。
3.材料选择:选择合适的材料来平衡重量、强度和成本的要求。
4.美学和品牌认知:车身设计作为汽车的外观代表,应该与品牌形象保持一致,并迎合消费者的审美需求。
第二步:车身设计的外观要素车身设计的外观是汽车设计中最直观和引人注目的部分。
以下是一些常见的外观要素:1.车身线条:车身线条的选择可以影响汽车的整体形象和动感感觉。
流线型线条可以减少空气阻力,提高燃油效率。
2.前脸设计:前脸是汽车的“面孔”,它不仅要符合品牌形象,还要满足空气动力学和冷却要求。
3.灯光设计:前大灯、尾灯和日间行车灯的设计不仅要满足照明功能,还要提供独特的视觉效果。
4.轮毂设计:轮毂是汽车外观的重要组成部分,合适的轮毂设计可以提升整体形象。
第三步:车身设计的结构要素除了外观设计,车身的结构也是至关重要的。
以下是一些结构要素:1.车身材料:常用的车身材料包括钢铁、铝合金和复合材料。
不同的材料具有不同的强度、重量和成本特性。
2.车身刚度和强度:车身的刚度和强度对于减少噪音、振动和提高安全性能至关重要。
3.安全系统:车身设计应该考虑碰撞保护和乘员安全。
合理布局防撞梁和安全气囊等安全系统。
4.车身连接技术:通过合适的连接技术,如焊接和胶接,确保车身结构的稳定和耐久性。
第四步:车身设计的未来发展趋势随着科技的发展和消费者需求的变化,车身设计也在不断演变。
车身设计指南

车身设计指南前言本文以网络资料为蓝本,主要从车身设计流程,车身设计原则,选料用料,车身设计的结构工艺性,零件命名规则等方面讲述。
目录1概述 (1)1.1车身设计要素 (1)1.1.1车身外形设计方面 (1)1.1.2车身室内布置设计方面 (1)1.1.3车身结构设计方面 (1)1.1.4产品开发方面 (1)1.2车身设计开发流程 (2)1.2.1产品预研 (4)1.2.2BENCHMARKING车分析 (5)1.2.3产品技术描述(Vehicle Technical Specification,简称VTS) (6)1.2.4车身外观匹配间隙和平度及内饰观匹配间隙和平度(DTS) (6)2白车身材料 (9)2.1材料相关参数 (9)2.1.1屈服强度σs (9)2.1.2抗拉强度(σb) (9)2.1.3表面质量分类及代号 (9)2.1.4硬化指数n(n值) (9)2.1.5厚向异性系数r(也叫塑性应变比r,简称r值) (9)2.1.6普通钢与强度钢的分类 (10)2.2普通冷连轧低碳钢系列 (10)2.3加磷高强度冷连轧钢系列 (10)2.4热烘烤硬化钢系列 (11)2.5双相高强度冷连轧钢系列 (11)2.6汽车结构用热轧钢板系列 (12)2.7低合金高强度冷连扎钢系列 (12)2.8冷连轧碳素钢板系列 (13)2.9冷成形用热轧钢板系列 (13)2.10不同钢厂常用牌号对照表 (14)2.11钢板及钢带表面质量区分和表面结构区分 (15)2.12材料选择原则 (15)2.13材料选择数据库 (15)2.14材料选择 (17)2.14.1车身材料用途和特点介绍 (17)2.14.2材料选择一般按下表选择 (20)2.14.3选材列举 (21)2.15白车身各系统材料选用 (24)2.16材料性能 (31)2.16.1冷轧板材料力学及工艺性能 (31)2.16.2加磷钢强度钢材料性能 (32)2.16.3烘烤硬化高强度钢 (32)2.16.4双相高强度钢 (33)2.16.5低合金高强度钢 (33)2.17热轧板材料力学及工艺性能 (33)2.17.1冷成型用热连轧钢板及钢带材料性能 (33)2.18白车身用板料在图样上的标注方法 (34)2.18.1常用黑色金属在图样上的标注方法 (34)2.18.2非金属材料在图样上的标注方法 (36)3车身零部件命名规则 (37)3.1白车身零部件编号原则 (37)3.2车身零部件的箭头系统 (40)3.3车身流水号打刻技术要求 (41)4CATIA V5 制图规范 (42)5车身设计的结构工艺性 (43)5.1冲压成型工艺性 (43)5.1.1分离工序 (43)5.1.2成型工序 (44)5.2冲裁 (46)5.3弯曲 (48)5.3.1变形特点(自由和校正弯曲) (48)5.3.2弯曲件的工艺性 (48)5.3.3弯曲件的回弹 (50)5.3.4弯曲件角度公差 (50)5.4拉深 (50)5.4.1拉深的工艺性 (51)5.5翻边 (54)5.6白车身焊装工艺性 (56)5.6.1白车身焊装工艺方法概述 (56)5.6.2点焊 (56)5.6.3凸焊 (61)5.6.4螺柱焊 (67)5.6.5车身钣金CO2焊 (69)5.7车身涂装工艺性设计 (71)5.7.1车身涂装工艺支点技术要求 (72)5.7.2车身防腐结构设计 (73)5.8车身总装工艺性设计 (76)5.8.1零件的装配性 (76)5.8.2零件的定位策略 (77)5.8.3人机工程 (77)5.8.4零件的放错 (77)6车身结构设计 (78)6.1车身典型断面的定义、定位和作用 (78)6.1.1车身典型截面的定义和作用 (78)6.1.2典型截面编号命名规则 (78)6.1.3微车典型截面定义 (80)6.2发动机罩盖的结构设计 (83)6.2.1发动机罩盖的组成零件 (83)6.2.2发动机罩盖设计所涉及的法规 (83)6.2.3发动机罩盖设计开发流程 (83)6.2.4发动机罩盖的结构设计 (84)1概述车身是整车的重要组成部分,是汽车零部件载体,主要包括车身本体、车身外装饰件、车身内装饰件及车身附件。
车身匹配知识点总结
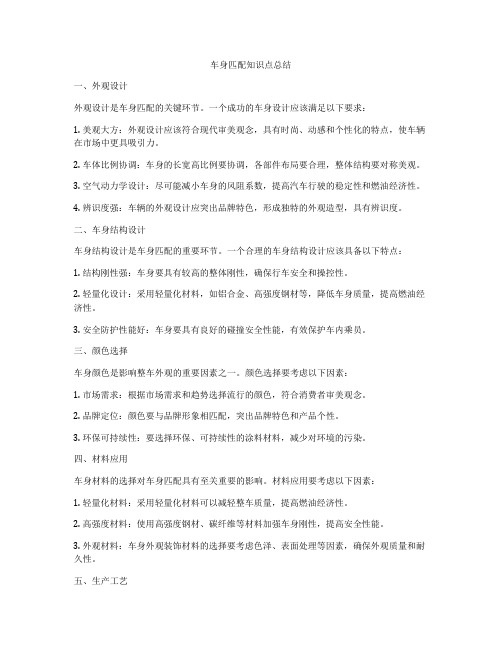
车身匹配知识点总结一、外观设计外观设计是车身匹配的关键环节。
一个成功的车身设计应该满足以下要求:1. 美观大方:外观设计应该符合现代审美观念,具有时尚、动感和个性化的特点,使车辆在市场中更具吸引力。
2. 车体比例协调:车身的长宽高比例要协调,各部件布局要合理,整体结构要对称美观。
3. 空气动力学设计:尽可能减小车身的风阻系数,提高汽车行驶的稳定性和燃油经济性。
4. 辨识度强:车辆的外观设计应突出品牌特色,形成独特的外观造型,具有辨识度。
二、车身结构设计车身结构设计是车身匹配的重要环节。
一个合理的车身结构设计应该具备以下特点:1. 结构刚性强:车身要具有较高的整体刚性,确保行车安全和操控性。
2. 轻量化设计:采用轻量化材料,如铝合金、高强度钢材等,降低车身质量,提高燃油经济性。
3. 安全防护性能好:车身要具有良好的碰撞安全性能,有效保护车内乘员。
三、颜色选择车身颜色是影响整车外观的重要因素之一。
颜色选择要考虑以下因素:1. 市场需求:根据市场需求和趋势选择流行的颜色,符合消费者审美观念。
2. 品牌定位:颜色要与品牌形象相匹配,突出品牌特色和产品个性。
3. 环保可持续性:要选择环保、可持续性的涂料材料,减少对环境的污染。
四、材料应用车身材料的选择对车身匹配具有至关重要的影响。
材料应用要考虑以下因素:1. 轻量化材料:采用轻量化材料可以减轻整车质量,提高燃油经济性。
2. 高强度材料:使用高强度钢材、碳纤维等材料加强车身刚性,提高安全性能。
3. 外观材料:车身外观装饰材料的选择要考虑色泽、表面处理等因素,确保外观质量和耐久性。
五、生产工艺车身匹配还需要考虑到生产工艺。
生产工艺会对车身匹配产生很大的影响:1. 模具设计:模具设计要符合车身零部件的外观要求和尺寸精度要求。
2. 制造工艺:采用现代化的制造工艺,如冲压、焊接、车削等工艺,确保车身的质量和精度。
3. 工艺流程:合理的工艺流程和装配工艺可以提高生产效率,降低生产成本。
车辆功能匹配方案设计规范

车辆功能匹配方案设计规范背景随着智能化、互联网化进程的加速,汽车已经不再仅仅是交通工具,而开始发挥出越来越多的智能化功能。
不仅如此,现代汽车还可以通过API进行物联网互联,实现车辆与其他设备的互动。
这使得汽车成为一个开放平台,使得车辆功能匹配方案成为现代汽车开发的重要组成部分之一。
本文旨在提供一些规范、方案设计和实现方法,以确保汽车厂商和开发者可以基于最佳实践共同开发出安全、稳定且高度兼容的车辆功能匹配方案。
设计规范1.模块化设计车辆功能匹配方案应该被设计成具有模块化结构。
这样可以将功能代码分成许多独立模块,从而实现不同模块的独立开发和测试,并且可以更轻松地添加新的功能或更新现有的功能。
2.低耦合性车辆功能匹配方案应该被设计成低耦合度的。
模块与模块之间应该尽可能地独立,使得更改一个模块不会对其他模块产生影响。
这样,设计和开发过程中就可以更加可控和可预测,减少出现问题和错误发生的可能性。
3.可拓展性车辆功能匹配方案应该被设计成可扩展的。
虽然在最初的设计中并不需要考虑所有的可能的功能,但还是应该将未来的扩展性考虑在内。
这样可以确保在需要添加新的功能时可以避免重构的情况,从而提高开发效率。
4.可配置性车辆功能匹配方案应该被设计成可配置的。
这样,汽车厂商可以通过配置文件为不同的车辆应用程序分配适当的模块和属性,从而提升开发、管理和维护的效率和便捷性。
方案设计为了设计一个功能匹配方案,需要考虑应用程序的目标、用户需求、汽车类型和相应的API和SDK。
1.定义应用程序目标应用程序目标是指应用程序的最终效果和目标。
例如,一个驾驶游戏的目标是提供高质量的游戏体验,而一个车辆控制系统的目标则是提供高质量、安全、高效的驾驶体验。
开发人员应该根据应用程序的目标,确定实现所需的API和SDK,并编写相应的代码以达到最佳效果。
2.了解不同的API和SDK汽车API和SDK提供了一系列功能、事件和动作,使得开发人员可以快速地构建车辆应用程序。
[整理版]白车身匹配技巧
![[整理版]白车身匹配技巧](https://img.taocdn.com/s3/m/d264d4fce109581b6bd97f19227916888486b96b.png)
白车身的匹配技术和过程质量控制要素研究白车身匹配工作就是使组成白车身的各个单件在焊接组合中,使白车身的结构尺寸满足产品设计及质量标准的要求。
白车身结构尺寸的优化是世界各大汽车厂家研究的一个永不完结的课题。
在八十年代德国、美国、日本等著名厂家对白车身精度只控制在±1.5MM之内,九十年代初才达到了±1MM的水平。
而目前高档车已达到±0.5MM的高精度要求。
也就是匹配技术和人才已被各大汽车、轿车集团所重视。
1、在白车身的匹配中,首先要在数以万计的白车身形面上确定数百个尺寸控制点,然后在这数百个点中确定30%左右的功能尺寸控制点,这些功能点做好了,白车身就达到了产品所规定的各项技术要求和标准。
2、白车身的功能点达到要求所具备的条件:1)、冲压单件必须满足图纸要求,通过3辆份和400辆份试装程序来实现;2)、要有检验所有外表面总成件的匹配状态的外部匹配主框架模型--Aussen Meisterbock,它是由根据CAD数据用铝合金型材制造成框架并在其上安装成标准白车身。
它可以装配侧围、车门、前后盖、顶盖、翼子板、后围和前后保险杠、前大灯、后尾灯、水箱面罩等总成件,观察它们之间的匹配情况、配合三座标测量确定零件的更改数据。
(Aussen Meisterbock示意图)3)、要有检查内饰件与白车身匹配关系的内匹配主框架模型--Innen Meisterbock;它是借助外部框架用合格焊接分总成组装的标准车身,来检查内饰件是否符合匹配要求的工具。
4)、要有正确反映车身下部,即前后轮罩、前后底板、仪表板之间匹配关系的标准车身下部主框架--Fuegen Meisterbock。
它的定位点和夹紧点与生产夹具的定位点完全一致,能实际反映出各总成之间的干涉点和贴合程度,从而确定焊接总成结构尺寸的正确性。
3、匹配过程中对夹具定位、夹紧和工艺的合理性进行验证。
(Inne Meisterbock示意图)1)、基准点系统是否合理、定位点是否与设计基准重合、是满足六点定位原则、定位点尺寸是否正确等;2)、零件的装配顺序是否合理、是否影响尺寸精度;3)、夹具的点定工位点定点是否正确、焊接点定后,到下一工位补焊时,能否保证尺寸稳定;4)、补焊点的顺序对尺寸的稳定性是否有利;5)、夹紧点是否正确,能否保证零件在夹具位臵的准确性;6)、夹具顺序是否合理,关键定位点是否首先夹紧;7)、确定能反映零件状态的测量点和功能尺寸;4、单件或总成在匹配过程中的具体步骤1)、首先将满足图纸尺寸的单件按工艺要求顺利放入夹具中,检查零件在夹具上是否贴合,并且无应力。
车身设计方案

车身设计方案一、引言车身设计是汽车工业中至关重要的一环,它直接影响到汽车外观的美观度、空气动力学性能以及乘坐者的舒适感受。
本文将针对车身设计方案进行探讨,通过详细介绍设计原则、材料选择以及外观造型等方面,提出一种全新的车身设计方案。
二、设计原则1.安全性车身设计应该以安全性为首要原则。
采用碰撞吸能结构,优化车辆布局,保护乘车人员免受碰撞伤害。
2.空气动力学性能优秀的空气动力学性能有助于降低风阻和提高燃油效率。
通过使用曲线线条和推进器等设计元素,降低车辆的空气阻力,提高整体性能。
3.轻量化采用轻量化设计原则,选择高强度和高刚性材料,如碳纤维增强复合材料,以提高车身的强度和刚性,减轻整车重量,提升燃油效率。
4.人性化车身设计应考虑乘坐者的舒适感受和使用便利性。
合理的空间布局、舒适的座椅设计、智能化的控制系统等都应纳入考虑范围。
三、材料选择1.碳纤维增强复合材料碳纤维增强复合材料具有极高的强度和刚性,同时具备轻量化和良好的耐腐蚀性能。
在车身设计中,采用碳纤维增强复合材料可以大幅度减轻车身重量,提高整车的燃油效率。
2.铝合金铝合金具有较好的机械性能和耐腐蚀性能,在车身设计中广泛应用。
通过采用铝合金部件,可以达到减轻车身重量、提高汽车整体性能的目的。
3.高强度钢高强度钢具有出色的耐冲击性和刚性,可以在保证车身强度的同时减轻车身重量。
合理地运用高强度钢材料,可以提高车身的安全性能和燃油效率。
四、外观造型1.动感线条车辆的外观造型应注重动感和流线型设计。
通过合理的线条和曲面设计,赋予汽车动感的外观,提升整车的视觉冲击力。
2.独特标识设计独特的车身标识和品牌标识,使车辆在外观上具有辨识度和个性。
3.光影效果考虑光影效果对车辆外观的影响,选择合适的车身颜色和材质,以在不同光线和角度下展现出不同的效果。
五、结论通过对车身设计方案的探讨,我们提出了以安全性、空气动力学性能、轻量化和人性化为原则的设计指导。
在材料选择方面,采用碳纤维增强复合材料、铝合金和高强度钢等材料可以有效提升车身性能。
白车身设计的要点

车门周边内间隙的设计:
中空海绵胶条 中空U形卡条
14
车门周边内间隙的设计: 第六,推算车门周边与侧围密封内间隙尺 寸。根据预设定的压缩比率、以及确定的密封 条基本尺寸进行计算,密封内间隙尺寸为: t = h × (1 - v ) 式中: t —车门周边与侧围密封内间隙 h —密封条被压缩方向原尺寸 v —预设定的压缩比率
6
设计实例应用
2、人机操纵空间尺寸设计
7
设计实例应用
3、车门玻璃升降器轨道设计
8
设计实例应用
4、车门铰链运动机构设计
9
车门周边内间隙的设计: 下面作一实例探讨: 在设计车门周边内间隙时,要从多方面 去考虑,特别是密封条工作空间,由于它处 于动态之中,设计上需要严格匹配。当对密 封胶条的性能要求考虑不周时,就会出现密 封间隙不均,车门二道锁无法锁上、外表面 衔接处面差大等缺陷。 如何更合理地设计车门内间隙?推荐设 计步骤如下:
10
车门周边内间隙的设计: 在多数车门密封间隙设计 中,基本上采用的是双道中空 式密封结构。设计时从如下方 面考虑: 首先,设置密封条压缩顺 序:为减少车门关闭时的密封 条反弹阻力,将重要密封处设 置为第一压缩部位,辅助密封 处设置为第二压缩部位。
11
车门周边内间隙的设计: 第二,设计密封条结构形 式。以扣钉式中空海绵条与 复合式中空U形卡条为例。 第三,确定密封条安装部 位与压紧接触面,分析压紧 力方向。 由于压紧力方向受铰链的 运动约束影响,各部位有所 不同,有侧向推压的、有接 近正向挤压的。规范与原理? 如果存在的话,是否会像发动机、变速 器的设计原理一样具有某种规律性? 对于这些问题需要采用综合性的技术来 全面解决,以达到尽可能地减少产品设计缺 陷的目的。 不难看出,在一些实例中有些已具备规 范与原理设计特点的,例如:
车身精度综合匹配和样板拼车的建立

证零 件 满 足 匹 配 目标 。样 板拼 车 主 要 依 照 MB检 测报 告 , 通过 反 复小 批量 拼 车 , 暴 露检 具 上难 以发 现 的零 件 问 题 , 分 析 零 部 件 产 生 缺 陷 的根 本 原
因。样 板车 间 主要对 生 产启 动 阶段 生产 的整 车 尺 寸 匹 配负 责 , 对 车辆 装 配 现 场 问题 进 行 分 析 且 对
量及 效率 , 对各 项 质 量 控制 活 动 和资 源 进行 合 理 安排和分配 , 以实 现 早 期 质 量 风 险 遏 制 , 缩 短 产
品开 发 周 期 , 提高过程控制能力 , 确 保 车 身 的制 造 精 度 和 质量 稳 定 性 。 生 产 启 动 阶 段 , 车 身 MB 工作 主要 分 为 4 个阶段 : 预 匹配 认 可 ( M B 1 ) 、 匹配 认可 ( MB 2 ) 、 零 件 提交 保 证 书 ( O T S ) 和 试 拼 试 装
对 零 件 已经 存 在 或者 可 能 的缺 陷进行 评 价 , 必 要
2 0 1 4 年第 4 期
汽车" 1 - 艺与材料 A T & M l 2 1
生
P 砸
按
零 部 件 主模 型 匹 配 的条 件 首 先是 符 合 检 具 ,
时可 借 助综 合 匹 配样 架 、 测 量 支 架 和焊 接工 装 等
文 献 标 识码 : B
■ 奇瑞商用车( 安徽) 有限公 司
戴 竞
MB和 D T都是 指 导零 部 件 匹配 质 量提 升 的重
要手 段 。综 合 匹 配 主要 依 靠 主模 型 匹配 、 匹 配样 架 和检 具 评 价 单个 零 件 的尺 寸合 格 率 , 侧 重 于保
车身与轮毂匹配优化设计研究
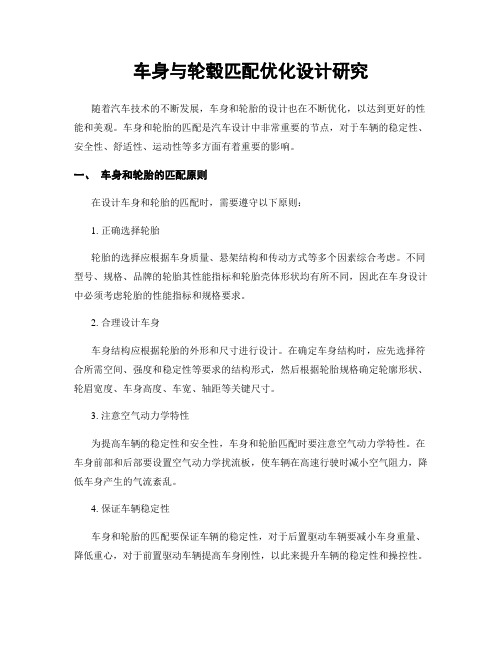
车身与轮毂匹配优化设计研究随着汽车技术的不断发展,车身和轮胎的设计也在不断优化,以达到更好的性能和美观。
车身和轮胎的匹配是汽车设计中非常重要的节点,对于车辆的稳定性、安全性、舒适性、运动性等多方面有着重要的影响。
一、车身和轮胎的匹配原则在设计车身和轮胎的匹配时,需要遵守以下原则:1. 正确选择轮胎轮胎的选择应根据车身质量、悬架结构和传动方式等多个因素综合考虑。
不同型号、规格、品牌的轮胎其性能指标和轮胎壳体形状均有所不同,因此在车身设计中必须考虑轮胎的性能指标和规格要求。
2. 合理设计车身车身结构应根据轮胎的外形和尺寸进行设计。
在确定车身结构时,应先选择符合所需空间、强度和稳定性等要求的结构形式,然后根据轮胎规格确定轮廓形状、轮眉宽度、车身高度、车宽、轴距等关键尺寸。
3. 注意空气动力学特性为提高车辆的稳定性和安全性,车身和轮胎匹配时要注意空气动力学特性。
在车身前部和后部要设置空气动力学扰流板,使车辆在高速行驶时减小空气阻力,降低车身产生的气流紊乱。
4. 保证车辆稳定性车身和轮胎的匹配要保证车辆的稳定性,对于后置驱动车辆要减小车身重量、降低重心,对于前置驱动车辆提高车身刚性,以此来提升车辆的稳定性和操控性。
二、轮胎和车身匹配的重要性1. 提升车辆性能车身和轮胎匹配的适当性能可以有效提升车辆性能,如减轻车身重量、降低重心、提升刚性、降低车身空气阻力等,可有效地减小车辆阻力系数、提高车辆行驶速度和降低能耗,从而提升车辆的性能。
2. 保证行驶安全合理的车身和轮胎匹配可以有效的保障车辆的安全,合适的轮胎品牌、型号、规格等有着重要的安全保护作用,如在湿滑路面上有着良好的抓地力、在高速行驶时减小空气阻力等,从而能够提升车辆的行驶安全性。
3. 提高驾驶舒适度车身和轮胎的匹配对车辆的驾驶舒适性也有着重要的影响,如在路面硬度和状况恶劣的情况下,车辆走过去会造成车轮跳动,从而影响驾驶员的视野和驾驶舒适度,因此在匹配车身和轮胎时,需要考虑到驾驶员的舒适性。
b2.4第四章及整车的匹配设计

第四章与整车的匹配设计为了使一个性能好的动力转向器能在汽车上正常发挥作用,还必须使该动力转向器在汽车上匹配设计的好。
包括在汽车上的布置要合理,相关联的转向盘、转向传动装置、转向器支架、转向摇臂、直拉杆设计的合理,动力转向器本身选型合理以及配套的转向油泵和转向油罐选型及匹配的合理。
这些因素都将对动力转向器能否在汽车上正常发挥作用产生影响。
下边将分别讨论:1.布置方式分类在汽车上布置整体式动力转向器必须按我国公路法规规定,转向器必须布置在汽车前进方向的左侧,一般称为左置转向器。
按转向器相对车架的位置分为立置、斜置和卧置(见图 4.1 )。
按转向器相对支架的位置分为输出轴朝内和输出轴朝外两种。
2.整体式动力转向器布置的要求(1)要把转向盘一转向传动装置一整体式动力转向器一转向杆系一车轮作为一个系统来考虑。
选择最优方案进行具体设计。
(2)尽量保证转向盘的大小,布置角度适合不同车型人体工程学的要求。
( 3 )尽量保证转向传动轴的布置能使转向盘与转向器转向轴等速,并保证作到布置在前翻驾驶室上的在翻转动作中不出现运动干涉。
(4)最大程度地发挥动力转向器的输出扭矩、输出援角。
图 4.1 整体式动力转向器布置方式a)立置;b)斜置;。
)卧置(5)保证杆系的运动合理,即直拉杆的运动不与轮胎产生于涉。
横拉杆布置符合转向几何学规定,前轮在行驶中上下跳动不能引发出现前轮摆头现象。
(6)保证前轮左右转向角度达到设计要求,保证整车转弯半径达到设计要求。
3.整体式动力转向器布置要点( 1 )转向盘的角度车型不同转向盘的角度不同,它的确定取决于人体工程学的考虑,目的是让驾驶员以最佳角度舒适的操纵转向盘。
轿车转向盘上平面相对于垂线的夹角应为25°~45°。
长头汽车转向盘上平面相对于垂线的夹角应为35°~55°。
平头汽车转向盘上平面相对于垂线的夹角应为50°~70°。
转向盘上平面的角度是总布置设计最终作图确定的。
- 1、下载文档前请自行甄别文档内容的完整性,平台不提供额外的编辑、内容补充、找答案等附加服务。
- 2、"仅部分预览"的文档,不可在线预览部分如存在完整性等问题,可反馈申请退款(可完整预览的文档不适用该条件!)。
- 3、如文档侵犯您的权益,请联系客服反馈,我们会尽快为您处理(人工客服工作时间:9:00-18:30)。
分类 关联零部件 转向管柱罩盖 手套箱总成
A柱下装饰板
仪表台骨架
功能
故障模式
开启不良 配合间隙不良
座舱系统物理匹配设计要点
匹配设计要点
DMU检查项目 添加日期
设计仪表板和转向管柱罩盖的最小间隙为4.7mm
√
仪表板安装零件、加强件、线束、继电器到手 套箱斗的间隙为12毫米 手套箱斗和仪表板开口之间的最小间隙为6毫米
配合间隙不良 配合间隙不良 配合间隙不良 配合间隙不良 配合间隙不良
配合间隙不良
A108案例 A108案例
仪表板表皮到驾驶员侧下面板的最小间隙为3毫 米 仪表板与A柱没有连接关系时,表皮到A柱饰板 的最小间隙为2毫米 仪表板到挡风玻璃的最小间隙为6mm
仪表板的加强件、零件模块、继电器等到仪表 板骨架的最小间隙为6mm. 仪表板加强件到COWL SIDE TRIM、 COWLCARPETING、cowl side 上的安装模块的 最小间隙为19毫米 仪表板到门内板的最小间隙为6+/-4,平行度公 差不超过2毫米 仪表板安装零件到其他仪表板安装零件的间隙 12毫米 前风档玻璃黑边,前下视野
散热
装配/维修
中控 台
信号干扰
√
DVD或CD主机面板和仪表台面板间隙0.3-
1.0mm,
√
√ 音响主机安装结构应能承受3Kg重量
DVD 与其它安装零件的间隙至少保证大于4
毫米
√
后部有足够的空间接插线束插件(>40mm)
√
导航传感器与周边零件最小间距为15mm
√ DVD反光校核,同比参考样车
转向盘调节角度
断面图 断面图
中控 台
通过性 开关卡滞 通过性 开关卡滞 电气开关 可装配性 外观/功能 C926案例
门感应开 感应门开 关 状态
引擎盖开 感应引擎 关 盖开启
空调出风 口 空调控制 器
加速踏板
A108案例 A108案例
制动踏板 离合踏板
C926案例
副仪表台 本体
副仪 表台
点烟器 烟灰缸 电气开关 驻车手柄
Y=过左H点截面
主仪 表台
PAB
PAB集气盒靠近副驾驶的面与原车坐标的xc-yc 平面的角度允许的角度范围是27°~85° 仪表台采用整体式时注意:与气囊模块配合部 位强度要足够,开口的最小尺寸为250*120,气 囊模块连接在仪表台上时仪表台和模块要有足 够的连接空间。开口采用U形翻转,翻转的时候 桃木装饰条不要对饰盖造成阻碍 组合仪表视野满足法规,同比参考样车
可见的位置,并和XZ平面成180度。SDS Detail
4-CC0004A
车内感应器应布置在不受冷热源影响和阳光无
2、
法照射到的部位
HA
车内感应器应布置通常布置在
范
VC
围内,并提供有效的通风面积387mm2。比正常
值小64mm2也是允许的
出风口的布置和吹风方向的规定参见SDS
Detail25015&25016
√
√
√
Y=0截面图
√
√
√
2008/3/4 2008/4/8 2008/4/8
Y=0截面图
√
过加速踏板中心法 面截面图
√
√
设计除雾器格栅最小低于仪表板表面或A柱饰板 表面2mm 仪表板前窗除雾器到挡风玻璃的最小间隙6mm
应保证空调进风的空气通道,保证在垂直其开
口100内不布置零件
阳光感应器应布置从与地平线成15度角的方向
外观 组合仪表 维修
R-Ⅱ案例
组合仪表饰框到组合仪表镜面的间隙3毫米,可 以在组合仪表饰框上设计突起间隔柱。 安装及拆卸方便、接插件插拔空间校核
视野
仪表周边间隙应通过装饰框等适当遮掩
外观
配合间隙不良
组合仪表饰框到组合仪表镜面的间隙3毫米,可 以在组合仪表饰框上设计突起间隔柱。
√
驾驶员侧
安装及拆卸方便、接插件插拔空间校核
开关
前档风玻璃除霜校核
空调出风 口
BMPV案例
侧除霜口角度、效果及安装方式
1、
出风面积
仪表
仪表板安装零件、加强件、线束、继电器到收
台
音机磁带立屏和周边部件不能挤压,最小间隙
信息显示
2mm,,屏幕面板和仪表台面板间隙0.3-1.0mm
√
外观 音响系统
承重
C926案例
变速操纵
C926案例
复位或锁止开关与周边间隙应大于0.5mm 翘板式开关,运动端间隙应大于1.0mm
后部有足够的空间接插线束插件。 开关行程一般3mm,所以开关盖一般高于周围面 板3-5mm 车门关闭状态时应具备5--6mm的干涉量,作为压 缩行程 引擎盖关闭状态时应具备约3mm的干涉量,作为 压缩工作行程,具体参数视开关行程而定 风口面积校核
组合仪表罩与方向盘中心线Y向值偏差<15mm
转向管柱在中间位置时组合仪表罩不遮挡视野
PAB的集气盒以H面(与原车坐标xc-zc平面平 行,距离为副驾驶H点坐标Y)左右对称,偏差 不超过20mm
√ √
√ 2008/4/15
资料输入
Y=过左、右H点截 面 过离合踏板中心法 面截面图 过放脚中心法面断 面图
手套箱锁安装及运动校核
腿部X向空间同比标杆车 √
腿部Y向空间同比标杆车
C926,A108,SRV案例 离合踏板左侧放脚方便性
配合间隙不良 偏孔
C926案例
仪表板骨架到A柱板金的最小间隙为6mm
√
仪表板骨架到DASH INSULATOR 的最小间隙为
6mm
√
安装方向管柱结构的刚性
主仪表台 本体
主仪 表台
加速踏板中心点与侧护板间隙>40mm 安装方式 安装方式 安装方式 手刹把手与周边的间隙 Z , X向36mm, Y向6mm
副仪表板手刹杆部与周边最小间隙为5.0毫米。
Shift ring 与上面板间隙为0,且有四周间隙 大于3mm.
自动档手球周边间隙50mm, 手动档45mm.
空调机模块到仪表板安装零件的间隙为12毫米 HVAC与隔热垫的距离>5mm 风道布置