年产280万吨热轧带钢车间设计
热轧带钢生产车间布置设计分析

热轧带钢生产车间布置设计分析热轧带钢简介以板坯或钢锭为原料用热轧方式生产各种中厚钢板、薄钢板和带钢的轧钢车间设计。
热轧板带钢车间设计范围包括中厚板车间设计、连续热轧宽带钢车间设计、施特克尔(炉卷)带钢轧钢车间设计和热轧窄带钢车间设计。
除了以上四类板带轧钢车间外,尚有叠轧薄板车间和行星轧板车间。
工艺流程热轧宽带钢主要生产工艺流程是板坯经加热后由粗轧机组及精轧机组制成带钢。
从精轧最后一架轧机出来的热钢带通过层流冷却到设定温度,由卷取机卷成钢带卷,冷却后的钢带卷,根据用户的不同需求,经过不同的精整作业线加工而成为钢板、平整卷及纵切钢带产品的过程。
设备构成主体、加热炉、推钢机、出钢机、粗轧机组(四机架)、飞剪、精轧机组(七机架连轧)、卷取机、吊车、精整机组(开卷机、矫直机、剪切机、张力卷取机等)。
在进行车间设计时主要是轧机型式和轧机组成的选择,同时从设备的可靠性、产品质量、维修方便、设备结构、外形和机组重量等因素进行比较和选择。
主要轧钢机有中厚钢板轧机、热轧宽带钢轧机、施特克尔(炉卷)带钢轧机和热轧窄带钢轧机。
(1)中厚钢板轧机。
有二辊式、三辊劳特式、四辊式。
轧机布置型式主要有单机架、双机架型式。
现代的中厚板车间设计均采用四辊式轧机,按产品和产量的不同选用单机架或双机架组成,最佳型式是粗轧机和精轧机,均为四辊轧机并顺列布置。
(2)热轧宽带钢轧机。
指辊身长度不小于1000mm的热轧带钢轧机,世界上建设最多的为1500~1800mm和2000~2300mm热轧带钢轧机,最大的达2690mm。
按粗轧机的型式和组成有半连续式、3/4连续式和连续式三种热轧宽带钢轧机。
(3)施特克尔带钢轧机。
主要用于轧制不锈钢、硅钢等难变形金属。
该轧机的特点是在轧机入口和出口设有带卷筒的加热保温炉,用以保持带钢轧制温度,因此在中国称炉卷轧机。
现代的施特克尔带钢车间,一般由一架四辊式可逆式万能粗轧机和一架四辊可逆式精轧机组成。
轧机后设有带钢冷却设备、卷取机和钢板剪切设备。
年产280万吨1780热轧带钢车间设计开题报告

二、设计方案
2.1主要研究内容 1.热轧带钢的生产现状,前景,建厂的目的和意义,产品的范围和产品规格。 2.典型产品道次选择(产品厚度3mm) ,轧机布置选择比较,粗轧机、精轧机形 式对比。 3.压下分配,轧制规程计算,温降计算,轧制力计算。 4.电机校核,轧辊强度校核,年产量计算。 5.辅助设备校核:加热炉形式选择,卷取机校核。 6.金属平衡、燃料消耗计算。 2.2 方法手段 设计年产 280 万吨 1780 热轧带钢生产线。通过设计方案比较,选择连铸机、轧 钢机以及各种辅助设备的形式,确定布置方式;根据典型产品规格(厚度为 3mm) 进行压下规程设计和计算(力能参数计算、轧辊强度验算和电机能力校核) ;并对选 取的新工艺和技术进行简要说明。
以及各种交通车辆的结构件,也用于船舶及铁路集装箱制造,石油井架、各种工程 机械和交通机械的制造。 5)耐海水腐蚀结构钢板带。用于石油井架、海港建筑、采油平台、船舶制造,也 用于化工、石油行业含硫化氢腐蚀性液体容器和铁路运输车辆的制造。 6)汽车制造用板钢系列。 7)集装箱用钢。专用于制造集装箱侧板、门板、顶板、底板、边框、立柱等构件。 8)管线用钢。石油天然气输送用管线,用于制造埋弧焊钢管以及直缝电焊钢管。 9)焊接气瓶及压力容器用钢。 用于制造液化气钢瓶及乙炔气钢瓶、较高工作温度 的压力容器及锅炉等。 10)造船用钢板。用于制造内河船体及上层建筑结构,远洋轮船上层建筑及隔舱 板。 11)矿用钢板。用于制造采矿用液压支架、矿用工程机械、矿用车斗、采用刮板 运输机,以及其他矿用机械耐磨结构件。 1.3题目来源 热轧板带钢轧机的发展已有80多年历史,汽车工业、建筑工业、交通运输业等的 发展,使得热轧及冷轧薄钢板的需求量不断增加 ,从而促使热轧板带钢轧机的建设获 得了迅速和稳定的发展。280万吨1780热轧带钢生产车间设计来源于市场需求。由于 当前的中国市场对高附加值产品的板带钢需求增加,尤其是汽车板带钢,船舶钢等 的需求增加,所以我选择了280万吨1780热电源变换器及4级计算机控制,并在国内首先采用了吊车跟踪系统。 在这个阶段国内还捆绑引进了3套薄板坯连铸连轧生产线,即1999年投产的珠钢 1500mm薄板坯生产线、 邯钢1900mm薄板坯生产线和2001年投产的包钢1750mm薄板 坯生产线。这些生产线采用第1代薄板坯连铸连轧技术,是当时世界最先进的薄板坯 生产线。其采用近终形连铸技术,使用漏斗形结晶器铸造50mm厚的薄板坯;并采用 了铸坯软压下,结晶器液压振动,隧道式加热炉。在轧机上采用高刚度轧机,新型 板形控制技术、液压AGC技术和新型除鳞技术等,从而使能耗、投资和生产成本降 低,生产流程大大缩短,产品质量提高。这些生产线的引进使我国拥有了新一代热 连轧带钢生产技术,也使我国目前成为世界上拥有薄板坯连铸连轧生产线最多的国 家;我国更多的大型钢铁企业,开始从只能生产普通低技术产品而转为向生产高层 次产品迈进,在技术上上了一个台阶。 第3阶段,这个阶段实际上是近1~2年开始的,是以提高效益、调整品种结构、 满足市场需要和提高企业竞争能力为目的的发展阶段。由于近年国家经济快速发展, 对钢材需求不断增加,因此除国营大中型企业外,中小型企业,甚至民营企业都把 生产宽带钢作为今后发展的重点,或引进或采用国产技术,或建设传统热连轧宽带 钢轧机或建设薄板坯连铸连轧生产线。这个阶段以鞍钢1700、2150mm(国产) , 唐 钢1780mm薄板坯和1700mm(国产) 、马钢1700mm薄板坯和2250mm、涟钢1700mm 薄板坯、莱钢1500mm(国产) 、本钢薄板坯、济钢1700mm(国产) 、新丰1700mm(国 产) 、宝钢1880mm、首钢2250mm、武钢2250mm、太钢2250mm轧机为代表。同时, 这个阶段对引进二手轧机和原技术较落后的国产轧机进行了全面技术改造,使其达 到了现代化水平。 这个阶段新建的传统带钢轧机,有以武钢2250mm轧机为代表的当代最先进的宽 带钢轧机,有以唐钢、马钢和涟钢为代表的新一代生产超薄带钢的薄板坯连铸连轧 机,有采用国产技术生产中等厚度薄板坯的连铸连轧生产线,还有一些炉卷轧机投 产和建设。现在建设和投产的所有轧机都具有现代化水平,如计算机 1、2级控制系 统、液压AGC系统、板形控制系统、交流传动、控轧控冷技术、热送热装技术等等。 国外刚出现的半无头轧制技术、铁素体加工技术、高强度冷却技术、新型卷取机等, 在一些轧机上也已应用。目前我国热连轧技术装备已完全摆脱落后状态,并已处于 世界先进水平之列[11]。 1.1.2发展趋势和特点 (1)热轧板带材短流程、高效率化。这方面的技术发展主要可分两个层次:① 常 规生产工艺的革新。为了大幅度简化工艺过程,缩短生产流程,充分利用冶金热能, 节约能源与金属等各项消耗,提高经济效益,不仅充分利用连铸板坯为原料,而且 不断开发和推广应用连铸板坯直接热装与直接轧制技术。② 薄板坯和薄带坯的连铸
热轧棒材车间工艺设计—本科毕业设计(论文)

热轧棒材车间工艺设计摘要本设计为热轧棒材车间工艺设计。
产品为Φ22的热轧不锈钢,主要钢种为1Cr13,优质碳素结构钢,低合金钢,产品质量执行国家标准。
根据成品规格选择尺寸为210mm×210mm×6000mm的连铸坯为原料,加热炉为三段步进梁式加热炉。
本设计采用全连续轧制生产工艺,全线共有轧机22架,其中粗轧机6架,中轧机6架,预精轧机6架,精轧4架。
终轧最大轧制速度为10m/s。
设计中采用的孔型系统为:箱(1#)—方箱(2#)—椭(3#)—圆(4#)—椭(5#)—圆(6#)—椭(7#)—圆(8#)—椭(9#)—圆(10#)—椭(11#)—圆(12#)—椭(13#)—圆(14#)—椭(15#)—圆(16#)—椭(17#)—圆(18#)—椭(19#)—圆(20#)—椭(21#)—圆(22#)。
关键词:工艺设计,热轧棒材,型钢,连铸坯Process Design of hot rolled bar WorkshopAbstractThis is the technology design for hot rolled bar workshop . The size of the product is Φ22 with the major steel grade of the stainless steel ,the carbon constructional quality steel or the low alloyed steel.And we carry out national standard during the production .According to the size of product we use the concast billets with the size of 210mm×210mm×6000mm for the raw material and the Walking Beam Heating Furnace . We use continuous rolling technology ,there is 22 mill in common ,6 for roughing mill ,6 for medium mill ,6 for beforehand finishing mill,6 for finishing mil . The largest end mill speed is about 10m/s .In the production of steel rolling we use the pass system of chest -square-ellipse-circle -ellipse-circle-ellipse-circle-ellipse-circle-ellipse-circle-ellipse-circle-ellipse-circle-ellipse-circle-ellipse-circle-ellipse-circle.Key words:process design,hot rolled ribbed bar,shape steel ,concast bil目录1 热轧棒材概述 (1)1.1 热轧棒材的产品概况 (1)1.2 1Cr13介绍 (3)1.2.1 1Cr13标准 (3)1.2.2 特性及适用范围 (3)1.2.3 1Cr13热处理工艺 (3)1.2.4 1Cr13特性 (4)1.2.5 1Cr13管材生产制造 (4)1.2.6 1Cr13、3Cr13用途 (4)2 典型产品轧制工艺制定 (5)2.1 生产工艺流程图 (5)2.2 坯料的选择 (5)2.3 坯料及成品尺寸 (6)2.4 坯料表面预处理 (7)2.4.1 表面缺陷清理 (7)2.4.2 表面氧化铁皮清除 (7)2.5 加热制度的制定 (8)2.5.1 加热目的 (8)2.5.2 加热温度 (8)2.5.3 加热速度 (9)2.5.4 加热时间 (9)3 主要设备参数 (10)3.1 步进梁式加热炉 (11)3.2 步进梁高压水除鳞设备 (11)3.3 粗轧机组 (12)3.4 中轧机组 (12)3.5 精轧机组 (12)3.6 剪切机 (13)3.7 两组水冷却箱 (13)3.8 850吨冷剪切机 (13)4 典型产品的工艺设计 (14)4.1 孔型及孔型设计的概念 (14)4.2 孔型设计的内容 (14)4.3 孔型设计的要求 (14)4.4 孔型设计的基本原则 (15)4.5 孔型系统分析与选择 (16)4.5.1 孔型系统的分析 (16)4.5.2 孔型系统的选择 (17)4.6 延伸系数的确定 (18)4.6.1 轧制道次的确定 (18)4.7 各孔型尺寸计算 (19)4.7.1 圆孔型系统的设计 (19)4.7.2 椭圆孔型系统的设计 (22)4.7.3 箱型孔孔型系统的设计 (25)4.8 连轧常数的计算 (27)5 力能参数计算 (29)5.1 各机组的温度制度 (29)5.2 轧制力及力矩的计算 (30)5.3 轧制力矩的计算 (35)6 设备能力校核 (37)6.1 咬入能力校核 (37)6.1.1 咬入条件 (37)6.1.2 咬入能力校核 (37)6.2 轧辊强度校核 (40)6.2.1 粗轧机组轧辊强度校核 (42)6.2.2 中轧机组轧辊强度校核 (44)6.3 电机能力校核 (45)6.3.1 轧制力矩 (45)6.3.2 附加摩擦力矩 (46)6.3.3 空转力矩: (46)6.3.4 电机能力校核 (47)7 环境保护及综合利用 (48)7.1 轧钢厂的环境保护 (48)7.2 节能和综合利用 (50)7.2.1 轧钢厂的节能 (50)7.2.2 轧钢厂的综合利用 (51)专题 (53)致谢 (87)参考文献 (88)附录1 (90)1 热轧棒材概述1.1 热轧棒材的产品概况近20年是我国型钢生产技术飞速发展的20年。
热轧带钢的生产方案和工艺处理步骤

热轧
160
53
Q275
1600)
12Mn2A, (2.5 ~ 5.0) ×
合金结构钢 16Mn2A (1400 ~
30Cr,40Cr 1600)
热轧
65
22
45Cr,45Mn
不锈钢
牌号
1Cr13, (2.0~6.0)×
0Cr18Ni9 (850~1700)
热轧
75
1Cr18Ni9
1Cr18Ni9Ti
2.1.2 编制产品方案的原则及方法
(1) 国民经济发展对产品的要求,既考虑当前的急需又要考虑将来发展的 需要。
(2) 产品的平衡,考虑全国各地的布局和配套加以平衡。 (3) 建厂地区的条件、生产资源、自然条件、投资等可能性。 (4) 考虑轧机生产能力的充分发挥,提高轧机的生产技术水平。
2.1.3 选择计算产品
钢板和钢带的表面允许有深度和高度不大于厚度公差之半的折印、麻点、划 伤、小拉痕、压痕以及氧化铁皮脱落所造成的表面粗糙等局部缺陷。对表面的薄 层氧化铁皮、轻微铁锈和残余涂料、活痕等不影响表面质量的局部缺陷亦允许存 在。
钢板和钢带表面的局部缺陷,允许用修磨方法清除,但清除深度不得大于钢 板和钢带厚度公差之半。
3.2.1板坯的选择和轧前准备
热轧带钢生产所用的板坯主要是连铸板坯,只有少量尚存初轧机冶金工厂采
年产280万吨炼钢生铁的炼铁车间设计
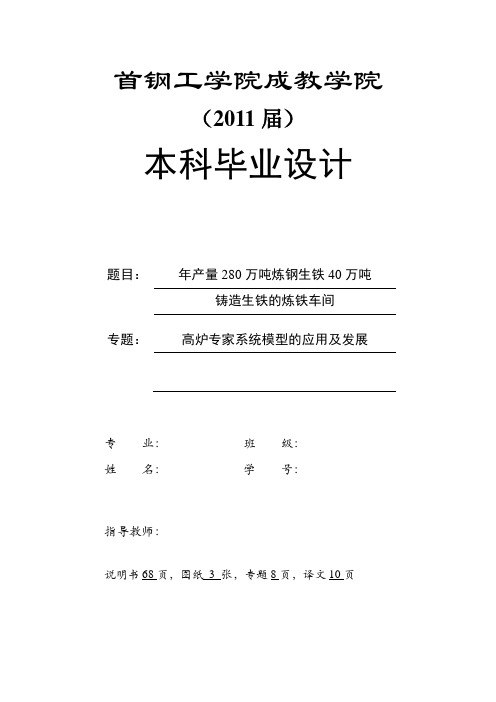
首钢工学院成教学院(2011届)本科毕业设计题目:年产量280万吨炼钢生铁40万吨铸造生铁的炼铁车间专题:高炉专家系统模型的应用及发展专业:班级:姓名:学号:指导教师:说明书68页,图纸3 张,专题8页,译文10页年产量280万吨炼钢生铁40万吨铸造生铁的炼铁车间摘要本设计是设计年产280万吨炼钢生铁,40万吨铸造生铁的高炉炼铁车间。
在设计中采用了2022m3的高炉2座,不设渣口,2个出铁口,采用矩形出铁场。
送风系统采用四座新日铁式外燃式热风炉,煤气处理系统采用重力除尘器、文氏管和电除尘。
渣铁处理系统采用拉萨法水淬渣(RASA)处理,特殊情况采用干渣生产,上料系统采用皮带上料机,保证高炉的不间断供料。
在设计中,首先做了物料平衡、热平衡,炉型的设计与计算,以及设备的选择;设计中应用了许多先进的工艺,这些工艺在实行大喷煤技术提高传热效率,节能,提高生产率方面起了重要的作用。
在设计中,广泛吸收前人技术革新和国内外科学研究成果。
根据实际需要及可能性,尽量采用先进设备、结构、材料及新工艺。
做到技术上先进,经济上合理,又减少环境污染。
车间总体布置形式为半岛式。
关键词:高炉,物料平衡,热平衡,半岛式Design of an ironmaking workshop with annual output of 2.8 million tons of steelmaking iron and 0.4 million tons ofCasting ironAbstractThe assignment is the design of the 2.8 million tons annual production capacity of steel-making pig iron, 0.4million of blast furnace cast pig iron workshop. I design two 1800 m3 blast furnaces,and set up two tap holes with no slag hole,which use rectangular field of iron. Blast system 4 Nippon external combustion hot stoves,Dust catcher system uses gravity precipitators, venturi tube and electrostatic precipitator. The methods of slag iron processing system use water quenching residue Lhasa (RASA), special circumstances use dry slag productions to deal with. The charging system is using belt feeding machine to ensuring uninterrupting charging of blast furnace. In the design,first of all, calculating the material balance, heat balance, and the furnace structure, as well as the choice of equipment; the design of the application of a number of advanced technology, these processes in the implementation of large pulverized coal injection technology to enhance heat transfer efficiency,to save energy ,to improve productivity ,which played an important role. The design has broadly absorpted technological innovations and the results of scientific research at home and abroad. According to the actual needs and possibilities use advanced equipment as far as possible,advanced structure,advanced materials and so on. Achieve technically advanced and economically rational,and reduce environmental pollution. The form of workshop with the overall layout is peninsula.Key words:blast furnace, material balance, eheat balance, peninsula目录绪论...................................................................................... 错误!未定义书签。
热轧带钢的生产方案和工艺流程
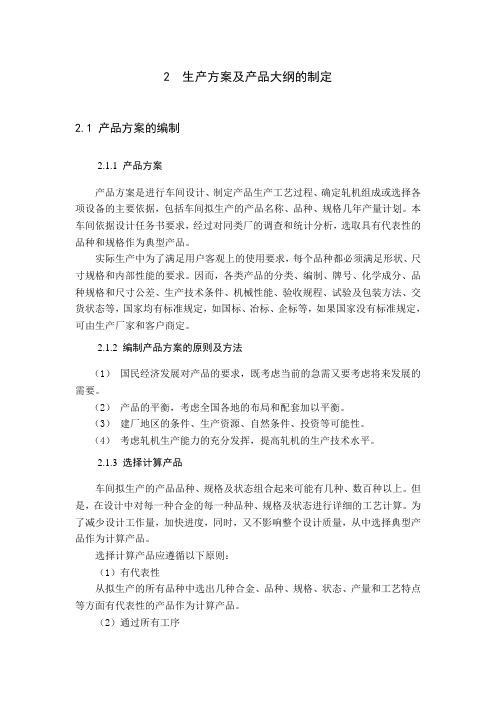
2 生产方案及产品大纲的制定2.1 产品方案的编制2.1.1 产品方案产品方案是进行车间设计、制定产品生产工艺过程、确定轧机组成或选择各项设备的主要依据,包括车间拟生产的产品名称、品种、规格几年产量计划。
本车间依据设计任务书要求,经过对同类厂的调查和统计分析,选取具有代表性的品种和规格作为典型产品。
实际生产中为了满足用户客观上的使用要求,每个品种都必须满足形状、尺寸规格和内部性能的要求。
因而,各类产品的分类、编制、牌号、化学成分、品种规格和尺寸公差、生产技术条件、机械性能、验收规程、试验及包装方法、交货状态等,国家均有标准规定,如国标、冶标、企标等,如果国家没有标准规定,可由生产厂家和客户商定。
2.1.2 编制产品方案的原则及方法(1)国民经济发展对产品的要求,既考虑当前的急需又要考虑将来发展的需要。
(2)产品的平衡,考虑全国各地的布局和配套加以平衡。
(3)建厂地区的条件、生产资源、自然条件、投资等可能性。
(4)考虑轧机生产能力的充分发挥,提高轧机的生产技术水平。
2.1.3 选择计算产品车间拟生产的产品品种、规格及状态组合起来可能有几种、数百种以上。
但是,在设计中对每一种合金的每一种品种、规格及状态进行详细的工艺计算。
为了减少设计工作量,加快进度,同时,又不影响整个设计质量,从中选择典型产品作为计算产品。
选择计算产品应遵循以下原则:(1)有代表性从拟生产的所有品种中选出几种合金、品种、规格、状态、产量和工艺特点等方面有代表性的产品作为计算产品。
(2)通过所有工序所选的所有计算产品要通过各工序,但不是说第一种计算产品都通过各工序,而是所有计算产品综合起来看的。
(3)所选的计算产品要与接近。
(4)计算产品要留一定的调整余量,也就是说所选的计算产品要品种灵活,容易生产多种规格的产品。
本次设计选用的三个典型产品分别是:Q215(10.0mm×1600mm)、30Cr(4.0mm ×1400mm)、1Cr18Ni9(2.0mm×1000mm)。
热轧带钢生产线及设备的设计论文

热轧带钢生产线及设备的设计论文引言热轧带钢是一种重要的金属材料,在工业生产和建筑行业中得到广泛应用。
它具有优良的机械性能和成型性能,能够满足各种工程的需求。
为了满足市场对热轧带钢的需求,热轧带钢生产线及设备的设计变得至关重要。
本论文旨在研究和探讨热轧带钢生产线及设备的设计原理和方法。
热轧带钢生产线的设计原则热轧带钢生产线的设计需要遵循一定的原则,以确保生产线的稳定运行和高效生产。
以下是热轧带钢生产线设计的一些原则:1. 按需生产热轧带钢生产线应根据市场需求和订单量进行生产调度。
生产线的设计应能够快速调整生产规模和生产速度,以满足市场的需求变化。
2. 自动化程度高热轧带钢生产线的自动化程度对生产效率和产品质量有着重要影响。
因此,在设计热轧带钢生产线时,应尽可能采用先进的自动化设备和控制系统,以提高生产效率和降低人工操作错误。
3. 设备可靠性高热轧带钢生产线的设备需要具备高可靠性和稳定性,以确保生产过程的连续性和稳定性。
在设备的选择和调试过程中,应注重设备的品质和性能,以避免设备故障和停机时间的影响。
4. 节能减排热轧带钢生产过程中会产生大量的能耗和废气废水。
为了减少对环境的影响,热轧带钢生产线的设计应注重节能和减排,采用先进的能源回收和废气处理设备。
热轧带钢生产设备的设计要点在设计热轧带钢生产设备时,需要考虑以下几个关键要点:1. 轧机的选择轧机是热轧带钢生产线中最核心的设备,对产品的质量和尺寸精度有着重要影响。
在选择轧机时,应考虑轧机的型号、参数和性能指标,以确保其能够满足生产线的需求。
2. 辊道系统的设计辊道系统是热轧带钢生产线中用于输送钢坯和成品钢带的重要设备。
辊道系统的设计应考虑到输送带钢的平稳性、减小辊道磨损和节约能源。
设计时应合理布局辊道,采用合适的辊道材料,并考虑辊道的维护和保养。
3. 冷却系统的设计热轧带钢在轧机上经过高温轧制后需要进行快速冷却,以提高产品的硬度和强度。
冷却系统的设计应能够提供适当的冷却速度和冷却剂,以满足产品的冷却要求。
250万吨热轧带钢生产线设计-正文
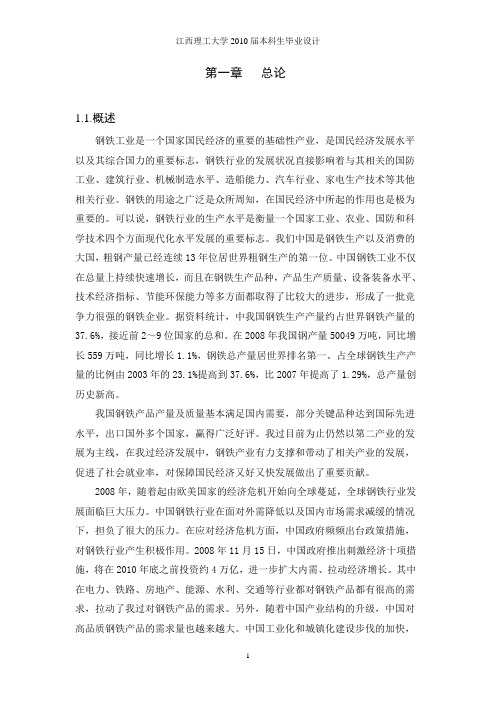
第一章总论1.1.概述钢铁工业是一个国家国民经济的重要的基础性产业,是国民经济发展水平以及其综合国力的重要标志,钢铁行业的发展状况直接影响着与其相关的国防工业、建筑行业、机械制造水平、造船能力、汽车行业、家电生产技术等其他相关行业。
钢铁的用途之广泛是众所周知,在国民经济中所起的作用也是极为重要的。
可以说,钢铁行业的生产水平是衡量一个国家工业、农业、国防和科学技术四个方面现代化水平发展的重要标志。
我们中国是钢铁生产以及消费的大国,粗钢产量已经连续13年位居世界粗钢生产的第一位。
中国钢铁工业不仅在总量上持续快速增长,而且在钢铁生产品种,产品生产质量、设备装备水平、技术经济指标、节能环保能力等多方面都取得了比较大的进步,形成了一批竞争力很强的钢铁企业。
据资料统计,中我国钢铁生产产量约占世界钢铁产量的37.6%,接近前2~9位国家的总和。
在2008年我国钢产量50049万吨,同比增长559万吨,同比增长1.1%,钢铁总产量居世界排名第一。
占全球钢铁生产产量的比例由2003年的23.1%提高到37.6%,比2007年提高了1.29%,总产量创历史新高。
我国钢铁产品产量及质量基本满足国内需要,部分关键品种达到国际先进水平,出口国外多个国家,赢得广泛好评。
我过目前为止仍然以第二产业的发展为主线,在我过经济发展中,钢铁产业有力支撑和带动了相关产业的发展,促进了社会就业率,对保障国民经济又好又快发展做出了重要贡献。
2008年,随着起由欧美国家的经济危机开始向全球蔓延,全球钢铁行业发展面临巨大压力。
中国钢铁行业在面对外需降低以及国内市场需求减缓的情况下,担负了很大的压力。
在应对经济危机方面,中国政府频频出台政策措施,对钢铁行业产生积极作用。
2008年11月15日,中国政府推出刺激经济十项措施,将在2010年底之前投资约4万亿,进一步扩大内需、拉动经济增长。
其中在电力、铁路、房地产、能源、水利、交通等行业都对钢铁产品都有很高的需求,拉动了我过对钢铁产品的需求。
- 1、下载文档前请自行甄别文档内容的完整性,平台不提供额外的编辑、内容补充、找答案等附加服务。
- 2、"仅部分预览"的文档,不可在线预览部分如存在完整性等问题,可反馈申请退款(可完整预览的文档不适用该条件!)。
- 3、如文档侵犯您的权益,请联系客服反馈,我们会尽快为您处理(人工客服工作时间:9:00-18:30)。
学号:200906040106HEBEI UNITED UNIVERSITY毕业设计摘要译文T RANSLATION O F G RANDUATE T HESIS’S A BSTRACT设计题目:年产280万吨1780热轧带钢车间设计学生姓名:张志芳专业班级:09成型1班学院:冶金与能源学院指导教师:杨海丽教授2013年05月28日摘要板带材生产技术水平不仅是冶金工业生产发展水平的重要标志,也反映了一个国家工业与科学技术发展的水平。
建设现代化的热轧宽带钢轧机要满足现代工业对热轧板品种质量的要求。
最终产品的质量取决于连铸坯的质量,传统厚度的板坯连铸工艺明显优于薄板坯连铸工艺。
薄板坯连铸连轧更适于生产中低档板材品种,在薄规格产品生产方面具有明显优势。
为了满足高质量和高性能板材要求,采用厚板坯常规连轧生产方式更合理。
本设计为年产280万吨1780热轧带钢车间设计,典型产品厚度为3.0mm。
为了满足高质量和高性能板材要求,本次设计结合唐钢1700mm、宁钢1780mm、鞍钢1780mm热轧车间设计了年产280万吨的1780mm常规热轧车间。
设计采用两架四辊可逆粗轧机,轧制六道次,精轧机选用六架非可逆轧机轧制六道次,通过采用CVC轧机、PC轧机和厚度自动控制(AGC)等技术相结合来控制板型和厚度,在精轧前采用无芯轴隔热屏热卷箱。
本设计粗轧机组选用两架独立的可逆轧机,两架带立棍的强力四辊可逆轧机,共完成6个道次粗轧,不但解决了粗轧轧制时间过长、与精轧机不匹配的问题,还能保证中间坯厚度及凸度的稳定性。
精轧选用6机架连轧,前四架采用板型控制良好的CVC技术。
全线采用许多新技术来保证稳定生产。
产品在质量、精度等各方面居于先进水平。
热轧板带机轧制连铸坯,生产厚度为1.5~12.0mm的带钢。
板坯在加热炉中加热到1200℃左右,由两架粗轧机将板坯轧到30mm左右。
粗轧后,由飞剪切头,进入精轧。
带钢经过由六架组成的精轧机组轧制。
然后,再经过层流冷却进行冷却,最后由地下卷取机卷取。
最终产品可经过冷轧进行再加工。
轧制前先除鳞,除鳞的方法有多种,而现代工厂只采用投资很少的高压水除鳞箱及轧机前后的高压水喷头即可满足除鳞要求,其水压过去为12MPa左右,嫌低,现已采用15~25MPa以上,合金钢则需更高的水压值。
考虑到缩短车间长度和粗轧时奥氏体回复再结晶程度以适应给冷轧薄板供坯的工艺需求,本次设计采用了两架独立的粗轧机,板坯在粗轧机上共轧制六道次,如果板坯厚度小,粗轧还可以分配空轧道次,同样可达到节能效果。
根据产品大纲要求,生产薄规格为6.0~15.0mm带钢要占40%以上,为提高精轧入口温度,减少中间坯头尾温差,提高终轧温度(绝大部分要在850℃以上),保证带钢应有的质量、内部组织性能,粗、精轧间采用保温设施是必要的。
热卷取箱保温效果较好,一次性设备投资虽高一些,但技术成熟,设备运转可靠,生产、维护费用较低,所以本设计选用它。
精轧机组的布置为六机架连轧。
带坯在进入精轧机之前,首先要进行测温、测厚并接着用飞剪切去头部和尾部。
切头的目的是为了除去温度过低的头部以免损伤辊面,并防止“舌头”、“鱼尾”卡在机架间的导卫装置或辊道缝隙中。
有时还要把轧件的后端切去,以防后端的“鱼尾”或“舌头”给卷取及其后的精整工序带来困难。
现代的切头飞剪机一般装置有两对刀刃,一对为弧形刀,用以切头,这有利于减小轧机咬人时的冲击负荷也有利于咬钢和减小剪切力。
飞剪设备主要用于切头、切尾、事故剪断及成品倍尺剪切,它在消除开花头子、减少头尾翘皮、倍尺优化和事故剪断等方面有着十分重要的作用。
由于飞剪是在轧件运行中进行剪切的,这就必须满足剪刃在水平方向上的分速度与轧件的运动速度同步的要求。
生产线上共设两处剪,即精轧入口与卷曲机前面,由于剪切过程是在轧件运动的同时完成的,故均选择飞剪。
活套对产品的质量起到了积极的作用。
通过活套可以调节带钢速度来保证稳定轧制。
例如,若张力较低,增加活套角,增大张力,使轧制稳定。
若张力较大,减小活套角,减小张力。
更全面的说,为了减小张力波动,活套角应保持在一定的角度。
为了在非稳定轧制时调节大的速度波动,活套角需有一个比较大的变化范围。
为了保证热轧中带钢的质量和速度,可以采用同时控制活套角和张力的方法。
在传统方式中,通过改变电机的速度来控制活套角,但没有张力反馈控制,这是因为在机架内部安装和固定张力测量装置有一定的困难。
传统的PI控制就是依据这种原理,这种控制在工业中曾被广泛应用。
为了满足产品大纲的所有产品的力学性能,机械性能和金属组织,终轧后选择层流冷却方式对带钢进行冷却,层流冷却采用恒定压力的低压水进行冷却,形成柱状水流,而且有比喷射多的动能冲击在板面上,击破板面的蒸气膜,形成核沸腾,整个冷却段大约27米,分为6段控制,其中最后1段可以实现水量微调控制以满足卷取温度误差控制,冷却水量6000立方米每小时,为了方便维修,上面的喷水横梁设计成为液压缸驱动的可以开闭式。
层流冷却系统的设计适用于全厚度范围,每一段的压力是通过调节喷水横梁上面的开口度来控制的,同时保持高水位水箱的水在一定的范围内测喷设备,通过向带钢的表面积喷射水压约为10千克力每毫米的水来吹走钢表面的冷却水,其目的是防止带钢冷却温度的弥散,它安装在精轧机核每段冷却段的后面,高压喷水由气动控制阀门来打开或者关闭。
地下式卷取机布置在热连轧机输出辊道。
由于它位于辊道标高之下,所以被成为地下式卷取机。
在整个连轧机组中,卷取机的工作条件最为恶劣,也是最易出故障的环节之一。
为了保持连轧机组的生产节奏,本设计采用两台卷取机,两台交替使用。
另外该设计附有车间平面布置图,以供参考。
关键词:半连轧工艺;步进式加热炉;热卷箱;液压AGC系统AbstractThe hot strip production technique level is not only a important marking of the metallurgy industry produce development level, but also reflects a level of the national industry and science technique.The new modern hot wide rolling mills should satisfy the request of modern industry to hot strip species quality.The quality of end product is by all means decided by quality of continuous casting slab. The continuous casting slab of traditional thickness is obviously better than thin slab continuous casting and rolling. Thin slab continuous casting and rolling is suitable to produce medium low file time plank material species and have obvious advantage at the thin specification product.For satisfying the request of obtaining the high quality and high performance strip, thick slab continuous casting produce method is considered more reasonable.The 1780 is designed to produce 2.8 million tons of hot rolled strip plant design, a typical product thickness3.0mm. To meet the requirements of high quality and high performance boards, this design combines the Tangshan Iron and Steel 1700mm, Ning steel 1780mm, Anshan Iron and Steel 1780mm hot rolling workshop designed annual output of 2.8 million tons of 1780mm conventional hot rolling workshop. Design uses two four-high reversing roughing mill, rolling six times, finishing mill selected six non-reversible rolling mill six times, through the use of CVC mill, PC mill and thickness control (AGC) to control panels and other technology-based combination and thickness, in the no-mandrel before finishing the heat shield coil box.In the design, the rough mills use one two-high un-reversible mill and one four-high reversible strong mill with vertical roll completing 6 pass rough.It not only solves the problem that the time of the rough rolling is too long and the Finishing mill does not match with rough mill , but also ensures stability of the middle billet thickness and the crown. The 6 stands continuous rolling is used in the finishing mill, the former three stand using good crown control of the CVC technology. All adopts many new technologies to ensure stable production. In quality, precision, and other aspects, the production occupied the advanced level.Hot rolling plate and strip rolling continuous casting machine, the production of 1.5~12.0mm thickness of the strip. Slab in the furnace heated to 1200 ℃ in about two rough slab rolling mill will be around to30mm. After roughing, the first cut by flying into the mill. After strip by six or seven units, composed of rolling mill. Then, another strip laminar cooling for cooling, and finally by the underground coiler coiler. After the final product can be re-processing of cold-rolled.Descaling before rolling, in addition to scale a number of means, practice shows that investment in modern factories using only a few high-pressure water descaling boxes and rolling mill before and after the high-pressure water descaling nozzles can meet the requirements of 12MPa pressure for about the past, too low, which has been adopted by more than 15 ~ 25MPa, alloy steel pressure value should be higher.Shorten the workshop, taking into account the length and rough rolling back when the austenite recrystallization in order to adapt to the degree of cold-rolled sheet for the demand for green technology, this design uses two independent roughing mill, slab in the rough rolling mill on the total six times that if the slab thickness of small, rough rolling mill can also pass the allocation of space, the same energy saving effect can be achieved.Outline based on product requirements, specifications for the production of thin strip to be 6.0 ~ 16.0mm accounted for more than 40%, to improve the finishing inlet temperature to reduce the temperature difference between the middle of billet head, raise the finishing temperature (the vast majority to more than 850 ℃), strip to ensure proper quality, the internal organization of performance, rough, finishing facilities between the use of thermal insulation is necessary. Hot-coiling me without heat, better insulation, although the high one-time investment in equipment, but the technology is mature, reliable equipment operation, production, lower maintenance costs, so the selection of its design.Finishing the layout of units to six rolling rack. With billet before entering the finishing mill, first of all to carry out temperature measurement, thickness measurement and then used to fly to the head and tail cut. The purpose of the first cut is to remove the head temperature is too low so as not to damage the roller surface, and to prevent the "tongue", "fish" cards in the rack between the guide roller device or gap in the. Sometimes rolled piece to the back-end truncated in order to prevent the back-end of the "fish tail" or "tongue" to the take-up and finishing the process difficult. First of all modern flying shear devices generally have two pairs of blades, one for the arc-shaped knife, to cut first, which is conducive to reduce the impact of mill load when bites will also help reduce the bite of steel and shear stress.Flying shear equipment used mainly for cutting head, cut tail, cut and finished the accident-foot shear times, the elimination of its flowering head, head and tail to reduce the outstanding skin, fold-foot cut, such as optimization and accidents have a very important role. As the flying shear is a rolled piece cut operation, which must meet the cut edge in the horizontal direction at the speed of the rolling velocity of synchronization requirements.A total of two lines cut, that is, finishing in front of the entrance and curl machine, as a result of shear in the rolling process is completed at the same time movement, it had opted for flying shear.Live sets of the quality of products has played an active role. Through the looper can be adjusted to ensure the stability of strip undulating speed. For example, if a lower tension and increase looper angle, increasing tension, so that the stability of rolling. If the tension, reducing the looper angle, reducing the tension. That a more comprehensive, in order to reduce the tension fluctuations looper angle should bemaintained at a certain angle. In order to regulate non-steady rolling speed of large fluctuations in looper angle to be have a relatively large range.Hot-rolled strip in order to ensure the quality and speed, can be used at the same time control of looper angle and tension of the method. In the traditional way, by changing the motor speed to control the looper angle, but there is no tension feedback control, which is installed in the rack and fixed internal tension measuring devices have certain difficulties. Traditional PI control is based on this principle, such control has been widely used in industry.Products to meet the outline of the mechanical properties of all the products, mechanical properties and metal organizations, after finishing options laminar flow cooling method for cooling of the strip, using a constant laminar cooling of the low pressure cooling water to form a cylindrical flow, but also than the kinetic energy of the impact of multijet in the plate surface, break up the steam plate membrane surface to form a nuclear boiling, the entire cooling section of about 27 meters, is divided into 6 control, which can last 1 to fine-tune control of water to meet the needs of coiling temperature error control, cooling water, 6,000 cubic meters per hour, in order to facilitate maintenance, the water above the beams designed to be driven by hydraulic cylinder-type.Laminar flow cooling system design applied to the entire thickness of the scope of each paragraph by regulating the water pressure is above the beams to control the degree of opening, while maintaining the high level of the water tank of the scope of a certain inner spray equipment, through to the strip injection pressure of the surface area of about 10 kg/mm of water each to get rid of steel cooling water, and its purpose is to prevent the diffusion strip cooling temperature, it installed in the finishing mill nuclear paragraph after each cooling, high pressure water jet by the pneumatic control valve to open or close down.Underground coiler arranged in the hot rolling mill roller output. Because of its elevation is located under the roller, it was becoming coiler Underground. Rolling in the whole unit, coiler worst working conditions, but also the most vulnerable segments of one of the fault. Rolling Mills in order to maintain the pace of production, the design uses two coiler, the two used interchangeably.In addition to the workshop with a graphic design layout for reference.Key words:semi-continuous hot rolling process, stepping furnace, hot coil box,automatic gauge control。