合成氨厂脱硫剂与脱硫工艺的选择
合成氨厂脱硫剂与脱硫工艺的选择

合成氨(联醇)厂干法脱硫工艺优化与脱硫剂经济选择苗茂谦郭汉贤上官炬王怀俊陈志勇(太原理工大学煤化所)(山西科灵催化净化技术发展公司太原030024)众所周知,传统意义的小化肥厂已不存在。
以煤为原料采用的合成氨厂净化过程一般都使用一种或数种干法脱硫剂。
干法脱硫的工艺优化和脱硫剂的经济选择是项重要内容。
随着合成氨厂生产规模的不断扩大和技术进步的不断提升,伴随着干法脱硫工艺的发展和脱硫剂性能的提高,干法脱硫工艺和脱硫剂选择已不仅仅是一个价格层面上的事情,而是涉及生产过程净化指标能否长时间达标,装置能否长期安全、稳定运行,进而影响企业经济效益的重大问题。
化肥生产中合成气采用“湿法+干法脱硫”,主要是为防止合成催化剂中毒。
干法脱硫剂及脱硫工艺要按照气体中硫形态、硫负荷、气氛及净化度要求来优化选择。
以下分别就合成氨(联醇)厂通常使用的干法脱硫工艺和脱硫剂使用情况进行分析比较。
1 变换气湿法脱硫后的干法脱硫工艺和脱硫剂选择变换气湿法脱硫后一般仍含有5.0-20 mg/m3(有的甚至更高)的H2S,并含有一定量的有机硫。
基于保护脱碳溶液或为降低CO2气体中H2S含量的考虑,许多厂都在变换气湿法脱硫后选用干法脱硫工艺。
一般情况下,变换气湿法脱硫后对干法脱硫要求的精度不是很高,能满足脱碳要求即可。
因此,通常选用单一的脱硫剂品种脱除大部分的H2S。
在流程安排上,如果硫化物含量较高,最好选择两开一备、并可交替倒塔串联的流程;如果硫化物含量较低,也可选择单塔流程。
脱硫剂型号的选择十分重要。
过去人们大都由于其脱硫要求的精度不高而选择使用普通的活性炭脱硫剂,也有一些厂家选择使用普通氧化铁脱硫剂。
事实上,变换气中脱除H2S基本上可以达到工艺要求。
但是,几乎所有的人都忽略了一种现象所引起的负面作用。
就是许多工厂在使用普通活性炭或氧化铁脱硫剂后,脱硫塔出口H2S含量虽然合格,但COS含量却明显增加,有的厂甚至有90%以上的H2S转化为COS。
几种脱硫工艺选择
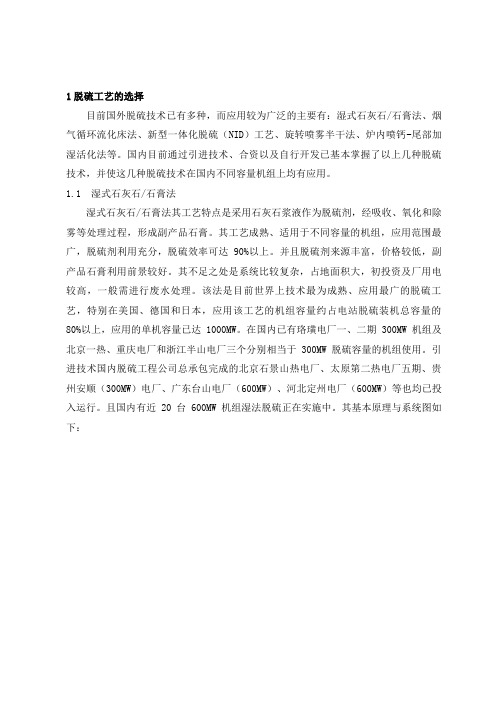
1脱硫工艺的选择目前国外脱硫技术已有多种,而应用较为广泛的主要有:湿式石灰石/石膏法、烟气循环流化床法、新型一体化脱硫(NID)工艺、旋转喷雾半干法、炉内喷钙-尾部加湿活化法等。
国内目前通过引进技术、合资以及自行开发已基本掌握了以上几种脱硫技术,并使这几种脱硫技术在国内不同容量机组上均有应用。
1.1 湿式石灰石/石膏法湿式石灰石/石膏法其工艺特点是采用石灰石浆液作为脱硫剂,经吸收、氧化和除雾等处理过程,形成副产品石膏。
其工艺成熟、适用于不同容量的机组,应用范围最广,脱硫剂利用充分,脱硫效率可达90%以上。
并且脱硫剂来源丰富,价格较低,副产品石膏利用前景较好。
其不足之处是系统比较复杂,占地面积大,初投资及厂用电较高,一般需进行废水处理。
该法是目前世界上技术最为成熟、应用最广的脱硫工艺,特别在美国、德国和日本,应用该工艺的机组容量约占电站脱硫装机总容量的80%以上,应用的单机容量已达1000MW。
在国内已有珞璜电厂一、二期300MW机组及北京一热、重庆电厂和浙江半山电厂三个分别相当于300MW脱硫容量的机组使用。
引进技术国内脱硫工程公司总承包完成的北京石景山热电厂、太原第二热电厂五期、贵州安顺(300MW)电厂、广东台山电厂(600MW)、河北定州电厂(600MW)等也均已投入运行。
且国内有近20台600MW机组湿法脱硫正在实施中。
其基本原理与系统图如下:1.2 烟气循环流化床干法烟气循环流化床干法脱硫(CFB-FGD)技术是世界著名环保公司德国鲁奇·能捷斯·比肖夫(LLB)公司开发的世界先进水平的循环流化床干法烟气脱硫技术。
CFB-FGD是目前干法脱硫技术商业应用中单塔处理能力较大、脱硫综合效益较为优越的一种方法。
该工艺已经先后在德国、奥地利、波兰、捷克、美国、爱尔兰等国家得到广泛应用,最大已运行单机、单塔机组容量为300MW,采用该技术设计的单塔处理烟气量可达到2800000Nm3/h。
合成氨脱硫工艺比较精选全文完整版
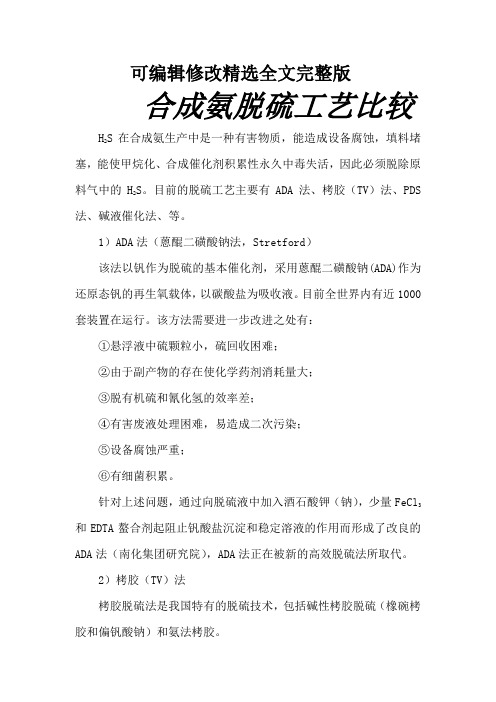
可编辑修改精选全文完整版合成氨脱硫工艺比较H2S在合成氨生产中是一种有害物质,能造成设备腐蚀,填料堵塞,能使甲烷化、合成催化剂积累性永久中毒失活,因此必须脱除原料气中的H2S。
目前的脱硫工艺主要有ADA法、栲胶(TV)法、PDS 法、碱液催化法、等。
1)ADA法(蒽醌二磺酸钠法,Stretford)该法以钒作为脱硫的基本催化剂,采用蒽醌二磺酸钠(ADA)作为还原态钒的再生氧载体,以碳酸盐为吸收液。
目前全世界内有近1000套装置在运行。
该方法需要进一步改进之处有:①悬浮液中硫颗粒小,硫回收困难;②由于副产物的存在使化学药剂消耗量大;③脱有机硫和氰化氢的效率差;④有害废液处理困难,易造成二次污染;⑤设备腐蚀严重;⑥有细菌积累。
针对上述问题,通过向脱硫液中加入酒石酸钾(钠),少量FeCl3和EDTA螯合剂起阻止钒酸盐沉淀和稳定溶液的作用而形成了改良的ADA法(南化集团研究院),ADA法正在被新的高效脱硫法所取代。
2)栲胶(TV)法栲胶脱硫法是我国特有的脱硫技术,包括碱性栲胶脱硫(橡碗栲胶和偏钒酸钠)和氨法栲胶。
栲胶脱硫主要是利用天然栲胶中存在的多羟基芳烃化合物所存在的酚式及醌式结构互变,再利用偏钒酸钠进行氧化还原来实现脱硫的。
其特点是资源丰富,价廉易得,运行费用比改良ADA法低,脱硫液腐蚀性小,脱硫效果较好,基本上无硫堵塔问题,但栲胶需熟化处理,脱硫废液存在钒污染。
3)PDS法PDS是东北师范大学开发的一种新型脱硫催化剂,活性物质为双核酞菁钴磺酸盐,同时加入助催化剂和碱性物质。
该法特点是:脱硫效率高,只需ppm浓度级的催化剂即可,无毒;生成得单质硫颗粒大,易分离;可脱除部分有机硫。
该方法不足之处是有时脱硫效率不太稳定,绝大部分时间需要复配其它成分一起使用。
4)碱液催化法碱液催化法脱硫工艺过程比较简单、技术成熟、成本较低,非常适合较小规模合成氨厂的煤气脱硫。
合成氨厂脱硫方法的工艺探讨 文档

年产35万吨合成氨厂脱硫工段的工艺设计学号2010231129 姓名石艳萍1.概述1.1引言氨是一种重要的化工产品,用途十分广泛。
合成氨是化学工业的基础,也是我国化学工业发展的重要先驱。
经过几十年的发展,我国合成氨工业在产业规模,技术水平等方面均得到了大幅提高。
目前,我国合成氨产业规模已居世界第一,总量占世界总量的三分之一。
合成氨作为化肥工业生产的重要基础,在我国国民经济中发挥着重要作用。
【1】我国合成氨工业能够满足氮肥工业生产需求,基本满足了农业生产需要。
合成氨的需求取决于氮肥的需求和工业用氮的需求,随着农业生产的不断发展,肥料需求的不断增加,合成氨工业对农业的作用实质是将空气中游离氮转化为能被植物吸收利用的化合态氮,这一过程称为固定氮。
我国合成氨产品主要分为农业用氮和工业用氮两大类,在农业方面,以氮为主要原料可以生产各种氮素肥料,如尿素、硝酸铵、碳酸氢铵、氯化铵、磷酸一铵、磷酸二铵、硝酸磷肥等各种含氮肥料。
工业方面主要用于生产硝酸、纯碱、等多种化工产品。
合成氨的工业的迅速发展,也促进了高压、催化、特殊金属材料、固体燃料气化、低温等科学技术的发展。
【2】合成氨工业在国民经济中占十分重要的地位,氨及氨加工工业已成为现代化学工业的一个重要部分。
(1.引自朝红梅:《我国合成氨工业进展评述》《化工工业》2010年第5期)(2.引自朝红梅:《我国合成氨产量分析》.《煤化工》第28卷第9期)1.2合成氨脱硫原理在合成氨工业中,脱硫技术是一个备受重视,随着优质原料煤供应的日益紧张,大多数以煤为原料合成氨厂不得不选用高硫无烟煤作为原料,生产出的半水煤气中H2S质量浓度在4—6g/m2甚至高达7—9 g/m2.脱硫技术问题成为公认难题。
合成氨所需的原料气,无论是天然气、油田气还是焦炉气、半水煤气都含有硫化物这些硫化物主要是硫化氢、二硫化碳、硫氧化碳、硫醇和噻吩等。
其中硫化氢属于无机化合物,称为“无机硫”天然气中硫经物的含量(标准状态)一般在0.5—15g/m2的范围内,有机硫以硫醇为主,在气田经过粗脱硫处理后的天然气,硫化物的含量(标准状态)在20—100mg/m3左右。
工艺|氨法脱硫工艺的那些事~

工艺|氨法脱硫工艺的那些事~氨法脱硫工艺是采用氨作为吸收剂除去烟气中的SO2的工艺,该工艺过程一般分成三大步骤:硫吸收、中间产品处理、副产品制造;根据过程和副产物的不同,又可分为氨-硫铵肥法、氨-磷铵肥法、氨-酸法、氨-亚硫酸铵法等;氨法脱硫对煤中硫含量的适应性广,低、中、高硫含量的煤种脱硫均能适应,特别适合于中高硫煤的脱硫。
采用石灰石/石膏法时,煤的含硫量越高,石灰石用量就越大,费用也就越高;而采用氨法时,特别是采用废氨水作为脱硫吸收剂时,由于脱硫副产物的价值较高,煤中含硫量越高,脱硫副产物硫酸铵的产量越大,也就越经济。
工艺流程氨法脱硫工艺主要由脱硫洗涤系统、浓缩系统、烟气系统、氨贮存系统、硫酸铵生产系统(若非氨-硫铵法则是于其工艺相对应的副产物制造系统)、电气自动控制系统等组成。
锅炉排出的烟气通过引风机增压后进入FGD系统,引风机用来克服整个FGD系统的压降。
烟道上设有挡板系统,以便于FGD系统正常运行或旁路运行,不考虑增设脱硫增压风机。
烟气通过引风机后,进入脱硫塔。
吸收塔分为三个区域:分别为吸收区、浆池区和除雾区,烟气向上通过脱硫塔,从脱硫塔内喷淋管组喷出的悬浮液滴向下降落,烟气与氨/硫酸铵浆液液滴逆流接触,发生传质与吸收反应,以脱除烟气中的SO2、SO3。
脱硫后的烟气经除雾器去除烟气中夹带的液滴后,从顶部离开脱硫塔,通过原烟道进入烟囱排放。
脱硫塔下部浆池中的氨/硫酸铵浆液由循环泵循环送至浆液喷雾系统的喷嘴,产生细小的液滴沿脱硫塔横截面均匀向下喷淋。
SO2和SO3与浆液中的氨反应,生成亚硫酸铵和硫酸铵。
在脱硫塔浆池中鼓入空气,将生成的亚硫酸铵氧化成硫酸铵,由于充分利用了烟气中的热量,使得脱硫塔中的水蒸气过饱和而析出硫酸铵结晶,硫酸铵浆液经过旋流器的脱水提浓厚再进入离心机进一步脱水,最后经干燥后得到硫酸铵产品。
反应过程烟气中的SO2从烟气主体进入吸收液的过程是物理吸收和化学反应的过程,通过这个过程,使SO2从气相进入液相而被捕获。
脱硫工艺比选

目前,国内外的天然气脱硫方法非常多,总的来说可分为间歇法、化学吸收法、物理吸收法、联合吸收法(化学―物理吸收法)、直接转化法,以及在80年代工业化的膜分离法等。
其中,采用溶液或溶剂作脱硫剂的脱硫方法习惯上又统称为湿法,采用固体作脱硫剂的脱硫方法又统称为干法。
2.3.1 物理吸收法这类方法又称为物理溶剂法。
它们采用有机化合物为吸收溶剂(物理溶剂),对天然气中的酸性组分进行物理吸收而将它们从气体中脱除。
在物理吸收过程中,溶剂的酸气负荷(即单位体积或每摩尔溶剂所吸收的酸性组分体积或摩尔量)与原料气中酸性组分的分压成正比。
吸收了酸性组分的富剂在压力降低时,随即放出所吸收的酸性组分。
物理吸收法一特般在高压和较低温度下进行,溶剂酸气负荷高,故适用于酸性组分分压高的天然气脱硫。
2.3.2 化学吸收法这类方法又称化学溶剂法。
它以碱性溶液为吸收溶剂(化学溶剂),与天然气中的酸性组分(主要是H2S和CO2)反应生成某种化合物。
吸收了酸性组分的富液在温度升高、压力降低时,该化合物又能分解释放出酸性组分。
这类方法中最有代表性的是醇胺(烷醇胺)法和碱性盐溶液法。
属于前者的有一乙醇胺(MEA)法、二乙醇胺(DEA)法、二甘醇胺(DGA)法、二异丙醇胺(DIPA)法、甲基二乙醇胺(MDEA)法,以及一些有专利权的方法如胺防护(Amine Guard)法、Flexsorb 法和Gas/Spec法等。
醇胺法是最常用的天然气脱硫方法。
2.3.3 联合吸收法联合吸收法兼有化学吸收和物理吸收两类方法的特点,使用的溶剂是醇胺、物理溶剂和水的混合物,故又称为混合溶液法或化学-物理吸收法。
目前,常用的联合吸收法有:①萨菲诺(Sulfinol)法,吸收溶剂为环丁砜(二氧化四氢噻吩)和DIPA的水溶液(Sulfinol—D法)或环丁砜和MDEA的水溶液(Sulfinol-M 法),习惯称为砜胺法;②Optisol法,吸收溶剂由醇胺、有机溶剂和水组成。
氨法脱硫技术论文

氨法脱硫技术论文氨法脱硫法是一种在化学工业领域应用普遍的技术。
这是店铺为大家整理的氨法脱硫技术论文,仅供参考!浅议烟气氨法脱硫技术篇一摘要:氨法脱硫技术是一种新的烟气脱硫技术,属于环保装置。
本文首先介绍了国内外烟气脱硫脱硫工艺各种技术的特点,对几种湿法脱硫工艺进行了对比分析,最后对氨法脱硫技术做了重点阐述和详细的说明。
关键字:烟气脱硫;氨法脱硫;二氧化硫;氨水我国是世界产煤和燃煤大国,燃煤排放的二氧化硫也不断增加,连续多年超过2000万吨,已居世界首位,致使我国酸雨和二氧化硫污染日趋严重。
国家把解决烟气脱硫问题纳入国家大计之中,强制要求火电厂必须安装烟气脱硫装置。
根据GB13223-2011,目前SO2排放限制为100mg/m3。
氨法脱硫技术是以氨作为吸收剂脱除烟气中的SO2,达到化害为利、变废为宝。
1.湿法烟气脱硫技术概述吸收法是净化烟气中SO2的最重要的、应用最广泛的方法。
吸收法通常指用液体吸收净化烟气中的SO2 ,因此吸收法烟气脱硫也称为湿法烟气脱硫。
按脱硫剂的种类划分为:以CaCO3(石灰石)为基础的钙法、以NH3为基础的氨法、以MgO为基础的镁法、以NaCO3为基础的钠法。
(1)MgO法锅炉烟气由引风机送入吸收塔预冷段,冷却至适合的温度后进入吸收塔,往上与逆向流下的吸收浆液反应,脱去烟气中的硫份。
净烟气经过除雾器降低烟气中的水分后排入烟囱。
粉尘与脏东西附着在除雾器上,会导致除雾器堵塞、系统压损增大,需由除雾器冲洗水泵提供工业水对除雾器进行喷雾清洗。
主要缺点是副产品销售没有形成规模,没有良好的销售渠道,并且对烟气的杂质要求很高。
(2)NaCO3法本法是用NaOH、Na2CO3和Na2SO3的水溶液为吸收剂,吸收烟气中的SO2。
此法实际上是采用Na2CO3和NaHSO3混合液为吸收剂。
当吸收剂中NaHSO3浓度达到80%-90%时,就要对吸收剂进行再生,可获得较高浓度的SO2和Na2CO3。
3学习情境三合成氨原料气的净化

学习情境三合成氨工作任务合成氨原料气的脱硫授课地点多媒体教室3-8教学方法讲授法课时 4任务描述及任务目标掌握干法脱硫、氨水催化法脱硫及两生过程的基本原理、主要设备和工艺条件的选择包含章节第三章第三节主要教具、设备、工具多媒体学习重点及难点脱硫方法的选择与对比碱法脱硫的原理及工艺指标的确定学生学习基础已具有无机化学,化工单元操作,物理化学,化工热力学等的学习基础,具有一定的自学能力,接受知识的能力也较强.知识点:第一节原料气的脱硫脱硫方法很多,主要可分为干法脱硫和湿法脱硫。
干法脱硫一般适用于含S量较少的情况。
湿法脱硫一般适用于含S量较大的场合。
一、干法脱硫(一)钴-钼加氢法钴钼加氢法还可将烯烃加氢转变成饱和烷烃,从而减少蒸汽转化工序析碳的可能。
钴钼加氢催化剂以氧化铝为载体,由氧化钴和氧化钼组成。
经硫化后活性组分为MoS2,Co9S8也是活性成份。
主要反应如下:RCH2SH+H2=RCH3 + H2SRCH2-S-CH2R´+2H2=RCH3 + R´CH3 +H2SRCH2S-SCH2R´+3H2=RCH3 + R´CH3 +2H2S操作温度一般在300 ~ 400°C,压力由不同催化剂而定,加氢量一般按照保持反应后气体中有5~10%氢为准。
(二)氧化锌法氧化锌脱除有机硫的能力很强,可使出口硫含量<0.1ppm,当原料气硫含量<50×10-6时,仅用它一步脱硫就行了。
若硫含量较高,可先用湿法,再用此法。
其基本原理如下:ZnO(s)+H2S(g)=ZnS(s)+H2O(g)ZnO(s)+C2H5SH(g)=ZnS(s)+C2H5OH(g)氧化锌脱硫的反应速度主要是内扩散控制,所以氧化锌脱硫剂都做成高孔率的小颗粒。
氧化锌脱硫性能的好坏用硫容量表示。
所谓硫容就是每单位质量氧化锌能脱除S的量。
氧化锌脱硫性能的好坏用硫容量表示。
所谓硫容就是每单位质量氧化锌能脱除S的量二、湿法脱硫湿法脱硫可分为化学吸收法、物理吸收法和化学物理综合吸收法等。
合成氨生产中硫化物净化工艺设备选择研究

合成氨生产中硫化物净化工艺设备选择研究摘要:通过分析硫化物的存在形式、工艺设备条件的选择和小氮肥企业脱硫工艺状况,论述了合成氨工艺中硫化物净化的影响因素和操作中注意的问题。
关键词:合成氨硫化物脱除设备选型煤是复杂的高分子有机化合物,主要由碳、氢、氧、氮、硫和磷等元素组成,而碳、氢、氧三者约占有机质95%以上;煤中无机质也含有少量碳、氢、氧、硫等元素。
煤中硫又分为有机硫和无机硫两大类。
一、工艺设备条件的选择以块煤为原料的化工企业,原料气中硫化氢的脱除方法主要有:吸收、吸附、化学转化。
针对硫化氢的腐蚀机理,在合成氨生产设备要充分考虑腐蚀,半水煤气脱硫一般是对设备进行内部环氧树脂防腐处理。
变换气脱硫设备一般采用复合板,运转设备泵的运转部件一般采用不锈钢材质。
二、小氮肥企业脱硫工艺状况1.半水煤气湿法脱硫一般的工艺路线为半水煤气由气柜经洗气塔、静电除焦、罗茨风机和降温塔后,进入脱硫塔,在脱硫塔中与脱硫液逆流接触,气体中的无机硫和部分有机硫被溶液吸收后,进入分离器和清洗冷却器,冷却分离后的气体进入静电除焦器后进入气体压缩机。
脱硫泵从贫液槽抽取“贫液”进入塔内,吸收后的“富液”进入富液槽经泵加压后送入再生槽,经喷射器吸收空气氧化再生后,硫以泡沫的形式从再生槽中浮选出来,“富液”转化为“贫液”,“贫液”经液位调节器进入贫液槽,如此循环使用。
目前脱硫塔根据硫化氢的含量和气体气量选择单塔和双塔。
双塔工艺中第一脱硫塔一般采用空塔喷淋,第二塔采用填料塔。
2.有机硫转化根据煤质的情况有的煤含有机硫含量较高,有机硫吸附主要靠吸附剂来吸收,运行费用高。
现在合成氨企业一般在变换工段增加水解塔,利用工段的热量使气体中的90%的有机硫转化成无机硫,无机硫在变换气脱硫中脱出。
3.变换气脱硫变换气脱硫各企业根据自身的条件选择不同的操作压力。
一般的工艺为:来自变换工段的气体进入脱硫塔,在脱硫塔填料层上与脱硫液逆流接触,气体中的h2s被溶液吸收后进入分离器,分离后气体进入后工段。
合成氨生产工艺脱硫

第七章脱硫工段第一节工艺流程及主要设备一、本工段任务从造气工段来的半水煤气中,除氢和氮外,还含有27%左右的CO,8%左右的C02,以及少量的硫化物和氧等。
硫化物(主在是仏5,约占半水煤气中硫总量的90%左右,其次还有CS2,COS和RSH等)含量约为1.0〜4.Og/Nm3。
这些硫化物对合成氨生产是有害的。
它会腐蚀设备、管道;会引起变换、合成、甲醇等工段触媒中毒、降低活性或失去活性;会破坏铜液成份。
H2S与铜液中的Cu2+和CU+作用生成CuS和Cu2S沉淀,堵塞设备管道与阀门,使精炼操作条件恶化。
生产过程中,h2s从溶液中解吸出来,或从设备管道中泄漏出来,会污染环境,影响人体健康。
本工段的主要任务,就是用脱硫液将半水煤气中的硫化物脱除至0.07g/Nr^以下,使半水煤气得到净化,以满足后工段生产工艺的要求。
吸收硫化氢的脱硫液经再生后循环使用,再生析出的硫回收成硫磺。
本工段要根据全厂生产情况,调节罗茨风机气垴。
脱硫的方法很多,根据脱硫剂的形态可分为湿法和干法两大类。
干法以固体为吸收剂,如活性碳法、分子筛法等。
湿法以液体为吸收剂,如氨水液相催化法、氨水中和法、ADA法,近年来还发展了拷胶法、PDS 法等。
B前,小氮肥厂脱硫采用较多的是氨水液相催化法。
现以本法为例,简述脱硫过程。
二、工艺流程简述氨水液相催化法脱硫是用脱硫液(贫液)吸收半水煤气中的硫化氢。
吸收硫化氢后的脱硫液(富液),在对苯二酚载氧体的催化作用下,经氧化再生后循环使用。
再生析出的硫泡沫经分离,熔融精制成硫锭。
主要反应方程式如下:NH4OH+H2S==MH4HS+H2O(脱硫反应)2NH4OH+CO2==(NH4)2CO3+H2O2NH4HS+Oz==2NH4OH+2S| (再生反应)2NH4HS+202=(NH4)2S203+H20来自造气工段的半水煤气,经除尘器除去所含的部份粉尘,煤焦油等杂质后,由罗茨鼓风机增压送入气体冷却器冷却,然后在喷旋脱硫塔的喷射器中与贫液并流接触而下,从喷旋塔底部进入,在旋流板中气液转为逆流接触,半水煤气中的硫化氢被贫液吸收。
合成氨脱硫工艺设计

合成氨脱硫工艺设计
1.工艺原理
合成氨脱硫使用了一种称为氧化剂的物质,通常是氧气和氯气的混合物,加之于废气中。
氧化剂与硫化物反应生成硫酸盐。
该反应需要一定的温度和压力条件下才能进行。
通常情况下,反应温度为120-200摄氏度,压力为1-3兆帕。
2.工艺流程
在吸收器中,还需要添加一种促进剂,以提高硫酸盐的转化率。
常用的促进剂包括硫酸铵和硝酸铵。
这些促进剂能增加硫酸盐的反应速率,并且防止硫酸盐结晶。
硫酸盐溶液在吸收废气中的过程中,会逐渐饱和。
当饱和度达到一定的程度时,需要对硫酸盐溶液进行再生。
再生通常通过加热溶液,释放出硫化物,并将其氧化成硫化氢。
然后将硫化氢处理成为硫酸盐。
3.设备设计
在工艺设计中,需要考虑各个设备的容量和尺寸,以满足处理废气的要求。
此外,还需考虑设备的材料选择,以保证其在高温、高压、腐蚀等恶劣条件下的使用寿命。
4.运行与控制
合成氨脱硫工艺需要建立一个完善的运行与控制系统,以保证整个工艺的稳定和高效运行。
应根据实际情况采用合适的控制策略,监测和调节各个参数,如废气流量、温度、压力、硫酸盐浓度等。
此外,还需建立一个规范的维护和保养计划,定期检查设备的状况,及时进行修复和更换。
总之,合成氨脱硫工艺设计需要考虑多个方面,包括工艺原理、工艺流程、设备设计和运行控制。
通过科学合理的设计和操作,可以有效降低硫化物的排放,减少环境污染。
氨法脱硫工艺介绍

氨法脱硫工艺介绍由于氨法脱硫工艺自身的一些特点,可充分利用我国广泛的氨源生产需求大的肥料,并且氨法脱硫工艺在脱硫的同时又可脱氮,是一项较适应中国国情的脱硫技术。
为帮助大家全面了解氨法,本文对氨法脱硫技术的发展、机理和不同技术的特点进行简述,并侧重介绍湿式回收法氨法脱硫技术。
1 氨法脱硫技术概况1.1氨法脱硫工艺特点氨法脱硫工艺是采用氨作为吸收剂除去烟气中的SO2的工艺。
氨法脱硫工艺具有很多特点。
氨是一种良好的碱性吸收剂,氨的碱性强于钙基吸收剂;而且氨吸收烟气中SO2是气-液或气-气反应,反应速度快、反应完全、吸收剂利用率高,可以做到很高的脱硫效率,相对于钙基脱硫工艺来说系统简单、设备体积小、能耗低。
另外,其脱硫副产品硫酸铵是一种常用的化肥,副产品的销售收入能大幅度降低运行成本。
1.2 氨法脱硫的发展70年代初,日本与意大利等国开始研制氨法脱硫工艺并相继获得成功。
氨法脱硫工艺主体部分属化肥工业范筹,这对电力企业而言较陌生,是氨法脱硫技术未得到广泛应用的最大因素,随着合成氨工业的不断发展以及厂家对氨法脱硫工艺自身的不断完善和改进,进入90年代后,氨法脱硫工艺渐渐得到了应用。
国外研究氨法脱硫技术的企业主要有:美国:GE、Marsulex、Pircon、Ba bcock & Wilcox;德国:Lentjes Bischoff、Krupp Koppers;日本:NKK、IHI、千代田、住友、三菱、荏原;等等。
国内目前成功的湿式氨法脱硫装置大多从硫酸尾气治理技术中发展而来,主要的技术商有江南环保工程建设有限公司、华东理工大学等,现国内湿式氨法脱硫最大的业绩是天津永利电力公司的60MW机组的烟气脱硫装置。
近来出现的磷铵法、电子束法、脉冲电晕放电等离子体法等烟气脱硫脱硝技术皆是氨法的演变与发展,改进之处在于降低水耗、改进氧化及后处理、降低装置压降、提高脱硝能力等方面,以求使氨法烟气脱硫技术更加经济更加适应锅炉的运行。
合成氨粗原料气的脱硫工艺概述

Hefei University题目:合成氨粗原料气的脱硫工艺综述系别:化学材料与工程系班级:12化工(2)姓名:学号:教师:朱德春合成氨粗原料气的脱硫工艺【摘要】合成氨原料气中的硫是以不同形式的硫化物存在的,其中大部分是以硫化氢形式存在的无机硫化物,还有少量的有机硫化物。
具体来说作为原料气的半水煤气中都含有一定数量的硫化氢和有机硫化物(主要有羰基硫、二硫化碳、硫醇、硫醚等),能导致甲醇、合成氨生产中催化剂中毒,增加液态溶剂的黏度,腐蚀、堵塞设备和管道,影响产品质量。
硫化物对合成氨的生产是十分有害的,燃烧物和工业装置排放的气体进入大气,造成环境污染,危害人体健康。
硫也是工业生产的一种重要原料。
因此为了保持人们优良的生存环境和提高企业最终产品质量,对半水煤气进行脱硫回收是非常必要的。
【关键词】脱硫;钴钼加氢法;改良ADA法【Abstract】ammonia synthesis feed gas sulfur is present in different forms sulfides, most of which is present in the form of inorganic sulfur compounds hydrogen sulfide, a small amount of organic sulfides. Specifically, as the raw material gas semi-water gas contain a certain amount of hydrogen sulfide and organic sulfides (mainly carbonyl sulfide, carbon disulfide, mercaptans, sulfides, etc.) can lead to methanol, ammonia synthesis catalyst poisoning, increasing the liquid solvent viscosity, corrosion, plugging equipment and pipelines, affecting product quality. Sulfide production of ammonia is very harmful, gas combustion and industrial installations emissions into the atmosphere, causing environmental pollution and endanger human health. Sulfur is also an important raw material for industrial production. So in order to keep good people and improve the living environment of the final product quality, semi-water gas desulfurization recovery is necessary.【Keywords】desulfurization; cobalt-molybdenum hydrogenation; modified ADA 【前言】固体燃料为原料所制得的粗原料气,经除尘后,含有一定量的硫化物、CO、CO2,这些都是氨合成催化剂的毒物,必须除去;而以液态烃、气态烃为原料制合成气,因原料中含有一定量的硫化物,在蒸气转化反应前就必须先行除去,否则会引起镍催化剂中毒。
合成氨脱硫工段工艺设计
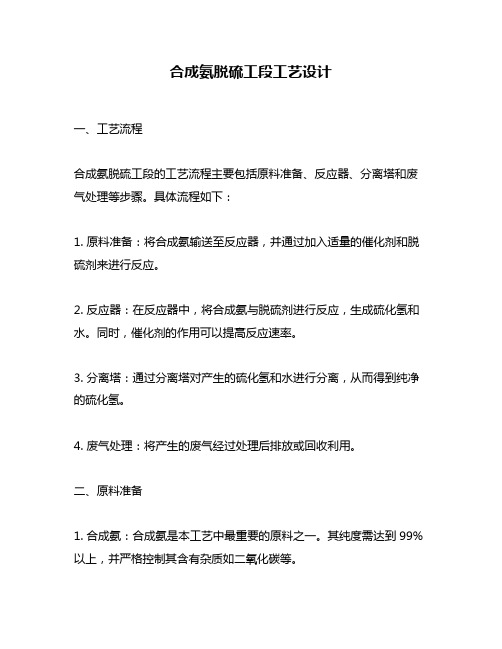
合成氨脱硫工段工艺设计一、工艺流程合成氨脱硫工段的工艺流程主要包括原料准备、反应器、分离塔和废气处理等步骤。
具体流程如下:1. 原料准备:将合成氨输送至反应器,并通过加入适量的催化剂和脱硫剂来进行反应。
2. 反应器:在反应器中,将合成氨与脱硫剂进行反应,生成硫化氢和水。
同时,催化剂的作用可以提高反应速率。
3. 分离塔:通过分离塔对产生的硫化氢和水进行分离,从而得到纯净的硫化氢。
4. 废气处理:将产生的废气经过处理后排放或回收利用。
二、原料准备1. 合成氨:合成氨是本工艺中最重要的原料之一。
其纯度需达到99%以上,并严格控制其含有杂质如二氧化碳等。
2. 催化剂:催化剂是本工艺中必不可少的组成部分。
常用的催化剂包括铝酸盐、钼酸盐等。
其作用是加速反应速率,提高产物纯度。
3. 脱硫剂:脱硫剂是用于吸收反应中生成的硫化氢的物质。
常用的脱硫剂包括三乙醇胺、二乙醇胺等。
三、反应器1. 反应器设计:反应器主要由反应釜、搅拌器、加热系统和控制系统等部分组成。
反应釜材质一般为不锈钢或碳钢,且内壁需进行防腐处理。
2. 反应条件:合成氨脱硫反应需要在一定的温度和压力下进行。
通常情况下,温度控制在150℃-250℃之间,压力控制在1MPa-3MPa之间。
四、分离塔1. 分离塔设计:分离塔主要由进料口、出料口、填料层和塔板层等部分组成。
填料层材质一般为陶瓷或金属,其作用是增加接触面积,提高分离效率。
2. 分离条件:分离塔需要在一定的温度和压力下进行。
通常情况下,温度控制在50℃-100℃之间,压力控制在0.1MPa-0.5MPa之间。
五、废气处理1. 废气处理方法:废气处理一般采用吸收法或燃烧法。
吸收法是将废气通过吸收剂中,使其中的有害物质被吸收,从而达到净化的目的。
燃烧法则是将废气进行高温燃烧,使其中的有害物质被分解,从而达到净化的目的。
2. 废气处理设备:废气处理设备包括吸收器、除尘器、脱臭器和排放管道等部分。
其中,吸收器和脱臭器材质一般为玻璃钢或不锈钢。
合成氨生产工艺脱硫
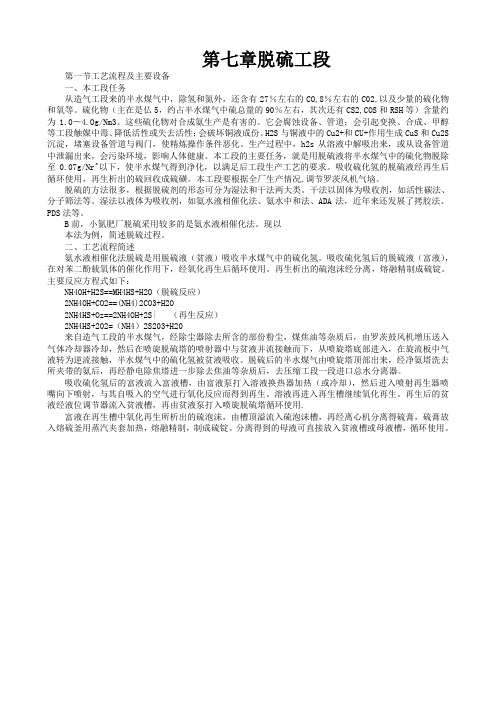
第七章脱硫工段第一节工艺流程及主要设备一、本工段任务从造气工段来的半水煤气中,除氢和氮外,还含有27%左右的CO,8%左右的C02,以及少量的硫化物和氧等。
硫化物(主在是仏5,约占半水煤气中硫总量的90%左右,其次还有CS2,COS和RSH等)含量约为1.0〜4.Og/Nm3。
这些硫化物对合成氨生产是有害的。
它会腐蚀设备、管道;会引起变换、合成、甲醇等工段触媒中毒、降低活性或失去活性;会破坏铜液成份。
H2S与铜液中的Cu2+和CU+作用生成CuS和Cu2S 沉淀,堵塞设备管道与阀门,使精炼操作条件恶化。
生产过程中,h2s从溶液中解吸出来,或从设备管道中泄漏出来,会污染环境,影响人体健康。
本工段的主要任务,就是用脱硫液将半水煤气中的硫化物脱除至0.07g/Nr^以下,使半水煤气得到净化,以满足后工段生产工艺的要求。
吸收硫化氢的脱硫液经再生后循环使用,再生析出的硫回收成硫磺。
本工段要根据全厂生产情况,调节罗茨风机气垴。
脱硫的方法很多,根据脱硫剂的形态可分为湿法和干法两大类。
干法以固体为吸收剂,如活性碳法、分子筛法等。
湿法以液体为吸收剂,如氨水液相催化法、氨水中和法、ADA法,近年来还发展了拷胶法、PDS法等。
B前,小氮肥厂脱硫采用较多的是氨水液相催化法。
现以本法为例,简述脱硫过程。
二、工艺流程简述氨水液相催化法脱硫是用脱硫液(贫液)吸收半水煤气中的硫化氢。
吸收硫化氢后的脱硫液(富液),在对苯二酚载氧体的催化作用下,经氧化再生后循环使用。
再生析出的硫泡沫经分离,熔融精制成硫锭。
主要反应方程式如下:NH4OH+H2S==MH4HS+H2O(脱硫反应)2NH4OH+CO2==(NH4)2CO3+H2O2NH4HS+Oz==2NH4OH+2S| (再生反应)2NH4HS+202=(NH4)2S203+H20来自造气工段的半水煤气,经除尘器除去所含的部份粉尘,煤焦油等杂质后,由罗茨鼓风机增压送入气体冷却器冷却,然后在喷旋脱硫塔的喷射器中与贫液并流接触而下,从喷旋塔底部进入,在旋流板中气液转为逆流接触,半水煤气中的硫化氢被贫液吸收。
脱硫技术、效率分析、工艺选择+湿法脱硫6个最优运行措施及方法

脱硫技术、效率分析.工艺选择一.焦炉煤宅脱硫效率分析及工艺选择煤气中的硫来自原料煤中,存在形式主要是H2S,亦有少量有机硫(主要是COS)oH2S不仅会造成环境的污染,还会腐蚀设备,使催化剂中毒,对生产造成很多不良影响,所以必须要脱去煤气中的硫。
煤气脱硫即采用一定的技术手段将H2S、HCN等有害物质从焦炉煤气中脱除,采用的工艺方法一般分为湿法脱硫和干法脱硫。
焦炉煤气常用的脱硫方法从脱硫剂的形态上来分:包括•干法脱硫技术和湿法脱硫技术。
2.1焦炉煤气干法脱硫技术干法脱硫工艺是利用固体吸收剂脱除煤气中的硫化氢,同时脱除氤化物及焦油雾等朵质。
干法脱硫又分为中温脱硫、低温脱硫和高温脱硫。
常用脱硫剂有铁系和锌系,氧化铁脱硫剂是一种传统的气体净化材料,适宜于对天然气、油气伴生气、城市煤气以及废气中硫化氢含量高的气体。
常温氧化铁脱硫原理是用水合氧化铁(Fe203・H20)脱除H2S,其反应包括脱硫反应与再生反应。
干法脱硫工艺多采用固定床原理,工艺简单,净化率高,操作简单可靠,脱硫精度高,但处理量小,适用于低含硫气体的处理,一般多用于二次精脱硫。
但由于气固吸附反应速度较慢,工艺运行所需设备一般比较庞大,而且脱硫剂不易再生,运行费用增高,劳动强度大,不能回收成品硫,废脱硫剂、废气、废水严重污染环境。
2.2焦炉煤气湿法脱硫技术湿法工艺是利用液体脱硫剂脱除煤气中的硫化氢和氤化氢。
常用的方法有氨水法、单乙醇胺法、碑碱法、VASC脱硫法、改良ADA 法、TH法、苦味酸法、对苯二酚法、HPF法以及一些新兴的工艺方法等。
2.2. 1 氨水法(AS法):氨水法脱硫是利用焦炉煤气中的氨,在脱硫塔顶喷洒氨水溶液(利用洗氨溶液)吸收煤气中H2S,富含H2S和NH3的液体经脱酸蒸氨后再循环洗氨脱硫。
在脱硫塔内发生的氨水与硫化氢的反应是:H2S+2NH3・H20-(\H4)2S+2H20。
AS循环脱硫工艺为粗脱硫,操作费用低,脱硫效率在90 %以上,脱硫后煤气中的H2S在200〜500 mg・m-3。
合成氨的湿法脱硫

改良ADA法脱硫工艺液脱除硫化氢。 栲胶法脱硫无需添加酒石酸钾钠等配位剂。
缺 1、净化度低 2、设备腐蚀 3、运转设备多,
点 电耗高
吸收的基本原理与吸收剂的选择
硫化氢是酸性气体,其水溶液呈酸性,可被碱性溶液吸收:
相平衡
解离
碱性吸收剂只能将原料气中的硫化氢吸收到溶液中,不能使硫化氢氧化为单质硫。 需借助其他物质来实现。 在溶液中添加催化剂作为载氧体,氧化态的催化剂将硫化氢氧化成为单质硫,其 自身呈还原态。还原态催化剂在再生时被空气中的氧氧化后恢复氧化能力,循环使 用。
4 0
3 0
2 0
81.3
8.5
8.7
0
PH值
0
2. 0
1. 5
1. 0 61052. 7
0
8 9 10 11 PH值
② 钒酸盐含量 应使ADA与偏钒酸盐的当量比为2左右。 ③ ADA用量 ADA作用是将V4+氧化为V5+,为了加快V4+的氧化速率,一般 使用5~10g/L。 ④ 酒石酸钠钾用量 与钒浓度成正比,为偏钒酸钠浓度的0.5倍。
能脱除硫化氢、二氧化碳,当与 有机硫反应时会使溶剂降解,不能 两再生
能脱除硫化氢、二氧化碳,与有 机硫反应慢,再生时可分解,回收 胺
能脱硫化氢、有机硫
主要脱二氧化碳兼脱 硫化氢
能脱硫化氢、有 机硫与二氧化碳
脱硫化氢,副产硫磺
同上
同上
能脱硫化氢和一部分有 机硫
适用 情况
适用于天然气
脱硫剂脱硫方案
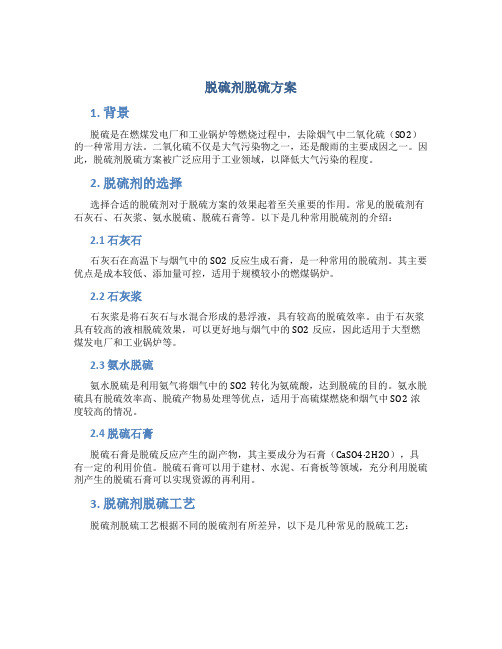
脱硫剂脱硫方案1. 背景脱硫是在燃煤发电厂和工业锅炉等燃烧过程中,去除烟气中二氧化硫(SO2)的一种常用方法。
二氧化硫不仅是大气污染物之一,还是酸雨的主要成因之一。
因此,脱硫剂脱硫方案被广泛应用于工业领域,以降低大气污染的程度。
2. 脱硫剂的选择选择合适的脱硫剂对于脱硫方案的效果起着至关重要的作用。
常见的脱硫剂有石灰石、石灰浆、氨水脱硫、脱硫石膏等。
以下是几种常用脱硫剂的介绍:2.1 石灰石石灰石在高温下与烟气中的SO2反应生成石膏,是一种常用的脱硫剂。
其主要优点是成本较低、添加量可控,适用于规模较小的燃煤锅炉。
2.2 石灰浆石灰浆是将石灰石与水混合形成的悬浮液,具有较高的脱硫效率。
由于石灰浆具有较高的液相脱硫效果,可以更好地与烟气中的SO2反应,因此适用于大型燃煤发电厂和工业锅炉等。
2.3 氨水脱硫氨水脱硫是利用氨气将烟气中的SO2转化为氨硫酸,达到脱硫的目的。
氨水脱硫具有脱硫效率高、脱硫产物易处理等优点,适用于高硫煤燃烧和烟气中SO2浓度较高的情况。
2.4 脱硫石膏脱硫石膏是脱硫反应产生的副产物,其主要成分为石膏(CaSO4·2H2O),具有一定的利用价值。
脱硫石膏可以用于建材、水泥、石膏板等领域,充分利用脱硫剂产生的脱硫石膏可以实现资源的再利用。
3. 脱硫剂脱硫工艺脱硫剂脱硫工艺根据不同的脱硫剂有所差异,以下是几种常见的脱硫工艺:3.1 干法脱硫工艺干法脱硫工艺是指将脱硫剂喷入烟气中,与SO2发生反应形成脱硫产物。
这种工艺适用于SO2浓度较低的情况,通常结合电除尘等工艺一起使用,以达到更好的脱硫效果。
3.2 湿法脱硫工艺湿法脱硫工艺是指将脱硫剂与烟气充分接触并发生化学反应。
这种工艺适用于SO2浓度较高的情况,脱硫效率较高。
湿法脱硫工艺可以分为石灰浆湿法脱硫、氨水湿法脱硫等。
3.3 半干法脱硫工艺半干法脱硫工艺是湿法脱硫与干法脱硫的结合,通过调整工艺条件,既保证了高脱硫效率,又降低了脱硫剂的消耗和除尘装置的负担。
- 1、下载文档前请自行甄别文档内容的完整性,平台不提供额外的编辑、内容补充、找答案等附加服务。
- 2、"仅部分预览"的文档,不可在线预览部分如存在完整性等问题,可反馈申请退款(可完整预览的文档不适用该条件!)。
- 3、如文档侵犯您的权益,请联系客服反馈,我们会尽快为您处理(人工客服工作时间:9:00-18:30)。
合成氨(联醇)厂干法脱硫工艺优化与脱硫剂经济选择苗茂谦郭汉贤上官炬王怀俊陈志勇(太原理工大学煤化所)(山西科灵催化净化技术发展公司太原030024)众所周知,传统意义的小化肥厂已不存在。
以煤为原料采用的合成氨厂净化过程一般都使用一种或数种干法脱硫剂。
干法脱硫的工艺优化和脱硫剂的经济选择是项重要内容。
随着合成氨厂生产规模的不断扩大和技术进步的不断提升,伴随着干法脱硫工艺的发展和脱硫剂性能的提高,干法脱硫工艺和脱硫剂选择已不仅仅是一个价格层面上的事情,而是涉及生产过程净化指标能否长时间达标,装置能否长期安全、稳定运行,进而影响企业经济效益的重大问题。
化肥生产中合成气采用“湿法+干法脱硫”,主要是为防止合成催化剂中毒。
干法脱硫剂及脱硫工艺要按照气体中硫形态、硫负荷、气氛及净化度要求来优化选择。
以下分别就合成氨(联醇)厂通常使用的干法脱硫工艺和脱硫剂使用情况进行分析比较。
1 变换气湿法脱硫后的干法脱硫工艺和脱硫剂选择变换气湿法脱硫后一般仍含有5.0-20 mg/m3(有的甚至更高)的H2S,并含有一定量的有机硫。
基于保护脱碳溶液或为降低CO2气体中H2S含量的考虑,许多厂都在变换气湿法脱硫后选用干法脱硫工艺。
一般情况下,变换气湿法脱硫后对干法脱硫要求的精度不是很高,能满足脱碳要求即可。
因此,通常选用单一的脱硫剂品种脱除大部分的H2S。
在流程安排上,如果硫化物含量较高,最好选择两开一备、并可交替倒塔串联的流程;如果硫化物含量较低,也可选择单塔流程。
脱硫剂型号的选择十分重要。
过去人们大都由于其脱硫要求的精度不高而选择使用普通的活性炭脱硫剂,也有一些厂家选择使用普通氧化铁脱硫剂。
事实上,变换气中脱除H2S基本上可以达到工艺要求。
但是,几乎所有的人都忽略了一种现象所引起的负面作用。
就是许多工厂在使用普通活性炭或氧化铁脱硫剂后,脱硫塔出口H2S含量虽然合格,但COS含量却明显增加,有的厂甚至有90%以上的H2S转化为COS。
这种现象在脱硫剂使用的后期尤为明显。
变换气干法脱硫后有机硫含量增加,直接导致脱碳后净化气和解吸气(CO2 )中有机硫增长,不仅增加了后工序脱硫的负荷,而且大大增加了后工序脱硫的难度和经济代价。
因为脱除有机硫难度远比脱除无机硫困难的多。
这种做法不仅为自己制造了不必要的麻烦,而且导致脱硫总费用的增加。
河北某厂变换气脱硫采用湿法串干法活性炭。
气体从活性炭脱硫塔出来到脱碳工序。
通常活性炭进口的H2S在10 mg /m3左右,COS在2.0~3.0 mg/m3之间。
但脱碳后解吸的CO2 气体中COS却高达2O~50 mg/m3,以至于尿素系统因硫含量居高不下而无法正常运行,这个数据明显不符合常理。
后经过我们检测,发现虽然活性炭脱硫塔出口H2S≤2.0 mg/m3 ,但是COS含量高达6.0~13.0 mg/m3。
在更换了山西科灵公司的TGC-3型活性炭脱硫剂后,活性炭脱硫塔出口H2S ≤1.0 mg/m3,COS在0.3~2.0 mg/m3之间,解吸的CO2 气中COS初期只有1.0 mg/m3以下,使用一年后仍在2.0~5.0 mg/m3之间,达到了尿素原料气的要求。
而原来使用的普通活性炭脱硫剂一般只能勉强维持3个月左右时间。
2 碳化尾气干法脱硫工艺和脱硫剂选择以碳铵(联醇)为产品的合成氨厂,碳化尾气中H2S含量一般在0~30 mg/m3以下。
为减轻精炼或精脱硫负荷,一般也都会选用某种干法脱硫剂对气体中的H2S进行预脱除。
碳铵厂生产规模都较小,预脱硫一般选用单塔流程即可。
预脱硫选用的脱硫剂与变换气湿法脱硫后的干法脱硫相类似,碳化气的精脱硫将在后面讨论。
3 脱碳净化气精脱硫工艺和脱硫剂选择以尿素(联醇)或液氨(联醇)为产品的企业,脱碳净化气中一般含有2.0 mg/m3以下的硫化物。
为满足联醇生产和后工序对总硫的要求,大都配有精脱硫装置,要求精脱硫后总硫达到0.10 mg/m3甚至0.05 mg/m3以下。
以前选用的精脱硫流程大多为“夹心饼”工艺,即:精脱H2S→加热→有机硫水解→冷却→精脱H2S。
在精脱硫技术最初的发展阶段,该工艺的确收到了很好的效果。
但是,该工艺的缺点是流程较长、脱硫剂装填量大、需要增设换热和冷却设备、能量利用不尽合理、操作比较繁琐,当原料中含有CS2和噻吩等硫化物时净化不彻底。
还有的企业在常温精脱硫工艺中选用了“水解催化剂 + 常温氧化锌脱硫剂”的流程。
该工艺从技术角度看是合理的,也是成熟的。
但是常温精脱硫技术发展到今天,已有性价比高的脱硫剂产品取而代之,用常温氧化锌脱硫,性价比不合理,经济上不可取。
如前所述,凡使用常温水解催化剂的地方必须要有换热和冷却设备,而氧化锌脱硫剂在常温条件下硫容量较低,对有机硫的脱除难以起到把关作用,而且其价格十分昂贵。
随着精脱硫技术的进步,目前可供尿素(联醇)或液氨(联醇)企业选择的、简便可靠的精脱硫工艺有以下几种。
3.1 CLEAN(科灵)两步法工艺该工艺为两塔串联流程,分别高精度脱除H2S和各种有机硫。
精脱硫出口各种形态硫可分别小于0.03 mg/m3,总硫≤ 0.10 mg/m3,同时可脱除少量的氯化物。
该工艺适用于与MDEA、PC、NHD和热钾碱法脱碳配套的精脱硫过程,也适用于碳铵(联醇)企业碳化气预脱硫后的精脱硫过程。
山西科灵公司开发的TGC系列活性炭脱硫剂在出口H2S≤0.03 mg /m3时,对H2S的工作硫容可达到15.O %~ 20.O%(质量分数,下同),TZX系列多功能净化剂在出口各种形态硫分别小于 0.03 mg/m3时,对COS、CS2的工作硫容可达到5.O %、对噻吩类有机硫的硫容量可达到1.5%左右。
鉴于各种脱碳方法的差异,可能在流程配置上需要根据具体情况做优化调整。
该流程已成功应用于6O余套生产装置,是目前应用最为广泛的工艺。
其中河南心连心化肥有限公司精脱硫运行周期高达60个月,同时该公司的联醇催化剂在运行60个月后仍能正常使用。
由于大修周期为两年,为稳妥起见才考虑同步更换。
此外还有众多的厂采用该工艺运行周期均超过48个月。
3.2 CLEAN(科灵)单塔一步法工艺该工艺为单塔流程,同时精脱H2S和各种有机硫。
精脱硫出口各种形态硫可分别小于0.03 mg/m3,总硫≤0.10 mg /m3,同时可脱除少量的氯化物。
该工艺适用于与PSA法脱碳或低温甲醇洗净化配套等硫负荷较低的精脱硫过程。
山西科灵公司开发的配套产品对H2S的硫容量可达18%~20%,对COS、CS2的硫容量可达5.0%,对噻吩类的硫容量可达到1.5%左右。
该流程的特点是设备简单、占地面积少、节省投资。
3.3 CLEAN(科灵)前置水解工艺该工艺将精脱硫分为两个部分:将水解过程提前到低变之后的适当位置,将精脱H2S和各种有机硫仍然安排在脱碳之后。
适用于醇/氨比较高、部分变换或其它有机硫含量较高的生产过程。
水解前置后须选用宽温型水解催化剂。
不仅省去了换热器和冷却器等设备,而且在温度较高的区域可明显减少水解催化剂的装填量。
COS在宽温型水解催化剂上的转化率可达90%左右,当水解温度在120℃以上时,还可转化绝大部分的CS2。
在经过变换气脱硫等环节后精脱硫的负荷明显减小,有利于延长精脱硫剂的寿命,实现稳产高产的目标。
该工艺精脱硫出口各种形态硫可分别小于0.03 mg/m3,总硫≤0.10 mg/m3,同时可脱除少量的氯化物。
河北某厂,醇/氨比在2/3左右,变换出口CO一般在9.5 %~11.0% 之间,变换气中COS在3.O~30.0 mg/m3之间。
在选用山西科灵公司的TGH-2Q型宽温水解催化剂后,出变换系统COS含量一般在0.30~2.80 mg/m3,对应的COS 转化率在85.0%~92.5%。
第一炉宽温水解催化剂已使用38个月、精脱硫剂已使48个月,出口总硫仍在0.10 mg/m3以下。
该厂目前已在全部3套系统都采用了前置水解工艺。
山西某小型化肥厂,醇/氨比接近1/1,过去曾先后采用“夹心饼”水解工艺和两步法精脱硫工艺,运行周期不超过1O个月。
采用山西科灵公司的前置水解工艺后,目前已正常运行15个月,各项分析数据均符合工艺要求,预计可运行24个月以上。
4 脱碳解吸CO2 气体的脱硫工艺和脱硫剂选择脱碳解吸得到的CO气中硫化物的含量都比较高,一般从10.0 mg/m3以下到最高达到200 mg/m3左右。
为满足尿素生产或CO2气的其它用途,都需要进一步脱除硫化物。
脱碳解吸得到的CO2气中硫化物的含量和成份都与变换气脱硫的效果有直接的关系。
一般认为,CO2气中硫化物的含量约为脱碳原料气中硫化物含量的3-4倍。
尿素生产用CO2气中硫化物的含量指标各厂控制不一,大都要求在 5.0-15.0 mg/m3以下。
绝大多数的厂都采用多塔活性炭脱硫剂脱硫,也有少数厂采用氧化铁脱硫剂。
还有的厂由于硫化物特别是有机硫含量过高,被迫采用了水解工艺。
对大多数的厂,采用多塔活性炭脱硫剂脱硫可以达到理想的效果。
但对于少数厂用氧化铁脱硫剂的做法需要重新考虑。
我们注意到,用氧化铁脱硫剂的厂脱硫剂更换周期很短,长的不超过3个月,短的只有一个月甚至一周时间。
有的厂在计算的工作硫容不到0.50%的情况下出口硫化物已经超标。
事实上,用普通氧化铁脱硫剂脱除CO2气中硫化物目前尚未见到十分成功的报道。
对于采用水解工艺脱除CO2气中硫化物,首先应当弄清硫化物的来源。
CO2气中过高的硫化物有以下两种情况:一是无变换气脱硫或效果太差,二是在变换气(干法)脱硫过程中大量地生成了有机硫。
找到问题的根源,后面的问题自然就迎刃而解了。
当然,如果将CO2气用作食品级CO2原料等其它情况时,精脱硫工艺将另当别论。
需要指出,脱除CO2气中硫化物选用活性炭脱硫剂仍有选择的问题。
劣质的活性炭脱硫剂不仅使用周期短、精度差,同时也存在着H2S向COS转化的问题。
山西某尿素厂,原来选用河南某公司的活性炭脱硫剂脱除CO2气中的硫化物,承诺可以保证使用6个月。
但运行两个多月后就发现出口硫含量明显增长,到四个多月时虽然出口H2S尚未超标(该厂控制的指标是H2S≤10 mg/Nm3,并未检测和控制有机硫),但尿素塔腐蚀严重,产品镍含量超标。
经检测分析,是由于活性炭脱硫剂生成了大量的COS所致。
后改用山西科灵公司的TGC-3型活性炭脱硫剂,到目前为止已运行15个月,出口总硫仍小于1.0 mg/Nm3。
其实,TGC-3型活性炭脱硫剂的价格不到原来使用产品价格的2倍,其性价比是显而易见的。
5 干法脱硫相关工艺操作条件的匹配要点综上所述,合成氨(联醇)厂在选用干法脱硫剂时,只要选择不同性能优质的活性炭脱硫剂(组合)就可以满足要求了。
对于特殊的醇/氨比较高(或有机硫较高)的企业可适当增加宽温水解催化剂,总硫控制在≤0.10 mg/Nm3甚至0.05 mg/Nm3以下是完全可以做到的。