欧洛特智能吊挂系统说明书
ROTORK IQ3中文使用说明书IQ Mk3

IQ系列安全使用、安装、基本设定及维护手册此手册包含了安全方面的重要内容,请确保在安装、操作或维护设备之前通读并理解此方面内容。
PUB002-039-00出版时间11/12目录1. 简介 _________________________________ 31.1. 执行器部件识别 (3)1.2. Rotork设定器 (4)1.3. 手册简介 (5)2. 健康与安全 ___________________________ 52.1. ATEX/IECFM认证的执行器 (6)3. 保存 _________________________________ 64. IQ执行器的操作 ______________________ 74.1. 手轮操作 (7)4.2. 电动操作 (7)4.3. 显示–就地指示 (8)4.4. 显示-主屏幕选项 (9)4.5. 显示状态指示-行程 (10)4.6. 显示状态指示-控制 (10)4.7. 显示报警指示 (10)4.8. 电池报警 (10)5. 准备驱动轴套 _________________________ 115.1. IQ所有的A、Z3型底座 (11)5.2. B型非推力底座 (12)6. 安装执行器 __________________________ 136.1. 提升杆式阀门 - 顶装 (14)6.2. 带齿轮箱的阀门 - 侧装 (14)6.3. 非提升杆式阀门 - 顶装 (14)6.4. 手轮密封 (15)6.5. IQM调节型执行器 (15)6.6. IQL和IQML直行程驱动装置 (15)6.7. IQL和IQML直行程驱动装置的调试 (16)7. 电缆连接 ____________________________ 177.1. 接地连接 (17)7.2. 卸下接线端子箱盖 (17)7.3. 电缆入口 (17)7.4. 连接至端子 (18)7.5. 回装接线端盖 (18)8. 调试 - 基本设定 ______________________ 198.1. 连接至执行器 (20)8.2. 安全 - 口令 (21)8.3. 基本设定菜单 (22)8.4. 基本设定 - 限位 (23)8.5. 关阀设定 (24)8.6. 开阀设定 (24)8.7. 力矩开关旁路 (25)9. 维护、监视及故障排除_________________ 2610. 环保处理 ____________________________ 2811. 重量和油量 __________________________ 2912. IQ认证 _____________________________ 3013. 认可的保险丝 ________________________ 3114. 振动、冲击和噪音 ____________________ 3115. 安全使用条件 ________________________ 3121.简介1.1.执行器部件识别手轮控制器盖电机底座接线端子箱盖电池密封塞金属(需要8 mm艾伦内六角扳手)塑料(需要10 mm艾伦内六角扳手)酌情而定。
NOLO 使用说明说明书
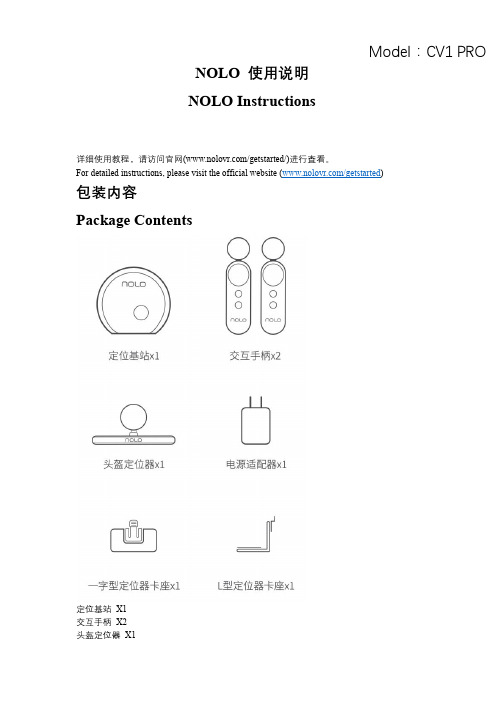
NOLO 使用说明NOLO Instructions详细使用教程,请访问官网(/getstarted/)进行査看。
For detailed instructions,please visit the official website (/getstarted )包装内容PackageContents定位基站X1交互手柄X2头盔定位器X1Model:CV1 PROPositioning Base Station*1 Interactive Controller*2 Headset Marker*1电源适配器X1一字型定位器卡座X1L型定位器卡座X1 Power Adapter*1 Slotted Positioner Socket*1 L-type Positioner Socket*1一分三充电线X1OTG数据线X21米数据线X1一字型定位器卡座X1Three-In-One Charging Cable*1OTG Data Cable*21m Data Cable*1Slotted Positioner Socket*1了解设备Learn More about the Device交互手柄1扳机键2配对键3侧按键4触控板5菜单键6指示灯7系统/电源键Interactive Controller1Trigger Key2Pairing Key3Side Keys(Each for the left and right sides) 4Touch Key5Menu Key6Indicator Lamp7System/Power Key定位基站电源键配对键Positioning Base Station Power KeyPairing Key头盔定位器指示灯USB接口配对键Headset Marker Indicator LampUSB Interface Pairing Key一.配合VR—体机使用说明I.Instructions for Standalone Headsets1.搭建网络环境1.Set up the network environment将路由器和电脑通过网线连接;将VR—体机和电脑连接至同一路由器的5G Wi-Fi频段。
欧标Eaton Moeller系列快速链接速控器说明书

Eaton 198818Eaton Moeller® series Rapid Link - Speed controllers, 5.6 A, 2.2 kW, Sensor input 4, 230/277 V AC, AS-Interface®, S-7.4 for 31 modules, HAN Q4/2, with manual override switchGeneral specificationsEaton Moeller® series Rapid Link Speed controller1988184015081968763157 mm 270 mm 220 mm 3.58 kg IEC/EN 61800-5-1 UL approval CEUL 61800-5-1 RoHSProduct NameCatalog NumberEANProduct Length/Depth Product Height Product Width Product Weight Certifications Catalog Notes 3 fixed speeds and 1 potentiometer speedcan be switched over from U/f to (vector) speed control Connection of supply voltage via adapter cable on round or flexible busbar junction Diagnostics and reset on device and via AS-InterfaceDiagnostics and reset on device and via AS-Interface Parameterization: FieldbusParameterization: KeypadParameterization: drivesConnect mobile (App) Parameterization: drivesConnectManual override switchIGBT inverterKey switch position AUTOSelector switch (Positions: REV - OFF - FWD)PTC thermistor monitoringControl unitKey switch position OFF/RESETTwo sensor inputs through M12 sockets (max. 150 mA) for quick stop and interlocked manual operationThermo-click with safe isolationInternal DC linkPC connectionKey switch position HANDFor actuation of motors with mechanical brake3 fixed speeds1 potentiometer speed IP65NEMA 121st and 2nd environments (according to EN 61800-3)IIISpeed controllerASIAS-Interface profile cable: S-7.4 for 31 modulesC2, C3: depending on the motor cable length, the connected load, and ambient conditions. External radio interference suppression filters (optional) may be necessary.C1: for conducted emissions only2000 VCenter-point earthed star network (TN-S network)AC voltagePhase-earthed AC supply systems are not permitted.Vertical15 g, Mechanical, According to IEC/EN 60068-2-27, 11 ms, Half-sinusoidal shock 11 ms, 1000 shocks per shaftResistance: 10 - 150 Hz, Oscillation frequencyResistance: 57 Hz, Amplitude transition frequency on accelerationResistance: 6 Hz, Amplitude 0.15 mmResistance: According to IEC/EN 60068-2-6Max. 2000 mAbove 1000 m with 1 % performance reduction per 100 m -10 °C40 °C-40 °C70 °CFeatures Fitted with:Functions Degree of protectionElectromagnetic compatibility Overvoltage categoryProduct categoryProtocolRadio interference classRated impulse withstand voltage (Uimp) System configuration typeMounting position Shock resistance Vibration AltitudeAmbient operating temperature - min Ambient operating temperature - max Ambient storage temperature - min Ambient storage temperature - maxIn accordance with IEC/EN 50178 < 95 %, no condensation0.5 - 5.6 A, motor, main circuit Adjustable, motor, main circuit < 10 ms, On-delay < 10 ms, Off-delay 98 % (η)5.3 A3.5 mA120 %Maximum of one time every 60 seconds 380 V480 V380 - 480 V (-10 %/+10 %, at 50/60 Hz)Synchronous reluctance motors Sensorless vector control (SLV) PM and LSPM motors U/f control BLDC motors 0 Hz500 HzAt 40 °CFor 60 s every 600 s8.4 AClimatic proofingCurrent limitationDelay timeEfficiency Input current ILN at 150% overload Leakage current at ground IPE - max Mains current distortion Mains switch-on frequencyMains voltage - min Mains voltage - max Mains voltage toleranceOperating modeOutput frequency - min Output frequency - max Overload current Overload current IL at 150% overload45 Hz66 Hz5.6 A at 150% overload (at an operating frequency of 8 kHz and an ambient air temperature of +40 °C)2.2 kW400 V AC, 3-phase480 V AC, 3-phase0.1 Hz (Frequency resolution, setpoint value)200 %, IH, max. starting current (High Overload), For 2 seconds every 20 seconds, Power section50/60 Hz8 kHz, 4 - 32 kHz adjustable, fPWM, Power section, Main circuitCenter-point earthed star network (TN-S network)AC voltagePhase-earthed AC supply systems are not permitted.3 HP≤ 0.6 A (max. 6 A for 120 ms), Actuator for external motor brake≤ 30 % (I/Ie)Adjustable to 100 % (I/Ie), DC - Main circuit230/277 V AC -15 % / +10 %, Actuator for external motor brake10 kAType 1 coordination via the power bus' feeder unit, Main circuit230/277 V AC (external brake 50/60 Hz)24 V DC (-15 %/+20 %, external via AS-Interface® plug)AS-InterfacePlug type: HAN Q4/2Number of slave addresses: 31 (AS-Interface®) Specification: S-7.4 (AS-Interface®)Max. total power consumption from AS-Interface® power supply unit (30 V): 190 mA C1 ≤ 1 m, maximum motor cable length C2 ≤ 5 m, maximum motor cable length C3 ≤ 25 m, maximum motor cable lengthMeets the product standard's requirements.Rated frequency - minRated frequency - maxRated operational current (Ie)Rated operational power at 380/400 V, 50 Hz, 3-phase Rated operational voltageResolutionStarting current - maxSupply frequencySwitching frequencySystem configuration type Assigned motor power at 460/480 V, 60 Hz, 3-phase Braking currentBraking torqueBraking voltageRated conditional short-circuit current (Iq)Short-circuit protection (external output circuits) Rated control voltage (Uc)Communication interfaceConnectionInterfacesCable length10.2.2 Corrosion resistanceMeets the product standard's requirements.Meets the product standard's requirements.Meets the product standard's requirements.Meets the product standard's requirements.Does not apply, since the entire switchgear needs to be evaluated.Does not apply, since the entire switchgear needs to be evaluated.Meets the product standard's requirements.Does not apply, since the entire switchgear needs to be evaluated.Meets the product standard's requirements.Does not apply, since the entire switchgear needs to be evaluated.Does not apply, since the entire switchgear needs to be evaluated.Is the panel builder's responsibility.Is the panel builder's responsibility.Is the panel builder's responsibility.Is the panel builder's responsibility.Is the panel builder's responsibility.Generation change from RA-MO to RAMO 4.0Generation Change RASP4 to RASP5Generation change from RA-SP to RASP 4.0Generation change RAMO4 to RAMO5Generation Change RA-SP to RASP5Connecting drives to generator suppliesConfiguration to Rockwell PLC for Rapid LinkElectromagnetic compatibility (EMC)Rapid Link 5 - brochureDA-SW-drivesConnect USB Driver DX-COM-PCKITDA-SW-USB Driver PC Cable DX-CBL-PC-1M5DA-SW-drivesConnectDA-SW-Driver DX-CBL-PC-3M0DA-SW-drivesConnect - installation helpDA-SW-USB Driver DX-COM-STICK3-KITDA-SW-drivesConnect - InstallationshilfeMaterial handling applications - airports, warehouses and intra-logisticsProduct Range Catalog Drives EngineeringProduct Range Catalog Drives Engineering-ENDA-DC-00003964.pdfDA-DC-00004184.pdfDA-DC-00004514.pdfDA-DC-00004508.pdfeaton-bus-adapter-rapidlink-speed-controller-dimensions-004.eps eaton-bus-adapter-rapidlink-speed-controller-dimensions-003.eps eaton-bus-adapter-rapidlink-speed-controller-dimensions-002.eps eaton-bus-adapter-rapidlink-speed-controller-dimensions-005.epsETN.RASP5-5402A31-412R000S1.edzIL034085ZU10.2.3.1 Verification of thermal stability of enclosures10.2.3.2 Verification of resistance of insulating materials to normal heat10.2.3.3 Resist. of insul. mat. to abnormal heat/fire by internal elect. effects10.2.4 Resistance to ultra-violet (UV) radiation10.2.5 Lifting10.2.6 Mechanical impact10.2.7 Inscriptions10.3 Degree of protection of assemblies10.4 Clearances and creepage distances10.5 Protection against electric shock10.6 Incorporation of switching devices and components10.7 Internal electrical circuits and connections10.8 Connections for external conductors10.9.2 Power-frequency electric strength10.9.3 Impulse withstand voltage10.9.4 Testing of enclosures made of insulating material Application notes BrochuresCatalogues Certification reports DrawingseCAD model Installation instructionsEaton Corporation plc Eaton House30 Pembroke Road Dublin 4, Ireland © 2023 Eaton. All rights reserved. Eaton is a registered trademark.All other trademarks areproperty of their respectiveowners./socialmediaThe panel builder is responsible for the temperature rise calculation. Eaton will provide heat dissipation data for the devices.Is the panel builder's responsibility. The specifications for the switchgear must be observed.Is the panel builder's responsibility. The specifications for the switchgear must be observed.The device meets the requirements, provided the information in the instruction leaflet (IL) is observed.Rapid Link 5MZ040046_EN MN034004EN MN040003_ENramo5_v24.dwg rasp5_v24.stp10.10 Temperature rise10.11 Short-circuit rating10.12 Electromagnetic compatibility 10.13 Mechanical function Installation videos Manuals and user guidesmCAD model。
METTLER TOLEDO MultiRange MO600 MO1200 吊顶秤梯型规范说明书

3.1 Evaluation of supporting structure ................................................... 8
3.2 Mounting possibilities ................................................................... 8
1 Installation
1.1 Preparatory work
1.1.1
Selecting installation location
▲ The explosion-protected overhead-rail is approved for operation in Zone 2 (gases) and Zone 22 (dusts) hazardous areas. There is an increased danger of injuries and damage when using the overhead-rail in hazardous areas! Special care must be taken when working in such hazardous areas. The rules for behaviour are based on the concept of "Safe Distribution" established by METTLER TOLEDO.
1.3 Transport locks / Rail carriers / Weighing rail insert........................... 4
1.4 Installing connection cable ............................................................ 5
欧圣 手持控制器 HBA 使用说明书

These operating instructions are valid only in connection with the data sheet of the rele-vant hand-held pendant station HBA and with the operating instructions of the relevant HBA handwheel!Correct useMachine installations in manual mode can be operated with hand-held pendant stations.Handwheels are used as part of an overall higher-level control system.Their use, installation and operation are permissible only in conformity with these operating instructions.Incorrect useHand-held pendant stations on their own must not be used as safety components for avoiding hazar-dous states in a machine installation.General functionHand-held pendant stations make it possible to operate a machine installation, for instance, in manual mode.Function of individual componentsThe hand-held pendant station may consist of the following components: HandwheelEMERGENCY-STOP device Enabling switches Selector switches PushbuttonsHBA handwheelThe electronic HBA handwheel is a universal pulse generator for manual shaft positioning.An output of 100 or 25 square-wave pulses per revolution is available. A second phase-shifted output allows the connected controller to detect the direction of movement.The pulses are evaluated in the controller.For details, please see the Electronic HBA handwheel operating instructions.EMERGENCY-STOP deviceThe EMERGENCY-STOP device is designed to be mani-pulation-proof in accordance with IEC 60947-5-1/EN ISO 13850.Enab ling switches, selector switches,pushbuttonsThese components are used to transfer additional information to the higher-level machine controller.AssemblyHand-held pendant stations are not used exclusively at a single site. The stations can be stored using a mounting magnet on the rear of the device or a holder.Electrical connectionAlways shield connecting leads.Ground the shield at the open end of the lead at a central grounding point, e.g. in the distribution board or in the control cabinet, over a large sur-face, with low resistance and with low inductance. In the case of leads with plug connectors, ensure that the connection type is EMC-compliant.Original connecting leads must not be shortened. G iven an extension or other modification to the connection cable, the operator must ensure that the valid EMC protection requirements are observed. Do not install connecting leads in the immediate vicinity of interference sources.Authorization according to:Operation with UL-class 2 power supply only.Connection leads of hand-held pendant stations in-stalled at the application site must be separated from all movable and permanently installed leads and non-insulated active parts of other installation parts which operate with a voltage of over 150 V, in such a way that a constant clearance of 50.8 mm is observed. This does not apply if the movable leads are equipped with suitable insulation materials which possess an identical voltage stability to the other relevant installation parts or higher.Service and inspectionEUCHNER handwheels require no maintenance.Handwheels may only be repaired by the manufac-turer.To clean the handwheels, only use solvent-free cle-aning agents and a soft cloth.Disclaimer of liabilityThe company is unable to accept liability in the following cases:if instructions are not followedif the safety instructions are not followedif the units are electrically connected by unautho-rised personnelif any external intervention occursDo not open hand-held pendant stations!Do not throw or drop the hand-held pendant stati-ons!LISTEDPOW. CONV. EQ.82HAEUCHNER GmbH + Co. KG Kohlhammerstra ße 16D-70771 Leinfelden-Echterdingen Tel. +49/711/75 97-0Fax +49/711/75 33 16www.euchner.de ***************S u b j e c t t o t e c h n i c a l m o d i f i c a t i o n s ; n o r e s p o n s i b i l i t y i s a c c e p t e d f o r t h e a c c u r a c y o f t h i s i n f o r m a t i o n .© E U C H N E R G m b H + C o . K G072850-05-02/12 (T r a n s l a t i o n o f t h e o r i g i n a l o p e r a t i n g i n s t r u c t i o n s )ColourGrey RAL 7040/Black RAL 9004Weight1.3 kg Operating temperature 0 °C ... +50 °C Storage temperature -20 °C ... +50 °CHumidity, max.80 %(condensation not permissible)Degree of protection to the frontIn accordance with EN60529 / IEC529IP 65In accordance with NEMA 250-12Resistance to vibrationVibrations (3 axes)DIN/IEC 68-2-6Shock (3 axes)DIN/IEC 68-2-27EMC protection requirements EN 61000-6-2in accordance with CEEN 61000-6-4Switching elements Max. 2 NC contactsUtilization categoryDC-13according to IEC 60947-5-1U e =24 V / I e= 3 A Resistive loadAC 30 V / 0.4 ADC 30 V / 0.1 A Switching voltage, max.30 V DC Switching current, max.0.1 A Switching capacity, max.1 VA see wiring diagramSwitching voltage, max.25 V Switching capacity, max.0,2 VAwww.euchner.deTechnical data, handwheelSee relevant operating instructions for HBA hand-wheel.AccessoriesSee EUCHNER catalogue for hand-held pendant stations or www.euchner.de.。
【最新2018】oulu,说明书-精选word文档 (10页)

本文部分内容来自网络整理,本司不为其真实性负责,如有异议或侵权请及时联系,本司将立即删除!== 本文为word格式,下载后可方便编辑和修改! ==oulu,说明书篇一:欧陆512C操作说明书单相控制器产品型号目录目录???????????????????????????????1 概述???????????????????????????????2 机械安装尺寸???????????????????????????3 电气规格?????????????????????????????4 环境条件?????????????????????????????5 基本接线?????????????????????????????6 接线端说明????????????????????????????7 系统框图?????????????????????????????10 安装须知?????????????????????????????11 基本设定程序???????????????????????????12 故障处理?????????????????????????????141概述SSD512控制器适用于永磁和并磁直流电机的转速和力矩控制。
装置有四种型号:512C/044A DC 512C/088A DC 512C/16 16A DC 512C/32 32A DC控制器计设在110-415VAC 50/60Hg 单相电流上运行,简单改变控制器上的变换抽头即可使装置使用于供电电压。
控制器采用全波半控可控硅/二极管功率桥块,封装在两块分开的模块中,以便使两模块及控制板可靠接地。
直流电动机的转速采用线性闭环控制,由电枢电压或测速发电机取得反馈讯号使电机转速能在负载波动情况下保持不变。
速度环内的电流环使受控制的电流电平适应于电动机,实际电平值用户可通过电流控制电位器和开关来调节。
由于过大的负载,电机可能堵转,约15秒后控制器会跳闸,由感应引起的严重过电流可以被瞬间过流脱机装置检测到。
欧特曼安全指南说明书

Table of Contents1.Introduction1.1.Introduction2.Life Saving Rules2.1.Safety Devices and Guards2.2.Electrical Work/Arc Flash2.3.Confined Space Entry2.4.Energy Control/Lockout-Tagout2.5.Fall Protection2.6.Seatbelts and Restraints3.Responsibilities3.1.EHS Compliance3.2.Housekeeping Requirements3.3.Safety Signs, Signals, and Barricades3.4.Injury and Illness Reporting3.5.Chemical Management4.Tools and Equipment4.1.Overview4.2.Hoisting Equipment -Cranes, Hoisting4.3.Tools- Hand, Portable Power, Pneumatic5.Specific Hazards and Procedures5.1.Hot Work- Welding, Cutting, Brazing5.2.Scaffolding and Ladders5.3.Powered Industrial Trucks5.4.Trenching and Excavations5.5.Demolition5.6.Painting5.7.Asbestos6.ClosureWelcome to Eaton. It is our goal to provide a secure and safe work environment for all of our employees, contractors, and visitors. Eaton commits to meet or exceed regulatory and companyrequirements consistent with Eaton’s policies on ethics and compliance. We will work to create a “zero incident safety culture” and to continuously improve our environmental, health, andsafety (EHS) p erformance through the implementation of Eaton’s EHS management system standard (MESH).This Handbook applies to all third parties performing activities at Eaton locations including suppliers, contingent workers, contractors, vendors, visitors, and all other non-Eaton employees. The Handbook provides a brief summary of the EHS practices required for working for Eaton. For additional information, please contact the Eaton project coordinator or site EHS. Compliance with the requirements of this Handbook and of all legal, site, and project-specific requirements is a condition of working for Eaton. All third parties must ensure that their employees and sub-contractors complete Eaton’s EHS orientation training and any additional training required prior to commencing work.Safety is fundamental to everything Eaton does. Eaton’s Safety Policy outlines the expectation for a safe work environment and reporting obligations. All third parties must comply with Eaton’s Safety Policy, available at “Safety” page.Within the Safety Policy, we have included the Life Saving Rules, which are a set of rules that all who enter our sites are expected to follow. Those that are found to be in non-compliance of the Life Saving Rules will be removed from the facility. The Life Saving Rules are non-negotiable and must be followed while visiting or working at an Eaton facility.The Life Saving Rules:Safety Devices and Guards: Devices installed to assure safe machine operationshall not be removed, tampered with or bypassed.Lock-out/ Tag-out: Lock-out tag-out procedures must be followed.Electrical Work/Arc Flash: Appropriate Personal Protective Equipment must beused when electrical work is being done or there is arc flash potential.Fall Protection: Fall-arrest systems must be used when working at unprotectedheights of 6 feet (1.82 meters) or greater.Permit-Required Confined Spaces: No person shall enter a permit-requiredconfined space without an approved permit.Seat Belts/Restraints: All operators and passengers of powered industrial trucksand equipment must use available seatbelts and restraints.EHS ComplianceContractors have sole responsibility for the health, safety, and welfare of their employees, subcontractors, and agents providing the services. All third parties must ensure that they have the appropriate skills, qualifications, certifications, licenses, and training to conduct the services prior to the commencement of the work.In addition, third parties must observe the following requirements.Air: The use of non-toxic, low volatility paints must be considered for all painting operations. The use of solvent-based paints or coatings must be approved by the Eaton EHS. Third parties conducting refrigerant processes must be certified, and control and document all ODCs.Storm Water: Storm water can carry pollutants. The following rules must be observed:∙Containers may not be stored outside or left exposed to the weather.∙Materials may not be stored outside, discarded or poured onto the ground or ditches.∙No garbage or trash may be left outside unless it is placed in the appropriate waste container.∙All scrap, trash, and debris must be removed on daily basis prior to leaving premises.Wastewater Discharges: Special care must be taken to prevent oil or other chemicals from entering the sewer system or other wastewater conveyance system. No material may be discharged into a sewer or other wastewater conveyance system without prior approval from the Eaton EHS.Waste Disposal: All waste must be placed in the proper receptacles. The management of hazardous and other regulated wastes generated on Eaton premises must be coordinated in advance with the Eaton EHS and may not be removed from the site without prior coordination with the Eaton. If third parties are removing hazardous waste from site, all third parties must be certified.Housekeeping RequirementsConstruction debris must be removed and properly disposed of daily. Burn barrels are not permitted. Materials and tools that remain on site must be neatly stacked, properly stored and identified with the third party’s company name. All work areas must be kept clean and in good working condition. Exit doors, exit routes, passageways, and emergency equipment must bekept unobstructed. Hoses, cables, and other potential tripping hazards must be located so as not to present a tripping hazard.Safety Signs, Signals, and BarricadesBarricades must be 104 centimeters (42 inches) high and erected at least 1.8 meters (6 feet) from the edge of the hazard. Yellow barricade tape should be used where entry is permitted under certain conditions. A tag should be posted on the tape to indicate the potential hazards and entry requirements. Red barricade tape indicates that entry into an area is prohibited.ReportingAll work-related injuries and illnesses must be immediately reported to the Eaton project coordinator or EHS site leader. All releases, spills or environmental incidents must be immediately reported to the Eaton EHS. Third parties will cooperate with Eaton in its investigation of any environmental, health or safety incident.Chemical ManagementAll chemicals along with the estimated amount to be brought on site must be approved by the Eaton site leader prior to the material being brought into the facility. Safety data sheets for chemicals at the site plant are maintained and will be made available to third party employees upon request. Third party management must provide Eaton with a copy of a safety data sheet for each chemical brought on site. Chemicals must be labeled and stored in accordance to all applicable legal requirements and any additional direction by site EHS.OverviewAll third parties may not use Eaton vehicles, equipment or tools without prior permission from the Eaton project coordinator. Third party management must provide documentation that employees are qualified to use loaned equipment or tools in accordance with applicable regulatory requirements. Eaton personnel will not repair tools or equipment for third party personnel. Defective tools must be removed from service immediately.Hoisting EquipmentCranesOnly trained and qualified employees are permitted to operate a crane. The rated load capacity of the crane is never to be exceeded. Cranes are to be operated within the design limits specified by the manufacturer. Mechanical parts of the crane must be inspected by the operator prior to each shift. Rated load capacities, recommended operating speeds, special hazards, warnings, or instructions must be posted conspicuously on all equipment. All accessible areas within the radius of the counterweight swing must be barricaded to prohibit access. Outriggers must be fully extended on firm ground. Operator must maintain a safe working clearance of at least 3 meters (10 feet) from energized electrical lines. Personnel are prohibited from riding on crane hooks.Hoisting EquipmentAll hoisting equipment must be inspected before each use. All hooks must be equipped with safety latches. Suspended loads shall not be left unattended, nor shall personnel be placed under suspended loads. All lifting devices must be visually inspected before each use. Damaged lifting devices must be immediately removed from service.ToolsHand ToolsDefective hand tools must not be used. Tools must be kept in good condition – sharp, clean, oiled, and dressed. Tools subject to impact, such as chisels, must be dressed to avoid “mushrooming” of the head of the tool. Tools may not be thrown from one location to another, from one employee to another, or dropped to lower levels. Tools must not be forced beyond their capacity. “Cheaters” shall not be used to increase tool capacity. All defective tools must be removed from service until repaired or replaced.Portable Power ToolsElectrical power tools may not be used in areas where flammable or combustible liquids or dusts are stored or handled unless the tools are approved for service in a hazardous location. Electrical tools must be double-insulated or contain a ground. The use of ground-fault circuit interrupters is required for all outdoor locations or indoor locations that are wet or damp. Safety guards must be in place on all power tools before use. Extension cords must be maintained in good working condition and may not contain any slices. Electrical tape may not be used to repair extension cords. Cords must be kept out of walkways and other areas where they could present trip hazards or where they can be damaged.Pneumatic Tools/Compressed AirPneumatic tools and hoses must be secured together by a positive means to prevent the tools from becoming accidentally disconnected. Compressed air may not be used for cleaning personnel or clothing.Hot Work- Welding, Cutting, BrazingBefore starting any hot work activities outside of a designated hot work area, a hot work permit must be obtained from the designated Eaton representative. The hot work permit is valid for one shift and must be posted in the area where the work is being performed. Hot work requirements include:∙No hot work may be performed while plant fire protection systems have been disabled;∙All flammable and combustible materials within 10.7 meters (35 feet) of the hot work site must be removed or covered. Wall and floor opening within 10.7 meters (35 feet) of the hot work must be protected;∙ A fire extinguisher and/or water hose must be provided at the job site;∙ A fire watch must be present for the duration of the hot work plus 60 minutes after the hot work is completed. The area shall be monitored for an additional 4 hours followingthe fire watch.All fuel and oxygen cylinders must be secured in an upright position. When oxygen and fuel gas cylinders are not connected for use, they must be separated by at least 6.1 meters (20 feet) or separated by a fire barrier with a 30-minute rating. Protective blinds must be used around welders. Local exhaust ventilation (LEV) must be used when welding or cutting in enclosed areas or confined spaces. Filter respirators or LEV must be used when welding or cutting on materials containing stainless steel, high-alloy specialty steels, galvanized steel, lead, zinc, cadmium, hexavalent chromium, or mercury.Scaffolding and LaddersScaffolds must be erected on solid footing. Scaffolds must be sound, rigid, and sufficient to carry the intended load without settling. Unstable objects, such as barrels, boxes, loose bricks or concrete blocks must not be used to support scaffold or planks. Scaffold must not be erected, moved, dismantled or altered except under the supervision of a competent person. Scaffolds must be equipped with guardrails, mid-rails and toe boards. Scaffold accessories such as braces, brackets, trusses, screw legs or ladders that are damaged or weakened from any cause must be immediately repaired or replaced. Scaffold platforms must be tightly planked with scaffold plank grade material or equivalent. A competent person must inspect the scaffolding upon completion and at least daily thereafter. Scaffolds must be at least 3 meters (10 feet) from electric power lines at all times. Scaffold must be accessed using ladders or stairs.The use of portable metal ladders is prohibited at our sites. All ladders must be equipped with safety feet and erected on solid footing. Ladders should be erected in a 4:1 ratio and extend 1 meter (3 feet) beyond the top of a structure. Extension ladders should be footed at the base by another employee or tied off at the top to prevent tipping. Do not stand on the top step of the ladder. The use of fall arrest system is explained on page 1 under “Lif e Saving Rules – Fall Protection.”Powered Industrial TrucksForklifts used at our sites can present an unexpected hazard to third parties. While working at sites utilizing forklifts, stay in the designated walkways. Eaton-owned powered industrial trucks (PITs) may not be operated by third party employees. PITs and mobile equipment, such as backhoes, must be inspected prior to each shift the equipment is used or operated. These inspections must be conducted and documented in accordance with the manufacturer’s requirements. Defective equipment must be removed from service until repaired.Trenching and ExcavationsA review of underground utilities must be performed before digging a hole. This review should occur at least 48 hours before the start of the project. Protective shoring or approved sloping techniques must be utilized to protect workers entering trenches 1.5 meters (5 feet) deep or greater. Soil must be kept at least 60 centimeters (2 feet) back form the edge of a trench. A ladder or ramp must be provided to exit a trench. Trenches must be inspected by a competent person on daily basis prior to entry and after any hazard-increasing event such as heavy rain, vibrations or excessive loads.DemolitionPrior to starting demolition operations, third party management must survey the structure to determine its condition. A written plan, identifying the safe work procedures to complete the demolition, must be developed. While conducting the work, the demolition area must bebarricaded. Crane operators involved must be able to see the work, or a signal person must be utilized to direct the crane operator. Employees may not work below other employees during demolition work. Unstable structures may not be left in place without temporary support. Do not throw materials to the ground; lower them by crane or chutes.PaintingLead-based paints may not be used. Respiratory protection is required for painters during spraying operations. Spray-painting equipment must be cleaned in an open, well-ventilated area at least 10.7 meters (35 feet) from any ignition source. Static charge dissipation measures must be taken while cleaning spray-painting equipment.AsbestosAny unknown insulation material or potential asbestos containing material (PACM) is to be treated as asbestos-containing material. Third parties may not remove or disturb material until the insulation is determined to be asbestos-free. Asbestos-containing material may only be removed by certified asbestos contractors and must be removed in accordance with local regulatory requirements.Energy Control (Lockout)All third parties performing servicing and maintenance or line breaking activities at Eaton sites must follow the requirements outlined in this procedure. Equipment will be locked out by an authorized lockout supervisor using red or blue locks and a lockout hasp in accordance with the applicable equipment-specific lockout procedure. Initial lockout-tagout application shall be witnessed by an Eaton authorized lockout supervisor. Third party personnel shall then install their red locks on the appropriate energy isolation device prior to starting a job.This H andbook is an extension of Eaton’s effort to care for all third party employees and visitors, and to achieve zero accidents in the work place. We commit to continuous improvement in our Environmental, Health and Safety performance. Conformance with this handbook is the responsibility of every third party performing activities at Eaton locations including suppliers, contingent workers, contractors, vendors, visitors, and other non-Eaton employees.。
optex bgs-dl10tn说明书

optex bgs-dl10tn说明书
1、自身调节。
绕线机光电开关在使用之初请先检查开关本身是否完好,外观是否完好等。
2、避开遮挡物时EL130光电开关使用时,对于一些货物如带色货物。
反射性较弱的货物。
小件间间隙较大的货物。
透明货物或在阳光或卤光照射环境下,光电开关就会有不起作用的现象,那是因为光线被干忧了。
3、高度调节时码盘上面另外一个ITR8402-A槽宽6mm的槽型光电开关感测不到货物时,可适当修正光电开关方向,使其直射货物中心;如不见效,可打开光电开关外壳调整感测距离,顺时针方向调节灵敏度旋钮,顺时针方向旋转,直至达到可靠感测到为止。
4、方向调节,光电开关感测到货物或电机转盘以外时,可逆时针调节灵敏度旋钮,逆时针方向向旋转,直至达到感测不到外物为止,再后是值得注意的地方是严禁带电操作!注意安全。
洛ctite 气动分配器说明书
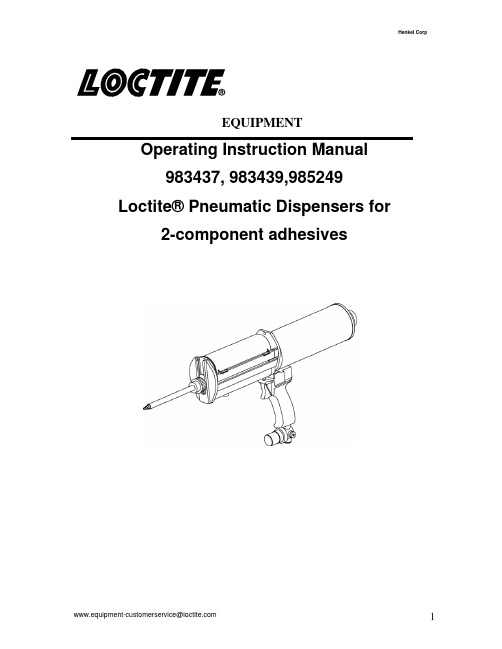
EQUIPMENTOperating Instruction Manual983437, 983439,985249 Loctite® Pneumatic Dispensers for 2-component adhesivesContents:1. Safety instructions 2-4Symbols used in the Operating Instruction ManualExplanation of the safety conceptIntended use2. Parts list for pneumatic dispenser 43. Preparing the dispenser for use 4-5Package contentsPreparation for useOperating principlePreparing the dispenser4. Operation of the dispenser 5-6Insert cartridgeConnect the dispenser to the compressed air supplyDispensing the adhesiveRemoving the cartridge5. Troubleshooting 66. Maintenance and Repair 7Ordering Spare Parts7. Technical data 78. Standards applied 79. Warranty 8Always keep this instruction manual easily accessible to users of the dispenser.1. Safety instructionsRead through this dispenser Operating Instruction Manual carefully. For safe andreliable operation, it is essential for users to understand and follow all the safetyinstructions provided in the Manual.Symbols used in the Manual and on the dispenserINFORMATIONImportant information on installation, operation or maintenance.DANGER / CAUTIONRisks or hazardous applications that can result in severe / fatal injuries or considerable material damage.WEAR GLOVESFailure to do so can result in serious personal injuryWEAR SAFETY GOGGLESFailure to do so can result in serious personalinjuryCEThe pneumatic dispenser is marked with the CEsymbol in compliance with the applicableEuropean directives.Do not use the dispenser until you have read and understood the operating procedure and the instructions contained in this Operating Instruction Manual. The dispenser operates under high pressure. Failure to follow these instructions can lead to inadvertent discharge of pressure or breakage of the dispenser at high pressure and may result in serious personal injury to the user or bystanders and/or property damage.The following instructions must be read and strictly observed:•The user of the dispenser and any persons standing in the vicinity must wear safety goggles and gloves at all times during operation of the dispenser.•The user should never point the barrel end of the dispenser at himself or in the direction of bystanders [animals] or objects during operation.•Never open the pneumatic drive or attempt to remove.•Handle the dispenser properly. Store in a cool dry place. Transport it carefully, with minimal vibration. Do not drop it to the ground or slam it on a bench or other workspace. •Safety devices must not be removed, worked around, bypassed or deactivated during operation.•Always comply with the warnings and notices on the device. Never, under any circumstances, remove these warnings and notices. Replace them immediately if theybecome detached or illegible.•Do not remove, tamper or manipulate pressure limiting valve and and strictly respect pressure limits.•Check the dispenser for visible damage and defects before each use. The dispenser must only be used if it is in good working order. If you have any doubt about the condition of the dispenser, or if there are any signs of breakage or other damage, immediately stop using the device and send it for inspection and repair by a site authorized by the manufacturer. •Keep the dispenser clean at all times. Failure to do so may result in malfunction of dispenser or bodily injury.•Do not attempt to modify or repair the dispenser. Maintenance and repairs must be carried out exclusively by qualified specialists. No such work may be carried out while thedispenser is connected to the compressed air supply.•Always follow safe workplace practices, such as making sure the air hoses are carefully routed so that neither you nor any other person can become entangled in the hoses or trip over them.•Be cautious connecting and disconnecting air pressure hose.•Always keep this instruction manual easily accessible to users of the dispenser.•Use only authentic Loctite® spare parts. Malfunctions or accidents may result if spare parts of other manufacturers are used, and any warranty claims against the manufacturer will be considered void.•Replace missing or damaged hazard warning labels / stickers.Modifications or changes to the dispenser by persons not authorized by the manufacturer and any failure to comply with the safety instructions given in the Operating Instruction Manual are dangerous and can lead to accidents with severe injuries and / or property damage.Intended use of the dispenserThe dispenser has been developed for mixing and applying 2-component adhesives of various different formulas. Any other or additional applications shall be considered as nonconforming, i.e. not conforming to the intended use. The intended use also includes compliance with the instructions in this Operating Instruction Manual as a basic requirement.2. Parts list for pneumatic dispenser:1. Cartridge guide2. Type designation and serial number3. Plunger4. Dispense volume indicator5. Pneumatic drive unit6. Piston rods7. Cartridge ejector button 8. Cartridge sleeve 9. Trigger10. Pressure limiting valve11. Compressed air supply fitting•983723 (packaged separately)12. Handle13. Red button (retract piston rod)3. Preparing the dispenser for use:Package contents•Dispenser• Cartridge sleeve• Mixer(sold separately)• Operating InstructionManualPreparation for useUsers must read and understand the Operating Instruction Manual before first useof the dispenser.Operating principleThe air pressure is reduced by the pressure reductionvalve (10). The piston rods (6) are pushed out of thehousing by the pneumatic piston of the drive unit (5),thereby forcing the component compounds A and Bthrough the mixer.The dispenser operates under high pressure. Failure to follow the instructions inthis Manual can lead to inadvertent release of pressure or breakage of thedispenser at high pressure and may result in serious personal injury to the useror bystanders and/or property damage.Preparing the dispenser•Remove the protective cap (11) from the pressure reduction valve (10).•Install the ¼" BSP adapter (external thread) on the inlet side of the pressure reduction valve, which will allow standard ¼” male connection to be madequick-release coupling.•The use of properly rated pneumatic hose and a quick-release coupling is also recommended.Caution: DANGER OF CRUSHING.Never place your hands or fingers between the plunger and the cartridge.The input pressure of the compressed air must not exceed max. 8 bar (max. 120psi). Requirements for the compressed air supply (see Technical Data).Strictly follow the manufacturer’s safety instructions for the 2-componentadhesive.4. Operation of the dispenserInsert cartridgeNever insert the cartridge while the dispenser is connected to thecompressed air supply.•Push the cartridge into the cartridge sleeve asshown in the drawing and press it down until it clicksinto position. To remove the cartridge stopper,unscrew the cap nut of the cartridge.•Fasten the mixer using the cap nut on the cartridgeoutlet thread.If the cartridge is not in the correct position, the trigger (9) cannot be pressed.•Connect the dispenser to the compressed air supplyDispensing the adhesivePress the trigger (9). Dispensing is started, and the red dispense volume indicator (4) moves forward. When the trigger (9) is released, dispensing stops.The dispense volume can be controlled by means of the pressure reducing valve (10).a) Pull the pressure reduction valve.b) Adjust the dispense volume by turning the adjuster in the + or –direction.c) Press the pressure reduction valve to confirm the set value.Do not remove, tamper or manipulate pressure limiting valve and strictly respect pressure limits.Removing the cartridgeRelease the trigger (9) and press the red button (13) until the feed plungers have retracted to the back end-stop. Using the release button (7), push the cartridge out of the cartridge retainer and pull it upwards out of the unit. Dispose of the cartridge and mixer in conformity with the m anufacturer’sspecifications.5. Troubleshooting:ProblemPotential Cause RemedyPlunger discs cannot enter the cartridgeCartridge not fully inserted in cartridge bedCheck that there is no foreign matter in the cartridge bed. Push the cartridge fully down into the cartridge bed. Mind your fingers.The cartridge cannot be removed from the dispenser .The plunger discs are still in position inside the cartridge . Press the red button to fully retract the plunger discs to theback end-stop.6 . Maintenance and repair:NoticesAll maintenance and repairs must only be carried out by sites authorized by themanufacturer and exclusively by qualified and suitably trained personnel.Always disconnect the compressed air supply from the dispenser duringmaintenance and repairs.Never open the pneumatic drive unit. If the pneumatic drive unit is or appears tobe in need of maintenance or repair, contact a Henkel authorized Service CenterKeep the dispenser clean at all times. Failure to do so may result inmalfunction of dispenser or bodily injury.Do not use aggressive cleaning products to clean the surface of the device.Information for ordering spare parts:Whenorderingspareparts,**************************************************information:•Dispenser Item numberFor 983437 Dispenser1:1/2:1 Cartridge tray- 983726For 983439 Dispenser1:1/2:1 Cartridge tray- 9837274:1 Conversion Kit - 984210For 985249 Dispenser10:1 Conversion Kit- 985287For all 3 units: ¼” BSP male to NPT female air line fitting - 9837237. Technical data:Operating pressure: max. 6 bar (max. 87 psi)Compressed air supply: max. 8 bar (max. 120 psi)Air requirements: ISO 8573-1.2.4.2Pressure adjustment: Variable 0- 6 bar (87 psi)Sound level: 83 dBAkg1.6Weight: 983437kg2.2983439/9852498. Standards applied:2006/42/EG:Machinery Directive97/23/EC:Pressure Equipment DirectiveISO 8573-1:Compressed air quality classes9 WARRANTYHenkel expressly warrants that all products referred to in this Instruction Manual for Loctite®Pneumatic Dual Cartridge Dispensers (hereafter called “Products”) shall be free from defects in materialsand workmanship. Liability for Henkel shall be limited, as its option, to replacing those Products which areshown to be defective in either materials or workmanship or to credit the purchaser the amount of thepurchase price thereof (plus freight and insurance charges paid therefore by the user). The purchaser’s soleand exclusive remedy for breach of warranty shall be such replacement or credit.A claim of defect in materials or workmanship in any Products shall be allowed only when it is submittedin writing within one month after discovery of the defect or after the time the defect should reasonably havebeen discovered and in any event, within (12) months after the delivery of the Products to the purchaser.No such claim shall be allowed in respect of products which have been neglected or improperly stored, transported, handled, installed, connected, operated, used or maintained. In the event of unauthorized modification of the Products including, where products, parts or attachments for use in connection with the Products areavailable from Henkel, the use of products, parts or attachments which are not manufactured by Henkel, noclaim shall be allowed.No Products shall be returned to Henkel for any reason without prior written approval from Henkel.Products shall be returned freight prepaid, in accordance with instructions from Henkel.NO WARRANTY IS EXTENDED TO ANY EQUIPM ENT WHICH HAS BEEN ALTERED, MISUSED, NEGLECTED, OR DAMAGED BY ACCIDENT.EXCEPT FOR THE EXPRESS WARRANTY CONTAINED IN THIS SECTION, HENKEL MAKES NO WARRANTY OF ANY KIND WHATSOEVER, EXPRESS OR IMPLIED, WITH RESPECT TO THE PRODUCTS.ALL WARRANTIES OF MERCHANTABILITY, FITN ESS FOR A PARTICULAR PURPOSE, ANDOTHER WARRANTIES OF WHATEVER KIND (INCLUDING AGAINST PATENT ORTRADEMARK INFRINGEMENT) ARE HEREBY DISCLAIMED BY HENKEL AND WAIVED BYTHE PURCHASER.THIS SECTION SETS FORTH EXCLUSIVELY ALL OF LIABILITY FOR HENKEL TO THEPURCHASER IN CONTRACT, IN TORT OR OTHERWISE IN THE EVENT OF DEFECTIVEPRODUCTS.WITHOUT LIMITATION OF THE FOREGOING, TO THE FULLEST EXTENT POSSIBLE UNDER APPLICABLE LAWS, HENKEL EXPRESSLY DISCLAIMS ANY LIABILITY WHATSOEVER FORANY DAMAGES INCURRED DIRECTLY OR INDIRECTLY IN CONNECTION WITH THE SALEOR USE OF, OR OTHERWISE IN CONNECTION WITH, THE PRODUCTS, INCLUDING, WITHOUT LIMITATION, LOSS OF PROFITS AND SPECIAL, INDIRECT OR CONSEQUENTIAL DAMAGES, WHETHER CAUSED BY NEGLIGENCE FROM HENKEL OR OTHERWISE.Henkel Corporation One Henkel Way Henkel Canada Corporation2225 Meadowpine BoulevardHenkel Capital, S.A. de C.V.Boulevard Magnocentro No. 8 Piso 252760 Huixquilucan, Estado de MexicoRocky Hill, CT 06067-3910 Mississauga, Ontario L5N 7P2® and ™ designate trademarks of Henkel Corporation or its affiliates. ® = registered in the U.S. and elsewhere. © Henkel Corporation, 2009. All rights reserved.Manual # 8902022, Date 07/2009。
Eaton Moeller EMS2 DOL电动启动器说明书

Eaton 197170Eaton Moeller® series EMS2 DOL starter, 230 V AC, 1,5 - 6,5 (AC-53a), 9 (AC-51) A, Screw terminalsGeneral specificationsEaton Moeller® series EMS2 DOLstarter1971704015080896111114.5 mm99 mm22.5 mm0.287 kgUL508IEC/EN 60947-4-2UL File No.: E29096UL Category Control No.: NLDX, NLDX7 UL 60947-4-1CSA-C22.2 No. 60947-4-1-14CE markingUL listedCertified by UL for use in CanadaUL report applies to both US and Canada EMS2-DO-Z-9-230VACProduct Name Catalog NumberEANProduct Length/Depth Product Height Product Width Product Weight Certifications Model CodeTemperature compensated overload protection DOL starting Motor protectionCLASS 10 ANoIP20 NEMA Other Direct starter Top-hat rail fixing (according to IEC/EN 60715, 35 mm) Rail mounting possible Motor feeder at bottom Vertical1.5 A9 AElectronic motor starter 0.2 - 2.5 mm², Main cables 0.14 - 2.5 mm², Control circuit cables 24 - 14, Main cables 26 - 14, Control circuit cables DOL starter (complete device)AC-25 °CClass A (EN 61000-6-3, emitted interference, radiated) EN 55011FunctionsClass Connection to SmartWire-DT Degree of protection Model Mounting methodMounting position Overload release current setting - min Overload release current setting - max Product category Terminal capacityTerminal capacity (AWG)TypeVoltage type Ambient operating temperature - min Radio interference class70 °C40 °C 80 °C 7 mA0 A4 mA85 - 253 V AC230 V (Actuating circuit ON, L, R) 230 V230 V0 V0 V0 V0 V9 A3 A6.5 A9 A6.5 A2 AAmbient operating temperature - maxAmbient storage temperature - min Ambient storage temperature - max Rated actuating current (Ic)Rated conditional short-circuit current (Iq), type 2, 380 V, 400 V, 415 VRated control supply current IsRated control supply voltageRated control voltage (Uc)Rated control supply voltage (Us) at AC, 50 Hz - minRated control supply voltage (Us) at AC, 50 Hz - maxRated control supply voltage (Us) at AC, 60 Hz - minRated control supply voltage (Us) at AC, 60 Hz - maxRated control supply voltage (Us) at DC - minRated control supply voltage (Us) at DC - maxRated operational current (Ie)Rated operational current (Ie) at AC-15, 220 V, 230 V, 240 V Rated operational current (Ie) at AC-3, 380 V, 400 V, 415 V Rated operational current (Ie) at AC-51Rated operational current (Ie) at AC-53A - maxRated operational current (Ie) at DC-13, 24 V1.5 kW3 kW3 kW42 - 550 V500 V AC0 - 44 V AC, Switching level "Low", Actuating circuit (ON, L, R) 85 - 253 V AC, Switching level "High", Actuating circuit (ON, L, R)11116.1 W0 W0 W9 A1 WIf necessary, Allow for deratingMeets the product standard's requirements.Meets the product standard's requirements.Meets the product standard's requirements.Meets the product standard's requirements.Meets the product standard's requirements.Does not apply, since the entire switchgear needs to be evaluated.Rated operational power at AC-3, 220/230 V, 50 HzRated operational power at AC-3, 380/400 V, 50 Hz Rated operational power at AC-53A, 380/400 V, 50 Hz Rated operational voltageSwitching level Number of auxiliary contacts (normally closed contacts) Number of auxiliary contacts (normally open contacts) Number of contacts (change-over contacts)Equipment heat dissipation, current-dependent PvidHeat dissipation capacity PdissHeat dissipation per pole, current-dependent PvidRated operational current for specified heat dissipation (In) Static heat dissipation, non-current-dependent PvsHeat dissipation details10.2.2 Corrosion resistance10.2.3.1 Verification of thermal stability of enclosures10.2.3.2 Verification of resistance of insulating materials to normal heat10.2.3.3 Resist. of insul. mat. to abnormal heat/fire by internal elect. effects10.2.4 Resistance to ultra-violet (UV) radiation10.2.5 LiftingDoes not apply, since the entire switchgear needs to be evaluated.Meets the product standard's requirements.Does not apply, since the entire switchgear needs to be evaluated.Meets the product standard's requirements.Does not apply, since the entire switchgear needs to be evaluated.Does not apply, since the entire switchgear needs to be evaluated.Is the panel builder's responsibility.Is the panel builder's responsibility.Is the panel builder's responsibility.Is the panel builder's responsibility.Is the panel builder's responsibility.The panel builder is responsible for the temperature rise calculation. Eaton will provide heat dissipation data for the devices.Is the panel builder's responsibility. The specifications for the switchgear must be observed.Is the panel builder's responsibility. The specifications for the switchgear must be observed.The device meets the requirements, provided the information in the instruction leaflet (IL) is observed.EMS 2 Electronic motor starters - brochureEMS 2 Electronic motor starters - flyerSwitching and protecting motors - catalogDA-DC-00004192.pdfDA-DC-00003980.pdfeaton-contactors-ems2-reversing-starter-characteristic-curve-002.eps eaton-contactors-ems2-reversing-starter-characteristic-curve.eps eaton-contactors-ems2-reversing-starter-characteristic-curve-004.epseaton-contactors-ems2-reversing-starter-dimensions-002.eps eaton-contactors-ems2-reversing-starter-3d-drawing-002.epsDA-CE-ETN.EMS2-DO-Z-9-230VACIL034064ZUEaton's electronic motor starter EMS2eaton-electronic-motor-starter-ems2-manual-mn034003en-us.pdfDA-CD-ems2_dos_ros_z_24_230vDA-CS-ems2_dos_ros_z_24_230v10.2.6 Mechanical impact10.2.7 Inscriptions10.3 Degree of protection of assemblies10.4 Clearances and creepage distances10.5 Protection against electric shock10.6 Incorporation of switching devices and components 10.7 Internal electrical circuits and connections10.8 Connections for external conductors10.9.2 Power-frequency electric strength10.9.3 Impulse withstand voltage10.9.4 Testing of enclosures made of insulating material 10.10 Temperature rise10.11 Short-circuit rating10.12 Electromagnetic compatibility10.13 Mechanical function BrochuresCatalogues Certification reports Characteristic curve DrawingseCAD model Installation instructions Installation videos Manuals and user guides mCAD modelEaton Corporation plc Eaton House30 Pembroke Road Dublin 4, Ireland © 2023 Eaton. All rights reserved. Eaton is a registered trademark.All other trademarks areproperty of their respectiveowners./socialmedia。
升降机使用说明介绍模板之欧阳体创编

物流输送线升降机使用说明书基信机械有限公司开机前的准备1.检查电源电压为3相4线制,380V,50Hz,无缺项;2.确认输送系统井口输送线与提升机的井口处及提升机上端倒料处无不安全情况(对设备和人体)存在;3.确认控制柜,操作箱上的紧急停止开关操作头处于旋出位置,还需确认上位机未给出急停信号;4.确认各光电开关没被遮挡;5.检查确认后,方能进行下述操作.电源操作1.合上控制柜上隔离开关QFO 为ON位置,接通给系统总电源;2.按压绿色启动开关,设备进入工作待机状态。
;控制流程1.选择运行方式:将现场操作箱上的手动/自动选择开关置手动位置,为手动方式;置自动位置,为自动方式.(注:在系统运行过程中切换手/自动运行方式时,系统会自动停机,再次启动系统需重新开机).2.运行操作:1)手动运行操作:当运行方式选择为手动运行模式时,按压升降机控制柜上的启动按钮,现场电柜上绿色运行指示灯亮。
系统手动启动完成,即可进行以下的手动操作.以下各手动操作按钮均为点动式;即按下相关点动按钮,相关动作运行;释放相关点动按钮,相关动作停止.◆手动进物料操作:在升降机内物料小车处于下层平层位置且物料小车上没有输送物(入料进限光电开关X4都没有被遮挡时),按压操作箱上的手动进料按钮,升降机内物料小车正转运行,若一直按压着手动进料按钮,则一直将输送物料送至箱内至进限位后停止.◆手动上升操作:在升降机不在上限位置,按压操作箱上的手动上升按钮,送料小车即上升,若一直按着手动上升按钮,则轿厢连续上升至上升到上限位置停止.◆手动出料操作:在升降机内物料小车处于下层平层或上层平层位置,按压操作箱上的手动出料按钮,升降机内物料小车反转运行,若一直按压着手动出料按钮,则一直将物料输送到升降机外的工作平台。
(2)自动运行操作:当运行方式选择为自动运行模式且满足自动运行条件---升降机处于下平层位(入料进限光电开关X4都没有被遮挡时),按压升降机控制柜上的启动按钮,现场电柜绿色运行指示灯长亮,系统自动启动完成,即可进行以下的自动运行操作,注:若不满足自动启动条件启动自动运行时,系统不会自动启动,同时红灯闪烁,塔灯声讯报警器鸣响报警,提示未满足自动条件,此时需转换为手动模式启动,手动运行系统以满足自动启动条件后再启动自动运行模式.◆系统自动启动后,此时在现场上料人员可以放进规定尺寸内的物料.,输送系统则将上料人员放上的物料自动送入升降机小车内限位(物料尾部脱离升降机进料口保护光栅时)→升降机小车上升→上升到上限平层位后停止上升→物料小车正转将物料传送出去到工作台→当物料脱离小车内进限位后停2秒→升降机内小车下降到下限平层位置,如此循环进行.◆停机◆自动模式运行中停止: 在电柜上的绿色塔灯为点亮状态时,(1)按压控制柜上货操作箱上的停止按钮,在升降机内小车升降运行到下限平层时,电柜上的运行绿色塔灯熄灭,黄色塔灯长亮,即实现系统的自动模式运行中停机.◆自动模式原点停止: 在电柜上的绿色塔灯为长亮状态时,(1)按压控制柜上的停止按钮,电柜上的运行绿色塔灯熄灭,黄色塔灯长亮,即实现系统的自动模式原点停止机.◆电源解除: 选择控制柜上的空气开关旋钮为OFF位置,解除设备电源.异常停机◆紧急停止:当设备运行中出现对人体及设备构成危害时,应立即安县现场操作箱上货控制柜上的紧急停止按钮,设备停止运行,进入紧急停止状态;故障排除后,先将紧急停止按钮操作头拔出,按压5秒升降机电控柜上的绿色启动按钮进行复位,紧急停止状态解除后,再启动系统。
F04 智能悬挂系统站点电控操作手册

F04 智能悬挂系统站点电控操作手册智能悬挂系统站点电控操作手册目录一、站点面板的基本操作(一)操作面板概述(二)输入对话框操作(三)员工登录、退出(四)普通车缝打出衣架、QC合格打出衣架(五)QC检验返工操作(六)员工查询产量信息二、端口状态及配置(一)站点的端口(二)修改端口(三)端口性能表三、系统参数四、用户参数一、站点面板的基本操作(一)操作面板概述图14设备启动时,员工登录后首页面如上图所示,显示屏主要内容:显示条目说明站号:1-2当前站点编号,主轨号1,站号2运行线体的状态,分为运行、停止,只有运行状态员工才能打衣架出站接收衣架表示当前站点允许接收衣架进站,可按“暂停”键切换停收衣架、接收衣架[MD584]张月英员工的工号、姓名车123登录的衣车编号123今日:0,效率0.00%表示员工在所有站点的产出工序数量及效率本站:0,效率0.00%表示员工在当前站点的产出工序数量及效率最后用时x秒表示最后一件衣架车缝用时按下向键(↓)切换到站位状态信息。
在此界面,按F1键可修改站内衣数(此功能需系统授权),输入数字按确定后生效。
站位状态信息界面条目说明条目说明组号1生产线编号1站号1-2主轨号1,站点编号2进站口衣架当前进站口读卡器读取到的衣架号,会实时显示在此处加工点衣架当前出站口读卡器读取到的衣架号,会实时显示在此处线上系统分配给本站点,但在主轨线上,还未进站的衣架数量站内站点内的衣架数量容量站点最大接收的衣架数量同步站点检测、或接收到的检测主轨推杆的同步信号OK、Err系统检测到正常的同步信号,且主轨运行稳定后,会显示OK,以表示可以正常地进出站;若显示Err,未接收到同步信号,或表示主轨运行不稳定,已影响到进出站动作,站点暂停进出站动作若站点是挂片站,继续按向下键(↓)会显示当前上线信息当前上线信息显示内容为:制单号,颜色,尺码,任务数量,单位(即一个衣架产出成品数量),累计挂裁片数量,今日挂裁片数量。
欧诺立体机操作说明书

欧诺立体机操作说明书欧诺立体机是一种高效、智能化的机器人,广泛应用于工业生产中。
本操作说明书将为您详细介绍欧诺立体机的使用方法。
一、欧诺立体机的基本构造欧诺立体机由机械臂、控制系统、传感器等组成,机械臂由多个关节组成,可实现多种运动方式。
控制系统采用先进的自主控制技术,使机器人能够实时感知环境变化并做出相应的动作。
二、欧诺立体机的操作方法1.开机按下欧诺立体机控制系统面板上的电源开关,等待机器人系统启动完成后,即可开始操作。
2.调试欧诺立体机需要在开始工作之前进行调试。
首先,将机器人放置在工作区域内,然后打开控制系统,进入调试模式,根据需要进行关节运动测试、末端执行器测试、传感器测试等。
3.设置工作参数设置欧诺立体机的工作参数,包括工作速度、工作轨迹、工作力度等,根据具体工作要求进行设置。
4.程序编制欧诺立体机可根据用户要求进行程序编制。
编制程序前,需确定机器人的工作任务以及具体的运动轨迹、速度、力度等参数。
编制完成后,将程序上传至机器人控制系统中,即可开始工作。
5.手动控制欧诺立体机还可进行手动控制。
手动控制需要在控制系统中选择手动模式,然后通过操纵杆或控制面板上的按钮进行机械臂的运动控制。
三、注意事项1.在操作欧诺立体机时,需严格按照操作说明书进行操作,避免误操作导致机器人故障。
2.在欧诺立体机工作时,需保持工作区域内的安全,避免机器人的末端执行器对周围人员或物品造成伤害。
3.在使用欧诺立体机时,需对其进行定期维护,保持机器人的正常运行。
4.在欧诺立体机工作时,需随时监控机器人的运行状态,及时发现故障并进行处理。
欧诺立体机是一种高效、智能的工业机器人,具有广泛的应用前景。
在使用欧诺立体机时,需按照操作说明书进行操作,避免误操作导致机器人故障。
同时,需注意机器人的安全使用,及时进行维护,保持机器人的正常运行。
OM-08511 CL系列中文 使用说明书
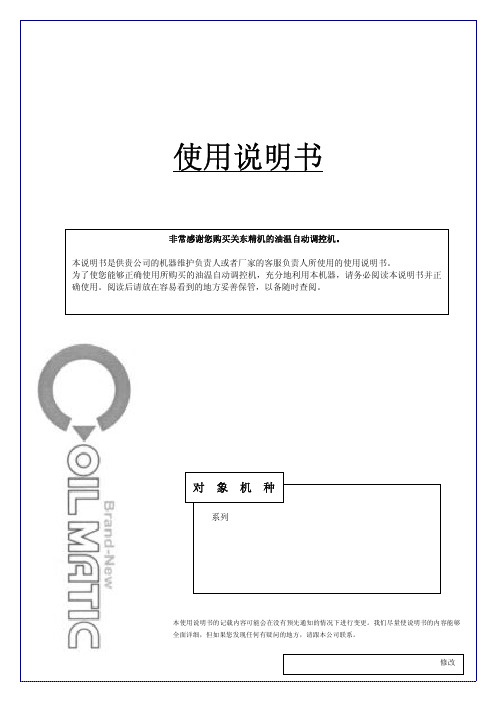
6-3停止 ................................................................................. 29
4-3供油 ................................................................................. 10
4-4接线连接 ............................................................................. 11 (1) 电源的连接............................................................................ 12 (2) 通过外部信号启动时.................................................................... 13 (3) 连接警报器输出触点时.................................................................. 13 (4) 标准温度传感器的安装(选项).......................................................... 13 4-5警报时间表 ........................................................................... 14 5、控制器操作方法............................................................................ 16 5-1操作面板具体内容 ..................................................................... 16
欧氏120663产品说明书

Eaton 120663Eaton Moeller series xPole - mRB4/6 RCBO - residual-current circuit breaker with overcurrent protection. RCD/MCB, 13A, 100mA, C-LS-Char, 3N pole, FI-Char: AGeneral specificationsEaton Moeller series xPole - mRB4/6 RCBO - residual-current circuit breaker with overcurrent protection120663401508118493480 mm 75.5 mm 70 mm 0.446 kg CE Marked RoHS conformCE mRB6-13/3N/C/01-AProduct NameCatalog Number EANProduct Length/Depth Product Height Product Width Product Weight Compliances Certifications Model CodeSwitchgear for residential and commercial applicationsmRB6Combined RCD/MCB devicesSwitchgear for industrial and advanced commercial applications Three-pole + N44CC13 A6 - 25 Ampere0.1 AType A, pulse-current sensitiveRCBO AC400 V230 V / 400 V400 V500 V4 kV30, 100, 300 MilliAmpere Partly surge-proof, 250 A 50 HzA6 kA6 kA6 kA0.5 x I∆n0 kA6 kA6 kAApplicationProduct rangeBasic functionProduct applicationNumber of polesNumber of poles (protected) Number of poles (total) Tripping characteristic Release characteristicRated currentRated current of product range Fault current rating Sensitivity typeType Voltage typeVoltage ratingVoltage rating at ACRated operational voltage (Ue) - maxRated insulation voltage (Ui)Rated impulse withstand voltage (Uimp)Rated fault currents of product rangeImpulse withstand currentFrequency ratingLeakage current typeRated switching capacityRated switching capacity (IEC/EN 60947-2)Rated switching capacity (IEC/EN 61009)Rated non-tripping currentRated short-circuit breaking capacity (EN 60947-2) Rated short-circuit breaking capacity (EN 61009) Rated short-circuit breaking capacity (EN 61009-1) Rated short-circuit breaking capacity (IEC 60947-2)0 kA 0.25 kAUndelayed Non-delayed 100 Ampere gL 3III245 mm480 mm70 mmTri-stable slide catch - enables removal from existing busbar combinationIP20IP40Twin-purpose1 - 25 Square MillimeterBusbar tag shroud to VBG41 mm²25 mm²1 mm²25 mm²2 mmIEC 68-2: 25 °C - 55 °C at 90 % - 95 % humiditySurge current capacityDisconnection characteristic TrippingBack-up fuseSelectivity class Overvoltage category Pollution degree FrameWidth in number of modular spacingsDevice heightBuilt-in depthMounting styleDegree of protectionDegree of protection (built in)Terminals (top and bottom)Solid terminal capacitiesTerminal protectionConnectable conductor cross section (solid-core) - min Connectable conductor cross section (solid-core) - max Connectable conductor cross section (multi-wired) - min Connectable conductor cross section (multi-wired) - max Material thicknessClimatic proofing13 A 0 W 9.4 W 45 W 0 W -25 °C 40 °C Meets the product standard's requirements.Meets the product standard's requirements.Meets the product standard's requirements.Meets the product standard's requirements.Meets the product standard's requirements.Does not apply, since the entire switchgear needs to be evaluated.Does not apply, since the entire switchgear needs to be evaluated.Meets the product standard's requirements.Does not apply, since the entire switchgear needs to be evaluated.Meets the product standard's requirements.Does not apply, since the entire switchgear needs to be evaluated.Does not apply, since the entire switchgear needs to be evaluated.Is the panel builder's responsibility.Is the panel builder's responsibility.Is the panel builder's responsibility.Rated operational current for specified heat dissipation (In) Heat dissipation per pole, current-dependentEquipment heat dissipation, current-dependentStatic heat dissipation, non-current-dependentHeat dissipation capacityAmbient operating temperature - minAmbient operating temperature - max 10.2.2 Corrosion resistance10.2.3.1 Verification of thermal stability of enclosures10.2.3.2 Verification of resistance of insulating materials to normal heat10.2.3.3 Resist. of insul. mat. to abnormal heat/fire by internal elect. effects10.2.4 Resistance to ultra-violet (UV) radiation10.2.5 Lifting10.2.6 Mechanical impact10.2.7 Inscriptions10.3 Degree of protection of assemblies10.4 Clearances and creepage distances10.5 Protection against electric shock10.6 Incorporation of switching devices and components10.7 Internal electrical circuits and connections10.8 Connections for external conductors10.9.2 Power-frequency electric strengthIs the panel builder's responsibility.Is the panel builder's responsibility.The panel builder is responsible for the temperature rise calculation. Eaton will provide heat dissipation data for the devices.Is the panel builder's responsibility. The specifications for the switchgear must be observed.Is the panel builder's responsibility. The specifications for the switchgear must be observed.The device meets the requirements, provided the information in the instruction leaflet (IL) is observed.3Concurrently switching N-neutralIEC/EN 61009eaton-xpole-mrb6-rcbo-catalog-ca019057en-en-us.pdfeaton-xpole-mrb4-rcbo-catalog-ca019058en-en-us.pdfDA-DC-03_mRB-3N03_mRB-3N_28111803_mRB-3p_200416eaton-xeffect-frbm6/m-characteristic-curve-002.jpgeaton-mcb-xpole-mrb4-6-characteristic-curve.epsDimensions xPole mRB4/mRB6 3Neaton-xeffect-frbm6/m-dimensions-004.jpgeaton-mcb-xpole-mrb4-6-dimensions.eps3D Drawing xPole mRB4/mRB6 3NIL019140ZUeaton-xpole-combined-mcb-rcd-device-rcbo-packaging-manual-multilingual.pdfDA-CD-faz_3pn_4pDA-CS-faz_3pn_4pCharacteristics xPole mRB4/mRB6 3Neaton-xeffect-frbm6/m-wiring-diagram-002.jpgContact Sequence xPole mRB4/mRB6 3N10.9.3 Impulse withstand voltage10.9.4 Testing of enclosures made of insulating material 10.10 Temperature rise10.11 Short-circuit rating10.12 Electromagnetic compatibility10.13 Mechanical function Current limiting class FeaturesStandards Catalogues Certification reports Characteristic curve DrawingsInstallation instructions mCAD modelTime/current curves Wiring diagramsEaton Corporation plc Eaton House30 Pembroke Road Dublin 4, Ireland © 2023 Eaton. All rights reserved. Eaton is a registered trademark.All other trademarks areproperty of their respectiveowners./socialmediaeaton-mcb-xpole-mrb4-6-wiring-diagram.eps。
SDL-SF60W(E)中文说明书

SDL-SF60W(E )控制器说明书■ 主要特点:1、 使用了单片机和专用软件,实现了智能控制;2、 利用蓄电池放电率特性修正的准确放电控制。
放电终了电压是由放电率曲线修正的控制点,消除了单纯的电压控制过放的不准确性,符合蓄电池固有的特性,即不同的放电率具有不同的终了电压。
3、 采用了串联式PWM 充电主电路,使充电回路的电压损失较使用二极管的充电电路降低近一半,充电效率较非PWM 高3%-6%,增加了用电时间;过放恢复的提升充电,正常的直充,浮充自动控制方式使系统由更长的使用寿命;同时具有高精度温度补偿;4、 直观的LED 发光管指示当前电瓶状态,让用户了解使用状况;5、 所有控制全部采用工业级芯片(仅对带I 工业级控制器),能在寒冷、高温、潮湿环境运行自如。
同时使用了晶振定时控制,定时控制精确。
6、 取消了电位器调整控制设定点,而利用了Flash 存储器记录各工作控制点,使设置数字化,消除了因电位器震动偏位、温漂等使控制点出现误差降低准确性、可靠性的因素;7、 使用了数字LED 显示及设置,可通过一键式遥控操作所有设置,使用极其方便直观。
8、 系统集成了LED 恒流源,可根据用户需求设置输出功率。
9、 分三时段设置控制恒流一体机以不同功率输出。
10、根据季节调整亮灯时间,具有双时段控制器功能。
11、使用了遥控器控制及显示,遥控器操作即可完成所有设置,使用极其方便直观。
12、防水防护功能等级达IP67。
■ 安装及使用:1. 控制器的固定要牢靠, 外形及安装尺寸如图示:外形尺寸:95X66X20.8mm) 安装孔尺寸:4.0X 3.5(mm)2. 导线的准备:建议使用多股铜芯绝缘导线。
先确定导线长度,在保证安装位置的情况下,尽可能减少连线长度,以减少电损耗。
按照不大于4A/mm 2的电流密度选择铜导线截面积,将控制器一侧的接线头剥去5mm 的绝缘。
按照电池板、蓄电池、负载的顺序安装。
3. 连接光电池导线,先连接控制器上光电池的接线端子,再将另外的端头连至光电池上,注意+,—极,不要反接,如果有阳光,充电指示灯应亮。
Eaton Moeller MSC-D DOL开关机启动器说明书

Eaton 283166Eaton Moeller® series MSC-D DOL starter, 380 V 400 V 415 V: 4 kW, Ir= 6.3 - 10 A, 24 V DC, DCGeneral specificationsEaton Moeller® series MSC-D DOL starter2831664015082831660MSC-D-10-M9(24VDC)95 mm 180 mm 45 mm 0.645 kgUL File No.: E36332 CE VDE 0660CSA Class No.: 3211-24 UL Category Control No.: NLRV CSA File No.: 012528 CSA-C22.2 No. 60947-4-1-14 CSAIEC/EN 60947-4-1 ULUL 60947-4-1Product NameCatalog Number EANModel CodeProduct Length/Depth Product Height Product Width Product Weight CertificationsShort-circuit releaseTemperature compensated overload protection CLASS 10 AScrew terminalsNo1IP20NEMA OtherDirect starterDIN rail16.3 A10 AIII36000 V ACAlso motors with efficiency class IE3 Starter with Bi-Metal releaseDCFitted with: Functions ClassConnectionConnection to SmartWire-DTCoordination typeDegree of protectionModelMounting methodNumber of auxiliary contacts (normally closed contacts) Number of auxiliary contacts (normally open contacts) Overload release current setting - minOverload release current setting - maxOvervoltage categoryPollution degreeRated impulse withstand voltage (Uimp)Suitable forTypeVoltage typeMax. 2000 m -25 °C55 °C 8.5 A9 A2.2 kW4 kW230 - 415 V AC15 A, 600 V AC, (UL/CSA)1 A, 250 V DC, (UL/CSA)A600, AC operated (UL/CSA) P300, DC operated (UL/CSA)150 A 155 A 2.6 W 0 V0 V0 V0 V 24 V 24 VAltitudeAmbient operating temperature - min Ambient operating temperature - max Rated operational current (Ie)Rated operational current (Ie) at AC-3, 380 V, 400 V, 415 V Rated operational power at AC-3, 220/230 V, 50 HzRated operational power at AC-3, 380/400 V, 50 HzRated operational voltageSwitching capacity (auxiliary contacts, general use) Switching capacity (auxiliary contacts, pilot duty)Rated conditional short-circuit current (Iq), type 2, 380 V, 400 V, 415 VShort-circuit release (Irm) - max Power consumption (sealing) at DCRated control supply voltage (Us) at AC, 50 Hz - min Rated control supply voltage (Us) at AC, 50 Hz - max Rated control supply voltage (Us) at AC, 60 Hz - min Rated control supply voltage (Us) at AC, 60 Hz - max Rated control supply voltage (Us) at DC - minRated control supply voltage (Us) at DC - max9 W0 W3 W9 A2.6 WMeets the product standard's requirements.Meets the product standard's requirements.Meets the product standard's requirements.Meets the product standard's requirements.Meets the product standard's requirements.Does not apply, since the entire switchgear needs to be evaluated.Does not apply, since the entire switchgear needs to be evaluated.Meets the product standard's requirements.Does not apply, since the entire switchgear needs to be evaluated.Meets the product standard's requirements.Does not apply, since the entire switchgear needs to be evaluated.Motor Starters in System xStart - brochureSimple, flexible and safe! Distribution system for motor-starter combinationsSave time and space thanks to the new link module PKZM0-XDM32MEProduct Range Catalog Switching and protecting motorsDA-DC-00004878.pdfDA-DC-00004910.pdfeaton-manual-motor-starters-motorstarter-msc-d-dol-starter-dimensions.epseaton-manual-motor-starters-mounting-msc-d-dol-starter-3d-drawing.eps eaton-general-ie-ready-dilm-contactor-standards.epsETN.MSC-D-10-M9(24VDC).edzIL034038ZUIL034014ZUWIN-WIN with push-in technologyDA-CS-msc_d_bg1DA-CD-msc_d_bg1eaton-manual-motor-starters-device-msc-d-dol-starter-wiring-diagram.epsEquipment heat dissipation, current-dependent PvidHeat dissipation capacity PdissHeat dissipation per pole, current-dependent PvidRated operational current for specified heat dissipation (In) Static heat dissipation, non-current-dependent Pvs10.2.2 Corrosion resistance10.2.3.1 Verification of thermal stability of enclosures10.2.3.2 Verification of resistance of insulating materials to normal heat10.2.3.3 Resist. of insul. mat. to abnormal heat/fire by internal elect. effects10.2.4 Resistance to ultra-violet (UV) radiation10.2.5 Lifting10.2.6 Mechanical impact10.2.7 Inscriptions10.3 Degree of protection of assemblies10.4 Clearances and creepage distances10.5 Protection against electric shock10.6 Incorporation of switching devices and components BrochuresCatalogsDeclarations of conformity DrawingseCAD modelInstallation instructions Installation videosmCAD modelWiring diagramsEaton Corporation plc Eaton House30 Pembroke Road Dublin 4, Ireland © 2023 Eaton. All Rights Reserved. Eaton is a registered trademark.All other trademarks areproperty of their respectiveowners./socialmediaDoes not apply, since the entire switchgear needs to be evaluated.Is the panel builder's responsibility.Is the panel builder's responsibility.Is the panel builder's responsibility.Is the panel builder's responsibility.Is the panel builder's responsibility.The panel builder is responsible for the temperature rise calculation. Eaton will provide heat dissipation data for the devices.Is the panel builder's responsibility. The specifications for the switchgear must be observed.Is the panel builder's responsibility. The specifications for the switchgear must be observed.The device meets the requirements, provided the information in the instruction leaflet (IL) is observed.10.7 Internal electrical circuits and connections 10.8 Connections for external conductors 10.9.2 Power-frequency electric strength 10.9.3 Impulse withstand voltage 10.9.4 Testing of enclosures made of insulating material 10.10 Temperature rise10.11 Short-circuit rating10.12 Electromagnetic compatibility10.13 Mechanical function。
couns1301说明书
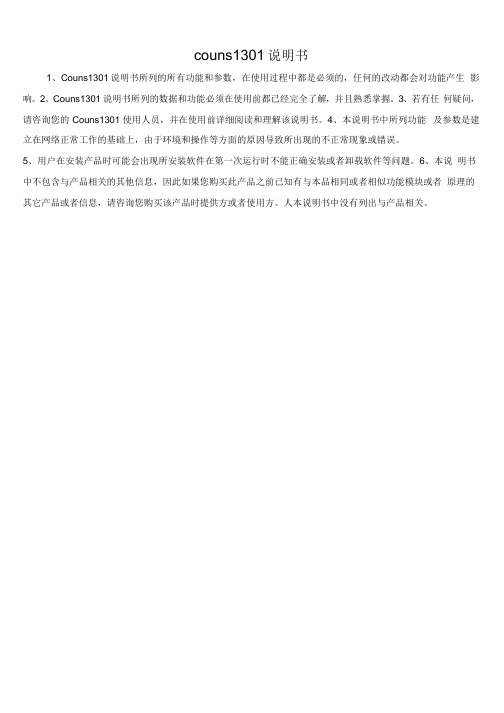
couns1301说明书
1、Couns1301说明书所列的所有功能和参数,在使用过程中都是必须的,任何的改动都会对功能产生影响。
2、Couns1301说明书所列的数据和功能必须在使用前都已经完全了解,并且熟悉掌握。
3、若有任何疑问,请咨询您的Couns1301使用人员,并在使用前详细阅读和理解该说明书。
4、本说明书中所列功能及参数是建立在网络正常工作的基础上,由于环境和操作等方面的原因导致所出现的不正常现象或错误。
5、用户在安装产品时可能会出现所安装软件在第一次运行时不能正确安装或者卸载软件等问题。
6、本说明书中不包含与产品相关的其他信息,因此如果您购买此产品之前已知有与本品相同或者相似功能模块或者原理的其它产品或者信息,请咨询您购买该产品时提供方或者使用方。
人本说明书中没有列出与产品相关。
- 1、下载文档前请自行甄别文档内容的完整性,平台不提供额外的编辑、内容补充、找答案等附加服务。
- 2、"仅部分预览"的文档,不可在线预览部分如存在完整性等问题,可反馈申请退款(可完整预览的文档不适用该条件!)。
- 3、如文档侵犯您的权益,请联系客服反馈,我们会尽快为您处理(人工客服工作时间:9:00-18:30)。
欧洛特智能吊挂系统说明书
欧洛特智能吊挂系统是一种用于提升和悬挂重物的先进设备,利用先进的技术和智能控制,为用户提供高效、安全、便捷的物品搬运解决方案。
本说明书将详细介绍欧洛特智能吊挂系统的特点、使用方法和注意事项,以帮助用户正确、安全地操作这一设备。
一、特点
1.1 高效节能:欧洛特智能吊挂系统采用先进的电动驱动技术,具有高效节能的特点。
其电机功率合理配置,能够在提供足够扭矩的同时减少能耗,提高工作效率。
1.2 智能控制:系统配备智能控制器,可根据不同的悬挂任务自动调整运行参数,实现自动化操作。
用户只需简单设置相关参数,系统即可自动完成吊挂任务,提高工作效率。
1.3 安全可靠:欧洛特智能吊挂系统具有多重安全保护措施,如过载保护、限位保护、紧急停止等,确保在工作过程中的安全可靠性。
系统还配备安全锁装置,防止意外滑落,保障操作人员的人身安全。
1.4 多功能应用:欧洛特智能吊挂系统可根据用户需求进行定制,配备不同的吊具和附件,适用于各种场景和工作环境。
无论是生产线上的物料搬运,还是仓库中的货物堆垛,都能得心应手。
二、使用方法
2.1 安装调试:欧洛特智能吊挂系统在使用前需要进行安装和调试。
首先,根据设备的安装图纸进行安装,确保设备牢固可靠。
然后,根据实际需要进行电气连接和参数设置。
最后,进行空载调试和负载试运行,确保设备正常工作。
2.2 操作指南:欧洛特智能吊挂系统的操作非常简单。
用户只需按下相应的按钮或操作面板上的指示,即可完成起升、下降、前进、后退等动作。
在操作过程中,需注意操作规范,避免超载和误操作,确保安全。
2.3 维护保养:为了保证欧洛特智能吊挂系统的稳定性和寿命,用户应定期进行维护保养工作。
包括清洁设备表面、检查电气连接、润滑传动部件等。
如发现异常情况,应及时进行处理或联系售后服务。
三、注意事项
3.1 严禁超载:在使用欧洛特智能吊挂系统时,严禁超过其额定载荷。
超载可能会导致设备故障、事故发生,严重威胁人身安全和设备正常运行。
3.2 避免碰撞:在操作过程中,应注意避免设备与其他物体发生碰撞,以免造成设备损坏或物体掉落。
3.3 定期检查:为了确保设备的稳定性和安全性,用户应定期对欧洛特智能吊挂系统进行检查。
包括检查电气设备、传动部件、安全保护装置等,发现问题及时处理。
3.4 妥善保管:在长时间不使用欧洛特智能吊挂系统时,应将设备妥善保管,避免长期暴露在潮湿、灰尘等环境中,以免影响设备性能。
3.5 周期检修:根据设备使用情况和工作环境,定期进行设备的检修和维护,以延长设备寿命,并确保其正常运行。
四、总结
欧洛特智能吊挂系统凭借其高效节能、智能控制、安全可靠等特点,成为现代物流搬运领域的重要设备。
本说明书通过介绍其特点、使用方法和注意事项,希望能够帮助用户正确、安全地操作和维护这一设备,提高工作效率,保障人身安全。
在使用过程中,用户应严格按照操作规范和注意事项进行操作,确保设备的稳定性和性能,延长设备的使用寿命。