模具质量的高低的质量控制
模具质量控制要点

模具质量控制要点引言概述:模具在工业生产中起着至关重要的作用,对于产品的质量和生产效率有着直接的影响。
为了确保模具的质量,需要进行有效的质量控制。
本文将从五个大点出发,详细阐述模具质量控制的要点。
正文内容:1. 模具设计阶段的质量控制要点1.1 模具结构设计:模具结构的合理性直接关系到模具的使用寿命和生产效率。
要点包括:合理的结构布局、适当的材料选择、充分考虑模具的易制造性等。
1.2 模具尺寸设计:模具尺寸的准确性对于产品的精度和一致性至关重要。
要点包括:合理的尺寸公差设定、考虑材料的收缩率和变形等因素、使用先进的设计软件进行模拟分析等。
1.3 模具表面处理:模具表面的处理对于产品的外观和质量有着直接的影响。
要点包括:选择合适的表面处理方法、考虑模具表面的耐磨性和耐腐蚀性、保证表面的光洁度和平整度等。
2. 模具加工制造阶段的质量控制要点2.1 材料采购和检验:模具的质量直接关系到材料的质量。
要点包括:选择合适的材料供应商、进行材料的化学成分和力学性能检验、保证材料的一致性和可靠性等。
2.2 加工设备和工艺控制:模具的加工质量与加工设备和工艺密切相关。
要点包括:选择先进的加工设备、制定合理的加工工艺流程、加强工艺控制和监测等。
2.3 模具装配和调试:模具的装配和调试对于模具的使用效果和寿命有着重要影响。
要点包括:严格按照装配图纸进行装配、进行合理的调试和测试、保证模具的运行稳定性和可靠性等。
3. 模具使用阶段的质量控制要点3.1 模具保养和维护:模具的保养和维护对于延长模具的使用寿命和保证产品质量至关重要。
要点包括:定期进行模具的清洁和润滑、进行模具的磨损检查和更换、及时处理模具的故障和问题等。
3.2 模具使用环境控制:模具的使用环境对于模具的稳定性和寿命有着直接影响。
要点包括:控制模具的使用温度和湿度、避免模具受到腐蚀和污染、保证模具的使用环境清洁和干燥等。
3.3 模具使用记录和反馈:模具的使用记录和反馈对于改进模具设计和加工工艺有着重要意义。
如何采用质量控制防止模具损坏和加工偏差

如何采用质量控制防止模具损坏和加工偏差模具是工程制造领域中不可或缺的一部分。
如何采用质量控制措施来防止模具损坏和加工偏差,是一项需要重视的课题。
本文将介绍质量控制的相关概念、控制方法和实施步骤,帮助读者全面掌握质量控制的技巧和方法。
一、质量控制的概念质量控制是一种在加工制造过程中,利用各种手段对加工制造过程进行全面检测、分析和控制的方法。
在模具制造中,质量控制可以通过严格的材料选择、工艺要求和现场操作等方面来完成,以确保模具的质量和精度达到所需的要求。
二、质量控制的方法1.材料选择材料的选择直接影响着模具的使用寿命和加工精度。
因此,在模具制造中应该选择高质量的材料,以确保模具具有良好的性能和稳定性。
2.工艺要求工艺要求是指要求从材料加工到零件装配,整个制造过程中,加工精度和工艺参数的要求等。
严格的工艺要求可以减少模具加工偏差,提高模具的加工精度。
3.现场操作现场操作是指加工制造现场的管理和操作,包括现场环境、设备使用、工艺流程等。
加强现场操作的管理和管控可以有效地减少对模具的损坏和偏差,提高生产效率和产品质量。
三、质量控制的实施步骤1.分析和评估控制难度和风险在实施质量控制之前,需要对模具制造中可能面临的风险进行全面的分析和评估。
根据具体情况进行分类,并制定相应的控制措施。
2.设计详细的质量控制方案设计详细的质量控制方案是确保实施质量控制的关键。
在制定方案之前,可以参考其他企业或者行业的标准和成功经验,并结合自身实际情况,制定符合企业实际情况的控制方案。
3.实施质量控制方案在制定好控制方案之后,需要将方案落实到具体控制过程中,确保每一个控制环节落实到位。
同时,需要根据实际情况及时调整控制措施,确保模具具有良好的加工精度和使用寿命。
四、总结质量控制是确保模具质量的关键因素,需要从材料选择、工艺要求和现场操作等方面全面控制和优化。
实施质量控制需要从分析和评估、设计详细控制方案和实施方案等多个方面入手,并不断进行调整和拓展,以达到最终的优化效果。
模具质量的高低的质量控制

模具质量的高低的质量控制模具质量的高低是影响产品质量和生产效率的重要因素之一。
为了确保模具的高质量,需要进行严格的质量控制。
本文将介绍模具质量控制的标准格式,包括质量控制的目标、方法和流程。
一、质量控制的目标模具质量控制的目标是确保模具的精度、耐用性和稳定性,以满足产品的设计要求和生产需求。
具体目标包括:1. 尺寸精度控制:确保模具的尺寸精度在设计要求范围内,以保证产品的尺寸精度。
2. 表面质量控制:确保模具的表面光洁度和平整度符合产品的要求,以保证产品的外观质量。
3. 耐用性控制:确保模具在长时间使用过程中不发生损坏或磨损,以保证模具的寿命和生产效率。
4. 稳定性控制:确保模具在连续生产过程中保持稳定的性能和精度,以保证产品的一致性和稳定性。
二、质量控制的方法模具质量控制的方法包括以下几个方面:1. 原材料控制:选择合适的模具材料,并进行严格的原材料检验,确保材料的质量符合要求。
2. 工艺控制:制定合理的模具制造工艺,包括加工工艺和热处理工艺等,确保模具的加工精度和热处理效果。
3. 加工控制:采用先进的数控机床和加工设备进行模具加工,配合合适的刀具和切削参数,确保模具的加工精度和表面质量。
4. 检测控制:采用各种检测手段对模具进行全面的检测,包括三坐标测量、硬度测试、表面粗糙度测试等,确保模具的尺寸精度和表面质量。
5. 耐用性控制:进行模具的耐久性测试和寿命评估,通过模具试模和模具寿命试验,评估模具的耐用性和寿命。
三、质量控制的流程模具质量控制的流程包括以下几个步骤:1. 设计评审:在模具设计阶段,进行设计评审,确保设计符合产品的要求和工艺的可行性。
2. 原材料检验:对模具的原材料进行检验,包括化学成分检验、力学性能检验等,确保原材料质量符合要求。
3. 制造过程控制:在模具制造过程中,进行工艺控制和加工控制,确保模具的加工精度和表面质量。
4. 检测和测试:对模具进行全面的检测和测试,包括尺寸检测、表面质量检测、耐久性测试等,确保模具的质量符合要求。
模具质量的高低的质量控制

模具质量的高低的质量控制模具质量的高低是指模具在设计、创造和使用过程中是否符合规定的技术要求和质量标准。
模具质量的高低直接影响到产品的质量和生产效率,因此,对于模具质量的控制是非常重要的。
本文将从模具设计、创造和使用三个方面介绍模具质量的控制。
一、模具设计中的质量控制1. 材料选择:选择适合的材料是保证模具质量的关键。
根据模具的使用环境和要求,选择具有良好机械性能、耐磨性和耐腐蚀性的材料,如优质钢材。
2. 结构设计:模具的结构设计直接影响到产品的质量和生产效率。
合理的结构设计可以提高模具的使用寿命和生产效率,减少产品的缺陷和废品率。
设计时应考虑模具的强度、刚度、稳定性和易于加工等因素。
3. 工艺设计:在模具设计中,要合理设置模具的加工工艺,包括切削工艺、热处理工艺、表面处理工艺等。
通过合理的工艺设计,可以提高模具的加工精度和表面质量,保证模具的使用性能。
二、模具创造中的质量控制1. 创造工艺控制:创造工艺是模具创造的核心环节,包括铣削、车削、磨削、电火花等工艺。
在创造过程中,要控制好各道工序的工艺参数,确保模具的尺寸精度和表面质量。
2. 检测与修正:创造过程中,要进行严格的检测和修正。
通过使用各种检测设备和工具,对模具的尺寸、形状、表面质量等进行检测,及时发现和修正问题,保证模具的质量。
3. 质量管理体系:建立完善的质量管理体系是保证模具质量的关键。
通过制定和执行相关的质量管理制度和标准,明确责任和要求,加强对创造过程的监控和控制,提高模具的质量稳定性和一致性。
三、模具使用中的质量控制1. 维护保养:模具在使用过程中,要定期进行维护保养,包括清洁、润滑、防锈等。
通过定期的维护保养,可以延长模具的使用寿命,减少故障和损坏。
2. 使用规范:在使用模具时,要按照规范进行操作,避免过度使用或者不当使用导致模具的损坏。
同时,要定期对模具进行检查,发现问题及时处理,避免因小问题导致的大故障。
3. 数据分析:通过对模具使用过程中的数据进行分析,可以了解模具的使用情况和问题,及时采取措施进行改进和优化。
模具质量的高低的质量控制
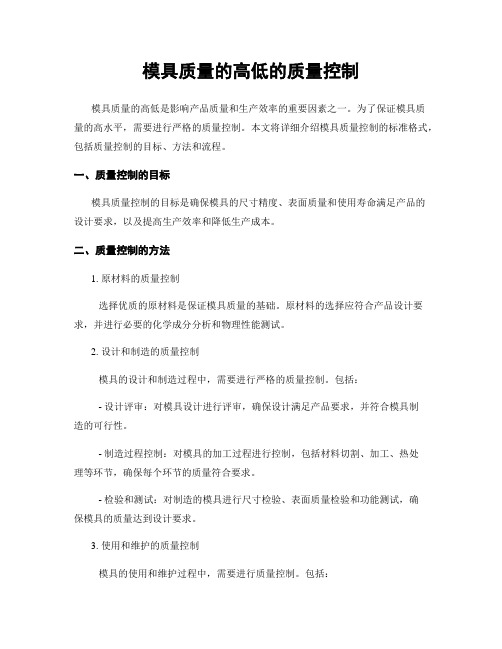
模具质量的高低的质量控制模具质量的高低是影响产品质量和生产效率的重要因素之一。
为了保证模具质量的高水平,需要进行严格的质量控制。
本文将详细介绍模具质量控制的标准格式,包括质量控制的目标、方法和流程。
一、质量控制的目标模具质量控制的目标是确保模具的尺寸精度、表面质量和使用寿命满足产品的设计要求,以及提高生产效率和降低生产成本。
二、质量控制的方法1. 原材料的质量控制选择优质的原材料是保证模具质量的基础。
原材料的选择应符合产品设计要求,并进行必要的化学成分分析和物理性能测试。
2. 设计和制造的质量控制模具的设计和制造过程中,需要进行严格的质量控制。
包括:- 设计评审:对模具设计进行评审,确保设计满足产品要求,并符合模具制造的可行性。
- 制造过程控制:对模具的加工过程进行控制,包括材料切割、加工、热处理等环节,确保每个环节的质量符合要求。
- 检验和测试:对制造的模具进行尺寸检验、表面质量检验和功能测试,确保模具的质量达到设计要求。
3. 使用和维护的质量控制模具的使用和维护过程中,需要进行质量控制。
包括:- 使用规范:制定模具的使用规范,包括使用条件、保养方法等,确保模具在使用过程中不受损坏。
- 维护保养:定期对模具进行保养,包括清洁、润滑、更换易损件等,延长模具的使用寿命。
- 故障分析:对模具出现的故障进行分析,找出故障原因,并采取相应的措施,避免类似故障再次发生。
三、质量控制的流程1. 原材料的质量控制流程- 选择优质的原材料供应商,与供应商建立长期稳定的合作关系。
- 对原材料进行化学成分分析和物理性能测试,确保原材料的质量符合要求。
- 对原材料进行入库检验,合格后方可使用。
2. 设计和制造的质量控制流程- 设计评审流程:组织设计评审会议,对模具设计进行评审,确保设计满足产品要求,并符合制造的可行性。
- 制造过程控制流程:制定制造工艺流程和质量控制计划,对模具的加工过程进行控制,确保每个环节的质量符合要求。
模具质量的高低的质量控制

模具质量的高低的质量控制一、引言模具是工业生产中不可或缺的工具,其质量的高低直接影响到产品的质量和生产效率。
因此,对模具质量的控制至关重要。
本文将详细介绍模具质量控制的标准格式,包括质量控制的目标、方法、流程和评估指标等。
二、质量控制的目标1. 提高模具的使用寿命:通过合理的设计和制造工艺,确保模具在使用过程中具有较长的寿命,减少更换模具的频率,降低生产成本。
2. 提高模具的精度和稳定性:确保模具制造的尺寸精度和形状精度达到设计要求,保证产品的质量稳定性。
3. 减少模具的故障率:通过严格的质量控制措施,降低模具的故障率,减少生产中的停机时间,提高生产效率。
三、质量控制的方法1. 设计阶段的质量控制:在模具设计阶段,应根据产品的要求和生产工艺的特点,合理选择材料和结构,确保模具的强度和稳定性。
2. 制造过程的质量控制:在模具制造过程中,应严格执行制造工艺规程,确保每个工序的质量要求得到满足,避免制造过程中的误差和缺陷。
3. 检测和测试的质量控制:在模具制造完成后,应进行严格的检测和测试,包括尺寸测量、材料检验、功能测试等,确保模具的质量符合设计要求。
四、质量控制的流程1. 设计阶段的质量控制流程:a) 确定模具的使用要求和生产工艺要求。
b) 根据要求进行模具的设计,包括结构设计和材料选择。
c) 进行设计评审,确保设计方案的合理性和可行性。
d) 编制设计文件,包括图纸和工艺文件。
2. 制造过程的质量控制流程:a) 按照工艺文件进行模具的制造,包括材料采购、零件加工和装配等。
b) 每个工序完成后,进行质量检查,确保工序质量符合要求。
c) 对关键工序进行特殊检测和测试,如焊接接头的无损检测等。
d) 完成模具的制造后,进行整体质量检查和测试。
3. 检测和测试的质量控制流程:a) 进行尺寸测量,包括三坐标测量和量具测量等。
b) 进行材料检验,包括金相检测和力学性能测试等。
c) 进行功能测试,确保模具的使用性能符合要求。
模具质量控制要点

模具质量控制要点引言概述:模具是创造工业中的关键设备,对于产品的质量和生产效率具有重要影响。
因此,模具质量控制是创造企业必须重视的问题。
本文将从五个方面介绍模具质量控制的要点。
一、设计阶段的质量控制要点:1.1 确定模具的使用环境和工作条件,包括温度、压力、材料等因素,以便确定模具的材料选择和结构设计。
1.2 采用CAD/CAM技术进行模具设计和分析,确保模具的结构合理、功能完善,并能满足产品的要求。
1.3 进行模具的可靠性分析和寿命预测,以提前发现潜在的问题并采取相应的措施。
二、加工创造阶段的质量控制要点:2.1 选择优质的模具材料,并进行严格的质量检测,确保材料的性能符合要求。
2.2 采用先进的加工设备和工艺,保证模具的加工精度和表面质量。
2.3 进行模具的装配和调试,确保模具的各个部件能够正常工作,同时进行必要的试模和调整。
三、使用阶段的质量控制要点:3.1 定期对模具进行维护和保养,包括清洁、润滑、紧固等,以延长模具的使用寿命。
3.2 定期对模具进行检测和测试,包括尺寸测量、性能测试等,以及时发现和修复模具的问题。
3.3 建立模具使用档案,记录模具的使用情况、维修情况等,以便进行后续的分析和改进。
四、质量控制的关键要点:4.1 引入先进的质量管理体系,如ISO9001等,建立完善的质量控制流程和标准。
4.2 建立模具质量控制的指标体系,包括尺寸精度、表面质量、使用寿命等指标,并进行定期的评估和改进。
4.3 加强对模具质量的监控和追溯,及时发现和处理质量问题,避免扩大化。
五、持续改进的质量控制要点:5.1 建立模具质量改进的机制和团队,定期进行质量分析和评估,找出问题的根本原因,并采取相应的改进措施。
5.2 加强与供应商的合作,确保模具材料和零部件的质量可控。
5.3 建立模具质量培训计划,提高员工的技术水平和质量意识,为模具质量控制提供坚实的基础。
总结:模具质量控制是创造企业必须重视的问题,本文从设计阶段、加工创造阶段、使用阶段、质量控制的关键要点以及持续改进的要点五个方面介绍了模具质量控制的要点。
模具质量控制要点
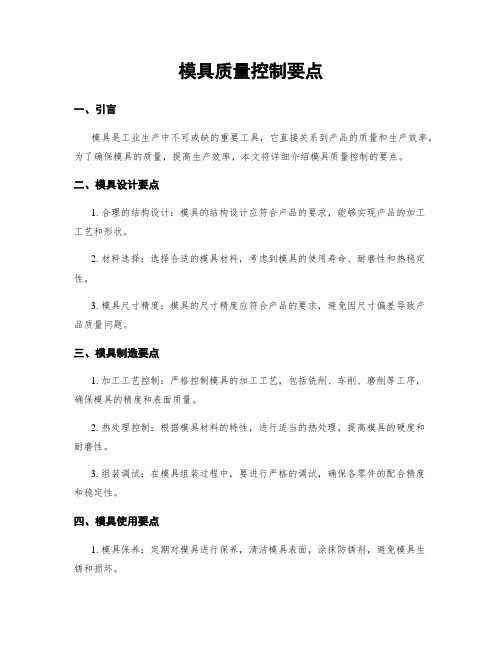
模具质量控制要点一、引言模具是工业生产中不可或缺的重要工具,它直接关系到产品的质量和生产效率。
为了确保模具的质量,提高生产效率,本文将详细介绍模具质量控制的要点。
二、模具设计要点1. 合理的结构设计:模具的结构设计应符合产品的要求,能够实现产品的加工工艺和形状。
2. 材料选择:选择合适的模具材料,考虑到模具的使用寿命、耐磨性和热稳定性。
3. 模具尺寸精度:模具的尺寸精度应符合产品的要求,避免因尺寸偏差导致产品质量问题。
三、模具制造要点1. 加工工艺控制:严格控制模具的加工工艺,包括铣削、车削、磨削等工序,确保模具的精度和表面质量。
2. 热处理控制:根据模具材料的特性,进行适当的热处理,提高模具的硬度和耐磨性。
3. 组装调试:在模具组装过程中,要进行严格的调试,确保各零件的配合精度和稳定性。
四、模具使用要点1. 模具保养:定期对模具进行保养,清洁模具表面,涂抹防锈剂,避免模具生锈和损坏。
2. 模具使用注意事项:使用模具时要注意操作规范,避免过度冲击和过度负荷,防止模具破损或变形。
3. 模具维修与更换:及时进行模具的维修和更换,避免因模具损坏导致生产中断和产品质量问题。
五、模具质量检测要点1. 尺寸测量:通过精密测量工具对模具的尺寸进行测量,检查模具是否符合设计要求。
2. 表面质量检测:使用表面质量检测仪器对模具表面进行检测,查找表面缺陷和损伤。
3. 使用寿命评估:通过对模具的使用情况进行监测和分析,评估模具的使用寿命和剩余寿命。
六、模具质量控制的意义1. 提高产品质量:通过严格控制模具的质量,可以保证产品的尺寸精度和表面质量,提高产品的质量稳定性。
2. 提高生产效率:优质的模具可以提高生产效率,减少生产中断和模具更换的次数。
3. 降低生产成本:通过合理设计和精确控制模具的质量,可以减少废品率和生产中断,降低生产成本。
七、结论模具质量控制是确保产品质量和提高生产效率的关键。
通过合理的设计、严格的制造和科学的检测,可以保证模具的质量稳定性和使用寿命,为企业的发展提供有力支持。
模具质量控制要点

模具质量控制要点引言概述:模具在创造过程中起着至关重要的作用,它直接影响着产品的质量和生产效率。
因此,对模具的质量进行严格控制是非常重要的。
本文将从四个方面详细介绍模具质量控制的要点,包括材料选择、加工工艺、尺寸精度和表面质量。
一、材料选择1.1 材料的强度和硬度:模具材料应具有足够的强度和硬度,以确保其在使用过程中不会发生变形或者磨损。
1.2 材料的耐磨性:模具时常与工件接触,因此材料应具有良好的耐磨性,以延长模具的使用寿命。
1.3 材料的热稳定性:模具在使用过程中会受到高温的影响,因此材料应具有良好的热稳定性,以避免在高温下发生变形或者破裂。
二、加工工艺2.1 设计合理性:模具的设计应符合工件的要求,并考虑到加工工艺的可行性,以确保模具能够顺利进行加工。
2.2 加工精度控制:模具的加工精度直接影响着产品的尺寸精度和表面质量,因此应采取适当的加工工艺和控制措施,确保加工精度的达到要求。
2.3 加工设备和工具的选择:选择适当的加工设备和工具,能够提高加工效率和加工质量,减少加工中的误差。
三、尺寸精度3.1 尺寸测量工具的使用:使用准确可靠的尺寸测量工具,如千分尺、显微镜等,对模具的尺寸进行测量和检验,确保尺寸精度的达到要求。
3.2 尺寸控制标准的制定:制定合理的尺寸控制标准,包括公差范围和允许偏差等,以便对模具的尺寸进行控制和评估。
3.3 尺寸调整和修正:对于尺寸不符合要求的模具,应及时进行调整和修正,以确保其尺寸精度的达到要求。
四、表面质量4.1 表面粗糙度控制:模具的表面粗糙度直接影响着产品的外观和性能,因此应采取适当的加工方法和控制措施,控制模具的表面粗糙度在允许范围内。
4.2 表面处理技术:通过表面处理技术,如抛光、电镀等,提高模具的表面质量,使其具有良好的光洁度和耐腐蚀性。
4.3 表面检验和评估:对模具的表面进行检验和评估,包括外观检查和表面缺陷检测等,以确保表面质量的达到要求。
结论:模具质量的控制是一个复杂而细致的过程,需要从材料选择、加工工艺、尺寸精度和表面质量等多个方面进行综合考虑和控制。
模具质量控制要点

模具质量控制要点引言概述:模具质量控制是创造业中非常重要的一环,它直接影响到产品的质量和生产效率。
本文将从五个方面详细介绍模具质量控制的要点,包括设计要求、材料选择、加工工艺、检测方法和维护保养。
一、设计要求:1.1 模具设计的准确性:模具设计是模具质量的基础,必须准确无误。
设计时要充分考虑产品的尺寸、形状和结构要求,确保模具能够满足产品的加工需求。
1.2 模具结构的合理性:模具结构要简单、合理,易于创造和维修。
合理的结构能够提高模具的使用寿命,降低生产成本。
1.3 模具材料的选择:根据产品的要求和使用环境选择合适的模具材料,如冷/热工作模具钢、不锈钢等。
材料的选择直接影响到模具的硬度、耐磨性和耐腐蚀性。
二、材料选择:2.1 材料的物理性能:模具材料应具有良好的硬度、强度和韧性,以保证模具在使用过程中不易变形、折断或者磨损。
2.2 材料的加工性能:模具材料应易于加工,能够满足模具的创造要求。
例如,易切削性好的材料能够提高模具的加工效率。
2.3 材料的耐磨性和耐腐蚀性:模具在使用过程中会受到磨损和腐蚀的影响,因此选择具有良好耐磨性和耐腐蚀性的材料能够延长模具的使用寿命。
三、加工工艺:3.1 加工精度的控制:模具的加工精度对产品的质量有着重要影响。
在加工过程中,要严格控制模具的尺寸和形状,确保其与产品的要求相符。
3.2 加工工艺的优化:通过合理的加工工艺,能够提高模具的生产效率和质量。
例如,采用先进的数控加工设备和工艺,能够提高模具的加工精度和稳定性。
3.3 表面处理的重要性:模具的表面处理能够提高模具的耐磨性和耐腐蚀性。
常见的表面处理方法包括氮化、硬质合金喷涂等。
四、检测方法:4.1 尺寸测量的准确性:模具的尺寸测量是模具质量控制的重要环节。
采用准确可靠的测量方法和设备,确保模具的尺寸与产品要求一致。
4.2 表面质量的检测:模具的表面质量对产品的外观和质量有着重要影响。
通过目视检查、触摸检测和光学检测等方法,确保模具表面无瑕疵和损伤。
模具质量的高低的质量控制

模具质量的高低的质量控制标题:模具质量的质量控制引言概述:模具在工业生产中扮演着重要的角色,其质量直接影响到产品的质量和生产效率。
因此,对模具质量的控制至关重要。
本文将从材料选择、加工工艺、检测手段、质量管理和维护保养等方面,探讨模具质量的高低的质量控制。
一、材料选择1.1 选择合适的材料:根据模具的使用环境和要求,选择合适的材料,如冷作模具、热作模具、塑料模具等。
1.2 材料质量控制:严格控制原材料的质量,确保材料的化学成分、力学性能等符合要求。
1.3 材料处理:对原材料进行热处理、表面处理等,提高模具的硬度、耐磨性和抗腐蚀性。
二、加工工艺2.1 设计合理的模具结构:根据产品的要求和生产工艺,设计合理的模具结构,避免出现应力集中、变形等问题。
2.2 精密加工:采用先进的加工设备和工艺,确保模具的精度和表面质量。
2.3 表面处理:对模具进行表面处理,如抛光、镀硬铬等,提高模具的耐磨性和使用寿命。
三、检测手段3.1 尺寸检测:采用三坐标测量仪、投影仪等设备,对模具的尺寸进行检测,确保其符合设计要求。
3.2 材料检测:通过金相显微镜、硬度计等设备,对模具的材料进行检测,确保其质量合格。
3.3 功能检测:进行模具的功能性测试,如模具的开合性能、成型性能等,确保其正常使用。
四、质量管理4.1 设立质量管理体系:建立模具质量管理体系,包括质量控制标准、过程控制、质量记录等。
4.2 培训员工:对模具制造人员进行培训,提高其对质量控制的认识和技能。
4.3 定期评估:定期对模具的质量进行评估,及时发现问题并进行改进。
五、维护保养5.1 定期保养:对模具进行定期的清洁、润滑和保养,延长模具的使用寿命。
5.2 故障处理:及时处理模具的故障和损坏,避免对生产造成影响。
5.3 记录管理:建立模具的使用记录和维护记录,为模具的管理和维护提供依据。
结语:模具质量的高低直接关系到产品的质量和生产效率,因此在模具制造过程中,应该严格控制材料选择、加工工艺、检测手段、质量管理和维护保养等方面,确保模具质量的稳定和提高。
模具质量的高低的质量控制

模具质量的高低的质量控制模具质量的高低是创造业中非常重要的一个指标,它直接影响到产品的质量和生产效率。
为了确保模具质量的高水平,需要进行严格的质量控制。
本文将详细介绍模具质量控制的标准格式,包括质量控制的目的、方法和流程。
一、质量控制的目的模具质量控制的目的是确保模具的设计、创造和使用过程中的各项要求得到满足,以提高产品的质量和生产效率。
具体目的包括:1. 确保模具的尺寸精度和形状精度符合设计要求,以保证产品的准确性和一致性。
2. 确保模具的材料选择和热处理过程正确,以提高模具的硬度、耐磨性和使用寿命。
3. 确保模具的结构合理,以提高模具的刚度和稳定性,减少变形和振动。
4. 确保模具的加工工艺正确,以提高模具的加工精度和表面质量。
5. 确保模具的使用和维护过程规范,以延长模具的使用寿命和减少故障率。
二、质量控制的方法模具质量控制的方法包括质量计划、质量检验和质量改进。
具体方法如下:1. 质量计划:制定模具质量控制计划,明确质量目标、质量标准和质量控制点,确定质量控制的方法和流程。
2. 质量检验:对模具的各个环节进行质量检验,包括原材料检验、加工工艺检验、成品检验等。
通过检验,及时发现和纠正质量问题,确保模具的质量符合要求。
3. 质量改进:根据质量检验的结果,分析和评估模具的质量问题,并采取相应的改进措施,提高模具的质量水平。
三、质量控制的流程模具质量控制的流程包括质量计划、质量检验和质量改进。
具体流程如下:1. 质量计划阶段:(1)确定模具的质量目标和质量标准,包括尺寸精度、形状精度、材料性能等。
(2)确定模具的质量控制点,明确关键环节和关键参数,制定相应的质量控制方法和要求。
(3)编制质量计划,包括质量检验的项目、方法、频次和责任人等。
2. 质量检验阶段:(1)原材料检验:对模具所用的原材料进行检验,包括材料的化学成份、机械性能和热处理状态等。
(2)加工工艺检验:对模具的加工工艺进行检验,包括加工设备的选择、加工工艺的参数和工艺流程等。
模具质量的高低的质量控制

模具质量的高低的质量控制模具质量的高低是影响产品质量的重要因素之一,因此,对于模具质量的控制非常重要。
本文将详细介绍模具质量控制的标准格式,包括质量控制的流程、方法和指标等方面的内容。
一、质量控制流程模具质量控制的流程包括以下几个关键步骤:1. 设定质量目标:根据产品要求和客户需求,制定模具质量目标,明确质量控制的要求和标准。
2. 设计评审:在模具设计阶段,进行设计评审,确保设计方案的合理性和可行性。
评审内容包括模具结构、材料选择、加工工艺等方面。
3. 材料采购与检验:选择合适的模具材料,确保材料的质量符合要求。
对采购的材料进行严格的检验,包括化学成份、机械性能等指标的检测。
4. 加工过程控制:对模具的加工过程进行严格的控制,包括加工工艺、加工设备的选择和操作等方面。
确保加工过程中的精度、表面质量等指标符合要求。
5. 零部件检验:对模具的零部件进行检验,包括尺寸、形状、配合度等方面的检测。
采用合适的检测设备和方法,确保零部件的质量符合要求。
6. 组装和调试:对模具进行组装和调试,确保模具的各个部份能够正常运行和配合。
检查模具的装配质量和运动性能,确保模具的精度和稳定性。
7. 首件检验:在模具完成后,进行首件检验,验证模具的质量和性能是否符合要求。
首件检验包括尺寸、外观、功能等方面的检测。
8. 过程控制与改进:在模具的使用过程中,进行质量控制的过程控制和改进。
根据实际情况,对模具的使用和维护进行调整和改进,提高模具的质量和寿命。
二、质量控制方法模具质量控制可以采用以下几种方法:1. 抽样检验:根据质量控制计划,对模具进行抽样检验。
根据检验结果,评估模具的质量状况,并采取相应的措施进行调整和改进。
2. 统计过程控制:通过对模具加工过程中的关键参数进行统计和分析,控制加工过程的稳定性和一致性。
通过统计过程控制,提高模具的加工精度和稳定性。
3. 全面质量管理:采用全面质量管理的方法,对模具质量进行全面的控制和管理。
模具质量的高低的质量控制

模具质量的高低的质量控制模具质量的高低是指模具产品在设计、创造和使用过程中是否符合质量标准的程度。
优质的模具质量能够提高产品的精度、稳定性和寿命,降低生产成本和维修费用。
为了控制模具质量的高低,需要从以下几个方面进行质量控制:1. 设计阶段的质量控制:在模具设计阶段,需要根据产品的要求和使用环境,合理选择材料、结构和加工工艺。
设计师应根据模具的功能和要求,进行合理的结构设计,确保模具的刚性、稳定性和精度。
同时,还需要进行模具的强度计算和模流分析,确保模具在使用过程中不会浮现断裂、变形等问题。
2. 材料的质量控制:模具的材料质量直接影响模具的使用寿命和稳定性。
在材料采购过程中,需要选择具有良好性能和稳定质量的材料供应商。
对于采购的材料,需要进行严格的质量检验,包括化学成份、机械性能和热处理状态等方面的检测,确保材料的质量符合要求。
3. 加工工艺的质量控制:模具的加工工艺包括铣削、车削、磨削、电火花等工艺。
在加工过程中,需要严格按照工艺要求进行操作,保证加工精度和表面质量。
同时,还需要对加工过程进行监控和检测,及时发现和纠正加工中的问题,避免不良加工对模具质量的影响。
4. 组装和调试的质量控制:在模具的组装和调试过程中,需要按照设计要求进行组装,确保各零部件的配合精度和装配质量。
同时,还需要进行模具的调试和试模,检验模具的使用性能和精度是否符合要求。
如有问题需要及时调整和改进,直到模具的使用效果达到预期。
5. 使用和维护的质量控制:在模具的使用过程中,需要按照使用说明和操作规程进行操作,避免不当使用导致模具的损坏。
同时,还需要定期对模具进行保养和维护,包括清洁、润滑和防锈等工作,延长模具的使用寿命和稳定性。
6. 质量管理体系的建立和运行:为了保证模具质量的高低,企业需要建立完善的质量管理体系,包括质量目标的设定、质量标准的制定、质量控制的流程和方法的规定等。
同时,还需要进行质量管理的监督和评估,及时发现和解决质量问题,不断提高模具质量的水平。
模具质量的高低的质量控制
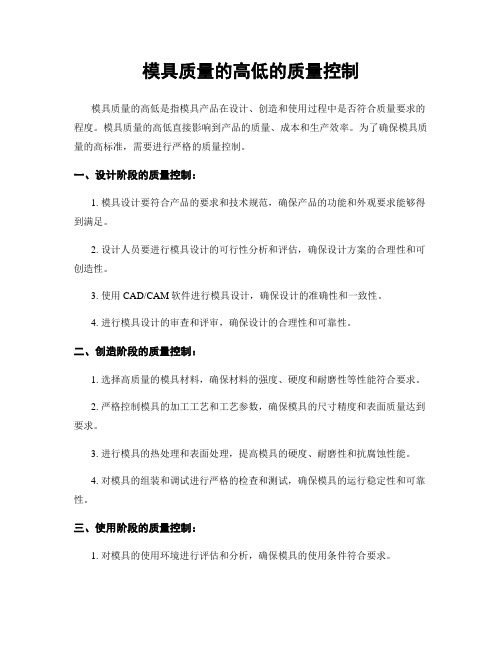
模具质量的高低的质量控制模具质量的高低是指模具产品在设计、创造和使用过程中是否符合质量要求的程度。
模具质量的高低直接影响到产品的质量、成本和生产效率。
为了确保模具质量的高标准,需要进行严格的质量控制。
一、设计阶段的质量控制:1. 模具设计要符合产品的要求和技术规范,确保产品的功能和外观要求能够得到满足。
2. 设计人员要进行模具设计的可行性分析和评估,确保设计方案的合理性和可创造性。
3. 使用CAD/CAM软件进行模具设计,确保设计的准确性和一致性。
4. 进行模具设计的审查和评审,确保设计的合理性和可靠性。
二、创造阶段的质量控制:1. 选择高质量的模具材料,确保材料的强度、硬度和耐磨性等性能符合要求。
2. 严格控制模具的加工工艺和工艺参数,确保模具的尺寸精度和表面质量达到要求。
3. 进行模具的热处理和表面处理,提高模具的硬度、耐磨性和抗腐蚀性能。
4. 对模具的组装和调试进行严格的检查和测试,确保模具的运行稳定性和可靠性。
三、使用阶段的质量控制:1. 对模具的使用环境进行评估和分析,确保模具的使用条件符合要求。
2. 定期对模具进行检查和维护,包括清洁、润滑和更换磨损部件等,确保模具的正常运行。
3. 对模具的使用过程进行监控和记录,及时发现和解决模具使用中的问题。
4. 对模具的故障和损坏进行分析和处理,总结经验并采取措施,以提高模具的使用寿命和稳定性。
四、质量控制的数据分析:1. 采集和记录模具的质量数据,包括模具的设计参数、加工工艺参数和使用情况等。
2. 对模具的质量数据进行统计和分析,评估模具的质量状况和存在的问题。
3. 进行质量数据的对照和趋势分析,找出模具质量的变化规律和影响因素。
4. 根据质量数据分析的结果,采取相应的措施和改进措施,提高模具的质量和性能。
总结:模具质量的高低对产品质量和生产效率有着重要的影响,因此需要进行全面的质量控制。
在设计阶段要确保设计方案的合理性和可靠性;在创造阶段要严格控制材料的选择和加工工艺;在使用阶段要定期检查和维护模具,并进行故障分析和处理;同时进行质量数据的采集和分析,以便及时采取改进措施。
模具质量的高低的质量控制
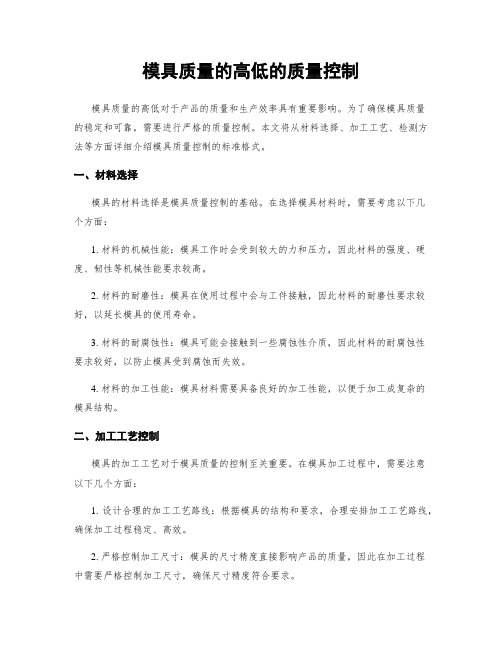
模具质量的高低的质量控制模具质量的高低对于产品的质量和生产效率具有重要影响。
为了确保模具质量的稳定和可靠,需要进行严格的质量控制。
本文将从材料选择、加工工艺、检测方法等方面详细介绍模具质量控制的标准格式。
一、材料选择模具的材料选择是模具质量控制的基础。
在选择模具材料时,需要考虑以下几个方面:1. 材料的机械性能:模具工作时会受到较大的力和压力,因此材料的强度、硬度、韧性等机械性能要求较高。
2. 材料的耐磨性:模具在使用过程中会与工件接触,因此材料的耐磨性要求较好,以延长模具的使用寿命。
3. 材料的耐腐蚀性:模具可能会接触到一些腐蚀性介质,因此材料的耐腐蚀性要求较好,以防止模具受到腐蚀而失效。
4. 材料的加工性能:模具材料需要具备良好的加工性能,以便于加工成复杂的模具结构。
二、加工工艺控制模具的加工工艺对于模具质量的控制至关重要。
在模具加工过程中,需要注意以下几个方面:1. 设计合理的加工工艺路线:根据模具的结构和要求,合理安排加工工艺路线,确保加工过程稳定、高效。
2. 严格控制加工尺寸:模具的尺寸精度直接影响产品的质量,因此在加工过程中需要严格控制加工尺寸,确保尺寸精度符合要求。
3. 合理选择加工设备和工具:根据模具的结构和要求,选择合适的加工设备和工具,确保加工过程顺利进行。
4. 加工过程中的质量检查:在加工过程中,需要进行质量检查,及时发现和纠正加工中的问题,确保加工质量符合要求。
三、质量检测方法质量检测是模具质量控制的重要环节。
常用的模具质量检测方法有以下几种:1. 外观检查:通过目视检查模具的表面是否存在缺陷、损伤、变形等问题,确保模具外观完好。
2. 尺寸测量:使用测量工具对模具的尺寸进行测量,与设计要求进行比对,确保模具尺寸精度符合要求。
3. 材料检验:对模具材料进行化学成分分析、金相组织观察等检测方法,确保材料质量符合要求。
4. 功能检测:对模具进行装配和试模,检测模具的功能是否正常,工作性能是否稳定。
模具质量的高低的质量控制

模具质量的高低的质量控制模具质量的高低是影响产品质量的重要因素之一,对于模具制造企业来说,实施有效的质量控制措施是确保产品质量稳定的关键。
本文将从模具质量控制的目标、方法和措施等方面进行详细介绍。
一、模具质量控制的目标模具质量控制的目标是确保模具制造过程中的每个环节都符合预定要求,以提高产品质量的稳定性和可靠性。
具体而言,模具质量控制应达到以下几个方面的目标:1. 尺寸精度控制:模具的尺寸精度是影响产品尺寸精度的关键因素之一。
通过控制模具的尺寸精度,可以确保产品的尺寸稳定性,提高产品的加工精度和装配精度。
2. 表面质量控制:模具的表面质量直接影响产品的外观和表面光洁度。
通过控制模具的表面质量,可以确保产品的外观质量,提高产品的市场竞争力。
3. 材料性能控制:模具的材料性能直接关系到模具的使用寿命和可靠性。
通过控制模具材料的性能,可以提高模具的抗磨性、抗腐蚀性和抗疲劳性,延长模具的使用寿命。
二、模具质量控制的方法模具质量控制的方法主要包括以下几个方面:1. 设计控制:在模具设计阶段,应根据产品的要求和工艺要求,合理选择模具结构和材料,确保模具具有良好的刚性和稳定性。
2. 加工控制:在模具加工过程中,应严格按照工艺要求进行加工,采用适当的加工工艺和加工设备,确保模具的尺寸精度和表面质量。
3. 热处理控制:模具的热处理对于提高模具的硬度和耐磨性具有重要作用。
在模具热处理过程中,应控制热处理工艺参数,确保模具的热处理效果符合要求。
4. 装配控制:在模具装配过程中,应严格按照装配要求进行装配,确保模具的各个零部件之间的配合精度和间隙符合要求。
5. 检测控制:模具质量的检测是确保模具质量的重要手段。
在模具制造过程中,应采用适当的检测方法和设备,对模具的尺寸精度、表面质量和材料性能进行检测,及时发现和解决问题。
三、模具质量控制的措施为了确保模具质量的稳定性和可靠性,模具制造企业应采取以下几个方面的措施:1. 建立质量管理体系:模具制造企业应建立完善的质量管理体系,包括质量目标、质量计划、质量控制和质量改进等方面的内容,确保质量管理工作有章可循。
模具质量的高低的质量控制

模具质量的高低的质量控制模具质量的高低是影响产品质量和生产效率的重要因素之一,因此质量控制在模具创造过程中显得尤其重要。
本文将从原材料选择、加工工艺、检测手段等方面详细介绍模具质量的高低的质量控制。
一、原材料选择1. 材料强度:根据模具的使用环境和要求,选择合适的材料强度,以确保模具在使用过程中不会发生变形或者断裂。
2. 材料耐磨性:模具在使用过程中会受到磨损,选择具有较高耐磨性的材料可以延长模具的使用寿命。
3. 材料耐腐蚀性:模具在特殊环境中可能会受到腐蚀,选择具有较好耐腐蚀性的材料可以提高模具的稳定性和耐久性。
二、加工工艺控制1. 设计合理性:在模具设计阶段,要考虑到产品的形状、尺寸和加工工艺的要求,合理设计模具的结构和零件布局,以确保模具的创造和使用的可行性。
2. 加工精度控制:在模具加工过程中,要严格控制各个零件的加工精度,特殊是模具的核心部份和配合部份,以确保模具的装配精度和使用精度。
3. 热处理控制:对于需要进行热处理的模具材料,要严格控制热处理工艺参数,以确保模具的硬度和耐磨性达到设计要求。
三、检测手段1. 外观检测:通过目测和测量工具对模具的外观进行检测,包括表面光洁度、尺寸偏差、形状偏差等,以确保模具的外观质量符合要求。
2. 三坐标测量:利用三坐标测量仪对模具的尺寸进行精确测量,以检测模具的几何形状和尺寸精度是否符合设计要求。
3. 材料检测:对模具所使用的材料进行化学成份分析和物理性能测试,以确保材料的质量符合要求。
4. 耐久性测试:通过模具的长期使用或者摹拟使用,对模具的耐久性进行测试,以评估模具的使用寿命和稳定性。
总结:模具质量的高低对产品质量和生产效率有着重要影响,为了确保模具质量的高低,需要从原材料选择、加工工艺控制和检测手段等方面进行全面的质量控制。
通过合理选择材料、控制加工工艺和使用适当的检测手段,可以提高模具的质量和稳定性,从而提高产品的质量和生产效率。
模具质量的高低的质量控制
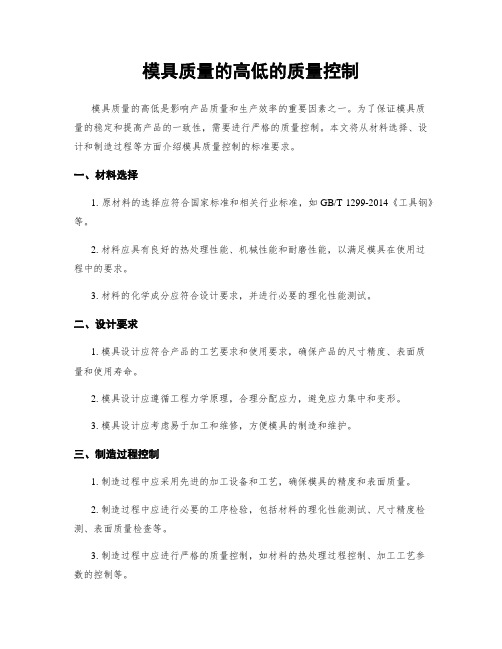
模具质量的高低的质量控制模具质量的高低是影响产品质量和生产效率的重要因素之一。
为了保证模具质量的稳定和提高产品的一致性,需要进行严格的质量控制。
本文将从材料选择、设计和制造过程等方面介绍模具质量控制的标准要求。
一、材料选择1. 原材料的选择应符合国家标准和相关行业标准,如GB/T 1299-2014《工具钢》等。
2. 材料应具有良好的热处理性能、机械性能和耐磨性能,以满足模具在使用过程中的要求。
3. 材料的化学成分应符合设计要求,并进行必要的理化性能测试。
二、设计要求1. 模具设计应符合产品的工艺要求和使用要求,确保产品的尺寸精度、表面质量和使用寿命。
2. 模具设计应遵循工程力学原理,合理分配应力,避免应力集中和变形。
3. 模具设计应考虑易于加工和维修,方便模具的制造和维护。
三、制造过程控制1. 制造过程中应采用先进的加工设备和工艺,确保模具的精度和表面质量。
2. 制造过程中应进行必要的工序检验,包括材料的理化性能测试、尺寸精度检测、表面质量检查等。
3. 制造过程中应进行严格的质量控制,如材料的热处理过程控制、加工工艺参数的控制等。
4. 制造过程中应进行必要的试模和调试工作,确保模具的性能和使用效果。
四、模具使用与维护1. 模具在使用过程中应按照设计要求和使用说明进行操作,避免过载和不当使用。
2. 模具使用过程中应定期进行维护和保养,包括模具表面的清洁、润滑剂的添加、零部件的更换等。
3. 模具使用过程中应及时处理模具的故障和损坏,确保模具的正常运行和寿命。
五、质量管理体系1. 建立完善的质量管理体系,包括质量目标的设定、质量控制计划的制定和执行、质量记录的管理等。
2. 进行质量管理体系的持续改进,包括对模具质量问题的分析和解决、对制造过程的优化和改进等。
3. 建立质量管理的责任制和考核机制,确保质量管理的有效实施和持续改进。
总结:模具质量的高低对产品质量和生产效率具有重要影响,为了保证模具质量的稳定和提高产品的一致性,需要从材料选择、设计和制造过程等方面进行严格的质量控制。
模具质量的高低的质量控制

模具质量的高低的质量控制模具质量的高低是影响产品质量和生产效率的重要因素之一。
为了保证模具质量的稳定和可靠,需要进行严格的质量控制。
本文将从模具设计、材料选择、加工工艺、检测方法等方面详细介绍模具质量控制的标准流程。
一、模具设计模具设计是模具质量控制的首要环节。
合理的模具设计能够提高产品的质量和生产效率。
在模具设计中,需要考虑以下几个方面:1.产品设计要求:根据产品的形状、尺寸、工艺要求等确定模具的结构和尺寸。
2.材料选择:根据产品的材料特性和使用要求选择合适的模具材料,如冷/热工作模具钢、合金钢等。
3.模具结构设计:合理的模具结构设计能够提高模具的使用寿命和生产效率。
需要考虑模具的分型面、导向装置、冷却系统等。
4.模具加工精度要求:根据产品的精度要求确定模具的加工精度,如尺寸公差、表面粗糙度等。
二、材料选择模具材料的选择对模具质量有着重要影响。
合适的材料能够提高模具的硬度、耐磨性和耐腐蚀性。
常用的模具材料包括工具钢、合金钢、硬质合金等。
选择材料时需要考虑以下几个因素:1.产品材料特性:根据产品的材料特性选择相应的模具材料,如塑料制品对应的模具材料可以选择优质的工具钢。
2.模具使用寿命要求:根据模具的使用寿命要求选择耐磨性好的模具材料,如合金钢、硬质合金等。
3.成本考虑:在选择材料时需要综合考虑材料的价格和性能,选择性价比较高的材料。
三、加工工艺模具的加工工艺对模具质量有着重要影响。
合理的加工工艺能够提高模具的加工精度和表面质量。
常用的加工工艺包括车削、铣削、磨削、电火花等。
在加工工艺中需要注意以下几个方面:1.加工设备的选择:根据模具的形状和尺寸选择合适的加工设备,如数控机床、磨床等。
2.加工刀具的选择:根据模具的材料和加工要求选择合适的切削刀具,如硬质合金刀具、涂层刀具等。
3.加工工艺参数的控制:在加工过程中需要控制好加工工艺参数,如切削速度、进给速度、切削深度等。
四、检测方法模具质量的检测是确保模具质量的重要环节。
- 1、下载文档前请自行甄别文档内容的完整性,平台不提供额外的编辑、内容补充、找答案等附加服务。
- 2、"仅部分预览"的文档,不可在线预览部分如存在完整性等问题,可反馈申请退款(可完整预览的文档不适用该条件!)。
- 3、如文档侵犯您的权益,请联系客服反馈,我们会尽快为您处理(人工客服工作时间:9:00-18:30)。
模具质量的高低的质量控制Document serial number【KK89K-LLS98YT-SS8CB-SSUT-SST108】模具质量的高低,在很大程度上决定着产品的质量、效益和新产品的开发能力,因此己成为衡量一个公司产品制造水平高低的重要标志。
模具的质量是模具生产厂家实力的最直接的体现。
作为一家模具行业的企业,要想提高自身的生产水平,其中一个入手点则是模具质量,而影响模具质量的重点则是模具的使用寿命。
当然,模具寿命必须建立在低成本的基础之上。
除了每个环节都要考虑到对模具寿命的影响,还必须通过各部门的通力合作,这也是企业自身实力的真实体现。
(一)设计制作过程的质量控制1.设计过程的质量控制1)要求模具设计方案的确定,方案的提出、方案的制定及方案的审定均须有一定能力的人员出席和最后审定。
2)模具设计人员必须充分了解塑料制品的各项技术要求,在模具设计中给予满足。
3)模具设计之后的工艺设计要满足加工的可能性、合理性及经济性。
4)要有合理的措施确保设计的差错减小到最小。
5)尽量采用先进的设计方法,确保设计质量。
6)设计人员的培训。
质量是由设计人员的素质和责任心来保证的,因此,要加强培训,不断提出新的目标,要有适当的考察。
2.制造过程的质量控制1)设备完好是模具制造过程质量控制的重要内容,要强化日常保养和精度监测。
2)工、刃、量具的合理选用是确保加工质量的重要因素之一,必须有相关的要求。
3)合理安排作业计划也是关系到模具的制造质量,也应有相关的要求。
4)对关系到模具精度和质量的关键机床和关键工艺要设置质量控制点加强控制。
5)人员培训是质量保证的重要环节,必须列出可靠的措施。
6)严格控制废、次品的去向,严防再次流入生产。
7)强化检测,对进料、更换工序、关系塑料制品零件尺寸、关系模具零件的配合尺寸等均要检测。
8)严格控制材料、标准件的质量。
(二)检验1.质量检测质量检测是将检验岗位置于每一个重要的、关键的过程始终,成为一个严密的系统。
A.质量检测的系统性。
应将整个设计、生产、销售的整个过程的每一个关键、重要的过程始终设置质量检测岗位,并能前后呼应成为系统。
例如,进货检验、设计方案的会审、设计图纸的审定、每一道加工工序的始终检验和试模过程的验证、模具装配及运行状况的检定、模压品的检验等等。
B.质量检测的严密性。
整个系统是一个严密的整体,环环紧扣,不可疏漏。
例如,模具零件的质量与所用的材料质量有关,就应设置材料的进货检验,而热处理也要影响零件的强度、耐磨性等,因此也必须进行检测。
同理模具的质量又与模具的设计水平紧密相关,所以模具设计的会审是必不可少的,主要对模具的结构形式、浇注系统方式、冷却方式、零件材料及其热处理、工艺性、经济性等采用主审和各方面人士会审的方法进行。
又例,模具零件的加工质量,除了加工中每道工序的始终均应设置检测岗位,对每个重要尺寸都要有检测外,对于机床的精度、量具的精度、测量的环境等均要进行检测。
C.检验工艺的拟制。
对于检测项目、方法、手段、方式等均应以检验工艺书的形式给予公示,一般应由技术部门事先进行策划和拟制,并以文件的形式下达,作为执行的依据。
检验的方式可以是抽检、互检,也可以是专检。
检验的项目要重点突出,前后呼应不可疏漏,但应考虑实行的可行性。
还有一点必须做到的,即必须将真实的数据记录下来,因此要制定相应的表式,便于记录。
记录的事项应全面,以便于今后进行综合分析,征求全体员工的意见和建议,提出改正预防措施和修正意见。
1)检测仪器的选用及其精度保证参与维护、监督质量体系的运行、协助内部质量审核工作;要确保的质量,生产中的质量控制环节比较重要,可从以下几方面着手:1)有效管理的进行产品数据管理、工艺数据管理、图纸文档管理:进行有效的产品数据管理、工艺数据管理、图纸文档管理、可以保证文件的全面性,图纸版本的一致性;使到图纸能达到有效共享和有效的查询利用。
可以建立完整的文件管理计算机数据库,将设计部门积累的设计图纸、散落的、将以前分散、隔离的信息整理集中起来利用,预防由于设计图档,2d、3d混乱,原始、设变、维修版本混乱、3d模型和2d 图纸数据的不一致,2d图纸设计的不规范、混乱而造成有问题不易被及时发现和及时纠正,造成要修改和返工,甚至作废,增加模具的制造成本,加长模具制造生产周期,影响纳期。
2)保持模具图纸、加工工艺、和实物的数据的一致性和完整性:通过有效的、细致的、严格的检测手段,保证模具图纸、加工工艺、和实物的数据的一致性和完整性。
3)每套模具的设计、制造成本必须要做到及时汇总:通过有效控制车间的工作传票的开出,有效管理的报废;通过准确的模具结构设计、高效的模具零件加工和准确的零配件检测,将有效的降低模具因设变、维修而带来的附加成本,从而获得每套模具的实际成本,有效地控制模具质量。
4)统筹规划:将计划、设计、加工工艺、车间生产情况、人力资源等的信息有机地组织、整合在一起进行统筹,从而有效协调计划和生产,能够有效保证模具质量并如期交货。
5)制定一套完整的、实用模具生产管理系统:制定一套完整的模具生产管理系统,实现模具生产管理流程的产品数据管理、工艺数据管理、计划管理、进度管理的计算机信息化管理系统,包括模具生产计划制定、模具设计、工艺制定、车间任务分派和产品检验,库房管理等,使模具制造及相关辅助信息从计划制定到完工交付能够实现全方位跟踪管理。
6)建立失效模式和影响分析库:建立模具设计、制造失效模式和影响分析库,通过会议、公告、计算机共享、加上奖、罚手段、预防下一次相同问题出现。
同时可以作为曰后质量评定和设计的参考。
7)建立加工工艺编制:建立加工工艺编制,汇总模具零件明细表、外购件明细表、标准件明细表、自制件明细表、自制标准件明细表、材料清单、热处理件明细表、易损件清单和模具费用,确保相关资源能够及时到位。
结合生产计划管理、进度管理,确保相关设备能得到有效使用,预防人员闲置,使加工制造中各环节能够环环相扣。
8)建立质检部门,严格规范检测手段,消除“差不多”的侥幸心理,确保模具加工各零配件的精度。
有效的控制模具质量,根据上下工序记录有效地将质量具体关联到个人。
可以加强设计、操作者的责任心。
9)依本公司、和客户的情况,制定适合本公司和客户的模具设计标准、模具设计作业指导书、;模具制造标准、模具制造作业指导书、规范模具设计和模具制造;预防因为个人的习惯,旧的制模思维造出不符合客户要求的模具。
10)规范采购、库房和下生产订单、物资出入库、报损、发货管理、理顺物料供应链,预防生产脱节。
11)建立考核制度,定期培训考核相关模具设计、模具制造人员,发现、培养公司的骨干精英队伍。
12)规范各岗位的职能,使到人尽其职,人尽其才,预防人浮于事。
13)建立模具项目跟进管理小组:架起客户—市场-工程-采购-制造-仓库-注塑等部门之间的沟通与监督桥梁,进行详细的事务和技术方面的沟通,全面详细了解客户的模具技术要求,记录、总结沟通的内容并准确进行传达到各部,避免反复、多次、试模、修改、返工,从而节省费用和时间。
针对每个客户逐步建立客户业务和技术资料知识库,在公司内部共享,以便提高客户服务水平,减少错误。
跟进、监督模具项目生产进度,安排试模,相关物料的跟催,样板检测确认、送样、安排走模等事项。
能根据检验标准要求对模具加工钳工制作问题进行反馈模具企业首先要解决的就是模具设计能力的问题,也就是对分型面、进料结构、脱模结构、模具运水进行充分合理考虑,相信模具不会出结构性的重大问题。
只要选材合理,加工方式合理,能制定出高标准的加工操作规范并严格执行,相信模具就不会出很多人为操作上的失误。
不过要做好的话需要模具企业管理者做相当大的投入,并长期坚持不懈的改进完善各个环节的操作规范。
我个人认为操作规范是规避人为因素最好的方法。
一直说模具厂管理有问题,也就是模具厂没有制定合理的操作规范。
至于设计能力就需要模具企业找至少2-3位技术相对全面的技师协调研究设计方案,从中找到最适合产品的模具结构设计方案。
只有多放协调才能避免因个人意识形态和主观因素造成模具结构上出现重大失误。
一、模具设计的合理性模具材料的质量控制三、模具加工过程的质量控制1.模具零件加工的质量控制。
2. 模具装配的质量控制⑴首先制件的设计要合理,尽可能选用最好的结构方案,制件的设计者要考虑到制件的技术要求及其结构必须符合模具制造的工艺性和可行性。
⑵模具的设计是提高模具质量的最重要的一步,需要考虑到很多因素,包括模具材料的选用,模具结构的可使用性及安全性,模具零件的可加工性及模具维修的方便性,这些在设计之初应尽量考虑得周全些。
①模具材料的选用既要满足客户对产品质量的要求,还需考虑到材料的成本及其在设定周期内的强度,当然还要根据模具的类型、使用工作方式、加工速度、主要失效形式等因素来⑶模具的制造过程也是确保模具质量的重要一环,模具制造过程中的加工方法和加工精度也会影响到模具的使用寿命。
各零部件的精度直接影响到模具整体装配情况,除掉设备自身精度的影响外,则需通过改善零件的加工方法,提高钳工在模具磨配过程中的技术水平,来提高模具零件的加工精度;若模具整体装配效果达不到要求,则会在试模中让模具在不正常状态下动作的几率提高,对模具的总体质量将会有很大影响。
因此,为保证模具具有良好的原始精度—原始的模具质量,在制造过程中首先要合理选择高精度的加工方法,如电火花、线切割、数控加工等等,同时应注意模具的精度检查,包括模具零件的加工精度、装配精度及通过试模验收工作综合检查模具的精度,在检查时还需尽量选用高精度的测量仪器,对于那些成形表面曲面结构复杂的模具零件,若用普通的直尺、游标卡就无法达到精确的测量数据,这时就需选用三坐标测量仪之类的精密测量设备,来确保测量数据的准确性。
⑷对模具主要成形零部件进行表面强化,以提高模具零件表面耐磨性,从而更好地提高模具质量。
对于表面强化,要根据不同用途的模具,选用不同的强化方法。
⑸模具的正确使用与维护,也是提高模具质量的一大因素。
四、模具出厂质量要求:6. 车间管理人员和设计者应出厂模具作详细质检,确认质量合格后签模具合格证,由车间管理人员登记钳工产值。
总之,要想提高模具的质量,首先必须每个环节都要考虑到对模具质量的影响,其次还须通过各部门的通力合作。
模具的质量是模具企业自身实力的真实体现。
结束语质量是一个古老而又常新的话题!模具的质量,无论是模具的设计者和制造者、制件的设计者,还是模具的使用者都应积极关心的问题,随着技术的不断创新、新材料的广泛采用、加工工艺的不断变革,使用与维护条件的差异等等都不同程度的影响模具的质量。
“模具质量”的涉及面很广泛,相当复杂,提高模具质量的方法有多种,途径也很多,本文仅从自己的观点略作阐述,应该能使模具行业的读者们对“如何提高模具质量”有更广泛、更深刻的认识。