制动系统匹配计算详解
制动计算
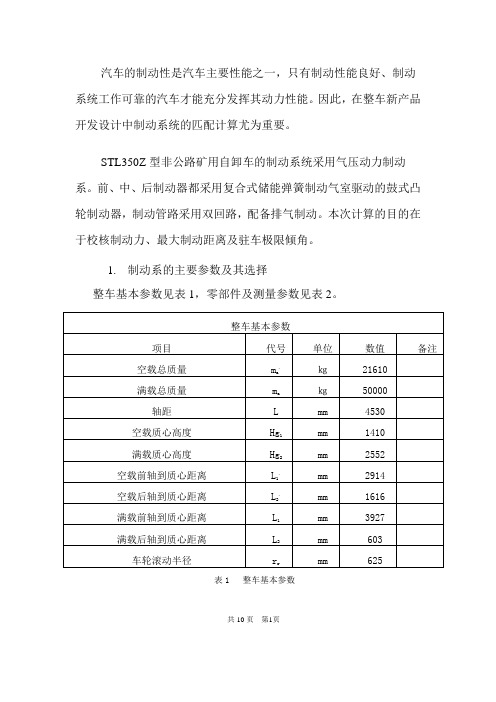
汽车的制动性是汽车主要性能之一,只有制动性能良好、制动系统工作可靠的汽车才能充分发挥其动力性能。
因此,在整车新产品开发设计中制动系统的匹配计算尤为重要。
STL350Z型非公路矿用自卸车的制动系统采用气压动力制动系。
前、中、后制动器都采用复合式储能弹簧制动气室驱动的鼓式凸轮制动器,制动管路采用双回路,配备排气制动。
本次计算的目的在于校核制动力、最大制动距离及驻车极限倾角。
1.制动系的主要参数及其选择整车基本参数见表1,零部件及测量参数见表2。
表1 整车基本参数共10页第1页零部件及测量参数同步附着系数φ00.355401 607路面附着系数φ0.4 重力加速度g m/s29.8最大制动减速度du/dt m/s2 4.8每个制动器制动力矩TfN·m 25000制动初速度v0m/s 8.33即30Km/h路面与轮胎间的滚动摩擦系数 f 0.018表2 零部件及测量参数制动力与制动力分配系数对于任一角速度ω>0的车轮,其力矩平衡方程为(1)T f—制动器对车轮的制动力矩,N •m;F B—地面对车轮的摩擦力,N;r e—车轮的有效半径,mm;则共10页第2页根据汽车制动时的整车受力分析,考虑到制动时的轴荷转移,可求得地面对前后轴车轮的法向反力Z1,Z2:(2)求得,前后轴车轮附着力为:(3)—前轴车轮附着力—后轴车轮附着力—汽车制动减速度—制动强度共10页第3页—公式引用来自《汽车设计》刘惟信主编因制动过程中,可能出现前先抱死拖滑、后轮先抱死拖滑、前后轮同时抱死拖滑三种情况,而其中以前后轮同时抱死拖滑附着条件利用最好,并且最安全可靠。
所以有:(4)该比值0.6符合《汽车设计》中的经验数据,在0.5~0.7之间。
—前轴车轮制动器制动力—后轴车轮制动器制动力—前轴车轮地面制动力—后轴车轮地面制动力由式(3)消去φ,可得(5)以、为坐标绘制前后轮制动器制动力分配曲线,即Ⅰ曲线。
共10页第4页。
制动系统匹配设计计算分解
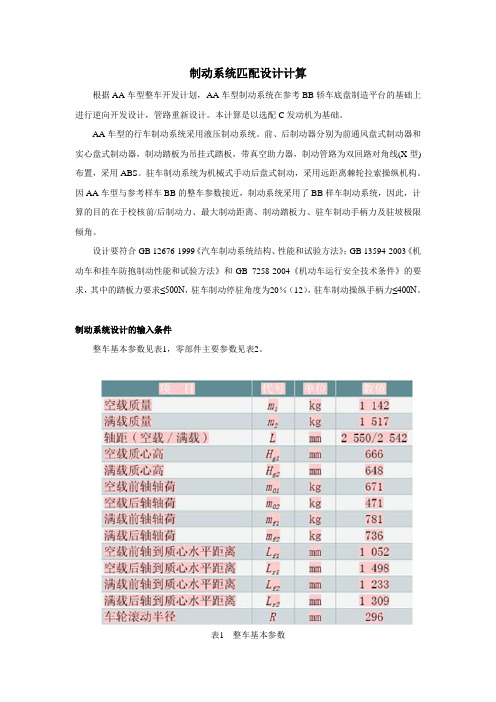
制动系统匹配设计计算根据AA车型整车开发计划,AA车型制动系统在参考BB轿车底盘制造平台的基础上进行逆向开发设计,管路重新设计。
本计算是以选配C发动机为基础。
AA车型的行车制动系统采用液压制动系统。
前、后制动器分别为前通风盘式制动器和实心盘式制动器,制动踏板为吊挂式踏板,带真空助力器,制动管路为双回路对角线(X型)布置,采用ABS。
驻车制动系统为机械式手动后盘式制动,采用远距离棘轮拉索操纵机构。
因AA车型与参考样车BB的整车参数接近,制动系统采用了BB样车制动系统,因此,计算的目的在于校核前/后制动力、最大制动距离、制动踏板力、驻车制动手柄力及驻坡极限倾角。
设计要符合GB 12676-1999《汽车制动系统结构、性能和试验方法》;GB 13594-2003《机动车和挂车防抱制动性能和试验方法》和GB 7258-2004《机动车运行安全技术条件》的要求,其中的踏板力要求≤500N,驻车制动停驻角度为20%(12),驻车制动操纵手柄力≤400N。
制动系统设计的输入条件整车基本参数见表1,零部件主要参数见表2。
表1 整车基本参数表2 零部件主要参数制动系统设计计算1.地面对前、后车轮的法向反作用力地面对前、后车轮的法向反作用力如图1所示。
图1 制动工况受力简图由图1,对后轮接地点取力矩得:式中:FZ1(N):地面对前轮的法向反作用力;G(N):汽车重力;b(m):汽车质心至后轴中心线的水平距离;m(kg):汽车质量;hg(m):汽车质心高度;L(m):轴距;(m/s2):汽车减速度。
对前轮接地点取力矩,得:式中:FZ2(N):地面对后轮的法向反作用力;a(m):汽车质心至前轴中心线的距离。
2.理想前后制动力分配在附着系数为ψ的路面上,前、后车轮同步抱死的条件是:前、后轮制动器制动力之和等于汽车的地面附着力;并且前、后轮制动器制动力Fm1、Fm2分别等于各自的附着力,即:根据式(1)、(2)及(3),消去变量ψ,得:由(1)、(2)、(3)及此时=zg,z=ψ=ψ0,可得:前轴:后轴:由此可以建立由Fu1和Fu2的关系曲线,即I曲线。
制动系统匹配计算讲义
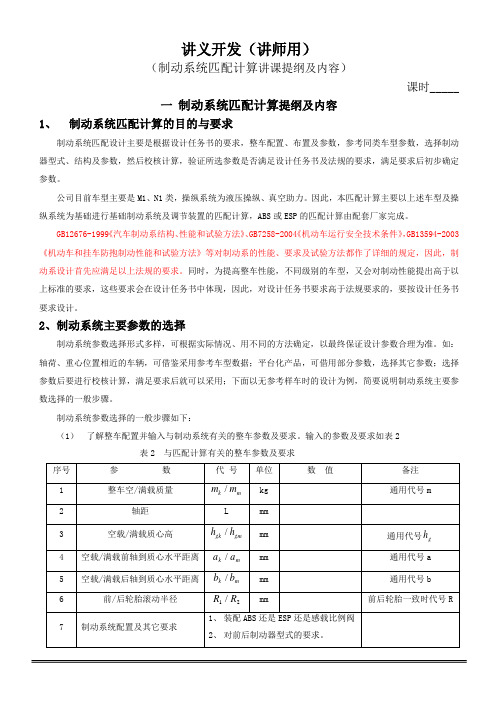
GB12676-1999《汽车制动系结构、性能和试验方法》、GB7258-2004《机动车运行安全技术条件》,GB13594-2003《机动车和挂车防抱制动性能和试验方法》等对制动系的性能、要求及试验方法都作了详细的规定,因此,制动系设计首先应满足以上法规的要求。同时,为提高整车性能,不同级别的车型,又会对制动性能提出高于以上标准的要求,这些要求会在设计任务书中体现,因此,对设计任务书要求高于法规要求的,要按设计任务书要求设计。
Fμ=Tμ/R………………………………………………………(2-3)
式中:Tμ—制动器对车轮作用的制动力矩,即制动器的摩擦力矩,其方向与车轮旋转方向相反。
R—车轮有效半径。
(3)理想的前、后制动器制动力分配
在附着系数为 的路面上,前、后车轮同步抱死的条件是:前、后轮制动器制动力之和 等于汽车与地面附着力 ;并且前、后轮制动器制动力 分别等于各自的附着力 ,即:
制动系统参数选择的一般步骤如下:
(1)了解整车配置并输入与制动系统有关的整车参数及要求。输入的参数及要求如表2
表2与匹配计算有关的整车参数及要求
序号
参 数
代 号
单位
数ቤተ መጻሕፍቲ ባይዱ值
备注
1
整车空/满载质量
kg
通用代号m
2
轴距
L
mm
3
空载/满载质心高
mm
通用代号
4
空载/满载前轴到质心水平距离
mm
通用代号a
5
空载/满载后轴到质心水平距离
制动系统匹配计算课件
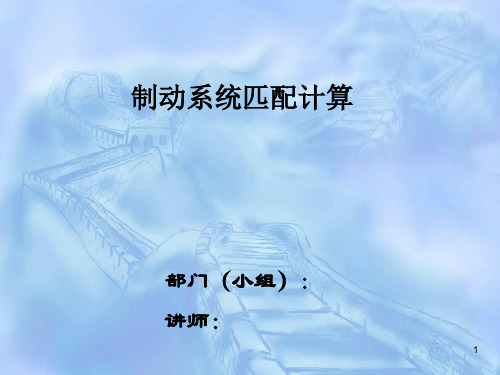
n1 n2
r1 R1 r2 R2
制动力分配系数:
………(2-19)
= Fu1
C1 p1
Fu1 Fu2 C1 p1 C2 p2
p1d12BF1n1r1 / R1
p1d12 B F1n1r1
/ R1
p2d
2 2
BF2
n2
r2
/ R2
………(2-20)
2.1.1 理想制动力分配曲线绘制
Fz
2
L
Ga
m
du dt
hg
………………..(2-2)
式中:FZ1、 FZ2——地面对前、后轮的法向反作用力,N; G—汽车重力,N;
a、b—汽车质心至前、后轴中心线的水平距离,mm;
m—汽车质量,kg;
hg—汽车质心高度,mm; L —轴距,mm;
du/dt —汽车减速度,m/s2。 7
感载比利阀时的同步附着系数:空载1.04,满载1.30。
11
2、制动系统主要参数的选择
2.1.2同步附着系数及制动力分配系数的初步选择
2、制动器制动力分配系数 前制动器制动力与汽车总的制动器制动力之比,称为
制动器制动力分配系数。
F1
F1
F F1 F 2
………………..(2-8)
已确定的参数、 系列化要求
轮缸直径
2.2.1前、后轴制动力确定
计算满载、前后轮同时抱死时的制动力:
F1
G L
(b
hg )
………………..(2-5)
无制动力调节装置的后轴制动力为:
F 2
1
(整理)制动系统匹配计算讲义
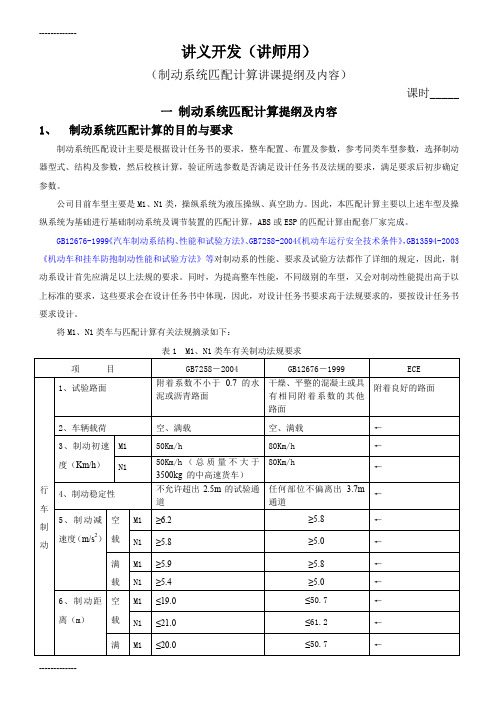
讲义开发(讲师用)(制动系统匹配计算讲课提纲及内容)课时_____一制动系统匹配计算提纲及内容1、制动系统匹配计算的目的与要求制动系统匹配设计主要是根据设计任务书的要求,整车配置、布置及参数,参考同类车型参数,选择制动器型式、结构及参数,然后校核计算,验证所选参数是否满足设计任务书及法规的要求,满足要求后初步确定参数。
公司目前车型主要是M1、N1类,操纵系统为液压操纵、真空助力。
因此,本匹配计算主要以上述车型及操纵系统为基础进行基础制动系统及调节装置的匹配计算,ABS或ESP的匹配计算由配套厂家完成。
GB12676-1999《汽车制动系结构、性能和试验方法》、GB7258-2004《机动车运行安全技术条件》,GB13594-2003《机动车和挂车防抱制动性能和试验方法》等对制动系的性能、要求及试验方法都作了详细的规定,因此,制动系设计首先应满足以上法规的要求。
同时,为提高整车性能,不同级别的车型,又会对制动性能提出高于以上标准的要求,这些要求会在设计任务书中体现,因此,对设计任务书要求高于法规要求的,要按设计任务书要求设计。
将M1、N1类车与匹配计算有关法规摘录如下:表1 M1、N1类车有关制动法规要求项目GB7258-2004 GB12676-1999 ECE行车制动1、试验路面附着系数不小于0.7 的水泥或沥青路面干燥、平整的混凝土或具有相同附着系数的其他路面附着良好的路面2、车辆载荷空、满载空、满载←3、制动初速度(Km/h)M1 50Km/h 80Km/h ←N150Km/h(总质量不大于3500kg 的中高速货车)80Km/h←4、制动稳定性不允许超出2.5m的试验通道任何部位不偏离出 3.7m通道←5、制动减速度(m/s2)空载M1 ≥6.2≥5.8←N1 ≥5.8 ≥5.0 ←满载M1 ≥5.9≥5.8←N1 ≥5.4 ≥5.0 ←6、制动距离(m)空载M1 ≤19.0≤50.7 ←N1 ≤21.0≤61.2 ←满M1 ≤20.0≤50.7 ←载N1 ≤22.0≤61.2 ←7、液压制动脚踏板力(N)空载M1 ≤400≤500←N1 ≤450≤700←满载M1 ≤500≤500←N1 ≤700≤700←8、液压制动踏板行程要求踏板行程不应大于踏板全行程的3/4;装有自动调整间隙装置时不应大于踏板全行程的4/5,且乘用车不应大于120 mm ,其它机动车不应大于150 mm。
某车型制动系统设计计算报告分析解析
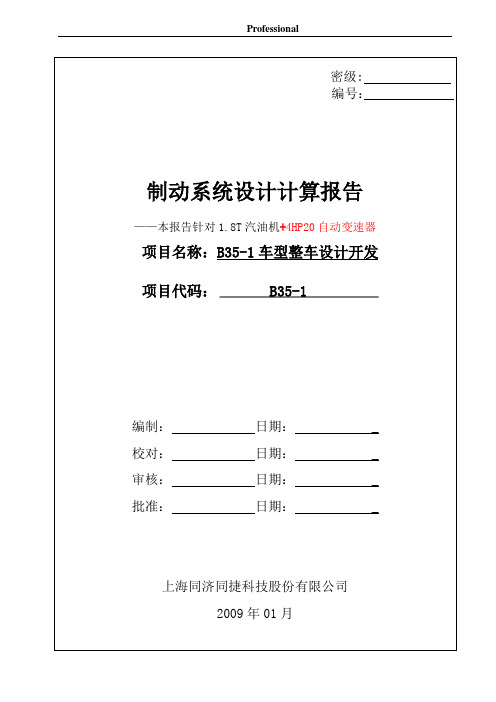
目录1 概述 (1)1.1 任务来源 (1)1.2 制动系统基本介绍 (1)1.3 制动系统的结构简图 (1)1.4 计算目的 (1)2 制动系统设计的输入条件 (1)2.1 制动法规基本要求 (2)2.2 整车基本参数 (2)2.3 制动系统零部件主要参数 (2)3 制动系统设计计算 (3)3.1 前、后制动器制动力分配 (3)3.2 制动减速度及制动距离校核 (10)3.3 真空助力器主要技术参数 (11)3.4 制动主缸行程校核 (11)3.5 制动踏板行程和踏板力校核 (12)3.6 驻车制动校核 (12)3.7 应急制动校核 (13)3.8 传能装置部分失效剩余制动力校核 (14)3.9 制动器能容量校核 (14)4 数据输出列表 (16)5 结论及分析 (16)参考文献 (17)制动系统设计计算报告1概述1.1任务来源根据B35-1整车开发要求,按照确认的设计依据和要求,并依据总布置的要求对制动系统的选型并作相应的计算。
1.2制动系统基本介绍1.8T-AT车型的行车制动系统采用液压制动系统。
前制动器为带有双制动轮缸的通风盘式制动器,后制动器为单制动轮缸的实心盘式制动器。
制动踏板为吊挂式踏板,带真空助力器,制动管路为双回路对角线(X型)布置,采用ABS 以防止车辆在紧急制动情况下发生车轮抱死。
驻车制动系统为杠杆式,作用于后轮。
ABS控制系统以及匹配计算由供应商完成,本文计算不做讨论。
1.3制动系统的结构简图制动系统的结构简图如图1:1. 带制动主缸的真空助力器总成2.制动踏板3.车轮4.轮速传感器5. 制动管路6. 制动轮缸7.ABS控制单元图1 制动系统的结构简图1.4计算目的制动系统计算的目的在于校核前、后制动力,最大制动距离、制动踏板力及驻坡极限倾角等是否符合法规及标准要求、制动系统匹配是否合理。
2制动系统设计的输入条件2.1制动法规基本要求(1)GB 12676-1999《汽车制动系统结构、性能和试验方法》(2)GB 13594-2003《机动车和挂车防抱制动性能和试验方法》(3)GB 7258-2004《机动车运行安全技术条件》表1-1是对相关法规主要内容的摘要。
关于制动系统的算法
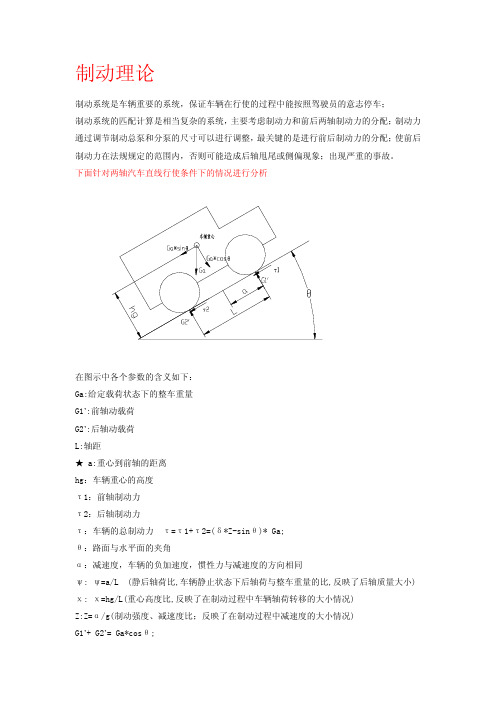
精确地确定β的值对制动性的分析有极端重要的作用。
车轴临界抱死的条件 车轴处于临界抱死的状态:τi=φi* Gi’; τ1= τ2= 对于给定的φ1=φ2=φ的情况下有:τμ1、τμ2、φ1、φ2 所组成的曲线如下所示, 得到τ1 和τ2 的方τ2 的关系的程如下: τ2*τ2+τ1*τ1+(1-ψ)*τ2* Ga*cosθ-ψ*τ1* Ga*cosθ/χ+2*τ1*τ2=0 配方成完全开方,得到理想的制动力分配方程: τ2= 假设: 、、、 、、、、 、、、 、、、 对于 I 曲线的准确理解;事实上 I 曲线表明同值φ1、φ2 线的交点即同步临界抱死点必在 I 点上,最能充分发挥附着力的潜力,而对稳定性或方向操纵性而言,并非最佳的。控制前后 车轮的制动力分配:就是控制后轴的制动力,将其控制在比较理想的范围内,防止后轮提前 抱死,给车辆的操纵稳定性带来麻烦。所有控制的策略都是围绕着这个中心进行的。
制动理论
制动系统是车辆重要的系统,保证车辆在行使的过程中能按照驾驶员的意志停车; 制动系统的匹配计算是相当复杂的系统,主要考虑制动力和前后两轴制动力的分配;制动力 通过调节制动总泵和分泵的尺寸可以进行调整,最关键的是进行前后制动力的分配;使前后 制动力在法规规定的范围内,否则可能造成后轴甩尾或侧偏现象;出现严重的事故。 下面针对两轴汽车直线行使条件下的情况进行分析
制动系统匹配设计
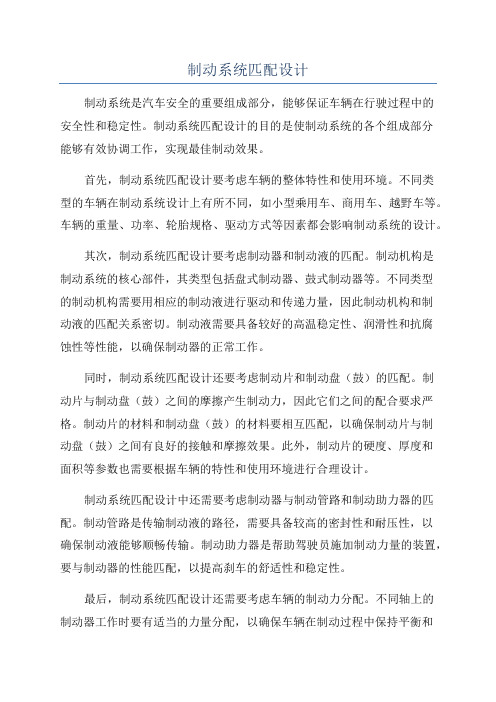
制动系统匹配设计制动系统是汽车安全的重要组成部分,能够保证车辆在行驶过程中的安全性和稳定性。
制动系统匹配设计的目的是使制动系统的各个组成部分能够有效协调工作,实现最佳制动效果。
首先,制动系统匹配设计要考虑车辆的整体特性和使用环境。
不同类型的车辆在制动系统设计上有所不同,如小型乘用车、商用车、越野车等。
车辆的重量、功率、轮胎规格、驱动方式等因素都会影响制动系统的设计。
其次,制动系统匹配设计要考虑制动器和制动液的匹配。
制动机构是制动系统的核心部件,其类型包括盘式制动器、鼓式制动器等。
不同类型的制动机构需要用相应的制动液进行驱动和传递力量,因此制动机构和制动液的匹配关系密切。
制动液需要具备较好的高温稳定性、润滑性和抗腐蚀性等性能,以确保制动器的正常工作。
同时,制动系统匹配设计还要考虑制动片和制动盘(鼓)的匹配。
制动片与制动盘(鼓)之间的摩擦产生制动力,因此它们之间的配合要求严格。
制动片的材料和制动盘(鼓)的材料要相互匹配,以确保制动片与制动盘(鼓)之间有良好的接触和摩擦效果。
此外,制动片的硬度、厚度和面积等参数也需要根据车辆的特性和使用环境进行合理设计。
制动系统匹配设计中还需要考虑制动器与制动管路和制动助力器的匹配。
制动管路是传输制动液的路径,需要具备较高的密封性和耐压性,以确保制动液能够顺畅传输。
制动助力器是帮助驾驶员施加制动力量的装置,要与制动器的性能匹配,以提高刹车的舒适性和稳定性。
最后,制动系统匹配设计还需要考虑车辆的制动力分配。
不同轴上的制动器工作时要有适当的力量分配,以确保车辆在制动过程中保持平衡和稳定。
制动力分配的主要方式有前后轮制动力分配和左右轮制动力分配两种。
综上所述,制动系统匹配设计是一个综合性的工程任务,需要综合考虑车辆的整体特性、使用环境和制动系统的各个组成部分之间的匹配关系。
只有进行合理的匹配设计,才能实现制动系统的最佳性能和安全效果。
制动系统选择与计算
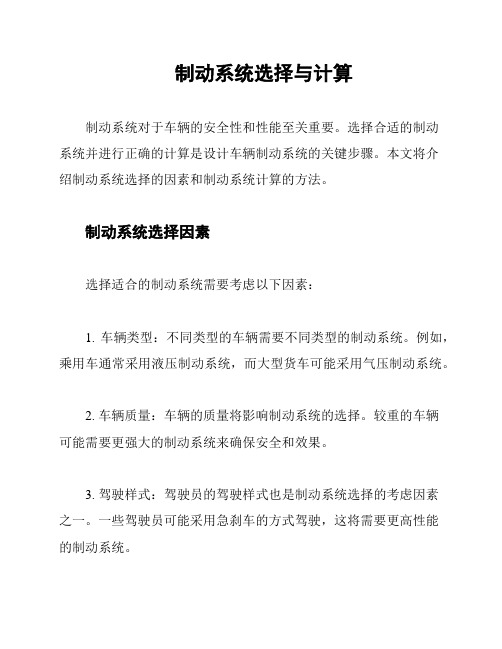
制动系统选择与计算制动系统对于车辆的安全性和性能至关重要。
选择合适的制动系统并进行正确的计算是设计车辆制动系统的关键步骤。
本文将介绍制动系统选择的因素和制动系统计算的方法。
制动系统选择因素选择适合的制动系统需要考虑以下因素:1. 车辆类型:不同类型的车辆需要不同类型的制动系统。
例如,乘用车通常采用液压制动系统,而大型货车可能采用气压制动系统。
2. 车辆质量:车辆的质量将影响制动系统的选择。
较重的车辆可能需要更强大的制动系统来确保安全和效果。
3. 驾驶样式:驾驶员的驾驶样式也是制动系统选择的考虑因素之一。
一些驾驶员可能采用急刹车的方式驾驶,这将需要更高性能的制动系统。
4. 驾驶环境:不同的驾驶环境也需要不同类型的制动系统。
例如,山区驾驶可能需要更强大的制动系统来应对陡峭的坡道。
制动系统计算方法制动系统计算的目标是确定合适的制动力和制动装置。
以下是一些常用的计算方法:1. 制动力计算:根据车辆的质量和设计要求,计算所需的制动力。
制动力通常以车辆质量的百分比来表示。
2. 制动装置计算:根据制动力和制动功率的要求,选择合适的制动装置。
制动装置包括制动盘、制动片、制动液等。
3. 制动力分配:根据车辆的重心位置和轮胎的附着力,将制动力分配到各个轮胎上,以保证车辆的稳定性和安全性。
4. 制动系统参数计算:根据车辆的设计要求和制动装置的特性,计算出制动系统的参数,例如制动管路的直径、制动盘的尺寸等。
总结制动系统选择与计算是设计车辆制动系统的重要步骤。
合适的制动系统选择和正确的计算有助于提高车辆的安全性和性能。
在选择制动系统和进行计算时,需要考虑车辆类型、车辆质量、驾驶样式和驾驶环境等因素,并使用合适的计算方法来确定制动力和制动装置。
制动系统设计计算报告
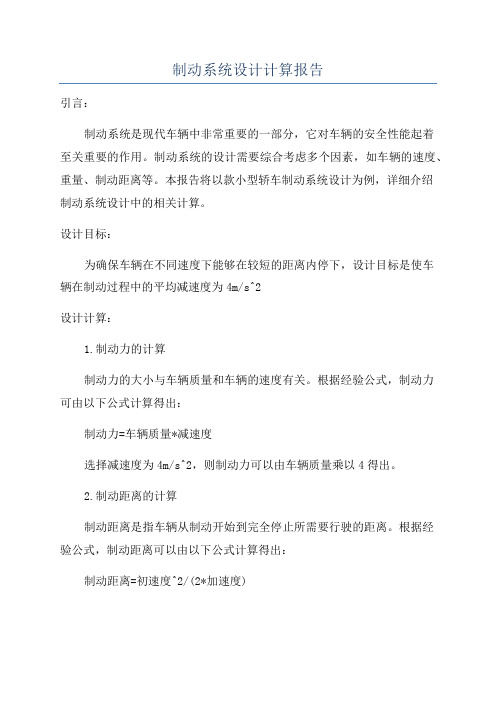
制动系统设计计算报告引言:制动系统是现代车辆中非常重要的一部分,它对车辆的安全性能起着至关重要的作用。
制动系统的设计需要综合考虑多个因素,如车辆的速度、重量、制动距离等。
本报告将以款小型轿车制动系统设计为例,详细介绍制动系统设计中的相关计算。
设计目标:为确保车辆在不同速度下能够在较短的距离内停下,设计目标是使车辆在制动过程中的平均减速度为4m/s^2设计计算:1.制动力的计算制动力的大小与车辆质量和车辆的速度有关。
根据经验公式,制动力可由以下公式计算得出:制动力=车辆质量*减速度选择减速度为4m/s^2,则制动力可以由车辆质量乘以4得出。
2.制动距离的计算制动距离是指车辆从制动开始到完全停止所需要行驶的距离。
根据经验公式,制动距离可以由以下公式计算得出:制动距离=初速度^2/(2*加速度)在制动过程中,加速度是负值(减速),所以加速度取为-4m/s^2、根据具体车辆的初始速度,可以计算出相应的制动距离。
3.制动盘和制动钳的尺寸计算制动盘和制动钳的尺寸需要考虑车辆的速度和质量。
根据经验公式,制动盘的直径与车速和减速度有关,可以通过以下公式计算得出:制动盘直径=停车速度*车辆质量*系数/制动力在本设计中,选择停车速度为60 km/h,车辆质量为1000 kg,系数为0.7、根据以上参数,可以计算出制动盘的直径。
根据制动盘的直径,可以确定制动钳的尺寸。
制动盘和制动钳的尺寸需要满足制动力的需求,并能够有效散热,以免在制动过程中过热导致制动力减弱。
4.制动液系统的计算制动液的压力和制动钳的工作效果有关。
根据经验公式,制动液的压力可以由以下公式计算得出:制动液压力=制动力/制动钳有效面积制动液压力需要根据制动钳的效率和制动力来选择合适的值。
根据经验,选择制动液压力为5MPa。
结论:根据以上计算结果,制动系统的设计可以满足要求。
制动力、制动距离、制动盘和制动钳的尺寸以及制动液压力的计算都能够保证车辆在制动过程中的安全性。
制动系统匹配计算讲义
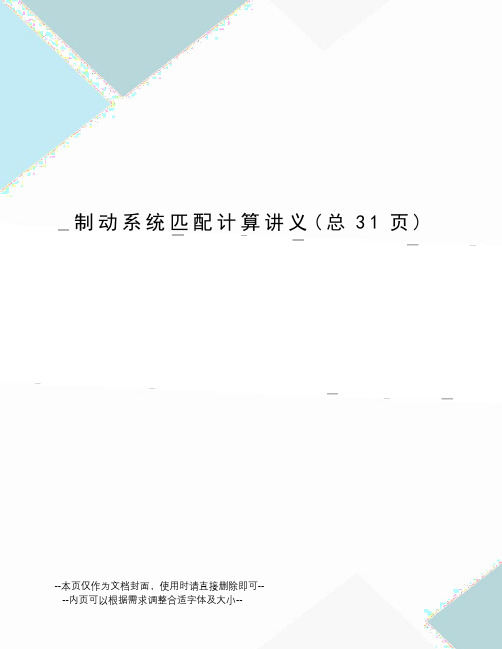
制动系统匹配计算讲义(总31页)--本页仅作为文档封面,使用时请直接删除即可----内页可以根据需求调整合适字体及大小--讲义开发(讲师用)(制动系统匹配计算讲课提纲及内容)课时_____一制动系统匹配计算提纲及内容1、制动系统匹配计算的目的与要求制动系统匹配设计主要是根据设计任务书的要求,整车配置、布置及参数,参考同类车型参数,选择制动器型式、结构及参数,然后校核计算,验证所选参数是否满足设计任务书及法规的要求,满足要求后初步确定参数。
公司目前车型主要是M1、N1类,操纵系统为液压操纵、真空助力。
因此,本匹配计算主要以上述车型及操纵系统为基础进行基础制动系统及调节装置的匹配计算,ABS或ESP的匹配计算由配套厂家完成。
GB12676-1999《汽车制动系结构、性能和试验方法》、GB7258-2004《机动车运行安全技术条件》,GB13594-2003《机动车和挂车防抱制动性能和试验方法》等对制动系的性能、要求及试验方法都作了详细的规定,因此,制动系设计首先应满足以上法规的要求。
同时,为提高整车性能,不同级别的车型,又会对制动性能提出高于以上标准的要求,这些要求会在设计任务书中体现,因此,对设计任务书要求高于法规要求的,要按设计任务书要求设计。
将M1、N1类车与匹配计算有关法规摘录如下:表1 M1、N1类车有关制动法规要求注:以上数据为发动机脱开的O型试验要求。
2、制动系统主要参数的选择制动系统参数选择形式多样,可根据实际情况、用不同的方法确定,以最终保证设计参数合理为准。
如:轴荷、重心位置相近的车辆,可借鉴采用参考车型数据;平台化产品,可借用部分参数,选择其它参数;选择参数后要进行校核计算,满足要求后就可以采用;下面以无参考样车时的设计为例,简要说明制动系统主要参数选择的一般步骤。
制动系统参数选择的一般步骤如下:(1)了解整车配置并输入与制动系统有关的整车参数及要求。
输入的参数及要求如表2表2 与匹配计算有关的整车参数及要求(2)初步选择系统主要参数。
汽车制动系统计算
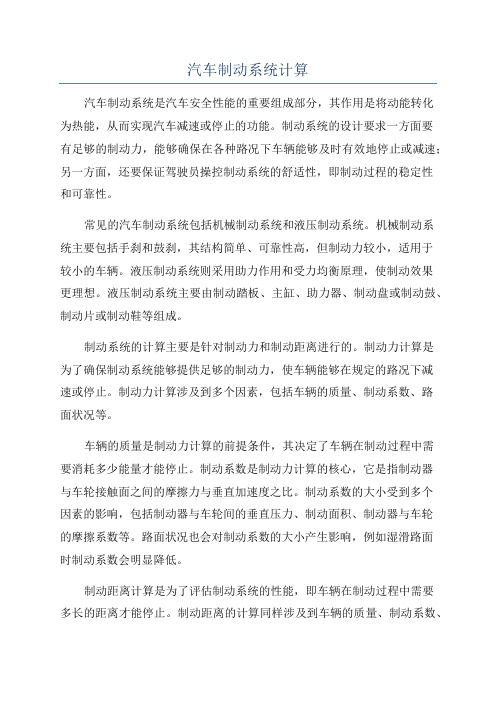
汽车制动系统计算汽车制动系统是汽车安全性能的重要组成部分,其作用是将动能转化为热能,从而实现汽车减速或停止的功能。
制动系统的设计要求一方面要有足够的制动力,能够确保在各种路况下车辆能够及时有效地停止或减速;另一方面,还要保证驾驶员操控制动系统的舒适性,即制动过程的稳定性和可靠性。
常见的汽车制动系统包括机械制动系统和液压制动系统。
机械制动系统主要包括手刹和鼓刹,其结构简单、可靠性高,但制动力较小,适用于较小的车辆。
液压制动系统则采用助力作用和受力均衡原理,使制动效果更理想。
液压制动系统主要由制动踏板、主缸、助力器、制动盘或制动鼓、制动片或制动鞋等组成。
制动系统的计算主要是针对制动力和制动距离进行的。
制动力计算是为了确保制动系统能够提供足够的制动力,使车辆能够在规定的路况下减速或停止。
制动力计算涉及到多个因素,包括车辆的质量、制动系数、路面状况等。
车辆的质量是制动力计算的前提条件,其决定了车辆在制动过程中需要消耗多少能量才能停止。
制动系数是制动力计算的核心,它是指制动器与车轮接触面之间的摩擦力与垂直加速度之比。
制动系数的大小受到多个因素的影响,包括制动器与车轮间的垂直压力、制动面积、制动器与车轮的摩擦系数等。
路面状况也会对制动系数的大小产生影响,例如湿滑路面时制动系数会明显降低。
制动距离计算是为了评估制动系统的性能,即车辆在制动过程中需要多长的距离才能停止。
制动距离的计算同样涉及到车辆的质量、制动系数、道路状况等因素。
制动距离的计算可以根据牛顿第二定律和运动学公式来进行,其中制动时间、制动段速度和制动段长度等参数需要进行实际测量或估算。
为了确保汽车制动系统的安全性和可靠性,制动力和制动距离的计算结果可以作为制动系统设计和制造的依据。
制动力应该保证在各种路况下都能够满足要求,并且具有一定的安全余量。
制动距离的计算结果可以与制动距离标准进行比较,以评估制动系统的性能是否合格。
总之,汽车制动系统的计算是保证汽车行驶安全的重要环节。
制动系统匹配设计计算
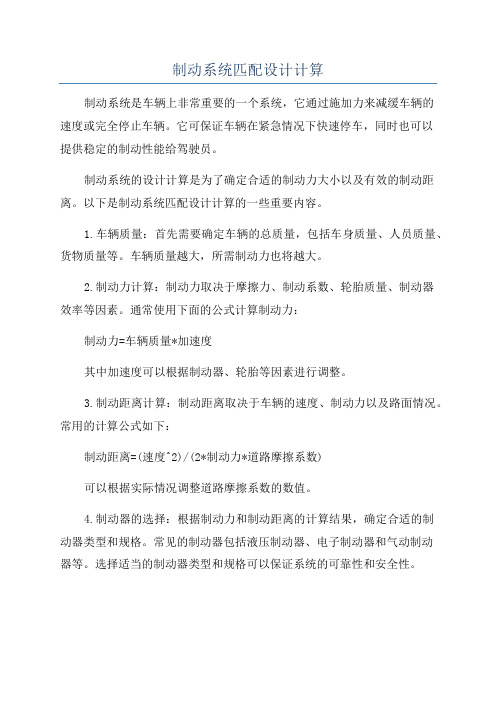
制动系统匹配设计计算制动系统是车辆上非常重要的一个系统,它通过施加力来减缓车辆的速度或完全停止车辆。
它可保证车辆在紧急情况下快速停车,同时也可以提供稳定的制动性能给驾驶员。
制动系统的设计计算是为了确定合适的制动力大小以及有效的制动距离。
以下是制动系统匹配设计计算的一些重要内容。
1.车辆质量:首先需要确定车辆的总质量,包括车身质量、人员质量、货物质量等。
车辆质量越大,所需制动力也将越大。
2.制动力计算:制动力取决于摩擦力、制动系数、轮胎质量、制动器效率等因素。
通常使用下面的公式计算制动力:制动力=车辆质量*加速度其中加速度可以根据制动器、轮胎等因素进行调整。
3.制动距离计算:制动距离取决于车辆的速度、制动力以及路面情况。
常用的计算公式如下:制动距离=(速度^2)/(2*制动力*道路摩擦系数)可以根据实际情况调整道路摩擦系数的数值。
4.制动器的选择:根据制动力和制动距离的计算结果,确定合适的制动器类型和规格。
常见的制动器包括液压制动器、电子制动器和气动制动器等。
选择适当的制动器类型和规格可以保证系统的可靠性和安全性。
5.制动系统的平衡:制动系统中的前轮制动力和后轮制动力需要进行合理的分配,以确保车辆能够稳定停止。
通常,前轮制动力应约为总制动力的70%,后轮制动力约为总制动力的30%。
在进行制动系统匹配设计计算时,还需要考虑以下几个因素:1.道路情况:不同路面的摩擦系数有所不同,需要根据实际道路情况调整计算中的摩擦系数。
2.制动器或刹车片的磨损:制动器磨损会导致制动力的减小,因此需要考虑磨损对制动力的影响。
3.轮胎的状态:轮胎的状况会影响制动力的传递效果,因此需要保证轮胎的状态良好。
4.驾驶员的反应时间:制动系统设计中需要考虑到驾驶员的反应时间,通常取2秒。
综上所述,在进行制动系统匹配设计计算时,需要考虑车辆质量、制动力、制动距离、制动器选择以及系统平衡等多个因素。
通过合理的计算可以确保制动系统满足安全性和可靠性的要求,并提供稳定的制动性能给驾驶员。
制动匹配应用(f线组-r线组与β线-I曲线的组合图表的意义)

制动匹配应用(f线组-r线组与β线-I曲线的组合图表的意义)
下图时一个满载状态下,2轴车型的制动线图。
表示不同附着系数φ路面上汽车制动过程情况。
当先遇到f线,前轴制动就会先抱死。
当先遇到r线,后轴制动就会先抱死。
遇到f或r线时,就会按着此线变化前后轴地面制动力。
之所以抱死后还会增长(指前轴)或降低制动力(指后轴),是因为制动时整车的质心转移。
在此同步附着系数的路面上制动时,直接沿着β线制动力变化,直到这个交点,即前后车轮同时抱死,不再有经过f线和r线的过程。
说明:因为β线是我们的制动器的实际制动力值。
此处我们可以直观的通过此图表判断我们选择的制动器在对应轮胎半径下其制动力是否能够满足相应地面附着系数路面上的使用要求。
即β线的最大值(横纵坐标)要在f线组和r线组的区域之外。
我们一般选择制动器的能力时会比f和r线组的值大一些(指相交之后的部分上的值),以保证有一定的富余。
但是注意不能超过制动器本身的能力,因为过大的制动力对制动器的寿命、摩擦片的磨损、制动鼓变形等都有不利影响。
另关于选择的前、后制动器规格是否合理,按GB 12676《商用车辆和挂车制动系统技术要求及试验方法》的附录“车轴间的制动力分配及牵引车与挂车协调性要求”校核确认。
《汽车理论》中也有相应的计算方法。
中重型商用车制动系统匹配计算

Science &Technology Vision科技视界0前言目前,国内车辆制动系统相关标准主要有GB12676-1999《汽车制动系统结构、性能和试验方法》和GB7258-2004《机动车运行安全技术条件》。
但作为国内主机厂研发人员设计的依据主要为GB12676,且GB12676的主要内容是引用欧洲的主要制动法规ECE R13,因此有广泛的使用性和实用性。
根据机动车型分类,中重型商用车应划分为N2、N3和O 类车辆。
因此本规范主要是为了符合GB12676对N2、N3和O 类车辆的制动性能的规定。
同时为了使车辆的制动性能满足我国路况,要求在匹配计算过程中充分考虑用户试验数据,使设计车辆制动性能实用性更好,满足客户使用需求。
1制动系统匹配计算图1制动时的车辆受力图1.1制动匹配计算相关参数的确立1.1.1整车质量m(kg)由于国内中重型商用车超载现象比较普遍,因此需根据国情把超载考虑进去。
定义:空载质量m 1;满载质量质量m 2;超载质量m 31.1.2车辆轴距L(m)对于双前桥或双后桥,由于制动时载轴转移计算复杂,为简化起见,将双前桥或双后桥合并为一桥,轴距测量点为两桥中心点。
1.1.3车辆质心距后轴距离质心距后轴距离可在整车三维数模上得出,但为了数据准确,可以对空载车辆各轴称重,得出L 21;L 22,L 23通过公式(1-1)、(1-2)得出:L 22=m 1L 21+(m 2-m 1)L 24m 2(1-1)L 23=m 1L 21+(m 3-m 1)L 24m 3(1-2)L 21、L 22、L 23———空载、满载、超载质心距后轴距离(m)L 24———载货质心距后轴距离(m)1.1.4车辆质心高h g (m)空载质心高h g1可在整车三维数模上得出,也可以通过悬吊法测得。
而h g2和h g3通过公式(1-3)、(1-4)得出:h g2=m 1h g 1+(m 2-m 1)h g 4m 2(1-3)h g3=m 1h g 1+(m 3-m 1)h g 4m 3(1-4)h g1、h g2、h g3———空载、满载、超载质心高(m)h g4———载货质心高m(m)1.1.5轴荷m L (kg)空载前后轴荷可通过称重获得,而满载和超载前后轴荷可通过公式(1-5)、(1-6)、(1-7)、(1-8)得出:m L21=m 2L 22L(1-5)m L22=m 2-m L21(1-6)m L31=m 3L23L(1-7)m L32=m 3-m L31(1-8)m L11、m L12———空载前、后轴荷;m L21、m L22———满载前、后轴荷;m L31、m L32———超载前、后轴荷。
制动系统设计计算书

制动系 统设计 计算书
(Φ 式制动 器,前:后= :)
mm
轴距L= 1765
空载
满载
811.700565 827.34375
785
843.3
885
960
478
510
0.54
0.53
后轴负 荷G2 (kg) 后轴质 量分配 % 3.汽车动 轴荷分配 计算: 3.1 动轴 荷计算: 当汽 车以减速 度jt制动 时,由于 减速度而 产生的惯 性力,使 轴荷分配 相应改 变:
=
Lb - b hg
=
4.4 满载 时前后轴 附着力 矩:(道 路附着系 数Φ =0.65时 的附着力 矩) 前轴附着 力矩:
j0
=
Lb - b hg
=
Mj前 = Pt1' ? Rk1 =
#VALUE!
#VALUE! #VALUE!
后轴附着 力矩:
4.5 最大 管路压力 :
产生 最大管路 压力矩时 (Φ =0.65)的 管路压力 为最大管 路压力, 故当Φ =0.65时,
表二
为汽车制 动时前后 在不同减 速度jt/g 值时动轴 荷分配 比:
表二 (见下 页):
jt/g=φ
G1' 空载 满载
G2' 空载 满载
4.汽车制 动力的计 算: 4.1.汽车 制动时所 需的制动 力Pτ(轴 制动力) 当汽车 以减速度 jt/g制动 时,前后 各自所需 的制动力 为: 前轴: Pτ1=G1 '×jt/g× 9.8 (N) 后轴: Pτ2=G2 '×jt/g× 9.8 (N)
0.1 58.5 57.9 41.5 42.1
0.2 62.2 61.9 37.8 38.1
制动系统匹配设计计算
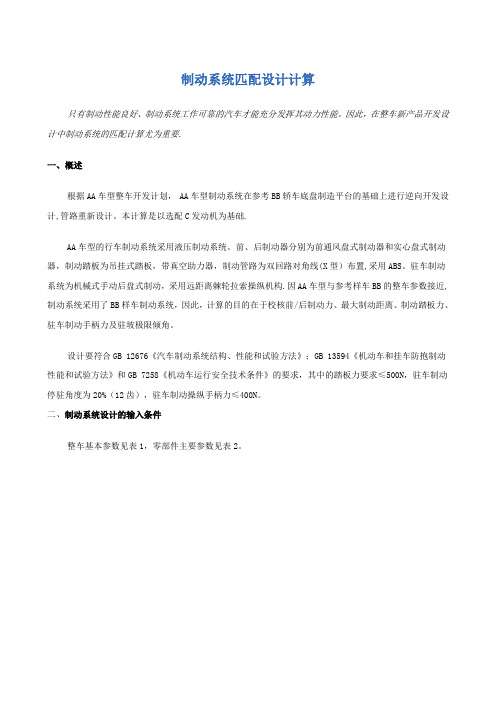
制动系统匹配设计计算只有制动性能良好、制动系统工作可靠的汽车才能充分发挥其动力性能。
因此,在整车新产品开发设计中制动系统的匹配计算尤为重要.一、概述根据AA车型整车开发计划, AA车型制动系统在参考BB轿车底盘制造平台的基础上进行逆向开发设计,管路重新设计。
本计算是以选配C发动机为基础.AA车型的行车制动系统采用液压制动系统。
前、后制动器分别为前通风盘式制动器和实心盘式制动器,制动踏板为吊挂式踏板,带真空助力器,制动管路为双回路对角线(X型)布置,采用ABS。
驻车制动系统为机械式手动后盘式制动,采用远距离棘轮拉索操纵机构.因AA车型与参考样车BB的整车参数接近,制动系统采用了BB样车制动系统,因此,计算的目的在于校核前/后制动力、最大制动距离、制动踏板力、驻车制动手柄力及驻坡极限倾角。
设计要符合GB 12676《汽车制动系统结构、性能和试验方法》;GB 13594《机动车和挂车防抱制动性能和试验方法》和GB 7258《机动车运行安全技术条件》的要求,其中的踏板力要求≤500N,驻车制动停驻角度为20%(12齿),驻车制动操纵手柄力≤400N。
二、制动系统设计的输入条件整车基本参数见表1,零部件主要参数见表2。
表1 整车基本参数表2 零部件主要参数三、制动系统设计计算(法规校核)1、地面对前、后车轮的法向反作用力地面对前、后车轮的法向反作用力如图1所示.图1 制动工况受力简图由图1,对后轮接地点取力矩得:(1)式中: FZ1(N):地面对前轮的法向反作用力;G(N):汽车重力;b(m):汽车质心至后轴中心线的水平距离;m(kg):汽车质量;hg(m):汽车质心高度;L(m):轴距;du/dt(m/s2):汽车减速度.对前轮接地点取力矩,得:(2)式中:FZ2(N):地面对后轮的法向反作用力;a(m):汽车质心至前轴中心线的距离.2、理想前后制动力分配在附着系数为ψ的路面上,前、后车轮同步抱死的条件是:前、后轮制动器制动力之和等于汽车的地面附着力;并且前、后轮制动器制动力Fμ1、Fμ2分别等于各自的附着力,即:(3)根据式(1)、(2)及(3),消去变量ψ,得:(4)由(1)、(2)、(3)及此时du/dt=z*g,z=ψ=ψ0,可得:前轴:(5)后轴:(6)由此可以建立由Fu1和Fu2的关系曲线,即I曲线。