详谈pcb钻孔孔壁镀铜开裂问题及解决方案-豆丁
PCB孔铜断裂分析报告

孔铜断裂通常表现为电气连接失 效,可能引发电路故障或产品性 能下降。
断裂原因与影响
原因
孔铜断裂可能由多种因素引起,包括 制造过程中的缺陷、材料问题、环境 因素等。
影响
孔铜断裂可能导致电路板功能失效, 增加产品故障率,降低产品质量和可 靠性。
断裂分析的重要性
确定断裂原因
优化制ቤተ መጻሕፍቲ ባይዱ工艺
通过对孔铜断裂进行分析,可以确定 导致断裂的具体原因,为后续的改进 和预防措施提供依据。
对PCB的布局和布线进 行优化,尽量减少应力 集中区域,特别是通孔 连接处的设计。可以考 虑增加过孔的直径或优 化过孔的排布来降低应 力水平。
加强质量检测与 可靠性评估
在PCB生产和组装过程 中,增加对通孔质量的 检测环节,确保无缺陷 产品流入市场。同时, 对已生产和在役的PCB 进行可靠性评估,特别 是针对可能承受较大应 力的区域进行重点检查 。
工艺优化与改进
总结词
优化和改进制造工艺可以有效降低PCB孔铜 断裂的风险。
详细描述
通过改进钻孔、电镀和焊接等工艺过程,可 以增强PCB的机械性能和耐久性。例如,优 化钻孔参数可以减少孔内缺陷和应力,提高 孔壁的附着力和强度。
环境因素控制
要点一
总结词
环境因素对PCB孔铜断裂具有重要影响,需严格控制。
切片分析
深入观察
通过将PCB切片,可以更深入地观察孔铜内部的断裂情况。 切片分析可以揭示断裂的起始点、扩展方向以及断裂面的微 观结构。
扫描电镜分析
高倍观察
扫描电镜可以提供高倍率的观察,帮助分析孔铜断裂的具 体细节。通过扫描电镜,可以观察到断裂面的微观形貌、 晶体结构和元素分布,为后续分析提供依据。
PCB钻孔工艺故障和解决

PCB钻孔工艺故障和解决钻孔时PCB工艺中一道重要的工序,看起来专门简单,但实际上却是一道专门关键的工序。
在此,笔者靠着个人钻孔工作的体会和方法,同大伙儿分析一下钻孔工艺的一些品质故障产生的缘故及其解决方法。
在制造业中,不良品的产生离不开人、机、物、法、环五大因素。
同样,钻孔工艺中也是如此,下面把用鱼骨图分列出阻碍钻孔的因素一、在众多阻碍钻孔加工时期,对各项不同的项目施行检验为了确保加工板子从投入前至产出,全部过程的品质都在合格范畴内。
以下列举PCB板钻孔加工常见的检验类不及项目。
(1)、钻孔前基板检验,项目有:品名、编号、规格、尺寸、铜铂厚;不刮伤;不弯曲、不变形;不氧化或受油污染;数量;无凹凸、分层剥落及折皱。
(2)、钻孔中操作员自主检验,项目为:孔径;批锋;深度是否贯穿;是否有爆孔;核对偏孔、孔变形;多孔少孔;毛刺;是否有堵孔;断刀漏孔;整板移位。
二、钻孔生产过程中经常显现故障详细分解1、断钻咀产生缘故有:主轴偏转过度;数控钻机钻孔时操作不当;钻咀选用不合适;钻头的转速不足,进刀速率太大;叠板层数太多;板与板间或盖板下有杂物;钻孔时主轴的深度太深造成钻咀排屑不良发生绞死;钻咀的研磨次数过多或超寿命使用;盖板划伤折皱、垫板弯曲不平;固定基板时胶带贴的太宽或是盖板铝片、板材太小;进刀速度太快造成挤压;补孔时操作不当;盖板铝片下严峻堵灰;焊接钻咀尖的中心度与钻咀柄中心有偏差。
解决方法:(1) 通知机修对主轴进行检修,或者更换好的主轴。
(2) A、检查压力脚气管道是否有堵塞;B、按照钻咀状态调整压力脚的压力,检查压力脚压紧时的压力数据,正常为7.5公斤;C、检查主轴转速变异情形及夹嘴内是否有铜丝阻碍转速的平均性;D、钻孔操作进行时检测主轴转速变化情形及主轴的稳固性;(能够作主轴与主轴之间对比)E、认真调整压力脚与钻头之间的状态,钻咀尖不可露出压脚,只承诺钻尖在压脚内3.0mm处;F、检测钻孔台面的平行度和稳固度。
pcb常见缺陷原因与措施

加强操作人员的安全意识教育, 确保生产过程中的安全和稳定。
04
PCB常见缺陷的检测方法与技 巧
目视检测法
直接观察PCB表面
通过肉眼或放大镜观察PCB表面是否存在裂纹、变形、气泡、污 渍等缺陷。
检查焊接质量
目视检测法可以用于检查焊接质量,如焊点大小、形状、光泽度等 是否符合要求。
识别元器件
目视检测法可以用于识别元器件的型号、规格、极性等是否正确。
焊盘腐蚀
使用合适的清洗剂清洗腐蚀的焊盘,然后用烘干机烘干。
阻焊层缺陷修复方法与技巧
阻焊层脱落
使用合适的涂料重新涂刷脱落的阻焊层,然后用烘干机烘 干。
阻焊层变色
使用合适的清洗剂清洗变色的阻焊层,然后用烘干机烘干 。
阻焊层起泡
检查阻焊层起泡原因,如果是由于涂层过厚导致,可以使 用砂纸打磨起泡区域,然后重新涂刷阻焊层,最后用烘干 机烘干。
生产设备问题
总结词
设备故障或误差
详细描述
PCB生产过程中使用的设备,如钻孔机、曝光机、蚀刻机等,如果出现故障或误 差,可能导致PCB出现孔径不准确、线路不清晰、蚀刻过度等缺陷。
生产工艺问题
总结词
工艺参数不当
详细描述
PCB生产过程中的各项工艺参数,如温度、压力、时间等,如果设置不当,可能导致PCB出现翘曲、起泡、氧化 等缺陷。
优化生产工艺和流程
对生产工艺和流程进行持续改 进,提高生产效率和产品质量 。
引入先进的生产技术和设备, 提高生产自动化程度。
优化生产布局和物流管理,减 少生产过程中的浪费和损失。
提高操作人员技能和素质
加强操作人员技能培训,提高操 作人员的技能水平和操作规范意
识。
建立激励机制,鼓励操作人员积 极参与技术革新和改进活动。
PCB镀层缺陷成因分析及其对策

PCB鍍層缺陷成因分析及其對策[摘要]分析了金属化孔镀层的主要缺陷及产生原因,从各主要工序出发,提出了如何优化工艺参数,进行严格的工艺及生产管理,以保证孔化质量的方法。
[关键词]多层印制板,金属化孔,镀层缺陷1 前言金属化孔质量与多层板质量及可靠性息息相关。
金属化孔起着多层印制线路电气互连的作用。
孔壁镀铜层质量是印制板质量的核心,不仅要求镀层有合适的厚度、均匀性和延展性,而且要求镀层在288℃热冲击10秒不能产生断裂。
因为孔壁镀铜层热冲击断裂是一种致命的缺陷,它将造成内层线路间和内层与外层线路之间断路;轻者影响线路断续导电,重者引起多层板报废。
目前,印制板生产中经常出现的金属化孔镀层缺陷主要有:金属化孔内镀铜层空洞、瘤状物、孔内镀层薄、粉红圈以及多层板孔壁与内层铜环连接不良等。
这些缺陷的绝大多数将导致产品报废,造成严重的经济损失,影响交货期。
2 金属化孔镀层主要缺陷的产生原因及相应对策我们首先简单回顾一下多层印制板的制造工艺过程。
下料→制板→蚀刻→黑化→层压→钻孔→去沾污及凹蚀处理→孔金属化→全板电镀→制板→图形电镀→脱膜→蚀刻→丝印阻焊→热风整平→丝印字符本文将从钻孔工序、孔壁去树脂沾污及凹蚀处理工序、电镀及多层板层压工序等几个方面,分析金属化孔镀层的主要缺陷及产生原因,阐述如何优化工艺参数,进行严格的工艺及生产管理,以保证孔化质量。
2.1 钻孔工序大多数镀层空洞部位都伴随出现钻孔质量差引起的孔壁缺陷,如孔口毛刺、孔壁粗糙、基材凹坑及环氧树脂腻污等。
由此造成孔壁镀铜层空洞,孔壁基材与镀层分离或镀层不平整。
下面,将对孔壁缺陷的成因及所采取的措施进行阐述:2.1.1 孔口毛刺的产生及去除无论是采用手工钻还是数控钻,也无论是采用何种钻头和钻孔工艺参数,覆铜箔板在其钻孔过程中,产生毛刺总是不可避免的。
孔口毛刺对于金属化孔质量的影响历来不被人们所重视,但对于高可靠性印制板的金属化孔质量来讲,它却是一个不可忽视的因素。
详谈pcb钻孔孔壁镀铜开裂问题及解决方案-豆丁
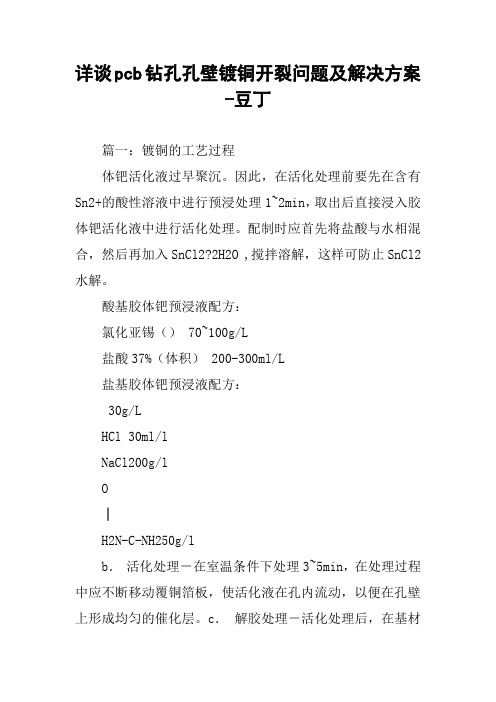
详谈pcb钻孔孔壁镀铜开裂问题及解决方案-豆丁篇一:镀铜的工艺过程体钯活化液过早聚沉。
因此,在活化处理前要先在含有Sn2+的酸性溶液中进行预浸处理1~2min,取出后直接浸入胶体钯活化液中进行活化处理。
配制时应首先将盐酸与水相混合,然后再加入SnCl2?2H2O ,搅拌溶解,这样可防止SnCl2水解。
酸基胶体钯预浸液配方:氯化亚锡() 70~100g/L盐酸37%(体积) 200-300ml/L盐基胶体钯预浸液配方:30g/LHCl 30ml/lNaCl200g/lO║H2N-C-NH250g/lb.活化处理-在室温条件下处理3~5min,在处理过程中应不断移动覆铜箔板,使活化液在孔内流动,以便在孔壁上形成均匀的催化层。
c.解胶处理-活化处理后,在基材表面吸附着以钯粒子为核心,在钯核的周围,具有碱式锡酸盐的胶体化合物。
在化学镀铜前,应将碱式锡酸盐去除,使活性的钯晶核充分暴露出来,从而使钯晶核具有非常强而均匀的活性。
经过解胶处理再进行化学镀铜,不但提高了胶体钯的活性,而且也显著提高化学镀铜层与基材间的结合强度。
常用的解胶处理液是5%的氢氧化钠水溶液或1%氟硼酸水溶液。
解胶处理在室温条件下处理1~2min,水洗后进行化学镀铜。
d.胶体铜活化液简介:明胶 2g/l/lDMAB(二甲胺基硼烷)5g/l水合肼 10 g/l钯20ppm配制过程:首先分别将明胶和硫酸铜用温水(40度C)溶解后将明胶加入至硫酸铜的溶液中,用25%H2SO4将PH值调至2..5当温度为45度C时,将溶解后DMAB在搅拌条件下缓慢加入上述的混合溶液中,并加入去离子稀释至1升,保温40~45度C,并搅拌至反应开始(约5~10分钟)溶液的颜色由蓝再变成绿色。
放置24小时颜色变成红黑色后加入水合肼。
篇二:PCB线路板镀铜表面粗糙问题原因分析PCB线路板镀銅表面粗糙问题原因分析可能原因如下:镀铜槽本身的问题1、阳极问题:成分含量不当导致产生杂质2、光泽剂问题(分解等)3、电流密度不当导致铜面不均匀4、槽液成分失调或杂质污染5、设备设计或组装不当导致电流分布太差…………当然作为镀铜本身来讲;以上问题导致粗糙的可能性不大前制程问题PTH制程带入其他杂质:1、活化成分失调钯浓度太高或者预浸盐残留板面2、速化失调板面镀铜是残有锡离子3、化学铜失调板面沉铜不均4、镀铜前酸洗不当导致板面残留杂质………………黑孔制程:微蚀不净导致残碳抗氧化不当导致板面不良烘干不良导致微蚀无法将板面碳剥除导致残碳电流输入输出不当导致板面不良…………篇三:化学镀铜常见故障和纠正方法-PCB工艺论文,SMT 技术文章-SMT专家网化学镀铜常见故障和纠正方法◎化学镀铜常见故障和纠正方法故障发生原因纠正方法化学镀铜空洞①钻孔粉尘,孔化后脱落①检查吸尘器,钻头质量,转速/进给等②加强去毛刺的高压水冲洗钻孔后孔壁裂缝或内层间分离检查钻头质量,转速/进给,以及层压板厚材料和层压工艺条件③除钻污过度,造成树脂变成海绵状,引起水洗不良和镀层脱落检查除钻污法工艺,适当降低去钻污强度④除钻污后中和处理不充分,残留Mn残渣检查中和处理工艺⑤清洁调整不足,影响Pd的吸附检查清洗调整处理工艺(如浓度、温度、时间)及副产物是否过量⑥活化液浓度偏低影响Pd吸附检查活化处理工艺补充活化剂⑦加速处理过度,在去除Sn的同时Pd也被除掉检查加速处理工艺条件(温度/时间/浓度)如降低加速剂浓度或浸板时间⑧水洗不充分,使各槽位的药水相互污染检查水洗能力,水量/水洗时间⑨孔内有气泡加设摇摆、震动等⑩化学镀铜液的活性差检查NaOH、HCHO、Cu2+的浓度以及溶液温度等⑾反应过程中产生气体无法及时逸出加强移动、振动和空气搅拌等。
PCB钻孔工艺故障与解决方法

PCB钻孔工艺故障与解决方法1. 引言在PCB〔Printed Circuit Board〕制造过程中,钻孔工艺是其中一个关键的步骤。
钻孔工艺的质量直接影响到电路板的可靠性和性能。
然而,钻孔工艺中常常会出现一些故障,如钻孔位置偏移、孔径不一致、刀具破损等。
本文将针对这些故障进行分析,并给出解决方法。
2. 钻孔位置偏移钻孔位置偏移是在PCB钻孔工艺中经常遇到的问题,对于高密度电路板来说尤为突出。
钻孔位置偏移会导致焊盘与元器件引脚无法对准,进而影响电路板的正常工作。
2.1 问题原因钻孔位置偏移通常有以下几个原因:•钻孔加工时刀具磨损不均匀;•钻孔机械误差;•钢板固定不稳定。
2.2 解决方法针对钻孔位置偏移问题,可以采取以下解决方法:•定期更换刀具,确保刀具磨损均匀;•定期校准钻孔机械误差,降低误差对钻孔位置的影响;•确保钢板固定稳定,防止在加工过程中发生移动。
3. 孔径不一致孔径不一致是指PCB钻孔中,同一个连接孔的多个孔径不一致。
孔径不一致会导致焊盘孔的尺寸不准确,从而影响元器件的安装。
3.1 问题原因孔径不一致通常有以下几个原因:•钻孔机加热不均匀,导致钻孔机的热胀冷缩不一致;•刀具磨损不均匀。
3.2 解决方法针对孔径不一致的问题,可以采取以下解决方法:•控制钻孔机的工作环境温度,确保加热均匀;•定期更换刀具,确保刀具磨损均匀。
4. 刀具破损刀具破损是在PCB钻孔工艺中比拟常见的问题,一旦刀具破损就需要更换,从而增加了生产本钱和工期。
4.1 问题原因刀具破损通常有以下几个原因:•钻孔加工时的压力过大;•刀具质量不过关。
4.2 解决方法针对刀具破损问题,可以采取以下解决方法:•控制钻孔加工时的压力,确保在合理范围内;•选择质量过关的刀具,提高刀具的使用寿命。
5. 结论钻孔工艺在PCB制造过程中扮演着重要的角色,但也容易出现故障。
本文从钻孔位置偏移、孔径不一致和刀具破损三个方面对这些故障进行了分析,并给出了相应的解决方法。
pcb常见缺陷原因与措施

污染物
空气中的微粒和有害气体可能污 染PCB的表面和内部,导致缺陷
。
静电
制造过程中的静电可能导致PCB 上的微粒移动,产生缺陷。
解决方法
控制温度和湿度
在制造过程中,应将温度和湿度控制在适当的范 围内。
空气净化
使用空气净化设备,减少空气中的微粒和有害气 体。
静电防护
采取静电防护措施,如使用防静电设备和材料, 减少静电的产生。
线路布局过于紧凑,导致 信号线交叉、重叠或干扰 。
走线不规范
走线弯曲、断裂或重叠, 导致信号传输不稳定。
未遵循最佳实践
设计时未遵循PCB设计的 最佳实践,如未考虑信号 完整性、电源完整性等因 素。
解决方法
优化布局
重新审查并调整线路布局 ,确保信号线之间保持适 当的间距,避免交叉、重 叠或干扰。
修正走线
制造工艺问题
02
制造过程中出现的问题,如曝光不良、显影不良、蚀刻不均等
。
压合工艺问题
03
多层板压合时,由于材料、温度等因素导致分层、扭曲等问题
。
解决方法
1 2
选用高质量板材
确保使用符合规格的板材,提高PCB的质量稳定 性。
优化制造工艺
通过对制造工艺的调整和改进,提高PCB的制造 质量。
3
压合工艺优化
加强制造质量控制:在制造过程中,应加强质量检查和控 制,确保不会出现短路的情况。
断路
优化制造工艺:在制造过程中,应采取适当的工艺和方法 ,确保线路的完整性和连续性。
定期维护和检查:在使用过程中,应定期对PCB进行检查 和维护,确保线路的完整性和连续性。
03
线路设计不良
原因分析
pcb板过孔与铜皮短路原因

pcb板过孔与铜皮短路原因PCB板是电子产品中不可缺少的元件,而其中的过孔和铜皮短路是常见的问题。
本文将探讨这两种问题的原因,并提出相应的解决方案。
一、 PCB板过孔原因1.1. 过孔设计错误过孔的设计是PCB板制作中重要的一环,如果设计不当,就会造成过孔质量不佳。
例如,过孔的直径、孔间距、板厚等参数未考虑周全,就会导致过孔不对称、孔径不足、孔壁不平等问题。
1.2. 过孔加工不当过孔加工是PCB板制作中的关键步骤,一旦加工不当就会导致过孔出现问题。
例如,钻孔过程中产生的碎屑未及时清理,就会导致过孔内部存在残留碎屑;过孔内部未光滑处理,就会导致过孔壁面不平等问题。
1.3. 过孔焊接不当PCB板上的元器件需要通过焊接技术与过孔相连,如果焊接不当,就会导致过孔出现问题。
例如,焊接温度不足、焊接时间不足、焊接方式不当等都会导致过孔焊点不牢固,易造成焊点断裂、短路等问题。
二、 PCB板铜皮短路原因2.1. 铜皮设计错误铜皮的设计是PCB板制作中不可忽视的一环,如果设计不当,就会造成铜皮短路问题。
例如,铜皮的厚度、铜皮间距、铜皮形状等参数未考虑周全,就会导致铜皮短路问题。
2.2. 铜皮加工不当铜皮加工是PCB板制作中的关键步骤,一旦加工不当就会导致铜皮出现问题。
例如,铜皮间距不足、铜皮形状不规则、铜皮缺陷等问题都会导致铜皮短路问题。
2.3. 元器件安装不当PCB板上的元器件需要通过焊接技术与铜皮相连,如果安装不当,就会导致铜皮短路问题。
例如,元器件间距不足、元器件位置不当、元器件引脚弯曲等问题都会导致铜皮短路问题。
三、解决方案针对上述问题,我们可以采取以下措施来解决:3.1. 设计合理的过孔和铜皮在PCB板设计阶段,应根据实际需要合理设计过孔和铜皮,避免出现过孔和铜皮短路问题。
3.2. 严格控制加工质量在PCB板加工过程中,应严格控制各个环节的质量,确保过孔和铜皮的加工质量达到标准要求。
3.3. 采用优质元器件在PCB板元器件的选择上,应尽量选择优质的元器件,避免因元器件质量差而导致的焊接和安装问题。
PCB镀通孔发生_空洞_的根本原因和对策

PCB镀通孔发生“空洞”的根本原因和对策林金堵 吴梅珠摘 要 文章概述了多层板镀通孔发生“空洞”的根本原因与对策。
基材、钻孔、孔壁粗糙度、孔尺寸、化学镀铜和电镀铜等都会影响PTH的“空洞”问题。
关键词 镀通孔;镀层“空洞”;镀层附着力;高性能基材;孔壁表面状态;化学镀铜中图分类号:TN41 文献标识码:A 文章编号:1009-0096(2010)4-0031-06The Basic and Countermeasureof the Plated Through Hole Voiding in PCBLIN Jin-du WU Mei-zhuAbstract The paper describes the basic and countermeasure of the plated through hole voiding in PCB. The substrate material, drilling hole, hole-wall topography, hole size, electroless copper, and plated copper can signi fi cantly impact the hole-wall voids, adhesion, and reliability of the PTH.Key words PTH(Plated Through-Hole); hole-wall voids; hole-wall adhesion; high-performance substrate; hole-wall topography; electroless copper目前,多层板随着高密度化发展和无铅化焊接要求等条件下,层间连接的导通孔面临着产生“空洞”等缺陷,其可靠性方面面临着严厉而复杂的挑战。
这些挑战:(1)是导通孔高厚径比(孔微小化和高多层化)化和盲孔化等带来孔金属化与电镀的复杂困难度;(2)是无铅化要采用更高的T d 、T g 温度的CCL (高性能)材料所带来“导通孔”的加工新问题;(3)由于无铅化焊接要求有耐更高的焊接温度、更长的高温焊接时间和快速的冷却速度,因此,导通孔内的铜镀层,不仅要有更好的延展性,而且更重要地是要与孔壁有更好的结合力,才能经得起更高的焊接条件的考验;(4)是所制造的成品要经得起更高幅度的多次“热循环”、“热冲击”(更高温度和更长的高温停留时间)等的“老化(可靠性)”考验。
pcb钻孔常见问题和改善措施

pcb钻孔常见问题和改善措施
PCB钻孔过程中常见的问题主要包括钻孔偏移、孔位不正、钻孔深度不合适、孔径不准确、孔内有毛刺、孔边有缺口等。
针对这些问题,可以采取以下改善措施:
1. 钻孔偏移:检查主轴是否偏转,减少叠板数量,增加钻头转速或降低进刀速率,重新检查钻头是否符合工艺要求,检查钻头顶尖是否具备良好同心度,检查钻头与弹簧夹头之间的固定状态是否紧固,重新检测和校正钻孔工作台的稳定和稳定性。
2. 孔位不正:检查钻头是否符合工艺要求,重新刃磨钻头,检查钻头是否合适,检查工作台是否水平,调整工作台的平行度,检查钻头与弹簧夹头之间的固定状态是否紧固。
3. 钻孔深度不合适:根据不同的板材厚度选择合适的钻咀长度和进刀量,适当调整钻孔的吸尘力。
4. 孔径不准确:检查钻咀的几何外形和磨损情况,选择合适的进刀量和转速,适当调整压力脚气管道是否有堵塞,调整压力脚与钻头之间的状态。
5. 孔内有毛刺:适当调整进刀速率,增加刀补值,选择合适的切削液,检查刀具是否锋利。
6. 孔边有缺口:检查刀具是否锋利,适当调整进刀速率和刀补值,增加压力脚气管道的压力,选择合适的切削液。
除了以上措施,还可以采取以下措施来提高钻孔质量和效率:
1. 选择合适的钻头材料和几何形状,根据不同的加工条件和材料选择合适的切削参数。
2. 定期检查和维护钻头和刀具,及时更换磨损和损坏的刀具。
3. 优化加工工艺流程,减少加工过程中的停顿和等待时间。
4. 提高操作人员的技能水平和工作责任心,加强对加工过程的监控和管理。
5. 采用先进的加工设备和控制系统,提高加工精度和效率。
PCB冲孔质量与疵病对策

PCB冲孔质量与疵病对策随着各行业的快速发展,印刷电路板(PCB)在各种电子设备中应用越来越广泛,由于印制电路板中存在许多小孔,而这些小孔是通过冲压技术来实现的。
然而,PCB冲孔质量与疵病对策也逐渐成为广大制造企业关注的焦点。
PCB冲孔质量的影响因素及其对策PCB冲孔质量涉及到多个因素,以下是一些常见的影响因素及其对策:1.冲压质量冲压工艺是冲孔的关键,冲压质量若不好可能会导致板子打偏、崩裂等情况。
由于PCB板材经过预钻后再进行冲压,因此,首先要做的就是确保预钻孔的尺寸和位置精度。
此外,冲压头的尺寸、硬度、形状等都会对冲压质量有影响。
对策:针对冲压质量不好的问题,生产厂家可以在冲模设计、冲头制造、冲压参数控制等方面加强管理,避免由于设备调试不当、工人操作不规范等原因导致的冲击不均、冲头磨损等问题。
2.孔壁质量PCB冲孔的孔壁质量指的是孔的圆度、平行度等尺寸精度问题。
良好的孔壁质量能够保证电路板上的器件插拔性能良好,同时可以提高电气特性,减少工作中的信号噪声。
对策:生产厂家可以通过改善制板材料、冲头和模具的质量以及加强冲压工艺控制等方式来提高冲孔的孔壁质量。
3. PCB 倾斜度PCB倾斜度是冲孔过程中容易出现的问题。
如果冲孔时板子不平整,就很容易导致冲出的孔口偏离使用位置,甚至使板子不符合规格要求。
对策:解决PCB 倾斜的问题,可以通过合理的固定夹具、平稳的传输轨道以及调整冲压工艺中的冲压速度、压力等参数来解决问题。
PCB冲孔疵病及防范措施除了注意冲孔质量外,生产厂家还应该关注PCB 冲孔的疵病问题。
常见的PCB 冲孔疵病有以下几点:1. 龟裂现象龟裂是PCB 冲孔难免会产生的一个疵病。
龟裂的出现会影响PCB 的正常使用,而且有时还会造成PCB 的氧化腐蚀,导致板子受损。
对策:解决龟裂现象可以从以下几个方面进行:调整冲孔机的冲压定位,加强冲压压力和速度的控制,优化钻孔孔径等。
2. 小孔不通PCB 冲孔时也会出现孔径不合适导致小孔不通的问题,这会直接影响PCB 的正常使用。
PCB 冲孔质量与疵病对策

PCB 冲孔质量与疵病对策1. 背景介绍PCB(Printed Circuit Board)是电子产品的核心组件之一,用于电子元器件的连接和固定。
冲孔是PCB制造过程中非常重要的一环,决定着电子元器件的插装质量和PCB的可靠性。
冲孔质量问题会直接影响到产品的性能和寿命,因此需要采取相应的对策来降低冲孔的疵病率。
2. PCB 冲孔质量问题分析2.1 冲孔疵病现象冲孔质量问题主要体现在以下几个方面:•孔径不准确:孔径偏小或偏大,导致电子元器件无法插装或插装不稳定。
•孔壁不光滑:孔壁存在毛刺,影响电子元器件和导线的接触质量。
•孔位置偏移:孔径在PCB上的位置与设计要求有偏移,导致元器件间连接错误或无法插装。
2.2 冲孔质量问题的原因冲孔质量问题的原因主要有以下几个方面:•冲孔钻头磨损严重:当冲孔钻头磨损严重时,会导致孔径不准确、孔壁不光滑等问题。
•冲孔钻头材料不合适:冲孔钻头的材料选择不合适,容易导致钻头磨损、冲孔质量下降。
•冲孔工艺参数设置不当:冲孔工艺参数包括冲孔速度、冷却液流量等,如果设置不当,容易导致冲孔质量问题。
•冲孔机械设备损坏:冲孔机械设备损坏或老化,会导致冲孔孔径不准确、孔壁不光滑等问题。
3. PCB 冲孔质量对策3.1 合适的冲孔钻头选择选择合适的冲孔钻头材料和尺寸,确保冲孔质量的稳定性。
常见的冲孔钻头材料有硬金属钎头、PCD钎头等,根据具体情况选择合适的材料。
3.2 优化冲孔工艺参数合理设置冲孔工艺参数,包括冲孔速度、冷却液流量、工作温度等。
通过合适的参数设置,提高冲孔质量的稳定性和准确性。
3.3 定期检查和维护冲孔机械设备定期检查和维护冲孔机械设备,确保设备的状态良好。
定期更换冲孔钻头、清洁冲孔机械设备,保证冲孔质量的稳定性和准确性。
3.4 强化人员培训和监控加强对冲孔操作人员的培训,提高其对冲孔质量要求的认识和理解。
建立冲孔质量监控体系,及时发现和处理冲孔质量问题。
3.5 建立冲孔质量检测流程建立冲孔质量检测流程,对冲孔质量进行检测和评估。
PCB钻孔工艺故障与解决方法(doc 13页)
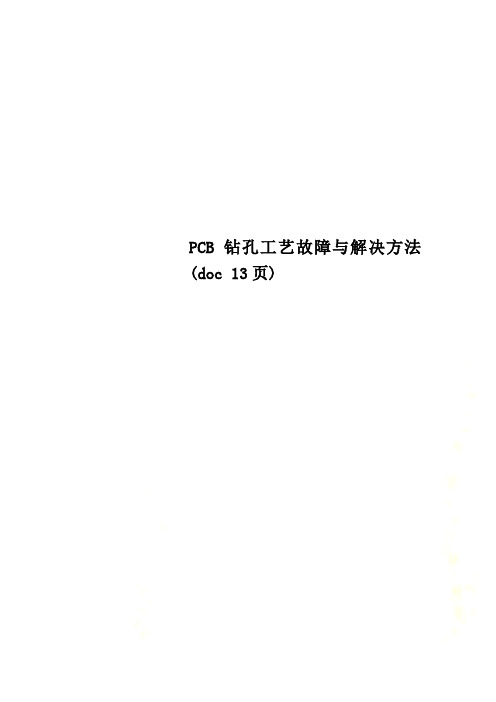
PCB钻孔工艺故障与解决方法(doc 13页)PCB钻孔工艺故障和解决钻孔时PCB工艺中一道重要的工序,看起来很简单,但实际上却是一道非常关键的工序。
在此,笔者凭着个人钻孔工作的经验和方法,同大家分析一下钻孔工艺的一些品质故障产生的原因及其解决方法。
在制造业中,不良品的产生离不开人、机、物、法、环五大因素。
同样,钻孔工艺中也是如此,下面把用鱼骨图分列出影响钻孔的因素一、在众多影响钻孔加工阶段,对各项不同的项目施行检验为了确保加工板子从投入前至产出,全部过程的品质都在合格范围内。
以下列举PCB板钻孔加工常见的检验类别及项目。
(1)、钻孔前基板检验,项目有:品名、编号、规格、尺寸、铜铂厚;不刮伤;不弯曲、不变形;不氧化或受油污染;数量;无凹凸、分层剥落及折皱。
(2)、钻孔中操作员自主检验,项目为:孔径;批锋;深度是否贯穿;是否有爆孔;核对偏孔、孔变形;多孔少孔;毛刺;是否有堵孔;断刀漏孔;整板移位。
二、钻孔生产过程中经常出现故障详细分解1、断钻咀产生原因有:主轴偏转过度;数控钻机钻孔时操作不当;钻咀选用不合适;钻头的转速不足,进刀速率太大;叠板层数太多;板与板间或盖板下有杂物;钻孔时主轴的深度太深造成钻咀排屑不良发生绞死;钻咀的研磨次数过多或超寿命使用;盖板划伤折皱、垫板弯曲不平;固定基板时胶带贴的太宽或是盖板铝片、板材太小;进刀速度太快造成挤压;补孔时操作不当;盖板铝片下严重堵灰;焊接钻咀尖的中心度与钻咀柄中心有偏差。
解决方法:(1) 通知机修对主轴进行检修,或者更换好的主轴。
(2) A、检查压力脚气管道是否有堵塞;B、根据钻咀状态调整压力脚的压力,检查压力脚压紧时的压力数据,正常为7.5公斤;C、检查主轴转速变异情况及夹嘴内是否有铜丝影响转速的均匀性;D、钻孔操作进行时检测主轴转速变化情况及主轴的稳定性;(可以作主轴与主轴之间对比)E、认真调整压力脚与钻头之间的状态,钻咀尖不可露出压脚,只允许钻尖在压脚内3.0mm处;F、检测钻孔台面的平行度和稳定度。
PCB生产过程中钻孔经常遇到的问题点

线路板在生产过程中钻孔遇到的问题一、为什么孔内玻纤突出(Fiber Proturusion in Hole)?1. 可能原因:退刀速率过慢对策:增快退刀速率。
2. 可能原因:钻头过度损耗对策:重新磨利钻尖,限制每只钻尖的击数,例如上线定位1500击。
3. 可能原因:主轴转速(RPM)不足对策:调整进刀速率和转速的关系到最佳的状况,检查转速变异情况。
4. 可能原因:进刀速率过快对策:降低进刀速率(IPM)。
二、为什么孔壁粗糙(Rough hole walls)?1. 可能原因:进刀量变化过大对策:维持固定的进刀量。
2. 可能原因:进刀速率过快对策:调整进刀速率与钻针转速关系至最佳状况。
3. 可能原因:盖板材料选用不当对策:更换盖板材料。
4. 可能原因:固定钻头所使用真空度不足对策:检查钻孔机台真空系统,检查主轴转速是否有变异。
5. 可能原因:退刀速率异常对策:调整退刀速率与钻头转速的关系至最佳状况。
6. 可能原因:针尖的切削前缘出现破口或算坏对策:上机前先检查钻针情况,改善钻针持取习惯。
三、为什么孔形真圆度不足?1. 可能原因:主轴稍呈弯曲对策:更换主轴中的轴承(Bearing)。
2. 可能原因:钻针尖点偏心或削刃面宽度不一对策:上机前应放大40倍检查钻针。
四、为什么板叠上板面发现藕断丝连的卷曲形残屑?1. 可能原因:未使用盖板对策:加用盖板。
2. 可能原因:钻孔参数不恰当对策:减低进刀速率(IPM)或增加钻针转速(RPM)。
五、为什么钻针容易断裂?1. 可能原因:主轴的偏转(Run-Out)过度对策:设法将的主轴偏转情况。
2. 可能原因:钻孔机操作不当对策:1) 检查压力脚是否有阻塞(Sticking)2) 根据钻针尖端情况调整压力脚的压力。
3) 检查主轴转速的变异。
4) 钻孔操作进行时间检查主轴的稳定性。
3. 可能原因:钻针选用不当对策:检查钻针几何外型,检验钻针缺陷,采用具有适当退屑槽长度的钻头。
PCB化学镀铜的问题与对策

氢氧化钠的来源 也必须使用试药级的氢氧化钠。因为许多工业级的氢氧化钠,其中含有铁离子、氯离子及其 他种类的杂质,这些都会对于槽液造成影响,应该尽量避免使用。
空气搅拌 槽液无论是在操作或是置放之时,均应随时保持在空气搅拌的情形。空气通入的流量不要过 多,否则将会产生过多的泡沫(Foaming),而使槽液的性质发生变化,适当的空气流量已经 足够维持槽液的安定。
甲醛的来源 必须使用试药级的甲醛,因为许多工业级的甲醛中含有铁离子、安定剂或是胶状(Colloidal) 的杂质等,这些杂质都会对槽液与化学铜层造成伤害,所以应尽量避免使用不纯的甲醛。
槽液成份的补充频率 经常以连续及少量的添加方式较佳,因为如果一次大量地进行添加,过量的安定剂会使槽液 产生强烈的冲击。两大部分的补充槽液因该分开进行添加,然后迅速搅拌均匀。任何一次的 添加量勿超过原来槽液体积的 10%以上,因为如此将会导致槽液产生不安定或是过于安定的 现象。如果槽液的浓度低于标准值的 70%以下的时候,则须暂时停止槽液的操作,而来进行 补充添加的工作,待其浓度达到标准数值的 90%以上的时候,即可继续进行槽液的操作。
槽液补充管线的配置 两大部份槽液的管线配置必须正确适当。除了应该分开配置之外,含有铜盐的管线,必须配 在槽体之中间部位,而含有氢氧化钠的管线,必须配在槽体的底部,如此两者才会迅速混合 均匀,而不会发生结块(Clot)与沉积的现象。
清洁剂/整孔剂的使用温度、浓度与时间 正确适当的清洁与整孔处理是必须的。温度过低或是浓度不够的药液,均不适合槽液的操作, 将会使得沉积镀层发生剥离与脱落的现象。再者,槽液当中所积累的铜离子浓度,亦须严格 地加以管制。
PCB钻孔工艺故障和解决(全面)

PCB钻孔工艺故障和解决钻孔时PCB工艺中一道重要的工序,看起来很简单,但实际上却是一道非常关键的工序。
在此,笔者凭着个人钻孔工作的经验和方法,同大家分析一下钻孔工艺的一些品质故障产生的原因及其解决方法。
在制造业中,不良品的产生离不开人、机、物、法、环五大因素。
同样,钻孔工艺中也是如此,下面把用鱼骨图分列出影响钻孔的因素一、在众多影响钻孔加工阶段,对各项不同的项目施行检验为了确保加工板子从投入前至产出,全部过程的品质都在合格范围内。
以下列举PCB板钻孔加工常见的检验类别及项目。
(1)、钻孔前基板检验,项目有:品名、编号、规格、尺寸、铜铂厚;不刮伤;不弯曲、不变形;不氧化或受油污染;数量;无凹凸、分层剥落及折皱。
(2)、钻孔中操作员自主检验,项目为:孔径;批锋;深度是否贯穿;是否有爆孔;核对偏孔、孔变形;多孔少孔;毛刺;是否有堵孔;断刀漏孔;整板移位。
二、钻孔生产过程中经常出现故障详细分解1、断钻咀产生原因有:主轴偏转过度;数控钻机钻孔时操作不当;钻咀选用不合适;钻头的转速不足,进刀速率太大;叠板层数太多;板与板间或盖板下有杂物;钻孔时主轴的深度太深造成钻咀排屑不良发生绞死;钻咀的研磨次数过多或超寿命使用;盖板划伤折皱、垫板弯曲不平;固定基板时胶带贴的太宽或是盖板铝片、板材太小;进刀速度太快造成挤压;补孔时操作不当;盖板铝片下严重堵灰;焊接钻咀尖的中心度与钻咀柄中心有偏差。
解决方法:(1) 通知机修对主轴进行检修,或者更换好的主轴。
(2) A、检查压力脚气管道是否有堵塞;B、根据钻咀状态调整压力脚的压力,检查压力脚压紧时的压力数据,正常为7.5公斤;C、检查主轴转速变异情况及夹嘴内是否有铜丝影响转速的均匀性;D、钻孔操作进行时检测主轴转速变化情况及主轴的稳定性;(可以作主轴与主轴之间对比)E、认真调整压力脚与钻头之间的状态,钻咀尖不可露出压脚,只允许钻尖在压脚内3.0mm处;F、检测钻孔台面的平行度和稳定度。
详谈PCB钻孔孔壁镀铜开裂问题及解决方案

详谈PCB钻孔孔壁镀铜开裂问题及解决方案纪龙江;王大伟;秦丽洁【期刊名称】《印制电路信息》【年(卷),期】2012(000)0z1【摘要】PCB作为重要的电子部件,其钻孔质量的优劣直接关系到产品性能的稳定程度,尤其在航空、航天、军事等重要领域,钻孔质量在电气连接特性及使用可靠性方面起着至关重要的作用。
文章针对PCB钻孔过程中出现的孔壁镀层开裂问题,结合金属切削理论基础,从钻孔参数、刀具选择、板材结构与叠层、分段钻孔、材料对比等方面进行了详尽的分析与交叉实验比较,下面对具体解决过程与结果进行阐述。
% As important electronic element, PCB’s drilling quality influences the stabilization of product capability. Especially, in the most important domain of aviation, spaceflight and military affairs, drilling quality is very important at the aspect of electric connection capability and reliability in use. This article aims at the craze between copper plating and hole wall in PCB’s manufacture process, combine the academic elements of metal line cutting, analysis particularly and make experiment at the aspect of drilling parameters, select of drill, laminate material’s fabric and st ack count, subsection drill, material’s compare,etc. Now we give brief about idiographic test process and result.【总页数】6页(P187-192)【作者】纪龙江;王大伟;秦丽洁【作者单位】大连太平洋电子有限公司;大连太平洋电子有限公司;大连太平洋电子有限公司【正文语种】中文【中图分类】TN41【相关文献】1.大口径机钻孔影响孔壁稳定的因素及稳定孔壁的措施 [J], 陈开凡2.PCB机械钻孔孔壁质量影响因素分析 [J], 何平;陈正清;黄刚3.PCB盲孔镀铜填孔添加剂研究进展 [J], 周珺成;何为;周国云;王守绪4.PCB机械钻孔孔壁粗糙度的影响因素 [J], 杨海永5.PCB孔壁镀铜层空洞的成因及对策 [J], 徐自金因版权原因,仅展示原文概要,查看原文内容请购买。
PCB孔壁分离的影响因素分析及改善措施
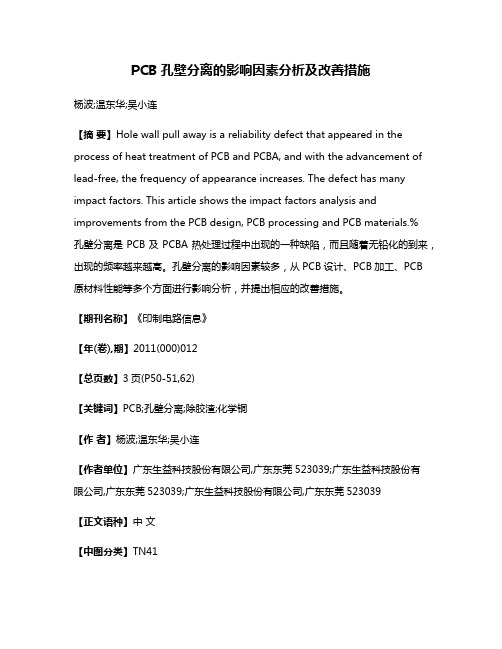
PCB孔壁分离的影响因素分析及改善措施杨波;温东华;吴小连【摘要】Hole wall pull away is a reliability defect that appeared in the process of heat treatment of PCB and PCBA, and with the advancement of lead-free, the frequency of appearance increases. The defect has many impact factors. This article shows the impact factors analysis and improvements from the PCB design, PCB processing and PCB materials.%孔壁分离是PCB及PCBA热处理过程中出现的一种缺陷,而且随着无铅化的到来,出现的频率越来越高。
孔壁分离的影响因素较多,从PCB设计、PCB加工、PCB原材料性能等多个方面进行影响分析,并提出相应的改善措施。
【期刊名称】《印制电路信息》【年(卷),期】2011(000)012【总页数】3页(P50-51,62)【关键词】PCB;孔壁分离;除胶渣;化学铜【作者】杨波;温东华;吴小连【作者单位】广东生益科技股份有限公司,广东东莞523039;广东生益科技股份有限公司,广东东莞523039;广东生益科技股份有限公司,广东东莞523039【正文语种】中文【中图分类】TN411 前言孔壁分离是PCB及PCBA热处理(热风整平锡、热冲击、回流焊)过程中,电镀通孔的孔壁铜与基材出现分离的一种缺陷,一旦出现将给PCB下游埋下可靠性隐患,如在PCB下游客户或终端因此缺陷出现可靠性问题,将给PCB生产厂家带来不利影响并伴随着巨额索赔。
所以孔壁分离问题一直困扰着PCB厂家及相关供应商并倍受关注。
- 1、下载文档前请自行甄别文档内容的完整性,平台不提供额外的编辑、内容补充、找答案等附加服务。
- 2、"仅部分预览"的文档,不可在线预览部分如存在完整性等问题,可反馈申请退款(可完整预览的文档不适用该条件!)。
- 3、如文档侵犯您的权益,请联系客服反馈,我们会尽快为您处理(人工客服工作时间:9:00-18:30)。
详谈pcb钻孔孔壁镀铜开裂问题及解决方案
-豆丁
篇一:镀铜的工艺过程
体钯活化液过早聚沉。
因此,在活化处理前要先在含有Sn2+的酸性溶液中进行预浸处理1~2min,取出后直接浸入胶体钯活化液中进行活化处理。
配制时应首先将盐酸与水相混合,然后再加入SnCl2?2H2O ,搅拌溶解,这样可防止SnCl2水解。
酸基胶体钯预浸液配方:
氯化亚锡() 70~100g/L
盐酸37%(体积) 200-300ml/L
盐基胶体钯预浸液配方:
30g/L
HCl 30ml/l
NaCl200g/l
O
║
H2N-C-NH250g/l
b.活化处理-在室温条件下处理3~5min,在处理过程中应不断移动覆铜箔板,使活化液在孔内流动,以便在孔壁上形成均匀的催化层。
c.解胶处理-活化处理后,在基材
表面吸附着以钯粒子为核心,在钯核的周围,具有碱式锡酸盐的胶体化合物。
在化学镀铜前,应将碱式锡酸盐去除,使活性的钯晶核充分暴露出来,从而使钯晶核具有非常强而均匀的活性。
经过解胶处理再进行化学镀铜,不但提高了胶体钯的活性,而且也显著提高化学镀铜层与基材间的结合强度。
常用的解胶处理液是5%的氢氧化钠水溶液或1%氟硼酸水溶液。
解胶处理在室温条件下处理1~2min,水洗后进行化学镀铜。
d.胶体铜活化液简介:
明胶 2g/l
/l
DMAB(二甲胺基硼烷)5g/l
水合肼 10 g/l
钯20ppm
配制过程:首先分别将明胶和硫酸铜用温水(40度C)溶解后将明胶加入至硫酸铜的溶液中,用25%H2SO4将PH值调至2..5当温度为45度C时,将溶解后DMAB在搅拌条件下缓慢加入上述的混合溶液中,并加入去离子稀释至1升,保温40~45度C,并搅拌至反应开始(约5~10分钟)溶液的颜色由蓝再变成绿色。
放置24小时颜色变成红黑色后加入水合肼。
篇二:PCB线路板镀铜表面粗糙问题原因分析
PCB线路板镀銅表面粗糙问题原因分析
可能原因如下:
镀铜槽本身的问题
1、阳极问题:成分含量不当导致产生杂质
2、光泽剂问题(分解等)
3、电流密度不当导致铜面不均匀
4、槽液成分失调或杂质污染
5、设备设计或组装不当导致电流分布太差
…………
当然作为镀铜本身来讲;以上问题导致粗糙的可能性不大前制程问题
PTH制程带入其他杂质:
1、活化成分失调钯浓度太高或者预浸盐残留板面
2、速化失调板面镀铜是残有锡离子
3、化学铜失调板面沉铜不均
4、镀铜前酸洗不当导致板面残留杂质
………………
黑孔制程:
微蚀不净导致残碳
抗氧化不当导致板面不良
烘干不良导致微蚀无法将板面碳剥除导致残碳电流输入输出不当导致板面不良…………
篇三:化学镀铜常见故障和纠正方法-PCB工艺论文,SMT 技术文章-SMT专家网
化学镀铜常见故障和纠正方法
◎化学镀铜常见故障和纠正方法
故障发生原因纠正方法
化学镀铜空洞①钻孔粉尘,孔化后脱落①检查吸尘器,钻头质量,转速/进给等
②加强去毛刺的高压水冲洗
钻孔后孔壁裂缝或内层间分离检查钻头质量,转速/进给,以及层压板厚材料和层压工艺条件③除钻污过度,造成树脂变成海绵状,引起水洗不良和镀层脱落检查除钻污法工艺,适当降低去钻污强度
④除钻污后中和处理不充分,残留Mn残渣检查中和处理工艺
⑤清洁调整不足,影响Pd的吸附检查清洗调整处理工艺(如浓度、温度、时间)及副产物是否过量
⑥活化液浓度偏低影响Pd吸附检查活化处理工艺补充活化剂
⑦加速处理过度,在去除Sn的同时Pd也被除掉检查加速处理工艺条件(温度/时间/浓度)如降低加速剂浓度或浸板时间
⑧水洗不充分,使各槽位的药水相互污染检查水洗能
力,水量/水洗时间
⑨孔内有气泡加设摇摆、震动等
⑩化学镀铜液的活性差检查NaOH、HCHO、Cu2+的浓度以及溶液温度等
⑾反应过程中产生气体无法及时逸出加强移动、振动和空气搅拌等。
以及降低温度表面张力。
化学镀铜层分层或起泡①层压板在层压时铜箔表面粘附树脂层加强环境管理和规范叠层操作②来自钻孔时主轴的油,用常规除油清洁剂无法除去定期进行主轴保养
③钻孔时固定板用的胶带残胶选择无残胶的胶带并检查清除残胶
④去毛刺时水洗不够或压力过大导致刷辊发热后在板面残留刷毛的胶状物检查去毛刺机设备,并按规范操作
⑤除钻污后中和处理不充分表面残留Mn化合物检查中和处理工艺时间/温度/浓度等
⑥各步骤之间水洗不充分特别是除油后水洗不充分,表面残留表面活性剂检查水洗能力水量/水洗时间等
⑦微蚀刻不足,铜表面粗化不充分检查微蚀刻工艺溶液温度/时间/浓度等
⑧活化剂性能恶化,在铜箔表面发生置换反应检查活化处理工艺浓度/温度/时间以副产物含量。
必要时应更换槽液
⑨活化处理过度,铜表面吸附过剩的Pd/Sn,在其后不
能被除去检查活化处理工艺条件⑩加速处理不足,在铜表面残留有Sn的化合物检查加速处理工艺温度/时间/浓度⑾加速处理液中,Sn含量增加更换加速处理液
⑿化学镀铜前放置时间过长,造成表面铜箔氧化检查循环时间和滴水时间
⒀化学镀铜液中副产物增加导致化学镀铜层脆性增大检查溶液的比重,必要时更换或部分更换溶液
⒁化学镀铜液被异物污染,导致铜颗粒变大同时夹杂氢气检查化学镀铜工艺条件
湿度/时间/溶液负荷检查溶液组份浓度,严禁异物带入。
产生瘤状物或孔粗①化学镀铜液过滤不足,板面沉积有颗粒状物检查过滤系统和循环量,定期更换滤芯
②化学镀铜液不稳定快分解,产生大量铜粉检查化学镀铜工艺条件:温度/时间/负荷/浓度加强溶液的管理
③钻孔碎屑粉尘检查钻孔条件,钻头质量和研磨质量
加强去毛刺高压水洗
④各槽清洗不足,有污染物积聚,在孔里或表面残留定期进行槽清洁保养
⑤水洗不够,导致各槽药水相互污染并产生残留物加强水洗能力水量/水洗时间等⑥加速处理液失调或失效调整或更换工作液
电镀后孔壁无铜①化学镀铜太薄被氧化增加化学镀铜厚度
②电镀前微蚀处理过度调整微蚀强度
③电镀中孔内有气泡加电镀震动器
孔壁化学铜底层有阴影钻污未除尽加强去除钻污处理强度,提高去钻污能力。
孔壁不规整①钻孔的钻头陈旧更换新钻头
②去钻污过强,导致树脂蚀刻过深而露玻璃纤维调整去钻污的工艺条件,降低去钻污能力。