汽车座椅强度性能试验台设计
汽车座椅颠簸蠕动试验台参数解析
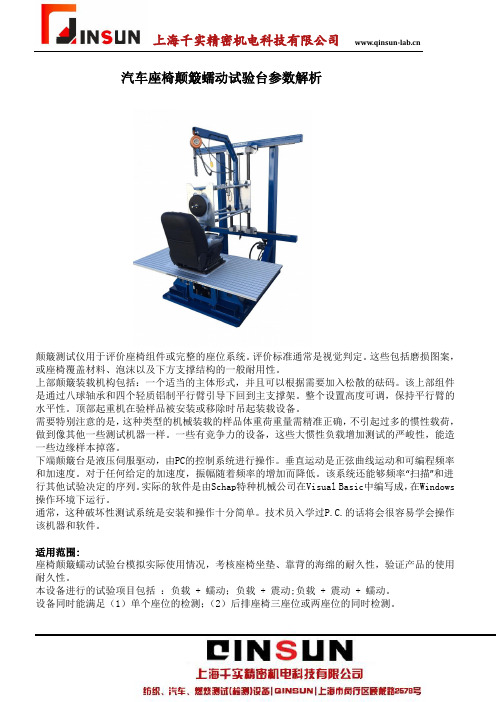
汽车座椅颠簸蠕动试验台参数解析颠簸测试仪用于评价座椅组件或完整的座位系统。
评价标准通常是视觉判定。
这些包括磨损图案,或座椅覆盖材料、泡沫以及下方支撑结构的一般耐用性。
上部颠簸装载机构包括:一个适当的主体形式,并且可以根据需要加入松散的砝码。
该上部组件是通过八球轴承和四个轻质铝制平行臂引导下回到主支撑架。
整个设置高度可调,保持平行臂的水平性。
顶部起重机在验样品被安装或移除时吊起装载设备。
需要特别注意的是,这种类型的机械装载的样品体重荷重量需精准正确,不引起过多的惯性载荷,做到像其他一些测试机器一样。
一些有竞争力的设备,这些大惯性负载增加测试的严峻性,能造一些边缘样本掉落。
下端颠簸台是液压伺服驱动,由PC的控制系统进行操作。
垂直运动是正弦曲线运动和可编程频率和加速度。
对于任何给定的加速度,振幅随着频率的增加而降低。
该系统还能够频率“扫描”和进行其他试验决定的序列。
实际的软件是由Schap特种机械公司在Visual Basic中编写成,在Windows 操作环境下运行。
通常,这种破坏性测试系统是安装和操作十分简单。
技术员入学过P.C.的话将会很容易学会操作该机器和软件。
适用范围:座椅颠簸蠕动试验台模拟实际使用情况,考核座椅坐垫、靠背的海绵的耐久性,验证产品的使用耐久性。
本设备进行的试验项目包括:负载 + 蠕动;负载 + 震动;负载 + 震动 + 蠕动。
设备同时能满足(1)单个座位的检测;(2)后排座椅三座位或两座位的同时检测。
颠簸台颠簸台为站式独立装置,可单独租赁或与液压动力组和上部框架租用一起租赁。
颠簸台可以产生环状(正弦波)输出,频率为0.1赫兹到50赫兹,0至50mm的振幅。
颠簸台由P.C.电脑控制,带有一个转动控制车,并且具有用于座位(或任何其他项目需要环状或振动测试)颠簸测试以及共振和阻尼测试的软件。
该颠簸台可在位移模式进行台面位移或上部(鞍)的位移操作。
颠簸台也可以在加速模式的下操作,颠簸的振幅变化不同,以保持颠簸台或上部(鞍)的一个恒定的加速度。
汽车座椅及安全带固定点强度电液伺服加载试验台的研制
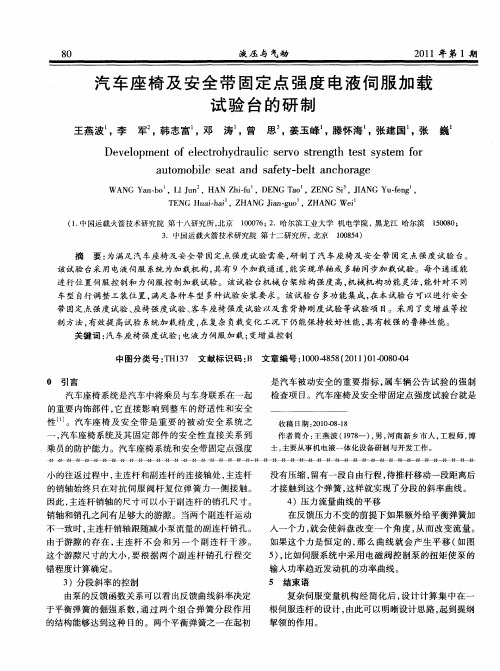
带 固定 点强度试 验 、 椅 强度试验 、 车座椅 强度试验 以及 靠 背静 刚度 试验 等试验 项 目。采 用 了变增益等控 座 客 制方法, 有效提 高试验 系统 加载精 度 , 复杂 负载 变化 工况下仍 能保持 较好 性能 , 在 具有较 强 的鲁棒性 能 。
关键 词 : 车座椅 强度试 验 ; 汽 电液 力伺服 加 载 ; 变增益控 制
的销轴始 终 只在对 抗伺 服 阀 杆 复位 弹 簧力 一 侧 接触 。
因此 , 主连 杆销轴 的尺寸可 以小 于副连 杆 的销 孔尺寸 。
才接 触到这 个 弹簧 , 样就 实现 了分段 的斜率 曲线 。 这
4 )压 力流量 曲线 的平移
销 轴和销 孔之 间有足 够大 的游 隙。 当两个 副 连杆运 动
(. 1 中国运载火箭技术研究院 第十八研究所 , 北京
10 7 ; .哈尔滨工业大学 机 电学 院,黑龙 江 哈尔滨 00 6 2 10 5 ) 0 84
10 8 5 00;
3 .中国运载火箭技术研究院 第十二研究所 , 北京
摘
要 : 满足 汽 车座椅及 安全 带 固定点 强度 试验 需要 , 制 了汽 车座 椅及 安 全 带 固定 点 强度 试验 台。 为 研
于平衡弹簧的倔强系数 , 通过两个组合弹簧分段作用 的结 构能 够达 到这种 目的 。两个平 衡 弹簧之一 在起初
21 0 1年 第 1期
液 压 与 气 动
统 以提高 能源 总效率 。
8 1
用 于评价汽 车座椅 和安 全带 固定点 是否 达到各 种 国内 外标 准强度 要求 的专 门试验 台 。
作者 简介 : 王燕 波 ( 9 8 ) 男 , 17 一 , 河南 新 乡市人 , 程师 , 工 博 士, 主要从事机 电液一体化设备研制与开发工作。
汽车座椅系统主要性能试验及设备要求
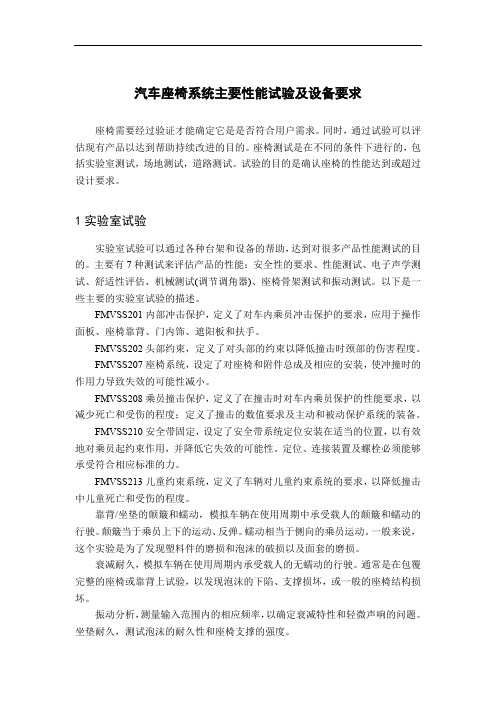
汽车座椅系统主要性能试验及设备要求座椅需要经过验证才能确定它是是否符合用户需求。
同时,通过试验可以评估现有产品以达到帮助持续改进的目的。
座椅测试是在不同的条件下进行的,包括实验室测试,场地测试,道路测试。
试验的目的是确认座椅的性能达到或超过设计要求。
1实验室试验实验室试验可以通过各种台架和设备的帮助,达到对很多产品性能测试的目的。
主要有7种测试来评估产品的性能:安全性的要求、性能测试、电子声学测试、舒适性评估、机械测试(调节调角器)、座椅骨架测试和振动测试。
以下是一些主要的实验室试验的描述。
FMVSS201内部冲击保护,定义了对车内乘员冲击保护的要求,应用于操作面板、座椅靠背、门内饰、遮阳板和扶手。
FMVSS202头部约束,定义了对头部的约束以降低撞击时颈部的伤害程度。
FMVSS207座椅系统,设定了对座椅和附件总成及相应的安装,使冲撞时的作用力导致失效的可能性减小。
FMVSS208乘员撞击保护,定义了在撞击时对车内乘员保护的性能要求,以减少死亡和受伤的程度;定义了撞击的数值要求及主动和被动保护系统的装备。
FMVSS210安全带固定,设定了安全带系统定位安装在适当的位置,以有效地对乘员起约束作用,并降低它失效的可能性。
定位、连接装置及螺栓必须能够承受符合相应标准的力。
FMVSS213儿童约束系统,定义了车辆对儿童约束系统的要求,以降低撞击中儿童死亡和受伤的程度。
靠背/坐垫的颠簸和蠕动,模拟车辆在使用周期中承受载人的颠簸和蠕动的行驶。
颠簸当于乘员上下的运动、反弹。
蠕动相当于侧向的乘员运动。
一般来说,这个实验是为了发现塑料件的磨损和泡沫的破损以及面套的磨损。
衰减耐久,模拟车辆在使用周期内承受载人的无蠕动的行驶。
通常是在包覆完整的座椅或靠背上试验,以发现泡沫的下陷、支撑损坏,或一般的座椅结构损坏。
振动分析,测量输入范围内的相应频率,以确定衰减特性和轻微声响的问题。
坐垫耐久,测试泡沫的耐久性和座椅支撑的强度。
《汽车座椅、座椅固定装置及枕强度要求和试验方法
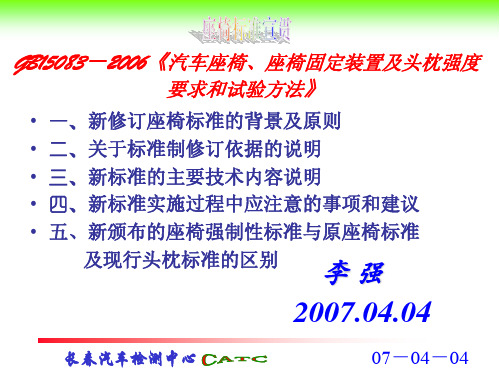
长春汽车检测中心
07-固定强度 a. 安装在车底板上的座椅总成,通过座椅质心,分别承受水平 向前和向后各施加的相当于座椅总成重量20倍的负荷,座椅总成和 车身本体不得分离。对于可调试座椅,其调节装置在试验中应能使 座椅保持原调节位置,但试验后调节装置允许失去调节功能。在座 椅背面有防止座椅后退的结构件时,对座椅可进行向前加载。 b. 对于向前座椅,当汽车安全带安装固定点在座椅上时,要求 在对座椅施加20倍座椅总成重量负荷的同时,还要按国GB14167《汽 车安全带安装固定点》中的有关规定在加13500±200N的负荷, 因为 在这种情况下安全带固定点受到的负荷也同时加到座椅固定点上,此 时对座椅的要求仍与a中规定一致。 c. 对铰链式可翻转座椅,通过座椅质心,沿水平方向只向前施 加相当于座椅总成重量20倍的负荷。座椅总成与车身本体不得分离。
07-04-04
• 编制原则: • 1、采用国际先进的汽车座椅系统技术法 规和安全标准; • 2、标准的编写按照GB/T1.1-2002《标 准化工作导则 第一部分:标准的结构和 编写规则》; • 3、在深入调研的基础上,吸收和听取汽 车主机厂和座椅生产企业等有关座椅的 科研、设计、制造、使用和管理等各相 关部门的意见。
长春汽车检测中心
07-04-04
长春汽车检测中心
07-04-04
长春汽车检测中心
07-04-04
3)在技术要求方面: a. 一般技术要求: 首先标准中与原标准修订前一致,强调了座椅调节 装置和移位装置方面的要求,但比原标准规定的更具体 和更有操作性。对M1类和M2、M3和N类汽车座椅分别进 行技术要求方面的详细说明。并对座椅背面部件按区域 规定了具体要求;对不适用于一些特殊座椅和部件的情 况作了具体解释说明。即“不适用于:表面凸起部分的 突出高度小于3.2mm,且突出高度不超过突出部分宽度一 半的区域;最后排座椅和背对背安装的座椅;位于通过 该排座椅最低R点的水平平面以下的座椅靠背部分(如果 每排座椅高低不同,则从后排座椅起,该水平面应通过 前排座椅的“R”点,在垂直方向或高或低形成一个台阶) 以及“柔性金属网”部件”。 长春汽车检测中心
座椅试验机说明书

2 工作原理该设备自动化程度高,适应范围广。
该设备可以对冲击头的水平和垂直位置进行调整,从而可以实现对座椅不同位置的冲击试验。
再者,冲击头可以绕垂直轴线旋转,适应对座椅的凸出部位进行试验。
采用进口高灵敏度的加速度传感器,使得测量精度大幅度提高。
配置手操控制器,方便操作者在不同位置调整设备。
配置易于使用的座椅固定夹具,可方便改变座椅的固定位置,极大提高试验效率。
提供一套座椅夹具,分别适应单人位和三人位的座椅。
本试验台采用了先进的微型电机、伺服电机及其伺服控制器,在微机控制下可以按照各种技术标准和法规规定的速度值自动完成对汽车座椅吸能性性能的检验和评价。
测试开始前首先要进行设备调整,将冲击头举升到要冲击的起始位置。
在发出释放命令后,冲击头将按照自由落体进行下落,在冲击过程中,计算机自动记录冲击时的加速度,速度和负荷等参数。
通过工业控制计算机对试验数据自动采集、存储、处理,自动绘制、打印加速度试验曲线。
自动以word格式生成试验报告,并可以简便的由用户进行自定义报告内容,试验报告可以显示座椅试验过程的曲线图。
操作软件具有多种条件保护,充分防止误操作;手动控制单元通过无线摇控方式实现,操作者可在遥控器上方便的进行机器的调整。
座椅不同角度位置试验中方向的改变通过微型旋转电机来实现,该电机可以在垂直轴线上±180度旋转.座椅夹具可携带座椅水平面内进行0-45º任意旋转。
3 技术参数1、试验台可在垂直和水平两个方向上调整冲击头的位置,调整范围为垂直方向在200~1200mm,水平方向在0~1000mm。
2、选用加速度计测量头型加速度,加速度测量范围±350g;精度±0.3%FS;分辨率±0.1%FS。
3、冲击速度:0-35km/h。
测量精度±0.2Km/h。
4、冲击速度重复性±0.05km/h以内。
5、具有反弹加速度80g以上超3毫秒的判定功能。
GB 15083-2006 汽车座椅、座椅固定装置及头枕强度要求和试验方法
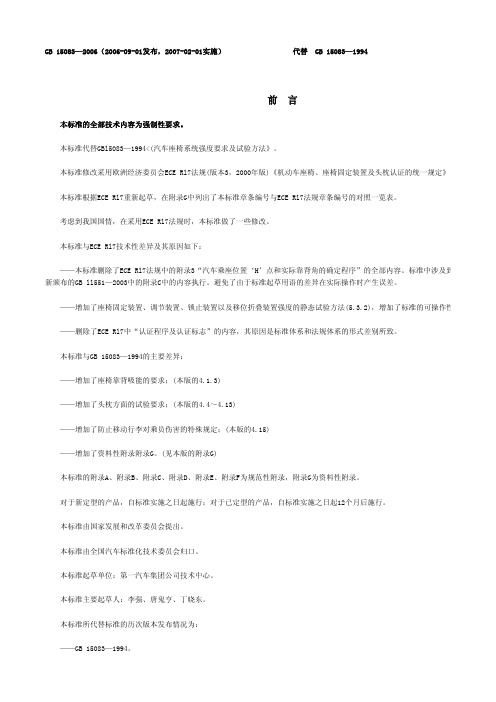
GB 15083—2006(2006-09-01发布,2007-02-01实施) 代替 GB 15083—1994前 言本标准的全部技术内容为强制性要求。
本标准代替GBl5083—1994<(汽车座椅系统强度要求及试验方法》。
本标准修改采用欧洲经济委员会ECE Rl7法规(版本3,2000年版)《机动车座椅、座椅固定装置及头枕认证的统一规定》本标准根据ECE Rl7重新起草,在附录G中列出了本标准章条编号与ECE Rl7法规章条编号的对照一览表。
考虑到我国国情,在采用ECE Rl7法规时,本标准做了一些修改。
本标准与ECE Rl7技术性差异及其原因如下:——本标准删除了ECE Rl7法规中的附录3“汽车乘座位置‘H’点和实际靠背角的确定程序”的全部内容。
标准中涉及到新颁布的GB ll551—2003中的附录C中的内容执行。
避免了由于标准起草用语的差异在实际操作时产生误差。
——增加了座椅固定装置、调节装置、锁止装置以及移位折叠装置强度的静态试验方法(5.3.2),增加了标准的可操作性——删除了ECE Rl7中“认证程序及认证标志”的内容,其原因是标准体系和法规体系的形式差别所致。
本标准与GB 15083—1994的主要差异:——增加了座椅靠背吸能的要求;(本版的4.1.3)——增加了头枕方面的试验要求;(本版的4.4~4.13)——增加了防止移动行李对乘员伤害的特殊规定;(本版的4.15)——增加了资料性附录附录G。
(见本版的附录G)本标准的附录A、附录B、附录C、附录D、附录E、附录F为规范性附录,附录G为资料性附录。
对于新定型的产品,自标准实施之日起施行;对于已定型的产品,自标准实施之日起12个月后施行。
本标准由国家发展和改革委员会提出。
本标准由全国汽车标准化技术委员会归口。
本标准起草单位:第一汽车集团公司技术中心。
本标准主要起草人:李强、唐鬼亨、丁晓东。
本标准所代替标准的历次版本发布情况为:——GB 15083—1994。
汽车座椅骨架强度分析及结构优化
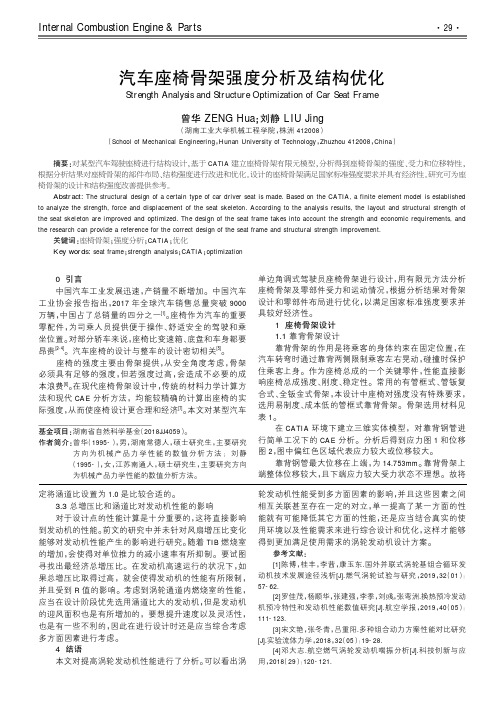
Internal Combustion Engine &Parts0引言中国汽车工业发展迅速,产销量不断增加。
中国汽车工业协会报告指出,2017年全球汽车销售总量突破9000万辆,中国占了总销量的四分之一[1]。
座椅作为汽车的重要零配件,为司乘人员提供便于操作、舒适安全的驾驶和乘坐位置。
对部分轿车来说,座椅比变速箱、底盘和车身都要昂贵[2-4]。
汽车座椅的设计与整车的设计密切相关[5]。
座椅的强度主要由骨架提供,从安全角度考虑,骨架必须具有足够的强度,但若强度过高,会造成不必要的成本浪费[6]。
在现代座椅骨架设计中,传统的材料力学计算方法和现代CAE 分析方法,均能较精确的计算出座椅的实际强度,从而使座椅设计更合理和经济[7]。
本文对某型汽车单边角调式驾驶员座椅骨架进行设计,用有限元方法分析座椅骨架及零部件受力和运动情况,根据分析结果对骨架设计和零部件布局进行优化,以满足国家标准强度要求并具较好经济性。
1座椅骨架设计1.1靠背骨架设计靠背骨架的作用是将乘客的身体约束在固定位置,在汽车转弯时通过靠背两侧限制乘客左右晃动,碰撞时保护住乘客上身。
作为座椅总成的一个关键零件,性能直接影响座椅总成强度、刚度、稳定性。
常用的有管框式、管钣复合式、全钣金式骨架,本设计中座椅对强度没有特殊要求,选用易制度、成本低的管框式靠背骨架。
骨架选用材料见表1。
在CATIA 环境下建立三维实体模型,对靠背钢管进行简单工况下的CAE 分析。
分析后得到应力图1和位移图2,图中偏红色区域代表应力较大或位移较大。
靠背钢管最大位移在上端,为14.753mm 。
靠背骨架上端整体位移较大,且下端应力较大受力状态不理想。
故将______________________________基金项目:湖南省自然科学基金(2018JJ4059)。
作者简介:曾华(1995-),男,湖南常德人,硕士研究生,主要研究方向为机械产品力学性能的数值分析方法;刘静(1995-),女,江苏南通人,硕士研究生,主要研究方向为机械产品力学性能的数值分析方法。
座椅骨架强度分析及零部件设计优化

座椅骨架强度分析及零部件设计优化引言汽车座椅属于汽车的基本装置,是汽车的重要安全部件,其主要作用是为乘员提供支撑、确定乘员位置,提供乘员驾乘舒适性以及保护乘员不受伤害。
随着汽车行业竞争日趋激烈,如何在保证安全等级不降的前提下,对产品结构优化,进行成本控制是当前很多主机厂研究的重要课题之一。
座椅的安全性主要取决于骨架强度;座椅骨架是由靠背骨架和坐垫骨架及核心件三部分组成,并由安装支脚通过螺栓固定在车身横梁上;其中座椅的核心件一般包括角调器总成、高调器总成和滑轨总成等,这些核心件一般是由专业厂家设计制造,产品质量一致性和通用性较高。
座椅靠背骨架总成是一般是由钢管框架、左右角调器总成(角调上下连接板和角调器核心件)、侧面支撑钢丝以及靠背弹簧等组成,如图1所示。
中高端车型一般采用冲压件框架替代钢管框架结构。
当前市场上A0级以下的车型成本压力巨大,经市场调查62款A0级以下车型低配前座椅骨架,其中单边角调骨架43款,约占70%;可见单边角调座椅骨架是A0级以下车型主流配置。
图1本文以某单边角调式座椅靠背骨架为例,用有限元方法分析座椅骨架及零部件受力情况,并与试验结果对比;参照有限元分析与试验结果对比,对零部件进行设计优化,以满足设计要求。
1、有限元分析工况与试验方法差异对比1.1 金属材料耐久性与静强度关系就钢材而言,当其承受正、负相等的交变应力时,其疲劳强度(材料承受的最大应力值)随材料可以承受的交变次数的增加而减小,如图2所示;当可以承受的交变次数达到107次以上时,疲劳强度就变成了一个固定值,称其为持久极限。
持久极限一般只有静强度的40%~50%,当应力低于持久极限时,材料具有无限寿命。
图2 金属材料S-N曲线图因此可以通过FEA,模拟静强度试验,考察骨架应力变化趋势是否与试验结果保持一致。
以此为依据,进而对结构进行优化,比对优化前后的分析结果,考量结构优化是否合理有效。
1.2 有限元分析工况与试验方法差异对比试验方法:将座椅按照设计位置固定在试验台架上,在座椅靠背顶端中间位置,沿垂直于假人躯干线方向,相对于“H”点施加指定的力矩,并加卸载循环指定次数。
汽车座椅头枕安全性能试验台架计算机检测系统的设计

参 数 。设计 的检 测 系统 基 本能 够满 足要 求 , 性能 可靠 稳定 。 关 键词 汽 车座 椅头 枕 安 全性能 试 验 台架 中图分 类号 T P 3 0 6 文献 标识 码 B 检 测 系统 设 计 文章 编号 1 4 0 2 1 0 - 6 6 3 4
2 0 1 4 年2 月1 日
E d u
性 能试 验 台架 汽 车座椅头枕 安全 计算机检测 系 统 的设计
包俊 群 田一 成 。
( 沈 阳金杯 江森 自 控 汽车 内饰 件有 限公 司 设备 动 力部 沈 阳 1 1 0 1 8 0 ) ( 辽 宁辽无 一 电子 科技 有 限公 司 沈阳 1 1 0 0 0 0 ) z
t h e r i g i d s p h e r e a n d d i s p l a c e me n t s e n s o r i s i n s t a l l e d o n t h e p i s t o n r o d f o r t h e t e s t r e q u i r e d p a r a me t e r s . Th e d e s i g n c a n n me t b a s i c a l l y t h e r e q u i r e me n t s o f t h e d e t e c t i o n s y s t e m o f t h e r e l i a b l e a n d s t e a d y p e r f o r ma n c e .
信 — 前 置 放 大 器 及低 通 滤 波器 - - I I 米 号 集
汽车座椅 座椅固定装置及头枕强度要求和试验方法
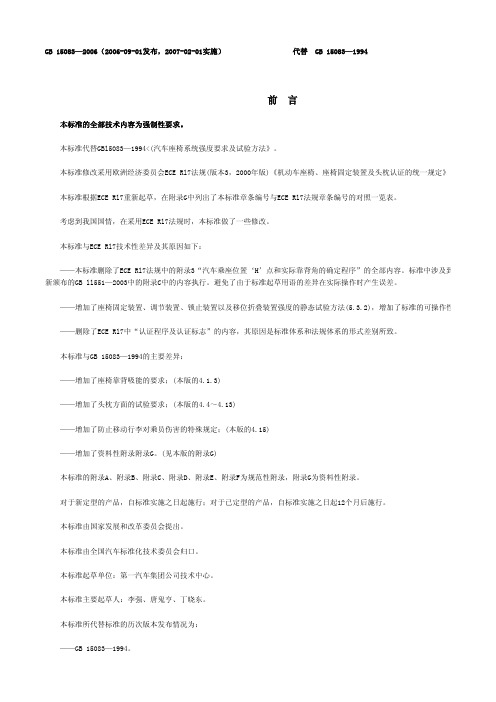
下列术语和定义适用于本标准。 3.1
车辆型式 vehicle type 是指在下列主要方面没有差异的车辆。 3.1.1 座椅的结构、形状、尺寸、材料以及质量,允许座椅蒙皮和颜色不同;允许质量差在批准座椅型式的座椅质量的5%范 3.1.2 座椅、座椅靠背及其组成部件的调节装置、位移装置及锁止装置的型式和尺寸; 3.1.3 座椅固定装置的型式和尺寸; 3.1.4 头枕的尺寸、构架、材料和衬垫,允许其蒙皮和颜色不同; 3.1.5 头枕附件的型式和尺寸,若头枕为分体式头枕还包括头枕连接部件的特性。 3.2 座椅 seat 供一个成年乘员乘坐且有完整装饰并与车辆结构为一体或分体的乘坐设施。它包括单独的座椅或长条座椅的一个座位。 3.3 长条座椅 bench seat
区域l内为2.5 mm; 区域2内为5.0 mm; 区域3内为3.2 mm; 区域的定义见5.8。 4.1.4.1 本规定不适用于: 4.1.4.1.1 表面凸起部分的突出高度小于3.2 mm,且突出高度不超过突出部分宽度一半的区域; 4.1.4.1.2 最后排座椅和背对背安装的座椅; 4.1.4.1.3 位于通过该排座椅最低R点的水平平面以下的座椅靠背部分(如果每排座椅高低不同,则 从后排座椅起,该水平面应通过前排座椅的“R”点,在垂直方向或高或低形成一个台阶); 4.1.4.1.4 诸如“柔性金属网”部件。 4.1.4.2 位于5.8.1.2规定的区域2内的表面,若满足本标准附录C规定的靠背吸能性试验,则允许其曲率半径小于5 mm,但不 表面应加衬垫以避免座椅与乘客头部直接接触。 4.1.4.3 位于上述区域内的部件,若表面材料邵尔(A)硬度低于50,则上述除对附录C规定的靠背吸能性试验要求之外的所有要 件。 4.1.5 在按5.2和5.3规定进行的试验过程中或试验后,座椅骨架、座椅固定装置、调节装置、移位折叠装置或其锁止装置均不 在碰撞过程中不会增加伤害程度的永久变形(包括断裂)且能承受规定载荷。 4.1.6 在进行5.3和附录F中F.2.1规定的试验过程中,锁紧装置不得松脱。 4.1.7 试验后,用于或有助于乘员通过的移位折叠装置应处于工作状态,且至少保证能解锁一次,并按需要使座椅或座椅的一 对于其他座椅移位折叠装置、调节装置和锁止装置,允许产生变形、断裂,但不允许失效,并保持在原位置。对于带有头 5.4.3.6试验过程中或试验后,如座椅或座椅靠背不出现断裂,则座椅靠背及其锁止装置满足5.2规定。否则,应进行5.2规定 椅靠背及其锁止装置的强度是否满足该规定要求。 对于座位个数多于头枕个数的座椅(长条座椅),也应进行5.2规定的试验。 4.2 M2、M3和N类汽车座椅的一般技术要求 4.2.1 座椅及长条座椅必须牢固地固定在汽车上。 4.2.2 可移动的座椅和长条座椅在其使用位置都应能自动锁紧。 4.2.3 可调式座椅靠背在调节范围内任意位置都应能锁止。 4.2.4 所有可前翻的座椅或可折叠的座椅靠背,在其使用过程中都应能自动锁止。 4.3 头枕的安装 4.3.1 M1类型汽车的头枕应安装在前排外侧座位上。装在用于其他类车辆和其他座位位置的头枕,其座椅也可以按照本标准进 4.3.2 M2类(总质量3500 kg以下)和N1类车辆的前排外侧座位应安装符合GB ll550的头枕。 4.4 装备或可以装备头枕座椅的特殊规定 4.4.1 头枕在任何使用位置上,都不应有任何可能对乘员造成伤害的凸起或尖棱。 4.4.2 位于5.8.1.1定义的区域1内的头枕,其前、后表面应满足下列吸能要求。 4.4.2.1 如果按照本标准附录C规定的方法进行试验,头型的减速度大于80 g的持续时间不应超过3 ms,并且试验过程中或试 的边棱出现。 4.4.3 位于5.8.1.2定义的区域2内的头枕,其前、后表面都应装有衬垫,以防乘员头部与骨架部分直接接触,并且满足适用于 的4.1.4的规定。 4.4.4 上述4.4.2和4.4.3规定不适用于最后排座椅头枕的后表面部分。 4.4.5 头枕在座椅或车身构件上的固定方式应保证头枕在试验过程中,由于头型的作用压力,其衬垫内或头枕与靠背连接处
《汽车座椅 座椅固定装置及枕强度要求和试验方法
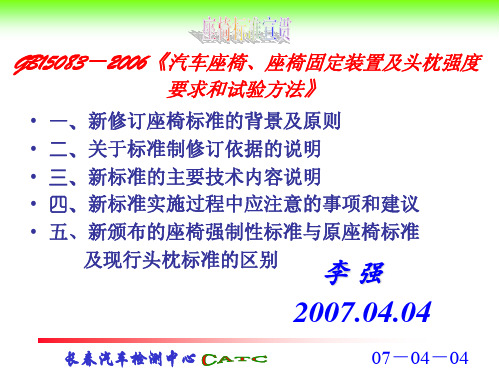
长春汽车检测中心
07-04-04
长春汽车检测中心
07-04-04
f)增加了对移动行李乘员防护的特殊规定。
增加该方面的要求,是针对目前国内对乘 用车多数均把后排座椅靠背和/或头枕构成行 李舱的通用设计来考虑的。因目前国内对于该 方面的试验基本上还没有开展,因此,对这部 分要求主要采用了ECE R17方面的相关规定。
长春汽车检测中心
07-04-04
• 3. 技术内容的说明:
• 1) 在规范性引用文件方面:共计引用了现行的国家或国际标准 7个。并明确说明凡是注日期的引用文件,其随后所有的修改单 (不包括勘误的内容)或修订版均不适用于本标准,凡是不注日 期的引用文件,其最新版本适用于本标准。
GB11550 汽车座椅头枕性能要求和试验方法
长春汽车检测中心
07-04-04
长春汽车检测中心
07-04-04
长春汽车检测中心
07-04-04
c) M1 类型汽车的头枕应安装在前排外侧座位上。装在用于其 它类车辆和其它座位位置的头枕,其座椅也可以按照本标准进行 认证。 M2 类(总质量3500Kg以下)和N1 类车辆的前排外侧座
位应安装符合GB11550的头枕。(见标准4.3) 在头枕高度方面比原标准增加了100mm的限值,并严格规定了在 750mm以下头枕不允许有使用位置。同时规定了几种特殊情况的 具体要求(见标准4. 5)。并且对安装高度可调的头枕规定了头
长春汽车检测中心
07-04-04
• 二、 关于标准制修订依据的说明:
• 从1995年开始,我国的汽车强制性标准逐步与国际接轨,并参照 欧洲ECE/EC汽车法规建立我国的汽车强制性标准体系。本标准 即为我国汽车强制性标准体系中关于汽车被动安全方面的重要标 准之一,其修订主要以欧洲ECE法规为依据并结合我国的国情对 其进行了适当的修改,其中技术内容修改采用欧洲经济委员会制 定的ECE R17法规(第三版修订4:2000年版)《机动车座椅、 座椅固定装置及头枕认证的统一规定》(英文版)。而对该法规 中有关座椅类型和车型认证方面的内容未与采用。并在附录G中 列出了本标准章条编号与ECE R17法规章条编号的对照一览表加 以说明。
汽车后排座椅试验法规及优化设计
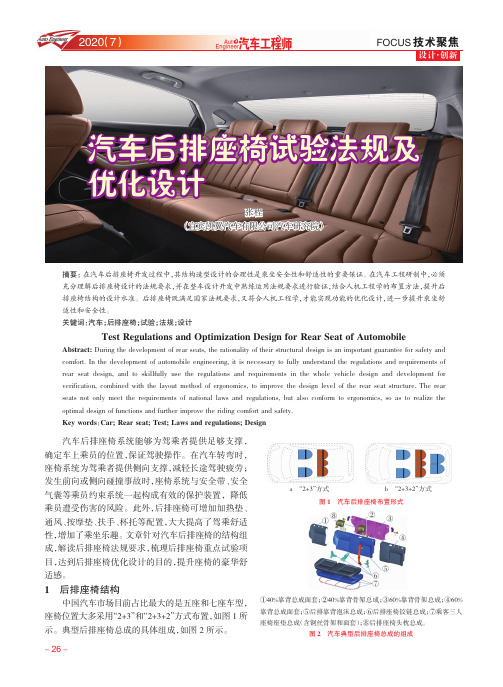
⑤ ⑥ ⑦
①40靠背总成面套;②40靠背骨架总成;③60靠背骨架总成;④60 靠背总成面套;⑤后排靠背泡沫总成;⑥后排座椅铰链总成;⑦乘客三人 座椅座垫总成(含钢丝骨架和面套);⑧后排座椅头枕总成。
图 C 汽车典型后排座椅总成的组成
- -
2第0270(期7)
技术聚焦
Design-Innovation 后排座椅靠背骨架由 40和 60靠背骨架两部分 持 50mm,纵向距离靠背 200mm。
组成。进行座椅冲击强度试验时,靠背骨架以实际机构 的连接方式固定在白车身上,白车身固定在台车上。座 椅靠背两侧的锁支架连接靠背锁,车身锁钩与靠背锁 处于锁止状态,以固定靠背上部,靠别通过螺栓固定在车身上。
后排座椅法规要求
后排座椅法规
汽车后排座椅系统能够为驾乘者提供足够支撑,
确定车上乘员的位置,保证驾驶操作。在汽车转弯时,
座椅系统为驾乘者提供侧向支撑,减轻长途驾驶疲劳;
发生前向或侧向碰撞事故时,座椅系统与安全带、安全 气囊等乘员约束系统一起构成有效的保护装置,降低 乘员遭受伤害的风险。此外,后排座椅可增加加热垫、 通风、按摩垫、扶手、杯托等配置,大大提高了驾乘舒适
图 行李箱冲击试验样块布置示意图
座椅需满足国家法规 GB7258《机动车运行安全技
试验过程中及试验后,如果后排座椅和靠背锁保
术条件》,座椅总成零部件级试验需满足 GB15083《汽 持原来位置且功能正常,则认为满足要求。在试验期
车座椅、座椅固定装置及头枕强度要求和试验方法》、 间,允许座椅靠背及其紧固件变形。
设计·创新
汽车后排座椅试验法规及 优化设计
张程 (宜宾凯翼汽车有限公司汽车研究院)
摘要:在汽车后排座椅开发过程中,其结构造型设计的合理性是乘坐安全性和舒适性的重要保证。在汽车工程研制中,必须
汽车座椅头枕强度试验台架设计

G B 1 1 5 5 0 — 2 0 0 9要求 , 为汽车座椅的设计提供详实可 力臂 , 为了实现精确控制 , 加载采取将 n 在背板上 靠的数 据和依据 ,确保 设计 的座 椅符合 国家法规 的作用点 固定 , F Βιβλιοθήκη 作用方 向在加 载过程中始终 与基
G B 1 1 5 5 0 — 2 0 0 9 要求 , 为乘员的安全提供切实有效 的 准线 r 垂直且绕 H点旋转 , 力臂 L 1 为固定值 的方法。 选 择 背 板 的 中心 为 几 作 用 点 , F 1 在 加 载 过 程 保障。 中 ,方 向始 终 与基准线 r 垂直 , F 1到 H点 的力 臂 l
油缸力加载可分为直接加载方式 和间接加载方 在试验过程 中,加载作用力及测量头枕后移距 间接加载方式又分为推和拉两种方式 , 以下就油 离 值 x都 是 以座 椅 的 H点 和基 准线 r 为基 准 , 因此 , 式, 试验 的第一步就是设计 3 一 D H装置, 如图 1 所示 , 将 缸力 的直 接加 载方 式分 析讨论 。 油缸 活 塞杆 作 为 F 1 载荷 杆 直接 作 用 在 背板 上 , H点和基准线 r 实体化为 3 一 D H装置中的点 和线 , 所示。 在F l 加载过程中, 作用点绕 H点旋转 , 按G B I 1 5 5 1 — 2 0 0 3《 乘用车正面碰撞的乘员保护》 中 如图 3 附录 c的操作程序 ,将 3 一 D H装置摆放到试验座椅 同时油缸活塞杆在施加力 的过程 中不断伸长 ,使得 油缸的轨迹较复杂 , 油缸基座安装机构设计较 困难 。 上, 确 定座 椅 H点 和基 准线 r , 如 图 2所示 。
1 设计 方案分析
1 . 1 座 椅 的 H点和 基 准线 r
取值为 3 0 0 m m 。F 1 的最终值 可确定 : F 1 =M1 / l
汽车座椅静强度试验综述

汽车座椅静强度试验综述随着汽车行业的迅猛发展,汽车安全问题备受关注。
作为车辆安全的重要组成部分,座椅的质量和强度也成为了关注的焦点。
汽车座椅静强度试验是评估座椅结构和材料强度的重要手段之一。
本文将对汽车座椅静强度试验进行综述,以便更好地了解和评估座椅的安全性能。
一、试验目的和原理汽车座椅静强度试验的目的是评估座椅结构和材料在静态荷载下的强度。
试验原理是将座椅固定在试验台上,施加一定的静态荷载,观察和记录座椅的变形情况和荷载下的应力分布,从而评估座椅的强度和稳定性。
二、试验流程和方法汽车座椅静强度试验通常分为以下几个步骤:1. 座椅固定:将座椅安装在试验台上,并确保固定牢固,以模拟实际使用条件。
2. 荷载施加:施加一定的静态荷载到座椅上,可以通过液压或机械装置实现。
荷载的大小根据相关标准和要求确定。
3. 测试数据记录:在施加荷载的过程中,需要记录座椅的变形情况、应力分布等数据。
可以使用传感器和数据采集系统来实现。
4. 试验结果分析:根据测试数据,分析座椅的强度、稳定性和安全性能,评估是否符合相关标准和要求。
三、试验标准和要求汽车座椅静强度试验的标准和要求通常由国家或行业组织制定。
常见的标准包括国际汽车工程师学会(SAE)的相关标准、欧洲汽车制造商协会(ACEA)的规范以及中国国家标准等。
试验标准通常包括对座椅的材料、结构和连接件要求,以及试验荷载、变形限制、应力分布等指标。
其中,静态荷载的大小和施加的位置是评估座椅强度的重要参数。
四、试验结果分析与应用试验结果的分析和应用是评估座椅的安全性能和改进设计的关键。
根据试验结果,可以评估座椅的强度和稳定性是否符合标准和要求。
如果不符合,需要进行结构和材料的改进,以提高座椅的安全性能。
试验结果还可以为汽车制造商提供重要的参考和依据,以选择合适的座椅供应商和优化座椅设计。
同时,试验结果也可以用于消费者选择汽车时的参考,以确保座椅的安全性能满足个人需求。
汽车座椅静强度试验是评估座椅安全性能的重要手段之一。
节制杆式模拟汽车座椅强度试验装置研究
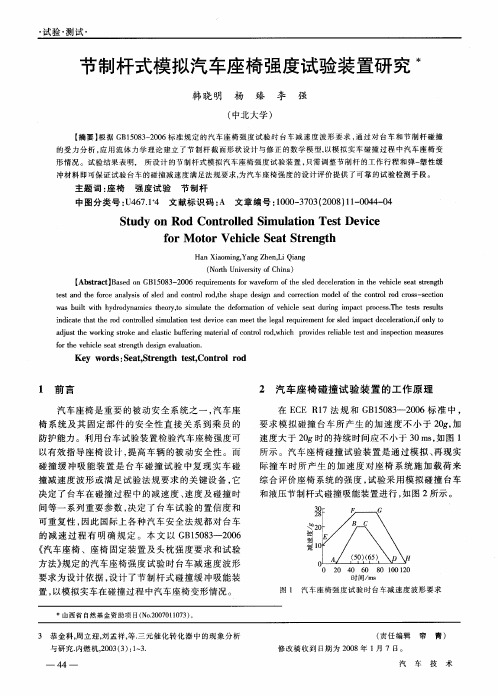
韩 晓 明 杨 臻 李 强
( 中北 大学 )
【 摘要】 根据 G 10 3 2 0 B 5 8— 0 6标准规定 的汽车座椅强度试验 时台车减速度波形要求 , 通过 对台车和节制 杆碰撞
的受 力 分 析 , 用 流体 力 学 理 论 建 立 了节 制 杆 截 面形 状 设 计 与 修 正 的数 学 模 型 , 应 以模 拟 实 车 碰 撞 过 程 中 汽 车 座椅 变 形 情 况 。 试 验结 果 表 明, 所 设计 的节 制 杆 式 模拟 汽 车 座 椅 强度 试 验 装 置 , 需 调 整节 制 杆 的 工作 行 程 和 弹 一 性 缓 只 塑
1 前 言
汽 车座 椅 是重 要 的被 动 安全 系 统之 一 , 车座 汽
2 汽 车座 椅 碰 撞试 验 装置 的工 作 原 理
在 E E R1 C 7法 规 和 G 10 3 O 6标 准 中 , B 5 8 —2 0 要 求 模 拟碰 撞 台车所 产 生 的 加速 度 不 小 于 2 g 加 0, 速 度大 于 2 g时 的持 续 时间应 不小 于 3 , 图 1 0 0 ms如 所 示 。汽 车座 椅碰 撞试 验装 置 是通 过 模 拟 、 现 实 再 际撞 车 时 所 产 生 的加 速 度 对座 椅 系统 施 加 载 荷 来
冲材 料 即 可 保证 试 验 台车 的 碰撞 减 速 度 满 足法 规 要 求 , 汽 车座 椅 强 度 的 设计 评 价 提 供 了 可靠 的试 验 检测 手 段 。 为
主 题词 : 椅 座
强度试 验
节制杆
中图分 类号 : 4 71 文 献标识 码 : 文 章编 号 :0 0 3 0 (0 8 1— 0 4 0 U 6 .4 + A 10 — 7 3 2 0 ) 10 4 — 4
某车型驾驶员座椅鞭打试验性能研究及改进

144AUTO TIMEAUTO PARTS | 汽车零部件某车型驾驶员座椅鞭打试验性能研究及改进1 引言在追尾事故中,被碰撞车辆的驾驶员、乘员在碰撞加速度与头部惯性力的共同作用下,颈部会产生一个像鞭子猛抽的动作称为鞭打伤害,追尾事故会给乘员颈部的骨骼或软组织造成严重的损伤[1]。
通过优化座椅设计减轻鞭打效应对人体的伤害成为各大汽车厂重点研究的内容。
本文根据C-NCAP 鞭打试验要求,对某款乘用车的驾驶员座椅运用有限元方法建立鞭打模型,针对鞭打试验分数较低,采用有限元进行仿真分析,提出增加靠背刚性、增加头枕骨架强度以及增加假人靠背穿透量等座椅改进方案,并对改进后的座椅再次进行仿真分析及实物试验验证,得到了有利于减小鞭打伤害的方法。
2 鞭打试验评估方法《C-NCAP 管理规则(2021年版)》[2]已经实施,C-NCAP 鞭打试验评价通过7项伤害指标分组加和并扣除3项罚分项形成总体得分,驾驶员座椅的总体得分的最高分是5分,最低分是0分且所有的得分均保留到小数点后三位。
7项伤害指标分别设置低性能限值和高性能限值,分别得分为0和满分,处于高、低性能限值之间的测试值按线性插值方法计算得分。
7项伤害指标分为三组,第一组为满分为2分的颈部伤害指数NIC;第二组为满分为1.5分的上颈部剪切力F x 、上颈部拉力F z 和上颈部扭矩M y ;第三组为满分为1.5分的下颈部剪切力F x 、下颈部拉力F z 和下颈部扭矩M y ,其中第二组和第三组选取每组最低分为该组得分。
3项罚分项分别是座椅靠背最大动态张角大于等于25.5°时扣2分;头枕干涉头部时扣2分;座椅滑轨动态位移大于20mm 时扣5分。
2021版鞭打试验总体评价指标及评分原则如表1所示。
3 鞭打试验模型的建立在有限元前处理软件HyperMesh 中将座椅中不同组件划分成不同的网格单元,设李海 赵座航 聂仁态 李雪晴上汽通用五菱汽车股份有限公司 广西柳州市 545007摘 要: 针对某车型驾驶员座椅在2021版鞭打试验中得分较低的问题,通过仿真分析影响座椅鞭打试验的因素,改进对鞭打试验分值影响较大的靠背刚度、头枕位置及其结构、靠背结构等参数,改善碰撞过程中座椅靠背和头枕骤然后倾的问题,减少了假人颈部伤害指数,提高鞭打试验得分。
汽车综合性能试验台
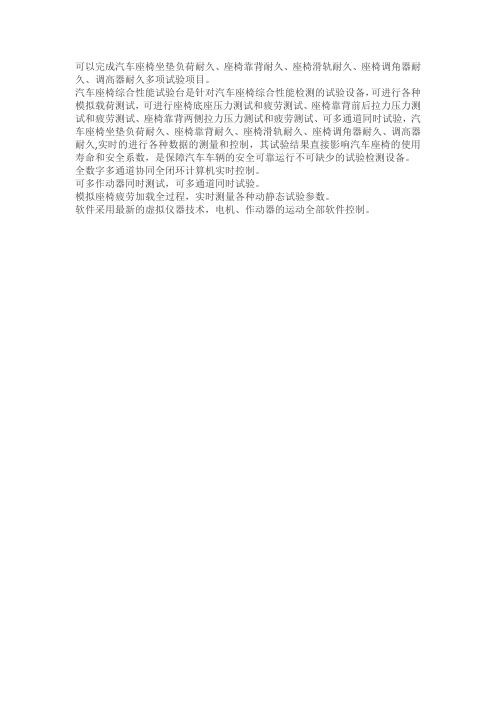
可以完成汽车座椅坐垫负荷耐久、座椅靠背耐久、座椅滑轨耐久、座椅调角器耐久、调高器耐久多项试验项目。
汽车座椅综合性能试验台是针对汽车座椅综合性能检测的试验设备,可进行各种模拟载荷测试,可进行座椅底座压力测试和疲劳测试、座椅靠背前后拉力压力测试和疲劳测试、座椅靠背两侧拉力压力测试和疲劳测试、可多通道同时试验,汽车座椅坐垫负荷耐久、座椅靠背耐久、座椅滑轨耐久、座椅调角器耐久、调高器耐久,实时的进行各种数据的测量和控制,其试验结果直接影响汽车座椅的使用寿命和安全系数,是保障汽车车辆的安全可靠运行不可缺少的试验检测设备。
全数字多通道协同全闭环计算机实时控制。
可多作动器同时测试,可多通道同时试验。
模拟座椅疲劳加载全过程,实时测量各种动静态试验参数。
软件采用最新的虚拟仪器技术,电机、作动器的运动全部软件控制。
- 1、下载文档前请自行甄别文档内容的完整性,平台不提供额外的编辑、内容补充、找答案等附加服务。
- 2、"仅部分预览"的文档,不可在线预览部分如存在完整性等问题,可反馈申请退款(可完整预览的文档不适用该条件!)。
- 3、如文档侵犯您的权益,请联系客服反馈,我们会尽快为您处理(人工客服工作时间:9:00-18:30)。
系统中的运动均为直线往复运动.且所需力度不大,因此均 采用轻型拉杆式液压缸,选择的液压缸缸径为63ram,活塞杆直 径为22mm。根据试验要求得到不I司速度。并计算出流量.如表1 所示。 表1各工况液压缸及系统所需流量
工况 执行元件名称
(2)巧妙的运用杆系机构实现了液压控制静力加载机构中
两个液压缸的运动解耦,使得液压:Ja沛J系统变得简单,容易实现。
图2试验台系统原理图
中靠背液压缸的活塞杆应该伸出还是收缩,从理论上讲只要检测 C杆上的测力传感器反馈值是否接近于0,如果大于0,则活塞杆 收缩;相反。如果小于0,则活塞杆伸出。
3试验台加载系统设计
如何实现汽车座椅的准确加载是汽车座椅强度性能试验台 的关键,汽车座椅靠背及调节装置强度试验和汽车座椅头枕静态 性能试验由静力加载机构完成,冲击摆锤加载机构用于完成汽车 座椅靠背及头枕吸能性试验。
机械设计与制造
118 文章编号:1001—3997(2012)06-01 18-03 Machinery Design&Manufacture
第6期 2012年6月
汽车座椅强度性能试验台设计
袁冬梅李亚辉征小梅 (重庆理工大学汽车学院,重庆400050) Design (College
on
Strength Test Bed of Automobile Seat 400050,China)
关键词:汽车座椅;强度:加载;试验台;设计 【Abstract】The
ort
seat
is
an
important
component
Olt
ofautomobile,which
standard.a strength
pe咖ormonee咖c拈directly
test
up-
security and
comfort of automobile.Based
such as strength
headrest
and energy absorption
testfor
regulating device,static peoCormance test如r seat backrest and headrest with the characteristics ofstrong univer-
-k来稿日期:201l加8一10-k基金项目:汽车零部件制造及检测技术教育部重点实验室开放基金项目(2010KLMT05)
万方数据
第6期
袁冬梅等:汽车座椅强度性能试验台设计
119
气控制系统再i酗立控制加载机构作用在待试验的汽车座椅上,并将 座椅反馈给加载机构的各种信号数据通过传感器反馈给数据采 集卡,传回工控机。整个试验台系统为闭环控制系统,工控机通过 处理传感器反馈的信息时时控制加载力的大小和方向,整个试验 过程全自动化,不但能提高试验效率,而且能确保试验的准确性。
ห้องสมุดไป่ตู้
3.2冲击摆锤加载机构设计
冲击摆锤加载机构用于汽车座椅靠背及头枕吸能性试验 中。摆锤加载机构的结构,如图4所示。整个撰锤机构支撑在导轨 立柱上,摆锤靠减速电机驱动减速换向后使摆锤抬升机构上升。 在模拟人体头部对头枕的撞击中,摆锤一端固定在中心轴上,将 摆锤抬升至一定高度(由摆锤抬升装置完成),然后释放摆锤,让 摆锤自由落下,摆锤的撞击速度可由摆锤抬升高度调整。 《座椅试验标准》中规定,试验中由前向后撞击座椅头枕前 表面时,撞击方向应位于纵向平面内并沿水平方向;由后向前撞 击座椅头枕后表面时,撞击方向应位于纵向平面内并与铅锤方向 成45。,同时模拟头型(摆锤)应以24.1 knda的速度撞击试验样
靠背及调节装置的强度试验的加载机构还可用于头枕静态
万方数据
No.6 120
机械设计与制造
Jun.2012
4液压系统设计
液压控制系统的设计关键在于对液压缸速度的控制,试验 中液压缸活塞杆的运动速度主要是试验前对机构位置的手动调 节、试验时的工进、试验结束后的快速回位等三种不同工况下液 压缸活塞杆的速度,液压缸活塞杆的速度由通过液压缸的流量 控制。 /
7、8、10、13、15、17.电磁换向阀9、II、16、18.调速阔12、l 9.i霞压缸 14、22.液控单向阔20.先导型溢流阀21.蓄能器
\、影
一\.
图6摆锤由后向前撞击座椅时的示意图
5结论
在汽车座椅相关试验标准基础上,提出了一种新型汽车座 椅强度性能试验台,重点对试验台总体方案、静力加载机构、摆 锤加载机构和液压控制系统进行了详细设计和分析,并得出以 下结论: (1)试验台采用液压控制静力加载机构和电机控制冲击摆 锤加载机构,能够准确模拟汽车座椅靠背及调节装置强度试验、 汽车座椅头枕静态性能试验和汽车座椅靠背及头枕吸能性试验 工况。
3.1静力加载机构设计
静力加载机构主要由液压缸和杆系组成,如图1中5所示。 其机构运动简图,如图3所示。根据《座椅试验标准》中对靠背及 调节装置的强度试验的要求,试验时要对座椅靠背沿纵向向后 施加相对于座椅“R”点530 N・rn力矩的负荷。采用液压缸作为 动力源,试验时,靠背受力会绕着转轴后倾,如果液压缸活塞杆 的方向不绕着“R”点运动,就无法对靠背提供满足要求的力矩。 为了克服这个缺陷,在靠背及调节装置的强度试验中.采用将 “R”点固定,靠背液压缸、A杆、B杆及c杆互相铰接。靠背液压 缸推动A杆,A、B、C三杆组成稳定的三角形连接,B杆上固定 假背模型对座椅靠背施加载荷。在整个试验过程中,B杆始终绕 着“R”点旋转,同时在c杆上安装测力传感器,由于c杆和B杆 垂直,受到B杆的反作用力方向在c杆轴心线上,c杆上的测 力传感器就可以及时反馈C杆的受力情况,B杆对靠背的力矩 就是c杆上测力传感器反馈值与B杆长度(根据座椅的尺寸大 小进行确定)的乘积。同时,根据<座椅试验标准》中对汽车座椅 头枕静态性能试验的规定,试验时应在头枕顶部向下65
mm
品。由能量守恒公式哪=争一2得:拓专=里;!霎}-2.287m=
。
2287mm.
处,通过直径为165ram的头型。施加一个垂直于移动后基准线 的初始负荷,其相对于“R”点的力矩为373
N・m。
图4摆锤机构的结构示意图
I.geg电机2插臂3导轨立柱4.螺旋升降机5.摆锤抬升机构6摆锤
摆锤抬升机构的长短不仅影响减速电机的功率和传动比,而
YUAN Dong-mei,LI YA-hui,ZHENG Xiao-mei of Automobile Engineering,Chongqing University of Technology,Chongqing
【摘要】汽车座椅是汽车的重要部件之一,其性能好坏直接影响汽车安全性和舒适性。在相关试
(3)所设计的试验台具有结构简单、通用性强、精度高,成本 低、自动化程度高和使用方便等特点。
霾 结构参数晋磊群嚣褊
参考文献
[1]吴何畏,周雄刚,冯小波.基于微机控制的汽车座椅调角器静强度试验 机『J].机电—体化,2006(4);61-63. 【2]韩晓明,杨臻,李强.节制杆式模拟汽车座椅强度试验装置研究[J].汽 车技术,2008(1i):44_47.
气系统及控制软件等部分组成。机械部分实现汽车座椅的装夹和 加载,主要包含试验台底座、静力加载机构、冲击摆锤加载机构、 摇臂机构等,如图1所示(所设计的试验台能同时进行两套座椅 的强度试验和—套座椅的吸能试验)。液压系统在电气系统和控 制软件的控制下实现域椅的准确加载.电7i系统和控制软件实现 试验台的综合控制和测试
且还会使机构出现不稳定现象。设计的摆锤抬升机构长度为 1500mm,当试验由前向后撞击座椅头枕前表面时,如图5所示。抬 升2287mm的高度约要从水平方向(最低点)举升到120";试验由
图3静力加载机构运动简图 I^杆2.B扦3.C杆4.D杆5.头枕液压缸6.靠背液压缸
后向前撞击座椅头枕后表面时,如图6所示。抬升2287mm的高度 约要从4507:向(距最低点约440mm)举升到1450位置。这不仅可 以满足试验要求,而且还可以避免到达最大角度(1800)位置。
sality,lIl‘咖accuracy,加Cost
and easy凇e.
Key words:Automobile Seat;Strength;Iamdlng;Test Bed;Design
中图分类号:'1'1-116,U467.3文献标识码:A
1引言
随着汽车产业的发展,人们除了考虑汽车动力经济性外,越 来越重视汽车的安全性和舒适性I-I。汽车座椅是车内乘员安全性 和舒适性的一个重要部件之一,汽车厂商必须对其性能进行检测 和试验日。座椅作为联系人与车的—个重要部件,承受着复杂的载 荷。一方面.由于路面的凸凹不平,汽车行驶时车体产生的随机振动 对汽车座椅产生随机动载荷;另一方面。汽车行驶中要经历起步、加 速、制动等复杂工况,汽车座椅因此会受到很大的冲击载荷M。由 于在试验室中很难再现这些复杂工况。研究人员将各种工况的极 限情况折算为等效的静态载荷,作为评定座椅承载性能的标准翌。 国家质量监督检验检疫总局出版的(GBl5083---2006汽车座椅、 座椅固定装置及头枕强度要求和试验方法)(下文简称<座椅试验 标准>)_就是一部比较完整的评定座椅承载性能的标准。在参考 <座椅试验标准)基础上。设计了一种汽车座椅强度性能试验台, 能检测汽车座椅靠背、调节装置以及头枕的性能,为汽车座椅强 度性能试验提供了一种行之有效的方法。
2试验台的组成原理
试验台主要完成汽车座椅靠背及调节装置强度试验、汽车 座椅头枕静态性能试验和汽车座椅靠背及头枕吸能性试验.结合 汽车座椅试验标准,设计的试验台主要由机械系统、液压系统、电
图1机械系统结构示意图 1.摇臂机构z立柱3.冲击摆锤加载机构4.座椅 5.静力加载机构6.座椅固定装置7.底座
试验台系统原理图,如图2所示。工控机通过数据采集卡给 液压控制系统和电气控制系统发送控制命令.液压控制系统和电