132m_2烧结机烟气脱硫改造
1×132㎡烧结机中温脱硝技术协议

XX有限公司1×132㎡烧结机烟气中温SCR脱硝工程XX有限公司1×132㎡烧结机烟气中温SCR脱硝工程技术协议甲方:乙方:XX有限公司1×132㎡烧结机烟气中温SCR脱硝工程目录1 总论 (5)1.1 项目名称 (5)1.2 建设规模 (5)1.3 编制依据及设计原则 (5)1.3.1 编制依据 (5)1.3.2 设计原则 (6)2 设计基本参数 (7)2.1 设计参数 (7)2.1.1 设计参数 (7)2.2 设计条件 (9)3.工艺路线 (9)3.1工艺路线选取依据、原则 (9)3.2 工艺路线 (10)4.中温SCR脱硝系统 (11)4.1原理说明及工艺流程 (11)4.1.1 中温SCR 脱硝原理 (11)4.1.2 工艺流程 (11)4.1.3 中温SCR 技术与电力行业SCR 技术的差异 (13)4.2工艺部分 (13)4.2.1 中温SCR 反应器 (14)4.2.2 催化剂 (15)4.2.3 氨喷射(AIG)系统及稀释风机及静态混合器 (18)4.2.4 烟道 (19)4.2.5 吹灰器 (21)4.2.6 稀释风机 (21)4.2.7检修、起吊设施 (22)4.2.8结构、平台和扶梯 (22)4.3仪表和控制系统 (24)4.4 电气系统 (35)4.5 回转式烟气换热器(GGH) (42)- 1 -XX有限公司1×132㎡烧结机烟气中温SCR脱硝工程4.5.1 烟气换热器寿命 (43)4.5.2烟气换热器运行参数 (44)4.5.3 总的要求 (46)4.5.4 机械设备 (47)4.5.5标准 (49)4.5.6性能保证值 (49)4.5.7 供货清单 (50)4.6 引风机 (51)4.6.1 引风机基本参数 (52)4.6.2 标准及规范 (52)4.6.3 引风机选型参数 (53)4.6.4 引风机性能要求 (54)4.6.5 结构要求(对风机制造的基本要求)/系统配置要求 (56)4.6.6 配供的辅助设备要求 (57)4.6.7性能保证及技术要求 (63)4.6.8 数据表 (65)4.6.9 供货范围 (67)4.7 冷凝消白烟系统 (70)4.8 土建 (71)4.8.1范围 (71)4.8.2 技术要求 (71)4.9废弃催化剂处理 (77)5 性能保证指标 (79)5.1 性能保证要求 (79)5.1.1 设备运转率 (79)5.1.2 能力保证 (79)5.1.3 噪音 (79)5.2 可靠性保证 (79)5.2.1 脱硝效率 (79)5.2.2 排放指标 (79)6 主要能源、介质消耗 (79)7 主要工艺设备清单 (81)8 供货范围 (87)- 2 -XX有限公司1×132㎡烧结机烟气中温SCR脱硝工程8.1 概述 (87)8.1.1 总论 (87)8.1.2 供货原则 (87)8.2 供货及工作范围 (88)8.2.1 设计范围 (88)8.2.1.1 脱硝还原剂 (89)8.2.1.2 烟气 (89)8.2.1.3 蒸汽 (89)8.2.1.4 压缩空气 (89)8.2.1.5 除盐水 (89)8.2.1.6 冷却水 (89)8.2.1.7 电气 (89)8.2.1.8 沟道、管架、支架 (89)8.2.1.9 平台、扶梯 (90)8.2.1.10 检修起吊设施 (90)8.2.1.11 保温、油漆 (90)8.2.1.12 电气、热控 (90)8.2.1.13 消防 (90)8.2.1.14 暖通、给排水、通讯 (90)8.2.1.15 土建 (90)8.2.2 供货范围 (90)8.2.2.1 乙方供货范围 (90)8.2.2.2 甲方的范围 (91)8.2.2.3 施工及安装 (91)8.2.2.4 调试 (91)8.2.3 供货项目 (91)8.3 工作要求 (93)9 技术资料及交付进度 (94)9.1、一般要求 (94)9.2、资料提交的基本要求 (94)9.3、图纸资料清单 (96)9.4、交付进度 (96)10 设备监造(检验)和性能验收试验 (96)10.1、概述 (96)10.2、工厂检验及试验 (97)10.3、设备监造 (97)10.4、调试指导 (101)10.5、性能验收试验 (101)11 技术服务和设计联络 (102)11.1、乙方现场技术服务 (102)- 3 -XX有限公司1×132㎡烧结机烟气中温SCR脱硝工程11.1.1 现场服务的基本要求 (102)1.2 乙方现场服务人员应具有的资质: (105)1.3 乙方现场服务人员的职责 (106)11.2、培训 (107)11.2.1 总则 (107)11.2.2 乙方的责任和义务 (108)11.2.3 业主的义务 (109)11.3、设计联络会 (110)11.3.1 目的 (110)11.3.2 第一次设计联络会 (110)11.3.3 第二次设计联络会 (111)11.3.4 第三次设计联络会 (112)11.3.5 签字 (112)11.3.6 日常联系和配合 (112)11.4、设计确认 (112)12 工期 (112)- 4 -XX 有限公司1×132㎡烧结机烟气中温SCR 脱硝工程51 总论1.1 项目名称项目名称:XX 有限公司1×132㎡烧结机烟气中温SCR 脱硝工程。
昆钢130m 2烧结机技术进步

昆钢 科 技 K n agK j u gn ei
2o 0 8年 l 1月
昆钢 1O 2烧 结 机 技 术进 步 m 3
桂 林峰 周 菊
( 炼铁 厂 )
摘
要
介 绍 了近几年 昆钢烧结 第二作 业区通 过布料 方式的改进 、增设 生石灰 消化 器和 水份 自动控 制 。以
及烧结机 漏风 治理 等生产工 艺技术改造 ,并通过 一 系列技 术管理措施 ,使 烧结矿 的各项 经济、技 术指标 获
得 了较 为显著 的提 高 ,取得 了较好的经济效益 。
关键词 技 术 改造 烧 结矿 产 量
l 前 言
昆钢炼铁厂现有两个烧结作 业区 ,其 中第二作业
区有两 台 10 烧结机 ,于 19 年 8月投产 ,设计生 3 98
这一矛盾 ,炼铁 厂于 2 o 底至 20 年初利用 烧结 06年 0r 7
曲线单层矿槽 ,使 用含油尼龙衬板 ,将下层 矿仓
由四方 型 改 为 圆 弧 型 ,进行 改 造 后 ,取 得 了较 好
的效 果 ,矿槽 堵 料 、棚 料 的 次 数 大 幅度 减 少 ,确 保 了布 料 的连续 、稳 定 。
性 能较差 的烧 结 矿 置 换 性 能较 好 的烧 结 矿作 为铺 底料 ,将 置换 出来 的烧 结 矿供 高 炉 使 用 ,从 而 达 到 改善入 炉 烧 结 矿 实 物 质 量 的 目的 。对 铺 底 料 粒
的探索 ,将 松 料 棒 改 为 宽 为 5 m 0 m,厚 度 为 1m 2m
混 合 料 矿槽 原 设 计 为 双 层 料 仓 ,矿 槽 内部 衬
表 1 混合料层粒度的分布情况
・
9 ・ 6
济钢320m2烧结机机头电除尘器技术改造
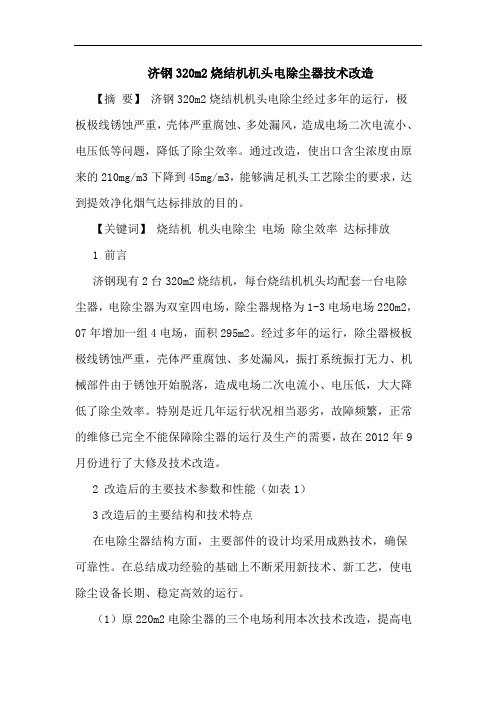
济钢320m2烧结机机头电除尘器技术改造【摘要】济钢320m2烧结机机头电除尘经过多年的运行,极板极线锈蚀严重,壳体严重腐蚀、多处漏风,造成电场二次电流小、电压低等问题,降低了除尘效率。
通过改造,使出口含尘浓度由原来的210mg/m3下降到45mg/m3,能够满足机头工艺除尘的要求,达到提效净化烟气达标排放的目的。
【关键词】烧结机机头电除尘电场除尘效率达标排放1 前言济钢现有2台320m2烧结机,每台烧结机机头均配套一台电除尘器,电除尘器为双室四电场,除尘器规格为1-3电场电场220m2,07年增加一组4电场,面积295m2。
经过多年的运行,除尘器极板极线锈蚀严重,壳体严重腐蚀、多处漏风,振打系统振打无力、机械部件由于锈蚀开始脱落,造成电场二次电流小、电压低,大大降低了除尘效率。
特别是近几年运行状况相当恶劣,故障频繁,正常的维修已完全不能保障除尘器的运行及生产的需要,故在2012年9月份进行了大修及技术改造。
2 改造后的主要技术参数和性能(如表1)3改造后的主要结构和技术特点在电除尘器结构方面,主要部件的设计均采用成熟技术,确保可靠性。
在总结成功经验的基础上不断采用新技术、新工艺,使电除尘设备长期、稳定高效的运行。
(1)原220m2电除尘器的三个电场利用本次技术改造,提高电场高度,与四电场上部平齐,下部保持原有高度,电除尘器的有效断面积增加为252m2。
板线极配是480c型极板配阴极线十齿芒刺线,芒刺为不锈钢,同极间距600mm改为450mm,通道数30个改为40个,阳极板390型改为480c型,阳极板排数32排改为42排。
(2)原295m2电除尘器保留原除尘器高度,板线极配是480c 极板配星形线不锈钢线,同极间距450mm,通道数48个,阳极板排数50排。
(3)振打系统阳极为底部挠臂锤双侧振打,阴极为中部葫芦锤双层振打。
(4)钢结构性能保证。
电除尘器的支座部分,是钢支柱与电除尘器本体的联接构件,本次技术改造应最大化利用现有支座,将原除尘器四电场的一固定支座改造为活动支座。
132m~2烧结机配料控制系统设计
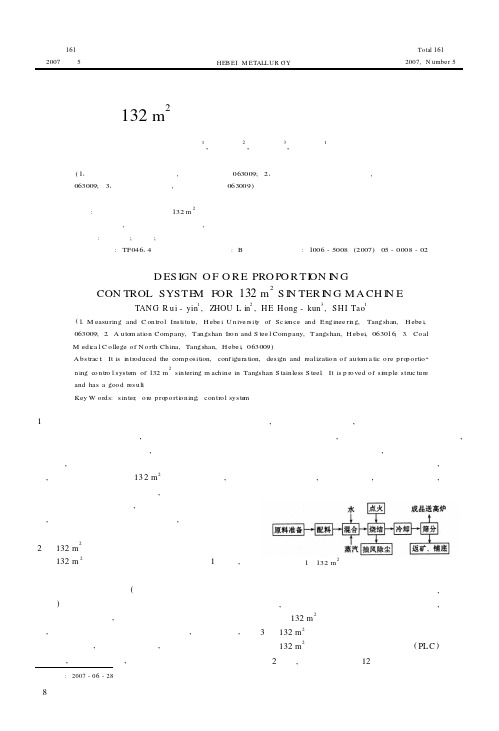
总第161期2007年第5期河北冶金HEB EI M ETALLUR GYTotal1612007,N umber5收稿日期68132m2烧结机配料控制系统设计唐瑞尹1,周 林2,何鸿鲲3,史 涛1(11河北理工大学 计控学院,河北 唐山 063009;21唐山钢铁公司 自动化公司,河北 唐山 063009;31华北煤炭医学院,河北 唐山 063009)摘要:介绍了唐山不锈钢厂132m2烧结机配料自动控制系统的组成、配置及各项控制功能的设计思想和实现方法,该控制系统结构简单,控制效果良好。
关键词:烧结机;配料;控制系统中图分类号:TF04614 文献标识码:B文章编号:1006-5008(2007)05-0008-02D ES IGN O F O RE PRO PO R TI ON I N GCON TROL SYSTE M FOR132m2S I N TER I N G M A CH I N E TAN G R u i-yin1,ZHOU L in2,H E H ong-kun3,SH I Tao1(1.M easuring and C ontrol Institut e,H ebe i U nive rsit y of Sc ience and E nginee ri ng,Tangshan,H ebe i, 063009;2.A uto m ati on Company,T angshan Iron and S tee l Company,T angshan,H ebei,063016;3.Coal M edi ca l C ollege of N orth China,Tangshan,H ebe i,063009)A bstrac t:It is i ntroduced the composition,conf igura tion,design and realization of auto m a tic ore pro portio2 ning contro l system of132m2sintering m achine in Tangshan S tainless S teel.It is p roved of si mple struc ture and has a good result.Key W ords:sinter;ore pro porti oning;control syste m1 引言在激烈的市场竞争中,高炉炼铁对入炉烧结矿的质量和用量要求日益提高,同时烧结设备向大型化发展,要求更高的生产率和更低的生产成本。
迁安燕山钢铁

河北钢铁集团燕山钢铁有限公司1 x 132 m²烧结机烟气脱硫工程唐山长城钢铁集团燕山钢铁有限公司一台132m2烧结机采用北京中科烟气脱硫技术建一套烟气脱硫装置。
脱硫装置建在机头静电除尘器和烧结主抽风机后,脱硫后的烟气不设除尘系统。
脱硫前烟气中SO2原始排放浓度:200~1000mg/Nm3,设计时按工况下最大SO2浓度1000mg/m3考虑,烟气脱硫后达到如下指标:SO2浓度≤50mg/Nm3。
工程建成后脱硫系统前期运行时采用石灰做脱硫剂,随后在燕山钢铁有限公司其它几套脱硫装置建成后统一改用镁砂烟气脱硫技术,由北京中科公司出资建一套硫酸镁回收生产线,生产袋装硫酸镁,我公司统一经营销售。
本脱硫系统主要特点如下:1、脱硫系统初期采用石灰-石膏法烟气脱硫方法,脱硫系统副产物为石膏。
2、本脱硫系统采用喷淋塔吸收技术,塔内喷淋及布流装置采用最优化设计,液气比远远低于传统的石灰-石膏法烟气脱硫技术,液气比仅为5L/Nm3。
3、脱硫系统采用多级液固分离技术及优质的压滤设备,脱硫副产物石膏含水量低于10%,为干态排放,无漏水及扬尘现象。
4、132m2烧结机机头烟气通过一座烟囱排放,烟气由一套脱硫系统处理(一塔)处理,节约成本。
5、整套脱硫系统的压力损失(压差)在1000~1300Pa。
6、脱硫塔直径为φ8m。
7、滤清液循环利用,整个脱硫系统无废水外排。
8、脱硫系统本着节约用电,降低成本的原则,不选用耗电高、功率大,效率底的电机、泵。
9、脱硫系统对环境无污染,包括水、空气、产物外排、噪音等均达到了国家行业、公司的最高要求。
10、脱硫设施运行后不影响烧结机工况。
11、脱硫工艺与设备技术先进,运行稳定可靠,操作维修简单易行。
烟气参数项目单位数据烟气量(工况,湿基)m3/h840000烟气温度℃100~160烟气压力Pa-450~-110SO2浓度(工况,湿基)mg/m3200~1000颗粒物浓度mg/m350~400氮氧化物mg/m30~160O2含量%0~20%烟气湿度%0~11%。
烧结机烟气脱硫改革项目环评表

对全部高中资料试卷电气设备,在安装过程中以及安装结束后进行高中资料试卷调整试验;通电检查所有设备高中资料电试力卷保相护互装作置用调与试相技互术关,通系电1,力过根保管据护线生高0不产中仅工资2艺料22高试2可中卷以资配解料置决试技吊卷术顶要是层求指配,机置对组不电在规气进范设行高备继中进电资行保料空护试载高卷与中问带资题负料2荷试2,下卷而高总且中体可资配保料置障试时2卷,32调需3各控要类试在管验最路;大习对限题设度到备内位进来。行确在调保管整机路使组敷其高设在中过正资程常料1工试中况卷,下安要与全加过,强度并看工且25作尽52下可22都能护可地1关以缩于正小管常故路工障高作高中;中资对资料于料试继试卷电卷连保破接护坏管进范口行围处整,理核或高对者中定对资值某料,些试审异卷核常弯与高扁校中度对资固图料定纸试盒,卷位编工置写况.复进保杂行护设自层备动防与处腐装理跨置,接高尤地中其线资要弯料避曲试免半卷错径调误标试高方中等案资,,料要编试求5写、卷技重电保术要气护交设设装底备备置。4高调、动管中试电作线资高气,敷料中课并设3试资件且、技卷料中拒管术试试调绝路中验卷试动敷包方技作设含案术,技线以来术槽及避、系免管统不架启必等动要多方高项案中方;资式对料,整试为套卷解启突决动然高过停中程机语中。文高因电中此气资,课料电件试力中卷高管电中壁气资薄设料、备试接进卷口行保不调护严试装等工置问作调题并试,且技合进术理行,利过要用关求管运电线行力敷高保设中护技资装术料置。试做线卷到缆技准敷术确设指灵原导活则。。:对对在于于分调差线试动盒过保处程护,中装当高置不中高同资中电料资压试料回卷试路技卷交术调叉问试时题技,,术应作是采为指用调发金试电属人机隔员一板,变进需压行要器隔在组开事在处前发理掌生;握内同图部一纸故线资障槽料时内、,设需强备要电制进回造行路厂外须家部同出电时具源切高高断中中习资资题料料电试试源卷卷,试切线验除缆报从敷告而设与采完相用毕关高,技中要术资进资料行料试检,卷查并主和且要检了保测解护处现装理场置。设。备高中资料试卷布置情况与有关高中资料试卷电气系统接线等情况,然后根据规范与规程规定,制定设备调试高中资料试卷方案。
烧结机烟气脱硫方案_secret

上海***钢铁股份有限公司4#烧结机烟气脱硫改造工程项目建议书ISO9001质量认证注册号:0204Q13071R2M工程设计证书甲级2892福建***脱硫脱硝工程有限公司二00八年六月目录1.前言 (1)2.主要设计原则 (2)3.工程条件 (4)4.标准和规范 (9)5.CFB-FGD脱硫工艺简介 (9)6.项目方案设计说明 (18)7.脱硫布袋除尘器 (23)8.脱硫灰应用介绍 (26)9.设备清册 (29)10.生产组织及人员编制 (35)12.环境效益 (37)13.项目投资及运行成本估算 (37)14.主要技术经济指标 (38)15.结论及建议 (38)16.附图及其它 (39)1.前言上海***钢铁股份有限公司对1#、2#烧结机进行易地改造,新建2台400m2烧结机(下简称4#、5#烧结机),一期先新建1台400m2烧结机(4#烧结机),根据南京市政府和宝钢股份的要求,烧结烟气排放需达到清洁生产标准等规定的要求,拟对400m2烧结机增设一套烟气脱硫装置,并进行全烟气脱硫处理。
针对上海***钢铁股份有限公司4#烧结机提供的设计条件,进行400m2烧结机烟气脱硫除尘项目的方案设计。
福建***脱硫脱硝工程有限公司认为采用循环流化床(干法)烟气脱硫工艺具有下列优势:1)循环流化床(干法)脱硫工艺整个过程为干态,符合烧结主工艺的干态要求,以实现文明生产。
2)循环流化床(干法)脱硫工艺可以脱除100%的SO3,因此烟道、烟囱不用防腐,大大节省烟囱防腐所需的防腐费用和运行维护费用。
3)循环流化床(干法)脱硫工艺可以有效地脱除HCl、HF、重金属等有害物质,实现多组份污染物脱除。
4)CFB-FGD脱硫工艺的出口烟温在75℃以上,无需烟气再热排放,对周围环境影响小。
CFB-FGD脱硫工艺无废水排放,符合梅钢清洁生产的要求。
5)CFB-FGD脱硫工艺在Ca/S比为1.3左右,脱硫率可达到95%以上,与湿法工艺相当,完全可满足环保要求。
烧结机烟气脱硫氧化镁法的应用课件

02
CATALOGUE
氧化镁法脱硫技术原理
氧化镁法脱硫技术的基本原理
氧化镁法脱硫技术是一种基于化学反应的烟气脱硫方法,利 用氧化镁作为吸收剂,通过与烟气中的二氧化硫反应,生成 硫酸镁和水,从而达到脱硫的目的。
该反应需要在一定温度和压力条件下进行,通过循环流化床 反应器实现高效脱硫。
氧化镁法脱硫技术的反应过程
烧结机烟气脱硫技术的发展
近年来,随着环保要求的不断提高,烧结机烟气脱硫技术也在不断发展。新型的脱硫剂和脱硫工艺不断涌现,如 氧化镁法、氧化钙法等。这些新技术具有更高的脱硫效率和更低的运行成本,为钢铁企业实现减排提供了更多选 择。
烧结机烟气脱硫技术的分类与比较
烧结机烟气脱硫技术的分 类
根据使用的脱硫剂和工艺的不同,烧结机烟 气脱硫技术可分为湿法脱硫和干法脱硫两大 类。湿法脱硫技术是指利用液态的脱硫剂对 烟气进行洗涤,通过化学反应将硫氧化物转 化为硫酸盐或硫化物。干法脱硫技术是指利 用固态的脱硫剂与烟气中的硫氧化物进行反 应,生成固态的硫酸盐或硫化物。
。
THANKS
感谢观看
பைடு நூலகம்
氧化镁法在烧结机烟气脱硫中的技术改进与优化
优化反应条件
通过调整反应温度、pH值、反应时间 等参数,提高氧化镁的利用率和脱硫效
率。
副产物的资源化利用
对脱硫副产物进行回收和再利用,如 提取其中的有价组分、生产建筑材料
等,实现资源的最大化利用。
新型催化剂的研究与应用
探索能够有效促进氧化镁脱硫反应的 催化剂,降低反应活化能,提高反应 速率。
烧结机烟气脱硫氧化镁法是一种有效 的烟气脱硫技术,具有较高的脱硫效 率和较低的运行成本,能够满足日益 严格的环保要求。
安钢2#烧结机烟气脱硫运行实践
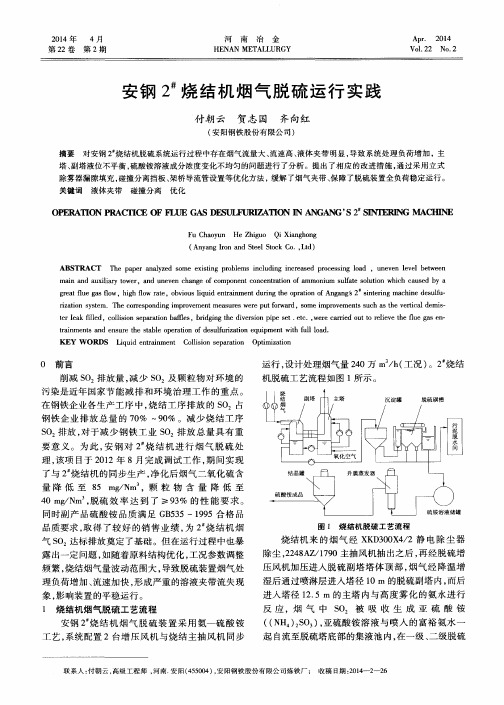
除雾器漏隙填充 , 碰撞 分离 挡板 、 架桥导流管设置 等优 化方 法 , 缓解 了烟气夹带 、 保障 了脱硫装置全负荷稳定运行 。
关键词 液体夹带 碰撞分离 优化
I ON T I N ANGANG ’ S 2 s 】 NI 1 Ⅱ M a印 E
OP E RAT I ON P RAC TI CE OF F L UE GAS DE S  ̄
t e r l e a k f i l l e d,c o l l i s i on s e p ra a t i o n b a f le f s ,br idg i n g t he d i v e r s i o n pi p e s e t. e t e ., we r e c a r r i e d o u t t o r e l i e v e t he l f ue g a s e n —
2 0 1 4年 4月
河
南
冶
金
Apr . 2 01 4
第2 2卷
第 2期
HE NAN MET AL L URGY
Vo 1 . 2 2 No . 2
安钢 2 # 烧 结 机 烟 气 脱 硫 运 行 实 践
付 朝 云 贺 志 国 齐 向红
( 安阳钢铁股份有限公司 )
t r a i n me n t s a n d e n s u r e t h e s t a b l e o p e r a t i o n o f d e s u f l u i r z a t i o n e q u i p me n t w i t h f u l l l o a d . KEY W ORDS L i q u i d e n t r a i n me n t C o l l i s i o n s e p ra a t i o n Op t i mi z a t i o n
钢铁有限公司一期132m2和二期180m2烧结机机头烟气脱硫工程可行性研究报告
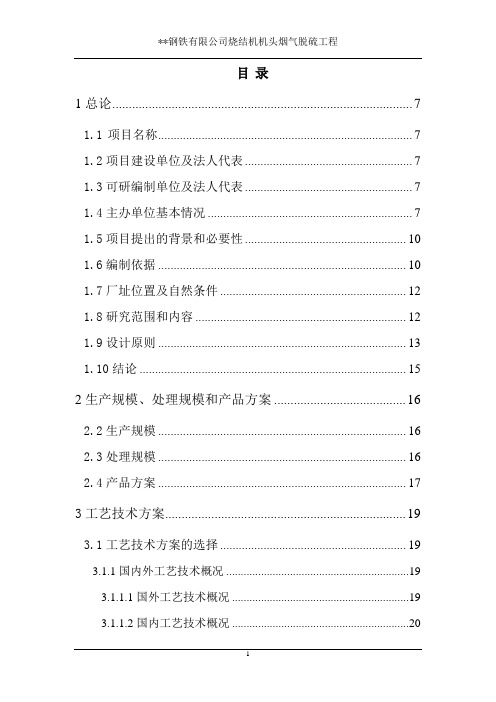
目录1总论 (7)1.1项目名称 (7)1.2项目建设单位及法人代表 (7)1.3可研编制单位及法人代表 (7)1.4主办单位基本情况 (7)1.5项目提出的背景和必要性 (10)1.6编制依据 (10)1.7厂址位置及自然条件 (12)1.8研究范围和内容 (12)1.9设计原则 (13)1.10结论 (15)2生产规模、处理规模和产品方案 (16)2.2生产规模 (16)2.3处理规模 (16)2.4产品方案 (17)3工艺技术方案 (19)3.1工艺技术方案的选择 (19)3.1.1国内外工艺技术概况 (19)3.1.1.1国外工艺技术概况 (19)3.1.1.2国内工艺技术概况 (20)3.1.2工艺技术方案的比较和选择 (20)3.2工艺流程 (22)3.2.1工艺流程概述 (22)3.2.1.1烟气系统及SO2吸收系统 (23)3.2.1.2脱硫剂浆液制备系统(一二期公用) (23)3.2.1.3石膏处理系统(一二期公用) (24)3.2.1.4物料系统(一二期公用) (24)3.2.2装置规模和年操作时数 (24)3.2.2.1装置组成 (24)3.2.2.2年操作时数 (26)3.2.3原材料和动力 (27)3.2.4物料平衡 (27)3.2.4.1一期132m2烧结机 (27)3.2.4.2二期180m2烧结机 (28)3.3主要设备选择 (30)3.3.1非标设备的设计制作 (30)3.3.2关键设备方案比选 (32)3.3.2.1脱硫增压风机 (32)3.3.2.2浆液循环泵 (32)3.3.2.3真空皮带脱水机(一二期公用) (32)3.4自动控制 (33)3.4.1控制方式 (33)3.4.2热工自动化功能 (34)3.4.3热工自动化设备选型 (36)3.4.4工业电视监控 (37)3.4.5电源 (37)3.4.6气源 (38)3.4.7控制室的设置 (38)4原材料、燃料和动力供应 (38)4.1主要原材料、燃料的种类、规格、年需要量 (39)4.2主要原材料市场分析 (39)4.2.1供应状况分析 (39)4.2.2供应可靠性分析 (39)4.3水、电和其它动力供应 (39)5总图布置和土建 (40)5.1总图布置 (40)5.1.1设计原则和依据 (40)5.1.2总平面布置 (40)5.1.3竖向布置 (41)5.1.4储运 (41)5.2土建 (42)5.2.1工程地质条件和地基基础 (42)5.2.2土建结构设计方案 (43)6公用工程 (44)6.1给排水 (44)6.2供电 (45)6.2.1设计范围 (45)6.2.2脱硫部分电气接线及布置 (45)6.2.3主要设备选择 (46)6.2.4照明电源 (47)6.2.5接地系统 (47)6.2.6电缆设施 (47)6.3维修设施 (47)7环境保护 (48)7.1环境状况 (48)7.2主要污染物排放 (48)7.3绿化 (50)7.4环境管理及监测机购 (50)8劳动保护与安全卫生 (50)8.1采取劳动保护和安全卫生的场所 (50)8.2防火防爆 (50)8.3防尘、防毒、防腐蚀 (51)8.4防电伤、防机械伤害及其它伤害 (51)8.5防噪声危害 (52)8.6防暑、防潮、防寒 (53)8.7机构设置 (54)9消防与节能 (54)9.1设计原则 (54)9.2防火措施 (55)9.3节能 (55)10组织机构和人力资源配制 (56)10.1组织机构设置 (56)10.2人员编制 (57)10.3职工培训 (57)11项目实施计划 (57)11.1项目组织和管理 (57)11.2实施进度计划 (57)12投资估算和资金筹措 (58)12.1总投资估算 (58)12.1.1投资范围 (58)12.1.2编制依据 (58)12.1.3工程投资估算 (59)12.2资金筹措 (59)13项目评价 (62)13.1基本经济数据 (62)13.2有关费用 (63)13.3财务评价 (63)13.4环境效益和社会效益 (63)13.4.1环境效益 (63)13.4.2社会效益 (64)14结论 (65)1总论1.1 项目名称**钢铁有限公司一期132m2和二期180m2烧结机机头烟气脱硫工程。
烧结机废气脱硫工程技术方案

烧结机废气脱硫工程技术方案
背景
烧结机是工业生产过程中常见的设备之一。
然而,烧结机在废
气排放中可能产生硫化物等有害物质,对环境和人体健康造成危害。
因此,为了保护环境和维护健康,需要进行废气脱硫处理。
技术方案
为了实现烧结机废气脱硫,我们提出以下技术方案:
1. 硫化物捕集装置:安装硫化物捕集装置来收集烧结机废气中
的硫化物。
该装置可以有效捕集硫化物,并将其转化为无害物质。
2. 脱硫剂注入系统:建立脱硫剂注入系统,将脱硫剂引入烧结
机废气中。
脱硫剂可以与废气中的硫化物发生化学反应,从而减少
硫化物的含量。
3. 脱硫反应池:配置脱硫反应池,用于使脱硫剂与废气中的硫
化物充分接触。
通过反应池中的化学反应,硫化物将被转化为更为
稳定和无害的物质。
4. 粉尘分离装置:在废气脱硫系统中添加粉尘分离装置,用于将废气中的粉尘分离出来。
这样可以确保脱硫系统的正常运行,并减少对后续设备的污染。
结论
通过以上技术方案,我们可以实现烧结机废气的脱硫处理,减少对环境的污染,保护人体健康。
此方案简洁有效,并可在实际生产中实施。
以上为烧结机废气脱硫工程技术方案的简要说明。
132平方米烧结机烟气脱硫治理工程可行性研究报告

132m2烧结机机头烟气脱硫治理工程可行性研究报告目录1、概述 (1)1.1、项目概况 (1)1.2 研究范围 (1)2、设计依据及基础资料 (2)2.1 设计依据 (2)2.2 治理目标 (2)2.3 治理原则 (3)2.4 设计基础资料及要求 (3)2.5、厂址概况 (5)2.6、工程地质 (5)2.7、水源情况 (5)2.8、交通运输 (6)2.9、大气污染物排放情况 (6)3、脱硫系统建设条件及工艺选择 (6)3.1、吸收剂供应 (6)3.2、可供脱硫系统建设的场地位置 (7)3.3、副产品处置及综合利用 (7)3.4、脱硫系统水、电、气供应状况 (11)3.5、烧结机烟气脱硫方案的选择与确定 (12)3.5.1常用脱硫工艺 (12)3.5.2 湿法脱硫工艺 (13)3.5.2.1 石灰-石膏法脱硫 (13)3.5.2.2 工艺特点: (14)3.5.3 脱硫技术要求 (16)4、脱硫工艺计算 (17)4.1 处理烟气量 (17)4.2 SO2原始排放浓度: (17)4.3 脱硫效率 (17)4.4 生石灰粉耗量 (17)4.5 年脱硫量: (17)4.6 石膏产量: (17)4.7 脱硫反应循环液气比: (18)4.8 Ca/S摩尔比: (18)4.9 Ca O浆液量 (18)4.10 制浆耗水量: (18)4.11 溶液循环流量: (18)4.12 废水排放量的计算 (18)4.13 水、电、汽耗量 (18)5、石灰—石膏法脱硫 (18)5.1 石灰—石膏法脱硫的技术参数 (18)5.2 脱硫工艺流程 (19)5.3 脱硫工艺系统 (20)5.4 主要设备的设计参数及选型 (22)5.5 设备布置 (25)5.6 电气及自动控制系统 (25)5.7设备、管道的防腐 (31)5.8 设备的维护与检修 (31)5.9给排水系统 (31)6、土建 (32)7、环境保护 (35)7.1 设计采用的环保标准 (35)7.2 脱硫系统主要污染源 (35)7.3 主要污染治理措施 (36)7.4、环境效益 (36)7.4.1、实施脱硫工程前后的环境影响分析 (36)7.4.2 社会及经济效益 (37)8、节能降耗 (37)9. 安全、消防与劳动保护 (38)9.1、劳动安全 (39)9.2安全防护措施 (39)9.3、劳动保护 (40)9.4、劳动保护措施 (40)10、劳动定员、调试和培训 (40)11、项目实施与工程进度计划 (43)11.1项目实施条件 (43)11.2项目实施办法 (44)11.3 项目实施进度计划 (44)12、主要设备表和技术经济分析 (45)12.1 主要设备表 (45)12.2 工程费用估算(详见后附表) (49)12.2.1、投资概况 (49)12.2.2、编制依据 (49)12.3 脱硫系统运行费用估算 (49)13、附图 (49)13.1 烟气脱硫工艺图 (49)13.2 烟气脱硫电气图 (49)13.3 烟气脱硫控制图 (49)14.结论 (50)14.1、主要结论和意见 (50)14.2、存在的问题 (50)1、概述1.1、项目概况1.1.1、编制依据1) 按照《火力发电厂烟气脱硫工程项目可行性研究报告内容深度规定》2) 按照《“十一五”十大重点节能工程实施意见》3) XX公司提供的有关资料1.1.2、项目概况XX公司(主要设备简介)现有132m2 烧结机一台,烧结主抽风机设计风量14500m3/min,全压值16.5KPa。
烧结烟气脱硫

烧结机烟气脱硫工程初步设计说明书目录第一章总论 (1)第二章脱硫工艺 (6)第三章供配电 (11)第四章自动控制系统 (20)第五章仪表 (35)第六章土建 (37)第七章总图 (39)第八章热力 (41)第九章给排水 (43)第十章技术经济分析 (44)第十一章环境保护与综合利用 (47)第十二章能源、安全与工业卫生 (48)第十三章工程进度 (49)1总论1.1概述本工程技术方案和设计是对主抽烟机后的烟道烟气进行脱硫。
烧结燃烧过程中产生烟气通过主抽烟系统排出,主抽烟系统由风箱、烟道、除尘器、主抽烟机及烟囱组成。
由风箱抽出的烟气进入烟道,然后进入该烟道后部的除尘器和主抽烟机,烟气经过主抽风机后直接排入烟囱,在主抽风机后安装脱硫装置,烟气经脱硫后再由烟囱排放。
当脱硫系统出现停机时,关闭脱硫系统进风烟道阀和出风烟道阀,打开旁路烟道阀,烟气经烟囱排放。
本方案相对于整体烧结系统实际为单独装置,因此也称脱硫岛。
(1) 厂址工程条件脱硫装置安装在XX130m2烧结机改造工程预留脱硫场地。
海拔高度(以海防高程零点为基准):1840m,最高气温:33.3℃,最低气温:—7℃,年平均气压:81000Pa。
年平均相对湿度:72%,地震烈度:8度。
(2)烧结生产用原燃料条件(3)烟气条件主抽风系统由风箱、集气管、多管除尘器、主抽风机及烟囱组成。
每台烧结机的风箱从烧结机台车抽风。
风箱下端连接进入总烟道,烟道内的烟气进入一台多管除尘器,烟气经多管除尘后,再经主抽风机室送入烟囱。
1.2范围烟气由主抽烟机后的脱硫系烟道引出,进入脱硫系统,脱硫后的烟气再送回主抽烟机后的脱硫系烟道。
项目范围包含整个烟气的引出、处理、返回过程的全部设施。
烟道接口位置见脱硫工艺平面图。
能源介质(除电源外)由业主方提供,交接点位置为业主方提供的红线外1m 处;6kV电源一回路直接由39AH高压柜用YJV-6kV电缆引到本项目变配电室的高压开关柜或高压电机软起动柜。
烧结机烟气脱硫工程技术方案

工艺流程图
根据选择的脱硫技术,绘制工艺流 程图,包括烟气收集、吸收剂制备 、吸收反应、产物处理等环节。
主要工艺参数
确定主要工艺参数,如吸收剂用量 、反应温度、气体流量等,以满足 脱硫效率和排放浓度的要求。
主要设备及材料需求
主要设备
根据所选的脱硫技术和工艺流程,确 定主要设备包括吸收塔、石灰浆制备 系统、循环泵、风机等。
05
技术方案效益评估及风险分析
环境效益评估
减少污染物排放
采用烟气脱硫技术可以显著减少 烧结机产生的二氧化硫等污染物 的排放,对改善周边环境和空气
质量具有积极作用。
降低对环境的破坏
减少污染物排放有助于减缓环境 破坏,降低生态系统的压力,为 生态环境的可持续发展做出贡献
。
符合环保政策
随着全球环保意识的提高,各国 政府对环境保护的要求越来越严 格,采用烟气脱硫技术符合政府
材料需求
根据所选的脱硫技术和工艺流程,确 定需要的材料包括石灰、吸收剂、滤 料等。同时需要考虑材料的质量要求 、供应能力等因素。
04
技术方案实施及运行管理
技术方案实施计划
方案设计
设备采购
包括脱硫效率、排放浓度、排放速率等关 键指标的设定,以及脱硫剂选择、吸收剂 喷射等具体技术路线的确定。
依据方案设计,采购符合要求的相关设备 ,确保设备性能稳定、满足环保要求。
经济风险
烟气脱硫技术投资较大,可能面临资金短缺、成本过高等问题。建议企业充分 考虑自身的经济实力和市场需求,制定合理的投资计划和成本控制策略。
06
结论与展望
技术方案结论
经过实验验证,该技术方案在烧结机烟气脱硫方面具有显著效果,能够有效降低烟气中的 SO2和颗粒物含量,达到国家排放标准。
提高烧结机烟气脱硫效率的措施
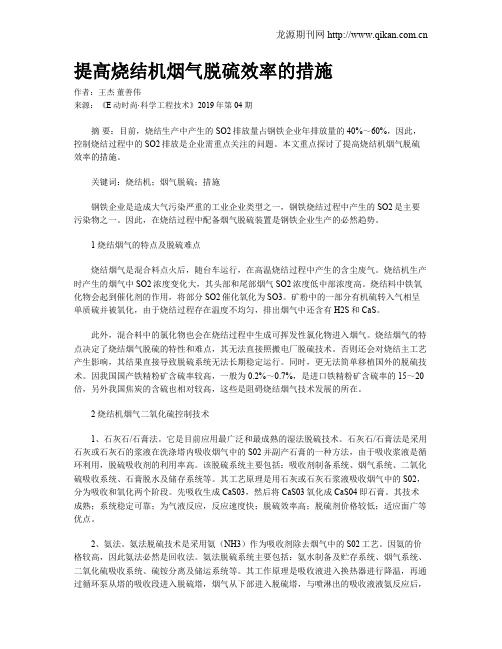
提高烧结机烟气脱硫效率的措施作者:王杰董善伟来源:《E动时尚·科学工程技术》2019年第04期摘要:目前,烧结生产中产生的SO2排放量占钢铁企业年排放量的40%~60%,因此,控制烧结过程中的SO2排放是企业需重点关注的问题。
本文重点探讨了提高烧结机烟气脱硫效率的措施。
关键词:烧结机;烟气脱硫;措施钢铁企业是造成大气污染严重的工业企业类型之一,钢铁烧结过程中产生的SO2是主要污染物之一。
因此,在烧结过程中配备烟气脱硫装置是钢铁企业生产的必然趋势。
1 烧结烟气的特点及脱硫难点烧结烟气是混合料点火后,随台车运行,在高温烧结过程中产生的含尘废气。
烧结机生产时产生的烟气中SO2浓度变化大,其头部和尾部烟气SO2浓度低中部浓度高。
烧结料中铁氧化物会起到催化剂的作用,将部分SO2催化氧化为SO3。
矿粉中的一部分有机硫转入气相呈单质硫并被氧化,由于烧结过程存在温度不均匀,排出烟气中还含有H2S和CaS。
此外,混合料中的氯化物也会在烧结过程中生成可挥发性氯化物进入烟气。
烧结烟气的特点决定了烧结烟气脱硫的特性和难点,其无法直接照搬电厂脱硫技术。
否则还会对烧结主工艺产生影响,其结果直接导致脱硫系统无法长期稳定运行。
同时,更无法简单移植国外的脱硫技术。
因我国国产铁精粉矿含硫率较高,一般为0.2%~0.7%,是进口铁精粉矿含硫率的15~20倍,另外我国焦炭的含硫也相对较高,这些是阻碍烧结烟气技术发展的所在。
2 烧结机烟气二氧化硫控制技术1、石灰石/石膏法。
它是目前应用最广泛和最成熟的湿法脱硫技术。
石灰石/石膏法是采用石灰或石灰石的浆液在洗涤塔内吸收烟气中的S02并副产石膏的一种方法,由于吸收浆液是循环利用,脱硫吸收剂的利用率高。
该脱硫系统主要包括:吸收剂制备系统、烟气系统、二氧化硫吸收系统、石膏脱水及储存系统等。
其工艺原理是用石灰或石灰石浆液吸收烟气中的S02,分为吸收和氧化两个阶段。
先吸收生成CaS03,然后将CaS03氧化成CaS04即石膏。
涟钢130m 2烧结机节能降耗的生产实践
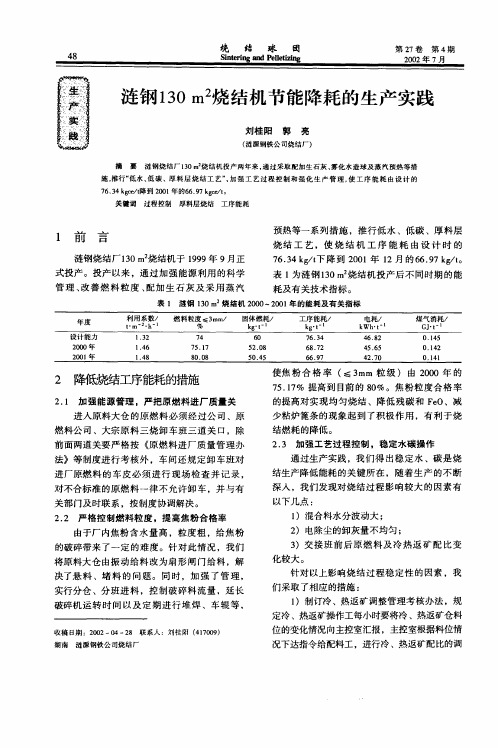
研究 表 明 ,生石灰 具 有 强 化 制 粒 ,改 善 料 层 透气性 的作 用 , 厚料 层烧 结 的有效 强 化 剂 。 是 涟 钢 10m 烧 结 机于 20 年 5月开 始配加 生 石 3 2 01 灰 ,实践 表 明 :生 石 灰 配 加 量 为 2 ~3 时 , % %
度 、终点温度 、冷热返矿仓料位 、混合料仓料
管配
耗 及有 关技 术指标 。
表 1 涟钢 10m 烧 结 机 20 2 0 年 的 能 耗 及 有 关 指标 3 0 0— 0 1
2 降低烧结工序能耗的措施
2 1 加 强 能源 管理 ,严 把原燃 料进 厂质 量关 .
位等 情况 ,并 与岗效 工 资挂钩 考核 。
混合料温度提高4℃以上 ,烧结矿产量可 提高
3 ~5 ,燃 耗可 降低 2 gt % % ~3k /。
24 推行 “ . 低水、低碳、厚料层烧结工艺” 1 )采 用雾 化水造球 和混合料仓蒸汽 预热 混合料技术 为了强化制粒过程和消除过湿带,为提高 料层厚度创造条件 ,20 00年上半年我们和北京
7 .4k /下 降 到 2 0 6 3 g t 0 1年 l 2月 的 6 .7k / 。 6 9 g t 表 1为涟 钢 10m 烧结 机 投 产后 不 同时期 的 能 3
涟钢烧 结 厂 10m 烧结 机 于 19 3 9 9年 9月正
式投 产 。投 产 以来 ,通 过 加 强 能 源 利用 的科 学
2 2 严 格控 制燃 料粒 度 。提高 焦粉 合格 率 .
通 过生 产 实践 ,我们 得 出稳 定 水 、碳 是 烧
结 生产 降低 能耗 的关 键所 在 ,随着 生 产 的 不 断
深入 ,我们 发现对 烧 结 过 程影 响较 大 的 因素 有
2023年钢铁行业烧结烟气脱硫技术

2023年钢铁行业烧结烟气脱硫技术2023年,随着环保意识的不断提高,钢铁行业在烟气处理技术方面迎来了新的突破。
其中烧结烟气脱硫技术是一项关键技术,能够有效减少钢铁行业对环境的污染。
下面将对2023年钢铁行业烧结烟气脱硫技术进行详细的分析。
一、技术原理烧结烟气脱硫技术是指通过一系列化学反应,将烟气中的二氧化硫(SO2)转化为无害的硫酸(H2SO4)或硫酸盐,从而达到减少对大气环境和人体健康的影响的目的。
在2023年,烧结烟气脱硫技术已经得到进一步的改进和创新,具体包括以下几个方面:1. 脱硫剂烧结烟气脱硫技术中最核心的环节就是脱硫剂的选择。
传统的脱硫剂主要是石灰石,但是其脱硫效率较低且生成的废料难以处理。
2023年,新型脱硫剂开始广泛应用,如活性氧化钙、活性炭、脱硫剂缓冲剂等。
这些新型脱硫剂具有脱硫效率高、易于处理废料等优点,能够提高脱硫效果。
2. 沉积物处理烧结烟气脱硫过程中会生成大量的沉积物,传统的处理方式是将其填埋,但这种方法对环境造成了一定的负面影响。
2023年,钢铁行业开始广泛采用沉积物资源化处理技术,将沉积物中的有价值成分回收利用。
同时,对于无法回收利用的沉积物,通过高温焚烧等技术进行无害化处理,减少对环境的影响。
3. 脱硫装置优化在2023年,钢铁行业对烧结烟气脱硫装置进行了进一步的优化。
采用先进的脱硫设备,如湿法烟气脱硫装置、干法烟气脱硫装置等,能够提高脱硫效率,并减少对环境的污染。
此外,还引入了自动化控制技术,能够实现对脱硫装置的自动监测和控制,提高了运行稳定性和可靠性。
二、技术应用2023年,烧结烟气脱硫技术在钢铁行业得到了广泛的应用。
以中国为例,钢铁行业是重要的大气污染源之一,烟气排放中的二氧化硫是主要的污染物之一。
在全国范围内,大量的钢铁企业开始采用烧结烟气脱硫技术进行治理,有效地减少了二氧化硫的排放。
在技术应用方面,钢铁企业通过引进先进的烧结烟气脱硫设备,提高了脱硫效率。
河北省某钢厂烧结机烟气脱硫脱硝技术改造研究

河北能源职业技术学院学报Journal of Hebei Energy College of Vocation and Technology第4期(总81期)2020年12月No.4 (Sum.81)Dec.2020河北省某钢厂烧结机烟气脱硫脱硝技术改造研究孙黎明(开滦能源化工股份有限公司,河北 唐山063000)摘 要:本文针对河北省某钢厂烧结机烟气不达标现状,增设SDA 喷雾旋转脱硫除尘及SCR 选择性催 化还原脱硝装置。
技改后,烧结烟气中颗粒物浓度降至1.8mg/m 3,二氧化硫浓度降至30mg/m 3,氮氧 化物浓度降至45mg/m3,实现达标排放。
关键词:烧结烟气;SDA 脱硫;SCR 脱硝中图分类法:X757 文献识别码:A 文章编号:1671-3974(2020)04-0054-02Research on Flue Gas Desulfurization and Denitrification Technology Transformation ofSintering Machine in a Steel Plant in Hebei ProvinceSun Liming(Kailuan Energy and Chemical Co., Ltd, Tangshan 063004, China)Abstract : In view of the current situation of sintering machine flue gas non —compEance in a steel plant in Hebeiprovince, SDA spray rotary desulfurization and dedusting and SCR selective catalytic reduction denitrationdevice were set up. After technical transformation, the concentration of particulate matter in sintering flue gas is reduced to 1.8 mg / m3, sulfur dioxide concentration to 30 mg / m3, and nitrogen oxide concentration to 45mg / m3, achieving the emission standard.Key words: sintering flue gas; SDA desulfurization; SCR denitration烧结是钢材生产工艺的关键环节,它是将铁矿粉、 焦粉和白云石等按一定比例配制搅拌,烧结出有充足抗压强度和粒度分布的烧结矿。
烧结机脱硫防腐施工方案

XXXX钢铁有限公司132m2烧结机烟气脱硫工程防腐施工组织方案XXXX防腐工程有限公司2009年8月目录第一章、概述 (3)第二章、编制依据 (3)第三章、防腐施工具体方案 (3)1、玻璃鳞片材料的介绍和说明 (3)2、衬里施工方案 (10)第四章、施工机械配置 (14)1。
0现场施工所需工具、辅助设备 (14)2。
0力能供应计划 (14)第五章、施工组织 (15)第六章、设备交接 (15)第七章、施工作业标准书 (16)1.0混凝土槽衬里施工要领 (16)2。
0玻璃鳞片衬里施工要领 (17)3。
0钢制母材设计、制造技术要求 (19)第八章、质量控制和检验 (20)1。
0玻璃鳞片树脂衬里检查规范 (20)2.0玻璃钢衬里检查规范 (22)第九章、安全措施 (24)1.0防腐主要施工内容 (24)2。
0防腐作业安全条件 (24)3。
0防腐安全文明施工措施 (24)4。
0相邻施工单位安全措施 (28)5。
0安全事故应急预案 (28)第十章、材料包装和现场保管 (31)第十一章、工程进度 (32)第十二章、玻璃鳞片、FRP过程保养及整体保养 (32)第一章、概述1、本施工组织适用于XXXX钢铁有限公司132m2烧结机烟气脱硫防腐工程。
包括施工、防腐材料的供应、检查、验收等方面的要求。
2、本施工组织指出的所有准则和标准将看成是本工程的最低要求,没有明确指出但能满足同样最低要求的其它标准,在取得发包人同意后可以采用。
3、材料(包括地方性材料等)的选择及采购供应是施工方的责任,材料保证有良好的性能,以保证防腐内衬工程安全可靠。
4、防腐内衬施工保证有详细的施工技术组织措施及施工方案和最好的工艺设计方案,施工方应承诺对其承担的防腐内衬施工的质量全面负责。
5、整个项目实施所需防腐内衬工程的技术规范包括:供货和服务范围技术要求6、防腐内衬施工执行国家及相关行业或原料供应商企业颁布的相关规程、规范、标准。
第二章、编制依据本要求适用于XXXX钢铁有限公司132m2烧结机烟气脱硫防腐工程。
- 1、下载文档前请自行甄别文档内容的完整性,平台不提供额外的编辑、内容补充、找答案等附加服务。
- 2、"仅部分预览"的文档,不可在线预览部分如存在完整性等问题,可反馈申请退款(可完整预览的文档不适用该条件!)。
- 3、如文档侵犯您的权益,请联系客服反馈,我们会尽快为您处理(人工客服工作时间:9:00-18:30)。
艺从脱硫除尘效果来看,不需预除尘,脱硫过程不影 响除尘。由于吸收塔的旋风分离器会分离一部分飞 灰,使进入除尘器的粉尘总量降低,因而提高了除尘 效率。
烧结机有关工艺参数和烟气脱硫目标如下: 烧结机/m2: 132 烟气流量/m3/h: 720 000 初始 SO2 浓度/㎎/Nm3: 1 200~1 400 初始含尘浓度/㎎/Nm3:200 初始烟气温度/℃: 75~120 排放 SO2 浓度/㎎/Nm3: ﹤200 烟气湿度/%: 2-4 排放含尘浓度/㎎/Nm3: 50 排放烟气温度/℃: ﹥70 设计除尘效率/%: 99.9 设计脱硫效率/%: 94 2.2 脱硫剂、副产品及质量指标 2.2.1 脱硫剂 本项目烧结机烟气脱硫采用生石灰(CaO)作为脱 硫剂。其质量要求如下: CaO≥85%; 粒径<6 mm; SiO2、AL2O3、Fe2O3 等杂物<3%; 反应活性(温升)>40 ℃; 活性度≥350 ml;
(收稿 2009-9-27 责编 崔建华)
作者简介
参考文献 [1] 李久立,李凯苓,李旦,等.机械制造技术基础 [M].济南:济南出
李庆丰,1993 年毕业于天津大学机电分校模具设计与制造专 业,工程师,现从事技术管理工作。
20
※生产工艺研究※
132 m2 烧结机烟气脱硫改造
脱硫剂采用专用石灰罐车运输,气力输送卸料。 2.2.2 脱硫灰
每台旋风分离器下方配一台物料循环给料机,用 来存储和供给循环物料,其底部安装的螺旋计量给料 机可以根据固粒再循环要求,精确控制加入反应塔的 循环量。另一台螺旋送料机则排除多余物料,为后置 除尘器起到了预除尘的作用。 2.4.6 布袋除尘器系统
高压脉冲布袋除尘器具有一般脉冲喷嘴袋除尘 器的结构。一般采用下进风、上排风圆形袋外滤式。根 据现场实际及工艺的需要也可以采用上进风、中部和 底部进风等多种进风方式。
2.4.1 烟道系统
净化烟道系统包括从烧结机出口经 GSCA 反应
塔和旋风分离器出口至布袋除尘器,烟气从除尘器排 出经增压风机排入烟囱,同时从增压风机出口引出循 环烟道构成烟道系统。所有烟道均为钢制,带有外部 加强筋,在适当位置设膨胀节。设有脱硫烟道入口烟 气挡板、增压风机出口烟道挡板、再循环烟道调节挡 板及附属执行机构,密封风机和相关附属设备、热工 仪表等。烟道外壁涂有防锈漆,并加保温。保温层外装 0.50 mm 厚护板。 2.4.2 脱硫剂储存和供给系统
反应塔的流化状态和浆液液膜的形成以及烟气 快速降温都有利于吸收反应的进行,特别是吸收剂的 循环使用,最大程度地利用了吸收剂,提高脱硫效率。 (3) 在更接近绝热饱和温度下运行
如上所述,GSCA 排灰含水量小于 1%,这使得除 尘系统可以在更接近烟气绝热饱和温度的条件下操 作,以达到更高的脱硫效率,而且可以避免固体颗粒 在系统内部堆积、结垢等问题。 (4) 脱硫剂高浓度循环使用,反应塔脱硫效率高
目前国内的烧结烟气脱硫工艺分为湿法和半干 法两种,其中湿法被公认为效率最高的脱硫工艺,但 在生产运行中暴露出很多问题,如投资、占地和耗水 量大,废水二次污染,设备及管路的腐蚀和堵塞。针对 湿法脱硫存在的问题,大连绿诺环境科技有限公司研 发 了 半 干 法 脱 硫 工 艺 , 具 有 代 表 性 的 , 如 :GSCA、 RCFB、SDA、CFB—FGD 和 NID 等。通过对这些方案 的比较,我们选择采用技术成熟可靠的气固悬浮吸收 (GSCA —Gas-Solid Circulating Absorption) 半干法工 艺。该工艺具有脱硫除尘效率高、吸收剂利用率高、耗 水量小、节电、副产品易于处理、占地小、造价低、运行 操作简单、对烟气负荷变化的适应性好、烯烃运行可 靠和无结垢堵塞等优点。与流化床反应塔相比,该工
由于反应塔内高浓度固体颗粒处于流化状态,促 使其能高效传递,因此反应充分,脱硫彻底。 (5) 高效去除酸性气体
由于 GSCA 可以在较低的温度下运行,使得系统 可以取得较高的酸性气体去除率,脱硫达 96%和脱 HCl98%以上。脱硫效率易于控制,可以通过控制出口 气体温度或吸收剂供给速率来实现。 2.5.2 精确控制固粒循环量
反应器,通过旋风分离器使脱硫产物与残留脱硫剂、
飞灰分离,残留脱硫剂和飞灰分离循环进入反应器,
提高脱硫剂的利用率。
2.3.4 副产物去向
反应器内生成的副产物随烟气一起进入旋风分
离器,被分离器捕集后,一部分进行循环再利用,一部
分与后续布袋除尘器收集的脱硫灰一并排至灰仓,送
到料场循环利用。
2.4 新增系统以及相关设备、设施
去处理
图 1 气固再循环烟气脱硫系统
2.3.1 烧结烟气脱硫的主要化学反应
2.3.2
CaO+ H2O→Ca(OH) Nhomakorabea Ca(OH)2+ SO2→CaSO3+ H2O Ca(OH)2+2HCI→CaCl2+2H2O
CaSO3+1/2O2→CaSO4 烟气流程
主抽风机出口烟气被引入反应器底部,在此与
水、脱硫剂和具有反应活性的循环灰相混合,脱去
脱硫工程采用的布袋除尘器有如下特点: (1) 采用气流分布均匀的进气和箱体结构。对于大 气量多箱体结构,采用空气动力模式确定布气设计; (2) 采用高压(0.7 MPa)脉冲,改善喷吹效果,延长 滤袋寿命; (3) 全气密封的结构设计和制作,消除漏风; (4) 脉冲喷吹控制灵活、可靠,可以离线或在线喷 吹,保证在各种工况下的喷吹效果; (5) 排灰和灰斗设计能有效防止金结和堵灰。 2.4.7 增压风机及烟气循环系统
在每套布袋除尘器之后装一台增压风机,克服净 化系统阻力。在增压风机出口烟道上引出烟气循环烟 道,返回 GSCA 反应塔。在烧结机低、变负荷运行时, 从增压风机出口引出净化后的烟气进入 GSCA 反应 塔与待净化烟气混合,使反应塔保持最佳气流量。 2.4.8 仪控系统
采用 PLC 系统控制气固循环一体化烟气脱硫净 化系统相关设备的启动、停运、参数调节和自动控制 以及安全保护,主要信号保持和烧结机总控制室的通 讯接口。 2.5 工作原理及特点 2.5.1 固粒流化态的反应塔
关键词 烧结机 烟气 脱硫 半干法 改造
1 前言 天铁集团烧结厂 132 m2 烧结机自 1989 年投产
以来,烧结过程中产生大量粉尘和 SO2 等有害物质, 对环境造成严重污染。为减少烧结生产过程中 SO2、烟 尘等有害物质的排放,满足环保要求,烧结厂在 132 m2 烧结机机头电除尘器工序后增加了气固再循环烟 气脱硫系统和布袋除尘器系统。增加的系统能够对烧 结机机头的烟气实施脱硫作用,除去机头烟气中的烟 尘和灰粒,净化后使通过烟囱排入大气的烟气符合国 家排放标准。 2 脱硫工艺 2.1 脱硫工艺选择
SO2,然后通过烟道引入后续除尘器,除去烟尘和灰 粒。净化后的烟气通过烟囱排入大气。
2.3.3 脱硫剂流程
脱硫剂通过输送系统进入反应器。在反应器中,
由于床料的存在使脱硫剂以较大的表面积散布,并与
含 SO2 的烟气充分接触,脱去烟气中的 SO2。在烟气作 用下,脱硫产物同残留脱硫剂和飞灰固体物一起贯穿
与其它循环流化床类脱硫反应塔不同,GSCA 反
22
※生产工艺研究※
132 m2 烧结机烟气脱硫改造
应塔采用装于文氏管内的三流体喷枪,将脱硫剂浆 液、水和压缩空气在喷嘴处混合喷入高速热气流中。 这样可使脱硫剂、水与烟气可在极短时间内充分混 合。脱硫剂均匀分布在浆液雾化后的细液滴中,有效 增大接触面积,易于充分吸收烟气中的酸性成分,提 高反应速度。由于浆液自气流中心区扩散,最大程度 地避免了粘壁积垢现象。采用定压变流量供喷枪浆液 和水,可以在保证压力稳定和雾化质量的前提下,精 确控制喷嘴浆液量和喷水量。 2.5.4 采用净化烟气再循环
21
2009 年第 6 期
喷枪位于文氏管喉部。熟化石灰浆液、压缩空气 和水一起进入喷枪混合喷出。浆液被压缩空气雾化, 在喉部高速气流作用下进一步粉碎、雾化,与烟气充 分混合。喷枪采用专门设计的拆装机构,可以在运行 中方便地拆、装、检修和更换。 2.4.4 旋风分离器
每一台吸收反应塔配置两台旋风分离器。旋风分 离器为直立圆形容器,底部为圆锥形,入口段贴有可 更换耐磨衬里,顶部为放射状出口。气体从切向进入, 旋风离心力作用下将烟气中的固体颗粒分离。 2.4.5 物料循环给料机
脱硫灰(副产品)包括:布袋除尘产生的灰、脱硫 塔下部落灰以及回料机的溢灰等三部分。脱硫副产品
来源于进入脱硫系统的烟气带入的飞灰、未反应的脱 硫剂以及随脱硫剂带入的杂质。 2.3 工艺流程
烧结烟气脱硫工艺流程简图如图 1。
反应器 生石灰 水
旋风分离器
浆液罐 水 压缩空气
烟气
喷嘴
除尘器
引风机 烟囱
再循环
GSCA 脱硫反应塔内的平均气速为传统的喷雾干 燥法反应塔的 5~10 倍,固粒处于流化状态。同时靠旋 风分离器及特有的回料机实现固粒再循环,使塔内气 流的固粒浓度提高数十倍至百倍,因而反应塔内的传 热、传质和化学反应强度大大提高。 (1) 反应塔内蒸发冷却充分
脱硫剂浆液雾化后在上行烟气中被加热、蒸发、 干燥,同时降低了烟气的温度,有助于酸性气体的吸 收。在文氏管的强紊流作用下,浆液滴与固粒碰撞,使 得颗粒表面形成薄液膜,这一过程又促进了快速蒸 发。比传统的喷雾干燥吸收法的滞留时间(8~12 s)缩 短 6 s,确保副产品含水量小于 1%,为实现干燥排放 创造了条件。 (2) 反应条件好,吸收剂利用率高
2009 年第 6 期
132 m2 烧结机烟气脱硫改造
孙锡荣 (天津天铁冶金集团有限公司烧结厂 ,河北省涉县 056404)
[ 摘要] 针对烧结过程中产生大量粉尘和 SO2 等有害物质,对环境造成严重污染的现状,进行了烧结机烟气脱硫技术改 造。结合 132 m2 烧结机烟气脱硫工程,分析了烧结机机头烟气的特性,采用了气固悬浮吸收半干法脱硫工艺进行烟气脱硫,使 改造后烟气中硫含量从 1200~1400mg/Nm3 已经降到 200mg/Nm3 以下,减少了污染,效果良好。