拉丝操作规程
拉丝工艺及安全操作规程
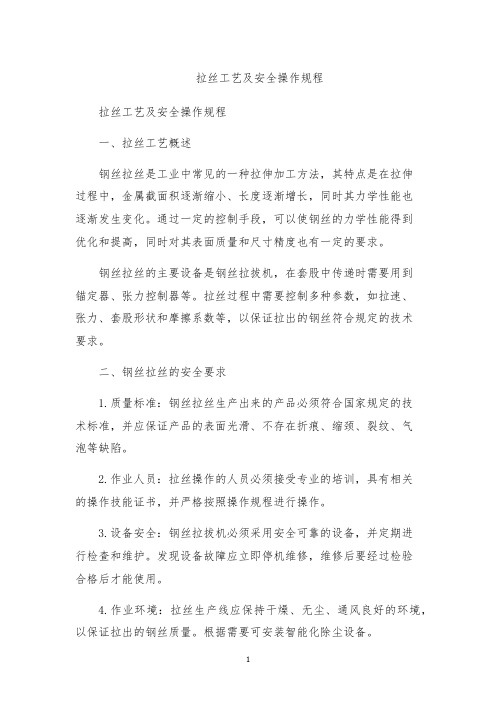
拉丝工艺及安全操作规程拉丝工艺及安全操作规程一、拉丝工艺概述钢丝拉丝是工业中常见的一种拉伸加工方法,其特点是在拉伸过程中,金属截面积逐渐缩小、长度逐渐增长,同时其力学性能也逐渐发生变化。
通过一定的控制手段,可以使钢丝的力学性能得到优化和提高,同时对其表面质量和尺寸精度也有一定的要求。
钢丝拉丝的主要设备是钢丝拉拔机,在套股中传递时需要用到锚定器、张力控制器等。
拉丝过程中需要控制多种参数,如拉速、张力、套股形状和摩擦系数等,以保证拉出的钢丝符合规定的技术要求。
二、钢丝拉丝的安全要求1.质量标准:钢丝拉丝生产出来的产品必须符合国家规定的技术标准,并应保证产品的表面光滑、不存在折痕、缩颈、裂纹、气泡等缺陷。
2.作业人员:拉丝操作的人员必须接受专业的培训,具有相关的操作技能证书,并严格按照操作规程进行操作。
3.设备安全:钢丝拉拔机必须采用安全可靠的设备,并定期进行检查和维护。
发现设备故障应立即停机维修,维修后要经过检验合格后才能使用。
4.作业环境:拉丝生产线应保持干燥、无尘、通风良好的环境,以保证拉出的钢丝质量。
根据需要可安装智能化除尘设备。
5.消防安全:作业场所应设置消防器材,尤其要注意控制氧气浓度,防止火灾事故发生。
三、钢丝拉丝的操作流程1.准备工作:检查、更换拉丝机主轴磨齿,确保双股机套件及张力传感器的安装、线圈、对轴预紧力基础调整、油泵导轨及上下缸等调整,客观检查轮轮缘及套股夹位,使其处于规定位置。
2.开机启动:按车间标准操作流程,注意操作顺序,如有任何不当立刻关闭全场,通过专业人员的检查调试恢复正常后方可重新投产。
3.控制拉速:通过控制马达转速和左、右轮之间的动态径向间隙来控制拉速,提高拉速可以提高钢丝的硬度,同时要注意拉速的控制不得超过拉丝机的承受极限。
4.张力控制:通过张力控制器来控制拉丝机各段的张力,以保证钢丝拉丝的平稳、连续进行,防止出现较大的误差、抖动或过大的张力等现象。
5.定尺切割:钢丝的定尺切割通常采用自动拉力切割机和红外线定位分切装置,要确保破碎区离放线轮够近,保证钢丝不会滑动,以及在破碎区前的进刀速度等参数的控制,以保证切割的精度和正确性。
拉丝机操作规程

拉丝机操作规程一、引言拉丝机是一种常用的金属加工设备,用于将金属材料拉制成细丝。
为了保证操作安全和提高工作效率,制定本操作规程。
二、适合范围本操作规程适合于拉丝机的操作和维护保养人员。
三、操作前准备1. 检查拉丝机的电源线是否接好,并确保接地良好。
2. 检查润滑系统的润滑油是否充足,并进行必要的加注。
3. 检查拉丝机的安全保护装置是否完好,如安全防护罩、急停按钮等。
四、操作步骤1. 打开拉丝机的电源开关,确保电源指示灯亮起。
2. 调整拉丝机的工作速度和拉丝力度,根据所需拉丝材料的特性进行调整。
3. 将待拉丝的金属材料固定在拉丝机的进料夹具上,并确保夹具坚固。
4. 启动拉丝机,观察材料的拉丝过程,确保拉丝平稳进行。
5. 拉丝完成后,住手拉丝机的运行,关闭电源开关。
6. 将拉丝好的金属丝从出料夹具上取下,并进行必要的清洁工作。
五、安全注意事项1. 操作人员必须穿戴好个人防护装备,如安全帽、护目镜、防护手套等。
2. 在操作过程中,严禁将手部或者其他身体部位挨近拉丝机的运动部件。
3. 禁止在拉丝机运行时进行维护保养工作,必须先停机并切断电源后才干进行。
4. 在操作过程中,如发现异常情况或者设备故障,应即将停机并通知维修人员进行检修。
5. 操作结束后,及时清理工作区域,保持整洁。
六、维护保养1. 定期检查拉丝机的润滑油是否需要更换,根据使用情况进行维护。
2. 定期清洁拉丝机的工作区域和运动部件,保持设备的良好状态。
3. 定期检查拉丝机的安全保护装置是否正常,如有损坏应及时更换。
七、故障排除1. 若拉丝机无法启动,首先检查电源是否接通,然后检查电源线是否损坏。
2. 若拉丝机运行时浮现异常声音或者震动,应即将停机并检查设备是否有松动或者损坏的部件。
3. 若拉丝机拉丝效果不理想,可调整工作速度、拉丝力度或者更换拉丝模具等。
八、操作规程的修订本操作规程的修订应由专业人员进行,修订后应重新培训操作人员并更新操作手册。
拉丝机安全操作规程有哪些(6篇)

拉丝机安全操作规程有哪些(6篇)(经典版)编制人:__________________审核人:__________________审批人:__________________编制单位:__________________编制时间:____年____月____日序言下载提示:该文档是本店铺精心编制而成的,希望大家下载后,能够帮助大家解决实际问题。
文档下载后可定制修改,请根据实际需要进行调整和使用,谢谢!并且,本店铺为大家提供各种类型的经典范文,如工作报告、合同协议、心得体会、演讲致辞、规章制度、岗位职责、操作规程、计划书、祝福语、其他范文等等,想了解不同范文格式和写法,敬请关注!Download tips: This document is carefully compiled by this editor. I hope that after you download it, it can help you solve practical problems. The document can be customized and modified after downloading, please adjust and use it according to actual needs, thank you!Moreover, our store provides various types of classic sample texts, such as work reports, contract agreements, insights, speeches, rules and regulations, job responsibilities, operating procedures, plans, blessings, and other sample texts. If you want to learn about different sample formats and writing methods, please pay attention!拉丝机安全操作规程有哪些(6篇)拉丝机安全操作规程有哪些篇1连续式拉丝机安全操作规程涵盖了设备的启动、运行、维护及紧急情况处理等多个环节,旨在确保操作人员的安全,提高生产效率,防止设备损坏。
拉丝机工安全操作规程范本
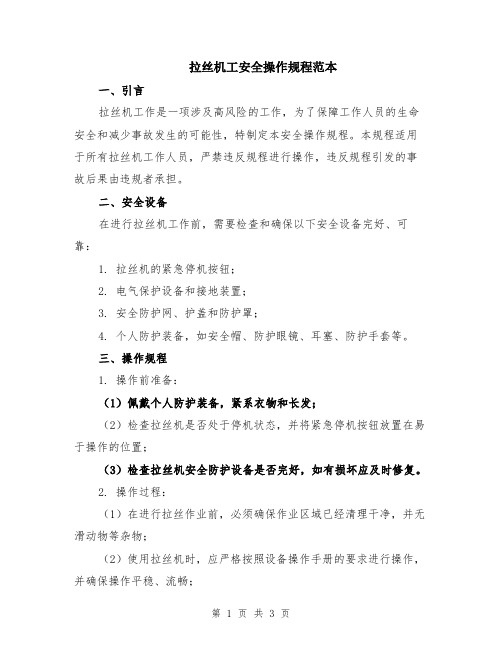
拉丝机工安全操作规程范本一、引言拉丝机工作是一项涉及高风险的工作,为了保障工作人员的生命安全和减少事故发生的可能性,特制定本安全操作规程。
本规程适用于所有拉丝机工作人员,严禁违反规程进行操作,违反规程引发的事故后果由违规者承担。
二、安全设备在进行拉丝机工作前,需要检查和确保以下安全设备完好、可靠:1. 拉丝机的紧急停机按钮;2. 电气保护设备和接地装置;3. 安全防护网、护盖和防护罩;4. 个人防护装备,如安全帽、防护眼镜、耳塞、防护手套等。
三、操作规程1. 操作前准备:(1)佩戴个人防护装备,紧系衣物和长发;(2)检查拉丝机是否处于停机状态,并将紧急停机按钮放置在易于操作的位置;(3)检查拉丝机安全防护设备是否完好,如有损坏应及时修复。
2. 操作过程:(1)在进行拉丝作业前,必须确保作业区域已经清理干净,并无滑动物等杂物;(2)使用拉丝机时,应严格按照设备操作手册的要求进行操作,并确保操作平稳、流畅;(3)禁止将手指、手臂等部位伸入拉丝机工作区域,避免产生危险;(4)当发现设备异常声音、异味或其他异常情况时,应立即停机检查,并通知相关负责人。
3. 操作后清理:(1)拉丝机工作结束后,应将设备停机,拔掉电源插头,并将紧急停机按钮复位;(2)清理拉丝机工作区域,保持整洁,清除杂物和废料。
四、紧急事故处理1. 事故发生时,应立即按下紧急停机按钮,并确保拉丝机完全停机;2. 通知现场负责人,并报告相关领导,进行事故报告;3. 由专业人员进行紧急事故处理,确保事故场所安全,并对事故原因进行调查。
五、培训和考核1. 拉丝机工作人员应接受安全操作规程的培训学习,了解操作规范及安全注意事项;2. 定期进行安全操作考核,确保工作人员正确掌握操作技能和应急处理能力。
六、安全检查和维护1. 定期对拉丝机进行安全检查,确保设备可靠性;2. 对设备进行维护保养,及时更换磨损部件,确保设备的正常运转;3. 及时处理设备故障,避免因故障引发安全事故的发生。
拉丝机-安全操作规程(9篇范文)

拉丝机:安全操作规程(9篇范文)第1篇拉丝机:安全操作规程1、严格执行技术规程,不违章作业,确保安全生产,做到懂原理、懂结构、懂性能、懂用途;2、对各润滑点润滑,每班不少于1次,并经常检查各传动部位润滑情况;3、设备试机时,应空载运转2~3分钟,确信无障碍物、紧固件无松动及不安全隐患,方可接通电源;4、进模:(1)将盘材置放在盘材座上,拉出头部,在砂轮机上磨成圆锥形;(2)将磨成圆锥形的线材头在轧尖机上轧细(轧到小于拉丝模孔径后),插入1#卷筒拉丝模内,并用牵引链轧住露出拉丝模的线材头部;(3)按动1#卷筒启动按钮,1~3分钟后停机,取下牵引链;(4)将绕在1#卷筒上的线材头绕过导轮架的导线轮后,按以上步骤再进入2#卷筒拉丝模,重复上述工作,以此类推;5、当拉丝机启动后,若出现有些卷筒上积丝过多或过少时,应及时加以排除,防止设备事故的发生;6、各卷筒必须在小于最大拉力状态下工作,不得超负荷拉拨;若加工含碳量在0.45%的材料时,原料直径不可超过6.5mm ,每个卷筒的拨细量不得超过前道拉丝模直径的20%;7、拉拨过程中,每个卷筒上的积丝圈应保持在20~30圈;8、钢丝拉拨、配模应合理,轧尖应符合所需拉丝模孔径要求,并用专用牵引工具进行拉拨;9、正常拉拨生产时,应经常检查拉拨质量、钢丝润滑、拉丝模磨损状况;10、设备运行时,操作人员注意力应集中,注视卷筒变化,并远离拉丝机,防止断丝伤人,严禁用手触摸运转部位和手握运行中的钢丝;11、停机:(1)揿下总停按钮;(2)将电源总开关扳到“分”位置;12、卸钢丝时,应待机停稳后,把钢丝捆扎牢固,防止钢丝散乱,并按规格做好标签;13、修理设备或电器时先断开电源,挂上“有人工作,严禁合闸”牌后,方可检修;14、按规定做好设备日常维护保养工作,做到整齐、清洁、润滑、安全。
第2篇拉丝机安全操作规程1、严格执行技术规程,不违章作业,确保安全生产,做到懂原理、懂结构、懂性能、懂用途;2、对各润滑点润滑,每班不少于1次,并经常检查各传动部位润滑情况;3、设备试机时,应空载运转2~3分钟,确信无障碍物、紧固件无松动及不安全隐患,方可接通电源;4、进模:(1)将盘材置放在盘材座上,拉出头部,在砂轮机上磨成圆锥形;(2)将磨成圆锥形的线材头在轧尖机上轧细(轧到小于拉丝模孔径后),插入1#卷筒拉丝模内,并用牵引链轧住露出拉丝模的线材头部;(3)按动1#卷筒启动按钮,1~3分钟后停机,取下牵引链;(4)将绕在1#卷筒上的线材头绕过导轮架的导线轮后,按以上步骤再进入2#卷筒拉丝模,重复上述工作,以此类推;5、当拉丝机启动后,若出现有些卷筒上积丝过多或过少时,应及时加以排除,防止设备事故的发生;6、各卷筒必须在小于最大拉力状态下工作,不得超负荷拉拨;若加工含碳量在0.45%的材料时,原料直径不可超过6.5mm ,每个卷筒的拨细量不得超过前道拉丝模直径的20%;7、拉拨过程中,每个卷筒上的积丝圈应保持在20~30圈;8、钢丝拉拨、配模应合理,轧尖应符合所需拉丝模孔径要求,并用专用牵引工具进行拉拨;9、正常拉拨生产时,应经常检查拉拨质量、钢丝润滑、拉丝模磨损状况;10、设备运行时,操作人员注意力应集中,注视卷筒变化,并远离拉丝机,防止断丝伤人,严禁用手触摸运转部位和手握运行中的钢丝;11、停机:(1)揿下总停按钮;(2)将电源总开关扳到"分"位置;12、卸钢丝时,应待机停稳后,把钢丝捆扎牢固,防止钢丝散乱,并按规格做好标签;13、修理设备或电器时先断开电源,挂上"有人工作,严禁合闸"牌后,方可检修;14、按规定做好设备日常维护保养工作,做到整齐、清洁、润滑、安全。
拉丝机操作规程
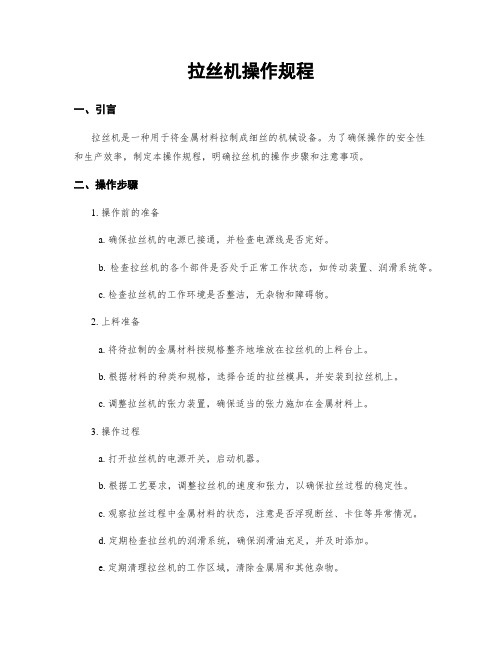
拉丝机操作规程一、引言拉丝机是一种用于将金属材料拉制成细丝的机械设备。
为了确保操作的安全性和生产效率,制定本操作规程,明确拉丝机的操作步骤和注意事项。
二、操作步骤1. 操作前的准备a. 确保拉丝机的电源已接通,并检查电源线是否完好。
b. 检查拉丝机的各个部件是否处于正常工作状态,如传动装置、润滑系统等。
c. 检查拉丝机的工作环境是否整洁,无杂物和障碍物。
2. 上料准备a. 将待拉制的金属材料按规格整齐地堆放在拉丝机的上料台上。
b. 根据材料的种类和规格,选择合适的拉丝模具,并安装到拉丝机上。
c. 调整拉丝机的张力装置,确保适当的张力施加在金属材料上。
3. 操作过程a. 打开拉丝机的电源开关,启动机器。
b. 根据工艺要求,调整拉丝机的速度和张力,以确保拉丝过程的稳定性。
c. 观察拉丝过程中金属材料的状态,注意是否浮现断丝、卡住等异常情况。
d. 定期检查拉丝机的润滑系统,确保润滑油充足,并及时添加。
e. 定期清理拉丝机的工作区域,清除金属屑和其他杂物。
4. 操作结束a. 拉丝完成后,关闭拉丝机的电源开关。
b. 将拉丝机上的金属丝剪断,并妥善存放。
c. 清理拉丝机的工作区域,保持整洁。
d. 对拉丝机进行日常维护保养,如清洁、润滑等。
三、注意事项1. 操作人员必须经过专业培训,并持有相关操作证书。
2. 在操作过程中,严禁戴手套、长袖衣物等松散物品,以免被卷入拉丝机。
3. 操作人员应戴上安全帽、防护眼镜、防护手套等个人防护装备。
4. 在操作过程中,严禁将手或者其他物体伸入拉丝机的工作区域。
5. 发现拉丝机浮现异常情况时,应即将停机检查并及时报修。
6. 操作结束后,及时清理工作区域,保持整洁。
四、安全措施1. 拉丝机的维护和保养应由专业人员进行,确保设备的正常工作。
2. 拉丝机应安装在稳固的地面上,并确保设备周围没有杂物和障碍物。
3. 拉丝机的电源线应符合安全标准,并定期检查电线的状况。
4. 拉丝机的操作区域应设有明显的警示标识,以提醒人员注意安全。
拉丝工艺及安全操作规程模版

拉丝工艺及安全操作规程模版一、目的与范围为了确保拉丝工艺的顺利进行,保障操作人员的人身安全,并减少误操作引起的事故风险,制定本规程。
本规程适用于工厂拉丝车间的操作人员。
二、拉丝工艺步骤1.准备工作1.1拉丝设备检查:确认拉丝设备完好、无损坏情况,检查设备连接处是否牢固,正常运转是否顺畅。
1.2检查材料:确认拉丝材料的质量和数量是否符合要求。
1.3个人装备检查:佩戴好相关的劳保用品,如手套、护目镜、耳塞等,确保个人安全。
2.设置拉丝机参数2.1确定拉丝机的基本参数,如拉丝速度、温度等。
2.2根据拉丝材料的特性和要求,调整相应的参数。
3.操作流程3.1启动拉丝机:按照操作手册的规定,启动拉丝机,确保正常工作。
3.2调整拉丝材料:根据实际情况,调整拉丝材料的位置和调整装置,确保材料进入拉丝机的正确位置。
3.3操作拉丝机:根据操作手册的要求,进行拉丝操作,保持材料平稳通过拉丝机,并根据需要调整参数。
3.4完成拉丝:拉丝结束后,停止拉丝机的运转,将拉丝产品进行检查和记录。
4.清洁工作4.1停机检查:关闭拉丝机电源,确保拉丝机处于停机状态后,进行后续的清洁工作。
4.2清洁设备:使用清洁剂对拉丝机进行清洁,清除积聚的杂质和残留物。
4.3清洁作业场地:清除拉丝过程中产生的废料和灰尘,确保工作环境的整洁和安全。
4.4维护设备:对拉丝机进行定期的维护保养,确保设备的正常运转。
三、操作安全规程1.严禁站立在工作区域以及运动杆附近,以免被运动杆打伤。
2.操作前必须佩戴好相关的劳保用品,如手套、护目镜、耳塞等,确保个人安全。
3.确保拉丝机处于停机状态后,方可进行设备和材料的调整操作。
4.防止杂物进入拉丝机,以免损坏设备或引发事故。
5.拉丝过程中,严禁随意触摸设备和拉丝材料,防止被夹伤。
6.拉丝完成后,切勿直接接触拉丝产品,待产品完全冷却后方可进行进一步处理。
7.发现设备故障或异常情况,应立即停机检查并报告维修人员处理,切勿擅自继续操作。
拉丝工艺及安全操作规程范本(2篇)

拉丝工艺及安全操作规程范本一、引言本规程旨在规范拉丝工艺的操作流程,并提供安全操作规定,以确保操作人员的安全和生产的顺利进行。
遵循本规程,能够有效减少事故的发生,提高工作效率,保证产品质量。
二、工艺流程1. 打样确认操作人员根据客户要求或者内部设计要求,制作样品,并进行确认。
确认后方可正式进行拉丝工艺。
2. 材料准备1)根据产品要求选择合适的材料,并进行充分的检查,确保材料表面没有明显缺陷或损坏。
2)将材料切割成合适的长度,确保长度适应拉丝机的工作要求,并进行严密包装,以防止材料受到外界污染。
3. 机台设置操作人员应根据产品要求进行机台的设置,包括调整机台的速度、温度、压力等参数。
确保机台能够正常运行,且不损坏材料。
4. 拉丝操作1)将材料加载到拉丝机的进料口,并进行合理的固定,以防止材料在拉丝过程中出现脱落。
2)启动拉丝机,逐渐调整机台的参数,确保拉丝过程的稳定进行。
3)根据产品要求进行拉丝。
注意控制拉丝的速度和拉丝力度,避免拉丝过程中材料出现断裂或变形。
5. 拉丝末处理1)拉丝完成后,及时停止拉丝机的运行。
2)将拉丝好的材料进行检查,确保表面的平整度和光洁度符合产品要求。
3)根据需要进行拉丝末的处理,如切割、打磨、清洗等。
三、安全操作规定1. 穿戴个人防护装备在进行拉丝工艺操作前,操作人员必须穿戴符合规定的个人防护装备,包括防护眼镜、耳塞、防护手套等。
确保个人身体的安全。
2. 机台操作安全1)在进行机台设置和调试时,必须停止机台的运行,并确保机台的电源已经关闭。
2)在进行拉丝操作时,操作人员应远离机台的运动部件,避免发生意外伤害。
3)操作人员离开机台时,必须将机台的电源关闭,以避免未经授权的人员操作机台导致事故发生。
3. 材料操作安全1)操作人员在选择和准备材料时,应注意材料的特性和潜在危险性,并采取相应的防护措施。
2)在加载材料到拉丝机时,必须将材料固定好,以防止材料在拉丝过程中发生脱落。
拉丝机安全操作规程范文(3篇)

拉丝机安全操作规程范文第一章总则第一条为了保障工作人员的人身安全和设备的正常运行,规范拉丝机的安全操作,制定本规程。
第二条本规程适用于所有使用拉丝机进行生产加工的工作人员。
第三条拉丝机的安全操作是指在使用拉丝机进行生产加工时,工作人员应按照安全规定进行操作,防止人员伤害和设备事故。
第四条拉丝机的安全操作应当遵守下列原则:(一)安全第一,预防为主;(二)明确责任,分工负责;(三)依法操作,合理使用;(四)注意细节,细心操作;(五)及时整改,隐患消除;(六)经验总结,不断改进。
第二章安全管理第五条拉丝机的安全管理应当由设备管理人员负责,具体工作包括:(一)制定拉丝机的安全管理制度;(二)组织安全培训,提高员工的安全意识和操作技能;(三)定期检查拉丝机的安全状况,及时消除安全隐患;(四)落实安全防护措施,确保设备的正常运行;(五)组织安全应急演习,提高员工应对突发事故的能力。
第六条拉丝机使用单位应当制定拉丝机的安全管理制度,明确各个岗位的职责,建立安全操作流程,严格执行。
第七条拉丝机使用单位应当设立安全监督员,负责对拉丝机的安全操作进行监督和管理,及时发现问题并提出整改意见。
第八条拉丝机使用单位应当保障工作人员的安全培训,确保其具备必要的安全知识和技能。
第九条拉丝机使用单位应当建立安全档案,包括设备维修保养记录、事故隐患排查记录、安全培训记录等。
第三章安全操作第十条拉丝机的操作人员应当是具备相应的操作技能和经验的人员,经过专门的培训合格后方可上岗操作。
第十一条拉丝机操作人员应当熟悉拉丝机的工作原理和技术规范,严格按照操作规程进行操作。
第十二条拉丝机操作人员在操作过程中应当遵守以下安全要求:(一)佩戴好劳动防护用品,如安全帽、安全鞋等;(二)严禁擅自修改设备参数,超负荷操作;(三)设备故障时应当立即停机检修,切勿私自开启;(四)操作过程中应当注意观察设备运行情况,发现异常及时报告。
第十三条拉丝机操作人员禁止进行下列行为:(一)饮酒、吸烟等影响工作安全的行为;(二)疲劳驾驶,超时操作;(三)在设备运行时随意接触设备部件;(四)停机维修时未切断电源、排放压缩空气等操作。
拉丝机安全操作规程范本(三篇)
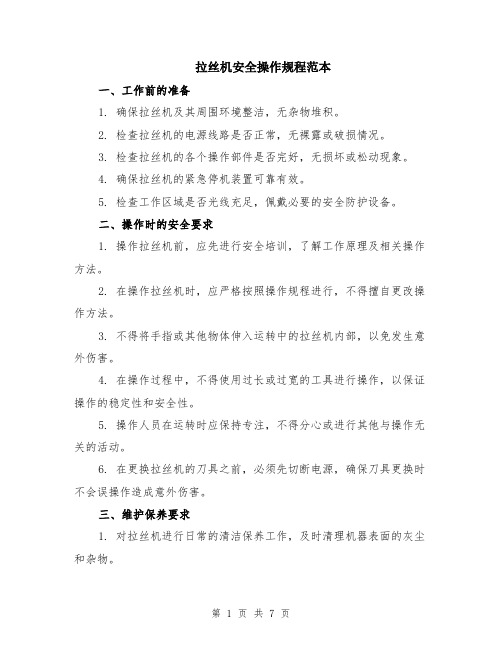
拉丝机安全操作规程范本一、工作前的准备1. 确保拉丝机及其周围环境整洁,无杂物堆积。
2. 检查拉丝机的电源线路是否正常,无裸露或破损情况。
3. 检查拉丝机的各个操作部件是否完好,无损坏或松动现象。
4. 确保拉丝机的紧急停机装置可靠有效。
5. 检查工作区域是否光线充足,佩戴必要的安全防护设备。
二、操作时的安全要求1. 操作拉丝机前,应先进行安全培训,了解工作原理及相关操作方法。
2. 在操作拉丝机时,应严格按照操作规程进行,不得擅自更改操作方法。
3. 不得将手指或其他物体伸入运转中的拉丝机内部,以免发生意外伤害。
4. 在操作过程中,不得使用过长或过宽的工具进行操作,以保证操作的稳定性和安全性。
5. 操作人员在运转时应保持专注,不得分心或进行其他与操作无关的活动。
6. 在更换拉丝机的刀具之前,必须先切断电源,确保刀具更换时不会误操作造成意外伤害。
三、维护保养要求1. 对拉丝机进行日常的清洁保养工作,及时清理机器表面的灰尘和杂物。
2. 定期检查拉丝机的电源线路和插头,保证其无脱落或断裂等危险情况。
3. 定期清理拉丝机的过滤器和冷却系统,确保其正常工作。
4. 不得随意拆卸和修理拉丝机,如出现故障应及时停机,并寻找专业人员进行维修。
四、紧急情况的应急措施1. 在拉丝机发生故障时,应立即切断电源,并进行相应的维修和检查。
2. 在必要时可以使用拉丝机的紧急停机装置进行急停操作,以确保操作者的安全。
3. 对于突发的火灾等紧急情况,应立即向相关部门报警并按照应急预案进行逃生和灭火。
结语:拉丝机是一种重要的生产设备,在操作和维护保养时必须严格按照操作规程进行。
通过正确的操作和维护,可以确保拉丝机的安全运行,防止意外事故的发生。
因此,操作者必须严格遵守安全要求,保障自己的安全同时也保障生产的安全,达到预期的生产效果。
拉丝机安全操作规程范本(二)拉丝机是一种常见的金属加工设备,用于将金属坯料通过拉伸作用,使其变细,形成所需的细丝或线材。
拉丝工艺及安全操作规程

拉丝工艺及安全操作规程一、工艺介绍拉丝工艺是一种金属加工方法,通过将金属材料拉伸,使其截面积减小,长度增加,从而得到希望的形状和尺寸。
拉丝工艺通常用于金属丝、线和管材的生产,广泛应用于机械、电器、汽车等行业。
二、工艺步骤1. 材料准备:根据产品要求选择适当的金属材料,并进行表面清洁和除杂处理。
2. 加热处理:将金属材料进行预热,以提高可塑性。
3. 钢丝拉拔:将金属材料放入拉丝机,通过连续拉拔、减小截面积的方式,使其逐渐细长。
4. 退火处理:在拉拔过程中,适时进行退火处理,以减少材料的硬度和提高韧性。
5. 表面处理:拉拔完成后,对产品表面进行清洁和去除氧化层的处理。
6. 包装:将拉丝成品按规格包装,并进行标识和入库。
三、安全操作规程1. 穿戴个人防护装备:在操作拉丝机前,必须穿戴好防护帽、防护眼镜、防护口罩、防护手套和防护鞋等个人防护装备。
2. 熟悉设备操作:操作人员必须接受拉丝机的专业培训,熟悉设备的结构和运行原理,并掌握操作技巧。
3. 检查设备状态:在操作拉丝机前,要仔细检查设备的电气线路、润滑系统和传动部件等是否正常,确保设备安全可靠。
4. 避免超负荷操作:根据产品要求和设备的负荷参数,合理安排拉丝速度、拉伸力和拉丝次数,避免超负荷操作。
5. 注意设备维护:定期对拉丝机进行保养和维护,包括清洁润滑、紧固螺栓、更换磨损部件等,以确保设备的正常运行。
6. 停机前的准备工作:在停机前,要关闭拉丝机电源、切断气源,并清理工作场地,将拉丝机及配件归位整理。
四、安全防范措施1. 防火安全:严禁在拉丝机附近进行吸烟、明火操作和使用易燃、易爆物品。
2. 用电安全:拉丝机电源接地良好,电气线路完好无损,严禁私拉乱接电源线,避免电气火灾。
3. 防护装置:拉丝机应安装防护罩和安全开关,确保操作人员不会接触到旋转部件和运动件,以减少事故风险。
4. 废料处理:拉丝过程中产生的废料要统一收集,严禁乱堆乱放,避免刮伤和坠落事故。
拉丝机操作规程
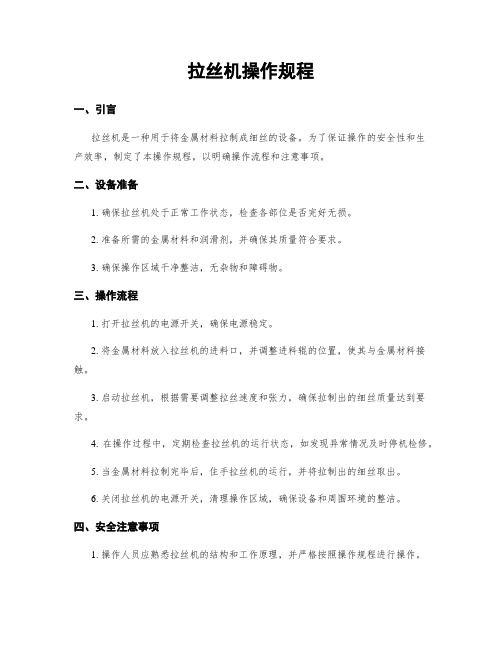
拉丝机操作规程一、引言拉丝机是一种用于将金属材料拉制成细丝的设备。
为了保证操作的安全性和生产效率,制定了本操作规程,以明确操作流程和注意事项。
二、设备准备1. 确保拉丝机处于正常工作状态,检查各部位是否完好无损。
2. 准备所需的金属材料和润滑剂,并确保其质量符合要求。
3. 确保操作区域干净整洁,无杂物和障碍物。
三、操作流程1. 打开拉丝机的电源开关,确保电源稳定。
2. 将金属材料放入拉丝机的进料口,并调整进料辊的位置,使其与金属材料接触。
3. 启动拉丝机,根据需要调整拉丝速度和张力,确保拉制出的细丝质量达到要求。
4. 在操作过程中,定期检查拉丝机的运行状态,如发现异常情况及时停机检修。
5. 当金属材料拉制完毕后,住手拉丝机的运行,并将拉制出的细丝取出。
6. 关闭拉丝机的电源开关,清理操作区域,确保设备和周围环境的整洁。
四、安全注意事项1. 操作人员应熟悉拉丝机的结构和工作原理,并严格按照操作规程进行操作。
2. 在操作过程中,严禁将手部或者其他物体挨近拉丝机的运动部位,以免发生危(wei)险。
3. 操作人员应佩戴好防护用具,如手套、护目镜等,确保个人安全。
4. 在操作前,应检查拉丝机的电源线是否接地良好,以防电击事故发生。
5. 操作人员应定期检查拉丝机的保护装置和安全设备是否完好,并及时修理或者更换损坏的部件。
6. 操作人员应严禁将湿手接触拉丝机或者其电源开关,以免发生触电事故。
7. 操作人员应保持操作区域的整洁,避免杂物和障碍物对操作造成干扰。
五、维护保养1. 定期对拉丝机进行清洁和润滑,确保设备的正常运行。
2. 检查拉丝机的传动部件和电气设备,如发现异常情况及时处理。
3. 定期更换拉丝机的磨损部件,如滚轮、皮带等,以保证设备的工作效率和安全性。
4. 每次操作结束后,对拉丝机进行全面检查,如发现问题及时报修。
六、紧急情况处理1. 在发生设备故障或者其他紧急情况时,即将停机,并按照紧急处理程序进行操作。
拉丝操作规程
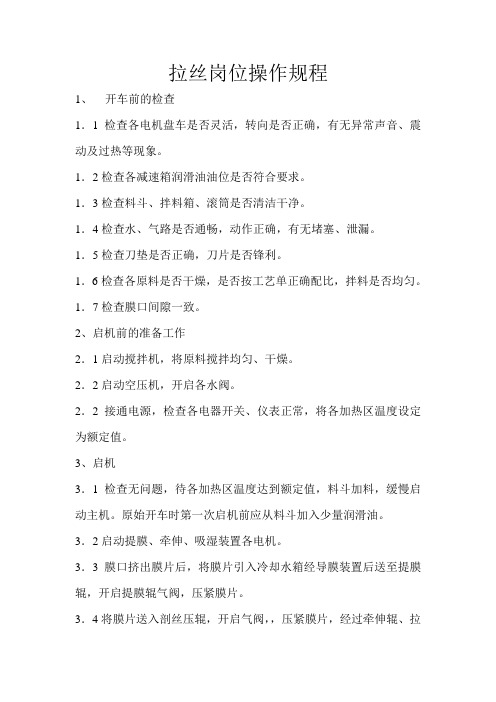
拉丝岗位操作规程1、开车前的检查1.1检查各电机盘车是否灵活,转向是否正确,有无异常声音、震动及过热等现象。
1.2检查各减速箱润滑油油位是否符合要求。
1.3检查料斗、拌料箱、滚筒是否清洁干净。
1.4检查水、气路是否通畅,动作正确,有无堵塞、泄漏。
1.5检查刀垫是否正确,刀片是否锋利。
1.6检查各原料是否干燥,是否按工艺单正确配比,拌料是否均匀。
1.7检查膜口间隙一致。
2、启机前的准备工作2.1启动搅拌机,将原料搅拌均匀、干燥。
2.2启动空压机,开启各水阀。
2.2接通电源,检查各电器开关、仪表正常,将各加热区温度设定为额定值。
3、启机3.1检查无问题,待各加热区温度达到额定值,料斗加料,缓慢启动主机。
原始开车时第一次启机前应从料斗加入少量润滑油。
3.2启动提膜、牵伸、吸湿装置各电机。
3.3膜口挤出膜片后,将膜片引入冷却水箱经导膜装置后送至提膜辊,开启提膜辊气阀,压紧膜片。
3.4将膜片送入剖丝压辊,开启气阀,,压紧膜片,经过牵伸辊、拉伸烘板、定型板、后送入边膜废丝吸收装置。
3.5检查膜片无杂质、无花纹、厚薄均匀后打下剖丝刀架。
3.6设定好主机、提膜、牵伸、定型各电机转速,测量扁丝厚度达到要求后,启动收卷机挂丝。
4、正常停机4.1将主机转速逐渐将至0,膜口不再有料挤出,关闭各单机按钮,关闭总电源。
4.2关闭气、水路,松开各压辊。
4.3将废丝清理干净,机器、地面打扫干净,现场摆放整洁。
5、紧急停机发生危及人生安全、设备重大事故时,按下紧急停机按钮,拉丝机将全部停止运行,然后按正常停机步骤进行停机。
拉丝机工安全操作规程模版(3篇)

拉丝机工安全操作规程模版第一章总则为了保障拉丝机工作人员的人身安全和设备设施的安全运行,提高工作效率,根据相关法律法规和安全规范,制定本拉丝机工安全操作规程。
第二章工作条件和环境1. 工作场所应保持整洁,通风良好,无易燃、易爆物品、有害气体和灰尘,地面应保持干燥,设有必要的安全警示标识。
2. 工作现场应配备灭火器、急救箱等应急设备,保持设备完好,随时可用。
3. 拉丝机应位于稳固平坦的地面上,并设置防护栏杆,禁止任何人员靠近或触摸设备。
第三章人员规定1. 拉丝机工作人员应取得相关岗位操作证书,并经过专业培训,掌握拉丝机的工作原理、操作方法和安全知识。
2. 工作人员必须严格遵守操作规程,熟悉掌握设备操作步骤,不得擅自修改或调整设备参数。
3. 着装要求:工作人员应穿戴符合工作要求的防护服、安全鞋,长发应束起或戴防护帽。
4. 严禁饮酒、吸烟、咀嚼口香糖等影响工作安全和操作的行为。
第四章设备操作1. 开机前,工作人员应进行设备检查,确认设备运行正常,各部位无杂物。
2. 操作前应先阅读设备操作手册,熟悉设备的操作流程和注意事项。
3. 操作中严禁将手或其他物体伸入运转中的拉丝机内,以避免伤害。
4. 拉丝机在运转过程中,禁止改变设备的运行状态或参数设置,并且应时刻保持设备的正常工作状态。
第五章安全防护1. 工作人员在操作设备时,应配戴好必要的安全防护用品,如护目镜、防护手套等。
特别是拉丝机操作中易产生的金属屑、飞溅的油烟等要增加相应的防护措施。
2. 按规定使用防护装置,如安全防护栏杆、防护网等,严禁随意拆卸、遮挡。
3. 当设备发生故障时,应立即停机并通知维修人员处理,严禁私自进行维修或继续使用。
第六章火灾和事故应急处理1. 拉丝机发生火灾时,应立即按设备上的应急按钮或灭火器将火灭掉,并及时通知消防部门。
2. 发生人员受伤、触电、中毒等事故时,应立即停机,并进行紧急救护措施或拨打急救电话。
3. 发生其他意外事故时,应根据现场情况采取安全措施,及时通知相关部门并进行事故调查和处理。
拉丝机操作规程
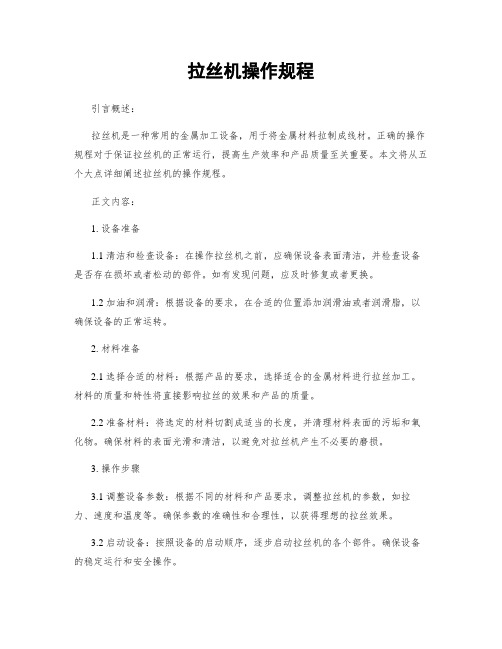
拉丝机操作规程引言概述:拉丝机是一种常用的金属加工设备,用于将金属材料拉制成线材。
正确的操作规程对于保证拉丝机的正常运行,提高生产效率和产品质量至关重要。
本文将从五个大点详细阐述拉丝机的操作规程。
正文内容:1. 设备准备1.1 清洁和检查设备:在操作拉丝机之前,应确保设备表面清洁,并检查设备是否存在损坏或者松动的部件。
如有发现问题,应及时修复或者更换。
1.2 加油和润滑:根据设备的要求,在合适的位置添加润滑油或者润滑脂,以确保设备的正常运转。
2. 材料准备2.1 选择合适的材料:根据产品的要求,选择适合的金属材料进行拉丝加工。
材料的质量和特性将直接影响拉丝的效果和产品的质量。
2.2 准备材料:将选定的材料切割成适当的长度,并清理材料表面的污垢和氧化物。
确保材料的表面光滑和清洁,以避免对拉丝机产生不必要的磨损。
3. 操作步骤3.1 调整设备参数:根据不同的材料和产品要求,调整拉丝机的参数,如拉力、速度和温度等。
确保参数的准确性和合理性,以获得理想的拉丝效果。
3.2 启动设备:按照设备的启动顺序,逐步启动拉丝机的各个部件。
确保设备的稳定运行和安全操作。
3.3 进料和拉丝:将准备好的材料送入拉丝机,并通过适当的张力和速度控制,使其通过拉丝机的机构进行拉制。
注意材料的进料速度和张力的控制,以避免产生拉丝不均匀或者断裂等问题。
4. 安全注意事项4.1 穿戴个人防护装备:操作拉丝机时,应佩戴适当的个人防护装备,如手套、护目镜和耳塞等,以保护自身安全。
4.2 遵守操作规程:严格按照操作规程进行操作,不得随意更改设备参数或者操作方式,以避免事故发生。
4.3 定期维护和检修:定期对拉丝机进行维护和检修,清理设备内部的杂物和润滑部件,以保证设备的正常运行和安全使用。
总结:综上所述,拉丝机的操作规程对于保证设备的正常运行和产品质量至关重要。
正确的设备准备、材料准备、操作步骤和安全注意事项将有助于提高生产效率和产品质量。
拔丝(拉丝)机机械安全技术操作规程

拔丝(拉丝)机机械安全技术操作规程拔丝(拉丝)是一种常见的金属加工工艺, 在金属制品制造、机械加工等领域广泛应用。
为确保工作安全、提高生产效率, 以下是拔丝(拉丝)机机械安全技术操作规程。
一、操作前的准备工作1.1 工作人员必须熟悉拔丝(拉丝)机的结构、性能和操作规程, 了解各种控制和保护装置的作用。
1.2 确定拔丝(拉丝)机械的通电、断电和主轴启动等操作的电源接线装置是否正常。
1.3 检查拔丝(拉丝)机的润滑系统, 确保润滑油充足, 并清理机床周围的杂物。
1.4 确认拔丝材料的品种、尺寸和数量与订单要求一致。
二、机械操作规程2.1 上岗前应穿戴好劳保用品, 包括安全鞋、工作服和劳保手套, 并戴好防护眼镜。
2.2 操作人员应按要求设置机械的工作参数, 包括拉丝速度、拉丝力和拉丝长度等, 并调整好针板位置和夹具。
2.3 开机前, 应确保工作台面和机床周围无杂物, 并通知其他相关人员远离操作区域。
2.4 启动机械前, 应拉动紧急停止开关, 确保机械处于安全状态。
2.5 启动机械后, 要用安全防护罩将拉丝区域封闭, 防止操作人员的身体或衣物被卷入机械中。
2.6 在操作过程中, 严禁使用手指或其他身体部位接触旋转机械部件, 切勿将手伸入安全防护罩内。
2.7 注意观察机械运行状况, 如发现异常应立即停机检查, 并通知上级或维修人员处理。
2.8 在拔丝(拉丝)机停机后, 应将机械上部分余料清理干净, 减少杂质对下次操作的影响。
三、安全措施3.1 严禁将非工作人员进入操作区域。
3.2 拔丝(拉丝)机的主电源必须使用专门的电源插头和插座, 并设置绝缘保护装置。
3.3 如需重启机械, 应先调整为最低速度, 并保持一段时间, 确认没有异常才能逐步增加速度。
3.4 禁止在操作机械时进行其他与工作无关的活动, 如吃东西、抽烟等。
3.5 操作人员在机械作业时不得戴有不利于安全的饰品, 如手链、项链等。
3.6 发生事故或发现不安全现象时, 应立即停机并及时上报相关负责人或维修人员, 严禁擅自私自处理。
拉丝工艺及安全操作规程

拉丝工艺及安全操作规程拉丝工艺是一项常见的加工工艺,用于加工金属材料,制造出用于各种领域的各种零件。
本文将介绍拉丝工艺及其安全操作规程。
拉丝工艺拉丝工艺是一种将金属材料经过一定的变形加工,使其变细长、光亮的工艺。
该工艺可以应用于多种金属材料,例如铜、铝、钢、锌、镁、锡、镍以及其它合金。
拉丝工艺一般按照以下步骤进行:1.材料准备:选择适当的金属材料,并配备相应的拉丝机械设备。
2.切割材料:使用切割工具将材料切割成合适的长度。
3.清洗材料:使用清洗工具将材料清洗干净,以便于后续的操作。
4.加热处理:对某些需要进行加热处理的材料,进行适当的加热,提高其塑性。
5.拉丝加工:将加热后的材料输送到拉丝机械设备,进行拉伸加工,逐渐将材料变细长、光亮。
6.清洗材料:将拉丝加工后的材料清洗干净,以去除表面残留物。
7.成品加工:将拉丝加工后的材料切割成合适的长度,并进行后续的加工处理。
安全操作规程在进行拉丝工艺时,需要注意一些安全操作规程,以保证人员和设备的安全。
以下是拉丝工艺中的安全操作规程:1. 操作前检查设备在进行拉丝工艺时,需要事先检查设备的连接状态和工作情况,确保设备连接紧密,且设备运转正常。
2. 穿戴安全防护装备在进行拉丝工艺时,需要穿戴安全防护装备,如手套、护目镜、耳塞等,以避免身体受到金属材料、机器以及杂音的伤害。
3. 安全围栏在拉丝机械设备周围需要设置足够高的安全围栏,以避免材料滑出机器或是不慎踩进机器造成人员伤害。
4. 操作时保持清醒在进行拉丝工艺时,必须保持清醒,避免精神状态不佳导致安全事故。
5. 材料处理夹持材料时,需要使用夹具或机械设备,杜绝手动操作。
同时,加工后的材料必须在指定的区域里存储,以避免操作时弯曲、压碎等数据。
6. 维护设备操作完成后,必须对设备进行日常维护保养,清理设备及周围区域。
7. 急救措施在操作时,如发生意外事故,必须立即停止设备运转,并采取相应的急救措施。
拉丝工艺及安全操作规程是保证加工质量、人员和设备安全的一项重要措施。
拉丝机工安全操作规程

拉丝机工安全操作规程拉丝机工安全操作规程一、基本要求1. 操作前须认真检查设备及工具是否完好无损,气压是否足够、电线是否有磨损或老化现象,如有问题应及时反映。
2. 进入工作区域前先了解工作环境,并佩戴好必要的防护用品。
3. 操作时不得戏闹打闹,注意分工协作,严格遵守工作规程。
4. 操作时应专心致志,不得分心、喧哗或接听手机等影响安全的行为。
5. 对设备进行维护、保养时,必须在机器停开后,拆卸、修复。
6. 改变设备的任何位置之前, 必须通知负责人员。
7. 操作结束后,及时清理设备,将各类工具摆放在指定位置。
二、机器操作1. 路径操作清洁、整洁,避免堵塞或有别的危险现象。
2. 严格依照生产计划工作,确保设备正常、平稳运转。
3. 不得超出机器规定的工作压力范围,保持油管连降压器连接紧密牢固。
4. 机器方向、转速及控制动作应严格按照操作规程或工艺流程要求,不得有偏差。
5. 禁止在因操作不当而把卷杆转未展开并停住时,仍然继续操作机器。
6. 放线中禁止在线轮拉动冷轧钢,禁止朝轴心方向塞入物品。
7. 禁止在卸下、装上卷杆的过程中,用手的粘杂物品去碰机器。
8. 人员在操作机器时,不得将手、脚等身体组件放入任何可能造成损害设备的位置,尤其更不能将任何身体组件伸进机器内部。
9. 防止切削液泄漏,要保持机床干净、清洁,关闭相关阀门,并及时汇报。
发现切削液泄漏,应立即停止机器运行,安排清洁、处理。
三、电气部分1. 电器设备应在合适的保养计划内进行检查、清理、保养。
2. 操作机器时,操作人员应先触动机器断电开关切断电源,然后操作设备开启。
3. 操作机器时,操作人员应勿超出设备的额定电压范围,同时应注意设备的加热情况,防止电气跳开。
4. 对电器设备进行维修保养时,必须保证设备断电后再进行,工具应当是绝缘的,严禁短路、不慎接地等操作不当行为。
四、个人安全1. 保持良好的个人卫生,工作服必须符合安全标准并且穿好,穿戴合适的防护用品。
拉丝机操作规程

拉丝机操作规程拉丝机操作规程一、操作前准备1. 确保拉丝机处于停止状态,且电源已关闭。
2. 检查机器是否有损坏或松动的部件,如有需及时修复或固定。
3. 清理工作台面、地面和机器周围的杂物,确保操作区域整洁有序。
4. 检查拉丝机的油液是否充足,如有必要,应添加或更换油液。
二、启动准备1. 确保拉丝机的电源插头已正确接入电源插座。
2. 检查拉丝机控制面板上的电源开关是否处于关闭状态。
3. 按照机器使用手册中的步骤,正确设置拉丝机的工作参数,如速度、张力等。
4. 检查液压系统是否正常,如液压油是否充足,压力是否正常。
三、操作步骤1. 调整模具:根据所需要的拉丝规格,选择合适的模具,安装到拉丝机上,并紧固好。
2. 放置工件:将需要拉丝的工件放置于拉丝机的工作台上,并调整工件的位置,确保工件与模具对齐。
3. 开启电源:打开拉丝机的电源开关,待机器进入正常工作状态后,进行下一步操作。
4. 设定参数:根据工件的材质和尺寸,设定拉丝机的拉丝参数,如速度、张力、润滑等。
5. 调试:将模具与工件接触,调整拉丝机的工作参数,逐渐增加工作压力,观察拉丝效果,如出现异常情况应立即停机检查。
6. 拉丝操作:按下控制面板上的启动按钮,拉丝机开始工作,同时手握拉丝机的操作杆,沿着工件的轴线进行拉动,以完成拉丝工作。
7. 检查质量:拉丝完成后,停止拉丝机的运行,取出拉丝后的工件,检查拉丝质量是否符合要求,如有问题应记录并及时调整机器或模具。
四、操作注意事项1. 操作人员必须熟悉拉丝机的操作流程和安全规程,并接受相关培训。
2. 操作人员应佩戴符合规定的个人防护装备,如安全帽、防护眼镜、耳塞等。
3. 在操作过程中,严禁戴手套、长袖衣物,以免发生危险。
4. 拉丝机的电源必须使用接地插头,并确保接地良好。
5. 在操作前应对拉丝机进行检查,如发现异常情况应立即停机并通知相关人员进行维修。
6. 拉丝机应定期进行保养和维护,确保设备处于良好的工作状态。
拉丝工艺及安全操作规程

仅供参考[整理] 安全管理文书
拉丝工艺及安全操作规程
日期:__________________
单位:__________________
第1 页共3 页
仅供参考[整理]
拉丝工艺及安全操作规程
一、拉丝工在交接班时首先要检查模具是否光滑,电机及传动设备是否运转正常,模具里是否有足够的拉丝油等。
二、拉丝工在上班时要穿戴好劳动保护用品,做到不串岗离岗,不去开与本职工作无关的机台或电器设备,每盘丝到头要特点注意小心头子甩出伤人。
三、每道工序在拉丝时要检查是否有突出、太精、太细、鱼鳞等明显的质量问题,拉丝过程中出现的断丝,应分清原因,自己拉的丝要做好自检工作,做到不把问题丝流到后道工序中去,做到后道监督前道,各道拉丝要轻拿轻放,不准野蛮操作,严禁检大甩小。
四、拉丝工在拉丝时产生的废丝,不准自行拿出拉出拉丝车间,必须有人称重后进行压捆或剪切,再放到指定的位置。
五、各道拉丝工在拉丝时要把上道的跟踪卡保管好,并按跟踪卡的批次进行拉丝,再填写上道跟踪卡所对应的本道跟踪卡,各道跟踪卡均有下道收取。
六、拉丝工在下班前必须做好自己机台周围的清洁卫生工作。
第 2 页共 3 页
仅供参考[整理] 安全管理文书
整理范文,仅供参考!
日期:__________________
单位:__________________
第3 页共3 页。
- 1、下载文档前请自行甄别文档内容的完整性,平台不提供额外的编辑、内容补充、找答案等附加服务。
- 2、"仅部分预览"的文档,不可在线预览部分如存在完整性等问题,可反馈申请退款(可完整预览的文档不适用该条件!)。
- 3、如文档侵犯您的权益,请联系客服反馈,我们会尽快为您处理(人工客服工作时间:9:00-18:30)。
拉丝操作规程
1、拉拔操作过程
工艺:放线——润滑——模具——收线
2、作业程序及要点
2.1拉拔定义:使直径较大的金属材料强行通过拉丝模具,得到所要求的直径大小。
2.2拉拔时的受力分析:代受到拉拔力,正压力与摩擦力。
2.3拉拔前的准备:各班准备各班所用的收线架,拉拔前注意投料的钢丝应是同一批号或炉号的原料组成,班组长应注意选择润滑剂,选择模具,查看拉丝机与冷却水的运转情况,以及扎尖机、对焊机与放线架、收线架的动转情况,与短线钳等拉丝用具。
2.4润滑剂的选择:对于不同直径,不同钢号的钢丝应选用不同的润滑剂,润滑剂的主要性能是粘附、耐热、耐压、延展性好、无误、无毒、不发生化学或物理变化。
本厂对中高碳钢丝选用G38或G58的拉丝粉。
2.5模具的选择:原则是根据钢丝含钢丝含碳量的大小选用模具,对于中高碳钢丝应选用硬质合金构造。
2.6模具的配置:根据成品钢丝的直径与所拉道次配模,也就是根据压缩比配模。
通常第一道次与最后一道次压缩比销小,中间道次逐渐递减的情况配模,初拉道次的压缩比不得超过40%。
2.7拉拔的过程:将钢丝用行车吊入放线架上,将钢丝的一头放入扎尖机上扎尖,然后在模具盒内放入模具与拉丝粉,打开冷却水阀门,扎尖好的钢丝穿过模具盒,再用铁链将钢丝卡紧,铁链的另一关挂在收线机上,最后开动主动放线机与收线机的操作仪器,钢丝即开始拉拔。
2.8拉拔过程中的注意事项:
2.8.1拉拔前班组长简单检验拉丝机放线机与收线机的电路情况。
2.8.2拉拔过程中应注意润滑剂的润滑效果。
2.8.3拉拔过程中应注意半成品钢丝的表面质量,不得有裂纹与结疤。
钢丝表面的颜色应为黑亮色。
2.8.4拉拔过程中每盘钢丝的对焊头应涂上硫酸铜,这样拉拔后的焊头就清晰可见,便于切除。
2.8.5拉拔后的最后一道钢丝也应挂上相应的标牌。
2.8.6拉出后的前三道半成品钢丝直径在范围在上下1.5mm之间。
2.9注意控制台与工作场地的卫生情况,做到交班打扫。
2.10班组长在交班前必须填写《生产进度管理表》与《钢丝拉拔作业交接班记录》。
3稳定化生产线操作过程
工艺:放线——定径——螺旋——润滑——矫直——加热——冷却——张力——牵引——飞剪——收线
3.1稳定化处理的定义:钢丝在受到30%~50%抗拉强度的作用下,对钢丝进行消除应力回火,温度在350~400,这种工艺好稳定化处理。
3.2稳定化处理的特点:消除钢丝的残余应力。
得到的松驰要求为低松驰级别。
伸直性良好,通条性能均匀稳定。
自动化程度高,节约成本,提高生产效率。
对环境无污染。
3.3放线操作:放线机离定径模之间的距离保持在5~7米。
便于更好的控制钢丝的走线速度,也利于发生意外时的紧急处理,放线机的走线速度应根据张力的变动来作自身调节。
5.4.4定径的操作:为了保证成品钢丝的性能要求,就要使处理时的进线直径在一个范围之间调整钢丝的进线直径是根据压缩比。
压缩比的范围在10%~15%之间。
3.5螺旋与轴承润滑的操作:保证钢丝经过螺旋模具后的肋纹在要求范围。
采用润滑剂时应注意用久后的液体会有杂质,应经常更换。
3.6矫直的操作:根据成品钢丝的伸直性来调节,组合式的矫直滑轮应该相互挤压。
3.7对定径、螺旋、矫直的注意事项:模具、模合的位置是否在同一条直线上。
矫直轮的挤压情况,保证钢丝的伸直性。
润滑液的清理情况,保证轴承的运转速度。
稳定化处理时应时常注意成品钢丝的螺旋肋高度与宽度。
3.8加热、冷却、张力、牵引、飞剪、收线操作:
操作时,先打开冷却装置的阀门,再打开测温仪的电源开关,让测温仪上的温度显示在500℃左右,然后将钢丝穿入加热炉内,然后启动张力轮与牵引轮以及收线机,将张力的频率调到30HZ,如过太慢会使得钢丝的加热炉内烧断,太快会浪费更多的钢丝。
然后将钢丝在张力轮上套上5圈后,就将钢丝穿入牵引轮,最后进入收线机内。
3.9注意事项:
升温时应随时注意测温仪的温度与张力频率之间的调节。
在达到稳定温度与稳定张力的时候,应在牵引轮后剪断钢丝,然后将钢丝换到另一个收线机上,不稳定处理时的钢丝做为下次处理的穿线钢丝。
应注意调节水量的大小,钢丝经过冷却后表面不得带有水珠。
在放线时进行的对焊头涂上硫酸铜,在经过处理后必须切除。
处理过程中,主动放线机与收线机的控制台都应该留有一人操作。
未经负责人同意,不得随意改变测温仪上的温度与张力装置的频率。
应注意,收线机的频率始终小于张力装置的频率。
3.10注意控制台与工作场地的卫生情况,做到交班打扫。
3.11做出《稳定化处理记录表》。
4收线打包操作规程:
4.1每盘重量:100~200公斤。
4.2换盘时间:60~70分钟。
4.3每盘打包次数:6次,并捆牢固。
4.4每盘剪切后应在头尾留有70cm的样品,并注入标识。
4.5在放线时的对焊头,稳定化处理后,必须切除。
4.9每盘重量可根据客户要求的更改做出临时通知。
4.10此规程均为在温度、张力恒定,不断线时采用,如遇断线情况。
则另行处理。