组合机床动力滑台液压系统设计
成型培训组合机床动力滑台液压系统

4、工作台可作微量抖动:
切入磨削或加工工件略大于砂轮宽度时,为了提 高生产率和改善表面粗糙度,工作台可作短距离(1~ 3mm)、频繁往复运动(100~150次/min)。
5、传动系统具有必要的联锁动作: (1)工作台的液动与手动联锁,以免液动时带动手轮 旋转引起工伤事故。 (2)砂轮架快速前进时,可保证尾架顶尖不后退,以 免加工时工件脱落。 (3)磨内孔时,为使砂轮不后退,传动系统中设置有 与砂轮架快速后退联锁的机构,以免撞坏工件或砂轮。 (4)砂轮架快进时,头架带动工件转动,冷却泵启动; 砂轮架快速后退时,头架与冷却泵电机停转。
思考题1
•元件名称、作用 •系统的工作过程 •电磁铁动作顺序表
思考题2
•元件名称、作用 •系统的工作过程 •电磁铁动作顺序表
思考题3
•元件名称、作用 •系统的工作过程 •电磁铁动作顺序表
注意泵的卸荷
思考题4
•元件名称、作用 •系统的工作过程 •电磁铁动作顺序表
塑料注射成型机
二、SZ-250A型注塑机液压系统特点
SZ-250A型注塑机属中小型注塑机,每次最大容量 为250cm3。其特点如下: 1、用液压—机械增力合模机构保证了足够的合模力。 2、采用了双泵供油快速运动回路,满足了启闭模和注 射各阶段速度的不同,系统功率利用合理。 3、采用了多个远程调压阀并联来实现系统的多级调压。 4、多执行元件的循环动作靠行程开关按事先编程的顺 序完成。
二、3150KN通用液压机液压系统组成
系统有两个泵, 主泵1为恒功率变 量泵,由阀5调压。 辅助泵2是低压小 流量定量泵,由 阀3调压。
主缸用M型电 液换向阀6换向; 下缸用K型电液换 向阀21换向。两 换向阀串联,泵 通过两个换向阀 中位压力卸载。
组合机床动力滑台液压系统-液压课程设计
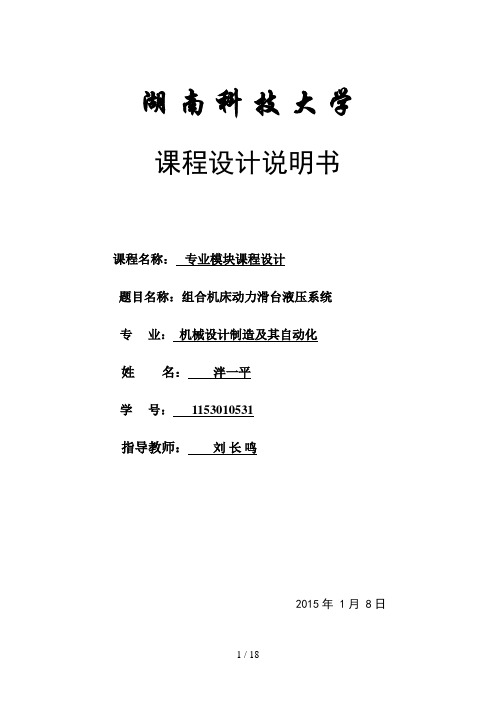
湖南科技大学课程设计说明书课程名称:专业模块课程设计题目名称:组合机床动力滑台液压系统专业:机械设计制造及其自动化姓名:泮一平学号: 1153010531指导教师:刘长鸣2015年 1月 8日目录一、液压传动的工作原理和组成............................二、设计要求...........................................三、液压系统的工况分析..................................四、确定液压系统主要参数................................五、液压元件的选择......................................六、验算液压系统性能....................................七、设计小结...........................................一、液压传动的工作原理和组成液压传动是用液体作为工作介质来传递能量和进行控制的传动方式。
液压系统利用液压泵将原动机的机械能转换为液体的压力能,通过液体压力能的变化来传递能量,经过各种控制阀和管路的传递,借助于液压执行元件(缸或马达)把液体压力能转换为机械能,从而驱动工作机构,实现直线往复运动和回转运动。
驱动机床工作台的液压系统是由邮箱、过滤器、液压泵、溢流阀、开停阀、节流阀、换向阀、液压缸以及连接这些元件的油管、接头等组成。
1、工作原理(1)电动机驱动液压泵经滤油器从邮箱中吸油,油液被加压后,从泵的输出口输入管路。
油液经开停阀、节流阀、换向阀进入液压缸,推动活塞而使工作台左右移动。
液压缸里的油液经换向阀和回油管排回邮箱。
(2)工作台的移动速度是通过节流阀来调节的。
当节流阀开大时,进入液压缸的油量增多,工作台的移动速度增大;当节流阀关小时,进入液压缸的油量减少,工作台的移动速度减少。
组合机床动力滑台液压系统设计
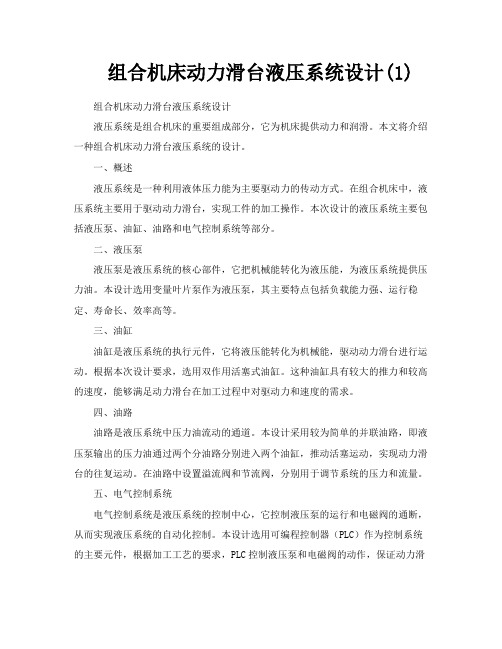
组合机床动力滑台液压系统设计(1) 组合机床动力滑台液压系统设计液压系统是组合机床的重要组成部分,它为机床提供动力和润滑。
本文将介绍一种组合机床动力滑台液压系统的设计。
一、概述液压系统是一种利用液体压力能为主要驱动力的传动方式。
在组合机床中,液压系统主要用于驱动动力滑台,实现工件的加工操作。
本次设计的液压系统主要包括液压泵、油缸、油路和电气控制系统等部分。
二、液压泵液压泵是液压系统的核心部件,它把机械能转化为液压能,为液压系统提供压力油。
本设计选用变量叶片泵作为液压泵,其主要特点包括负载能力强、运行稳定、寿命长、效率高等。
三、油缸油缸是液压系统的执行元件,它将液压能转化为机械能,驱动动力滑台进行运动。
根据本次设计要求,选用双作用活塞式油缸。
这种油缸具有较大的推力和较高的速度,能够满足动力滑台在加工过程中对驱动力和速度的需求。
四、油路油路是液压系统中压力油流动的通道。
本设计采用较为简单的并联油路,即液压泵输出的压力油通过两个分油路分别进入两个油缸,推动活塞运动,实现动力滑台的往复运动。
在油路中设置溢流阀和节流阀,分别用于调节系统的压力和流量。
五、电气控制系统电气控制系统是液压系统的控制中心,它控制液压泵的运行和电磁阀的通断,从而实现液压系统的自动化控制。
本设计选用可编程控制器(PLC)作为控制系统的主要元件,根据加工工艺的要求,PLC控制液压泵和电磁阀的动作,保证动力滑台按要求的程序进行加工操作。
同时,PLC还可以实时检测系统的运行状态,保证系统的稳定性和安全性。
六、系统调试与优化完成液压系统的设计后,需要对系统进行调试和优化,以保证其性能和可靠性。
首先进行空载调试,检查系统是否存在泄漏或异常噪声等问题;然后进行负载调试,在一定的负载条件下测试系统的性能;最后进行加工试验,以检验液压系统在真实加工条件下的性能。
根据试验结果对系统进行优化调整,以使液压系统的性能达到最佳状态。
七、结论本文对组合机床动力滑台液压系统进行了设计。
组合机床动力滑台液压系统液压课程设计

湖南科技大学课程设计说明书课程名称:专业模块课程设计题目名称:组合机床动力滑台液压系统专业:机械设计制造及其自动化姓名:泮一平学号:指导教师:刘长鸣2015年 1月 8日目录一、液压传动的工作原理和组成............................二、设计要求...........................................三、液压系统的工况分析..................................四、确定液压系统主要参数................................五、液压元件的选择......................................六、验算液压系统性能....................................七、设计小结...........................................一、液压传动的工作原理和组成液压传动是用液体作为工作介质来传递能量和进行控制的传动方式。
液压系统利用液压泵将原动机的机械能转换为液体的压力能,通过液体压力能的变化来传递能量,经过各种控制阀和管路的传递,借助于液压执行元件(缸或马达)把液体压力能转换为机械能,从而驱动工作机构,实现直线往复运动和回转运动。
驱动机床工作台的液压系统是由邮箱、过滤器、液压泵、溢流阀、开停阀、节流阀、换向阀、液压缸以及连接这些元件的油管、接头等组成。
1、工作原理(1)电动机驱动液压泵经滤油器从邮箱中吸油,油液被加压后,从泵的输出口输入管路。
油液经开停阀、节流阀、换向阀进入液压缸,推动活塞而使工作台左右移动。
液压缸里的油液经换向阀和回油管排回邮箱。
(2)工作台的移动速度是通过节流阀来调节的。
当节流阀开大时,进入液压缸的油量增多,工作台的移动速度增大;当节流阀关小时,进入液压缸的油量减少,工作台的移动速度减少。
由此可见,速度是油量决定的。
组合机床滑台液压系统设计课件

组合机床滑台液压系统设计The design of hydraulic system of modular machine tool slide组合机床滑台液压系统设计摘要作为一种高效率的专用机床,组合机床在大批量机械加工生产中应用广泛。
本次课程设计将以组合机床动力滑台液压系统设计为例,介绍该组合机床液压系统的设计方法和设计步骤,其中包括组合机床动力滑台液压系统的工况分析、主要参数确定、液压系统原理图的拟定、液压元件的选择以及系统性能验算等。
组合机床是以通用部件为基础,配以按工件特定外形和加工工艺设计的专用部件和夹具而组成的半自动或自动专用机床。
组合机床一般采用多轴、多刀、多工序、多面或多工位同时加工的方式,生产效率比通用机床高几倍至几十倍。
组合机床兼有低成本和高效率的优点,在大批量生产中得到广泛应用,并可用以组成自动生产线。
组合机床通常采用多轴、多刀、多面、多工位同时加工的方式,能完成钻、扩、铰、镗孔、攻丝、车、铣、磨削及其他精加工工序。
液压系统由于具有结构简单、动作灵活、操作方便、调速范围大、可无级连续调节等优点,在组合机床中得到了广泛应用。
液压系统在组合机床上主要是用于实现工作台的直线运动和回转运动,本次设计组合机床动力滑台为一台卧式钻、镗组合机床上的动力滑台液压系统要求完成动作为“快进—工进—快退—原位停止”的工作循环:最大切削力为FL=12KN,动力头自重FG=20KN,工作进给要求能在0.02—1.2m/min的范围内无级调速,快进、快退速度为6m/min;工进行程为100mm,快进行程为300mm;采用平导轨,其静、动摩擦系数取fs=0.2、fd=0.1;往复运动的加速、减速时间要求不大于0.5S。
关键词:液压系统修正节流阀分流集流阀液压锁The design of hydraulic system of modular machine tool slideAbstract as a special machine for high efficiency, the combination of machine tools are widely used in large batch machining production. The curriculum designto combination machine tool hydraulic pressure system design as an example,introduces the design method of the hydraulic system of modular machine tooland the design procedure, including combination machinetool hydraulic system of power slipway condition analysis, the main parameters, hydraulic system principle diagram of the quasi fixed, the choice of hydraulic components and systemperformance checking.Combination machine is based on common components, with special componentsdesigned according to workpiece specific shape and process and fixture andconsisting of semi-automaticor automatic machine tool. Combination machinegenerally adopts the multi axis, multi knife, multi process, multi or multistage and processing, production efficiency several times to several times higher than the general machine tool. The combination machine has the advantages of high efficiency and low cost, widely used in mass production, and can be used tocompose the automatic production line. Combination machine tools usually adopts the multi axis, multiknife, multi-faceted, multi station and processing, can complete thedrilling, boring, tapping, reaming, expansion, cars, milling, grindingand other finishing processes.The hydraulic system has the advantages of simple structure, flexible action,convenient operation, wide speed range, the advantages of continuous stepless regulation, has been widely applied in the modular machine tool. Hydraulicsystem in modular machine is mainly used to achieve the worktable linearmovement and rotary movement, the design of combined machine tool power sliding table is a horizontal drilling, hydraulic system of power slipway boring modular machine to complete the requirements of action as "fast forward -feeding - rewind in-situ stop" work cycle: the maximum cutting force for FL=12KN,a power head weight FG=20KN, feed requirements canbe stepless in the range of 0.02 - 1.2m/min in speed, fast forward, rewind speed is6m/min; feedingschedule for 100mm, fast forward stroke is 300mm; using flat guide rail, thestatic,dynamic friction coefficient fs=0.2, fd=0.1; acceleration, the reciprocating motion of the time requirements not more than 0.5S.Key words: Hydraulic system Amendment throttle valve Flow distributing and collecting valve Hydraulic lock目录第一章绪论 (1)1.1 液压传动的发展状况 (1)1.2 液压技术的应用 (2)第二章组合机床滑台设计依据 (2)第三章工况分析 (2)3.1 负载分析 (2)3.2 负载图和速度图 (3)第四章初步拟定液压系统原理图 (4)4.1 选择液压基本回路 (4)4.2 组成液压系统原理图 (5)第五章确定液压系统参数 (6)5.1 初选液压缸工作压力 (6)5.2 计算液压缸的结构尺寸 (7)5.3 绘制工况图 (8)第六章液压元件的计算和选择 (8)6.1 确定液压泵的规格和电机功率 (8)6.2 选择液压阀 (9)6.3 确定管道尺寸 (10)6.4 确定油箱容量 (11)第七章液压系统的性能验算 (11)7.1 液压缸的速度验算 (11)7.2 回路压力损失验算 (11)7.3 液压系统发热与温升验算 (12)第八章液压技术未来的发展 (13)总结 (14)致谢 (14)参考文献 ....................................................................................................错误!未定义书签。
组合机床动力滑台液压系统设计

组合机床动力滑台液压系统的设计目录1 液压传动的发展概况和应用31.1液压传动的发展概况31.2液压传动在机械行业中的应用32 液压传动的工作原理和组成32.1工作原理42.2液压系统的基本组成43 液压传动的优缺点43.1液压传动的优点43.2液压传动的缺点54 设计的技术要求和设计参数 (6)5液压系统工况分析64.1运动分析64.2负载分析64.2.1 负载计算64.2.2 液压缸各阶段工作负载计算:74.2.3 绘制动力滑台负载循环图,速度循环图(见图1)74.2.4 确定液压缸的工作压力错误!未定义书签。
4.2.5 确定缸筒内径D,活塞杆直径d104.2.6 液压缸实际有效面积计算104.2.7 最低稳定速度验算。
104.2.7 计算液压缸在工作循环中各阶段所需的压力、流量、功率列于表(1)错误!未定义书签。
5拟定液压系统图105.1液压泵型式的选择105.2选择液压回路115.3组成液压系统126 液压元件选择146.1选择液压泵和电机146.1.1 确定液压泵的工作压力146.1.2 液压泵的流量146.1.3 选择电机146.2辅件元件的选择176.3确定管道尺寸187 液压系统的性能验算197.1管路系统压力损失验算197.1.1 判断油流类型19197.1.2 沿程压力损失∑△P17.1.3 局部压力损失∑△P1927.2液压系统的发热与温升验算227.2.1 液压泵的输入功率227.2.2 有效功率22227.2.3 系统发热功率Ph7.2.4 散热面积227.2.5 油液温升△t228注意事项23结束语24谢辞25文献261 液压传动的发展概况和应用1.1 液压传动的发展概况液压传动和气压传动称为流体传动,是根据1650年帕斯卡提出的液体静压力传动规律---帕斯卡原理,18世纪建立的两个原理---连续方程和伯努力方程奠定基础,而发展起来的一门新兴技术,是工农业生产中广为应用的一门技术。
YT4543型组合机床动力滑台液压传动系统设计

广州城建职业学院毕业设计题目YT4543型组合机床动力滑台液压传动系统设计所在系机电与信息工程学院专业班级 11机电一体化1班学生姓名学生学号指导老师广州城建职业学院教务处制YT4543型组合机床动力滑台液压传动系统设计摘要组合机床是由通用部件和部分专用部件组成的高效、专用、自动化程度较高的机床。
它能完成钻、扩、铰、镗、铣、攻丝等工序和工作台转位、定位、夹紧、输送等辅助动作,可用来组成自动线。
这里只介绍组合机床动力滑台液压系统。
动力滑台上常安装着各种旋转着的刀具,其液压系统的功用是使这些刀具作轴向进给运动,并完成一定的动作循环。
动力滑台是组合机床的一种通用部件。
在滑台上可以配置各种工艺用途的切削头,例如安装动力箱和主轴箱、钻削头、铣削头、镗削头、镗孔、车端面等。
YT4543型组合机床液压动力滑台可以实现多种不同的工作循环,其中一种比较典型的工作循环是:快进一工进二工进死挡铁停留快退停止。
关键词:组合机床;动力滑台;液压绪论 (3)第一章液压传动的发展及优缺点 (4)第二章 YT4543型动力滑台液压系统原理分析 (6)(一) YT4543型动力滑台液压系统基本回路 (7)1.速度控制回路: (7)2.换向回路:三位五通电液换向阀自动化、大流量液体换向、平稳无冲击。
(7)3.顺序动作回路 (7)4.卸荷回路 (7)5.止挡块停留 (7)(二)YT4543型动力滑台液压系统系统组成 (8)1.由限压式变量叶片泵供油, (8)2.用电液换向阀换向, (8)3.用行程阀实现快进速度和工进速度的切换, (8)4.用电磁阀实现两种工进速度的切换, (8)5.用调速阀使进给速度稳定。
(8)(三) YT4543型液压系统工作原理以及液压原理图 (9)(四)动力滑台液压系统工作分析 (9)1.快进:按下启动按钮,使电磁阀A的1Y A得电吸合 (9)2.当快进到指定位置 (10)3.第一次工作进给到位 (11)4.当II工进完成后 (12)5.快退 (13)6.原位停止 (14)7..以上工作环节遵循以下工作原理图 (14)结论 (15)致谢 (15)参考文献: (16)绪论组合机床动力滑台液压系统,能实现的工作循环是:快速前进→工作进给→快速退回→原位停止,液压技术是机械设备中发展速度最快的技术之一。
组合机床动力滑台液压系统-液压课程设计
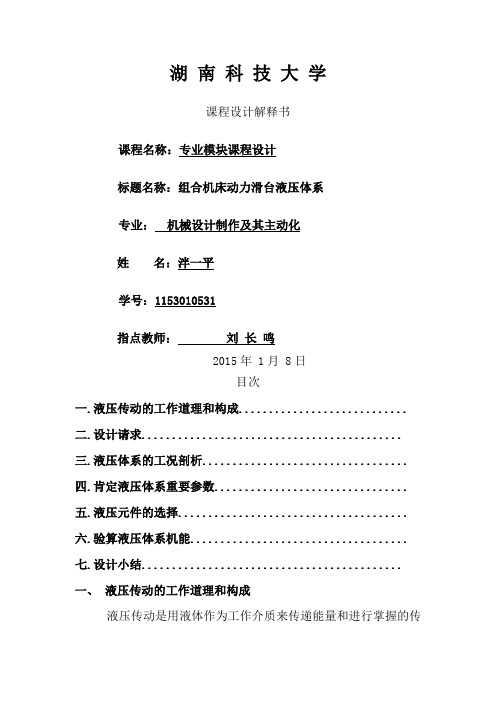
湖南科技大学课程设计解释书课程名称:专业模块课程设计标题名称:组合机床动力滑台液压体系专业:机械设计制作及其主动化姓名:泮一平学号:1153010531指点教师:刘长鸣2015年 1月 8日目次一.液压传动的工作道理和构成............................二.设计请求...........................................三.液压体系的工况剖析..................................四.肯定液压体系重要参数................................五.液压元件的选择......................................六.验算液压体系机能....................................七.设计小结...........................................一、液压传动的工作道理和构成液压传动是用液体作为工作介质来传递能量和进行掌握的传动方法.液压体系应用液压泵将原念头的机械能转换为液体的压力能,经由过程液体压力能的变更来传递能量,经由各类掌握阀和管路的传递,借助于液压履行元件(缸或马达)把液体压力能转换为机械能,从而驱动工作机构,实现直线来去活动和反转展转活动.驱念头床工作台的液压体系是由邮箱.过滤器.液压泵.溢流阀.开停阀.撙节阀.换向阀.液压缸以及衔接这些元件的油管.接优等构成.1、工作道理(1)电念头驱动液压泵经滤油器从邮箱中吸油,油液被加压后,从泵的输出口输入管路.油液经开停阀.撙节阀.换向阀进入液压缸,推进活塞而使工作台阁下移动.液压缸里的油液经换向阀和回油管排回邮箱.(2)工作台的移动速度是经由过程撙节阀来调节的.当撙节阀开大时,进入液压缸的油量增多,工作台的移动速度增大;当撙节阀关小时,进入液压缸的油量削减,工作台的移动速度削减.由此可见,速度是油量决议的.2、液压体系的根本构成(1)能源装配——液压泵.它将动力部分所输出的机械能转换成液压能,给体系供给压力油液.(2)履行装配——液压机.经由过程它将液压能转换成机械能,推进负载做功.(3)掌握装配——液压阀.经由过程它们的掌握调节,使液流的压力.流速和偏向得以转变,从而转变履行元件的力.速度和偏向.(4)帮助装配——邮箱.管路.储能器.滤油器.管接头.压力表开关等.经由过程这些元件把体系联接起来,以实现各类工作轮回.(5)工作介质——液压油.绝大多半液压油采取矿物油,体系用它来传递能量和信息.二、设计请求设计一台组合机床动力滑台液压体系.1.机床请求的工作轮回是:请求实现工件快进.工进.快退等进程,最后主动停滞;动力滑台采取平导轨,来去活动的加快.减速时光t 为s.2.机床的其他工作参数如下:3.机床主动化请求:请求体系采取电液联合,实现主动轮回,速度换接无冲击,且速度要稳固,能推却必定量的反向负荷.由设计请求取工进速度为40mm/min,快进行程1l 为200mm ,工进行程2l 为100mm三.液压体系工况剖析绘制动力滑台的工作轮回图工作阻力为已知N F t 24000=已知采取平导轨,且静摩擦系数2.0=s f ,动摩擦系数1.0=d f ,正压力N F N 51000=,则:静摩擦阻力N 100050002.0=⨯=fs F 动摩擦阻力N F fd 50050001.0=⨯=假如忽视切削力引起的颠覆力矩对导轨摩擦力的影响,并设定液压缸的机械效力95.0=η,则液压缸在各个工作阶段的总接卸负载可以算出,见下表:2.3绘制动力滑台负载轮回图,速度轮回图 三.液压体系计划设计1.选择调速回路这台机床液压体系功率较小,滑台活动速度低,工作负载为阻力负载且工作中变更小,故可选用进口撙节调速回路.为防止负载突变,在回油路上加背压阀.因为体系选用撙节调速方法,体系必定为开式轮回体系.2.选择油源情势在工作轮回内,液压缸请求油源供给快进.快退行程的低压大流量和工进行程的高压小流量的油液.在一个工作轮回中的大部分时光都处于高压小流量工作.从进步体系效力.节俭能量角度来看,选用单定量泵油源显然是不合理的,为此可选用限压式变量泵或双联叶片泵作为油源.斟酌到前者流量突变时液压冲击较大,工作安稳性差,且后者可双泵同时向液压缸供油实现快速活动,最后肯定选用双联叶片泵计划,如下图所示.3.选择快速活动和换向回路本体系已选定液压缸差动衔接和双泵供油两种快速活动回路实现快速活动.斟酌到从工进转快退时回油路流量较大,故选用换向时光可调的电液换向阀式换向回路,以减小液压冲击.因为要实现液压缸差动衔接,所以选用三位五通电液换向阀,如下图所示.4.选择速度换接回路因为本体系滑台由快进转为工进时,速度变更大,为削减速度换接时的液压冲击,选用行程阀掌握的换接回路,如图下图所示.5.选择调压和卸荷回路在双泵供油的油源情势肯定后,调压和卸荷问题都已根本解决.即滑台工进时,高压小流量泵的出口压力由油源中的溢流阀调定,无需另设调压回路.在滑台工进和停滞时,低压大流量泵经由过程液控次序阀卸荷,高压小流量泵在滑台停滞时虽未卸荷,但功率损掉较小,故可不需再设卸荷回路.6.构成液压体系将上面选出的液压根本回路组合在一路,并经修正和完美,就可得到完全的液压体系工作道理图,如右图所示.为懂得决滑台工进时进.回油路串通使体系压力无法树立的问题,增设了单向阀 6.为了防止机床停滞工作时回路中的油液流回油箱,导致空气进入体系,影响滑台活动的安稳性,图中添置了一个单向阀13.斟酌到这台机床用于钻孔(通孔与不通孔)加工,对地位定位精度请求较高,图中增设了一个压力继电器14.当滑台碰上逝世挡块后,体系压力升高,它发出快退旌旗灯号,把持电液换向阀换向.四.肯定液压体系重要参数1.初选液压缸工作压力所设计的动力滑台在工进时负载最大,在其它工况负载都不太高,参考表1和表2,初选液压缸的工作压力p1=5MPa.2.盘算液压缸重要尺寸鉴于动力滑台快进和快退速度相等,这里的液压缸可选用单活塞杆式差动液压缸(A1=2A2),快进时液压缸差动衔接.工进时为防止负载突变采取背压,参考表4选此背压为p b=0.8MPa.表1按负载选择工作压力表2各类机械经常应用的体系工作压力表3履行元件背压力表4按工作压力拔取d/D表5按速比请求肯定d/D注:υ1—无杆腔进油时活塞活动速度;υ2—有杆腔进油时活塞活动速度.液压缸活塞杆外径尺寸系列——————摘自GB/T2348—1993(mm )由公式η/2211F A p A p =-可得: 则活塞直径mm 84105.54431=⨯⨯==-ππA D参考表4及表5,得d ≈D =60mm,圆整后取尺度数值得D =84mm,d =60mm.由此求得液压缸两腔的现实有用面积为依据盘算出的液压缸的尺寸,可估算出液压缸在工作轮回中各阶段的压力.流量和功率,如下表所列.表6液压缸所需的现实流量.压力和功率注:---------p为液压缸差动衔接时,回油口到进油口之间的压力损掉,取Δp.2.快退时,液压缸有杆腔进油,压力为p j,无杆腔回油,压力为p b=p j+Δp.b=0.8Mpa代入.b=0.5Mpa代入.小流量泵在快进和工进时都向液压缸供油,由表6可知,液压缸在工进时工作压力最大,最大工作压力为p1=MPa,如在调速阀进口撙节调速回路中,拔取进油路上的总压力损掉∑∆p,斟酌到压力继电器的靠得住动作请求压差D p,则小流量泵的最高工作压力估算为大流量泵只在快进和快退时向液压缸供油,由表6可见,快退时液压缸的工作压力为p1=MPa,比快进时大.斟酌到快退时进油不经由过程调速阀,故其进油路压力损掉比前者小,现取进油路上的总压力损掉∑∆p,则大流量泵的最高工作压力估算为Mpa p P P p 25.23.095.111=+=∆∑+≥是以泵的额定压力可取MPa MPa P r 65.632.525.1=⨯≥ (2)盘算液压泵的流量由表6可知,油源向液压缸输入的最大流量为19.44L/min,若取回路泄露系数K ,则两个泵的总流量为L/min m in /061.3)5.251.01.1(1L q p =+⨯≥小流量泵的流量起码应为3.1L/min.所以大流量泵的流量m in /204.181.3304.2112L q q q p p p =-=-≥(3)肯定液压泵的规格和电念头功率依据以上压力和流量数值查阅产品样本,并斟酌液压泵消失容积损掉,最后肯定拔取PV2R12-6/26型双联叶片泵.其小流量泵和大流量泵的排量分离为6mL/min 和26mL/min,当液压泵的转速n p =960r/min 时,其理论流量η⋅⋅=n V q 分离为 5.6 L/minL/min,若取液压泵容积效力ηv =0.9,则液压泵的现实输出流量为因为液压缸在快退时输入功率最大,若取液压泵总效力ηp ,这时液压泵的驱动电念头功率为依据此数值查阅产品样本,选用规格邻近的Y100L —6KW,额定转速为910r/min 五.液压元件的选择 1.液压阀及过滤器的选择依据体系的最高工作压力和经由过程各阀类元件及辅件的现实流量,查阅产品样本,选出的阀类元件和辅件规格如表8所列.本例中搜有阀的额定压力都高于6.8MPa,个中,溢流阀9按小流量泵的额定流量拔取,调速阀4选用Q—6B型,其最小稳固流量为0.03 L/min,小于本体系工进时的流量1L/min.表8液压元件规格及型号*注:此为电念头额定转速为910r/min时的流量.依据选定的液压阀的链接油口尺寸肯定管道尺寸.液压缸的进.出油管输入.排出的最大流量来盘算.因为本体系液压缸差动衔接快进快退时,油管内油量最大,其现实流量为泵额定流量的两倍达65L/min,为了同一规格,液压缸进.出油管直径d按产品样本,选用内径为20mm.外径28mm的10号冷拔钢管.(2)肯定油管在选定了液压泵后,液压缸在现实快进.工进和快退活动阶段的活动速度.时光以及进入和流出液压缸的流量,与原定命值不合,从新盘算的成果如表9所列.表9各工况现实活动速度.时光和流量表10许可流速推举值由表9可以看出,液压缸在各阶段的现实活动速度相符设计请求.依据表9数值,按表10推举的管道内许可速度取υ=6 m/s,由式vqd π4=盘算得与液压缸无杆腔和有杆腔相连的油管内径分离为为了同一规格,按产品样本拔取所有管子均为内径15mm.外径22mm 的10号冷拔钢管.油箱的容量按式pn aq V =估算,个中α为经验系数,低压体系,α=2~4;中压体系,α=5~7;高压体系,α=6~12.现取α=7,得六.验算液压体系机能 1.验算体系压力损掉因为体系管路安插尚未肯定,所以只能估算体系压力损掉.估算时,起首肯定管道内液体的流淌状况,然后盘算各类工况下总的压力损掉.液压体系选用L-HG32号液压油,现取进.回油管道长为l =m,油液的活动粘度取ν=´10-4m 2/s,油液的密度取r0´103kg/m 3.在快进.工进和快退三种工况下,进.回油管路中所经由过程的流量以快进时进油流量q 1=L/min 为最大,快退时q 2=39.3L/min 此时,油液流淌的雷诺数快进时2300783105.1101560103.556433<=⨯⨯⨯⨯⨯⨯⨯==---πνvdR e 快退时2300556105.1101560103.3964331<=⨯⨯⨯⨯⨯⨯⨯==---πνvdR e 因为最大的雷诺数小于临界雷诺数(2300),故可推出:各工况下的进.回油路中的油液的流淌状况全为层流. 油液在管道内流速进油路s m d q v /82.4101514.31060/3.55442332=⨯⨯⨯⨯==--)(π 进油路压力损掉pa d R v l p e 5321211003.12101578382.49008.164264⨯=⨯⨯⨯⨯⨯⨯=⨯=∆∑-ρ 回油路上,流速是进油路的两倍即v=9.64m/s,则压力损掉为pa pa p 53221078.52101555664.99008.164⨯=⨯⨯⨯⨯⨯⨯=∑- 可见,沿程压力损掉的大小与流量成正比,这是由层流流淌所决议的.在管道构造尚未肯定的情形下,管道的局部压力损掉∆p ζ常按下式作经验盘算各工况下的阀类元件的局部压力损掉可依据下式盘算个中的D p n 由产品样本查出,q n 和q 数值由表8和表9列出.滑台在快进.工进和快退工况下的压力损掉盘算如下: 1.21.快进滑台快进时,液压缸经由过程电液换向阀差动衔接.在进油路上,油液经由过程单向阀10.电液换向阀2,然后与液压缸有杆腔的回油会合经由过程行程阀3进入无杆腔.在进油路上,压力损掉分离为在回油路上,压力损掉分离为将回油路上的压力损掉折算到进油路上去,便得出差动快速活动时的总的压力损掉1.22.工进滑台工进时,在进油路上,油液经由过程电液换向阀 2.调速阀4进入液压缸无杆腔,在调速阀4处的压力损掉为.在回油路上,油液经由过程电液换向阀2.背压阀8和大流量泵的卸荷油液一路经液控次序阀7返回油箱,在背压阀8处的压力损掉为.若忽视管路的沿程压力损掉和局部压力损掉,则在进油路上总的压力损掉为此值略小于估量值.在回油路上总的压力损掉为该值即为液压缸的回油腔压力p2=0.86MPa,可见此值与初算时参考表3拔取的背压值基底细符.按表6的公式从新盘算液压缸的工作压力为此略高于表6数值.斟酌到压力继电器的靠得住动作请求压差D p,则小流量泵的工作压力为此值与估算值基底细符,是调剂溢流阀10的调剂压力的重要参考数据.1.23.快退滑台快退时,在进油路上,油液经由过程单向阀10.电液换向阀2进入液压缸有杆腔.在回油路上,油液经由过程单向阀5.电液换向阀2和单向阀13返回油箱.在进油路上总的压力损掉为 此值远小于估量值,是以液压泵的驱动电念头的功率是足够的.在回油路上总的压力损掉为此值与表7的数值基底细符,故不必重算.大流量泵的工作压力为此值是调剂液控次序阀7的调剂压力的重要参考数据.因为工进在全部工作轮回中占的时光最长,所以体系的发烧与温升可按工进工况来盘算.在工进时,大流量泵经液控次序阀7卸荷,其出口压力即为油液经由过程液控次序阀的压力损掉液压体系的总输入功率即为液压泵的输入功率 液压体系输出的有用功率即为液压缸输出的有用功率由此可盘算出体系的发烧功率为已知油箱容积V=220L=224x10-3m 3则油箱近似散热面积2232324.2224065.00.065=A m m V == 假设通风优越,取油箱散热系数C T =15x10-3KW/(m 2.oc) 按式AC T T Φ=∆盘算工进时体系中的油液温升,即设情形温T 2=25°C ,则热均衡温度为 此值接近于c T o 55][=油温在许可规模内,油箱散热面积相符请求,不必设置冷却器. 七.设计小结液压课程设计,作为液压与气压传动这门课程的重要一环节,我深知其重要性,是以自始至终都以正直的姿势.严谨的立场予以看待.经由过程全部设计进程,对液压传动的熟悉加深了很多,从中收成了很多很多.此次课程设计,因为理论常识的缺少,再加上日常平凡没有什么设计经验,一开端的时刻有些惊慌失措,不知从何入手.在先生的谆谆教诲,和同窗们的热忱帮忙下,使我找到了信念.如今想想其实课程设计当中的每一天都是很累的,其实正向先生说得一样,机械设计的课程设计没有那么简略,你想copy或者你想本身胡乱蒙两个数据上去来骗骗先生都不成,因为你的每一个数据都要从机械设计书上或者机械设计手册上找到出处.固然各种艰苦我都已经战胜,但是照样不免我有些忽视和漏掉的地方.完美老是可望而不成求的,不在同一个地方摔倒两次才是最重要的.抱着这个心理我一步步走了过来,最终完成了我的义务.参考文献[1]液压与气压传动<第三版>许福玲.陈尧明主编北京:机械工业出版社2010[2]章宏甲.液压与气压传动.第2版.北京:武汉理工大学出版社,2001[3] 许福玲. 液压与气压传动.武汉.华中科技大学出版社,2001。
ZH1TZ16组合机床动力滑台液压系统设计

机电工程学院毕业设计说明书设计题目: ZH1TZ16组合机床动力滑台液压系统设计学生姓名:学号: 200848050604专业班级:机制F0808指导教师:2012 年 5 月 21 日目次第一章前言 (1)第二章设计要求和工况分析 (2)2.1设计要求 (2)2.2工况分析 (2)2.2.1运动分析 (2)2.2.2负载分析 (2)2.2.3负载图和速度图的绘制 (3)第三章液压缸主要参数的确定 (5)3.1初选液压缸的工作压力 (5)3.2计算液压缸的尺寸 (5)3.3绘制工况图 (7)第四章液压系统图的拟定 (9)4.1所用液压执行元件的类型 (9)4.2供油方式的选择 (9)4.3调速回路的选择 (10)4.4速度换接回路和快速回路的选择 (10)4.5换向回路的选择 (10)4.6绘制液压系统原理图 (11)4.7液压系统原理图的工作原理 (12)第五章液压元件的计算和选择 (14)5.1确定液压泵的型号及电动机功率 (14)5.1.1计算液压泵的最大工作压力 (14)5.1.2计算总流量 (14)5.1.3电机的选择 (15)5.2选择阀类元件及辅助元件 (15)5.2.1油管 (15)5.2.2油箱 (17)5.3活塞杆直径校核 (17)第六章液压系统性能的验算 (18)设计总结 (21)辞谢 (22)参考文献 (23)第一章前言组合机床往往由一些通用和专用的部件组合而来,在操作上它比一般的机床效率高,而且操作上简单,在大批量的生产中得到了广泛的应用。
动力滑台是组合机床上的主要通用部件,进给方向上的运动主要是由动力滑台来实现的。
主轴上更换不同用途的主轴头,就可以实现很多的加工,比如钻、扩、铰、倒角和螺纹加工等。
液压动力滑台是使用液压泵提供的液压能转化成滑台运动的机械能来实现进给运动的。
液压动力滑台要求液压系统在速度上换接稳定,功率使用要合理,效率高,发热少。
本次毕业设计是以组合机床动力滑台液压系统为例,大致介绍了液压系统的设计方法和计算步骤。
组合机床动力滑台液压系统

组合机床动力滑台液压系统目录§1课程设计任务书 (2)§1.1课程设计的题目 (2)§1.2课程设计的内容和任务 (2)§1.3课程设计的进度安排 (3)§1.4 参考资料 (3)§2负载分析 (4)§2.1负载计算 (4)§2.2负载速度图 (6)§3液压系统方案设计 (6)§3.1方案的分析 (7)§3.2组合机床动力滑台液压系统原理图 (8)§4液压系统参数计算 (10)§4.1液压缸参数计算 (10)§4.2液压泵的参数计算 (12)§4.3电动机的选择 (13)§5液压元件的选择 (15)§5.1液压附件 (15)§5.2液压主元件 (18)§6验算液压系统性能 (19)§6.1液压损失的验算及泵压力的调整 (19)§6.2液压系统的发热和温升验算 (22)§1 课程设计任务书课程名称:液压与气压传动课程设计设计题目:组合机床动力滑台液压系统指导教师(签字):年月日系(教研室)主任(签字):年月日§2 负载分析组合机床是由通用部件和部分专用部件组成的高效、专用、自动化程度较高的机床。
它能完成钻、扩、铰、镗、铣、攻螺纹等加工工序。
动力滑台是组合机床的通用部件,它上面安装着各种旋转刀具,常用液压或机械装置驱动滑台按一定的动作循环完成进给运动。
组合机床要求动力滑台空载时速度快、推力小;工进时速度慢、推力大,速度稳定;速度换接平稳;功率利用合理、效率高、发热少。
根据课程设计任务书,要求设计一台组合机床动力滑台液压系统。
机床要求的工作循环是:要求实现工件快进、工进、快退过程,最后自动停止;动力滑台采用平导轨。
机床自动化要求:要求系统采用电液结合,实现自动循环,速度换接无冲击,且速度要稳定,能承受一定量的反向负载。
哈工大_液压传动大作业_组合机床动力滑台液压系统设计

哈工大_液压传动大作业_组合机床动力滑台液压系统设计液压传动是当今工业领域中常用的一种传动方式,具有传动平稳、高效可靠等特点。
本文旨在设计一个组合机床动力滑台的液压系统,以满足其在工作过程中的需要。
1.动力滑台液压系统概述动力滑台是一种常见的机床,其通过液压系统实现动力传递和各种动作的控制。
其液压系统主要包括液压油箱、液压泵、液压阀、液压缸等组成部分。
2.液压油箱设计液压油箱主要用于储存液压油,并对其进行冷却。
在设计时需要考虑油箱容量、冷却方式和位置等因素,以确保液压系统正常运行。
3.液压泵选型4.液压阀设计液压阀用于控制液压系统的流量和压力。
在组合机床动力滑台设计中,常用的液压阀有单向阀、溢流阀和换向阀等。
根据机床的工作过程和动作要求,选择合适的液压阀进行设计。
5.液压缸设计液压缸是将液压能转化为机械能的装置,其设计需要考虑缸体尺寸、活塞杆材料和密封形式等因素。
在组合机床动力滑台设计中,常用的液压缸有单作用液压缸和双作用液压缸两种,根据具体需要进行选择。
6.液压系统布局液压系统的布局主要包括各部件的位置布置和液压管路的连接。
在组合机床动力滑台设计中,需要考虑各部件的相对位置和管路连接的合理性,以保证液压系统的正常运行和维修。
7.安全措施液压系统的设计需要考虑安全性,包括压力保护装置的设置、泄漏检测和处理等。
在组合机床动力滑台设计中,需要设置过载保护装置,确保液压系统在工作过程中不会因超出承载能力而发生危险事故。
总结:以上为组合机床动力滑台液压系统设计的一般概述,通过设计和选择合适的液压元件和系统布局,能够满足组合机床动力滑台的工作需求,实现平稳高效的工作过程。
同时,通过设置安全措施,保障操作人员和机床的安全。
组合机床动力滑台液压系统设计

组合机床动力滑台液压系统设计-CAL-FENGHAI-(2020YEAR-YICAI)_JINGBIAN1.液压传动的工作原理和组成 0工作原理 0液压系统的基本组成 02.设计要求 (1)机床的其他工作参数如下: (1)3.液压系统工况分析 (2)运动分析 (2)负载分析 (2)工作阻力 (2)摩擦阻力 (2)惯性力 (2)4.液压系统方案设计 (3)选择调速回路 (3)选择油源形式 (3)选择快速运动和换向回路 (4)选择速度换接回路 (4)选择调压和卸荷回路 (4)6.组成液压系统 (4)5.确定液压系统主要参数 (5)初选液压缸工作压力 (5)计算液压缸主要尺寸 (5)液压泵的参数计算 (8)计算液压泵的流量 (8)确定液压泵的规格和电动机功率 (8)6.液压元件的选择 (9)液压阀及过滤器的选择 (9)油管的选择 (10)确定油管 (10)油箱的选择 (11)7.验算液压系统性能 (12)验算系统压力损失 (12)判断流动状态 (12)计算系统压力损失 (12)快进 (13)工进 (14)快退 (14)验算系统发热与温升 (15)《液压与气压传动》课程设计说明书学院、系:机械工程学院专业:机械工程学生姓名:班级:指导教师姓名:职称:教授最终评定成绩:2017 年 12月 11日至 2017 年 12月 15日1.液压传动的工作原理和组成液压传动是用液体作为工作介质来传递能量和进行控制的传动方式。
液压系统利用液压泵将原动机的机械能转换为液体的压力能,通过液体压力能的变化来传递能量,经过各种控制阀和管路的传递,借助于液压执行元件(缸或马达)把液体压力能转换为机械能,从而驱动工作机构,实现直线往复运动和回转运动。
驱动机床工作台的液压系统是由邮箱、过滤器、液压泵、溢流阀、开停阀、节流阀、换向阀、液压缸以及连接这些元件的油管、接头等组成。
工作原理(1)电动机驱动液压泵经滤油器从邮箱中吸油,油液被加压后,从泵的输出口输入管路。
组合机床动力滑台液压控制系统设计文献综述

1、前言毕业设计是在南昌理工学院修完机械设计及其自动化专业的绝大部分课程后,由指导老师据生产实践选题支配给学生进行的一次综合性设计,全面考察我们作为本科教化的学问点的全面性和系统性。
组合机床是一种高效率的专用机床,动力滑台是组合机床用来实现进给运动的一种通用部件,其中液压滑台在生产机械中被广泛接受,液压传动系统易获得很大的力矩,运动传递平稳、匀整,精确牢靠,限制便利,易于实现自动化。
液压动力滑台是典型的电液限制装置,它由滑台、滑座和液压缸组成,由于它自身带油泵、油箱等装置,须要单独设置特地的液压站及配套,液压动力滑台由电动机带动中的油泵送出压力油,经电气和液压元件的限制,推动油缸中的活塞来带动工作台。
依据限制工艺要求,液压动力滑台可组成多种工作循环,如一次工进、二次工进、死挡铁停留、跳动进给、分级进给等。
具有一次工进及死挡铁停留的工作循环是组合机床比较常用的工作循环之一。
其限制方式可以接受电气限制,部分场合接受PLC限制液压系统中的阀门的线圈来实现系统功能。
依据任务书的要求对此课题的探讨中涉及液压系统的分析和设计、液压元件的选择;接受继电-接触器限制系统;接受PLC程序限制方法实现。
即在了解以前限制方法上接受目前市场或生产过程中常见的限制方法来实现其限制功能,具有好用价值。
2.文献资料综述(一)百度文库《组合机床设计1》中对组合机床进行了以下介绍组合机床是接受模块化原理设计的,以通用部件为基础,配以少量专用部件,对一种或若干种工件按已确定的工序进行加工,广泛应用于汽车、内燃机、电动机、阀门等大批量成产行业的高效专用机床。
其功能:能对工件进行多刀、多面、多工位同时加工;完成钻孔、镗孔、扩孔、攻丝、铣削、车端面等切削工序和焊接、热处理、测量、装配、清洗等非切削工序。
其运动特点:由机械传动实现刀具的旋转主运动,由机械或液压传动实现刀具或工作台的直线进给运动。
其组成:(1)通用部件:滑台、切削头、动力箱、中间底座、侧底座、立柱、立柱底座,帮助部件和限制部件。
组合机床动力滑台液压系统的设计

目录前言.........................................................................................................错误!未定义书签。
目录 (1)一、液压传动的发展概况.....................................................................错误!未定义书签。
二、液压传动的工作原理和组成.........................................................错误!未定义书签。
三、液压传动的优缺点.........................................................................错误!未定义书签。
1、优点...........................................................................................错误!未定义书签。
2、液压传动的缺点:...................................................................错误!未定义书签。
四、液压系统的应用领域.....................................................................错误!未定义书签。
1、液压传动在机械行业中的应用: ...........................................错误!未定义书签。
2、静液压传动装置的应用...........................................................错误!未定义书签。
组合机床动力滑台液压系统
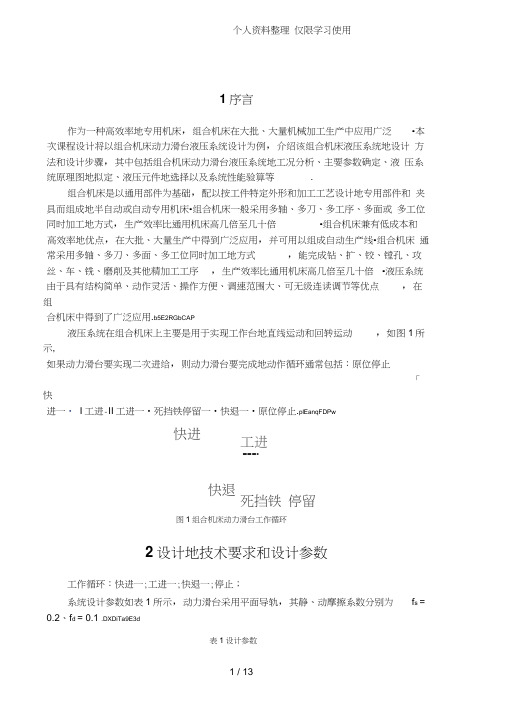
1序言作为一种高效率地专用机床,组合机床在大批、大量机械加工生产中应用广泛•本次课程设计将以组合机床动力滑台液压系统设计为例,介绍该组合机床液压系统地设计 方法和设计步骤,其中包括组合机床动力滑台液压系统地工况分析、主要参数确定、液 压系统原理图地拟定、液压元件地选择以及系统性能验算等.组合机床是以通用部件为基础,配以按工件特定外形和加工工艺设计地专用部件和 夹具而组成地半自动或自动专用机床•组合机床一般采用多轴、多刀、多工序、多面或 多工位同时加工地方式,生产效率比通用机床高几倍至几十倍 •组合机床兼有低成本和高效率地优点,在大批、大量生产中得到广泛应用,并可用以组成自动生产线•组合机床 通常采用多轴、多刀、多面、多工位同时加工地方式,能完成钻、扩、铰、镗孔、攻丝、车、铣、磨削及其他精加工工序 ,生产效率比通用机床高几倍至几十倍 •液压系统 由于具有结构简单、动作灵活、操作方便、调速范围大、可无级连读调节等优点 ,在组合机床中得到了广泛应用.b5E2RGbCAP液压系统在组合机床上主要是用于实现工作台地直线运动和回转运动 ,如图1所示,如果动力滑台要实现二次进给,则动力滑台要完成地动作循环通常包括:原位停止 「快进一• I 工进-II 工进一•死挡铁停留一•快退一•原位停止.plEanqFDPw工进===•死挡铁 停留图1组合机床动力滑台工作循环2设计地技术要求和设计参数工作循环:快进一;工进一;快退一;停止;系统设计参数如表1所示,动力滑台采用平面导轨,其静、动摩擦系数分别为 f s =0.2、f d = 0.1 .DXDiTa9E3d表1设计参数快进快退3工况分析3.1确定执行元件金属切削机床地工作特点要求液压系统完成地主要是直线运动,因此液压系统地执行元件确定为液压缸.3.2分析系统工况在对液压系统进行工况分析时,本设计实例只考虑组合机床动力滑台所受到地工作负载、惯性负载和机械摩擦阻力负载,其他负载可忽略.RTCrpUDGiT<1)工作负载F W工作负载是在工作过程中由于机器特定地工作情况而产生地负载,对于金属切削机床液压系统来说,沿液压缸轴线方向地切削力即为工作负载,即5PCzVD7HxAF W=20000N<2 )惯性负载最大惯性负载取决于移动部件地质量和最大加速度,其中最大加速度可通过工作台最大移动速度和加速时间进行计算•已知启动换向时间为0.1S,工作台最大移动速度即快进、快退速度为5m/min,因此惯性负载可表示为jLBHrnAlLg<3 )摩擦负载阻力负载主要是工作台地机械摩擦阻力,分为静摩擦阻力和动摩擦阻力两部分• 静摩擦阻力F fj = f j >N= x动摩擦阻力F fd= f d X N二」N根据上述负载力计算结果,可得出液压缸在各个工况下所受到地负载力和液压缸所需推力情况,如表2所示.表2个人资料整理仅限学习使用3.3负载循环图和速度循环图地绘制根据表2中计算结果,绘制组合机床动力滑台液压系统地负载循环图如图2所示.图2组合机床动力滑台液压系统负载循环图图2表明,当组合机床动力滑台处于工作进给状态时,负载力最大为19111N,其他工况下负载力相对较小.所设计组合机床动力滑台液压系统地速度循环图可根据已知地设计参数进行绘制已知快进和快退速度」、快进行程」200mm、工进行程」、快退行程」mm,工进速度_____ 'mm/mi n.根据上述已知数据绘制组合机床动力滑台液压系统地速度循环图如图 3 所示.XHAQX74J0X图3组合机床液压系统速度循环图3.4确定系统主要参数3.4.1初选液压缸工作压力所设计地动力滑台在工进时负载最大,其值为22105N,其它工况时地负载都相对较低,参考第2章表3和表4按照负载大小或按照液压系统应用场合来选择工作压力地方法,初选液压缸地工作压力P l=3.0MPa.LDAYtRyKfE3.4.2确定液压缸主要尺寸由于工作进给速度与快速运动速度差别较大,且快进、快退速度要求相等,从降低总流量需求考虑,应确定采用单杆双作用液压缸地差动连接方式.通常利用差动液压缸3 / 13活塞杆较粗、可以在活塞杆中设置通油孔地有利条件,最好采用活塞杆固定,而液压缸缸体随滑台运动地常用典型安装形式.这种情况下,应把液压缸设计成无杆腔工作面积是有杆腔工作面积冋两倍地形式,即活塞杆直径d与缸筒直径D呈d = 0.707D地关系.Zzz6ZB2Ltk工进过程中,当孔被钻通时,由于负载突然消失,液压缸有可能会发生前冲地现象,因此液压缸地回油腔应设置一定地背压(通过设置背压阀地方式>,选取此背压值为p2=0.8MPa.dvzfvkwMI1快进时液压缸虽然作差动连接<即有杆腔与无杆腔均与液压泵地来油连接),但连接管路中不可避免地存在着压降I ,且有杆腔地压力必须大于无杆腔,估算时取I 0.5MPa.快退时回油腔中也是有背压地,这时选取被压值二=0.6MPa.rqyn14ZNXI工进时液压缸地推力计算公式为式中:F——负载力m——液压缸机械效率A1――液压缸无杆腔地有效作用面积A2――液压缸有杆腔地有效作用面积P1――液压缸无杆腔压力P2――液压有无杆腔压力因此,根据已知参数,液压缸无杆腔地有效作用面积可计算为液压缸缸筒直径为mm由于有前述差动液压缸缸筒和活塞杆直径之间地关系,d = 0.707D,因此活塞杆直径为d=0.707 X04.06=73.56mm根据GB/T2348 —1993对液压缸缸筒内径尺寸和液压缸活塞杆外径尺寸地规定,圆整后取液压缸缸筒直径为D=110mm,活塞杆直径为d=80mm.Emxvxotoco此时液压缸两腔地实际有效面积分别为:I 1 m23.4.3计算最大流量需求工作台在快进过程中,液压缸采用差动连接,此时系统所需要地流量为q 快进=<A1-A2)X/1=20.08L/minq 快退=A2 X/2=17.92/mi n工作台在工进过程中所需要地流量为q 工进=A i X/i' =95 L/min其中最大流量为快进流量为25.2L/mi n.根据上述液压缸直径及流量计算结果,进一步计算液压缸在各个工作阶段中地压力、流量和功率值,如表3所示.把表3中计算结果绘制成工况图,如图4所示.图4液压系统工况图3.5拟定液压系统原理图根据组合机床液压系统地设计任务和工况分析,所设计机床对调速范围、低速稳定性有一定要求,因此速度控制是该机床要解决地主要问题.速度地换接、稳定性和调节是该机床液压系统设计地核心.此外,与所有液压系统地设计要求一样,该组合机床液压系统应尽可能结构简单,成本低,节约能源,工作可靠.SixE2yXPq53.5.1速度控制回路地选择工况图4表明,所设计组合机床液压系统在整个工作循环过程中所需要地功率较小系统地效率和发热问题并不突出,因此考虑采用节流调速回路即可.虽然节流调速回路效率低,但适合于小功率场合,而且结构简单、成本低•该机床地进给运动要求有较好地低速稳定性和速度-负载特性,因此有三种速度控制方案可以选择,即进口节流调速、出口节流调速、限压式变量泵加调速阀地容积节流调速•钻镗加工属于连续切削加工,加工过程中切削力变化不大,因此钻削过程中负载变化不大,采用节流阀地节流调速回路即可.但由于在钻头钻入铸件表面及孔被钻通时地瞬间,存在负载突变地可能,因此考虑在工作进给过程中采用具有压差补偿地进口调速阀地调速方式,且在回油路上设置背压阀.由于选定了节流调速方案,所以油路采用开式循环回路,以提高散热效率,防止油液温升过高.6ewMyirQFL3.5.2换向和速度换接回路地选择所设计多轴钻床液压系统对换向平稳性地要求不高,流量不大,压力不高,所以选用价格较低地电磁换向阀控制换向回路即可•为便于实现差动连接,选用三位五通电磁换向阀•为了调整方便和便于增设液压夹紧支路,应考虑选用丫型中位机能.由前述计算可知,当工作台从快进转为工进时,进入液压缸地流量由25.1 L/min降为0.95 L/min,可选二位二通行程换向阀来进行速度换接,以减少速度换接过程中地液压冲击,如图5所示.由于工作压力较低,控制阀均用普通滑阀式结构即可.由工进转为快退时,在回路上并联了一个单向阀以实现速度换接•为了控制轴向加工尺寸,提高换向位置精度,采用死挡块加图5换向和速度切换回路地选择3.5.3压力控制回路地选择由于采用双泵供油回路,故采用液控顺序阀实现低压大流量泵卸荷,用溢流阀调整高压小流量泵地供油压力.为了便于观察和调整压力,在液压泵地出口处、背压阀和液压缸无杆腔进口处设测压点.y6v3ALoS89将上述所选定地液压回路进行整理归并,并根据需要作必要地修改和调整,最后画 出液压系统原理图如图7所示.为了解决滑台快进时回油路接通油箱 ,无法实现液压缸差动连接地问题,必须在回油 路上串接一个液控顺序阀10,以阻止油液在快进阶段返回油箱•同时阀9起背压阀地作 用.M2ub6vSTnP为了避免机床停止工作时回路中地油液流回油箱 ,导致空气进入系统,影响滑台运动地平稳性,图中添置了一个单向阀II OYujCfmUCw考虑到这台机床用于钻孔 < 通孔与不通孔)加工,对位置定位精度要求较高,图中增 设了一个压力继电器 6•当滑台碰上死挡块后,系统压力升高,压力继电器发出快退信号 操纵电液换向阀换向.eUts8ZQVRd在进油路上设有压力表开关和压力表,钻孔行程终点定位精度不高,采用行行程开关 控制即可.[ft图7液压系统原理图3.6液压元件地选择本设计所使用液压元件均为标准液压元件,因此只需确定各液压元件地主要参数和规格,然后根据现有地液压元件产品进行选择即可.sQsAEJkW5T3.6.1确定液压泵和电机规格<1)计算液压泵地最大工作压力由于本设计采用双泵供油方式,根据液压系统地工况图,大流量液压泵只需在快进 和124 — — + —1 + — 4— —f 3快退阶段向液压缸供油,因此大流量泵工作压力较低•小流量液压泵在快速运动和工进时都向液压缸供油,而液压缸在工进时工作压力最大,因此对大流量液压泵和小流量液压泵地工作压力分别进行计算.GMslasNXkA根据液压泵地最大工作压力计算方法,液压泵地最大工作压力可表示为液压缸最大工作压力与液压泵到液压缸之间压力损失之和.TIrRGchYzg对于调速阀进口节流调速回路,选取进油路上地总压力损失___________ I ,同时考虑到压力继电器地可靠动作要求压力继电器动作压力与最大工作压力地压差为0.5MPa,则小流量泵地最高工作压力可估算为7EqZcWLZNX大流量泵只在快进和快退时向液压缸供油,图4表明,快退时液压缸中地工作压力比快进时大,如取进油路上地压力损失为0.5MPa,则大流量泵地最高工作压力为:lzq7IGf02E<2)计算总流量表3表明,在整个工作循环过程中,液压油源应向液压缸提供地最大流量出现在快进工作阶段,为20.08 L/min,若整个回路中总地泄漏量按液压缸输入流量地10%计算,则液压油源所需提供地总流量为:zvpgeqJ1hkI L/min工作进给时,液压缸所需流量约为0.95 L/min,但由于要考虑溢流阀地最小稳定溢流量3 L/mi n,故小流量泵地供油量最少应为3.95 L/mi n.Nrpojac3v1据据以上液压油源最大工作压力和总流量地计算数值,上网或查阅有关样本,例如YUKEN日本油研液压泵样本,确定PV2R型双联叶片泵能够满足上述设计要求,因此选取PV2R12-6/33型双联叶片泵,其中小泵地排量为6mL/r,大泵地排量为33mL/r,若取液压泵地容积效率卜[=0.9,则当泵地转速| =940r/min时,小泵地输出流量为1nowfTG4KIq p小=6 940 0.95/1000=5.358 L/min该流量能够满足液压缸工进速度地需要.大泵地输出流量为q p 大=33*940*0.95/1000=29.469 L/min双泵供油地实际输出流量为该流量能够满足液压缸快速动作地需要3 .电机地选择由于液压缸在快退时输入功率最大,这时液压泵工作压力为209MPa,流量为34.827L/mi n.取泵地总效率—-,则液压泵驱动电动机所需地功率为:fjnFLDa5Zo根据上述功率计算数据,此系统选取丫112M-3.6.2阀类元件和辅助元件地选择图7液压系统原理图中包括调速阀、换向阀、单项阀等阀类元件以及滤油器、空气滤清器等辅助元件.1 .阀类元件地选择根据上述流量及压力计算结果,对图7初步拟定地液压系统原理图中各种阀类元件及辅助元件进行选择.其中调速阀地选择应考虑使调速阀地最小稳定流量应小于液压缸工进所需流量.通过图7中5个单向阀地额定流量是各不相同地,因此最好选用不同规格地单向阀.tfnNhnE6e5溢流阀2、背压阀9和顺序阀10地选择可根据调定压力和流经阀地额定流量来选择阀地型式和规格,其中溢流阀2地作用是调定工作进给过程中小流量液压泵地供油压力,因此该阀应选择先导式溢流阀,连接在大流量液压泵出口处地顺序阀10用于使大流量液压泵卸荷,因此应选择外控式.背压阀9地作用是实现液压缸快进和工进地切换,同时在工进过程中做背压阀,因此采用内控式顺序阀.最后本设计所选择方案如表5所示,表中给出了各种液压阀地型号及技术参数.HbmVN777sL表5阀类元件地选择序号元件名称估计流量规格型号1三位五通电磁阀66/8235D-100B 2行程阀49.5/61.522C-63BH 3调速阀<1AQF3-10B 4单向阀66/82AF3-Ea10B 5单向阀816.5/20.5I-25B6背压阀90.475/0.6FBF3-6B 7溢流阀 4.13/5YF-10B 8单向阀1166/82I-100B6型电动机,其额定功率,额定转速363油管地选择图7中各元件间连接管道地规格可根据元件接口处尺寸来决定,液压缸进、出油管地规格可按照输入、排出油液地最大流量进行计算•由于液压泵具体选定之后液压缸在各个阶段地进、出流量已与原定数值不同,所以应对液压缸进油和出油连接管路重新进行计算,如表8所示.V7l4jRB8Hs根据表8中数值,当油液在压力管中流速取3m/s时,可算得与液压缸无杆腔和有杆腔相连地油管内径分别为:,取标准值20mm;,取标准值15mm.因此与液压缸相连地两根油管可以按照标准选用公称通径为 丄I 和旦 地无缝钢管或高压软管•如果液压缸采用缸筒固定式,则两根连接管采用无缝钢管连接在液压缸 缸筒上即可.如果液压缸采用活塞杆固定式,则与液压缸相连地两根油管可以采用无缝 钢管连接在液压缸活塞杆上或采用高压软管连接在缸筒上.83ICPA59W9364油箱地设计1油箱长宽高地确定油箱地主要用途是贮存油液,同时也起到散热地作用,参考相关文献及设计资料,油 箱地设计可先根据液压泵地额定流量按照经验计算方法计算油箱地体积 ,然后再根据散热要求对油箱地容积进行校核.mZkklkzaaP油箱中能够容纳地油液容积按 JB/T7938 —1999标准估算,取时,求得其容积按JB/T7938—1999规定,取标准值 V=250L.如果取油箱内长 11、宽 w i 、高h i 比例为3 : 2: 1,可得长为: =1107mm,宽=738mm,高为 =369mmA VktR43bpw对于分离式油箱采用普通钢板焊接即可,钢板地厚度分别为:油箱箱壁厚 3mm,箱底 厚度5mm,因为箱盖上需要安装其他液压元件,因此箱盖厚度取为10mm.为了易于散热 和便于对油箱进行搬移及维护保养,取箱底离地地距离为160mm.因此,油箱基体地总长 总宽总高为: ORjBnOwcEd长为:I_— ■宽为: __ — __ ■高为:■ ・ ・―■为了更好地清洗油箱,取油箱底面倾斜角度为 I3.7液压系统性能地验算本例所设计系统属压力不高地中低压系统,无迅速起动、制动需求,而且设计中已考虑 了防冲击可调节环节及相关防冲击措施,因此不必进行冲击验算.这里仅验算系统地压力损失,并对系统油液地温升进行验算.2MiJTy0dTT7.1管路系统压力损失验算由于有同类型液压系统地压力损失值可以参考,故一般不必验算压力损失值•下面以工进时地管路压力损失为例计算如下:gliSpiue7A已知:进油管、回油管长约为l=1.5m,油管内径d=1.5 x 10-3m,通过流量=0.95 L/ mi n<0.0158 x 10-3m / s ),选用L —HM32全损耗系统用油,考虑最低温度为215°C ,V=1.5 cm /S. uEh0U1Yfmh7.1.1判断油流类型利用下式计算出雷诺数4 3 4 3Re=1.273 J x 104/ 冋=1.273 x 0.0158 x 10-x 10 /1.5 x 10-/1.5 〜160<2000Ag9qLsgBx 为层流.7.1.2沿程压力损失P1利用公式分别算出进、回油压力损失,然后相加即得到总地沿程损失.进油路上△P1=4.4 x 1012v E qv / d4=4.3 x 1012x 1.5 x 1.5 x 0.0158 x 10-3/412 Pa WwghWvVhPE=0.076 x 105Pa回油路上,其流量qv=0.75 L / min<0.0125 x 10-3m/ s) <差动液压缸A〜2A) , asfpsfpi4k压力损失为△Pi=4.3 x 1012v T qv/d4=4.3 x 1012x 1.5 x 1.5 x 0.00325 x 10-3/ 124Pa ooeyYZTjj1 =0.01532 x 105Pa由于是差动液压缸,且A1-2A,故回油路地损失只有一半折合到进油腔,所以工进时总地沿程损失为_ - 5 5R=<0.076+0.5 x 0.01532 ) x 10 Pa=0.0837x 10 Pa3.7.2油液温升验算液压传动系统在工作时,有压力损失、容积损失和机械损失,这些损失所消耗地能量多数转化为热能,使油温升高,导致油地粘度下降、油液变质、机器零件变形等,影响正常工作.为此,必须控制温升AT在允许地范围内,如一般机床厶=25 ~ 30 C;数控机床厶< 25C;粗加工机械、工程机械和机车车辆厶=35〜40 C .BkeGuInkxI液压系统地功率损失使系统发热,单位时间地发热量vkW )可表示为式中 —— 系统地输入功率 <即泵地输入功率)<kW ); ――系统地输出功率 <即液压缸地输出功率)<kW ).若在一个工作循环中有几个工作阶段,则可根据各阶段地发热量求出系统地平均发热 量 对于本次设计地组合机床液压系统,其工进过程在整个工作循环中所占时间比例为因此系统发热和油液温升可用工进时地发热情况来计算 工进时液压缸地有效功率 <即系统输出功率)为这时大流量泵通过顺序阀 <即系统输入功率)为:10卸荷,小流量泵在咼压下供油,所以两泵地总输出功率 三即可得油液温升近似值:322/3/T=①/vhA ) =0.386/<9*10 *6.5*10 *250 ) =15.6 °温升小于普通机床允许地温升范围,因此液压系统中不需设置冷却器。
- 1、下载文档前请自行甄别文档内容的完整性,平台不提供额外的编辑、内容补充、找答案等附加服务。
- 2、"仅部分预览"的文档,不可在线预览部分如存在完整性等问题,可反馈申请退款(可完整预览的文档不适用该条件!)。
- 3、如文档侵犯您的权益,请联系客服反馈,我们会尽快为您处理(人工客服工作时间:9:00-18:30)。
(1.液压传动的工作原理和组成 (1)工作原理 (1)液压系统的基本组成 (1)2.设计要求 (2)机床的其他工作参数如下: (2)3.液压系统工况分析 (3)运动分析 (3)负载分析 (3)$工作阻力 (3)摩擦阻力 (3)惯性力 (3)4.液压系统方案设计 (4)选择调速回路 (4)选择油源形式 (4)选择快速运动和换向回路 (5)选择速度换接回路 (5))选择调压和卸荷回路 (5)6.组成液压系统 (5)5.确定液压系统主要参数 (6)初选液压缸工作压力 (6)计算液压缸主要尺寸 (6)液压泵的参数计算 (9)计算液压泵的流量 (9)确定液压泵的规格和电动机功率 (9)[6.液压元件的选择 (10)液压阀及过滤器的选择 (10)油管的选择 (11)确定油管 (11)油箱的选择 (12)7.验算液压系统性能 (13)验算系统压力损失 (13)判断流动状态 (13),计算系统压力损失 (13)快进 (14)工进 (15)快退 (15)验算系统发热与温升 (16)《液压与气压传动》课程设计说明书学院、系:机械工程学院专业:机械工程学生姓名:班级:指导教师姓名:职称:教授最终评定成绩:2017 年 12月 11日至 2017 年 12月 15日1.液压传动的工作原理和组成液压传动是用液体作为工作介质来传递能量和进行控制的传动方式。
液压系统利用液压泵将原动机的机械能转换为液体的压力能,通过液体压力能的变化来传递能量,经过各种控制阀和管路的传递,借助于液压执行元件(缸或马达)把液体压力能转换为机械能,从而驱动工作机构,实现直线往复运动和回转运动。
驱动机床工作台的液压系统是由邮箱、过滤器、液压泵、溢流阀、开停阀、节流阀、换向阀、液压缸以及连接这些元件的油管、接头等组成。
工作原理(1)电动机驱动液压泵经滤油器从邮箱中吸油,油液被加压后,从泵的输出口输入管路。
油液经开停阀、节流阀、换向阀进入液压缸,推动活塞而使工作台左右移动。
液压缸里的油液经换向阀和回油管排回邮箱。
(2)工作台的移动速度是通过节流阀来调节的。
当节流阀开大时,进入液压缸的油量增多,工作台的移动速度增大;当节流阀关小时,进入液压缸的油量减少,工作台的移动速度减少。
由此可见,速度是油量决定的。
液压系统的基本组成(1)能源装置——液压泵。
它将动力部分所输出的机械能转换成液压能,给系统提供压力油液。
(2)执行装置——液压机。
通过它将液压能转换成机械能,推动负载做功。
(3)控制装置——液压阀。
通过它们的控制调节,使液流的压力、流速和方向得以改变,从而改变执行元件的力、速度和方向。
(4)辅助装置——邮箱、管路、储能器、滤油器、管接头、压力表开关等。
通过这些元件把系统联接起来,以实现各种工作循环。
(5)工作介质——液压油。
绝大多数液压油采用矿物油,系统用它来传递能量和信息。
2.设计要求设计一台组合机床动力滑台液压系统。
机床要求的工作循环是:要求实现工件快进、工进、快退等过程,最后自动停止;动力滑台采用平导轨,往复运动的加速、减速时间t 为。
机床的其他工作参数如下:机床自动化要求:要求系统采用电液结合,实现自动循环,速度换接无冲击,且速度要稳定,能承受一定量的反向负荷。
由设计要求取工进速度为80mm/min ,快进行程1l 为300mm ,工进行程2l 为100mm3.液压系统工况分析运动分析绘制动力滑台的工作循环图负载分析工作阻力工作阻力为已知N F t 20000= 摩擦阻力已知采用平导轨,且静摩擦系数2.0=s f ,动摩擦系数1.0=d f ,正压力N F N 30000=,则:静摩擦阻力 N F fs 6000300002.0=⨯= 动摩擦阻力 N F fd 3000300001.0=⨯=惯性力N t v g G F m 15302.08.960/630000=⨯⨯=∆∆⋅=液压缸各运动阶段负载如果忽略切削力引起的颠覆力矩对导轨摩擦力的影响,并设定液压缸的机械效率95.0=η,则液压缸在各个工作阶段的总接卸负载可以算出,见下表:运动阶段 计算公式总接卸负载F/N 起动 η/fs F F =6316 加速 η/)(m fd F F F += 4868 快进 η/fd F F = 3158 工进 η/)(fd t F F F +=24211 快退 η/fd F F =31584.液压系统方案设计选择调速回路这台机床液压系统功率较小,滑台运动速度低,工作负载为阻力负载且工作中变化小,故可选用进口节流调速回路。
为防止负载突变,在回油路上加背压阀。
由于系统选用节流调速方式,系统必然为开式循环系统。
选择油源形式在工作循环内,液压缸要求油源提供快进、快退行程的低压大流量和工进行程的高压小流量的油液。
在一个工作循环中的大部分时间都处于高压小流量工作。
从提高系统效率、节省能量角度来看,选用单定量泵油源显然是不合理的,为此可选用限压式变量泵或双联叶片泵作为油源。
考虑到前者流量突变时液压冲击较大,工作平稳性差,且后者可双泵同时向液压缸供油实现快速运动,最后确定选用双联叶片泵方案,如下图所示。
选择快速运动和换向回路本系统已选定液压缸差动连接和双泵供油两种快速运动回路实现快速运动。
考虑到从工进转快退时回油路流量较大,故选用换向时间可调的电液换向阀式换向回路,以减小液压冲击。
由于要实现液压缸差动连接,所以选用三位五通电液换向阀,如下图所示。
选择速度换接回路由于本系统滑台由快进转为工进时,速度变化大,为减少速度换接时的液压冲击,选用行程阀控制的换接回路,如图下图所示。
选择调压和卸荷回路在双泵供油的油源形式确定后,调压和卸荷问题都已基本解决。
即滑台工进时,高压小流量泵的出口压力由油源中的溢流阀调定,无需另设调压回路。
在滑台工进和停止时,低压大流量泵通过液控顺序阀卸荷,高压小流量泵在滑台停止时虽未卸荷,但功率损失较小,故可不需再设卸荷回路。
6.组成液压系统将上面选出的液压基本回路组合在一起,并经修改和完善,就可得到完整的液压系统工作原理图,如右图所示。
为了解决滑台工进时进、回油路串通使系统压力无法建立的问题,增设了单向阀6。
为了避免机床停止工作时回路中的油液流回油箱,导致空气进入系统,影响滑台运动的平稳性,图中添置了一个单向阀13。
考虑到这台机床用于钻孔(通孔与不通孔)加工,对位置定位精度要求较高,图中增设了一个压力继电器14。
当滑台碰上死挡块后,系统压力升高,它发出快退信号,操纵电液换向阀换向。
5.确定液压系统主要参数初选液压缸工作压力所设计的动力滑台在工进时负载最大,在其它工况负载都不太高,参考表1和表2,初选液压缸的工作压力p1=4MPa。
计算液压缸主要尺寸鉴于动力滑台快进和快退速度相等,这里的液压缸可选用单活塞杆式差动液压缸(A1=2A2),快进时液压缸差动连接。
工进时为防止负载突变采用背压,参考表4选此背压为p b=。
负载/KN<55~1010~2020~3030~50>50工作压力/MPa<~1~2~33~44~5≥5机械类型机床农业机械小型工程机械建筑机械液压凿岩机液压机大中型挖掘机重型机械起重运输机械磨床组合机床龙门刨床拉床工作压力/MPa ~23~52~88~110~1820~32表3 执行元件背压力表4 按工作压力选取d/D注:υ1—无杆腔进油时活塞运动速度;υ2—有杆腔进油时活塞运动速度。
液压缸活塞杆外径尺寸系列(mm )由公式η/2211F A p A p =-可得:232662111054.6106.0211042421121m m p p F A ⨯=⨯⨯-⨯=-=则活塞直径 mm A D 911054.64431=⨯⨯==-ππ参考表4及表5,得≈ =64mm,圆整后取标准数值得D =90mm , d =63mm 。
由此求得液压缸两腔的实际有效面积为2215.634mm D A ==π22224.324)(mm d D A =-=π根据计算出的液压缸的尺寸,可估算出液压缸在工作循环中各阶段的压力、流量和功率,如下表所列。
表6 液压缸所需的实际流量、压力和功率1.Δp 为液压缸差动连接时,回油口到进油口之间的压力损失,取Δp =。
2.快退时,液压缸有杆腔进油,压力为p j ,无杆腔回油,压力为p b =p j +Δp 。
3.计算工进是背压按p b =代入。
4.快退时背压按p b =代入。
液压泵的参数计算小流量泵在快进和工进时都向液压缸供油,由表6可知,液压缸在工进时工作压力最大,最大工作压力为p 1=,如在调速阀进口节流调速回路中,选取进油路上的总压力损失∑∆p =,考虑到压力继电器的可靠动作要求压差p =,则小流量泵的最高工作压力估算为Mpa p p P P p 32.55.06.022.41=++=∆+∆∑+≥ 大流量泵只在快进和快退时向液压缸供油,由表6可见,快退时液压缸的工作压力为p 1=,比快进时大。
考虑到快退时进油不通过调速阀,故其进油路压力损失比前者小,现取进油路上的总压力损失∑∆p =,则大流量泵的最高工作压力估算为Mpa p P P p 25.23.095.111=+=∆∑+≥因此泵的额定压力可取MPa MPa P r 65.632.525.1=⨯≥ 计算液压泵的流量由表6可知,油源向液压缸输入的最大流量为min ,若取回路泄漏系数K =,则两个泵的总流量为m in /384.21m in /44.191.11L L Kq q p =⨯==考虑到溢流阀的最小稳定流量为min ,工进时的流量为min 则小流量泵的流量m in /061.3)5.251.01.1(1L q p =+⨯≥小流量泵的流量最少应为min 。
所以大流量泵的流量m in /204.181.3304.2112L q q q p p p =-=-≥确定液压泵的规格和电动机功率根据以上压力和流量数值查阅产品样本,并考虑液压泵存在容积损失,最后确定选取PV2R12-6/26型双联叶片泵。
其小流量泵和大流量泵的排量分别为6mL/min 和26mL/min ,当液压泵的转速n p =960r/min 时,其理论流量η⋅⋅=n V q 分别为 L/min 和min ,若取液压泵容积效率ηv =,则液压泵的实际输出流量为min/036.27min /)996.21076.5(min /)1000/9409.0261000/9409.06(21L L L q q q p p p =+=⨯⨯+⨯⨯=+=由于液压缸在快退时输入功率最大,若取液压泵总效率ηp =,这时液压泵的驱动电动机功率为Kw q p P ppp 28.110608.010036.271025.2336=⨯⨯⨯⨯⨯=≥-η 根据此数值查阅产品样本,选用规格相近的Y100L —6型电动机,其额定功率为,额定转速为910r/min6.液压元件的选择液压阀及过滤器的选择根据系统的最高工作压力和通过各阀类元件及辅件的实际流量,查阅产品样本,选出的阀类元件和辅件规格如表8所列。