induction hardening - 齿轮 感应淬火
双频齿轮感应淬火生产线技术原理分析

双频齿轮感应淬火生产线技术原理分析下面两点介绍美国TOCCO公司设计制造的一条内齿轮及恒星齿轮的双频感应淬火生产线原理。
1、内齿轮感应淬火原理此生产线内齿轮每次卸下一件,由相对而立的两个气缸操纵。
当工件处于1号装料位置,一个接近开关动作,使气动往复杆推工件到淬火工位。
此工位有一个可变速度的伺服驱动及垂直扫描的托架。
齿轮到达淬火工位,另一个接近开关动作,于是,立式扫描器将内齿轮从往复杆上托起,并把工件放到感应器下面的定向位置。
有两个接近开美用作专用的定位指示,如果定错位置,工件即回到往复杆,以便再次装料。
错位1s后中频炉即停止运转,与此同时,一个诊断犀示屏幕指示出工件不在淬火工位。
如果内齿轮定位正确,为工件定向工位所接受,扫描机构将把它送入感应器。
一但感应器位于内齿轮中,中频电源开始进行加热,工件旋转.同时扫描机构使工件下降,使感应器扫描并预热内齿轮的全长。
中频预热完成后,扫描定位器上升,回到原来位置,电源转换开关转接刭高频电源,工件再次旋转下降,将预热过的齿轮用高频进行扫描并淬火。
淬火后的内齿轮降下到往复杆后,往复杆推工件到圆火工位,其定位信号动作与淬火工位相同。
回火是一次加热方式,回火时工件是旋转着的。
回火功率较小,是在齿轮高频淬火的闻段时间进行的。
回火工序完成后,齿轮降到往复杆上,推向冷却工位,由喷淋头冷却到装卸温度,然后工件被推向分检工位(合格或剔出)。
剔出是由许多检测装置所确定的。
如果内齿轮被确定剔出,则装在侧面的一个气动卸料杆将水平地将该齿轮推动,并滑到剔出卸料箱;如果齿轮合格则推到出料箱。
2、恒星齿轮的淬火与回火原理此淬火机构动作与内齿轮淬火中频炉相似,工件是在感应器中进行一次加热的。
中频预热及高频加热时。
工件均是旋转的。
高频加热后,淬火液从组合式感应器中喷液。
由于恒星齿轮的结构特点,在它进入回火工位前,必须将附存的淬火液清除掉。
有一个工件轻抖动工位将恒星轮托起呈110角度,并进行抖动,将附存的淬火液排除。
齿轮火焰及感应淬火工艺及其质量控制jbt9171

中华人民共和国机械行业标准
齿轮火焰及感应淬火 工艺及其质量控制
Gear flame or induction hardening process and its quality control
JB/T 9171-1999
代替 ZB/T J17 004—90
1 范围
本标准规定了齿轮火焰及感应淬火(高频、超音频、中频)的有关术语、材料选择、使用设备、 工艺及质量检验。
3 术语
本标准采用下列定义。 3. 1 齿面硬度
成品齿轮轮齿工作高度中间部位的齿面硬度。 3. 2 齿槽底面硬度
国家机械工业局 1999-06-24 批准
2000-01-01 实施
1
JB/T 9171-1999
成品齿轮齿宽中部齿槽底面部位的表面硬度。
3. 3 有效淬硬层深度
齿轮经火焰或感应淬火,并经回火后,于齿宽中部轮齿法截面上,在齿高中部沿垂直于齿面方
表4
表面硬度偏差值 同一件
4 4.5 5
表5
表面硬度偏差值 同一件
8
同一批 5 5.5 6
感应淬火全齿宽硬化工艺你了解多少?
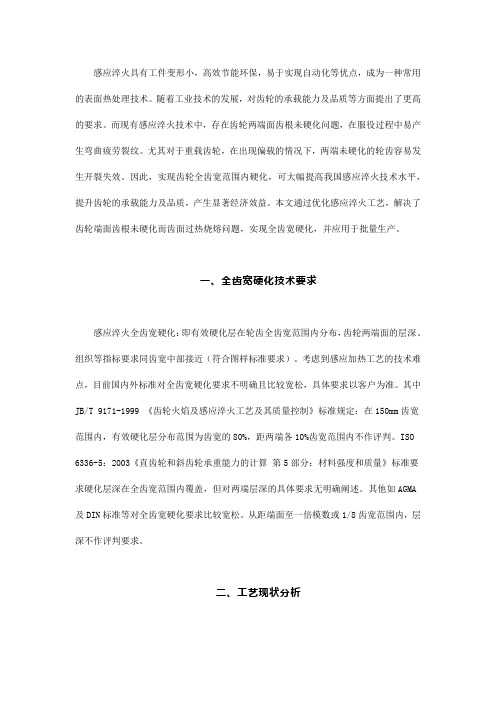
感应淬火具有工件变形小,高效节能环保,易于实现自动化等优点,成为一种常用的表面热处理技术。
随着工业技术的发展,对齿轮的承载能力及品质等方面提出了更高的要求。
而现有感应淬火技术中,存在齿轮两端面齿根未硬化问题,在服役过程中易产生弯曲疲劳裂纹。
尤其对于重载齿轮,在出现偏载的情况下,两端未硬化的轮齿容易发生开裂失效。
因此,实现齿轮全齿宽范围内硬化,可大幅提高我国感应淬火技术水平,提升齿轮的承载能力及品质,产生显著经济效益。
本文通过优化感应淬火工艺,解决了齿轮端面齿根未硬化而齿面过热烧熔问题,实现全齿宽硬化,并应用于批量生产。
一、全齿宽硬化技术要求感应淬火全齿宽硬化:即有效硬化层在轮齿全齿宽范围内分布,齿轮两端面的层深、组织等指标要求同齿宽中部接近(符合图样标准要求)。
考虑到感应加热工艺的技术难点,目前国内外标准对全齿宽硬化要求不明确且比较宽松,具体要求以客户为准。
其中JB/T 9171-1999 《齿轮火焰及感应淬火工艺及其质量控制》标准规定:在150mm齿宽范围内,有效硬化层分布范围为齿宽的80%,距两端各10%齿宽范围内不作评判。
ISO 6336-5:2003《直齿轮和斜齿轮承重能力的计算第5部分:材料强度和质量》标准要求硬化层深在全齿宽范围内覆盖,但对两端层深的具体要求无明确阐述。
其他如AGMA 及DIN标准等对全齿宽硬化要求比较宽松。
从距端面至一倍模数或1/8齿宽范围内,层深不作评判要求。
二、工艺现状分析感应淬火工艺的问题点包括:尖角处涡流集中加热温度高,而内圆角不易加热等。
因此,齿轮在感应加热过程中易出现端部齿面尖角过热烧熔,而内圆角位置的齿根未硬化或硬化层深不足问题,如图1所示。
由于国内外标准对端面的硬化层深要求比较宽松,通常采取降低加热功率方法,防止齿轮出现端面烧熔这一明显的外观质量缺陷,而忽略了端面齿根硬化层深严重偏浅或未硬化的质量隐患。
降低了齿轮的承载能力及品质,存在早期失效风险。
针对该问题,本文通过设计新型感应器结构及调整工艺参数,对感应淬火工艺进行了优化。
感应淬火常见问题及解决措施

中频炉感应淬火件常见淬火缺陷,主要有硬度不够、软块、变形超差与淬火裂纹,还有局部烧熔等。
1、表面淬火后硬度不够:表面淬火后硬度不够是罪常见的问题,其原因亦是多方面的。
1)材料因素①火花鉴别法:这是最简单的方法,检查工件在砂轮上磨出的火花,可大致知道工件的含碳量是否有变化,含碳量越高,火花越多。
②直读光谱仪鉴别钢材的成分,现代化的直读光谱仪能在极短的时间内,将工件材料的各种元素及其含量进行检验并打印出来,可确定钢材是否符合图样要求。
③排除工件表面贫碳或脱碳因素,较常见的冷拔钢材,材料表面有一层贫碳或脱碳层,此时表面硬度低,使用砂轮或锉刀去掉0.5mm后,再测定硬度,如果发现该处硬度比外面为高,并达到要求,这表面工件表面有贫碳或脱碳层。
为进一步验证此问题,可用金相显微镜观察,表面贫碳层得组织与次层得显微组织明显不同,表面只有少量托氏体及大量铁素体,而次层则为马氏体,如果将此样品在保护气体下正火后在检验,表层只有少量珠光体,而次层则有该钢号应有的珠光体面积,如45钢,珠光体面积接近50%2)淬火加热温度不够或预冷时间长淬火加热温度不够或预冷时间太长,致使淬火时温度太低。
以中碳钢为例,前者淬火组织中含有大量未溶铁素体,后者其组织为托氏体或索氏体。
3)冷却不足①特别在扫描淬火时,由于喷液区域太短,工件淬火后,经过喷液区后,心部热量又使表面自回火(阶梯轴大台阶在上位时最易产生),此时表面自回火温度过高,常能从表面颜色及温度感测到。
②一次加热法时,冷却时间太短,自回火温度过高,或由于喷液孔因水垢减少了喷液孔截面积,导致自回火温度过高(带喷液孔的齿轮淬火感应器,最易产生次弊病)。
③淬火液温度过高,流量减少,浓度变化,淬火液中混有油污等。
④喷液孔局部堵塞,其特点是局部硬度不足,软块区常与喷液孔堵塞位置相对应。
感应加热设备之表面热处理表面淬火常见缺陷及对策信息编辑:郑州高氏发布时间:2012-06-21 用交流电流流向被卷曲成环状的导体(通常为铜管),由此产生磁束,将金属放置其中,磁束就会贯通金属体,在与磁束自缴的方向产生窝电流(旋转电流)这感应电流在窝电流的影响下产生发热用这样的加热方式就是感应加热。
Y10T输出齿轮轴的感应淬火
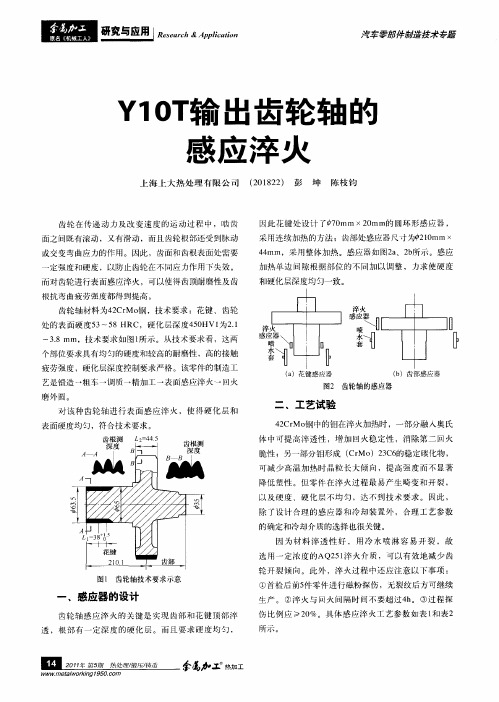
【 )齿 部 感应 器 b
图2 齿 轮轴的感应器
=、工艺试验
4 cr 钢 中的钼在淬火加热时 ,一部分融人 奥氏 2 Mo 体 中可提 高淬透 性 ,增加 回火稳 定性 ,消除第 二 回火 脆性 ;另一部 分钼形成 ( r )2 C 的稳定碳化物 , C Mo 3 6 可减 少高温 加热 时 晶粒长大 倾 向 ,提高 强度而 不显著
.
感应 器的 设计
齿 轮轴 感应 淬火 的关 键是 实现 齿 部和花 键 顶部 淬 透 ,根部 有一 定深 度 的硬化 层 。而且 要求 硬 度均 匀 ,
伤 比例应 ≥2 %。具 体感应 淬火 工艺 参数 如表 l 0 和表 2
所示 。
_ ■ 丝! ! 垫 丝 ! 主笪 塑 竺 笪巫 堡丝
选用 一定浓 度的AQ2 l 火介 质 ,可 以有效地 减少 齿 5淬
轮开 裂倾 向。此 外 ,淬 火过 程中还 应注意 以下事 项 :
图1 齿轮轴技 术要求示意
一
①首检后 前5 件零 件进行磁粉 探伤 ,无裂 纹后方可继续
生 产 。 ② 淬 火 与 回 火 间 隔 时 间 不 要 超 过 4 。 ③过 程 探 h
时 间/ 介 质 s
1 1 8 1 2O 2: 4 0 0 1
lO 2 3 5 8 4 0 %AQ2 ] 5
三 结 果分 析与 讨论
加 热 过程 中 齿部 的齿 顶 、齿根 处均 达 到淬 火所需 温度 ,但淬火后 硬度和硬化层深 均达不到工艺规定 。多 次调整工艺参数 ,还是满足不 了技 术要求 。最后 ,我们
面之 间既 有滚动 ,又有滑动 ,而且齿 轮根部还受到脉动
或 交 变 弯 曲 应 力 的 作 用 。 因此 ,齿 面 和 齿 根 表 面 处 需 要
中频感应淬火的S48C钢齿轮的弯曲疲劳性能研究
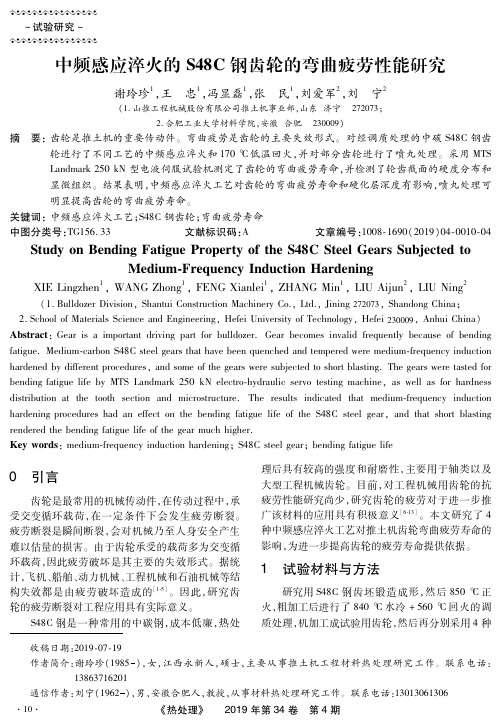
fatigue.MediumcarbonS48Csteelgearsthathavebeenquenchedandtemperedweremediumfrequencyinduction
hardenedbydifferentprocedures,andsomeofthegearsweresubjectedtoshortblasting.Thegearsweretastedfor
hardeningprocedureshadaneffectonthebendingfatiguelifeoftheS48C steelgear,andthatshortblasting
renderedthebendingfatiguelifeofthegearmuchhigher.
Keywords:mediumfrequencyinductionhardening;S48Csteelgear;bendingfatiguelife
2.SchoolofMaterialsScienceandEngineering,HefeiUniversityofTechnology,Hefei230009,AnhuiChina)
Abstract:Gearisaimportantdrivingpartforbulldozer.Gearbecomesinvalidfrequentlybecauseofbending
0 引言
齿轮是最常用的机械传动件,在传动过程中,承 受交变循 环 载 荷,在 一 定 条 件 下 会 发 生 疲 劳 断 裂。 疲劳断裂是瞬间断裂,会对机械乃至人身安全产生 难以估量的损害。由于齿轮承受的载荷多为交变循 环载荷,因此疲劳破坏是其主要的失效形式。据统 计,飞机、船舶、动力机械、工程机械和石油机械等结 构失效都是由疲劳破坏造成的 。 [15] 因此,研 究 齿 轮的疲劳断裂对工程应用具有实际意义。
齿轮高频淬火工作原理

齿轮高频淬火设备采用感应加热,其感应器一般是输入中频或高频交流电(1000-300000Hz或更高)的空心铜管,感应加热的原理是:将齿轮等工件放到感应器内,产生的交变磁场,又在工件中产生出同频率的感应电流,这种感应电流在工件内的分布是不均匀的,利用这个集肤效应,可使齿轮等工件表面迅速加热,在几秒钟内表面温度上升到800-1000℃,而心部温度升高很小,从而满足我们的要求。
高频淬火,是指利用高频电流(30K-1000KHZ)使工件表面局部进行加热、冷却,获得表面硬化层的热处理方法,是对齿轮等工件进行一定深度的表面强化,而心部基本上保持不变,因而具有高强度、高耐磨性和高韧性的天热点,又因是局部加热,所以能显著减少淬火变形,降减能源消耗。
齿轮高频淬火设备的用途:
一、热处理行业:各种电动工具齿轮轴的高频淬火热处理;各种齿轮、各种拔叉、各种花键轴、传动半轴、各种小轴曲柄销、各种摇臂、摇臂轴等高频淬火热处理;五金工具高频淬火热处理,如老虎钳、锤、大力钳、扳手。
二、锻压行业:标准件,紧固件的透热成型;五金工具透热,如钳子,扳手等加热透热成型;钢管透热成型,如弯管等;钢板加热,折弯成型。
三、钎焊:黄铜、紫铜的应用;硬质合金刀具的焊接,如车刀、铣刀、绞刀;探矿用的钻头焊接、如一字钻头,羊角钻头的焊接;金刚石刀头的焊接,如金刚石锯片、磨具、锯齿焊接。
感应淬火 (2)
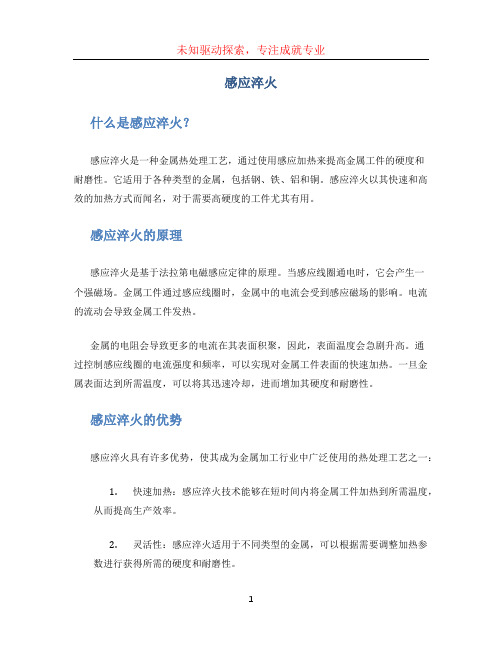
感应淬火什么是感应淬火?感应淬火是一种金属热处理工艺,通过使用感应加热来提高金属工件的硬度和耐磨性。
它适用于各种类型的金属,包括钢、铁、铝和铜。
感应淬火以其快速和高效的加热方式而闻名,对于需要高硬度的工件尤其有用。
感应淬火的原理感应淬火是基于法拉第电磁感应定律的原理。
当感应线圈通电时,它会产生一个强磁场。
金属工件通过感应线圈时,金属中的电流会受到感应磁场的影响。
电流的流动会导致金属工件发热。
金属的电阻会导致更多的电流在其表面积聚,因此,表面温度会急剧升高。
通过控制感应线圈的电流强度和频率,可以实现对金属工件表面的快速加热。
一旦金属表面达到所需温度,可以将其迅速冷却,进而增加其硬度和耐磨性。
感应淬火的优势感应淬火具有许多优势,使其成为金属加工行业中广泛使用的热处理工艺之一:1.快速加热:感应淬火技术能够在短时间内将金属工件加热到所需温度,从而提高生产效率。
2.灵活性:感应淬火适用于不同类型的金属,可以根据需要调整加热参数进行获得所需的硬度和耐磨性。
3.均匀加热:感应淬火能够实现金属表面的均匀加热,可以避免局部热应力和变形。
4.环保:相比传统的加热方式,感应淬火减少了能源消耗和排放,对环境更友好。
感应淬火的应用感应淬火广泛应用于各个行业,包括汽车、机械、航空航天等。
以下是几个常见的应用领域:1.汽车零部件:感应淬火可用于加工发动机气门、凸轮轴和传动轴等零部件,使其具有更高的硬度和耐磨性。
2.钢铁加工:对于一些需要高硬度和耐磨性的钢材,如轴承钢和切割工具钢,感应淬火可以提供更好的性能。
3.电力行业:感应淬火可用于制造电机转子和发电机组件等关键元件,提高其耐用性和效率。
4.金属模具:通过感应淬火处理,金属模具可以获得更高的硬度和表面耐磨性,延长使用寿命。
感应淬火的挑战尽管感应淬火具有许多优势,但也存在一些挑战需要考虑:1.设备成本:感应加热设备的价格相对较高,这可能对小型企业和初创公司构成一定的挑战。
2.参数控制:感应淬火需要准确控制加热参数,包括电流强度、频率和加热时间等。
齿轮淬火芯部硬度

齿轮淬火芯部硬度Gears are an essential part of many machines and equipment, helping to transmit power and motion. With the crucial role that gears play, it is essential to ensure that they are appropriately hardened to withstand the wear and tear that they endure. The hardness of the core of a gear is particularly important, as it affects the overall strength and durability of the gear.齿轮是许多机器和设备的重要组成部分,有助于传输动力和运动。
由于齿轮所扮演的重要角色,确保它们经过适当淬火以承受它们所承受的磨损是至关重要的。
齿轮芯部的硬度尤为重要,因为它影响着齿轮的整体强度和耐久性。
The hardening process of gears can involve various techniques, with one common method being induction hardening. Induction hardening involves heating the gear with an alternating magnetic field to a certain temperature, followed by quenching to achieve the desired hardness. This process allows for precise control over the hardening depth and hardness level, ensuring that the core retains the necessary strength while the surface becomes wear-resistant.齿轮的淬火过程可以涉及各种技术,其中一种常见的方法是感应淬火。
齿轮齿面高频淬火工艺

齿轮齿面高频淬火工艺齿轮是现代机械设备中不可或缺的机械传动元件,广泛应用于各个领域。
齿轮的齿面质量直接影响到机械设备的可靠性和使用寿命。
而齿轮齿面高频淬火工艺则是一种有效提高齿轮齿面硬度和耐磨性的方法。
齿轮齿面高频淬火工艺是指利用高频感应加热原理,在齿轮齿面上形成瞬时高温,并通过淬火介质迅速冷却,使齿面表层形成高硬度的淬火组织。
这种工艺具有淬火速度快、变形小、工件表面质量好等优点,被广泛应用于齿轮制造领域。
高频淬火工艺的核心是高频感应加热设备。
该设备通过电磁感应原理,将电能转化为热能,快速加热齿轮齿面。
在加热过程中,工件表面形成高温区域,同时淬火介质迅速冷却工件,使其形成高硬度的表层。
这种淬火方式具有可控性好、加热均匀等优点,能够满足不同齿轮的淬火要求。
高频淬火工艺的关键是淬火介质的选择。
常用的淬火介质包括水、油和气体。
水冷速度快,但易造成变形和开裂;油冷速度适中,能够有效控制淬火过程,但油污染问题较为突出;气体冷却速度较慢,但能够避免淬火介质的污染。
根据不同齿轮的要求,可以选择不同的淬火介质,以达到最佳的淬火效果。
高频淬火工艺的优点还体现在淬火后的齿轮齿面质量上。
淬火后的齿轮齿面硬度高,耐磨性好,能够承受更大的载荷和更长的使用寿命。
同时,淬火还能改善齿轮齿面的粗糙度和尺寸精度,提高齿轮的传动效率和运行平稳性。
然而,高频淬火工艺也存在一些问题。
首先是设备投资和运行成本较高,需要专门的设备和维护。
其次是淬火过程对工件的变形和开裂问题,需要通过合理的工艺参数和淬火介质选择来解决。
此外,淬火后齿轮齿面的残余应力较大,可能会对工件的稳定性和寿命造成影响,需要进行适当的回火处理。
齿轮齿面高频淬火工艺是一种提高齿轮齿面硬度和耐磨性的有效方法。
通过合理选择淬火介质和优化工艺参数,可以得到理想的淬火效果。
然而,淬火工艺的选择还应结合实际情况,考虑到工件的材料、尺寸和使用条件等因素,以确保齿轮的质量和可靠性。
未来,随着科技的不断进步,淬火工艺将会得到更大的发展和应用。
齿轮齿面高频淬火工艺

齿轮齿面高频淬火工艺齿轮作为机械传动系统中重要的零部件,其质量和性能直接关系到整个机械设备的运行效果。
为了提升齿轮的硬度和耐磨性,高频淬火工艺应运而生。
本文将介绍齿轮齿面高频淬火工艺的原理、过程和应用。
一、原理齿轮齿面高频淬火工艺是利用高频电磁感应加热的原理,在齿轮齿面上形成高温区域,然后迅速冷却,使齿面达到所需的硬度。
其主要原理如下:1. 高频电磁感应加热:通过高频电源产生高频电流,经过感应线圈产生高频磁场,齿轮齿面在高频磁场中感应出涡流,从而产生热量。
2. 热传导:齿面所产生的热量会迅速传导到整个齿轮,使齿轮表面温度升高。
3. 快速冷却:通过喷水、喷气等方式进行快速冷却,使齿轮齿面迅速冷却至所需的温度,形成高硬度。
二、过程齿轮齿面高频淬火工艺的过程一般包括以下几个步骤:1. 准备工作:选择适合的高频电源和感应线圈,根据齿轮的材质和尺寸确定加热参数。
2. 加热:将齿轮放置在感应线圈中,开启高频电源,使齿面产生高温区域,加热时间一般为几秒至几十秒。
3. 冷却:加热后立即进行快速冷却,可以通过喷水、喷气等方式进行,冷却时间一般为几秒至几十秒。
4. 温度控制:通过控制加热时间和冷却时间,控制齿轮齿面的温度,以达到所需的硬度。
三、应用齿轮齿面高频淬火工艺在机械制造领域中有着广泛的应用,主要体现在以下几个方面:1. 提升齿轮硬度:高频淬火可以使齿轮表面的硬度显著提高,提高齿轮的耐磨性和承载能力,延长齿轮的使用寿命。
2. 改善齿轮的表面质量:高频淬火可以消除齿轮表面的毛刺和氧化层,提高齿面的光洁度和平整度,减小齿轮的摩擦和噪音。
3. 提高生产效率:高频淬火具有加热速度快、冷却均匀等优点,可以大幅度提高齿轮的生产效率,缩短生产周期。
4. 适用于各种材质和尺寸的齿轮:高频淬火适用于各种材质的齿轮,包括低碳钢、高碳钢、合金钢等,也适用于各种尺寸的齿轮,从小型齿轮到大型齿轮都可以进行高频淬火处理。
齿轮齿面高频淬火工艺通过高频电磁感应加热和快速冷却的方式,可以提升齿轮的硬度和耐磨性,改善齿轮的表面质量,提高生产效率,适用于各种材质和尺寸的齿轮。
齿轮仿齿形连续感应加热淬火工艺研究

齿轮仿齿形连续感应加热淬火工艺研究齿轮是一种常见的机械传动装置,其结构复杂,制造过程也十分严谨。
其中,齿轮齿形的精度对于齿轮的传动效率、噪声和寿命等方面都有着重要的影响。
因此,如何提高齿轮的齿形精度和耐磨性成为了齿轮制造业面临的一个重要问题。
齿轮仿齿形连续感应加热淬火工艺是一种新兴的齿轮淬火工艺,其原理是通过感应加热技术对齿轮齿面进行加热处理,使其达到淬火的温度,然后通过水冷快速冷却,使齿面产生高硬度的淬火组织,从而提高齿轮的耐磨性和齿形精度。
该工艺的具体步骤如下:1.齿轮的仿齿形加工在仿齿形加工过程中,需要确保齿轮的齿形精度符合要求。
通常采用数控加工中心进行加工,以保证齿轮齿形的精度和表面质量。
2.齿轮的表面清洗在加热淬火前需要对齿轮表面进行清洗,以去除表面的油污和杂质,保证淬火效果。
3.齿轮的感应加热将齿轮放置在感应加热器中,对齿轮的齿面进行加热处理。
在加热过程中需要控制加热温度和时间,以确保齿轮的齿面达到淬火的温度。
4.齿轮的快速冷却加热结束后,齿轮需要立即进行快速冷却,通常采用水冷的方式进行冷却。
通过快速冷却可以使齿面产生高硬度的淬火组织,提高齿轮的耐磨性和齿形精度。
5.齿轮的回火处理经过淬火处理后的齿轮会产生一定的残余应力,需要进行回火处理以消除残余应力,并提高齿轮的韧性和抗疲劳性能。
总之,齿轮仿齿形连续感应加热淬火工艺是一种能够有效提高齿轮的齿形精度和耐磨性的新型工艺,具有以下几个优点:1.提高齿轮的硬度和韧性通过仿齿形连续感应加热淬火工艺处理后,齿轮的表面硬度得到提高,可以更好地耐受强烈的磨损和冲击,提高齿轮的耐用性和韧性。
2.提高齿轮的精度仿齿形连续感应加热淬火工艺可实现齿轮的局部淬火,齿面硬度均匀,避免了传统淬火工艺中齿根处淬火不足的问题,同时可避免过渡淬火造成的齿面变形,从而提高齿轮的齿形精度和传动效率。
3.生产效率高采用仿齿形连续感应加热淬火工艺,生产效率高。
整个工艺流程中只需要进行一次淬火,且淬火加热和冷却时间短,可以大大提高生产效率。
感应淬火工艺流程

感应淬火工艺流程Induction hardening is a specialized heat treatment process that is commonly used in the manufacturing industry to increase the hardness and wear resistance of metal components. This process involves the use of high frequency induction heating to selectively harden specific areas of a metal part, such as the surface or a specific region of the part.感应淬火是一种专门的热处理工艺,通常在制造业中用于增加金属零部件的硬度和耐磨性。
这个过程涉及使用高频感应加热来选择性地硬化金属零件的特定区域,比如表面或零部件的特定区域。
One of the key advantages of induction hardening is its ability to provide localized hardening without affecting the overall properties of the metal part. This means that manufacturers can achieve the desired hardness and wear resistance in specific areas of a part, while maintaining the desired properties in other areas.感应淬火的一个关键优势是它能够在不影响金属零件整体性能的情况下提供局部硬化。
这意味着制造商可以在零件的特定区域实现所需的硬度和耐磨性,同时保持其他区域的所需性能。
齿轮高频淬火

齿轮高频淬火齿轮高频淬火是一种常用的齿轮表面处理技术,其目的是提高齿轮的硬度和耐磨性。
本文将从淬火原理、工艺流程、优点和应用等方面,介绍齿轮高频淬火的相关知识。
一、淬火原理齿轮高频淬火是利用高频感应加热技术,在齿轮表面局部加热至淬火温度,然后迅速冷却,使齿轮表面发生相变,从而提高其硬度。
这种淬火方式具有以下特点:1. 局部加热:只对齿轮表面进行加热,不影响齿轮的整体性能。
2. 快速冷却:迅速冷却可以使齿轮表面形成致密的马氏体组织,提高硬度。
3. 淬火温度控制:通过调整加热功率和加热时间,可以精确控制淬火温度,以满足不同齿轮的要求。
二、工艺流程齿轮高频淬火的工艺流程主要包括以下几个步骤:1. 清洗:将齿轮表面的油污和杂质清洗干净,以保证淬火效果。
2. 预热:将齿轮整体加热至一定温度,以减少温度梯度,防止齿轮变形。
3. 加热:利用高频感应加热设备对齿轮表面进行局部加热,使其达到淬火温度。
4. 淬火:迅速冷却齿轮表面,使其形成马氏体组织。
5. 温度回火:将齿轮加热至一定温度,保持一段时间,以减少残余应力和改善齿轮的韧性。
6. 冷却:将齿轮冷却至室温,完成整个淬火工艺。
三、优点齿轮高频淬火具有以下优点:1. 提高齿轮的硬度:淬火后,齿轮表面的硬度可以达到50-60HRC,大大提高了齿轮的耐磨性。
2. 改善齿轮的强度:淬火后,齿轮表面形成的马氏体组织可以提高齿轮的强度和承载能力。
3. 减少齿轮变形:高频淬火过程中的快速冷却可以减少齿轮的热变形,保证齿轮的精度和几何形状。
4. 提高生产效率:高频感应加热技术具有加热速度快、温度控制精确等优点,可以大大提高生产效率。
四、应用领域齿轮高频淬火广泛应用于各个行业的齿轮制造中,特别是对于高精度、高负载的齿轮产品,更是必不可少的工艺。
主要应用领域包括:1. 汽车工业:汽车变速箱、差速器等关键部件的齿轮。
2. 机械工业:工程机械、冶金机械等的传动齿轮。
3. 航空航天工业:飞机、火箭等航空航天器的传动齿轮。
感应淬火

7.不仅用在表面淬火还可用在穿透加热与化学热处理等。载线、电容器、变压器、感应器、机床几部分组成。
感应淬火分类
感应淬火类型分为:工频、低频、中频、超音频、高频、超高频几种,根据淬硬深度需要来选择适用频率。淬硬层深度越大,所需频率越低,反之,则越高。
感应淬火英文名称:induction hardening定义:利用感应电流通过材料或工件所产生的热量,使材料或工件表层、局部或整体加热并快速冷却的淬火。
简介
感应淬火(induction hardening)
感应加热就是利用电磁感应在工件内产生涡流而将工件进行加热。感应加热表面淬火与普通淬火比具有如下优点:
1.热源在工件表层,加热速度快,热效率高
感应淬火设备
2.工件因不是整体加热,变形小
3.工件加热时间短,表面氧化脱碳量少
4.工件表面硬度高,缺口敏感性小,冲击韧性、疲劳强度以及耐磨性等均有很大提高。有利于发挥材料的潜力,节约材料消耗,提高零件使用寿命
5.设备紧凑,使用方便,劳动条件好
6.便于机械化和自动化
目前感应淬火以中频、超音频、高频、超高频为主。
中频一般为可控硅,目前国内有用IGBT感应电源做中频的,比可控硅节能,但是价格较可控硅的高。相对来说,IGBT是发展趋势,因其转换效率较高,而且性能稳定,内部实现软开关,不容易出故障。
超音频、高频则是IGBT感应电源。目前国内IGBT感应电源已经历三代。第一代为窄频率多主板为显著特征。第二代则是宽频率范围,单一主板为主要特征。第三代,则从技术结构上进行了革命性的改变,实现数字化控制,能传输和储存能量监控数据,便于实现标准化管理。
感应淬火的研究
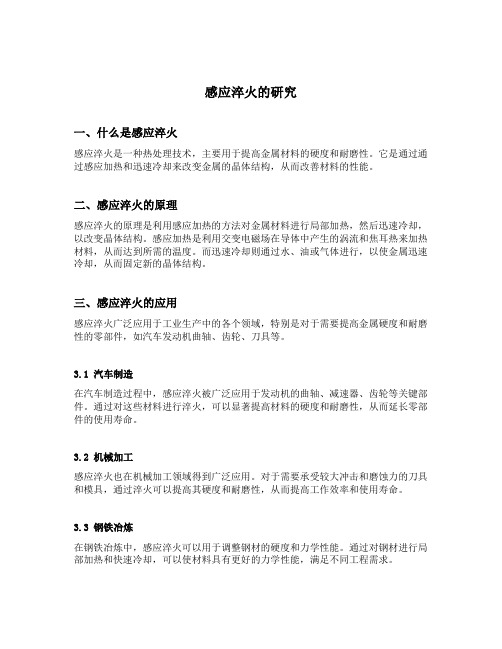
感应淬火的研究一、什么是感应淬火感应淬火是一种热处理技术,主要用于提高金属材料的硬度和耐磨性。
它是通过通过感应加热和迅速冷却来改变金属的晶体结构,从而改善材料的性能。
二、感应淬火的原理感应淬火的原理是利用感应加热的方法对金属材料进行局部加热,然后迅速冷却,以改变晶体结构。
感应加热是利用交变电磁场在导体中产生的涡流和焦耳热来加热材料,从而达到所需的温度。
而迅速冷却则通过水、油或气体进行,以使金属迅速冷却,从而固定新的晶体结构。
三、感应淬火的应用感应淬火广泛应用于工业生产中的各个领域,特别是对于需要提高金属硬度和耐磨性的零部件,如汽车发动机曲轴、齿轮、刀具等。
3.1 汽车制造在汽车制造过程中,感应淬火被广泛应用于发动机的曲轴、减速器、齿轮等关键部件。
通过对这些材料进行淬火,可以显著提高材料的硬度和耐磨性,从而延长零部件的使用寿命。
3.2 机械加工感应淬火也在机械加工领域得到广泛应用。
对于需要承受较大冲击和磨蚀力的刀具和模具,通过淬火可以提高其硬度和耐磨性,从而提高工作效率和使用寿命。
3.3 钢铁冶炼在钢铁冶炼中,感应淬火可以用于调整钢材的硬度和力学性能。
通过对钢材进行局部加热和快速冷却,可以使材料具有更好的力学性能,满足不同工程需求。
3.4 其他行业应用此外,感应淬火还可以用于其他行业的热处理需求,例如航空航天、船舶制造、电子设备等。
通过感应淬火技术,这些行业可以提高产品的质量和性能,提高工作效率。
四、感应淬火的优势感应淬火相对于传统的淬火方法具有一些明显的优势。
1.高效:感应加热可以实现局部加热,避免了整体加热的热能浪费,提高了能源利用率。
同时,感应淬火的加热速度快,可以缩短生产周期,提高生产效率。
2.均匀性好:感应加热可以实现局部加热,能够更好地控制材料的温度分布,避免了由于不均匀加热导致的变形和裂纹。
3.精确控制:感应加热设备可以实时监控和控制温度,可以精确控制加热温度和保持时间,以确保淬火的效果。
齿轮感应淬火要求
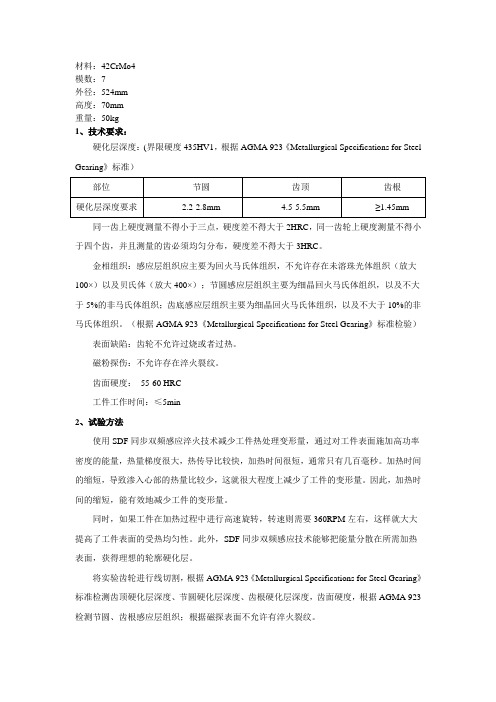
材料:42CrMo4模数:7外径:524mm高度:70mm重量:50kg1、技术要求:硬化层深度:(界限硬度435HV1,根据AGMA 923《Metallurgical Specifications for Steel Gearing》标准)部位节圆齿顶齿根硬化层深度要求 2.2-2.8mm 4.5-5.5mm ≥1.45mm 同一齿上硬度测量不得小于三点,硬度差不得大于2HRC,同一齿轮上硬度测量不得小于四个齿,并且测量的齿必须均匀分布,硬度差不得大于3HRC。
金相组织:感应层组织应主要为回火马氏体组织,不允许存在未溶珠光体组织(放大100×)以及贝氏体(放大400×);节圆感应层组织主要为细晶回火马氏体组织,以及不大于5%的非马氏体组织;齿底感应层组织主要为细晶回火马氏体组织,以及不大于10%的非马氏体组织。
(根据AGMA 923《Metallurgical Specifications for Steel Gearing》标准检验)表面缺陷:齿轮不允许过烧或者过热。
磁粉探伤:不允许存在淬火裂纹。
齿面硬度:55-60 HRC工件工作时间:≤5min2、试验方法使用SDF同步双频感应淬火技术减少工件热处理变形量,通过对工件表面施加高功率密度的能量,热量梯度很大,热传导比较快,加热时间很短,通常只有几百毫秒。
加热时间的缩短,导致渗入心部的热量比较少,这就很大程度上减少了工件的变形量。
因此,加热时间的缩短,能有效地减少工件的变形量。
同时,如果工件在加热过程中进行高速旋转,转速则需要360RPM左右,这样就大大提高了工件表面的受热均匀性。
此外,SDF同步双频感应技术能够把能量分散在所需加热表面,获得理想的轮廓硬化层。
将实验齿轮进行线切割,根据AGMA 923《Metallurgical Specifications for Steel Gearing》标准检测齿顶硬化层深度、节圆硬化层深度、齿根硬化层深度,齿面硬度,根据AGMA 923 检测节圆、齿根感应层组织;根据磁探表面不允许有淬火裂纹。
一种用于齿轮表面淬火的感应加热装置及齿轮表面淬火方法[发明专利]
![一种用于齿轮表面淬火的感应加热装置及齿轮表面淬火方法[发明专利]](https://img.taocdn.com/s3/m/b797a214a4e9856a561252d380eb6294dd88228d.png)
(19)中华人民共和国国家知识产权局(12)发明专利申请(10)申请公布号 (43)申请公布日 (21)申请号 201811321976.3(22)申请日 2018.11.08(71)申请人 燕山大学地址 066004 河北省秦皇岛市海港区河北大街西段438号(72)发明人 韩毅 肖瑶 (74)专利代理机构 北京挺立专利事务所(普通合伙) 11265代理人 刘阳(51)Int.Cl.C21D 1/10(2006.01)C21D 1/667(2006.01)C21D 9/32(2006.01)(54)发明名称一种用于齿轮表面淬火的感应加热装置及齿轮表面淬火方法(57)摘要本发明公开了一种用于齿轮表面淬火的感应加热装置及齿轮表面淬火方法,涉及热处理领域。
本发明中的感应加热装置,包括相互逆向旋转的加热齿轮轴、工件齿轮轴,安装于加热齿轮轴上的感应加热齿轮,安装于工件齿轮轴上的待淬火齿轮工件;所述感应加热齿轮与待淬火齿轮工件无接触啮合;所述感应加热齿轮的齿为仿齿形感应线圈。
本发明采用形状与工件啮合齿轮相似的感应线圈对工件进行旋转式扫描加热,感应线圈与工件同时旋转时,工件与感应线圈上定位滑轮的接触点始终在啮合线上,可以有效加热工件承受载荷的位置,提高加热深度,水冷后增加该位置的硬化层厚度,从而提高工件的使用寿命并减小均匀加热带来的能量损耗。
权利要求书1页 说明书5页 附图5页CN 109112259 A 2019.01.01C N 109112259A1.一种用于齿轮表面淬火的感应加热装置,其特征在于:包括相互逆向旋转的加热齿轮轴、工件齿轮轴,安装于加热齿轮轴上的感应加热齿轮,安装于工件齿轮轴上的待淬火齿轮工件;所述感应加热齿轮与加热齿轮轴上同轴旋转,所述待淬火齿轮工件与工件齿轮轴上同轴旋转;所述感应加热齿轮与待淬火齿轮工件无接触啮合;所述感应加热齿轮的齿为仿齿形感应线圈。
2.根据权利要求1所述的一种用于齿轮表面淬火的感应加热装置,其特征在于:所述加热齿轮轴以及工件齿轮轴活动固定在底座上,所述加热齿轮轴上固定中心轮,所述工件齿轮轴固定行星轮,所述中心轮与行星轮啮合。
- 1、下载文档前请自行甄别文档内容的完整性,平台不提供额外的编辑、内容补充、找答案等附加服务。
- 2、"仅部分预览"的文档,不可在线预览部分如存在完整性等问题,可反馈申请退款(可完整预览的文档不适用该条件!)。
- 3、如文档侵犯您的权益,请联系客服反馈,我们会尽快为您处理(人工客服工作时间:9:00-18:30)。
eldec Induction USA Inc.
Agenda:
1. 2. 3. Introduction of eldec What is Contour True Hardening? Why bother with Hardening as an integral part of the process chain? 4. Workpiece and Manufacturing modifications to incorporate Hardening into the process chain 5. 6. 7. 8. The eldec SDF® process Case studies Products and Systems Q&A
TOTAL PROCESS TIME FEASIBILITY OF SINGLE-PIECE PART FLOW
MULTIPLE HOURS ++
30 – 60 SEC.
< 30 SEC.
VERY LOW
MEDIUM
HIGH
++ Rule of thumb for carburizing is 1 hr per 0.1 mm carb depth (eg., 1.5 mm depth in 15 hours at 1 atmosphere)
In-Line Induction Hardening
eldec Induction USA Inc.
4.
Workpiece and Manufacturing modifications to incorporate Hardening into the process chain SUITABLE MATERIAL: C > 0.35% SUITABLE WORKPIECE AND LOT SIZE SHORT PROCESS TIME = HIGH POWER DENSITY
Data not available
Hardening With Single Frequency Hardening With Dual Frequency eldec SDF® Total Power: 450 kW HF Total Power: 820 kW HF + MF Heat Time: 12 sec pulsed Heat Time: 0.32 sec Energy Used: ≈ 3000 kWs Energy Used: ≈ 290 kWs
eldec Induction USA Inc.
3.
Why bother with Hardening as an integral part of the process chain?
■ TO LOWER COST
Line with remote carburizing ovens
■ TO SAVE TIME ■ TO SAVE ENERGY
PROCESS CAPABILITY (SPC) FLEXIBILITY ENVIRONMENTAL IMPACT ENERGY EFFICIENCY
NEUTRAL HIGH HIGH LOW
POSITIVE MEDIUM LOW MEDIUM
POSITIVE PLUS HIGH VERY LOW HIGH
eldec Inductiot is Contour True Hardening? Process Comparison
Carburization True contour 1. Carburizing the case above Ac3 in oven Induction Single Frequency Non-true contour 1. Single frequency coil induces eddy current in workpiece 2. Quench to harden with fluids 3. Temper to achieve case depth hardness based on mechanical properties required. Quenched and tempered steels with C > 0.35%, example 1040 or 4140 (42CrMo4) Induction Simultanious Dual Frequency SDF® True contour 1. Simultaneous dual frequency coil induces eddy current in workpiece 2. Quench to harden with fluids 3. Temper to achieve case depth hardness based on mechanical properties required. Quenched and tempered steels with C > 0.35%, example 1040 or 4140 (42CrMo4)
Suitable Materials
Sectioned Parts:
eldec Induction USA Inc.
2.
What is Contour True Hardening? Comparison of Workpiece Mechanical Properties
Carburization TRUE CONTOUR Induction Single Frequency NON TRUE CONTOUR Induction Simultanious Dual Frequency SDF® TRUE CONTOUR
eldec Induction USA Inc.
Medium frequency only
A = MF- inductor current B = Eddy current C = Heat mainly in root of gear tooth
With medium frequency the root area of the teeth will be heated rather then the tip of the teeth. The inductive current is canceling out in the flange area, due to the lower frequencies (D too small for lower frequencies).
eldec Induction USA Inc.
The broad range generator program consists of medium frequency and high frequency generators starting at 1.5 kW to 500kW as well as the SDF®-Generators starting at 15 to 3000 kW.
eldec Induction USA Inc.
2.
What is Contour True Hardening? Comparison of Additional Process Considerations
Process Carburization TRUE CONTOUR Induction Single Frequency NON TRUE CONTOUR Induction Simultanious Dual Frequency SDF® TRUE CONTOUR
Process
Process Principals
2. Quench to harden with fluids or gases 3. Temper to achieve case depth hardness based on mechanical properties required. Quenched and tempered carburized steels with C < 0.25%, example 5115 (16MnCr5)
Process
WEAR RESISTANT CASE PART DISTORTION DUCTILE CORE STRUCTURE TENSILE STRENGTH
++ HIGH +
CORE HARDNESS ACHIEVED IN PROCESS
++ MEDIUM +
++ LOW + +
+
Thru Hard teeth
eldec Induction USA Inc
Company History
1982 Formation of eldec Schwenk Induktorbau GmbH by Wolfgang Schwenk. Vision for application and development of Induction technology and coil design. 1993 Delivery of the first eldec-designed IGBT high frequency and medium frequency generators. 1998 eldec Induction USA was founded. 2000 Delivery of the first Dual Frequency SDF® generators. 2004 Delivery of the first 1-MW SDF® hardening system. 2006 Completion of the first 3-MW SDF® hardening system. 2008 Modular Induction (MIND) Hardening Machine introduced at AMB Stuttgart. 2009 The SDF®-Technology is gaining further market share. eldec establishes Sales and Service facility in China.