DFM、DFT和产品试制验证管理
产品中试管理

精品培训课程课程名称RDM012产品中试管理--从样品到量产Product Piloting-from sample to mass production参加对象企业CEO/总经理、研发总经理/副总、测试部经理、中试/试产部经理、制造部经理、工艺/工程部经理、质量部经理、项目经理/产品经理、高级制造工程师等课程背景我们在为企业提供研发管理咨询服务的过程中发现,很多企业的新产品开发从样机到量产的过程中(产品化过程)存在着共同的问题:1. 新品没有经过中试或中试的时间很短,制造部门戏称研发的新品是“三无”产品,没有生产文件、没有工装、生产现场出了问题没人管;2. 转产没有标准,研发想快点转产,生产对有问题的产品又不愿接收,希望研发把问题都解决了才转过来,而市场又催得急,经常被迫接收,长此以往,导致研发与生产的矛盾激化;3. 有些企业开始成立中试部门,希望在中试阶段把产品质量问题解决掉,但中试的定位与运作也很困惑,发生质量与进度的冲突时,如何取舍与平衡,以前研发与制造的矛盾转化为研发与中试、中试与生产的矛盾,中试成了矛盾集散中心;4. 市场的压力并不因中试的产生而减少,中试需要从哪些方面努力才能满足产品的质量、进度的要求?中试的业务是面向研发还是面向制造,还是兼而有之?5. 量产后才发现产品可制造性差、成品率低、经常返工,影响发货;6. 产品到了生产后还发生大量的设计变更;7. 产品到了客户手中还冒出各种各样的问题以致要研发人员到处去“救火”。
本课程将基于多年的实践、长期的研发咨询积累,总结出一套理论与实践相结合的可操作的方法,配以大量实际案例,以指导研发/试产/制造部门主管如何高效的实现产品从样品走向量产。
培训收益1. 了解业界公司在不同发展阶段的产品中试管理模式与实践2. 掌握面向制造系统的产品设计(DFM)的方法与实施过程3. 掌握面向生产测试的产品设计(DFT)的方法与实施过程4. 掌握面向制造系统的新产品验证的过程与方法5. 掌握在满足质量标准的前提下缩短产品试制周期的方法和技巧6. 了解如何建立从样品到量产的管理机制培训课时2天(12小时)课程大纲一、案例研讨二、从样品到量产概述1. 企业在追求什么:技术?样品?产品?商品?2. 研发与制造的矛盾:1). 制造系统如何面对研发的三无产品?2). 研发如何面对制造系统越来越高的门槛?3. 研发与制造矛盾的激化:中试的产生成为必然4. 中试的定位与发展:1). 研发(RD)、中试(D&P)、生产(P)的关系2). 中试的使命是什么?3). 中试如何定位?4). 中试的发展问题:●大而全?●专业化分工?●产品线划分与共享平台●中试人员的发展定位:广度与深度问题5. 中试的业务范围1). 中试业务:新产品导入(NPI)2). 承上:如何面向产品的研发?3). 启下:如何面向产品的制造?4). 桥梁:中试作为连接研发与制造的桥梁,独木桥还是阳关道?6. 演练与问题讨论1). 根据企业的实际情况,是否需要建立并发展中试的职能?三、新产品导入团队1. 新产品导入团队的构成1). 工艺工程2). 设备工程3). 测试工程4). 工业工程5). 产品验证6). 试生产(计划、生产、质量)2. 新产品导入团队的职责3. 新产品导入团队与产品开发团队的关系1). 开发模式的演变:串行变并行2). 并行工程在产品开发中如何体现?3). 新产品导入团队如何提前介入研发?●为什么要提前介入?●提前到什么时候介入?●提前介入做什么?4). 新产品导入团队的管理●新产品导入团队与产品开发团队、职能部门的沟通●新产品导入团队成员的汇报、考核和管理机制4. 演练与问题讨论1). 根据企业的实际情况,研讨建立新产品导入团队的时机四、面向制造系统的产品设计(DFM)1. 如何在产品设计与开发过程中进行可制造性设计1). 从制造的角度来看产品设计2). 工艺人员介入产品开发过程的切入点:从立项就开始3). 工艺管理的三个阶段:工艺设计、工艺调制与验证、工艺管制4). 工艺设计:●如何提出可制造性需求?●需要哪些典型的工艺规范?●可制造性需求如何落实到产品设计方案中?●工艺设计与产品设计如何并行?●产品工艺流程设计●电装、整装、包装与物流的可制造性设计分析●如何确保可制造性需求在产品开发中已被实现?●工艺评审如何操作?●什么时候考虑工装?●如何在开发过程中同步输出工艺文件与生产操作指导文件5). 工艺调制与验证●工艺验证的时机●工艺验证方案包括哪些内容?●如何实施工艺验证?●工艺验证报告的内容●如何推动工艺验证的问题解决?●研发人员如何配合新产品的工艺验证?●制造外包模式下的工艺如何验证?6). 工艺管制●工艺管制的困惑:救火何时是尽头?●工艺转产评审(标准、流程、责任)●量产过程中的例行监控与异常管理2. 演练与问题讨论1). 分析学员企业的工艺管理工作做到什么程度?存在哪些差距?3. 工艺管理平台建设1). 谁负责工艺平台的建设?2). 工艺委员会的产生:责任与运作模式3). 如何进行工艺规划?4). 基础工艺研究与应用5). 支撑工艺管理平台的四大规范:●品质规范●设备规范●工艺规范。
DFM面向制造的设计
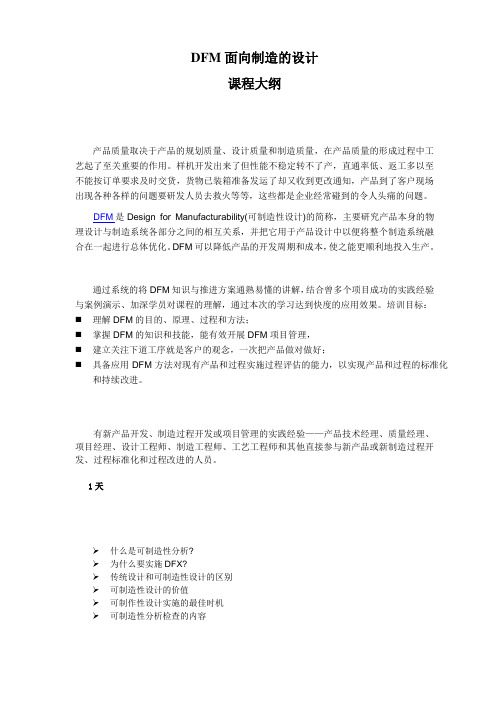
DFM面向制造的设计课程大纲产品质量取决于产品的规划质量、设计质量和制造质量,在产品质量的形成过程中工艺起了至关重要的作用。
样机开发出来了但性能不稳定转不了产,直通率低、返工多以至不能按订单要求及时交货,货物已装箱准备发运了却又收到更改通知,产品到了客户现场出现各种各样的问题要研发人员去救火等等,这些都是企业经常碰到的令人头痛的问题。
DFM是Design for Manufacturability(可制造性设计)的简称,主要研究产品本身的物理设计与制造系统各部分之间的相互关系,并把它用于产品设计中以便将整个制造系统融合在一起进行总体优化。
DFM可以降低产品的开发周期和成本,使之能更顺利地投入生产。
通过系统的将DFM知识与推进方案通熟易懂的讲解,结合曾多个项目成功的实践经验与案例演示、加深学员对课程的理解,通过本次的学习达到快度的应用效果。
培训目标:⏹理解DFM的目的、原理、过程和方法;⏹掌握DFM的知识和技能,能有效开展DFM项目管理,⏹建立关注下道工序就是客户的观念,一次把产品做对做好;⏹具备应用DFM方法对现有产品和过程实施过程评估的能力,以实现产品和过程的标准化和持续改进。
有新产品开发、制造过程开发或项目管理的实践经验——产品技术经理、质量经理、项目经理、设计工程师、制造工程师、工艺工程师和其他直接参与新产品或新制造过程开发、过程标准化和过程改进的人员。
1天➢什么是可制造性分析?➢为什么要实施DFX?➢传统设计和可制造性设计的区别➢可制造性设计的价值➢可制作性设计实施的最佳时机➢可制造性分析检查的内容➢DFX 的分类➢DFM, 可制造性分析➢DFT, 可测试性分析➢DFA,可组装性分析➢为什么要建立DFM体系?➢如何实施DFM?➢如何有效的推行DFM➢如何与设计团队进行沟通改进➢掌握DFM 的分析方法➢概述与DFM相关的IPC 标准➢DFM行业相关标准➢DFM案例分析➢元件的分类➢元件属性在DFM分析中的作用➢钢网设计分析➢PCB 简介➢PCB 类型➢PCB 专业术语➢PCB 制造流程➢PCB 表面处理➢PCB 缺陷及处理方法➢DFM 报告模板➢DFM 跟踪反馈的重要性➢DFM评价循环圈➢如何评价可制造性设计的效果➢某电子通讯企业的完整DFM操作分享。
新产品DFX可制造测试性审核管理程序

文件制修订记录1.0目的指导新品开发阶段的可制造、测试性审核工作,确保新品符合生产的可制造性要求。
2.0适用范围适用于公司产品的开发,包括工程验证、试产、预生产等过程。
3.0相关文件表面组装印制电路板设计指导规范可制造性工艺规范4.0术语与定义4.1 Prototype:手工样机阶段,研发过程中第一次做出的样机,一般有1~2台,是对方案满足规格要求的初步验证,在此阶段还须完成结构图设计、外观模型(Mockup)制作(如果必要)、电原理图、初步BOM和关键部品清单等4.2 EVT:工程样机验证阶段(Engineering Verification Test)。
介于手工样机(Prototype)和设计验证测试(DVT)阶段之间的新品开发阶段,主要完成内容:产品的功能和可靠性设计;安规认证试验通过;完成产品使用说明书、工程规格等设计文件的拟制。
4.3 DVT:设计验证测试阶段 (Design Verification Test)。
试产阶段,此时产品已满足工程规格的要求,主要进行产品批量生产的可行性验证。
4.4首产:首次批量生产。
验证产品进行大批量生产的可行性。
4.5 DFM: 可制造性设计(Design for Manufacturing ),指新产品设计满足产品相关过程进行优化的活动(包括对维修服务、测试、制造装配、成本等方面的考虑),包括: DFA可装配性设计(Design for Assembly);DFR可靠性设计、DFT可测试性设计(Design for Testing)、DFS可维修性设计(Design for Service)4.6 ICT:In Circuit Test 在线测试。
4.7设计部门:XXXX5.0职责和权限5.1工艺部门(略)5.2设计部门(略)5.3制造部门(略)5.4品保部门(略)6.0流程图:见附件。
7.0活动内容7.1新品可制造性、可测试性审核的时机及审核重点7.1.1 根据新品开发各阶段的要求,新品可制造性审核分为四个阶段。
DFM简介PPT精选文档
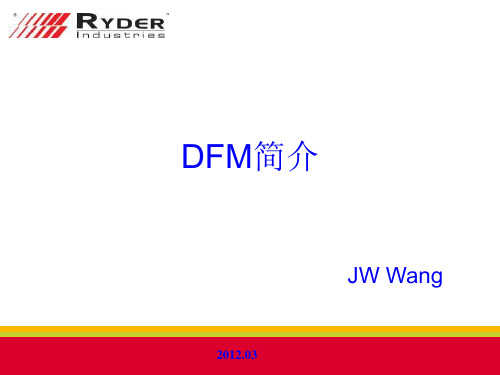
24+/-1mil
改善后
无短路
DFM简介
51
DFM案例
案例四: 将插件物料改为SMT物料,改进生产效率
背景:X144 PCBA C2&C3&L3&L4为插件物料且采 用手工焊接,生产效率低
DFM简介
52
DFM案例
X144 PCBA C2&C3&L3&L4更改为SMT物料并采 用机器生产方式,提升生产效率
13
怎样做DFM
7. Small SMT 到Sub 0.050" Pitch的距离
DFM简介
14
怎样做DFM
8. BGA, CCGA到其他零件的距离
DFM简介
15
怎样做DFM
9. Small SMT 到其他SMT的距离
DFM简介
16
怎样做DFM
10. Small SMT 到插件元的距离
DFM简介
导入DFM,势在必行!
DFM简介
7
第一章&第二章内容回顾
DFM简介
8
怎样做DFM
第三讲、怎样做DFM
一、 DFM六要素
业界标准 (IPC等)
相关工具 (DFM工具Valor等)
材料特性(零 件,材料)
客户要求
DFM
设备能力(SMT,波 峰焊,自动化等) 制程能力 (Know-How)
DFM简介
9
怎样做DFM
二、PCBA及组装生产中常用的关于DFM的知识
1.各类元件距离PCB板边的距离
元件類型及描述 SMT零件到回焊爐的軌道板邊 SMT零件到過錫爐的軌道板邊 SMT零件距离非軌道邊 插件距离錫爐的軌道板邊 插件的PIN腳距离板邊 SMT元件高度大于9mm的元件距离板邊
DFM电子产品可制造设计

● PCB可制造性设计
5.PCB拼板
3.拼板设计主要考虑三个问题:拼板如何连接?
V-CUT连接
a. 当板与板之间为直线连接,边缘平整且不影响器件安装的PCB可用此种连接。V-CUT 为直通型,不能在中间转弯。
b. V-CUT设计要求的PCB推荐的板厚≤3.0mm。 c. 元器件距离PCB板边≥3mm。包括与V槽,邮票孔,定位孔距离。(极限距离,非常
● PCB可制造性设计
PCB设计常见不良
1.元器件封装尺寸选择错误.
2.焊盘上设计测试孔
3.Bottom面只有7个贴片元件.
4.无ICT测试点
5.晶振金属壳容与焊盘接触短路
6.三个元件相互干涉
● PCB可制造性设计
1.板材的选择
基材:应适当选择Tg较高的基材——玻璃化转变温度Tg是聚合物特 有的性能,是决定材料性能的临界温度,是选择基板的一个关键参数。 环氧树脂的Tg在125~140 ℃左右,再流焊温度在220℃左右,远远高 于PCB基板的Tg,高温容易造成PCB的热变形,严重时会损坏元件。 *Tg应高于电路工作温度。
参考文件:PCB制作要求说明书模板
● PCB可制造性设计
2.PCB尺寸大小
1、尺寸范围 从生产角度考虑,理想的尺寸范围是“宽(200 mm~250 mm)×长
(250 mm~350 mm)”。 对PCB长边尺寸小于125mm、或短边小于100mm的PCB,采用拼板的方式, 使之转换为符合生产要求的理想尺寸,以便插件和焊接。
铣槽
辅助边
● PCB可制造性设计
5.PCB拼板 2.拼板设计主要考虑三个问题:该如何拼板?
*有金手指的插卡板,需将其对拼,将其金手指朝外,以方便镀金。
2smt印制板dfm设计及审核

B
(2) 单面混装(SMD和THC分别在PCB的两面)
B面施加贴装胶
贴装SMD
胶固化
翻转PCB
A面插装THC
B面波峰焊。
或:A面插装THC(机器) B面点胶贴装固化
A B
再波峰焊。
25
(3) 双面混装(THC在A面,A、B两面都有SMD)
A面施加焊膏
贴装SMD 再流焊
A
翻转PCB
B
B面施加贴装胶
贴装SMD 胶固化
10. 元器件整体布局设置
11. 再流焊与波峰焊贴片元件 的排列方向设计 12. 元器件的间距设计 13. 散热设计 14. 高频及抗电磁干扰设计 15. 可靠性设计 16. 降低生产成本设计
22
1. 印制板的组装形式及工艺流程设计
1.1 印制板的组装形式
23
1.2 工艺流程设计
1.2.1 纯表面组装工艺流程
(1) 单面表面组装工艺流程
施加焊膏
贴装元器件
A B
再流焊。
(2) 双面表面组装工艺流程
A面施加焊膏
贴装元器件
翻转PCB
B面施加焊膏
贴装元器件
A B
再流焊
再流焊。
24
1.2.2 表面贴装和插装混装工艺流程
(1) 单面混装(SMD和THC都在同一面)
A面施加焊膏
贴装SMD 再流焊
A
A面插装THC
B面波峰焊。
制造加工精度差造成的。其结果造成虚焊或电气断路。
13
• (4) 元器件布局不合理 • a 没有按照再流焊要求设计,再流焊时造成温度不均匀。
14
• b 没有按照波峰焊要求设计,波峰焊时造成阴影效应。
从样品走向量产-DFM和DFT

从样品走向量产–DFM和DFT参加对象企业CEO/总经理、研发总经理/副总、测试部经理、中试/试产部经理、制造部经理、工艺/工程部经理、质量部经理、项目经理/产品经理、高级制造工程师等。
课程背景我们在为企业提供研发管理咨询服务的过程中发现,很多企业的新产品开发从样机到量产的过程中(产品化过程)存在着共同的问题:1. 新品没有经过中试或中试的时间很短,制造部门戏称研发的新品是“三无”产品,没有生产文件、没有工装、生产现场出了问题没人管;2. 转产没有标准,研发想快点转产,生产对有问题的产品又不愿接收,希望研发把问题都解决了才转过来,而市场又催得急,经常被迫接收,长此以往,导致研发与生产的矛盾激化;3. 有些企业开始成立中试部门,希望在中试阶段把产品质量问题解决掉,但中试的定位与运作也很困惑,发生质量与进度的冲突时,如何取舍与平衡,以前研发与制造的矛盾转化为研发与中试、中试与生产的矛盾,中试成了矛盾集散中心;4. 市场的压力并不因中试的产生而减少,中试需要从哪些方面努力才能满足产品的质量、进度的要求?中试的业务是面向研发还是面向制造,还是兼而有之?5. 量产后才发现产品可制造性差、成品率低、经常返工,影响发货;6. 产品到了生产后还发生大量的设计变更;7. 产品到了客户手中还冒出各种各样的问题以致要研发人员到处去“救火”……本课程将基于多年的实践、长期的研发咨询积累,总结出一套理论与实践相结合的可操作的方法,配以大量实际案例,以指导研发/试产/制造部门主管如何高效的实现产品从样品走向量产。
培训收益1、业界公司在不同发展阶段的产品中试管理模式与实践2、面向制造系统的产品设计(DFM)的方法与实施过程3、面向生产测试的产品设计(DFT)的方法与实施过程4、面向制造系统的新产品验证的过程与方法5、在满足质量标准的前提下缩短产品试制周期的方法和技巧6、如何建立从样品到量产的管理机制课程内容一、案例研讨二、从样品到量产概述1. 企业在追求什么:技术?样品?产品?商品?2. 研发与制造的矛盾:1)制造系统如何面对研发的三无产品?2)研发如何面对制造系统越来越高的门槛?3. 研发与制造矛盾的激化:中试的产生成为必然4. 中试的定位与发展:1)研发(RD)、中试(D&P)、生产(P)的关系2)中试的使命是什么?3)中试如何定位?4)中试的发展问题:* 大而全?* 专业化分工?* 产品线划分与共享平台* 中试人员的发展定位:广度与深度问题5. 中试的业务范围1)中试业务:新产品导入(NPI)2)承上:如何面向产品的研发?3)启下:如何面向产品的制造?4)桥梁:中试作为连接研发与制造的桥梁,独木桥还是阳关道?6. 演练与问题讨论根据企业的实际情况,是否需要建立并发展中试的职能?三、新产品导入团队1. 新产品导入团队的构成1)工艺工程2)设备工程3)测试工程4)工业工程5)产品验证6)试生产(计划、生产、质量)2. 新产品导入团队的职责3. 新产品导入团队与产品开发团队的关系1)开发模式的演变:串行变并行2)并行工程在产品开发中如何体现?3)新产品导入团队如何提前介入研发?* 为什么要提前介入?* 提前到什么时候介入?* 提前介入做什么?4)新产品导入团队的管理* 新产品导入团队与产品开发团队、职能部门的沟通* 新产品导入团队成员的汇报、考核和管理机制4. 演练与问题讨论根据企业的实际情况,研讨建立新产品导入团队的时机四、面向制造系统的产品设计(DFM)1. 如何在产品设计与开发过程中进行可制造性设计1)从制造的角度来看产品设计2)工艺人员介入产品开发过程的切入点:从立项就开始3)工艺管理的三个阶段:工艺设计、工艺调制与验证、工艺管制4)工艺设计:* 如何提出可制造性需求?* 需要哪些典型的工艺规范?* 可制造性需求如何落实到产品设计方案中?* 工艺设计与产品设计如何并行?* 产品工艺流程设计* 电装、整装、包装与物流的可制造性设计分析* 如何确保可制造性需求在产品开发中已被实现?* 工艺评审如何操作?* 什么时候考虑工装?* 如何在开发过程中同步输出工艺文件与生产操作指导文件5)工艺调制与验证* 工艺验证的时机* 工艺验证方案包括哪些内容?* 如何实施工艺验证?* 工艺验证报告的内容* 如何推动工艺验证的问题解决?* 研发人员如何配合新产品的工艺验证?* 制造外包模式下的工艺如何验证?6)工艺管制* 工艺管制的困惑:救火何时是尽头?* 工艺转产评审(标准、流程、责任)* 量产过程中的例行监控与异常管理2. 演练与问题讨论分析学员企业的工艺管理工作做到什么程度?存在哪些差距?3. 工艺管理平台建设1)谁负责工艺平台的建设?2)工艺委员会的产生:责任与运作模式3)如何进行工艺规划?4)基础工艺研究与应用5)支撑工艺管理平台的四大规范:* 品质规范* 设备规范* 工艺规范* 设计规划6)工艺管理部门如何推动DFM业务的开展?7)工艺体系的组织构成、发展与演变8)工艺人员的培养与技能提升4. 演练与问题讨论分析学员企业的工艺平台建设工作做到什么程度?存在哪些差距?如何改进?五、面向生产测试的产品设计(DFT)1. 基于产品生命周期全流程的测试策略1)研发测试(Alpha)、试验局测试(Beta)、生产测试2. 研发测试(Alpha)与BETA测试1)测试人员介入产品开发过程的时机(提可测试性需求的时机)2)可测试性需求需要考虑的内容(示例)3)单元测试、模块测试、系统集成测试、专业化测试、BETA测试的重点分析4)产品开发过程中测试业务流程分析5)企业在不同的发展阶段如何开展测试的相关工作(短平快的项目测试工作如何开展)3. 面向生产测试业务的产品设计与开发1)生产测试业务流程分析2)典型的部品测试、整机测试方法介绍3)开发专门的生产测试工装的条件分析4)生产测试工装的开发管理5)在产品开发过程中如何实施面向生产测试的产品设计?* 如何提出可测试性需求?* 可测试性需求如何落实到产品设计方案中?* 研发面对众多的需求如何取舍?可测试性需求的优先级分析* 如何在产品开发过程中同步开发生产测试工装?* 如何在产品开发过程中同步输出生产测试所需的操作指导文件?* 如何进行测试工装的验证?* 如何推动测试验证问题的解决?6)如何推动可测试性设计(DFT)业务的开展7)如何进行测试平台的建设?4. 演练与问题讨论分析学员企业的DFT工作做到什么程度?存在哪些差距?如何改进?六、产品试制验证管理1. 影响产品试制周期的因素分析2. 研发人员对试制准备提供的支持3. 试制团队的构成、职责与定位(设置试制部门的时机与优缺点分析)4. 试制人员介入产品开发过程的时机1)如何进行试制准备(准备要素示例)5. 面向制造系统的验证1)研发人员如何在试制过程中进行产品设计的优化2)制造系统的验证策略与计划3)制造系统的验证方案4)如何实施制造系统的验证:* 工艺验证(工艺流程、工艺路线、单板工艺、整机工艺、包装工艺、物流工艺)* 工装验证(装配工装、测试工装、生产设备)* 结构验证* 产品数据验证(BOM验证、制造文档验证)* 产品试制验证(质量、效率、成本)5)批次验证报告,验证多少批才合适?6)如何推动验证问题的解决?6. 转产评审1)研发人员如何支持新产品的转产工作2)转产评审的评审组织如何构成?* 评审标准是什么?* 如何判定是否转产?* 评审流程与运作机制7. 产品转产后的管理1)新产品的试制效果评价2)新产品的质量目标达成情况3)工程变更管理4)缺陷与问题管理5)质量审计8. 演练与问题讨论分析学员企业的产品试制验证过程,分析差距,提出改进建议讲师资质Charles 资深顾问专业背景十几年高科技行业从业背景,丰富的研发管理咨询经验,在国内某大型知名企业工作近10年,主持和参与过多个大型产品的研发工作,先后担任过开发工程师、项目经理、产品经理、新产品导入部总监、研发项目管理部总监等职位。
DFM——精选推荐
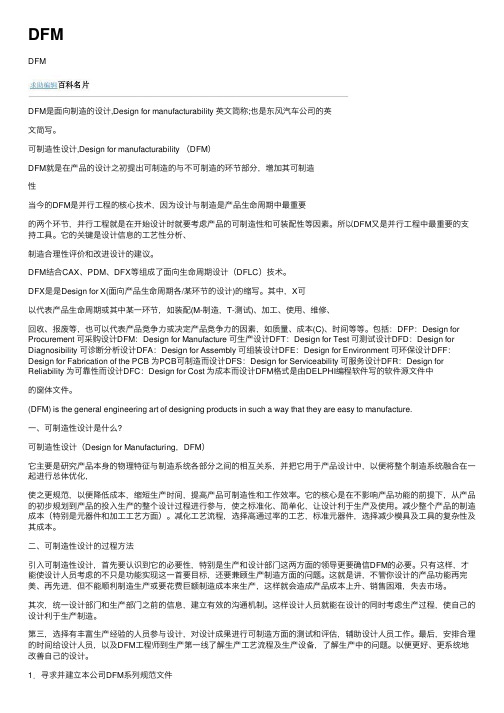
DFMDFMDFM是⾯向制造的设计,Design for manufacturability 英⽂简称;也是东风汽车公司的英⽂简写。
可制造性设计,Design for manufacturability (DFM)DFM就是在产品的设计之初提出可制造的与不可制造的环节部分,增加其可制造性当今的DFM是并⾏⼯程的核⼼技术,因为设计与制造是产品⽣命周期中最重要的两个环节,并⾏⼯程就是在开始设计时就要考虑产品的可制造性和可装配性等因素。
所以DFM⼜是并⾏⼯程中最重要的⽀持⼯具。
它的关键是设计信息的⼯艺性分析、制造合理性评价和改进设计的建议。
DFM结合CAX、PDM、DFX等组成了⾯向⽣命周期设计(DFLC)技术。
DFX是是Design for X(⾯向产品⽣命周期各/某环节的设计)的缩写。
其中,X可以代表产品⽣命周期或其中某⼀环节,如装配(M-制造,T-测试)、加⼯、使⽤、维修、回收、报废等,也可以代表产品竞争⼒或决定产品竞争⼒的因素,如质量、成本(C)、时间等等。
包括:DFP:Design for Procurement 可采购设计DFM:Design for Manufacture 可⽣产设计DFT:Design for Test 可测试设计DFD:Design for Diagnosibility 可诊断分析设计DFA:Design for Assembly 可组装设计DFE:Design for Environment 可环保设计DFF:Design for Fabrication of the PCB 为PCB可制造⽽设计DFS:Design for Serviceability 可服务设计DFR:Design for Reliability 为可靠性⽽设计DFC:Design for Cost 为成本⽽设计DFM格式是由DELPHI编程软件写的软件源⽂件中的窗体⽂件。
(DFM) is the general engineering art of designing products in such a way that they are easy to manufacture.⼀、可制造性设计是什么?可制造性设计(Design for Manufacturing,DFM)它主要是研究产品本⾝的物理特征与制造系统各部分之间的相互关系,并把它⽤于产品设计中,以便将整个制造系统融合在⼀起进⾏总体优化,使之更规范,以便降低成本,缩短⽣产时间,提⾼产品可制造性和⼯作效率。
dfm管理制度

dfm管理制度
DFM(Design for Manufacturing)是一种管理制度,旨在通过设计产品时考虑到制造过程的要求和限制,从而提高产品的制造效率和质量。
DFM管理制度通常涉及以下几个方面:
1. 设计规范:DFM要求产品设计人员了解制造工艺和设备的能力,以便在设计阶段就能够避免一些生产上的困难和问题。
设计规范包括材料选择、尺寸和公差要求、装配方式等,以确保产品能够顺利制造。
2. 制造可行性评估:在产品设计的早期阶段,DFM管理制度鼓励制造工程师与设计团队合作,进行制造可行性评估。
这包括分析产品设计是否符合制造流程、工艺能力和工厂设备的限制,以及评估生产成本和周期等因素。
3. 设计优化:DFM管理制度鼓励产品设计团队进行设计优化,以提高产品的制造效率和质量。
这可能涉及到简化部件结构、减少零件数量、优化装配方式、考虑材料和加工工艺的选择等方面。
4. 制造工艺改进:DFM管理制度鼓励制造工程师进行持续改进,以提高制造过程的效率和质量。
这包括对工艺流程的优化、设备的更新和改进、员工培训等方面,以确保产品能够以最佳的方式制造出来。
通过实施DFM管理制度,企业可以在产品设计阶段就考虑到制造的要求,从而避免一些后期生产上的问题和延误。
这有助于提高产品的制造效率、降低生产成本,并提升产品的质量和竞争力。
品质术语
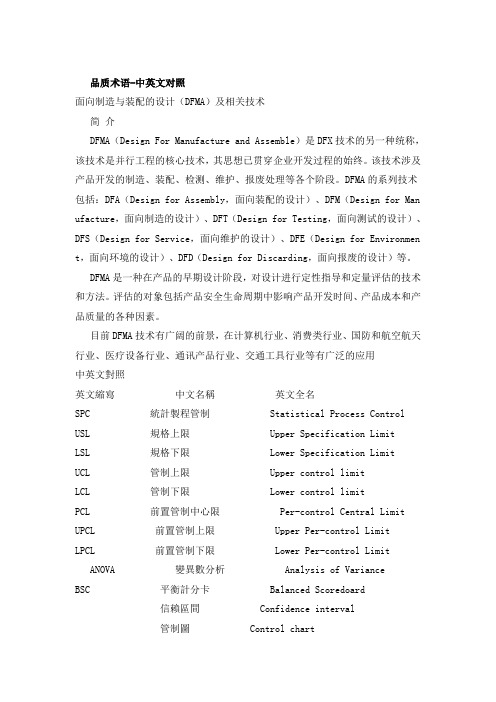
品质术语-中英文对照面向制造与装配的设计(DFMA)及相关技术简介DFMA(Design For Manufacture and Assemble)是DFX技术的另一种统称,该技术是并行工程的核心技术,其思想已贯穿企业开发过程的始终。
该技术涉及产品开发的制造、装配、检测、维护、报废处理等各个阶段。
DFMA的系列技术包括:DFA(Design for Assembly,面向装配的设计)、DFM(Design for Man ufacture,面向制造的设计)、DFT(Design for Testing,面向测试的设计)、DFS(Design for Service,面向维护的设计)、DFE(Design for Environmen t,面向环境的设计)、DFD(Design for Discarding,面向报废的设计)等。
DFMA是一种在产品的早期设计阶段,对设计进行定性指导和定量评估的技术和方法。
评估的对象包括产品安全生命周期中影响产品开发时间、产品成本和产品质量的各种因素。
目前DFMA技术有广阔的前景,在计算机行业、消费类行业、国防和航空航天行业、医疗设备行业、通讯产品行业、交通工具行业等有广泛的应用中英文對照英文縮寫中文名稱英文全名SPC 統計製程管制 Statistical Process Control USL 規格上限 Upper Specification LimitLSL 規格下限 Lower Specification LimitUCL 管制上限 Upper control limitLCL 管制下限 Lower control limitPCL 前置管制中心限 Per-control Central Limit UPCL 前置管制上限 Upper Per-control LimitLPCL 前置管制下限 Lower Per-control Limit ANOVA 變異數分析 Analysis of VarianceBSC 平衡計分卡 Balanced Scoredoard信賴區間 Confidence interval管制圖 Control chartCTQ 品質關鍵 Critical to qualityDPMO 每百萬個機會的缺點數 Defects per million opportunitiesDPM 每百萬單位的缺點數 Defects per million DPU 單位缺點數 Defects per unitDFSS 六個希格瑪設計 Design for six sigma DOE 實驗設計 Design of experimentDFM 製造設計 Design of manufactringFMEA 故障型態與效應分析 Failure mode and effect analysis故障率 Failure rateGage R & R 量規重複能力與重製能力 Gage repeatability & r eproducibility直方圖 Histogram假設檢定 Hypothesis testingKM 知識管理 Knowledge ManagementMRP 物料需求規劃 Material require planning常態分配 Normal distributionQFD 品質機能展開 Quality function deployment 6 σ六個希格瑪 Six Sigmaσ, s 標準差 Standard deviationσ2, S2 變異數 VarianceABC 作業制成本制度 Activity-Based CostingBTF 計劃生產 Build To ForecastBTO 訂單生產 Build To OrderCPM 要徑法 Critical Path MethodCPM 每一百萬個使用者會有幾次抱怨 Complaint per MillionCRM 客戶關係管理 Customer Relationship ManagemeCRP 產能需求規劃 Capacity Requirements Planning CS 顧客滿意度 Customer SatisfactionCTO 客製化生產 Configuration To OrderDVT 設計驗證 Design Verification TestingDSS 決策支援系統 Decision Support SystemEC 設計變更/工程變更 Engineer ChangeEC 電子商務 Electronic CommerceEMC 電磁相容 Electric Magnetic CapabilityEOQ 基本經濟訂購量 Economic Order QuantityERP 企業資源規劃 Enterprise Resource Planning FMS 彈性製造系統 Flexible Manufacture System FQC 成品品質管制 Finish or Final Quality Contro lIPQC 製程品質管制 In-Process Quality Control IQC 進料品質管制 Incoming Quality ControlISO 國際標準組織 International Organization for StandardizationISAR 首批樣品認可 Initial Sample Approval Reque stJIT 即時管理 Just In TimeMES 製造執行系統 Manufacturing Execution System MO 製令 Manufacture OrderMPS 主生產排程 Master Production ScheduleMRO 請修(購)單 Maintenance Repair Operation MRP 物料需求規劃 Material Requirement Planning MRPII 製造資源計劃 Manufacturing Resource Plann ingNFCF 更改預估量的通知 Notice for Changing ForecOEM 委託代工 Original Equipment Manufacture ODM 委託設計與製造 Original Design & Manufactur eOPT 最佳生產技術 Optimized Production Technolog yOQC 出貨品質管制 Out-going Quality Control PDCA PDCA管理循環 Plan-Do-Check-ActionPO 訂單 Purchase OrderQA 品質保證 Quality AssuranceQC 品質管制 Quality ControlQCC 品管圈 Quality Control CircleQE 品質工程 Quality EngineeringRMA 退貨驗收 Returned Material ApprovalROP 再訂購點 Re-Order PointSCM 供應鏈管理 Supply Chain ManagementSFC 現場控制 Shop Floor ControlSO 訂單 Sales OrderSOR 特殊訂單需求 Special Order RequestTOC 限制理論 Theory of ConstraintsTPM 全面生產管理 Total Production Management TQC 全面品質管制 Total Quality ControlTQM 全面品質管理 Total Quality ManagementWIP 在製品 Work In Process5S Sort, Storage, Shine, Standardize, SustainA PartABC Activity Based CostingABM Activity Based ManagementAPS Advanced Planning SystemAOP Annual Operating PlanAPQP Advanced Product Quality PlanningASQ/AIAG American Society of Quality/Automotive Industry Action GroupB PartBOM Bill of MaterialC PartCAD Computer Added DesignCAM Computer Added ManufacturingCNC Computer Numerically ControlledCOPQ Cost of Poor QualityCpk Capability Index for Stable ProcessD PartDFM Design for ManufacturabilityDFX Brings Six Sigma tools to the design process. DFX includes:DFM (Design for Manufacturing),DFC (Design for Cost),DFT (Design for Test),DFS (Design for Service)DOE Design of ExperimentsE PartEDI Electronic Data InterchangeEPA Environmental Protection AgencyESI Early Supplier InvolvementF PartFAI First Article InspectionFMEA Failure Modes and Effects AnalysisG PartG&A General & AdministrativeGR&R Gage Repeatability & ReproducibilityH PartHS&E Health Safety and EnvironmentI PartIPDS Integrated Product & Development SystemISO International Standards OrganizationISW Initial Sample WarrantL PartL/T Lead TimeM PartMPS Master Production ScheduleMRP Material Resource PlanningMSA Measurement System AnalysisMSDS Material Data Safety SheetsN PartNPD New Product DevelopmentNRE Non Reoccurring EngineeringO PartOHSA Occupational Heath and Safety ActP PartPEP Product Excellence ProcessPFMEA Process Failure Modes and Effects Analysis P/N Part NumberPPM Parts Per MillionPPAP Production Part Approval ProcessQ PartQS-9000 Quality System Requirements (Automotive)R PartRCCA Root Cause and Corrective ActionRCCP Rough Cut Capacity PlanningRFQ Request for QuoteRMA Returned Material AuthorizationS PartSAVE Supply Chain Assisted Value EngineeringSIOP Sales, Inventory & Operations PlanningSLT Short Lead TimeSOP Sales and Operations PlanningSPC Statistical Process ControlSPRS Supplier Performance Rating SystemSTS Ship to StockT PartTPM Total Preventative MaintenanceTQ Total QualityTSCA Toxic Substance Control ActW PartWIP Work In ProgressControl plan 管制计划Accuracy 准确度Correction 纠正Active 主动Correlation Methods 相关分析法Action 评价.处理Cost down 降低成本Activity 活动CPI: continuouse Process Improveme连续工序改善hypergeometric 超几何分配Creep 渐变Addition rule 加法运算规则Cross Tabulation Tables 交*表Analysis Covariance 协方差分析CS: customer Sevice 客户中心Analysis of Variance 方差分析Cushion 缓冲Appraisal Variation 评价变差DSA: Defects Analysis System 缺陷分析系统Approved 承认Data Collection 数据收集ASQC 美国质量学会Data concentrator 资料集中缓存器Attribute 计数值DCC: Document Control Center 文控中心Audit 审核Decision 决策.判定Automatic database recovery 数据库错误自动回复Defects per unit 单位缺点数verage 平均数Description 描述balance 平衡Detection 难检度Balance sheet 资产负债对照表Device 装置Binomial 二项分配Digital 数字Body 机构DOE: Design of Experiments 实验设计Brainstorming Techniques 脑力风暴法Element 元素Business Systems Planning 企业系统规划Engineering recbnology 工程技术Cable 电缆Entropy 函数Capability 能力Environmental 环境Cause and Effect matrix 因果图.鱼骨图Equipment 设备Center line 中心线Estimated accumulative frequency 计算估计累计数check 检查EV: Equipment Variation 设备变异Check Sheets 检查表Event 事件Chi-square Distribution 卡方分布External Failure 外部失效,外部缺陷Clutch spring 离合器弹簧FA: Failure Analysis 坏品分析Coining 压印加工Fact control 事实管理Common cause 共同原因Fatique 疲劳Complaint 投诉FMEA: Failure Mode and Effect analysis 失效模式与效果分析Compound factor 调合因素FPY 合格率Concept 新概念FQA: Final Quality Assurance 最终品质保证Condenser 聚光镜FQC: Final Quality control 最终品质控制Conformity 合格Full-steer 完全转向Connection 关联function 职能Consumer's risk 消费者之风险Gauge system 量测系统Control 控制Grade 等级Control characteristic 管制特性Gum-roll 橡皮滚筒Histogram 直方图Health meter 体重计Hi-tech 高科技Heat press 冲压粘着Absolute deviation, 绝对离差Absolute number, 绝对数Absolute residuals, 绝对残差Acceleration array, 加速度立体阵Acceleration in an arbitrary direction, 任意方向上的加速度Acceleration normal, 法向加速度Acceleration space dimension, 加速度空间的维数Acceleration tangential, 切向加速度Acceleration vector, 加速度向量Acceptable hypothesis, 可接受假设Accumulation, 累积Accuracy, 准确度Actual frequency, 实际频数Adaptive estimator, 自适应估计量Addition, 相加Addition theorem, 加法定理Additivity, 可加性Adjusted rate, 调整率Adjusted value, 校正值Admissible error, 容许误差Aggregation, 聚集性Alternative hypothesis, 备择假设Among groups, 组间Amounts, 总量Analysis of correlation, 相关分析Analysis of covariance, 协方差分析Analysis of regression, 回归分析Analysis of time series, 时间序列分析Analysis of variance, 方差分析Angular transformation, 角转换ANOV A (analysis of variance), 方差分析ANOV A Models, 方差分析模型Arcing, 弧/弧旋Arcsine transformation, 反正弦变换Area under the curve, 曲线面积AREG , 评估从一个时间点到下一个时间点回归相关时的误差ARIMA, 季节和非季节性单变量模型的极大似然估计Arithmetic grid paper, 算术格纸Arithmetic mean, 算术平均数Arrhenius relation, 艾恩尼斯关系Assessing fit, 拟合的评估Associative laws, 结合律Asymmetric distribution, 非对称分布Asymptotic bias, 渐近偏倚Asymptotic efficiency, 渐近效率Asymptotic variance, 渐近方差Attributable risk, 归因危险度Attribute data, 属性资料Attribution, 属性Autocorrelation, 自相关Autocorrelation of residuals, 残差的自相关Average, 平均数Average confidence interval length, 平均置信区间长度Average growth rate, 平均增长率Bar chart, 条形图Bar graph, 条形图Base period, 基期Bayes' theorem , Bayes定理Bell-shaped curve, 钟形曲线Bernoulli distribution, 伯努力分布Best-trim estimator, 最好切尾估计量Bias, 偏性Binary logistic regression, 二元逻辑斯蒂回归Binomial distribution, 二项分布Bisquare, 双平方Bivariate Correlate, 二变量相关Bivariate normal distribution, 双变量正态分布Bivariate normal population, 双变量正态总体Biweight interval, 双权区间Biweight M-estimator, 双权M估计量Block, 区组/配伍组BMDP(Biomedical computer programs), BMDP统计软件包Boxplots, 箱线图/箱尾图Breakdown bound, 崩溃界/崩溃点Canonical correlation, 典型相关Caption, 纵标目Case-control study, 病例对照研究Categorical variable, 分类变量Catenary, 悬链线Cauchy distribution, 柯西分布Cause-and-effect relationship, 因果关系Cell, 单元Censoring, 终检Center of symmetry, 对称中心Centering and scaling, 中心化和定标Central tendency, 集中趋势Central value, 中心值CHAID -χ2 Automatic Inter action Detector, 卡方自动交互检测Chance, 机遇Chance error, 随机误差Chance variable, 随机变量Characteristic equation, 特征方程Characteristic root, 特征根Char acteristic vector, 特征向量Chebshev criterion of fit, 拟合的切比雪夫准则Cherno ff faces, 切尔诺夫脸谱图Chi-square test, 卡方检验/χ2检验Choleskey decompositi on, 乔洛斯基分解Circle chart, 圆图 Class interval, 组距Class mid-value, 组中值Class upper limit, 组上限Classified variable, 分类变量Cluster analysis, 聚类分析Cluster sampling, 整群抽样Code, 代码Coded data, 编码数据Coding, 编码Coeffic ient of contingency, 列联系数Coefficient of determination, 决定系数Coefficient of multiple correlation, 多重相关系数Coefficient of partial correlation, 偏相关系数Coefficient of production-moment correlation, 积差相关系数Coefficient of rank correlation, 等级相关系数Coefficient of regression, 回归系数Coefficient of skewness, 偏度系数Coefficient of variation, 变异系数Cohort study, 队列研究C olumn, 列Column effect, 列效应Column factor, 列因素Combination pool, 合并Comb inative table, 组合表Common factor, 共性因子Common regression coefficient, 公共回归系数Common value, 共同值Common variance, 公共方差Common variation, 公共变异Communality variance, 共性方差Comparability, 可比性Comparison of bathes, 批比较Comparison value, 比较值Compartment model, 分部模型Compassion, 伸缩Comp lement of an event, 补事件Complete association, 完全正相关Complete dissociatio n, 完全不相关Complete statistics, 完备统计量Completely randomized design, 完全随机化设计Composite event, 联合事件Composite events, 复合事件Concavity, 凹性C onditional expectation, 条件期望Conditional likelihood, 条件似然Conditional pr obability, 条件概率Conditionally linear, 依条件线性Confidence interval, 置信区间Confidence limit, 置信限Confidence lower limit, 置信下限Confidence upper lim it, 置信上限Confirmatory Factor Analysis , 验证性因子分析Confirmatory research,证实性实验研究Confounding factor, 混杂因素Conjoint, 联合分析Consistency, 相合性Consistency check, 一致性检验Consistent asymptotically normal estimate, 相合渐近正态估计Consistent estimate, 相合估计Constrained nonlinear regression, 受约束非线性回归Constraint, 约束Contaminated distribution, 污染分布Contaminated Gausssian, 污染高斯分布Contaminated normal distribution, 污染正态分布Contamina tion, 污染Contamination model, 污染模型Contingency table, 列联表Contour, 边界线Contribution rate, 贡献率Control, 对照Controlled experiments, 对照实验Conventional depth, 常规深度Convolution, 卷积Corrected factor, 校正因子Corrected me an, 校正均值Correction coefficient, 校正系数Correctness, 正确性 Correlation co efficient, 相关系数Correlation index, 相关指数Correspondence, 对应Counting, 计数Counts, 计数/频数Covariance, 协方差Covariant, 共变 Cox Regression, Cox回归C riteria for fitting, 拟合准则Criteria of least squares, 最小二乘准则Critical r atio, 临界比Critical region, 拒绝域Critical value, 临界值Cross-over design, 交*设计Cross-section analysis, 横断面分析Cross-section survey, 横断面调查Crossta bs , 交*表 Cross-tabulation table,复合表Cube root, 立方根Cumulative distribution function, 分布函数Cumulative probability, 累计概率Curvature, 曲率/弯曲Curvature, 曲率C urve fit , 曲线拟和 Curve fitting, 曲线拟合Curvilinear regression, 曲线回归Curvilinear relation, 曲线关系Cut-and-try method, 尝试法Cycl e, 周期Cyclist, 周期性D test, D检验Data acquisition, 资料收集Data b ank, 数据库Data capacity, 数据容量Data deficiencies, 数据缺乏Data ha ndling, 数据处理Data manipulation, 数据处理Data processing, 数据处理Data reduction, 数据缩减Data set, 数据集Data sources, 数据来源Data t ransformation, 数据变换Data validity, 数据有效性Data-in, 数据输入Dat a-out, 数据输出Dead time, 停滞期Degree of freedom, 自由度Degree of p recision, 精密度Degree of reliability, 可靠性程度Degression, 递减Den sity function, 密度函数Density of data points, 数据点的密度Dependent variable, 应变量/依变量/因变量 Dependent variable, 因变量Depth, 深度Derivative matrix, 导数矩阵Derivative-free methods, 无导数方法Desi gn, 设计Determinacy, 确定性Determinant, 行列式Determinant, 决定因素D eviation, 离差Deviation from average, 离均差Diagnostic plot, 诊断图D ichotomous variable, 二分变量Differential equation, 微分方程Direct s tandardization, 直接标准化法Discrete variable, 离散型变量DISCRIMINAN T, 判断 Discriminant analysis, 判别分析Discriminant coefficient, 判别系数Discriminant function, 判别值Dispersion, 散布/分散度Disproportional, 不成比例的Disproportionate sub-class numbers, 不成比例次级组含量Distribution free, 分布无关性/免分布Distribution shape, 分布形状Distribution-free method, 任意分布法Distributive laws, 分配律Disturb ance, 随机扰动项Dose response curve, 剂量反应曲线 Double blind metho d, 双盲法Double blind trial, 双盲试验Double exponential distributio n, 双指数分布Double logarithmic, 双对数Downward rank, 降秩Dual-space plot, 对偶空间图DUD, 无导数方法Duncan's new multiple range method, 新复极差法/Duncan新法。
DFM基本概念
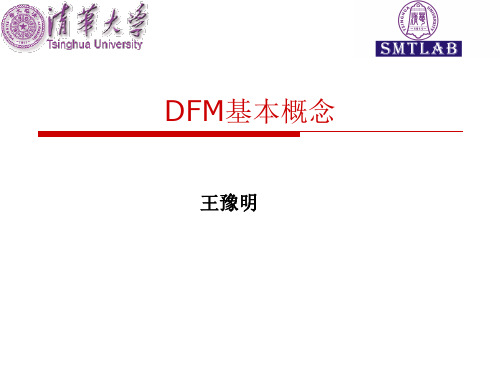
二、DFM介绍:3.DFM-优点
减少改版次数或不需修改设计,减少开发成本。 没有DFM规范控制的产品,在产品开发的后期,甚至常在批量生 产阶段才会发现各种生产问题,此时又更改设计,无疑增加开 发成本,例:BGA的焊盘间距设计:公英制转换误差。 降低返工、返修成本、 发现各种生产问题,往往花费人力、物力进行返工、返修,才 能达到目的。例:焊盘上有过孔的问题。
作为一种科学的方法,DFX将不同团队的资源组织在一起,共同参与产品的 设计和制造过程,通过发挥团队的共同作用,缩短参品开发周期,提高产品质 量、可靠性和客户满意度,最终缩短从概念到客户手中的整个时间周期。
DFM: DFT: DFD: DFA: DFE: DFF:
Design Design Design Design Desibn Design
二、DFM介绍:3.DFM-优点
提高产品质量和可靠性 产品生产最好一次成功,任何返修、返工都会使可靠性下降。同 时影响声誉。 例:在售后维修的产品中,80%出自产品出厂前返修过的产品。 例:某公司开展2年DFM后,波峰焊不良率下降为原来的1/10。
有利于技术转移,简化产品转 移流程。 企业一般外包,则企业与OEM、 EMS/CM之间的有效沟通非常必 要。具有良好可制造性的产品可 与OEM、EMS/CM间实现平滑 的技术转移和过渡,快速组织生通过反馈步骤来证实所有DFM的内容对生产的影响,起到的作用。 第六:利用DFM工具和软件 1. PCB设计软件中的DFM功能 2. DFM软件工具 (1)购买商业性DFM软件工具 Valor Trilogy 是一种广泛应用的DFM分析设计软件。 (2)自行创建适合自己的DFM软件工具 世界级公司常常这样做。 第七. DFM审核报告 DFM审核报告是反映整个DFM过程中所发现的问题。
产品dfm报告是什么意思

产品dfm报告是什么意思什么是DFMDFM是Design for Manufacturability(可制造性设计)的缩写,是一种将产品设计、工程和制造领域的原则和方法相结合的设计过程。
DFM的目标是通过优化产品的设计,使得产品在制造、装配和维护过程中更容易和更经济地生产。
DFM考虑了材料的选取、工艺的选择、零件的设计、装配的方案等诸多因素,以最大程度地提高制造效率、降低成本、增强产品质量。
什么是产品DFM报告产品DFM报告是对产品设计可制造性的评估和分析的文档,旨在为设计师、工程师和制造商提供指导和建议,帮助他们改进产品设计,以便更好地满足制造要求和标准。
产品DFM报告通常由专业的DFM团队或工程师编制,涵盖了产品设计、材料、工艺、质量和成本等方面的考虑。
产品DFM报告的内容产品DFM报告通常包括以下内容:1. 产品设计评估产品设计评估是产品DFM报告中的重要部分。
它涉及对产品设计图纸、样品或虚拟模型的分析,以评估其制造可行性和可优化性。
产品设计评估主要考虑以下因素:- 零件的形状和结构:评估零件的形状、尺寸和结构是否符合制造工艺的要求,是否能够在加工过程中保持稳定性和精度。
- 零件材料的选择:评估零件材料的可用性、成本和适用性,以及其对产品性能和质量的影响。
- 零件的装配方式:评估零件的装配方式和顺序,以确保装配过程的顺利进行和高效性。
2. 材料选择和工艺优化产品DFM报告还涉及材料选择和工艺优化的建议。
这部分主要考虑以下内容:- 材料的选择:根据产品的需求和制造要求,评估不同材料的可行性,并提出合适的材料选择建议。
- 工艺的选择:评估不同工艺的优劣,选择最适合产品要求和制造成本的工艺,并提供工艺优化的建议。
- 加工和装配方法:提供加工和装配方法的建议,以确保零件和组件能够在制造过程中顺利加工和装配。
3. 质量控制和测试方案产品DFM报告还包括质量控制和测试方案的建议。
这部分内容主要考虑以下方面:- 质量控制方法:提供质量控制方法和措施的建议,以确保产品在制造过程中达到预定质量标准。
电子产品DFX培训(DFA,DFM,DFI,DFS,DFR)
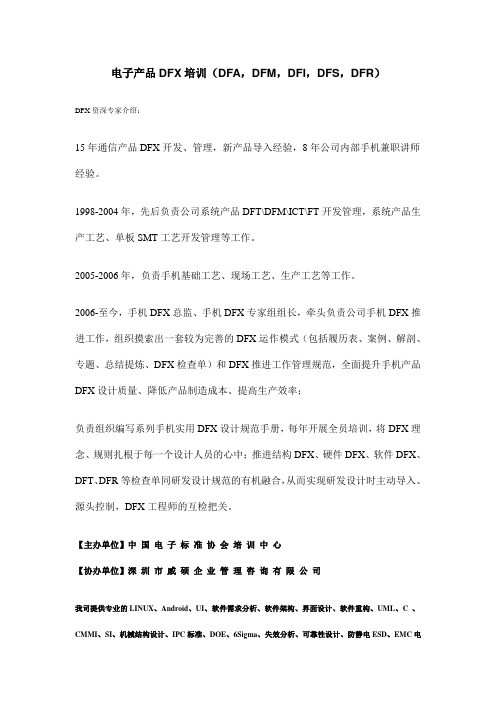
电子产品DFX培训(DFA,DFM,DFI,DFS,DFR)
DFX资深专家介绍:
15年通信产品DFX开发、管理,新产品导入经验,8年公司内部手机兼职讲师经验。
1998-2004年,先后负责公司系统产品DFT\DFM\ICT\FT开发管理,系统产品生产工艺、单板SMT工艺开发管理等工作。
2005-2006年,负责手机基础工艺、现场工艺、生产工艺等工作。
2006-至今,手机DFX总监、手机DFX专家组组长,牵头负责公司手机DFX推进工作,组织摸索出一套较为完善的DFX运作模式(包括履历表、案例、解剖、专题、总结提炼、DFX检查单)和DFX推进工作管理规范,全面提升手机产品DFX设计质量、降低产品制造成本、提高生产效率;
负责组织编写系列手机实用DFX设计规范手册,每年开展全员培训,将DFX理念、规则扎根于每一个设计人员的心中;推进结构DFX、硬件DFX、软件DFX、DFT、DFR等检查单同研发设计规范的有机融合,从而实现研发设计时主动导入、源头控制,DFX工程师的互检把关。
【主办单位】中国电子标准协会培训中心
【协办单位】深圳市威硕企业管理咨询有限公司
我司提供专业的LINUX、Android、UI、软件需求分析、软件架构、界面设计、软件重构、UML、C 、CMMI、SI、机械结构设计、IPC标准、DOE、6Sigma、失效分析、可靠性设计、防静电ESD、EMC电
磁兼容设计、软件可靠性设计、电路设计、DFT、开关电源设计、电路设计的工程计算、射频电路设计、SMT、热设计热分析、DFM、硬件测试技术、APQP/FMEA/SPC/MSA、软件项目配置管理等等各种技术、管理、销售、研发等培训课程。
工厂dfm工作职责及内容

工厂dfm工作职责及内容工厂DFM(Design for Manufacturing,制造设计)的工作职责包括:1. 与产品设计团队合作,评估设计方案的可制造性和生产效率。
2. 提供技术建议和指导,以确保产品设计符合工厂的生产能力和设备要求。
3. 参与产品设计评审会议,提供关于设计的制造观点和建议。
4. 分析和评估材料选择、零部件采购和供应链管理方案,以优化制造成本和交货时间。
5. 开展生产流程分析和工艺改进工作,以提高生产效率和质量。
6. 制定和执行工艺标准和操作规程,确保生产过程的一致性和稳定性。
7. 协助制定和更新工厂的设备、工具和技术投资计划。
8. 协调与供应商和外部合作伙伴的沟通与合作,确保制造过程的顺利进行。
9. 参与解决产品制造过程中遇到的技术问题和质量问题,帮助工厂改进工作。
10. 持续跟踪和评估制造指标,提供改进建议和报告。
工厂DFM的内容主要包括:1. 设计评估:评估产品设计方案的可制造性、装配性和维修性,提供与工厂生产能力相关的建议。
2. 质量控制:制定和执行品质标准和操作规程,确保生产过程中的质量控制,并及时解决质量问题。
3. 工艺改进:分析生产流程和工艺问题,提出改进建议,以提高生产效率和降低制造成本。
4. 设备规划:参与评估和选择生产设备,制定设备投资计划,确保设备满足生产需求。
5. 供应链管理:参与材料和零部件的采购决策,优化供应链管理,以确保及时供应并降低库存成本。
6. 技术支持:提供技术指导和支持,解决制造过程中的技术问题,改进工作方法和经验分享。
7. 数据分析与报告:跟踪生产指标并进行数据分析,及时提供改进建议和报告,为决策提供支持。
DFM
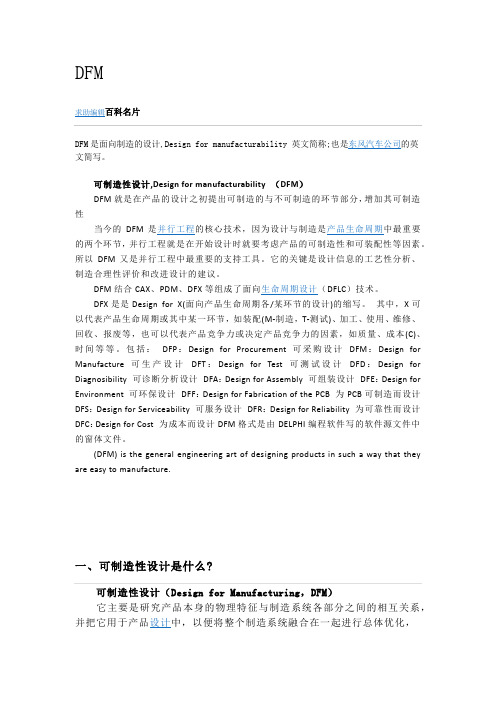
DFMDFM是面向制造的设计,Design for manufacturability 英文简称;也是东风汽车公司的英文简写。
可制造性设计,Design for manufacturability (DFM)DFM就是在产品的设计之初提出可制造的与不可制造的环节部分,增加其可制造性当今的DFM是并行工程的核心技术,因为设计与制造是产品生命周期中最重要的两个环节,并行工程就是在开始设计时就要考虑产品的可制造性和可装配性等因素。
所以DFM又是并行工程中最重要的支持工具。
它的关键是设计信息的工艺性分析、制造合理性评价和改进设计的建议。
DFM结合CAX、PDM、DFX等组成了面向生命周期设计(DFLC)技术。
DFX是是Design for X(面向产品生命周期各/某环节的设计)的缩写。
其中,X可以代表产品生命周期或其中某一环节,如装配(M-制造,T-测试)、加工、使用、维修、回收、报废等,也可以代表产品竞争力或决定产品竞争力的因素,如质量、成本(C)、时间等等。
包括:DFP:Design for Procurement 可采购设计DFM:Design for Manufacture 可生产设计DFT:Design for Test 可测试设计DFD:Design for Diagnosibility 可诊断分析设计DFA:Design for Assembly 可组装设计DFE:Design for Environment 可环保设计DFF:Design for Fabrication of the PCB 为PCB可制造而设计DFS:Design for Serviceability 可服务设计DFR:Design for Reliability 为可靠性而设计DFC:Design for Cost 为成本而设计DFM格式是由DELPHI编程软件写的软件源文件中的窗体文件。
(DFM) is the general engineering art of designing products in such a way that they are easy to manufacture.一、可制造性设计是什么?可制造性设计(Design for Manufacturing,DFM)它主要是研究产品本身的物理特征与制造系统各部分之间的相互关系,并把它用于产品设计中,以便将整个制造系统融合在一起进行总体优化,使之更规范,以便降低成本,缩短生产时间,提高产品可制造性和工作效率。
产品开发部试生产与验证计划

产品开发部试生产与验证计划一、介绍产品开发部试生产与验证计划的目的和重要性产品开发部试生产与验证计划是为了确保新产品能够在正式投产之前经过充分的测试和验证,以确保产品的质量和性能达到预期目标。
试生产与验证是产品开发流程中的重要环节,它可以帮助我们发现并解决产品设计和生产过程中的问题,为后续的量产阶段做好准备。
二、确定试生产与验证的时间和地点在确定试生产与验证的时间和地点时,需要考虑产品开发进度、设备和场地的可用性等因素。
产品开发部将与生产部门和相关供应商协商确定试生产与验证的具体时间和地点,确保各项资源能够顺利配备到位。
三、确定试生产与验证的流程试生产与验证的流程包括原材料采购、生产制造、设备检测、质量评估等环节。
每个环节的任务和责任都需要明确规定,以确保整个流程的顺利进行。
同时,需要建立有效的沟通机制,及时解决和反馈问题,使试生产与验证的流程能够高效运行。
四、确定试生产与验证的指标和标准试生产与验证的指标和标准是评价产品质量和性能的依据。
产品开发部将根据产品设计要求和市场需求确定试生产与验证的指标和标准,并与相关部门和供应商进行确认。
在试生产和验证过程中,需要对产品进行全面的测试和评估,确保产品符合标准要求。
五、确定试生产与验证的关键问题和风险在试生产与验证过程中,可能会遇到一些关键问题和风险,如生产工艺难题、材料供应问题等。
产品开发部将对相关问题进行分析和评估,并制定相应的应对策略,确保试生产与验证工作的顺利进行。
六、确定试生产与验证的人员和资源配置试生产与验证需要配备专业的技术人员和相应的设备和工具。
产品开发部将根据试生产与验证的具体需求,合理配置人员和资源,并确保其培训和能力达到要求。
人员和资源的配置要细化到每个环节,确保试生产与验证的各项任务得以顺利完成。
七、试生产与验证工作的监督和跟进试生产与验证工作需要进行有效的监督和跟进,及时发现和解决问题。
同时,还需要建立评估和反馈机制,对试生产与验证过程中的不足和问题进行总结和改进。
DFM DFT和产品试制验证管理
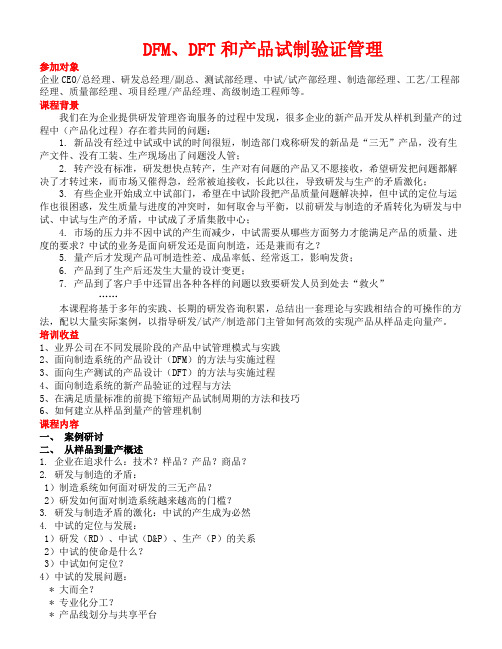
DFM、DFT和产品试制验证管理参加对象企业CEO/总经理、研发总经理/副总、测试部经理、中试/试产部经理、制造部经理、工艺/工程部经理、质量部经理、项目经理/产品经理、高级制造工程师等。
课程背景我们在为企业提供研发管理咨询服务的过程中发现,很多企业的新产品开发从样机到量产的过程中(产品化过程)存在着共同的问题:1. 新品没有经过中试或中试的时间很短,制造部门戏称研发的新品是“三无”产品,没有生产文件、没有工装、生产现场出了问题没人管;2. 转产没有标准,研发想快点转产,生产对有问题的产品又不愿接收,希望研发把问题都解决了才转过来,而市场又催得急,经常被迫接收,长此以往,导致研发与生产的矛盾激化;3. 有些企业开始成立中试部门,希望在中试阶段把产品质量问题解决掉,但中试的定位与运作也很困惑,发生质量与进度的冲突时,如何取舍与平衡,以前研发与制造的矛盾转化为研发与中试、中试与生产的矛盾,中试成了矛盾集散中心;4. 市场的压力并不因中试的产生而减少,中试需要从哪些方面努力才能满足产品的质量、进度的要求?中试的业务是面向研发还是面向制造,还是兼而有之?5. 量产后才发现产品可制造性差、成品率低、经常返工,影响发货;6. 产品到了生产后还发生大量的设计变更;7. 产品到了客户手中还冒出各种各样的问题以致要研发人员到处去“救火”……本课程将基于多年的实践、长期的研发咨询积累,总结出一套理论与实践相结合的可操作的方法,配以大量实际案例,以指导研发/试产/制造部门主管如何高效的实现产品从样品走向量产。
培训收益1、业界公司在不同发展阶段的产品中试管理模式与实践2、面向制造系统的产品设计(DFM)的方法与实施过程3、面向生产测试的产品设计(DFT)的方法与实施过程4、面向制造系统的新产品验证的过程与方法5、在满足质量标准的前提下缩短产品试制周期的方法和技巧6、如何建立从样品到量产的管理机制课程内容一、案例研讨二、从样品到量产概述1. 企业在追求什么:技术?样品?产品?商品?2. 研发与制造的矛盾:1)制造系统如何面对研发的三无产品?2)研发如何面对制造系统越来越高的门槛?3. 研发与制造矛盾的激化:中试的产生成为必然4. 中试的定位与发展:1)研发(RD)、中试(D&P)、生产(P)的关系2)中试的使命是什么?3)中试如何定位?4)中试的发展问题:* 大而全?* 专业化分工?* 产品线划分与共享平台* 中试人员的发展定位:广度与深度问题5. 中试的业务范围1)中试业务:新产品导入(NPI)2)承上:如何面向产品的研发?3)启下:如何面向产品的制造?4)桥梁:中试作为连接研发与制造的桥梁,独木桥还是阳关道?6. 演练与问题讨论根据企业的实际情况,是否需要建立并发展中试的职能?三、新产品导入团队1. 新产品导入团队的构成1)工艺工程2)设备工程3)测试工程4)工业工程5)产品验证6)试生产(计划、生产、质量)2. 新产品导入团队的职责3. 新产品导入团队与产品开发团队的关系1)开发模式的演变:串行变并行2)并行工程在产品开发中如何体现?3)新产品导入团队如何提前介入研发?* 为什么要提前介入?* 提前到什么时候介入?* 提前介入做什么?4)新产品导入团队的管理* 新产品导入团队与产品开发团队、职能部门的沟通* 新产品导入团队成员的汇报、考核和管理机制4. 演练与问题讨论根据企业的实际情况,研讨建立新产品导入团队的时机四、面向制造系统的产品设计(DFM)1. 如何在产品设计与开发过程中进行可制造性设计1)从制造的角度来看产品设计2)工艺人员介入产品开发过程的切入点:从立项就开始3)工艺管理的三个阶段:工艺设计、工艺调制与验证、工艺管制4)工艺设计:* 如何提出可制造性需求?* 需要哪些典型的工艺规范?* 可制造性需求如何落实到产品设计方案中?* 工艺设计与产品设计如何并行?* 产品工艺流程设计* 电装、整装、包装与物流的可制造性设计分析* 如何确保可制造性需求在产品开发中已被实现?* 工艺评审如何操作?* 什么时候考虑工装?* 如何在开发过程中同步输出工艺文件与生产操作指导文件5)工艺调制与验证* 工艺验证的时机* 工艺验证方案包括哪些内容?* 如何实施工艺验证?* 工艺验证报告的内容* 如何推动工艺验证的问题解决?* 研发人员如何配合新产品的工艺验证?* 制造外包模式下的工艺如何验证?6)工艺管制* 工艺管制的困惑:救火何时是尽头?* 工艺转产评审(标准、流程、责任)* 量产过程中的例行监控与异常管理2. 演练与问题讨论分析学员企业的工艺管理工作做到什么程度?存在哪些差距?3. 工艺管理平台建设1)谁负责工艺平台的建设?2)工艺委员会的产生:责任与运作模式3)如何进行工艺规划?4)基础工艺研究与应用5)支撑工艺管理平台的四大规范:* 品质规范* 设备规范* 工艺规范* 设计规划6)工艺管理部门如何推动DFM业务的开展?7)工艺体系的组织构成、发展与演变8)工艺人员的培养与技能提升4. 演练与问题讨论分析学员企业的工艺平台建设工作做到什么程度?存在哪些差距?如何改进?五、面向生产测试的产品设计(DFT)1. 基于产品生命周期全流程的测试策略1)研发测试(Alpha)、试验局测试(Beta)、生产测试2. 研发测试(Alpha)与BETA测试1)测试人员介入产品开发过程的时机(提可测试性需求的时机)2)可测试性需求需要考虑的内容(示例)3)单元测试、模块测试、系统集成测试、专业化测试、BETA测试的重点分析4)产品开发过程中测试业务流程分析5)企业在不同的发展阶段如何开展测试的相关工作(短平快的项目测试工作如何开展)3. 面向生产测试业务的产品设计与开发1)生产测试业务流程分析2)典型的部品测试、整机测试方法介绍3)开发专门的生产测试工装的条件分析4)生产测试工装的开发管理5)在产品开发过程中如何实施面向生产测试的产品设计?* 如何提出可测试性需求?* 可测试性需求如何落实到产品设计方案中?* 研发面对众多的需求如何取舍?可测试性需求的优先级分析* 如何在产品开发过程中同步开发生产测试工装?* 如何在产品开发过程中同步输出生产测试所需的操作指导文件?* 如何进行测试工装的验证?* 如何推动测试验证问题的解决?6)如何推动可测试性设计(DFT)业务的开展7)如何进行测试平台的建设?4. 演练与问题讨论分析学员企业的DFT工作做到什么程度?存在哪些差距?如何改进?六、产品试制验证管理1. 影响产品试制周期的因素分析2. 研发人员对试制准备提供的支持3. 试制团队的构成、职责与定位(设置试制部门的时机与优缺点分析)4. 试制人员介入产品开发过程的时机1)如何进行试制准备(准备要素示例)5. 面向制造系统的验证1)研发人员如何在试制过程中进行产品设计的优化2)制造系统的验证策略与计划3)制造系统的验证方案4)如何实施制造系统的验证:* 工艺验证(工艺流程、工艺路线、单板工艺、整机工艺、包装工艺、物流工艺)* 工装验证(装配工装、测试工装、生产设备)* 结构验证* 产品数据验证(BOM验证、制造文档验证)* 产品试制验证(质量、效率、成本)5)批次验证报告,验证多少批才合适?6)如何推动验证问题的解决?6. 转产评审1)研发人员如何支持新产品的转产工作2)转产评审的评审组织如何构成?* 评审标准是什么?* 如何判定是否转产?* 评审流程与运作机制7. 产品转产后的管理1)新产品的试制效果评价2)新产品的质量目标达成情况3)工程变更管理4)缺陷与问题管理5)质量审计8. 演练与问题讨论分析学员企业的产品试制验证过程,分析差距,提出改进建议讲师资质Charles 资深顾问专业背景十几年高科技行业从业背景,丰富的研发管理咨询经验,在国内某大型知名企业工作近10年,主持和参与过多个大型产品的研发工作,先后担任过开发工程师、项目经理、产品经理、新产品导入部总监、研发项目管理部总监等职位。
- 1、下载文档前请自行甄别文档内容的完整性,平台不提供额外的编辑、内容补充、找答案等附加服务。
- 2、"仅部分预览"的文档,不可在线预览部分如存在完整性等问题,可反馈申请退款(可完整预览的文档不适用该条件!)。
- 3、如文档侵犯您的权益,请联系客服反馈,我们会尽快为您处理(人工客服工作时间:9:00-18:30)。
DFM、DFT和产品试制验证管理参加对象企业CEO/总经理、研发总经理/副总、测试部经理、中试/试产部经理、制造部经理、工艺/工程部经理、质量部经理、项目经理/产品经理、高级制造工程师等。
课程背景我们在为企业提供研发管理咨询服务的过程中发现,很多企业的新产品开发从样机到量产的过程中(产品化过程)存在着共同的问题:1. 新品没有经过中试或中试的时间很短,制造部门戏称研发的新品是“三无”产品,没有生产文件、没有工装、生产现场出了问题没人管;2. 转产没有标准,研发想快点转产,生产对有问题的产品又不愿接收,希望研发把问题都解决了才转过来,而市场又催得急,经常被迫接收,长此以往,导致研发与生产的矛盾激化;3. 有些企业开始成立中试部门,希望在中试阶段把产品质量问题解决掉,但中试的定位与运作也很困惑,发生质量与进度的冲突时,如何取舍与平衡,以前研发与制造的矛盾转化为研发与中试、中试与生产的矛盾,中试成了矛盾集散中心;4. 市场的压力并不因中试的产生而减少,中试需要从哪些方面努力才能满足产品的质量、进度的要求?中试的业务是面向研发还是面向制造,还是兼而有之?5. 量产后才发现产品可制造性差、成品率低、经常返工,影响发货;6. 产品到了生产后还发生大量的设计变更;7. 产品到了客户手中还冒出各种各样的问题以致要研发人员到处去“救火”……本课程将基于多年的实践、长期的研发咨询积累,总结出一套理论与实践相结合的可操作的方法,配以大量实际案例,以指导研发/试产/制造部门主管如何高效的实现产品从样品走向量产。
培训收益1、业界公司在不同发展阶段的产品中试管理模式与实践2、面向制造系统的产品设计(DFM)的方法与实施过程3、面向生产测试的产品设计(DFT)的方法与实施过程4、面向制造系统的新产品验证的过程与方法5、在满足质量标准的前提下缩短产品试制周期的方法和技巧6、如何建立从样品到量产的管理机制课程内容一、案例研讨二、从样品到量产概述1. 企业在追求什么:技术?样品?产品?商品?2. 研发与制造的矛盾:1)制造系统如何面对研发的三无产品?2)研发如何面对制造系统越来越高的门槛?3. 研发与制造矛盾的激化:中试的产生成为必然4. 中试的定位与发展:1)研发(RD)、中试(D&P)、生产(P)的关系2)中试的使命是什么?3)中试如何定位?4)中试的发展问题:* 大而全?* 专业化分工?* 产品线划分与共享平台* 中试人员的发展定位:广度与深度问题5. 中试的业务范围1)中试业务:新产品导入(NPI)2)承上:如何面向产品的研发?3)启下:如何面向产品的制造?4)桥梁:中试作为连接研发与制造的桥梁,独木桥还是阳关道?6. 演练与问题讨论根据企业的实际情况,是否需要建立并发展中试的职能?三、新产品导入团队1. 新产品导入团队的构成1)工艺工程2)设备工程3)测试工程4)工业工程5)产品验证6)试生产(计划、生产、质量)2. 新产品导入团队的职责3. 新产品导入团队与产品开发团队的关系1)开发模式的演变:串行变并行2)并行工程在产品开发中如何体现?3)新产品导入团队如何提前介入研发?* 为什么要提前介入?* 提前到什么时候介入?* 提前介入做什么?4)新产品导入团队的管理* 新产品导入团队与产品开发团队、职能部门的沟通* 新产品导入团队成员的汇报、考核和管理机制4. 演练与问题讨论根据企业的实际情况,研讨建立新产品导入团队的时机四、面向制造系统的产品设计(DFM)1. 如何在产品设计与开发过程中进行可制造性设计1)从制造的角度来看产品设计2)工艺人员介入产品开发过程的切入点:从立项就开始3)工艺管理的三个阶段:工艺设计、工艺调制与验证、工艺管制4)工艺设计:* 如何提出可制造性需求?* 需要哪些典型的工艺规范?* 可制造性需求如何落实到产品设计方案中?* 工艺设计与产品设计如何并行?* 产品工艺流程设计* 电装、整装、包装与物流的可制造性设计分析* 如何确保可制造性需求在产品开发中已被实现?* 工艺评审如何操作?* 什么时候考虑工装?* 如何在开发过程中同步输出工艺文件与生产操作指导文件5)工艺调制与验证* 工艺验证的时机* 工艺验证方案包括哪些内容?* 如何实施工艺验证?* 工艺验证报告的内容* 如何推动工艺验证的问题解决?* 研发人员如何配合新产品的工艺验证?* 制造外包模式下的工艺如何验证?6)工艺管制* 工艺管制的困惑:救火何时是尽头?* 工艺转产评审(标准、流程、责任)* 量产过程中的例行监控与异常管理2. 演练与问题讨论分析学员企业的工艺管理工作做到什么程度?存在哪些差距?3. 工艺管理平台建设1)谁负责工艺平台的建设?2)工艺委员会的产生:责任与运作模式3)如何进行工艺规划?4)基础工艺研究与应用5)支撑工艺管理平台的四大规范:* 品质规范* 设备规范* 工艺规范* 设计规划6)工艺管理部门如何推动DFM业务的开展?7)工艺体系的组织构成、发展与演变8)工艺人员的培养与技能提升4. 演练与问题讨论分析学员企业的工艺平台建设工作做到什么程度?存在哪些差距?如何改进?五、面向生产测试的产品设计(DFT)1. 基于产品生命周期全流程的测试策略1)研发测试(Alpha)、试验局测试(Beta)、生产测试2. 研发测试(Alpha)与BETA测试1)测试人员介入产品开发过程的时机(提可测试性需求的时机)2)可测试性需求需要考虑的内容(示例)3)单元测试、模块测试、系统集成测试、专业化测试、BETA测试的重点分析4)产品开发过程中测试业务流程分析5)企业在不同的发展阶段如何开展测试的相关工作(短平快的项目测试工作如何开展)3. 面向生产测试业务的产品设计与开发1)生产测试业务流程分析2)典型的部品测试、整机测试方法介绍3)开发专门的生产测试工装的条件分析4)生产测试工装的开发管理5)在产品开发过程中如何实施面向生产测试的产品设计?* 如何提出可测试性需求?* 可测试性需求如何落实到产品设计方案中?* 研发面对众多的需求如何取舍?可测试性需求的优先级分析* 如何在产品开发过程中同步开发生产测试工装?* 如何在产品开发过程中同步输出生产测试所需的操作指导文件?* 如何进行测试工装的验证?* 如何推动测试验证问题的解决?6)如何推动可测试性设计(DFT)业务的开展7)如何进行测试平台的建设?4. 演练与问题讨论分析学员企业的DFT工作做到什么程度?存在哪些差距?如何改进?六、产品试制验证管理1. 影响产品试制周期的因素分析2. 研发人员对试制准备提供的支持3. 试制团队的构成、职责与定位(设置试制部门的时机与优缺点分析)4. 试制人员介入产品开发过程的时机1)如何进行试制准备(准备要素示例)5. 面向制造系统的验证1)研发人员如何在试制过程中进行产品设计的优化2)制造系统的验证策略与计划3)制造系统的验证方案4)如何实施制造系统的验证:* 工艺验证(工艺流程、工艺路线、单板工艺、整机工艺、包装工艺、物流工艺)* 工装验证(装配工装、测试工装、生产设备)* 结构验证* 产品数据验证(BOM验证、制造文档验证)* 产品试制验证(质量、效率、成本)5)批次验证报告,验证多少批才合适?6)如何推动验证问题的解决?6. 转产评审1)研发人员如何支持新产品的转产工作2)转产评审的评审组织如何构成?* 评审标准是什么?* 如何判定是否转产?* 评审流程与运作机制7. 产品转产后的管理1)新产品的试制效果评价2)新产品的质量目标达成情况3)工程变更管理4)缺陷与问题管理5)质量审计8. 演练与问题讨论分析学员企业的产品试制验证过程,分析差距,提出改进建议讲师资质Charles 资深顾问专业背景十几年高科技行业从业背景,丰富的研发管理咨询经验,在国内某大型知名企业工作近10年,主持和参与过多个大型产品的研发工作,先后担任过开发工程师、项目经理、产品经理、新产品导入部总监、研发项目管理部总监等职位。
在任研发项目管理总监期间,成功组织建立了适合当时情况的研发流程管理、项目管理、技术管理体系。
并作为核心组成员全程参与了集成产品开发变革项目,与IBM顶尖咨询顾问一起工作了四年。
全面负责了集成产品开发管理变革项目在某产品线的具体流程落地和推行工作,对整个管理变革项目的成功起到了至关重要的作用。
后又与IBM顾问合作,成功主导了功能领域能力提升项目――新产品导入流程与平台的建设;在国内某大型知名企业工作期间,经历了该公司研发管理从不规范到规范化的整个过程,熟练掌握将国际先进的研发管理经验与中国企业实际情况相结合来构建研发管理体系的方法。
后应某知名通讯公司的邀请,以顾问的身份进入该公司的技术中心主导研发管理体系、研发IT规划、MARKETING管理体系的平台建设工作。
咨询背景从事研发管理咨询工作以来,作为项目总监成功的主持了格林威尔、广州威创日新、某电子科技集团研究所、国人通信等数十家企业的产品规划流程体系设计、试验局流程设计、知识管理体系设计、中试业务管理体系梳理、研发IT规划、研发项目管理体系设计、研发质量管理体系、研发绩效管理体系设计、研发KPI体系设计等方面的管理咨询项目。
培训背景曾在各地多次举办研发质量管理、研发项目管理、新产品开发流程优化与管理、从样品走向量产等公开课,为数千家企业提供了研发管理公开课的培训,为数百家企业进行了研发管理的内训;从事研发管理咨询工作以来,作为项目总监成功的主持完成了数十个研发管理咨询项目体系的建设<产品规划流程体系设计、试验局流程设计、知识管理体系设计、中试业务管理体系梳理、研发IT 规划、研发项目管理体系设计、研发质量管理体系、研发绩效管理体系设计、研发KPI体系设计等方面>,有着丰富的研发管理咨询经验,涉及的行业包括通信、软件、家电、电信运营商、芯片、医疗器械、交通运输等,帮助这些企业建立高效、完备的研发管理体系,对中国企业研发管理体系及创新体制有着深刻的研究和理解,受到客户的高度评价。