连续模常见的设计缺陷
连续模的维护要领及常见故障产生的原因

连续模的维护要领及常见故障产生的原因连续模的维护要领及常见故障产生的原因、处理对策:一.模具的维护要领连续模的维护,须做到细心、耐心、按部就班,切忌盲目从事。
因故障修模时需附有料带,以便问题的查询。
打开模具,对照料带,检查模具状况,确认故障原因,找出问题所在,再进行模具清理,方可进行拆模。
拆模时受力要均匀,针对卸料弹簧在固定板与卸料板之间和卸料弹簧直接顶在内导柱上的模具结构,其卸料板的拆卸要保证卸料板平衡弹出,卸料板的傾斜有可能导致模具内凸模的断裂。
1.凸凹模的维护凸凹模拆卸时应留意模具原有的状况,以便后续装模时方便复原,有加垫或者移位的要在零件上刻好垫片的厚度并做好记录。
更换凸模要试插卸料块、凹模是否顺畅,并试插与凹模间隙是否均匀,更换凹模也要试插与冲头间隙是否均匀。
针对修磨凸模后凸模变短需要加垫垫片达到所需要的长度应检查凸模有效长度是否足够。
更换已断凸模要查明原因,同时要检查相对应的凹模是否有崩刃,是否需要研磨刃口。
组装凸模要检查凸模与固定块或固定板之间是否间隙足够,有压块的要检查是否留有活动余量。
组装凹模应水平置入,再用平铁块置如凹模面上用铜棒将其轻敲到位,切不可斜置强力敲入,凹模底部要倒角。
装好后要检查凹模面是否与模面相平。
凸模凹模以及模芯组装完毕后要对照料带做必要检查,各部位是否装错或装反,检查凹模和凹模垫块是否装反,落料孔是否堵塞,新换零件是否需要偷料,需要偷料的是否足够,模具需要锁紧部位是否锁紧。
注意做脱料板螺丝的锁紧确认,锁紧时应从内至外,平衡用力交叉锁紧,不可先锁紧某一个螺丝再锁紧另一个螺丝,以免造成脱料板傾斜导致凸模断裂或模具精度降低。
2.卸料板的维护卸料板的拆卸可先用两把起子平衡撬起,再用双手平衡使力取出。
遇拆卸困难时,应检查模具内是否清理干净,锁紧螺丝是否全部拆卸,是否应卡料影起的模具损伤,查明原因再做相应处理,切不可盲目处置。
组装卸料板时先将凸模和卸料板清理干净,在导柱和凸模导入处加润滑油,将其平稳放入,再用双手压到位,并反复几次。
连续模工艺缺口标准
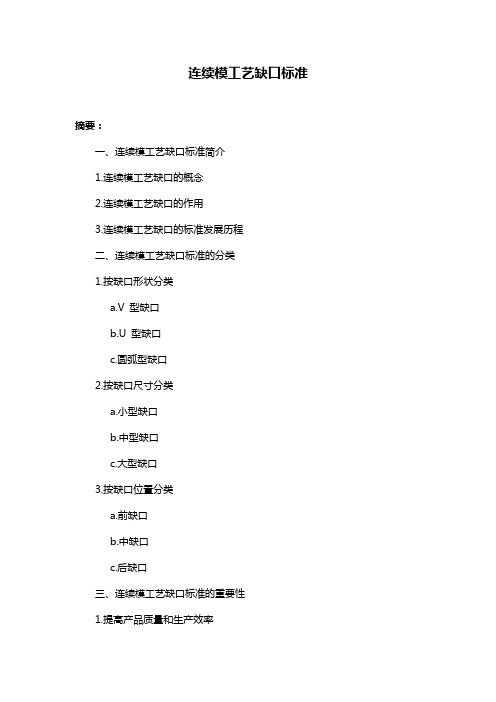
连续模工艺缺口标准摘要:一、连续模工艺缺口标准简介1.连续模工艺缺口的概念2.连续模工艺缺口的作用3.连续模工艺缺口的标准发展历程二、连续模工艺缺口标准的分类1.按缺口形状分类a.V 型缺口b.U 型缺口c.圆弧型缺口2.按缺口尺寸分类a.小型缺口b.中型缺口c.大型缺口3.按缺口位置分类a.前缺口b.中缺口c.后缺口三、连续模工艺缺口标准的重要性1.提高产品质量和生产效率2.降低生产成本3.促进产业链的发展四、连续模工艺缺口标准的应用领域1.汽车制造业2.电子制造业3.机械制造业4.其他行业五、连续模工艺缺口标准的未来发展趋势1.更高的精度和一致性2.更环保的制造工艺3.更广泛的应用领域正文:连续模工艺缺口标准是模具制造领域中一个重要的标准体系,它对产品的质量、生产效率和生产成本有着直接的影响。
本文将对连续模工艺缺口标准进行详细介绍,包括其概念、作用、发展历程、分类、重要性以及应用领域和未来发展趋势。
一、连续模工艺缺口标准简介连续模工艺缺口标准,主要是针对连续模工艺中的缺口部分进行规范和指导。
缺口,作为连续模工艺中的一个重要组成部分,主要用于产品的分离、定位和导向。
随着模具制造技术的不断发展,对缺口的要求也越来越高,因此制定一套完善的连续模工艺缺口标准具有重要意义。
二、连续模工艺缺口标准的分类连续模工艺缺口标准主要根据缺口形状、尺寸和位置进行分类。
不同类型的缺口在实际应用中具有不同的特点和优劣,因此需要根据具体的产品和工艺要求选择合适的缺口类型。
三、连续模工艺缺口标准的重要性连续模工艺缺口标准对于提高产品质量和生产效率具有重要作用。
合理的缺口设计可以降低产品的缺陷率,提高生产效率,从而降低生产成本。
此外,标准化的缺口设计还有助于推动产业链的发展,为相关企业提供技术支持。
四、连续模工艺缺口标准的应用领域连续模工艺缺口标准广泛应用于汽车制造业、电子制造业、机械制造业等多个行业。
在这些领域,连续模工艺缺口标准对于保证产品质量、提高生产效率和降低生产成本具有重要意义。
模具成形的缺陷种类及其原因

模具成形的缺陷种类及其原因1、充型不良现象有充型不满、边部塌陷等形式。
主要会造成产品成形的失败、原料的浪费、人工工艺和时间的浪费。
缺陷成因有很多,填充材料温度低、供给不足、流动性差;成形机预制射出压力低,管嘴孔径太小,汽筒管嘴堵塞;模具内表面润滑不良、温度低、入胶口流道小、水口位置不当、通气口位置不当或没有、冷却渣堵在流道或入胶口等2、毛刺现象主要是接缝毛刺。
会导致产品的加工困难和走形,严重时也可能使产品报废。
成因是填充材料温度高、供给过剩、流动性太好,成形机预制射出压力高,模具束模力度不足、温度高、相对机械能力,及其投影面积大等。
,3、缩水现象主要是出模后的塑性变形引起的。
成因是填充材料温度高、供给不足、收缩率太大,成形机预制射出压力低、保压时间短、射出速度过慢,模具内表面温度高、冷却时间短、成形壳体壁厚不一、入胶口流道小、推出不当等。
4、结合线现象主要是针对异形件而言,在线形转折处形成明显的痕迹。
成因是填充材料温度低、硬化过快、干燥不充分、润滑不良,成形机预制射出压力低、射出速度慢,模具内表面温度低、润滑不良、温度低、入胶口流道小、水口位置不当、通气口位置不当或没有等。
5、表面不良、有阴影主要是局部表面颜色和光泽的异常。
成因是填充材料挥发性大、混有异物、干燥不充分,供给不足,成形机预制射出压力低、管嘴堵塞或径小、射出速度慢,模具入胶口流道小、腐蚀对策不充分、离模材太多、通气口位置不当或没有等。
6、气痕现象成因有很多,填充材料温度低、流动性差、润滑不良,成形机预制射出压力低、射出速度慢、管嘴孔径太小,模具内表面润滑不良、温度低、入胶口流道小等。
7、银条痕气泡成因有很多,填充材料温度高、挥发性大、干燥不充分,成形机预制射出压力低、射出速度快、射出容量小、保压时间短,模具通气孔不当、成形壳体壁厚不一、入胶口流道小等。
8、黑条痕成因有很多,填充材料温度高、润滑剂过多、干燥不充分,模具通气孔位置不。
当或没有、模槽粘着油垢等。
连续刚构桥梁常见通病(介绍2)
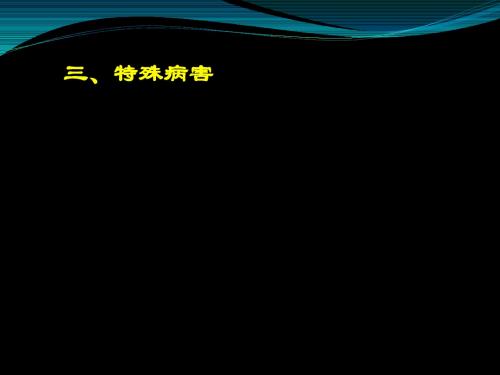
节,施工和监理应专人把关、监督实施。
千斤顶、试验仪器等,应按照相关规范规定,及时进
病害
1、竖向预应力粗钢筋下锚垫板位置处 砼不密实,张拉时锚垫板断裂,预应力 失效。
2、竖向预应力粗钢筋未注浆,粗钢筋锈蚀。
3、竖向预应力筋下锚端砼不密实,预应力 施加不到位。
4、箱梁底板混凝土崩裂。
5、箱梁腹板内外侧斜裂缝。
箱体外侧
箱体外侧
箱体内侧
箱体内侧
箱体内侧
6、跨中合拢段底板、腹板出现横(竖)向 裂缝。
7、箱梁底板混凝土不密实,露筋、露波纹管
8、外露波纹管内未注浆
9 、预应力张拉不到位,部分钢绞线松弛
10、横向预应力扁锚封锚混凝土不密实,锚 头外露锈蚀。
四、预防与控制
严格按照《桥涵施工技术规范》及设计文件的的要求,
控制每一个施工环节,以保证桥梁施工质量。
箱梁砼浇注、预应力张拉、波纹管注浆等关键施工环
常见模具缺陷及解决办法
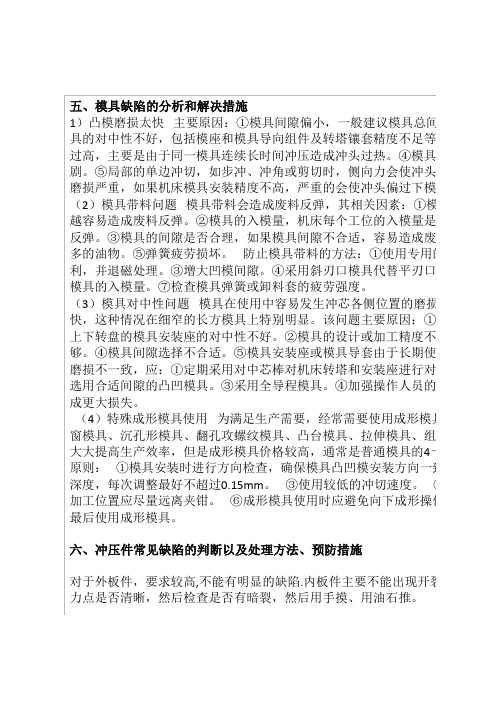
4)毛刺 判断方法:用眼睛看 原因:凸凹模间隙大。 处理办法:修模
5)孔偏 判断方法:上检具检查,与样件比较。 原因:工件没摆好,模具定位装置问题。 处理办法:如工件摆正后仍孔偏,应报告班长,通知修模。
6) 少孔 判断方法:与样件比较。 原因:冲头断掉。 处理办法判断方法:用眼睛看 原因:模具上模工作面粘附有颗粒状杂质。
11)拉伤 判断方法:用眼睛看 原因:模具工作面磨损,模具硬度不够。
12)砂粒 判断方法:用油石推 原因:材料或模具表面不干净。 处理办法:检查
13)碰伤、划伤 判断方法:用眼睛看 原因:进料或出料碰到模具等硬质物体。 产品要轻拿轻放,必要时将模具的闭合高度调大。
2.预防废品的主要措施:
A原材料必须与规定的技术条件相符合 (严格检查原材料的规格与牌号,在有条件的情况下对尺寸精度和表面质量要求 B对于工艺规程中所规定的各个环节应全面的严格的遵守 C所使用的压力机和冲模等工装设备,应保证在正常的工作状态下工作。 D生产过程中建立起严格的检验制度, 冲压件首件一定要全面检查, 检查合格后才能 投入生产,同时加强巡检,当发生意外时要及时处理。 E坚持文明生产制度, 如工件和坯件的传送一定要用合适的工位器具, 否则会压伤和 擦伤工件表面影响到工件的表面质量。 F在冲压过程中要保证模具腔内的清洁, 工作场所要整理的有条理加工后的工件要摆放整齐。
7)孔变形 判断方法:用眼睛看。 原因:冲头磨损。 处理办法:轻微的打油,严重的打油仍出现变形的应报告班长,通知修模。
8)拉深不到位 判断方法:看压力点是否清晰。 原因:主压力偏小。 处理办法:适当调高主压
9)折边不良 判断方法:与样件比较 原因:件没摆好,定位装置问题。
冲压连续模常见不良及处理方法

冲压连续模常见不良及处理方法较滑润之弯折角:15.送料不准&误送:料带在进给过程中,其进给行程(Pitch)会有所变化,而导致成品尺寸差异,严重者导致误送无法再进进给.一般造成原因有1.送料机垫片磨损2.标准Gauge安装错误3.卧式送料机无作动4.送料垂弧导致后缩5.导料销位置精度6.导料销的初始定位7.放松时间的调整8.导料销的直线长度9.是否需踢料10.料条前端及缺口处有无碰撞干涉11.扇形12.翘曲13.浮升具型式弹簧强度14.导板与料带的滑动间隙及平行性15.导板有无平顺---等变因.16.扇形:料带在经冲压工过程中,其料带会遭受来自冲剪,弯曲成形,压料力,和料带本身桡度,其料带会产生曲率呈一扇形.扇形不但影响冲模本身的顺送性,更会导致后制程电镀及装配无法上线,除上述外,其非常态的压伤,成形的拉扯亦是造成扇形的要因.一般采其特性,利用调整杆打点冲挤来抵消其变形桡度,其他异物的清扫及模具的钳工修整都是必要的优化措施.“A”依扇形方向选择打点方向矫正扇形摆幅DETAIL“A”扇形示意图:尖V凸出部调扇形打点尖凸部:17.高低针:在长针弯形端子,在其接触区或身长,易受成形因素影响,在其标齐线上呈高低起浮状.使产品易产生短路现象.一般除成形回弹造成的不同外,模具压着,二次冲压的不良,包装纸张力的压着,后制程不良的拉扯,装配夹具的配合性等.可由模具的调整站来矫正,但须注意来料的均质性及机具的周期变化,适时的察验,才不会跳脱质量的规范.高低针样例:(DoRaMi)18.结合自动化落料:除多数料带是卷收外,有多数散装的端子或五金壳件,都必须考虑在高速冲压中考虑落料收集的确实性.一般有自由落体,踢料杆采用,空气的吹移吸引,斜落,二次机具剥除,弹性体的弹出.在低速加工中,可采机构拨杆,吸盘手,磁性手,机构推移---等模具机构自动化来配合作动.>35度斜落方式空气吹出落料方式样例:19.有关顺送不良:料带在模具中进给,其顺送性是影响冲压S.P.M的要因之一,必将阻碍消除或至碰触的平滑性提高.所以1.浮料的高度和平衡性2.浮升具的型式3.成品形态的进给方向4.料带厚度强度是否易于传送5.送料的幅长6.多料带的几何变化7.导板的滑动间隙高度8.定位导引具的脱离性9.跳屑10.扇形11.模具安装正确的定位12.来料的平整性.13.空站设置的搭配14.来自送料机段的不良15.送料高度调整16.定位销的确实定位17.V-Cut深度18.寸动的进给速度控制及辅助调整---等都是设计前及遭遇顺送不良可改善的空间.送料方向易干涉较滑顺Layout方式样例:送料机&模具歪斜送料机床台料带未到定位最佳定位定位关系:问题与讨论:冲压常见不良因素及参考解决法准备事项:1.时数:6小时(依讲师授课补充添加时数)1.~9.(有关冲剪部份)/3Hr.10.~19.(有关弯曲部份)/3Hr.2.教材:端子,料带,五金壳件,钨钢冲头,剥板入块,下模入块,(轻便模具一组),雷射笔,其他.内容大纲:前言:1.跳屑:2.偏摆:3.冲头研削方向:4.切边的必要性:5.细,圆孔之阻塞:6.尖角不良:7.粉屑:8.压伤:9.翘曲:10.擦伤:11.弯曲变形:12.剪切方向对弯曲裂痕之影响:13.弯曲回弹:14:预镀材较佳之成型R:15.送料不准&误送:16.扇形:17.高低针:18.结合自动化落料:19.有关顺送不良:问题与讨论:前言:在产品类别日益增多的情况下,随着制造公差的细小,有着违反冲切特性,料料特性的挑战,在满足客户需求的基本前提下,冲压加工在其高速量产的本务上,工程中人,事,地,物,机具,管理等的种种差异与变化,使得延生出许多无奇不有的技术障碍,随着冲压团队经验的累积,对较严重且易发生的变因以能对其根本掌握并加以控制,此将针对模具生产部份所生之不良付诸文字,其列举之例并非以篇盖全,技术之渊至深广仍需团队诸君共同努力研究.希望藉由讲述者的深入说明,得以加速了解冲压特性.不仅有技术的授予,更有理念的传承.1.跳屑:由于高速冲切时,冲头吃入材料,造成冲头端部与材料间呈真空状态,故冲切后料片随之吸附跳出模穴.造成行进间的料带压伤,及变形.其冲切的轮廓形状,间隙,材料特性及厚度,冲切油选用及用量,S.P.M速度,刀口利钝,冲切深度-----等.都是影响跳屑的主要因素.厂内以下模披覆和空气吸引最为常用,另有落料锥度的变化,吹气法,冲头端面变化法,顶料杆设制,下模抓料法,下料轮廓变化法,下模刃口修角法及吃入深度,---等调整法视实务搭配使用.真空吸附油膜沾粘开模跳出跳屑形成样例:下料轮廓改变披覆法倒锥度阶级孔&抓料钩.修R弧下模变化防跳屑法举例:2.偏摆:细长件在冲切时,因受冲切断面来自的分力影响,使得成品偏移所规范理想的中心线,其受异物压挤亦会造成偏摆之不良.在弯曲工程中,针长扭转,弯曲成形冲头与下模不对称,亦会造成弯曲后成品的偏摆.一般就藉其特性,施以打点,斜面,设计补正等调整措施来控制.DETAIL“A”调整杆斜面调整打点挤塑调整偏摆不良例&调整法:4.切边之必要性:由于卷材系由呀压延后裁分所需之宽度尺寸,故卷材之边侧留存较不均的应力及毛边,随冲压工站的传送及冲压处的不平均,导致应力随之释放,使得料带受力变形.另因铜材搬运和堆栈的方式,材料边际会受外力碰撞些许变形;分条裁切之直线性亦会受材料特性差异的影响,所以在确保连续模制品均质性和顺送的考虑,会施以适当之切边工站.5.细·圆孔之阻塞:由于落料路径的不顺畅,造成废屑屯塞,迭挤堵住落料口,经下料次数的增多,反作用力终将冲头挤压造成挫屈断裂.其下模1.落料斜度大小2.刃口直线部的长短3.背板模座逃孔的大小4.切削油的粘度5.冲剪的轮廓6.落料过度翻转,---等,均影响落料的难易.小圆孔塞阻原因示意图:Air吸引Air吹入刃部卡料保持2~3t逃孔offset<1mm/side,或刃部下4~6’斜度.逃孔尽大面粗度佳刃部过长孔位置偏移逃孔过大,易翻转油膜黏滞不良例较佳例7.粉屑:在冲压过程中,因模具,材料,机具特性的不协调导致在高速的冲切中,材料受摩擦延伸有刮,搓,挫,压,磨,---等破坏.使料带边际,表面,毛边,晶粒,镀层,---等,受力脱离,由于体积细微,在长期的冲压中积累,不管是对模具寿命,成品尺寸外观和电镀功能性都是严重的致命伤.常见原因有1.冲剪间隙不当2.弯曲冲子下模角隅无消除3.过切重复切刀口模摩擦4.毛边过大5.穿越间隙过小6.刀具加工痕及面粗度7.弯曲间隙擦光8.导位销刮磨9.材料硬度10.模具本身零件摩擦剥落11.导套铝屑,----等.毛头的产生:8.压伤:因模具零件的安装不当,或异物,零件干涉所造成料带表面破坏成品外观上的不良.常见的有1.冲子未让位2.跳屑,模具脏污3.冲子下模长度错误4.角隅无消除5.模仁面粗糙6.扇形,来料不良7.送料段干涉不良8.模具合模线中的干涉8.模具零件的崩落---等造成原因.操作者必须依实际料条不良情况,对照上述等假设变因,逐样于以彻底修除.9.翘曲:料带经冲切成形后所造成之本体的弯曲现象.其造成的原因除冲切成形不平衡应力导致桡度外,其卷材包装造成的弹性疲乏,切边的有无,送料的平顺性,材料本身的内应力大小,均质性等.都是影响的要因.除模具设置的调整站外,辗平机的使用,料带Layout的强度,空站的设置,浮升具与剥板的配合,物料搬运的稳定性及存放,---都有其改善的空间.10.擦伤:材料或成品在成形过程中,受模仁摩擦所造成之表面之损伤.另铜材氧化的判别亦需注意.常见有1.直角弯曲间隙过小2.接触R弧过小3.面粗度不佳4.摩擦面过长过大5.润滑不当,模具精度不佳6.S.P.M 的速度,行程速度的等速性7.模仁加工对称度不佳8.调整杆斜面角度9.料片成形中的滑移10.冲床下死点精度不良---等均会造成.所以必视产品的要求性,及后加工性质,在变项中加以控制及优化.11.弯曲变形:由于材料本身大小,厚度,形状等特性的不同,在不同位置的弯曲成形在线做功,加上成形模仁设计的不适当,延伸出成形的困难性,造成无法全达到我们预设的永久变形.常见有细长件的偏摆,细窄边缘的折弯,折法籣,摩擦干涉,流动不良的成形弯曲,都可因为模具及成行条件的不良造成,由其在成形条件无法覆盖料材内应变时,不均匀的弹性变形就会产生.力的分布图断面变形凸变部弯前切除补正弯曲变形:下死点精度:较佳例倾斜例晃动例R1=R2翘曲变形下死点不良或位置度不准.\V形直线部的不等长及弯曲.身长的弯曲及变形.不良成品:弯曲不良图示:弯曲偏摆:位置度确保12.剪切方向对弯曲裂痕之影响:料片剪切面及撕裂面在弯曲侧的不同,裂痕产生的可能性亦有所高低,当R/T值不变时,光滑的剪切光泽面于外拉伸侧,边际较不会产生裂痕,反之则裂痕易从粗糙的撕裂面顺隙产生裂痕,影响成品强度.另在材料压延方向(Goodway&Badway),对弯曲裂痕影响更大.所以在功能性要求高的弯曲处,要考虑是否超越其最小弯曲R.剪切面方向与裂痕:裂痕光泽带于外侧撕裂面于外侧GoodwayBadway压延方向与最小弯曲R:13.弯曲回弹:材料弯曲成形后,当外力消除后,材料本身的弹性变形会导致成形夹角会外弹变大;其R/T,材质,冲床吨数及弯曲型式都会对回弹角度的值有所影响.除倚靠经验值及缩小R补正外,还会采用偏移中心二次弯折,压折线,角隅逃逸,折弯R弧浮凸,冲头接触面逃逸和运用调整杆,侧滑块等加以运用控制.回弹最大角正常角过弯角冲头加压力(位置)弹性角度变化弯曲弹性变化:冲头过弯让位角隅加压强力托盘防止回弹例举:14.预镀材较佳之成形R:依产品的功能性不同,会使用以完成电镀的料材,因镀附材的特性和基材的特性有异,外观亦较细致光亮,故较剧烈的成形及过小的成形R,都是造成成形过程中路径不滑顺,而导致摩擦力过高伤害表面镀层,降低其电气特性.常施以钳工抛光,加大R,增加工站来于以优化.附图为较佳之参考值.弯曲造成之摩擦:。
五金连续冲模常见不良及其改善措施

五金连续冲模常见不良及其改善措施一、冲裁中常见不良(一)跳屑1.跳屑的几种情况:(1)切边时的跳屑:原因:系不完整的冲孔废料难以有效卡在模仁里,故易跳屑。
改善措施:修边结构复杂化。
(2)小方孔,小圆孔跳屑:原因:a、间隙太大b、有较多的油c、料太薄改善措施:a、收紧间隙b、减少用油c、加向下吹气,在废料下面形成负压d、设变模仁加工方式(改为PG加工),提高刃口段光洁度e、对冲子结构作重新设计f、对铁材产品模具备品须退磁干净(3)细小废屑:(常见于有撕破的模具,有重切时尤为时显,821-220模)(4)大片废屑的跳屑原因:同(2)改善措施:a、加顶杆b、加吹气c、对其形状复杂化(和carry相连一侧)(5)其他状况的跳屑:原因:工序排配设计不合理。
改善措施:重新调整工序排配(重新设计接刀)2.跳屑的危害(1)产生模痕,压伤等不良(2)对间歇性跳屑,不易发现,极易流出不良品。
(3)维修不易(常采用异性冲子,刃口披覆等有损备品寿命和产品断面质量的方式)致生产效率和稼动率低(4)不良品产生时常需要大量的人工进行挑选(二)金属丝危害1、组装成成品后,极易造成短路(short),是要绝对禁止的严重一种不良2、脱落时易在产品上产生模痕3、当有发生时须耗费大量的人力对其重工产生原因常见于有撕破的模具,比如:1、先向下撕破,后又被向上拍平,撕破切口处产生二次挤压,形成金属丝2、先向一个方向撕破后又向相反方向折弯成形3、一次撕破折弯不到位时,让设计不合理改善措施1、撕破处后面工站闪开(放电)避免撕破和被反复拍打。
(抽引毛坯的准备)2、对抽引,有撕破准备毛坯的后面各工站,均应闪开撕破缝隙处,或是重新对carry进行设计,以改善其变形,防止接缝段太长。
3、撕破方向应和后续**进行的成形方向一致,能采用一次撕破折弯成形方案的要尽可能采用。
4、在撕破处须进行二次forming,要合理设计穿过缝隙的冲子和模仁与撕破口间的间隙>0.02(三)冲子蹦根源:结构设计不合理1、直刀面太长为(大于10mm)2、该用PG加工(光学研磨)的未用,由于压板槽的影响,使用强度大大削弱(820-380N1)3、采用PG加工时结构设计不合理,PG槽对其削弱很多,822-173U形冲子4、弧量的部分太过细长5、太过细小冲子的导向段送样不合理(入子加工方式不好)改善措施:1、PG加工的冲子直刀面应小于10mm2、长*宽<3*3者应采用PG加工方式来设计和加工3、对大多数改U形结构冲子来讲,尽量采用PG加工,也应采用分体式结构,以尽量减小对其强度的削弱。
大总结!模板工程十六大通病分析及防治措施!

大总结!模板工程十六大通病分析及防治措施!一、轴线位移1、混凝土浇筑后拆除模板时,发现墙柱实际位置与建筑物轴线位置有偏移。
图片原因1、翻样不认真或技术交底不清。
2、轴线测放时产生误差。
3、模板安装加固不牢固,发生偏移后未能及时校正,造成累积误差。
4、模板安装时未拉水平、竖向通线进行控。
5、模板自身刚度差。
6、混凝土浇筑时未对称均匀下料,或一次浇筑高度过高造成侧压力过大挤压模板变形。
7、对啦螺栓、顶撑使用不当或松动造成轴线偏移。
防治措施1、施工前必须进行熟悉图纸、技术交底、模板放样。
2、轴线测放后必须进行复核。
3、墙柱模板根部和顶部必须设置可靠的限位措施并加固牢固,保证位置准确。
4、支模前要啦水平、竖向通线,保证模板水平、竖向位置准确。
5、根据结构特点,对模板进行设计,以保证模板及其支撑体系具有足够的强度、刚度和稳定性。
6、浇筑混凝土前仔细检查,发现问题及时处理。
7、浇筑混凝土时要对称下料,严格控制下料高度。
二、上下层墙柱接茬处错台1、楼梯间剪力墙及楼层层间接槎较大,漏浆严重。
图片防治措施在楼层间模板上采用上部配长50cm,并在层间向下有一道对拉螺栓为标准。
拆模时保留此外模板与上部墙外模拼接。
;另在下层接缝处用密封泡沫粘嵌条嵌实以防止漏浆剪力墙楼梯支模示意图外墙模板层间节点详图三、结构变形1、拆模后发现混凝土柱、梁、墙出现鼓凸、缩颈或翘曲现象。
图片柱上部变形楼梯踏步板变形原因1、支撑及围檩间距过大,模板刚度差。
连接件末按规定设置,造成模板整体性差。
2、对拉螺栓或螺栓间距过大,螺栓规格过小。
3、竖向支撑过少。
4、砼浇筑墙、柱混凝土速度过快,一次浇灌高度过高,振捣过度。
防治措施1、严格按方案施工,控制立杆及剪刀撑间距,保证模板刚度和稳定性。
排架间距必须符合施工方案,一般在800-900,底层必须加连杆和扫地杆(扫地杆可一隔一设置)。
2、梁底加设支撑确保稳固。
3、墙柱模板设置足够的对啦螺杆或包箍。
4、浇捣混凝土时要均匀对称下浆,严格控制浇灌高度,特别是门窗洞口模板两侧,既要保证混凝土振捣密实,又要防止过分振捣引起模板变形。
连续冲模常见的模具设计缺陷

连续冲模常见的模具设计缺陷引言连续冲模是一种常见的模具类型,广泛应用于汽车零部件、电子产品、家电和医疗器械等制造行业。
然而,由于设计不当或缺陷,连续冲模可能会导致产品质量不稳定、生产效率低下甚至模具损坏等问题。
本文将讨论连接冲模的常见设计缺陷及其对模具性能和产品质量的影响,并提供相应的解决方案。
1. 模腔设计缺陷1.1 腔型结构不合理在连续冲模的模具设计中,腔型结构的设计是至关重要的。
不合理的腔型结构可能导致产品成形精度低、变形、裂纹等问题。
常见的腔型设计缺陷包括: - 壁厚不均匀:不合理的壁厚分布会导致金属在冲击过程中的流动不均匀,影响产品的成形精度。
- 毛刺和划痕:腔型表面的毛刺和划痕会在冲压过程中留下痕迹,降低产品表面质量。
- 冲裁不良:腔型设计不当可能导致冲裁不完全或边缘残留,影响产品的结构完整性。
解决方案: - 合理设计腔型结构,确保壁厚分布均匀,避免毛刺和划痕。
- 使用高硬度、高耐磨损的材料制作模具,提高模具的使用寿命。
- 定期检查模具,及时修复或更换受损的部件。
1.2 腔型温度控制不当连续冲模的腔型温度对产品成形质量有着重要影响。
腔型温度过高或过低都会导致产品尺寸不稳定、变形等问题。
常见的腔型温度控制缺陷包括: - 温度不均匀:腔型温度不均匀会导致产品在冷却过程中出现温度差异,从而影响成形质量。
- 温度过高:过高的腔型温度会导致产品热胀冷缩不均匀,引起尺寸变化和变形。
- 温度过低:过低的腔型温度会导致产品冷却速度过快,增加应力和残余应力,容易导致开裂或收缩不均。
解决方案: - 使用合适的冷却系统,确保腔型温度均匀,并进行及时调整。
-使用温度传感器对腔型温度进行监控,及时调整冷却系统的工作状态。
- 对于过高或过低的腔型温度,适当调整冲压参数,控制冲压速度和冷却速度。
2. 引导部件设计缺陷连续冲模的引导部件设计是确保模具正常运行的关键。
不合理的引导部件设计可能导致模具寿命短、生产效率低下等问题。
连续冲模常见的模具设计缺陷
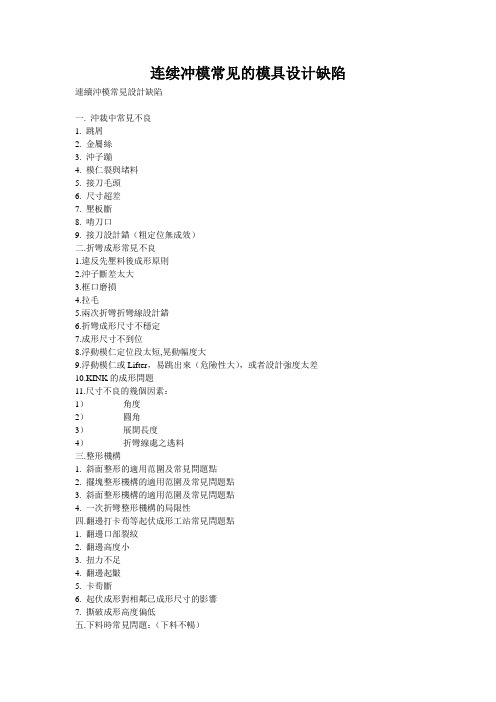
连续冲模常见的模具设计缺陷連續沖模常見設計缺陷一. 沖裁中常見不良1. 跳屑2. 金屬絲3. 沖子蹦4. 模仁裂與堵料5. 接刀毛頭6. 尺寸超差7. 壓板斷8. 啃刀口9. 接刀設計錯(粗定位無成效)二.折彎成形常見不良1.違反先壓料後成形原則2.沖子斷差太大3.框口磨損4.拉毛5.兩次折彎折彎線設計錯6.折彎成形尺寸不穩定7.成形尺寸不到位8.浮動模仁定位段太短,晃動幅度大9.浮動模仁或Lifter,易跳出來(危險性大),或者設計強度太差10.KINK的成形問題11.尺寸不良的幾個因素:1)角度2)圓角3)展開長度4)折彎線處之逃料三.整形機構1. 斜面整形的適用范圍及常見問題點2. 擺塊整形機構的適用范圍及常見問題點3. 斜面整形機構的適用范圍及常見問題點4. 一次折彎整形機構的局限性四.翻邊打卡荀等起伏成形工站常見問題點1. 翻邊口部裂紋2. 翻邊高度小3. 扭力不足4. 翻邊起皺5. 卡荀斷6. 起伏成形對相鄰已成形尺寸的影響7. 撕破成形高度偏低五.下料時常見問題:(下料不暢)1. 廢料留在模面(821-762N1)2. 下料不暢,加吹氣,頂桿3. 混料4. 下產品改為下廢料(吹氣方式)六.抽引中常見問題點1. 毛坯太大2. 毛坯太小3. 抽引拉裂4. 抽引起皺5. 壁部拉毛6. Carry相互擠壓7. 定位不可靠8. 大肚子七.結構設計中常見問題:1. 定位針固定在沖子固定板上2. 剝料套設計不良3. 料條定位不行(追加導板)4. 壓板,彈簧斷裂(改沖子固定方式)5. 背板螺絲太靠外6. 抽引第一抽不分開7. 缺少整形工站8. 定位針太少,太細9. Lifter無爬坡(模仁太短)八.料條設計問題:1. 剛性太差2. 前後工序排配不合理3. 粗定位無效4. 定位針孔太靠後九.幾種常見的典型機構十.其它常見問題:1. 大平面的平面度問題2. SMT PAD的共面度問題3. 鉚合中的一些問題及解決措施4. 料帶式產品的扇形(波浪形)第一章沖裁中常見不良一.跳屑一)跳屑的幾種情況:1.切邊時的跳屑:缘故:系不完整的沖孔廢料難以有效卡在模仁裡,故易跳屑改善措施:修邊結構復雜化2.小方孔,小圓孔跳屑缘故:1)間隙太大2)有較多的油3)料太薄改善措施:1)收緊間隙2)減少用油3)加向下吹氣,在廢料下面形成負壓4)設變模仁加工方式(改為PG加工),提高刃口段光潔度5)對沖子結構作重新設計6)對鐵材產品模具備品須退磁幹凈)3.細小廢屑:(常見於有撕破的模具,有重切時尤為時顯,821-220模)4.大片廢屑的跳屑缘故: 同2改善措施:1)加頂桿2)加吹氣3)對其形狀復雜化(和carry相連一側)5.其它狀況的跳屑:缘故:工序排配設計不合理改善措施:重新調整工序排配(重新設計接刀)二)跳屑的危害:1.產生模痕,壓傷等不良2.對間歇性跳屑,不易發現,極易流出不良品3.維修不易(常採用異形沖子,刃口披覆等有損備品壽命和產品斷面質量的方式)致生產效率和稼動率低4.不良品產生時常需大量的人工進行挑選二.金屬絲一)危害:1.組裝成成品後,極易造成短路(SHORT),是要絕對禁止的嚴重一種不良2.脫落時易在產品上產生模痕3.當有發生時須耗費大量的人力對其重工二)產出缘故:常見於有撕破的模具,比如:1.先向下撕破,後又被向上拍平,撕破切口處產生二次擠壓,形成金屬絲2.先向一個方向撕破後又向相反方向折彎成形3.一次撕破折彎不到位時,讓設計不合理三)改善措施:1.撕破處後面工站閃開(放電)幸免撕破和被反復拍打。
冲压件产生连续模缺口的原因

冲压件产生连续模缺口的原因
其次,操作方面的原因也可能导致冲压件产生连续模缺口。
比如,操作人员在使用模具时操作不当或者使用过程中出现异常情况
未及时处理,都可能导致模具受到损坏而产生连续模缺口。
另外,原材料的质量问题也是产生连续模缺口的一个可能原因。
如果原材料的硬度、强度或者表面质量不符合要求,那么在冲压过
程中就会对模具造成损坏,从而产生连续模缺口。
此外,冲压过程中的工艺参数设置不当也可能导致连续模缺口
的产生。
比如,冲床的调节不当、冲头的选择不合适、冲压速度过
快或者过慢,都可能对模具造成损坏而产生连续模缺口。
综上所述,冲压件产生连续模缺口的原因可能涉及模具设计、
制造、操作、原材料质量以及工艺参数等多个方面。
要解决这个问题,需要综合考虑以上各个方面的因素,进行全面的分析和改进。
10、连续模折弯时产品变形或尺寸变异的原因是什么,应采取什么对策?

10、连续模折弯时产品变形或尺寸变异的原因是什么,应采取什
么对策?
10、连续模折弯时产品变形或尺寸变异的原因是什么,应采取什么对策?
连续模折弯时产品变形或尺寸变异的原因及相应的对策有:
1) 导正销磨损,销径不足,更换导正销;
2) 折弯导位部分精度差磨损,重新研磨或更换;
3) 折弯凸凹模磨损(压损),重新研磨或更换;
4) 模具让位不足,检查,修正;
5) 材料滑移,折弯凸凹模无导位功能,折弯时未施以预压,可以修改设计,增设导位及预压功能;
6) 模具结构及设计尺寸不良,可以采用修改设计尺寸,分解折弯,增加折弯整形等措施;
7) 冲件毛边,引发折弯不良时需研修下料位刀口时;
8) 折弯部位凸模凹模加设垫片较多,造成尺寸不稳定,需调整采用整体钢垫;
9) 材料厚度尺寸或机械性能变异时需更换材料,控制进料质量;。
浅谈模板缺陷产生的原因及防治措施

浅谈模板缺陷产生的原因及防治措施础、梁、柱、楼梯、墙五个部位的模板工程容易出现的问题进行了总结,并提出了防治措施,以提高模板工程的施工质量,从而保证现浇结构的工程质量。
标签模板;缺陷;原因;措施在现浇混凝土结构施工中,模板工程是一项比较重要的分项工程,模板工程的好坏直接关系到现浇结构施工质量的优劣。
根据多年施工总结,下面就模板在基础、梁、柱、墙、楼梯等部位的施工容易出现的缺陷及防治措施作个介绍。
1、基础模板缺陷1. 1 现象1)条形基础模板长度方向上口不直,宽度不一;2)杯形基础中心线位置不准,芯模在浇筑混凝土时上浮或侧向偏移,芯模难拆除;3)上阶侧模下口陷入混凝土内,拆模后产生“烂脖子”;4)侧向胀模、松动、脱落。
1. 2 原因分析1)条形基础模板拼接处的上口不在同一条直线上;模板上口未设定位支撑,支撑围檩刚度不足,在混凝土侧压力下向外位移(俗称胀模)。
2)杯形基础中心线弹线不规方,芯模的拼装或外表面处理不当,芯模底板不透气,芯模四周混凝土浇捣不同步,造成芯模上浮或侧移;拆模时间超过混凝土终凝时间,造成芯模难拆除。
3)上阶侧模未撑牢,下口未设置钢筋支架或混凝土垫块,脚手板直接搁置在模板上,造成上阶侧模下口陷入混凝土内,拆模后上台阶根部产生“烂脖子”。
1. 3 防治措施1)条形基础支模,通长拉线并挂线找准,以保证模板上口垂直。
上口应定位,以控制条形基础上口宽度。
2)杯形基础支模前,复查地基垫层标高及中心线位置;弹出基础四面边线并进行复核,用水平仪测定标高,依线支设模板;木芯模要刨光直拼,芯模侧板应包底板;底板应钻孔以便排气,芯模外壳应涂刷脱模剂,上口要临时遮盖;采用组合钢模板时应按照杯口底尺寸,在四边模中间通过楔板用M12 螺栓连接、拧紧,组合成杯口模板,内侧设一道水平支撑以增加刚度,防止浇筑混凝土时芯模位移;采用芯模无底板时,杯口底面标高应比设计标高低20 mm~50 mm,拆模后立即将浇捣时翻上的混凝土找平至柱底标高。
模板工程常见质量通病
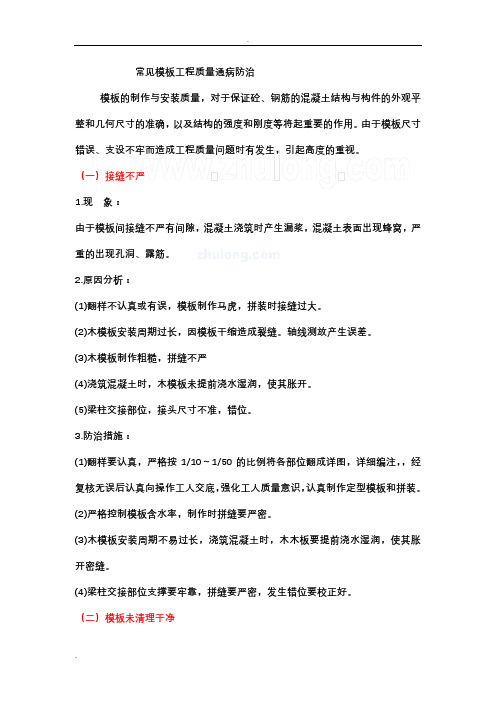
常见模板工程质量通病防治模板的制作与安装质量,对于保证砼、钢筋的混凝土结构与构件的外观平整和几何尺寸的准确,以及结构的强度和刚度等将起重要的作用。
由于模板尺寸错误、支设不牢而造成工程质量问题时有发生,引起高度的重视。
(一)接缝不严1.现象:由于模板间接缝不严有间隙,混凝土浇筑时产生漏浆,混凝土表面出现蜂窝,严重的出现孔洞、露筋。
2.原因分析:(1)翻样不认真或有误,模板制作马虎,拼装时接缝过大。
(2)木模板安装周期过长,因模板干缩造成裂缝。
轴线测放产生误差。
(3)木模板制作粗糙,拼缝不严(4)浇筑混凝土时,木模板未提前浇水湿润,使其胀开。
(5)梁柱交接部位,接头尺寸不准,错位。
3.防治措施:(1)翻样要认真,严格按1/10~1/50的比例将各部位翻成详图,详细编注,,经复核无误后认真向操作工人交底,强化工人质量意识,认真制作定型模板和拼装。
(2)严格控制模板含水率,制作时拼缝要严密。
(3)木模板安装周期不易过长,浇筑混凝土时,木木板要提前浇水湿润,使其胀开密缝。
(4)梁柱交接部位支撑要牢靠,拼缝要严密,发生错位要校正好。
(二)模板未清理干净1.现象:(1)模板内残留木块、浮浆残渣、碎石等建筑垃圾,拆模后发现混凝土中有缝隙,且有垃圾夹杂物。
(2)模板内残留木块、浮浆残渣、碎石等建筑垃圾,拆模后发现砼有缝隙,且有垃圾杂物。
2.原因分析:(1)钢筋绑扎完毕,未用压力水冲洗模板,封模前未进行清扫。
(2)墙柱根部,梁柱接头最低处未留清扫孔,或所留位置不当无法进行清扫。
3.防治措施:(1)钢筋绑扎完毕,用高压水冲洗模板,清除模内垃圾。
(2)封模前派专人清扫模内垃圾。
(3)墙柱根部、梁柱接头处预留清扫孔,预留孔尺寸≥100mm*100mm,模内垃圾清除完毕后及时封严清扫口。
(三)柱模板缺陷1.现象(1)炸模,造成截面尺寸不准,鼓出、漏浆,混凝土不密实或蜂窝麻面。
(2)偏斜,一排柱子不在同一轴线上(3)柱身扭曲,梁柱接头处偏差大。
10、连续模折弯时产品变形或尺寸变异的原因是什么,应采取什么对策?
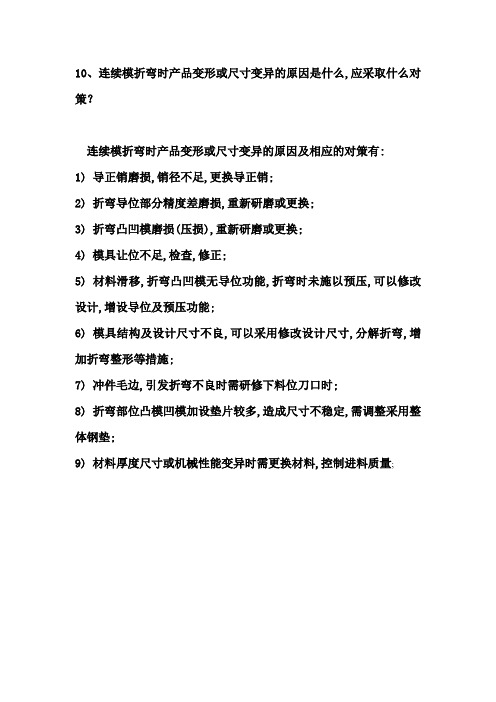
10、连续模折弯时产品变形或尺寸变异的原因是什么,应采取什么对策?
连续模折弯时产品变形或尺寸变异的原因及相应的对策有:
1) 导正销磨损,销径不足,更换导正销;
2) 折弯导位部分精度差磨损,重新研磨或更换;
3) 折弯凸凹模磨损(压损),重新研磨或更换;
4) 模具让位不足,检查,修正;
5) 材料滑移,折弯凸凹模无导位功能,折弯时未施以预压,可以修改设计,增设导位及预压功能;
6) 模具结构及设计尺寸不良,可以采用修改设计尺寸,分解折弯,增加折弯整形等措施;
7) 冲件毛边,引发折弯不良时需研修下料位刀口时;
8) 折弯部位凸模凹模加设垫片较多,造成尺寸不稳定,需调整采用整体钢垫;
9) 材料厚度尺寸或机械性能变异时需更换材料,控制进料质量;。
常见模具缺陷及解决办法

7)孔变形 判断方法:用眼睛看。 原因:冲头磨损。 处理办法:轻微的打油,严重的打油仍出现变形的应报告班长,通知修模
8)拉深不到位 判断方法:看压力点是否清晰。 原因:主压力偏小。 处理办法:适当调高
9)折边不良 判断方法:与样件比较 原因:件没摆好,定位装置问题。 应向班长报告,通知模修人员修模。
五、模具缺陷的分析和解决措施 1)凸模磨损太快 主要原因:①模具间隙偏小,一般建议模具总间隙为材 具的对中性不好,包括模座和模具导向组件及转塔镶套精度不足等原因造 过高,主要是由于同一模具连续长时间冲压造成冲头过热。④模具刃磨方 剧。⑤局部的单边冲切,如步冲、冲角或剪切时,侧向力会使冲头偏向一 磨损严重,如果机床模具安装精度不高,严重的会使冲头偏过下模,造成 (2)模具带料问题 模具带料会造成废料反弹,其相关因素:①模具刃口 越容易造成废料反弹。②模具的入模量,机床每个工位的入模量是一定的 反弹。③模具的间隙是否合理,如果模具间隙不合适,容易造成废料反弹 多的油物。⑤弹簧疲劳损坏。 防止模具带料的方法:①使用专用的防带料 利,并退磁处理。③增大凹模间隙。④采用斜刃口模具代替平刃口模具。 模具的入模量。⑦检查模具弹簧或卸料套的疲劳强度。 (3)模具对中性问题 模具在使用中容易发生冲芯各侧位置的磨损量不同 快,这种情况在细窄的长方模具上特别明显。该问题主要原因:①机床转 上下转盘的模具安装座的对中性不好。②模具的设计或加工精度不能满足 够。④模具间隙选择不合适。⑤模具安装座或模具导套由于长期使用磨损 磨损不一致,应:①定期采用对中芯棒对机床转塔和安装座进行对中性检 选用合适间隙的凸凹模具。③采用全导程模具。④加强操作人员的责任心 成更大损失。 (4)特殊成形模具使用 为满足生产需要,经常需要使用成形模具或特殊 窗模具、沉孔形模具、翻孔攻螺纹模具、凸台模具、拉伸模具、组合式模 大大提高生产效率,但是成形模具价格较高,通常是普通模具的 原则: ①模具安装时进行方向检查,确保模具凸凹模安装方向一致。 度,每次调整最好不超过0.15mm。 ③使用较低的冲切速度。 工位置应尽量远离夹钳。 ⑥成形模具使用时应避免向下成形操作。 使用成形模具。
- 1、下载文档前请自行甄别文档内容的完整性,平台不提供额外的编辑、内容补充、找答案等附加服务。
- 2、"仅部分预览"的文档,不可在线预览部分如存在完整性等问题,可反馈申请退款(可完整预览的文档不适用该条件!)。
- 3、如文档侵犯您的权益,请联系客服反馈,我们会尽快为您处理(人工客服工作时间:9:00-18:30)。
连续模常见的设计缺陷一. 冲裁中常见不良1. 跳屑2. 金属丝3. 冲子蹦4. 模仁裂与堵料5. 接刀毛头6. 尺寸超差7. 压板断8. 啃刀口9. 接刀设计错(粗定位无效果)二.折弯成形常见不良1.违反先压料后成形原则2.冲子断差太大3.框口磨损4.拉毛5.两次折弯折弯线设计错6.折弯成形尺寸不稳定7.成形尺寸不到位8.浮动模仁定位段太短,晃动幅度大9.浮动模仁或Lifter,易跳出来(危险性大),或者设计强度太差10.KINK的成形问题11.尺寸不良的几个因素:1)角度2)圆角3)展开长度4)折弯线处之逃料三.整形机构1. 斜面整形的适用范围及常见问题点2. 摆块整形机构的适用范围及常见问题点3. 斜面整形机构的适用范围及常见问题点4. 一次折弯整形机构的局限性四.翻边打卡荀等起伏成形工站常见问题点1. 翻边口部裂纹2. 翻边高度小3. 扭力不足4. 翻边起皱5. 卡荀断6. 起伏成形对相邻已成形尺寸的影响7. 撕破成形高度偏低五.下料时常见问题:(下料不畅)1. 废料留在模面(821-762N1)2. 下料不畅,加吹气,顶杆3. 混料4. 下产品改为下废料(吹气方式)六.抽引中常见问题点1. 毛坯太大2. 毛坯太小3. 抽引拉裂4. 抽引起皱5. 壁部拉毛6. Carry相互挤压7. 定位不可靠8. 大肚子七.结构设计中常见问题:1. 定位针固定在冲子固定板上2. 剥料套设计不良3. 料条定位不好(追加导板)4. 压板,弹簧断裂(改冲子固定方式)5. 背板螺丝太靠外6. 抽引第一抽不分开7. 缺少整形工站8. 定位针太少,太细9. Lifter无爬坡(模仁太短)八.料条设计问题:1. 刚性太差2. 前后工序排配不合理3. 粗定位无效4. 定位针孔太靠后九.几种常见的典型机构十.其它常见问题:1. 大平面的平面度问题2. SMT PAD的共面度问题3. 铆合中的一些问题及解决措施4. 料带式产品的扇形(波浪形)第一章冲裁中常见不良一.跳屑一)跳屑的几种情况:1.切边时的跳屑:原因:系不完整的冲孔废料难以有效卡在模仁里,故易跳屑改善措施:修边结构复杂化2.小方孔,小圆孔跳屑原因:1)间隙太大2)有较多的油3)料太薄改善措施:1)收紧间隙2)减少用油3)加向下吹气,在废料下面形成负压4)设变模仁加工方式(改为PG加工),提高刃口段光洁度5)对冲子结构作重新设计6)对铁材产品模具备品须退磁干凈)3.细小废屑:(常见于有撕破的模具,有重切时尤为时显,821-220模)4.大片废屑的跳屑原因: 同2改善措施:1)加顶杆2)加吹气3)对其形状复杂化(和carry相连一侧)5.其它状况的跳屑:原因:工序排配设计不合理改善措施:重新调整工序排配(重新设计接刀)二)跳屑的危害:1.产生模痕,压伤等不良2.对间歇性跳屑,不易发现,极易流出不良品3.维修不易(常采用异形冲子,刃口披覆等有损备品寿命和产品断面质量的方式)致生产效率和稼动率低4.不良品产生时常需大量的人工进行挑选二.金属丝一)危害:1.组装成成品后,极易造成短路(SHORT),是要绝对禁止的严重一种不良2.脱落时易在产品上产生模痕3.当有发生时须耗费大量的人力对其重工二)产出原因:常见于有撕破的模具,比如:1.先向下撕破,后又被向上拍平,撕破切口处产生二次挤压,形成金属丝2.先向一个方向撕破后又向相反方向折弯成形3.一次撕破折弯不到位时,让设计不合理三)改善措施:1.撕破处后面工站闪开(放电)避免撕破和被反复拍打。
(抽引毛坯的准备)2.对抽引,有撕破准备毛坯的后面各工站,均应闪开撕破缝隙处,或是重新对carry进行设计,以改善其变形,防止接缝段太长。
3.撕破方向应和后续**进行的成形方向要一致,能采用一次撕破折弯成形方案的要尽可能采用。
4.在撕破处须进行二次forming,要合理设计穿过缝隙的冲子和模仁与撕破口间的间隙>0.02.三.冲子蹦根源:1.结构设计不合理1)直刀面太长为(大于10mm)2)该用PG加工的未用,由于压板槽的影响,使用强度大大削弱(820-380N1)3)采用PG加工时结构设计不合理,PG槽对其削弱很多,822-173 U形冲子4)弧量的部分太过细长5)太过细小冲子之导向段送样不合理(入子加工方式不好)改善措施:1. PG加工之冲子直刀面应小于10mm2. 长*宽<3*3者应采用PG方式来设计和加工3. 对大多改U形结构冲子来讲,尽量采用PG加工,也应采用分体式结构,以尽量减小对其强度的削弱。
分体和整体式加工时的差异:因分体式时可采用垂直于深槽的方向进刀,可减小许多切削量。
4. 当有弧悬的细小部位存在时,1)排样时尽量避免(排样重新考虑)2)无法避免时,应采用PG方式设计5. 当有细长的冲子存在时(<直径1.0时)冲子导向段和工作段应分开(工作段长度应<2.0)(长径比不大于3),其结构如下:五.毛头1. 现象2.原因:1)接刀设计不良:在圆弧顶点或平面上接刀→无2)垂切3)间隙不合理4)冲子模仁材质选择不合理5)刀口保养做得不确实3.改善措施:1)接刀设计不改善2)避免在圆弧顶点或平面上接刀增加工艺逃料(避免垂切)3)采用合理日冲裁间隙4)尽量将冲子和模仁选用不同的材质(冲子V3,则模仁用ASP23或SKD11),反之易可。
六.冲裁的尺寸超差1.原因:1)材料有翻转2)材料有流动3)成形与下料工序排配不当4)打COIN的影响5)打倒角的影响6)下料的侧边的成形设计不合理2. 改善措施:1)对材料作强压(不允压痕者除外2)作限位,防止材料流动3)据试模作修正4)调整成形和下料工序的先后排配(不影响模仁强度的状况下)5)据经验值修正因打COIN,打倒角,而会引起变异的量,0.05~0.10)6)不会引起细小废屑的时候加精切,通常不用)7)后工序段加调整原则:首先使成形尺寸稳定后再修正下料,*七.压板断:(螺丝断)1. 原因:压板不足以承受剥料力,常见设计缺陷:1)大冲子只有一个压板2)压板悬臂太长,A太大,A≦9mm为宜2.改善措施:1)增加压板2)改压板固定冲子为键固定冲子3)改用螺纹吊(Mini Din产品的翻边冲子)八.接刀设计错误:1.粗定位无效果1)A>P+0.22) A<P2. 接刀时垂切3. 精切的量太少4. 接刀的先后顺序反第二章折弯成形常见设计不良一.角度不到位二.表面拉毛三.尺寸不到位四.变形五.尺寸不稳定六.包料一.角度不到位1. 原因分析:1)折弯高度小于最小折弯高度2)间隙不合理3)无整形工站4)压料不确实(弧形)5)框口磨损6)冲子刚性太差7)无后角2. 解决措施:(洽制工,产生更改规格)1)追加整形工站(成二次折弯工站)(斜向,滑块,摆块……)2)调整折弯间隙3)打Coin(允许时)作用:减小料厚===减小最小折弯高度(圆角,料厚)4)改善压料:A.增大Lifter面积B.磨加强筋C.换强力弹簧D.下死点时迭死E.收冲子成形为剥料扳成形(下死点迭死)5)追加模板入子6)下模加冲子挡块7)模仁闪后角二.表面拉毛1. 原因:1)间隙太小2)冲子材质和零件材质存在亲和力3)润滑不良4)冲子表面光洁度不够2. 改善措施:1)调整间隙至0~0.012)改冲子材质(与零件材质有关:WC,B,Tic,C,陶瓷)3)适当加油4)生产试模时抛光冲子表面3. 对镀后成形产品的折弯工序排配建议:1)采用两次折弯成形工艺2)采用折弯加整形工站冲子尽可能的采用嵌件结构4)生产时加油的考虑和种类须严格控制5)冲压工艺难以解决时协商制工产发工程师共同解决三.尺寸不到位:1.原因:1)角度不到位2)展开长度不良3)圆角R尺寸不良4)有变形5)COIN的影响6)折弯线位置不对7)折弯力不够3. 改善措施:1)先修正角度到位2)CHK折弯线位置有无错误3)CHK展开长度4)CHK折弯有无变形5)是否有打COIN(对尺寸是否会造成影响)6)消除以上所有不良之后,再决定是否要修正下料*试模修模小技巧:调整折弯圆角(模仁)可对折弯成形尺寸作一定范围的微调。
7)弹簧力不足以提供折弯力。
(料厚,折弯线长时,尤其明显)有时也采用剥料板成形也不足以到达要求的折弯力(S02A和P01A间有0.10的间隙),可以追加迭死冲子。
四.变形(不包含闪位不够的变形)1. 状况:2. 原因:1)压料不好2)折弯间隙太小(对细小折弯影响很明显)3)折弯冲子断差太大3. 解决措施:1)改善压料2)适当放松间隙(采用二次折弯或加整形工站等使角度到位减小冲子断差至(6+0.05~0.10)<0.5此类改善做得极多,约占以前总改善量的30%断差的作用:1. 下死点时对折弯圆角作整形,增塑性变形,减小回弹2. 方便生产中对折弯间隙作调整,(可位移)五.尺寸不稳定1. 材质有变化2. 折弯线不稳定原因:1=冲子无入子,框口或冲子磨损2=折弯模仁晃动(尤其是浮动折弯模仁)3=浮动折弯模仁定位段短4=浮动模仁或框口磨损解决措施:1=加大模仁,增加定位段2=加入子,沉入下垫板六.包料与折弯裂纹1. 原因:1=折弯模仁圆角小于最小折弯圆角3=折弯角度小于90∘(外侧伸长量大于材料的延伸率)4=材料的性能变异2.模具设计时注意点:1=CHK折弯圆角,是否小于最小折弯圆角2=折弯模仁圆角不能取得过小3=对两次折弯或(一次折弯+整形)中的第一次折弯模仁不要与第二次折弯(或整形模仁作成整体)当料硬度低,折弯圆角小时,第一次折弯极易形包料第一次折弯模仁不闪后角则不会包料七.几种典型折弯整形机构的优缺点:一=斜面整形1. 优点:结构简单,成本低,所需模具空间小2. 缺点:效果有限,同时有如下问题:受力点不在折弯线附近1=产生弧形当折弯面上有孔等其它减其弱度的情形存在时,整形屈服点将不在我们所希望折弯线处,而在最薄弱处2=形成毛头3. 适用范围:1=尺寸与角度要求均不高的埸合2=料厚与折弯线均不大的场合3=折弯高度不大于5mm的场合4. 设计要点:α<20∘L值要合理二=侧推滑块整形1.优点:稳定。
可靠,可将折弯角度整形至小于90∘,在实际设计中适用最广泛的机构2. 缺点:结构复杂,零件多,成本高,占有模具空间大,使用场合受到一定的限制。
3. 适用范围:广泛运用于尺寸和角度要求高或角度要求90∘时折弯整形工站,只要模具结构空间允许,均可大胆采用。
4. 设计要点:1=防止滑块跳出a. 用压板压b. 用导板压c. 用T形槽2=α1<α23=H不能太高,25 OR30厚下模板时最好采用一个垫块4=行程要足够,不能和产品的已成形部分干涉,须L1>L2否则:产品(料条)上行时会和滑块干涉5. 调整量要合适,原则:设计时:调整到最内时,滑块和折弯模仁间的最小间隙应不小于0.5否则:当调整适量时会造成滑块或模仁损坏原文来自:/viewthread.php?tid=22258。