镁合金压铸件成品设计要点39页PPT
压铸件产品设计注意规范 PPT

二、铸造圆角与脱模斜度
1)铸造圆角 压铸件各部分相交应有圆角(分型面处除
外),使金属填充时流动平稳,气体容易排出, 并可避免因锐角而产生裂纹。对于需要进 行电镀与涂饰得压铸件,圆角可以均匀镀 层,防止尖角处涂料堆积。 压铸件得圆角半径R一般不宜小于1mm,最 小圆角半径为0、5 mm,见表2。铸造圆角 半径得计算见表3。
配合面得最小脱模 非配合面得最小脱
斜度
模斜度
α
外表面α 内表面β 外表面α 内表面β
锌合金
0°10′ 0°15′ 0°15′ 0°45′
β
铝、镁合金 0°15′ 0°30′ 0°30′
1°
铜合金
0°30′ 0°45′
1°
1°30′
说明:①、由此斜度而引起得铸件尺寸偏差,不计入尺寸公差值内。 ②、表中数值仅适用型腔深度或型芯高度≤50mm,表面粗糙度在Ra0、1,大端 与小端尺寸得单面差得最小值为0、03mm。当深度或高度>50mm,或表面 粗糙 度超过Ra0、1时,则脱模斜度可适当增加。
2
0
8
7
3
M6
5、 58~ 5、70
5、 38~ 5、50
≥10
M8
7、45 ~ 7、
60
7、15 ~ 7、
30
≥13、 3
旋入深度t
t≥1、5d
我司现较为常用得自攻螺钉规格为M4与M5, 其采用得底孔直径如下表:
d2
d3
t
M4
3、84
0 -0、1
3、59 +0、1 0
10
M5
4、84
0 -0、1
表5 最小孔径与最大孔深
孔 合金 径
类别
镁合金压铸件模具设计要点

浇、流道系统设计(6/10)
浇口设计
浇口面积计算公式
Ag V Vg t
V:压铸件体积(含溢流井体积)(cm3)
Vg:浇口速度 (m/s)
t:充填时间 (s)
Ag:浇口面积(mm2)
举例说明:铸件(含溢流井)重400g,平均壁厚1.4mm, V=400/1.8=222.22 cm3 (镁铸件比重为1.8) 假设Vg=55m/s, t=0.03 则Ag=222.22/(55*0.03)=134.68 mm2 , 另浇口厚度不得超出铸件厚度的一半,因而在此定为
精级拔模角 D 0.8( L / C) , (D/ L) / 0.01746度
一般级拔模角所需C值
精级拔模角所需C值
内表面(单边)=7
内表面(单边)=7.8
外表面(单边)=14
外表面(单边)=15.6
孔(全部)=4.76
孔(全部)=5.3
压铸方案设计程序 (1/2)
选择压铸机 决定压铸条件
4
4
5
6
6
镁压铸品模销孔径大于25mm时,直径与深度比 为1:6
镁压铸品模销孔直径 (mm)
3
4
5
7
10 13 16 20 25
镁压铸品模销孔标准深度
单位:倍
1
1 1.5 2
2
2
2.5 2.5
3
镁压铸品尺寸公差 (6/9)
平面之角度公差(ADCI-E11-65)
平面和基准面在同一模穴或同一侧滑模之一部份 面长75mm以下…………………………..0.13mm 超过75mm每25mm追加公差……………0.025mm
压铸件结构设计 ppt课件
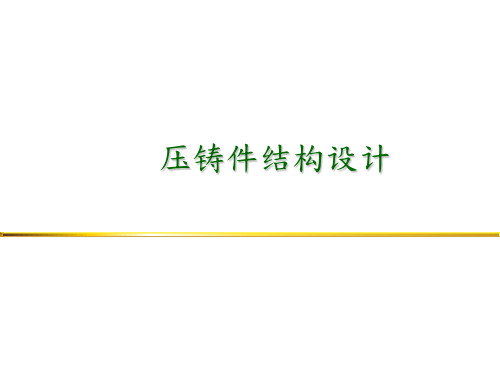
好的案例
说明
深入模穴尽量位置于 制品之同一方向。
型模固定侧之心型形 状﹐应避免因收缩而
固着。
压铸件结构设计
不好的案例
好的案例
说明
切面肉厚较厚处所﹐ 增强肋之厚度应与肉 厚均一。
肉厚需有均一之厚度 。
压铸件结构设计
不好的案例
好的案例
说明
为使深入之增强肋脱 模容易﹐尽量使用最 大之退缩倾斜﹒
阶级部角隅应尽量放 大R来连接。
压铸件结构设计
不好的案例
好的案例
说明
T形切面之接合面将 产生凹陷﹐在心型侧 边缘设置锲入改善之 。
由于型模构造更改﹐ 避免"A"部肉厚过薄 。
压铸件结构设计
压铸件结构设计
压铸件结构设计
同一产品内壁厚应尽量保持一致,且应 平滑过渡,不然容易产生卷气影响产品 强度,壁厚突然过度还会导致厚的地 方产生收缩,粘模,影响外观。
压铸件结构设计
铜合金
D
铝合金
L
锌合金 镁合金
脱模斜度查询表
压铸件结构设计
压铸件结构设计
压铸件结构设计
压铸件结构设计
压铸件结构设计
一般来说,除外模具分型面处外,产品上两壁相连处不管是钝角还是锐角 ,都需要做倒圆角处理。适当圆角不但有利于产品的成型,防止产品 开裂,还能有效的延长模具的寿命。当铸件的内角必须为清角时,应按 以下图片所示做产品结构。
压铸件结构设计
压铸件结构设计
压铸件结构设计
压铸件结构设计
压铸件结构设计
压铸件结构设计
内容大纲
产品的壁厚(模具成型的基础) 产品的拔模(模具脱模的保障) 产品的圆角(模具寿命的关键) 加强筋的设计(结构优化的手段)
镁合金压铸产品设计要点

镁合金压铸产品设计要求1、尺寸公差要求
4、散热齿高度、厚度及拔模斜度等要求
此项指标与铝合金相比,同等尺寸下,高度可以稍高一点、厚度薄一些、拔模斜度稍小一点可行,若按原铝合金设计生产镁没有问题。
5、凸台/凹槽要求
这些没有特殊要求,主要根据产品结构而定,按铝合金设计可以再优化一点。
6、后面机加需留的余量
加工余量根据产品结构和精度要求而定,一般留0.5mm左右即可。
7、其他与铝合金压铸产品不同,设计上需要注意的地方
从制造工艺上来讲,铝合金生产时需用水来冷却,镁合金需加热,贵司产品结构设计考虑功能要求,有点问题我们可以从工艺上进行改良。
镁合金压铸件成品设计要点
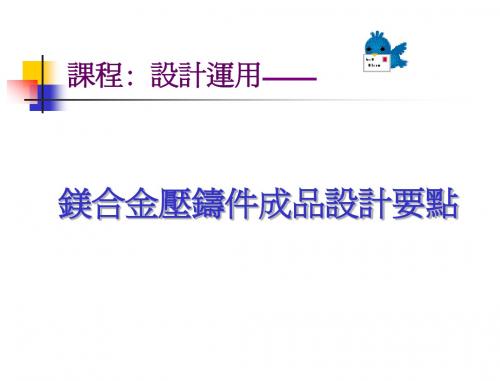
C尺寸 0.55 0.6 0.65
E
D尺寸 0.51~0.66 0.66~0.81 0.77~0.92
E尺寸(C+D) 尺寸(C+D) 1.06~1.21 1.26~1.41 1.42~1.57
六.幾個參數(Mg經驗值)
2.鑽孔後,再用銑刀加工,最後才攻牙
絲攻
A:螺紋倒角(C0.3)
B A
B:有效牙深 C:絲攻的無效牙長度
± 0.25
± 0.025
± 0.025
三.位於分模面上的尺寸公差
分模面上的直角方向因漲模 因素,公母模分開成形的尺 寸,較易變化,其與制品投 影面積成正比關系。
型分割面
壓鑄的投影面積 320CM2以下 320~650CM2 650~1300CM
2
鋅合金
A
鋁合金
鎂合金
銅合金
± 0.1 ± 0.15 ± 0.2 ± 0.3
以切削加工來通孔
一.關於鎂合金壓鑄件成品設計建議
溢流井 溢流井
滑塊 滑塊
L
滑塊
L
L
陰影區域 未充填
湯口
陰影區域 未充填
湯口
附圖( 附圖(二)
一.關於鎂合金壓鑄件成品設計建議
部位 小pin 外圓角 內圓角 原因
小Pin易折斷。 1.外圓角不足易踫傷. 2.模具易龜裂. 參考附圖(四) 內圓角不足易發生制品龜 裂,及應力集中。 參考附圖(四)。
± 0.05mm
2~3um 0.03~0.1mm 一次完成品 50~70um 二次上塗(重工一次) 70~80um 三次上塗(重工二次) 80~100um 一次完成品 60~80um 二次上塗(重工一次) 80~100um 三次上塗(重工二次) 100~120um 厚0.4~0.6mm(視Rib高度5~10mm) 5‰~5.5‰
镁合金压铸模具规划PPT教学课件

頂 出 排 氣 溢 料 井
模 溫 油 路 配 置
導 銷 模 座 大 小
模座及配件 市購品發包
客戶 出圖
A
會同客戶、業務人員 壓鑄人員、模具設計 治具設計方案討論
成品圖 3D構圖
倒勾尺寸 脫模角檢查
模仁圖 O.K 模具圖 3D拆圖 2D繪圖
圖面 OK
檢討
.
N.G
N.G
模仁素材 水孔攻牙
模仁CAM 程式製作
生產
操作規範 檢驗規範
模具移交記錄表
製程中檢、出貨檢查表 自主檢查表
2
XXXX 股 份 有 限 公 司
鎂合金壓鑄模具作業流程
入 料 方 式 位 置
模加 分滑合 穴工 模塊金 數位 毛倒公 目置 邊勾差 排方 位處縮 列式 置理水
肉月外 厚產觀 脫量形 模總狀 角產品 度量質
心 型 大 小 位 置
澆 口 流 道 料 管
試模 FAI
會議記錄
成品圖 模具設計流程圖
模具製作組立圖 (檢、治具)驗收
成品圖
協力廠提供製作規範
樣品製作進度表 托外加工單 樣品驗收單
模具設計進度表 模具設計圖面 模具結構圖 模具材料規範書 模具製作進度表 模具保養卡
模具托外製作合約書 模具驗收報告
試模報告 機台條件設定表
FAI 表
模具移交 品質規劃
電極CAM 程式製作
模仁CNC 銑床粗加工
淬火 熱處理
N.G
N.G
模仁CNC 銑床細加工
O.K 放電 檢驗 線割
加工
檢驗
O.K 整模 組模
試模
O.K
O.K
刻字
回火氮化 熱處理
量產Biblioteka 2020/12/10N.G
镁合金压铸成型

环保与可持续发展
环保材料的应用
为了满足日益严格的环保要求,镁合金作为一种可再生资源,其 应用越来越广泛,有助于减少对有限金属资源的依赖。
节能减排技术
在镁合金压铸成型过程中,通过采用先进的节能技术和减排措施, 降低能耗和减少环境污染。
循环经济与资源回收
发展循环经济,推动镁合金废料的回收和再利用,实现可持续发展。
THANK YOU
感谢聆听
06
实际应用案例分析
汽车制造业中的应用
镁合金压铸成型在汽车制造业 中广泛应用于发动机、变速器 等零部件的制造。
由于镁合金具有轻量化、高强 度、高刚性等特点,使用镁合 金压铸成型能够显著降低汽车 重量,提高燃油经济性和动力 性能。
镁合金压铸成型还具有生产效 率高、成本低等优势,因此在 汽车制造业中具有广阔的应用 前景。
随着科技的不断进步,镁合金压铸成型技术也在不断创新,如研究 开发出高能效、高精度的压铸设备,提高生产效率和产品质量。
模具设计与制造技术
模具是压铸成型的关键,通过优化模具设计和制造技术,可以提升 镁合金压铸件的精度和表面质量,满足更高端产品的需求。
自动化与智能化生产
随着工业4.0的推进,镁合金压铸成型将逐步实现自动化和智能化生 产,提高生产效率和降低人工成本。
电子产品外壳制造中的应用
02
01
03
随着电子产品向轻薄化、小型化方向发展,镁合金压 铸成型在电子产品外壳制造中越来越受到青睐。
镁合金具有良好的电磁屏蔽性能和散热性能,能够满 足电子产品对外观、性能和轻量化的要求。
通过镁合金压铸成型,可以快速、高效地生产出高品 质的电子产品外壳,提高产品市场竞争力。
镁合金压铸成型
目
《镁合金压铸成型》课件
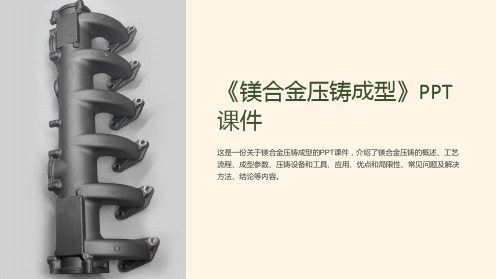
其他工具
用于辅助镁合金压铸的工具,如喷嘴、模具喷 涂剂、测温仪等。
镁合金压铸的应用
汽车工业
用于制造汽车零部件,如发动机壳体、底盘 构件等。
计算机工业
制造计算机外壳、键盘框架等。
轻型工业
在航空航天、电子设备等领域广泛应用。
其他行业
镁合金压铸可应用于各种行业,如医疗设备、 家电、体育器材等。
镁合金压铸的优点和局限性
设备操作问题
对操作人员进行培训,加 强设备维护和安全措施, 减少操作问题。
结论
1 镁合金压铸成型的前景
随着科学技术的不断进步,镁合金压铸将成为制造业的重要方向。
2 发展趋势
镁合金压铸将更加注重绿色环保、节能减排、提高自动化程度等方面的发展。
参考文献
1. 李明. 镁合金压铸工艺[D]. 东南大学, 2018. 2. 陈宇飞, 等. 镁合金压铸技术应用[J]. 机械制造与自动化, 2019, 48(10): 55-58.
《镁合金压铸成型》PPT 课件
这是一份关于镁合金压铸成型的PPT课件,介绍了镁合金压铸的概述、工艺 流程、成型参数、压铸设备和工具、应用、优点和局限性、常见问题及解决 方法、结论等内容。
镁合金压铸概述
1 轻量化材料
镁合金是一种相对较轻 的材料,具有良好的机 械性能和强度,被广泛 应用于各个行业。
2 高精度成型
冷却
4
充模具的空腔,形成零件的形状。
冷却注铸后的镁合金零件,使其固
化成型,具备所需的强度和刚性。
5
脱模
将固化的镁合金零件从模具中取出,
后处理
6
准备进行后续处理。
对镁合金零件进行去毛刺、修整、 抛光等工艺,以获化的镁合金的温度, 确保它在注铸过程中具有适 当的流动性。
镁合金压铸成型设计要点

鎂合金壓鑄成型設計要點報告大綱l壓鑄機之選擇l熱室壓鑄機構造l鎂合金壓鑄件成品設計要點l壓鑄方案設計程序l壓鑄條件之決定(充填時間及澆口速度) l澆、流道系統設計l模具分割面設定要因l鎂壓鑄品尺寸公差壓鑄機之選擇(1/2) l選擇壓鑄機A: 成品投影面積(cm2)1.3A: 成品投影面積+流道&溢流井等鑄件投影面積(cm2) P: 鑄造壓力(Kg/cm2)熱室機鎂合金壓鑄壓力約為200~350 Kg/cm2鎖模力(噸) T=1.3AP/1000壓鑄機之選擇(2/2) l熱室壓鑄機之模具安裝關係規範u拉桿直徑(mm)u拉桿間隔(mm)u模具行程(mm)u模具高度(最大~最小) (mm)鎖模力u最大射出力(噸)u柱塞行程(mm)u柱塞直徑(Φmm)u可鑄重量(g)u鑄造壓力(Kg/cm2)u射出噴嘴位置(mm)u押出力(噸)u押出行程(mm)u噴嘴最大凸出量(Φmm)熱室壓鑄機構造l 壁厚須力求平均l 孔徑與深度關係鎂合金壓鑄件成品設計要點(1/4)最小孔徑d (mm)深度為孔徑d 的倍數經濟上合理孔徑技術上可能孔徑不通孔孔徑通孔孔徑l 肋與壁厚關係ðD ≦4~5t 在此比例下應不會產生縮水痕,但非必要還是以力求壁厚平均為佳。
2 1.5d> 5 d <5d> 5 d <55d 4d 10d 8d鎂合金壓鑄件成品設計要點(2/4)l圓角ð當T1=T2時;若R2=R1+T1則R1=T1 ,若R2=0則R1=1~1.25 T1鎂合金壓鑄件成品設計要點(3/4) l圓角ð當T1=最小壁厚時§當T型相交時,則R1=1~1.25 T1§當T2 > T1時,則R1=2/3( T1+T2) & R2=0~(R1+T2)§當十字或Y型相接時l當Θ=90°時,則R1= T1l當Θ=45°時,則R1= 0.7 T1 & R2= 1.5 T1l當Θ=30°時,則R1= 0.5 T1 & R2= 2.5 T1鎂合金壓鑄件成品設計要點(4/4))l拔模角(依ADAC建議壓鑄方案設計程序(1/2)l選擇壓鑄機l決定壓鑄條件ð決定充填時間ð澆口ð決定澆口速度ð模具分割面ð鑄口ð流道ð湯井ð排氣溝ð冷卻水孔ð押出銷Remark:鎂合金縮水率約為5~7/1000壓鑄方案設計程序(2/2)壓鑄條件之決定(1/2)l決定充填時間ð鑄件平均壁厚薄者宜短ð鑄件厚度不均形狀複雜者宜長ð鑄件表面光滑度好者宜短ð鑄件模具溫度低者宜短ð鑄件重量重者宜長(反之,輕者宜短) Remark:鎂合金壓鑄充填時間依平均厚度(mm)參考值如下表厚度(mm)充填時間(Second)2.00.0363.00.0553.50.07壓鑄條件之決定(2/2) l決定澆口速度ð鑄件平均壁厚薄者宜快ð鑄件厚度不均形狀複雜者宜快ð鑄件表面光滑度好者宜快ð鑄件充填長度長者宜快Remark:鎂合金壓鑄澆口速度40~75 m/s (參考值)澆、流道系統設計(1/10)l一般通則ð澆口應在充填困難地方優先設置ð各澆口大小應依其主要充填區、鑄件體積比例分配設置ð各澆口設置應在最小阻抗位置ð分流道與主流道必須維持平衡及漸縮ð流道轉彎處應設凸出部以吸收雜質(如鑄液之前端固化物)ð流道轉彎及截面積避免突然改變(因尖角易造成亂流及捲入空氣)ð流道轉彎時,截面積應適度減小才不會捲入空氣ð流道轉彎截面積漸縮一般原則如下圖:澆、流道系統設計(2/10)澆、流道系統設計(3/10) l充填模式ð橫越式充填模式(常用於平板充填)ð漩渦式充填模式(常用於中間有孔鑄件充填) l決定充填模式的原則ð各個充填區域儘量能同時充填完畢ð非直接充填區域越小越好ð金屬流動路徑越短越好l 扇形澆口系統設計ð扇形澆口系統適用於澆口長度受限的鑄件ð扇形澆口其特性中央速度高,兩端速度較小ð扇形澆口兩端夾角應小於90°,如開的太大兩側並無熔澆、流道系統設計(4/10)湯射出ð扇形澆口其特性就是由較窄的流道轉變到較寬的澆口ð扇形澆口截面積由進口到出口其截面的寬與深建議比例如下:§流道面積:澆口面積= 1.5: 1§流道厚度:澆口厚度= 3: 1§扇形長度:澆口寬度= 1.34: 1澆、流道系統設計(5/10)l錐形流道系統設計ð錐形流道適用於澆口長度較長的鑄件其流道所佔體積較小ð錐形流道其特性是藉改變流道入口面積與澆口面積比,來控制流動角的大小ð錐形流道藉控制流動角的大小,便可控制充填模式l 澆口設計ð澆口面積計算公式V :壓鑄件體積(含溢流井體積)(cm 3) Vg:澆口速度(m/s) t:充填時間(s) 澆、流道系統設計(6/10)tVg Ag ×=VAg:澆口面積(mm 2)ð舉例說明:鑄件(含溢流井)重400g,平均壁厚1.4mm, V =400/1.8=222.22 cm 3(鎂鑄件比重為1.8) 假設Vg=55m/s, t=0.03 則Ag=222.22/(55*0.03)=134.68 mm 2,另澆口厚度不得超出鑄件厚度的一半,因而在此定為0.55mm ,故澆口寬度=134.68/0.55=245mm ,但澆口形狀計算值應為實際生產時的75~85% ,以利試鑄後之修正澆、流道系統設計(7/10) l澆口與鑄件接合之方式ð側向充填:使熔湯進入模穴時有特定角度澆、流道系統設計(8/10)l澆口與鑄件接合之方式ð端部充填:使熔湯容易往上充填,適用於深槽壓鑄件澆、流道系統設計(9/10) l澆口與鑄件接合之方式ð對合充填:適用於圓筒形壓鑄件澆、流道系統設計(10/10)l澆口與鑄件接合之方式ð墊形充填:適用於平板壓鑄件及整緣容易要求鑄件模具分割面設定要因(1/7)l熔液流動性l尺寸精度l模具構造模具分割面設定要因(2/7)l模具分割面選定原則ð無死角ð製品須卡在可動模ð符合壓鑄品的品質要求ð必須利於對熔液有流動影響的鑄口、流道、澆口與湯井等位置及面積設立ð壓鑄後半成品須無去邊、修飾、機械加工上的問題ð應利於模具製造加工及模具壽命ð應利於鑄造生產性模具分割面設定要因(3/7)l模具分割面的記號ð分割面以此記號表示,此記號表示模具打開方向,此方向側通常應在可動模。
《压铸件设计》课件

未来发展趋势
展望压铸件设计的未来发展趋势。
《压铸件设计》PPT课件
掌握压铸件设计的方法和技巧,提高设计质量和效率。
概述
压铸件具有独特特点,应用广泛。
压铸件设计的基本要素
材料的选择
选择合适的材料是设计成功 的关键。
构件的几何形状
几何形状对产品质量和性能 影响重大。
工艺性能的考虑
考虑到工艺性能可以提高生 产效率。
压铸件设计的主要步骤
1
材料的选择和验算
合理设计压铸模可以提高生产效率。
2 压铸过程中的温度、压力等参数的控制
严格控制各种参数,确保产品质量。
3 压铸件的缺陷及处理方法
分析和处理压铸件的常见缺陷。
压铸件设计案例分析
实际生产中的例子分析
通过实际案例深入探讨压铸件设计。
压铸件设计优化实践
分享优化实践经验,提高设计效果。
总结
压铸件设计的作用和意义
2
选择适合的材料,并进行验算。
3
工艺性能的分析和优化
4
分析工任务的确定
明确设计目标,为后续步骤提供指导。
构件的几何形状的确定
确定合适的几何形状,考虑到实际生产 的要求。
产品的试制和修正
进行产品试制,并进行必要的修正。
压铸件设计需要注意的问题
1 压铸模的设计