中板生产工艺简介共37页文档
中密度纤维板生产线工艺流程
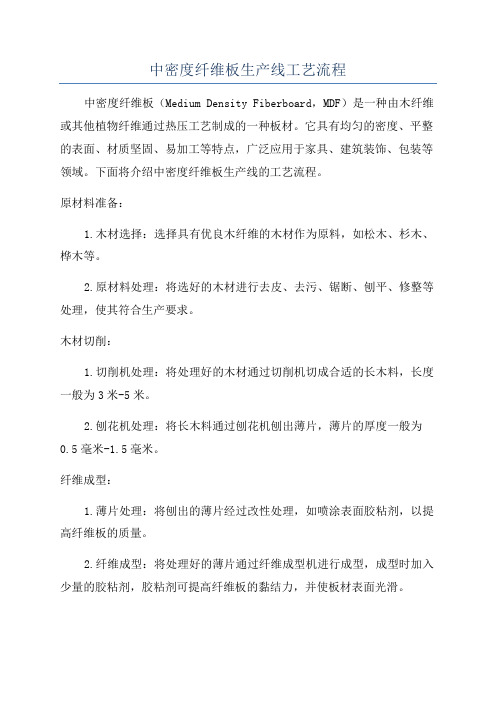
中密度纤维板生产线工艺流程中密度纤维板(Medium Density Fiberboard,MDF)是一种由木纤维或其他植物纤维通过热压工艺制成的一种板材。
它具有均匀的密度、平整的表面、材质坚固、易加工等特点,广泛应用于家具、建筑装饰、包装等领域。
下面将介绍中密度纤维板生产线的工艺流程。
原材料准备:1.木材选择:选择具有优良木纤维的木材作为原料,如松木、杉木、桦木等。
2.原材料处理:将选好的木材进行去皮、去污、锯断、刨平、修整等处理,使其符合生产要求。
木材切削:1.切削机处理:将处理好的木材通过切削机切成合适的长木料,长度一般为3米-5米。
2.刨花机处理:将长木料通过刨花机刨出薄片,薄片的厚度一般为0.5毫米-1.5毫米。
纤维成型:1.薄片处理:将刨出的薄片经过改性处理,如喷涂表面胶粘剂,以提高纤维板的质量。
2.纤维成型:将处理好的薄片通过纤维成型机进行成型,成型时加入少量的胶粘剂,胶粘剂可提高纤维板的黏结力,并使板材表面光滑。
3.热压:将成型好的纤维板放入热压机中进行热压处理,使纤维板的内部纤维更加紧密,提高板材的密度和强度。
修整与涂层:1.修整:将热压后的纤维板进行修整,去除边角毛刺,使板材的尺寸更加精确。
2.涂层:根据生产需求,对板材进行表面涂层处理,如喷涂染色剂、漆膜等,以改善纤维板的外观质感和保护作用。
质检与包装:1.质检:对生产好的纤维板进行质量检查,检查项包括板材尺寸、密度、强度、表面平整度等。
2.包装:将合格的纤维板进行包装,一般采用塑料薄膜包装或纸箱包装,以便运输和储存。
以上是中密度纤维板生产线的主要工艺流程。
在实际生产中,还需要根据具体需求,对工艺进行调整和改进,以提高生产效率和产品质量。
五矿营口中厚板生产流程介绍综述
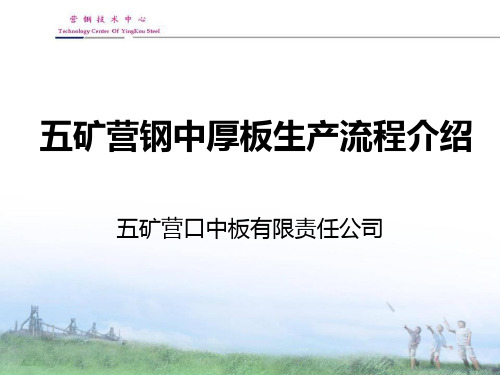
五矿营口中板有限责任公司
目录
一、炼钢工序 二、轧钢工序 三、钢板检验
.
一、炼钢工序
1、炼钢工艺流程
一、炼钢工序
1、混铁炉
混铁炉1座
公称容量为900吨
储存铁水
一、炼钢工序
2、预处理 脱硫站1座 深脱硫能力 0.005%以下
一、炼钢工序
3、转炉吹炼
型式:氧气顶吹式 数量:3座 公称容量:120吨 吹炼周期:35min 脱碳、脱硅、脱P、 脱S
四、钢板检验
7、DWTT实验
JL-5000J落锤试验机-威海 冲击能量:2000J5000J 主要用于钢板韧性的检 验
四、钢板检验
8、NDT实验
新三思NDT落锤冲击试 验机 冲击能量:最大3000J 主要用于韧脆转变温度 的测定
四、钢板检验
9、金相检验
Carl Zeiss金相显微镜 最大放大倍数1000倍 用于检测晶粒度、夹杂 物、带状组织、及观察金 相组织
二、轧钢工序--宽厚板厂
四辊可逆式精轧机 工作辊:5300mm 支撑辊:4950mm 最大轧制力12000t 延展轧制
二、轧钢工序--宽厚板厂
ACC
冷却宽度: 4980mm 总长:24000mm
作用加速冷却,实现 TMCP轧制
二、轧钢工序--宽厚板厂
热矫直机
9辊矫直机 矫直力4000t 辊身长5200mm 矫直厚度范围:6100mm 矫直温度范围:500800℃
四、钢板检验
5、弯曲实验
新三思 微机控制电液 伺服弯曲试验机 垂直最大负荷2000KN 水平最大负荷1000KN 最大弯曲直径150mm 最小弯曲直径12mm
四、钢板检验
中厚板生产流程

中厚板生产流程
中厚板生产流程主要包括原材料准备、板坯制备、轧制、热处理、表面处理和成品检验等环节。
1. 原材料准备:根据设计要求,选购合适的钢材原料,包括钢坯、铁矿石、合金等。
2. 板坯制备:将选购的钢坯加热至一定温度,使其变软,然后通过轧机或铸造等工艺,将钢坯加工成板坯。
板坯的尺寸和形状要符合生产要求。
3. 轧制:将板坯放入轧机中进行轧制,包括热轧和冷轧两种方式。
热轧是在高温下进行的,通过辊机将板坯加热、轧制成所需尺寸和形状的板材;冷轧是在室温下进行的,通过辊机将板坯压制成所需的尺寸和形状。
轧制过程中会伴随有热处理。
4. 热处理:通过控制板材的温度,使其在一定时间内保持在高温下,并进行冷却处理,以调整材料的组织结构、获得所需的力学性能。
常用的热处理方法有退火、正火、淬火和回火等。
5. 表面处理:对板材的表面进行处理,以满足不同的工程要求。
常见的表面处理方法有喷漆、喷涂、脱油、磨砂等。
6. 成品检验:对成品板材进行检验,包括尺寸、力学性能、化学成分、外观质量等方面的检测。
确保产品符合要求后即可交付使用。
以上是中厚板生产的基本流程,具体操作会根据钢材的品种和用途有所差别,同时考虑经济性、环保性等因素。
中密度纤维板生产线实用工艺流程

生产中厚板时原木不要求剥皮,但树皮允许体积分数小于8%%。原木装
载机将小径木、枝桠材等木材原料放在储木台上,通过皮带运输机送 入削片
机,削片机前装有金属探测器,避免带有金属的木材进入削片机。进
入削片机
的木材被削成规格木片,经由螺旋运输机和斗式提升机送人木片储仓 储存。
由于软材硬材要按比例混合,所以采用两个储仓,分别储存软材和硬 材木片。
理化学性质稳定、来源广泛、价格低廉、无毒无味无污染等特点,但 蒸汽用于热压工序时也有几个不易克服的缺点:一是热压工序通常需 要较高的温度,一般在160――220C之间,与此相对应的蒸汽压力 为1.6――2.5MPa,因此,需要整个供热系统(包括锅炉、管道及其
附件与接头等)具有较高的耐压强度,这就使供热系统结构复杂,投 资增大,运行管理不便;二是为了保证热压质量,要求热压板面温度 尽可能均匀一致,一般要求同一块压板板面上的温差小于3°C,各层 热压板之间的温差小于5°C,这就要求载热体在进出热压板时的温度 差要尽可能小。采用蒸汽加热时,往往会由于凝结水排故不及时,使 热压质量降低;三是蒸汽在热压机中放热后排出的凝结水具有较高的 温度(一般在160C以上),其回收难度较大,若处理不当,则可能造 成严重的能源浪费。由于蒸汽加热具有这些不易克服的缺点,所以, 近年来越来越多的汽车内饰生产热压机都采用了高温热油供热系统。 热油供热的特点热油又称为导热油,属于一种高温有机热载体,
被送入直径为4500MM的高效旋风分离器,在这里将纤维和湿空气 分离,湿热空气排到大气中。干燥纤维能力为5000KG/H,蒸汽耗 量最大为8200KG/H,设计
风量为95000M3/H,风压为4500PA。于纤维通过旋转出料器排出 至螺旋称重进
料机,纤维在这里被准确称出重量。该装置还ห้องสมุดไป่ตู้按预置定的胶和纤维 的比例
中厚钢板的生产
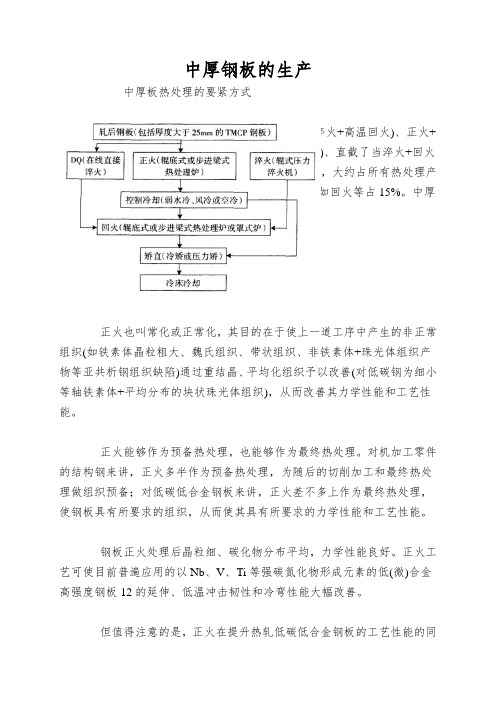
中厚钢板的生产中厚板热处理的要紧方式中厚钢板热处理的要紧方式有正火、调质(淬火+高温回火)、正火+控冷、正火+回火、回火、退火、直截了当淬火(DQ)、直截了当淬火+回火等。
其中,处理量最大的是正火板,包括正火+回火,大约占所有热处理产品的70%左右;其次是调质板,占15%左右;其它如回火等占15%。
中厚板热处理工艺流程见图1。
图1 中厚板热处理工艺流程1 正火工艺的特点及注意事项正火也叫常化或正常化,其目的在于使上一道工序中产生的非正常组织(如铁素体晶粒粗大、魏氏组织、带状组织、非铁素体+珠光体组织产物等亚共析钢组织缺陷)通过重结晶、平均化组织予以改善(对低碳钢为细小等轴铁素体+平均分布的块状珠光体组织),从而改善其力学性能和工艺性能。
正火能够作为预备热处理,也能够作为最终热处理。
对机加工零件的结构钢来讲,正火多半作为预备热处理,为随后的切削加工和最终热处理做组织预备;对低碳低合金钢板来讲,正火差不多上作为最终热处理,使钢板具有所要求的组织,从而使其具有所要求的力学性能和工艺性能。
钢板正火处理后晶粒细、碳化物分布平均,力学性能良好。
正火工艺可使目前普遍应用的以Nb、V、Ti等强碳氮化物形成元素的低(微)合金高强度钢板12的延伸、低温冲击韧性和冷弯性能大幅改善。
但值得注意的是,正火在提升热轧低碳低合金钢板的工艺性能的同时,往往降低钢的强度,屈服强度和抗拉强度一样降低20~50MPa,关于控轧控冷钢板严峻的可降低80~120MPa。
因此,为保证钢板的交货性能,在正火钢板成分设计时,应不同于一样控轧控冷钢板,可适当增加C、Mn 等固溶强化元素以提升强度(注意碳当量指标不要过高),尽管热轧后钢板的延伸率或冲击功有所降低,但这两项指标在正火处理后会有大幅提升。
2 正火+控冷(+回火)新工艺常化炉除处理“双高”产品外,另一大作用是挽救专门多热轧后延伸或冲击不合产品,减少改判率。
但随之而来的一个咨询题是一些延伸、冲击不合需挽救的产品本身强度富裕量小,容易导致处理后强度反而不合。
中密度纤维板生产工艺设计

中密度纤维板生产、基本工艺设计中密度纤维板生产工艺包括生产部分和辅助部分(以木材原料为主)。
生产部分包括原料堆场和备料、热磨施胶干燥、铺装预压热压、后处理、中间储存及砂光工段。
辅助部分有实验室、磨刀间和维修间等。
中密度纤维板生产基本工艺设计. 原料堆场原料堆场是生产工艺的组成部分。
原料在储存过程中,受自然条件的影喻而减少水分和均衡含水率,能减少树脂含量及果胶、淀粉、蛋白等成分,有利于原料质量的稳定,使原料更适于解纤。
而不恰当的原料储存方式和管理方法,不但会造成原料的腐朽变质和浪费,甚至会有火灾的隐患。
在设计中必须根据工厂的生产规模、工艺流程、原料种类、储存季节、场地利用和防火规范要求等来综合考虑原料堆场的储存方式和面积、工艺布局。
原木进场后应按树种和径级以及进场时间的先后顺序分类归堆。
考虑到原料供应的季节性作业和由于市场变化、运输等不可预测的因素,会使原料供应不及时而影响正常生产,为满足企业的正常连续生产必须要有一定的储备量。
对于木材原料来说,原木储存量不能少于1个月的正常生产的需要量。
以3~4个月的生产需要量为最佳。
采用铲车堆垛作业工艺,。
堆积高度按3~5m计算;外购到厂的木片可用简易棚或露天堆场堆放,露天堆场的木片堆积高度可达20~30m。
为避免原料堆垛自燃导致火灾和腐烂变质,堆垛之间要求留有足够的垛间距及通风道。
堆垛间距一般在1~2m,至少不小于0.5m;垛组间距一般在10~15m,垛区间距一般为15~25m。
原料场最好设置在生产区的下风向,堆垛长度方向应与常年主导风向成一个角度,以利通风。
非木材植物纤维原料则在很大程度上受季节影响,必须根据原料收购季节和运输条件等来考虑原料储存期、储存面积及储存方式。
这些原料一般用打捆方式运进料场储存,储存期一般在6个月以上,棉杆、庶渣类的储存量在6~9个月,芦苇、秸秆为7~10个月,竹材一般为2~3个月。
可采取分场地储存,但生产区内至少要储存1~3个月的生产用量。
中板生产工艺简介

主
要
特
点
双 边 滚 切 剪
(1)SMS型三轴三 偏心滚切式双边 剪。 (2)剪刃间隙可自 动调整,剪刃可快 速更换。 (3)采用激光画线、 磁力对中、自动 测长和送钢,控 制精度高,维修 方便。
钢板切头尾、定尺、取样 装备了一台由第二重型机 器厂制造的滚切式定尺剪。可以使钢板达到成品所需 要的长度,并将钢板头尾轧制缺陷切除,并为性能检 验切取大试样。其主要参数如下:
轧机日历作业率 指轧机生产时间在日历时间中的比率。
2008年中厚板全行业平均水平为83.01%,中板工序 完成93.15%(如果去年按照正常情况安排年修,这一 指标应在90~91%之间),处于行业领先水平。 机时产量 指轧机每小时生产合格板材的数量。2008 年中厚板全行业平均水平为164.20t/h,中板工序完成 119.64 t/h,处于行业较差水平。 合格率 指板材合格品占生产量的比例。板材合格率算 法比较多,行业交流以轧制成品中无轧制表面缺陷产 品所占的比例计算,2008年中厚板全行业平均水平为 99.77%,中板工序完成99.94%,处于行业中上水平。 轧辊消耗 指每轧制一吨合格板材消耗的轧辊重量。 2008年中厚板全行业平均水平为0.44kg/t,中板工序 完成0.30kg/t,处于行业先进水平。
钢板平面形状不好矩形度差会影响用户生产下料严重时甚至无法使用也要加以控制对于切边板来说其产生原因通常是钢板在双边剪或定尺剪对中不好或跑偏双边剪或定尺剪及其附属设备故障或未调整对于轧后毛板来说则跟钢坯来料形状钢坯加热质量轧机前后锥辊推床轧机压下系统轧辊轧辊轴承等诸多因素有关
炼轧厂中板工序中板生产线于1998年10月投产,设计产 能年产50万吨中厚板,现有生产、设备保障两个作业 区,共有职工300人,目前达到年产100万吨的规模。 一、原料 使用原料以自产炼钢连铸坯为主,其厚度为160mm和 220mm,宽度950~1600mm,长度为1900~ 2750mm,可用原料单重2.1~7.8吨。也使用了一些 外购板坯,其产地包括济钢、莱钢、日照钢厂、天津 铁厂、安钢等,厚度190~230mm,宽度1250~ 1550。 二、成品 可生产的成品规格为厚度6~40mm(切边板),宽度 1500~2700mm,长度2~16m。厚度超过40mm 的钢板不能按照国标交货,只能按照协议供应毛边、 不保证性能的产品,其正常交货的最大厚度为85mm (厚度大于85mm时无法组织大批量生产,且表面平
中板轧机工艺流程
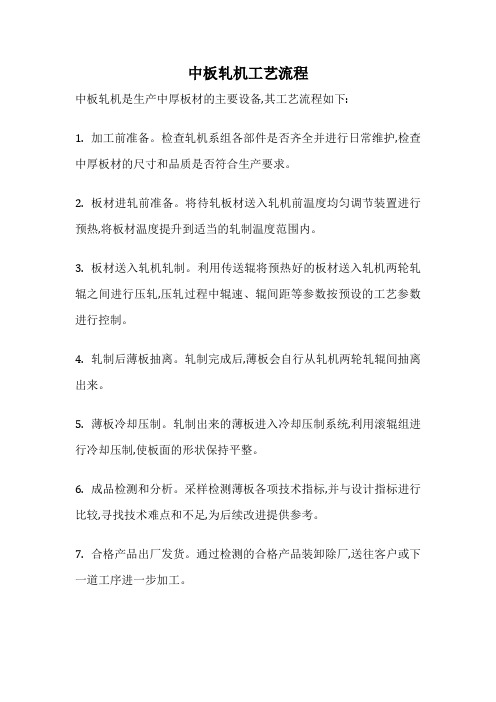
中板轧机工艺流程
中板轧机是生产中厚板材的主要设备,其工艺流程如下:
1. 加工前准备。
检查轧机系组各部件是否齐全并进行日常维护,检查中厚板材的尺寸和品质是否符合生产要求。
2. 板材进轧前准备。
将待轧板材送入轧机前温度均匀调节装置进行预热,将板材温度提升到适当的轧制温度范围内。
3. 板材送入轧机轧制。
利用传送辊将预热好的板材送入轧机两轮轧辊之间进行压轧,压轧过程中辊速、辊间距等参数按预设的工艺参数进行控制。
4. 轧制后薄板抽离。
轧制完成后,薄板会自行从轧机两轮轧辊间抽离出来。
5. 薄板冷却压制。
轧制出来的薄板进入冷却压制系统,利用滚辊组进行冷却压制,使板面的形状保持平整。
6. 成品检测和分析。
采样检测薄板各项技术指标,并与设计指标进行比较,寻找技术难点和不足,为后续改进提供参考。
7. 合格产品出厂发货。
通过检测的合格产品装卸除厂,送往客户或下一道工序进一步加工。
中厚板生产概述

1.中厚钢板概述中厚钢板:厚度大于4mm的钢板属于中厚钢板。
其中,厚度4.5-25.0mm的钢板称为中厚板,厚度25.0-100.0mm的称为厚板,厚度超过100.0mm的为特厚板。
中厚板主要用于建筑、机械、造船、石油、电力等行业,中厚板分为普通中厚板和优质中厚板,应用更为广泛的是普通中厚板,它主要用于制造各种容器、炉壳、炉板、桥梁及汽车、拖拉机某些零件及焊接构件。
普通中厚板用途:广泛用来制造各种容器、炉壳、炉板、桥梁及汽车静钢钢板、低合金钢钢板、桥梁用钢板、造船钢板、锅炉钢板、压力容器钢板、花纹钢板、汽车大梁钢板、拖拉机某些零件及焊接构件。
桥梁用钢板用于大型铁路桥梁。
要求承受动载荷、冲击、震动、耐蚀等。
造船钢板:用于制造海洋及内河船舶船体。
要求强度高、塑性、韧性、冷弯性能、焊接性能、耐蚀性能都好。
锅炉钢板:用于制造各种锅炉及重要附件,由于锅炉钢板处于中温(350°C以下)高压状态下工作,除承受较高压力外,还受到冲击,疲劳载荷及水和气腐蚀,要求保证一定强度,还要有良好的焊接及冷弯性能。
压力容器用钢板:主要用于制造石油、化工气体分离和气体储运的压力容器或其它类似设备,一般工作压力在常压到320kg/cm2甚至到630kg/cm2,温度在-20-450°C范围内工作,要求容器钢板除具有一定强度和良好塑性和韧性外,还必须有较好冷弯和焊接性能。
汽车大梁钢,用于制造汽车大梁(纵梁、横梁)用厚度为2.5-12.0mm的低合金热轧钢板。
汽车板属于高附加值产品,特别是载货汽车中,横梁、竖梁、车桥、以及车轮等结构件广泛使用中厚板。
由于汽车大梁形状复杂,除要求较高强度和冷弯性能外,要求冲压性能好。
花纹板由于表面存在花纹,增加防滑能力,用于制造厂房、船舶、扶梯、工作平台、工作踏板等。
另外,优质中厚板主要用于机械、车辆等零件、构件、工具等。
不锈板用于航空、石油化工、纺织、食品、医疗等。
2.中厚板生产企业及生产情况概述2007年1-9月,我国中厚板产量达到3835.27万吨,其中中板累计生产2234.61万吨,同比增长36.35%;特厚板累计生产322.47万吨,同比增长45.9%;宽厚板1278.19万吨,同比增长41.2%。
中厚板 冶炼工艺流程

中厚板冶炼工艺流程
中厚板冶炼工艺流程大致如下:从原料矿石开始,经过破碎、球磨等工序制成生铁水或钢水;钢水在转炉或电炉中进行脱碳、脱硫、脱磷等冶炼操作,调整成分至所需规格;钢水流入LF精炼炉进行二次精炼,去除夹杂物、微调成分,保证钢质纯净度;钢水通过连铸机连续浇铸成板坯;板坯经过加热炉加热至适于轧制的温度,送入热连轧生产线,经多道次轧制达到预定厚度和宽度,成为中厚钢板;钢板进行冷却、矫直、剪切等后续处理,检验合格后入库。
中厚板生产

皮下气孔和夹杂
皮下气孔和夹杂不规则地分布在连铸坯表面上。 夹杂产生的原因:结晶器中钢液面的波动卷入 保护渣或有缺陷的浸入式水口在钢液内破损。 皮下气孔产生的原因:钢水脱氧不充分,或当 中间包潮湿以及引锭杆头部潮湿时,最先浇注的 板坯部分出现皮下气孔。
25
鼓肚
鼓肚是指连铸坯厚度沿宽度方向的中部增大。 连铸机支承辊对连铸坯的支撑不充分或 没有支撑,连铸坯芯部钢水对坯壳的静 压力而使得坯壳膨胀。
13
单机架
单机架中厚板轧机,一个机架既是粗轧机,又是精轧
机。 采用单机架生产,只要按规程勤换辊,钢板表面质量
是可以保证的。因此,有些新建厂因限于产量和投资, 先采用单机架,预留第二架位置,将来扩建成双机架。
二辊式轧机 淘汰
单机架
三辊劳特式轧机 改造
四辊式轧机
14
双机架
双机架中厚钢板轧机呈纵列式布置,前一架 为粗轧机,后一架为精轧机。
适用范围:用于板坯长度大于或等于钢板宽度 时。
特点:如果用初轧板坯作原料,那么由于初轧 时轧件的延伸方向与厚板轧制时的延伸方向相垂 直,因而大大地改善钢板的各向异性,显著改善 钢板的横向性能。因此全横轧法经常用于以初轧 坯为原料的中厚板生产。但由于受到钢坯长度规 格数量的限制,调整钢板宽度的灵活性小。
10
图2-4 四辊轧机电动机直接传动轧辊的主传动示意图 1-电动机;2-传动轴;3-接轴移出缸;4-接轴平衡装置; 5-万向接轴;6-工作机座
11
1.4 万能式轧机
图2-5 万能式轧机轧制过程示意图 图2-6 V-H轧机的精轧机
12
二、中厚板轧机的布置
布置形式
有三种: (1)单机架布置 (2)双机架布置(主要布置形式) (3)半连续或连续式布置
管道中板材料的生产工艺及质量控制

管道中板材料的生产工艺及质量控制管道在现代工业和建筑领域扮演着至关重要的角色。
而管道中的板材料作为管道的主要组成部分,其生产工艺及质量控制显得尤为重要。
本文将深入探讨管道中板材料的生产工艺以及质量控制的关键要点。
首先,管道中板材料的生产工艺涉及到材料的选择和加工过程。
在材料的选择方面,常见的板材材料有碳钢、不锈钢、铜、铝等。
不同材料具有不同的特性,需要根据具体的管道应用环境和要求来选择合适的材料。
例如,对于耐腐蚀性要求较高的管道,不锈钢是一个常用的选择。
在加工过程中,板材需要经过切割、熔接、折弯等多个步骤。
这些步骤需要根据管道的尺寸和形状要求来进行精确的控制,以保证板材的几何形状和尺寸的精度。
其次,质量控制是确保管道中板材料质量的关键。
质量控制包括两个主要方面,即原材料的质量控制和生产过程中的质量控制。
对于原材料的质量控制,主要从以下几个方面考虑:材料的化学成分、机械性能、表面质量以及尺寸偏差等。
这些参数的合格性将直接影响到板材的最终质量和使用性能。
生产过程中的质量控制需要关注板材的几何尺寸、表面质量、焊接质量等。
尤其是焊接工艺的控制,对于确保管道的密封性和机械强度至关重要。
在质量控制过程中,产品的检测和测试也是必不可少的一环。
常用的测试方法包括物理性能测试、化学成分测试、金相组织分析、超声波和射线检测等。
这些测试方法可以帮助生产者了解板材的物理和化学性能,以及存在的缺陷和问题。
通过及时的检测和测试,可以对不合格产品进行处理,保证合格产品的出厂质量。
此外,在管道中板材料的质量控制中,还需要关注环境保护和安全生产。
生产过程中应严格遵循环保法规,控制废气、废水和固体废物的排放,以减少对环境的污染。
同时,对于涉及高温和高压的管道,操作人员需要严格遵守安全操作规程,确保生产过程的安全性和稳定性。
综上所述,管道中板材料的生产工艺及质量控制是确保管道质量和安全的关键要素。
从材料的选择到生产过程的控制,以及质量测试和环境安全的重视,这些方面都需要充分考虑和实施。
中厚板工艺流程简介优选演示
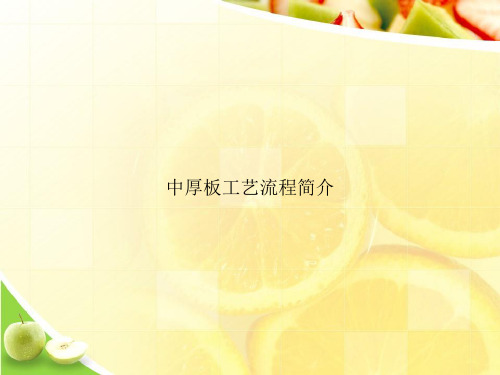
纵向轧制 轧钢
纵向轧制 轧钢
控冷
123456789000
123456789000
矫直,热喷印
剪切线生产流程
扫描钢板轮廓
冷PS床G冷却
检查台架
123456789000
子板号
123456789000
不剖分钢板-单 排标识
123456789
试样,子板标识
子板号
12345…..890
12345…..890
中厚板工艺流程简介
优选中厚板工艺流程简介
中厚板生产工艺流程
•轧机区域 •剪切线区域 •特厚板区域 •热处理区域
热轧区域生产流程
中厚板工艺平面布置示意图
中厚板工艺平面布置示意图
8 888.88 Kg 称重
装炉
加热
出钢
除鳞
转钢 轧钢
展宽轧制 轧钢
展宽轧制 轧钢
纵转向钢轧制 轧钢
废边
切边/剖分
剖分后单块切割
定尺切割
1234567890
废尾
1234567890
1234567890
子板2
子板1
样条
剖分后单块切割
定尺切割
剖分后单块切割
定尺切割
剖分后单块切割
定尺切割
不剖分单块切割
定尺切割
表面喷 字
表面打钢 字
侧标识
表面打钢 字
局部放大
成品标识
成品检查,入库
剖分后双块切割
12345…..890
12345…..890
12345…..890
12345…..890
40
40
0
0
-
-
37
37