模具的生产工艺
模具生产工艺
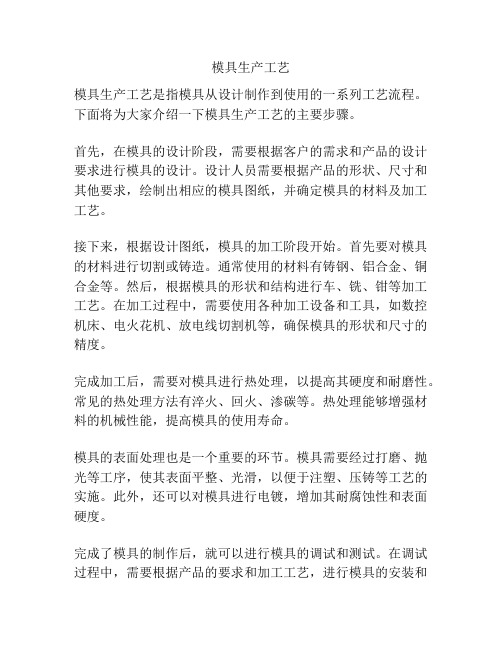
模具生产工艺模具生产工艺是指模具从设计制作到使用的一系列工艺流程。
下面将为大家介绍一下模具生产工艺的主要步骤。
首先,在模具的设计阶段,需要根据客户的需求和产品的设计要求进行模具的设计。
设计人员需要根据产品的形状、尺寸和其他要求,绘制出相应的模具图纸,并确定模具的材料及加工工艺。
接下来,根据设计图纸,模具的加工阶段开始。
首先要对模具的材料进行切割或铸造。
通常使用的材料有铸钢、铝合金、铜合金等。
然后,根据模具的形状和结构进行车、铣、钳等加工工艺。
在加工过程中,需要使用各种加工设备和工具,如数控机床、电火花机、放电线切割机等,确保模具的形状和尺寸的精度。
完成加工后,需要对模具进行热处理,以提高其硬度和耐磨性。
常见的热处理方法有淬火、回火、渗碳等。
热处理能够增强材料的机械性能,提高模具的使用寿命。
模具的表面处理也是一个重要的环节。
模具需要经过打磨、抛光等工序,使其表面平整、光滑,以便于注塑、压铸等工艺的实施。
此外,还可以对模具进行电镀,增加其耐腐蚀性和表面硬度。
完成了模具的制作后,就可以进行模具的调试和测试。
在调试过程中,需要根据产品的要求和加工工艺,进行模具的安装和调整。
一般来说,需要通过试模来检验模具的性能和质量,确保其能够满足产品的生产需求。
最后,模具的使用阶段开始。
在使用模具时,需要注意模具的保养和维护,及时清理模具上的残留物,防止模具损坏和质量问题。
定期进行模具的维修和更换,以保证模具的使用寿命和质量。
综上所述,模具生产工艺是一个复杂的过程,需要设计人员、加工人员、技术人员等多个环节的配合和协作。
只有通过科学的工艺流程和严格的质量控制,才能生产出质量可靠、性能稳定的模具,为产品的生产提供保障。
模具生产工艺流程
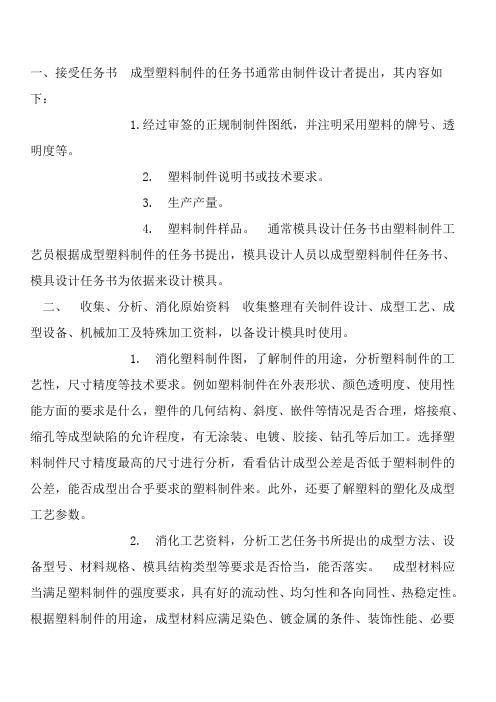
一、接受任务书成型塑料制件的任务书通常由制件设计者提出,其内容如下:1.经过审签的正规制制件图纸,并注明采用塑料的牌号、透明度等。
2. 塑料制件说明书或技术要求。
3. 生产产量。
4. 塑料制件样品。
通常模具设计任务书由塑料制件工艺员根据成型塑料制件的任务书提出,模具设计人员以成型塑料制件任务书、模具设计任务书为依据来设计模具。
二、收集、分析、消化原始资料收集整理有关制件设计、成型工艺、成型设备、机械加工及特殊加工资料,以备设计模具时使用。
1. 消化塑料制件图,了解制件的用途,分析塑料制件的工艺性,尺寸精度等技术要求。
例如塑料制件在外表形状、颜色透明度、使用性能方面的要求是什么,塑件的几何结构、斜度、嵌件等情况是否合理,熔接痕、缩孔等成型缺陷的允许程度,有无涂装、电镀、胶接、钻孔等后加工。
选择塑料制件尺寸精度最高的尺寸进行分析,看看估计成型公差是否低于塑料制件的公差,能否成型出合乎要求的塑料制件来。
此外,还要了解塑料的塑化及成型工艺参数。
2. 消化工艺资料,分析工艺任务书所提出的成型方法、设备型号、材料规格、模具结构类型等要求是否恰当,能否落实。
成型材料应当满足塑料制件的强度要求,具有好的流动性、均匀性和各向同性、热稳定性。
根据塑料制件的用途,成型材料应满足染色、镀金属的条件、装饰性能、必要的弹性和塑性、透明性或者相反的反射性能、胶接性或者焊接性等要求。
3. 确定成型方法采用直压法、铸压法还是注射法。
4、选择成型设备根据成型设备的种类来进行模具,因此必须熟知各种成型设备的性能、规格、特点。
例如对于注射机来说,在规格方面应当了解以下内容:注射容量、锁模压力、注射压力、模具安装尺寸、顶出装置及尺寸、喷嘴孔直径及喷嘴球面半径、浇口套定位圈尺寸、模具最大厚度和最小厚度、模板行程等,具体见相关参数。
要初步估计模具外形尺寸,判断模具能否在所选的注射机上安装和使用。
5. 具体结构方案(一)确定模具类型如压制模(敞开式、半闭合式、闭合式)、铸压模、注射模等。
冲压模具生产工艺流程
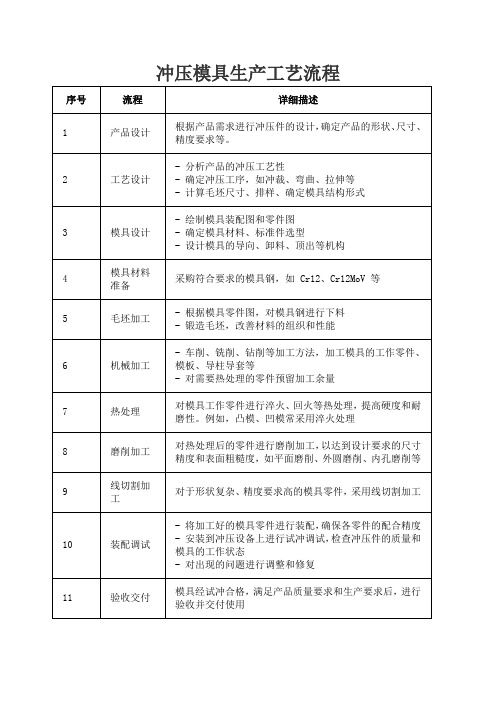
11
验收交付
模具经试冲合格,满足产品质量要求和生产要求后,进行验收并交付使用
4
模具材料准备
采购符合要求的模具钢,如 Cr12、Cr12MoV 等
5
毛坯加工
- 根据模具零件图,对模具钢进行下料
- 锻造毛坯,改善材料的组织和性能
6机械Leabharlann 工- 车削、铣削、钻削等加工方法,加工模具的工作零件、模板、导柱导套等
- 对需要热处理的零件预留加工余量
7
热处理
对模具工作零件进行淬火、回火等热处理,提高硬度和耐磨性。例如,凸模、凹模常采用淬火处理
冲压模具生产工艺流程
序号
流程
详细描述
1
产品设计
根据产品需求进行冲压件的设计,确定产品的形状、尺寸、精度要求等。
2
工艺设计
- 分析产品的冲压工艺性
- 确定冲压工序,如冲裁、弯曲、拉伸等
- 计算毛坯尺寸、排样、确定模具结构形式
3
模具设计
- 绘制模具装配图和零件图
- 确定模具材料、标准件选型
- 设计模具的导向、卸料、顶出等机构
8
磨削加工
对热处理后的零件进行磨削加工,以达到设计要求的尺寸精度和表面粗糙度,如平面磨削、外圆磨削、内孔磨削等
9
线切割加工
对于形状复杂、精度要求高的模具零件,采用线切割加工
10
装配调试
- 将加工好的模具零件进行装配,确保各零件的配合精度
- 安装到冲压设备上进行试冲调试,检查冲压件的质量和模具的工作状态
生产工艺流程——模具生产工艺

生产工艺流程
——模具生产工艺
前言
我们日常生产、生活中所使用到的各种工具和产品, 大到机床的底座、机身外壳,小到一个胚头螺丝、纽扣 以及各种家用电器的外壳,无不与模具有着密切的关系。 模具的形状决定着这些产品的外形,模具的加工质量与 精度也就决定着这些产品的质量。因为各种产品的材质、 外观、规格及用途的不同,模具分为了铸造模、锻造模、 压铸模、冲压模等非塑胶模具,以及塑胶模具。
模具的分类
模具的一般分类:可分为塑胶模具及非塑胶模具:
(1)非塑胶模具有:铸造模、锻造模、冲压模、压铸模等 (2)塑胶模具根据生产工艺和生产产品的不同又分为: A.注射成型模——电视机外壳、键盘按钮(应用最普遍) B.吹气模——饮料瓶 C.压缩成型模——电木开关、科学瓷碗碟 D.转移成型模——集成电路制品 E.挤压成型模——胶水管、塑胶袋 F.热成型模——透明成型包装外壳 G.旋转成型模——软胶洋娃娃玩具
模具是什么?
模具的一般定义:在工业生产中,用各种压力机和 装在压力机上的专用工具,通过压力把金属或非金 属材料制出所需形状的零件或制品,这种专用工具 统称为模具。 模具是一种生产塑料制品的工具。它由几组零件部 分构成,这个组合内有成型模腔。注塑时,模具装 夹在注塑机上,熔融塑料被注入成型模腔内,并在 腔内冷却定型,然后上下模分开,经由顶出系统将 制品从模腔顶出离开模具,最后模具再闭合进行下 一次注塑,整个注塑过程是循环进行的。
模具生产工艺
购入材料 成品
开模
包装
模具生产工艺流程
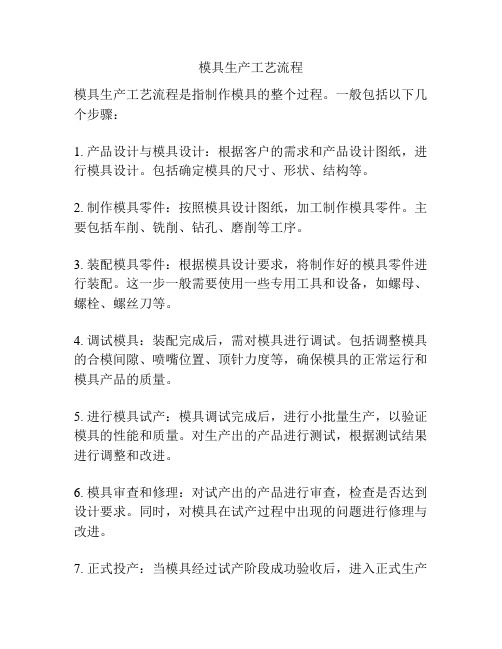
模具生产工艺流程
模具生产工艺流程是指制作模具的整个过程。
一般包括以下几个步骤:
1. 产品设计与模具设计:根据客户的需求和产品设计图纸,进行模具设计。
包括确定模具的尺寸、形状、结构等。
2. 制作模具零件:按照模具设计图纸,加工制作模具零件。
主要包括车削、铣削、钻孔、磨削等工序。
3. 装配模具零件:根据模具设计要求,将制作好的模具零件进行装配。
这一步一般需要使用一些专用工具和设备,如螺母、螺栓、螺丝刀等。
4. 调试模具:装配完成后,需对模具进行调试。
包括调整模具的合模间隙、喷嘴位置、顶针力度等,确保模具的正常运行和模具产品的质量。
5. 进行模具试产:模具调试完成后,进行小批量生产,以验证模具的性能和质量。
对生产出的产品进行测试,根据测试结果进行调整和改进。
6. 模具审查和修理:对试产出的产品进行审查,检查是否达到设计要求。
同时,对模具在试产过程中出现的问题进行修理与改进。
7. 正式投产:当模具经过试产阶段成功验收后,进入正式生产
阶段。
8. 维护与保养:模具生产过程中,需要定期对模具进行维护与保养,保证模具的正常使用寿命和生产效率。
以上是一般模具生产工艺流程的基本步骤,实际生产中还会根据具体情况进行调整和改进。
模具的生产工艺
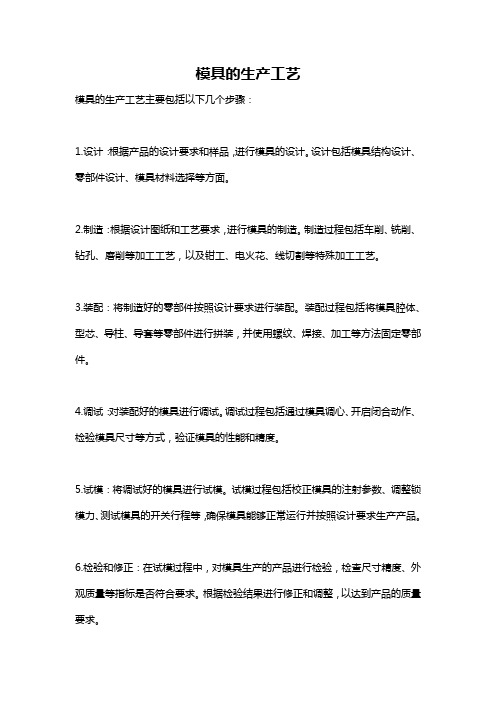
模具的生产工艺
模具的生产工艺主要包括以下几个步骤:
1.设计:根据产品的设计要求和样品,进行模具的设计。
设计包括模具结构设计、零部件设计、模具材料选择等方面。
2.制造:根据设计图纸和工艺要求,进行模具的制造。
制造过程包括车削、铣削、钻孔、磨削等加工工艺,以及钳工、电火花、线切割等特殊加工工艺。
3.装配:将制造好的零部件按照设计要求进行装配。
装配过程包括将模具腔体、型芯、导柱、导套等零部件进行拼装,并使用螺纹、焊接、加工等方法固定零部件。
4.调试:对装配好的模具进行调试。
调试过程包括通过模具调心、开启闭合动作、检验模具尺寸等方式,验证模具的性能和精度。
5.试模:将调试好的模具进行试模。
试模过程包括校正模具的注射参数、调整锁模力、测试模具的开关行程等,确保模具能够正常运行并按照设计要求生产产品。
6.检验和修正:在试模过程中,对模具生产的产品进行检验,检查尺寸精度、外观质量等指标是否符合要求。
根据检验结果进行修正和调整,以达到产品的质量要求。
7.维护保养:模具生产主要依赖于原始图纸、技术数据和合理的操作程序。
对模具进行定期的维护保养,包括清洁、润滑、更换易损件等,以确保模具的正常使用和延长模具的使用寿命。
需要注意的是,不同类型的模具(如塑料模具、铸造模具、冲压模具等)在生产工艺的细节和步骤上会稍有不同。
以上仅为一般模具生产工艺的大致步骤,具体情况还需根据实际项目和产品进行调整。
模具加工工艺及流程

模具加工工艺及流程模具加工工艺及流程模具加工是指设计、制作、组装、加工、试模等一系列工序,最终得到能够生产出理想产品的模具。
模具是现代工业生产过程中不可缺少的生产工具,因此模具加工技术的发展对于提高生产效率、降低成本、保证产品质量等方面都具有重要作用。
下面将介绍模具加工的工艺及流程。
一、设计模具制作的第一步是根据产品的要求进行模具设计。
设计人员需要结合产品的形态特征、使用要求、生产工艺等因素进行综合分析和考虑,制定出合理的模具结构。
设计注意事项:1.要按照零件原理、标准规范进行设计。
2.设计前要对所需材料进行详细的了解和分析,选择合适的材料。
3.在设计过程中要注意加工和使用的方便性,以提高加工效率和降低失败率。
4.设计完成后要结合实际情况仔细斟酌,进行模具设计优化和改进。
二、制模制模是模具加工的主要环节之一,它的精准度和成功率直接关系到整个加工过程的成败。
制模工序包含模具主体加工、零部件加工、元件制作、组装调试等环节。
1. 模具主体加工:模具主体是模具的主体结构,包含了模腔壳体、模心、导柱等。
在模具设计合格后,需要进行主体加工。
2. 零部件加工:零部件主要包括模具底板、卡板、顶板、定位销等,这些零部件需要与主体进行组合而形成完整的模具。
零件加工过程中需要注重加工精度。
3. 元件制作:元件主要包括弹簧、卡簧、顶针、定位圈等,这些元件起到了对模具加工过程中防止伤害和保护作用。
4. 组装调试:在模具中应用到的零件必须进行预装和调试,避免出现安装过程中的不匹配问题,确保模具的高效运行。
三、加工精度控制对模具加工的加工精度进行控制非常重要。
通过引入计算机数控加工技术能够实现更精确的加工精度,提高了模具生产的效率和精度。
加工精度控制主要包括以下几个方面:1. 高精度加工设备的选择和应用:数控机床、电火花加工机、线切割加工机等具有较高加工精度,能够保证模具的高精度加工。
2. 加工刀具的选择:高精度加工刀具精度高,寿命长,性能稳定可靠。
汽车模具生产工艺

汽车模具生产工艺
汽车模具生产工艺是指在汽车模具制造过程中所采用的一系列生产工艺和技术。
下面简单介绍一下汽车模具生产工艺的主要步骤。
首先是模具设计。
根据汽车零部件的设计要求和技术参数,通过计算机辅助设计软件进行模具设计。
设计过程中需要考虑到模具的结构、强度、加工精度以及流程的合理性等因素。
接下来是模具材料的选择和检验。
汽车模具通常采用高强度、耐磨性好的材料,如合金钢、工具钢等。
在材料选择过程中需要进行严格的质量检验,确保材料符合相关标准要求。
然后是模具加工和制造。
根据模具设计图纸进行加工工艺的制定,包括车削、铣削、钻孔、铣槽、磨削、热处理等工艺。
其中热处理是非常重要的一步,通过对模具进行淬火、回火等处理,可以提高模具的硬度和耐磨性。
模具装配和调试是模具制造的重要环节。
在模具装配过程中,需要将各个零部件按照设计要求进行装配,确保模具的精度和质量。
调试过程中会对模具进行试模,检查是否存在问题,如有需要还需进行修改和调整。
最后是模具试产和产品认证。
在试产过程中,会对模具进行批量加工生产,以验证模具的稳定性和可靠性。
同时还需要对产品进行质量认证,如ISO/TS16949认证等。
总之,汽车模具生产工艺是一个复杂而精密的过程,需要专业的人员和先进的设备来完成。
通过不断改进和优化工艺流程,可以提高模具的质量和效率,为汽车行业的发展做出积极贡献。
模具制造工艺 第2版 项目一 模具制造工艺基础

项目一 模具制造工艺基础
模具机械加工工序卡
项目一 模具制造工艺基础
3、制定模具图纸 审查零件图与装配图 * 审查设计图纸的完整性和正确性 * 审查零件的技术要求 * 审查零件的选材是否恰当 * 审查零件的结构工艺性 2、毛坯的选择 3、拟定工艺路线 4、确定工序具体内容 5、填写工艺文件
项目一 模具制造工艺基础
一、模具加工工艺规程概述
1、工艺过程及其组成 将原材料转变为模具成品的全过程称为模具生产 过程。主要包括: 模具方案策划、结构设计 生产技术准备 模具成型件加工 装配与试模 验收与试用
模具生产过程中直接改变生产对象的形状、尺寸、相对 位置和性质等,使其成为半成品或成品的过程,称为工艺 过程。
项目一 模具制造工艺基础
四、选择加工方法时需要考虑的因素 在选择从粗到精的加工方法及过程时,要综合考
虑多方面的因素,重点考虑以下问题:
(1)被加工零件的结构形状和表面的精度 一般所采用加工方法的经济精度,应保证零件
所要求的加工精度和表面质量。 加工经济精度:是指在正常加工条件下(采用
符合质量标准的设备、工艺装备和标准技术等级的工 人,不延长加工时间)所能保证的加工精度。
加工方法及工序顺序凹模镶套零件的主
要尺寸标注都是以零件的轴心线为基准
的,这使得零件加工时容易与设计基准
进行统一
项目一 模具制造工艺基础
六.安排加工顺序
* 先粗后精 * 基准先行 * 先主后次 * 先面后孔 适当安排热处理(预备热处理和最终热处理) 检验、去毛刺、倒棱、清洗、防锈等辅助工序要 按需设置,不能遗漏。 在确定工序数目时,恰当地决定工序集中与工序 分散问题。
二、模具加工工艺规程及作用:
模具生产工艺流程
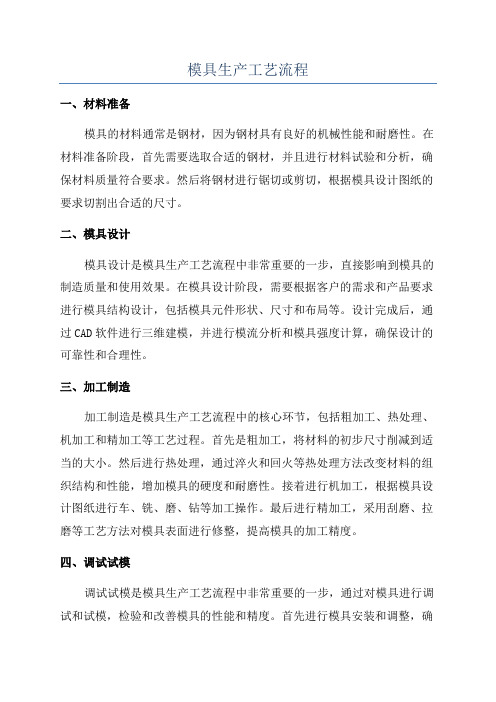
模具生产工艺流程一、材料准备模具的材料通常是钢材,因为钢材具有良好的机械性能和耐磨性。
在材料准备阶段,首先需要选取合适的钢材,并且进行材料试验和分析,确保材料质量符合要求。
然后将钢材进行锯切或剪切,根据模具设计图纸的要求切割出合适的尺寸。
二、模具设计模具设计是模具生产工艺流程中非常重要的一步,直接影响到模具的制造质量和使用效果。
在模具设计阶段,需要根据客户的需求和产品要求进行模具结构设计,包括模具元件形状、尺寸和布局等。
设计完成后,通过CAD软件进行三维建模,并进行模流分析和模具强度计算,确保设计的可靠性和合理性。
三、加工制造加工制造是模具生产工艺流程中的核心环节,包括粗加工、热处理、机加工和精加工等工艺过程。
首先是粗加工,将材料的初步尺寸削减到适当的大小。
然后进行热处理,通过淬火和回火等热处理方法改变材料的组织结构和性能,增加模具的硬度和耐磨性。
接着进行机加工,根据模具设计图纸进行车、铣、磨、钻等加工操作。
最后进行精加工,采用刮磨、拉磨等工艺方法对模具表面进行修整,提高模具的加工精度。
四、调试试模调试试模是模具生产工艺流程中非常重要的一步,通过对模具进行调试和试模,检验和改善模具的性能和精度。
首先进行模具安装和调整,确保各个模具零件的配合和工作正常。
然后进行试模,通过模具来生产样品或产品,并进行调整和改进,以达到产品的要求和客户的需求。
五、模具保养模具保养是模具生产工艺流程中的最后一步,为了延长模具的使用寿命和提高模具的生产效率,需要进行定期的保养和维护。
保养工作包括模具的清洁、润滑、防锈和更换损耗零件等,确保模具的正常运行。
同时还需要进行模具的记录和台账,以便统计和分析模具的使用情况,提升模具的管理水平。
总的来说,模具生产工艺流程包括材料准备、模具设计、加工制造、调试试模和模具保养五个方面。
每个环节都非常重要,缺一不可。
只有经过科学规范的工艺流程,才能制作出高质量的模具,满足客户的需求。
模具生产工艺流程
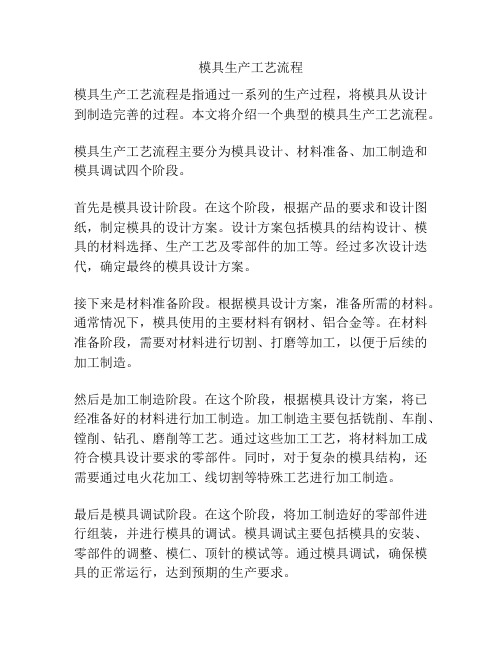
模具生产工艺流程
模具生产工艺流程是指通过一系列的生产过程,将模具从设计到制造完善的过程。
本文将介绍一个典型的模具生产工艺流程。
模具生产工艺流程主要分为模具设计、材料准备、加工制造和模具调试四个阶段。
首先是模具设计阶段。
在这个阶段,根据产品的要求和设计图纸,制定模具的设计方案。
设计方案包括模具的结构设计、模具的材料选择、生产工艺及零部件的加工等。
经过多次设计迭代,确定最终的模具设计方案。
接下来是材料准备阶段。
根据模具设计方案,准备所需的材料。
通常情况下,模具使用的主要材料有钢材、铝合金等。
在材料准备阶段,需要对材料进行切割、打磨等加工,以便于后续的加工制造。
然后是加工制造阶段。
在这个阶段,根据模具设计方案,将已经准备好的材料进行加工制造。
加工制造主要包括铣削、车削、镗削、钻孔、磨削等工艺。
通过这些加工工艺,将材料加工成符合模具设计要求的零部件。
同时,对于复杂的模具结构,还需要通过电火花加工、线切割等特殊工艺进行加工制造。
最后是模具调试阶段。
在这个阶段,将加工制造好的零部件进行组装,并进行模具的调试。
模具调试主要包括模具的安装、零部件的调整、模仁、顶针的模试等。
通过模具调试,确保模具的正常运行,达到预期的生产要求。
总结起来,模具生产工艺流程包括模具设计、材料准备、加工制造和模具调试四个阶段。
在每个阶段中,都需要严格按照设计要求和工艺规范进行操作,确保模具的质量和生产效率。
通过这个工艺流程,能够实现高效、精确、稳定的模具制造,满足产品的生产要求。
塑料挤出模具生产工艺流程
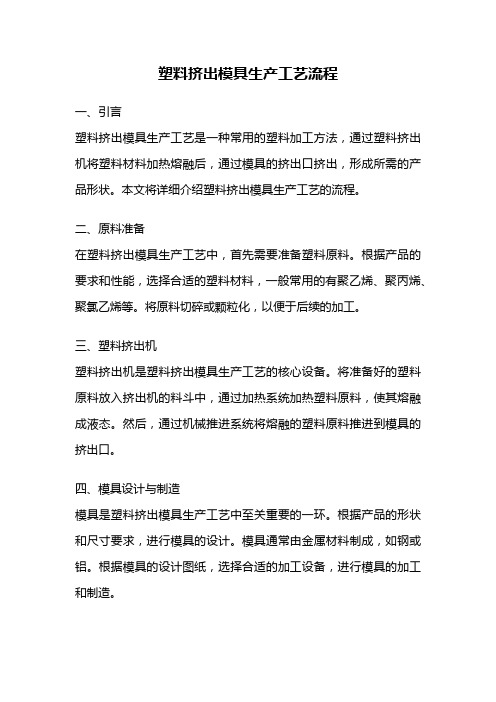
塑料挤出模具生产工艺流程一、引言塑料挤出模具生产工艺是一种常用的塑料加工方法,通过塑料挤出机将塑料材料加热熔融后,通过模具的挤出口挤出,形成所需的产品形状。
本文将详细介绍塑料挤出模具生产工艺的流程。
二、原料准备在塑料挤出模具生产工艺中,首先需要准备塑料原料。
根据产品的要求和性能,选择合适的塑料材料,一般常用的有聚乙烯、聚丙烯、聚氯乙烯等。
将原料切碎或颗粒化,以便于后续的加工。
三、塑料挤出机塑料挤出机是塑料挤出模具生产工艺的核心设备。
将准备好的塑料原料放入挤出机的料斗中,通过加热系统加热塑料原料,使其熔融成液态。
然后,通过机械推进系统将熔融的塑料原料推进到模具的挤出口。
四、模具设计与制造模具是塑料挤出模具生产工艺中至关重要的一环。
根据产品的形状和尺寸要求,进行模具的设计。
模具通常由金属材料制成,如钢或铝。
根据模具的设计图纸,选择合适的加工设备,进行模具的加工和制造。
五、模具安装与调试模具制造完成后,将模具安装到挤出机上。
确保模具安装稳固,并进行必要的调试工作。
调试包括模具的开合速度、温度控制、挤出压力等参数的调整,以确保挤出过程中塑料原料能够顺利地通过模具挤出口。
六、挤出成型当模具安装调试完成后,可以开始进行挤出成型工艺。
打开塑料挤出机的加热系统,使塑料原料熔融,并通过机械推进系统推进到模具的挤出口。
在模具的作用下,塑料原料被挤出,并形成所需的产品形状。
挤出的产品可以是管状、板材状或其他形状。
七、冷却与定型挤出成型后的产品需要进行冷却与定型。
通过冷却系统,将挤出的产品迅速降温,使其固化并保持所需的形状。
冷却时间和冷却方式需要根据所使用的塑料材料和产品的要求进行合理调整,以确保产品的质量。
八、切割与包装冷却定型后,产品需要进行切割和包装。
根据产品的尺寸和需求,采用切割设备对产品进行切割,使其达到所需的长度或形状。
然后,将切割好的产品进行包装,以便于运输和存储。
九、质量检测与改进在塑料挤出模具生产工艺中,质量检测是非常重要的环节。
模具生产加工工艺排程
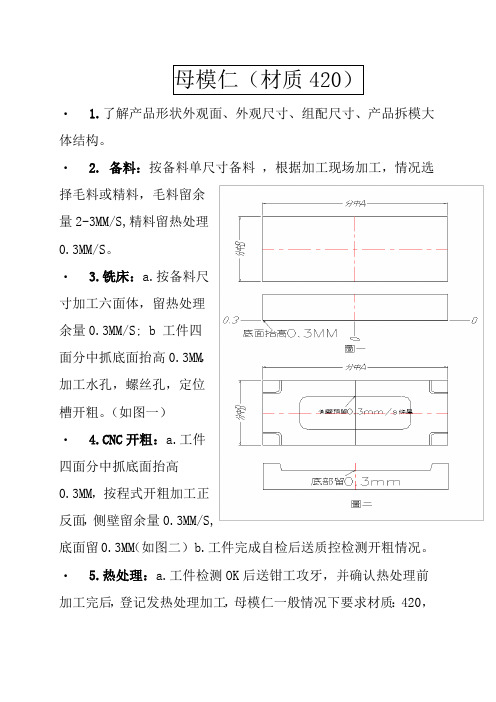
母模仁(材质420)• 1.了解产品形状外观面、外观尺寸、组配尺寸、产品拆模大体结构。
• 2. 备料:按备料单尺寸备料,根据加工现场加工,情况选择毛料或精料,毛料留余量2-3MM/S,精料留热处理0.3MM/S。
• 3.铣床:a.按备料尺寸加工六面体,留热处理余量0.3MM/S; b 工件四面分中抓底面抬高0.3MM,加工水孔,螺丝孔,定位槽开粗。
(如图一)• C开粗:a.工件四面分中抓底面抬高0.3MM,按程式开粗加工正反面,侧壁留余量0.3MM/S,底面留0.3MM(如图二) b.工件完成自检后送质控检测开粗情况。
• 5.热处理:a.工件检测OK后送钳工攻牙,并确认热处理前加工完后,登记发热处理加工,母模仁一般情况下要求材质:420,硬度HRC48±1°; b.工件热处理回厂后送质控检测硬度,变形。
• 6.研磨:工件四面分中底面研磨0.3MM,见光加工至图面尺寸,公差±0.01mm(如图一),工件完成后送质控质检。
•C精加工:a. 按图面尺寸四面分中抓底面精加工(如图三)。
b. 型腔部分底部精到字体最高面,抛光后加工下一工序,以便保证字体美观。
四个定位加工时,单边过切0.015mm, 以防公母模仁擦破撑住(如图三),底部定位槽需用定位块实配加工。
C.工件加工完成后自检OK,送质控检测•8.线割:工件四面分中抓底面按图面尺寸加工入子孔进胶孔,入子孔公差为异形孔用入子实配加工完成後送质检检测.•9.放电:按图面四面分中抓底面放电加工,模仁上机前加工人员检查模仁口部有无撞坏圆角,电极有无变形等情况•10.抛光:加工人员对照产品外观要求及钳工交接事项,要求顺产品脱模方向抛光加工,保证其工件无圆角无变形二、公模仁• 1.备料 : 按备料单尺寸备料,根据加工现场加工情况选择毛料或精料,毛料余量2-3MM/S,精料余量0.3MM/S .• 2.铣床: a.按备料尺寸加工六面体,留热处理余量0.3MM/S;b. 四面分中抓底抬高0.3MM,加工水孔,螺丝孔,顶针穿丝孔,定位槽开粗(如图一),工件OK後送质控检测• C开粗:a. 工件四面分中抓底面抬高0.3MM,按程式开粗加工正反面,侧壁留余量0.3MM/S,最高面预留0.5MM(如图4)• 4.热处理: a.工件经钳工功牙确认热处理前加工完成情况後送质控检测;b.热处理加工公模仁一般情况要求材质SKD61硬度HRC±1度,热处理完成回厂後质控检测工件变形度,硬度情况.• 5.研磨:工件四面分中,底面研磨0.3MM,加工至图面尺寸公差±0.01,(如图一), 工件完成後送质控检测.• 6.线割:按图面尺寸四面分中,抓底面加工顶针孔,入子孔,斜销孔公差为顶针孔 ,丝筒孔一般为±0加2. 如有异形入子孔需用入子实配加工,工件完成送质控检测•7. CNC精加工:a. 按图面尺寸四面分中抓底面精加工正反面,(如图三). b. 形腔顶面CNC加工至字体最高面,胶片部分整体预留0.1MM余量,配入子斜销一起加工外观面,PL面CNC尽量做到数或补一精工电极,四个定位台到位,反面定位槽用定位块实配加工,斜销孔侧壁单边预留0.1MM,底部尽量到位,以防线割与CNC 加工有偏位过切; c. 工件加工完成後自检OK送质控检测尺寸情况.•8.放电: 按图面四面分中抓底面放电加工,模仁上机前加工人员检查模仁有无撞伤,电极有无变形等情况,先放电加工斜销孔侧壁清角,以便配入斜销一起放电加工,保证外观面一致,尽量整体NC线割电极一体,再装起来整体放电加工.•9.抛光: 加工人员对照产品外观要求及钳工交接事项,按产品脱模方向抛光加工筋位卡扣等情况以便出模• 1.快丝:按图面尺寸加工外形,留研磨余量0.1MM/S.• 2.研磨:加工入子外形尺寸,挂台斜面,厚度民尽量公差+0.02MM,以便实配模仁• 3.放电:先单独放电加工牛角形状尺寸,再配入模仁整体电极放电加工,以便保证外观面美观,一致.注:制作中牛角进胶标准(如图五)• 4.抛光:牛角状流道顺利脱模• 1.按图面尺寸加工斜销最大外形尺寸,顶面留0.05MM,以便配入公仁放电加工,顶面火花纹外观.• 2.按图面尺寸研磨加工直角形状及外形台阶磨线头(如图六)• 3.放电按图面加工胶位部分,加工完成後送质控• 4.抛光:按钳工交接顺脱方向加工作业.• 1.备料:按备料尺寸备料,毛胚料预留後加工余量2-3MM/S• 2.铣床:按备料单尺寸加工六面体,预留热处理後研磨余量0.3MM/S,工件四面分中(图一),抓底面(如图二)预留热处理後研磨余量0.3MM,按图加工螺丝孔,水路孔,定位槽开粗,穿丝孔,加工完成後送质控检测.• C粗:工件四面分中(图一),抓底面抬刀0.3MM(图二),作为工件底面零位置面,按程式粗加工,加工完成後送质控检测.• 4.热处理:工件经钳工攻牙并确认热处理前加工完成後送热处理.材质:420,硬度HRC±1度,热处理完成後送质控检测硬度,变形.• 5.研磨:工件六面分中研磨加工到图面尺寸(图一),公差:±0.01MM,加工完成後送质控检测.• C精:工件四面分中(图一),抓底面为零位对刀(图三),按程式加工,确认加工完成,表面无弹刀痕,台阶後送质控检测•7.线割:工件四面分中(图一),按图加工入子孔,进胶孔,入子孔加工爲,加工完成後送质控检测.(非精密模具入子孔公差可单边0.02mm)•8.放电:工件四面分中(图一),抓底面爲0位(图三),按程式单放电坐标加工,模仁上机前检查其口部有无摺角,撞伤,电极无变形,撞伤,刀痕後,放电加工,确认加工完成後送质控检测•9.抛光:加工人员接到工件後,对照产品外观处理,彩图及钳工标示交接,明确加工要求後顺产品脱模方向加工,抛顺,保证其工件无圆角,摺角,• 1.备料:按备料单尺寸备料,毛肧料预留後加工余量2-3MM/S• 2.铣床:按备料单尺寸飞料六面体,预留热处理後研磨余量0.3MM/S,工件四面分中(图一),抓底面(图二),预留热处理余量0.3MM,按图加工螺丝孔,穿丝孔,水路孔,定位槽开粗,确认加工完成後送质控检测.• C粗:工件四面分中(图一),抓底面抬刀0.3MM,为工件底面0位,按程式粗加工,粗加工完成後送质控检测.• 4.热处理:工件经钳工攻牙并确认热处理前加工完成後送热处理:材质:SKD61,硬度:HRC48±1度,加工完成後送质控检测硬度,变形.• 5.工件六面分中研磨到图面尺寸(图一),公差:±0.01,加工完成後送质控检测• 6.研磨:工件四面分中(图一),抓底面为0位对刀(图三),按程式加工,四角定位台侧面加工过切0.02MM/S(图4),确认加工完成後,表面无台阶,弹刀痕後送质控检测•7.线割:工件四面分中(图一),按图加工顶针,入子及斜销孔,入子斜销孔公差为,顶针为±0.01mm,加工完成後送质控检测.•8.放电:工件四面分中(图一),抓底面为0位(图三).按程式单放电坐标加工,模仁上机前检查有们摺角,撞伤,电极无变形,撞伤,刀痕後放电加工,确认加工完成後送质控检测•9.抛光:加工人员接到工件後,对照产品外观处理,彩图及钳工标示交接,明确加工要求後顺产品脱模方向加工,抛顺.三、滑块加工流程(材质420)• 1.备料:按备料单备料,毛肧料预留後加工余量2-3MM/S.• 2.铣床:a.按备料单尺寸加工六面体.留热处理余量0.3MM/S; b.工件四面分中(图一),抓底面预留0.3MM热处理後研磨余量(图2),按图加工螺丝孔,水路孔,挂台开粗,加工完成後送质控检测.• C开粗:工件四面分中(图一),抓底面对刀抬刀0.3MM,作为工件底面0位面,按程式粗加工,加工完成後送质控检测• 4.热处理:工件经钳工攻牙并确认热处理前加工完成後送热处理:材质:420,硬度:HRC48±1度,热处理完成後,送质控检测硬度,变形.• 5.研磨:工件四面分中研磨到图面尺寸(图一),抓底面磨掉0.3MM(图二),注:抓直角时应以长边较直,磨平,抓短边直角.加工完成後送质控检测.• C精:工件四面分中(图一),抓底面(图三)对刀,按程式加工,确以加工完成,表面无弹力痕,台阶後下机,送质控检测•7.放电:工件四面分中(图一),抓底面(图三).按程式单放电坐标加工,工件上机前应检查口部有无撞伤摺角,电极无变形,加工面无刀纹,撞痕後放电加工,确认加工完成後送质控检测•8.抛光:加工人员接到工件後,对照产品外观处理要求彩图,及钳工标示交接,明确加工要求後顺产品脱模方向加工抛顺,保证其工件无摺角,圆角.• 1.线割:按图档编辑程式,按侧视图线割主体,模仁与斜销插破面时,插破面应预留配模余量0.05MM(图一).用大於斜销宽度尺寸0.1-0.5MM热处理後的板料,按程式加工,线头应留在斜销挂台方向正面(图二).• 2.研磨: 工件接线头,抓直角,外形尺寸及台阶,筋位,加工到尺寸,加工完成送质控检测.• 3.快丝:按图加工斜销挂台,以工件R头部高点取数,留0.2MM/S,研磨余量(图三)• 4.研磨:研磨按图加工挂台到尺寸:加工完成後送质控检测.• 5.放电:检查工件,电极有无变形,撞伤後,将正弦台调到图面斜度,按程式坐标放电加工确认加工完成後送质控检测.• 6.抛光:按钳工标示,顺脱模方向抛光.六、入子加工图(材质:SKD61)• 1.快丝:按视图加工入子外形,留工艺台,高度同挂台尺寸一样(图一),留研磨余量0.1MM/S• 2.研磨:按图加工入子外形尺寸,挂台斜面及直角筋位,公差:,加工完成後送质控检测. • 3.放电:装入模仁放电.• 4.抛光:按钳工交接标示顺脱模方向抛顺.。
模具生产工艺流程图

打磨、抛光
计
计
划
计
划
划
实
实
际
实
际
际
总装、试模
计 划
实 际
生产准备检 查
镶件加工
生产准备检 查
材 料
图 纸
划线,加工吊 环孔
计 划
实 际
凸台、镶件槽 CNC 加工
计 划
实 际
E材DM 清角 料
计 划钻水孔、螺孔
计
实计
划图
际划
纸
实
实
际扩司筒、顶针孔 际铰司筒、顶针孔
配镶件
钻镶件槽螺孔
计
计
划
划
实
实
C际NC 加 工 成 型 际EDM 加工
实 际
生产准备检查 材料 图纸
深孔钻加工水 CNC 加工 孔
计
计
划
划
实
实
际
际
实 际 摇臂钻钻孔
EDM 加工
计
计
划
划
实
实
际
际
配镶件
计 划
实 际
配镶件
计 划
EDM 加工
计 划
铜公加工
镶 计件 划
抛光
实 际计
划
生产准备检 查
材 料
图 纸
镶件加工 实 际
计 划
生产准备检查
实
实
际
际
材料
实 配际滑块、配模
图纸
钻斜导柱孔, 钻攻抽芯螺孔
面
装镶件,配模 芯、模板
计 划
实配模 际
钻司筒、顶针孔
计 划
实 际抛光
计 划
计划生查 产 准 备 检
冲压模具生产工艺流程

冲压模具生产工艺流程冲压模具,是在冷冲压加工中,将材料(金属或非金属)加工成零件(或半成品)的一种特殊工艺装备,称为冷冲压模具(俗称冷冲模)。
小编给大家整理了关于冲压模具生产工艺流程,希望你们喜欢!冲压模具生产工艺流程五金冲压模具制作流程一.毛胚材料加工:1.铣六面对角尺(垂直度误差不大于0.1/300),同一付模具材料长宽尺寸一致即可,厚度留0.2mm磨量(需淬火件留0.5mm磨量);棱边倒角。
2.磨上下两平面,(需淬火工件留0.3mm)二.机加工:1.根据图纸分别钻、攻各螺钉牙孔及过孔以及穿丝孔等;2.铣各漏料孔或成形部分;3.热处理后,工件需磨上下两平面及基准边;4.车加工各回转件,公差按图要求。
☆☆所有销钉孔都不能先加工:需热处理的钻穿丝孔,其余都在装配是配钻、铰三.线割:按图纸规定的配合要求线割各个成型部分。
导柱、导套与模架紧配合;冲头与固定板过渡配合;销钉与各孔均为过渡配合。
四.装配:1.先按图装配模架,确保导柱、导套与模架垂直并运动顺畅;2.在模架上先固定凹模,按图纸给定间隙将相应厚度的铜皮均匀地放在凹模周边,再装入凸模,试冲纸片确定四周毛刺均匀后,紧固凸、凹模并配打销钉。
(如果是复合模,还需对好冲头间隙再固定凸、凹模)。
3.之后再装好卸料及顶出机构五.模具整体加工顺序:1.优先加工需要热处理的工件2.其次加工.需要线切割的工件3.然后加工模架部件即上托和底座4.再后加工其它部件。
5.装配、试模五金冲压模具的分类按完成工序的性质分类,包括冲裁模、弯曲模、拉深模等;按工序的组合程度分类,包括单工序模、级进模、复合模等;按自动化程度分类,包括全自动模、半自动模、手动模;按模具材料分类,包括聚氨酯橡胶模、钢模等;看你从哪个角度说。
如果是按第一种分类,具体包括冲孔模、落料模、切边摸、切断模、剖切模、整修模、切舌模、弯曲模、拉弯模、拉伸模、卷圆模、胀形模、翻边模、翻孔模、缩口模、扩口模、整形模、校平模、精冲模等。
精密模具制造工艺流程_精密模具加工过程

精密模具制造工艺流程_精密模具加工过程精密模具加工流程/精密模具制造工艺过程:审图—备料—加工—模架加工—模芯加工—电极加工—模具零件加工—检验—装配—飞模—试模—生产A:模架加工:1打编号,2A/B板加工,3面板加工,4顶针固定板加工,5底板加工B:模芯加工:1飞边,2粗磨,3铣床加工,4钳工加工,5CNC粗加工,6热处理,7精磨,8CNC精加工,9电火花加工,10省模C:模具零件加工:1行位加工,2压紧块加工,3分流锥浇口套加工,4镶件加工一、模具精密模具加工流程/精密模具制造工艺加工细节描述:1.模芯加工细节1)粗加工飞六边:在铣床上加工,保证垂直度和平行度,留磨余量1.2mm2)粗磨:大水磨加工,先磨大面,用批司夹紧磨小面,保证垂直度和平行度在0.05mm,留余量双边0.6-0.8mm 3)铣床加工:先将铣床机头校正,保证在0.02mm之内,校正压紧工件,先加工螺丝孔,顶针孔,穿丝孔,镶针沉头开粗,机咀或料咀孔,分流锥孔倒角再做运水孔,铣R 角。
4)钳工加工:攻牙,打字码5)CNC粗加工6)发外热处理HRC48-52 7)精磨;大水磨加工至比模框负0.04mm,保证平行度和垂直度在0.02mm之内8)CNC精加工9)电火花加工10)省模,保证光洁度,控制好型腔尺寸。
11)加工进浇口,排气,锌合金一般情况下浇口开0.3-0.5mm,排气开0.06-0.1mm,铝合金浇口开0.5-1.2mm排气开0.1-0.2,塑胶排气开0.01-0.02,尽量宽一点,薄一点。
2.斜顶的加工:知识点:用来处理模具死角(倒勾)的零件。
加工时注意装配尺寸,要求极高。
3.行位的加工:知识点:行位是用来处理模具死角的零件。
加工时注意装配尺寸,要求比较高。
4.镶件的加工:知识点:镶件是为方便加工而产生的,一般情况下后模拆镶件。
像有些模具的插/碰穿位经常拆镶件,原因是那些位置经常磨损,拆镶件后便于修模。
5.前后模运水(水路):知识点:水路是塑胶模具的冷却系统.加工时用钻床加工成型.6.后模顶针位置孔:知识点:顶针是顶出脱模机构的核心零件.对顶针孔加工有很高的配合要求.顶针是标准零件,可以根据需要进行选择。
- 1、下载文档前请自行甄别文档内容的完整性,平台不提供额外的编辑、内容补充、找答案等附加服务。
- 2、"仅部分预览"的文档,不可在线预览部分如存在完整性等问题,可反馈申请退款(可完整预览的文档不适用该条件!)。
- 3、如文档侵犯您的权益,请联系客服反馈,我们会尽快为您处理(人工客服工作时间:9:00-18:30)。
模具的生产工艺
模具是现代工业生产中不可或缺的重要工具,广泛应用于汽车、电子、家电和机械等领域。
下面将简要介绍模具的生产工艺。
模具的生产工艺可以分为设计、加工和装配三个主要步骤。
首先,模具的设计。
在设计模具时,需要根据产品的要求、使用环境和成本等因素进行设计。
设计师需要提供详细的图纸和制造工艺流程,在图纸上标注各个零件的尺寸和要求。
设计师还需要考虑模具的结构和材料选择,以及模具的制造和维护方便性。
接着是模具的加工。
模具加工通常分为粗加工和精加工两个步骤。
粗加工是将大型模具的基础部分进行切削和切割,以获得所需的形状。
精加工是通过刻度、钻孔、铣削、车削等工艺将模具零件进行加工,以达到精确的尺寸和表面质量。
加工过程需要使用各种加工设备和工具,如铣床、钻床、车床和磨床等。
最后是模具的装配。
在装配过程中,将各个加工好的零件按照设计要求进行组合。
装配工人需要将模具的零件进行清洁和检查,确保尺寸和表面光洁度符合要求。
然后依次将各个零件装配在一起,并进行调整和调试,直到模具的功能和精度达到预期。
装配过程中还需要进行防锈和润滑处理,以延长模具的使用寿命。
除了这三个主要步骤,模具的生产工艺还需要涉及一些附加工艺,如热处理、表面处理和质量检测等。
热处理可以改变模具
的组织结构和硬度,提高模具的强度和耐磨性。
表面处理可以提高模具的表面质量和防止氧化腐蚀。
质量检测是确保模具符合设计要求的重要步骤,包括尺寸测量、硬度测试和功能验证等。
总的来说,模具的生产工艺是一个复杂而精细的过程。
通过设计、加工和装配等步骤,可以制造出满足产品要求的模具。
合理的模具生产工艺能够提高模具的质量和寿命,同时也能够提高生产效率和降低成本。
随着科技的不断进步和制造技术的提高,模具生产工艺也在不断创新和发展,为不同行业的生产提供更好的支持。