土木工程毕业设计中英文翻译
土木工程毕业设计外文翻译原文+翻译

The bridge crack produced the reason to simply analyseIn recent years, the traffic capital construction of our province gets swift and violent development, all parts have built a large number of concrete bridges. In the course of building and using in the bridge, relevant to influence project quality lead of common occurrence report that bridge collapse even because the crack appears The concrete can be said to " often have illness coming on " while fracturing and " frequently-occurring disease ", often perplex bridge engineers and technicians. In fact , if take certain design and construction measure, a lot of cracks can be overcome and controlled. For strengthen understanding of concrete bridge crack further, is it prevent project from endanger larger crack to try one's best, this text make an more overall analysis , summary to concrete kind and reason of production , bridge of crack as much as possible, in order to design , construct and find out the feasible method which control the crack , get the result of taking precautions against Yu WeiRan.Concrete bridge crack kind, origin cause of formation In fact, the origin cause of formation of the concrete structure crack is complicated and various, even many kinds of factors influence each other , but every crack has its one or several kinds of main reasons produced . The kind of the concrete bridge crack, on its reason to produce, can roughly divide several kinds as follows :(1) load the crack caused Concrete in routine quiet .Is it load to move and crack that produce claim to load the crack under the times of stress bridge, summing up has direct stress cracks , two kinds stress crack onces mainly. Direct stress crack refer to outside load direct crack that stress produce that cause. The reason why the crack produces is as follows, 1, Design the stage of calculating , does not calculate or leaks and calculates partly while calculating in structure; Calculate the model is unreasonable; The structure is supposed and accorded with by strength actually by strength ; Load and calculate or leak and calculate few; Internal force and matching the mistake in computation of muscle; Safety coefficient of structure is not enough. Do not consider the possibility that construct at the time of the structural design; It is insufficientto design the section; It is simply little and assigning the mistake for reinforcing bar to set up; Structure rigidity is insufficient; Construct and deal with improperly; The design drawing can not be explained clearly etc.. 2, Construction stage, does not pile up and construct the machines , material limiting ; Is it prefabricate structure structure receive strength characteristic , stand up , is it hang , transport , install to get up at will to understand; Construct not according to the design drawing, alter the construction order of the structure without authorization , change the structure and receive the strength mode; Do not do the tired intensity checking computations under machine vibration and wait to the structure . 3, Using stage, the heavy-duty vehicle which goes beyond the design load passes the bridge; Receive the contact , striking of the vehicle , shipping; Strong wind , heavy snow , earthquake happen , explode etc.. Stress crack once means the stress of secondary caused by loading outside produces the crack. The reason why the crack produces is as follows, 1, In design outside load function , because actual working state and routine , structure of thing calculate have discrepancy or is it consider to calculate, thus cause stress once to cause the structure to fracture in some position. Two is it join bridge arch foot is it is it assign " X " shape reinforcing bar , cut down this place way , section of size design and cut with scissors at the same time to adopt often to design to cut with scissors, theory calculate place this can store curved square in , but reality should is it can resist curved still to cut with scissors, so that present the crack and cause the reinforcing bar corrosion. 2, Bridge structure is it dig trough , turn on hole , set up ox leg ,etc. to need often, difficult to use a accurate one diagrammatic to is it is it calculate to imitate to go on in calculating in routine, set up and receive the strength reinforcing bar in general foundation experience. Studies have shown , after being dug the hole by the strength component , it will produce the diffraction phenomenon that strength flows, intensive near the hole in a utensil, produced the enormous stress to concentrate. In long to step prestressing force of the continuous roof beam , often block the steel bunch according to the needs of section internal force in stepping, set up the anchor head, but can often see the crack in the anchor firm section adjacent place. So if deal with improper, in corner or component form sudden change office , block place to be easy to appear crack strengthreinforcing bar of structure the. In the actual project, stress crack once produced the most common reason which loads the crack. Stress crack once belong to one more piece of nature of drawing , splitting off , shearing. Stress crack once is loaded and caused, only seldom calculate according to the routine too, but with modern to calculate constant perfection of means, times of stress crack to can accomplish reasonable checking computations too. For example to such stresses 2 times of producing as prestressing force , creeping ,etc., department's finite element procedure calculates levels pole correctly now, but more difficult 40 years ago. In the design, should pay attention to avoiding structure sudden change (or section sudden change), when it is unable to avoid , should do part deal with , corner for instance, make round horn , sudden change office make into the gradation zone transition, is it is it mix muscle to construct to strengthen at the same time, corner mix again oblique to reinforcing bar , as to large hole in a utensil can set up protecting in the perimeter at the terms of having angle steel. Load the crack characteristic in accordance with loading differently and presenting different characteristics differently. The crack appear person who draw more, the cutting area or the serious position of vibration. Must point out , is it get up cover or have along keep into short crack of direction to appear person who press, often the structure reaches the sign of bearing the weight of strength limit, it is an omen that the structure is destroyed, its reason is often that sectional size is partial and small. Receive the strength way differently according to the structure, the crack characteristic produced is as follows: 1, The centre is drawn. The crack runs through the component cross section , the interval is equal on the whole , and is perpendicular to receiving the strength direction. While adopting the whorl reinforcing bar , lie in the second-class crack near the reinforcing bar between the cracks. 2, The centre is pressed. It is parallel on the short and dense parallel crack which receive the strength direction to appear along the component. 3, Receive curved. Most near the large section from border is it appear and draw into direction vertical crack to begin person who draw curved square, and develop toward neutralization axle gradually. While adopting the whorl reinforcing bar , can see shorter second-class crack among the cracks. When the structure matches muscles less, there are few but wide cracks, fragility destruction may take place in thestructure 4, Pressed big and partial. Heavy to press and mix person who draw muscle a less one light to pigeonhole into the component while being partial while being partial, similar to receiving the curved component. 5, Pressed small and partial. Small to press and mix person who draw muscle a more one heavy to pigeonhole into the component while being partial while being partial, similar to the centre and pressed the component. 6, Cut. Press obliquly when the hoop muscle is too dense and destroy, the oblique crack which is greater than 45?? direction appears along the belly of roof beam end; Is it is it is it destroy to press to cut to happen when the hoop muscle is proper, underpart is it invite 45?? direction parallel oblique crack each other to appear along roof beam end. 7, Sprained. Component one side belly appear many direction oblique crack, 45?? of treaty, first, and to launch with spiral direction being adjoint. 8, Washed and cut. 4 side is it invite 45?? direction inclined plane draw and split to take place along column cap board, form the tangent plane of washing. 9, Some and is pressed. Some to appear person who press direction roughly parallel large short cracks with pressure.(2) crack caused in temperature changeThe concrete has nature of expanding with heat and contract with cold, look on as the external environment condition or the structure temperature changes, concrete take place out of shape, if out of shape to restrain from, produce the stress in the structure, produce the temperature crack promptly when exceeding concrete tensile strength in stress. In some being heavy to step foot-path among the bridge , temperature stress can is it go beyond living year stress even to reach. The temperature crack distinguishes the main characteristic of other cracks will be varied with temperature and expanded or closed up. The main factor is as follows, to cause temperature and change 1, Annual difference in temperature. Temperature is changing constantly in four seasons in one year, but change relatively slowly, the impact on structure of the bridge is mainly the vertical displacement which causes the bridge, can prop up seat move or set up flexible mound ,etc. not to construct measure coordinate , through bridge floor expansion joint generally, can cause temperature crack only when the displacement of the structure is limited, for example arched bridge , just bridge etc. The annual difference in temperature of our country generally changes therange with the conduct of the average temperature in the moon of January and July. Considering the creep characteristic of the concrete, the elastic mould amount of concrete should be considered rolling over and reducing when the internal force of the annual difference in temperature is calculated. 2, Rizhao. After being tanned by the sun by the sun to the side of bridge panel , the girder or the pier, temperature is obviously higher than other position, the temperature gradient is presented and distributed by the line shape . Because of restrain oneself function, cause part draw stress to be relatively heavy, the crack appears. Rizhao and following to is it cause structure common reason most , temperature of crack to lower the temperature suddenly 3, Lower the temperature suddenly. Fall heavy rain , cold air attack , sunset ,etc. can cause structure surface temperature suddenly dropped suddenly, but because inside temperature change relatively slow producing temperature gradient. Rizhao and lower the temperature internal force can adopt design specification or consult real bridge materials go on when calculating suddenly, concrete elastic mould amount does not consider converting into and reducing 4, Heat of hydration. Appear in the course of constructing, the large volume concrete (thickness exceeds 2. 0), after building because cement water send out heat, cause inside very much high temperature, the internal and external difference in temperature is too large, cause the surface to appear in the crack. Should according to actual conditions in constructing, is it choose heat of hydration low cement variety to try one's best, limit cement unit's consumption, reduce the aggregate and enter the temperature of the mould , reduce the internal and external difference in temperature, and lower the temperature slowly , can adopt the circulation cooling system to carry on the inside to dispel the heat in case of necessity, or adopt the thin layer and build it in succession in order to accelerate dispelling the heat. 5, The construction measure is improper at the time of steam maintenance or the winter construction , the concrete is sudden and cold and sudden and hot, internal and external temperature is uneven , apt to appear in the crack. 6, Prefabricate T roof beam horizontal baffle when the installation , prop up seat bury stencil plate with transfer flat stencil plate when welding in advance, if weld measure to be improper, iron pieces of nearby concrete easy to is it fracture to burn. Adopt electric heat piece draw law piece draw prestressing force at the component ,prestressing force steel temperature can rise to 350 degrees Centigrade , the concrete component is apt to fracture. Experimental study indicates , are caused the intensity of concrete that the high temperature burns to obviously reduce with rising of temperature by such reasons as the fire ,etc., glueing forming the decline thereupon of strength of reinforcing bar and concrete, tensile strength drop by 50% after concrete temperature reaches 300 degrees Centigrade, compression strength drops by 60%, glueing the strength of forming to drop by 80% of only round reinforcing bar and concrete; Because heat, concrete body dissociate ink evaporate and can produce and shrink sharply in a large amount(3) shrink the crack causedIn the actual project, it is the most common because concrete shrinks the crack caused. Shrink kind in concrete, plasticity shrink is it it shrinks (is it contract to do ) to be the main reason that the volume of concrete out of shape happens to shrink, shrink spontaneously in addition and the char shrink. Plasticity shrink. About 4 hours after it is built that in the course of constructing , concrete happens, the cement water response is fierce at this moment, the strand takes shape gradually, secrete water and moisture to evaporate sharply, the concrete desiccates and shrinks, it is at the same time conduct oneself with dignity not sinking because aggregate,so when harden concrete yet,it call plasticity shrink. The plasticity shrink producing amount grade is very big, can be up to about 1%. If stopped by the reinforcing bar while the aggregate sinks, form the crack along the reinforcing bar direction. If web , roof beam of T and roof beam of case and carry baseplate hand over office in component vertical to become sectional place, because sink too really to superficial obeying the web direction crack will happen evenly before hardenning. For reducing concrete plasticity shrink,it should control by water dust when being construct than,last long-time mixing, unloading should not too quick, is it is it take closely knit to smash to shake, vertical to become sectional place should divide layer build. Shrink and shrink (do and contract). After the concrete is formed hard , as the top layer moisture is evaporated progressively , the humidity is reduced progressively , the volume of concrete is reduced, is called and shrunk to shrink (do and contract). Because concrete top layermoisture loss soon, it is slow for inside to lose, produce surface shrink heavy , inside shrink a light one even to shrink, it is out of shape to restrain from by the inside concrete for surface to shrink, cause the surface concrete to bear pulling force, when the surface concrete bears pulling force to exceed its tensile strength, produce and shrink the crack. The concrete hardens after-contraction to just shrink and shrink mainly .Such as mix muscle rate heavy component (exceed 3% ), between reinforcing bar and more obvious restraints relatively that concrete shrink, the concrete surface is apt to appear in the full of cracks crackle. Shrink spontaneously. Spontaneous to it shrinks to be concrete in the course of hardenning , cement and water take place ink react, the shrink with have nothing to do by external humidity, and can positive (whether shrink, such as ordinary portland cement concrete), can negative too (whether expand, such as concrete, concrete of slag cement and cement of fly ash). The char shrinks. Between carbon dioxide and hyrate of cement of atmosphere take place out of shape shrink that chemical reaction cause. The char shrinks and could happen only about 50% of humidity, and accelerate with increase of the density of the carbon dioxide. The char shrinks and seldom calculates . The characteristic that the concrete shrinks the crack is that the majority belongs to the surface crack, the crack is relatively detailed in width , and criss-cross, become the full of cracks form , the form does not have any law . Studies have shown , influence concrete shrink main factor of crack as follows, 1, Variety of cement , grade and consumption. Slag cement , quick-hardening cement , low-heat cement concrete contractivity are relatively high, ordinary cement , volcanic ash cement , alumina cement concrete contractivity are relatively low. Cement grade low in addition, unit volume consumption heavy rubing detailed degree heavy, then the concrete shrinks the more greatly, and shrink time is the longer. For example, in order to improve the intensity of the concrete , often adopt and increase the cement consumption method by force while constructing, the result shrinks the stress to obviously strengthen . 2, Variety of aggregate. Such absorbing water rates as the quartz , limestone , cloud rock , granite , feldspar ,etc. are smaller, contractivity is relatively low in the aggregate; And such absorbing water rates as the sandstone , slate , angle amphibolite ,etc. are greater, contractivity is relatively high. Aggregate grains of foot-path heavy to shrink light inaddition, water content big to shrink the larger. 3, Water gray than. The heavier water consumption is, the higher water and dust are, the concrete shrinks the more greatly. 4, Mix the pharmaceutical outside. It is the better to mix pharmaceutical water-retaining property outside, then the concrete shrinks the smaller. 5, Maintain the method . Water that good maintenance can accelerate the concrete reacts, obtain the intensity of higher concrete. Keep humidity high , low maintaining time to be the longer temperature when maintaining, then the concrete shrinks the smaller. Steam maintain way than maintain way concrete is it take light to shrink naturall. 6, External environment. The humidity is little, the air drying , temperature are high, the wind speed is large in the atmosphere, then the concrete moisture is evaporated fast, the concrete shrinks the faster. 7, Shake and smash the way and time. Machinery shake way of smashing than make firm by ramming or tamping way concrete contractivity take little by hand. Shaking should determine according to mechanical performance to smash time , are generally suitable for 55s / time. It is too short, shake and can not smash closely knit , it is insufficient or not even in intensity to form the concrete; It is too long, cause and divide storey, thick aggregate sinks to the ground floor, the upper strata that the detailed aggregate stays, the intensity is not even , the upper strata incident shrink the crack. And shrink the crack caused to temperature, worthy of constructing the reinforcing bar againing can obviously improve the resisting the splitting of concrete , structure of especially thin wall (thick 200cm of wall ). Mix muscle should is it adopt light diameter reinforcing bar (8 |? construct 14 |? ) to have priority , little interval assign (whether @ 10 construct @ 15cm ) on constructing, the whole section is it mix muscle to be rate unsuitable to be lower than 0 to construct. 3%, can generally adopt 0 . 3%~0. 5%.(4), crack that causes out of shape of plinth of the groundBecause foundation vertical to even to subside or horizontal direction displacement, make the structure produce the additional stress, go beyond resisting the ability of drawing of concrete structure, cause the structure to fracture. The even main reason that subside of the foundation is as follows, 1, Reconnoitres the precision and is not enough for , test the materials inaccuratly in geology. Designing, constructing without fully grasping the geological situation, this is the main reason that cause the ground not to subside evenly .Such as hills area or bridge, district of mountain ridge,, hole interval to be too far when reconnoitring, and ground rise and fall big the rock, reconnoitring the report can't fully reflect the real geological situation . 2, The geological difference of the ground is too large. Building it in the bridge of the valley of the ditch of mountain area, geology of the stream place and place on the hillside change larger, even there are weak grounds in the stream, because the soil of the ground does not causes and does not subside evenly with the compressing. 3, The structure loads the difference too big. Under the unanimous terms, when every foundation too heavy to load difference in geological situation, may cause evenly to subside, for example high to fill out soil case shape in the middle part of the culvert than to is it take heavy to load both sides, to subside soon heavy than both sides middle part, case is it might fracture to contain 4, The difference of basic type of structure is great. Unite it in the bridge the samly , mix and use and does not expand the foundation and a foundation with the foundation, or adopt a foundation when a foot-path or a long difference is great at the same time , or adopt the foundation of expanding when basis elevation is widely different at the same time , may cause the ground not to subside evenly too 5, Foundation built by stages. In the newly-built bridge near the foundation of original bridge, if the half a bridge about expressway built by stages, the newly-built bridge loads or the foundation causes the soil of the ground to consolidate again while dealing with, may cause and subside the foundation of original bridge greatly 6, The ground is frozen bloatedly. The ground soil of higher moisture content on terms that lower than zero degree expands because of being icy; Once temperature goes up , the frozen soil is melted, the setting of ground. So the ground is icy or melts causes and does not subside evenly . 7, Bridge foundation put on body, cave with stalactites and stalagmites, activity fault,etc. of coming down at the bad geology, may cause and does not subside evenly . 8, After the bridge is built up , the condition change of original ground . After most natural grounds and artificial grounds are soaked with water, especially usually fill out such soil of special ground as the soil , loess , expanding in the land ,etc., soil body intensity meet water drop, compress out of shape to strengthen. In the soft soil ground , season causes the water table to drop to draw water or arid artificially, the ground soil layer consolidates and sinks again,reduce the buoyancy on the foundation at the same time , shouldering the obstruction of rubing to increase, the foundation is carried on one's shoulder or back and strengthened .Some bridge foundation is it put too shallow to bury, erode , is it dig to wash flood, the foundation might be moved. Ground load change of terms, bridge nearby is it is it abolish square , grit ,etc. in a large amount to put to pile with cave in , landslide ,etc. reason for instance, it is out of shape that the bridge location range soil layer may be compressed again. So, the condition of original ground change while using may cause and does not subside evenly Produce the structure thing of horizontal thrust to arched bridge ,etc., it is the main reason that horizontal displacement crack emerges to destroy the original geological condition when to that it is unreasonable to grasp incompletely , design and construct in the geological situation.桥梁裂缝产生原因浅析近年来,我省交通基础建设得到迅猛发展,各地建立了大量的混凝土桥梁。
土木工程毕业设计中英文翻译

土木工程毕业设计中英文翻译附录:中英文翻译英文部分:LOADSLoads that act on structures are usually classified as dead loads or live loads.Dead loads are fixed in location and constant in magnitude throughout the life of the ually the self-weight of a structure is the most important part of the structure and the unit weight of the material.Concrete density2varies from about 90 to 120 pcf (14 to 19 )for lightweight concrete,and is about 145 pcf (23 KN/m2)for normal concrete.In calculating the dead load of structural concrete,usually a 5 pcf (1 KN/m2)increment is included with the weight of the concrete to account for the presence of the KN/mreinforcement.Live loads are loads such as occupancy,snow,wind,or traffic loads,or seismic forces.They may be either fully or partially in place,or not present at all.They may also change in location.Althought it is the responsibility of the engineer to calculate dead loads,live loads are usually specified by local,regional,or national codes and specifications.Typical sources are the publications of the American National Standards Institute,the American Association of StateHighway and Transportation Officials and,for wind loads,the recommendations of the ASCE Task Committee on Wind Forces.Specified live the loads usually include some allowance for overload,and may include measures such as posting of maximum loads will not be exceeded.It is oftern important to distinguish between the specified load,and what is termed the characteristic load,that is,the load that actually is in effect under normal conditions of service,which may be significantly less.In estimating the long-term deflection of a structure,for example,it is the characteristic load that isimportant,not the specified load.The sum of the calculated dead load and the specified live load is called the service load,because this is the maximum load which may reasonably be expected to act during the service resisting is a multiple of the service load.StrengthThe strength of a structure depends on the strength of the materials from which it is made.Minimum material strengths are specified incertain standardized ways.The properties of concrete and its components,the methods of mixing,placing,and curing to obtain the required quality,and the methods for testing,are specified by the American Concrete Insititue(ACI).Included by refrence in the same documentare standards of the American Society for TestingMaterials(ASTM)pertaining to reinforcing and prestressing steels and concrete.Strength also depends on the care with which the structure isbuilt.Member sizes may differ from specified dimensions,reinforcement may be out of position,or poor placement of concrete may result in voids.An important part of the job of the ergineer is to provide proper supervision of construction.Slighting of this responsibility has had disastrous consequences in more than one instance.Structural SafetySafety requires that the strength of a structure be adequate for all loads that may conceivably act on it.If strength could be predicted accurately and if loads were known with equal certainty,then safely could be assured by providing strength just barely in excess of the requirements of the loads.But there are many sources of uncertainty in the estimation of loads as well as in analysis,design,andconstruction.These uncertainties require a safety margin.In recent years engineers have come to realize that the matter of structural safety is probabilistic in nature,and the safety provisions of many current specifications reflect this view.Separate consideration is given to loads and strength.Loadfactors,larger than unity,are applied to the calculated dead loads and estimated or specified service live loads,to obtain factorde loads that the member must just be capable of sustaining at incipient failure.Loadfactors pertaining to different types of loads vary,depending on the degree of uncertainty associated with loads of various types,and with the likelihood of simultaneous occurrence of different loads.Early in the development of prestressed concrete,the goal of prestressing was the complete elimination of concrete ternsile stress at service loads.The concept was that of an entirely new,homogeneous material that woukd remain uncracked and respond elastically up to the maximum anticipated loading.This kind of design,where the limiting tensile stressing,while an alternative approach,in which a certain amount of tensile amount of tensile stress is permitted in the concrete at full service load,is called partial prestressing.There are cases in which it is necessary to avoid all risk of cracking and in which full prestressing is required.Such cases include tanks or reservious where leaks must be avoided,submerged structures or those subject to a highly corrosive envionment where maximum protection of reinforcement must be insured,and structures subject to high frequency repetition of load where faatigue of the reinforcement may be a consideration.However,there are many cses where substantially improved performance,reduced cost,or both may be obtained through the use of a lesser amount of prestress.Full predtressed beams may exhibit an undesirable amount of upward camber because of the eccentric prestressing force,a displacement that is only partially counteracted by the gravity loads producing downward deflection.This tendency isaggrabated by creep in the concrete,which magnigies the upward displacement due to the prestress force,but has little influence on the should heavily prestressed members be overloaded and fail,they may do so in a brittle way,rather than gradually as do beams with a smaller amount of prestress.This is important from the point of view of safety,because suddenfailure without warning is dangeroud,and gives no opportunity for corrective measures to be taken.Furthermore,experience indicates that in many cases improved economy results from the use of a combination of unstressed bar steel and high strength prestressed steel tendons.While tensile stress and possible cracking may be allowed at full service load,it is also recognized that such full service load may be infrequently applied.The typical,or characteristic,load acting is likely to be the dead load plus a small fraction of the specified liveload.Thus a partially predtressed beam may not be subject to tensile stress under the usual conditions of loading.Cracks may from occasionally,when the maximum load is applied,but these will close completely when that load is removed.They may be no more objectionablein prestressed structures than in ordinary reinforced.They may be no more objectionable in prestressed structures than in ordinary reinforced concrete,in which flexural cracks always form.They may be considered a small price for the improvements in performance and economy that are obtained.It has been observed that reinforced concrete is but a special case of prestressed concrete in which the prestressing force is zero.Thebehavior of reinforced and prestressed concrete beams,as the failure load is approached,is essentially the same.The Joint European Committee on Concrete establishes threee classes of prestressed beams.Class 1:Fully prestressed,in which no tensile stress is allowed in the concrete at service load.Class 2:Partially prestressed, in which occasional temporary cracking is permitted under infrequent high loads.Class 3:Partially prestressed,in which there may be permanent cracks provided that their width is suitably limited.The choise of a suitable amount of prestress is governed by avariety of factors.These include thenature of the loading (for exmaple,highway or railroadbridged,storage,ect.),the ratio of live to dead load,the frequency of occurrence of loading may be reversed,such as in transmission poles,a high uniform prestress would result ultimate strength and in brittle failure.In such a case,partial prestressing provides the only satifactory solution.The advantages of partial prestressing are important.A smaller prestress force will be required,permitting reduction in the number of tendons and anchorages.The necessary flexural strength may be provided in such cases either by a combination of prestressed tendons and non-prestressed reinforcing bars,or by an adequate number of high-tensile tendons prestredded to level lower than the prestressing force isless,the size of the bottom flange,which is requied mainly to resist the compression when a beam is in the unloaded stage,can be reduced or eliminated altogether.This leads in turn to significant simplification and cost reduction in the construction of forms,as well as resulting in structures that are mor pleasing esthetically.Furthermore,by relaxing the requirement for low service load tension in the concrete,a significant improvement can be made in the deflection characteristics of a beam.Troublesome upward camber of the member in the unloaded stage fan be avoeded,and the prestress force selected primarily to produce the desired deflection for a particular loading condition.The behavior of partially prestressed beamsm,should they be overloaded to failure,is apt to be superior to that of fully prestressed beams,because the improved ductility provides ample warning of distress.英译汉:荷载作用在结构上的荷载通常分为恒载或活载。
土木工程专业毕业设计外文文献及翻译

英文原文:Rehabilitation of rectangular simply supported RC beams with shear deficiencies using CFRP compositesAhmed Khalifa a,* , Antonio Nanni ba Department of Structural Engineering, University of Alexandria, Alexandria 21544, Egyptb Department of Civil Engineering, University of Missouri at Rolla, Rolla, MO 65409, USAReceived 28 April 1999; received in revised form 30 October 2001; accepted 10 January 2002AbstractThe present study examines the shear performance and modes of failure of rectangular simply supported reinforced concrete(RC) beams designed with shear deficiencies. These members were strengthened with externally bonded carbon fiber reinforced polymer (CFRP) sheets and evaluated in the laboratory. The experimental program consisted of twelve full-scale RC beams tested to fail in shear. The variables investigated within this program included steel stirrups, and the shear span-to-effective depth ratio, as well as amount and distribution of CFRP. The experimental results indicated that the contribution of externally bonded CFRP to the shear capacity was significant. The shear capacity was also shown to be dependent upon the variables investigated. Test results were used to validate a shear design approach, which showed conservative and acceptable predictions.○C2002 Elsevier Science Ltd. All rights reserved.Keywords: Rehabilitation; Shear; Carbon fiber reinforced polymer1. IntroductionFiber reinforced polymer (FRP) composite systems, composed of fibers embedded in a polymeric matrix, can be used for shear strengthening of reinforced con-crete(RC) members [1–7]. Many existing RC beams are deficient and in need of strengthening. The shear failure of an RC beam is clearly different from its flexural failure. In shear, the beam fails suddenly without sufficient warning and diagonal shear cracks are consid-erably wider than the flexural cracks [8].The objectives of this program were to:1. Investigate performance and mode of failure of simply supported rectangular RC beams with shear deficien-cies after strengthening with externally bonded CFRP sheets.2. Address the factors that influence shear capacity of strengthened beams such as: steel stirrups, shear span-to-effective depth ratio (a/d ratio), and amount and distribution of CFRP.3. Increase the experimental database on shear strength-ening with externally bonded FRP reinforcement.4. Validate the design approach previously proposed by the authors [9].For these objectives, 12 full-scale, RC beams designed to fail in shear were strengthened with different CFRP schemes. These members were tested as simple beams using a four-point loading configuration with two different a/d ratios.2. Experimental program2.1. Test specimens and materialsTwelve full-scale beam specimens with a total span of 3050 mm. and a rectangular cross-section of 150-mm-wide and 305-mm-deep were tested. The specimens were grouped into two main series designated SW and SO depending on the presence of steel stirrups in the shear span of interest.Series SW consisted of four specimens. The details and dimensions of the specimens designated series SW are illustrated in Fig. 1a. In this series, four 32-mm steel bars were used as longitudinal reinforcement with two at top and two at bottom face of the cross-section to induce a shear failure. The specimens were reinforced with 10-mm steel stirrups throughout their entire span. The stirrups spacing in the shear span of interest, right half, was selected to allow failure in that span.Series SO consisted of eight beam specimens, which had the same cross-section dimension and longitudinal steel reinforcement as for series SW. No stirrups were provided in the test half span as illustrated.Each main series (i.e. series SW and SO) was subdivided into two subgroups according to shear span-to-effective depth ratio. This was selected to be a/d = 3 and 4, resulting in the following four subgroups: SW3;SW4; SO3; and SO4.The mechanical properties of the materials used for manufacturing the test specimens are listed in Table 1.Fabrication of the specimens including surface preparation and CFRP installation is described elsewhere [10].2.2. Strengthening schemesOne specimen from each series (SW3-1, SW4-1, SO3-1 and SO4-1) was left without strengthening as a control specimen, whereas eight beam specimens were strengthened with externally bonded CFRP sheets following three different schemes as illustrated in Fig. 2.In series SW3, specimen SW3-2 was strengthened with two CFRP plies having perpendicular fiber directions (90°/0°). The first ply was attached in the form of continuous U-wrap with the fiber direction oriented perpendicular to the longitudinal axis of the specimen (90°). The second ply was bonded on the two sides of the specimen with the fiber direction parallel to the beam axis(0°).This ply [i.e. 0°ply] was selected to investigate the impact of additional horizontal restraint on shear strength.In series SW4, specimen SW4-2 was strengthened with two CFRP plies having perpendicular fiber direction (90°/0°) as for specimen SW3-2.Four beam specimens were strengthened in series SO3. Specimen SO3-2 was strengthened with one-ply CFRP strips in the form of U-wrap with 90°-fiber orientation. The strip width was 50 mm with center-to-center spacing of 125 mm. Specimen SO3-3 was strengthened in a manner similar to that of specimen SO3-2, but with strip width equal to 75 mm. Specimen SO3-4 was strengthened with one-plycontinuous U-wrap (90°). Specimen SO3-5 was strengthened with twoCFRP plies (90°/0°) similar to specimens SW3-2 and SW4-2.In series SO4, two beam specimens were strengthened. Specimen SO4-2 was strengthened with one-ply CFRP strips in the form of U-wrap similar to specimen SO3-2. Specimen SO4-3 was strengthened with one-ply continuous U-wrap (90°) similar to SO3-4.2.3. Test set-up and instrumentationAll specimens were tested as simple span beams subjected to a four-point load as illustrated in Fig. 3. A universal testing machine with 1800 KN capacity was used in order to apply a concentrated load on a steel distribution beam used to generate the two concentrated loads. The load was applied progressively in cycles, usually one cycle before cracking followed by three cycles with the last one up to ultimate. The applied load vs. deflection curves shown in this paper are the envelopes of these load cycles.Four linear variable differential transformers (LVDTs) were used for each test to monitor vertical displacements at various locations as shown in Fig. 3. Two LVDTs were located at mid-span on each side of the specimen. The other two were located at the specimen supports to record support settlement.For each specimen of series SW, six strain gauges were attached to three stirrups to monitor the stirrup strain during loading as illustrated in Fig. 1a. Three strain gauges were attached directly to the FRP sheet on the sides of each strengthened beam to monitor strain variation in the FRP. The strain gauges were oriented in the vertical direction and located at the section mid-height with distances of 175, 300 and 425 mm, respectively, from the support for series SW3 and SO3. For beam specimens of series SW4 and SO4, the strain gauges were located at distance of 375, 500 and 625 mm, respectively, from the support.3. Results and discussionIn the following discussion, reference is always made to weak shear span or spanof interest.3.1. Series SW3Shear cracks in the control specimen SW3-1 were observed close to the middle of the shear span when the load reached approximately 90 kN. As the load increased, additional shear cracks formed throughout, widening and propagating up to final failure at a load of 253 kNIn specimen SW3-2 strengthened with CFRP (90°/0°), no cracks were visible on the sides or bottom of the test specimen due to the FRP wrapping. However,a longitudinal splitting crack initiated on the top surface of the beam at a high load of approximately 320 kN.The crack initiated at the location of applied load and extended towards the support. The specimen failed by concrete splitting at total load of 354 kN. This was an increase of 40% in ultimate capacity compared to the control specimen SW3-1. The splitting failure was due to the relatively high longitudinal compressive stress developed at top of the specimen, which created a transverse tension, led to the splitting failure. In addition, the relatively large amount of longitudinal steel reinforcement combined with over-strengthening for shear by CFRP wrap probably caused this mode of failure. The load vs. mid-span deflection curves for specimens SW3-1 and SW3-2 are illustrated , to show the additional capacity gained by CFRP. The maximum CFRP vertical strain measured at failure in specimen SW3-2 was approximately 0.0023 mm/mm, which corresponded to 14% of the reported CFRP ultimate strain. This value is not an absolute because it greatly depends on the location of the strain gauges with respect to a crack. However, the recorded strain indicates that if the splitting did not occur, the shear capacity could have reached higher load.Comparison between measured local stirrup strains in specimens SW3-1 and SW3-2 are shown in Fig. 6. The stirrups 1, 2 and 3 were located at distance of 175, 300 and 425 mm from the support, respectively. The results showed that the stirrups2 and3 did not yield at ultimate for both specimens. The strains (and the forces) in the stirrups of specimen SW3-2 were, in general, smaller than those of specimen SW3-1 at the same level of loading due to the effect of CFRP.3.2. Series SW4In specimen SW4-1, the first diagonal crack was formed in the member at a total applied load of 75 kN. As the load increased, additional shear cracks appeared throughout the shear span. Failure of the beam occurred when the total applied load reached 200 kN. This was a decrease of 20% in shear capacity compared to the specimen SW3-1In specimen SW4-2, the failure was controlled by concrete splitting similar to test specimen SW3-2. The total applied load at ultimate was 361 kN with an 80% increase in shear capacity compared to the control specimen SW4-1. In addition, the measured strains in the stirrups for specimen SW4-2 were less than those of specimen SW4-1. The applied load vs. mid-span deflection curves for beams SW4-1 and SW4-2 are illustrated . It may be noted that specimen SW4-2 resulted in greater deflection when compared to specimen SW4-1.When comparing the test results of series SW3 specimens to that of series SW4, the ultimate failure load of specimen SW3-2 and SW4-2 was almost the same. However, the enhanced capacity of specimen SW3-2 (a/d=3) due to the addition of the CFRP reinforcement was 101 kN, while specimen SW4-2 (a/d=4) was 161 kN. This indicates that the contribution of external CFRP reinforcement may be influenced by the ayd ratio and appears to decrease with a decreasing a/d ratio. Further, for both strengthened specimens (SW3-2 and SW4-2), CFRP sheets did not fracture or debond from the concrete surface at ultimate and this indicates that CFRP could provide additional strength if the beams did not failed by splitting.3.3. Series SO3Fig. 8 illustrates the failure modes for series SO3 specimens. That details the applied load vs. mid-span deflection for the specimens.The failure mode of control specimen SO3-1 was shear compression. Failure of the specimen occurred at a total applied load of 154 kN. This load was a decrease of shear capacity by 54.5 kN compared to the specimen SW3-1 due to the absent of the steel stirrups. In addition, the crack pattern in specimen SW3-1 was different from of specimen SO3-1. In specimen SW3-1, the presence of stirrups provided a better distribution of diagonal cracks throughout the shear span.In specimen SO3-2, strengthened with 50-mm CFRP strips spaced at 125 mm, the first diagonal shear crack was observed at an applied load of 100 kN. The crack propagated as the load increased in a similar manner to that of specimen SO3-1. Sudden failure occurred due to debonding of the CFRP strips over the diagonal shear crack, with spalled concrete attached to the CFRP strips. The total ultimate load was 262 kN with a 70% increase in shear capacity over the control specimen SO3-1. The maximum local CFRP vertical strain measured at failure in specimen SO3-2 was 0.0047 mm/mm (i.e. 28% of the ultimate strain), which indicated that the CFRP did not reach its ultimate.Specimen SO3-3, strengthened with 75-mm CFRP strips failed as a result of CFRP debonding at a total applied load of 266 kN. No significant increase in shear capacity was noted compared to specimen SO3-2. The maximum-recorded vertical CFRP strain at failure was 0.0052 mmymm (i.e. 31% of the ultimate strain).Specimen SO3-4, which was strengthened with a continuous CFRP U-wrap (908), failed as a result of CFRP debonding at an applied load of 289 kN. Results show that specimen SO3-4 exhibited increase in shear capacity of 87, 10 and 8.5% over specimens SO3-1,SO3-2 and SO3-3, respectively. Applied load vs. vertical CFRP strain for specimen SO3-4 is illustrated in Fig. 10 in which strain gauges sg1, sg2 and sg3 were located at mid-height with distances of 175, 300 and 425 mm from the support, respectively. Fig. 10 shows that the CFRP strain was zero prior to diagonal crack formation, then increased slowly until the specimen reached a load in the neighborhood of theultimate strength of the control specimen. At this point, the CFRP strain increased significantly until failure. The maximum local CFRP vertical strain measured at failure was approxi- mately 0.0045 mm/mm.When comparing the results of beams SO3-4 and SO3-2, the CFRP amount used to strengthen specimen SO3-4 was 250% of that used for specimen SO3-2. Only a 10% increase in shear capacity was achieved for the additional amount of CFRP used. This means that if an end anchor to control FRP debonding is not used, there is an optimum FRP quantity, beyond which the strengthening effect is questionable. A previous study [11] showed that by using an end anchor system, the failure mode of FRP debonding could be avoided. Reported findings are consistent with those of other research [7], which was based on a review of the experimental results available in the literature, and indicated that the contribution of FRP to the shear capacity increases almost linearly, with FRP axial rigidity expressed byf f E ρ(f ρ is the FRP area fraction and f E is the FRP elastic modulus) up to approximately 0.4 GPa. Beyond this value, the effectiveness of FRP ceases to be positive.In specimen SO3-5, the use of a horizontal ply over the continuous U-wrap (i.e. 90°/0°) resulted in a concrete splitting failure rather than a CFRP debonding failure. The failure occurred at total applied load of 339 kN with a 120% increase in the shear capacity compared to the control specimen SO3-1. The strengthening with two perpendicular plies (i.e. 90°/0°) resulted in a 17% increase in shear capacity compared to the specimen with only one CFRP ply in 90° orientation (i.e. specimen SO3-4). The maximum local CFRP vertical strain measured at failure was 0.0043 mm/mm.By comparing the test results of specimens SW3-2 and SO3-5, having the same a/d ratio and strengthening schemes but with different steel shear reinforcement, the shear strength (i.e. 177 and 169.5 kN for specimens SW3-2 and SO3-5, respectively), and the ductility are almost identical. One may conclude that the contribution of CFRP benefits the beam capacity to a greater degree for beams without steel shear reinforcement than for beams with adequate shear reinforcement.3.4. Series SO4Series SO4 exhibited the largest increase in shear capacity compared to the other series investigated with this research study. The experimental results in terms of applied load vs mid-span deflection for this series is illustrated in Fig. 11.The control specimen SO4-1 failed as a result of shear compression at a total applied load of 130 kN. Specimen SO4-2, strengthened with CFRP strips, the failure was controlled by CFRP debonding at a total load of 255 kN with 96% increase in shear capacity over the control specimen SO4-1. The maximum local CFRP vertical strain measured at failure was 0.0062mmymm.When comparing the test results of specimen SO4-2 to that of specimen SO3-2, the enhanced shear capacity of specimen SO4-2 (a/d=4) due to addition of CFRP strips was 62.5 kN, while specimen SO3-2 (a/d=3) resulted in added shear capacity of 54 kN. As expected, the contribution of CFRP reinforcement to resist the shear appeared to decrease with decreasing a/d ratio. Specimen SO4-3, strengthened with continuous U- wrap, failed as a result of concrete splitting at an applied load of 310 kN with a 138% increase in shear capacity compared to that of specimen SO4-1. The maximum local CFRP vertical strain measured at failure was 0.0037 mm/mm.4. Design approachThe design approach for computing the shear capacity of RC beams strengthened with externally bonded CFRP reinforcement, expressed in ACI design code [12] format, was proposed and published in 1998 [13]. The design model described two possible failure mechanisms of CFRP reinforcement namely: CFRP fracture; and CFRP debonding. Furthermore, two limits on the contribution of CFRP shear were proposed. The first limit was set to control the shear crack width and loss of aggregate interlock, and the second was to preclude web crushing. Also, the concrete strength and CFRP wrap- ping schemes were incorporated as design parameters. In recent study [9,10], modifications were proposed to the 1998 design approach toinclude results of a new study on bond mechanism between CFRP sheets and concrete surface [14]. In addition, the model was extended to provide the shear design equations in Eurocode as well as ACI format. Comparing with all test results available in the literature to date, 76 tests, the design approach showed acceptable and conservative estimates [10,13]. In this section, the summary of the design approach is presented. The comparison between experimental results and the calculated factored shear strength demonstrates the ability of the design approach to predict the shear capacity of the strengthened beams. demonstrates the ability of the design approach to predict the shear capacity of the strengthened beams.4.1. Summary of the shear design approach — ACI formatIn traditional shear design (including the ACI Code), the nominal shear strength of an RC section is the sum of the nominal shear strengths of concrete and steel shear reinforcement. For beams strengthened with externally bonded FRP reinforcement, the shear strength may be computed by the addition of a third term to account of the FRP contribution. This is expressed as follows:The design shear strength,n Vφ, is obtained by multiplying the nominal shear strength by a strength reduction factor for shear,φ. It was suggested that the reduction factor φ=0.85 given in ACI [12] be main-tained for the concrete and steel terms. However, a more stringent strength reduction factor of 0.7 for the CFRP contribution was suggested w10x. This is due to the relative novelty of this repair technique. Thus, the design shear strength is expressed as follows.4.2. Contribution of CFRP reinforcement to the shear capacityThe expression used to compute shear contribution of CFRP reinforcement is given in Eq. (3). This equation is similar to that for shear contribution of steel stirrups and consistent with the ACI format.The area of CFRP shear reinforcement,f A , is the total thickness of the sheet (usually f t 2or sheets on both sides of the beam) times the width of the CFRP stripf ω. The dimensions used to define the area of CFRP in addition to the spacingf s and the effective depth of CFRP,f d , are shown in Fig. 12. Note that for continuousvertical shear reinforcement, the spacing of the strip,f s , and the width of the strip,f ω, are equal.In Eq. (3), an effective average CFRP stressfe f , smaller than its ultimate strength,fu f , was used to replace the yield stress of steel. At the ultimate limit state for the member in shear, it is not possible to attain the full strength of the FRP [7,13]. Failure is governed by either fracture of the FRP sheet at average stress levels well below FRP ultimate capacity due to stress concentrations, debonding of the FRP sheet from the concrete surface, or a significant decrease in the post- cracking concrete shear strength from a loss of aggregate interlock. Thus, the effective average CFRP stress is computed by applying a reduction coefficient, R, to the CFRP ultimate strength as expressed in Eq. (4).The reduction coefficient depends on the possible failure modes (either CFRPfracture or CFRP debonding). In either case, an upper limit for the reduction coefficient is established in order to control shear crack width and loss of aggregate interlock.4.3. Reduction coefficient based on CFRP sheet fracture failureThe proposed reduction coefficient was calibrated on all available test results to date, 22 tests with failure controlled by CFRP fracture [10,13]. The reduction coefficient was established as a function of f f E ρ (where f ρis the area fraction ofCFRP) and expressed in Eq.(5) for ≤f f E ρ0.7 GPa.4.4. Reduction coefficient based on CFRP debonding failureThe shear capacity governed by CFRP debonding from the concrete surface was presented [9,10]as a function of CFRP axial rigidity, concrete strength, effective depth of CFRP reinforcement, and bonded surface configurations. In determining the reduction coefficient for bond, the effective bond length, e L , has to be determined first. Based on analytical and experimental data from bond tests, Miller [14] showed that the effective bond length slightly increases as CFRP axial rigidity,f f E t , increases. However, he suggested a constant conservative value e L for equal to 75 mm. The value may be modified when more bond tests data becomes available.After a shear crack develops, only that portion of the width of CFRP extending past the crack by the effective bonded length is assumed to be capable of carrying shear.[13] The effective width, fe W , based on the shear crack angle of 45°, and the wrapping scheme is expressed in Eqs. (6a) and (6b);if the sheet in the form of a U-wrap (6a)if the sheet is bonded only to the sides of the beam. (6b)The final expression for the reduction coefficient, R, for the mode of failure controlled by CFRP debonding is expressed in Eq. (8)Eq. (7) is applicable for CFRP axial rigidity, f f E t , ranging from 20 to 90 mm-GPa (kN/mm). Research into quantifying the bond characteristics for axial rigidities above 90 mm·GPa is being conducted at the University of Missouri, Rolla (UMR).4.5. Upper limit of the reduction coefficientIn order to control the shear crack width and loss of aggregate interlock, an upper limit of reduction coefficient, R, was suggested and calibrated with all of the availabletest results [10] to be equal to fu ε/006.0where fu εis the ultimate tensile CFRP strain. This limit is such that the average effective strain in CFRP materials at ultimate can not be greater than 0.006 mm/mm (without the strengthening reduction factor,φ).4.6. Controlling reduction coefficientThe final controlling reduction coefficient for the CFRP system is taken as the lowest value determined from the two possible modes of failure and the upper limit. Note that if the sheet is wrapped entirely around the beam or an effective end anchor is used, the failure mode of CFRP debonding is not to be considered. The reduction coefficient is only controlled by FRP fracture and the upper limit.4.7. CFRP spacing requirementsSimilar to steel shear reinforcement, and consistent with ACI provision for the stirrups spacing[12], the spacing of FRP strips should not be so wide as to allow the formation of a diagonal crack without intercepting a strip. For this reason, if strips are used, they should not be spaced by more than the maximum given in Eq. (8).4.8. Limit on total shear reinforcementACI 318M-95 [12] 11.5.6.7 and 11.5.6.8 set a limit on the total shear strength that may be provided by more than one type of shear reinforcement to preclude the web crushing. FRP shear reinforcement should be included in this limit. A modification to ACI 318M-95 Section 11.5.6.8 was suggested as follows:4.9. Shear capacity of a CFRP strengthened section — Eurocode formatThe proposed design equation wEq. (3)x for computing the contribution of externally bonded CFRP reinforcement may be rewritten in Eurocode (EC2 1992) [15] format as Eq. (10).In this equation, the partial safety factor for CFRP materials,f , was suggestedequal to 1.3 [10].5. Conclusions and further recommendation An experimental investigation was conducted to study the shear behavior and the modes of failure of simply supported rectangular section RC beams with shear deficiencies, strengthened with CFRP sheets. The parameters investigated in this program were existence of steel shear reinforcement, shear span-to-effective depth ratio (ayd ratio), and CFRP amount and distribution.The results confirm that the strengthening technique using CFRP sheets can be used to increase significantly shear capacity, with efficiency that varies depending on the tested variables. For the beams tested in this program, increases in shear strength of 40–138% were achieved.Conclusions that emerged from this study may be summarized as follows:● The contribution of externally CFRP reinforcement to the shear capacity isinfluenced by the a/d ratio.● Increasing the amount of CFRP may not result in a proportional increase in theshear strength. The CFRP amount used to strengthen specimen SO3-4 was 250% of that used in specimen SO3-2, which resulted in a minimal (10%) increase in shear capacity. An end anchor is recommended if FRP debonding is to be avoided. ● The test results indicated that contribution of CFRP benefits the shear capacity ata greater degree for beams without shear reinforcement than for beams with adequate shear reinforcement.● The results of series SO3 indicated that the 0° ply improved the shear capacity byproviding horizontal restraint.● The shear design algorithms provided acceptable and conservative estimates forthe strengthened beams. Recommendations for future research are as follows:● Experimental and analytical investigations are required to link the shearcontribution of FRP with the load condition. These studies have to consider both the longitudinal steel reinforcement ratio and the concrete strength as parameters. Laboratory specimens should maintain practical dimensions.● The strengthening effectiveness of FRP has to be addressed in the cases of shortand very short shear spans in which arch action governs failure.● The interaction between the contribution of external FRP and internal steel shearreinforcement has to be investigated.● To optimize design algorithms, additional specimens need to be tested withdifferent CFRP amount and configurations to create a large database of information.● Shear design algorithms need to be expanded to include strengthening witharamid FRP and glass FRP sheets in addition to CFRP .6. NomenclatureA: Shear spanf A :Area of CFRP shear reinforcements=2t f w fw b : Width of the beam cross-sectionD: Depth from the top of the section to the tension steel reinforcement centroidf d :Effective depth of the CFRP shear reinforcement (usually equal to d for rectangular sections and dyts for T-sections)f E :Elastic modulus of FRP (GPa)'c f :Nominal concrete compressive strength (MPa)fef :Effective tensile stress in the FRP sheet in the direction of the principal fibers (stress level in the FRP at failure)fu f :Ultimate tensile strength of the FRP sheet in the direction of the principal fibers e L :Effective bond length (mm)。
【设计】土木工程毕业设计英语论文及翻译
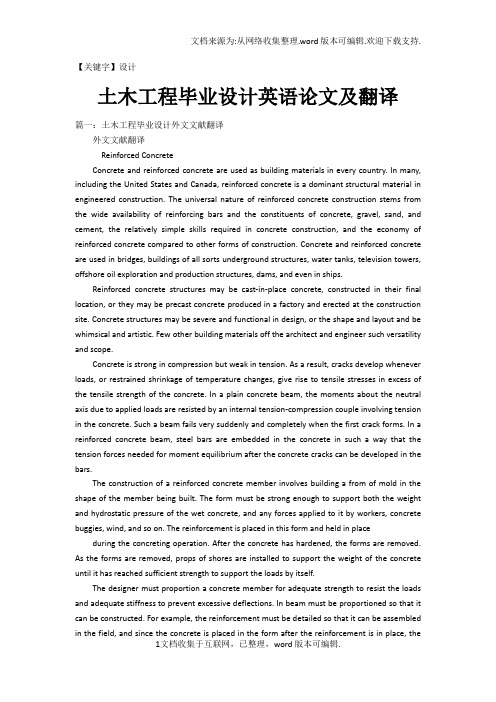
【关键字】设计土木工程毕业设计英语论文及翻译篇一:土木工程毕业设计外文文献翻译外文文献翻译Reinforced ConcreteConcrete and reinforced concrete are used as building materials in every country. In many, including the United States and Canada, reinforced concrete is a dominant structural material in engineered construction. The universal nature of reinforced concrete construction stems from the wide availability of reinforcing bars and the constituents of concrete, gravel, sand, and cement, the relatively simple skills required in concrete construction, and the economy of reinforced concrete compared to other forms of construction. Concrete and reinforced concrete are used in bridges, buildings of all sorts underground structures, water tanks, television towers, offshore oil exploration and production structures, dams, and even in ships.Reinforced concrete structures may be cast-in-place concrete, constructed in their final location, or they may be precast concrete produced in a factory and erected at the construction site. Concrete structures may be severe and functional in design, or the shape and layout and be whimsical and artistic. Few other building materials off the architect and engineer such versatility and scope.Concrete is strong in compression but weak in tension. As a result, cracks develop whenever loads, or restrained shrinkage of temperature changes, give rise to tensile stresses in excess of the tensile strength of the concrete. In a plain concrete beam, the moments about the neutral axis due to applied loads are resisted by an internal tension-compression couple involving tension in the concrete. Such a beam fails very suddenly and completely when the first crack forms. In a reinforced concrete beam, steel bars are embedded in the concrete in such a way that the tension forces needed for moment equilibrium after the concrete cracks can be developed in the bars.The construction of a reinforced concrete member involves building a from of mold in the shape of the member being built. The form must be strong enough to support both the weight and hydrostatic pressure of the wet concrete, and any forces applied to it by workers, concrete buggies, wind, and so on. The reinforcement is placed in this form and held in place during the concreting operation. After the concrete has hardened, the forms are removed. As the forms are removed, props of shores are installed to support the weight of the concrete until it has reached sufficient strength to support the loads by itself.The designer must proportion a concrete member for adequate strength to resist the loads and adequate stiffness to prevent excessive deflections. In beam must be proportioned so that it can be constructed. For example, the reinforcement must be detailed so that it can be assembled in the field, and since the concrete is placed in the form after the reinforcement is in place, theconcrete must be able to flow around, between, and past the reinforcement to fill all parts of the form completely.The choice of whether a structure should be built of concrete, steel, masoy, or timber depends on the availability of materials and on a number of value decisions. The choice of structural system is made by the architect of engineer early in the design, based on the following considerations:1. Economy. Frequently, the foremost consideration is the overall const of the structure. This is, of course, a function of the costs of the materials and the labor necessary to erect them. Frequently, however, the overall cost is affected as much or more by the overall construction time since the contractor and owner must borrow or otherwise allocate money to carry out the construction and will not receive a return on this investment until the building is ready for occupancy. In a typical large apartment of commercial project, the cost of construction financing will be a significant fraction of the total cost. As a result, financial savings due to rapid construction may more than offset increased material costs. For this reason, any measures the designer can take to standardize the design and forming will generally pay off in reduced overall costs.In many cases the long-term economy of the structure may be more important than the first cost. As a result, maintenance and durability are important consideration.2. Suitability of material for architectural and structural function.A reinforced concrete system frequently allows the designer to combine the architectural and structural functions. Concrete has the advantage that it is placed in a plastic condition and is given the desired shapeand texture by means of the forms and the finishing techniques. This allows such elements ad flat plates or other types of slabs to serve as load-bearing elements while providing the finished floor and / or ceiling surfaces. Similarly, reinforced concrete walls can provide architecturally attractive surfaces in addition to having the ability to resist gravity, wind, or seismic loads. Finally, the choice of size of shape is governed by the designer and not by the availability of standard manufactured members.3. Fire resistance. The structure in a building must withstand the effects of a fire and remain standing while the building is evacuated and the fire is extinguished. A concrete building inherently has a 1- to 3-hour fire rating without special fireproofing or other details. Structural steel or timber buildings must be fireproofed to attain similar fire ratings.4. Low maintenance. Concrete members inherently require less maintenance than do structural steel or timber members. This is particularly true if dense, air-entrained concrete has been used for surfaces exposed to the atmosphere, and if care has been taken in the design to provide adequate drainage off and away from the structure. Special precautions must be taken for concrete exposed to salts such as deicing chemicals.5. Availability of materials. Sand, gravel, cement, and concrete mixing facilities are verywidely available, and reinforcing steel can be transported to most job sites more easily than can structural steel. As a result, reinforced concrete is frequently used in remote areas.On the other hand, there are a number of factors that may cause one to select a material other than reinforced concrete. These include:1. Low tensile strength. The tensile strength concrete is much lower than its compressive strength ( about 1/10 ), and hence concrete is subject to cracking. In structural uses this is overcome by using reinforcement to carry tensile forces and limit crack widths to within acceptable values. Unless care is taken in design and construction, however, these cracks may be unsightly or may allow penetration of water. When this occurs, water or chemicals such as road deicing salts may cause deterioration or staining of the concrete. Special design details are required in such cases. In the case of water-retaining structures, special details and / of prestressing are required to prevent leakage.2. Forms and shoring. The construction of a cast-in-place structure involves three steps not encountered in the construction of steel or timber structures. These are ( a ) the construction of the forms, ( b ) the removal of these forms, and (c) propping or shoring the new concrete to support its weight until its strength is adequate. Each of these steps involves labor and / or materials, which are not necessary with other forms of construction.3. Relatively low strength per unit of weight for volume. The compressive strength of concrete is roughly 5 to 10% that of steel, while its unit density is roughly 30% that of steel. As a result, a concrete structure requires a larger volume and a greater weight of material than does a comparable steel structure. As a result, long-span structures are often built from steel.4. Time-dependent volume changes. Both concrete and steel undergo-approximately the same amount of thermal expansion and contraction. Because there is less mass of steel to be heated or cooled, and because steel is a better concrete, a steel structure is generally affected by temperature changes to a greater extent than is a concrete structure. On the other hand, concrete undergoes frying shrinkage, which, if restrained, may cause deflections or cracking. Furthermore, deflections will tend to increase with time, possibly doubling, due to creep of the concrete under sustained loads.In almost every branch of civil engineering and architecture extensive use is made of reinforced concrete for structures and foundations. Engineers and architects requires basic knowledge of reinforced concrete design throughout their professional careers. Much of this text is directly concerned with the behavior and proportioning of components that make up typical reinforced concrete structures-beams, columns, and slabs. Once the behavior of these individual elements is understood, the designer will have the background to analyze and design a wide range of complex structures, such as foundations, buildings, and bridges, composed of these elements.Since reinforced concrete is a no homogeneous material that creeps, shrinks, and cracks, its stresses cannot be accurately predicted by the traditional equations derived in a course instrength of materials forhomogeneous elastic materials. Much of reinforced concrete design in therefore empirical, i.e., design equations and design methods are based on experimental and time-proved results instead of being derived exclusively from theoretical formulations.A thorough understanding of the behavior of reinforced concrete will allow the designer to convert an otherwise brittle material into tough ductile structural elements and thereby take advantage of concrete’s desirable characteristics, its high compressive strength, its fire resistance, and its durability.Concrete, a stone like material, is made by mixing cement, water, fine aggregate ( often sand ), coarse aggregate, and frequently other additives ( that modify properties ) into a workable mixture. In its unhardened or plastic state, concrete can be placed in forms to produce a large variety of structural elements. Although the hardened concrete by itself, i.e., without any reinforcement, is strong in compression, it lacks tensile strength and therefore cracks easily. Because ueinforced concrete is brittle, it cannot undergo large deformations under load and fails suddenly-without warning. The addition fo steel reinforcement to the concrete reduces the negative effects of its two principal inherent weaknesses, its susceptibility to cracking and its brittleness. When the reinforcement is strongly bonded to the concrete, a strong, stiff, and ductile construction material is produced. This material, called reinforced concrete, is used extensively to construct foundations, structural frames, storage takes, shell roofs, highways, walls, dams, canals, and innumerable other structures and building products. Two other characteristics of concrete that are present even when concrete is reinforced are shrinkage and creep, but the negative effects of these properties can be mitigated by careful design.A code is a set technical specifications and standards that control important details of design and construction. The purpose of codes it produce structures so that the public will be protected from poor of inadequate and construction.Two types f coeds exist. One type, called a structural code, is originated and controlled by specialists who are concerned with the proper use of a specific material or who are involved with the safe design of a particular class of structures.篇二:土木工程毕业设计中英文翻译附录:中英文翻译英文部分:LOADSLoads that act on structures are usually classified as dead loads or live loads.Dead loads are fixed in location and constant in magnitude throughout the life of the ually the self-weight of a structure is the most important part of the structure and the unit weight of the material.Concrete density varies from about 90 to 120 pcf (14 to 19 KN/m2)for lightweight concrete,and is about 145 pcf (23 KN/mKN/m2)for normal concrete.In calculating the dead load of structural concrete,usually a 5pcf (1 )increment is included with the weight of the concrete to account for the presence of the 2 reinforcement.Live loads are loads such as occupancy,snow,wind,or traffic loads,or seismic forces.They may be either fully or partially in place,or not present at all.They may also change in location.Althought it is the responsibility of the engineer to calculate dead loads,live loads are usually specified by local,regional,or national codes and specifications.Typical sources are the publications of the American National Standards Institute,the American Association of State Highway and Transportation Officials and,for wind loads,the recommendations of the ASCE Task Committee on Wind Forces.Specified live the loads usually include some allowance for overload,and may include measures such as posting of maximum loads will not be exceeded.It is oftern important to distinguish between the specified load,and what is termed the characteristic load,that is,the load that actually is in effect under normal conditions of service,which may be significantly less.In estimating the long-term deflection of a structure,for example,it is the characteristic load that is important,not the specified load.The sum of the calculated dead load and the specified live load is called the service load,because this is the maximum load which may reasonably be expected to act during the service resisting is a multiple of the service load.StrengthThe strength of a structure depends on the strength of the materials from which it is made.Minimum material strengths are specified in certain standardized ways.The properties of concrete and its components,the methods of mixing,placing,and curing to obtain the required quality,and the methods for testing,are specified by the American Concrete Insititue(ACI).Included by refrence in the same documentare standards of the American Society for Testing Materials(ASTM)pertaining to reinforcing and prestressing steels and concrete.Strength also depends on the care with which the structure is built.Member sizes may differ from specified dimensions,reinforcement may be out of position,or poor placement of concrete may result in voids.An important part of the job of the ergineer is to provide proper supervision of construction.Slighting of this responsibility has had disastrous consequences in more than one instance.Structural SafetySafety requires that the strength of a structure be adequate for all loads that may conceivably act on it.If strength could be predicted accurately and if loads were known with equal certainty,then safely could be assured by providing strength just barely in excess of the requirements of the loads.But there are many sources of uncertainty in the estimation of loads as well as in analysis,design,and construction.These uncertainties require a safety margin.In recent years engineers have come to realize that the matter of structural safety isprobabilistic in nature,and the safety provisions of many current specifications reflect this view.Separate consideration is given to loads and strength.Load factors,larger than unity,are applied to the calculated dead loads and estimated or specified service live loads,to obtain factorde loads that the member must just be capable of sustaining at incipient failure.Load factors pertaining to different types of loads vary,depending on the degree of uncertainty associated with loads of various types,and with the likelihood of simultaneous occurrence of different loads.Early in the development of prestressed concrete,the goal of prestressing was the complete elimination of concrete ternsile stress at service loads.The concept was that of an entirely new,homogeneous material that woukd remain uncracked and respond elastically up to the maximum anticipated loading.This kind of design,where the limiting tensile stressing,while an alternative approach,in which a certain amount of tensile amount of tensile stress is permitted in the concrete at full service load,is called partial prestressing.There are cases in which it is necessary to avoid all risk of cracking and in which full prestressing is required.Such cases include tanks or reservious where leaks must be avoided,submerged structures or those subject to a highly corrosive envionment where maximum protection of reinforcement must be insured,and structures subject to high frequency repetition of load where faatigue of the reinforcement may be a consideration.However,there are many cses where substantially improved performance,reduced cost,or both may be obtained through the use of a lesser amount of prestress.Full predtressed beams may exhibit an undesirable amount of upward camber because of the eccentric prestressing force,a displacement that is only partially counteracted by the gravity loads producing downward deflection.This tendency is aggrabated by creep in the concrete,which magnigies the upward displacement due to the prestress force,but has little influence on the should heavily prestressed members be overloaded and fail,they may do so in a brittle way,rather than gradually as do beams with a smaller amount of prestress.This is important from the point of view of safety,because suddenfailure without warning is dangeroud,and gives no opportunity for corrective measures to be taken.Furthermore,experience indicates that in many cases improved economy results from the use of a combination of unstressed bar steel and high strength prestressed steel tendons.While tensile stress and possible cracking may be allowed at full service load,it is also recognized that such full service load may be infrequently applied.The typical,or characteristic,load acting is likely to be the dead load plus a small fraction of the specified live load.Thus a partially predtressed beam may not be subject to tensile stress under the usual conditions of loading.Cracks may from occasionally,when the maximum load is applied,but these will close completely when that load is removed.They may be no more objectionable in prestressed structures than in ordinary reinforced.They may be no more objectionable in prestressed structures than in ordinary reinforced concrete,in which flexural cracks alwaysform.They may be considered a small price for the improvements in performance and economy that are obtained.It has been observed that reinforced concrete is but a special case of prestressed concrete in which the prestressing force is zero.The behavior of reinforced and prestressed concrete beams,as the failure load is approached,is essentially the same.The Joint European Committee on Concrete establishes threee classes of prestressed beams.Class 1:Fully prestressed,in which no tensile stress is allowed in the concrete at service load.Class 2:Partially prestressed, in which occasional temporary cracking is permitted under infrequent high loads.Class 3:Partially prestressed,in which there may be permanent cracks provided that their width is suitably limited.The choise of a suitable amount of prestress is governed by a variety of factors.These include thenature of the loading (for exmaple,highway or railroad bridged,storage,ect.),the ratio of live to dead load,the frequency of occurrence of loading may be reversed,such as in transmission poles,a high uniform prestress would result ultimate strength and in brittle failure.In such a case,partial prestressing provides the only satifactory solution.The advantages of partial prestressing are important.A smaller prestress force will be required,permitting reduction in the number of tendons and anchorages.The necessary flexural strength may be provided in such cases either by a combination of prestressed tendons and non-prestressed reinforcing bars,or by an adequate number of high-tensile tendons prestredded to level lower than the prestressing force is less,the size of the bottom flange,which is requied mainly to resist the compression when a beam is in the unloaded stage,can be reduced or eliminated altogether.This leads in turn to significant simplification and cost reduction in the construction of forms,as well as resulting in structures that are mor pleasing esthetically.Furthermore,by relaxing the requirement for low service load tension in the concrete,a significant improvement can be made in the deflection characteristics of a beam.Troublesome upward camber of the member in the unloaded stage fan be avoeded,and the prestress force selected primarily to produce the desired deflection for a particular loading condition.The behavior of partially prestressed beamsm,should they be overloaded to failure,is apt to be superior to that of fully prestressed beams,because the improved ductility provides ample warning of distress.英译汉:荷载作用在结构上的荷载通常分为恒载或活载。
土木工程毕业设计中英文翻译.doc
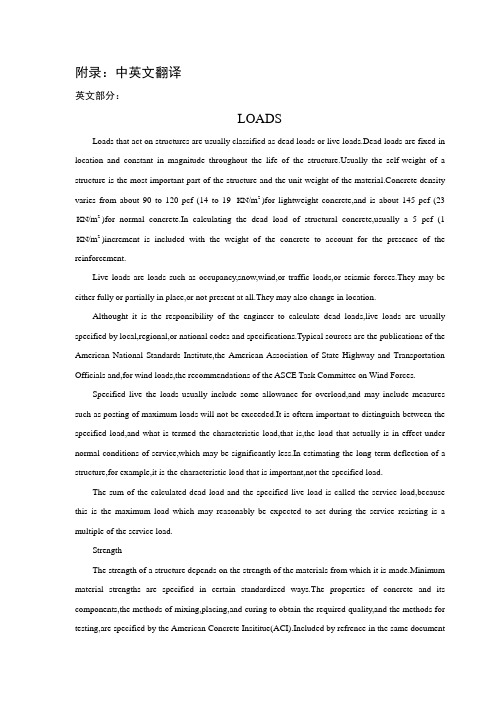
附录:中英文翻译英文部分:LOADSLoads that act on structures are usually classified as dead loads or live loads.Dead loads are fixed in location and constant in magnitude throughout the life of the ually the self-weight of a structure is the most important part of the structure and the unit weight of the material.Concrete density varies from about 90 to 120 pcf (14 to 19 2KN/m)for lightweight concrete,and is about 145 pcf (23 2KN/m)for normal concrete.In calculating the dead load of structural concrete,usually a 5 pcf (1 2KN/m)increment is included with the weight of the concrete to account for the presence of the reinforcement.Live loads are loads such as occupancy,snow,wind,or traffic loads,or seismic forces.They may be either fully or partially in place,or not present at all.They may also change in location.Althought it is the responsibility of the engineer to calculate dead loads,live loads are usually specified by local,regional,or national codes and specifications.Typical sources are the publications of the American National Standards Institute,the American Association of State Highway and Transportation Officials and,for wind loads,the recommendations of the ASCE Task Committee on Wind Forces.Specified live the loads usually include some allowance for overload,and may include measures such as posting of maximum loads will not be exceeded.It is oftern important to distinguish between the specified load,and what is termed the characteristic load,that is,the load that actually is in effect under normal conditions of service,which may be significantly less.In estimating the long-term deflection of a structure,for example,it is the characteristic load that is important,not the specified load.The sum of the calculated dead load and the specified live load is called the service load,because this is the maximum load which may reasonably be expected to act during the service resisting is a multiple of the service load.StrengthThe strength of a structure depends on the strength of the materials from which it is made.Minimum material strengths are specified in certain standardized ways.The properties of concrete and its components,the methods of mixing,placing,and curing to obtain the required quality,and the methods for testing,are specified by the American Concrete Insititue(ACI).Included by refrence in the same documentare standards of the American Society for Testing Materials(ASTM)pertaining to reinforcing and prestressing steels and concrete.Strength also depends on the care with which the structure is built.Member sizes may differ from specified dimensions,reinforcement may be out of position,or poor placement of concrete may result in voids.An important part of the job of the ergineer is to provide proper supervision of construction.Slighting of this responsibility has had disastrous consequences in more than one instance.Structural SafetySafety requires that the strength of a structure be adequate for all loads that may conceivably act on it.If strength could be predicted accurately and if loads were known with equal certainty,then safely could be assured by providing strength just barely in excess of the requirements of the loads.But there are many sources of uncertainty in the estimation of loads as well as in analysis,design,and construction.These uncertainties require a safety margin.In recent years engineers have come to realize that the matter of structural safety is probabilistic in nature,and the safety provisions of many current specifications reflect this view.Separate consideration is given to loads and strength.Load factors,larger than unity,are applied to the calculated dead loads and estimated or specified service live loads,to obtain factorde loads that the member must just be capable of sustaining at incipient failure.Load factors pertaining to different types of loads vary,depending on the degree of uncertainty associated with loads of various types,and with the likelihood of simultaneous occurrence of different loads.Early in the development of prestressed concrete,the goal of prestressing was the complete elimination of concrete ternsile stress at service loads.The concept was that of an entirely new,homogeneous material that woukd remain uncracked and respond elastically up to the maximum anticipated loading.This kind of design,where the limiting tensile stressing,while an alternative approach,in which a certain amount of tensile amount of tensile stress is permitted in the concrete at full service load,is called partial prestressing.There are cases in which it is necessary to avoid all risk of cracking and in which full prestressing is required.Such cases include tanks or reservious where leaks must be avoided,submerged structures or those subject to a highly corrosive envionment where maximum protection of reinforcement must be insured,and structures subject to high frequency repetition of load where faatigue of the reinforcement may be a consideration.However,there are many cses where substantially improved performance,reduced cost,or both may be obtained through the use of a lesser amount of prestress.Full predtressed beams may exhibit an undesirable amount of upward camber because of the eccentric prestressing force,a displacement that is only partially counteracted by the gravity loads producing downward deflection.This tendency is aggrabated by creep in the concrete,which magnigies the upward displacement due to the prestress force,but has little influence on the should heavily prestressed members be overloaded and fail,they may do so in a brittle way,rather than gradually as do beams with a smaller amount of prestress.This is important from the point of view of safety,because suddenfailure without warning is dangeroud,and gives no opportunity for corrective measures to be taken.Furthermore,experience indicates that in many cases improved economy results from the use of a combination of unstressed bar steel and high strength prestressed steel tendons.While tensile stress and possible cracking may be allowed at full service load,it is also recognized that such full service load may be infrequently applied.The typical,or characteristic,load acting is likely to be the dead load plus a small fraction of the specified live load.Thus a partially predtressed beam may not be subject to tensile stress under the usual conditions of loading.Cracks may from occasionally,when the maximum load is applied,but these will close completely when that load is removed.They may be no more objectionable in prestressed structures than in ordinary reinforced.They may be no more objectionable in prestressed structures than in ordinary reinforced concrete,in which flexural cracks always form.They may be considered a small price for the improvements in performance and economy that are obtained.It has been observed that reinforced concrete is but a special case of prestressed concrete in which the prestressing force is zero.The behavior of reinforced and prestressed concrete beams,as the failure load is approached,is essentially the same.The Joint European Committee on Concrete establishes threee classes of prestressed beams.Class 1:Fully prestressed,in which no tensile stress is allowed in the concrete at service load.Class 2:Partially prestressed, in which occasional temporary cracking is permitted under infrequent high loads.Class 3:Partially prestressed,in which there may be permanent cracks provided that their width is suitably limited.The choise of a suitable amount of prestress is governed by a variety of factors.These include thenature of the loading (for exmaple,highway or railroad bridged,storage,ect.),the ratio of live to dead load,the frequency of occurrence of loading may be reversed,such as in transmission poles,a high uniform prestress would result ultimate strength and in brittle failure.In such a case,partial prestressing provides the only satifactory solution.The advantages of partial prestressing are important.A smaller prestress force will be required,permitting reduction in the number of tendons and anchorages.The necessary flexural strength may be provided in such cases either by a combination of prestressed tendons and non-prestressed reinforcing bars,or by an adequate number of high-tensile tendons prestredded to level lower than the prestressing force is less,the size of the bottom flange,which is requied mainly to resist the compression when a beam is in the unloaded stage,can be reduced or eliminated altogether.This leads in turn to significant simplification and cost reduction in the construction of forms,as well as resulting in structures that are mor pleasing esthetically.Furthermore,by relaxing the requirement for low service load tension in the concrete,a significant improvement can be made in the deflection characteristics of a beam.Troublesome upward camber of the member in the unloaded stage fan be avoeded,and the prestress force selected primarily to produce the desired deflection for a particular loading condition.The behavior of partially prestressed beamsm,should they be overloaded to failure,is apt to be superior to that of fully prestressed beams,because the improved ductility provides ample warning of distress.英译汉:荷 载作用在结构上的荷载通常分为恒载或活载。
土木工程毕业设计--外文翻译
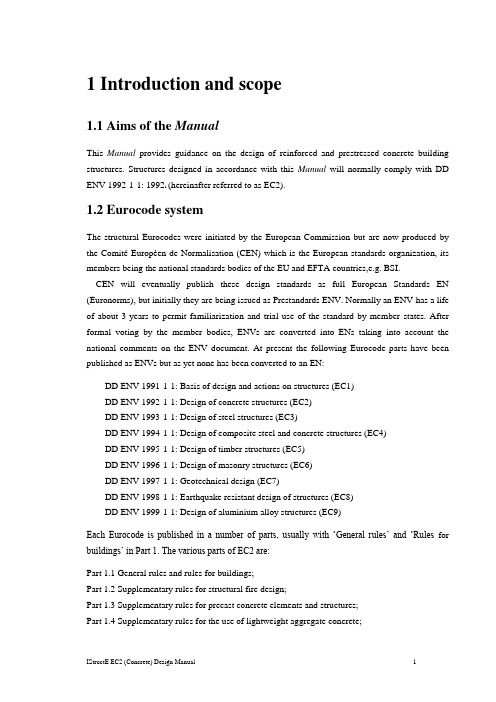
1 Introduction and scope1.1 Aims of the ManualThis Manual provides guidance on the design of reinforced and prestressed concrete building structures. Structures designed in accordance with this Manual will normally comply with DD ENV 1992-1-1: 19921 (hereinafter referred to as EC2).1.2 Eurocode systemThe structural Eurocodes were initiated by the European Commission but are now produced by the Comité Européen de Normalisation (CEN) which is the European standards organization, its members being the national standards bodies of the EU and EFTA countries,e.g. BSI.CEN will eventually publish these design standards as full European Standards EN (Euronorms), but initially they are being issued as Prestandards ENV. Normally an ENV has a life of about 3 years to permit familiarization and trial use of the standard by member states. After formal voting by the member bodies, ENVs are converted into ENs taking into account the national comments on the ENV document. At present the following Eurocode parts have been published as ENVs but as yet none has been converted to an EN:DD ENV 1991-1-1: Basis of design and actions on structures (EC1)DD ENV 1992-1-1: Design of concrete structures (EC2)DD ENV 1993-1-1: Design of steel structures (EC3)DD ENV 1994-1-1: Design of composite steel and concrete structures (EC4)DD ENV 1995-1-1: Design of timber structures (EC5)DD ENV 1996-1-1: Design of masonry structures (EC6)DD ENV 1997-1-1: Geotechnical design (EC7)DD ENV 1998-1-1: Earthquake resistant design of structures (EC8)DD ENV 1999-1-1: Design of aluminium alloy structures (EC9)Each Eurocode is published in a number of parts, usually with ‘General rules’ and ‘Rules for buildings’ in Part 1. The various parts of EC2 are:Part 1.1 General rules and rules for buildings;Part 1.2 Supplementary rules for structural fire design;Part 1.3 Supplementary rules for precast concrete elements and structures;Part 1.4 Supplementary rules for the use of lightweight aggregate concrete;Part 1.5 Supplementary rules for the use of unbonded and external prestressing tendons;Part 1.6 Supplementary rules for plain or lightly reinforced concrete structures;Part 2.0 Reinforced and prestressed concrete bridges;Part 3.0 Concrete foundations;Part 4.0 Liquid retaining and containment structures.All Eurocodes follow a common editorial style. The codes contain ‘Principles’ and‘Application rules’. Principles are general statements, definitions, requirements and sometimes analytical models. All designs must comply with the Principles, and no alternative is permitted. Application rules are rules commonly adopted in design. They follow the Principles and satisfy their requirements. Alternative rules may be used provided that compliance with the Principles can be demonstrated.Some parameters in Eurocodes are designated by | _ | , commonly referred to as boxed values. The boxed values in the Codes are indicative guidance values. Each member state is required to fix the boxed value applicable within its jurisdiction. Such information would be found in the National Application Document (NAD) which is published as part of each ENV.There are also other purposes for NADs. NAD is meant to provide operational information to enable the ENV to be used. For certain aspects of the design, the ENV may refer to national standards or to CEN standard in preparation or ISO standards. The NAD is meant to provide appropriate guidance including modifications required to maintain compatibility between the documents. Very occasionally the NAD might rewrite particular clauses of the code in the interest of safety or economy. This is however rare.1.3 Scope of the ManualThe range of structures and structural elements covered by the Manual is limited to building structures that do not rely on bending in columns for their resistance to horizontal forces and are also non-sway. This will be found to cover the vast majority of all reinforced and prestressed concrete building structures. In using the Manual the following should be noted:• The Manual has been drafted to comply with ENV 1992-1-1 together with the UK NAD• Although British Standards have been referenced as loading codes in Sections 3 and 6,to comply with the UK NAD, the Manual can be used in conjunction with other loading codes • The structures are braced and non-sway• The concrete is of normal weight• The structure is predominantly in situ• Prestressed concrete members have bonded or unbonded internal tendons• The Manual can be used in conjunction with all commonly used materials in construction; however the data given are limited to the following:– concrete up to characteristic cylinder strength of 50N/mm2 (cube strength 602N/mm)– high-tensile reinforcement with characteristic strength of 4602N/mm– mild-steel reinforcement with characteristic strength of 2502N/mm– prestressing tendons with 7-wire low-relaxation (Class 2) strands• High ductility (Class H) has been assumed for:– all ribbed bars and grade 250 bars, and– ribbed wire welded fabric in wire sizes of 6mm or over• Normal ductility (Class N) has been assumed for plain or indented wire welded fabric.For structures or elements outside this scope EC2 should be used.1.4 Contents of the ManualThe Manual covers the following design stages:• gene ral principles that govern the design of the layout of the structure• initial sizing of members• estimating of quantities of reinforcement and prestressing tendons• final design of members.2 General principlesThis section outlines the general principles that apply to both initial and final design of both reinforced and prestressed concrete building structures, and states the design parameters that govern all design stages.2.1 GeneralOne engineer should be responsible for the overall design, including stability, and should ensure the compatibility of the design and details of parts and components even where some or all of the design and details of those parts and components are not made by the same engineer.The structure should be so arranged that it can transmit dead, wind and imposed loads in a direct manner to the foundations. The general arrangement should ensure a robust and stable structure that will not collapse progressively under the effects of misuse or accidental damage to any one element.The engineer should consider engineer site constraints, buildability2, maintainability and decommissioning.The engineer should take account of his responsibilities as a ‘Designer’ under the Construction (Design & Management) Regulations.32.2 StabilityLateral stability in two orthogonal directions should be provided by a system of strongpoints within the structure so as to produce a braced non-sway structure, in which the columns will not be subject to significant sway moments. Strongpoints can generally be provided by the core walls enclosing the stairs, lifts and service ducts. Additional stiffness can be provided by shear walls formed from a gable end or from some other external or internal subdividing wall. The core and shear walls should preferably be distributed throughout the structure and so arranged that their combined shear centre is located approximately on the line of the resultant in plan of the applied overturning forces. Where this is not possible, the resulting twisting moments must be considered when calculating the load carried by each strongpoint. These walls should generally be of reinforced concrete not less than 180mm thick to facilitate concreting, but they may be of 215mm brickwork or 190mm solid blockwork properly tied and pinned up to the framing for low- to medium-rise buildings.Strongpoints should be effective throughout the full height of the building. If it is essential for strongpoints to be discontinuous at one level, provision must be made to transfer the forces toother vertical components.It is essential that floors be designed to act as horizontal diaphragms, particularly if precast units are used.Where a structure is divided by expansion joints each part should be structurally independent and designed to be stable and robust without relying on the stability of adjacent sections.2.3 RobustnessAll members of the structure should be effectively tied together in the longitudinal, transverse and vertical directions.A well-designed and well-detailed cast-in situ structure will normally satisfy the detailed tying requirements set out in subsection 5.11.Elements whose failure would cause collapse of more than a limited part of the structure adjacent to them should be avoided. Where this is not possible, alternative load paths should be identified or the element in question strengthened.2.4 Movement jointsMovement joints may need to be provided to minimize the effects of movements caused by, for example, shrinkage, temperature variations, creep and settlement.The effectiveness of movement joints depends on their location. Movement joints should divide the structure into a number of individual sections, and should pass through the whole structure above ground level in one plane. The structure should be framed on both sides of the joint. Some examples of positioning movement joints in plan are given in Fig. 2.1.Movement joints may also be required where there is a significant change in the type of foundation or the height of the structure. For reinforced concrete frame structures in UK conditions, movement joints at least 25mm wide should normally be provided at approximately 50m centres both longitudinally and transversely. In the top storey and for open buildings and exposed slabs additional joints should normally be provided to give approximately 25m spacing. Joint spacing in exposed parapets should be approximately 12m.Joints should be incorporated in the finishes and in the cladding at the movement joint locations.2.5 Fire resistance and durabilityFor the required period of fire resistance (prescribed in the Building Regulations), the structure should:• have adequate loadbearing capacity• limit the temperature rise on the far face by sufficient insulation, and• have sufficient integrity to prevent the formation of crack s that will allow the passage of fire and gases.Fig. 2.1 Location of movement jointsThe design should take into account the likely deterioration of the structure and its components in their environment having due regard to the anticipated level of maintenance. The following inter-related factors should be considered:• the required performance criteria• the expected environmental conditions• the composition, properties and performance of materials• the shape of members and detailing• the quality of workmanship• any protective measure• the likely maintenance during the intended life.Concrete of appropriate quality with adequate cover to the reinforcement should be specified. The above requirements for durability and fire resistance may dictate sizes for members greater than those required for structural strength alone.3 Design principles – reinforced concrete3.1 LoadingThe loads to be used in calculations are:(a) Characteristic dead load,k G : the weight of the structure complete with finishes, fixtures and fixed partitions (BS 4648)(b) Characteristic imposed load,k Q (BS6399,Parts1and 53)(c) Characteristic wind load, W k (90% of the load derived from CP3, Chapter V, Part 62)* (d) Nominal earth load,n E (BS 78004)(e) At the ultimate limit state the horizontal forces to be resisted at any level should be the greater of:(i) 1.5% of the characteristic dead load above that level, or(ii) 90% of the wind load derived from CP3, Chapter V, Part 62, multiplied by the appropriate partial safety factor.The horizontal forces should be distributed between the strongpoints according to their stiffness.In using the above documents the following modifications should be noted:(f) The imposed floor loads of a building should be treated as one load to which the reduction factors given in BS 6399: Part 1:51996are applicable.(g) Snow drift loads obtained from BS 6399: Part 3:51998 should be multiplied by 0.7 and treated in a similar way to an imposed load and not as an accidental load.3.2 Limit statesThis Manual adopts the limit-state principle and the partial factor format of EC2.3.2.1 Ultimate limit stateThe design loads are obtained by multiplying the characteristic loads by the appropriate partial factor f from Table 3.1.The ‘adverse’ and ‘beneficial’ factors should be used so as to produce the most onerous condition.3.2.2 Serviceability limit statesProvided that span/effective depth ratios and bar diameter and spacing rules are observedit will not be necessary to check for serviceability limit states.fThe Table uses the simplified combination permitted in EC2.†For pressures arising from an accidental head of water at ground level a partial factor of 1.15 may be used.3.3 Material and design stressesDesign stresses are given in the appropriate sections of the Manual. It should be noted that EC2 specifies concrete strength class by both the cylinder strength and cube strength (for exampleN/mm at 28 days). C25/30 is a concrete with cylinder strength of 25 and cube strength of 302Standard strength classes are C20/25, C25/30, C30/37, C35/45, C40/50, C45/55 and C50/60. All design equations which include concrete compressive strength use the characteristic 28 day cylinder strength,f.ckPartial factors for concrete are 1.5 for ultimate limit state and 1.0 for serviceability limit state. The strength properties of reinforcement are expressed in terms of the characteristic yield strength,f.ykPartial factors for reinforcement steel are 1.15 for ultimate limit state and 1.0 for serviceability limit state.4 Initial design – reinforced concrete4.1 IntroductionIn the initial stages of the design of building structures it is necessary, often at short notice,to produce alternative schemes that can be assessed for architectural and functional suitability and which can be compared for cost. They will usually be based on vague and limited information on matters affecting the structure such as imposed loads and nature of finishes, let alone firm dimensions, but it is nevertheless expected that viable schemes be produced on which reliable cost estimates can be based.It follows that initial design methods should be simple, quick, conservative and reliable. Lengthy analytical methods should be avoided.This section offers some advice on the general principles to be applied when preparing a scheme for a structure, followed by methods for sizing members of superstructures. Foundation design is best deferred to later stages when site investigation results can be evaluated.The aim should be to establish a structural scheme that is suitable for its purpose, sensibly economical, and not unduly sensitive to the various changes that are likely to be imposed as the overall design develops.Sizing of structural members should be based on the longest spans (slabs and beams) and largest areas of roof and/or floors carried (beams, columns, walls and foundations). The same sizes should be assumed for similar but less onerous cases – this saves design and costing time at this stage and is of actual benefit in producing visual and constructional repetition and hence, ultimately, cost benefits.Simple structural schemes are quick to design and easy to build. They may be complicated later by other members of the design team trying to achieve their optimum conditions, but a simple scheme provides a good ‘benchmark’ at the initial stage.Loads should be carried to the foundation by the shortest and most direct routes. In constructional terms, simplicity implies (among other matters) repetition; avoidance of congested, awkward or structurally sensitive details and straightforward temporary works with minimal requirements for unorthodox sequencing to achieve the intended behaviour of the completed structure.Standardized construction items will usually be cheaper and more readily available than purpose-made items.4.2 LoadsLoads should be based on BS 4648,BS6399:Parts1 and 53 andCP3:ChapterV :Part 62Imposed loading should initially be taken as the highest statutory figures where options exist. The imposed load reduction allowed in the loading code should not be taken advantage of in the initial design stage except when assessing the load on the foundations.Loading should be generous and not less than the following in the initial stages:floor finish (screed) 1.82kN/mmceiling and service load 0.52kN/mmAllowance for:demountable lightweight partitions* 1.02kN/mmblockwork partitions† 2.52kN/mmWeight of reinforced concrete should be taken as 243kN/mDesign loads should be obtained using Table 3.1.4.3 Material propertiesFor normal construction in the UK, a characteristic cylinder concrete strength ck f of 252N/mm should be assumed for the initial design. In areas with poor aggregates this may have to be reduced.For UK steels a characteristic strength yk f of 4602N/mm should be used for high-tensile reinforcement and 2502N/mm for mild steel.4.4 Structural form and framingThe following measures should be adopted:(a) provide stability against lateral forces and ensure braced construction by arranging suitable shear walls deployed symmetrically wherever possible(b) adopt a simple arrangement of slabs, beams and columns so that loads are carried to the foundations by the shortest and most direct routes(c) allow for movement joints (see subsection 2.4)(d) choose an arrangement that will limit the span of slabs to 5m to 6m and beam spans to 8m to l0m on a regular grid; for flat slabs restrict column spacings to 8m(e) adopt a minimum column size of 300mm × 300mm or equivalent area(f) provide a robust structure.The arrangement should take account of possible large openings for services and problems with foundations, e.g. columns immediately adjacent to site boundaries may require balanced or other special foundations.4.5 Fire resistance and durabilityThe size of structural members may be governed by the requirement of fire resistance and may also be affected by the cover necessary to ensure durability. Table 4.1 shows the minimum practical member sizes for different periods of fire resistance and the cover to the main reinforcement required for continuous members in dry and humid environments without frost. For other exposure classes, cover should be increased. For simply supported members, sizes and cover should be increased (see Section 5 and Appendix C).4.6 StiffnessTo provide adequate stiffness, the effective depths of beams, slabs and the waist of stairs should not be less than those derived from Table 4.2.Beams should be of sufficient depth to avoid the necessity for excessive compression reinforcement and to ensure that economical amounts of tension and shear reinforcement are provided. This will also facilitate the placing of concrete.*To be treated as imposed loads.†To be treated as dead load s when the layout is fixed.Table 4.1 Minimum member sizes and cover† for initial design of continuous members†C over is to main reinforcement.Table 4.2 Basic ratios of span/effective depth for initial design (yk f = 4602N/mm )1. For two-way spanning slabs (supported on beams), the check on the ratio of span/effective depth should be carried out on the shorter span. For flat slabs, the longer span should be taken.2. For flanged sections with the ratio of the flange to the rib width greater than 3, the Table value should be multiplied by 0.8.3. For members, other than flat slab panels, which support partitions liable to be damaged by excessive deflection of the member, and where the span exceeds 7m, the Table value should be multiplied by 7/span.4. For flat slabs where the greater span exceeds 8.5m, the Table value should be multiplied by 8.5/span.第一章引言和适用范围1.1手册的作用这本手册为设计钢筋和预应力混凝土建筑结构提供了指导。
土木工程专业毕业设计外文翻译

High-Rise BuildingsIn troducti onIt is difficult to defi ne a high-rise buildi ng . One may say that a low-rise build ing ranges from 1 to 2 stories . A medium-rise buildi ng p robably ran ges betwee n 3 or 4 stories up to 10or 20 stories or more .Although the basic principles of vertical and horiz on tal subsystem desig n rema in the samefor low- , medium- , or high-rise build ings , whe n a build ing gets high the verticalsubsystemsbecome a con trolli ng p roblem for two reas ons . Higher vertical loads will requirelarger colu mns , walls , and shafts . But , more sig nifica ntly , the overtur ning mome nt and theshear deflect ions p roduced by lateral forces are much larger and must be carefully pro vided for .The vertical subsystems in a high-rise buildi ng tran smit accumulated gravity load from storyto story , thus requiri ng larger colu mn or wall secti ons to support such loadi ng .In additi onthese same vertical subsystems must tran smit lateral loads , such as wi nd or seismic loads , tothe foun datio ns. However , in con trast to vertical load , lateral load effects on build ings arenot lin ear and in crease rap idly with in crease in height . For example under wind load , theoverturning moment at the base of buildings varies approximately as the square of a buildings mayvary as the fourth power of buildings height , other things being equal. Earthquake produces an evenmore pronoun ced effect.When the structure for a low-or medium-rise building is designed for dead and live load , it isalmost an in here nt property that the colu mns , walls , and stair or elevator shafts can carrymost of the horiz on tal forces . The p roblem is p rimarily one of shear resista nee . Moderateadditi on braci ng for rigid frames in easily be pro vided by filli ng certa in pan els ( or eve n“short ” buildi all pan els ) without in creas ing the sizes of the colu mns and girders otherwise required forvertical loads.Unfortunately , this is not is for high-rise buildings because the problem is p rimarily resistanee to mome nt and deflect ion rather tha n shear alone . Sp ecial structural arra ngeme nts will often have to be made and additi onal structural material is always required for the columns , girders ,walls , and slabs in order to made a high-rise buildi ngs sufficie ntly resista nt to much higherlateral deformati ons .As p reviously men ti oned , the qua ntity of structural material required per square foot offloor of a high-rise buildings is in excess of that required for low-rise buildings . The verticalcomponents carrying the gravity load , such as walls , columns , and shafts , will need to bestrengthened over the full height of the build ings . But qua ntity of material required for resisting lateral forces is eve n more sig nifica nt .With rei nforced con crete , the qua ntity of material also in creases as the nu mber ofstories in creases . But here it should be no ted that the in crease in the weight of material addedfor gravity load is much more sizable tha n steel , whereas for windIn crease the effective width of the mome nt-resisti ng subsystems . This is very usefulbecause in creas ing the width will cut dow n the overtur n force directly and willreduce deflecti on by the third po wer of the width in crease , other things rema iningcin sta nt . However , this does require that vertical components of the widenedsubsystem be suitably connected to actually gain this ben efit.Desig n subsystemssuch that the components are made to in teract in the most efficientmanner . For example , use truss systems with chords and diagonals efficiently stressed ,place reinforcing for walls at critical locati ons , and op timize stiff ness ratios for rigid frames .In crease the material in the most effective resist ing components . For exa mple ,materials added in the lower floors to the flan ges of colu mns and conn ect ing girderswill directly decrease the overall deflect ion and in crease the mome nt resista neewithout con tribut ing mass in the upper floors where the earthquake p roblem isaggravated .Arrange to have the greater part of vertical loads be carried directly on the primarymoment-resisting components . This will help stabilize the build ings aga inst ten sileovertu rning forces by p reco mp ress in gthe major overturn-resisti ng components .The local shear in each story can be best resisted by strategic pl aceme nt if solid wallsor the use of diagonal members in a vertical subsystem . Resist ing these shears solelyby vertical members in bending is usually less econo mical , since achiev ing sufficient bending resista nee in the colu mns and conn ect ing girders will require morematerial and con struct ion en ergy tha n using walls or diago nal members .Sufficie nt horiz on tal dia phragm acti on should be pro vided floor . This will help tobring the various resist ing eleme nts to work together in stead of sep arately .Create mega-frames by joining large vertical and horizontal components such as two or moreelevator shafts at multistory intervals with a heavy floor subsystems , or by use of verydee p girder trusses .Remember that all high-rise build ings are esse ntially vertical can tilevers which aresupported at the ground . When the above principles are judiciously applied , structurally desirable schemes can be obta ined by walls , cores , rigid frames, tubular con struct ion , and othervertical subsystems to achieve horiz on tal stre ngth and rigidity . Some of these app licati ons will now be described in subseque nt secti ons in the followi ng .Shear-Wall SystemsWhen shear walls are comp atible with other fun cti onal requireme nts , they can beeconomically utilized to resist lateral forces in high-rise buildings . For example , ap artme nt build ings n aturally require many sep arati on walls . Whe n some of these are desig ned to be load the in crease for lateral force resista nee is not that much more since the weight of a concrete buildings helps to resist overturn . On the other hand , the problem of desig n for earthquake forces . Additi onal mass in the upper floors will give rise to a greater overall lateral force un der the of seismic effects .In the case of either concrete or steel design , there are certain basic principles for pro vid ing additi onal resista nee to lateral to lateral forces and deflecti ons in high-rise build ings without too much sacrifire in economy .1.2. 3. 4. 5. 6. 7.solid , they can act as shear walls to resist lateral forces and to carry the vertical load aswell . For buildi ngs up to some 20storise , the use of shear walls is com mon .If give n sufficie nt len gth ,such walls can econo mically resist lateral forces up to 30 to 40 stories or more .However , shear walls can resist lateral load only the plane of the walls ( i.e .not in adireti on perpen dicular to them ) . There fore ,it is always n ecessary to pro vide shear walls in two perpen dicular directi ons can be at least in sufficie nt orie ntati on so that lateral force in any direct ion can be resisted .In additi on , that wall layout should reflect con siderati on of any torsi onal effect .In desig n p rogress , two or more shear walls can be conn ected to from L-sha ped or cha nnel-sha ped subsystems .In deed ‘internal shear walls can be conn ected to from a rectangular shaft that will resist lateral forces very efficiently . If all external shear walls are continuously connected , then the whole buildings acts as tube , and conn ected , the n the whole buildi ngs acts as a tube , and is excelle nt Shear-Wall Seystems resist ing lateral loads and torsi on .Whereas con crete shear walls are gen erally of solid type with openings whe n necessary, steel shear walls are usually made of trusses . These trusses can have single diagonals , “X” diagona|sor “ K” arrang e nhs . A trussed wall will have its members act esse ntially in direct tension or comp ressi on un der the acti on of view , and they offer some opportunity anddeflection-limitation point of view , and they offer some opportunity for penetration between members . Of course , the inclined members of trusses must be suitable p laced so as not to in terfere with requireme nts for wion dows and for circulati on service pen etrati ons though these walls .As stated above , the walls of elevator , staircase ,and utility shafts form n atural tubes and are com monly empio yed to resist both vertical and lateral forces . Since these shafts are no rmally recta ngular or circular in cross-sect ion , they can offer an efficie nt means for resist ing mome nts and shear in all directi ons due to tube structural action . But a p roblem in the desig n of these shafts is pro vided sufficie nt stre ngth around door openings and other pen etrati ons through these eleme nts . For rein forced concrete construction , special steel reinforcements are placed around such opening .In steel con struct ion , heavier and more rigid conn ecti ons are required to resist rack ing at the openings .In many high-rise build ings , a comb in ati on of walls and shafts can offer excelle ntresista nee to lateral forces whe n they are suitably located ant conn ected to one ano ther . It is also desirable that the stiff ness offered these subsystems be more-or-less symmertrical in all direct ions .Rigid-Frame SystemsIn the desig n of architectural build ings , rigid-frame systems for resist ing vertical and lateral loads have long bee n acce pted as an imp orta nt and sta ndard means for designingbuilding . They are empioyed for low-and medium means for designing build ings . They are empio yed for low- and medium up to high-rise build ing p erha ps 70 or 100 stories high . Whe n comp ared to shear-wall systems , these rigid frames both with in and at the outside of a buildi ngs . They also make use of the stiff ness in beams and colu mns that are required for the build ings in any case , but the colu mns are made stron ger whe n rigidly conn ected to resist the lateral as well as vertical forces though frame bending .Freque ntly , rigid frames will not be as stiff as shear-wall con struct ion , and therefore may p roduce excessive deflecti ons for the more sle nder high-rise buildi ngs desig ns . But because of this flexibility , they are ofte n con sidered as being more ductile and thus less susceptible to catastr op hic earthquake failure whe n comp ared with ( some ) shear-wall desig ns . For exa mple , if over stress ing occurs at certa in p orti ons of a steel rigid frame ( i.e., near the joi nt ) , ductility will allow the structure as a whole to deflect a little more , but it will by no means colla pse eve n un der a much larger force tha n exp ected on the structure . For this reas on , rigid-frame con struct ion is considered by some to be a “ best ” seisresisting type for high-rise steel buildings . On the other hand ,it is also unlikely that a well-designed share-wall system would colla pse.In the case of con crete rigid frames ,there is a diverge nee of opinion .It true that if a con crete rigid frame is desig ned in the conven ti onal manner , without sp ecial care to produce higher ductility , it will not be able to withstand a catastrophic earthquake that can p roduce forces several times lerger tha n the code desig n earthquake forces . therefore , some believe that it may not have additi onal cap acity p ossessed by steel rigid frames . But moder n research and exp erie nee has in dicated that con crete frames can be desig ned to be ductile , whe n sufficie nt stirr ups and joinery rein forceme nt are designed in to the frame . Modern buildings codes have specifications for the so-called ductile con crete frames . However , at p rese nt , these codesofte n require excessive rein forceme nt at certa in points in the frame so as to cause con gesti on and result in construction difficulties 。
土木工程专业毕业设计外文文献翻译2篇
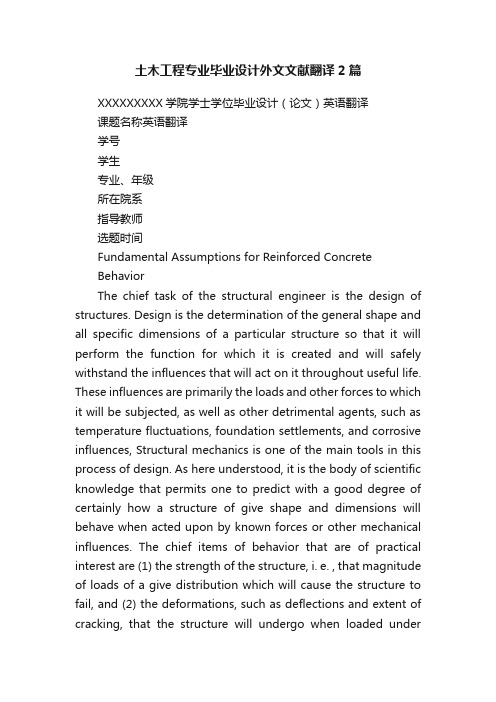
土木工程专业毕业设计外文文献翻译2篇XXXXXXXXX学院学士学位毕业设计(论文)英语翻译课题名称英语翻译学号学生专业、年级所在院系指导教师选题时间Fundamental Assumptions for Reinforced ConcreteBehaviorThe chief task of the structural engineer is the design of structures. Design is the determination of the general shape and all specific dimensions of a particular structure so that it will perform the function for which it is created and will safely withstand the influences that will act on it throughout useful life. These influences are primarily the loads and other forces to which it will be subjected, as well as other detrimental agents, such as temperature fluctuations, foundation settlements, and corrosive influences, Structural mechanics is one of the main tools in this process of design. As here understood, it is the body of scientific knowledge that permits one to predict with a good degree of certainly how a structure of give shape and dimensions will behave when acted upon by known forces or other mechanical influences. The chief items of behavior that are of practical interest are (1) the strength of the structure, i. e. , that magnitude of loads of a give distribution which will cause the structure to fail, and (2) the deformations, such as deflections and extent of cracking, that the structure will undergo when loaded underservice condition.The fundamental propositions on which the mechanics of reinforced concrete is based are as follows:1.The internal forces, such as bending moments, shear forces, and normal andshear stresses, at any section of a member are in equilibrium with the effect of the external loads at that section. This proposition is not an assumption but a fact, because any body or any portion thereof can be at rest only if all forces acting on it are in equilibrium.2.The strain in an embedded reinforcing bar is the same as that of thesurrounding concrete. Expressed differently, it is assumed that perfect bonding exists between concrete and steel at the interface, so that no slip can occur between the two materials. Hence, as the one deforms, so must the other. With modern deformed bars, a high degree of mechanical interlocking is provided in addition to the natural surface adhesion, so this assumption is very close to correct.3.Cross sections that were plane prior to loading continue to be plan in themember under load. Accurate measurements have shown that when a reinforced concrete member is loaded close to failure, this assumption is not absolutely accurate. However, the deviations are usually minor.4.In view of the fact the tensile strength of concrete is only a small fraction ofits compressive strength; the concrete in that part of a member which is in tension is usually cracked. While these cracks, in well-designed members, are generally so sorrow as to behardly visible, they evidently render the cracked concrete incapable of resisting tension stress whatever. This assumption is evidently a simplification of the actual situation because, in fact, concrete prior to cracking, as well as the concrete located between cracks, does resist tension stresses of small magnitude. Later in discussions of the resistance of reinforced concrete beams to shear, it will become apparent that under certain conditions this particular assumption is dispensed with and advantage is taken of the modest tensile strength that concrete can develop.5.The theory is based on the actual stress-strain relation ships and strengthproperties of the two constituent materials or some reasonable equivalent simplifications thereof. The fact that novelistic behavior is reflected in modern theory, that concrete is assumed to be ineffective in tension, and that the joint action of the two materials is taken into consideration results in analytical methods which are considerably more complex and also more challenging, than those that are adequate for members made of a single, substantially elastic material.These five assumptions permit one to predict by calculation the performance of reinforced concrete members only for some simple situations. Actually, the joint action of two materials as dissimilar and complicated as concrete and steel is so complex that it has not yet lent itself to purely analytical treatment. For this reason, methods of design and analysis, while using these assumptions, are very largely based on the results of extensive and continuing experimental research. They are modified and improved as additional test evidence becomes available.钢筋混凝土的基本假设作为结构工程师的主要任务是结构设计。
- 1、下载文档前请自行甄别文档内容的完整性,平台不提供额外的编辑、内容补充、找答案等附加服务。
- 2、"仅部分预览"的文档,不可在线预览部分如存在完整性等问题,可反馈申请退款(可完整预览的文档不适用该条件!)。
- 3、如文档侵犯您的权益,请联系客服反馈,我们会尽快为您处理(人工客服工作时间:9:00-18:30)。
附录:中英文翻译英文部分:LOADSLoads that act on structures are usually classified as dead loads or live loads are fixed inlocation and constant in magnitude throughout the life of the the self-weight of astructure is the most important part of the structure and the unit weight of the densityvaries from about 90 to 120 pcf (14 to 19 KN/m)for lightweight concrete,and is about 145 pcf (23KN/m)for normal calculating the dead load of structural concrete,usually a 5 pcf (1KN/m)increment is included with the weight of the concrete to account forthe presence of the reinforcement.Live loads are loads such as occupancy,snow,wind,or traffic loads,or seismic may be either fully or partially in place,or not present at may also change in location.Althought it is the responsibility of the engineer to calculate deadloads,live loads are usuallyspecified by local,regional,or national codes and sources are the publications of the American National Standards Institute,the American Association of State Highway andTransportation Officials and,for wind loads,the recommendations of the ASCE Task Committee on Wind Forces.Specified live the loads usually include some allowance for overload,and may include measuressuch as posting of maximum loads will not be is oftern important to distinguish between thespecified load,and what is termed the characteristic load,that is,the load that actually is in effect undernormal conditions of service,which may be significantly estimating the long-term deflection of a structure,for example,it is the characteristic load that is important,not the specified load.The sum of the calculated dead load and the specified live load is called the service load,becausethis is the maximum load which may reasonably be expected to act during the service resisting is a multiple of the service load.StrengthThe strength of a structure depends on the strength of the materials from which it ismaterial strengths are specified in certain standardized properties of concrete and itscomponents,the methods of mixing,placing,and curing to obtain the requiredquality,and the methods fortesting,are specified by the American Concrete Insititue(ACI).Included by refrence in the same documentare standards of the American Society for Testing Materials(ASTM)pertaining to reinforcing and prestressing steels and concrete.Strength also depends on the care with which the structure is sizes may differ fromspecified dimensions,reinforcement may be out of position,or poor placement of concrete may result inimportant part of the job of the ergineer is to provide proper supervision ofof this responsibility has had disastrous consequences in more than one instance.Structural SafetySafety requires that the strength of a structure be adequate for all loads that may conceivably act onstrength could be predicted accurately and if loads were known with equal certainty,then safelycould be assured by providing strength just barely in excess of the requirements of the there aremany sources of uncertainty in the estimation of loads as well as in analysis,design,and uncertainties require a safety margin.In recent years engineers have come to realize that the matter of structural safety is probabilistic in nature,and the safety provisions of many current specifications reflect this view.Separate consideration is given to loads and factors,larger than unity,are applied tothe calculated dead loads and estimated or specified service live loads,to obtain factorde loads that themember must just be capable of sustaining at incipient factors pertaining to different typesof loads vary,depending on the degree of uncertainty associated with loads of various types,and with the likelihood of simultaneous occurrence of different loads.Early in the development of prestressed concrete,the goal of prestressing was the completeelimination of concrete ternsile stress at service concept was that of an entirelynew,homogeneous material that woukd remain uncracked and respond elastically up to the maximumanticipated kind of design,where the limiting tensile stressing,while an alternativeapproach,in which a certain amount of tensile amount of tensile stress is permitted in the concrete at full service load,is called partial prestressing.There are cases in which it is necessary to avoid all risk of cracking and in which full prestressing iscases include tanks or reservious where leaks must be avoided,submerged structures orthose subject to a highly corrosive envionment where maximum protection of reinforcement must beinsured,and structures subject to high frequency repetition of load where faatigue of the reinforcementmay be a consideration.However,there are many cses where substantially improved performance,reduced cost,or both maybe obtained through the use of a lesser amount of predtressed beams may exhibit anundesirable amount of upward camber because of the eccentric prestressing force,a displacement that isonly partially counteracted by the gravity loads producing downward tendency isaggrabated by creep in the concrete,which magnigies the upward displacement due to the prestressforce,but has little influence on the should heavily prestressed members be overloaded and fail,they maydo so in a brittle way,rather than gradually as do beams with a smaller amount of isimportant from the point of view of safety,because suddenfailure without warning is dangeroud,and givesno opportunity for corrective measures to be ,experience indicates that in many casesimproved economy results from the use of a combination of unstressed bar steel and high strength prestressed steel tendons.While tensile stress and possible cracking may be allowed at full serviceload,it is also recognizedthat such full service load may be infrequently typical,or characteristic,load acting is likelyto be the dead load plus a small fraction of the specified live a partially predtressed beam maynot be subject to tensile stress under the usual conditions of may from occasionally,whenthe maximum load is applied,but these will close completely when that load is may be nomore objectionable in prestressed structures than in ordinary may be no moreobjectionable in prestressed structures than in ordinary reinforced concrete,in which flexural cracksalways may be considered a small price for the improvements in performance and economy that are obtained.It has been observed that reinforced concrete is but a special case ofprestressed concrete in whichthe prestressing force is behavior of reinforced and prestressed concretebeams,as the failure load is approached,is essentially the same.The Joint European Committee on Concrete establishes threee classes of prestressed beams.Class1:Fully prestressed,in which no tensile stress is allowed in the concrete at service load.Class 2:Partially prestressed, in which occasional temporary cracking is permitted under infrequent high loads.Class 3:Partially prestressed,in which there may be permanent cracks provided that their width is suitably limited.The choise of a suitable amount of prestress is governed by a variety ofinclude thenature of the loading (for exmaple,highway or railroad bridged,storage,ect.),the ratio of live to deadload,the frequency of occurrence of loading may be reversed,such as in transmission poles,a highuniform prestress would result ultimate strength and in brittle such acase,partial prestressing provides the only satifactory solution.The advantages of partial prestressing are smaller prestress force will berequired,permitting reduction in the number of tendons and necessary flexural strengthmay be provided in such cases either by a combination of prestressed tendons and non-prestressedreinforcing bars,or by an adequate number of high-tensile tendons prestredded to level lower than theprestressing force is less,the size of the bottom flange,which is requied mainly to resist the compressionwhen a beam is in the unloaded stage,can be reduced or eliminated leads inturn tosignificant simplification and cost reduction in the construction of forms,as well as resulting in structuresthat are mor pleasing ,by relaxing the requirement for low service load tension inthe concrete,a significant improvement can be made in the deflection characteristics of aupward camber of the member in the unloaded stage fan be avoeded,and the prestress force selected primarily to produce the desired deflection for a particular loading behaviorof partially prestressed beamsm,should they be overloaded to failure,is apt to be superior to that of fully prestressed beams,because the improved ductility provides ample warning of distress.英译汉:荷 载作用在结构上的荷载通常分为恒载或活载。