ansys疲劳分析
ansys疲劳分析基本方法

载荷的循环次数;每一个循环的应力幅;每一个循环的平均应力;存在局部应力集中现象。
真正的疲劳计算要考虑所有这些因素,因为在预测其生命周期时,它计算“消耗”的某个部件是如何形成的。
ANSYS程序处理疲劳问题的过程ANSYS 疲劳计算以ASME锅炉和压力容器规范(ASME Boiler and Pressure Vessel Code)第三节(和第八节第二部分)作为计算的依据,采用简化了的弹塑性假设和Mimer累积疲劳准则。
除了根据 ASME 规范所建立的规则进行疲劳计算外,用户也可编写自己的宏指令,或选用合适的第三方程序,利用 ANSYS 计算的结果进行疲劳计算。
《ANSYS APDL Programmer‘s Guide》讨论了上述二种功能。
ANSYS程序的疲劳计算能力如下:对现有的应力结果进行后处理,以确定体单元或壳单元模型的疲劳寿命耗用系数(fatigue usage factors)(用于疲劳计算的线单元模型的应力必须人工输入);可以在一系列预先选定的位置上,确定一定数目的事件及组成这些事件的载荷,然后把这些位置上的应力储存起来;可以在每一个位置上定义应力集中系数和给每一个事件定义比例系数。
基本术语位置(Location):在模型上储存疲劳应力的节点。
这些节点是结构上某些容易产生疲劳破坏的位置。
事件(Event):是在特定的应力循环过程中,在不同时刻的一系列应力状态,见本章§。
载荷(Loading):是事件的一部分,是其中一个应力状态。
应力幅:两个载荷之间应力状态之差的度量。
程序不考虑应力平均值对结果的影响。
疲劳计算完成了应力计算后,就可以在通用后处理器 POST1 中进行疲劳计算。
一般有五个主要步骤:1、进入后处理 POST1,恢复数据库;2、建立位置、事件和载荷的数目,定义材料疲劳性质,确定应力位置和定义应力集中系数;3、存储不同事件和不同载荷下关心位置的应力,并指定事件的重复次数和比例系数;4、激活疲劳计算;5、查看结果。
ansys疲劳分析基本方法
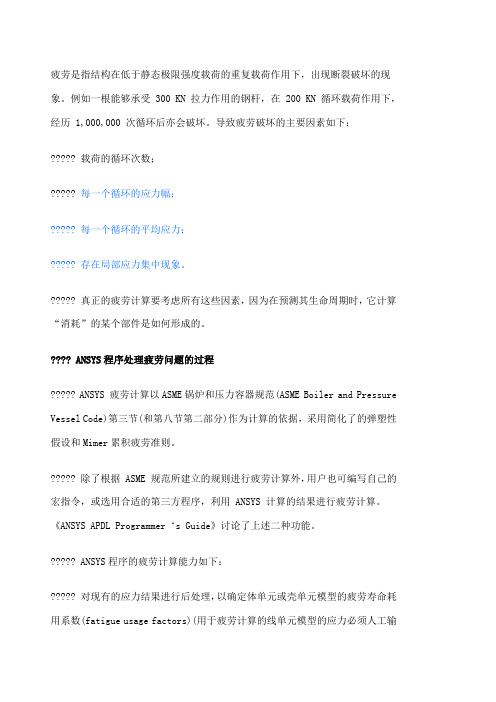
疲劳是指结构在低于静态极限强度载荷的重复载荷作用下,出现断裂破坏的现象。
例如一根能够承受 300 KN 拉力作用的钢杆,在 200 KN 循环载荷作用下,经历 1,000,000 次循环后亦会破坏。
导致疲劳破坏的主要因素如下:????? 载荷的循环次数;????? 每一个循环的应力幅;????? 每一个循环的平均应力;????? 存在局部应力集中现象。
????? 真正的疲劳计算要考虑所有这些因素,因为在预测其生命周期时,它计算“消耗”的某个部件是如何形成的。
???? ANSYS程序处理疲劳问题的过程????? ANSYS 疲劳计算以ASME锅炉和压力容器规范(ASME Boiler and Pressure Vessel Code)第三节(和第八节第二部分)作为计算的依据,采用简化了的弹塑性假设和Mimer累积疲劳准则。
????? 除了根据 ASME 规范所建立的规则进行疲劳计算外,用户也可编写自己的宏指令,或选用合适的第三方程序,利用 ANSYS 计算的结果进行疲劳计算。
《ANSYS APDL Programmer‘s Guide》讨论了上述二种功能。
????? ANSYS程序的疲劳计算能力如下:????? 对现有的应力结果进行后处理,以确定体单元或壳单元模型的疲劳寿命耗用系数(fatigue usage factors)(用于疲劳计算的线单元模型的应力必须人工输入);????? 可以在一系列预先选定的位置上,确定一定数目的事件及组成这些事件的载荷,然后把这些位置上的应力储存起来;????? 可以在每一个位置上定义应力集中系数和给每一个事件定义比例系数。
???? 基本术语?????位置(Location):在模型上储存疲劳应力的节点。
这些节点是结构上某些容易产生疲劳破坏的位置。
????? 事件(Event):是在特定的应力循环过程中,在不同时刻的一系列应力状态,见本章§。
????? 载荷(Loading):是事件的一部分,是其中一个应力状态。
ansys疲劳分析报告基本方法

疲劳是指结构在低于静态极限强度载荷的重复载荷作用下,出现断裂破坏的现象。
例如一根能够承受 300 KN 拉力作用的钢杆,在 200 KN 循环载荷作用下,经历1,000,000 次循环后亦会破坏。
导致疲劳破坏的主要因素如下:载荷的循环次数;每一个循环的应力幅;每一个循环的平均应力;存在局部应力集中现象。
真正的疲劳计算要考虑所有这些因素,因为在预测其生命周期时,它计算“消耗”的某个部件是如何形成的。
3.1.1 ANSYS程序处理疲劳问题的过程ANSYS 疲劳计算以ASME锅炉和压力容器规范(ASME Boiler and Pressure Vessel Code)第三节(和第八节第二部分)作为计算的依据,采用简化了的弹塑性假设和Mimer累积疲劳准则。
除了根据 ASME 规范所建立的规则进行疲劳计算外,用户也可编写自己的宏指令,或选用合适的第三方程序,利用 ANSYS 计算的结果进行疲劳计算。
《ANSYS APDL Programmer‘s Guide》讨论了上述二种功能。
ANSYS程序的疲劳计算能力如下:对现有的应力结果进行后处理,以确定体单元或壳单元模型的疲劳寿命耗用系数(fatigue usage factors)(用于疲劳计算的线单元模型的应力必须人工输入);可以在一系列预先选定的位置上,确定一定数目的事件及组成这些事件的载荷,然后把这些位置上的应力储存起来;可以在每一个位置上定义应力集中系数和给每一个事件定义比例系数。
3.1.2 基本术语位置(Location):在模型上储存疲劳应力的节点。
这些节点是结构上某些容易产生疲劳破坏的位置。
事件(Event):是在特定的应力循环过程中,在不同时刻的一系列应力状态,见本章 §3.2.3.4。
载荷(Loading):是事件的一部分,是其中一个应力状态。
应力幅:两个载荷之间应力状态之差的度量。
程序不考虑应力平均值对结果的影响。
3.2疲劳计算完成了应力计算后,就可以在通用后处理器 POST1 中进行疲劳计算。
ansys疲劳分析基本方法

疲劳是指结构在低于静态极限强度载荷的重复载荷作用下,出现断裂破坏的现象;例如一根能够承受 300 KN 拉力作用的钢杆,在 200 KN 循环载荷作用下,经历 1,000,000 次循环后亦会破坏;导致疲劳破坏的主要因素如下:载荷的循环次数;每一个循环的应力幅;每一个循环的平均应力;存在局部应力集中现象;真正的疲劳计算要考虑所有这些因素,因为在预测其生命周期时,它计算“消耗”的某个部件是如何形成的;ANSYS程序处理疲劳问题的过程ANSYS 疲劳计算以ASME锅炉和压力容器规范ASME Boiler and Pressure Vessel Code第三节和第八节第二部分作为计算的依据,采用简化了的弹塑性假设和Mimer累积疲劳准则;除了根据 ASME 规范所建立的规则进行疲劳计算外,用户也可编写自己的宏指令,或选用合适的第三方程序,利用 ANSYS 计算的结果进行疲劳计算;ANSYS APDL Programmer‘s Guide讨论了上述二种功能;ANSYS程序的疲劳计算能力如下:对现有的应力结果进行后处理,以确定体单元或壳单元模型的疲劳寿命耗用系数fatigue usage factors用于疲劳计算的线单元模型的应力必须人工输入;可以在一系列预先选定的位置上,确定一定数目的事件及组成这些事件的载荷,然后把这些位置上的应力储存起来;可以在每一个位置上定义应力集中系数和给每一个事件定义比例系数;基本术语位置Location:在模型上储存疲劳应力的节点;这些节点是结构上某些容易产生疲劳破坏的位置;事件Event:是在特定的应力循环过程中,在不同时刻的一系列应力状态,见本章§;载荷Loading:是事件的一部分,是其中一个应力状态;应力幅:两个载荷之间应力状态之差的度量;程序不考虑应力平均值对结果的影响;疲劳计算完成了应力计算后,就可以在通用后处理器 POST1 中进行疲劳计算;一般有五个主要步骤:1、进入后处理 POST1,恢复数据库;2、建立位置、事件和载荷的数目,定义材料疲劳性质,确定应力位置和定义应力集中系数;3、存储不同事件和不同载荷下关心位置的应力,并指定事件的重复次数和比例系数;4、激活疲劳计算;5、查看结果;进入POST1和恢复数据库依照下列步骤进行疲劳计算:1、进入POST1命令:POST1GUI:Main Menu>General Postproc2、把数据库文件读入到在内存中如果所要做的疲劳计算是正在进行的 ANSYS 计算过程的继续,则文件已在内存中;结果文件必须已经存在并将其读入内存; 命令:RESUMEGUI:Utility Menu>File>Resume from建立疲劳计算的规模、材料疲劳性质和疲劳计算的位置定义下列数据:位置、事件和载荷的最大数目;材料的疲劳性质;应力位置与应力集中系数SCFs;1、定义位置、事件和载荷的最大数目缺省情况下,疲劳计算最多包括5个节点位置,10个事件,每个事件中3个载荷;如果需要,可以通过下面的命令来设置较大的规模即较多的位置、事件和载荷; 命令:FTSIZEGUI:Main Menu>General Postproc>Fatigue>Size Settings2、定义材料的疲劳性质为了计算各种耗用系数,以及为了包含简化弹塑性效应,必须定义材料的疲劳性质;在疲劳计算中,感兴趣的材料性质有:S-N 曲线:应力幅Smax -Smin/2-疲劳循环次数的关系曲线;ASME S-N 曲线考虑了最大平均应力的影响;如果需要,应把输入的 S-N 曲线进行调节以便考虑平均应力强度效应;如果不输入S-N曲线,那么对于各种可能的应力状态的组合,应力幅将降序排列,但不计算耗用系数;命令:FPGUI:Main Menu>General Postproc>Fatigue>S-N TableSm-T曲线:设计应力强度值-温度曲线;如要考虑检查应力范围是否进入塑性,就必须定义该曲线;命令:FPGUI:Main Menu>General Postproc>Fatigue>Sm_T Table弹塑性材料参数 M 和 N应变强化指数;只在需要使用简化的弹塑性准则时,才输入 M、N;这些参数可以从 ASME 规范中获得;命令:FPGUI:Main Menu>General Postproc>Fatigue>Elas-plas Par下述例子说明了用于输入疲劳材料性质的FP命令的使用方法:Define the S-N table:FP,1,10,30,100,300,1000,10000 Allowable Cycles, NFP,7,100000,1000000 "FP,21,650,390,240,161,109,59 Alternating Stress-FP,27,37,26 Intensity Range, S, ksiDefine the Sm-T table:FP,41,100,200,300,400,500,600 Temperature, deg FFP,47,650,700,750,800 "FP,51,20,20,20,,, "Design Stress-IntensityFP,57,,, Value", Sm =2/3Sy or1/3 Su, ksiDefine the elastic-plastic material parameters:FP,61,,.3 M and N3、定义应力位置和应力集中系数下面的选项允许用户显式地定义疲劳计算中关心的节点位置、该位置的应力集中系数,以及在该位置的一个短的标题可用20个字母;命令:FLGUI:Main Menu>General Postproc>Fatigue>Stress Locations注意--不是所有的疲劳分析都需要使用FL命令;如果使用FS、FSNODE或FSSECT等命令见下,则疲劳节点位置是自动定义的;假使在建模时包含有足够细的网格,则所计算的应力是准确的,因此不必指定应力集中系数 SCFs 但是如果考虑表面影响、尺寸影响和腐蚀影响,则仍然需要指定 SCFs ;在计算疲劳时如果只需要考察一个位置,则可以省略标题;假使定位明确,或是不需要应力集中系数和标题,则可完全不使用FL命令;这里给出了在一个圆柱筒分析中应用FL命令的例子;整体坐标 Y 轴为旋转轴;在不同璧厚交界处的外壁给出了应力集中系数 SCFs 针对轴向线性化应力; FL,1,281,,,,Line 1 at insideFL,2,285,,,,Line 1 at outsideFL,3,311,,,,Line 2 at insideFL,4,315,,,,Line 2 at outside图3-1 圆柱筒应力集中系数 SCFs储存应力、指定事件循环次数和比例因子储存应力为了进行疲劳计算,程序必须知道每一个位置上不同事件和载荷时的应力,以及每一个事件的循环次数;可采用下列选项来存储每一个位置、事件和载荷组合情况下的应力:人工储存应力;从文件中取得节点应力;横截面应力;警告:程序从不假定存在0应力条件;如果一定要考虑零应力条件,就必须在每一个事件中明确地输入何处产生零应力;下面的命令序列,说明如何存储应力;在某些情况下,用户也可以用LCASE命令代替SET命令;人工储存应力: FS从中取出节点应力: SET,FSNODE横截面应力: PATH,PPATH,SET,FSSECT横截面计算也需从的数据中取得可以用不同的方法在一个事件中储存应力;下面说明各种不同的方法;.1 人工储存应力可以人工存储应力和温度不是直接从的结果文件取得;在这种情况下,实际并没有将 POST1 的疲劳模块作为后处理器,而是仅仅作为疲劳计算器使用;线单元如梁单元的应力必须人工输入,因为疲劳模块不能如体元或壳元那样从结果文件中读取数据;命令:FSGUI:Main Menu>General Postproc>Fatigue>-Store Stresses-Specified Val下面的例子说明用上述命令输入的方式:FS,201,1,2,1,,,,,,FS,201,1,2,7,在这个例子中,只输入了全应力1~6项和温度;如果还要输入线性化应力,它们将紧随在温度后面,即8~13项;注意--对只有轴向应力的梁单元,只需输入一个应力分量SX,其余各项空白;.2 从结果文件中提取应力该方法把包含有6个分量的节点应力向量直接储存在结果的数据库内;随后可以用FS命令修正存入的应力分量;注意--在执行FSNODE命令之前,必须使用SET命令,可能还有SHELL命令;SET命令从数据库的文件中读取某一特殊载荷子步下的结果,SHELL命令可选择从壳单元的顶面、中面或底面读取结果缺省是从顶面读取结果;命令:FSNODEGUI:Main Menu>General Postproc>Fatigue>-Store Stresses-From rst File下面给出用FSNODE命令在一个事件的一个节点位置输入应力结果的例子: SET,1 Define data set for load step 1FSNODE,123,1,1 Stress vector at node 123 assigned to event 1,loading 1.SET,2 Define data set for load step 2FSNODE,123,1,2 ...event 1, loading 2SET,3 ...load step 3FSNODE,123,1,3 ...event 1, loading 3图3-2 一个事件中的三个荷载.3 横截面应力本选项计算和存储截面路径它是由以前的PATH和PPATH命令定义的端点的线性化应力;因为通常线性化应力计算是在能代表两个表面的最短距离的线段上进行的,因此,只需在两个表面上各取一个点来描述PPATH命令中的路径;这一步骤将从计算结果的数据库中获得应力;因此必须在SET命令之前使用FSSECT 命令;用FSSECT命令储存的应力分量可用FS 命令修正;命令:FSSECTGUI:Main Menu>General Postproc>Fatigue> -Store Stresses -At Cross Sect使用FSSECT命令的方法可用下述例子说明;如果节点位置没有在FL命令中指定,则在该例子中命令FSSECT将自动给两个路径节点 391 和 395 设定位置编号;见图3-3;图3-3 在执行 FSSECT 命令之前由 PPATH 命令识别的表面节点列表、显示或删除储存的应力用下列选项对储存的应力进行列表、绘图或删除;1、列出每一个位置、每一个事件、每一种载荷或每一种应力状态下的储存应力:命令:FSLISTGUI:Main Menu>General Postproc>Fatigue>-Store Stresses- List Stresses2、对某一位置和事件,以载荷号的函数来显示应力项:命令:FSPLOTGUI:Main Menu>General Postproc>Fatigue>-Store Stresses- Plot Stresses3、删除储存在某一位置、事件和载荷下的应力状态:命令:FSDELEGUI:Main Menu>General Postproc>Fatigue>-Store Stresses- Dele Stresses4、删除某一位置上的所有应力:命令:FLGUI:Main Menu>General Postproc>Fatigue>Stress Locations 5、删除在某一事件中各种载荷下的所有应力:命令:FEGUI:Main Menu>General Postproc>Fatigue>Erase Event Data设定事件重复次数和比例系数本选项确定事件重复次数对该事件的所有荷载和所有位置;也可对该事件中构成载荷的所有应力施加比例系数;命令:FEGUI:Main Menu>General Postproc>Fatigue>Assign Events下面给出该步骤的一个例子:FE,1,-1 Erase all parameters and fatigue stresses formerlyused for event 1.FE,2,100, Assign 100 occurrences to events 2, 3 and 4,REPEAT,3,1 and scale by .FE,5,500 Assign 500 occurrences to event 5.获得准确的耗用系数结构常常承受各种最大和最小应力,它们发生的顺序是未知的甚至是随机的;因此就必须小心地考虑如何在各种可能的应力范围内,得到正确的重复循环次数,以获得有效的疲劳寿命耗用系数;ANSYS 程序自动计算所有可能的应力范围,同时采用我们通常所知道的“雨流”法记数,跟踪这些应力发生的次数;在选定的节点位置,对所有事件进行搜索,以寻找产生最大应力幅的载荷对应力矢量;记录这些应力幅的重复次数,同时包含这些载荷的事件的剩余重复次数随之减少;最终至少有一个事件在某一位置被“用光”,而属于这一事件的其它应力状态,在随后的过程中将被忽略;这一过程一直进行着,直到所有的应力幅及重复次数都被计及后结束;警告通常容易误用疲劳模块的记数功能;如果需要使疲劳计算得到正确的耗用系数,就必须小心地设计好事件;设计事件时遵循下列规则:1、了解 ANSYS 的内部逻辑记数算法,参见ANSYS Theory Reference§,详细地讲述 ANSYS 程序如何记数;2、由于在三维应力状态,很难预测哪一个载荷步具有极值应力,因此可以对每一个事件采用多个载荷群,以便成功获得极值应力见图3-2;3、如果在某一给定的事件中,只包含一个极值应力,则将获得一个较保守的结果;如果在一个事件中,引入不止一个极值应力,则有时将产生不保守的结果;如下例所示:考察一个加载历程,由两个稍有不同的循环构成:载荷循环1:做 500次循环,Sx = + ~ ksi;载荷循环2:做1000次循环,Sx = + ~ ksi;显然这是应力幅为 50 Ksi的 1500 次循环;然而,如果不小心把这些载荷划分成两个事件,则将导致不正确的记数结果;请看该结果如何:事件1 载荷1: Sx = 500次循环载荷2: Sx =事件2 载荷1: Sx = 1000次循环载荷2: Sx =可能的应力幅是:a、从 E1,L1 到 E1,L2: ksib、从 E1,L1 到 E2,L1: ksic、从 E1,L1 到 E2,L2: ksid、从 E1,L2 到 E2,L1: ksie、从 E1,L2 到 E2,L2: ksif、从 E2,L1 到 E2,L2: ksi把这些应力幅从大到小排列:d、从 E1,L2 到 E2,L1: ksia、从 E1,L1 到 E1,L2: ksif、从 E2,L1 到 E2,L2: ksic、从 E1,L1 到 E2,L2: ksib、从 E1,L1 到 E2,L1: ksie、从 E1,L2 到 E2,L2: ksi则记数将如此:d、从 E1,L2 到 E2,L1 500 次循环 - E1 和 E2 用去500 次循环a、从 E1,L1 到 E1,L2 0 次循环 - E1 已用光f、从 E2,L1 到 E2,L2 500 次循环 - E2 又用去 500 次循环c、从 E1,L1 到 E2,L2 0 次循环 - 两个事件都用光b、从 E1,L1 到 E2,L1 0 次循环 - 两个事件都用光e、从 E1,L2 到 E2,L2 0 次循环 - 两个事件都用光上面记录了 50 ksi 应力幅的 1000 次循环,而不是已知的 1500 次循环;这个错误的结果是由于不恰当的事件组合导致的;假使载荷被描述为各自分离的事件如E1,L1 => E1; E1,L2 => E2; E2,L1 => E3; E2,L2 => E4,则将得到下列的记数范围:d、从E2 到E3 的500次循环,用去 500次循环a、从 E1 到 E2 的 0 次循环,因为E2“用光”了f、从 E3 到 E4 的 500 次循环,E3 又用去500次循环,E4 用去500次循环c、从 E1 到 E4 的 500 次循环,E4 又用去500次循环d、从 E1 到 E3 的 0 次循环,因为E3 “用光”了e、从 E2 到 E4 的 0 次循环,因为 E2 和 E4 都“用光”了;上述情况恰当地记录了累积疲劳损伤被,即 50 ksi 应力幅的 1500 次循环;4、相反,对每一个最大和最小应力条件应用分离的事件,则将使记录变得太保守;在这种情况下,应小心地选择应被一起记数的载荷,将它们划分为同一事件;下面的示例说明一些事件如何才能够包括多个极值应力条件;考虑由两个载荷循环组成的载荷历程:载荷循环1:从 Sx = + 到 + ksi,做 500 次循环载荷循环2:从 Sx = + 到 + ksi,做 1000 次循环显然这些循环的最不利组合为以大约 25 ksi 的应力幅做 500 次循环;在本例中,如果将载荷划分为两个事件,则产生了 25 ksi 范围内进行 500 次循环的正确记录;如每一个载荷作为一个独立的事件,将产生一种过于保守的记录,形成 25 ksi 应力幅的 1000 次循环;激活疲劳计算现在有了位置、应力、事件及所有指定的材料参数,可在指定位置执行疲劳计算;位置的确定可用节点本身,也可用位置编号;命令:FTCALCGUI:Main Menu>General postproc>Fatigue>Calculate Fatig查看计算结果疲劳计算结果被输出在输出窗口;如果你将输出转向/OUTPUT到文件中如,就可打开该文件查看结果;命令:LISTGUI:Utility Menu>List>Files>Other>如果用户已输入 S-N 曲线,则所有部位的应力幅从大到小排列与相应的事件/载荷、使用循环次数、允许循环次数、温度和阶段耗用系数一起以表格形式输出;随后输出累积寿命耗用系数;正如前面提到的,FTCALC输出时,将对任一给定的应力幅显示相应的事件和载荷,这些信息能帮助分离出那些引起最大的疲劳损伤的事件与载荷;修正事件的一个方便的方法是把所有的疲劳数据写入文件中它可以在执行FTCALC命令前或后做;写入文件的数据是疲劳模块的命令流;可通过编辑文件文本文件来修改事件,然后用/INPUT命令重新读入被修改的疲劳命令;命令:FTWRITEGUI:Main Menu>General postproc>Fatigue>Write Fatig Data.其它记数方法前面曾介绍过“雨流”记数法;在时间-载荷历程未知的情况下,这一技术才有用处;如果时间-载荷历程已知,对每一个接连的事件分别做疲劳分析FTCALC,然后人工相加这些耗用系数,则可避免得到不恰当的保守结果;疲劳分析示例命令流方法下面是一个疲劳计算输入命令流:Enter POST1 and Resume the Database:/POST1RESUME,...Number of Locations, Events, and LoadingsFTSIZE,...Material Fatigue Properties:FP,1,.... N valuesFP,21,... S valuesFP,41,... T valuesFP,51,... Sm valuesFP,61,... Elastic-plastic material parametersLocations, Stress Concentration Factors, and Location TitlesFL,...Store Stresses 3 Different MethodsStore Stresses Manually:FS,...Retrieve Stresses from the Results File: SET,...FSNODE,...Store Stresses at a Cross-Section:PPATH,...SET,...FSSECT,...Event Repetitions and Scale FactorsFE,...Activate the Fatigue CalculationsFTCALC,...Review the Results List the output fileFINISH其中的 FTSIZE,FP,FL,FS,FSNODE,PPATH,FSSECT,FE 和FTCALC 命令,请参考ANSYS Commands Reference;ANSYS 疲劳计算以ASME锅炉和压力容器规范ASME Boiler and Pressure Vesse l Code第三节和第八节第二部分作为计算的依据,采用简化了的弹塑性假设和M imer累积疲劳准则; 除了根据 ASME 规范所建立的规则进行疲劳计算外,用户也可编写自己的宏指令,或选用合适的第三方程序,利用 ANSYS 计算的结果进行疲劳计算;ANSYS APDL Programmer‘s Guide讨论了上述二种功能; ANSYS 程序的疲劳计算能力如下:对现有的应力结果进行后处理,以确定体单元或壳单元模型的疲劳寿命耗用系数fatigue usage factors用于疲劳计算的线单元模型的应力必须人工输入;可以在一系列预先选定的位置上,确定一定数目的事件及组成这些事件的载荷,然后把这些位置上的应力储存起来;可以在每一个位置上定义应力集中系数和给每一个事件定义比例系数; 基本术语位置Location:在模型上储存疲劳应力的节点;这些节点是结构上某些容易产生疲劳破坏的位置; 事件Event:是在特定的应力循环过程中,在不同时刻的一系列应力状态,见本章§; 载荷Loading:是事件的一部分,是其中一个应力状态; 应力幅:两个载荷之间应力状态之差的度量;程序不考虑应力平均值对结果的影响;疲劳计算完成了应力计算后,就可以在通用后处理器 POST1 中进行疲劳计算;一般有五个主要步骤: 1、进入后处理 POST1,恢复数据库; 2、建立位置、事件和载荷的数目,定义材料疲劳性质,确定应力位置和定义应力集中系数;3、存储不同事件和不同载荷下关心位置的应力,并指定事件的重复次数和比例系数;4、激活疲劳计算;5、查看结果; 进入POST1和恢复数据库依照下列步骤进行疲劳计算: 1、进入POST1 命令:POST1 GUI:Main Menu>General Postproc 2、把数据库文件读入到在内存中如果所要做的疲劳计算是正在进行的 ANSYS 计算过程的继续,则文件已在内存中;结果文件必须已经存在并将其读入内存; 命令:RESUME GUI:Utility Menu>File>Resume from 建立疲劳计算的规模、材料疲劳性质和疲劳计算的位置定义下列数据:位置、事件和载荷的最大数目;材料的疲劳性质;应力位置与应力集中系数SCFs; 1、定义位置、事件和载荷的最大数目缺省情况下,疲劳计算最多包括5个节点位置,10个事件,每个事件中3个载荷;如果需要,可以通过下面的命令来设置较大的规模即较多的位置、事件和载荷; 命令:FTSIZE GU I:Main Menu>General Postproc>Fatigue>Size Settings 2、定义材料的疲劳性质为了计算各种耗用系数,以及为了包含简化弹塑性效应,必须定义材料的疲劳性质;在疲劳计算中,感兴趣的材料性质有: S-N 曲线:应力幅-疲劳循环次数的关系曲线;ASME S-N 曲线考虑了最大平均应力的影响;如果需要,应把输入的 S-N 曲线进行调节以便考虑平均应力强度效应;如果不输入S-N曲线,那么对于各种可能的应力状态的组合,应力幅将降序排列,但不计算耗用系数; 命令:FP GUI:Main Menu>General Postproc>Fatigue>S-N Table Sm-T曲线:设计应力强度值-温度曲线;如要考虑检查应力范围是否进入塑性,就必须定义该曲线; 命令:FP GUI:Main Menu>General Postproc>Fatigue>Sm_T Ta ble 弹塑性材料参数 M 和 N应变强化指数;只在需要使用简化的弹塑性准则时,才输入 M、N;这些参数可以从 ASME 规范中获得; 命令:FP GUI:Main Menu>General Postproc>Fatigue>Elas-plas Par 下述例子说明了用于输入疲劳材料性质的FP命令的使用方法: Define the S-N table: FP,1,10,30,1 00,300,1000,10000 Allowable Cycles, N FP,7,100000,1000000 " FP,2 1,650,390,240,161,109,59 Alternating Stress- FP,27,37,26 Intensity Range, S, ksi Define the Sm-T table: FP,41,100,200,300,400,500,600 Temperature, deg F FP,47,650,700,750,800 " FP,51,20,20,20,,, " Design Stress-Intensity FP,57,,, Value", Sm =2/3Sy or 1/3 Su, ksi Define the elastic-plastic material parameters: FP,61,,.3 M and N 3、定义应力位置和应力集中系数下面的选项允许用户显式地定义疲劳计算中关心的节点位置、该位置的应力集中系数,以及在该位置的一个短的标题可用20个字母; 命令:FL GUI:Main Menu>General Postproc>Fatigue>Str ess Locations 注意--不是所有的疲劳分析都需要使用 FL 命令;如果使用 F S、FSNODE 或 FSSECT 等命令见下,则疲劳节点位置是自动定义的;假使在建模时包含有足够细的网格,则所计算的应力是准确的,因此不必指定应力集中系数 SC Fs 但是如果考虑表面影响、尺寸影响和腐蚀影响,则仍然需要指定 SCFs ;在计算疲劳时如果只需要考察一个位置,则可以省略标题;假使定位明确,或是不需要应力集中系数和标题,则可完全不使用 FL 命令; 这里给出了在一个圆柱筒分析中应用 FL 命令的例子;整体坐标 Y 轴为旋转轴;在不同璧厚交界处的外壁给出了应力集中系数 SCFs 针对轴向线性化应力;。
ansys疲劳分析解析

1.1 疲劳概述结构失效的一个常见原因是疲劳,其造成破坏与重复加载有关。
疲劳通常分为两类:高周疲劳是当载荷的循环(重复)次数高(如1e4 -1e9)的情况下产生的。
因此,应力通常比材料的极限强度低,应力疲劳(Stress-based)用于高周疲劳;低周疲劳是在循环次数相对较低时发生的。
塑性变形常常伴随低周疲劳,其阐明了短疲劳寿命。
一般认为应变疲劳(strain-based)应该用于低周疲劳计算。
在设计仿真中,疲劳模块拓展程序(Fatigue Module add-on)采用的是基于应力疲劳(stress-based)理论,它适用于高周疲劳。
接下来,我们将对基于应力疲劳理论的处理方法进行讨论。
1.2 恒定振幅载荷在前面曾提到,疲劳是由于重复加载引起:当最大和最小的应力水平恒定时,称为恒定振幅载荷,我们将针对这种最简单的形式,首先进行讨论。
否则,则称为变化振幅或非恒定振幅载荷。
1.3 成比例载荷载荷可以是比例载荷,也可以非比例载荷:比例载荷,是指主应力的比例是恒定的,并且主应力的削减不随时间变化,这实质意味着由于载荷的增加或反作用的造成的响应很容易得到计算。
相反,非比例载荷没有隐含各应力之间相互的关系,典型情况包括:σ1/σ2=constant在两个不同载荷工况间的交替变化;交变载荷叠加在静载荷上;非线性边界条件。
1.4 应力定义考虑在最大最小应力值σmin和σmax作用下的比例载荷、恒定振幅的情况:应力范围Δσ定义为(σmax-σmin)平均应力σm定义为(σmax+σmin)/2应力幅或交变应力σa是Δσ/2应力比R是σmin/σmax当施加的是大小相等且方向相反的载荷时,发生的是对称循环载荷。
这就是σm=0,R=-1的情况。
当施加载荷后又撤除该载荷,将发生脉动循环载荷。
这就是σm=σmax/2,R=0的情况。
1.5 应力-寿命曲线载荷与疲劳失效的关系,采用的是应力-寿命曲线或S-N曲线来表示:(1)若某一部件在承受循环载荷, 经过一定的循环次数后,该部件裂纹或破坏将会发展,而且有可能导致失效;(2)如果同个部件作用在更高的载荷下,导致失效的载荷循环次数将减少;(3)应力-寿命曲线或S-N曲线,展示出应力幅与失效循环次数的关系。
ansys疲劳分析汇总

1.1 疲劳概述结构失效的一个常见原因是疲劳,其造成破坏与重复加载有关。
疲劳通常分为两类:高周疲劳是当载荷的循环(重复)次数高(如1e4 -1e9)的情况下产生的。
因此,应力通常比材料的极限强度低,应力疲劳(Stress-based)用于高周疲劳;低周疲劳是在循环次数相对较低时发生的。
塑性变形常常伴随低周疲劳,其阐明了短疲劳寿命。
一般认为应变疲劳(strain-based)应该用于低周疲劳计算。
在设计仿真中,疲劳模块拓展程序(Fatigue Module add-on)采用的是基于应力疲劳(stress-based)理论,它适用于高周疲劳。
接下来,我们将对基于应力疲劳理论的处理方法进行讨论。
1.2 恒定振幅载荷在前面曾提到,疲劳是由于重复加载引起:当最大和最小的应力水平恒定时,称为恒定振幅载荷,我们将针对这种最简单的形式,首先进行讨论。
否则,则称为变化振幅或非恒定振幅载荷。
1.3 成比例载荷载荷可以是比例载荷,也可以非比例载荷:比例载荷,是指主应力的比例是恒定的,并且主应力的削减不随时间变化,这实质意味着由于载荷的增加或反作用的造成的响应很容易得到计算。
相反,非比例载荷没有隐含各应力之间相互的关系,典型情况包括:σ1/σ2=constant在两个不同载荷工况间的交替变化;交变载荷叠加在静载荷上;非线性边界条件。
1.4 应力定义考虑在最大最小应力值σmin和σmax作用下的比例载荷、恒定振幅的情况:应力范围Δσ定义为(σmax-σmin)平均应力σm定义为(σmax+σmin)/2应力幅或交变应力σa是Δσ/2应力比R是σmin/σmax当施加的是大小相等且方向相反的载荷时,发生的是对称循环载荷。
这就是σm=0,R=-1的情况。
当施加载荷后又撤除该载荷,将发生脉动循环载荷。
这就是σm=σmax/2,R=0的情况。
1.5 应力-寿命曲线载荷与疲劳失效的关系,采用的是应力-寿命曲线或S-N曲线来表示:(1)若某一部件在承受循环载荷, 经过一定的循环次数后,该部件裂纹或破坏将会发展,而且有可能导致失效;(2)如果同个部件作用在更高的载荷下,导致失效的载荷循环次数将减少;(3)应力-寿命曲线或S-N曲线,展示出应力幅与失效循环次数的关系。
ANSYSworkbench教程—疲劳分析

第一章简介1.1 疲劳概述结构失效的一个常见原因是疲劳,其造成破坏与重复加载有关。
疲劳通常分为两类:高周疲劳是当载荷的循环(重复)次数高(如1e4 -1e9)的情况下产生的。
因此,应力通常比材料的极限强度低,应力疲劳(Stress-based)用于高周疲劳;低周疲劳是在循环次数相对较低时发生的。
塑性变形常常伴随低周疲劳,其阐明了短疲劳寿命。
一般认为应变疲劳(strain-based)应该用于低周疲劳计算。
在设计仿真中,疲劳模块拓展程序(Fatigue Module add-on)采用的是基于应力疲劳(stress-based)理论,它适用于高周疲劳。
接下来,我们将对基于应力疲劳理论的处理方法进行讨论。
1.2 恒定振幅载荷在前面曾提到,疲劳是由于重复加载引起:当最大和最小的应力水平恒定时,称为恒定振幅载荷,我们将针对这种最简单的形式,首先进行讨论。
否则,则称为变化振幅或非恒定振幅载荷。
1.3 成比例载荷载荷可以是比例载荷,也可以非比例载荷:比例载荷,是指主应力的比例是恒定的,并且主应力的削减不随时间变化,这实质意味着由于载荷的增加或反作用的造成的响应很容易得到计算。
相反,非比例载荷没有隐含各应力之间相互的关系,典型情况包括:σ1/σ2=constant在两个不同载荷工况间的交替变化;交变载荷叠加在静载荷上;非线性边界条件。
1.4 应力定义考虑在最大最小应力值σmin和σmax作用下的比例载荷、恒定振幅的情况:应力范围Δσ定义为(σmax-σmin)平均应力σm定义为(σmax+σmin)/2应力幅或交变应力σa是Δσ/2应力比R是σmin/σmax当施加的是大小相等且方向相反的载荷时,发生的是对称循环载荷。
这就是σm=0,R=-1的情况。
当施加载荷后又撤除该载荷,将发生脉动循环载荷。
这就是σm=σmax/2,R=0的情况。
1.5 应力-寿命曲线载荷与疲劳失效的关系,采用的是应力-寿命曲线或S-N曲线来表示:(1)若某一部件在承受循环载荷, 经过一定的循环次数后,该部件裂纹或破坏将会发展,而且有可能导致失效;(2)如果同个部件作用在更高的载荷下,导致失效的载荷循环次数将减少;(3)应力-寿命曲线或S-N曲线,展示出应力幅与失效循环次数的关系。
ANSYSWORKBENCH疲劳分析指南

ANSYSWORKBENCH疲劳分析指南第一章简介1.1 疲劳概述结构失效的一个常见原因是疲劳,其造成破坏与重复加载有关。
疲劳通常分为两类:高周疲劳是当载荷的循环(重复)次数高(如1e4 -1e9)的情况下产生的。
因此,应力通常比材料的极限强度低,应力疲劳(Stress-based)用于高周疲劳;低周疲劳是在循环次数相对较低时发生的。
塑性变形常常伴随低周疲劳,其阐明了短疲劳寿命。
一般认为应变疲劳(strain-based)应该用于低周疲劳计算。
在设计仿真中,疲劳模块拓展程序(Fatigue Module add-on)采用的是基于应力疲劳(stress-based)理论,它适用于高周疲劳。
接下来,我们将对基于应力疲劳理论的处理方法进行讨论。
1.2 恒定振幅载荷在前面曾提到,疲劳是由于重复加载引起:当最大和最小的应力水平恒定时,称为恒定振幅载荷,我们将针对这种最简单的形式,首先进行讨论。
否则,则称为变化振幅或非恒定振幅载荷。
1.3 成比例载荷载荷可以是比例载荷,也可以非比例载荷:比例载荷,是指主应力的比例是恒定的,并且主应力的削减不随时间变化,这实质意味着由于载荷的增加或反作用的造成的响应很容易得到计算。
相反,非比例载荷没有隐含各应力之间相互的关系,典型情况包括:σ1/σ2=constant在两个不同载荷工况间的交替变化;交变载荷叠加在静载荷上;非线性边界条件。
1.4 应力定义考虑在最大最小应力值σ和σ作用下的比例载荷、恒定振幅的情况:应力范围Δσ定义为(σ-σ)平均应力σ定义为(σ+σ)/2应力幅或交变应力σa是Δσ/2应力比R是σ/σ当施加的是大小相等且方向相反的载荷时,发生的是对称循环载荷。
这就是σm=0,R=-1的情况。
当施加载荷后又撤除该载荷,将发生脉动循环载荷。
这就是σ=σ/2,R=0的情况。
1.5 应力-寿命曲线载荷与疲劳失效的关系,采用的是应力-寿命曲线或S-N曲线来表示:(1)若某一部件在承受循环载荷, 经过一定的循环次数后,该部件裂纹或破坏将会发展,而且有可能导致失效;(2)如果同个部件作用在更高的载荷下,导致失效的载荷循环次数将减少;(3)应力-寿命曲线或S-N曲线,展示出应力幅与失效循环次数的关系。
利用ANSYS随机振动分析功能实现随机疲劳分析

利用ANSYS随机振动分析功能实现随机疲劳分析ANSYS是一款常用的工程仿真软件,具有强大的分析功能。
在进行随机疲劳分析时,可以利用ANSYS的随机振动分析功能来模拟随机加载下的疲劳损伤。
随机疲劳分析是一种考虑工作载荷随机性对结构疲劳寿命影响的方法。
通过采用随机振动分析,可以考虑到工作载荷的随机特性,进一步分析结构的疲劳损伤。
ANSYS中的随机振动分析功能可以通过以下步骤来进行:1.几何建模:首先,需要进行结构的几何建模。
使用ANSYS的几何建模工具可以创建出要进行疲劳分析的结构。
2.材料属性定义:在进行材料属性的定义时,需要确定材料的弹性模量、泊松比、密度和疲劳参数等。
可以根据材料的材料数据手册来获取这些参数。
3.边界条件设置:在进行随机振动分析时,需要设置结构的边界条件。
这些边界条件可以是结构受到的随机外载荷或者是结构与其他部件的接触情况。
4.加载设置:在进行随机振动分析时,需要设置结构受到的随机载荷。
这些载荷可以是来自于实际工况的随机载荷,也可以通过振动台试验数据等手段获取。
5.随机振动分析:利用ANSYS的随机振动分析功能,可以进行频域分析或时域分析。
频域分析可以用于计算结构的响应功率谱密度,时域分析可以用于计算结构的随机响应。
6.疲劳寿命计算:在获得结构的随机响应后,可以进行疲劳寿命计算。
根据结构的随机响应和材料的疲劳性能参数,可以使用ANSYS的疲劳分析功能来计算结构的疲劳寿命。
通过以上步骤,可以利用ANSYS的随机振动分析功能实现随机疲劳分析。
这种方法能够更全面地考虑结构在实际工作环境下的疲劳寿命,为结构的设计和改进提供准确的参考。
需要注意的是,在进行随机疲劳分析时,需要对随机载荷进行合理的统计分析,获取载荷的概率密度函数。
如果没有足够的载荷数据,也可以使用统计模型进行估计。
此外,还需要对材料的疲劳性能参数进行准确的测定,以保证疲劳寿命计算的准确性。
总之,利用ANSYS的随机振动分析功能进行随机疲劳分析是一种有效的方法,可以更准确地评估结构在随机工作载荷下的疲劳性能,为结构的设计和改进提供有力的支持。
ANSYS-随机振动分析功能实现随机疲劳分析

利用 ANSYS随机振动分析功能实现随机疲劳分析ANSYS 随机振动分析功能可以获得结构随机振动响应过程的各种统计参数(如:均值、均方根和平均频率等),根据各种随机疲劳寿命预测理论就可以成功地预测结构的随机疲劳寿命。
本文介绍了ANSYS随机振动分析功能,以及利用该功能,按照Steinberg 提出的基于高斯分布和Miner 线性累计损伤定律的三区间法进行 ANSYS随机疲劳计算的具体过程。
1.随机疲劳现象普遍存在在工程应用中,汽车、飞行器、船舶以及其它各种机械或零部件,大多是在随机载荷作用下工作,当它们承受的应力水平较高,工作达到一定时间后,经常会突然发生随机疲劳破坏,往往造成灾难性的后果。
因此,预测结构或零部件的随机疲劳寿命是非常有必要的。
2.ANSYS随机振动分析功能介绍ANSYS随机振动分析功能十分强大,主要表现在以下方面:1.具有位移、速度、加速度、力和压力等 PSD类型;2.能够考虑 a 阻尼、阻尼、恒定阻尼比和频率相关阻尼比;3.能够定义基础和节点 PSD激励;4.能够考虑多个 PSD激励之间的相关程度:共谱值、二次谱值、空间关系和波传播关系等;5.能够得到位移、应力、应变和力的三种结果数据: 1 位移解, 1 速度解和 1 加速度解;3.利用 ANSYS随机振动分析功能进行疲劳分析的一般原理在工程界,疲劳计算广泛采用名义应力法,即以S-N 曲线为依据进行寿命估算的方法,可以直接得到总寿命。
下面围绕该方法举例说明 ANSYS随机疲劳分析的一般原理。
当应力历程是随机过程时,疲劳计算相对比较复杂。
但已经有许多种分析方法,这里仅介绍一种比较简单的方法,即Steinberg 提出的基于高斯分布和 Miner 线性累计损伤定律的三区间法(应力区间如图 1 所示):应力区间发生的时间68.3% 的时-1~+1间27.1% 的时-2~+2间4.33% 的时-3~+3间99.73%大于 3的应力仅仅发生在0.27%的时间内,假定其不造成任何损伤。
ANSYS疲劳分析

ANSYS疲劳分析疲劳是指结构在低于静态极限强度载荷的重复载荷作用下,出现断裂破坏的现象。
例如一根能够承受300 KN 拉力作用的钢杆,在200 KN 循环载荷作用下,经历1,000,000 次循环后亦会破坏。
导致疲劳破坏的主要因素如下:载荷的循环次数;每一个循环的应力幅;每一个循环的平均应力;存在局部应力集中现象。
真正的疲劳计算要考虑所有这些因素,因为在预测其生命周期时,它计算“消耗”的某个部件是如何形成的。
1.ANSYS程序处理疲劳问题的过程ANSYS 疲劳计算以ASME锅炉和压力容器规范(ASME Boiler and Pressure Vessel Code)作为计算的依据,采用简化了的弹塑性假设和Mimer累积疲劳准则。
除了根据ASME 规范所建立的规则进行疲劳计算外,用户也可编写自己的宏指令,或选用合适的第三方程序,利用ANSYS 计算的结果进行疲劳计算。
《ANSYS APDL Programmer’s Guide》讨论了上述二种功能。
ANSYS程序的疲劳计算能力如下:(1)对现有的应力结果进行后处理,以确定体单元或壳单元模型的疲劳寿命耗用系数(fatigue usage factors)(用于疲劳计算的线单元模型的应力必须人工输入);(2)可以在一系列预先选定的位置上,确定一定数目的事件及组成这些事件的载荷,然后把这些位置上的应力储存起来;(3)可以在每一个位置上定义应力集中系数和给每一个事件定义比例系数。
2.基本术语位置(Location):在模型上储存疲劳应力的节点。
这些节点是结构上某些容易产生疲劳破坏的位置。
事件(Event):是在特定的应力循环过程中,在不同时刻的一系列应力状态。
载荷(Loading):是事件的一部分,是其中一个应力状态。
应力幅:两个载荷之间应力状态之差的度量。
程序不考虑应力平均值对结果的影响。
3.疲劳计算完成了应力计算后,就可以在通用后处理器POST1 中进行疲劳计算。
ansys疲劳分析基本方法

疲劳是指结构在低于静态极限强度载荷的重复载荷作用下,出现断裂破坏的现象。
例如一根能够承受 300 KN 拉力作用的钢杆,在 200 KN 循环载荷作用下,经历 1,000,000 次循环后亦会破坏。
导致疲劳破坏的主要因素如下:载荷的循环次数;每一个循环的应力幅;每一个循环的平均应力;存在局部应力集中现象。
真正的疲劳计算要考虑所有这些因素,因为在预测其生命周期时,它计算“消耗”的某个部件是如何形成的。
3.1.1 ANSYS程序处理疲劳问题的过程ANSYS 疲劳计算以ASME锅炉和压力容器规范(ASME Boiler and Pressure Vessel Code)第三节(和第八节第二部分)作为计算的依据,采用简化了的弹塑性假设和Mimer累积疲劳准则。
除了根据 ASME 规范所建立的规则进行疲劳计算外,用户也可编写自己的宏指令,或选用合适的第三方程序,利用 ANSYS 计算的结果进行疲劳计算。
《ANSYS APDL Programmer‘s Guide》讨论了上述二种功能。
ANSYS程序的疲劳计算能力如下:对现有的应力结果进行后处理,以确定体单元或壳单元模型的疲劳寿命耗用系数(fatigue usage factors)(用于疲劳计算的线单元模型的应力必须人工输入);可以在一系列预先选定的位置上,确定一定数目的事件及组成这些事件的载荷,然后把这些位置上的应力储存起来;可以在每一个位置上定义应力集中系数和给每一个事件定义比例系数。
3.1.2 基本术语位置(Location):在模型上储存疲劳应力的节点。
这些节点是结构上某些容易产生疲劳破坏的位置。
事件(Event):是在特定的应力循环过程中,在不同时刻的一系列应力状态,见本章§3.2.3.4。
载荷(Loading):是事件的一部分,是其中一个应力状态。
应力幅:两个载荷之间应力状态之差的度量。
程序不考虑应力平均值对结果的影响。
3.2 疲劳计算完成了应力计算后,就可以在通用后处理器 POST1 中进行疲劳计算。
Ansys疲劳分析

Ansys疲劳分析1 疲劳的定义疲劳是指结构在低于静态极限强度载荷的重复载荷作用下,出现断裂破坏的现象。
例如一根能够承受 300 KN 拉力作用的钢杆,在 200 KN 循环载荷作用下,经历 1,000,000 次循环后亦会破坏。
导致疲劳破坏的主要因素如下:载荷的循环次数;每一个循环的应力幅;每一个循环的平均应力;存在局部应力集中现象。
真正的疲劳计算要考虑所有这些因素,因为在预测其生命周期时,它计算“消耗”的某个部件是如何形成的。
1.1 ANSYS程序处理疲劳问题的过程ANSYS 疲劳计算以ASME锅炉和压力容器规范(ASME Boiler and Pressure Vessel Code)作为计算的依据,采用简化了的弹塑性假设和Mimer累积疲劳准则。
除了根据 ASME 规范所建立的规则进行疲劳计算外,用户也可编写自己的宏指令,或选用合适的第三方程序,利用 ANSYS 计算的结果进行疲劳计算。
《ANSYS APDL Programmer‘s Guide》讨论了上述二种功能。
ANSYS程序的疲劳计算能力如下:对现有的应力结果进行后处理,以确定体单元或壳单元模型的疲劳寿命耗用系数(fatigue usage factors)(用于疲劳计算的线单元模型的应力必须人工输入);可以在一系列预先选定的位置上,确定一定数目的事件及组成这些事件的载荷,然后把这些位置上的应力储存起来;可以在每一个位置上定义应力集中系数和给每一个事件定义比例系数。
1.2 基本术语位置(Location):在模型上储存疲劳应力的节点。
这些节点是结构上某些容易产生疲劳破坏的位置。
事件(Event):是在特定的应力循环过程中,在不同时刻的一系列应力状态。
载荷(Loading):是事件的一部分,是其中一个应力状态。
应力幅:两个载荷之间应力状态之差的度量。
程序不考虑应力平均值对结果的影响。
2 疲劳计算完成了应力计算后,就可以在通用后处理器 POST1 中进行疲劳计算。
ANSYSWorkbench基础教程与工程分析详解第八章疲劳分析
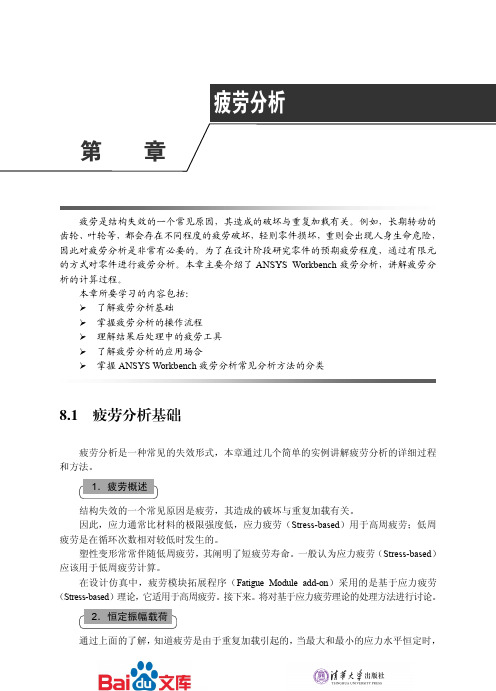
疲劳是结构失效的一个常见原因,其造成的破坏与重复加载有关。
例如,长期转动的齿轮、叶轮等,都会存在不同程度的疲劳破坏,轻则零件损坏,重则会出现人身生命危险,因此对疲劳分析是非常有必要的。
为了在设计阶段研究零件的预期疲劳程度,通过有限元的方式对零件进行疲劳分析。
本章主要介绍了ANSYS Workbench疲劳分析,讲解疲劳分析的计算过程。
本章所要学习的内容包括:¾了解疲劳分析基础¾掌握疲劳分析的操作流程¾理解结果后处理中的疲劳工具¾了解疲劳分析的应用场合¾掌握ANSYS Workbench疲劳分析常见分析方法的分类8.1 疲劳分析基础疲劳分析是一种常见的失效形式,本章通过几个简单的实例讲解疲劳分析的详细过程和方法。
结构失效的一个常见原因是疲劳,其造成的破坏与重复加载有关。
因此,应力通常比材料的极限强度低,应力疲劳(Stress-based)用于高周疲劳;低周疲劳是在循环次数相对较低时发生的。
塑性变形常常伴随低周疲劳,其阐明了短疲劳寿命。
一般认为应力疲劳(Stress-based)应该用于低周疲劳计算。
在设计仿真中,疲劳模块拓展程序(Fatigue Module add-on)采用的是基于应力疲劳(Stress-based)理论,它适用于高周疲劳。
接下来。
将对基于应力疲劳理论的处理方法进行讨论。
通过上面的了解,知道疲劳是由于重复加载引起的,当最大和最小的应力水平恒定时,得到计算。
相反,非比例载荷没有隐含各应力之间的关系,典型的情况包括以下几种。
(1)12constam σ=。
(2)在两个不同载荷工况件的交替变化。
(3)交变载荷叠加在静载荷上。
(4)非线性边界条件。
考虑在最大最小应力值max min σσ和作用下的比例载荷、恒定振幅的情况有以下几种。
(1)应力范围σ∆定义为(max min σσ-)。
(2)平均应力m σ定义为max min ()σσ+/2。
Ansys疲劳分析

Ansys疲劳分析影响疲劳的主要因素包括:●载荷循环的次数●每一个载荷循环中应力值的范围●每一个载荷循环周期中平均应力值●是否存在局部应力集中(local stress concentrations)ANSYS疲劳分析计算基于ASME Boiler和pressure vessel code(压力容器程序),第三节,来指导范围计算,简化弹塑性适用条件,并根据Miner’s准则累积计算实效总和。
ANSYS可进行下列疲劳计算:●可以通过后处理已有的应力结果,来确定实体单元或壳单元的疲劳因子(也可以手动输入应力值来计算线单元模型的疲劳)●对于某工况可以存储其应力和载荷。
●对于每一个位置可以定义其应力集中系数和每一个工况的缩放因子其中,位置是指模型中的一个节点,将存储此处的疲劳应力。
位置一般选在易发生疲劳破坏的点处。
工况是指在一个特定应力循环周期内,不同时间出现的一系列应力条件。
载荷是指一种应力条件,是工况的一部分。
交变应力集度(alternating stress intensity)用来度量两个不同载荷之间应力状态的差别。
进行疲劳分析通常由5个步骤:1.调用ANSYS数据,进入后处理模块2.确定大小(位置的数量,工况和载荷),定义疲劳材料属性,确定应力位置,并定义应力集中系数。
3.存储各种工况和载荷条件下的关注点的应力值;赋予工况重复和缩放因子。
4.激活疲劳计算。
5.查看结果。
14.3.1调用ansys数据,进入后处理模块具体的过程为:1.进入后处理模块,Command(s): /POST1GUI: Main Menu> General Postproc2.调用ansys数据,Command(s): RESUMEGUI: Utility Menu> File> Resume from14.3.2确定大小,疲劳材料属性和位置需要定义如下数据:●位置、工况和载荷的最大值●疲劳材料属性●应力的位置和应力集中系数。
ansys-workbench疲劳分析流程

ansys workbench疲劳分析流程基于S-N曲线的疲劳分析的最终目的是将变化无规律的多轴应力转化为简单的单轴应力循环,以便查询S-N曲线,得到相应的疲劳寿命。
ansysworkbench 的疲劳分析模块采用如下流程,其中r=Smin/Smax,Sa为应力幅度,Sm应力循环中的应力均值,注意后一个m不是大写:):(1)无规律多轴应力-->无规律单轴应力这个转换其实就是采用何种应力(或分量)。
只能有以下选择:Von-Mises等效应力;最大剪应力;最大主应力;或某一应力分量(Sx,Syz 等等)。
有时也采用带符号的Mises应力(大小不变等于Mises应力,符号取最大主应力的符号,好处是可以考虑拉或压的影响(反映在平均应力或r上))。
同强度理论类似,Von-Mises等效应力和最大剪应力转换适用于延展性较好的材料,最大主应力转换用于脆性材料。
(2)无规律单轴应力-->简单单轴应力循环其本质是从无规律的高高低低的等效单轴应力--时间曲线中提取出一系列的简单应力循环(用Sa,Sm表征)以及对应的次数。
有很多种方法可以完成此计数和统计工作,其中又分为路径相关方法和路径无关方法。
用途最广的雨流法(rainflowcountingmethod)就是一种路径相关方法。
其算法和原理可见“Downing, S., Socie, D. (1982) Simplified rain flow counting algorithms. Int J Fatigue,4, 31–40“。
经过雨流法的处理后,无规律的应力--时间曲线转化为一系列的简单循环(Sa,Sm和ni,ni为该循环的次数,Sm如果不等于0,即r!=-1,需要考虑r的影响)。
然后将r!=-1的循环再转化到r=-1对应的应力循环(见下),这样就可以根据损伤累计理论(Miner准则)计算分析了:Sum(ni/Ni) Ni为该应力循环对应的寿命(考虑Sa,Sm)。
ANSYS疲劳分析

ANSYS疲劳分析ANSYS是一种流行的工程仿真软件,用于进行各种工程问题的有限元分析。
在工程实践中,疲劳分析是一个非常重要的领域。
疲劳是指材料在重复载荷作用下逐渐破坏的过程。
疲劳分析的目的是评估结构在实际使用条件下的寿命和性能。
ANSYS可以用来进行疲劳分析,通过确定应力和应变的分布,评估结构在长期使用中可能出现的问题。
在进行疲劳分析之前,首先要进行有限元模型的建立。
这包括将结构模型导入到ANSYS中,确定边界条件和加载条件等。
在进行疲劳分析时,首先要确定疲劳载荷的类型和大小。
这可以通过实验测量或数值模拟来获取。
然后,将载荷应用在结构模型上,并进行动态分析。
ANSYS可以模拟不同的载荷情况,例如正弦载荷、随机载荷和脉冲载荷等。
通过分析结果,可以获得结构在不同位置的应力和应变分布。
在完成动态分析后,可以对结果进行验证和修正。
如果分析的结果与实际测量不符,可能需要对模型进行修正。
修正的方法包括调整材料的本构模型、改变模型的几何形状或重新定义载荷条件等。
完成验证后,可以进行疲劳分析。
在ANSYS中,可以使用不同的疲劳分析模块进行分析。
其中最常用的是疲劳寿命评估模块。
该模块可以根据疲劳参数和材料的S-N曲线,预测结构在给定载荷下的疲劳寿命。
这可以帮助工程师评估结构的安全性和可靠性,并采取适当的措施来延长结构的使用寿命。
疲劳分析还可以进行应力寿命曲线分析。
该分析方法可以通过建立不同应力水平和循环数的组合,预测结构的疲劳寿命。
这对于识别结构中的关键部位和进行寿命预测非常有帮助。
此外,还可以使用应变寿命方法进行疲劳分析。
该方法通过应变历程和损伤累积,评估结构在疲劳载荷下的性能。
在完成疲劳分析后,可以对结果进行后处理。
这包括评估结构的疲劳寿命、疲劳裕度和故障位置等。
通过分析结果,可以确定哪些部位可能会在疲劳过程中发生破坏,并采取适当的措施来加强这些部位。
总之,ANSYS是进行疲劳分析的强大工具。
它可以用于建立结构模型、应用载荷、进行动态分析和预测结构的疲劳寿命。
- 1、下载文档前请自行甄别文档内容的完整性,平台不提供额外的编辑、内容补充、找答案等附加服务。
- 2、"仅部分预览"的文档,不可在线预览部分如存在完整性等问题,可反馈申请退款(可完整预览的文档不适用该条件!)。
- 3、如文档侵犯您的权益,请联系客服反馈,我们会尽快为您处理(人工客服工作时间:9:00-18:30)。
1。
1 疲劳概述结构失效的一个常见原因是疲劳,其造成破坏与重复加载有关.疲劳通常分为两类:高周疲劳是当载荷的循环(重复)次数高(如1e4 —1e9)的情况下产生的。
因此,应力通常比材料的极限强度低,应力疲劳(Stress—based)用于高周疲劳;低周疲劳是在循环次数相对较低时发生的。
塑性变形常常伴随低周疲劳,其阐明了短疲劳寿命.一般认为应变疲劳(strain-based)应该用于低周疲劳计算。
在设计仿真中,疲劳模块拓展程序(Fatigue Module add-on)采用的是基于应力疲劳(stress—based)理论,它适用于高周疲劳。
接下来,我们将对基于应力疲劳理论的处理方法进行讨论。
1。
2 恒定振幅载荷在前面曾提到,疲劳是由于重复加载引起:当最大和最小的应力水平恒定时,称为恒定振幅载荷,我们将针对这种最简单的形式,首先进行讨论.否则,则称为变化振幅或非恒定振幅载荷。
1.3 成比例载荷载荷可以是比例载荷,也可以非比例载荷:比例载荷,是指主应力的比例是恒定的,并且主应力的削减不随时间变化,这实质意味着由于载荷的增加或反作用的造成的响应很容易得到计算。
相反,非比例载荷没有隐含各应力之间相互的关系,典型情况包括:σ1/σ2=constant在两个不同载荷工况间的交替变化;交变载荷叠加在静载荷上;非线性边界条件。
1。
4 应力定义考虑在最大最小应力值σmin和σmax作用下的比例载荷、恒定振幅的情况:应力范围Δσ定义为(σmax-σmin)平均应力σm定义为(σmax+σmin)/2应力幅或交变应力σa是Δσ/2应力比R是σmin/σmax当施加的是大小相等且方向相反的载荷时,发生的是对称循环载荷。
这就是σm=0,R=-1的情况。
当施加载荷后又撤除该载荷,将发生脉动循环载荷。
这就是σm=σmax/2,R=0的情况.1。
5 应力-寿命曲线载荷与疲劳失效的关系,采用的是应力-寿命曲线或S-N曲线来表示:(1)若某一部件在承受循环载荷, 经过一定的循环次数后,该部件裂纹或破坏将会发展,而且有可能导致失效;(2)如果同个部件作用在更高的载荷下,导致失效的载荷循环次数将减少;(3)应力—寿命曲线或S-N曲线,展示出应力幅与失效循环次数的关系。
S—N曲线是通过对试件做疲劳测试得到的弯曲或轴向测试反映的是单轴的应力状态,影响S-N曲线的因素很多,其中的一些需要的注意,如下:材料的延展性,材料的加工工艺,几何形状信息,包括表面光滑度、残余应力以及存在的应力集中,载荷环境,包括平均应力、温度和化学环境,例如,压缩平均应力比零平均应力的疲劳寿命长,相反,拉伸平均应力比零平均应力的疲劳寿命短,对压缩和拉伸平均应力,平均应力将分别提高和降低S-N曲线。
因此,记住以下几点:一个部件通常经受多轴应力状态。
如果疲劳数据(S-N 曲线)是从反映单轴应力状态的测试中得到的,那么在计算寿命时就要注意:(1)设计仿真为用户提供了如何把结果和S—N曲线相关联的选择,包括多轴应力的选择;(2)双轴应力结果有助于计算在给定位置的情况.平均应力影响疲劳寿命,并且变换在S—N曲线的上方位置与下方位置(反映出在给定应力幅下的寿命长短):(1)对于不同的平均应力或应力比值,设计仿真允许输入多重S-N曲线(实验数据);(2)如果没有太多的多重S—N曲线(实验数据),那么设计仿真也允许采用多种不同的平均应力修正理论。
早先曾提到影响疲劳寿命的其他因素,也可以在设计仿真中可以用一个修正因子来解释。
1。
6 总结疲劳模块允许用户采用基于应力理论的处理方法,来解决高周疲劳问题。
以下情况可以用疲劳模块来处理:恒定振幅,比例载荷(参考第二章);变化振幅,比例载荷(参考第三章);恒定振幅,非比例载荷(参考第四章).需要输入的数据是材料的S-N曲线:S-N曲线是疲劳实验中获得,而且可能本质上是单轴的,但在实际的分析中,部件可能处于多轴应力状态。
S—N曲线的绘制取决于许多因素,包括平均应力,在不同平均应力值作用下的S—N曲线的应力值可以直接输入,或可以执行通过平均应力修正理论实现。
2.1 基本情况进行疲劳分析是基于线性静力分析,所以不必对所有的步骤进行详尽的阐述。
疲劳分析是在线性静力分析之后,通过设计仿真自动执行的。
对疲劳工具的添加,无论在求解之前还是之后,都没有关系,因为疲劳计算不并依赖应力分析计算.尽管疲劳与循环或重复载荷有关,但使用的结果却基于线性静力分析,而不是谐分析.尽管在模型中也可能存在非线性,处理时就要谨慎了,因为疲劳分析是假设线性行为的。
在本章中,将涵盖关于恒定振幅、比例载荷的情况。
而变化振幅、比例载荷的情况和恒定振幅、非比例载荷的情况,将分别在以后的第三和四章中逐一讨论。
2.1.1 疲劳程序下面是疲劳分析的步骤,用斜体字体所描述的步骤,对于包含疲劳工具的应力分析是很特殊的:模型指定材料特性,包括S—N曲线;定义接触区域(若采用的话);定义网格控制(可选的);包括载荷和支撑;(设定)需要的结果,包括Fatigue tool;求解模型;查看结果。
在几何方面,疲劳计算只支持体和面,线模型目前还不能输出应力结果,所以疲劳计算对于线是忽略的,线仍然可以包括在模型中以给结构提供刚性,但在疲劳分析并不计算线模型。
2.1.2 材料特性由于有线性静力分析,所以需要用到杨氏模量和泊松比:如果有惯性载荷,则需要输入质量密度;如果有热载荷,则需要输入热膨胀系数和热传导率;如果使用应力工具结果(Stress Tool result),那么就需要输入应力极限数据,而且这个数据也是用于平均应力修正理论疲劳分析.疲劳模块也需要使用到在工程数据分支下的材料特性当中S—N曲线数据:数据类型在“疲劳特性”(“Fatigue Properties")下会说明;S-N曲线数据是在材料特性分支条下的“交变应力与循环”(“Alternating Stress vs。
Cycles")选项中输入的。
如果S—N曲线材料数据可用于不同的平均应力或应力比下的情况, 那么多重S-N曲线也可以输入到程序中.2.1.3 疲劳材料特性添加和修改疲劳材料特性:在材料特性的工作列表中,可以定义下列类型和输入的S-N曲线,插入的图表可以是线性的(“Linear”)、半对数的(“Semi—Log"即linear for stress, log for cycles)或双对数曲线(“Log-Log”).记得曾提到的,S—N曲线取决于平均应力.如果S-N曲线在不同的平均应力下都可适用的,那么也可以输入多重S-N曲线,每个S-N曲线可以在不同平均应力下直接输入,每个S—N曲线也可以在不同应力比下输入.可以通过在“Mean Value”上点击鼠标右键添加新的平均值来输入多条S-N曲线。
2。
1。
4 疲劳特征曲线材料特性信息可以保存XML文件或从XML文件提取,保存材料数据文件,在material条上按右键,然后用“Export …”保存成XML外部文件,疲劳材料特性将自动写到XML文件中,就像其他材料数据一样.一些例举的材料特性在如下安装路径下可以找到:C:\ProgramFiles\AnsysInc\v80\AISOL\CommonFiles\Language\en—us\EngineeringData\Materials,“Alu minum”和“Structural Steel”的XML文件,包含有范例疲劳数据可以作为参考,疲劳数据随着材料和测试方法的不同而有所变化,所以很重要一点就是,用户要选用能代表自己部件疲劳性能的数据2。
1.5 接触区域接触区域可以包括在疲劳分析中,注意,对于在恒定振幅、成比例载荷情况下处理疲劳时,只能包含绑定(Bonded)和不分离(No—Separation)的线性接触,尽管无摩擦、有摩擦和粗糙的非线性接触也能够包括在内,但可能不再满足成比例载荷的要求.例如,改变载荷的方向或大小,如果发生分离,则可能导致主应力轴向发生改变;如果有非线性接触发生,那么用户必须小心使用,并且仔细判断;对于非线性接触,若是在恒定振幅的情况下,则可以采用非比例载荷的方法代替计算疲劳寿命.2。
1.6 载荷与支撑能产生成比例载荷的任何载荷和支撑都可能使用,但有些类型的载荷和支撑不造成比例载荷:螺栓载荷对压缩圆柱表面侧施加均布力,相反,圆柱的相反一侧的载荷将改变;预紧螺栓载荷首先施加预紧载荷,然后是外载荷,所以这种载荷是分为两个载荷步作用的过程;压缩支撑(Compression Only Support)仅阻止压缩法线正方向的移动,但也不会限制反方向的移动,像这些类型的载荷最好不要用于恒定振幅和比例载荷的疲劳计算.2.1。
7 (设定)需要的结果对于应力分析的任何类型结果,都可能需要用到:应力、应变和变形–接触结果(如果版本支持);应力工具(Stress Tool)。
另外,进行疲劳计算时,需要插入疲劳工具条(Fatigue Tool):在Solution子菜单下,从相关的工具条上添加“Tools 〉Fatigue Tool”,Fatigue Tool的明细窗中将控制疲劳计算的求解选项;疲劳工具条(Fatigue Tool)将出现在相应的位置中,并且也可添加相应的疲劳云图或结果曲线,这些是在分析中会被用到的疲劳结果,如寿命和破坏.2.1.8 需要的结果在疲劳计算被详细地定义以后,疲劳结果可下在Fatigue Tool下指定;等值线结果(Contour)包括Lifes(寿命),Damage(损伤),Safety Factor(安全系数),BiaxialityIndication(双轴指示),以及Equivalent Alternating Stress(等效交变应力);曲线图结果(graph results))仅包含对于恒定振幅分析的疲劳敏感性(fatigue sensitivity);这些结果的详细分析将只做简短讨论.2.2 Fatigue Tool2。
2.1 载荷类型当Fatigue Tool在求解子菜单下插入以后,就可以在细节栏中输入疲劳说明:载荷类型可以在“Zero-Based”、“Fully Reversed”和给定的“Ratio”之间定义;也可以输入一个比例因子,来按比例缩放所有的应力结果。
2。
2.2 平均应力影响在前面曾提及,平均应力会影响S—N曲线的结果. 而“Analysis Type”说明了程序对平均应力的处理方法:“SN-None”:忽略平均应力的影响“SN—Mean Stress Curves":使用多重S-N曲线(如果定义的话)“SN—Goodman,"“SN—Soderberg,"和“SN—Gerber”:可以使用平均应力修正理论。