汽车内外饰工艺数据checklist
钣金车身工艺-铸造-NC数模checklist流转单A1-2006

白车身数模质量要求 白车身数模质量要求 白车身数模质量要求 白车身数模质量要求
24 25 26 27 28 29 30 31 32 33
34 35 NC数模应包含实体数模 失效模式: 1代表不可原谅错误 2代表严重错误 3代表一般错误
外表面符合性检查 白车身数模质量要求 结构符合焊接工艺性 焊接总成焊点分布合理 白车身零部件工艺性审查规定 凸焊螺母、凸焊螺栓工艺可行性 白车身零部件工艺性审查规定 孔功能描述报告符合性检查,不漏孔,无多余孔 安装孔孔位与硬点报告的符合性检查 凸焊螺母和螺栓底孔孔径满足企业要求,凸焊螺母底 孔孔径比螺母规格(公称直径)大1mm,凸焊螺栓底孔 孔径比螺栓公称直径大0.5mm(长城企业标准) 装配密集断面检查,干涉量不得大于0.1mm,安装关系 正确,间隙正确 运动干涉和运动间隙检查满足要求 过孔满足过孔规定:逆向时,过孔按照样车设计;新 设计时,过孔直径在安装孔的直径基础上逐层加大2mm 或3mm 涂装工艺孔及切口的设计及分布是否合理
P P P P P P P P P P P P
P P P P P P P P P P P P
P P P P P P P P P P P P
P P P P P P P P P P P P
P P P P P P P P P P P P
P P P P P P P P P P P P
1 2 2 2 2 2 2 2 2 2 2 1
ZB•Q•0004/03.02
A1-2006 项目 失效 总监 模式 P 1 3 2 3 2 2 2 P P P P P P P P P P P P P P P P P P P 3 3 2 2 2 2 2 2 2 2 2 2 3 1 1 1
自检 校对 审核 质检 总布置 总师 P P P P P P P P P P P P P P P P P P P P P P P P P P P P P P P P P P P P P P P P P P P P P P P P P P P P P P P P P P P P P P P P P P P P P P P P P P P P P P P P P P P P P P P
16949 Check List

(海量营销管理培训资料下载)过程审核提问表上汽集团奇瑞汽车有限公司(海量营销管理培训资料下载) (海量营销管理培训资料下载) (海量营销管理培训资料下载)供应商质量保证 供应商:过程审核零件名称:产品与过程控制质量保证地址:审核人员: 审核日期:(海量营销管理培训资料下载) (海量营销管理培训资料下载) (海量营销管理培训资料下载)【1.1】图纸、标准清单是否为最新版本?1.2 核查生产零件的工艺平面布置图、工艺流程图在生产是否得到执行?【1.3】核查工艺卡、作业指导书与监控计划是否具有一 致性?1.4 工艺卡、作业指导书、持续改进质量、监控计划与图 纸上的关键特性参数是否一致?是否有关关键特性参数 清单?1. 图 纸 、 标 准 及 技 术 文 件 的 审 核【1.5】对工序是否进行了故障模态分析,并在工艺文件及工序中得以实施?【2.1】外购件产品在供货和仓库存放时是否符合产品特 性要求?(产品的防潮、防尘、防光、包装、防磕碰、防 污染、有毒化学品的管理、搬运及工位器具)2. 外 购 件 质 量 保 证2.2 仓库管理员是否对存放零件的属性有足够的了解? (零件的先进先出、存放要求、存放周期及各种包装标识 内容) (海量营销管理培训资料下载) (海量营销管理培训资料下载)第1页审核内容审核要求存在问题适合待改善不可接受 不存在【2.3】仓库的区域划分,各种类型零件的标识是否完善、 合理?能否保证先进先出、帐、卡、物是否一致?(布局是否合理,如何防止混料、混批,待检、返工、返修区域的标识是否明确)2.4 检验工艺文件是否完善?检测频次是否合理并考虑 了关键项目?2.5 外协件及原材料的可追溯性标识是否明确? (如炉号、模号、生产日期等)2.6 检测手段是否齐全?不具备的是否定期外委?【2.7】是否按监控计划的要求对入库零件进行供货验 收?2. 外 购 件 质 量 保 证【2.8】零件的供货资格及合同是否确认?是否有主机厂确认的供货零件清单是否留存标样用于对比验收? (海量营销管理培训资料下载) (海量营销管理培训资料下载)2.9 是否对供货厂家的供货质量进行统计,对有问题 的零件是否要求供应商进行整改并进行跟踪审核?第2页审核内容审核要求存在问题适合待改善不可接受 不存在2.10 是否定期对仓库的库存量进行清理,并制定合理的 零件最低、最高库存指标?2.11 外协件检测间的布局是否合理?2. 外 购 件 质 量 保 证2.12 对关键的外协件是否进行现场审核?3. 生 产 【3.1】设备、模具、装备及检测手段等是否到位并按规 定的程序进行终验收,设备的可用性是否符合设备技术任务书的目标? (海量营销管理培训资料下载) (海量营销管理培训资料下载)3.2 对每台设备验收时遗留的问题是否制定了整改措施 并实施?3.3 设备、模具、装备及检测手段的图纸、操作说明书、备件易损件清单,检查或标定是否说明并转交给使用者?准 备 与 组 织【3.4】设备、模具、装备、检测手段是否都经过编码、 标识、登记台帐,并有清单?第3页审核内容审核要求存在问题适合待改善不可接受 不存在3.5 设备的备件、易损件仓库如何管理,是否满足生产要求?3. 生 产 准 备 与 组【3.6】设备能力是否符合目标的要求? (海量营销管理培训资料下载) (海量营销管理培训资料下载)【3.7】试验、监控、检查、测量设备是否经过检查、鉴 定或校准?3.8 设备、模具、装备、检测手段等环境条件是否符合技术任务书的要求?【3.9】设备、模具、装备、检测手段是否制定了预防性 维修计划?3.10 模具的使用寿命是否有明确的定义并据此准备相应 的备用模?织3.11 模具设计是否考虑了各种标识?(零件号、生产日 期、厂标、模号及模腔号)第4页审核内容审核要求存在问题适合待改善不可接受 不存在 (海量营销管理培训资料下载) (海量营销管理培训资料下载)3.12 零件是否通过生产文件批准?3.13 工序之间的布局是否合理,是否便于提供效率?3.14 对于复杂、关键的设备、模具等,在自身无法维修的情况下,是否有保全措施?3. 生 产 准 备 与 组 织3.15 是否按要求对模具、模腔进行定期清洗保养?有无 保养计划?【4.1】对关键工序的工序能力指数是否进行计算并得以 很好的控制?【4.2】产品监控计划在生产中是否得以实施?4. 生 产 管 理4.3 对工人和检验员所需的相应工艺与检验规程是否挂 在相应的工位上? (海量营销管理培训资料下载) (海量营销管理培训资料下载)第5页审核内容审核要求存在问题适合待改善不可接受 不存在4.4 作业指导书是否完善,操作人员是否严格执行?【4.5】工序中重要的参数是否得到控制并有监控记录?4.6 生产岗位、检测岗位的在线检测手段是否齐全并满足 产品的特性要求?是否有适合批量生产在线检测的专用 检具?4.7 环境是否整洁并考虑了安全及照明,物流是否畅通?4. 生 产 管 理4.8 是否考虑了产前及产后零件的合理摆放以提高效率? (海量营销管理培训资料下载) (海量营销管理培训资料下载)4.9 工装、工位器具是否考虑了产品特性要求?(防磕 碰、挤压)4.10 对有外观、焊接等要求的项目是否有标样? (待标样的标识、有效期)第6页审核内容审核要求存在问题适合待改善不可接受 不存在 4.13 返修件、报废件是否有明显的标记并有相应的工位 器具?是否采取隔离存放以防混装?4.14 对返修件是否有特殊的规定以保证返修件的质量?4.15 对已发现的工序质量问题是否记录并进行统计分 析?4. 生 产 管 理4.16 对出现的问题是否采取了改进措施并验证措施的有 效? (海量营销管理培训资料下载) (海量营销管理培训资料下载)【4.17】当零件、设备、工艺、工装、生产场地等发生变更是否按程序进行重新审核,以验其有效性?4.18 是否定期对过程进行审核,有无审核记录及改进措 施?4.19 在生产出现意外或造成停线时,是否有适宜的措施 以保证产品的质量,并做到可追溯性?(如首件检查,对 照处理、浇铸、加工件等的控制)第7页审核内容审核要求存在问题适合待改善不可接受 不存在 4.20 对由于返工、返修可能引进的失效模式是否有分 析?4. 生 产 管 理4.21 各种设备、工位器具、生产线等是否符合人体工程 学的要求? (海量营销管理培训资料下载) (海量营销管理培训资料下载)5.1 成品检测手段是否满足产品特性要求?5.2 成品检验工艺是否符合产品特性?【5.3】是否按检验作业指导书的要求进行成品件检测, 关键项目是否考虑到?【5.4】对检测中发现的问题是否进行了分析并采取改进 措施?5. 成 品 检 验5.5 对改进效果是否进行验证并在改进产品上做标识,以上情况是否通知主机厂?第8页审核内容审核要求存在问题适合待改善不可接受 不存在 (海量营销管理培训资料下载) (海量营销管理培训资料下载)5.6 是否定期对产品进行审核,有无审核记录及改进措 施?5.7 是否定期对产品进行可靠性试验?5.8 产品应在有效期内使用并有有效期标识?5. 成 品 检 验5.9 是否进行产品质量展示?6.1 人员是否了解产品的生产指标、质量指标和安全指 标,这些指标应包括目标值并有相应的跟踪报表?【6.2】人员素质是否符合岗位要求?6. 人 员 培 训6.3 多技能岗位对照表是否明示? (海量营销管理培训资料下载) (海量营销管理培训资料下载)第9页审核内容审核要求存在问题适合待改善不可接受 不存在 6.4 人员数量是否能满足生产产量需求?【6.5】是否有为全员设计的培训计划?6. 人 员 培 训6.6 是否对培训的效果进行评价?【7.1】是否有安全法规件的管理程序?【7.2】对于安全法规件各生产过程及工艺文件上是否有 标记?7. 安 全 法 规 件 的 管 理7.3 质量记录保存期限是否符合要求? (海量营销管理培训资料下载) (海量营销管理培训资料下载)7.4 生产人员是否理解?第10页审核内容审核要求存在问题适合待改善不可接受 不存在 8.1 是否与奇瑞公司明确包装容器?8.2 是否对包装容器及运输方式进行可行性分析?8.3 外包装标识是否符合奇瑞公司要求?8.4 在确认包装方式前是否考虑奇瑞公司装配线的要 求?8. 包 装 、 运 输8.5 对中转库是否实施仓库管理评审?(包括容器、运输及安全库存等)(海量营销管理培训资料下载)第11页序号 审核内容 审核总项目 实审项目 应得分 扣分 得分率1 图纸、标准及技术文件的审核2 外购件质量保证3 生产准备与组织4 生产质量5 外品检验6 人员培训7 安全/法规件的管理8 包装、运输(海量营销管理培训资料下载)(海量营销管理培训资料下载) 结论:第12页(海量营销管理培训资料下载)。
汽车内外饰系统设计点检表

汽车内外饰系统设计点检表(原创版)目录1.汽车内外饰设计简介2.设计点检表的目的和意义3.设计点检表的主要内容4.设计点检表在汽车内外饰设计中的应用5.总结正文汽车内外饰设计简介汽车内外饰设计是一项涉及汽车整体造型、功能布局、舒适性和安全性等多方面因素的综合性设计工作。
汽车内外饰设计师需要兼顾车辆的美观性和实用性,以及考虑驾驶员和乘客的操作便利性和舒适性。
在设计过程中,需要全面考虑整车造型,驾驶控制子系统、信息系统、舒适性系统(例如空调控制器、收音机、开关、线束模块)等各种信息系统的布置,以及提供碰撞保护、储存区域和实用工具(如烟灰缸、硬币盒、杯托等)等方面的设计。
设计点检表的目的和意义汽车内外饰设计点检表是为了确保设计过程中各项要素得到充分考虑和有效实施而制定的一个指导性文档。
设计点检表旨在明确设计目标、梳理设计思路、划分设计任务和职责,以及确保设计质量和进度。
通过设计点检表,可以全面、系统地对汽车内外饰设计进行管理和控制,从而提高设计效率和质量。
设计点检表的主要内容设计点检表主要包括以下几个方面的内容:1.设计目标和要求:明确汽车内外饰设计的目标和要求,包括造型、功能、舒适性、安全性等方面的具体指标。
2.设计过程和方法:阐述汽车内外饰设计的具体过程和方法,包括造型设计、功能布局、材料选择、色彩搭配、工艺设计等方面的内容。
3.设计任务和分工:明确设计团队各成员的任务和职责,确保设计工作的高效协同和顺利推进。
4.设计质量和进度控制:通过设计点检表,对设计过程进行实时监控和控制,确保设计质量和进度达到预期目标。
5.设计验证和优化:对设计结果进行验证和评价,根据验证结果对设计进行优化和调整,以满足设计要求和用户需求。
设计点检表在汽车内外饰设计中的应用在汽车内外饰设计过程中,设计点检表起到了重要的指导和控制作用。
通过设计点检表,设计师可以确保设计工作按照既定的目标和要求进行,避免出现设计失误和漏洞。
同时,设计点检表也有助于设计师在设计过程中发现问题和不足,及时进行调整和优化,从而提高设计质量和用户满意度。
汽车门护板总成设计审核清单要求DOOR TRIMCheck List
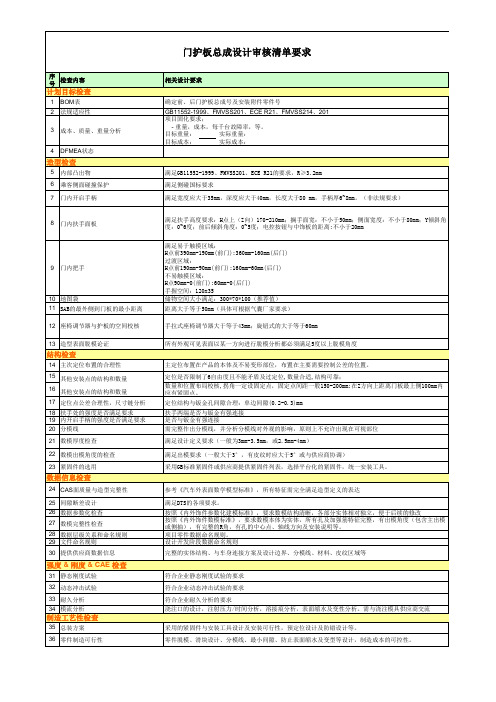
பைடு நூலகம்
37 安装扭矩 38 材料选用 39 维护性能
重大历史问题
40 内开拉手断裂、脱卡。 41 门护板内部异响、卡扣脱落。 42 门护板上本体吸附皮革起皱
43 门护板内部件之间的搭配不牢固。
紧固件等级与扭矩设计匹配状况,扭矩的一致性。 同时考虑材料回收利用问题(最少95%的回收利用) 玻璃升降器维修方便性;其他电器线束件检查方便性;考虑操作空间;门护板更换、维护方式及维护工具 等
满足出模要求(一般大于3°,有皮纹时应大于5°或与供应商协调) 采用GB标准紧固件或供应商提供紧固件列表,选择平台化的紧固件,统一安装工具。
参考《汽车外表面数学模型标准》,所有特征需完全满足造型定义的表达
满足DTS的各项要求。 按照《内外饰件参数化建模标准》,要求数模结构清晰,各部分实体相对独立,便于后续的修改 按照《内外饰件数模标准》,要求数模本体为实体,所有孔及加强筋特征完整,有出模角度(包含主出模 或侧抽),有完整的R角,有孔的中心点、轴线方向及安装说明等。 项目零件数据命名规则。 设计开发阶段数据命名规则 完整的实体结构、与车身连接方案及设计边界、分模线、材料、皮纹区域等
确定前、后门护板总成号及安装附件零件号
GB11552-1999、FMVSS201、ECE R21、FMVSS214、201 项目固化要求;
- 重量,成本,每千台故障率,等。
目标重量:
实际重量:
目标成本:
实际成本:
满足GB11552-1999、FMVSS201、ECE R21的要求,R≥3.2mm 满足侧碰国标要求
25 间隙断差设计 26 数据参数化检查 27 数模完整性检查 28 数据层级关系和命名规则 29 文件命名规则 30 提供供应商数据信息
内饰相关质量检验标准

乘用车内空气质量评价车内空气中有机物浓度要求(东风日产乘用车公司)检验方法:1.车内空气中有机物的浓度检测按HJ/T400-2007的规定进行。
实施采样时,在HJ/T400-2007规定的环境条件下,受检车辆处于静止状态,车辆门、窗和乘员舱进风口风门均处于关闭状态,发动机和空调等设备不工作。
2.对可能影响检测结果的其他条件(如汽车出厂时的内饰状态改变与否、出厂与检测的间隔时间等),可由相关方协商约定。
汽车内饰材料的燃烧特性(GB 8410-2006)内饰材料:汽车内饰零件所用的单一材料或层积复合材料,如座垫、座椅靠背、座椅套、安全带、头枕、扶手、活动式折叠车顶、所有装饰性衬板(包括门内护板、侧围护板、后围护板、车顶棚衬里)、仪表板、杂物箱、室内货架板或后窗台板、窗帘、底板覆盖层、遮阳板、轮罩覆盖物、发动机罩覆盖物和其他任何室内有机物,包括装车时吸收碰撞能量的填料、缓冲装置等材料。
技术要求内饰材料的燃烧特性必须满足以下技术要求:燃烧速度不大于100mm/min。
内饰材料燃烧特性取样要求:标准试样形状和尺寸见下图,试样的厚度为零件厚度,但不超过13mm。
以不同种类材料进行燃烧性能比较时,试样必须具有相同尺寸(长、宽、高),通常取样时必须使试样沿全长有相同的横截面。
当零件的形状和尺寸不足以制成规定尺寸的标准试样时,则应保证下列最小尺寸试样,但要记录。
a)如果零件宽度介于3mm~60mm,长度应至少为356mm。
在这种情况下试样要尽量做成接近零件的宽度。
b)如果零件宽度大于60mm,长度应至少为138mm。
此时,可能的燃烧距离相当于从第一标线到火焰熄灭时的距离或从第一标线开始至试样末端的距离。
c)如果零件宽度介于3mm~60mm,且长度小于356mm或零件宽度大于60mm,长度小于138mm,则不能按GB 8410标准试验。
燃烧速度计算:V=60x(L/T),式中:V---燃烧速度,单位为mm/min;L---燃烧距离,单位为mm;T---燃烧距离L所用的时间,单位为秒(s)。
一文看懂10大汽车内外饰常用工艺方法【附1400家全球供应商名录】

一文看懂10大汽车内外饰常用工艺方法【附1400家全球供应商名录】110大汽车内外饰常用工艺方法添加工作人员微信,免费领取《一文看懂10大汽车内外饰常用工艺方法》PDF一份!添加时请备注:公司姓名职位主营电话扫码添加工作人员电话:178****4041(同微信)2全球知名汽车内外饰零部件企业名录汽车产业是人类第一大工业品,主要是因为包括了整车和零部件。
汽车零部件产业,比汽车整车产业还要大。
因为,汽车在生命周期里面还需要更换启动电池,保险杠,轮胎,玻璃,汽车电子等。
中国,作为全球最大的汽车零部件产业规模非常大,全国竟然有超过10万家企业,其中有统计数据的有5.5万家,而规模以上(也就是年销售在2000万元以上)的竟然有1.3万家。
今天,我们就汇编了一份1400 家全球知名汽车内外饰零部件企业名录,专门针对内饰件、外饰件、车门系统、座椅系统、车身等企业。
整理汇总的维度包括:公司名称、公司简介、主营产品、所在省市、主要客户等信息。
# 内饰件 ## 外饰件 ## 车镜 ## 车门及附件企业 ## 座椅及附件企业 ## 车身本体白车身企业 ## 如何获取汽车内外饰企业名录 #该名录字数400000 ,汇聚311家内饰件企业,275家外饰件企业,249家车镜企业,245家汽车车门及附件企业,178家座椅及附件企业,136家车身本体白车身企业,带你快速了解各省市汽车内外饰企业分布。
详细目录如下一、2019年中国汽车内饰行业发展背景1.1 2019年全球汽车销量情况1.2 2019年中国汽车销量情况二、汽车内饰竞争格局及经营情况三、全球知名汽车内外饰公司3.1 佛吉亚(Faurecia)3.2 麦格纳3.3 英提尔3.4 敏实集团(MINTH GROUP)3.5 伟世通公司(visteon)3.6 安道拓3.7 彼欧集团(全耐塑料)3.8 安通林3.9 李尔3.10 丰田纺织3.11 丰田合成3.12 埃驰(IAC)集团3.13 现代摩比斯3.14 东海理化3.15 全兴国际集团3.16 华翔集团3.17 宁波双林3.18 延锋汽车饰件系统有限公司3.19 江南模塑科技3.20 海拉车灯四、中国汽车内外饰上市公司五、中国汽车内外饰企业5.1 内饰件5.2 外饰件5.3 车镜5.4 车门及附件5.5 座椅及附件# 精彩内容抢先看 #点击图片查看高清大图…………《中国汽车内外饰企业名录(2020年)》。
车身内饰结构设计工艺性审查标准

上海同济同捷科技股份有限公司企业标准TJI/DG·0003·A1-2005 车身内饰结构设计工艺性审查标准2005-7-30发布2005-XX-XX实施上海同济同捷科技股份有限公司发布TJI/DG·0003·A1-2005前言为使本公司汽车设计技术规范化,参照国外汽车设计―制造的程序化模式,结合我国自行设计―开发汽车的实际情况,特编制“车身内饰结构设计工艺性审查标准”,以便在汽车设计―开发实践中进一步充实、提高和完善。
内容:1. 适用范围2. 结构设计工艺性3. 有关内饰件成型、焊接、装配.等结构工艺性的审查要点本规定由上海同济同捷科技有限公司提出。
本规定由上海同济同捷科技有限公司总师办归口管理。
主要起草人:杨志莹目录序号名称页次1 主题内容与适用范围 (4)2 引用标准 (4)3 术语·························································4-5 4结构设计工艺审查要求······································5-105 举例说明···················································10-126 参考文献···················································12-13上海同济同捷科技股份有限公司企业标准1.主题内容与适用范围内饰件是指车身本体上的装饰件,它们除满足自身的功能外还要有很强的装饰性,目前汽车的内饰件基本以塑料件为主,此《内饰件设计结构工艺审查标准》只针对塑料件的部分提出在数模上的要求,规定了内饰结构设计工艺性审查的要求。
汽车散热器面罩设计审核清单要求checklist
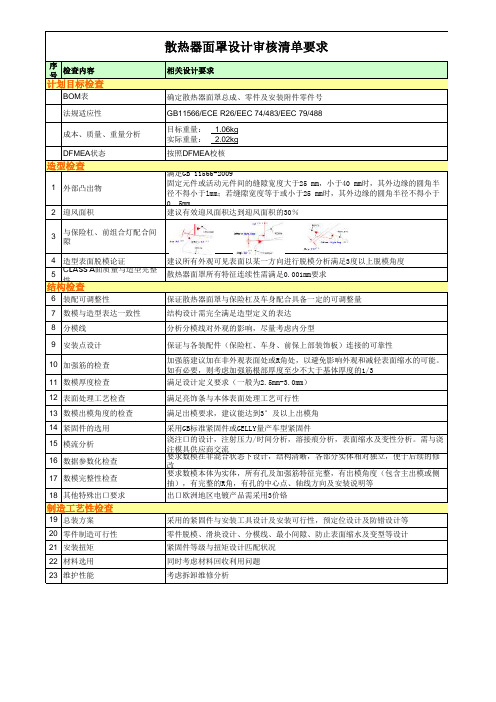
序号检查内容相关设计要求BOM 表确定散热器面罩总成、零件及安装附件零件号法规适应性GB11566/ECE R26/EEC 74/483/EEC 79/488成本、质量、重量分析目标重量: 1.06kg 实际重量: 2.02kg DFMEA 状态按照DFMEA 校核1外部凸出物满足GB 11566-2009固定元件或活动元件间的缝隙宽度大于25 mm,小于40 mm时,其外边缘的圆角半径不得小于lmm;若缝隙宽度等于或小于25 mm时,其外边缘的圆角半径不得小于0.5mm2迎风面积建议有效迎风面积达到迎风面积的30%3与保险杠、前组合灯配合间隙4造型表面脱模论证建议所有外观可见表面以某一方向进行脱模分析满足3度以上脱模角度5C LASS A 面质量与造型完整性散热器面罩所有特征连续性需满足0.001mm要求6装配可调整性保证散热器面罩与保险杠及车身配合具备一定的可调整量7数模与造型表达一致性结构设计需完全满足造型定义的表达8分模线分析分模线对外观的影响,尽量考虑内分型9安装点设计保证与各装配件(保险杠、车身、前保上部装饰板)连接的可靠性10加强筋的检查加强筋建议加在非外观表面处或R角处,以避免影响外观和减轻表面缩水的可能。
如有必要,则考虑加强筋根部厚度至少不大于基体厚度的1/311数模厚度检查满足设计定义要求(一般为2.5mm-3.0mm)12表面处理工艺检查满足亮饰条与本体表面处理工艺可行性13数模出模角度的检查满足出模要求,建议能达到3°及以上出模角14紧固件的选用采用GB标准紧固件或GELLY量产车型紧固件15模流分析浇注口的设计,注射压力/时间分析,溶接痕分析,表面缩水及变性分析。
需与浇注模具供应商交流16数据参数化检查要求数模在非混合状态下设计,结构清晰,各部分实体相对独立,便于后续的修改17数模完整性检查要求数模本体为实体,所有孔及加强筋特征完整,有出模角度(包含主出模或侧抽),有完整的R角,有孔的中心点、轴线方向及安装说明等18其他特殊出口要求出口欧洲地区电镀产品需采用3价铬19总装方案采用的紧固件与安装工具设计及安装可行性,预定位设计及防错设计等20零件制造可行性零件脱模、滑块设计、分模线、最小间隙、防止表面缩水及变型等设计21安装扭矩紧固件等级与扭矩设计匹配状况22材料选用同时考虑材料回收利用问题23维护性能考虑拆卸维修分析制造工艺性检查散热器面罩设计审核清单要求计划目标检查造型检查结构检查。
汽车冲压件模具验收CHECKLIST
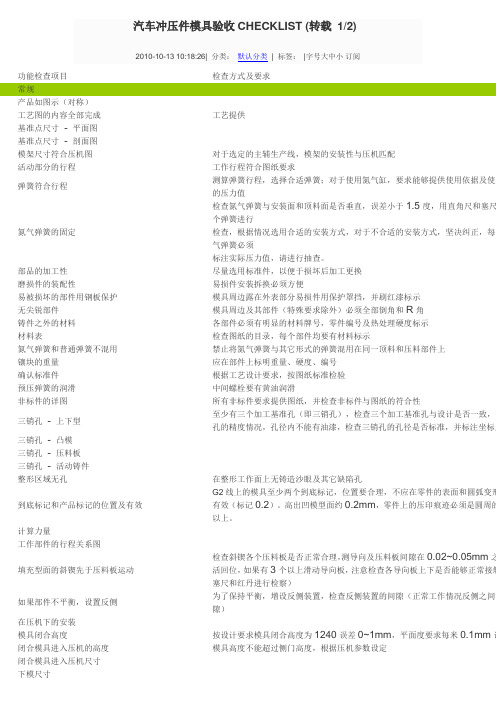
汽车冲压件模具验收CHECKLIST (转载1/2)2010-10-13 10:18:26| 分类:默认分类| 标签:|字号大中小订阅功能检查项目检查方式及要求常规产品如图示(对称)工艺图的内容全部完成工艺提供基准点尺寸- 平面图基准点尺寸- 剖面图模架尺寸符合压机图对于选定的主辅生产线,模架的安装性与压机匹配活动部分的行程工作行程符合图纸要求弹簧符合行程测算弹簧行程,选择合适弹簧;对于使用氮气缸,要求能够提供使用依据及使用的压力值氮气弹簧的固定检查氮气弹簧与安装面和顶料面是否垂直,误差小于1.5度,用直角尺和塞尺个弹簧进行检查,根据情况选用合适的安装方式,对于不合适的安装方式,坚决纠正,每个气弹簧必须标注实际压力值,请进行抽查。
部品的加工性尽量选用标准件,以便于损坏后加工更换磨损件的装配性易损件安装拆换必须方便易被损坏的部件用钢板保护模具周边露在外表部分易损件用保护罩挡,并刷红漆标示无尖锐部件模具周边及其部件(特殊要求除外)必须全部倒角和R角铸件之外的材料各部件必须有明显的材料牌号,零件编号及热处理硬度标示材料表检查图纸的目录,每个部件均要有材料标示氮气弹簧和普通弹簧不混用禁止将氮气弹簧与其它形式的弹簧混用在同一顶料和压料部件上镶块的重量应在部件上标明重量、硬度、编号确认标准件根据工艺设计要求,按图纸标准检验预压弹簧的润滑中间螺栓要有黄油润滑非标件的详图所有非标件要求提供图纸,并检查非标件与图纸的符合性三销孔- 上下型至少有三个加工基准孔(即三销孔),检查三个加工基准孔与设计是否一致,注孔的精度情况,孔径内不能有油漆,检查三销孔的孔径是否标准,并标注坐标尺三销孔- 凸模三销孔- 压料板三销孔- 活动铸件整形区域无孔在整形工作面上无铸造沙眼及其它缺陷孔到底标记和产品标记的位置及有效G2线上的模具至少两个到底标记,位置要合理,不应在零件的表面和圆弧变形有效(标记0.2)。
高出凹模型面约0.2mm,零件上的压印痕迹必须是圆周的以上。
验车checklist

结论
第二步:检查车身外部 1 (1) (2) (3) (4) (5) 2 (1) (2) (3) (4) (5) 3 4 (1) 5 (1) (2) 车外观:检查车身是否有刮痕 前后保险、车门等容易被刮的部位 一些常被忽略的地方如后视镜、发动机盖等 是否存在漆色与周围不同或者出现波纹,该部位则可能被修补过,、凹陷; 发动机盖、翼子板、尾箱盖等钣金接缝是否均匀到位 些外露的胶条以及雨刮是否老化,如有则说明露天停放的时间较久或者环境比较恶劣 检查车门 拉拉车门,看车门的开关是否轻松灵活,正常的车门开关都能一步到位, 车门的缝隙是不是均等,防水橡皮条/门窗密封条 注意门把手上是否松动 看玻璃是否为原配,原配的玻璃下面都是有标识的 锁车功能检查 拉各个门 看车底盘,趴下身看车底下都有没有机油点,底盘也都有没有油污 看电瓶, 看接头有否腐蚀以及小窗是否绿色。电瓶接头一般是松的,开走前一定要JS拧紧 轮胎 轮胎表现的小毛刺有没有被磨掉,新车的轮胎因为行驶里程不多,胎面上的小毛刺都会 存在 4个轮胎规格是否相同,备胎与其规格是否相同
3
第五步:试驾 1 (1) (2) 启动时发动机的状况 拧动钥匙,如果点火时间超过5秒还不能启动,则说明点火系统不正常 启动发动机之后,将车门窗关好,看怠速时车内震动是否过于明显,然后到车外听听发 动机声音是否大于其它车辆 (听见发动机内部的声音是否有杂音,比如环子声、敲缸声、气门的嘀嘀声等等。好发 动机只有一种„呼噜呼噜‟声,不会有其他的杂音。) 试驾过程中车子的状况 试驾的时候应该注意发动机是否平顺,有没有异响 轻轻踩油门,检查发动机反应是否连续 行走时候注意车辆是否跑偏,方向机是否有异响,踏板是否顺畅。
汽车照明系统Check List
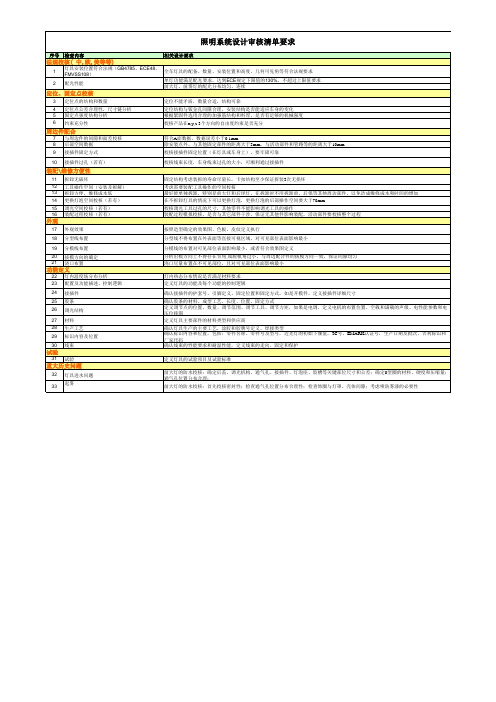
18 分型线布置
分型线不得布置在外表面等直接可视区域,对可见部位表面影响最小
19 分模线布置
20 拔模方向的确定 21 浇口布置
功能定义
22 灯内温度场分布分析 23 配置及功能描述、控制逻辑
分模线的布置对可见部位表面影响最小,或者符合效果图定义 分析出模方向上不得存在负角,或脱模角过小,与周边配合件的拔模方向一致,保证间隙均匀 浇口尽量布置在不可见部位,且对可见部位表面影响最小
灯内热态分布情况是否满足材料要求 定义灯具的功能及每个功能的控制逻辑
24 接插件 25 胶条 26 调光结构
27 材料 28 生产工艺 29 标识内容及位置 30 线束
试验
31 试验
重大历史问题
32 灯具进水问题 33 起雾
确认接插件的护套号、引脚定义、固定位置和固定方式,如是开模件,定义接插件详细尺寸 确认胶条的材料、成型工艺、长度、位置、固定方式 定义调节点的位置、数量、调节范围、调节工具、调节力矩,如果是电调,定义电机的布置位置、空载和满载的声级、电性能参数和电 压位移图 定义灯具主要部件的材料类型和供应商 确认灯具生产的主要工艺,涂胶和胶牌号定义,焊接类型 确认标识内容和位置,包括:零件名称、零件号及型号,近光灯的初始下倾值,3C号、EMARK认证号,生产日期及批次、吉利标识和 厂家代码 确认线束的性能要求和耐温性能,定义线束的走向、固定和保护
定义灯具的试验项目及试验标准
前大灯的防水校核:确定后盖、调光机构、通气孔、接插件、灯泡座、胶槽等关键部位尺寸和公差;确定O型圈的材料、硬度和压缩量; 通气孔位置分布合理; 前大灯的防水校核:首先校核密封性;检查通气孔位置分布合理性;检查饰圈与灯罩、壳体间隙;考虑喷防雾漆的必要性
车身项目Checklist(检查清单)的应用方法
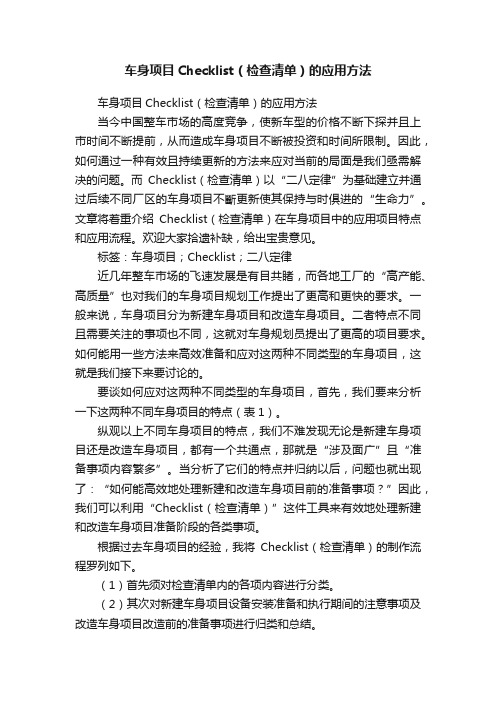
车身项目Checklist(检查清单)的应用方法车身项目Checklist(检查清单)的应用方法当今中国整车市场的高度竞争,使新车型的价格不断下探并且上市时间不断提前,从而造成车身项目不断被投资和时间所限制。
因此,如何通过一种有效且持续更新的方法来应对当前的局面是我们亟需解决的问题。
而Checklist(检查清单)以“二八定律”为基础建立并通过后续不同厂区的车身项目不斷更新使其保持与时俱进的“生命力”。
文章将着重介绍Checklist(检查清单)在车身项目中的应用项目特点和应用流程。
欢迎大家拾遗补缺,给出宝贵意见。
标签:车身项目;Checklist;二八定律近几年整车市场的飞速发展是有目共睹,而各地工厂的“高产能、高质量”也对我们的车身项目规划工作提出了更高和更快的要求。
一般来说,车身项目分为新建车身项目和改造车身项目。
二者特点不同且需要关注的事项也不同,这就对车身规划员提出了更高的项目要求。
如何能用一些方法来高效准备和应对这两种不同类型的车身项目,这就是我们接下来要讨论的。
要谈如何应对这两种不同类型的车身项目,首先,我们要来分析一下这两种不同车身项目的特点(表1)。
纵观以上不同车身项目的特点,我们不难发现无论是新建车身项目还是改造车身项目,都有一个共通点,那就是“涉及面广”且“准备事项内容繁多”。
当分析了它们的特点并归纳以后,问题也就出现了:“如何能高效地处理新建和改造车身项目前的准备事项?”因此,我们可以利用“Checklist(检查清单)”这件工具来有效地处理新建和改造车身项目准备阶段的各类事项。
根据过去车身项目的经验,我将Checklist(检查清单)的制作流程罗列如下。
(1)首先须对检查清单内的各项内容进行分类。
(2)其次对新建车身项目设备安装准备和执行期间的注意事项及改造车身项目改造前的准备事项进行归类和总结。
(3)Checklist(检查清单)必须与时俱进,不断更新,将各厂区车身项目发生的一些特有的需要注意的事项进行实时添加。
产线设备和工艺验收checklist(浓缩版)

工序项目裁剪房温湿度裁剪尺寸开孔焊接参数焊接外观拉托力层压机EL EL图片直角焊接间距返工区域层压参数温度偏差剥离力真空度交联率接线盒打胶非自动益胶补胶的胶量自动溢胶的总胶量接线盒焊接温度AB胶配比rate of A and B inweight 自动串焊机裁剪层压机叠层装框标准温度范围为23+/-3℃,湿度小于30~70RH%;3mmfollow作业指导书无锡珠、毛刺,表面清洁,无明显助焊剂;无空焊、虚焊、侧焊、过焊、破片;焊带与电池片主栅线错位≤0.5mm≥2N-焊接标准见作业指导书见60和72pcs间距要求,和胶带贴方式串焊返工不良区域均需要有吸盘实测温度与设定温度的误差-1℃~+2℃以内 ;±3℃EVA和背板≥40NEVA和玻璃≥40N120s内真空度达到100pa以下80~95%接头处预留5~7mm,400+/-15℃AB胶配比标准,回天5299W-S,质量比A:B为5:1,质量比值范围4.8~5.2;天山1533,质量比A:B为5.5:1,质量比值范围5.3~5.7;天辰HT6360/AB,质量比A:B为5.5:1,质量比值范围5.3~5.7 ;要求Y/N备注温湿度要求24h均达到分别记录裁剪样品量50pcs,按照点检表单以样品为准,无毛刺,光滑满足作业指导书中焊接温度等参数要求工废建议值≤0.2%正反面EL图片清晰可见要求员工熟练要求层压后无间距不良(此为重点关注)要求员工手不能拿电池片在层压要求的范围内,满足要求,I区域: A≤2mm2,Q≤2E区域: A≤2mm2,Q≤3距玻璃边沿5mm,距电池片边缘0.3mm,电池片上,都不允许有气泡,无鼓包;不允许有尖锐物造成之穿刺性凹坑,无破损、孔洞及任何尺寸的带电体伸出背板,无污迹、硅胶、EVA、纸屑等残留,无水印;分别是使用长杆和多路测温仪进行温度监控层压机4个位置均要做层压机4个位置的交联率均要做按照接线盒轨迹设定好程序型材内框打胶两侧空留≤5mm;底部铺满,总胶量≥65ml;边框型材打胶,平铺槽底深度2-3mm拆框后型材底部均有胶量,并且四周均匀益胶要求灌胶设备能打达到上述参数要求。
(最新)汽车内外饰工艺数据checklist
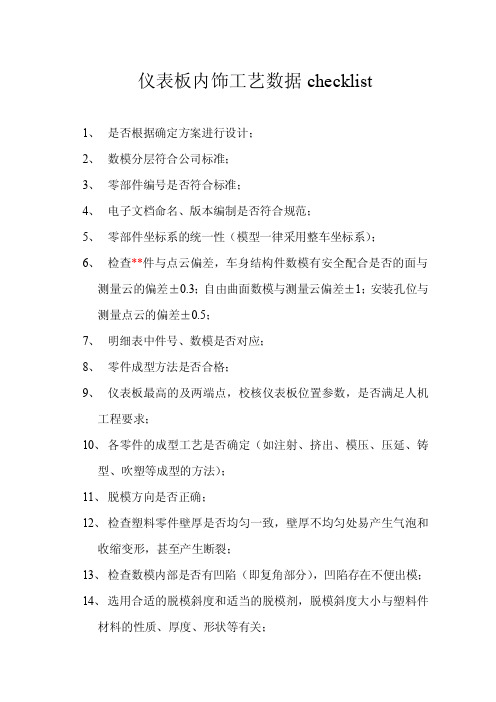
仪表板内饰工艺数据checklist1、是否根据确定方案进行设计;2、数模分层符合公司标准;3、零部件编号是否符合标准;4、电子文档命名、版本编制是否符合规范;5、零部件坐标系的统一性(模型一律采用整车坐标系);6、检查**件与点云偏差,车身结构件数模有安全配合是否的面与测量云的偏差±0.3;自由曲面数模与测量云偏差±1;安装孔位与测量点云的偏差±0.5;7、明细表中件号、数模是否对应;8、零件成型方法是否合格;9、仪表板最高的及两端点,校核仪表板位置参数,是否满足人机工程要求;10、各零件的成型工艺是否确定(如注射、挤出、模压、压延、铸型、吹塑等成型的方法);11、脱模方向是否正确;12、检查塑料零件壁厚是否均匀一致,壁厚不均匀处易产生气泡和收缩变形,甚至产生断裂;13、检查数模内部是否有凹陷(即复角部分),凹陷存在不便出模;14、选用合适的脱模斜度和适当的脱模剂,脱模斜度大小与塑料件材料的性质、厚度、形状等有关;15、载塑料零件上,是否避免锐角及直角过渡;16、安装方式是否正确;17、正确的选择定位尺寸基准,应尽可能使设计基准和工艺基准重合,避免装配过程中,误差的积累过大;18、经常所装的零部件,为了更换方便,应以螺栓成自攻螺钉和簧片螺母配合紧固连接;19、明确安装工具,预留所需的被动空间;20、在安装过程中,需要进行装配调整的零部件要考虑孔位的合理布置及适当地预留间隙调整;21、考虑到仪表板内线束的固定,明确线卡固定点及固定方式,钣金上的线束的过孔是否加以保护套成翻边结构;22、检查保险杆外表面在X方向是否有负面保证模具成型后外表面的完整和美观;23、检查外表面面与面的偏差是否超标;24、检查外表面可增厚性;25、检查零件的强度是否适当,是否有强度薄弱的区域(薄弱的区域需增加加强筋);26、检查零件的材料选用是否适当(如毛面需要镀铬地零件应选用同ABS等可镀铬材料,不能选用PP难镀的材料;27、在塑料件结构设计中,为避免转角处应刀集中,应采用圆弧过渡,这对于模具制造及使用寿命足很有利的;28、对于保险杆要进行相关国家法规的检查(接近角、离车角等);29、检查零件开孔的合理性,孔一般设计成通孔,避免¢5以下盲孔,盲孔底部应设计成半球面或圆锥面,以利物料流动、孔径与深度比一般为1∶2或1∶3 ;30、检查前保险杆与翼子板的间隙是否合适(与翼子板间隙,轿车1—3mm);31、检查前保险杆与前大灯的间隙【与前大灯的间隙:2.5(下限为2.5大小)—4mm】;32、检查前保险杆与发动机舱盖间隙(与发动机舱盖间隙:8—15mm);33、检查保险杆与雾灯的间隙(与雾灯的间隙:2—3mm);34、检查结构设计完成的外饰件的周边与车身的间隙是否与外表面上所给的间隙一致;35、检查数模是否已经装配好,并且装配是根据明细表来装配,是否已经装了标准件,装配数模中是否有多余的点、线、面(装配数模中不允许有的参数);36、剖断面检查总成内部零件装配是否可靠,间隙是否合理适当,是否有干涉现象(安装点的位置及零件间搭接部位是重点剖吻得部位);37、在外饰上很对筋除加强的作用外,有的还起到了支撑外面的作用,检查这些筋与钣金的合理间隙;38、检查保险杆两端与挡泥板连接的翻边是否太长,原则上满足安装点的空间就可以了,太宽了对模具不利;39、检查加强筋的宽度是都适当,表面是否出现缩痕的危险;40、检查外饰件在车身的安装点是否对应,装配面是否贴合,安装孔的开孔方式是否合理(该开腰形孔的不能开圆孔);41、检查外饰件在车身的安装点是否合理,总体强度是否足够,与车身的装配是否合理;对于安装点,安装时人手的可接近性是否好,气枪或套筒扳手是否有空间;42、对于零件总成(如保险杠),检查总成内零件的装配是否合理,零件间是否靠谱,定位是否准确;43、检查外饰件表面是否有足够高的弧高,尤其装饰条等零件,其表面弧高要66车身外表面大;44、检查通风盖板与发动机盖内外板的间隙大小是否合理,间隙是否均匀;45、检查通风盖板与风窗玻璃的关系是否合理;46、检查通风盖板与风刮的关系是否合理,检查雨刮在两个极限位置时是否与通风盖板干涉;47、检查通风盖板两端与发动机白色铰链的关系是否合理,是否有干涉;48、对于车身表面的装饰条,如果是粘接上的,检查粘接面大小是否足够,粘接间隙是否留出;49、检查通风盖板两侧与发动机舱两端的关系是否合理,是否有干涉;50、检查挡泥板与轮胎包络线的间隙是否合理;51、检查挡泥板与车身及悬架等零件是否存在干涉,与车身是否有很好的贴近性;52、检查散热器的功能性,设计时要考虑散热器前面开口面积,风扇倾斜带来的空气流入量的变化及前面看时发动机室内部的遮蔽性;53、散热器罩通常表面需要镀铬,镀铬与非镀铬表面有明显的分界,检查部门镀铬地可能性;54、检查后保险杠与排气管的间隙是否合理;55、检查后保险杠与后行李盖的间隙(通常为:8—15mm ,应多测量一些车,取平均值);56、检查保险杠与倒车雷达装配是否合理可靠,倒车雷达分布是否合理;57、检查保险杠与防撞杆的关系是否合理;58、检查保险杠上牌照空间是否足够,以及牌照安装孔是否对称;59、检查零件通用性,能对称尽量做对称件,能合并一个件尽量合并一个件;60、外饰件孔径尺寸要调整,边缘要光顺;61、筋的壁厚要小于料厚的二分之一,表面做皮纹件拔横角大于5°;62、A柱护板与前风挡玻璃间隙3—4mm(轿车),6—8mm(MPV、SUV等);63、A柱护板材料:PP、P/E等,料厚:2.5—3mm ;64、A柱护板与A柱内板之间,应留足够线束(或洗涤液管)通过的空间一般留有16*14的截面空间;65、A柱护板在前门柜处通过密封条压住,A柱护板允许密封条压入留间隙0.5—1mm ;66、A柱护板压在密封条下,为使密封条对A柱护板有一定的压力,A柱护柱侧面斜角应该大于密封条压边自然状态下的角度,约20度左右;67、A柱护板通过卡口连接到A柱内板上,A柱内板应该起凸坑,其过孔表面法向于卡扣中心轴线平行,卡扣弹性球面回弹量0.5mm ;68、A柱护板在上部,压在顶蓬上,不留间隙,压边重叠宽度应大于20mm ;69、A柱护板在上部,压在仪表板上,仪表板若为注塑件,两者之间间隙1—2mm ,若为发泡件,应根据发泡件压缩量计算间隙;70、B柱护板材料:PP、P/E、PE等,料厚一般为:2.5—3mm ;71、B柱护板成型方式:一般为注塑;72、B柱上护板5B柱内板之间,应留足前座椅安全带升降器总成的空间,B柱下护板与B柱加强板之间安装安全带卷缩器,B柱下护板与B柱内板距离16—18mm ,B柱下护板与B柱加强板距离18—22mm ;73、B柱护板在门柜处,通过密封条压住,B柱护板应允许密封条压入留间隙0.5—1mm ;74、为使密封条对B柱护板有一定压力,B柱护板侧面斜条应大于密封条压边白丝状态下角度20度左右;75、B柱上护板压在顶蓬上,不留间隙,压边重叠宽度应大于20mm ;76、C柱护板材料:PP、P/E、PE等,料厚:2.5—3mm ;77、C柱护板与三角窗玻璃(后风挡玻璃)之间间隙3—4mm (轿车),6—8mm(MPV、SUV),多测一些车,取一个平均值;78、C柱护板与C柱内板及加强板之间不小于5mm ;79、C柱护板通过卡扣装到C柱内板上,C柱内板上立起凸台(凹坑),凸台平面法线与卡扣中心线方向平行,卡扣弹性球面回弹量0.5mm ,侧位压缩量0.75mm ;80、C柱护板压在顶蓬上,不留间隙,压边重叠宽度大于20mm ;81、前门内护板总成材料,前门装饰板材料一般为:PP、ABS、PE、麻毡+PBM发泡+PVC表皮等,料厚:2.5—3mm ;前门三角护板材料:PP、ABS、PE等,料厚:2.5—3mm ;扶手材料:PP、DA 等,前门地图袋、前门喇叭材料一般为:PP、ABS等,料厚2.5—3mm ;82、前门内护板周边到前门门柜密封条间隙,6—8mm ,周边间隙均匀,在前门槛处可略大(该间隙处不可见区,略大的间隙可消除制造误差对装配的影响;83、前门内护板周边翻边压在门内板面上,不留间隙;84、前门内护板通过卡扣拉紧在门内板上,卡扣轴向回弹量0.5mm ,侧面压入压缩量0.75mm ,常用过孔¢8(¢5)卡扣压入端,大径¢9.5(¢8),括号内尺寸为推荐使用的变形补偿卡扣;85、前门内护板内有防水膜,在防水膜粘胶区,内护板应保持均匀间隙4—5mm ;86、在内板上若留有内护板压槽,内护板翻边与槽边缘应有均匀间隙;87、前门内护板与仪表板配合处间隙6—8mm ,要求间隙均匀;88、前门内护板与前座椅之间距离不小于16mm ,应多测一些车,取平均值;89、前门内护板与门内板之间最小间隙大于4mm ;90、门内开拉手、车门把手及门窗玻璃升降器按钮位置需要经过人机校核;91、门内开拉手、车门把手均需要螺钉(或螺栓)紧固件固定在门内板上,以手受拉力;92、后门内护板周边与后门柜密封条间隙6—8mm ,周边要求间隙均匀,在后门槛处间隙可略大(此处为不可见区,大间隙可消除制造误差对装配的影响;93、后门内护板周边翻边压在门内板面上,不留间隙;94、后门内护板通过卡扣拉紧在门内板面上,卡扣轴向压缩量0.5mm ,侧面压入压缩量0.75mm ;95、后门内护板有防水膜,在防水膜的粘胶区,内护板与内板应保持均匀间隙4—5mm ;96、后门内护板与后座椅之间间隙不小于16mm ,应多测一些汽车,取平均值;97、后门内护板与门内间隙常最小处应大于4mm ;98、背内护板材料:后门装饰板材料一般为:PP、ABS、PE等,料厚:2.5—3mm ;99、背门内板周边到后背门门柜密封条,以背门槛护板之间间隙8—10mm ,周边要求间隙均匀;100、背门内护板周边到后背门内板间距最小应大于5mm ,与后雨刮器机构间隙应大于6mm ;101、背门通过卡扣拉紧在背门内板面上,卡扣轴向球面压缩量0.5mm ,侧面压入压缩量0.75mm ;102、前门槛护板可压在背门门柜密封条上,也可压在前门柜密封条下,后者应允许密封条在门槛装好后压入,间隙0.5—1mm ;103、前门槛护板与内饰之间应留足线束通过空间,一般大于20mm ;104、顶蓬固定方式:卡扣和螺钉连接,卡扣主要用在后部起拉紧固定作用,螺钉主要在安全拉手处;105、顶棚大面大体与顶盖大面呈偏差关系(正向设计),距离12—16mm ;106、顶棚在附件位置处(如拉手、遮阳板、阅读灯等)应与内板保持3—4mm间隙,顶蓬在门柜处压在门柜密封条下,允许密封条压入,留间隙1—2mm ;107、顶棚在位于横梁处,要求与横梁表面保持3mm间隙,在其余位置顶棚与内板间隙应为12—16mm ,顶棚与侧面内板间隙大于10mm,允许线束通过,顶棚与顶盖横梁处于钣金距离3—5mm ;(安装点零距离贴合)108、在顶蓬与A、B、C柱的搭接部位应有支撑件,且支撑件要不影响线束通过;109、在前、后风挡玻璃处,顶蓬有两种连接方式,分别为粘接和密封条连接,其连接方式为密封条连接时,应注意顶蓬卡在距钣金卡槽中心位置6mm处,并存在20度夹角关系;110、地毯通过侧面护板,前后门槛板压在地板上,其压缩量为2mm ,与护板重叠部分宽度为20mm ;111、通过地毯的运动件部分用开孔,孔边界与运动件极限位置间隙5mm 。
一种汽车内外饰数据检查方法

一种汽车内外饰数据检查方法英文回答:Automotive Interior and Exterior Data Inspection Methodology.Introduction.Data inspection is a critical step in the automotive manufacturing process to ensure the quality and accuracy of the data used for design, engineering, and production. For automotive interiors and exteriors, data inspection involves verifying the dimensional accuracy, surface quality, and other attributes of the physical components against the design specifications. The following methodology provides a comprehensive approach to automotive interior and exterior data inspection.Data Collection.The first step in data inspection is to collect the necessary data from the manufacturing process. This includes:3D scan data of the physical components.Inspection reports from automated inspection systems.Manual measurements and observations.Data Processing.Once the data is collected, it is processed to prepare it for inspection. This includes:Converting 3D scan data into a point cloud.Aligning the point cloud to the design model.Filtering and cleaning the data to remove noise and outliers.Data Inspection.The processed data is then inspected against the design specifications using a variety of techniques:Dimensional Accuracy.Compare the measured dimensions to the target dimensions.Identify any deviations outside of the tolerance limits.Surface Quality.Inspect the surface for defects such as scratches, dents, or warps.Measure the surface roughness and compare it to the specified range.Other Attributes.Check for proper assembly and fit.Verify the presence and correct placement of all components.Inspect for any non-conformities or deviations from the design.Inspection Tools.The tools used for data inspection include:3D scanning systems.Automated inspection machines.Measuring devices.Inspection software.Inspection Report.The results of the data inspection are documented in an inspection report. The report includes:A summary of the inspection findings.A list of any non-conformities or deviations.Recommendations for corrective actions.Data Inspection Workflow.The following diagram illustrates the typical workflow for automotive interior and exterior data inspection:[Diagram: Data Inspection Workflow]Benefits of Data Inspection.Data inspection provides numerous benefits for automotive manufacturing:Ensures the accuracy and quality of the data used for design and production.Reduces the risk of errors and defects in the final product.Improves communication between design, engineering, and production teams.Streamlines the production process and reduces production time.Protects brand reputation and customer satisfaction.Conclusion.Automotive interior and exterior data inspection is a critical quality control process that verifies the dimensional accuracy, surface quality, and other attributes of the physical components against the design specifications. By following a comprehensive methodology, manufacturers can ensure the reliability, safety, andperformance of their vehicles.中文回答:汽车内外饰数据检查方法。
汽车通用提车检查表checklist
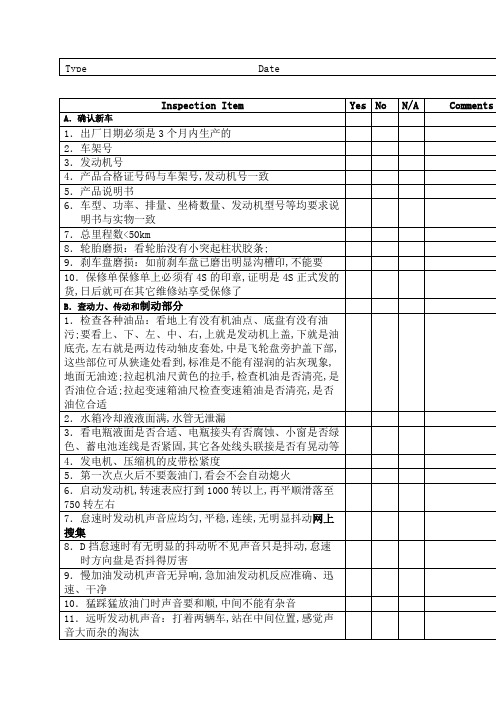
1. 大灯远光、近光,左右前照灯灯光强度、角度是否一致
2. 方向灯、故障警告灯:6个都看前、后、左、右、两侧后视镜
3. 前、后雾灯
4. 刹车灯,包括高位刹车灯
5. 倒车灯
F.试驾并接车
1. 加93汽油约50升
2. 调好驾驶员座椅和三个后视镜
3. 试刹车:仔细体会刹车踏板踩下去的深浅变化和制动力大小的关系
2.水箱冷却液液面满,水管无泄漏
3.看电瓶液面是否合适、电瓶接头有否腐蚀、小窗是否绿色、蓄电池连线是否紧固,其它各处线头联接是否有晃动等
4.发电机、压缩机的皮带松紧度
5.第一次点火后不要轰油门,看会不会自动熄火
6.启动发动机,转速表应打到1000转以上,再平顺滑落至750转左右
7.怠速时发动机声音应均匀,平稳,连续,无明显抖动网上搜集
12.查看真皮座椅有无开裂小口子
13.试验安全带功能,快速拉动安全带,应该会卡死拉不动
14.试内后视镜、遮阳挡板及开关
15.测试后窗电加热除霜功能,后雨刮
16.熄火后试听CD音响和收音机功能:换碟、AM/FM、选台、音量、各个按钮
17.点火后音响有无高频交流声熄火时没有的
18.CD播放时开大灯不能连续播放网上搜集
8. 检查随车配件是否齐全,特别是产品说明书、千斤顶、工具包
9. 试驾一段路程再上快速主路,关键是要先熟悉一下车性
10. 头500公里以内车速应控制在80km/h以下,发动机转速不要超过3000rpm
InspectionItem
Yes
No
N/A
Comments
A.确认新车
1.出厂日期必须是3个月内生产的
2.车架号
3.发动机号
外观制程checklist

稽核状态பைடு நூலகம்
下侧2PCS螺钉锁付滑落干涉机箱R角掉漆
物流车上侧取面板,导致面板两两刮蹭干涉 安装过程未以定位基准盲扣导致面板与箱体刮蹭 传动过程测试端口刮蹭箱体箱体 端口盲插导致机箱测试口外观不良 老化上架未按区间摆放且作业时箱体间未保留间隙导致干涉 老化架泡棉档板缺失或防护失效 上下架流水线未按网格摆放 老化测试U盘周转盒及电源线干涉机箱 机箱直接放置维修桌面、侧面板外观面朝下放置旧面 机箱打散物料干涉壳体 维修台面工具干涉壳体 手工抬板跳入下工节点导致机箱移位或干涉 不良品货架未按区间摆放导致机箱干涉 单件中转未使用托盘及其它防护板 机箱整套未安装到位周转导致过程脱落干涉
观制程checklist
制程管控 栈板禁止批量摘除保护袋,执行摘除一个上线一个 电批用完禁止放置桌面或插入台面周转泡棉 按节拍生产,依旧面线体放置位或标识网格线放置,禁止多外产品追尾式推动 检验岗位光照度满足,禁止灭灯作业 分检上车禁止同时拿取多件产品 轨道线首板位禁止投入产品 物流架上禁止同时拿取多件产品,取机箱一个上线一个 机箱上线要求以传送板两角定位基准摆放
定位治具用后放置指定区域
安装完成主板确认机箱与传送板放置位置并摆正
电批用完复位,禁止摆放或暂放轨道作业区域内 要求100%正确使用防护盖板,用后放置指定区域 要求先穿线缆完成后再依定位柱固定钢片,避免钢片干涉外箱 传递板面禁止暂放螺钉,出现螺钉掉落需立即清理后方可继续作业 禁止手持扣合笔挪动机箱
依节拍作业,当岗位控制踏板作业,
工段
岗位
物流拆箱 线
机箱拆箱
机箱投入
组装
机箱粘贴导 电泡棉 主板安装至 机箱 人工补打螺 钉岗位 组装主副天 线
扣合WIFI模 组RF端子
很全的汽车内外饰设计资料
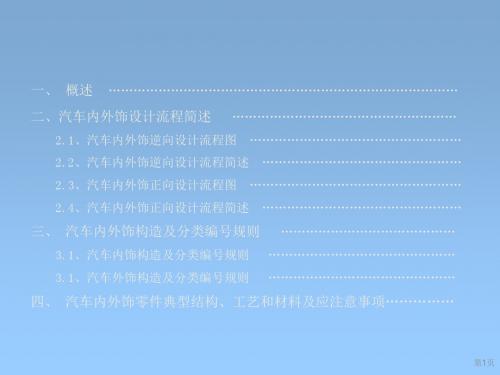
手套箱总成
手套箱一般位于仪表台副驾驶侧的中下位置。手套箱一般由手套箱门、箱体、手套箱附件组成。 手套箱门一般由外板和内板组成,他们之间采用震动摩檫焊、热板焊和螺钉固定。 手套箱储物空间一般有两种形式,固定式和翻斗式。
翻斗式手套箱,储物空间在门上,打开时与内斗一起翻 出来,便于取物,但空间有限。
固定式手套箱,基本结构与翻斗式差不多, 只是内板上不带斗,储物空间做在手套箱 箱体上,能提供较大的储物空间,且能布 置手套箱灯等附件。
主仪表台总成 仪表台总成是内饰中结构和制造工艺最复杂的组件。车上各种驾驶仪表、操控踏板、控制开关、空 调、音响娱乐系统、安全气囊等附件都是安装在仪表板本体和管梁上。 仪表台通常由仪表台本体、组合仪表罩、中控面板、手套箱、风口、烟灰盒、储物盒等零件组成。
第10页
仪表台本体 仪表台本体按其表面质感可分为硬质仪表台和软质仪表台。
尼龙针刺地毯没有EVA重涂层和无纺布,采用热压工艺成型。 PVC地毯没有EVA重涂层和无纺布,同样采用热压工艺成型。 目前簇绒地毯和针刺地毯在成型后多采用水切割工艺来加工边界和开口。
汽车内饰地毯总成零件结构设计注意事项
1:地毯的颜色:地毯的颜色是整个内饰系统颜色的重要组成部分,要满足整个内饰系统的要求。为满足耐脏要求, 颜色一般为深色,只有在使用条件比较良好的豪华车上才使用浅色。 2:地毯的环境和安全要求:环境要求包括使用温度(热带和寒带),尘土、湿度、耐腐蚀性、和色牢度等。地毯 还要满足内饰材料的燃烧性。 3:地毯的质量要求:一般要求是小于10KG,太重会导致安装不方便,不能满足人机工程要求。(为提高舒适感和 良好的隔声\吸音性能,地毯背面还有PU发泡层,这样会导致地毯太重,这样就需要将地毯分块。 4:地毯的定位及与周边钣金的配合:地毯一般由型面贴合钣金定位,必要时可增加固定件。地毯的制造公差较大 (包括型面公差和边界公差),所以地毯设计时在前后、左右方向与钣金和线束等零件应保留适当的距离,否则会产 生褶皱。对于地毯上面的覆盖件,如门槛饰板、副仪表台等,设计时需要与地毯留足够的搭接边与过盈量,保证地毯 被踩踏后不会露出毛边和间隙。
- 1、下载文档前请自行甄别文档内容的完整性,平台不提供额外的编辑、内容补充、找答案等附加服务。
- 2、"仅部分预览"的文档,不可在线预览部分如存在完整性等问题,可反馈申请退款(可完整预览的文档不适用该条件!)。
- 3、如文档侵犯您的权益,请联系客服反馈,我们会尽快为您处理(人工客服工作时间:9:00-18:30)。
仪表板内饰工艺数据checklist1、是否根据确定方案进行设计;2、数模分层符合公司标准;3、零部件编号是否符合标准;4、电子文档命名、版本编制是否符合规范;5、零部件坐标系的统一性(模型一律采用整车坐标系);6、检查**件与点云偏差,车身结构件数模有安全配合是否的面与测量云的偏差±0.3;自由曲面数模与测量云偏差±1;安装孔位与测量点云的偏差±0.5;7、明细表中件号、数模是否对应;8、零件成型方法是否合格;9、仪表板最高的及两端点,校核仪表板位置参数,是否满足人机工程要求;10、各零件的成型工艺是否确定(如注射、挤出、模压、压延、铸型、吹塑等成型的方法);11、脱模方向是否正确;12、检查塑料零件壁厚是否均匀一致,壁厚不均匀处易产生气泡和收缩变形,甚至产生断裂;13、检查数模内部是否有凹陷(即复角部分),凹陷存在不便出模;14、选用合适的脱模斜度和适当的脱模剂,脱模斜度大小与塑料件材料的性质、厚度、形状等有关;15、载塑料零件上,是否避免锐角及直角过渡;16、安装方式是否正确;17、正确的选择定位尺寸基准,应尽可能使设计基准和工艺基准重合,避免装配过程中,误差的积累过大;18、经常所装的零部件,为了更换方便,应以螺栓成自攻螺钉和簧片螺母配合紧固连接;19、明确安装工具,预留所需的被动空间;20、在安装过程中,需要进行装配调整的零部件要考虑孔位的合理布置及适当地预留间隙调整;21、考虑到仪表板内线束的固定,明确线卡固定点及固定方式,钣金上的线束的过孔是否加以保护套成翻边结构;22、检查保险杆外表面在X方向是否有负面保证模具成型后外表面的完整和美观;23、检查外表面面与面的偏差是否超标;24、检查外表面可增厚性;25、检查零件的强度是否适当,是否有强度薄弱的区域(薄弱的区域需增加加强筋);26、检查零件的材料选用是否适当(如毛面需要镀铬地零件应选用同ABS 等可镀铬材料,不能选用PP难镀的材料;27、在塑料件结构设计中,为避免转角处应刀集中,应采用圆弧过渡,这对于模具制造及使用寿命足很有利的;28、对于保险杆要进行相关国家法规的检查(接近角、离车角等);29、检查零件开孔的合理性,孔一般设计成通孔,避免¢5以下盲孔,盲孔底部应设计成半球面或圆锥面,以利物料流动、孔径与深度比一般为1∶2或1∶3;30、检查前保险杆与翼子板的间隙是否合适(与翼子板间隙,轿车1—3mm);31、检查前保险杆与前大灯的间隙【与前大灯的间隙:2.5(下限为2.5大小)—4mm】;32、检查前保险杆与发动机舱盖间隙(与发动机舱盖间隙:8—15mm);33、检查保险杆与雾灯的间隙(与雾灯的间隙:2—3mm);34、检查结构设计完成的外饰件的周边与车身的间隙是否与外表面上所给的间隙一致;35、检查数模是否已经装配好,并且装配是根据明细表来装配,是否已经装了标准件,装配数模中是否有多余的点、线、面(装配数模中不允许有的参数);36、剖断面检查总成内部零件装配是否可靠,间隙是否合理适当,是否有干涉现象(安装点的位置及零件间搭接部位是重点剖吻得部位);37、在外饰上很对筋除加强的作用外,有的还起到了支撑外面的作用,检查这些筋与钣金的合理间隙;38、检查保险杆两端与挡泥板连接的翻边是否太长,原则上满足安装点的空间就可以了,太宽了对模具不利;39、检查加强筋的宽度是都适当,表面是否出现缩痕的危险;40、检查外饰件在车身的安装点是否对应,装配面是否贴合,安装孔的开孔方式是否合理(该开腰形孔的不能开圆孔);41、检查外饰件在车身的安装点是否合理,总体强度是否足够,与车身的装配是否合理;对于安装点,安装时人手的可接近性是否好,气枪或套筒扳手是否有空间;42、对于零件总成(如保险杠),检查总成内零件的装配是否合理,零件间是否靠谱,定位是否准确;43、检查外饰件表面是否有足够高的弧高,尤其装饰条等零件,其表面弧高要66车身外表面大;44、检查通风盖板与发动机盖内外板的间隙大小是否合理,间隙是否均匀;45、检查通风盖板与风窗玻璃的关系是否合理;46、检查通风盖板与风刮的关系是否合理,检查雨刮在两个极限位置时是否与通风盖板干涉;47、检查通风盖板两端与发动机白色铰链的关系是否合理,是否有干涉;48、对于车身表面的装饰条,如果是粘接上的,检查粘接面大小是否足够,粘接间隙是否留出;49、检查通风盖板两侧与发动机舱两端的关系是否合理,是否有干涉;50、检查挡泥板与轮胎包络线的间隙是否合理;51、检查挡泥板与车身及悬架等零件是否存在干涉,与车身是否有很好的贴近性;52、检查散热器的功能性,设计时要考虑散热器前面开口面积,风扇倾斜带来的空气流入量的变化及前面看时发动机室内部的遮蔽性;53、散热器罩通常表面需要镀铬,镀铬与非镀铬表面有明显的分界,检查部门镀铬地可能性;54、检查后保险杠与排气管的间隙是否合理;55、检查后保险杠与后行李盖的间隙(通常为:8—15mm,应多测量一些车,取平均值);56、检查保险杠与倒车雷达装配是否合理可靠,倒车雷达分布是否合理;57、检查保险杠与防撞杆的关系是否合理;58、检查保险杠上牌照空间是否足够,以及牌照安装孔是否对称;59、检查零件通用性,能对称尽量做对称件,能合并一个件尽量合并一个件;60、外饰件孔径尺寸要调整,边缘要光顺;61、筋的壁厚要小于料厚的二分之一,表面做皮纹件拔横角大于5°;62、A柱护板与前风挡玻璃间隙3—4mm(轿车),6—8mm(MPV、SUV 等);63、A柱护板材料:PP、P/E等,料厚:2.5—3mm;64、A柱护板与A柱内板之间,应留足够线束(或洗涤液管)通过的空间一般留有16*14的截面空间;65、A柱护板在前门柜处通过密封条压住,A柱护板允许密封条压入留间隙0.5—1mm;66、A柱护板压在密封条下,为使密封条对A柱护板有一定的压力,A柱护柱侧面斜角应该大于密封条压边自然状态下的角度,约20度左右;67、A柱护板通过卡口连接到A柱内板上,A柱内板应该起凸坑,其过孔表面法向于卡扣中心轴线平行,卡扣弹性球面回弹量0.5mm;68、A柱护板在上部,压在顶蓬上,不留间隙,压边重叠宽度应大于20mm;69、A柱护板在上部,压在仪表板上,仪表板若为注塑件,两者之间间隙1—2mm,若为发泡件,应根据发泡件压缩量计算间隙;70、B柱护板材料:PP、P/E、PE等,料厚一般为:2.5—3mm;71、B柱护板成型方式:一般为注塑;72、B柱上护板5B柱内板之间,应留足前座椅安全带升降器总成的空间,B柱下护板与B柱加强板之间安装安全带卷缩器,B柱下护板与B柱内板距离16—18mm,B柱下护板与B柱加强板距离18—22mm;73、B柱护板在门柜处,通过密封条压住,B柱护板应允许密封条压入留间隙0.5—1mm;74、为使密封条对B柱护板有一定压力,B柱护板侧面斜条应大于密封条压边白丝状态下角度20度左右;75、B柱上护板压在顶蓬上,不留间隙,压边重叠宽度应大于20mm;76、C柱护板材料:PP、P/E、PE等,料厚:2.5—3mm;77、C柱护板与三角窗玻璃(后风挡玻璃)之间间隙3—4mm (轿车),6—8mm(MPV、SUV),多测一些车,取一个平均值;78、C柱护板与C柱内板及加强板之间不小于5mm;79、C柱护板通过卡扣装到C柱内板上,C柱内板上立起凸台(凹坑),凸台平面法线与卡扣中心线方向平行,卡扣弹性球面回弹量0.5mm,侧位压缩量0.75mm;80、C柱护板压在顶蓬上,不留间隙,压边重叠宽度大于20mm;81、前门内护板总成材料,前门装饰板材料一般为:PP、ABS、PE、麻毡+PBM发泡+PVC表皮等,料厚:2.5—3mm;前门三角护板材料:PP、ABS、PE等,料厚:2.5—3mm;扶手材料:PP、DA等,前门地图袋、前门喇叭材料一般为:PP、ABS等,料厚2.5—3mm;82、前门内护板周边到前门门柜密封条间隙,6—8mm,周边间隙均匀,在前门槛处可略大(该间隙处不可见区,略大的间隙可消除制造误差对装配的影响;83、前门内护板周边翻边压在门内板面上,不留间隙;84、前门内护板通过卡扣拉紧在门内板上,卡扣轴向回弹量0.5mm,侧面压入压缩量0.75mm,常用过孔¢8(¢5)卡扣压入端,大径¢9.5(¢8),括号内尺寸为推荐使用的变形补偿卡扣;85、前门内护板内有防水膜,在防水膜粘胶区,内护板应保持均匀间隙4—5mm;86、在内板上若留有内护板压槽,内护板翻边与槽边缘应有均匀间隙;87、前门内护板与仪表板配合处间隙6—8mm,要求间隙均匀;88、前门内护板与前座椅之间距离不小于16mm,应多测一些车,取平均值;89、前门内护板与门内板之间最小间隙大于4mm;90、门内开拉手、车门把手及门窗玻璃升降器按钮位置需要经过人机校核;91、门内开拉手、车门把手均需要螺钉(或螺栓)紧固件固定在门内板上,以手受拉力;92、后门内护板周边与后门柜密封条间隙6—8mm,周边要求间隙均匀,在后门槛处间隙可略大(此处为不可见区,大间隙可消除制造误差对装配的影响;93、后门内护板周边翻边压在门内板面上,不留间隙;94、后门内护板通过卡扣拉紧在门内板面上,卡扣轴向压缩量0.5mm,侧面压入压缩量0.75mm;95、后门内护板有防水膜,在防水膜的粘胶区,内护板与内板应保持均匀间隙4—5mm;96、后门内护板与后座椅之间间隙不小于16mm,应多测一些汽车,取平均值;97、后门内护板与门内间隙常最小处应大于4mm;98、背内护板材料:后门装饰板材料一般为:PP、ABS、PE等,料厚:2.5—3mm;99、背门内板周边到后背门门柜密封条,以背门槛护板之间间隙8—10mm,周边要求间隙均匀;100、背门内护板周边到后背门内板间距最小应大于5mm,与后雨刮器机构间隙应大于6mm;101、背门通过卡扣拉紧在背门内板面上,卡扣轴向球面压缩量0.5mm,侧面压入压缩量0.75mm;102、前门槛护板可压在背门门柜密封条上,也可压在前门柜密封条下,后者应允许密封条在门槛装好后压入,间隙0.5—1mm;103、前门槛护板与内饰之间应留足线束通过空间,一般大于20mm;104、顶蓬固定方式:卡扣和螺钉连接,卡扣主要用在后部起拉紧固定作用,螺钉主要在安全拉手处;105、顶棚大面大体与顶盖大面呈偏差关系(正向设计),距离12—16mm;106、顶棚在附件位置处(如拉手、遮阳板、阅读灯等)应与内板保持3—4mm间隙,顶蓬在门柜处压在门柜密封条下,允许密封条压入,留间隙1—2mm;107、顶棚在位于横梁处,要求与横梁表面保持3mm间隙,在其余位置顶棚与内板间隙应为12—16mm,顶棚与侧面内板间隙大于10mm,允许线束通过,顶棚与顶盖横梁处于钣金距离3—5mm;(安装点零距离贴合)108、在顶蓬与A、B、C柱的搭接部位应有支撑件,且支撑件要不影响线束通过;109、在前、后风挡玻璃处,顶蓬有两种连接方式,分别为粘接和密封条连接,其连接方式为密封条连接时,应注意顶蓬卡在距钣金卡槽中心位置6mm 处,并存在20度夹角关系;110、地毯通过侧面护板,前后门槛板压在地板上,其压缩量为2mm,与护板重叠部分宽度为20mm;111、通过地毯的运动件部分用开孔,孔边界与运动件极限位置间隙5mm。