穿孔机操作规程
穿孔机技术操作规程完整

穿孔机技术操作规程完整
一、安全操作措施
1.在使用穿孔机前,应随时关注机器清洁及安全状况,确保安全正常
运行。
2.操作之前,应更换新的护目镜,戴上手套、工作服等安全防护用品。
3.在穿孔机操作过程中,必须进行定期维护和保养,确保机械部件的
主要零部件、开关、电路良好工作。
4.请勿改变机器安全设置,未经许可不得自行拆动机器,以免发生安
全事故。
5.请勿擅自添加机器附件,以免造成安全隐患并影响机器使用效率。
二、操作步骤
1.检查机器各个部分的紧固,并检查电源接口是否牢固。
如有损坏应
及时进行维修。
2.上电后,按机器操作要求操作控制面板,选择穿孔机程序,将待穿
孔材料装在工作台上,打开安全开关并确认安全装置无误。
3.调节穿孔机参数,如穿孔孔径,深度,速度,运行时间等。
4.选择合适的穿孔钻头,安装到主轴上,确保螺纹牢固,穿孔钻头角
度正确。
5.连接机器电源,然后进行穿孔。
穿孔完成后,清理工作台,进行安
全检查。
6.最后,请关闭机器上的电源,并收拾好工作现场。
三、主要问题
1.使用过程中,有时会出现穿孔孔口大小偏差,其原因可能是穿孔钻头参数有误。
穿孔机操作规程

穿孔机操作规程一、引言穿孔机是一种常见的机械设备,广泛应用于工业生产中的金属加工环节。
为了确保操作人员的安全、提高工作效率和保障机器设备的稳定运行,制定一套穿孔机操作规程是必要的。
本文将为操作人员提供一份详细且易于理解的穿孔机操作规程。
二、操作前准备1. 检查穿孔机设备的工作状态,确保所有零部件正常运转,没有损坏或松动的情况。
2. 穿孔机操作前需佩戴符合安全要求的个人防护装备,如护目镜、护耳器、防护手套等。
3. 检查工作区域,清理所有与穿孔机操作无关的工具和杂物,确保工作环境整洁有序。
4. 确保穿孔机周围没有电缆、水管等杂物,以免干扰操作或导致安全事故。
5. 将操作说明和紧急联系方式放置在显眼的位置,以备不时之需。
三、操作步骤1. 打开穿孔机电源,确保电源线接触良好,插头牢靠。
2. 根据待处理的材料类型,选择合适的穿孔刀头和穿孔模具,并安装到机器上。
3. 根据穿孔尺寸要求,调整穿孔机的尺寸和深度设置,确保精准的穿孔效果。
4. 将待处理材料放置在穿孔机工作台上,并用夹具固定住,确保工件的稳定性。
5. 按下启动按键,启动穿孔机,待机器开启后,缓慢将工件移动到穿孔位置,不要用力过猛或过快。
6. 在穿孔过程中,注意观察机器运行情况和工件质量,如发现异常及时停机处理。
7. 穿孔结束后,等穿孔刀头完全停止后,再关闭穿孔机电源。
四、操作注意事项1. 在操作穿孔机时,不得穿戴宽松衣物,长发应盘起或用帽子遮盖,以免被机器夹紧。
2. 操作过程中,应保持清醒、专心,不要与他人闲聊或分心做其他事情。
3. 使用穿孔机时,切勿将手指或其他身体部位靠近穿孔刀头附近,以免发生意外伤害。
4. 穿孔机操作完毕后,应及时清理工作区域,保持机器设备整洁。
5. 定期对穿孔机进行维护保养,检查零部件的磨损情况,确保操作的安全性和设备的正常运转。
五、紧急情况处理1. 在操作穿孔机时,如果发生异常或机器故障,应立即停机,并按照紧急处理程序进行操作。
精密自动穿孔机安全操作及保养规程

精密自动穿孔机安全操作及保养规程一、前言精密自动穿孔机是一种高精度的加工设备,因其自动化程度较高、操作简便、处理效率快等特点,在现代制造领域得到了广泛应用。
但由于器械本身具有一定的危险性,不规范操作和保养容易导致事故的发生。
为了保障人员安全,提高设备的使用寿命,本文总结出一些精密自动穿孔机的安全操作及保养规程,供用户参考。
二、操作规程1. 穿孔前的准备在进行任何操作前,应先对精密自动穿孔机进行必要的检查和准备。
1.检查工作环境是否安全,周围是否有烟火等易燃物品。
2.检查穿孔机的工作台和镜台是否放置平稳,夹具是否安装正确。
3.检查钻头切削端是否磨损严重,是否有损伤。
4.检查冷却液是否充足,并对管路进行检查,保证畅通通畅。
5.保证控制面板和电源系统正常工作,检查所有电器和机械装置是否牢固。
2. 启动精密自动穿孔机启动机器前需进行以下步骤:1.拉起主机电源,启动整个控制系统。
2.开启冷却系统,使其开始运作,并对其进行检查确认。
3.将工件夹具按照正确的位置安装在工作台上。
4.在控制面板上选择相应的工艺参数,并根据实际需要进行调整。
3. 穿孔操作1.穿孔操作前,必须保证操作人员处于安全位置。
2.操作人员必须佩戴工作手套、安全眼镜等防护装备。
3.穿孔操作过程中,不得离开工作台前方,避免造成危险。
4.穿孔完毕后,应及时切断电源并关闭冷却系统。
5.检查钻孔成果,并对机器的表面和附件进行清理。
三、保养规程精密自动穿孔机在机器使用过程中,避免不规范的保养会影响机器的使用寿命,导致机器运行不稳定,具体的保养规程如下:1. 定期清理冷却系统冷却液在机器使用过程中有收集异物和产生污渍的风险,定期清理可确保其畅通无阻,并让机器保持最佳表现。
2. 定期检查钻头机器的钻头是非常耐用的,但也需要进行定期检查,检查其切削端是否磨损、是否有损伤以及是否出现钝化等情况。
3. 定期保养机器定期保养机器有很多好处,例如:1.在机器需要清理或修理时减少停机时间。
穿孔机安全操作及保养规程
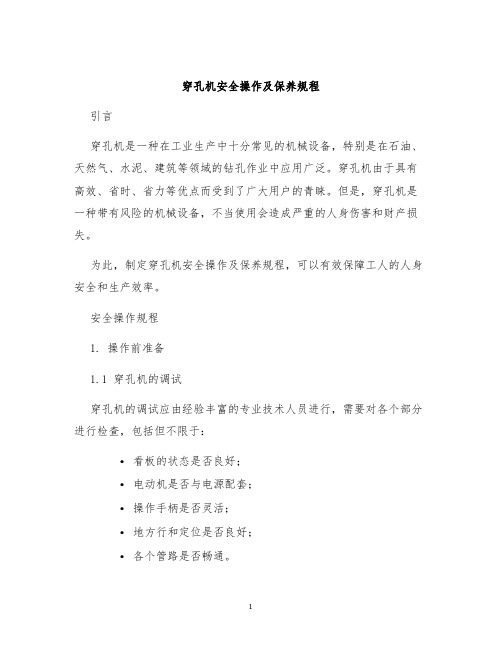
穿孔机安全操作及保养规程引言穿孔机是一种在工业生产中十分常见的机械设备,特别是在石油、天然气、水泥、建筑等领域的钻孔作业中应用广泛。
穿孔机由于具有高效、省时、省力等优点而受到了广大用户的青睐。
但是,穿孔机是一种带有风险的机械设备,不当使用会造成严重的人身伤害和财产损失。
为此,制定穿孔机安全操作及保养规程,可以有效保障工人的人身安全和生产效率。
安全操作规程1. 操作前准备1.1 穿孔机的调试穿孔机的调试应由经验丰富的专业技术人员进行,需要对各个部分进行检查,包括但不限于:•看板的状态是否良好;•电动机是否与电源配套;•操作手柄是否灵活;•地方行和定位是否良好;•各个管路是否畅通。
1.2 操作者的准备在操作前,需要落实以下措施:•充分了解穿孔机的工作原理和构造,了解各个部分的作用和定位。
•穿戴合适的劳动防护用品,包括防护手套、安全眼镜、口罩等。
•准备好必要的工具,如扳手、螺丝刀等。
•熟悉紧急停机的操作方法。
2. 操作过程注意事项2.1 穿孔机的安装•确保安装的稳定性,不要在不平稳的地面上操作穿孔机。
•安装完成后要对穿孔机不同部位进行检查、调试。
2.2 进行钻孔操作•保持安全距离,避免发生钻头断裂、轴承故障、冷却液溅射等情况。
•随时检查钻头的磨损、断裂等状况。
如有磨损或断裂的情况由有资质的专业技术人员进行更换。
•随时保持清洁,避免杂物进入穿孔机造成危险。
•当操作过程中发现异常情况,应立即紧急停机并寻找对应的解决方案。
3. 操作后维护•操作完成后,及时关掉电源,停止冷却液的供给,清理残余粉尘。
•钻头和其它部位需要每日进行检查和维护,避免出现故障。
对于有故障的部位需及时维修或更换。
保养规程1.需要定期进行的保养•钻头定期需要进行清洗、维修和保养工作。
•对于钻孔加工的过程中涉及的液压元件和电气元件,也需要定期清理、加油、检查保养。
2.日常保养•钻头和其它部位需要每日进行检查和维护,避免出现故障。
对于有故障的部位需及时维修或更换。
穿孔机组安全技术操作规程
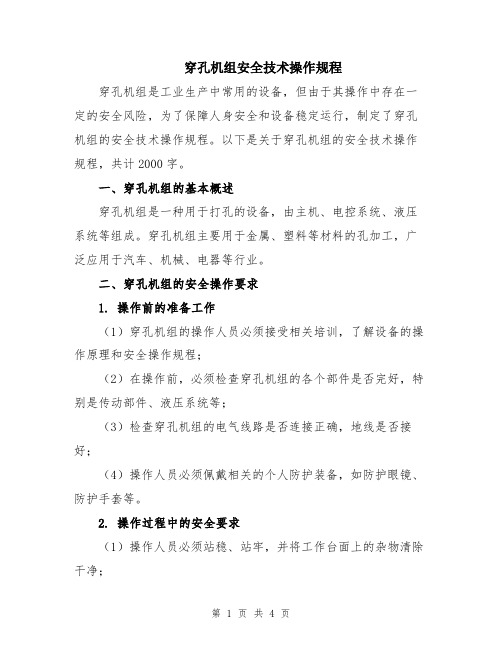
穿孔机组安全技术操作规程穿孔机组是工业生产中常用的设备,但由于其操作中存在一定的安全风险,为了保障人身安全和设备稳定运行,制定了穿孔机组的安全技术操作规程。
以下是关于穿孔机组的安全技术操作规程,共计2000字。
一、穿孔机组的基本概述穿孔机组是一种用于打孔的设备,由主机、电控系统、液压系统等组成。
穿孔机组主要用于金属、塑料等材料的孔加工,广泛应用于汽车、机械、电器等行业。
二、穿孔机组的安全操作要求1. 操作前的准备工作(1)穿孔机组的操作人员必须接受相关培训,了解设备的操作原理和安全操作规程;(2)在操作前,必须检查穿孔机组的各个部件是否完好,特别是传动部件、液压系统等;(3)检查穿孔机组的电气线路是否连接正确,地线是否接好;(4)操作人员必须佩戴相关的个人防护装备,如防护眼镜、防护手套等。
2. 操作过程中的安全要求(1)操作人员必须站稳、站牢,并将工作台面上的杂物清除干净;(2)操作人员在操作穿孔机组时,必须集中注意力,不得分散注意力;(3)操作人员禁止将手指、头发等靠近穿孔机组运动部位;(4)穿孔机组在运行过程中,操作人员禁止随意触摸设备;(5)机组停止工作后,操作人员严禁将安全防护装置解除,必须等到设备完全停止后方可操作。
3. 穿孔机组的维护保养(1)穿孔机组的维护保养必须由专业人员进行,并按照设备维护保养手册的要求进行操作;(2)定期检查穿孔机组的润滑系统,确保润滑油的充足和润滑系统的正常工作;(3)定期检查穿孔机组的电气线路,确保电线连接良好,不得出现老化、断裂等情况;(4)对穿孔机组的传动系统进行定期检查,确保传动带、链条等没有松动、磨损等情况;(5)定期清理穿孔机组的工作台面,保持设备的整洁。
三、穿孔机组的常见故障及处理方法1. 机组停止工作可能原因:液压系统故障、电器故障等。
处理方法:首先检查液压系统的压力是否正常,是否有漏油等情况;其次,检查电气线路是否正确连接,电源是否正常供电。
穿孔机(钻机)操作规程

穿孔机(钻机)操作程序
1、驾驶员应在换档前检查方向、制动器、润滑系统、提升系统、
各种电表、按钮、开关、手柄等是否完好灵敏,电压低于360V停止起动。
2、炮眼工检查钻头、钻杆、锁子、锤子、锄头、水桶是否齐全完好,如果钻机上的零件不完整且不敏感,危害安全生产时,应停止作业,并报告领导。
3、行走时,钻杆不能安装在钻机上(取下钻杆),司机先按起动
电钮,变速手把换到低速档,脚放在刹车板上,炮眼工负责指挥行走,查看码口稳定,拉电缆,严禁高速、中速行走。
4、钻孔:
⑴、两配合,对准设计的孔位,首先将手柄转到顺时针位置,按
起动电钮,手握提升手柄,掌握土质软硬程度,下钻速度,接头位置。
⑵、连接钻杆,必须待转动停止后,用锤子或棍子牢牢夹住钻杆,插上销子并固定好,人站离钻杆50cm外,司机才能作业。
⑶、刮钻灰时,不要在钻杆附近刮擦,严禁用手刮。
⑷、当土壤较软且钻灰不出来时,沿钻孔位灌水一至二桶,再用
锄头打压严整,然后下钻。
⑸、取钻杆,钻杆提不动时,立即按下停止按钮,把手柄扳到倒
转位,然后按起动电钮,进行正常作业(停稳转速,拔销子,挂钩)。
⑹、当天不爆破的炮眼,必须盖好,防止其他物体落入孔中。
5、作业时,马达温度超过65°C或听到电机异响,应立即停机检查,并把查出来的情况报告领导。
6、下班前,将钻机开到场外开口处5m以外的安全区,把钻头钻下1m左右,关好开关,切断电缆电源,收好钻杆和工具,打扫司机室内卫生,锁好机门。
打孔机安全操作规程
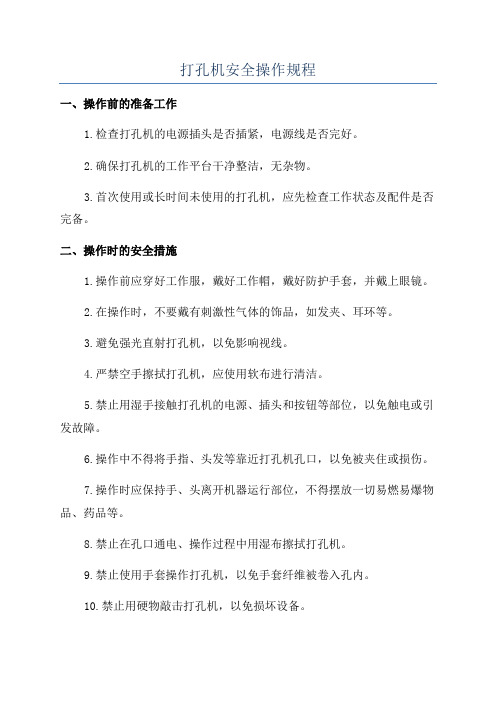
打孔机安全操作规程一、操作前的准备工作1.检查打孔机的电源插头是否插紧,电源线是否完好。
2.确保打孔机的工作平台干净整洁,无杂物。
3.首次使用或长时间未使用的打孔机,应先检查工作状态及配件是否完备。
二、操作时的安全措施1.操作前应穿好工作服,戴好工作帽,戴好防护手套,并戴上眼镜。
2.在操作时,不要戴有刺激性气体的饰品,如发夹、耳环等。
3.避免强光直射打孔机,以免影响视线。
4.严禁空手擦拭打孔机,应使用软布进行清洁。
5.禁止用湿手接触打孔机的电源、插头和按钮等部位,以免触电或引发故障。
6.操作中不得将手指、头发等靠近打孔机孔口,以免被夹住或损伤。
7.操作时应保持手、头离开机器运行部位,不得摆放一切易燃易爆物品、药品等。
8.禁止在孔口通电、操作过程中用湿布擦拭打孔机。
9.禁止使用手套操作打孔机,以免手套纤维被卷入孔内。
10.禁止用硬物敲击打孔机,以免损坏设备。
三、操作事项1.严禁超负荷使用打孔机,避免过度磨损或损坏机器。
2.遇到异常声音、异味、烟雾等现象,应立即停机检查,不能强行操作。
3.每次使用结束后,应先切断电源,然后等待一段时间后再进行清理和维护。
4.在打孔机孔口边,设有明显的警示标识,应注意遵守。
5.严禁在打孔机上安装或更换部件,应经过专业技术人员检测确认后方可进行。
6.禁止私自改变打孔机的工作程序、参数等,严禁私自拆卸、修理打孔机。
四、维护保养1.定期检查打孔机的电源插头和电源线,如果有破损或老化现象,应及时更换。
2.打孔机应定期清理,避免灰尘或杂物的堆积造成故障。
3.检查打孔机的电源,并定期进行维护和保养。
4.每次使用结束后,应切断电源,清理机器,并加润滑油适量涂抹在运动件上,保持机器的正常工作状态。
5.长时间不使用的打孔机,应存放在干燥通风处,远离湿气和腐蚀性气体。
总结:打孔机作为一种常用的办公设备,如果使用不当会给人们的工作带来一定的危险。
因此,制定和遵守打孔机安全操作规程是非常必要的。
穿孔机操作规程

穿孔机操作规程
《穿孔机操作规程》
一、穿孔机的基本操作流程
1. 按照穿孔机的安全要求,确认操作人员身着合适的工装,并戴好安全帽和手套。
2. 开启穿孔机的主电源开关,将机器预热5-10分钟。
3. 调整机器的参数,包括速度、力度和穿孔模具的位置。
4. 将需要加工的材料放置在穿孔机的工作台上,并确保材料的位置和固定。
5. 启动穿孔机,进行穿孔作业。
6. 完成作业后,关闭穿孔机的主电源开关,清理工作台和机器,确保机器处于安全状态。
二、穿孔机操作中的注意事项
1. 操作人员需经过专业培训,了解穿孔机的基本原理和操作流程。
2. 在操作穿孔机时,不得随意触碰机器的运动部件,以免造成意外伤害。
3. 在穿孔机作业过程中,如遇到异常情况,应立即停机并及时报告相关人员进行处理。
4. 操作人员应定期对穿孔机进行检查和保养,确保机器的正常运转。
5. 穿孔机操作结束后,应按规定对机器进行清洁和维护,保持机器的良好状态。
三、穿孔机的故障处理
1. 在穿孔机操作过程中,如出现异常噪音或异味,应立即停机,并及时检查和处理故障。
2. 对于一些常见的穿孔机故障,操作人员应按照相关标准进行处理,或者及时联系专业维修人员进行维修。
通过严格遵守《穿孔机操作规程》,可以确保穿孔机的安全操作和正常运行,提高工作效率,保障人员的人身安全。
穿孔机安全操作规程

穿孔机作业岗位安全操作规程1 范围: 本规程适用于零部件车间操作数控外圆磨床,负责设备班前、班后检查、保养的作业人员。
2 岗位主要危险有害因素(危险源)4 劳动防护用品穿戴要求●作业人员应穿戴工作服、工作帽,长发应盘在工作帽内,袖口及衣服角应系扣;●加工铸铁工件、清扫铸铁粉末时,应佩戴活性炭防尘口罩;●班后停机清理铁屑时可佩戴防水手套;5 作业安全要求5.1作业前安全操作准备●操作人员应熟悉本机性能,结构等,并经培训合格方可上岗;●使用前按设备点检卡进行检查,按规定加油,检查油质,油量,油路要畅通;●运行前,必须认真检查各操作手柄及控制按钮是否置于安全档位,转动各旋转部位,安全装置是否齐全,可靠。
●操作过程中,发现设备有不正常声音及故障、应立即停机、关闭●查看前一班次的交接班记录,检查设备各部位是否完好,各手柄是否处在正常位置;检查传动带、齿轮安全罩是否完好有效,是否有未完成的工件且装卡完成。
5.2 作业过程安全操作要求●操作过程中严禁用手触摸转动的铜管轧辊,更换时必须停机,确保正确后,方可开机。
●发现顶杆或铜管轧辊弯曲,漏水等情况要及时停机检查,及时更换相应配件。
●穿孔过程中,严禁跨越顶杆,铜管轧辊的行程范围,禁止在周边逗留,禁止在运转部件上放工具。
●工件加工前先固定锁紧,检查确认安装牢固,位置正确后方可加工;加工前检查设备本部件位置正确,无异常;●认真操作,加工过程中严禁离开设备,严格按操作程序控制机台;5.3 设备停机后的作业安全要求●清扫设备、润滑机床,严禁开机作业,应关闭电源进行。
●清除切屑应用专用钩子或毛刷等工具,不得用手,防止刀尖、切屑等物划伤手。
●交接班时,应对穿孔机的设备和环境卫生进行全面清理,及时填写交班报告和岗位记录。
6 岗位应急要求6.1 砂轮与工件发生碰撞等现象时,应立即停机,停机前人员立即离开工件旋转方向,并通知周边人员离开现场。
6.2 切屑进入眼睛皮肤,应立即到厂医务室治疗;若碎片嵌入身体,切勿随意拔出,应由医师负责清理。
穿孔机安全操作规程
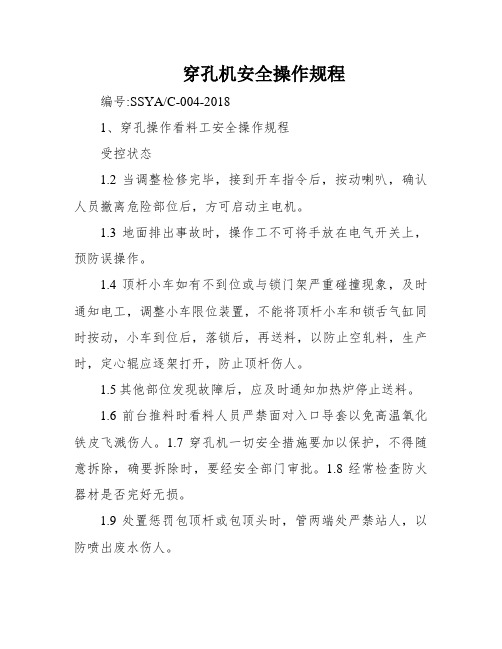
穿孔机安全操作规程编号:SSYA/C-004-20181、穿孔操作看料工安全操作规程受控状态1.2当调整检修完毕,接到开车指令后,按动喇叭,确认人员撤离危险部位后,方可启动主电机。
1.3地面排出事故时,操作工不可将手放在电气开关上,预防误操作。
1.4顶杆小车如有不到位或与锁门架严重碰撞现象,及时通知电工,调整小车限位装置,不能将顶杆小车和锁舌气缸同时按动,小车到位后,落锁后,再送料,以防止空轧料,生产时,定心辊应逐架打开,防止顶杆伤人。
1.5其他部位发现故障后,应及时通知加热炉停止送料。
1.6前台推料时看料人员严禁面对入口导套以免高温氧化铁皮飞溅伤人。
1.7穿孔机一切安全措施要加以保护,不得随意拆除,确要拆除时,要经安全部门审批。
1.8经常检查防火器材是否完好无损。
1.9处置惩罚包顶杆或包顶头时,管两端处严禁站人,以防喷出废水伤人。
1.10装卸顶头时,首先通知操作台上操作工,顶杆停稳后方可进行。
1.1.1穿孔机在启动时,严禁穿管,待运转1-3分钟后方可穿管,以防启动电流太大又增加负荷导致跳闸,形成设备事故,严禁不停车换导板。
1.1.2严格执行交接班制度,下班时清理现场卫生,保持安全检查文明生产。
2、穿孔机调车工安全操作规程2.1必须熟练掌握穿孔机的性能、构造和道理等操作技术规程,工作时按规定穿戴好劳动保护用品。
2.2开车前要认真搜检设备各部件安全办法及工具是否良好,发现问题应实时修理或更换(严禁用手触摸转动的轧辊,更换时,必须停车),确保一般后,方可通知开车。
2.3发现顶杆弯曲导板有裂纹应实时更换。
2.4不准轧制过烧、欠烧的坯,以免抱顶杆或穿破伤人。
2.5穿孔过程中,严禁跨越顶杆,定心辊及小车滑道,禁止在穿孔机出料及定心辊周围逗留,禁止在运转部件上抬工具等。
2.6交接班时,应对穿孔机的设备和环境卫生进行全面清理,及时填写交接班报告和岗位记录。
2.7认真操作、严格按操作程序控制机台,不得翻弯管,翻斜料。
穿孔机组安全技术操作规程
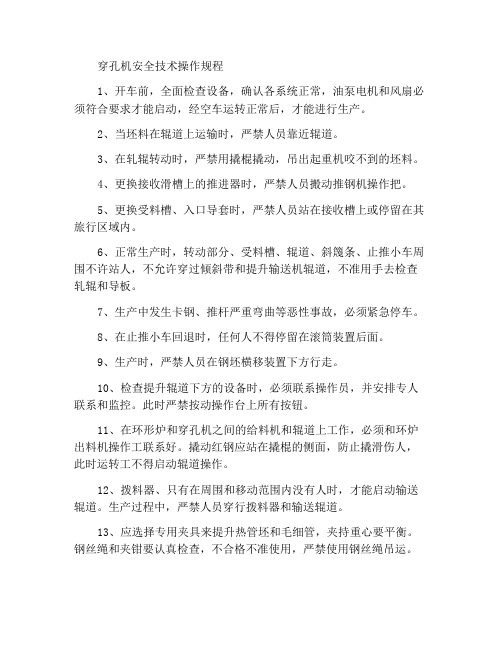
穿孔机安全技术操作规程1、开车前,全面检查设备,确认各系统正常,油泵电机和风扇必须符合要求才能启动,经空车运转正常后,才能进行生产。
2、当坯料在辊道上运输时,严禁人员靠近辊道。
3、在轧辊转动时,严禁用撬棍撬动,吊出起重机咬不到的坯料。
4、更换接收滑槽上的推进器时,严禁人员搬动推钢机操作把。
5、更换受料槽、入口导套时,严禁人员站在接收槽上或停留在其旅行区域内。
6、正常生产时,转动部分、受料槽、辊道、斜篾条、止推小车周围不许站人,不允许穿过倾斜带和提升输送机辊道,不准用手去检查轧辊和导板。
7、生产中发生卡钢、推杆严重弯曲等恶性事故,必须紧急停车。
8、在止推小车回退时,任何人不得停留在滚筒装置后面。
9、生产时,严禁人员在钢坯横移装置下方行走。
10、检查提升辊道下方的设备时,必须联系操作员,并安排专人联系和监控。
此时严禁按动操作台上所有按钮。
11、在环形炉和穿孔机之间的给料机和辊道上工作,必须和环炉出料机操作工联系好。
撬动红钢应站在撬棍的侧面,防止撬滑伤人,此时运转工不得启动辊道操作。
12、拨料器、只有在周围和移动范围内没有人时,才能启动输送辊道。
生产过程中,严禁人员穿行拨料器和输送辊道。
13、应选择专用夹具来提升热管坯和毛细管,夹持重心要平衡。
钢丝绳和夹钳要认真检查,不合格不准使用,严禁使用钢丝绳吊运。
14、吊运顶杆要遵守挂吊工操作规程,顶杆必须单支吊运,必须用≥¢17.5mm的钢丝绳作业。
严禁用单根或不均匀的钢丝绳起吊。
15、更换受料槽、处理滚动堵塞或在接收槽下部工作时,必须关闭机器并关闭电锁,并向炉子发出停料警示。
16、提高功耗时间,做到最大限度“削峰填谷”,保持“节能、降耗”。
17、循环水的合理利用,控制水质,不得外排。
18、更换穿孔辊时要有专人指挥行车和上下协调,必须使用专用吊具和钢丝绳,任何人不得在穿孔机盖移动装置下方和周围逗留。
19、进行孔型调整操作时,严禁人员停留在穿孔机通道处。
操作规程穿孔机组安全技术操作规程

操作规程穿孔机组安全技术操作规程一、安全指导原则1.1 安全第一,预防为主1.2 发现危险、隐患必须及时报告1.3 熟知设备操作规程和注意事项二、操作规程2.1 操作前检查在操作穿孔机前,必须检查穿孔机上下模具的装配是否正确、刀具是否锋利以及是否进行了正确的润滑。
2.2 插排线及开机操作操作人员必须严格按流程执行操作,接好插排线并保证接地良好。
开机前必须先启动控制系统。
在开机后必须先进行手动操作测试,检查穿孔机是否正常运行。
2.3 保持设备整洁操作人员在长时间操作之后必须检查穿孔机的工作状况,并清理穿孔机设备及现场,保证现场整洁。
2.4 润滑维护操作人员必须定期对穿孔机进行润滑养护。
在使用切削液的同时必须按照产品要求进行规范操作,保证设备长期正常运行。
三、安全事项3.1 禁止在操作穿孔机时戴手套操作人员在操作穿孔机的过程中,禁止戴手套,以免手套被卷入机器,造成安全隐患。
3.2 插排线需要按照流程进行接线操作人员在接线时必须按照规定流程进行接线,保证插排接线正确并且接地良好,以免发生电击事故。
3.3 遵守工作规程操作人员在操作过程中必须严格遵守工作规程,加强自我保护意识和保护他人的意识。
四、应急措施4.1 电气故障如果发生电气故障,操作人员必须按照规定的操作流程进行排除故障,如果不具备排除故障的能力,必须及时报告维护人员进行排除故障。
4.2 机械故障如果发生机械故障,操作人员必须及时停机,并通知维护人员进行故障排除、修理。
五、操作注意要点5.1 穿孔机如何保持稳定在操作穿孔机的过程中,必须严格按照操作规程进行操作,稳定穿孔机设备是操作关键,操作人员必须进行稳定的操作并及时检查设备状态。
5.2 设备操作清晰明了操作人员的操作指令必须清晰明了,并有专人跟踪确认,确保操作无误。
六、设备故障排除6.1 电气故障排除1)首先,检查穿孔机设备连接是否正确。
2)其次,排查故障是否由其它原因引起。
3)如果仍然无法解决,必须及时通知维修人员进行排除故障。
穿孔机组安全技术操作规程范文(二篇)
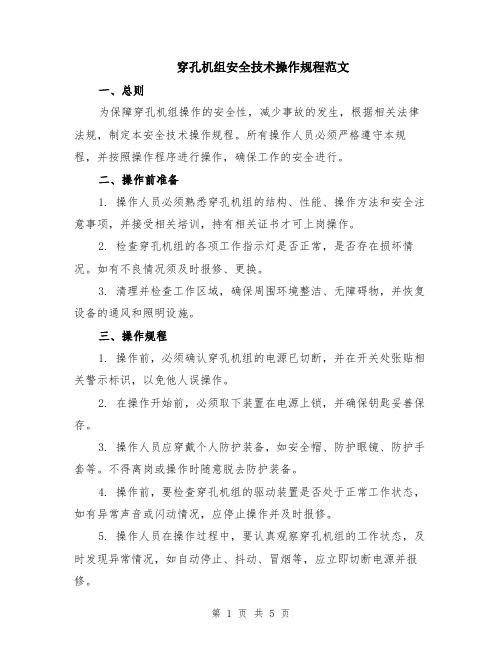
穿孔机组安全技术操作规程范文一、总则为保障穿孔机组操作的安全性,减少事故的发生,根据相关法律法规,制定本安全技术操作规程。
所有操作人员必须严格遵守本规程,并按照操作程序进行操作,确保工作的安全进行。
二、操作前准备1. 操作人员必须熟悉穿孔机组的结构、性能、操作方法和安全注意事项,并接受相关培训,持有相关证书才可上岗操作。
2. 检查穿孔机组的各项工作指示灯是否正常,是否存在损坏情况。
如有不良情况须及时报修、更换。
3. 清理并检查工作区域,确保周围环境整洁、无障碍物,并恢复设备的通风和照明设施。
三、操作规程1. 操作前,必须确认穿孔机组的电源已切断,并在开关处张贴相关警示标识,以免他人误操作。
2. 在操作开始前,必须取下装置在电源上锁,并确保钥匙妥善保存。
3. 操作人员应穿戴个人防护装备,如安全帽、防护眼镜、防护手套等。
不得离岗或操作时随意脱去防护装备。
4. 操作前,要检查穿孔机组的驱动装置是否处于正常工作状态,如有异常声音或闪动情况,应停止操作并及时报修。
5. 操作人员在操作过程中,要认真观察穿孔机组的工作状态,及时发现异常情况,如自动停止、抖动、冒烟等,应立即切断电源并报修。
6. 在操作过程中,严禁使用生锈、变形或磨损的工具。
使用工具前要检查其完好性,确保安全使用。
7. 不得在穿孔机组上放置杂物,以免引发摩擦或其他意外。
8. 在穿孔机组上工作前,需要将移动部件锁定以防止意外开启或移动。
9. 操作人员在操作穿孔机组时,应专心致志,不得随意离开岗位。
如需暂时离位,应关闭穿孔机组的电源并上锁。
10. 操作结束后,应进行设备的清洁和维护,确保穿孔机组的正常运行。
四、事故处理1. 若在操作过程中发生事故,首先应立即切断穿孔机组电源,并通知相关人员进行救援。
2. 处理事故时要冷静沉着,切勿慌乱行动,保护好自己和他人的人身安全。
3. 事故发生后,要立即报告相关负责人,并进行详细记录,以便事后查找原因。
五、违规行为处理1. 对于违反规程操作、未佩戴个人防护装备、离岗或离位未关闭机组电源等违规行为,要给予相应的处理和教育,严重者可予以停职、罚款或解除劳动合同。
穿孔机岗位操作规程

穿孔机岗位操作规程_______________________________________________________________________________________________________穿孔机岗位操作规程1.0 目的:按“工艺技术规程”将加热,定心的管坯通过斜轧穿孔后,符合顶管机组预穿芯棒,顶管的毛管。
2.0 范围:热定心机,穿孔机组调整,操作。
3.0 职责:3.1 根据“热轧管生产作业指令”正确调整热定心,穿孔机各参数,组织生产,严格执行符合顶管机组要求的毛管。
3.2 操作人员严格按本岗位操作规范要求作业,并做好相关记录。
3.3 加强上下工序生产过程监控,控制轧制节奏。
3.4 做好回炉管坯(毛管.废毛管)的标色和可追溯性工作。
3.5 利用现有通讯工具,及时“呼叫”相关人员。
4.0 作业程序:4.1岗位(作业)要求:4.1.1 岗位要求:4.1.1.1 技术标准:结构用无缝钢管GB/T8162输送流体用无缝钢管GB/T8163低中压锅炉用无缝钢管GB3087高压锅炉用无缝钢管GB5310无缝和焊接、热镀锌钢管ASTMA53高温作业用碳素钢无缝钢管ASTMA106套管和油管规范API SPEC 5CT管线钢管规范API SPEC 5L汽车半轴套用无缝钢管YB/T5035钻探用无缝钢管Q/BQB230_______________________________________________________________________________________________________4.1.1.2 工艺规程:本岗位作业根据“热轧无缝钢管工艺技术规程”(ZCBJ01)第五、第六章节内容。
即:(一)热定心:钳口材质: H12 管坯直径加工钳口Ø130mmØ 134mmØ140mm Ø144mm液压缸:定心液压缸:Ø220x180mm Pmax=100Mpa夹紧液压缸:Ø300x480mm Pmax=100Mpa液压油工作压力:<60bar定心孔尺寸:直径:Ø40mm深度:15~30mm偏心度:<2mm(二)穿孔机:管坯直径x长度:Ø130mm(Ø140mm)x750~2150mm(碳钢,低合金钢)毛管直径x壁厚x长度:Ø130(Ø140)x16~20x1500~4500mm轧辊直径x长度:Ø480~520x360mmα=6°~10°主电机: 1600kw 970转/分推缸机: 汽缸直径:Ø100mm,行程2300mm推杆长度: 管坯长推杆长1200~1650mm 750mm750~1200mm 1200mm1650~2150mm 300mm_______________________________________________________________________________________________________4.1.1.3 生产合同要求:根据“生产作业令,工艺简表”认真执行合同(包括用户特殊)要求。
穿孔机高速穿孔机安全操作及保养规程

穿孔机高速穿孔机安全操作及保养规程穿孔机是一种常见的机械设备,广泛应用于自动化车间和工厂生产线中。
在进行穿孔操作时,我们必须严格按照规程进行操作,以保证操作安全,提高生产效率和产品质量。
本文将详细介绍穿孔机高速穿孔机的安全操作及保养规程。
安全操作1. 穿孔机操作前的准备工作在进行穿孔机操作前,必须先进行以下准备工作:•关闭电源开关•穿孔机调至初始状态•验证刀具、刀柄、工件和夹具是否合适,是否装配正确•检查穿孔机各部位的螺丝、密封件和润滑油是否充足2. 穿孔机安全操作流程在进行穿孔机操作时,必须严格按照以下步骤进行,以确保操作安全:(1) 打开电源打开电源前,必须检查电线是否正常,电源开关是否处于关闭状态。
(2) 穿孔机手动调整状态操作人员必须确认穿孔机处于手动调整状态,并确认刀具摆动幅度是否适当、刀具路径是否正确。
(3) 给工件定位给工件定位时,必须先将工件清洁干净,然后将其放入夹具内,确认工件是否固定牢靠。
(4) 手动启动穿孔机在穿孔机启动前,必须确认机器处于手动状态,然后慢慢地启动机器,观察刀具摆动的幅度和轨迹是否正常。
(5) 穿孔加工穿孔加工前,必须确认工件与夹具处于水平状态,并确定工件加工位置。
在穿孔过程中,操作人员必须保持警惕,随时注意刀具摆动幅度和路径。
(6) 关闭电源当穿孔完成后,必须关闭电源开关,并检查穿孔机各部件是否正常运行,然后将穿孔机调整到初始状态。
3. 安全注意事项在进行穿孔机操作时,操作人员必须明确以下安全注意事项:•在操作过程中,必须佩戴工作手套、护目镜、口罩等个人防护器材•禁止直接接触刀具和机器的旋转部件•禁止将身体或者其他物体伸进机器的加工区域内•在机器进行高速运转时,必须保持操作区域的干净、整洁,防止滑倒或者碰伤。
保养规程穿孔机的长期使用需要进行合理的保养,以确保穿孔机的效率、使用寿命和安全性。
以下是穿孔机保养规程:1. 定期清洁机器在穿孔机的使用过程中,需要定期对其进行清洁,并保持机器干净、整洁。
穿孔机操作规程
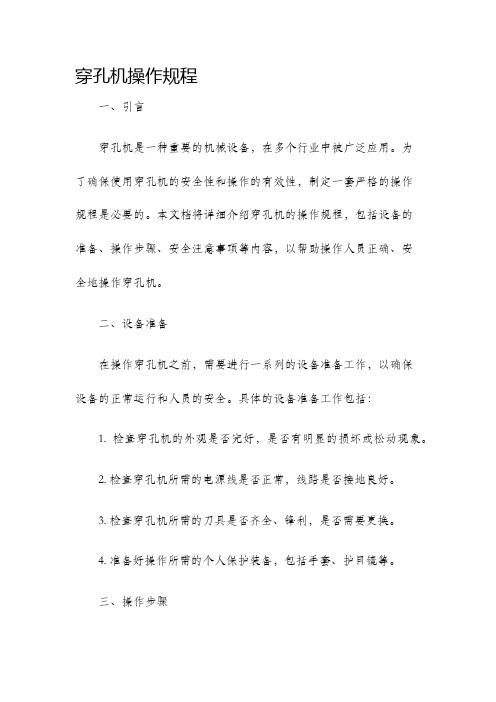
穿孔机操作规程一、引言穿孔机是一种重要的机械设备,在多个行业中被广泛应用。
为了确保使用穿孔机的安全性和操作的有效性,制定一套严格的操作规程是必要的。
本文档将详细介绍穿孔机的操作规程,包括设备的准备、操作步骤、安全注意事项等内容,以帮助操作人员正确、安全地操作穿孔机。
二、设备准备在操作穿孔机之前,需要进行一系列的设备准备工作,以确保设备的正常运行和人员的安全。
具体的设备准备工作包括:1. 检查穿孔机的外观是否完好,是否有明显的损坏或松动现象。
2. 检查穿孔机所需的电源线是否正常,线路是否接地良好。
3. 检查穿孔机所需的刀具是否齐全、锋利,是否需要更换。
4. 准备好操作所需的个人保护装备,包括手套、护目镜等。
三、操作步骤1. 打开穿孔机的电源开关,确保电源供应正常。
2. 设置穿孔机的相关参数,包括穿孔深度、穿孔速度等。
根据不同的材料和穿孔需求进行调整。
3. 将需要穿孔的材料或工件放置在穿孔机的工作台上,并固定好。
4. 进行试样穿孔,通过调整参数和刀具位置,确保穿孔的准确性和质量。
5. 开始正式的穿孔作业,根据工件的要求和数量进行连续穿孔。
6. 在穿孔过程中,注意观察穿孔机的工作情况,如有异常情况及时停机检查。
7. 穿孔完成后,关闭穿孔机的电源开关,进行设备的清洁和维护。
四、安全注意事项1. 在操作穿孔机之前,必须对设备的安全操作规程进行充分了解,并接受相关培训。
2. 在穿孔机操作过程中,必须佩戴个人防护设备,如手套、护目镜等。
3. 使用穿孔机时,应注意材料的选择。
必须使用符合规范要求的材料进行穿孔。
4. 操作人员必须足够熟悉穿孔机的结构和功能,以便正确使用设备。
5. 在穿孔机工作期间,严禁将手指或其他身体部位靠近刀具或其他运动部分,以免造成伤害。
6. 当出现穿孔机异常情况时,如设备噪音异常、冒烟等,应立即停止操作,并通知相应的维修人员进行检修。
7. 在完成穿孔作业后,应及时清理工作台和穿孔机设备,保持设备的清洁和良好状态。
打孔机操作规程

打孔机操作规程
一.开机前安全检测
1.1将手动、自动开关打到手动位置。
1.2将手动调速电位器按逆时针方向旋转到不动为止。
1.3合上电控箱空气开关,按总电开按钮,指示灯亮。
1.4按顺时针方向旋转手动调速电位器,使打孔机钻头旋转。
1.5按胶条实际打孔方向,正确设定正转、反转开关位置。
二、开机
2.1按总电开按钮打开电源。
2.2配合手动调速电位器,将胶条在工位上安装好。
2.3将胶条套在自动跟踪摇臂上。
2.4按电钻开关,指示灯亮,高速电钻开始工作。
2.5将手动、自动开关打到自动位置,打孔机正常工作。
三、关机
3.1按总电关按钮,电源指示灯灭,打孔机停止工作。
3.2将手动调速电位器,逆时针旋转到不动为止。
3.3对工作台面进行清洁保养。
编制:审核:审批:
日期:。
穿孔机作业指导书

穿孔机作业指导书引言概述:穿孔机是一种常用的机械设备,用于在材料表面制作孔洞。
它在许多行业中都有广泛的应用,如金属加工、木工、纺织等。
为了正确、安全地操作穿孔机,本指导书将详细介绍穿孔机的操作步骤和注意事项。
正文内容:1. 穿孔机的基本操作1.1 准备工作- 确保穿孔机处于稳定的工作台上,避免机器晃动。
- 检查穿孔机的电源线是否连接稳固,电源是否正常。
- 检查刀具是否安装正确,刀具是否磨损或者损坏。
1.2 开机操作- 打开穿孔机的电源开关,并确保电源指示灯亮起。
- 调整穿孔机的工作速度和深度,根据材料的硬度和厚度进行合适的设置。
- 按下启动按钮,穿孔机开始工作。
1.3 操作注意事项- 在操作穿孔机时,应保持双手稳定,避免手部接近刀具。
- 注意刀具的运转方向,避免与材料相反方向运动,以防刀具卡住或者造成材料损坏。
- 在操作过程中,要保持专注,避免分心或者疲劳,以免发生意外。
2. 穿孔机的维护保养2.1 清洁工作- 在使用穿孔机后,应及时清理切屑和灰尘,以保持机器的正常运转。
- 使用软布擦拭机器表面,避免使用有腐蚀性的清洁剂。
2.2 润滑工作- 定期检查穿孔机的润滑情况,确保各润滑点的油脂充足。
- 使用适当的润滑油进行润滑,避免使用过多或者过少的润滑剂。
2.3 零部件维护- 定期检查刀具的磨损情况,及时更换损坏的刀具。
- 检查机器的传动部件是否松动,如有松动现象应及时紧固。
3. 穿孔机的安全操作3.1 穿孔机的防护装置- 确保穿孔机配备了必要的安全防护装置,如安全开关、防护罩等。
- 在操作穿孔机时,要保持防护罩完好,避免将手或者其他物体伸入机器内部。
3.2 人员安全- 操作穿孔机的人员应穿戴好安全装备,如安全帽、护目镜和防护手套。
- 不得将手部或者其他身体部位挨近刀具,以免发生伤害。
3.3 紧急情况处理- 在紧急情况下,应即将住手穿孔机的运转,并切断电源。
- 如发生故障或者异常情况,应及时通知维修人员进行处理。
钢管有限责任公司穿孔机操作工安全操作规程
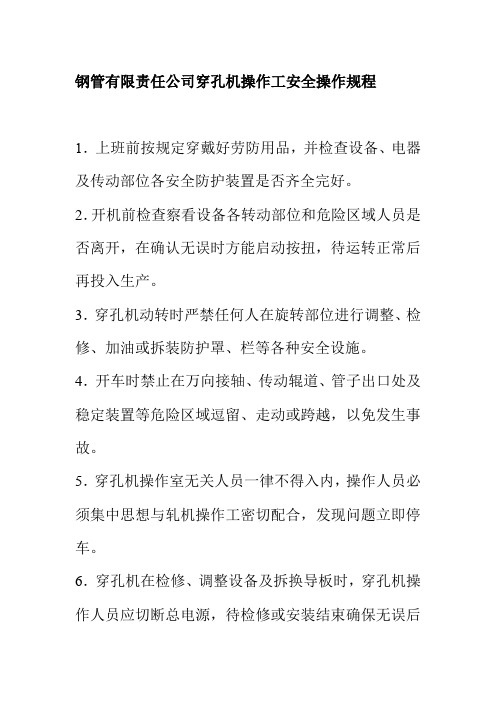
钢管有限责任公司穿孔机操作工安全操作规程
1.上班前按规定穿戴好劳防用品,并检查设备、电器及传动部位各安全防护装置是否齐全完好。
2.开机前检查察看设备各转动部位和危险区域人员是否离开,在确认无误时方能启动按扭,待运转正常后再投入生产。
3.穿孔机动转时严禁任何人在旋转部位进行调整、检修、加油或拆装防护罩、栏等各种安全设施。
4.开车时禁止在万向接轴、传动辊道、管子出口处及稳定装置等危险区域逗留、走动或跨越,以免发生事故。
5.穿孔机操作室无关人员一律不得入内,操作人员必须集中思想与轧机操作工密切配合,发现问题立即停车。
6.穿孔机在检修、调整设备及拆换导板时,穿孔机操作人员应切断总电源,待检修或安装结束确保无误后
再启动总电源。
7.主电机严禁带负荷启动,启动后待主电机进入运行状态后方可进行穿孔。
8.经常检查吊运工具(钢丝绳、链条、钩子)等,发现隐患应及时调换。
- 1、下载文档前请自行甄别文档内容的完整性,平台不提供额外的编辑、内容补充、找答案等附加服务。
- 2、"仅部分预览"的文档,不可在线预览部分如存在完整性等问题,可反馈申请退款(可完整预览的文档不适用该条件!)。
- 3、如文档侵犯您的权益,请联系客服反馈,我们会尽快为您处理(人工客服工作时间:9:00-18:30)。
3、穿孔机区技术操作规程3.1、穿孔机设备及工具概述3.1.1、锥形辊穿孔机性能机架结构机架上有2个上下布置的轧辊,两旁导板导向。
轧辊材质50 Mn60 Mn轧辊直径Φ1300~Φ1150 mm辊身长度 1000mm安装方式上下安装随轧辊装配及转鼓同时拆装喂入角8°~15°无级可调辗轧角15°固定额定辊速64 r/min轧辊转矩每个轧辊最大转矩为1100 kN.m 输出转速范围42~92 r/min输出速度范围600~1 150 mm/s生产率 max 1.5 pcs/min主传动主电机功率 1800KW ×2×2 DC转速 375/900 r/min过载系数 2主减速机速比 5.7893.1.2、工具概述3.1.2.1、穿孔机轧辊喉径处轧辊直径最大Ф1300 mm重车量 75mm轧辊辊身长度 1000mm入口锥角度 2.7°入口锥长度 425 mm出口锥角度 3.7°出口锥长度 575 mm轧辊材质50 Mn、60 Mn成分 C: 0.47~0.55Si: 0.15~0.40Mn: 0.60~0.90 P: Max 0.035S: Max 0.035硬度 220~250 HBW3.1.2.2、顶杆:规格:外径Φ121~Φ299 mm壁厚25~34 mm长度 17295mm(从法兰面至顶头鼻部)材质34CrMo4V、 35CrMnSiA或Cr5Mo冷却方式内水冷为主,外水冷为辅与接套、顶头的安装方式固定式,人工拆装3.1.2.3、顶头接套:规格外径Φ121~Φ299 mm;壁厚25~34 mm连接段长度 254~324mm材质34CrNi3Mo与顶杆、顶头的安装方式:固定式,人工拆装。
3.1.2.4、顶头:规格Ф200系列8种Ф250系列21种Ф300系列8种Ф330系列15种Ф350系列7种直径Φ116~Φ333mm长度370~650 mm材质成分C: 0.15~0.25Mn: 0.75~1.00Si: 0.50~0.60Ni: 2.5~3.2Cr: 1.00~1.60Mo: Max 0.50P: Max 0.035S: Max 0.035硬度 250~350 HBW冷却方式空心,内水冷为主,外水冷为辅与顶杆、接套的安装方式固定式,人工拆装3.1.2.5、导板:规格Ф200、Ф250、Ф300、Ф330、Ф350系列5种导板材质高碳高铬铸钢成分 C: 1.4~1.50Mn: 1.0~1.10Si: 0.50~0.70Ni: 8.00~10.00Cr: 25.00~27.00Mo: 0.50~0.70P: Max 0.04S: Max 0.04硬度 220~250 HBW3.1.2.6、入口导套规格Ф200、Ф250、Ф300、Ф350、Ф390系列5种导套材质203.1.2.7、脱管衬套规格1种Ф150(随机)导套材质45硬度 241~269 HBW表面淬火硬度HRC45~55深度 2 mm3.2、穿孔机正常工作的前提条件——轧辊形状、尺寸要符合要求,调整(辊距、导板距、咬入角等)要灵活,显示值与实际值要相符。
——顶头形状、尺寸、表面质量要符合要求,伸出量调整要灵活,显示值与实际值要相符。
——轧辊转速显示值与实际要求要相符。
——管坯端面切斜度要符合要求,如果进行定心,定心孔要正(否则要调整高度)。
——入口导套必须紧固。
——三辊导向装置的毛管位开口度调整要正确、准确。
——出口台升降辊道的运输位开口度(即高度)调整要正确、准确。
——脱管挡板符合毛管及顶杆的要求。
——推坯机运行灵活,停位准确,速度满足要求。
——顶杆止推小车运行灵活,停位准确,速度满足要求。
——管坯实际尺寸应符合工艺要求。
——管坯的加热温度、开轧温度要符合工艺要求。
——液压系统工作正常,。
液压管路无泄漏现象。
——冷却水畅通。
——干油润滑系统及稀油润滑系统润滑充分,管路无泄漏现象。
——电气控制可靠,电气元器件工作灵敏。
3.3、设备的试运转在试运转前要检查:——为保证管坯、顶杆(顶头)在穿孔机主机上的正常轧制及辅机上的正常运输。
检查电气控制系统是否正常。
——检查推坯杆是否对准中心。
——入口导槽高度与管坯规格是否相符合,若不符合,要调整导槽的高度,保证导槽上的管坯轴线与轧制中心线对准。
——推坯机是否处于初始位置。
——所有防护、切断及类似装置是否正确就位。
——检查所有润滑部位是否正常,冷却水是否打开。
——电气检测元件信号的灵敏性。
——穿孔机各动作部位都空负荷动作3~5次,检查是否正常。
——开车前操作工按二次铃,当主电室回三次铃后才能启动主马达,并检查主电机转速是否合符工艺要求。
3.4、管坯及毛管的尺寸范围管坯直径Φ200、Φ250、Φ300、Φ330、Φ350 mm(预留)管坯长度 1.5~4.5m毛管规格外径Φ225~Φ379 mm壁厚 19~69mm长度最大10.0m穿孔工艺方式等径或扩径穿孔3.5、设备的调整操作及注意事项3.5.1、穿孔机进口台当坯料通过过渡台架进入穿孔机进口台的托槽,推坯机以300mm/s的速度将管坯推入轧辊,待咬入100~120 mm后,进口台推坯机返回到初始位置,其退回速度为700 mm/s。
托槽的中心线可以根据管坯规格调整,电机驱动,通过锥齿轮减速机及两根万向节轴,驱动两台蜗轮丝杠升降机,使托槽绕转轴摆动,实现托槽中心线标高的调整,调整完毕后,托槽锁紧,调整位置由指针标牌显示。
托槽内管坯的规格与蜗轮丝杠升降机升降行程的对应关系参见表3-1。
管坯规格与升降机行程的对应关系表3-1 管坯直径Φ200 Φ250 Φ300 Φ330 Φ350升降机行程70.5 60.5 50 43.5 39.5 注:升降机的原始位置行程为0。
严禁将降温的黑钢坯推入穿孔机进行穿孔,一般碳素结构钢的穿孔温度1225~1250℃,合金结构钢的穿孔温度大于1100℃。
3.5.2、穿孔机主机3.5.2.1、轧辊的校准调整目的:以轧制中心线为基准调整两个轧辊轴线,由辊径和测量工具厚度尺寸所决定的轧辊距离(指高点距离)的理论值要输入操作室显示系统。
调整分初调和精调两个阶段,初调主要完成轧辊的快速运动,减少操作时间,在初调基础上进行的精调主要保证轧辊的精确定位。
初调和精调的过程和结果可以在操作室显示器上显示。
轧辊的调整采用专用调整工具完成,调整工具的结构参见附图,它主要包括一套对中架、接杆(1)、接杆(2)、接套,及三个对中头,接杆(1)为带测量平面(方形块)的焊接件,接杆(2)为焊接件,接杆(1)与接杆(2)通过十字轴连接,可以在任意方向转动,根据需要用接套将两个接杆连接为刚性杆或万向接轴,对中头(1)与对中头(3)配合用于调整轧辊的位置,对中头(2)与对中头(3)配合用于找正轧制线。
安装有对中头(1)的对中架固定到机架的专用安装孔上,对中头(1)的顶尖就在轧制线上,将接杆(2)固定在出口台一段三辊导向装置的导向辊所围成的圆形孔型中,自动定心。
接杆(1)中部的测量平面(下表面)靠在下轧辊上,对中头(3)安装于接杆(1)的自由端,与对中头(1)相对。
调正下轧辊的高度,直到对中头(3)的顶尖与对中头(1)的顶尖在同一个水平高度为止。
上轧辊下降,直到辊面接触到测量平面上表面为止,由于上下辊径相同,所以它们到中心线是等距的,初调即完毕。
轧制时再进行轧辊高点的精调。
3.5.2.2、导板的初调导板初调的目的在于调整导板到轧制中心线间的距离(即导板距)。
采用专用的调整用导板完成。
与轧辊调整原理类似,导板的初调也是通过调整工具实现的,差别只是上下调整改为左右调整。
调整工具靠在已调正好的下辊上,上辊抬起,导板向轧制中心线调整,其中一个导板直到与接杆(1)的测量平面(侧面)接触,并使安装对中头(3)的接杆(1)沿水平面摆动,直到对中头(3)的顶尖与对中头(1)的顶尖正对为止。
类似地调整好另一个导板,这样两个导板到轧制中心线就等距了。
两导板距离的读数通过数显装置可以显示在操作室的显示器上。
3.5.2.3、轧辊对轧制线的调整。
当压下(上)电机完成调整动作后,上、下轧辊可同步或分别地相对轧制线进行调整。
通过数显系统,辊距将显示在控制台上,通过进位选择器将辊径和所需要的辊缝值输入终端,在取出内存之后,工作辊就可自动调整,改变内存可修正辊缝大小。
轧辊重车后,必须重新校正轧辊辊距。
工作辊重新初调后的数据可按上述步骤(3.5.2.1)分别地进行检查。
换辊或出故障时,选择器可以自动进入“换辊”或“疑难”状态。
3.5.2.4、导板对轧制线的水平调整导板水平调整由侧压进电机完成,左右两侧导板可根据调整的状态同时或分别进行调整。
通过数显系统,在操作室控制台上显示导板的间距。
通过十进位选择器将导板厚度和理想间距输入终端且取出内存后,导板将自动调整,改变内存可修正导板间距,可以按上述步骤(3.5.2.2)检查导板重新初调后的数据。
3.5.2.5、工作辊送进角的调整轧辊送进角可通过控制台用按钮调整。
数显系统将显示所调轧辊的倾斜角即送进角(必须保证上、下轧辊的送进角相同)。
根据穿孔以后毛管的D/S值选择轧辊送进角及转速,一般可参考以下原则确定:参见表3-2:送进角选择参考原则表3-2序号D/S值送进角(°)轧辊转速(r/min)1 <6 8~9 100~1102 6.1~8.0 8~8.5 120~1303 8.1~9.5 7~8 110~1204 9.6~10.5 6~7 90~100轧辊送进角的调整必须停机进行,两个轧辊所显示的送进角应一致。
调整完成以后,必须对数显参数进行人工校验。
3.5.3、穿孔机出口台3.5.3.1、顶杆(顶头)位置的调整首先,根据图纸尺寸,穿孔机中心线到顶杆止推小车与顶杆法兰结合面的距离为17145mm,选择合适的基准,确定顶杆止推小车的零位,零位确定后,顶杆止推小车向穿孔机方向的运行行程为175mm,取负值,顶杆止推小车沿轧制线方向的运行行程为175mm,取正值。
其次,根据轧制工艺表的序号选择不同热轧成品管穿孔时所需的顶头位置数据(即顶头前伸量,它是变动的)。
测量方法,将顶杆及顶头送入变形区内,出口台二段的闭锁装置动作,将顶杆锁紧定位于零位,调整闭锁装置向穿孔机或沿轧制线方向运行,用直尺直接测量运行行程,满足轧制表中顶头前伸量的要求,即为顶杆所调位置。
顶头位置也可通过数显装置显示于操作室的显示器上。
更换顶杆时,应对新换上的顶杆旋转检查,发现明显弯曲者禁止使用。
顶杆弯曲度≤1mm/m。
使用顶头时要经常检查顶头表面情况,不准粘有金属或严重磨损,如发现顶头有影响毛管质量的缺陷应及时更换。
3.5.3.2、三辊导向装置的操作按轧制工艺表要求,调正好辊距、导板距、顶头伸出量后将顶杆(带顶头)开到轧机中去,因穿孔前穿孔机是以一恒定的轧制线工作,六组三辊导向装置对毛管和顶杆进行导向作用。