冲孔落料复合模具设计
落料冲孔复合模具设计
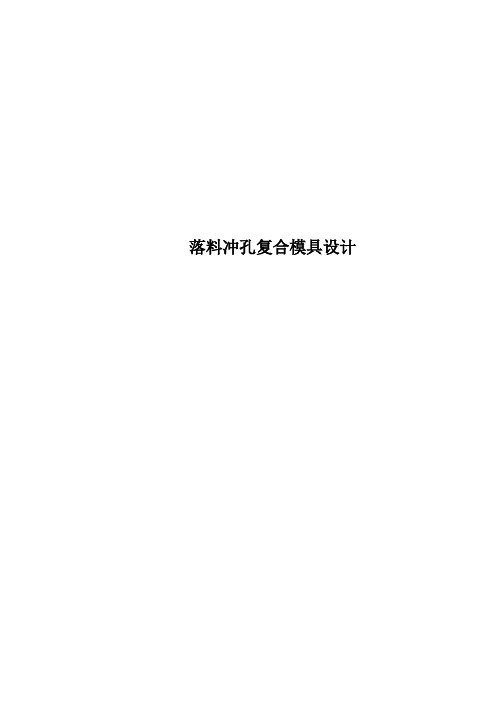
落料冲孔复合模具设计落料冲孔复合模具设计绪论模具主要类型有:冲模,锻模,塑料模,压铸模,粉末冶金模,玻璃模,橡胶模,陶瓷模等。
除部分冲模以外的的上述各种模具都属于腔型模,因为他们一般都是依靠三维的模具形腔是材料成型。
(1)冲模:冲模是对金属板材进行冲压加工获得合格产品的工具。
冲模占模具总数的50%以上。
按工艺性质的不同,冲模可分为落料模,冲孔模,切口模,切边模,弯曲模,卷边模,拉深模,校平模,翻孔模,翻边模,缩口模,压印模,胀形模。
按组合工序不同,冲模分为单工序模,复合模,连续模。
(2)锻模:锻模是金属在热态或冷态下进行体积成型是所用模具的总称。
按锻压设备不同,锻模分为锤用锻模,螺旋压力机锻模,热模锻压力锻模,平锻机用锻模,水压机用锻模,高速锤用锻模,摆动碾压机用锻模,辊锻机用锻模,楔横轧机用锻模等。
按工艺用途不同,锻模可分为预锻模具,挤压模具,精锻模具,等温模具,超塑性模具等。
(3)塑料模:塑料模是塑料成型的工艺装备。
塑料模约占模具总数的35%,而且有继续上升的趋势。
塑料模主要包括压塑模,挤塑模,注射模,此外还有挤出成型模,泡沫塑料的发泡成型模,低发泡注射成型模,吹塑模等。
(4)压铸模:压铸模是压力铸造工艺装备,压力铸造是使液态金属在高温和高速下充填铸型,在高压下成型和结晶的一种特殊制造方法。
压铸模约占模具总数的6%。
(5)粉末冶金模:粉末冶金模用于粉末成型,按成型工艺分类粉末冶金模有:压模,精整模,复压模,热压模,粉浆浇注模,松装烧结模等。
目前,我国17000多个模具生产厂点,从业人数五十多万。
除了国有的专业模具厂外,其他所有制形式的模具厂家,包括集体企业,合资企业,独资企业和私营企业等,都得到了快速发展。
研究和发展模具技术,对于促进国民经济的发展具有特别重要的意义,模具技术已成为衡量一个国家产品制造技术的重要标志之一,随着工业生产的迅速发展,模具工业在国民经济中的地位日益提高,并在国民经济发展过程中发挥越来越大的作用。
落料冲孔复合模设计说明书

I摘要本次设计了一套冲孔﹑落料的模具。
经过查阅资料,首先要对零件进行工艺分析,经过工艺分析和对比,采用冲孔落料工序,通过冲裁力、顶件力、卸料力等计算,确定模具的类型。
得出将设计的模具类型后将模具的各工作零部件设计过程表达出来。
在论文中第一部分,主要叙述了冲压模具的发展状况,说明了冲压模具的重要性,接着是对冲压件的工艺分析,完成了工艺方案的确定。
第二部分,对零件排样图的设计,完成了材料利用率的计算。
再进行冲裁工艺力的计算和冲裁模工作部分的设计计算,对选择冲压设备提供依据。
最后对主要零部件的设计和标准件的选择,为本次设计模具的绘制和模具的成形提供依据。
通过前面的设计方案画出模具各零件图和装配图。
本模具性能可靠,运行平稳,能够适应大批量生产要求,提高了产品质量和生产效率,降低劳动强度和生产成本。
关键词:冲压;落料冲孔模;模具结构;目录1冲压基础知识 (1)2工艺分析 (3)2.1零件的功用与经济性分析 (3)2.2零件钣金成形工艺性分析 (3)2.2.1结构形状与尺寸分析: (3)2.2.2 精度与表面粗糙度 (4)2.2.3 材料 (4)3制定工艺方案 (5)3.1工艺方案的分析 (5)3.2工艺方案的确定 (5)4工艺计算 (6)4.1排样及材料的利用率 (6)4.11排样的选用原则 (6)4.12材料利用率的计算 (6)4.2落料力、冲孔力、卸料力、推件力的计算 (7)4.4模具刃口的尺寸和公差的确定 (10)4.41冲裁间隙的确定 (10)4.42凸、凹模刃口尺寸计算 (10)5 主要零部件设计 (13)5.1 凹模设计 (13)5.2 凸模的设计 (14)5.3 凸凹模设计 (15)5.4 卸料橡胶的设计 (16)5.5 卸料板的设计 (17)5.6 固定板的设计 (17)5.7 上下模座、模柄的选用 (18)6 冲压设备的校核与选定 (20)6.1 冲压设备的校核 (20)6.2 冲压设备的选用 (20)7 绘制模具总装图及零件图 (21)7.1装配图绘制 (21)参考文献 (22)1冲压基础知识冲压是利用模具使板料沿一定的轮廓形状产生分离的一种冲压工序。
二_落料_正反拉伸_冲孔_翻孔复合模具设计的工作零件结构尺寸的计算

二、落料、正反拉伸、冲孔、翻孔复合模具设计的工作零件结构尺寸的计算1.落料凹模结构设计及刃口尺寸的计算1.1确定凹模板外形尺寸凹模板采用圆形凹模板,由于压力中心在几何中心,查表2-17(见冲压工艺与模具设计一书)可得:凹模壁厚为35至45mm,本次设计C取40根据凹模的直径D=124+2C,所以可得凹模的最小外形尺寸:D=124+2⨯40=204mm查国标取标准值:凹模直径为200φmm查国标GB2873.3-81得模架的零件为;上垫板尺寸为:200⨯8上固定板尺寸为:200⨯22下固定板尺寸为:200⨯22卸料板、压边圈尺寸为:200⨯18上模螺钉尺寸为:124颗上模圆柱销钉尺寸为:124颗下模螺钉尺寸为:124颗下模圆柱销钉尺寸为:124颗孔的布置均在164的圆周上。
1.2刃口尺寸的计算124φ01-的落料拉深凸凹模的制造公差由表1—22(见冲压模具设计与制造)查得mm 040.0=凹δ,mm 030.0=凸δ。
查表1—20(见冲压模具设计与制造)查得180.0max =Z min Z =0.126由于min max 070.0Z Z ->=+凸凹δδ=0.180-0.126=0.054mm,故采用凸模与凹模配合加工方法,该冲裁件属落料件,选凹模为设计基准件,采用配合加工,只需要计算落料凹模刃口尺寸及制造公差,凸模刃口尺寸根据凹模实际尺寸按间隙要求配作。
因数由1-23(见冲压模具设计与制造)因为冲裁件精度IT14级,查得X=0.5,则落料凹模的基本尺寸计算如下:mmX D D 25.0014141max 5.12315.0124+⨯+∆+=⨯-=∆-=)()(凹凸D 按凹模尺寸配制,根据表1—20(见冲压模具设计与制造)查得其双面间隙为0.126~0.180mm ,其工作部分结构尺寸如图所示:1.3凹模的厚度的计算凹模的厚度为:H=)(1.0321mm F K K1K -凹模材料修正系数,合金工具钢取1,碳素工具钢取1.3;2K -凹模刃口周边长度修正系数见表2-18(见冲压工艺与模具设计一书);F 为冲裁力(N);冲裁力N Lt F b 1811404002.1378=⨯⨯==σ所以凹模厚度mmH 361811401.037.113≈⨯⨯⨯=根据模具结构计算凹模厚度:依据经验值取顶件块的高度为15mm,安全距离取10mm,凹模厚度:492410151=++=++=h H H H 安顶mm 按GB2858.5-81最大标准值32mm,本次设计凹模厚度取50mm.1.4凹模刃口高度的确定凹模刃口高度查表1-26(见冲压模具设计与制造), 1t 5.2≤h 6≥本次设计取h 为10mm.落料孔要安装顶件块,本次设计单边扩大10mm。
落料冲孔复合模具设计
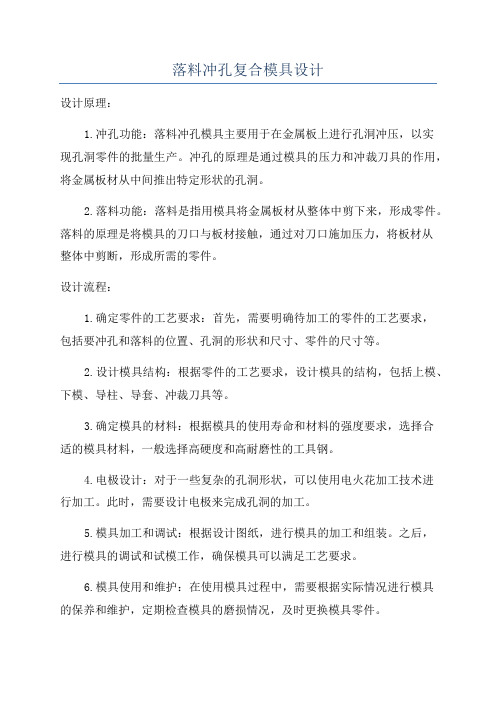
落料冲孔复合模具设计设计原理:1.冲孔功能:落料冲孔模具主要用于在金属板上进行孔洞冲压,以实现孔洞零件的批量生产。
冲孔的原理是通过模具的压力和冲裁刀具的作用,将金属板材从中间推出特定形状的孔洞。
2.落料功能:落料是指用模具将金属板材从整体中剪下来,形成零件。
落料的原理是将模具的刀口与板材接触,通过对刀口施加压力,将板材从整体中剪断,形成所需的零件。
设计流程:1.确定零件的工艺要求:首先,需要明确待加工的零件的工艺要求,包括要冲孔和落料的位置、孔洞的形状和尺寸、零件的尺寸等。
2.设计模具结构:根据零件的工艺要求,设计模具的结构,包括上模、下模、导柱、导套、冲裁刀具等。
3.确定模具的材料:根据模具的使用寿命和材料的强度要求,选择合适的模具材料,一般选择高硬度和高耐磨性的工具钢。
4.电极设计:对于一些复杂的孔洞形状,可以使用电火花加工技术进行加工。
此时,需要设计电极来完成孔洞的加工。
5.模具加工和调试:根据设计图纸,进行模具的加工和组装。
之后,进行模具的调试和试模工作,确保模具可以满足工艺要求。
6.模具使用和维护:在使用模具过程中,需要根据实际情况进行模具的保养和维护,定期检查模具的磨损情况,及时更换模具零件。
设计注意事项:1.强化模具的刚性:落料冲孔复合模具的刚性对于冲孔和落料的质量有很大影响。
因此,设计时需要合理设计模具的结构,提高模具的刚性。
2.合理选择冲裁刀具:根据孔洞的形状和尺寸,选择合适的冲裁刀具。
冲裁刀具应具有足够的硬度和耐磨性,以确保冲裁的质量和寿命。
3.注意冲孔位置的精度:冲孔位置的精度对于零件的质量和装配性能有很大影响。
因此,在设计模具时需要特别注意冲孔位置的精度要求,并通过合理的设计和加工保证冲孔位置的精度。
4.设计合理的导向装置:为了确保模具在使用过程中的精度和稳定性,需要设计合理的导向装置,保证模具在工作时能够准确导向。
总结:落料冲孔复合模具设计需要根据零件的工艺要求和性能要求来设计模具的结构和工艺。
落料、冲孔、弯曲复合模设计

模具设计作业题:冲孔弯曲复合模设计:零件简图:如图1所示;生产批量:大批量;材料:Q235A ;零件厚度: 3 mm。
图1 零件简图1、冲压件的工艺分析以及方案的确定通过对冲压件图样的分析得出对于这类工件,一般采用先落料、冲孔,再弯曲的加工顺序进行加工。
如果把三道工序放到一起,可以大大提高工作效率,降低整个模具的开发成本,能够减轻工作量,节约能源,产品质量稳定而且在加工时不需再将手伸入模具空间, 保护了操作者的人身安全。
将三道工序复合在一起,可以有以下两个不同的工艺方案:方案一、先落料,然后冲孔和弯曲在同一工步;方案二、冲孔为同一工步首先完成,然后再进行弯曲。
采用第一种方案加工工件,不易保证长度尺寸的精度,而且容易磨损内孔冲头,降低模具寿命。
经分析、比较最后确认方案二。
对弯曲的回弹,可以用减小间隙的方法来避免或减小回弹。
该冲压件的形状较为简单对称,由《冷冲压成形工艺与模具设计制造》中的表4-9和表4-11查的,冲裁件内外形达到的经济精度为IT12~IT13,弯曲部分用r=2.5mm 的圆角进行过渡。
除孔0.021018+Φmm 有精度要求外, 其余尺寸的精度要求不高。
Q235- A 钢冲压性能较好, 孔与外缘的壁厚较大, 复合模中的凸凹模壁厚部分具有足够的强度。
因此, 该工件采用落料、冲孔及弯曲复合模加工较合理。
2、主要工艺参数的计算2.1 毛坯尺寸的计算在计算毛坯尺寸前,需要先确定弯曲前的形状和尺寸,又有弯曲半径 r=2.5mm > 0.5t=0.5x3=1.5mm,故这类弯曲件变薄不严重,横断面畸变较小,可以按应变中性层展开长度等于毛坯长度的原则计算毛坯尺寸,即: 12++()180ar kt L l l π+=式中的L ——毛坯的展开长度,k ——与变形程度有关的系数,r K t==2.53 =0.83查书本中表4-5利用插值法算得 k=0.4064,带入数据L=9.5+80.5+3.1490(2.50.40643)180⨯+⨯=95.84 mm2.2 排样的设计与计算排样设计主要确定排样形式、送料步距、条料宽度、材料利用率和绘制排样图。
模具毕业设计56接线端子板冲孔、落料、压弯复合模设计
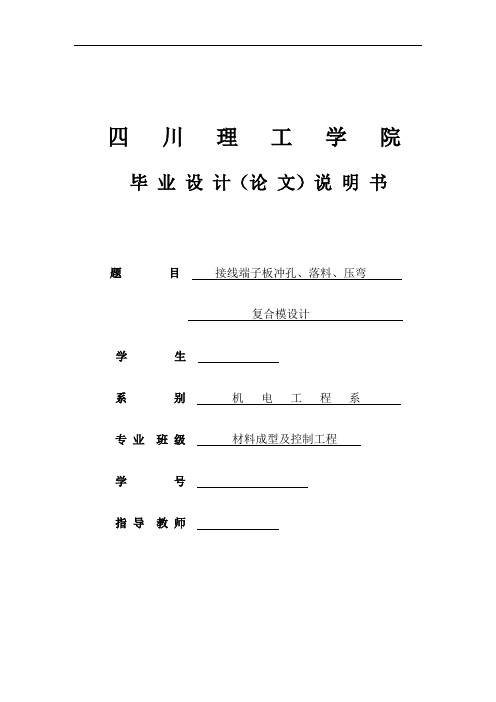
四川理工学院毕业设计(论文)说明书题目接线端子板冲孔、落料、压弯复合模设计学生系别机电工程系专业班级材料成型及控制工程学号指导教师四.毕业设计附图名称:接线端子板工件图1.材料技术要求:(1)厚度δ=0.560.09mm牌号 H62(软黄铜)(2)表面质量:平整2.大批量生产1摘要摘要:阐述了冲孔、落料、压弯复合模的结构设计及工作原理。
通过工艺分析,在冲压材料厚度较薄的小型弯曲件时,采用冲孔、落料、弯曲复合模比采用连续或级进模简单。
通过冲裁力、顶件力、卸料力等计算,确定模具类型。
该模具采用后侧导柱模架结构形式。
废料从凸凹模和下底座中所开的槽中排出。
本模具性能可靠,运行平稳,能够适应大批量生产要求,提高了产品质量和生产效率,降低劳动强度和生产成本。
关键字:冲压;冲孔、落料、弯曲;复合模;IAbstracAbstract: Expounded punching, blanking, bending modulus of the composite structure design and principle. Process analysis by the stamping of thinner material thickness small curved pieces, will use the punching, blanking, flexural modulus composites than continuous or Progressive Die simple. Punching through, the top pieces, such as the discharge of calculation to determine the type mold. The posterior mold using derivative-scale structures form. Waste from the punch and die and the base under which opened the tank discharges. The mold reliable, stable operation to adapt to the requirements of large-scale production, improve product quality and production efficiency. reduce labor intensity and the cost of production.Keywords: Ramming; The punch holes, Fall the material curving; Superposable die;II前言科学技术发展的进程表明,机械工业是科学技术物化为生产力的重要载体,而模具设计与制造在机械行业占有举足轻重的地位。
毕业设计——垫片冲孔落料复合模具设计 (2)
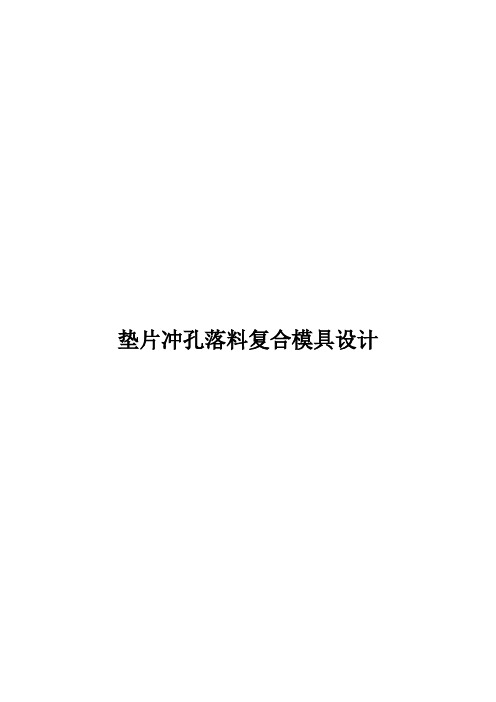
垫片冲孔落料复合模具设计摘要改革开放以后,我们国家在飞速发展,尤其在工业方面呈现飞跃式的发展,一跃成为工业大国。
然而,工业的发展跟模具行业是离不开的,国家的发展同时也给模具行业的发展打下基石。
因此,各类模具变应运而生,推动着中华文明走向一个新的纪元。
此次我选择的是冷冲压,所选的零件为垫片。
垫片是一种常见而且结构非常简单的零件,我们生活中随处可见的一种零件。
因为垫片使用比较广泛,所以制作过程中就要控制好垫片的成本,这样才能使企业在市场中占据绝对的优势。
论文中设计的垫片冲设计,选材,模具制造,压力机选择都是在市场竞争中占据优势的。
关键词:冲孔落料零件复合模具模具凸模模具凹模计算机协助设计目录引言 (1)一、冲孔落料件的工艺分析............................ 错误!未定义书签。
(一)零件图 (4)(二)零件图的工艺分析 (4)二、冲裁力、卸料力、顶出力的计算 (5)(一)冲裁力的计算 (5)(二)卸料力的计算 (5)(三)顶件力的计算 (5)(四)计算总冲裁力 (6)三、初选压力机 (6)四、凸模的结构设计 (7)(一)凸模选取原则 (7)(二)凸模的结构 (7)(三)计算凸模的长度 (7)(四)凸模强度的校核 (8)五、凹模的结构设计 (9)(一)凹模结构 (9)(二)计算凹模的厚度 (9)六、刃口的尺寸计算 (10)七、压力中心的计算 (10)八、卸料装置的设计 (11)(一)卸料板的选用 (11)(二)弹性元件的选取及计算 (11)(三)卸料螺钉的选取: (12)九、顶料装置的设计 (13)十、冲模的导向选用 (13)十一、整个模具的动作分析 (14)总结................................................ 错误!未定义书签。
参考资料............................................ 错误!未定义书签。
冲孔落料复合模具设计

冲孔落料复合模具设计
一、概述
冲孔落料复合模具是一种常见的复杂成型模具。
它通过模具做成空心
的产品,通常用于金属制品和塑料制品的制作,可以实现冲孔、落坯和成
型功能。
本文的主要内容是设计一种新型的冲孔落料复合模具,它具有较
高的体积效率、较高的加工精度,能够有效减少成型周期,并有效提高生
产率和工作效率。
二、复合模具结构
1.冲孔落料复合模具由上模、开口上模、开口下模和下模4部分组成,它们分别由定子构件组成,定子构件上设有冲孔板、落料板和成型板三种
板材。
2.上模包括定子座、凸模、凹模、垫块和支架等组成部分,它们相互
配合,形成复合模具的上表面。
3.定子构件支撑着开口上模和下模,开口上模上设有冲孔孔洞,而开
口下模上设有成型孔洞,它们两者之间隔有一定的距离,能够实现冲孔落
料功能。
4.下模由定子座、支架和支撑构件等组成,它们之间由螺栓和垫圈固定,形成复合模具的下表面。
三、冲孔落料复合模具优点
1.高体积效率:冲孔落料复合模具能够实现冲孔落料一体化,不需要
多种模具,能够有效减少模具组合,提高机械组合效率,节省生产空间,
提高生产效率。
2.高加工精度:冲孔落料复合模。
冲孔落料复合模具设计

冲孔落料复合模具设计一、引言冲孔落料是一种常见的金属板材加工方式,可以通过冲孔和落料来实现对材料上的孔洞和缺口的加工。
为了提高生产效率和产品质量,设计一种冲孔落料复合模具是十分关键的。
二、模具结构设计1.上模上模采用较硬的材料,如合金钢等,以提高其耐磨性和耐腐蚀性。
上模一般设计为多个冲孔模块的集合,可以根据产品的设计要求进行选择。
冲孔孔径的大小和形状需要根据产品的要求进行设计,一般可以通过拉伸槽的装置来调整冲孔的位置和角度。
2.下模下模采用较软的材料,如塑料或橡胶等,以减少对下方的金属板材的损伤。
下模的形状需要与上模的冲孔模块相匹配,以保证冲孔的准确性和质量。
下模可以通过气动或液动装置来实现冲孔和落料的动作,可以根据产品的要求进行调整。
三、模具工作原理当上模和下模合并时,上模的冲孔模块和下模的落料形状之间会形成一个工作腔。
通过施加压力,上模以一定的速度向下冲击,使上模冲孔模块与金属板材接触,将孔洞冲出。
同时,下模的形状会顶住冲孔孔洞,使其成为落料形状。
当冲孔和落料动作完成后,上模和下模分开,取出已经冲孔和落料的金属板材。
四、模具优化设计在冲孔落料复合模具设计过程中,要考虑以下几个方面的优化设计。
1.优化上模的冲孔模块排列方式,使得冲孔过程更加均匀、稳定,并减少模具的使用次数和更换时间。
2.优化下模的形状和结构,通过减小落料形状的尺寸和加工槽口的数量,以提高产品的加工精度和成品率。
3.采用先进的材料和工艺,如表面处理和涂层等,以提高模具的耐用性和寿命。
4.考虑模具的维修和维护问题,设计合理的拆卸和安装装置,以便进行模具的更换和维修。
五、结论冲孔落料复合模具的设计是一项复杂而重要的工作。
通过优化设计模具的结构和工作原理,可以提高产品的加工效率和质量,并减少对模具的使用和更换次数。
因此,在实际设计中,需要综合考虑材料性能、工艺要求和经济效益,以达到最佳的设计效果。
落料冲孔复合模具设计
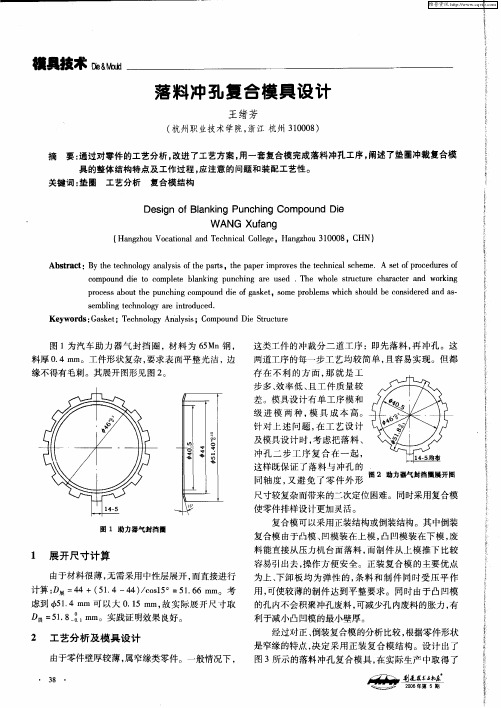
经过对正 、 倒装复合模 的分析 比较 , 根据零件形状 是窄缘的特点, 决定采用正装复合模结构 。设计 出了
图3 所示的落料冲孔复合模具, 在实 际生产 中取得 了
、 ‘ O牛 幂 w 0 ^} }
维普资讯
D 梗 具 技术 i e &
De in o a kn n hn mp u d Di sg fBln ig Pu c ig Co o n e W ANG f n Xu a g
( nzo oai a adTcncl ol e Haghu30 0 ,C N) HaghuV ctnl n ehia C lg , nzo 08 H o e 1
维普资讯
棱其技术 &
落料冲孔复合模具设计
王绪芳
( 杭州职业技术学院, 浙江 杭州 300 ) I 1 8 0 摘 要: 通过对零件的工艺分析, 改进了工艺方案。 用一套复合模完成落料冲孔工序 , 阐述了垫圈冲裁复合模
具 的整 体 结构特 点及 工作 过 程 , 注意 的 问题和 装 配工艺 性 。 应 关 键词 : 圈 垫 工 艺分析 复合模 结构
p o e sa o tt e pu c ng c mp u d de o a ke ,s me p o lmswh c h u d b o sd r d a d a — r c s b u h n hi o o n i fg s t o r b e i h s o l ec n i e e n s
定 在下模 板上 。为保 证零 件 的设计 要求 , 凸模 l 略 4应
9 进入凹模 5时 , 先落料再继续下行时完成 冲孔工序 ; 压力 机此 时恰 好 到 达 下 死 点 。 中 间废 料 由打 杆 7打
出。当上模返回时 , 上卸料 板 3在橡胶 1 弹力作用 1 下, 把边缘废料从 凸凹模 9上卸下 , 同时下卸料板把工
冲孔落料弯曲复合模具设计

1 绪论改革开放以来,随着国民经济的高速发展,工业产品的品种和数量的不断增加,更新换代的不断加快,在现代制造业中,企业的生产一方面朝着多品种、小批量和多样式的方向发展,加快换型,采用柔性化加工,以适应不同用户的需要;另一方面朝着大批量,高效率生产的方向发展,以提高劳动生产率和生产规模来创造更多效益,生产上采取专用设备生产的方式。
模具,做为高效率的生产工具的一种,是工业生产中使用极为广泛与重要的工艺装备。
采用模具生产制品和零件,具有生产效率高,可实现高速大批量的生产;节约原材料,实现无切屑加工;产品质量稳定,具有良好的互换性;操作简单,对操作人员没有很高的技术要求;利用模具批量生产的零件加工费用低;所加工出的零件与制件可以一次成形,不需进行再加工;能制造出其它加工工艺方法难以加工、形状比较复杂的零件制品;容易实现生产的自动化的特点。
2 弯曲件的工艺分析图2—1 零件图如图2—1所示零件图。
生产批量:大批量;材料:LY21-Y;该材料,经退火及时效处理,具有较高的强度、硬度,适合做中等强度的零件。
尺寸精度:按公差IT14查出来的。
尺寸精度较低,普通冲裁完全能够。
其他的形状尺寸均未标注公差,属自由尺寸,可安IT14级确定工件的公差。
经查公差表,各尺寸公差为:Ø90 +0。
3020 0-0.52 600-0.52工件结构形状:制件需要进行落料、冲孔、弯曲三道基本工序,尺寸较小。
结论:该制件可以进行冲裁制件为大批量生产,应重视模具材料和结构的选择,保证磨具的复杂程度和模具的寿命。
3 确定工艺方案及模具的结构形式根据制件的工艺分析,其基本工序有落料、冲孔、弯曲三道基本工序,按其先后顺序组合,可得如下几种方案;(1)落料——弯曲——冲孔;单工序模冲压(2)落料——冲孔——弯曲;单工序模冲压。
(3)冲孔——落料——弯曲;连续模冲压。
(4)冲孔——落料——弯曲;复合模冲压。
方案(1)(2)属于单工序模冲裁工序冲裁模指在压力机一次行程内完成一个冲压工序的冲裁模。
冲孔落料复合模设计

模具设计计算书零件简图:如图1 所示生产批量:小批量材料:Q235材料厚度:0.5mm未标注尺寸按照IT10级处理, 未注圆角R2.(图1)一、工艺方案:由零件图可知,该零件包含冲孔和落料两个工序。
形状较为规则,尺寸较小,精度要求IT10。
材料低硬度。
二、计算冲裁压力、压力中心和选用压力机1、排样方式的确定及材料利用率计算(1)排样方式的确定查《冲压手册》表2-17,两工件之间按矩形取搭边值b=2.5mm,侧边取a=2.5mm。
进料步距为h=12+2.5=14.5mm;条料宽度为B=(D+2×a)0-Δ,查《冲压手册》表2-19得,条料宽度偏差Δ=0.4mm,冲裁件垂直于送料方向的尺寸为D=45mm,则B=(D+2×a)0-Δ=(45+2×2.5)0-0.4=500-0.4mm(2)材料利用率计算板料规格选用0.5×1000×2000mm;采用纵裁时:每板的条数 n1=1000/40=25条每条的工件数 n2=2000/12.5=160件每板的工件数 n=n1×n2=25×160=4000个利用率为:η=4000×10×35/(1000×2000)×100%=70%采用横裁时:每板的条数: n1=2000/40=50条每条的工件数: n2=1000/12.5=80件每板的工件数: n=n1×n2=50×80=4000个利用率:η=4000×10×35/(1000×2000)×100%=70% 经计算横裁.纵裁时板料利用率相同都为70%,故采用横裁或纵裁都可以. 排样图如下图所示:2、计算冲裁力、卸料力:查表得材料Q235的抗张强度为δb=400MPa;落料尺寸:L1=90;冲圆形孔尺寸:L2=9.42,冲方形孔尺寸:L3=32 (1)落料力F落=L1tδb=90×0.5×400=18×103 N(2)冲孔力F2=L2tδb=9.42×0.5×400=1884 NF3=L3tδb=32×0.5×400=6400 NF冲=F2+F3=8284 N(3)冲孔推件力F推=nK推F冲(查表计算n=16 k=0.045 F冲=8284N)F推=16×0.04×8284=5964.5 N (4)落料时的卸料力F卸=k卸×F落=0.03×18×103=540 N冲床总压力F总=F冲+F推+F落+F卸=32.789×103 N3、确定压力中心计算出各个凸模的冲裁周边长度:L1=3.14×5=15.7mmL2=2×6+2×4=20mmL3=L2=20mmX1=55-8=47mmX2=18+10-2.5=25.5mmX3=10+10-2.5=17.5mmY1=Y2=Y3=15mm对整个工件选定x、y坐标轴,代入公式:X0=(L1X1+L2X2+L3X3)/(L1+L2+L3)=23.93mmY0=(L1Y1+L2Y2+L3Y3)/(L1+L2+L3)=15mm压力中心在工件中的位置是距右边为23.93-10=13.93mm,距中间15-10=5mm。
落料拉深冲孔复合模毕业设计
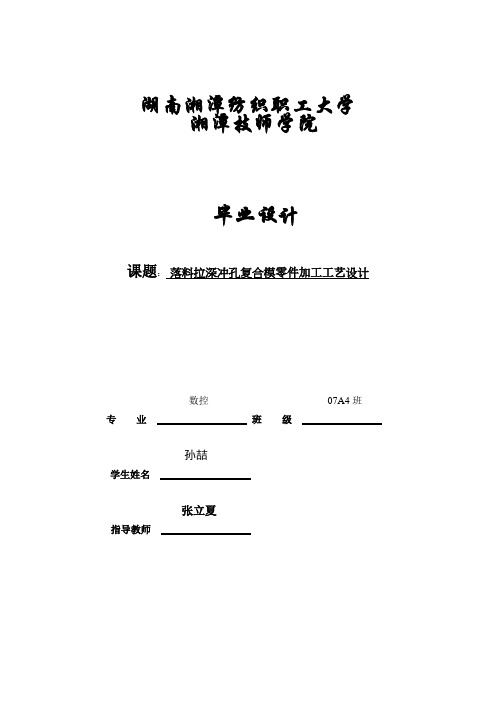
湖南湘潭纺织职工大学湘潭技师学院毕业设计课题:落料拉深冲孔复合模零件加工工艺设计数控07A4班专业班级孙喆学生姓名张立夏指导教师目录绪论任务书 (3)第一章、分析理解及备CAD图 (4)第二章、本次设计的基本内容 (10)一、冲裁机械运动 (10)二、拉深模具的机械运动 (11)三、模具的工作原理 (11)第三章、主要零件加工工艺分析 (14)一、落料凹模 (14)二、落料拉深凸凹模 (17)三、冲孔凸模 (21)四、拉深冲孔凸凹模 (23)五、凸模固定板 (28)设计总结 (31)参考文献 (32)绪论加入世贸组织后,我国机械制造业迎来了空前的发展机遇,我国正逐步变成世界制造中心。
为了增强竞争能力,中国制造业开始广泛使用先进的数控技术、模具技术、二十一世纪机械制造业的竞争,其实是数控技术的竞争。
随着数控技术,模具技术的迅速发展及数控机床的急剧增长,我国机械企业急需大批数控机床编程、操作等技术人才,体现现代技术高速发展的情况。
随着科学技术的飞速发展,社会对产品多样化的要求日益强烈,产品更新越来越快,多品种、批量生产的比重明显增加;同时,激烈的市场竞争要求产品研制生产周期越来越短,形状复杂的零件越多,精度要求也越高。
传统的加工设备和制造方法难于适应这种多样化、柔性化与复杂形状的高效高质量加工要求。
本内容反映了理论密切结束实际,分析重于计算,贯穿了质量、生产率和经济性的辩证关系,在能力培养上应力图由浅入深,由表及里。
强调科学分析实验验证和择优决策的能力培养。
必须重视生产实习和现场教学等实践性环节。
密切联系生产实践,在实践中发现问题,提出关键之所在并找到有效解决问题解决问题的措施,从而加深课程内容的理解,在实践中强化对所学知识的应用。
数控技术应用专业毕业设计任务书设计题目:拉深冲孔复合模主要零件的设计与制造工艺姓名:孙喆班级:07A4指导老师:张立夏一、要求:理解拉深冲孔复合模的结构特点与工作过程。
二、根据落料拉深冲孔复合模的总装图(见附件)设计其主要零件的零件图,包括:冲孔凸模、拉深冲孔凸凹模、落料拉深凸凹模以及落料凹模。
垫圈落料冲孔复合模具设计

垫圈落料冲孔复合模具设计一、设计原则1.尺寸精确:模具设计的尺寸要精确,以确保最后制作出的垫圈符合规格要求。
2.结构紧凑:模具的结构要简单紧凑,以提高生产效率和质量。
3.制造成本低:要考虑到模具的制造成本,选用合适的材料和加工工艺,以降低生产成本。
4.使用寿命长:模具的设计要考虑到使用寿命,尽可能延长模具的寿命,避免频繁更换。
二、构造设计1.上模和下模:上模和下模是构成模具的主要部分,上模用于冲孔,下模用于落料。
上模和下模的尺寸要与垫圈的规格相匹配,确保加工出符合要求的垫圈。
2.垫圈导向机构:为了确保垫圈在冲压过程中位置准确,需要设计导向机构来限制垫圈的运动方向。
导向机构可以采用导向销、导向板等方式。
3.冲孔机构:冲孔是模具的主要功能之一,冲孔机构需要设计合适的冲头和冲孔座,确保冲出的孔径和位置准确。
4.落料机构:落料机构用于将原料板料送入模具,落料机构需要设计合适的导向和定位装置,确保原料板料的位置准确。
5.排渣机构:在冲孔过程中会产生大量的废料和渣滓,需要设计排渣机构,将废料排出,保持模具的干净。
6.压紧机构:在落料和冲孔过程中需要采用压紧机构,将模具和板料固定在一起,确保加工精度和质量。
三、工艺参数1.材料选择:模具的材料应选择具有较高硬度和韧性的特点,常用的材料有合金工具钢、高速钢等。
2.加工精度:模具加工的精度要求要与垫圈的规格相匹配,冲孔精度要小于垫圈的公差要求。
3.加工表面处理:为了延长模具的使用寿命,可以对模具进行表面处理,如镀硬铬、镀涂层等。
4.模具安装:模具的安装要牢固可靠,确保加工过程中没有松动和位移。
总结:垫圈落料冲孔复合模具设计的关键是尺寸精确、结构紧凑、制造成本低以及使用寿命长等。
通过合理的构造设计和工艺参数,可以实现高效、精确的垫圈制造。
- 1、下载文档前请自行甄别文档内容的完整性,平台不提供额外的编辑、内容补充、找答案等附加服务。
- 2、"仅部分预览"的文档,不可在线预览部分如存在完整性等问题,可反馈申请退款(可完整预览的文档不适用该条件!)。
- 3、如文档侵犯您的权益,请联系客服反馈,我们会尽快为您处理(人工客服工作时间:9:00-18:30)。
集美大学课程设计说明书题目:冲孔落料复合模具设计姓名:蓝丽华专业:材料成型及控制工程班级:材料1111班学号:2011717001指导老师:黄清民樊晓红2 0 1 5 年1 月14 日集美大学机械与能源工程学院专业课程设计任务书——机械与能源工程学院设计题目:冲孔落料复合模设计任务:设计一简单冲压零件,并根据该零件设计一副冲压模具。
制件年产量:50万件完成的任务:1.冲压工艺过程卡一份;2.产品零件图一份;3.冲压模具装配及模具成形零件工程图各一份;4.设计说明书一份。
时间安排:1. 借资料、产品的结构设计及绘制零件图;(1.5天)2.确定零件冲压工艺方案,填写冲压工艺过程卡;(1天)3.零件工艺性分析及冲压工艺方案的确定;毛坯排样方案设计及材料利用率计算;冲裁力及压力中心计算;选择压力设备;模具总体结构设计,包括送料方式、卸料和出件方式、凹模板外形尺寸的计算、其它模板尺寸的确定和模架的选择;凸、凹模零件设计,包括刃口尺寸计算、凸模结构及凹模型腔结构设计;卸料和顶件装置设计;模具结构三维设计。
(4天)4.绘制模具结构装配图、模具成型零件工程图;(2.5天)5.编写设计说明书;(2天)6.答辩。
(1天)参考书目:[1]翁其金.冲压工艺及冲模设计[M].北京:机械工业出版社,2004[2]黄毅宏.模具制造工艺[M].北京:机械工业出版社,2004[3]王新华.冲模结构图册[M].北京:机械工业出版社,2004[4]陈锡栋.实用模具设计简明手册[M].北京:机械工业出版社,2001[5]郑家贤.冲压工艺与模具设计实用技术[M].北京:机械工业出版社,2005[6]杨玉英.实用冲压工艺模具设计手册[M].北京:机械工业出版社,2005指导教师:黄清民樊晓红2015年1月14 日机械与能源工程学院材料级1111 班学生:蓝丽华学号:2011717001目录一、零件工艺性分析 (2)1、材料分析 (2)2、结构分析 (2)3、精度分析 (2)二、冲裁工艺方案的确定 (3)三、零件工艺计算 (4)1、刃口尺寸计算 (4)2排样方式确定及冲裁力计算 (5)3、压力中心计算 (8)四、模具整体设计 (9)五、主要零部件设计 (10)1、工作零件的设计 (10)2、定位零件的设计 (11)3、出件装置的设计 (11)4、卸料部分的设计 (11)5、模架及其它零部件的设计和选用 (12)6、卸料装置中弹性元件的计算 (12)7、模具各部分材料的选用 (13)六、冲压设备选定 (15)七、参考资料 (16)八、设计小结 (17)一、零件工艺性分析工件为图1所示的落料冲孔件,材料为Q235钢,材料厚度1mm ,年生产量为30万件,生产批量为大批量。
工艺性分析内容如下:图1-1 工件尺寸图1.材料分析Q235为普通碳素结构钢,具有较好的冲裁成形性能。
抗拉强度b σ≥295MPa ;屈服强度s σ≥175MPa ;伸长率δ%≥30%;断面收缩率ψ≥60% 符合冲裁要求。
2. 结构分析零件结构简单对称,对冲裁加工较为有利。
零件中部有一孔,对角上共4个孔,孔的最小尺寸为7mm ,满足冲裁最小孔径min d ≥ 1.5mm 0.1=t 的要求。
另外,经计算异形孔距零件外形之间的最小孔边距为11.5mm ,满足冲裁件最小孔边距min l ≥ 2.25mm 5.1=t 的要求。
所以,该零件的结构满足冲裁的要求。
3. 精度分析零件上采用制造精度为ST3,则各尺寸的尺寸公差为0.0550±,0084.0-62,00.058-7,0.0484+,0.0536±二、冲裁工艺方案的确定零件为一落料冲孔件,可提出的加工方案如下: 方案一:先落料,后冲孔。
采用两套单工序模生产。
方案二:落料—冲孔复合冲压,采用复合模生产。
方案三:冲孔—落料连续冲压,采用级进模生产。
方案一模具结构简单,但需两道工序、两副模具,生产效率低,零件精度较差,在生产批量较大的情况下不适用。
方案二只需一副模具,冲压件的形位精度和尺寸精度易保证,且生产效率高。
尽管模具结构较方案一复杂,但由于零件的几何形状较简单,模具制造并不困难。
方案三也只需一副模具,生产效率也很高,但与方案二比生产的零件精度稍差。
欲保证冲压件的形位精度,需在模具上设置导正销导正,模具制造、装配较复合模略复杂。
所以,比较三个方案欲采用方案二生产。
现对复合模中凸凹模壁厚进行校核,由符合模最小壁厚校核公式δ)( 2.5~2.0h ≥ 1≥δ时当材料厚度为1mm 时,可查得凸凹模最小壁厚为3.75mm ,现零件上的最小孔边距为6.5mm ,所以可以采用复合模生产,即采用方案二。
同时工件平面度要求不高,因此采用倒装复合模。
三、零件工艺计算1.刃口尺寸计算根据零件形状特点,刃口尺寸计算可采用配作法。
可查[]1表5-3可查得凸、凹模最小间隙Zmin=0.10mm ,最大间隙Zmax=0.140mm ,(1)落料件尺寸的基本计算以凹模为基准1)凹模磨损变大的是0.0550±,按一般落料凹模尺寸公式计算4max A )x (∆+-=ΔD D=025.00)01.050(+-=025.009.49+落料凸模刃口尺寸,按凹模实际尺寸配制,并保证最小间隙Zmin=0.10mm 。
凸模刃口尺寸按凹模实际尺寸配制,保证双面间隙值为Zmin-Zmax(2)冲孔尺寸的基本计算以凸模为基准1)凸模磨损变小的是0.04807+,0.05015+,按一般冲孔凸模尺寸公式计算4in A1)x (∆++=ΔD D m=013.00)05.07(++=013.0005.7+4in A2)x (∆++=ΔD D m=013.00)05.015(++=013.0005.15+(3)中心距:孔心距计算基本公式4L L d1∆+= 尺寸1mm .040±mm )4/1.040(±=L=40.00±0.025 尺寸1mm .003±mm )4/1.030(±=L=30.00±0.025冲孔凹模刃口尺寸,按凸模实际尺寸配制,并保证最小间隙Zmin=0.10mm 。
凹模刃口尺寸按凸模实际尺寸配制,保证双面间隙值为Zmin-Zmax2.排样方式确定及冲裁力计算分析零件形状,应采用单直排的排样方式,排样方式有图。
图3-1排样方式有图现选用1000mm ×1000 mm 的钢板,则需计算采用不同的裁剪方式时,每张板料能出的零件总个数。
(1)裁成宽59mm 、长1000mm 的条料,则一张板材能出的零件总个数为042161527.51000591000=⨯=⎥⎦⎤⎢⎣⎡⨯⎥⎦⎤⎢⎣⎡。
取两工件间的最小搭边:a 1=1mm ,侧面搭边值:a=2mm 。
其具体排样图如图3所示:查[]2表5-15图3-2零件排样图该模具采用倒装式复合模,拟选弹性卸料,刚性出件,冲压力的相关计算见下表。
表1-1 排样冲压力计算表3.压力中心计算零件外形为对称件,所以该零件的压力中心就是零件外形中心线的交点。
如图:图3-3模具压力中心确定四、模具总体设计(1)模具类型的选择由冲压工艺性分析可知,采用复合冲压,所以模具类型为冲孔落料复合模。
(2)条料定位装置的选择该模具采用的是条料,控制条料的送进方向采用导料销无侧压装置。
控制条料的送进步距采用固定挡料销来定距。
(3)卸料、出件方式的选择倒装式复合模,采用弹性卸料,刚性出件。
(4)导向方式的选择为方便安装调整,同时为送料的方便,故采用中间导柱模架。
压力中心五、主要零部件设计1、工作零件的设计(1)落料凹模凹模的厚度:H=kb (≥15mm )=0.35⨯50=17.5mm(参考文献[]1表3-13)取整25 凹模的壁厚:C=(1.5~2)H (≥30~40mm ) 凹模宽度:B=b+2c=50+2⨯40=130mm 凹模长度:L=212s s + =26+2⨯40 =106(查参考文献[]1表3-12取得2s =40)凹模厚度:由上计算厚度20mm ,将凹模做成薄板形式并加空心垫板后厚度取10mm 。
并将B 和L 值取整,得凹模轮廓:130x106x25mm(2)凹凸模高度:L=1h +h+2h =20+21+10=51mm如下图式中:1h 为凹凸模固定板厚度(查参考文献[]1表3-13初选130⨯106⨯20mm ),2h 弹性卸料板厚度(初选130⨯106⨯10mm ),h 为增加高度(冲压时橡胶高20mm+凹凸模高过卸料板1mm=21mm )。
(3)冲孔凸模结合工件外形考虑加工,将凸模设计成直通式凸模,与凸模固定板按H7/m6配合。
其总长度:L=3h +4h +5h =10+15+20=45mm式中各参数如上图中: 3h 凹模厚度、4h 空心垫板厚度、5h 凸模固定板厚。
采用凸缘式凸模。
图5-1凸缘式凸模2、定位零件的设计 (1)挡料销:因模具采用橡胶弹性卸料,且卸料橡胶安装高度21mm 较高。
为方便挡料,采用橡胶弹顶挡料销装置。
挡料销需高出卸料板3mm ,卸料板厚15mm ,故取挡料销H=18mm 。
挡料销与卸料板采用H9/g9间隙配合。
(2)导料销:使用两个导料销,采用橡胶弹顶导料装置。
导料销需高出卸料板6~8mm ,卸料板厚15mm ,故取导料销H=21mm 。
挡料销与卸料板采用H9/g9间隙配合。
3、出件装置的设计采用刚性出件,由推杆直接推动推件块,将凹模内的工件推出。
根据推杆连接的各板高度,和模柄孔径查参考文献[]4附录J3取推杆:A 12X140 JB/T 7650.1-2008。
推件块的周界尺寸和零件的周界尺寸相同,考虑凹模厚度、空心垫板厚度、及推杆安装、凹模修模量等因素,取高度16mm 。
4、卸料部分的设计卸料板:由挡料销和导料销安装高度:选用卸料板轮廓125⨯125⨯15mm 卸料螺钉:模具采用橡胶弹性卸料橡胶由上可知橡胶孔直径12.5mm ,查标准取M8X60 JB/T 7650.5-2008卸料钉尾部有足够的形成空间,卸料螺钉拧紧后,应使卸料板超出凹凸模端面1mm ,有误差时通过在螺钉与卸料板之间安装垫片来调节。
5、模架及其它零部件的设计和选用该模具的闭和高度:H闭=H上模座+H垫+L+H+H下模座-h2=40+8+45+65+50-1=208mm式中:L为凸模长度;H凹凸模厚度;H垫垫板;h2凸模进入凹凸模的深度。
查文献[]3表9-3,可得模架规格为140×125(L×B),从而得一下零件规格,如下表。
表5-1 其余模具零件规格表(1)冲模中用到的紧固螺钉主要是螺钉和销钉,螺钉起连接紧固作用,销钉起定位作用,采用8个M10的内六角螺钉,4个导正销1个定位销,4个紧固销钉紧固上模和下模部分。