带钢热连轧生产线自动控制系统
短流程连铸连轧成套装备的自动控制系统及其功能和特点

短流程连铸连轧成套装备的自动控制系统及其功能和特点随着工业化进程的不断发展,铁路、建筑、汽车等行业对高强度钢材的需求逐渐增加。
而短流程连铸连轧工艺由于其高效率、低成本的优势,成为满足这些需求的重要生产方式。
短流程连铸连轧成套装备的自动控制系统作为其中的核心组成部分,具有重要的作用。
本文将详细介绍短流程连铸连轧成套装备的自动控制系统及其功能和特点。
首先,短流程连铸连轧成套装备自动控制系统的主要功能之一是实现整个生产过程的自动化。
传统的连铸连轧工艺中,操作人员需要手动控制铸机、轧机等设备的运行,存在操作不准确、效率低下等问题。
而自动控制系统通过引入先进的控制算法和传感器技术,实现对设备各项参数的自动监测和调节,从而大大提高了生产效率和产品质量。
其次,短流程连铸连轧成套装备自动控制系统还能实现生产过程中的数据采集和分析。
通过传感器对设备运行状态、温度、速度等关键参数进行实时监测,自动控制系统能够将这些数据收集起来,并进行处理和分析。
通过对数据的分析,可以发现生产过程中的潜在问题,并及时采取相应的措施进行调整,从而降低了生产事故的发生率,提高了工作安全性。
与此同时,短流程连铸连轧成套装备自动控制系统还具有良好的系统稳定性和可靠性。
在生产过程中,自动控制系统具有快速响应的特点,能够在毫秒级的时间内对设备进行调节和控制。
同时,自动控制系统还具备良好的抗干扰能力,能够在强电磁干扰、温度变化等复杂环境下稳定工作。
这使得自动控制系统能够适应不同的工作环境和生产要求,实现连铸连轧工艺的高质量生产。
另外,短流程连铸连轧成套装备自动控制系统还具备一定的人机交互功能。
在系统界面设计上,考虑到操作人员的使用习惯和操作需求,自动控制系统采用直观简洁的操作界面,方便操作人员对设备进行监视和调整。
操作面板上的指示灯和图形显示,能够直观地显示设备运行状态和异常情况,方便操作人员进行故障诊断和处理,提高了系统的可操作性。
此外,短流程连铸连轧成套装备自动控制系统还具有良好的灵活性和可扩展性。
带钢热连轧机组活套自动控制及应用

带钢热连轧机组活套自动控制及应用作者:晁永军孔德鸿吴胜春东四正来源:《科技资讯》2016年第12期【摘要】:活套是在金属热连轧过程用来调整轧机之间张力的最主要设备,由于金属热轧制的发展已有几十年的历程,在此过程中,随着自动化控制技术的日益提升,活套控制的精度和智能化越来越高,本文通过带钢热连轧生产线精轧机组活套的应用,对其先进的功能和作用进行了详细介绍和说明,并分别说明了活套的两种控制方法:常规PI控制和ILQ控制的原理以及在两种自动控制方法在轧制过程中的实际应用。
[关键词]:活套;常规PI控制;ILQ控制中图分类号:TG334.9 文献标识码:A 文章编号:1674-098X(2015)04(c)-0000-001.概述本文以某钢铁集团年产240万吨超薄带钢热轧生产线—UTSP热轧板带工程为例对活套先进的功能和作用进行了详细介绍和说明,其产品产品工艺规格为宽度800-1600(mm),厚度0.8-12.7(mm)的各类型热轧带钢。
主轧线分为粗轧和精轧两个机组,共有7架轧机组成,其中粗轧两架,精轧5架,各机架均采用三相同步电机传动,在F1-F5五架精轧机组之间设有4个活套。
设定活套的目的是为了确保两机架之间保持特定张力,当下游机架流量高于上游机架、下游机架速度过快时候产生张力,当下游机架速度小于上游机架时活套抬起建张,如果不设活套这一特殊设备,在轧制过程中,带钢套量将逐渐增加最终会形成折叠和扭曲,如果形成折叠或者扭曲,带钢将以好几倍的厚度进入下游机架,产生堆钢事故,最终结果会影响轧辊和轴承以及轴承支撑等机械设备以及现场传感器的寿命。
2.活套的作用介绍2.1 活套的角度给定轧制过程中活套的角度由二级计算机数据库给定,活套根据计算机数据库的给定值进行程序的最初给定,在实际轧制过程中,活套角度微调由一级基础自动化程序来计算并给定。
在一级基础自动化程序中,活套在自动操作情况下,要具备以下互锁条件:1)控制选择3)轧机主传动健康4)液压控制正常5)活套PLC系统健康6)位置传感器健康7)活套压头健康2.2 活套的张力给定活套的张力给定也是通过二级计算机系数据库进行计算,给定后,在轧制过程中,操作工在-20%到+50%之间通过每秒10%的调节度进行速度调节,在带钢生产过程中,带钢保持恒定的张力具有降低轧制力、防止轧件跑偏、改善带钢平直度、适当调节主机负荷等作用。
热连轧基础自动化的主要功能

Ethernet网络:L1各个控制器之间及L1与L2之 间的通讯。采用标准的TCP/IP通讯协议,通讯 速率100MB/s,通讯主干网络采用光缆,其它采 用屏蔽对绞电缆。 GDM(Globe Data Memory)网络:基础自 动化TDC之间的高速网络通讯。由一个中央机架 ,内装中央数据存储器组成。通过多模光缆与 TDC和IBA连接。 远程I/O:选用SIEMENS公司的ET200M,并 通过Profibus-DP现场总线与控制器连接。
3.6 精轧急停系统 S7
序 号 4
用 途 卷取及运输链 区
设备型 主要技 数 备 单位 号 术参数 量 注
4.1 卷取通用控制 TDC 4.2 1#、2#卷取 TDC 工艺控制
套 套 套
1 2 1
4.4 卷取急停系统 S7
3. 1450mm热连轧基础自动化软件 配置
• 系统软件:控制软件的开发,S7和TDC系统
• • • • • • • • •
• 加热炉区主要控制功能如下: 板坯跟踪与协调控制; 板坯长度测量及称重; 板坯自动定位; 装钢机、出钢机和步进梁控制; 加热炉炉温控制; 燃烧控制; 各种压力控制; 汽化冷却站的控制; 人机接口(HMI),用于操作、设定、维护,故障报警 和状态指示; 数据管理及数据通讯。
第2节
1450mm热连轧各区域功能 介绍
1. 加热炉区(板加区) 加热炉区基础自动化系统结构
1.1 加热炉基础自动化系统配置见图1-1:
入炉操作室
板坯库 HMI 电控 HMI 仪表 HMI 仪表 HMI
出炉操作室
汽化冷却 HMI 打印机
L2 服务器
HMI 服务器
工程师 站
工程师 站
加热炉主电室
自动化系统基本设计规格书
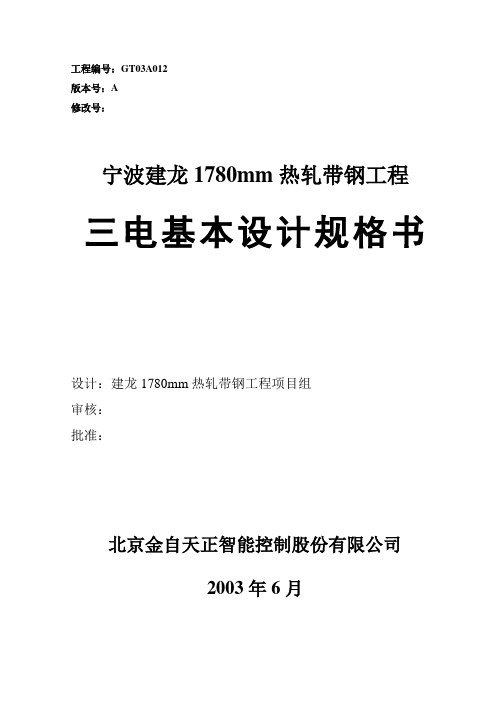
工程编号:GT03A012版本号:A修改号:宁波建龙1780mm热轧带钢工程三电基本设计规格书设计:建龙1780mm热轧带钢工程项目组审核:批准:北京金自天正智能控制股份有限公司2003年6月目录第 1 章建龙1780mm热轧带钢生产线工艺及设备................................. 1-1 1.1设计依据....................................................................................................................................... 1-1 1.2设计范围与设计原则................................................................................................................... 1-1 1.2.1.1设计范围.............................................................................................................................. 1-1 1.2.2设计原则 .................................................................................................................................. 1-1 1.3生产规模、成品大纲与金属平衡............................................................................................... 1-2 1.3.1生产规模 .................................................................................................................................. 1-2 1.3.2成品大纲 .................................................................................................................................. 1-2 1.3.3金属平衡 .................................................................................................................................. 1-4 1.4生产线主要设备组成与布置....................................................................................................... 1-4 1.5生产线工艺简述..........................................................................................................................1-10 1.5.1生产线工艺流程 .....................................................................................................................1-10 1.5.2生产线工艺与装备主要特点 .................................................................................................1-13 第 2 章自动化控制系统综述 ................................................................... 2-1 2.1自动化控制系统总体配置方案................................................................................................... 2-1 2.1.1网络系统 .................................................................................................................................. 2-1 2.1.2过程机系统 .............................................................................................................................. 2-9 2.1.3HMI设备 .................................................................................................................................2-12 2.1.3.1HMI服务器.........................................................................................................................2-12 2.1.3.2HMI ....................................................................................................................................2-12 2.1.3.3打印机.................................................................................................................................2-14 2.1.4PLC设备..................................................................................................................................2-14 2.2系统设备配置与功能分配..........................................................................................................2-18 2.2.1过程自动化系统的配置和功能 .............................................................................................2-18 2.2.2HMI服务器的配置和功能 .....................................................................................................2-20 2.2.3HMI的配置和功能 .................................................................................................................2-20 2.2.3.1L2级HMI的功能分配 ........................................................................................................2-20 2.2.3.2L1级HMI的功能分配 ........................................................................................................2-21 2.2.4基础自动化控制系统PLC、TDC 的控制功能 ..................................................................2-25 2.3轧线自动化控制系统的控制方式及非正常情况处理 ..............................................................2-33 2.3.1轧线自动化控制系统的控制方式 .........................................................................................2-332.3.2轧线的非正常情况处理 .........................................................................................................2-34 第 3 章过程自动化控制系统 ................................................................... 3-1 3.1过程控制系统功能和结构........................................................................................................... 3-1 3.1.1过程控制计算机与基础自动化级的数据通信....................................................................... 3-1 3.1.1.1过程控制计算机与HMI服务器之间的数据通讯 .............................................................. 3-1 3.1.1.2过程控制计算机与PLC之间的数据通讯........................................................................... 3-1 3.1.1.3过程控制计算机之间的数据通讯...................................................................................... 3-2 3.1.1.4过程控制计算机与数据中心计算机通讯.......................................................................... 3-2 3.1.2过程控制级系统功能 .............................................................................................................. 3-2 3.1.2.1轧制规程的设定.................................................................................................................. 3-2 3.1.2.2轧制规程的再设定.............................................................................................................. 3-2 3.1.2.3提高成品率.......................................................................................................................... 3-2 3.1.2.4提高产品质量...................................................................................................................... 3-3 3.1.2.5加快新品种、新工艺研制.................................................................................................. 3-3 3.1.3过程控制计算机结构 .............................................................................................................. 3-3 3.1.3.1数据采集子系统.................................................................................................................. 3-3 3.1.3.2轧件跟踪子系统.................................................................................................................. 3-3 3.1.3.3过程监控子系统.................................................................................................................. 3-3 3.1.3.4轧机控制子系统.................................................................................................................. 3-3 3.1.3.5实用工具软件子系统.......................................................................................................... 3-4 3.1.4过程控制计算机系统的功能说明 .......................................................................................... 3-4 3.2过程控制计算机系统数据管理................................................................................................... 3-5 3.2.1ORACLE数据库数据处理...................................................................................................... 3-5 3.2.2过程控制计算机ORACLE数据库设计 .................................................................................. 3-5 3.2.2.1过程控制计算机ORACLE数据库设计.............................................................................. 3-5 3.2.2.2数据库中数据表的组成...................................................................................................... 3-6 3.2.3过程控制计算机C++编程环境及全局变量处理 ................................................................... 3-7 3.2.4过程控制计算机启动时全局变量处理 .................................................................................. 3-8 3.2.5过程控制计算机通信数据 ...................................................................................................... 3-8 3.2.5.1过程控制计算机与基础自动化级通信数据...................................................................... 3-8 3.2.5.2过程控制计算机与操作站级通信数据.............................................................................. 3-9 3.2.6过程控制计算机启动时数据处理 .......................................................................................... 3-9 3.3过程控制计算机轧件跟踪........................................................................................................... 3-9 3.3.1过程控制计算机轧件跟踪实现方法 ...................................................................................... 3-93.3.1.1过程控制计算机轧件跟踪基本原理.................................................................................. 3-9 3.3.1.2过程控制计算机轧件跟踪实现方法.................................................................................. 3-9 3.3.1.3轧件跟踪实现方法.............................................................................................................3-10 3.3.1.4跟踪映象表的结构:.........................................................................................................3-10 3.3.1.5轧件跟踪信息的有效性检查............................................................................................. 3-11 3.3.1.6过程控制计算机轧件跟踪修正功能.................................................................................3-12 3.3.1.7过程控制计算机轧件数据库数据存取方式.....................................................................3-13 3.3.1.8过程控制计算机轧件跟踪进程功能.................................................................................3-13 3.3.1.9过程控制计算机轧件跟踪进程信号来源.........................................................................3-13 3.3.1.10过程控制计算机轧件数据库SRTCOM更新方式.............................................................3-13 3.3.1.11跟踪传感器的选择.............................................................................................................3-15 3.3.1.12跟踪修正.............................................................................................................................3-15 3.3.1.12.1轧件跟踪加热炉区跟踪事件传感器选择 ....................................................................3-15 3.3.1.12.2粗轧区跟踪区跟踪事件传感器选择 ............................................................................3-16 3.3.1.12.3精轧跟踪区跟踪事件传感器选择 ................................................................................3-16 3.3.1.12.4轧件跟踪卷取跟踪区传感器选择 ................................................................................3-16 3.3.1.13加热炉区轧件跟踪.............................................................................................................3-17 3.3.1.13.1加热炉区板坯核对 ........................................................................................................3-17 3.3.1.13.2加热炉区板坯装炉规则 ................................................................................................3-17 3.3.1.13.3加热炉入口侧跟踪方法 ................................................................................................3-18 3.3.1.13.4加热炉入口侧跟踪事件 ................................................................................................3-18 3.3.1.13.5加热炉炉内跟踪方法 ....................................................................................................3-18 3.3.1.13.6加热炉炉内跟踪事件 ....................................................................................................3-19 3.3.1.13.7加热炉炉内位置跟踪 ....................................................................................................3-19 3.3.1.13.8加热炉炉内位置跟踪修正 ............................................................................................3-20 3.3.1.13.9加热炉出炉轧件跟踪 ....................................................................................................3-21 3.3.1.13.10加热炉出炉轧件跟踪事件 ......................................................................................3-21 3.3.1.13.11加热炉强制入炉 ......................................................................................................3-21 3.3.1.13.12加热炉跟踪修正 ......................................................................................................3-21 3.3.1.14粗轧区轧件跟踪.................................................................................................................3-21 3.3.1.14.1粗轧区轧件跟踪方法 ....................................................................................................3-21 3.3.1.14.2粗轧区轧件跟踪事件 ....................................................................................................3-21 3.3.1.15精轧区轧件跟踪.................................................................................................................3-22 3.3.1.15.1精轧区轧件跟踪方法 ....................................................................................................3-223.3.1.15.2精轧区轧件跟踪事件 ....................................................................................................3-22 3.3.1.16卷取区轧件跟踪.................................................................................................................3-22 3.3.1.16.1卷取区轧件跟踪方法 ....................................................................................................3-22 3.3.1.16.2卷取区轧件跟踪事件 ....................................................................................................3-22 3.3.1.17卷取区卷取出口部分轧件跟踪.........................................................................................3-23 3.3.1.17.1过程控制计算机轧件跟踪实现方法的特点 ................................................................3-24 3.3.2轧件跟踪激活的轧线控制 .....................................................................................................3-24 3.3.2.1轧件跟踪激活的设定模型.................................................................................................3-25 3.3.2.1.1轧件位于加热炉入口时激活的设定模型 ....................................................................3-25 3.3.2.2轧件位于加热炉出口时激活的设定模型.........................................................................3-26 3.3.2.2.1轧件位于加热炉出口且实际出炉温度与轧制尺寸有效 ............................................3-26 3.3.2.2.2轧件位于加热炉出口高温计D.O.PY201激活自学习模型..........................................3-26 3.3.2.2.3轧件首次位于PY202入口时激活的设定模型 .............................................................3-26 3.3.2.2.4轧件位于E1R1粗轧末道次出口激活的设定模型 .......................................................3-26 3.3.2.2.5轧件位于LCE1 (正向)、轧件LCR1 (反向)入口激活的在线模型..............................3-26 3.3.2.2.6轧件位于LCE2 (正向)、轧件LCR2 (反向)入口激活的在线模型..............................3-26 3.3.2.2.7轧件位于E1R1末道次出口激活的在线模型 ...............................................................3-26 3.3.2.2.8轧件位于E2R2末道次出口激活的在线模型 ...............................................................3-26 3.3.2.2.9轧件位于E2R2粗轧末道次出口激活的设定模型 .......................................................3-27 3.3.2.2.10轧件位于精轧入口高温计PY302激活的设定模型 .....................................................3-27 3.3.2.2.11轧件位于精轧F1、F2、F3咬钢时激活的自适应模型................................................3-27 3.3.2.2.12轧件位于精轧F2或F3咬钢时激活的设定模型............................................................3-27 3.3.2.2.13轧件位于精轧末机架咬钢时激活的在线模型 ............................................................3-27 3.3.2.2.14轧件位于精轧出口高温计出口PY303激活模型 .........................................................3-27 3.3.2.2.15轧件位于卷取机入口高温计入口时激活的在线模型 ................................................3-27 3.3.2.2.16轧件位于卷取机入口高温计出口时激活的模型 ........................................................3-27 3.3.2.2.17卷取机出口事件激活的自学习模型 ............................................................................3-27 3.3.2.3模型输入输出.....................................................................................................................3-27 3.3.2.3.1粗轧模型设定计算输入输出 ........................................................................................3-27 3.3.2.3.2卷取机模型设定计算输入输出 ....................................................................................3-28 3.3.2.3.3精轧0次设定模型计算输入输出 ..................................................................................3-28 3.3.2.3.4精轧1次设定模型计算输入输出 ..................................................................................3-29 3.3.2.3.5精轧2次设定模型计算输入输出 ..................................................................................3-30 3.3.2.3.6层流冷却设定模型输入输出 ........................................................................................3-313.4.2轧制节奏控制的工作方式 .....................................................................................................3-33 3.4.3轧制节奏触发事件 .................................................................................................................3-34 3.4.4轧制节奏控制模型 .................................................................................................................3-34 3.5报表子系统..................................................................................................................................3-34 3.5.1生产报表 .................................................................................................................................3-35 3.5.2故障报表 .................................................................................................................................3-37 3.6过程控制计算机的监控功能......................................................................................................3-37 3.6.1报警信息 .................................................................................................................................3-37 3.6.2生产计划输入和管理 .............................................................................................................3-37 3.6.2.1轧制计划的组织和主要数据内容.....................................................................................3-37 3.6.2.2轧制计划的输入和传送.....................................................................................................3-42 3.6.3轧制计划的管理 .....................................................................................................................3-42 3.6.3.1轧制计划的编辑和显示.....................................................................................................3-43 3.6.4轧辊数据接收和存档 .............................................................................................................3-43 3.6.4.1轧辊数据输入和存档.........................................................................................................3-43 3.6.4.2轧辊数据修改.....................................................................................................................3-43 3.6.4.3轧辊数据.............................................................................................................................3-44 3.7精轧卷取区轧制规程计算及精轧卷取模型系统 ......................................................................3-44 3.7.1精轧策略 .................................................................................................................................3-44 3.7.1.1压下率方式.........................................................................................................................3-44 3.7.1.2轧制力分配方式.................................................................................................................3-44 3.7.1.3精轧轧制规程计算流程.....................................................................................................3-44 3.7.2精轧轧制规程计算 .................................................................................................................3-45 3.7.2.1精轧轧制规程计算模型结构.............................................................................................3-45 3.7.2.2精轧轧制规程计算模型表.................................................................................................3-46 3.7.3精轧轧制规程计算方法 .........................................................................................................3-47 3.7.3.1精轧轧制规程压下制度计算.............................................................................................3-48 3.7.4机架速度设定值计算 .............................................................................................................3-49 3.7.5精轧在线控制功能 .................................................................................................................3-50 3.7.5.1穿带自适应.........................................................................................................................3-50 3.7.6终轧温度的在线控制 .............................................................................................................3-50 3.7.7卷取机设定计算 .....................................................................................................................3-503.8.2精轧模型 .................................................................................................................................3-51 3.8.3卷取机模型 .............................................................................................................................3-55 3.8.4自学习方法 .............................................................................................................................3-58 3.8.4.1长期自学习.........................................................................................................................3-58 3.8.4.2短期自学习.........................................................................................................................3-58 3.9系统维护工具..............................................................................................................................3-58 3.10模拟轧钢......................................................................................................................................3-59 3.11过程控制计算机之间的通信数据..............................................................................................3-59 3.11.1加热炉过程控制计算机传送给精轧过程控制计算机信号..................................................3-59 3.11.2粗轧过程控制计算机传送给精轧过程控制计算机信号......................................................3-59 3.11.3精轧过程控制计算机传送给粗轧过程控制计算机信号......................................................3-60 3.11.4精轧过程控制计算机传送给数据中心计算机信号..............................................................3-61 3.11.5数据中心计算机传送给精轧卷取过程控制计算机信号......................................................3-61 第 4 章加热炉区基础自动化控制系统 ................................................... 4-1 4.1公共逻辑控制系统PLC101 .......................................................................................................... 4-1 4.1.1系统配置及硬件组成 .............................................................................................................. 4-1 4.1.2PLC101功能说明..................................................................................................................... 4-2 4.1.3操作台、机旁箱 ...................................................................................................................... 4-6 第 5 章粗轧区基础自动化控制系统 ....................................................... 5-15.1粗轧区公共逻辑与介质控制系统PLC201A、PLC201B ........................................................... 5-1 5.1.1PLC201A .................................................................................................................................. 5-1 5.1.1.1系统配置及硬件组成.......................................................................................................... 5-1 5.1.1.2PLC201A功能说明 ............................................................................................................. 5-2 5.1.1.3机旁操作箱、机旁控制箱.................................................................................................. 5-5 5.1.2PLC201B .................................................................................................................................. 5-5 5.1.2.1PLC201B系统配置图 ......................................................................................................... 5-5 5.1.2.2PLC201B功能说明 ............................................................................................................. 5-6 5.2粗轧E1 & R1控制系统PLC202 ................................................................................................5-10 5.2.1系统配置及硬件组成 .............................................................................................................5-10 5.2.2PLC202功能说明.................................................................................................................... 5-11 5.2.3操作台、机旁箱 .....................................................................................................................5-185.3粗轧E2 & R2区控制系统PLC203 ............................................................................................5-18 5.3.1系统配置及硬件组成 .............................................................................................................5-18 5.3.2PLC203功能说明....................................................................................................................5-19 5.3.3操作台、机旁箱 .....................................................................................................................5-25 5.4粗轧E1 & E2 AWC控制系统PLC204 .......................................................................................5-25 5.4.1系统配置及硬件组成 .............................................................................................................5-25 5.4.2PLC204功能说明....................................................................................................................5-26 5.4.3操作台、机旁箱 .....................................................................................................................5-29 5.5粗轧R2自动厚度控制系统PLC205 ............................................................................................5-29 5.5.1系统配置及硬件组成 .............................................................................................................5-29 5.5.2PLC205功能说明....................................................................................................................5-30 5.5.3操作台、机旁箱 .....................................................................................................................5-35 第 6 章精轧区自动化控制系统 ............................................................... 6-16.1飞剪控制系统PLC301.................................................................................................................. 6-1 6.1.1系统配置及硬件组成 .............................................................................................................. 6-1 6.1.2功能说明 .................................................................................................................................. 6-1 6.1.3操作台、机旁箱 ...................................................................................................................... 6-5 6.2精轧区公共逻辑及介子控制系统PLC302A、PLC302B ........................................................... 6-5 6.2.1PLC302A .................................................................................................................................. 6-5 6.2.1.1系统配置及硬件组成.......................................................................................................... 6-5 6.2.1.2功能说明.............................................................................................................................. 6-7 6.2.1.3操作台、机旁箱................................................................................................................. 6-11 6.2.1.4PLC302B ............................................................................................................................6-12 6.2.1.4.1PLC302B系统配置及硬件组成....................................................................................6-12 6.2.1.4.2PLC302B功能说明........................................................................................................6-12 6.2.1.4.3精轧液压站 ....................................................................................................................6-15 6.2.1.4.4AGC液压站 ...................................................................................................................6-15 6.2.1.4.5精轧1#稀油润滑站 ........................................................................................................6-16 6.2.1.4.6精轧2#稀油润滑站 ........................................................................................................6-16 6.2.1.4.7精轧3#稀油润滑站 ........................................................................................................6-17 6.2.1.4.8精轧4#稀油润滑站 ........................................................................................................6-17 6.3精轧速度主令及活套控制系统PLC303 .....................................................................................6-18 6.3.1系统配置及硬件组成 .............................................................................................................6-18 6.3.2功能说明 .................................................................................................................................6-18。
热连轧过程及计算机控制(L-2)

(3) 半连续式热带轧机(Semi-continuous Hot Strip Mills)(图2-3a) 粗轧机有两个以上的可逆机座,或者全部为可逆机座。
(4) 3/4连续式热带轧机(3/4 Continuous Hot Strip Mills)(图2-3c) 4座粗轧机中有一个可逆机座。
生产效率提高。 (5)热加工变形可引起组织性能的变化,以满足对产品某些组织与性能的要求。
WUST
图1-1 铁碳合金相图
WUST
热加工变形除具有上述优点,使之在生产实践中得到广泛的应用外,同其 他加工方法相比较它也有如下的不足:
(1) 对薄或细的轧件由于散热较快,在生产中保持热加工的温度条件比较 困难;
(2) 热加工后轧件的表面不如冷加工生产的尺寸精确和光洁; (3) 热加工后产品的组织及性能不如冷加工时均匀; (4) 从提高钢材的强度来看,热加工不及冷加工。
热加工变形可以认为是加工硬化和再结晶两个过程的相互重叠。在此过 程中由于再结晶能充分进行和变形时靠三向压应力状态等因素的作用,可使:
(1) 铸态金属组织中的缩孔、疏松、空隙、气泡等缺陷得到压密或焊合。 (2) 在热加工变形中可使晶粒细化和夹杂物破碎。 (3)金属在热变形过程中产生带状组织。
(5) 带卷取箱的热带轧机(图2-4)
WUST
Left Furnace Coiler
FourHight Mill
Right Furnace Coiler
Slab Feed roll
Fig.2-1 Schematic diagram of Steckel mill
GE Rx7i PLC在热连轧带钢生产线飞剪控制系统中的应用
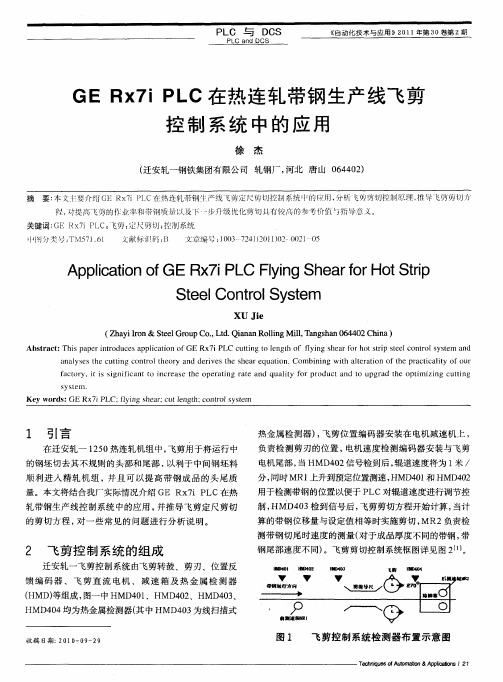
关键词 : E Rx iP 飞 ; G T i C; 定尺翦切 ; 控制系统
}冬,类 : M5 16 1 J, j T 7 .1 之献 标 识 码 : B 文 章 编 r:0 3 2 12 1)2 0 1 5 ] 10 7 4 (0 10 0 2 O ‘
Ap l aino E Rx i C ligSh a r t t p pi t f 7 c o G PL Fyn e ro r f Ho S i
s t . ysem
Ke r s GE T LC; y n h a ; u e g h; o to yse y wo d : Rx i P l f i g s e r c tln t c n r l s t m
1 引 言
在 迁安轧一 1 5 2 0热连轧机组 中, 飞剪用 于将运行 中
钢尾部速度不 同) 。飞剪 剪切 控制系统框图详见 图 21。 1 l
埔_柏 l 嘲鼬l 2 o l ‘3 ■B o
轧带钢 生产线控 制系统 中的应用 , 并推导飞剪 定尺剪切
的剪切方程 , 对一 些常见 的 问题 进行 分析说 明。
2 飞 剪 控 制 系统 的组 成
迁 安轧一 飞剪控制系统 由飞剪转 鼓 、剪 刃、位置反
Ab t a t Th s p p ri to u e p l a i n o s r c : i a e n r d c sa p i to fGE 7 LC u t g t e g h o y n h a o o ti t e o to y t m n c Rx i P c ti o ln t f f i g s e rf rh tsrp se l n r l se a d n l c s
摘
要 : 史十要介缁 G x iP C在热连轧带钢牛产线飞剪定尺 本 ER7 L
热连轧带钢自动宽度控制技术的研究
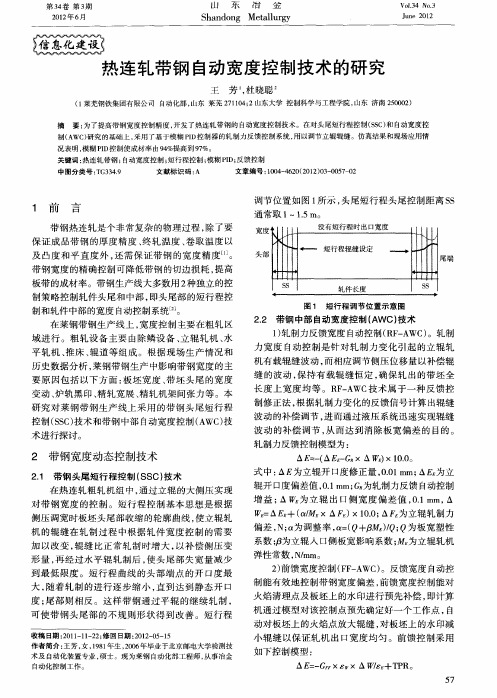
式 中 : E为立辊 开 口度 动态设定 计算值 , m; m 1 为 V
最后 道次 出 口侧 目标 宽度值 , m; m B为水平 宽展量 ,
种情 况 的取 值对 系统 响应 的影 响较 大 , 取值要 大 小适 中, 以保证 系统 响应速 度 。 3 当l较 小 即接 近于设 定值 时 , ) e l 为使 系 统有 良 好 的稳 态性 能 , 增加 和 的取 值 , 应 同时 为避 免 系统在 设定值 附近 出现振荡 , 考虑 系统 的抗干 扰 并 性 能 , 的取 值 是 相 当重 要 的 。 一 般 是 当 lI 小 ‰ e较 。 时 , 可取 大一些 ; e较 大时 ,D 取小一些 。 ‰ 当ll 。 K应
3 动 态补偿 ( S ) ) D U 。动态 设定功 能仅用 于粗轧
规则 , 最后找到最佳控制规则 , 成控制规则表 。 形 PD参数模糊 调整规则 如下 : I 1 当偏差 较大 时 , 了加 快 系统 的响应 速度 , ) 为
应取 较 大 的 K ; p同时为 了 避免 由于 开 始 时偏 差 e 的
波 动 的补 偿调 节 , 而达 到 消 除板 宽偏 差 的 目的 。 从
研究 对 莱 钢 带 钢生 产 线 上采 用 的带 钢 头尾 短 行 程
控制 ( S ) 术 和带钢 中部 自动宽 度控 制 ( WC 技 SC 技 A ) 术 进行探 讨 。
轧制力反 馈控制模 型为 :
2 带钢 宽度动态 控制技术
大, 随着 轧 制 的进 行 逐 步 缩小 , 到达 到 静 态 开 口 直
AE + (t X△ ) 0 ; 为立辊 轧制 力 E oM ̄ X1 . A l 0
热连轧机电气控制系统的联动调试技术方案

热连轧机电气控制系统的联动调试电气控制系统的联动调试系指在上级过程计算机和自动化仪表控制设备未参与的情况下,仅包含基础自动化级控制设备及轧线各传动控制设备和系统而进行的模拟轧钢的调试。
各基准给定信号、运行方式等均由操作(调试)人员在操作台(或操作键盘)上给出,如轧制速度给定、辊缝设定等。
模拟轧制过程中,钢坯与带材的跟踪检测信号均以模拟开关动作来生产。
现代化热轧生产线均设有专用于模拟调试的“模拟柜(屏)”。
由于试验时没有实际带钢的束缚,活套挑高度控制、活套及卷取张力控制等均不投入,它们的调试待实际穿带轧制时进行。
同理,温度控制、轧制力控制等也待实际轧钢与自动化仪表联动运行调试才完成对它们的检查确认和调试。
22.11.1 基础自动化级控制系统的调试基础自动化级控制设备分为可编程序控制器(PC)、直接数字控制器(DDC)和微机控制装置。
热轧厂中基础自动化级包括板坯库、加热炉、粗轧机组、精轧机组、带钢冷却、卷取机等若干系统,按上级过程计算机或人工给出的基本给定值和运行方式选择信号,对系统区分内设备进行顺序控制和闭环调节控制。
系统之间以及系统内多台基础自动化设备间的信息交换与传输是通过通讯母线进行的。
系统与下级电气传动间的信息交换与传输则多通过硬接口I/O及远程I/O(输入/输出)接口进行。
采用基础自动化级的热轧操作台内设有用于人—机接口的“操作员站”,它由可编程序控制器或微机装置、操作键盘、CRT显示器和打印装置组成,集操作控制、设备运行监视、故障报警、记录打印多功能于一体,经通讯接口与各系统作信息交换。
基础自动化级的调试包括设备硬件检查和程序(软件)的模拟调试两大内容。
不同设备组成的系统调试的具体步骤与内容有一定差别,原则上要根据设计和软件编制单位提供的调试手册,在设计和软件编制人员协作下进行。
调试的基本内容与方法与可编程序控制器控制系统类似,可参阅本手册第8章。
22.11.1.1 一般检查和设定1)设备清点,配线检查,屏蔽状况检查;2)绝缘检查,设备通电;3)各插件板,基板上设定开关的初始值设定,I/0插件板的地址设定。
宽带钢热连轧计算机控制系统概述

主要完 成 主辅传 动 、 液 、 电、 气动 作执 行 、 仪表 数 据 制器 的宽带 钢热 连轧计 算机 控制 系统 。 宽带 钢热 连轧 生产 线有 大量 的机 电 、液 压 设 制 、 辑 控 制 、 备 控 制及 实 时 数 据采 集 等 功 能 ; 备 , 性小 , 合性 强 , 逻 设 惯 耦 控制 功能 多 而复 杂 , 键 的 关 过 程控 制级 (2 主要完 成过 程参 数 的设 定计算 和 质 量 指 标 ( 板 形 ) 以控 制 , 求 其计 算 机 控 制 L) 如 难 要
s se frawieh tsr yh tc niu u ol g ae ito u e . hss s m sd v lp d i- y tm o d o t p b o o t o srl n r nrd c d T i yt i e eo e n i n i e
S m m a ieo m p tr Co to y tm o i eHo ti i u rz n Co u e n r lS se f rW d tS rp M l l
HeA riS nWe q a ,o g o g G oQa g nu ,u n u n S n n , u in Y
摘要 : 绍 了 国内 自主 开发 、 介 管控一 体的 带钢 热连轧 计算机 控制 系统 的特 点和 主要 功 能 。
该 系统 已成功 应用 于 国 内多条 宽带钢 热连 轧 生产线 上 , 取得 了 良好 的控 制 效果 。
关键词 :热 带钢 轧机 ; 制 系统 ; 学模 型 控 数 中 图分 类 号 : G 3 , F T 33 T 3 文献标 识码 : A 文章 编号 : 1 0 — 6 3 2 1 )6 0 0 — 6 0 6 4 1 (0 1 0 — 0 1 0
基于TDC的1500mm热连轧带钢自动生产线

fr h g u l y s rp,1 0 l h ts rp l e Wa u l b ag n n 2 0 .Th o ti i ei a s to u l o ih q a i t i 0mi o ti i Sb i y I i a g i 0 4 t 5 l n t e h ts rp l s e ff l n y a t ma i h t i l d sg e n ma u a t r d b u s l e . Pr d c n e l iu s me h n c l e u p u o t ots rp mi e i n d a d c l n fc u e y o r e v s o u i g tem q e , c a ia q i —
张大 志 董 博浩 技 大 学高效轧 制 国家工程研 究 中心 2 .莱芜钢铁 ( 团) 司 集 公
摘 要 : 了优 化 产 品结 构 、 高 生 产 效 益 、 足市 场 对 高 质 量 热 轧 带 钢 的 需 求 , 钢 于 2 0 为 提 满 莱 04年 投 资 建 造
( uo tcj mpc n r 1s se ,1v l s t pmah mai d l a tma i o to ) y tm e e2 eu t e tcmo es,h tc i b xc n r1s se a do h rc n u o o1 o e te yt m n te o
me t ,TDC( e h o o y a d d i e o t o )c n r l y t m ,c mmis n n n r d c i n st a in we e i — ns t c n l g n rv s c n r 1 o to s e s o s i i g a d p o u t i t r n o o u o
轧制过程计算机控制系统

板坯库是连铸连轧产线与A炼钢连铸之间重要的缓冲环节。板坯库管理主要是对来自A炼钢的冷装板坯、 B炼钢有质量异议的板坯、回炉坯进行管理。
H 钢卷库管理
钢卷库存放轧线产出的钢卷,当质量判定合格后交销售部门向用户发货。
I 产品外发管理
产品只有经过成品发货才能到达客户手中,完成企业的生产目标,实现企业的利润。根据客户的要求 运输方式有汽车和火车两种方式。根据企业的管理业务流程,客户在销售公司收到货款,开具提货单 时,热轧厂才能进行发货处理。合同全部发货完成后应在生产控制级系统进行合同结案处理,以防止 生产部门为该合同多配料生产,产出非计划品。
车间设备全面采用计算机控制,是从原料送上加热炉辊道开始,尺寸、温 度、轧制过程、冷却过程、卷取过程都实现程序设定和实时控制,满足轧制 生产稳定、安全和高质量要求,为生产出高精度高档次的产品奠定基础。
计算机控制系统有不同分布方式、计算模型选择,不同计算处理速度和通 讯速度,这些都成为控制水平高低的影响因素。
3)特殊功能模块
为了增强PLC的功能,扩大其应用领域,PLC都有各种各样的功能模块。它们主要用于完成某些特殊功 能任务,减少CPU的负担,如通讯MPI模块,存储显示模块等。通信处理器用于PLC之间、PLC与远程 I/O之间、PLC与计算机和其他智能设备之间的通信,可以将PLC接入MPI、PROFIBUS-DP、AS-i和工 业以太网,或者用于点对点通信。有的S7-300/400CPU集成有MPI之外的通信接口,相当于CPU模块
(2)控制功能不断完善。从代替人工操作的设定闭环控制,发展到产 品质量控制、故障诊断,并实现了控制轧制。
(3)控制范围不断扩大。20世纪60年代初期,以控制精轧机为主,主 要是进行压下位置和轧机速度的预设定。20世纪60年代中后期,控制范 围扩大到加热炉、粗轧机、精轧机、卷取机。20世纪80年代,过程控制 与管理控制相结合,范围又扩大到板坯库、钢卷库、成品库以及热平整 线和热剪切线,从而覆盖了整个热轧厂。
带钢热连轧的模型与控制

带钢热连轧的模型与控制引言带钢热连轧是一种重要的金属加工方法,用于将宽度较大的钢坯通过一系列辊道进行塑性变形,最终得到所需的带钢产品。
在这个过程中,模型与控制起着关键作用,能够有效提高生产效率、产品质量和设备稳定性。
本文将介绍带钢热连轧的模型与控制方法,并对其进行详细分析和讨论。
带钢热连轧模型带钢热连轧模型是描述带钢在连轧过程中力学行为和变形规律的数学模型。
它通常包括以下几个方面的内容:压下力模型压下力是指压下辊对带钢施加的垂直压力,它直接影响到带钢的变形和塑性流动。
压下力模型可以通过分析辊道几何形状、材料特性以及工艺参数等因素来建立。
常用的压下力模型包括基于弹塑性理论和有限元方法等。
温度场模型温度场是指带钢在连轧过程中的温度分布情况,它对带钢的塑性变形和组织结构起着重要影响。
温度场模型可以通过考虑带钢的传热、传质和相变等过程来建立。
常用的温度场模型包括基于热传导方程和热力学原理等。
变形行为模型变形行为是指带钢在连轧过程中的塑性变形规律,包括应力、应变和流动规律等。
变形行为模型可以通过考虑带钢的材料本构关系、摩擦特性和辊道几何形状等因素来建立。
常用的变形行为模型包括基于弹塑性理论和流体力学原理等。
带钢热连轧控制带钢热连轧控制是指通过调节工艺参数和辊道状态,实现对带钢连轧过程的精确控制。
它可以提高产品质量、降低生产成本,并确保设备稳定运行。
常用的带钢热连轧控制方法包括以下几种:轧制力控制轧制力控制是通过调节辊道间隙、辊道形状和压下力等参数,实现对带钢轧制力的控制。
它可以保证带钢的正常变形和塑性流动,并避免过大或过小的轧制力对设备和产品造成损伤。
常用的轧制力控制方法包括模型预测控制、自适应控制和模糊控制等。
温度控制温度控制是通过调节加热设备、冷却设备和工艺参数等,实现对带钢温度的控制。
它可以保证带钢在连轧过程中的合理温度范围,避免过高或过低的温度对产品质量产生不良影响。
常用的温度控制方法包括PID控制、模型预测控制和神经网络控制等。
日照1580mm带钢热连轧粗轧区控制系统

电 气传 动 2 0 年 第 3 08 8卷 第 1 期 1
日照 1 T带 钢 热 连 轧粗 轧 区控 制 系 统 8 ml 50 l
裴红平, 郭强 , 王京 , 为 民 , 忻 刘安 平
包括 : 加热 炉 出 口除鳞 箱 和除 鳞水 、 除鳞 辊பைடு நூலகம் 、 E1
前 延伸 辊道 、 1前工 作辊 道 、 1前侧 导 板 、 l前 E E E
除鳞水 、 1立 辊 轧 机 主 传 动 、 1立 辊 轧 机 侧 压 、 E E R14辊 轧机 主传 动 、 Rl4辊 轧机 压下 、 后 除鳞 R1 水 、 后 工 作 辊 道 、 后 侧 导 板 、 后 延 伸 辊 R1 R1 R1
中 图分 类号 : P 7 T 23 文献标识码 : A
Ro g ilCo t o se o 0m m o t i t e ili iha r n & Ste . u h M l n r lSy tm f r 158 H tS rp S e lM l n R z o I o e lCo P n — ig, EIHo g pn GUO a g, ANG ig, N e— n, U — ig Qin W Jn XI W imi LI An pn
Tc n lg iig, iig 1 0 8 , h n eh o y Be n Bejn 0 0 3 C ia) o j
Ab ta t Ro g l i a n ip n a l a to o t i t e l Ba e n t e d vc s n tu n sa d s r c : u h mi s n id s e s b e p r fh ts rp s e l l mi . s d o h e ie ,i s r me t n 1
热轧带钢终轧温度控制系统的改造与应用
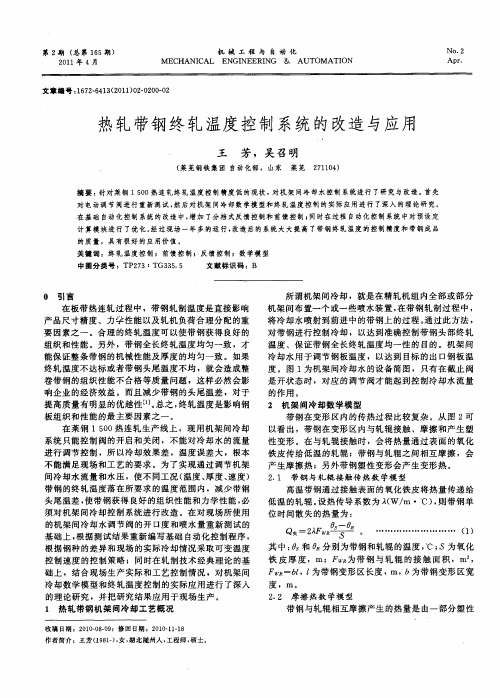
将冷 却水 喷射 到前进 中 的带 钢上 的过程 。 通过 此方 法 , 对 带钢进 行控制 冷却 ,以达 到准确 控制 带钢 头部终 轧 温度 、保 证带钢 全长 终轧 温度均一 性 的 目的 。机架 间 冷却 水用 于调节 钢板 温度 ,以达 到 目标 的 出 口钢板 温 度 。图 1为机 架间冷 却水 的设备 简 图 ,只有 在截止 阀 是 开状态 时 ,对 应 的调节 阀才能起 到控 制冷 却水 流量 的作 用 。 2 机 架间冷 却数 学模型 带 钢在变形 区内的传 热过程 比较复 杂 。从 图 2可
丹 一 疗
Q失一 2 F
L)
。
……… …… …… …… () 1
其 中 : 和 分 别 为带钢和 轧辊 的温度 , S为氧化 f C;
铁 皮 厚 度 ,m;Fw 为 带 钢 与 轧 辊 的 接 触 面 积 ,m。 , F =b, 为带 钢变形 区长 度 ,T, lz 1 b为带钢 变形 区宽 I
热 轧 带钢终 轧 温度 控 制 系统 的改造 与应 用
王 芳 ,吴 召 明
( 芜 钢 铁 集 团 自动 化 部 , 山东 莱 芜 莱 210) 7 14
摘 要 : 对莱 钢 150热 连 轧 终 轧 温 度 控 制 精 度 低 的 现状 , 机 架 间冷 却 水 控 制 系 统进 行 了研 究 与改 造 。首 先 针 0 对 对 电 动调 节 阀进 行 重新 测 试 , 后 对 机 架 间 冷 却 数 学模 型 和 终 轧 温 度 控 制 的 实 际 应 用 进 行 了深入 的理 论 研 究。 然 在 基 础 自动 化 控 制 系统 的 改造 中 , 加 了分 档 式 反馈 控 制 和 前 馈 控 制 ; 增 同时 在 过 程 自动化 控 制 系统 中对 预设 定 计 算 模 块 进 行 了优 化 。 过 现 场 一 年 多 的运 行 , 经 改造 后 的 系统 大 大 提 高 了带 钢 终 轧 温度 的控 制 精 度 和 带 钢 成 品
带钢热连轧机组轧后控制冷却系统的配置及发展历史
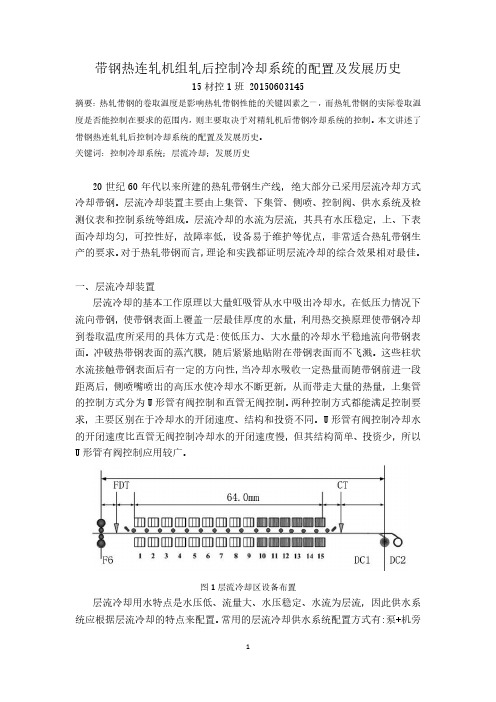
带钢热连轧机组轧后控制冷却系统的配置及发展历史15材控1班 20150603145摘要:热轧带钢的卷取温度是影响热轧带钢性能的关键因素之一,而热轧带钢的实际卷取温度是否能控制在要求的范围内,则主要取决于对精轧机后带钢冷却系统的控制。
本文讲述了带钢热连轧轧后控制冷却系统的配置及发展历史。
关键词:控制冷却系统;层流冷却;发展历史20世纪60年代以来所建的热轧带钢生产线,绝大部分已采用层流冷却方式冷却带钢。
层流冷却装置主要由上集管、下集管、侧喷、控制阀、供水系统及检测仪表和控制系统等组成。
层流冷却的水流为层流,其具有水压稳定,上、下表面冷却均匀,可控性好,故障率低,设备易于维护等优点,非常适合热轧带钢生产的要求。
对于热轧带钢而言,理论和实践都证明层流冷却的综合效果相对最佳。
一、层流冷却装置层流冷却的基本工作原理以大量虹吸管从水中吸出冷却水,在低压力情况下流向带钢,使带钢表面上覆盖一层最佳厚度的水量,利用热交换原理使带钢冷却到卷取温度所采用的具体方式是:使低压力、大水量的冷却水平稳地流向带钢表面。
冲破热带钢表面的蒸汽膜,随后紧紧地贴附在带钢表面而不飞溅。
这些柱状水流接触带钢表面后有一定的方向性,当冷却水吸收一定热量而随带钢前进一段距离后,侧喷嘴喷出的高压水使冷却水不断更新,从而带走大量的热量,上集管的控制方式分为U形管有阀控制和直管无阀控制。
两种控制方式都能满足控制要求,主要区别在于冷却水的开闭速度、结构和投资不同。
U形管有阀控制冷却水的开闭速度比直管无阀控制冷却水的开闭速度慢,但其结构简单、投资少,所以U形管有阀控制应用较广。
图1层流冷却区设备布置层流冷却用水特点是水压低、流量大、水压稳定、水流为层流,因此供水系统应根据层流冷却的特点来配置。
常用的层流冷却供水系统配置方式有:泵+机旁水箱、泵+高位水箱+机旁水箱、泵+减压阀。
泵+机旁水箱的供水系统,通过水箱稳定水压和调节水量,系统配置简单,节能效果明显。
带钢热连轧生产线自动控制系统

带钢热连轧生产线自动控制系统陈春雨牛东风何万民赵国安王万福摘要以凌钢热连轧生产线自动控制系统为例,论述了热连轧生产线基础自动控制系统的基本结构、硬件软件配置、控制功能、系统测试和现场调试等内容,同时也指出了该自动化系统进一步改造的要点。
关键词热连轧自动化控制系统Automaticcontrol systemforasemi-continuous hot strip millChen ChunyuNiu Dongfeng He Wanminﻫ(AutomationResearch Instituteof MMI Beijing100071) ﻫZhao Guoan Wang Wanfu(Lingyuan Iron & Steel Co)AbstractTaking the automation system of hot strip mill ofLingyuan Iron& Steel Co as an example,thebasicstructure,configuration of hardwareand software,controlfunctions, testing andcommissioning onsite for the automatic control systemof hot strip mill are described. Also, severalpointsto bemodified further in the future are presented.Key wordshotstrip rolling;automation; control system0 前言凌源钢铁公司880mm中宽带热连轧机生产线是1992年开始建设的。
这是国内首次完全依靠自己的技术力量为中宽带热连轧机设计和配套的自动控制系统并取得良好效果的工程项目。
该套轧机原来是德国Krupp公司Leverkusen工厂1956年建造的,1993年拆迁到我国凌源钢铁公司,在工艺设备布置方面做了必要的修改。
轧钢自动化原理幻灯片

•19
三、自动控制原理(以钢铁厚度自动控制为例)
闭环控制系统的特点:具有自动补偿由于系统内部和外部 干扰所引起的系统误差的能力,因而能够有效提高系统的 精度;系统参数应适当选择,否则可能不能正常工作。
3.3.3复合控制
复合控制是开环和闭环控制相结合的一种控制方式。它在 闭环控制回路的基础上,附加一个输入信号或扰动信号的 畅馈通路,用来提高系统的控制精度。此畅馈通路通常由 对输入信号的补偿器或对扰动信号的补偿器组成。 优点:高控制精度,可抑制几乎所有的可量测扰动。 缺点:补偿器的参数要有较高的稳定性。
复合控制系统简图(下页)
•20
三、自动控制原理(以钢铁厚度自动控制为例) 复合控制系统简图
•21
轧钢生产自动化
结束!
谢谢!
•22
1.2.2 自动控制基本理论发展简史
稳定性理论的早期发展 根轨迹法的建立 脉冲控制理论的建立与发展 经典控制理论(或古典控制理论)(19世纪初) 现代控制理论(20世纪60年代) 大系统控制理论 智能控制理论(20世纪70年代)
•4
一、轧钢与自动化的背景介绍
1.2.3 自动控制技术的发展
自动化技术形成时期是在18世纪末~20世纪30年代,两种典 型的动力技术为风车技术和蒸汽机技术。1935~1950年左右为其经 典控制时期。50年代末进入现代控制时期,随着现代控制理论和电 子计算机的推广应用,自动控制与信息处理结合起来,自动化控制技 术日渐得到广泛应用,如我国863高技术计划、神舟飞船发射等都与 其有着密切联系。
•14
三、自动控制原理(以钢铁厚度自动控制为例)
反馈控制系统的组成、名词术语、定义(有 图)(下16)
•15
包钢热连轧卷取机自动控制系统的研究
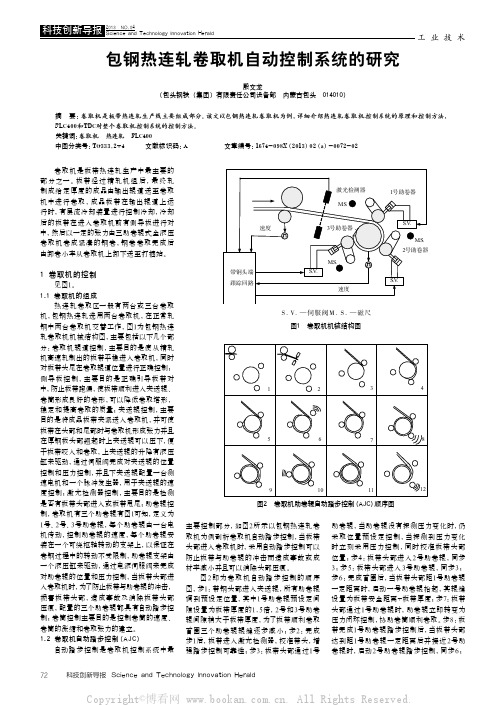
工业技术
殷文龙 (包头钢铁(集团)有限责任公司设备部 内蒙古包头 014010)
Hale Waihona Puke 摘 要:卷取机是板带热连轧生产线主要组成部分。该文以包钢热连轧卷取机为例,详细介绍热连轧卷取机控制系统的原理和控制方法,
图2即为卷取 机自动踏 步控制的顺序 图,步1:带 钢头部进入夹 送辊,所有助卷辊 调 到 预 设 定位 置,其中1号助卷 辊 预 设 定间 隙设 置为板带厚度的1.5 倍,2号和 3号助卷 辊 间隙 稍 大 于 板 带 厚 度,为了板 带 顺 利 卷 取 首圈三个助 卷 辊 辊 缝 逐步 减 小;步2:完 成 步1后,板带 进入激光检测器,校准带头,增 强踏 步控制可靠性;步3:板带头部通 过1号
72
科技创新导报 Science and Technology Innovation Herald
Copyright©博看网 . All Rights Reserved.
工业技术
科技创新导报 2013 NO.04
Science and Technology Innovation Herald
步 9:板带头部通 过 2号助卷辊完成2号助卷辊 踏 步控制,同步7;步 10:板带 头 部通 过 2号助卷 辊 并距离3号助卷 辊一定 距离时,起动3 号助卷 辊 踏 步控制,同步 6;步11:板带头部通 过3号助卷 辊并 完成 3号助卷辊 踏步控制,同步7。重复步 6到步11直到张力建立。步12: 卷取 机 张力建立 后,为了起 到安 全甩尾1号助卷 辊 退 到最 大 外径 位 置,2 号 和 3 号助 卷 辊 复位 到 初 始 位 置。 1.3 卷取机控制方式
热连轧过程自动化控制系统

热连轧过程自动化控制系统热连轧计算机系统包括生产管理级、生产控制级、过程控制级和设备控制级。
过程控制级也称过程优化级。
执行对轧件从炉前辊道开始直到卷取结束的全线物料跟踪、板坯装炉出炉操作控制、炉内最佳加热控制、主轧线上的切头控制、活套控制、板宽控制、板厚控制、轧制温度控制、卷取温度控制、过程数据采集与处理、过程设备巡检、诊断报警、过程控制计算机之间的数据通讯等功能。
过程控制计算机系统调试是热连轧多级计算机系统调试的核心部分。
调试方法在上一级计算机中存贮着事先编制好的各种轧制计划表及各种板坯的基本数据,按时序将轧制计划和原始数据发送到过程控制机。
加热、粗轧、精轧等过程均有相应的模拟试验程序,用以模拟实际工艺过程、发出轧件通过各生产区段所产生的动作信号,并用模拟事件激活过程控制机的各部分功能程序。
模拟试验主要是测试各部分应用程序的功能,在此阶段可将放置在现场各操作室内的显示终端和打印机暂时安放在主机房,以供调试人员及时观察模拟试验情况,进行检查和分析。
此时应将过程控制计算机传送给设备控制级的设定值和设备控制级传送到被控制设备输出的信号端暂时切断,这些信号可以从显示器或打印机上输出,供分析核对使用。
在修正和完善应用软件功能及排除设备故障之后,方可进入模拟轧钢阶段。
逐渐接通过程控制机向设备控制计算机以及被控设备的信号连线,将控制信号直接施加给被控对象,观察被控设备的动作情况。
模拟程序要具有较强的人机对话功能,包括对程序的跟踪、修改和过程参数的打印、显示和修改等。
在模拟调试过程中,操作者应随时注意画面上所报出的提示信息,对于错误操作,操作者可及时更正;属于数据传输错误或计算错误而使结果超限时,应进行人工干预,输入正确的数值。
除在现场操作室内进行显示和打印外,通常也可以在主机房的显示终端、系统打字机和行式打字机上进行。
调试内容包括加热过程、粗轧过程、精轧过程、带钢冷却过程、卷取过程等控制计算机系统的调试以及备用机和设备故障检测机的调试。
- 1、下载文档前请自行甄别文档内容的完整性,平台不提供额外的编辑、内容补充、找答案等附加服务。
- 2、"仅部分预览"的文档,不可在线预览部分如存在完整性等问题,可反馈申请退款(可完整预览的文档不适用该条件!)。
- 3、如文档侵犯您的权益,请联系客服反馈,我们会尽快为您处理(人工客服工作时间:9:00-18:30)。
带钢热连轧生产线自动控制系统陈春雨牛东风何万民赵国安王万福摘要以凌钢热连轧生产线自动控制系统为例,论述了热连轧生产线基础自动控制系统的基本结构、硬件软件配置、控制功能、系统测试和现场调试等内容,同时也指出了该自动化系统进一步改造的要点。
关键词热连轧自动化控制系统Automatic control system for a semi-continuous hotstrip millChen Chunyu Niu Dongfeng He Wanmin(Automation Research Institute of MMI Beijing 100071)Zhao Guoan Wang Wanfu(Lingyuan Iron &Steel Co)Abstract Taking the automation system of hot strip mill of Lingyuan Iron &Steel Co as an example, the basic structure,configuration of hardware and software, control functions, testing and commissioning on site for the automatic control system of hot strip mill are described. Also, several points to be modified further in the future are presented.Key words hot strip rolling; automation; control system0 前言凌源钢铁公司880mm中宽带热连轧机生产线是1992年开始建设的。
这是国内首次完全依靠自己的技术力量为中宽带热连轧机设计和配套的自动控制系统并取得良好效果的工程项目。
该套轧机原来是德国Krupp公司Leverkusen工厂1956年建造的,1993年拆迁到我国凌源钢铁公司,在工艺设备布置方面做了必要的修改。
主要电气控制系统全部由国内配套,厂房是利用旧厂房扩建的,在较短的时间内投产见效,为凌钢增产创效奠定了基础。
冶金部自动化研究院在建设过程中承担了全部电气控制系统新设备的设计配套和利旧设备的修配改工作,在同类生产线建设中具有典型意义。
本文主要以该工程的实施过程为例,介绍热连轧生产线自动控制系统的基本结构、硬件软件配置、控制功能、系统测试和现场调试等方面的内容,为以后类似工程提供借鉴。
1 工艺简介该套生产线改造后,形成了较为典型的3/4连轧模式,总装机容量37000kW,年产50万t热轧板卷。
其工艺设备包含4个部分:加热炉区、粗轧区、精轧区、卷取区。
如图1所示。
图1 轧制线工艺设备布置示意图加热炉为推钢式加热炉,由上料台、炉体、回料车、取钢机等设备组成。
粗轧区主要由1架立辊轧机(E1)、电动压下的四辊可逆粗轧机(R1)、前后侧导板、二辊单向粗轧机(R2)、双工位热卷箱(CB)、飞剪(SH)以及辊道组成。
精轧区主要由1架立辊轧机(E2)、电动压下的四辊精轧机(F1,F2,F3,F4,F5,F6)、活套装置(H1,H2,H3,H4,H5)、导卫装置等组成。
卷取区主要由2套夹送辊、地下卷取机(DC1,DC2)、废品卷取机、卸卷机、运输链等组成。
工艺过程为:来料150mm厚、7500mm长的连铸坯,经加热炉加热后,由R1轧制5~7道次,再经R2轧制1道次,成为16~25mm的中间坯,由热卷箱卷起保温,开卷后头尾对调,进入精轧机组轧制6道次,成为2~6mm薄板,经喷水冷却后,由卷取机卷成带卷。
2 控制系统配置2.1 系统模式60年代以来,带钢热连轧机的自动化不断发展,已经形成了功能齐全、技术成熟、效果显著的计算机自动控制系统。
根据生产的需要,该套轧制线的电气控制系统按3个层次进行配置,分别为:操作站系统、自动控制系统、电气传动及检测仪表系统。
各部分的控制功能都是由应用软件实现的,驻留在各个控制子系统中。
各部分的控制信息通过计算机网络传递。
层次结构如图2所示。
图2 控制系统层次结构示意图这是1个典型的基础自动化控制系统,其核心为1级的自动控制系统,它完成全部的控制功能,协调整个生产过程;0级的传动系统和仪表系统以及其他气动和液动设备作为执行机构,完成能量转换,驱动机械设备;2级的操作站系统作为人机界面设备,完成生产过程的设定、监控、统计等任务。
工程师站主要用于工程技术人员定期对控制系统进行必要的维护和技术培训等,生产过程中,工程师站可在线也可离线工作。
由这3部分构成了1个完整的控制系统,完成整个生产线的协调自动控制,而每层又都分成若干个子系统,完成相应的控制任务。
这种控制系统模式,既实用,又经济,为大多数用户所接受,也是目前国内中小企业普遍采用的模式。
2.2 硬件系统根据生产的需要和生产中各工艺设备之间的运行逻辑关系,整个生产线的电气控制系统分2段进行构造:粗轧段和精轧卷取段。
2段系统之间既彼此独立,又相互联系,协调工作,分述如下。
2.2.1 粗轧段粗轧段的硬件系统由1套操作站系统和6套可编程序控制器系统构成。
操作站系统为新系统,由IBM-7537工业控制微机为主配置而成;可编程序控制器系统分为3部分:R1轧机的速度控制和压下控制分别由A-B公司的PLC5/40L新系统构成,R2的控制系统和热卷箱的控制系统分别由3台SIEMENS公司的S5 130A 旧系统构成,飞剪控制系统由A-B公司的SLC500新系统构成,新系统由1条A-BDHplus网络连为一体。
新旧系统之间信息交换通过硬件I/O进行。
如图3所示。
图3 粗轧段控制系统配置示意图2.2.2 精轧卷取段精轧卷取段的硬件系统由2套操作站系统和6套可编程序控制器系统构成,全部为新系统,分别完成精轧机的速度、压下、活套和1#卷取机、2#卷取机以及喷水冷却控制功能。
操作站系统由IBM-7537工业控制微机为主配置而成;可编程序控制器系统均由A-B公司的PLC5/40L新系统为主配置而成,由1条A-BDHplus网络连为一体。
传动系统由模拟U2系统构成,通过硬件I/O与自动化系统接口。
如图4所示。
图4 精轧卷取段控制系统配置示意图2.3 软件系统软件系统分为2部分:系统软件和应用软件。
操作站系统的系统软件主要由WINDOWS操作系统和A-BCONTROLVIEW画面软件平台以及C语言系统构成;可编程序控制器的系统软件为A-B6203编程软件,以梯形图方式开发应用软件,它具有强大的算术、浮点和逻辑运算功能,编程清晰方便;网络系统选用A-BDHplus网络系统配置。
应用软件系统亦分为2部分:系统软件和应用软件。
系统软件是指控制设备生产厂家为控制系统运行而设计的监控、总线管理、数据管理等基本软件或软件平台。
应用软件是系统集成者满足某一特定用户的具体控制要求而设计的控制功能软件或软件模块。
操作站画面、报表系统的应用软件除少部分由C语言编制而成外,大部分都是由CONTROLVIEW系统配置的设定、操作、报警、报表等画面。
生产过程中,操作人员只需在画面上通过功能键和数字键简单操作即可完成生产过程的设定等任务。
画面的结构为树状结构,切换原则是:同一根下的同级画面可直接切换,不同分支上的画面要经过相应的根才能切换。
可编程序控制器系统的应用软件系统主要是实现生产过程的功能控制,通过梯形图语言逐条编制而成,采用模块化结构设计,清晰、易读、易维护。
程序模块分为通用模块和独立模块,都驻留在相应的控制系统中,各模块之间的组织关系由主控程序管理。
其主控程序结构如图5所示。
图5 主程序结构示意图在软件模块设计时,大量采用了成熟的控制原理和控制算法,采用条件控制和时序控制相结合的方式,以有效利用系统能力资源和适应现场具体情况。
操作方式为手动、半自动、自动等3种方式,在轧钢前可由操作人员根据设备状况自由选择。
而轧钢过程中,只能按由高级到低级的顺序降级选择。
程序设计中充分考虑了设备的安全因素和操作人员对生产过程的适当干预能力。
3 基本控制功能控制系统的全部功能都是通过软件实现的,由驻留在各子系统中的功能模块完成,具体分解如下。
3.1 初轧区初轧区控制系统的主要控制功能有:整个区域的速度设定、协调和控制;E1轧机和侧导板的开口度设定与控制;R1、R2轧机压下系统和位置设定与控制;R1制止道次设定、判别与控制;高压水除鳞控制;热卷箱的卷取、带尾定位和开卷控制;飞剪的定位、切头和切尾控制;粗轧区操作逻辑;粗轧区辅助系统联锁;粗轧区正常停车与紧急停车控制;粗轧区故障报警和打印;粗轧生产过程监控;粗轧生产参数设定与打印;粗轧生产报表的生成、显示和打印。
3.2 精轧区精轧区控制系统的主要控制功能有:整个区域的速度设定、协调和控制;E2轧机的开口度设定与控制;F1、F2、F3、F4、F5、F6轧机压下系统的位置设定与控制;精轧机的AGC(预留);H1、H2、H3、H4、H5活套的高度、张力以及起落控制;活套控制自适应;高压水除鳞控制;精轧区操作逻辑;精轧区辅助系统联锁;精轧区正常停车与紧急停车控制;精轧区故障报警和打印;精轧生产过程的监控;精轧生产参数设定、存储与打印;精轧生产报表的生成、显示、存储和打印。
3.3 卷取区卷取区控制系统的主要控制功能有:整个区域的速度设定、协调和控制;喷水冷却系统的控制;1#和2#卷取机的卷筒及其助卷辊控制;1#和2#夹送辊的控制;1#和2#卷取机的张力卷取过程控制;卸卷和带卷运输链的控制;卷取区操作逻辑;卷取区辅助系统联锁;卷取区正常停车与紧急停车控制;卷取故障报警和打印;卷取生产过程监控;卷取参数设定、存储与打印;生产报表的生成、显示、存储和打印。
4 系统调试和投运该系统设计和制造完成之后,在实验室里进行了模拟调试和测试,称为实验室调试,分2个阶段:单体测试和系统联调。
单体测试的主要任务是以模拟方式单个运行子系统,纠正硬件和软件中的错误,调整不合适的控制方式。
然后,对系统施加适当的设定信号,模拟相应的反馈值,记录系统输出结果,对应用软件模块进行“黑箱”测试,分析控制趋势,检查各种参数是否基本合适。
系统联调的主要任务是检查整个控制系统的工作状况,包括系统网络运行状态、各子系统之间的协调关系,各种数据流向等方面。
在实验室调试完成后,要对系统的各个方面进行详细的记录和备份,以便到现场系统恢复时使用。
系统在现场安装完成后,进行了必要的系统恢复和现场调试。
系统恢复是指将系统重新恢复到实验室系统联调完成时的状态,不同的是用现场实际信号取代实验室的模拟信号。
现场调试包括:单体试车、联动试车、负荷试车3个阶段。