套筒加工工艺规程设计
车床尾座套筒的材料与加工工艺设计
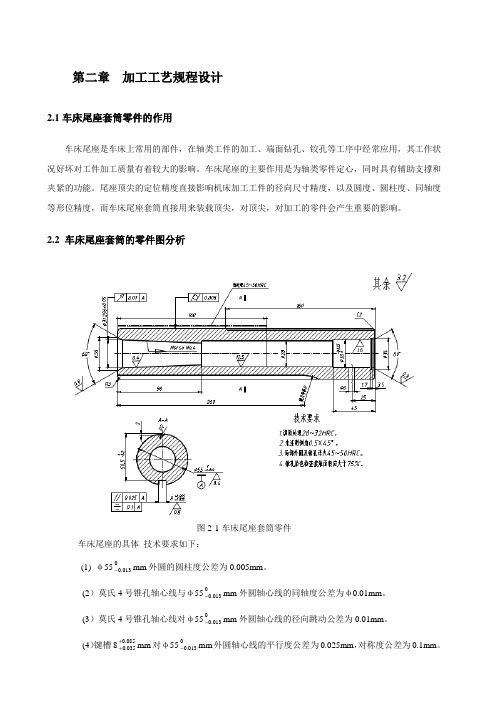
第二章 加工工艺规程设计2.1车床尾座套筒零件的作用车床尾座是车床上常用的部件,在轴类工件的加工、端面钻孔、铰孔等工序中经常应用,其工作状况好坏对工件加工质量有着较大的影响。
车床尾座的主要作用是为轴类零件定心,同时具有辅助支撑和夹紧的功能。
尾座顶尖的定位精度直接影响机床加工工件的径向尺寸精度,以及圆度、圆柱度、同轴度等形位精度,而车床尾座套筒直接用来装载顶尖,对顶尖,对加工的零件会产生重要的影响。
2.2 车床尾座套筒的零件图分析图2-1车床尾座套筒零件车床尾座的具体 技术要求如下:(1) φ550013.0-mm 外圆的圆柱度公差为0.005mm 。
(2)莫氏4号锥孔轴心线与φ550013.0-mm 外圆轴心线的同轴度公差为φ0.01mm 。
(3)莫氏4号锥孔轴心线对φ550013.0-mm 外圆轴心线的径向跳动公差为0.01mm 。
(4)键槽8085.0035.0++mm 对φ550013.0-mm 外圆轴心线的平行度公差为0.025mm ,对称度公差为0.1mm 。
(5)锥孔涂色检查其接触面积应大于75%。
(6)调质处理28~32HRC。
(7)局部外圆及锥孔淬火45~50HRC。
2.3 车床尾座套筒的毛坯设计2.3.1毛坯材料的选择在制订机械加工工艺规程时,正确选择合适的毛坯,对零件的加工质量、材料消耗和加工时都有很大的影响。
显然毛坯的尺寸和形状越接近成品零件,机械加工的劳动量就越少,但是毛坯的制造成本就越高,所以应根据生产纲领,综合考虑毛坯制造和机械加工的费用来确定毛坯,以求得最好的经济效益。
机械加工中常用的毛坯有铸件、锻件、冲压件和型材等,选用时主要考虑一下因素。
(1)零件的材料与力学性能;(2)零件的结构形状与外形尺寸;(3)生产类型;(4)毛坯车间的生产条件;(5)利用新工艺、新技术、新材料的可能性。
本设计根据零件图的技术要求采用45钢作为毛坯材料。
2.3.2毛坯的成型方式、尺寸套筒类零件的毛坯制造形式主要有铸造与锻造(压)等方法。
套筒工艺规程编制

套筒零件工艺规程的编制姓名学号班级完成时间一 分析零件图用A4纸单独画出零件图1零件的结构形状 作用 由减速器结构可知,低速轴是减速器的运动输出机构,起支承齿轮、传递扭矩的作用。
两Ф35±0.008外圆轴颈用于安装轴承, Ф42+0.018 +0.002外圆及轴肩用于安装齿轮及齿轮轴向定位,采用普通平键周向固定。
外圆Ф28+0.015 +0.002及螺纹M24×1.5-6g 为完成减速器运动的输出与其它构件相联。
Ф33 0 -0.039用于穿过轴承端盖,并安装V 型密封圈。
2.分析零件的技术要求⑴减速器低速轴各轴段的加工精度如表1.18所示。
表1.18 减速器低速轴各轴段的加工精度为3.2μm ;键槽深度尺寸精度相当于IT12,要求较低。
⑶螺纹M24×1.5-6g 为中等精度细牙普通螺纹,中径和顶径公差带均为6g 。
⑷两端中心孔均为B 型中心孔,其中D =3.15mm ,D 2=10mm 。
⑸退刀槽、砂轮越程槽、左右端面、轴环、倒角及过渡圆角等加工表面,尺寸及表面精度要求都比较低。
3.明确零件的热处理方式零件图上的热处理方式T235是指材料调质后的硬度范围220~250HBC 。
4.零件结构工艺性分析通过对减速器低速轴的结构、尺寸标注逐一分析,认为该零件的结构工艺性可行。
二确定生产类型1.计算零件的生产纲领由减速器低速轴零件图可知:零件的生产纲领为200件/年,考虑备品率(取a =5%)和废品率(取b =1%),则减速器低速轴的生产纲领计算如下: N =Qn(1+a )(1+b )=200×1(1+5%)(1+1%)=212 件/年2.确定零件的生产类型及工艺特征 减速器低速轴属于轻型机械类零件。
根据生产纲领(212件/年)及零件类型(轻型机械),由表1.8可查出,减速器低速轴的生产类型为小批生产,由此得出应具有如下工艺特征,见表1.19。
(可不用列表,文字说明即可)表1.19 减速器低速轴的生产纲领和生产类型三 确定毛坯制造形式1.确定毛坯制造形式根据减速器低速轴的制造材料45钢及零件的生产类型,毛坯类型可采用型材或锻件。
车床尾座套筒加工工艺规程及夹具设计说明书
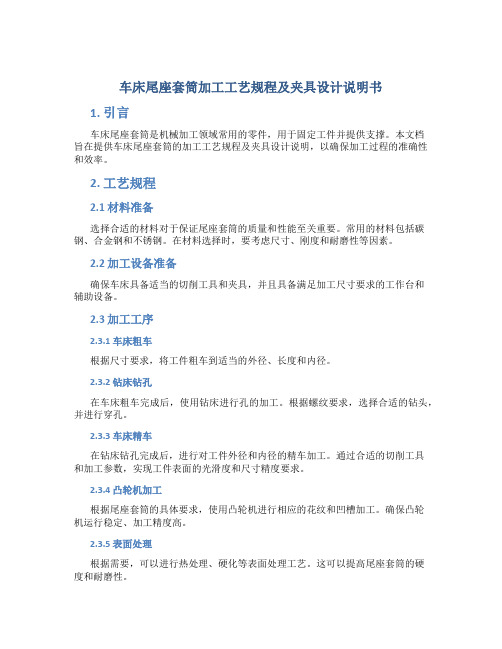
车床尾座套筒加工工艺规程及夹具设计说明书1. 引言车床尾座套筒是机械加工领域常用的零件,用于固定工件并提供支撑。
本文档旨在提供车床尾座套筒的加工工艺规程及夹具设计说明,以确保加工过程的准确性和效率。
2. 工艺规程2.1 材料准备选择合适的材料对于保证尾座套筒的质量和性能至关重要。
常用的材料包括碳钢、合金钢和不锈钢。
在材料选择时,要考虑尺寸、刚度和耐磨性等因素。
2.2 加工设备准备确保车床具备适当的切削工具和夹具,并且具备满足加工尺寸要求的工作台和辅助设备。
2.3 加工工序2.3.1 车床粗车根据尺寸要求,将工件粗车到适当的外径、长度和内径。
2.3.2 钻床钻孔在车床粗车完成后,使用钻床进行孔的加工。
根据螺纹要求,选择合适的钻头,并进行穿孔。
2.3.3 车床精车在钻床钻孔完成后,进行对工件外径和内径的精车加工。
通过合适的切削工具和加工参数,实现工件表面的光滑度和尺寸精度要求。
2.3.4 凸轮机加工根据尾座套筒的具体要求,使用凸轮机进行相应的花纹和凹槽加工。
确保凸轮机运行稳定、加工精度高。
2.3.5 表面处理根据需要,可以进行热处理、硬化等表面处理工艺。
这可以提高尾座套筒的硬度和耐磨性。
2.4 检测与质量控制每个加工工序完成后,都需要进行相应的检测和质量控制。
通过合适的检测工具和设备,确保尾座套筒的尺寸和质量符合要求。
2.5 产品包装和出厂完成所有加工工序后,按照客户要求进行产品包装,并妥善安排出厂。
3. 夹具设计说明书3.1 夹具种类根据尾座套筒的加工特点和要求,设计合适的夹具以确保加工过程的稳定性和准确性。
常见的夹具种类包括三爪自动夹具、四爪自动夹具和专用夹具。
3.2 夹具结构设计在夹具结构设计中,要考虑到以下因素:•要保证夹具刚度,以确保工件在切削力作用下不发生变形。
•要有足够的可调节性,以适应不同规格和尺寸的尾座套筒。
•要有足够的稳定性,避免在工件加工过程中出现震动和位移。
•要设计合适的夹紧力,以确保工件与夹具之间的牢固连接。
车床尾座套筒加工工艺规程设计

四、机械加工工艺过程
4. 3 热处理
调质28~32HRC 一般习惯将淬火加高温回火相结合的热处理称为调质处理。 作用:调质处理后得到回火索氏体组织,它的机械性能均 比相同硬度的正火索氏体组织为优,为后续加工作准备。
车床尾座套筒加工工艺规程设计
四、机械加工工艺过程
4. 4 .1 半精车
车床尾座套筒加工工艺规程设计
三、分析零件图
3.3 其他结构
Ф6的孔是排气 孔,位置精度和尺 寸精度要求精度不 高。
Ф30的内孔是用 来安装手轮丝杆的, 因此有配合精度要 求。
车床尾座套筒加工工艺规程设计
四、机械加工工艺过程
4.1制造毛坯
下料: 棒料Ф80mm×165mm 锻造: 锻造尺寸Ф60mm×285mm 热处理:正火
车床尾座套筒加工工艺规程设计
四、机械加工工艺过程
4.5 精车
夹左端外圆, 中心架托右端外圆, 找正外圆,车mm孔 至mm,深44.5mm, 车Ф34mm×1.7mm槽, 保证3.5mm和1.7mm
车床尾座套筒加工工艺规程设计
四、机械加工工艺过程
4.5 精车
倒头,夹右端外圆中心架左端外圆,找正外圆,车莫 氏4号内锥孔,至大端尺寸为mm,车左端头Ф36mm×60°
四、机械加工工艺过程
4.8 钻孔、修毛刺
钻Ф6mm孔, 其中心距右端面为 25mm
钳工:修毛刺
车床尾座套筒加工工艺规程设计
四、机械加工工艺过程
4.9 热处理
左端莫氏4号锥孔及160mm长的外圆部分,高频感 应加热淬火45~50HRC
车床尾座套筒加工工艺规程设计
四、机械加工工艺过程
4.10 研磨
套筒座工艺规程及夹具课程设计

目录一、设计任务 (3)二、生产纲领、确定生产类型 (4)三、零件的分析 (5)3.1、零件的作用 (5)3.2、零件的工艺分析 (5)四、确定毛坯的制造方法、初步确定毛坯形状 (6)五、工艺规程设计 (7)5.1、定位基准的选择 (7)5.2、工件表面加工方法的选择 (8)5.3、制定工艺路线 (9)5.4、确定加工余量、工序尺寸及公差 (11)5.5、确定切削用量、基本工时(机动时间) (15)六、夹具设计 (31)6.1、设计要求 (31)6.2、夹具设计的有关计算 (32)6.3、夹具结构设计及操作简要说明 (33)七、设计小结 (34)八、参考文献 (34)3 零件的分析3.1 分析零件的作用及技术要求套筒座顾名思义就是支承套筒的作用,起定位、夹紧套筒的作用。
技术要求有套筒座的圆角为R3-R5,倒角1.5︒⨯45,套筒支承孔是重要表面,所以其精度要求很高。
而加工套筒支承孔需要底面作精基准,所以底面的粗糙度也有很高的要求。
底面的6个螺栓孔上表面也有表面粗糙度的要求,还有套筒支承孔自身有个圆柱度要求。
具体的要求是:套筒支承孔对底面的平行度为0.01;套筒支承孔的圆柱度是0.01;支承孔中心到底面尺寸为80±0.02,支承孔尺寸要求为Φ50H7套筒支承孔内表面粗糙度Ra值为1.6;底面的表面粗糙度要求是Ra值为1.6;底面6个螺栓孔上表面粗糙度要求是Ra值为12.5;还有套筒支承孔两断面表面粗糙度是Ra 值为6.3;顶面螺纹孔上表面粗糙度要求是Ra值为12.5。
3.2 零件的工艺分析套筒座的主要加工表面是套筒支承孔和底面、支承孔两端面。
因为这是与其他零件直接接触的表面,对加工及加工精度有很大的影响。
套筒支承孔的内表面必须要有足够的粗糙度才能保证零件的加工要求同时必须相对于底面又要有很高的平行度,因为支承孔的轴线与底面的定位有很大的关系。
同时底面要有足够的粗糙度才能保证与支承孔轴线的平行度。
C620车床尾架套筒的工艺规程设计和铣8mm槽的夹具设计
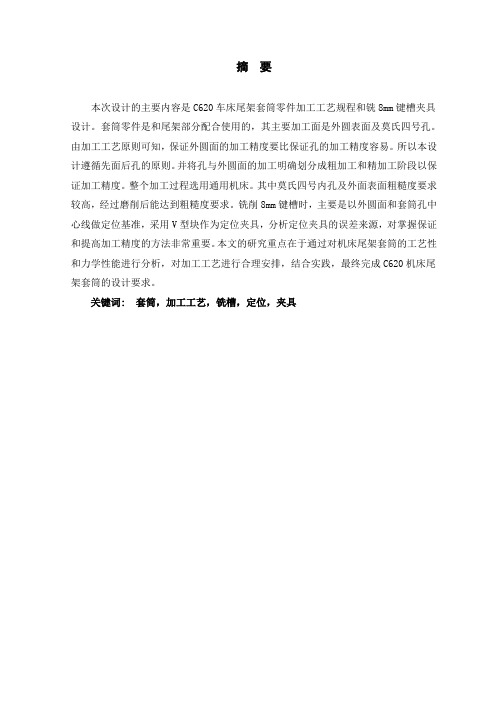
本次设计的主要内容是C620车床尾架套筒零件加工工艺规程和铣8mm键槽夹具设计。
套筒零件是和尾架部分配合使用的,其主要加工面是外圆表面及莫氏四号孔。
由加工工艺原则可知,保证外圆面的加工精度要比保证孔的加工精度容易。
所以本设计遵循先面后孔的原则。
并将孔与外圆面的加工明确划分成粗加工和精加工阶段以保证加工精度。
整个加工过程选用通用机床。
其中莫氏四号内孔及外面表面粗糙度要求较高,经过磨削后能达到粗糙度要求。
铣削8mm键槽时,主要是以外圆面和套筒孔中心线做定位基准,采用V型块作为定位夹具,分析定位夹具的误差来源,对掌握保证和提高加工精度的方法非常重要。
本文的研究重点在于通过对机床尾架套筒的工艺性和力学性能进行分析,对加工工艺进行合理安排,结合实践,最终完成C620机床尾架套筒的设计要求。
关键词: 套筒,加工工艺,铣槽,定位,夹具The main content of this design is to design the tailstock sleeve parts processing procedures and milling 8mm keyway fixture C620 lathe. Sleeve parts and the tailstock part matched, the main processing surface is a cylindrical surface and Morse No. four holes. By the principle known processing, ensure the machining accuracy of cylindrical holes than guarantee the machining precision easy. So the design follows the principle of the surface after the first hole. And the processing hole and excircle surface clearly divided into roughing and finishing stages of processing to ensure accuracy. The entire process used universal machine tool. The Morse No. four bore and outside surface roughness higher, after grinding can reach roughness requirements. Keyway milling 8mm, mainly outside circular surface and the sleeve hole center line to do the locating datum, using V block as a positioning clamp, error source analysis positioning fixture, to guarantee and improve the machining precision of the method is very important. The focus of this paper is that through the analysis process and the mechanical properties of the tailstock sleeve, the processing technology for reasonable arrangement, combined with the practice, finally completed the design requirement of the C620 machine tool tailstock sleeve.Keywords: sleeve, machining, milling, positioning, clamping目录摘要 (2)引言 (4)1套筒加工工艺规程设计 (5)1.1生产纲领及生产类型的确定 (6)1.2 零件的分析 (6)1.3 选择毛坯 (6)1.4 工艺规程计 (6)1.4.1定位基准的选择 (6)1.4.2零件表面加工工方法的选择 (6)1.4.3制定工艺路线 (7)1.4.4确定机械加工余量及毛坯尺寸,设计毛坯——零件综合图 (8)1.4.5工序设计 (9)1.4.6.确定切削用量及基本时间(机动时间).......................... (13)2夹具设计 (21)2.1夹具的结构方案 (21)2.1.1确定夹具的类型 (21)2.1.2确定套筒的定位方案 (22)2.1.3确定套筒的夹紧形式 (22)2.1.4确定刀具的导向方式或对刀装置 (22)2.1.5确定其它机械,如分度、装卸用的辅助装置等 (23)2.1.6夹具体的结构类型的设计 (23)2.1.7夹具总图设计 (23)2.2夹具精度的校核 (23)2.2.1绘制夹具零件图样 (25)总结 (26)参考文献 (26)附录 (27)致谢 (28)1.引言制造业是向国民经济各部门提供装备的部门,是现代经济的支柱产业;装备制造业的发达程度,是衡量一个国家工业化阶段的重要标准。
套筒类零件加工工艺规程
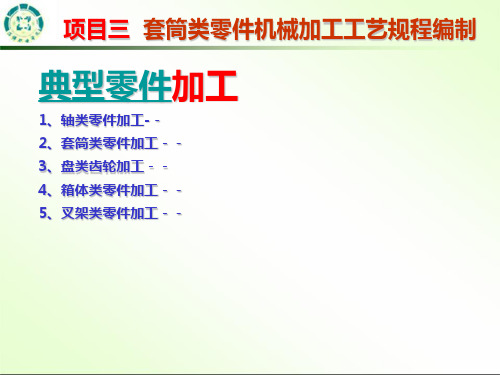
分类
项目三 套筒类零件机械加工工艺规程编制
图6-1 各类套筒零件 a )、 b )滑动轴承 c )钻套 d ) 轴承衬套 e )气缸套 f )液压缸
项目三 套筒类零件机械加工工艺规程编制
套筒类零件 套筒类零件的结构
套筒类零件在机械中应用十分广泛。 其加工表面主要有端面、外圆表面、内圆(孔)表面。 端面和外圆加工,通常在车床上进行。 套筒类零件的内孔,作为支承或导向的主要表面,其加 工方法根据使用的刀具不同,通常采用车孔、钻孔(包 括扩孔、锪孔)、铰孔、镗孔、拉孔、磨孔以及各种孔 的光整加工和特种加工等。
复习: 机床夹具设计基础 1、机床夹具设计基础
夹具的组成:
机床夹具
定位装置
夹紧装置
其他装置 或元件
夹具体
Text
项目三
套筒类零件机械加工工艺规程编制
钻床夹具设计特点
1)钻床夹具的主要类型
◆在钻床上进行孔的钻、扩、铰、 锪、攻螺纹等加工所用的夹具称 为钻床夹具,也称钻模。
项目三
套筒类零件机械加工工艺规程编制
项目三 套筒类零件机械加工工艺规程编制 相关知识:
一、车孔 2.车孔的关键技术是解决内孔车刀的刚性和排屑问题。 1)尽量增加刀杆的截面积,使内孔车刀的刀尖位于刀杆的中心 线上。 2)刀杆的伸出长度尽可能缩短,使刀杆伸出长度略大于孔深即 可。 3)为了使内孔车刀的后面既不和工件孔面发生干涉和摩擦,也 不使内孔车刀的后角磨得过大时削弱刀尖强度,内孔车刀的后 面一般磨成两个后角的形式。 4)为了使已加工表面不致于被切屑划伤,通孔的内孔车刀最好 磨成正刃倾角,切屑流向待加工表面(前排屑)。不通孔的内 孔车刀当然无法从前端排屑,只能从后端排屑,所以刃倾角一 般取-2°~0°。
套筒零件的机械加工工艺规程及夹具设计(含全套CAD图纸)

算; 4)、夹具总装图绘制。
9、刀具、量具没计。(绘制刀具量具工作图)
10、某工序数控编程程序设计。
四、上交资料(除资料 2 使用标准 A3 手写外,其余电子文稿指导教师审核后,打印上交)
1、零件机械加工工艺规程制订设计说明书一份;(按统一格式撰写)
2、工艺文件一套(含工艺过程卡片、每一道工序的工序卡片,工序附图);
第五章 第 30、35、65、70 号工序数控编程设计说明书 ........................... 23 1.数控加工工艺性分析.................................................... 23
2.走刀路线的确定........................................................ 23 3.刀具及切削用量确定.................................................... 23 4.编程原点的确定及数值计算.............................................. 24 5.程序编写及说明........................................................ 25 第六章 毕业设计体会........................................................ 29 第七章 参考资料............................................................ 30 致 谢....................................................................... 31
(整理)套筒加工工艺规程
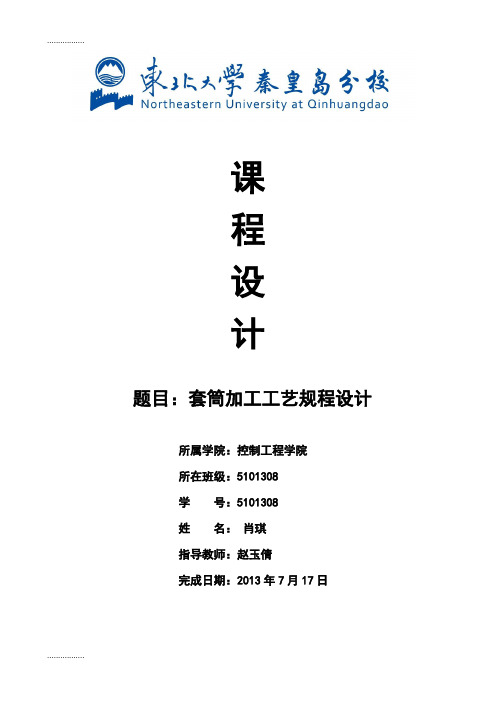
课程设计题目:套筒加工工艺规程设计所属学院:控制工程学院所在班级:5101308学号:5101308姓名:肖琪指导教师:赵玉倩完成日期:2013年7月17日目录课程设计要求 (3)一、零件分析 (4)二、产品类型确定 (4)三、确定毛坯 (4)四、确定各加工表面的加工、定位及方案加紧 (6)五、安排工艺过程 (8)六、工序设计 (9)(一)绘制工序图,选择机床、工艺装备 (9)(二)确定工序尺寸 (10)(三)切削用量的制定 (13)七、课程设计总结 (16)套筒零件机械加工工艺过程卡 (17)套筒零件机械加工工序卡(一) (18)套筒零件机械加工工序卡(二) (19)附录 (20)设计题目:套筒的机械加工工艺规程设计设计参数:下图示为套筒,材料45#钢,是某产品上的一个零件。
该产品年生产4000台,产品零件备品率4%,机加工废品率1%。
编制其机械加工规程。
设计任务:1)被加工零件的零件图和三维仿真图;2)零件毛坯二维图;3)机械加工工艺过程卡片和机械加工工序卡片;4)编写课程设计说明书。
一、零件分析该零件结构简单明了,结构工艺性好,无不方便加工之处。
φ60外圆、3×1凹槽尺寸精度均为11级,φ20+00.033孔、φ25+00.033孔、φ40-00.039外圆尺寸精度均为准公差8级,表面粗糙度要求最高是Ra≤1.6um,未标注形位公差,无热处理要求,是一个加工要求中等的零件。
但是轴向尺寸20-00.2和65-00.2不便直接测量,如何保证其精度是该零件加工和检测的一个重点。
二、确定生产类型1、生产纲领:根据以知数据可求得该零件的年生产纲领。
N=Qm(1+a%+b%)=4000×1×(1+4%+1%)=4200(件/年)2、生产类型的划分:查表1-1可得确定该零件生产类型为中批生产类型。
表1-1机械加工零件生产类型划分三、确定毛坯根据该零件的材料、生产类型、结构形状、尺寸大小、技术要求等的因其选用棒料。
钢筋套筒的工艺流程
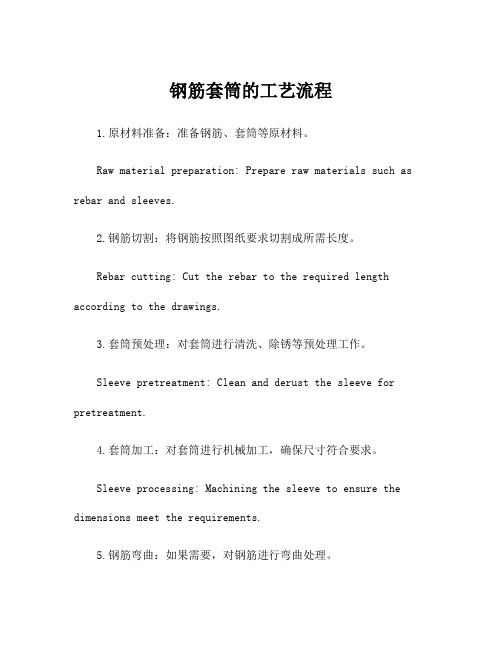
钢筋套筒的工艺流程1.原材料准备:准备钢筋、套筒等原材料。
Raw material preparation: Prepare raw materials such as rebar and sleeves.2.钢筋切割:将钢筋按照图纸要求切割成所需长度。
Rebar cutting: Cut the rebar to the required length according to the drawings.3.套筒预处理:对套筒进行清洗、除锈等预处理工作。
Sleeve pretreatment: Clean and derust the sleeve for pretreatment.4.套筒加工:对套筒进行机械加工,确保尺寸符合要求。
Sleeve processing: Machining the sleeve to ensure the dimensions meet the requirements.5.钢筋弯曲:如果需要,对钢筋进行弯曲处理。
Rebar bending: If necessary, bend the rebar as required.6.焊接:将钢筋固定在套筒上,进行焊接。
Welding: Fix the rebar to the sleeve and proceed with welding.7.电镀:对焊接后的产品进行电镀处理,提高表面光洁度和耐腐蚀性。
Electroplating: Electroplate the welded products to improve surface finish and corrosion resistance.8.质量检验:对加工完成的钢筋套筒进行质量检验。
Quality inspection: Perform quality inspection on the processed rebar sleeves.9.包装:对合格的产品进行包装,准备发货。
直螺纹套筒规范

直螺纹套筒规范 The manuscript was revised on the evening of 2021规范一、施工准备1、材料准备:钢筋应具有出厂合格证和力学性能,所有检验结果,均应符合现行规范的规定和设计要求。
连接套筒应有出厂合格证,一般为或优质炭素结构钢,其抗拉承载力标准值应大于、等于被连接钢筋的受拉承载力标准值的倍,套筒长为钢筋直径的二倍,套筒应有保护盖,保护盖上应注明套筒的规格。
套筒在运输、储存过程中,要防止锈蚀和沾污,套筒的尺寸偏差及精度要求见表1。
表1:套筒尺寸偏差及精度要求套筒直径D 外径允许偏差长度允许偏差≤50±±6H/GB197-81>50 ±±6H/GB197-81套筒出场质量检验要求见表2表2:套筒出厂质量检验要求序号检验项目量具名称检验要求1 外观质量目测表面应无裂纹和影响接头质量的其它缺陷2 外型尺寸或专用量规长度及外径应满足图纸要求3 螺纹尺寸通端螺纹赛规能顺利连接套筒并达到旋合长度止端螺纹赛规?赛规允许从套筒两端部分旋合,旋入量不应超过3P常用连接套筒有四种形式,分别是标准型套筒、正反丝扣型套筒、变径型套筒、可调型套筒。
标准型套筒主要用于相同直径可转动钢筋的连接;正反丝扣型套筒用于两端钢筋不能转动但至少有一根钢筋可以轴向移动的,如拐铁钢筋的施工;变径型套筒用于不同直径钢筋的连接;可调型套筒用于两端不能转动的钢筋连接,也可用于拐铁处钢筋连接。
当两端钢筋轴向位置不能移动时,只能使用此种拉头形式,如在两个预制大型连接施工中的钢筋对接。
技术准备:在进行时,应综合考虑以下几个问题:1)滚压直螺纹接头的厚度应满足现行国家标准《》中受力钢筋保护层最小厚度的要求,且不得小于15nmm。
2)受力钢筋滚压直螺纹接头位置应相互错开。
在任一接头中心至长度为钢筋直径的35倍的区段内,有接头的受力钢筋截面面积占钢筋总截面面积的百分率,应符合下列规定:a、受拉区的受力钢筋接头百分率不宜超过50%,b、接头宜避开有要求的框架的梁端和柱端的;当无法避开时,接头的百分率不应超过50%。
典型套筒类零件加工工艺分析
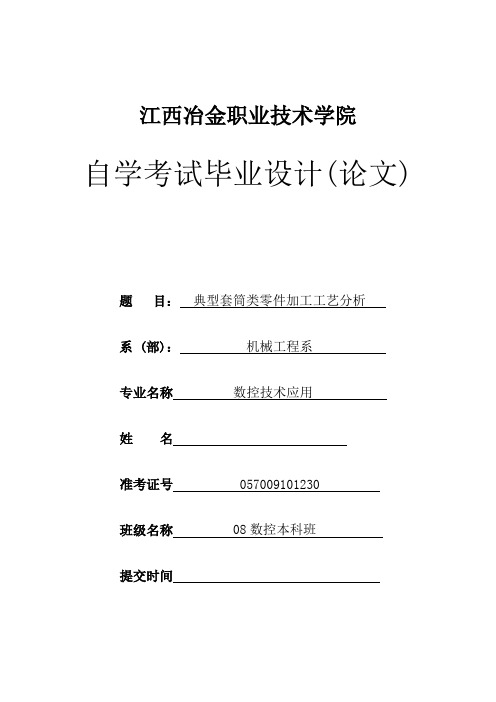
江西冶金职业技术学院自学考试毕业设计(论文)题目:典型套筒类零件加工工艺分析系 (部):机械工程系专业名称数控技术应用姓名准考证号 0570********班级名称 08数控本科班提交时间摘要高效率、高精度加工是套筒类最主要特点之一。
利用套筒零件加工,其产品加工的质量一致性好,尤其在轮廓不规则、复杂的曲线或曲面、多工艺复合化加工和高精度要求的产品加工时,其优点是传统数控零件加工所无法比拟的。
随着科学技术飞速发展和经济竞争的日趋激烈,机械产品的更新速度越来越快,数控加工技术作为先进生产力的代表,在机械及相关行业领域发挥着重要的作用,机械制造的竞争,其实质是数控技术的竞争。
本次设计就是进行套类零件的数控加工工艺,对套类零件的加工工艺分析,并绘制零件图。
其中零件工艺规程的分析是此次论文的重点和难点。
关键字:套筒类零件;液压缸;工艺分析目录引言 (1)一、套筒类零件的结构特点及工艺分析 (1)1.1轴承套加工工艺分析加工 (1)1.2液压缸加工工艺分析 (2)二、套筒类零件加工中的主要工艺问题 (4)2.1 保证相互位置精度 (4)2.2 防止变形的方法 (6)三、套筒类零件的程序编程 (8)四、套筒类零件加工中的主要工艺问题 (11)4.1 保证相互位置精度 (11)五、套简类零件的功用及结构特点 (11)5. 1 套筒类零件技术要求 (12)5.2 套筒类零件的材料、毛坯及热处理 (13)结束语 (14)致谢 (15)参考文献 (16)典型套筒类零件加工工艺分析引言理想的加工程序不仅应保证加工出符合图样的合格工件,同时应能使数控机床的功能得到合理的应用和充分的发挥。
数控机床是一种高效率的自动化设备,它的效率高于普通机床的2~3倍,要充分发挥数控机床的这一特点,必须在编程之前对工件进行工艺分析,根据具体条件,选择经济、合理的工艺方案。
数控加工工艺考虑不周是影响数控机床加工质量、生产效率及加工成本的重要因素。
套筒加工工艺规程设计
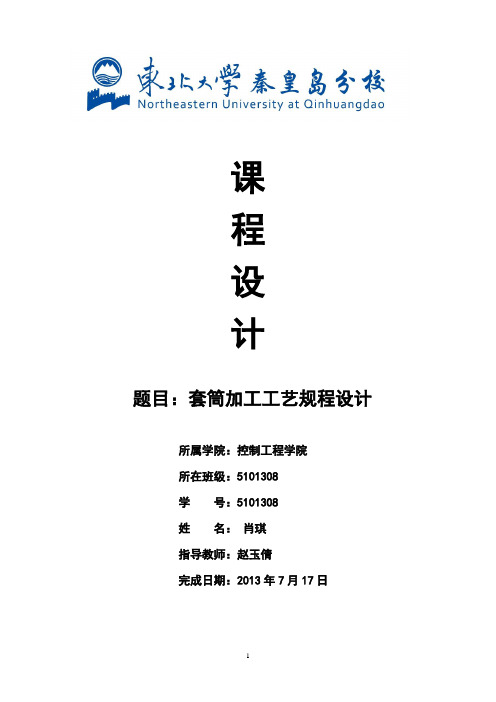
课程设计题目:套筒加工工艺规程设计所属学院:控制工程学院所在班级:5101308学号:*******姓名:肖琪指导教师:***完成日期:2013年7月17日目录课程设计要求 (3)一、零件分析 (4)二、产品类型确定 (4)三、确定毛坯 (4)四、确定各加工表面的加工、定位及方案加紧 (6)五、安排工艺过程 (8)六、工序设计 (9)(一)绘制工序图,选择机床、工艺装备 (9)(二)确定工序尺寸 (10)(三)切削用量的制定 (13)七、课程设计总结 (16)套筒零件机械加工工艺过程卡 (17)套筒零件机械加工工序卡(一) (18)套筒零件机械加工工序卡(二) (19)附录 (20)设计题目:套筒的机械加工工艺规程设计设计参数:下图示为套筒,材料45#钢,是某产品上的一个零件。
该产品年生产4000台,产品零件备品率4%,机加工废品率1%。
编制其机械加工规程。
设计任务:1)被加工零件的零件图和三维仿真图;2)零件毛坯二维图;3)机械加工工艺过程卡片和机械加工工序卡片;4)编写课程设计说明书。
一、零件分析该零件结构简单明了,结构工艺性好,无不方便加工之处。
φ60外圆、3×1凹槽尺寸精度均为11级,φ20+00.033孔、φ25+00.033孔、φ40-00.039外圆尺寸精度均为准公差8级,表面粗糙度要求最高是Ra≤1.6um,未标注形位公差,无热处理要求,是一个加工要求中等的零件。
但是轴向尺寸20-00.2和65-00.2不便直接测量,如何保证其精度是该零件加工和检测的一个重点。
二、确定生产类型1、生产纲领:根据以知数据可求得该零件的年生产纲领。
N=Qm(1+a%+b%)=4000×1×(1+4%+1%)=4200(件/年)2、生产类型的划分:查表1-1可得确定该零件生产类型为中批生产类型。
表1-1机械加工零件生产类型划分三、确定毛坯根据该零件的材料、生产类型、结构形状、尺寸大小、技术要求等的因其选用棒料。
套筒机械加工工艺规程制订

目录一. 对零件进行工艺分析 (1)二. 确定毛坯 (1)三. 制定零件的机械加工工艺路线 (1)四. 工序尺寸计算及公差 (2)五. 选择机床及工、夹、量、刀具 (3)六. 检测方法 (5)七. 确定各工序的切削用量和时间定额 (5)八. 参考书目 (7)九. 机械加工工序卡 (8)十. 附图………………………………………………………………17一 . 对零件进行工艺分析1.分析零件的主要作用及零件图上的技术要求;零件是水平转盘的定心套筒。
外圆φ40m6 与该转盘的盘面内孔采用过渡配合,并加平键连接避免转动;外圆φ35g6与基准件内孔采用间隙配合,以保证转盘绕基准件的轴向连接;孔φ22H7用来安装校正心轴。
故此零件的主要技术要求是孔和两段外圆的尺寸精度;两段外圆对内孔的同轴度;台阶端面对内孔圆跳动。
2.分析零件主要加工表面的尺寸、形状及位置精度、表面粗糙度以及设计基准等;零件的加工表面要求较高的是:键槽轴段外圆表面φ0.0250.00940++, 中间轴段外圆表面0.0090.02535φ--,小孔直径0.021022φ+ , 螺纹外径33 1.56M g ⨯-。
3.分析零件的材质、热处理及机械加工的工艺性。
材料40Cr ,高频淬火45—50HRC 。
二 . 确定毛坯1.毛坯种类选择此零件在力学性能上没有更高的要求,孔径也小,故毛坯选用热轧圆钢。
2.确定毛坯的形状和尺寸选择毛坯的形状和尺寸:热轨圆钢φ55⨯86三 . 制定零件的机械加工工艺路线1.确定加工工艺路线下料——铣端面——粗车、半精车各段外圆——车螺纹,切退刀槽,倒角——钻孔、镗孔——钳工画线——铣键槽——钳工去毛刺——高频淬火——磨内孔——粗、半精磨外圆并靠磨端面——检验 2.选择定位基准,进行工艺尺寸计算对零件图纸进行简单分析选孔为统一的精基准终加工各段外圆和台阶端面,能保证各主要表面有较高的相互位置精度。
工件不长,选外圆为粗基准比较方便。
- 1、下载文档前请自行甄别文档内容的完整性,平台不提供额外的编辑、内容补充、找答案等附加服务。
- 2、"仅部分预览"的文档,不可在线预览部分如存在完整性等问题,可反馈申请退款(可完整预览的文档不适用该条件!)。
- 3、如文档侵犯您的权益,请联系客服反馈,我们会尽快为您处理(人工客服工作时间:9:00-18:30)。
课程设计题目:套筒加工工艺规程设计所属学院:控制工程学院所在班级:5101308学号:*******姓名:肖琪指导教师:***完成日期:2013年7月17日目录课程设计要求 (3)一、零件分析 (4)二、产品类型确定 (4)三、确定毛坯 (4)四、确定各加工表面的加工、定位及方案加紧 (6)五、安排工艺过程 (8)六、工序设计 (9)(一)绘制工序图,选择机床、工艺装备 (9)(二)确定工序尺寸 (10)(三)切削用量的制定 (13)七、课程设计总结 (16)套筒零件机械加工工艺过程卡 (17)套筒零件机械加工工序卡(一) (18)套筒零件机械加工工序卡(二) (19)附录 (20)设计题目:套筒的机械加工工艺规程设计设计参数:下图示为套筒,材料45#钢,是某产品上的一个零件。
该产品年生产4000台,产品零件备品率4%,机加工废品率1%。
编制其机械加工规程。
设计任务:1)被加工零件的零件图和三维仿真图;2)零件毛坯二维图;3)机械加工工艺过程卡片和机械加工工序卡片;4)编写课程设计说明书。
一、零件分析该零件结构简单明了,结构工艺性好,无不方便加工之处。
φ60外圆、3×1凹槽尺寸精度均为11级,φ20+00.033孔、φ25+00.033孔、φ40-00.039外圆尺寸精度均为准公差8级,表面粗糙度要求最高是Ra≤1.6um,未标注形位公差,无热处理要求,是一个加工要求中等的零件。
但是轴向尺寸20-00.2和65-00.2不便直接测量,如何保证其精度是该零件加工和检测的一个重点。
二、确定生产类型1、生产纲领:根据以知数据可求得该零件的年生产纲领。
N=Qm(1+a%+b%)=4000×1×(1+4%+1%)=4200(件/年)2、生产类型的划分:查表1-1可得确定该零件生产类型为中批生产类型。
表1-1机械加工零件生产类型划分三、确定毛坯根据该零件的材料、生产类型、结构形状、尺寸大小、技术要求等的因其选用棒料。
经查表1-2取棒料直径为φ67 x 106 mm.表1-2常用毛坯制造方法及其工艺特点四、确定各加工表面的加工、定位及方案加紧1、加工方案:φ40-00.039外圆和尺寸精度(IT8)及表面质量要求(Ra≤3.2),查表1-3,φ40-00.039外圆加工方更方便,取粗车-半精车(精车)。
3×1凹槽和φ60外圆尺寸精度(IT11)及表面质量要求(Ra≤12.5),查表1-3,取粗车。
φ25+00.033孔尺寸精度(IT8)及表面质量要求(Ra≤3.2),由于φ25+00.033孔是平底孔,不便用扩孔钻扩孔和用绞刀绞孔,也无需要镗床镗孔(因为该零件是小型回转体),在车床上车孔。
φ20+00.033孔的表面粗糙度较细(Ra≤1.6),结合其尺寸精度(IT8)和毛坯查表1-4取其加工方案为钻-扩-绞。
大端面上的通槽要求低,一次铣削即可。
2、定位方案:为使得个表面之间有较好的相互位置精度和较好的加工连续性,尽量在一次装夹下完成多个表面的加工。
以此,首先以毛坯外圆定位加工好小端面、φ40-00.039外圆、φ25+00.033孔,再以φ40-00.039外圆定位加工大端面、φ60外圆、3×1凹槽、φ20+00.033孔。
对于宽5的通槽,定位时需限制工件4个自由度(两个移动自由度和两个转动自由度)。
按基准重合定位原则,可考虑用φ25+00.033孔或φ40-00.039外圆定位以满足槽的对中性要求,用φ25+00.033孔的底面定位满足槽的深度设计尺寸(65-00.2)要求。
考虑到用φ25+00.033孔及其底面定位,会使工件定位的稳定性和牢靠性差,可选用φ40-00.039外圆及其台阶面作为定位。
铣槽时,选用三面刃圆盘铣刀铣削较为方便,工件竖直安装。
因而外圆台阶面为主定位面,限制工件三个自由度,φ40-00.039外圆限制工件两个自由度。
综上所述,该零件各加工表面的加工、定位及加紧方案如表1-5所示:表1-5各加工表面的加工、定位及加紧方案五、安排工艺过程由于结构简单、加工要求不高,又是中批生产类型,零件加工过程不必划分加工阶段,结合个表面加工、定位和夹紧方案的分析、确定,除宽5的通槽,其余表面均可在同一台车床上完成加工。
这样,该零件加工工艺过程简单,工序少。
机械加工工艺过程安排如表1-6:六、工序设计(一)绘制工序图,选择机床、工艺装备工序20 车在工序20,因轴向尺寸φ20+00.033不能直接测量φ25+00.033孔深度工序尺寸和φ40-00.039外圆长度尺寸(30.1±0.03和50±0.03)间接得到.因工件尺寸比较小,加工要求不高,选择常用的CA6140机床即可。
外圆的加工余量比较多,应选用硬质合金车刀。
在工序30,槽宽由刀具宽度直接保证,槽宽由调整法得到。
铣槽工序尺寸标注位置如工序图所示。
三面刃圆盘铣刀铣该工件通槽比较方便,铣床应是卧式的(X62W)。
在批量生产的情况下,为保证精度的稳定性,需要专用夹具安装工件。
工序30 铣(二)确定工序尺寸1.判断是否需要工艺尺寸链来确定工序尺寸将零件图上的设计尺寸位置与工序图上的工序尺寸位置逐一对照,发现轴向设计尺寸20-00.2、65-00.2和100在工序图上找不到,说明这三个设计尺寸间接得到,需要以它们作为封闭环分别建立三个工艺尺寸链,才能计算出影响他们的相应工序尺寸。
镜像工序尺寸的确定不需要尺寸链。
2.径向工序尺寸的确定表1-7径向工序尺寸工序尺寸精度等级加工面加工方案加工余量工序尺寸及公差值φ60外圆车7 - φ603×1凹槽车28 - φ39φ40-00.039外圆车27 IT8,T=0.039 φ40-00.039φ25+00.033孔钻车187IT12,T=0.21IT8,T=0.033φ18+00.21φ25+00.033φ20+00.033孔钻扩铰181.80.2IT12,T=0.21IT10,T=0.084IT8,T=0.033φ18+00.21φ19.8+00.084φ20+00.0333.轴向工序尺寸的确定(1)建立工艺尺寸链工序尺寸追踪图在工艺过程复杂、工序多的情况下,为了能快速正确地建立好工艺尺寸链,可采用“工序尺寸追踪法”。
①将同一方向的工序尺寸按先后得到的顺序画在零件图下方,见上图。
②确定封闭环根据工序尺寸追踪图与两件图上的设计尺寸逐一对照,得出三个封闭环:轴向设计尺寸20-00.2、65-00.2和100。
③查找组成环,建立工艺尺寸链1)在工序尺寸追踪图上,分别从某一封闭环的两端沿着竖线往上走,碰到箭头就拐弯,直到会和在某一条竖线上。
所经过的工序尺寸既为尺寸链中的组成环,按行走路线原样画下来。
工艺尺寸链(1)工艺尺寸链(2)工艺尺寸链(3)2)工艺尺寸链的计算工艺尺寸链(1)确定各组组成环公差TΣ=0.2=T1+T2+T4按各组成环加工、检测的难易程度分配封闭环公差。
取T1=T2=0.06,则T4=0.08。
确定各组成环基本尺寸从工序尺寸追踪图中可直接得到A1=50,A2=30.1,A4=45。
确定各组成环上下偏差设A1=50±0.03,A2=30.1±0.03,则A4=45±0.04。
因工序尺寸精度不高,其加工与检测无难度。
同理,工艺尺寸链(2)各组成环基本尺寸为:A1=50,A2=30.1,A4=45。
各组成环上下偏差为:A1=50±0.03,A2=30.1±0.03。
封闭环上下偏差为:AΣ=19.9±0.06。
工艺尺寸链(3)各组成环基本尺寸为:A1=50,A3=50。
各组成环上下偏差为:A1=50±0.03,A3=50。
封闭环上下偏差为:AΣ=100±0.03。
(三)切削用量的制定工序20中φ40-00.039外圆:加工余量=(67-40)/2=13.5,因之后要车3×1凹槽,所以车φ40-00.039外圆时多车出3mm,因端面表面粗糙度要求不高,所以背吃刀量可以大一点,先选择3mm车4次,再选择1.5mm车1次。
当a p=3mm时,因背吃刀量大,所以进给量要尽量减小以免损坏车刀和保证表面粗糙度,通过查硬质合金车刀常用切削速度表我们选择车刀进给量为0.7mm/r,切削速度为60m/min,计算出主轴转速n=1000v/πd=477.7r/min。
再查卧式车床刀架进给量表取进给量标准值f=0.73mm/r,查卧式车床主轴转速表取标准转速n=500r/min,计算出切削速度V=62.8m/min。
当a p=1.5mm时,通过查硬质合金车刀常用切削速度表我们选择车刀进给量为0.1mm/r,切削速度为110m/min,计算出主轴转速n=875.8r/min。
再查卧式车床刀架进给量表取进给量标准值f=0.1mm/r,查卧式车床主轴转速表取标准转速n=900r/min,计算出切削速度V=113m/min。
3×1凹槽:因一开始以车去半径13.5mm,所以加工余量为1mm,所以选择背吃刀量为1mm,为方便操作,主轴转速与粗车φ40-00.039外圆数据一样。
小端面:加工余量=106-100=6mm,所以选择在两端各车3mm。
又因端面表面粗糙度要求不高,所以背吃刀量可以大一点,选择3mm,一次性车出,通过查硬质合金车刀常用切削速度表我们选择车刀进给量为0.7mm/r,再查卧式车床刀架进给量表取进给量标准值f=0.71,为方便操作,主轴转速与粗车φ40-00.039外圆数据一样,计算出切削速度V=62.8m/min。
φ25+00.033孔:因后面要钻、扩、铰φ20+00.033孔,为减少工作程序和工作时间,一次性钻出φ18通孔,在车出φ25+00.033孔。
钻φ18通孔时,取背吃刀量为18mm,查高速钢麻花钻钻削碳钢、合金钢的切削用量表取进给量为0.26mm/r,切削速度为17m/min,计算出主轴转速n=300.8/min。
再查卧式车床刀架进给量表取进给量标准值f=0.25mm/r,查卧式车床主轴转速表取标准转速n=320r/min,计算出切削速度V=18m/min。
车φ25+00.033孔时,切削余量为(25-18)/2=3.5mm,选择背吃刀量为1.75,车两次完成,通过查硬质合金车刀常用切削速度表我们选择车刀进给量为0.35mm/r,切削速度为80m/min,计算出主轴转速n=1019.2r/min。
再查卧式车床刀架进给量表取进给量标准值f=0.35mm/r,查卧式车床主轴转速表取标准转速n=950r/min,计算出切削速度V=74.6m/min。
φ60外圆:加工余量=(67-60)/2=3.5,因端面表面粗糙度要求不高,所以背吃刀量可以大一点,选择 3.5mm,一次性车出,通过查硬质合金车刀常用切削速度表我们选择车刀进给量为0.7mm/r,切削速度为60m/min,计算出主轴转速n=318.5r/min。