乳化液浓度配比标准作业流程
乳化液配比要求及水质规定
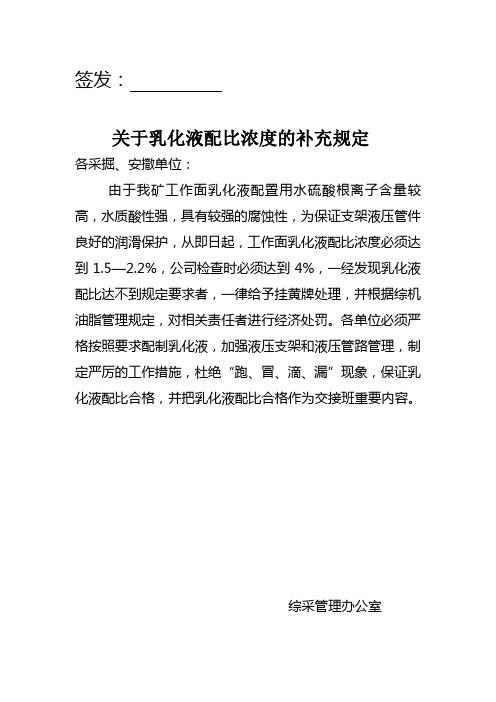
签发:
关于乳化液配比浓度的补充规定
各采掘、安撤单位:
由于我矿工作面乳化液配置用水硫酸根离子含量较高,水质酸性强,具有较强的腐蚀性,为保证支架液压管件良好的润滑保护,从即日起,工作面乳化液配比浓度必须达到1.5—2.2%,公司检查时必须达到4%,一经发现乳化液配比达不到规定要求者,一律给予挂黄牌处理,并根据综机油脂管理规定,对相关责任者进行经济处罚。
各单位必须严格按照要求配制乳化液,加强液压支架和液压管路管理,制定严厉的工作措施,杜绝“跑、冒、滴、漏”现象,保证乳化液配比合格,并把乳化液配比合格作为交接班重要内容。
综采管理办公室
2012年1月6日
关于乳化液配制用水和配比要求的说明
济宁二号煤矿使用的乳化油为ME20-5型乳化油,配比要求达到1.5—2.2%,要求乳化液配置用水是中性或偏碱性,PH值在6—9之间,硫酸根离子含量≤400毫克/升。
经从15301工作面、9301工作面和2308工作面抽取水样化验,其硫酸根离子含量分别达到612.8毫克/升、964.8毫克/升和564.2毫克/升,硫酸根离子含量均超标。
综机管理中心提出水与乳化油的配制质量比不得低于5%的要求。
(1)中性水溶液,pH=-lgaH+=-lg10-7=7
(2)酸性水溶液,Ph<7,pH值越小,表示酸性越强;
(3)碱性水溶液,Ph>7,pH值越大,表示碱性越强。
综采管理办公室2012年1月6日。
2016新编乳化油配比

乳化油配比线切割工作液由专用乳化油与自来水配制而成,有条件采用蒸馏水或磁化水与乳化油配制效果更好,工作液配制的浓度取决于加工工件的厚度、材质及加工精度要求。
从工件厚度来看,厚度小于30mm的薄型工件,工作液浓度在1O%~15%之间;30~lOOmm的中厚型工件,浓度大约在5%~1O%之间;大于1OOmm的厚型工件,浓度大约在3%~5%之间。
从工件材质来看,易于蚀除的材料,如铜、铝等熔点和气化潜热低的材料,可以适当提高工作液浓度,以充分利用放电能量,提高加工效率,但同时也应选较大直径的电极丝进行切割,以利于排屑充分。
从加工精度来看,工作液浓度高,放电间隙小,工件表面粗糙度较好,但不利于排屑,易造成短路。
工作液浓度低时,工件表面粗糙度较差,但利于排屑。
总之,在配制线切割工作液时应根据实际加工的情况,综合考虑以上因素,在保证排屑顺利、加工稳定的前提下,尽量提高加工表面质量。
另外必需注意:在配制乳化液时,如果乳化油自身的流动性和乳化性能好,只要按一定比例将乳化油加入稀释水中,充分搅拌后即可达到乳化状态,得到均匀的乳化液。
但一定要将乳化油加入稀释水中。
如果反其道而行之,将稀释水加入乳化油中,在某些情况下(如温度较低),可能生成胶状物质,很难溶解开。
对于粘度大、甚至呈膏状的乳化油,需要将乳化油加热,或者先使用部分热水冲调,待其充分乳化后再用水稀释至所需浓度。
因为热水可以使乳化油的粘度降低,热水分子有较大的动能,而且热水的表面张力小,有利于乳化油的均匀分散。
如果乳化油自身的乳化性能不够好,应在乳化的初始阶段在不断搅拌下先向乳化油中缓慢地加入少量稀释水,待到乳化油已被充分乳化、变成均匀的乳化液后,再冲调大量的稀释水,并不断搅拌,直至达到所需配制的浓度。
这样做的目的是使其先形成油包水型(W/O)乳状液,在不断搅拌并继续加入稀释水的过程中,使其发生相转变,由W/O型转变为O/W型.这样做虽然费时、费事,但所得到的乳状液颗粒较均匀、细致,乳化液的稳定性较高,可以在一定程度上弥补乳化油本身乳化性能的欠缺。
最新乳化液处理操作规程228
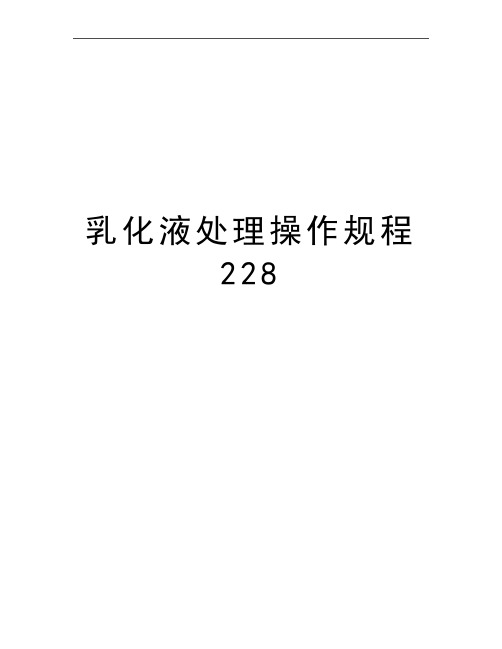
乳化液处理操作规程228中国第一汽车集团公司管理文件综合利用有限公司污水车间乳化液处理操作规程1 简要说明根据污水厂实际条件,本处理系统采用破乳后再用污水厂二级出水进行稀释,并采用混凝、气浮、过滤、吸附等工艺进行处理,出水水质达到污水厂进水指标,然后排入污水厂进口,再进行生化二级处理,出水达到国家二级排放标准。
破乳过程中产生的油由专门的设备收集后,进行回收处理。
由气浮产生的浮渣,进入污泥罐后再用污泥泵提升至污泥浓缩罐,浓缩后的污泥进入污泥脱水机进行脱水,干泥外运。
2 工艺流程2.1废乳化液→乳化液储池→破乳槽→混凝反应器→浮选机→中间水箱→石英砂过滤器→活性炭过滤器→出水从破乳槽产生的浮油用桶收集后,运送到专门的回收方,进行回收处理。
破乳后的高浓度有机废水,进入混凝反应器→气浮→过滤→吸附,产生的泥渣送到污泥脱水机干化处理。
3工艺流程图4 工艺设备及主要性能4.1破乳槽规格:φ6000×5000 型号:YA-E在废乳化液中加入破乳剂氯化钙,使乳化油与水分离。
4.2混凝反应器规格:φ1200×11500 型号:ZLH-600破乳后的乳化液进入混凝反应器,先加入氢氧化钠调节PH,然后再加入聚合氯化铝及聚丙烯酰胺,使水中的悬浮物形成较大絮体,易于去除。
4.3气浮净水装置规格:φ300×11500 型号:QF-150混合反应器出水进入100吨/小时气浮装置,利用气浮原理将水中悬浮物去除。
4.4集水槽规格:φ2500×2500 型号:HY-Ⅱ气浮出水进入集水槽,用来均衡水量。
4.5集油槽规格:φ2500×5000 型号:YA-C破乳槽表面浮油用刮油机刮入集油槽。
然后收集。
4.6污泥槽规格:φ3000×3000 型号:QF-100浮选机表面浮渣进入污泥槽。
用污泥泵输送至污泥处理间处理。
4.7加药装置规格:φ1200×2000 型号:JY-Ⅲ由碱配药箱、加药箱;聚铝配药箱、加药箱;聚丙烯酰胺配药箱、加药箱组成。
乳化液化验操作规程

乳化液化验操作规程1主题内容与适用范围:1.1本规程规定了轧机机组所使用乳化液的化验操作要点。
具体分析项目有:PH、皂化值、酸值、油含量、ESI(稳定系数)、灰份、铁份、氯离子含量。
1.2本规程适用于水处理化验室化验分析。
2术语:2.1 皂化值:油脂在碱存在下水解,水解产生的高级脂肪酸与碱作用生成脂肪酸盐,油脂在碱性溶液中的水解过程叫做皂化。
皂化1g油脂所需要氢氧化钾的毫克数叫做该油脂的皂化值。
2.2 ESI(稳定系数):系指乳化液充分摇匀后一定的体积所含的油量与静止一段时间后分液时下部相同体积液体所含的油量的比值。
3操作规程:3.1 PH的测定方法3.1.1适用范围:本方法适用于乳化液中PH的测定。
3.1.2方法概要:于试样中插入玻璃电极及参比电极,根据两电极间的电位差求得试样PH值。
3.1.3试剂3.1.3.1标准溶液PH6.85(混合磷酸盐)3.1.3.2标准溶液PH4.01(邻苯二甲酸氢钾)3.1.3.3标准溶液PH9.18(硼砂)3.1.4仪器3.1.4.1 PHS-3C型酸度计:量程1-14 ,精度0.013.1.4.2小型电磁搅拌器3.1.4.3水银温度计:量程0-100℃,精度0.1℃3.1.4.4烧杯:100ml3.1.5取样量:取试样160ml分两次用100ml烧杯测定,现取现测。
3.1.6操作步骤3.1.6.1根据仪器说明书对PH计进行校正。
3.1.6.2乳化液的测定:先用试样将烧杯(100ml)洗2-3次,再往烧杯中倒入一定量的试样,加入一粒搅拌子,将用水洗净滤纸擦干的电极插入试样中,按下“测量”开关,开动搅拌器搅拌一分钟,停止搅拌,待PH计的指针稳定后,读取PH值。
在重复测定一次。
3.1.7报告:取两次测定读数的平均值作为结果,精确到小数点后两位。
3.2皂化值3.2.1适用范围:本方法适用于乳化液中皂化值的测定3.2.2方法概要:乳化液以氯化钠破乳分解后,用丁酮萃取油份,蒸发除去丁酮,按GB8021─87石化产品皂化值测定法,测定皂化值。
乳化液配制的基本程序(doc 12页)

乳化液配制的基本程序(doc 12页)目录一、化液配制准备和配制条件;二、乳化液配制加油,加水计算方法;三、乳化液配制程序;四、乳化液管理人员日常操作;五、乳化液临时调控指标;六、乳化液应用相关数据检测和收集;七、其它;八、附录5)关闭污油箱与净油箱的排液阀门,打开油箱与净油箱的连通阀门。
6)将清洗剂溶液(冷轧油相同时可不加清洗剂)加入到系统中,加入量以能使系统循环为准,并加热到400C。
启动循环泵和供液泵(包括加热泵)循环清洗整个系统。
准备站清洗视情况而定。
7)将系统排空再次用新水按条款1.4进行清洗并排放。
8)加自来水同时加热到400C再次运行1小时后排空,配液系统视情况决定。
乳化液配制加油,加水计算方法系统加油1、油桶加热方式,(侍定)2、根据需求计算加油加水量,第一次充填量如下:a、第一次配制目标浓度为2.0%,主要用于系统简单压下调试;如果道次压下量需要达到30%以上时,可先将浓度提高至3.0%;b、第一次配制乳化液总体积为100m3。
c、所需总油量为100m3*2.0%=2m3,每桶为200L/185kg,合计需要10桶。
3、准备站总体积为3 m3,可用液位为2.5m3,按浓度15%进行预配,需要加入2500×15%=375kg,约2桶;因此,每次在准备站中加入2桶轧制油,配制过程如下:a、在箱中加入水2.2m3后,开动搅拌和加热;b、加入2桶轧制油完毕后搅拌15-20分钟;c、开动送液泵,向乳化液箱送液;d、重复上述过程5次,直完成所需加油量;系统加水1、初次配液,在开始加水时,检查系统排放阀门已经关闭;并记录开始时间和温度;2、由乳化液箱配置的脱盐水管路向系统加水乳化液配制程序1、 在系统中注入脱盐水,其总量约为正常量的60-70%(约60m 3)2、 打开净油箱和污油箱中的机械搅拌;3、 打开系统小循环(乳化液箱-加热泵-加热-净油箱);4、 打开加热器,开始加热升温;控制温度为35-450C ;5、 从准备站中加入预配液,直至完成所需加油量6、 乳化液取样测定浓度,同时将系统温度升至所需温度( 约为500C );7、 如果所测浓度高于设定浓度,向系统中补水,直至达到或低于设定浓度;8、 根据测定浓度,向净油箱内加入15%高浓度乳化液,达到所需浓度;9、在日常生产过程中,须要加油时,可按同样方式操作;注:按乳化液系统总体积约为100m 3计算,每次从配液箱加入1m 3浓度为15%的乳化液,系统浓度可提高约0.15%,可以据此计算所需的预配液。
乳化液配制的基本程序
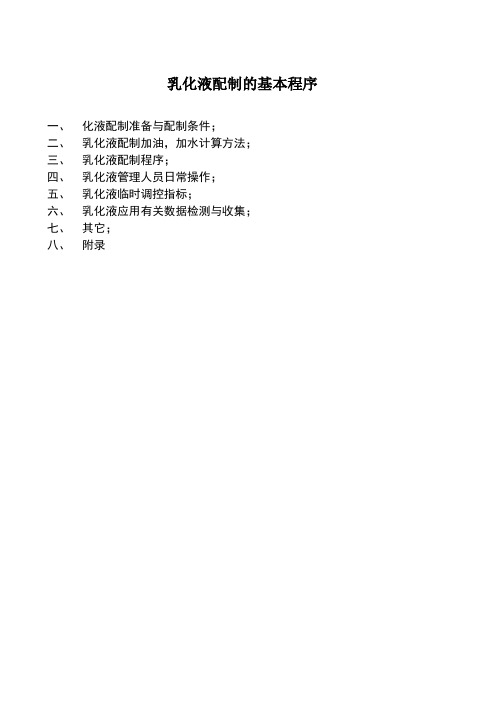
乳化液配制的基本程序一、化液配制准备与配制条件;二、乳化液配制加油,加水计算方法;三、乳化液配制程序;四、乳化液管理人员日常操作;五、乳化液临时调控指标;六、乳化液应用有关数据检测与收集;七、其它;八、附录乳化液配制准备与配制条件在乳化液配制前,需首先进行如下准备工作1、乳化液系统及输送设备经确认正常;a、系统的大循环(净液箱-加热泵-加热-喷嘴排-收集箱-磁分离器-污油箱)已测试正常;b、系统旁路循环(净液箱-加热泵-加热-净油箱)经测试正常,搅拌正常,以保证乳化液在配制后,长期不应用时保持状态。
2、系统排空第一次配液前应完成必要的清洗工作后,并通过乳化液供方与我方共同确认,内容为:a、基本无可见杂质与残余涂油;b、无大量清洗水残留(小于总体积的1%或者1m3);c、乳化液系统已经用去离子水至少冲洗过一次,以减少杂质离子对乳化液的首次污染;d、制时水后已确认去离子水符合要求,及管道系统完成清洗,在管出口处取样检测;3、加热系统经测试正常,保证乳化液配制后在长期不使用时能保持温度400C以上,以防止细菌生长;4、原油加热系统经检查运行正常,保证油桶内油品能够加热至可流淌状态;5、检查轧制油的名称、批号,确保使用所需轧制油;注:乳化液系统清箱操作如下1)通知废乳化液处理站准备接收废乳化液。
2)关闭所有系统泵,(包含供液泵、循环过滤泵、循环加热泵、搅拌器、带式的、撇油机、磁分离器)3)打开污油箱与净油箱的排液阀门。
4)系统排空后,用高压水清洗下列部位。
污油箱、净油箱(包含加热器)、配液槽、磁分离器、平床过滤器、主轧机及收集池与喷嘴排。
5)关闭污油箱与净油箱的排液阀门,打开油箱与净油箱的连通阀门。
6)将清洗剂溶液(冷轧油相同时可不加清洗剂)加入到系统中,加入量以能使系统循环为准,并加热到400C。
启动循环泵与供液泵(包含加热泵)循环清洗整个系统。
准备站清洗视情况而定。
7)将系统排空再次用新水按条款1.4进行清洗并排放。
乳化液分析方法

乳化液分析方法浓度测量方法1 取样: 在现场用100ml的量筒取100ml乳化液。2 将取样倒入油分瓶。3 在油分瓶中放入少量沸腾石。(2-6个)4 在油分瓶中倒入盐酸。5 煮沸,煮沸10-15分钟。6 将油分瓶从加热炉取下,将加热了的盐水一点点的倒入油分瓶中,一直倒到7-8之间。7 将上述油分瓶放入热水恒温槽,放置20-30分钟。8 取出后尽快读取数据。ESI的侧量方法1在现场取样200ml。2 倒入250ml的分液漏斗(分液漏斗不用盖子)。3 用秒表(或手表)测量静置时间, 静置15分钟。4 将油分瓶放在天平上,从分液漏斗中取下层100克(ml)放入油分瓶中。5 测量其浓度。(同浓度的侧量方法)计算: ESI=下层浓度/全浓度×100铁粉的测量方法(EDTA滴定法)1.操作手续1)使用乳化液10ml(用10ml的玻璃瓶从现场直接取样)倒入100ml烧杯。
2)往烧杯中加入约5ml的盐酸,1ml的硝酸。3)加蒸馏水,全量为50ml左右,加入沸腾石,加热煮沸,约15分钟。4)酸分解后,再次加入蒸馏水,全量至约50ml(补充蒸发掉的蒸馏水量)5)静置冷却后,移至250ml的分液漏斗。这时用盐酸50ml,MIBK30ml把烧杯洗净,倒入分液漏斗。6)充分晃动分液漏斗,然后静置10分钟左右,把下层透明部分扔掉。7)往分液漏斗中再次添加40ml蒸馏水,充分晃动分液漏斗, 然后静置10分钟左右,把下层透明部分倒入容量为200-300ml的锥型瓶中。8)在锥型瓶中加入约50ml的BUFFAR-4液体。9)加入一点水杨酸(耳勺约3勺),然后把锥型瓶放入50-70摄氏度温水中使之溶解, 变成威示忌颜色。10) 滴入1/100N-EDTA。(终点:红色消失,或者变成淡黄色。) 2.计算铁粉(ppm)=55.84×滴定量(ml)酸值的测量方法1.往200-300ml的锥型瓶中准确的倒入1-3克左右的试料。
乳化液浓度配比标准作业流程

液压泵工
2
检查乳化液箱及乳化液
1)检查乳化液箱;
2)检查乳化液箱液位;
3)检查乳化液质量.
1)乳化液箱无漏液,观察窗清晰,箱内干净无杂物,阀动作灵活可靠;
2)液面在液箱三分之二位置以上;
3)乳化液无析油、析皂、沉淀、变色、变味.
《煤矿安全质量标准化基本要求及评分方法》第四部分—采煤第四项
1
1。1流程图
1。2流程概述
流程名称
乳化液浓度配比标准作业流程
流程编号
流程说明
适用范围
井工矿
流程接口
1.3标准作业工单
序号
流程步骤
作业内容
作业标准
相关制度
作业表单
作业人员
安全提示
1
检查作业环境
1)检查乳化液泵站位置的巷道支护;
2)检查顶板淋水。
1)顶板、两帮支护完好,无漏顶、片帮;
2)防淋水措施到位。
《煤矿安全质量标准化基本要求及评分方法》第四部分-采煤第四项
设备运行记录(采煤)
液压泵工
6-1
清理作业现场
1)整理工具;
2)清理卫生。
1)工具干净,放回原处,码放整齐;
2)卫生干净整洁。
液压泵工
6—2
填写记录
填写乳化液泵运行记录。
内容真实、规范、清晰。
设备运行记录(采煤)
液压泵工
设备运行记录(采煤)
液压泵工
3—1
准备配液材料及检测工具
1)准备乳化油;
2)准备清水;
3)准备测量乳化液浓度的折射仪.
1)乳化油标号符合要求,备量充足;
2)水质符合要求;
3)折射仪完好。
乳化液浓度配比标准作业流程

设备运行记录(采煤)
液压泵工
6-1
清理作业现场
1)整理工具;
2)清理卫生。
1)工具干净,放回原处,码放整齐;
2)卫生干净整洁。
液压泵工
6-2
填写记录
填写乳化液泵运行记录。
内容真实、规范、清晰。
设备运行记录(采煤)
液压泵工
设备运行记录(采煤)
液压泵工
3-1
准备配液材料及检测工具
1)准备乳化油;
2)准备清水;
3)准备测量乳化液浓度的折射仪。
1)乳化油标号符合要求,备量充足;
2)水质符合要求;
3)折射仪完好。
液压泵工
3-2
检查乳化液配液设备
1)检查乳化油箱;
2)检查清水管;
3)检查浮球阀;
4)检查射流泵。
1)完好,油量足,油质合格;
设备运行记录(采煤)
液压泵工
2
检查乳化液箱及乳化液
1)检查乳化液箱;
2)检查乳化液箱液位;
3)检查乳化液质量。
1)乳化液箱无漏液,观察窗清晰,箱内干净无杂物,动作灵活可靠;
2)液面在液箱三分之二位置以上;
3)乳化液无析油、析皂、沉淀、变色、变味。
《煤矿安全质量标准化基本要求及评分方法》第四部分-采煤第四项
1
1.1流程图
1.2流程概述
流程名称
乳化液浓度配比标准作业流程
流程编号
流程说明
适用范围
井工矿
流程接口
1.3标准作业工单
序号
流程步骤
作业内容
作业标准
相关制度
作业表单
作业人员
乳化液分析技术操作规程

乳化液分析技术操作规程乳化液pH(玻璃电极测定法)1适用范围本方法适用于乳化液pH值的测定。
2方法概要在试样中侵入玻璃电极及参比电极。
根据测定两电极间电位差,求得试样的pH值。
3仪器3.1仪器及试剂3.1.1玻璃电极pH值。
(pHS-25型)3.1.2小型电磁搅拌器及搅拌子3.1.3温度计,0-50℃分度值0.2℃。
3.2试剂3.2.1 pH=4.00缓冲溶剂:称10.21克一级邻苯二甲酸氢钾试剂,溶解于1000ml蒸馏水中,溶解完全后放入百里酚防腐剂一粒。
3.2.2 pH=6.86缓冲溶剂:称3.40克一级磷酸二氢钾和3.55克一级磷酸氢二钠试剂,溶解于1000ml蒸馏水中,以去掉二氧化碳,溶解后放入百里酚防腐剂一粒.3. 2. 3 pH=9.18缓冲溶液;称3.81克一级四硼酸纳试剂,煮沸1000ml蒸馏水以去掉二氧化碳,等冷却后溶入四硼酸钠,溶解后放入百里酚防腐剂一粒.3.2.4缓冲溶液的pH值与溶液温度有关,见下表:4取样量:80ml5操作步骤5.1电计的检查通过下列操作方法,可初步判断仪器是否正常a将“选择”开关置于“+mV”或“-mV”。
短路插插入电极插座。
b“范围”开关置于中间位置,开仪器电源开关,此时电源指示灯应亮,表针位置在未开机时的位置。
c将“范围”开关置于“7-0”档,指示电表的示值应为0mV(±10mV)位置。
d将“选择”置“pH”档,调节“电位”,电表示值应能调至小于6pH。
e将“范围”开关置“7-14”档,调节“定位”,电表示值应能调至大于8pH。
当仪表经过以上方法检验,都能符合要求后,则可以认为仪器的工作基本正常。
5.2仪器的pH标定平放的复合电极在使用前必须侵泡8小时以上(蒸馏水中侵泡)。
用前使复合电极的参比电极加液小孔露出,甩去玻璃电极下端气泡,将仪器的电极插座上短路拔去插入复合电极。
仪器在使用之前,即测未知溶液pH值之前,先要标定,但这并不是说每次使用前都要标定,一般说,每天标定一次已能达到要求。
乳化液操作规程
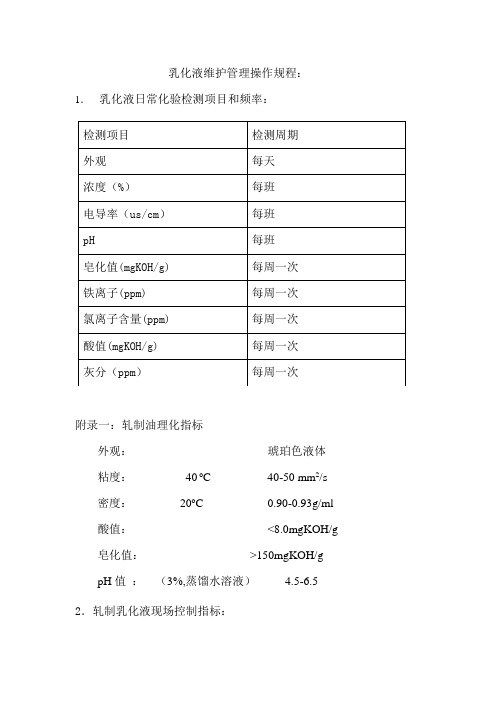
乳化液维护管理操作规程:1.乳化液日常化验检测项目和频率:附录一:轧制油理化指标外观:琥珀色液体粘度:40 o C 40-50 mm2/s密度:20o C 0.90-0.93g/ml酸值:<8.0mgKOH/g 皂化值:>150mgKOH/gpH值:(3%,蒸馏水溶液) 4.5-6.5 2.轧制乳化液现场控制指标:浓度:0.8-1.5% (常规使用)pH值(3%,蒸馏水溶液): 4.5-6.5电导率(25℃):< 500 us/cm皂化值:> 150 mgKOH/g铁离子含量:< 150ppm氯离子含量:<50ppm酸值:<30mgKOH/g灰分:<800ppm脱盐水:pH<7.0 电导率<20um/cm以上乳化液检测指标,是通常控制范围,当发现数据超差,应及时查找原因,及时设法解决。
3.乳化液现场维护和管理:3.1 加油浓度控制:0.8-1.5%3.2 加油量计算:本班加油量=上班轧制产量*0.25至0.3kg (根据轧制规格适当调整添加量)3.3 蒸汽管加热:乳化液箱内乳液温度:50-58 o C (蒸汽管始终保持乳化液恒温)3.4 乳化液循环:始终保持乳化液循环流动,轧制时,乳化液打开大循环正常生产。
停机时,实现小循环,保持乳化液流动,日常维护乳化液不能出现静止状态,“流水不腐”能够保证乳液循环防止变质腐败。
3.5停机必要时关闭气体搅拌,让杂油浮出乳液表面,然后用撇油器撇除(正常情况保持乳化液循环且气体搅拌常开)。
开机时,搅拌常开。
3.6 乳化液液位控制:保持乳化液净液箱满液位,防止污油箱内杂油介入净液箱。
要及时补充新鲜脱盐水和轧制油,维持乳化液正常浓度,保证轧制过程润滑需求。
3.7 加油方式:实行“少量多批”加油方式,将计算好的本班加油量,分批少量加到乳化液中,这样对降低消耗和有效利用乳化液起到重要作用。
加油时,必须在实现大循环时,开启气体搅拌,在输出泵前加油为佳,利用泵的搅拌力有效搅拌均匀乳液。
乳化液操作规程

乳化液操作规程乳化液维护管理操作规程:1.乳化液日常化验检测项目和频率:附录一:轧制油理化指标外观:琥珀色液体粘度: 40 o C 40-50 mm2/s密度:20o C 0.90-0.93g/ml 酸值:<8.0mgKOH/g皂化值:>150mgKOH/g pH值:(3%,蒸馏水溶液) 4.5-6.52.轧制乳化液现场控制指标:浓度: 0.8-1.5% (常规使用)pH值(3%,蒸馏水溶液): 4.5-6.5电导率(25℃): < 500 us/cm皂化值: > 150 mgKOH/g铁离子含量: < 150ppm氯离子含量: <50ppm酸值: <30mgKOH/g灰分: <800ppm脱盐水: pH<7.0 电导率<20um/cm以上乳化液检测指标,是一般控制范围,当发现数据超差,应及时查找原因,及时设法解决。
3.乳化液现场维护和管理:3.1 加油浓度控制:0.8-1.5%3.2 加油量计算:本班加油量=上班轧制产量*0.25至0.3kg (根据轧制规格适当调整添加量)3.3 蒸汽管加热:乳化液箱内乳液温度: 50-58 o C (蒸汽管始终保持乳化液恒温)3.4 乳化液循环:始终保持乳化液循环流动,轧制时,乳化液打开大循环正常生产。
停机时,实现小循环,保持乳化液流动,日常维护乳化液不能出现静止状态,“流水不腐”能够保证乳液循环防止变质腐败。
3.5停机必要时关闭气体搅拌,让杂油浮出乳液表面,然后用撇油器撇除(正常情况保持乳化液循环且气体搅拌常开)。
开机时,搅拌常开。
3.6 乳化液液位控制:保持乳化液净液箱满液位,防止污油箱内杂油介入净液箱。
要及时补充新鲜脱盐水和轧制油,维持乳化液正常浓度,保证轧制过程润滑需求。
3.7 加油方式:实行“少量多批”加油方式,将计算好的本班加油量,分批少量加到乳化液中,这样对降低消耗和有效利用乳化液起到重要作用。
(推荐)乳化液操作规程
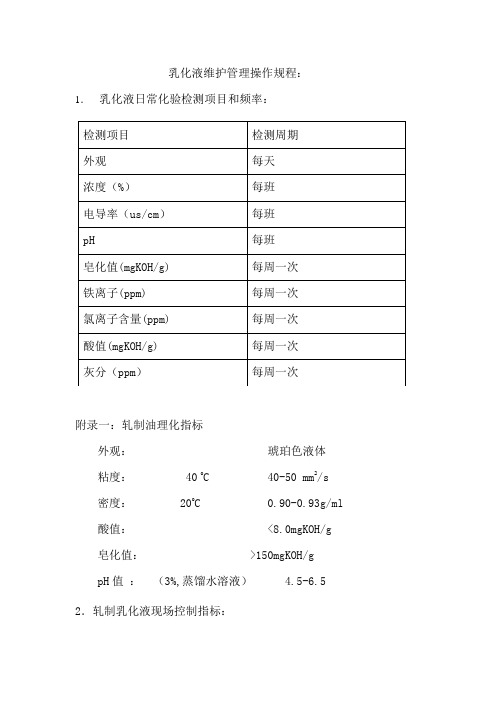
乳化液维护管理操作规程:1.乳化液日常化验检测项目和频率:附录一:轧制油理化指标外观:琥珀色液体粘度: 40 o C 40-50 mm2/s密度:20o C 0.90-0.93g/ml 酸值:<8.0mgKOH/g皂化值:>150mgKOH/gpH值:(3%,蒸馏水溶液) 4.5-6.5 2.轧制乳化液现场控制指标:浓度: 0.8-1.5% (常规使用)pH值(3%,蒸馏水溶液): 4.5-6.5电导率(25℃): < 500 us/cm皂化值: > 150 mgKOH/g铁离子含量: < 150ppm氯离子含量: <50ppm酸值: <30mgKOH/g灰分: <800ppm脱盐水: pH<7.0 电导率<20um/cm以上乳化液检测指标,是通常控制范围,当发现数据超差,应及时查找原因,及时设法解决。
3.乳化液现场维护和管理:3.1 加油浓度控制:0.8-1.5%3.2 加油量计算:本班加油量=上班轧制产量*0.25至0.3kg (根据轧制规格适当调整添加量)3.3 蒸汽管加热:乳化液箱内乳液温度: 50-58 o C (蒸汽管始终保持乳化液恒温)3.4 乳化液循环:始终保持乳化液循环流动,轧制时,乳化液打开大循环正常生产。
停机时,实现小循环,保持乳化液流动,日常维护乳化液不能出现静止状态,“流水不腐”能够保证乳液循环防止变质腐败。
3.5停机必要时关闭气体搅拌,让杂油浮出乳液表面,然后用撇油器撇除(正常情况保持乳化液循环且气体搅拌常开)。
开机时,搅拌常开。
3.6 乳化液液位控制:保持乳化液净液箱满液位,防止污油箱内杂油介入净液箱。
要及时补充新鲜脱盐水和轧制油,维持乳化液正常浓度,保证轧制过程润滑需求。
3.7 加油方式:实行“少量多批”加油方式,将计算好的本班加油量,分批少量加到乳化液中,这样对降低消耗和有效利用乳化液起到重要作用。
加油时,必须在实现大循环时,开启气体搅拌,在输出泵前加油为佳,利用泵的搅拌力有效搅拌均匀乳液。
切削液、乳化油操作规范

切削液、乳化油操作规范(一)、配制方法正确的配制方法是将水先注入水箱中,然后加入计量的原液,搅拌均匀后,用糖度计测定浓度,得到所需的配制浓度。
1、配制浓度:乳化油、切削液的使用浓度一般掌握在5%~7%,应根据加工要求和使用特点,按实际情况确定最佳配制浓度。
2、水质要求:纯水或冷凝水。
3、计量:根据系统实际容积,计算所需乳化油、切削液量和水量。
4、加水:将所需的水放入清洗后洁净的槽体内。
5、加乳化油、切削液:开启泵,在系统已循环的状态下缓慢倒入乳化油、切削液原液。
原液倒入点应选在能迅速充分搅匀的位置。
6、混配均匀:乳化油、切削液加完后,应再循环20~30分钟,使工作液完全混合均匀。
测定浓度和pH值。
即可进行切、削(磨)等操作。
(二)、补加方法工作液在使用过程中因消耗或水份蒸发,会导致其浓度偏差或使用液量减少,正确的补加方法是先按1所述配制好稀释液(根据实际情况,浓度的高低自行掌握)然后加入水箱中;如只是浓度偏低,则可直接补加原液,然后用糖度计测定,直至达到所需的配制浓度。
1、在乳化油、切削液的使用过程中,工作液必然会有不断的消耗。
应保持工作液的适当浓度和液位,及时向供液系统中添加乳化油、切削液原液和清洁自来水。
2、添加乳化油、切削液时,应测定现有工作液浓度。
根据现有浓度和液位差值计算出所需原液的数量。
3、应在开泵循环状态下,添加原液和自来水,至规定的浓度和液位。
(三)、浓度管理由于工作液的浓度直接关系到使用液的各项性能,如浓度异常,则可能会发生以下问题。
(四)、PH 值管理PH值降低是造成工作液腐败、工件生锈的直接原因之一,因此经常测定使用液的PH值,并使其保持在指标值范围之内,将有效地防止工作液的腐败和工件、设备的锈蚀现象。
PH值的测定最好采用PH计,避免因试纸误差而带来的管理不善。
如发现PH值降低现象,首先进行浓度检查;如浓度正常,则添加PH值调节剂。
如浓度偏低,则首先补充原液,校正浓度,如PH值仍偏低,则同样应添加PH调节剂以提高PH值。
乳化液操作规程

乳化液维护管理操作规程:1.乳化液日常化验检测项目和频率:附录一:轧制油理化指标外观:琥珀色液体粘度:40 o C 40-50 mm2/s密度:20o C 0.90-0.93g/ml酸值:<8.0mgKOH/g 皂化值:>150mgKOH/gpH值:(3%,蒸馏水溶液) 4.5-6.5 2.轧制乳化液现场控制指标:浓度:0.8-1.5% (常规使用)pH值(3%,蒸馏水溶液): 4.5-6.5电导率(25℃):< 500 us/cm皂化值:> 150 mgKOH/g铁离子含量:< 150ppm氯离子含量:<50ppm酸值:<30mgKOH/g灰分:<800ppm脱盐水:pH<7.0 电导率<20um/cm以上乳化液检测指标,是通常控制范围,当发现数据超差,应及时查找原因,及时设法解决。
3.乳化液现场维护和管理:3.1 加油浓度控制:0.8-1.5%3.2 加油量计算:本班加油量=上班轧制产量*0.25至0.3kg (根据轧制规格适当调整添加量)3.3 蒸汽管加热:乳化液箱内乳液温度:50-58 o C (蒸汽管始终保持乳化液恒温)3.4 乳化液循环:始终保持乳化液循环流动,轧制时,乳化液打开大循环正常生产。
停机时,实现小循环,保持乳化液流动,日常维护乳化液不能出现静止状态,“流水不腐”能够保证乳液循环防止变质腐败。
3.5停机必要时关闭气体搅拌,让杂油浮出乳液表面,然后用撇油器撇除(正常情况保持乳化液循环且气体搅拌常开)。
开机时,搅拌常开。
3.6 乳化液液位控制:保持乳化液净液箱满液位,防止污油箱内杂油介入净液箱。
要及时补充新鲜脱盐水和轧制油,维持乳化液正常浓度,保证轧制过程润滑需求。
3.7 加油方式:实行“少量多批”加油方式,将计算好的本班加油量,分批少量加到乳化液中,这样对降低消耗和有效利用乳化液起到重要作用。
加油时,必须在实现大循环时,开启气体搅拌,在输出泵前加油为佳,利用泵的搅拌力有效搅拌均匀乳液。
乳化液配比操作规程

乳化液配比工操作规程一.上岗条件第1条:必须经过专业技术培训,考试合格取得合格证后,持证上岗方准操作:第2条:应熟知操作反渗透水处理成套设备的结构、性能、工作原理、技术特征,能独立操作。
第3条:实习作业人员操作应经主管部门批准并指定专人指导监护。
第4条:作业人员应身体健康,应无妨碍本职工作的病症。
二.安全规定第1条:每班安排两人值班,一正一副。
操作时,副值班操作,正值班监护。
上岗按规定穿好劳保用品。
第2条:上班前严禁饮酒,班中严禁睡觉与吸烟,不做与本职工作无关的事情。
严格执行交接班制度和工种岗位责任制,坚守工作岗位,遵守本操作规程、《煤矿安全规程》及有关规定。
第3条:检修设备或处理故障时,严格执行“停电挂牌制度”,设专人监护并制定有效的安全措施。
第4条:经常检查维护反渗透水处理系统各种计量装置,阀门和安全装置等,保证灵活可靠,每天要对全部设备的外表进行一次擦洗。
第5条:精滤器和保安滤器进水水压压差升高至0.15MPa时需要更换滤芯;炭滤器内的活性炭每半年检测一次炭滤器出水中余氯的含量,并与原水中余氯含量比较,若进出水中余氯含量无明显差异,则表明活性炭已失效,需更换;当钛棒过滤器进水水压压差达0.15MPa 时,应对钛棒滤芯进行清洗。
第6条:当出现标准化产水量降低10%以上、标准化脱盐率增加5%以上、进水和浓水之间的标准化压差上升了15%的情况中任意一项时,需要清洗膜元件。
当准备清洗液时,应确保在循环进入膜元件前,所有的化学品得到很好的溶解和混合。
在清洗液循环期间,清洗液温度不能超过35摄氏度。
第7条:掌握电气设备防、灭火知识,能正确使用灭火器材。
第8条:坚守本职岗位,爱岗敬业。
三.操作准备第1条:按规定检查RO水生产线、饮用水生产线、乳化液生产线成套设备状况,确保无重大缺陷和不安全因素。
第2条:根据交接班情况,重点检查存在问题的处理情况,达到各项保护齐全有效,所有阀门开关位置正确、压力表、流量计完好。
乳化液泵操作工岗位标准化作业流程

乳化液泵操作工岗位标准化作业流程
第一节 岗位流程图
流程图
起动乳化液泵
清理工作区卫生
按下泵停止按钮控制开关打到断
电
开始
填写检查、维护、交接班记录
填写记录
打开手动卸载阀泵空载
运行 停泵
监视仪表显示
正常运行
接收送液信号
开泵
检查作业环境
安全确认
关闭高压供液阀泵吸液
阀 监听机器声音
监视机器温度
发出开泵信号
向工作面供液
检查乳化泵设
备
监视乳化液液位
结束
第二节岗位描述
第三节作业流程标准清单
第四节作业流程风险辨识
第五节岗位隐患排查治理与应急措施。
- 1、下载文档前请自行甄别文档内容的完整性,平台不提供额外的编辑、内容补充、找答案等附加服务。
- 2、"仅部分预览"的文档,不可在线预览部分如存在完整性等问题,可反馈申请退款(可完整预览的文档不适用该条件!)。
- 3、如文档侵犯您的权益,请联系客服反馈,我们会尽快为您处理(人工客服工作时间:9:00-18:30)。
1.1流程图
1.2流程概述
流程名称
乳化液浓度配比标准作业流程
流程编号
流程说明
适用范围
井工矿
流程接口
1.3标准作业工单
序号
流程步骤
作业内容
安全提示
1
检查作业环境
1)检查乳化液泵站位置的巷道支护;
2)检查顶板淋水。
1)顶板、两帮支护完好,无漏顶、片帮;
2)防淋水措施到位。
2)完好,水流畅通;
3)完好;
4)完好。
《煤矿安全质量标准化基本要求及评分方法》第四部分-采煤第四项
设备运行记录(采煤)
液压泵工
4
配制乳化液
启动乳化液自动配液设备。
自动配液正常。
液压泵工
5
检查乳化液
1)检查乳化液箱液位;
2)检测乳化液浓度。
1)液面在液箱三分之二位置以上;
2)乳化液配制合格(浓度3%-5%)。
《煤矿安全质量标准化基本要求及评分方法》第四部分-采煤第四项
设备运行记录(采煤)
液压泵工
6-1
清理作业现场
1)整理工具;
2)清理卫生。
1)工具干净,放回原处,码放整齐;
2)卫生干净整洁。
液压泵工
6-2
填写记录
填写乳化液泵运行记录。
内容真实、规范、清晰。
设备运行记录(采煤)
液压泵工
设备运行记录(采煤)
液压泵工
3-1
准备配液材料及检测工具
1)准备乳化油;
2)准备清水;
3)准备测量乳化液浓度的折射仪。
1)乳化油标号符合要求,备量充足;
2)水质符合要求;
3)折射仪完好。
液压泵工
3-2
检查乳化液配液设备
1)检查乳化油箱;
2)检查清水管;
3)检查浮球阀;
4)检查射流泵。
1)完好,油量足,油质合格;
设备运行记录(采煤)
液压泵工
2
检查乳化液箱及乳化液
1)检查乳化液箱;
2)检查乳化液箱液位;
3)检查乳化液质量。
1)乳化液箱无漏液,观察窗清晰,箱内干净无杂物,阀动作灵活可靠;
2)液面在液箱三分之二位置以上;
3)乳化液无析油、析皂、沉淀、变色、变味。
《煤矿安全质量标准化基本要求及评分方法》第四部分-采煤第四项