机械制造技术 孔的常规加工方法25页PPT
孔的加工PPT课件
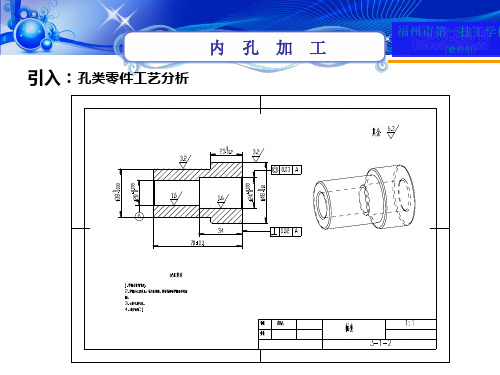
钻孔时,钻头与工件之间的相对运动称为钻削运动。钻削运动由 如下两种运动构成: (1)主运动
钻孔时,钻头装在钻床主轴(或其他机械)上所做的旋转运动称 为主运动。 (2)进给运动 钻头沿轴线方向的移动称为进给运动。
内孔加工
福州市第一技工学校
(数控组)
2、钻削特点
➢ 钻削时,钻头是在半封闭的状态下进行切削的,转速高,切削用量大, 排屑又很困难,因此钻削具有如下特点:
(3)手动进给 通孔将要钻穿时,必须减小进给量,如果采用自动进给,则应改为 手动进给。
内孔加工
福州市第一技工学校
(数控组)
➢ 钻孔时,由于加工零件的材料和加工要求不同,所用切削液的种类和 作用就不同。钻孔一般属于粗加工,又是半封闭状态加工,摩擦严重, 散热困难,加切削液的目的应以冷却为主。
一般用煤油;钻削铸铁、黄铜、青铜时,一般不用切削液;钻削 镁合金时,切忌用切削液。
内孔加工
福州市第一技工学校
(数控组)
➢ ②进给量 孔的精度要求较高且表面粗糙度值较小时,应选择较小的进给量;
钻较深孔、钻头较长以及钻头刚性、强度较差时,也应选择较小的进 给量。
福州市第一技工学校
(数控组)
内孔加工
(2)修磨主切削刃 修磨主切削刃,主要
是磨出二重顶角。延长钻头 寿命,减少孔壁的残留面积, 降低孔的表面粗糙度值。
福州市第一技工学校
(数控组)
内孔加工
(3)修磨前刀面 修磨主切削刃和副切
削刃交角处的前刀面, 磨去一块,如图中阴影 部位所示,这样可提高 钻头强度。钻削黄铜时, 还可避免切削刃过分锋 利而引起扎刀现象。
➢ 硬质合金钻头有整体式和镶嵌式。直径较小的常做成整体式;直径较大 的常做成镶嵌式,它是在钻头切削部分嵌焊硬质合金刀片 硬质合金刀片的材 料是YG8或YT2。
数控孔加工PPT课件
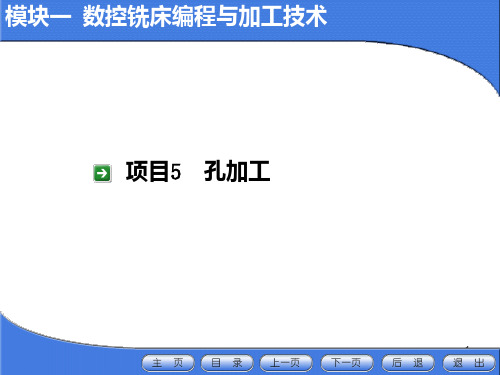
.
19
模块一 数控铣床编程与加工技术
2.钻(扩)孔循环G81与锪孔循环G82
一般钻孔循环指令G81 格式:G98(G99)G81X_Y_Z_R_F_
刀具以进给速度向下运动钻孔,到达孔底 位置后,快速退回(无孔底动作),用于一般定 点钻。 带停顿的钻孔循环指令G82
格式:G98(G99)G82X_Y_Z_R_P_ F_ 与G81指令唯一的区别是有孔底暂停动作, 暂停时间由P指定。执行该指令使孔的表面更光 滑,孔底平整。常用于做沉头台阶孔。
5000个/年。
图5-1 端盖零件图
.
2
模块一 数控铣床编程与加工技术
5.2 知识链接
5.2.1 孔加工工艺知识
1.孔的加工方法 在数控铣床上加工孔的方法很多,根据孔的尺寸精度、 位置精度及表面粗糙度等要求,一般有点孔,钻孔、扩 孔,锪孔、铰孔、镗孔及铣孔等。常用孔的加工方法如 表5-1所示。
.
3
.
15
模块一 数控铣床编程与加工技术
③ 固定循环编程格式 孔加工循环的通用编程格式如下: G73~G89 X Y Z R Q P F K ; X Y :孔在XY平面内的位置; Z :孔底平面的位置; R :R点平面所在位置; Q :G73和G83深孔加工指令中刀具每次加工深度或G76和G87 精镗孔指令中主轴准停后刀具沿准停反方向的让刀量; P :指定刀具在孔底的暂停时间,数字不加小数点,ms。
孔加工导入量(图5-6中ΔZ) 是指在孔加工过程中,刀具自快 进转为工进时,刀尖点位置与孔 上表面间的距离。导入量通常取 2~5mm。超越量如图1-中的 ΔZ'所示,当钻通孔时,超越 量通常取ZP+(1~3)mm,ZP为 钻尖高度(通常取0.3倍钻头直 径);铰通孔时,超越量通常取 3~5 mm;镗通孔时,超越量通 常取1~3 mm。
常用加工方法教学课件ppt

xx年xx月xx日
目录
• 加工方法介绍 • 加工技术特点 • 加工方法比较 • 加工精度及效率分析 • 选择合适的加工方法
01
加工方法介绍
机械加工
定义
机械加工是一种通过切削、磨 削或研磨等手段,将原材料表 面加工成所需要的外形和尺寸
的过程。
分类
车削、铣削、钻孔、磨削、齿轮 加工等。
应用范围
广泛应用于汽车、船舶、航空航天 、电子等领域。
数控加工
定义
数控加工是一种利用数字控制技术 对工件进行加工的方法。
组成
数控装置、数控机床和编程器。
分类
数控铣削、数控车削、数控电火花 加工等。
应用范围
广泛应用于复杂零件的精密加工和 批量生产。
成型加工
定义
成型加工是一种通过模具或其 他工具来加工工件,使其形状
和尺寸符合要求的方法。
分类
铸造、锻造、冲压、塑料成型 等。
应用范围
广泛应用于制造各类结构件、 钣金件、塑料制品等。
02
加工技术特点
机械加工技术特点
总结词
高效、精准、低成本。
详细描述
机械加工技术是指利用切削、磨削、钻孔等方式,将工件材料去除加工成所需形状和尺寸的技术。其高效、精 准的特点使其成为制造业中应用最广泛的加工方法之一。此外,机械加工技术还具有低成本的优势,适用于大 规模生产和小批量生产。
03
加工方法比较
机械加工与数控加工比较
机械加工
使用传统机械工具,如机床、刀具等进行加工,工艺成熟, 可批量生产,但精度和效率较低,劳动力成本高。
数控加工
采用数控机床、计算机编程等技术,实现高精度、高效率、 自动化生产,但设备投入成本高,技术要求较高。
机械制造技术基础课件最新版第一章机械加工方法

Δm=0 材料基本不变原理,如铸造、锻造及模具成形(注塑、冲压等) 工艺,在成形前后,材料主要是发生形状变化,而质量基本不变。
Δm>0 材料累加成形原理,如20世纪80年代出现的快速原形(Rapid Prototyping)技术,在成形过程中通过材料累加获得所需形状。
第二节 机械加工方法
按照铣削时主运动速度方向与工件进方向的相同或相反,又分为顺铣 和逆铣。
顺铣:铣削力的水平分力与工件的进给方 向相同,而工作台进给丝杠与固定螺母之间一般又 有间隙存在,因此切削力容易引起工件和工作台一 起向前窜动,使进给量突然增大,容易引起打刀。
在顺铣铸件或锻件等表面有硬皮的工件时
二、等材制造技术(Δm=0) 等材制造技术主要是指用模具成形的方法,成形前后,材料质量基本不
变,只是形状的改变。
值得注意的是,统计数据表明,机电产品40%~50%的零件是由模具成 形的,因此模具的作用是显而易见的。模具可分为注塑模、压铸模、锻模、 冲压模、吹塑模等。在我国模具的设计与制造是一个薄弱环节。模具制造 精度一般要求较高,其生产方式往往是单件生产。模具的设计要用到CAD、 CAE等一系列技术,是一个技术密集型的产业。
图1-10 电火花加工原理示意图 1—床身 2—立柱 3—工作台 4—工件电极 5—工具电极 6—进给机构 7—工作液 8—脉冲电源 9—工作液循环过滤系统
第三节 特种加工
电火花加工机床已有系列产品,根据加工方式,可将其分成两种类型: ➢用特殊形状的电极工具加工相应工件的电火花成形加工机床(如前所述); ➢用线(一般为钼丝、钨丝或铜丝)电极加工二维轮廓形状工件的电火花线切割机床。
机械制造技术ppt课件完整版
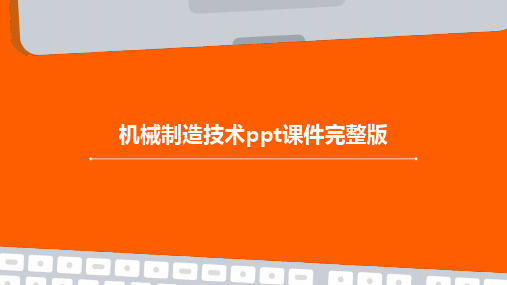
•机械制造技术概述•机械制造工艺基础•先进制造技术目录•自动化制造系统•现代生产管理方法•绿色制造与可持续发展•未来展望与挑战01机械制造技术概述定义与发展历程定义机械制造技术是指通过加工、装配、调试等手段,将原材料或零部件转化为具有特定功能和使用价值的机械产品的过程。
发展历程机械制造技术经历了手工制造、机械化制造、自动化制造和智能制造等阶段,不断向着高效、高精度、高质量的方向发展。
1 2 3机械制造技术是工业发展的基础,为国民经济各部门提供装备和技术支持,推动工业化和现代化进程。
促进工业发展机械制造技术通过优化生产流程、提高加工精度和效率,降低生产成本,提高企业的竞争力和经济效益。
提高生产效率机械制造技术的不断创新和发展,为制造业提供了更多的可能性,推动了新技术、新工艺和新产品的不断涌现。
推动技术创新机械制造技术的重要性机械制造技术的分类及应用领域分类机械制造技术可分为金属切削加工技术、特种加工技术、装配与调试技术等。
应用领域机械制造技术广泛应用于汽车、航空航天、能源、轨道交通、模具等领域,为这些领域的发展提供了重要的技术支持。
02机械制造工艺基础切削运动、切削力、切削热等切削加工的基本概念车刀、铣刀、钻头等刀具的种类与结构车床、铣床、钻床等切削机床的组成与分类车削、铣削、钻削等切削加工的应用实例切削加工原理及设备铸造方法、铸造合金、铸造缺陷与防止铸造工艺锻造方法、锻造设备、锻造缺陷与防止锻造工艺焊接方法、焊接材料、焊接接头设计与工艺焊接工艺砂型铸造、自由锻、电弧焊等铸造、锻造与焊接的应用实例铸造、锻造与焊接工艺A BC D热处理与表面处理技术热处理工艺退火、正火、淬火、回火等热处理与表面处理的原理及设备加热炉、淬火槽、电镀设备等表面处理技术电镀、喷涂、化学转化膜等热处理与表面处理的应用实例调质处理、渗碳淬火、镀锌等03先进制造技术数控加工技术概述数控加工设备数控编程技术数控加工工艺数控加工技术01020304定义、发展历程、应用领域等。
孔的加工.ppt

利用孔加工刀具在钻床上进行各种类型的 孔加工的切削方法。可进行粗加工、半精 加工和精加工。 主运动:刀具的旋转运动; 进给运动:刀具或工件的平动。
特点:钻削加工属于定尺寸切削加工, 孔径尺寸受到刀具直径的限制。
二、钻削特点
钻削时钻头是在半封闭状态下进行切削,转速高、 切削量大,排屑困难。特点如下: 1.摩擦严重,需要较大的钻削力; 2.产生的热量多,传导、散热困难; 3.钻头的高速旋转和较高的切削温度,易磨损; 4.由于钻削时的挤压和摩擦,易产生孔壁的“冷作 硬化”现象,给下道工序增加困难; 5.钻头细而长,钻孔容易产生振动; 6.加工精度低,尺寸精度可达IT11左右的,粗糙度 一般为Ra50~12.5。只能加工要求不高的孔或作为 孔的粗加工。
夹住或卸下。
2.钻夹套 钻头套又称钻套或钻库,是用来装夹锥柄钻头的夹具。 钻套以莫氏锥度为标准,以不同尺寸,组成一组。
锥柄钻头的柄部采用1号至6呈莫氏锥体。 直径6~15.5mm为1号莫氏锥体; 直径15.6~23.5mm为2号莫氏锥体; 直径23.6~32.5mm为3呈莫氏锥体; 直径32.6~49.5mm为4号莫氏锥体; 直径49.6~65mm为5号莫氏锥体; 直径65~80mm为6号莫氏锥体。 一般立式钻床的主轴孔为3号或4号莫氏锥体,摇臂 钻床的主轴孔是5号或6号莫氏锥体。当用较小直径的钻 头钻孔时,钻头的莫氏锥柄不能直接与钻床主轴孔相配合, 就要用钻头套“过渡” 夹持,因此钻头套又称为过渡锥套。
S型横刃钻
钻孔时的切削用量
一、钻孔时的切削用量
(一)切削用量 1.切削速度v
钻孔时的切削速度,是指钻头切削刃上最外一点(直径处)的线速 度。单位为m/min。与钻头直径及转速有关。
v
Dn
孔加工ppt
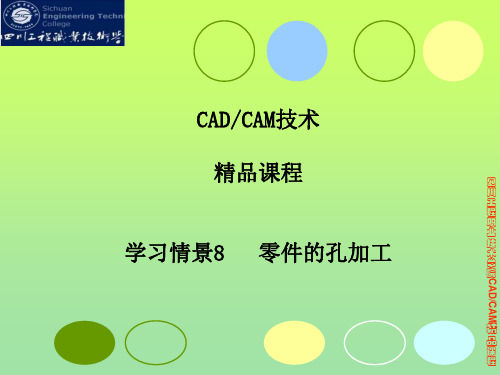
CAD/CAM
精 品
课 程
四 川 工 程 职 业
图8—5 【创建操作】对话框。 创建操作】对话框。
技 术 学 院
从图8 从图8—5对话框中可看出,子类型的图标有13个,适合于孔的各 对话框中可看出,子类型的图标有13个 13 种加工。选择不同的子类型,将创建不同的孔加工操作。 种加工。选择不同的子类型,将创建不同的孔加工操作。
四 川 工 程 职 业 技 术 学 院 CAD/CAM
1.孔加工基础 1.孔加工基础 在实际加工中,根据零件图画出零件图的模型, 在实际加工中,根据零件图画出零件图的模型,如果已创建好了 模型,要分析零件图与模型孔位是否正确,清楚每个孔的精度。 模型,要分析零件图与模型孔位是否正确,清楚每个孔的精度。孔位 可以是点,也可以是圆心点。只要能标明其孔位中心位置即可。 可以是点,也可以是圆心点。只要能标明其孔位中心位置即可。如果 孔位较多,则需要对孔位顺序进行组织。另外, 孔位较多,则需要对孔位顺序进行组织。另外,如果孔零件有表面属 尽量利用零件上表面和底面控制孔加工深度。 性,尽量利用零件上表面和底面控制孔加工深度。
CAD/CAM
精 品
课 程
2.2 设置对话框 选择图8 图标, 程序】 选择图8—5中的普通钻孔 图标,在【程序】下拉列表中指定程序父 使用几何体】下拉列表框中指定几何体组, 使用刀具】 组,在【使用几何体】下拉列表框中指定几何体组,在【使用刀具】下 拉列表框中指定需要的刀具, 使用方法】 拉列表框中指定需要的刀具,在【使用方法】下拉列表框中指定操作适 合的方法,并在【名称】下拉列表框中指定操作的名称, 合的方法,并在【名称】下拉列表框中指定操作的名称,单击 确定 按 将弹出如图8 所示的【孔加工操作】对话框。 扭,将弹出如图8—6所示的【孔加工操作】对话框。
机械制造技术ppt课件(完整版)

机械制造技术课件
汇报人:
目录
01 02 03 04 05 06
机械制造概述 传统机械制造技术 现代机械制造技术 机械制造工艺流程 机械制造质量控制 机械制造的未来发展
01
机械制造概述
机械制造的定义
机械制造是将原材料转化为成品的生产过程。 机械制造包括产品设计、工艺设计、加工制造、检测和质量控制等环节。 机械制造广泛应用于各个领域,如航空、汽车、机床等。 机械制造的核心目标是提高生产效率、降低成本、保证产品质量。
05
机械制造质量控制
质量控制的方法
统计过程控制 测量系统分析 过程能力分析 质量改进方法
质量检测的步骤
检测计划制定 检测工具准备 样品选择与制备 检测数据记录与分析
质量问题的解决
确定问题:明确机械制造过程中出现的质量问题
分析原因:分析问题产生的原因,如材料、工艺、设备等
制定措施:根据分析,制定相应的解决措施,如改进工艺、更换材料、 调整设备等 实施方案:按照制定的措施实施方案,并对实施过程进行监控和调 整
精密加工技术
定义:使用精密机床和精细加工刀具进行加工 分类:超精加工、镜面加工、纳米加工等 应用:航空航天、医疗器械、光学仪器等领域 发展趋势:高精度、高效率、智能化
04
机械制造工艺流程
零件的定位与装夹
定位原理:六点 定位原理,限制 工件的自由度
装夹方法:如三 爪卡盘、四爪卡 盘等,固定工件
定位元件:如V 形块、定位销等, 限制工件的自由 度
焊接工艺及 设备
焊接种类及 特点
焊接应用及 发展
切削加工技术
定义:利用切削 工具从工件上切 除多余材料的加 工方法
分类:车削、铣 削、钻孔、刨削、 磨削等
机械装配工艺规程的制订PPT课件( 25页)
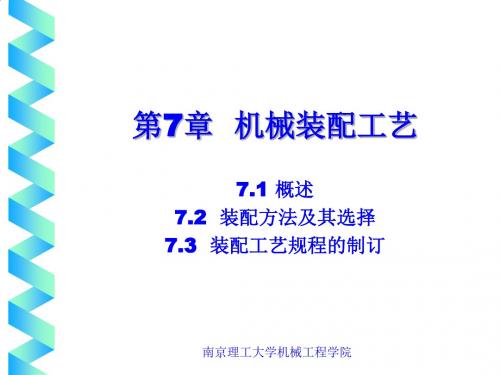
南京理工大学机械工程学院
3)误差抵消调整法
在装配中,调整组成零件的相对位置,使各件加工 误差相互抵消一部分,以提高装配精度的办法称为 误差抵消调整法。
特点:可在不提高组成零件加工精度的条件下, 提高装配精度。但它需事先测出各组成零件的误 差方向和大小,装配时需要技术熟练的工人,增 加装配前准备工作量和装配工作量,使装配组织 工作比较复杂。
南京理工大学机械工程学院
2)制订装配工艺规程的主要据
(1)产品装配图样(总装配图样、部件装配图 样和组件装配图样)及验收技术条件(验收的内 容和方法 )。 (2)产品的生产纲领 、生产类型。 (3)现有生产条件:装配车间的面积、现有装 配设备与工艺装备、现有工人的技术水平和现有 的管理模式、工艺资料和各种标准。
清洗的方法:有擦、浸、喷和超声波振动等。 常用的清洗液:有煤油、汽油、碱液和化学清 洗液等。 2)联接:是装配的主要工作。连接包括: 可拆连接(用螺纹、键、销连接等) 不可拆连接(用焊接、粘结、铆接和过盈配合等)
南京理工大学机械工程学院
7.1.2 装配工作的基本内容
3)校正、调整与配作:为保证装配精度,提高经济 性。 校正是指相关零、部件间相互位置的找正、找直、 找平及相应的调整工作。 调整是指相关零、部件间相互位置的调节工作。 配作是指几个零件配钻、配铰、配刮和配磨等,是 装配中间附加的一些钳工和机械加工工作。配钻和 配铰要在校正、调整后进行。配刮和配磨的目的是 为增加相配表面的接触面积和提高接触刚度。
第7章 机械装配工艺
7.1 概述 7.2 装配方法及其选择 7.3 装配工艺规程的制订
孔位加工方法PPT课件

• 卧式镗床结构示意图 • 1-主轴箱 2-前立柱 3-镗杆 4-平旋盘 5-工作台 6-上滑座 7-下滑座 8-导轨 9-后支架 10-后立
柱 • 加工范围广,尤其适合于大型、复杂的箱体类零件上的孔的加工。除镗孔外,还可以加工端面、
平面、外圆、螺纹及钻孔等。零件可在一次安装中完成多表面的加工。
第49页/共82页
特点图示
第14页/共82页
第15页/共82页
一、钻孔
3. 钻削用量
1) 背吃刀量asp 单位:mm
asp do
第16页/共82页
一、钻孔
3. 钻削用量
2)钻削速度vc 单位:m/min
vc do n 1000
第17页/共82页
一、钻孔
3. 钻削用量 3)钻削进给量与进给速度:
f 单位:mm/r fz 单位:mm/z Vf 单位:mm/min
第44页/共82页
三 镗孔
图 镗床镗孔
图 车床镗孔
第45页/共82页
镗刀旋转作主运动,工件或镗刀作进给运动的切削加 工方法称为镗削加工。镗削加工主要在铣镗床、镗床 上进行,是常用的孔加工方法。
铣镗床镗孔主要用于机座、箱体、支架等大型零件 上孔和孔系的加工。此外,铣镗床还可以加工外圆和 平面。由于一些箱体和大型零件上的一些外圆和端面 与它们上的孔有位置精度要求,所以在镗床上加工孔 的同时,也希望能在一次装夹工位内把这些外圆和端 面都加工出来。镗孔加工精度为IT7~IT8,表面粗糙 度Ra值为0.8~0.1μm。
第46页/共82页
镗床分为卧式镗床、坐标镗床、立式镗床 等。
卧式镗床:箱体、机架类零件上的孔或孔 系; 钻床或铣床:单件小批生产; 车床:回转体零件上轴线与回转体轴线重 合的孔。
机械制造基础5.2 孔的常规加工方法
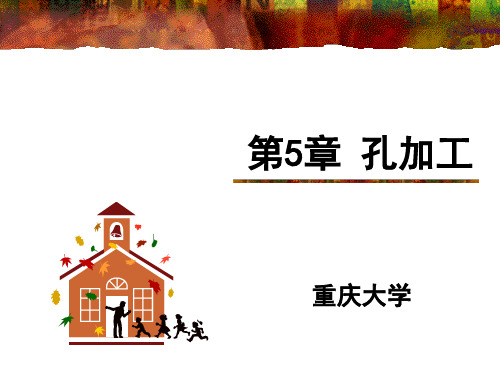
一般深孔加工按加工方式可分为:
1)实心钻孔法
一般深孔加工按加工方式可分为:
2)镗孔法
一般深孔加工按加工方式可分为:
3)套料钻孔法
(2)深孔加工的特点
1) 不能直接观察到刀具的切削情况。 2) 切削热不易传散。 3) 切屑不易排出。 4) 工艺系统刚性差。
2.深孔钻的结构
枪钻 内排屑深孔钻 深孔麻花钻 套料钻 深孔扁钻
(3)一般,拉削前的工件表面应先经过机械加工。 (4)在切削加工中,对于多边形孔和某些成形孔,
拉削虽然是一种有效的加工方法,但采用电 火花或线切割等特种加工方法,也可以完5)需要正确配置拉削工装。
4.拉削加工的合理应用
(5)需要正确配置拉削工装。
4.拉削加工的合理应用
镗孔与车外圆相比,工作条件较恶劣, 主要有以下几个方面: (1)镗刀杆的长径比大,悬伸距离长。 (2)镗削时,排屑比较困难。 (3)观察困难。
2.镗刀
(1)单刃镗刀
固定 T形 镗刀杆 螺钉 螺栓刀座 滑块 镗刀盘
镗刀 镗床用单刃镗刀
2.镗刀
1)单刃镗刀
镗刀头 刀片 调整螺母
镗刀杆
拉紧螺钉
2.镗刀
4.铰削用量
(2)切削速度和进给量
铰削速度为 1.5 ~ 5m/min; 铰削钢件时,进给量为 0.3 ~ 2mm/r; 铰削铸铁件时,进给量为 0.5 ~ 3mm/r。
5.工艺特点
(1)铰孔是孔的精加工方法; (2)可加工精度为IT7、IT8、IT9的孔; (3)孔的表面粗糙度可控制在Ra3.2 ~ 0.2μm; (4)铰刀是定尺寸刀具; (5)切削液在铰削过程中起着重要的作用。
1.拉削过程及特点
齿升量
粗加工,齿升量较大; 精加工,齿升量较小。
常用加工方法教学课件ppt
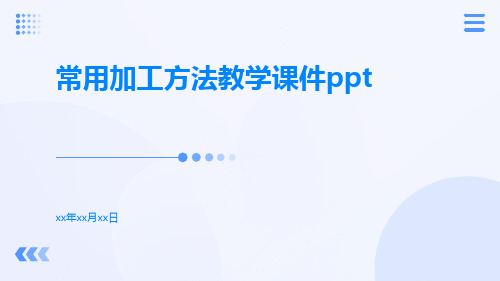
数控加工应用实例
数控铣床
数控车床
数控铣床是一种使用数控技术控制铣削过程 的机床。可加工复杂的三维形状,广泛应用 于机械制造业。
数控车床是一种使用数控技术控制车削过程 的机床。适用于加工轴类、盘类等回转体零 件。
数控钻床
数控磨床
数控钻床是一种使用数控技术控制钻孔过程 的机床。可实现高效、精确的钻孔作业。
利用数控磨床进行磨削加工,可实现高精度 、高效率的加工。
特种加工方法
电火花加工
利用电火花腐蚀原理,去除工件材料,可 实现硬材料和复杂形状的加工。
激光加工
利用激光束的高能量,去除工件材料,可 实现高精度、高效率的加工。
电化学加工
利用化学反应原理,去除工件材料,可实 现大规模和复杂形状的加工。
水切割加工
数控磨削加工
定义
数控磨削加工是指利用数控机床进 行磨削操作,对工件进行表面精整 、超精整等加工活动。
适用范围
广泛应用于机械制造、模具制造、 航空制造等领域,适合加工高精度 要求的零件。
加工特点
高效、高精度、高灵活性,可实现 复杂形状的加工。
发展趋势
随着技术的不断发展,数控磨削加 工正朝着高精度、高效率、智能化 方向发展。
定义
数控车削加工是指利用数控机床进 行车削操作,对工件进行切削、钻 孔、攻丝等加工活动。
适用范围
广泛应用于机械制造、汽车制造、 航空制造等领域,适合加工轴类、 盘类、壳体等零件。
加工特点
高效、高精度、高灵活性,可实现 复杂形状的加工。
发展趋势
随着技术的不断发展,数控车削加 工正朝着高精度、高效率、智能化 方向发展。
05
常用加工方法比较与选择
各种加工方法的优缺点比较