统计过程控制培训(最终)ppt
合集下载
统计过程控制(SPC)(PPT58页)
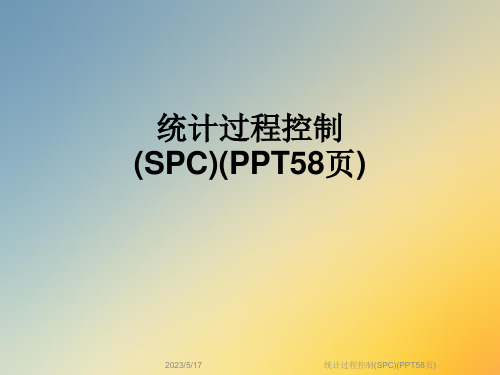
➢ 普通原因 ➢ 特殊原因
江铃汽车股份有限公司
统计过程控制(SPC)(PPT58页)
普通原因 普通原因造成变差的一个原因,它影响被研究过程的所
有单值。(处于统计控制状态;在统计上受控;受控) 造成随着时间的推移具有稳定的且可重复的分布过程中
的许多变差的原因 特点
过程分布将不发生变化 过程的输出是可预测的 过程是稳定、可控的。 采取系统的措施,由管理人员解决问题
江铃汽车股份有限公司
统计过程控制(SPC)(PPT58页)
2.3局部措施和系统措施
措施 对比
对象
系统措施
通常用来消除变差的普 通原因
局部措施
通常用来消除变 差的特殊原因
实施人员
几乎总是要求管理措施, 以便纠正
通常由与过程直 接相关的人员实 施
效果
大约可纠正85%的过程 问题
通常可纠正大约 15%的过程问题
一个可接受的过程必须是处于受控统计控制 状态的且其固有变差(能力)必须小于图纸 的公差
应通过检查并消除变差的特殊原因使过程处 于受统计控制状态,那么性能是可预测的, 变可评定其满足顾客期望的能力。这是持续 改进的基础
江铃汽车股份有限公司
统计过程控制(SPC)(PPT58页)
3.4过程改进循环
2.1过程的理解及过程控制
1.过程—所谓过程是指共同作用以产出输出的供方、生产 者、人、设备、输入材料、方法和环境及使用输出的顾 客的集合。
过程性能取决于:
供方与顾客之间的沟通
过程设计及实施的方式
运作和管理的方式
2.过程的信息
通过分析过程输出可以获得许多与过程性能有关的信息。如过程 是否稳定,过程能力如何。
4.1控制图应用说明
江铃汽车股份有限公司
统计过程控制(SPC)(PPT58页)
普通原因 普通原因造成变差的一个原因,它影响被研究过程的所
有单值。(处于统计控制状态;在统计上受控;受控) 造成随着时间的推移具有稳定的且可重复的分布过程中
的许多变差的原因 特点
过程分布将不发生变化 过程的输出是可预测的 过程是稳定、可控的。 采取系统的措施,由管理人员解决问题
江铃汽车股份有限公司
统计过程控制(SPC)(PPT58页)
2.3局部措施和系统措施
措施 对比
对象
系统措施
通常用来消除变差的普 通原因
局部措施
通常用来消除变 差的特殊原因
实施人员
几乎总是要求管理措施, 以便纠正
通常由与过程直 接相关的人员实 施
效果
大约可纠正85%的过程 问题
通常可纠正大约 15%的过程问题
一个可接受的过程必须是处于受控统计控制 状态的且其固有变差(能力)必须小于图纸 的公差
应通过检查并消除变差的特殊原因使过程处 于受统计控制状态,那么性能是可预测的, 变可评定其满足顾客期望的能力。这是持续 改进的基础
江铃汽车股份有限公司
统计过程控制(SPC)(PPT58页)
3.4过程改进循环
2.1过程的理解及过程控制
1.过程—所谓过程是指共同作用以产出输出的供方、生产 者、人、设备、输入材料、方法和环境及使用输出的顾 客的集合。
过程性能取决于:
供方与顾客之间的沟通
过程设计及实施的方式
运作和管理的方式
2.过程的信息
通过分析过程输出可以获得许多与过程性能有关的信息。如过程 是否稳定,过程能力如何。
4.1控制图应用说明
统计过程控制培训教材(PPT 246页)

3.使学员掌握过程能力评估的方法,改善过程能力.
3
二、课程大纲
一.SPC统计过程控制概论 1.何谓统计过程控制 2.统计方法的意义 3.SPC的起源 4.SPC的基本原理 5.统计过程控制之意义 6.SPC能解决过程之问题 7.SPC的特点
二.SPC理论讲解 1.过程控制基本理论 2.过程变异 3.常态分配等基础统计学理论介绍 4.过程变异原因 (普通原因/特殊原因分析)
更有效的方法是---预防
29
对许多人来说预防和策略听起来很明智,甚至显然的。 经常能听到这样的口号“第一次就把工作做好。”但光在 口号是不够的。所要求的是理解统计过程控制系统和各个 要素。下述逐步介绍了这些要素。并可以看成是下列问题 的答案: ◆ 什么是过程控制系统? ◆ 变差是如何影响过程输出的? ◆ 统计技术是如何区分一个问题实质是局部的还是涉
Control: (控制)事物的发展和变 化是可预测的;
13
二.统计方法的意义
•策划数据的收集,整理与解释资料,并据以导 出结论或予以推广的过程,称为统计方法。 •阐述统计方法与理论的科学,即为统计学。 •上述统计方法,从全部资料中,抽取部分数据, 对此部分数据的收集、整理,并将其结果加以 解释,使不了解统计方法的人得以了解,并据 以对全部资料作成结论,或推导出全部资料所 蕴含的特性。
16
四.SPC的基本原理
▪ 波动无处不在; ▪ 正常波动和异常波动; ▪ 通过保持过程受控和稳态提高过程能力
和品质水平.
17
3 σ 原理
X
ቤተ መጻሕፍቲ ባይዱ
68% 95% 99.7%
18
五.SPC的意义
➢ 全面、及时了解品质信息,信息共享; ➢ 有效监测和预防,提高生产率; ➢ 提高客户满意度,赢得更多客户; ➢ 保持产品和服务品质的稳定性及进一步的持
3
二、课程大纲
一.SPC统计过程控制概论 1.何谓统计过程控制 2.统计方法的意义 3.SPC的起源 4.SPC的基本原理 5.统计过程控制之意义 6.SPC能解决过程之问题 7.SPC的特点
二.SPC理论讲解 1.过程控制基本理论 2.过程变异 3.常态分配等基础统计学理论介绍 4.过程变异原因 (普通原因/特殊原因分析)
更有效的方法是---预防
29
对许多人来说预防和策略听起来很明智,甚至显然的。 经常能听到这样的口号“第一次就把工作做好。”但光在 口号是不够的。所要求的是理解统计过程控制系统和各个 要素。下述逐步介绍了这些要素。并可以看成是下列问题 的答案: ◆ 什么是过程控制系统? ◆ 变差是如何影响过程输出的? ◆ 统计技术是如何区分一个问题实质是局部的还是涉
Control: (控制)事物的发展和变 化是可预测的;
13
二.统计方法的意义
•策划数据的收集,整理与解释资料,并据以导 出结论或予以推广的过程,称为统计方法。 •阐述统计方法与理论的科学,即为统计学。 •上述统计方法,从全部资料中,抽取部分数据, 对此部分数据的收集、整理,并将其结果加以 解释,使不了解统计方法的人得以了解,并据 以对全部资料作成结论,或推导出全部资料所 蕴含的特性。
16
四.SPC的基本原理
▪ 波动无处不在; ▪ 正常波动和异常波动; ▪ 通过保持过程受控和稳态提高过程能力
和品质水平.
17
3 σ 原理
X
ቤተ መጻሕፍቲ ባይዱ
68% 95% 99.7%
18
五.SPC的意义
➢ 全面、及时了解品质信息,信息共享; ➢ 有效监测和预防,提高生产率; ➢ 提高客户满意度,赢得更多客户; ➢ 保持产品和服务品质的稳定性及进一步的持
统计过程控制培训课件(PPT 75页)

个体:组成总体的每个单元(产品)叫做个体。
总体含量(总体大小):总体中所含的个体数,常用N表示。
第四节 总体与样本
样本(子样):是指从总体中随机抽取出来并且要对它进行详细研 究分析的一部分个体(产品);样本是由1个或若干个样品组成的。
样本容量(样本大小):样本中所含的样品数目,常用n表示。
抽样:是指从总体中随机抽取样品组成样本的活动过程。
2. 推断性 ——统计方法都要通过详细研究样本来达到了解、推测总体状况的目 的,因此它具有由局部推断整体的性质。
3. 风险性 ——统计方法既然要推断用部分整体,那么这种由推断而得出的结论 就不会是百分之百正确,即可能有错误。犯错误就要担风险。
三、统计方法的用途
• 1. 提供表示事物特征的数据;(平均值、中位数、标准偏差、方差、极差) • 2. 比较两事物的差异;(假设检验、显著性检验、方差分析、水平对比、分层法、树图、
第二节 产品质量波动
一、正常波动 二、异常波动
一、正常波动
——正常波动是由随机原因(普通原因)引起的产品质量波动; ——仅有正常波动的生产过程称为处于统计控制状态,简称为控制状 态或稳定状态。
二、异常波动
——异常波动是由系统原因(特殊原因)引起的产品质量波动; ——有异常波动的生产过程称为处于非统计控制状态,简称为失控状 态或不稳定状态。
三、 变差的种类
普通原因 由于正常的磨耗和磨损,如工具磨损。
特殊原因 非正常情况,如工具损坏。
第四节 控制图
• 一、概述 • 二、应用控制图的步骤 • 三、应用实例 • 四、控制图的观察与分析
一、概述
--控制图又叫管制图。它是用来区分由异常原因引起的波动、或 是由过程固有的随机原因引起的偶然波动的一种工具。
总体含量(总体大小):总体中所含的个体数,常用N表示。
第四节 总体与样本
样本(子样):是指从总体中随机抽取出来并且要对它进行详细研 究分析的一部分个体(产品);样本是由1个或若干个样品组成的。
样本容量(样本大小):样本中所含的样品数目,常用n表示。
抽样:是指从总体中随机抽取样品组成样本的活动过程。
2. 推断性 ——统计方法都要通过详细研究样本来达到了解、推测总体状况的目 的,因此它具有由局部推断整体的性质。
3. 风险性 ——统计方法既然要推断用部分整体,那么这种由推断而得出的结论 就不会是百分之百正确,即可能有错误。犯错误就要担风险。
三、统计方法的用途
• 1. 提供表示事物特征的数据;(平均值、中位数、标准偏差、方差、极差) • 2. 比较两事物的差异;(假设检验、显著性检验、方差分析、水平对比、分层法、树图、
第二节 产品质量波动
一、正常波动 二、异常波动
一、正常波动
——正常波动是由随机原因(普通原因)引起的产品质量波动; ——仅有正常波动的生产过程称为处于统计控制状态,简称为控制状 态或稳定状态。
二、异常波动
——异常波动是由系统原因(特殊原因)引起的产品质量波动; ——有异常波动的生产过程称为处于非统计控制状态,简称为失控状 态或不稳定状态。
三、 变差的种类
普通原因 由于正常的磨耗和磨损,如工具磨损。
特殊原因 非正常情况,如工具损坏。
第四节 控制图
• 一、概述 • 二、应用控制图的步骤 • 三、应用实例 • 四、控制图的观察与分析
一、概述
--控制图又叫管制图。它是用来区分由异常原因引起的波动、或 是由过程固有的随机原因引起的偶然波动的一种工具。
SPC统计过程控制培训课件PPT(48张)

音干扰、振动、照明、室内净化、现场
因 污染程度等等。
素
7
过程能力
SQE Training
过程能力(process capability)以往称为工序能力
过程能力是指工序处于控制状态下的实际加工能 力。---素充分标准化,处于稳定状态 下,工序所表现出来的保证工序质量的能力。
14
指数分类
SQE Training
1、Cp:分布中心无偏离规格中心时衡量 过程能力的指数;
2、Cpk: 分布中心偏离规格中心时衡量 过程能力的指数;
3、Cpm:目标值与规格中心不一致时衡量 过程能力的指数;
4、Cpu:上单侧过程能力指数; 5、Cpl: 下单侧过程能力指数。
15
SQE Training
过程能力决定于质量因素:人、机、料、法、环, 而与公差无关。过程能力是过程的固有属性。
8
SQE Training
进行过程能力分析的意义
一、保证产品质量的基础工作; 二、提高过程能力的有效手段; 三、找出产品质量改进的方向; 四、向客户证明加工过程的能力。
9
指数分类
SQE Training
Cp,Cpk,Cpm Pp,Ppk,Ppm
Ppk修正的过程性能指数 Ppk:“我们实际真正做到多好”
13
SQE Training
Cp,Cpk与Pp,Ppk的应用时机
短期过程能力指数
长期过程能力指数
Cp,Cpk,Cpm
Pp,Ppk,Ppm
新产品试作阶段; 初期生产阶段; 工程变更或设备变更时; 用于初始过程能力研究;
• 量产阶段; • 用于过程能力研究;
SQE Training
Statistical
因 污染程度等等。
素
7
过程能力
SQE Training
过程能力(process capability)以往称为工序能力
过程能力是指工序处于控制状态下的实际加工能 力。---素充分标准化,处于稳定状态 下,工序所表现出来的保证工序质量的能力。
14
指数分类
SQE Training
1、Cp:分布中心无偏离规格中心时衡量 过程能力的指数;
2、Cpk: 分布中心偏离规格中心时衡量 过程能力的指数;
3、Cpm:目标值与规格中心不一致时衡量 过程能力的指数;
4、Cpu:上单侧过程能力指数; 5、Cpl: 下单侧过程能力指数。
15
SQE Training
过程能力决定于质量因素:人、机、料、法、环, 而与公差无关。过程能力是过程的固有属性。
8
SQE Training
进行过程能力分析的意义
一、保证产品质量的基础工作; 二、提高过程能力的有效手段; 三、找出产品质量改进的方向; 四、向客户证明加工过程的能力。
9
指数分类
SQE Training
Cp,Cpk,Cpm Pp,Ppk,Ppm
Ppk修正的过程性能指数 Ppk:“我们实际真正做到多好”
13
SQE Training
Cp,Cpk与Pp,Ppk的应用时机
短期过程能力指数
长期过程能力指数
Cp,Cpk,Cpm
Pp,Ppk,Ppm
新产品试作阶段; 初期生产阶段; 工程变更或设备变更时; 用于初始过程能力研究;
• 量产阶段; • 用于过程能力研究;
SQE Training
Statistical
统计过程控制培训讲义(PPT 67页)
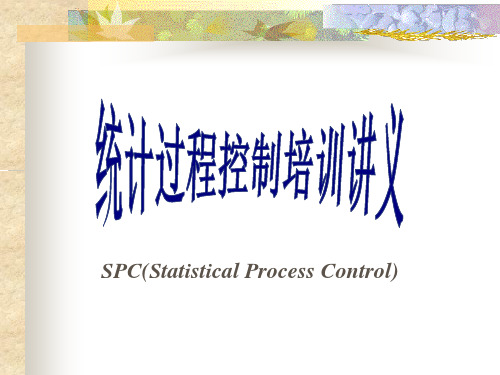
SPC(Statistical Process Control)
持续改进及过程控制 • 企业目标-客户满意 • 实现目标-持续改进,强调缺陷的预防 • 有效方法-统计过程控制
检验和预防 • 检验是对过程结束后的输出进行测量 – 通过抽样检验--发现合格/不合格 – 通过100%检验--发现合格/不合格 • 预防是在生产中对过程进行测量 – 通过对过程的测量,使质量问题在导致报废、返
计数型数值和计量型数值
特殊原因
普通原因
一种间断性的,不可预 造成变差的一个原因,
计的,不稳定的变差来
它影响被研究过程输
源。有时被称为可查明
出的所有单值;在控
原因,存在它的信号是: 制图分析中,它表现
存在超过控制线的点或
为随机过程变差的一
存在在控制线之内的链
部分。
或其他非随机性的情形。
局部措施和对系统采取措施
1-4、选择控制图的刻度 4-1 两个控制图的纵坐标分别用于 X 和 R 的测量值。 4-2 刻度选择 :
接上页
对于X 图,坐标上的刻度值的最大值与最小值的差应至少为子组均值 (X)的最大值与最小值的差的2倍,对于R图坐标上的刻度值的最大值 与最小值的差应为初始阶段所遇到的最大极差(R)的2倍。 注:一个有用的建议是将 R 图的刻度值设置为 X 图刻度值的2倍。
等过程调整到稳态后,延长控制图的控制线作为控 制用控制图。应用过程参数判断
控制图类型
X-R 均值和极差图 计量 型数 X-δ均值和标准差图 据
X -R 中位值极差图
X-MR 单值移动极差图
计数 型数 据
P chart 不合格品率控制图 nP chart不合格品数控制图 C chart 缺陷数控制图
持续改进及过程控制 • 企业目标-客户满意 • 实现目标-持续改进,强调缺陷的预防 • 有效方法-统计过程控制
检验和预防 • 检验是对过程结束后的输出进行测量 – 通过抽样检验--发现合格/不合格 – 通过100%检验--发现合格/不合格 • 预防是在生产中对过程进行测量 – 通过对过程的测量,使质量问题在导致报废、返
计数型数值和计量型数值
特殊原因
普通原因
一种间断性的,不可预 造成变差的一个原因,
计的,不稳定的变差来
它影响被研究过程输
源。有时被称为可查明
出的所有单值;在控
原因,存在它的信号是: 制图分析中,它表现
存在超过控制线的点或
为随机过程变差的一
存在在控制线之内的链
部分。
或其他非随机性的情形。
局部措施和对系统采取措施
1-4、选择控制图的刻度 4-1 两个控制图的纵坐标分别用于 X 和 R 的测量值。 4-2 刻度选择 :
接上页
对于X 图,坐标上的刻度值的最大值与最小值的差应至少为子组均值 (X)的最大值与最小值的差的2倍,对于R图坐标上的刻度值的最大值 与最小值的差应为初始阶段所遇到的最大极差(R)的2倍。 注:一个有用的建议是将 R 图的刻度值设置为 X 图刻度值的2倍。
等过程调整到稳态后,延长控制图的控制线作为控 制用控制图。应用过程参数判断
控制图类型
X-R 均值和极差图 计量 型数 X-δ均值和标准差图 据
X -R 中位值极差图
X-MR 单值移动极差图
计数 型数 据
P chart 不合格品率控制图 nP chart不合格品数控制图 C chart 缺陷数控制图
统计过程控制培训教材(PPT 38张)

控制图原理
2、基本原理
质量波动理论
“人、机、料、法、环” + “软(件)、辅(助材料)、公用系统
质量波动因素 = 偶然因素 +异常因素
偶然因素:过程固有、始终存在、影响微小、难以除去 异常因素:并非固有、时有时无、影响较大、不难去除
小概率原理
小概率事件在一次试验中几乎不可能发生、若发生则判断异常。 超出UCL为千分之一。
12
13 14 15 16 17 18 19 20
100
100 100 100 100 100 100 100 100
6
8 5 2 3 6 2 7 5
0.06
0.08 0.05 0.02 0.03 0.06 0.02 0.07 0.05
22
23 24 25 合计 平均
100
100 100 100 2500 100
P控制图(不良率)
1.公式 (1) 公组样本大小n相等时:
P CL = P UCL = P
LCL =
P(1 -P)/n -P)/n + 3 P(1
P (2) n不等,且相差小于20% 时: P(1 -P)/ n P P(1 -P)/ n CL = P
UCL = LCL = + 3 - 3
判定规则
判定规则
判定规则
判定规则
判定规则
案例
案例
案例
常规控制图及用途
计量控制图
计量值的数据收集:按一定时间间 隔抽取一定的样本,然后进行测量, 再将测量到的数据记录下来。计量 型数据具有连续性,故它的抽样计 划与计数值有很大的差异。它通常 根据产品要求,对产品的重要特性 定时抽取固定样本个数。
统计过程控制培训课件
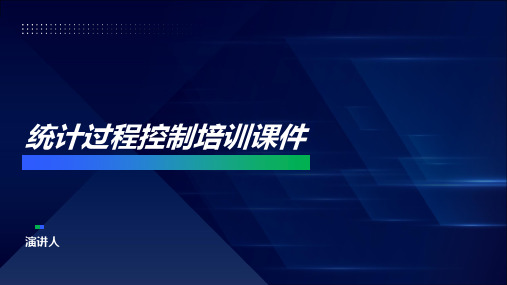
04
应用:可用 于生产过程、 质量控制、 项目管理等 领域
过程改进方法
收集数据:通过 观察、测量等方 式收集数据
分析数据:对数 据进行整理、分 析,找出问题所 在
制定改进方案: 根据分析结果, 制定改进方案
实施改进方案: 按照改进方案进 行实施,并对实 施效果进行评估 和改进
3
统计过程控制的案例分析
03
政府部门:用 于公共政策和 公共服务的质 量控制和改进
05
02
服务业:用 于服务质量 的控制和改 进
04
教育行业:用 于教育质量和 教学效果的控 制和改进
2
统计过程控制的方法
控制图的使用
控制图的定义:用于监控 生产过程中产品质量波动 的工具
控制图的使用方法:选择 合适的控制图类型,设定 控制限,绘制控制图,分 析控制图,采取措施
案例背景
某公司生产过程中出现质 量问题
A
解决方案:采用统计过程 控制方法进行改进
C
B
问题原因:生产过程中的 参数控制不当
D
改进效果:产品质量得到 显著提升,生产效率提高
案例分析过程
问题描述:明确 案例的背景、问 题及目标
原因分析:根据数 据分析结果,找出 问题的原因
数据收集:收集与 问题相关的数据, 如生产数据、质量 数据等
统计过程控制主要 包括控制图、过程 能力分析、抽样检 验等方法。
统计过程控制可以 帮助企业及时发现 生产过程中的异常 情况,并采取措施 进行纠正。
统计过程控制的目的
提高产 品质量
降低生 产成本
提高生 产效率
预防质 量问题
统计过程控制的应用领域
制造业:用 于生产过程 的质量控制 和改进
统计过程控制SPC培训教材ppt课件

方 法
材 料
人 员
机 器
中要因
中要因
中要因
中要因
小要因
如何做
小要因
*
6. 直方图(Histogram;亦称柱状图):将所收集的测定特性值或结果 值,分为几个相等的区间作为横轴,并将各区间内所测定的特性值或 结果值依所出现的次数累积而成的面积,用柱子排起来的图形,称为 直方图。亦即指用来对特征数据进行分级整理,将杂乱无章的资料, 解析出其规律性,以得出其分布特征的统计分析的方法。
与要求相比偏高
与要求相比偏低
正常
SL=130
Sμ=160
20 15 10 5
*
7. 控制图(Control Chart):用来表示一个过程特性的图象,图上标 有根据那个特性收集到的一些统计数据,如一条中心线、一条或两条 控制限,它能减少I类错误和Ⅱ类错误的净经济损失。它有两个基本 的用途:一是用来判定一个过程是否一直受统计控制;二是用来帮助 过程保持受控状态。亦即指附有控制界限的图表,用以描述样本数据 与界限比较。若数据超出界限或出现“链”及非随机图形,表示过程 存在特殊原因变差,则应采用适当的措施加以消除。 7.1 Ⅰ类错误:拒绝一个真实的假设。例如:采取了一个适用于特 殊原因的措施而实际上过程还没有发生变化;即过度控制。 7.2 Ⅱ类错误:没有拒绝一个错误的假设。例如:对实际上受特殊 原因影响的过程没有采取适当的措施;即控制不足。 7.3 计数值控制图与计量值控制图的应用比较:
*
铸造车间产品生产废品统计表
*
5. 特性要因分析图(Characteristic Diagram ;亦称石川图或鱼骨图/鱼刺图 或因果图):指将造成某项结果的众多原因,以有系统的方式来表达结果 (特性)与原因之间的关系图表。 5.1 因果图(Cause-and-Effect Diagram):一种用于解决单个问题的简 单工具,它对各种过程要素采用图形描述来分析过程可能的变差源, 也被称作鱼刺图(以其形状命名)或石川图(以其发明命名)。 A)、某项结果的形成,必定有其原因,应设法利用图解法找出其原 因来,这个概念是由日本品管大师石川馨博士提出的。 B)、特性要因图是利用5M+1E:人员(Man)、机器(Machine)、材 料(Material)、方法(Method)、测量(Measurement)、环 境(Environment)等五大类加以分析及应用的。
材 料
人 员
机 器
中要因
中要因
中要因
中要因
小要因
如何做
小要因
*
6. 直方图(Histogram;亦称柱状图):将所收集的测定特性值或结果 值,分为几个相等的区间作为横轴,并将各区间内所测定的特性值或 结果值依所出现的次数累积而成的面积,用柱子排起来的图形,称为 直方图。亦即指用来对特征数据进行分级整理,将杂乱无章的资料, 解析出其规律性,以得出其分布特征的统计分析的方法。
与要求相比偏高
与要求相比偏低
正常
SL=130
Sμ=160
20 15 10 5
*
7. 控制图(Control Chart):用来表示一个过程特性的图象,图上标 有根据那个特性收集到的一些统计数据,如一条中心线、一条或两条 控制限,它能减少I类错误和Ⅱ类错误的净经济损失。它有两个基本 的用途:一是用来判定一个过程是否一直受统计控制;二是用来帮助 过程保持受控状态。亦即指附有控制界限的图表,用以描述样本数据 与界限比较。若数据超出界限或出现“链”及非随机图形,表示过程 存在特殊原因变差,则应采用适当的措施加以消除。 7.1 Ⅰ类错误:拒绝一个真实的假设。例如:采取了一个适用于特 殊原因的措施而实际上过程还没有发生变化;即过度控制。 7.2 Ⅱ类错误:没有拒绝一个错误的假设。例如:对实际上受特殊 原因影响的过程没有采取适当的措施;即控制不足。 7.3 计数值控制图与计量值控制图的应用比较:
*
铸造车间产品生产废品统计表
*
5. 特性要因分析图(Characteristic Diagram ;亦称石川图或鱼骨图/鱼刺图 或因果图):指将造成某项结果的众多原因,以有系统的方式来表达结果 (特性)与原因之间的关系图表。 5.1 因果图(Cause-and-Effect Diagram):一种用于解决单个问题的简 单工具,它对各种过程要素采用图形描述来分析过程可能的变差源, 也被称作鱼刺图(以其形状命名)或石川图(以其发明命名)。 A)、某项结果的形成,必定有其原因,应设法利用图解法找出其原 因来,这个概念是由日本品管大师石川馨博士提出的。 B)、特性要因图是利用5M+1E:人员(Man)、机器(Machine)、材 料(Material)、方法(Method)、测量(Measurement)、环 境(Environment)等五大类加以分析及应用的。
- 1、下载文档前请自行甄别文档内容的完整性,平台不提供额外的编辑、内容补充、找答案等附加服务。
- 2、"仅部分预览"的文档,不可在线预览部分如存在完整性等问题,可反馈申请退款(可完整预览的文档不适用该条件!)。
- 3、如文档侵犯您的权益,请联系客服反馈,我们会尽快为您处理(人工客服工作时间:9:00-18:30)。
统计过程控制
2012.5.25
前言(1)
• 日本名古屋大学调查了115家日本中小型企业, 结果发现平均每家工厂采用137张控制图
• 美国柯达彩色胶卷公司有5000职工,一共应用 35000张控制图,平均每个员工7张。因为胶卷 的片基上需要分别涂上8层厚度为1um至2um的 药膜;此外,对于种类繁多的化学原料也要应 用控制图进行控制。
四、分析用控制图和控制用控制图
分析用控制图主要分析两个方面的问题:
• 所分析的过程 是否处与稳态
• 过程能力指数是否满足要求,过程能力指数必须在 稳态下计算,故先要将过程调整到统计稳态,然后 再调整到技术稳态。
状态I:统计控制状态与技术控制状态同时达到是最 理想的状态Ⅱ:统计控制状态未达到,技术控制状 态达到; 状态Ⅲ:统计控制状态达到,技术控制状态未达到; 状态Ⅳ:统计控制状态与技术控制状态均未达到, 是最不理想的状态。
一.基本概念
• SPC的定义
SPC:Statistical Process Control
利用统计学的原理对过程中的各个阶段进 行评估和监控,建立并保持过程处于可接 受的并且稳定的水平,从而保证产品和服 务符合规定要求的质量管理技术。
控制图由来
SPC是美国休哈特在20世纪20年代所创造 的理论,它能科学地区分出生产过程中产 品质量的偶然波动与异常波动,从而对过 程的异常及时告警,以便人们采取措施, 消除异常,恢复过程的稳定
小概率原理又称为实际推断原理,当然运用小概率 原理也可能导致错误,但犯错误的可能性恰恰就是此 小概率。
三.控制图结构和原理
• 反证法思想
一旦控制图上点子越出界限线或其他小概率事件发生, 则怀疑原生产过程失控,也即不稳定,此时要从5MIE去找 原因,看是否发生了显著性变化。
三.控制图结构和原理
3σ准则
在生产过程中,仅有偶然性误差存在时,质量特性X服从 正态分布N( µ, σ ),则据正态分布的概率性质,有
P{µ - 3 σ < X< µ + 3 σ }=99.73 %
根据3σ原理,在一次试验中,如果样品出现在分布范围 (μ-3σ,μ+3σ)的外面,则认为生产处于非控制状态。 我们把μ-3σ定为LCL,μ+3σ定为UCL,μ定为CL,这样得 到的控制图称为3σ原理的控制图,也即称为休哈特控制图。
我们并不单纯追求控制图的多少,但工厂中使 用控制图的张数在一定程度上反映上管理现代 化的程度。
前言(2)
• 从上世纪初至今,质量管理发展阶段回顾 1、以产品检验为主要手段的质量检验阶段。 2、以数理统计方法和质量管理相结合的统计
质量控制阶段。
统计过程控制之父——休哈特,于1924年提出了世界上 第一张控制图。
3、全面质量管理阶段。
大家知道这几个概念吗?
• 控制图是什么?有什么用? • 什么是X?什么是R图? • X-R,是一张图还是两张图,是先做R
图,还是X图,还是无所谓先后? • UCL、LCL、USL、LSL 本次培训将给大家讲解这些问题。
目录
一、基本概念 二、统计过程控制特点 三、控制图结构和结构 四、分析用控制图和控制用控制图 五、控制图的两类错误和判异准则 六、控制图的类型及选用原则
3、SPC要解决的不是对特定工序要用什么 控制图的问题,它强调整个过程,重点 在“P”(Process)
三.控制图结构和原理
样本统计量数值
UCL CL
LCL
控制图示例
时间或样本号
• 图上横坐标:以时间先后排列的样本组号(子组号);
• 纵坐标为质量特性值或样本统计量。
• 两条控制限线一般用虚线表示,上面一条称为上控制限(记为UCL,Upper Control Limit),下面一条称为下控制限(记为LCL,Lower Control Limit);
三.控制图原理和结构
规范限
控制限
Y
6.8 6.4
6 5.6 5.2 4.8 4.4
4 3.6 3.2 2.8 2.4
2 1.6 1.2 0.8 0.4
0
X13.51013.62413.733δ713.85113.96414.07814.19114.30μ514.41814.53214.64514.75914.83721δ4.98615.099
三.控制图结构和原理
异常波动对控制图来说,包括两方面的内容: 1. 控制图界外的点 2.控制图内不随机的点
85
80 UCL
75
70 CL
65 60 LCL
异常波动
三.控制图结构和原理
• 小概率原理
所谓小概率原理,即认为小概率事件一般是不会发 生的。
由准则可知,若X服从正态分布,则X的可能值超 出控制界限的可能性只有0.27%。因此,一般认为不 会超出控制界限。
人、机器、原材料、工艺方法、测量及生产环境
• 正态曲线演化成控制图
UCL CL LCL
三.控制图结构和原理
质量波动理论: 偶然原因:过程固有,始终存在,对质量影
响微小,但难以去除。如脱水机开动时的 振动。 异常原因:非过程固有,有时存在,有时不 存在,对质量影响大,但不难去除,如切 割刀片的磨损。
SPC的内容包括2个方面:
• 利用控制图分析 • 计算过程能力指
过程的稳定性, 数分析稳定的过
看过程是否稳定, 程能力满足技术
对过程的异常因 要求的程度,对
素进行预警。
过程质量进行评
价。
二.统计过程控制的特点
1、贯彻预防性原则是现代质量管理的一个 特点。 SPC是一种预防性的方法。
2、SPC不是少数质量管理人员的事情,它 强调全员参与和团队合作精神。
• 中心线用实线表示(记为CL,Central Line)。
三.控制图结构和原理
• 正态性假定:任何生产过源自生产出来的产品,其质量特性值总会存 在一定程度的波动,当过程稳定或者说受控时,这些 波动主要是由5M1E的微小变化造成的随机误差。此时, 绝大多数质量特性值均服从或近似服从正态分布。
5M1E:
三.控制图结构和原理
• 3σ 原则即是控制图中的CL,UCL及LCL由下式确定 UCL=μ + 3σ CL = μ LCL= μ - 3σ
μ 和σ分别是统计量的总体均值和总体标准差,不可 能精确知道,可以通过已知的数据来加以估计。
注意:规范限(USL、LSL)不能用做控制限。规范限 用以区分合格与不合格,控制限用以区分偶然和异 常波动,两者不能混淆。
2012.5.25
前言(1)
• 日本名古屋大学调查了115家日本中小型企业, 结果发现平均每家工厂采用137张控制图
• 美国柯达彩色胶卷公司有5000职工,一共应用 35000张控制图,平均每个员工7张。因为胶卷 的片基上需要分别涂上8层厚度为1um至2um的 药膜;此外,对于种类繁多的化学原料也要应 用控制图进行控制。
四、分析用控制图和控制用控制图
分析用控制图主要分析两个方面的问题:
• 所分析的过程 是否处与稳态
• 过程能力指数是否满足要求,过程能力指数必须在 稳态下计算,故先要将过程调整到统计稳态,然后 再调整到技术稳态。
状态I:统计控制状态与技术控制状态同时达到是最 理想的状态Ⅱ:统计控制状态未达到,技术控制状 态达到; 状态Ⅲ:统计控制状态达到,技术控制状态未达到; 状态Ⅳ:统计控制状态与技术控制状态均未达到, 是最不理想的状态。
一.基本概念
• SPC的定义
SPC:Statistical Process Control
利用统计学的原理对过程中的各个阶段进 行评估和监控,建立并保持过程处于可接 受的并且稳定的水平,从而保证产品和服 务符合规定要求的质量管理技术。
控制图由来
SPC是美国休哈特在20世纪20年代所创造 的理论,它能科学地区分出生产过程中产 品质量的偶然波动与异常波动,从而对过 程的异常及时告警,以便人们采取措施, 消除异常,恢复过程的稳定
小概率原理又称为实际推断原理,当然运用小概率 原理也可能导致错误,但犯错误的可能性恰恰就是此 小概率。
三.控制图结构和原理
• 反证法思想
一旦控制图上点子越出界限线或其他小概率事件发生, 则怀疑原生产过程失控,也即不稳定,此时要从5MIE去找 原因,看是否发生了显著性变化。
三.控制图结构和原理
3σ准则
在生产过程中,仅有偶然性误差存在时,质量特性X服从 正态分布N( µ, σ ),则据正态分布的概率性质,有
P{µ - 3 σ < X< µ + 3 σ }=99.73 %
根据3σ原理,在一次试验中,如果样品出现在分布范围 (μ-3σ,μ+3σ)的外面,则认为生产处于非控制状态。 我们把μ-3σ定为LCL,μ+3σ定为UCL,μ定为CL,这样得 到的控制图称为3σ原理的控制图,也即称为休哈特控制图。
我们并不单纯追求控制图的多少,但工厂中使 用控制图的张数在一定程度上反映上管理现代 化的程度。
前言(2)
• 从上世纪初至今,质量管理发展阶段回顾 1、以产品检验为主要手段的质量检验阶段。 2、以数理统计方法和质量管理相结合的统计
质量控制阶段。
统计过程控制之父——休哈特,于1924年提出了世界上 第一张控制图。
3、全面质量管理阶段。
大家知道这几个概念吗?
• 控制图是什么?有什么用? • 什么是X?什么是R图? • X-R,是一张图还是两张图,是先做R
图,还是X图,还是无所谓先后? • UCL、LCL、USL、LSL 本次培训将给大家讲解这些问题。
目录
一、基本概念 二、统计过程控制特点 三、控制图结构和结构 四、分析用控制图和控制用控制图 五、控制图的两类错误和判异准则 六、控制图的类型及选用原则
3、SPC要解决的不是对特定工序要用什么 控制图的问题,它强调整个过程,重点 在“P”(Process)
三.控制图结构和原理
样本统计量数值
UCL CL
LCL
控制图示例
时间或样本号
• 图上横坐标:以时间先后排列的样本组号(子组号);
• 纵坐标为质量特性值或样本统计量。
• 两条控制限线一般用虚线表示,上面一条称为上控制限(记为UCL,Upper Control Limit),下面一条称为下控制限(记为LCL,Lower Control Limit);
三.控制图原理和结构
规范限
控制限
Y
6.8 6.4
6 5.6 5.2 4.8 4.4
4 3.6 3.2 2.8 2.4
2 1.6 1.2 0.8 0.4
0
X13.51013.62413.733δ713.85113.96414.07814.19114.30μ514.41814.53214.64514.75914.83721δ4.98615.099
三.控制图结构和原理
异常波动对控制图来说,包括两方面的内容: 1. 控制图界外的点 2.控制图内不随机的点
85
80 UCL
75
70 CL
65 60 LCL
异常波动
三.控制图结构和原理
• 小概率原理
所谓小概率原理,即认为小概率事件一般是不会发 生的。
由准则可知,若X服从正态分布,则X的可能值超 出控制界限的可能性只有0.27%。因此,一般认为不 会超出控制界限。
人、机器、原材料、工艺方法、测量及生产环境
• 正态曲线演化成控制图
UCL CL LCL
三.控制图结构和原理
质量波动理论: 偶然原因:过程固有,始终存在,对质量影
响微小,但难以去除。如脱水机开动时的 振动。 异常原因:非过程固有,有时存在,有时不 存在,对质量影响大,但不难去除,如切 割刀片的磨损。
SPC的内容包括2个方面:
• 利用控制图分析 • 计算过程能力指
过程的稳定性, 数分析稳定的过
看过程是否稳定, 程能力满足技术
对过程的异常因 要求的程度,对
素进行预警。
过程质量进行评
价。
二.统计过程控制的特点
1、贯彻预防性原则是现代质量管理的一个 特点。 SPC是一种预防性的方法。
2、SPC不是少数质量管理人员的事情,它 强调全员参与和团队合作精神。
• 中心线用实线表示(记为CL,Central Line)。
三.控制图结构和原理
• 正态性假定:任何生产过源自生产出来的产品,其质量特性值总会存 在一定程度的波动,当过程稳定或者说受控时,这些 波动主要是由5M1E的微小变化造成的随机误差。此时, 绝大多数质量特性值均服从或近似服从正态分布。
5M1E:
三.控制图结构和原理
• 3σ 原则即是控制图中的CL,UCL及LCL由下式确定 UCL=μ + 3σ CL = μ LCL= μ - 3σ
μ 和σ分别是统计量的总体均值和总体标准差,不可 能精确知道,可以通过已知的数据来加以估计。
注意:规范限(USL、LSL)不能用做控制限。规范限 用以区分合格与不合格,控制限用以区分偶然和异 常波动,两者不能混淆。