车削加工参数
车削切削参数计算

车削切削参数计算包括计算切削线速度、主轴转速、金属去除率、净功率、加工时间以及特定切削力。
这些参数的计算公式如下:
1. 切削线速度:Vc = πDn/1000(m/min),其中D为工件或刀具直径(mm),n为主轴转速(rpm)。
2. 主轴转速:n = 1000Vc/πD(rpm),其中D为工件或刀具直径(mm),Vc为切削线速度(m/min)。
3. 金属去除率:Q = F×Vc×S×η,其中F为切削截面积(mm^2),Vc为切削线速度(m/min),S为切削行程(mm),η为刀具寿命(min)。
4. 净功率:Pc = Q×Z/60,其中Q为金属去除率(cm^3/min),Z 为机械效率。
5. 加工时间:Tc = T×n,其中T为切削时间(min),n为主轴转速(rpm)。
6. 特定切削力:Kc = F×η/S,其中F为切削截面积(mm^2),η为刀具寿命(min),S为切削行程(mm)。
这些公式可以用来计算车削过程中的切削参数,有助于优化加工过程和提高生产效率。
车削加工

40
46 52 57 63
63
72 81 89 97
100
115 130 140 155
160
185 210 230 250
250
290 320 360 400
400
460 520 570 630
车削
车削
ID 1 2 3 4 5 6 7 加工方法 自动气割、带锯或圆盘锯割断 切断(车) 切断(铣) 切断(砂轮) 车削外圆(粗车) 车削外圆(半精车金属) 车削外圆(半精车非金属)
车刀
2.按结构可分为: ① 整体式车刀 刀头部分和刀杆部分均为同一种材料。用作整体式车刀的刀具材料一般是 整体高速钢 ② 焊接式车刀 刀头部分和杆部分分属两种材料。即刀杆上镶焊硬质合金刀片,而后经 刃磨所形成的车刀。 ③ 机械夹固式车刀 刀头部分和刀杆部分分属两种材料。它是将硬质合金刀片用机械夹固的方 法固定在刀杆上的, 。它又分为机夹重磨式和机夹不重磨式两种车刀。两者区 别在于:后者刀片形状为多边形,即多条切削刃,多个刀尖,用钝后只需将 刀片转位即可使新的刀尖和刀刃进行切削而不须重新刃磨;前者刀片则只有 一个刀尖和一个刀刃,用钝后就必须的刃磨。
9
11 13 15
13
16 19 22
21
25 30 35
33
39 46 54
52
62 74 87
84
100 120 140
130
160 190 220
210
250 300 350
>120~180
>180~250 >250~315 >315~400 >400~500
18
20 23 25 27
25
不锈钢的车削参数

1 什么是不锈钢?通常,人们把含铬量大于12%或含镍量大于8%的合金钢叫不锈钢。
这种钢在大气中或在腐蚀性介质中具有一定的耐蚀能力,并在较高温度(>450℃)下具有较高的强度。
含铬量达16%~18%的钢称为耐酸钢或耐酸不锈钢,习惯上通称为不锈钢。
钢中含铬量达12%以上时,在与氧化性介质接触中,由于电化学作用,表面很快形成一层富铬的钝化膜,保护金属内部不受腐蚀;但在非氧化性腐蚀介质中,仍不易形成坚固的钝化膜。
为了提高钢的耐蚀能力,通常增大铬的比例或添加可以促进钝化的合金元素,加Ni、Mo、Mn、Cu、Nb、Ti、W、Co等,这些元素不仅提高了钢的抗腐蚀能力,同时改变了钢的内部组织以及物理力学性能。
这些合金元素在钢中的含量不同,对不锈钢的性能产生不同的影响,有的有磁性,有的无磁性,有的能够进行热处理,有的则不能热处理。
由于不锈钢所具有的上述特性,越来越广泛地应用于航空、航天、化工、石油、建筑和食品等工业部门及日常生活中。
所含的合金元素对切削加工性影响很大,有的甚至很难切削。
2 不锈钢可分为哪几类?不锈钢按其成分,可分为以铬为主的铬不锈钢和以铬、镍为主的铬镍不锈钢两大类。
工业上常用的不锈钢一般按金相组织分类,可分为以下五大类:1. 马氏体不锈钢:含铬量12%~18%,含碳量0.1%~0.5%(有时达1%),常见的有1Cr13、2Cr13、3Cr13、4Cr13、1Cr17Ni2、9Cr18、9Cr18MoV、30Cr13Mo等。
2. 铁素体不锈钢:含铬量12%~30%,常见的有0Cr13、0Cr17Ti、0Cr13Si4NbRE、1Cr17、1Cr17Ti、1Cr17M02Ti、1Cr25Ti、1Cr28等。
3. 奥氏体不锈钢:含络量12%~25%,含镍量7%~20%(或20%以上),最典型的代表是1Cr18Ni9Ti,常见的还有00Cr18Ni10、00Cr18Ni14Mo2Cu2、0Cr18Ni12Mo2Ti、0Cr18Ni18Mo2Cu2Ti、0Cr23Ni28M03Cu3Ti、1Cr14Mn14Ni、2Cr13Mn9Ni4、1Cr18Mn8Ni5N等。
车削加工

第一章车削加工概述车削加工是机械加工中最基本的一种加工方法,它所用的机床是车床,到目前为止已出现了卧式车床、立式车床、多刀车床、自动及半自动车床、仪表车床、数控车床等多种类型的车床。
所用的刀具为车刀,也可以用钻头、滚花刀、铰刀等,利用这些切削刀具与工件的一系列相对运动,可以完成多重切削。
车削加工的加工范围很广,可以加工出各种类型的带有旋转体表面的零件,如内外圆柱面、内外圆锥面、内外成形面、内外螺旋面等,其经济精度达到IT11~IT06,表面粗糙度为Ra12.5µm~0.8µm。
另外,在车床上安装上夹具和附件还可以进行镗孔、铣削、磨削、研磨、抛光等。
随着数字控制技术的发展,出现了数控车床与车削加工中心等现代化的制造设备,虽然目前所占的比例较少,但它以高柔性、高效率、高精度等传统加工所不能及的独特优点,正逐渐成为现代机械加工的重要技术装备之一,占据着越来越重要的地位。
1.1 机械类专业一、机械类专业实习纲要1、教学要求1) 基本知识①了解车削加工基本概念、设备、刀具、工、夹、量具、切削运动和切削用量适用范围及地位;②了解普通车床及其型号、结构、组成、作用、传动系统等并掌握其操作技术;③掌握车刀的组成,形状参数,材料性能及适用条件;④了解车削加工工件的安装夹持方法及所用附件,掌握三爪卡盘的应用;⑤了解车削加工工件的测量方法及量具并掌握其使用技术;⑥掌握基本车削加工方法,如车外圆、端面、锥面、钻孔、滚花、螺纹的加工工艺方法与技术;2)基本技能①熟练正确操作车床,掌握车床各手柄用途;②能独立完成车工作业件的加工;③掌握车工工具、量具的使用方法,正确测量工件;2、教学重点1)切削用量三要素的合理选择;2)车刀的几何参数;3)车床的操作;4)车削加工工艺过程;3、教学难点1)零件加工及操作;2)零件的测量准确程度;3)正确使用各类车刀;二、机械类专业实习总体安排三、机械类专业实习具体安排1、第一天1)上午 7:30~9:00 理论知识讲解(90′)车床与车削一、概述金属切削机床是用切削的方法将金属毛坯加工成机械零件的机器,是制造机器的机器,故又称为“工作母机”,一般简称机床。
不锈钢车削参数

不锈钢车削参数不锈钢车削参数是指在车削加工过程中,针对不锈钢材料的特性和要求所设定的一系列切削参数。
这些参数对于保证加工质量和提高生产效率具有重要意义。
以下是一些建议的不锈钢车削参数:1. 切削速度(Vc):切削速度是刀具在旋转时与工件接触点的速度。
对于不锈钢材料,切削速度应适当降低,以防止刀具过热和磨损。
一般推荐切削速度为20-60m/min。
2. 进给量(f):进给量是指刀具在每次切削行程中沿工件轴向移动的距离。
对于不锈钢材料,进给量应适当降低,以减小刀具磨损和切削力。
一般推荐进给量为0.1-0.3mm/r。
3. 切削深度(ap):切削深度是指刀具在每次切削行程中切入工件的深度。
对于不锈钢材料,切削深度应适当降低,以减小刀具磨损和切削力。
一般推荐切削深度为0.1-0.5mm。
4. 刀具前角(γo):刀具前角是指刀具主切削刃与工件表面的夹角。
对于不锈钢材料,刀具前角应适当增大,以提高切削性能和减少刀具磨损。
一般推荐前角为10-20°。
5. 刀具后角(αo):刀具后角是指刀具主切削刃与工件表面的夹角。
对于不锈钢材料,刀具后角应适当增大,以提高切削性能和减少刀具磨损。
一般推荐后角为8-12°。
6. 切削液:不锈钢车削过程中,应使用适当的切削液来冷却和润滑刀具和工件,以降低切削温度和减少刀具磨损。
常用的切削液有水溶性切削液、油溶性切削液和乳化液等。
7. 刀具材质:不锈钢车削过程中,应选择具有良好耐磨性和抗腐蚀性的刀具材质,如硬质合金、陶瓷和高速钢等。
8. 机床刚性:不锈钢车削过程中,应选择具有较高刚性的机床,以保证加工精度和表面质量。
9. 工艺路线:不锈钢车削过程中,应根据工件的形状和尺寸选择合适的工艺路线,以减少切削力和热量对加工质量的影响。
总之,不锈钢车削参数的选择应根据具体的工件材料、形状和尺寸以及加工要求进行综合考虑,以达到最佳的加工效果。
20号低碳钢车削参数

20号低碳钢车削参数
低碳钢的车削参数会受到多种因素的影响,包括材料的硬度、刀具的类型和几何形状、加工条件以及所需的加工质量等。
以下是一些常见的20 号低碳钢车削参数范围供参考:
1. 切削速度(Vc):通常在50 至150 米/分钟之间,具体速度取决于刀具材料和工件的硬度。
2. 进给量(f):一般在0.1 至0.5 毫米/转之间,进给量的选择要考虑刀具的耐磨性和加工表面质量。
3. 切削深度(ap):通常在1 至5 毫米之间,具体深度取决于工件的直径和加工要求。
需要注意的是,以上参数仅为一般范围,实际的车削参数应根据具体的加工情况进行调整和优化。
在选择车削参数时,建议参考刀具制造商的建议、实际加工经验以及工件的要求,以获得最佳的加工效果和刀具寿命。
此外,还应注意刀具的选用、冷却液的使用以及加工过程中的安全措施等方面,以确保高效、安全地进行车削加工。
如果你有具体的车削需求,建议咨询专业的机械加工工程师或相关技术人员,以获得更准确和适合的参数建议。
车削参数及刀具角度

第二章 金属切削过程2-1 什么是切削用量三要素?在外圆车削中,它们与切削层参数有什么关系? 答:切削用量三要素是指切削速度v 、进给量f 、背吃刀量a p (切削深度)。
在外圆车削中,它们与切削层参数的关系是:sin /sin D rD p r D ph f b a A fa κκ===切削层公称厚度: 切削层公称宽度: 切削层公称横截面积:2-2 确定外圆车刀切削部分几何形状最少需要几个基本角度?试画图标出这些基本角度。
答:确定外圆车刀切削部分几何形状最少需要7个基本角度:前角、后角、主偏角、副偏角、副前角、副后角和刃倾角,这些基本角度如下图所示(其中副前角、副后角不做要求)。
2-3 试述刀具标注角度和工作角度的区别。
为什么车刀作横向切削时,进给量取值不能过大?答:刀具标注角度是在静态情况下在刀具标注角度参考系中测得的角度;而刀具工作角度是在刀具工作角度参考系中(考虑了刀具安装误差和进给运动影响等因素)确定的刀具角度。
车刀作横向切削时,进给量取值过大会使切削速度、基面变化过大,导致刀具实际工作前角和工作后角变化过大,可能会使刀具工作后角变为负值,不能正常切削加工2-4 刀具切削部分的材料必须具备哪些基本性能?答:(P24)(1) 高的硬度和耐磨性;(2) 足够的强度和韧性;(3) 高耐热性;(4) 良好的导热性和耐热冲击性能;(5)良好的工艺性。
2-5 常用的硬质合金有哪几类?如何选用?答:(P26)常用的硬质合金有三类:P类(我国钨钴钛类YT),主要用于切削钢等长屑材料;K类(我国钨钴类YG),主要用于切削铸铁、有色金属等材料;M类(我国通用类YW),可以加工铸铁、有色金属和钢及难加工材料。
2-6 怎样划分切削变形区?第一变形区有哪些变形特点?答:切削形成过程分为三个变形区。
第一变形区切削层金属与工件分离的剪切滑移区域,第二变形区前刀面与切屑底部的摩擦区域;第三变形区刀具后刀面与已加工表面的摩擦区域。
CBN刀具车削加工淬火钢件的切削参数范围

CBN刀具车削加工淬火钢件的切削参数范围CBN刀具车削加工淬火钢件,已经是非常普遍的一种现象,采用CBN刀具以车代磨加工淬火钢件效率成倍提高,而且干式切削,车削加工过程中不添加切削,绿色环保,更适合制造业的绿色制造。
CBN刀具虽然广泛应用于淬火钢件的车削加工,但很多工人还不太了解CBN刀具的切削参数,经常刚上去就出现崩刀、打刀现象。
主要就是不了解CBN刀具的切削参数,用硬质合金刀具的参数测试,效果不好。
小编在机械加工行业摸爬滚打了十几年,还算是有一点小心得,今天分享给大家。
在先介绍CBN刀具车削加工淬火钢件的切削参数范围之前,先来了解一下淬火钢都有哪些难加工问题。
1、淬火钢件的粗加工:车削加工淬火过的齿轮,齿圈的生产过程中,一些齿轮、齿圈淬火或渗碳淬火后,硬度一般在HRC55以上,而且变形严重,如高铁齿轮,工程机械大齿圈,重工行业用大齿圈等,这些大型齿轮齿圈淬火后变形量非常大,这就涉及到淬火钢粗加工。
同样,在模具钢生产过程中,淬火钢的粗加工也经常看到,但很多厂家采取的措施也五花八门,有的先把大余量线切割掉,有的用硬质合金刀具慢慢啃,有的用立方氮化硼(PCBN)刀具多次走刀才能完成加工,工人感慨粗加工淬火钢是有劲使不出,干着急,没办法。
2、淬火钢件的断续加工:间断切削加工一直是个难题,何况是动辄HRC60左右的淬火钢。
特别是在高速车削淬火钢时,刀具在间断车削淬火钢时会以每分钟100次以上的冲击来完成加工,对刀具的抗冲击性能是个很大的挑战。
以汽车齿轮加工为例,淬硬齿轮以车代磨已经成为一种趋势,据了解,作为齿轮产业的三大市场之一,车辆齿轮占据了齿轮市场总额的62%,其中汽车齿轮又占据了车辆齿轮市场份额的62%。
也就是说,汽车所用齿轮占有了整个齿轮市场近40%的比重,可见齿轮对于汽车产业的重要性。
虽然淬火钢的以车代磨和硬车削已经很普及,其实汽车淬硬齿轮加工过程中仍然遇到很多问题,如一些汽车齿轮内孔有油孔,这就出现间断切削加工难题,很多CBN刀具在高速运转时期遇到油孔容易崩刀,齿轮的位置公差难以保证,等等3、淬火钢件的切槽加工:举一个简单的例子,同步器滑套啮合槽淬火后的硬车削加工,虽然立方氮化硼刀具厂家开发出了同步器滑套专用立方氮化硼切槽刀具,但PCBN刀具的寿命仍然不尽如人意。
车削加工路径、切削参数选择

铸铁 HBS<200
精加工 切断(宽度<5mm)
(3)选择切削用量时应注意的几个问题 ①主轴转速 应根据零件上被加工部位的直径,并按零件和刀 具的材料及加工性质等条件所允许的切削速度来确定。切削速度除 了计算和查表选取外,还可根据实践经验确定,需要注意的是交流 变频调速数控车床低速输出力矩小,因而切削速度不能太低。根据 切削速度可以计算出主轴转速。 ②车螺纹时的主轴转速 数控车床加工螺纹时,因其传动链的 改变,原则上其转速只要能保证主轴每转一周时,刀具沿主进给轴 (多为Z轴)方向位移一个螺距即可。 在车削螺纹时,车床的主轴转速将受到螺纹的螺距P(或导程) 大小、驱动电机的升降频特性,以及螺纹插补运算速度等多种因素
在数控车床上加工零件,应按工序集中的原则划分工序,在 一次装夹下尽可能完成大部分甚至全部表面的加工。根据结构形
状不同,通常选择外圆、端面或内孔、端面装夹,并力求设计基
准、工艺基准和编程原点的统一。在批量生产中,常用下列方法 划分工序。
(1)按零件加工表面划分工序 即以完成相同型面的那一部分工艺过程为一道工序,对于加工 表面多而复杂的零件,可按其结构特点(如内形、外形、曲面和平 面等)划分成多道工序。 将位置精度要求较高的表面在一次装夹下完成,以免多次定位 夹紧产生的误差影响位置精度。 如图4-19所示工件,按照零件的 工艺特点,将外轮廓和内轮廓的 粗、精加工各放在一道工序内完 成,减少了装夹次数,有利于保
影响,故对于不同的数控系统,推荐不同的主轴转速选择范围。 大多数经济型数控车床推荐车螺纹时的主轴转速n(r/min)为: n≤(1200/P)-k
式中P——被加工螺纹螺距,mm; k——保险系数,一般取为80。
数控车床车螺纹时,会受到以下几方面的影响: ●螺纹加工程序段中指令的螺距值,相当于以进给量f(mm/
各种加工方法的加工精度

各种加工方法的加工精度一:车削车削中工件旋转,形成主切削运动.刀具沿平行旋转轴线运动时,就形成内、外园柱面。
刀具沿与轴线相交的斜线运动,就形成锥面.仿形车床或数控车床上,可以控制刀具沿着一条曲线进给,则形成一特定的旋转曲面。
采用成型车刀,横向进给时,也可加工出旋转曲面来。
车削还可以加工螺纹面、端平面及偏心轴等.车削加工精度一般为IT8—IT7,表面粗糙度为6.3—1.6μm。
精车时,可达IT6—IT5,粗糙度可达0。
4—0.1μm。
车削的生产率较高,切削过程比较平稳,刀具较简单。
二:铣削主切削运动是刀具的旋转。
卧铣时,平面的形成是由铣刀的外园面上的刃形成的。
立铣时,平面是由铣刀的端面刃形成的。
提高铣刀的转速可以获得较高的切削速度,因此生产率较高.但由于铣刀刀齿的切入、切出,形成冲击,切削过程容易产生振动,因而限制了表面质量的提高。
这种冲击,也加剧了刀具的磨损和破损,往往导致硬质合金刀片的碎裂。
在切离工件的一般时间内,可以得到一定冷却,因此散热条件较好。
按照铣削时主运动速度方向与工件进给方向的相同或相反,又分为顺铣和逆铣。
顺铣铣削力的水平分力与工件的进给方向相同,工件台进给丝杠与固定螺母之间一般有间隙存在,因此切削力容易引起工件和工作台一起向前窜动,使进给量突然增大,引起打刀.在铣削铸件或锻件等表面有硬度的工件时,顺铣刀齿首先接触工件硬皮,加剧了铣刀的磨损。
逆铣可以避免顺铣时发生的窜动现象。
逆铣时,切削厚度从零开始逐渐增大,因而刀刃开始经历了一段在切削硬化的已加工表面上挤压滑行的阶段,加速了刀具的磨损。
同时,逆铣时,铣削力将工件上抬,易引起振动,这是逆铣的不利之处.铣削的加工精度一般可达IT8—IT7,表面粗糙度为6。
3—1。
6μm.普通铣削一般只能加工平面,用成形铣刀也可以加工出固定的曲面。
数控铣床可以用软件通过数控系统控制几个轴按一定关系联动,铣出复杂曲面来,这时一般采用球头铣刀。
数控铣床对加工叶轮机械的叶片、模具的模芯和型腔等形状复杂的工件,具有特别重要的意义。
车削加工参数
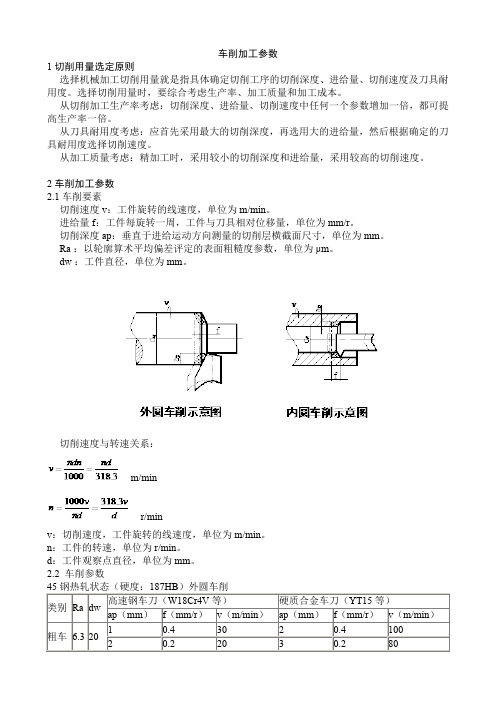
车削加工参数
1切削用量选定原则
选择机械加工切削用量就是指具体确定切削工序的切削深度、进给量、切削速度及刀具耐用度。
选择切削用量时,要综合考虑生产率、加工质量和加工成本。
从切削加工生产率考虑:切削深度、进给量、切削速度中任何一个参数增加一倍,都可提高生产率一倍。
从刀具耐用度考虑:应首先采用最大的切削深度,再选用大的进给量,然后根据确定的刀具耐用度选择切削速度。
从加工质量考虑:精加工时,采用较小的切削深度和进给量,采用较高的切削速度。
2车削加工参数
2.1车削要素
切削速度v:工件旋转的线速度,单位为m/min。
进给量f:工件每旋转一周,工件与刀具相对位移量,单位为mm/r。
切削深度ap:垂直于进给运动方向测量的切削层横截面尺寸,单位为mm。
Ra:以轮廓算术平均偏差评定的表面粗糙度参数,单位为μm。
dw:工件直径,单位为mm。
切削速度与转速关系:
m/min
r/min
v:切削速度,工件旋转的线速度,单位为m/min。
n:工件的转速,单位为r/min。
d:工件观察点直径,单位为mm。
2.2车削参数。
车削零件数控加工工艺编制

毕业设计论文题目:车削零件数控加工工艺编制系别专业班级姓名学号指导教师目录前言 (3)摘要 (4)第一章数控加工慨述 (6)一、数控车床原理介绍及发展 (6)二、数控车床加工的优越性 (6)第二章数控加工零件图纸 (8)一、零件图纸 (8)二、图纸分析 (8)第三章制定工艺方案 (9)一、确定加工内容及加工设备 (9)二、工序与装夹方式 (9)三、进给路线的确定 (11)四、切削用量的选择 (14)五、刀具的选择 (16)第四章编制数控加工程序 (18)一、零件基点、节点的计算 (18)二、编程误差及其控制 (18)三、加工程序的编制 (19)第五章零件的加工 (23)一、零件加工模拟运行 (23)二、零件加工 (23)三、精度检查 (23)小结 (24)致谢词 (25)参考文献 (26)前言本次毕业设计是学院为了提高学生的数控技术及相关技能等综合运用能力,通过毕业设计和完成毕业论文也是学院对毕业生生毕业资格的审核条件,同时也为我们以后的工作打下理论基础,本次设计是在指导老师倪祥明老师精心指导下和同学的共同协作下完成的。
数控技术是数字程序控制数控机械实现自动工作的技术。
它广泛用于机械制造和自动化领域,较好地解决多品种、小批量和复杂零件加工以及生产过程自动化问题。
随着科技的迅猛发展,自动控制技术已广泛地应用于数控机床、机器人以及各类机电一体化设备上。
同时,社会经济的飞速发展,对数控装置和数控机械要求在理论和应用方面有迅速的发展和提高。
数控加工和编程毕业设计是数控专业教学体系中构成数控加工技术专业知识及专业技能的重要组成部分,通过毕业设计使我们学会了对相关学科中的基本理论、基本知识进行综合运用,同时使对本专业有较完整的、系统的认识,从而达到巩固、扩大、深化所学知识的目的,培养和提高了综合分析问题和解决问题的能力,以及培养了科学的研究和创造能力。
数控技术不断的发展,数控技术很快会普极中国工业基地,成为工业发展的标志,数控技术的成熟也是当代科技发展的标志,所以数控技术也是国家经济的体现,中国经济正加快向新兴工业化道路发展,制造业已成为国民经济的支柱产业。
车削刀具切削参数参考表

车削刀具切削参数参考表金属车削技术资料参照表铁材加工切削参数:机床类型刀具粗前扫刀精前扫刀后扫刀槽刀牙刀镗刀切断刀高速钢硬质合金丝锥参数麻花钻麻花钻切削速度120~180120~20080~15050~10020~4060~12050~12030~5040~6010~20 m/min走芯式电进刀量0.15 ~0.02 ~0.02 ~0.01 ~依据螺距大小~0.02 ~依据钻头大小依据钻头大小脑车mm/rev确立进刀量确立进刀量确立进刀量寿命350~3000~100002000~80002500~100002000~80003000~80002000~60003000~80002000~70003000~80001200m切削速度90~16090~15060~12040~9020~4050~10040~10030~5040~6010~20 m/min走刀式电进刀量0.15 ~0.02 ~0.02 ~0.01 ~依据螺距大小~0.02 ~依据钻头大小依据钻头大小脑车mm/rev确立进刀量确立进刀量确立进刀量寿命350~3000~100002000~80002500~100002000~80003000~80002000~60003000~80002000~70003000~80001200m不锈钢材加工切削参数:机床类型刀具粗前扫刀精前扫刀后扫刀槽刀牙刀镗刀切断刀高速钢硬质合金丝锥参数麻花钻麻花钻切削速度100~16080~15060~12040~8015~3550~10040~10010~2525~4010~15 m/min走芯式电进刀量0.15 ~0.02 ~0.02 ~0.01 ~依据螺距大小~0.02 ~依据钻头大小依据钻头大小脑车mm/rev确立进刀量确立进刀量确立进刀量寿命300~3000~100004000~120003500~100002000~80002000~60003000~80002000~60001500~50002000~60001000m切削速度80~12070~12050~11040~8015~3540~9040~9010~2525~4010~15 m/min走刀式电进刀量0.15 ~0.02 ~0.02 ~0.01 ~依据螺距大小~0.02 ~依据钻头大小依据钻头大小脑车mm/rev确立进刀量确立进刀量确立进刀量寿命300~3000~100004000~120003500~100002000~80002000~60003000~80002000~60001500~50002000~60001000m铜、铝材加工切削参数:机床类型刀具粗前扫刀精前扫刀后扫刀槽刀牙刀镗刀切断刀高速钢硬质合金丝锥参数麻花钻麻花钻切削速度150~200180~250150~20080~15025~50100~20080~20040~7060~10015~25 m/min走芯式电进刀量0.2 ~0.02 ~0.03 ~0.03 ~依据螺距大小0.02 ~0.03 ~依据钻头大小依据钻头大小脑车mm/rev确立进刀量确立进刀量确立进刀量寿命500~5000~200008000~250006000~220005000~200005000~200006000~220005000~100003000~100005000~120003000m切削速度120~180150~200120~18060~12025~5080~16060~16040~7060~10015~25 m/min走刀式电进刀量0.2 ~0.02 ~0.03 ~0.03 ~依据螺距大小0.02 ~0.03 ~依据钻头大小依据钻头大小脑车mm/rev确立进刀量确立进刀量确立进刀量寿命500~5000~200008000~250006000~220005000~200005000~200006000~220005000~100003000~100005000~120003000m 技术资料:1、刀尖角 R与线速度 Vc、进给 F之间的关系:刀尖角 R增大,线速度 Vc降低,进给 F提升;反之相反。
数控车削切削用量的选择原则
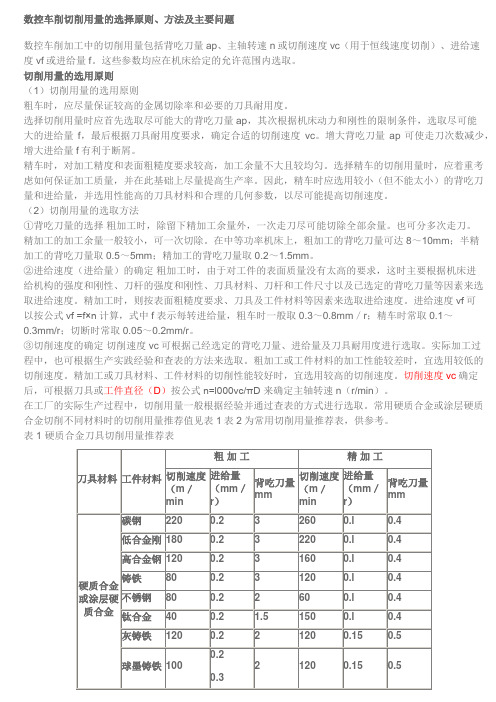
数控车削切削用量的选择原则、方法及主要问题数控车削加工中的切削用量包括背吃刀量ap、主轴转速n或切削速度vc(用于恒线速度切削)、进给速度vf或进给量f。
这些参数均应在机床给定的允许范围内选取。
切削用量的选用原则(1)切削用量的选用原则粗车时,应尽量保证较高的金属切除率和必要的刀具耐用度。
选择切削用量时应首先选取尽可能大的背吃刀量ap,其次根据机床动力和刚性的限制条件,选取尽可能大的进给量f,最后根据刀具耐用度要求,确定合适的切削速度vc。
增大背吃刀量ap可使走刀次数减少,增大进给量f有利于断屑。
精车时,对加工精度和表面粗糙度要求较高,加工余量不大且较均匀。
选择精车的切削用量时,应着重考虑如何保证加工质量,并在此基础上尽量提高生产率。
因此,精车时应选用较小(但不能太小)的背吃刀量和进给量,并选用性能高的刀具材料和合理的几何参数,以尽可能提高切削速度。
(2)切削用量的选取方法①背吃刀量的选择粗加工时,除留下精加工余量外,一次走刀尽可能切除全部余量。
也可分多次走刀。
精加工的加工余量一般较小,可一次切除。
在中等功率机床上,粗加工的背吃刀量可达8~10mm;半精加工的背吃刀量取0.5~5mm;精加工的背吃刀量取0.2~1.5mm。
②进给速度(进给量)的确定粗加工时,由于对工件的表面质量没有太高的要求,这时主要根据机床进给机构的强度和刚性、刀杆的强度和刚性、刀具材料、刀杆和工件尺寸以及已选定的背吃刀量等因素来选取进给速度。
精加工时,则按表面粗糙度要求、刀具及工件材料等因素来选取进给速度。
进给速度νf可以按公式νf =f×n计算,式中f表示每转进给量,粗车时一般取0.3~0.8mm/r;精车时常取0.1~0.3mm/r;切断时常取0.05~0.2mm/r。
③切削速度的确定切削速度vc可根据己经选定的背吃刀量、进给量及刀具耐用度进行选取。
实际加工过程中,也可根据生产实践经验和查表的方法来选取。
粗加工或工件材料的加工性能较差时,宜选用较低的切削速度。
车削加工工艺参数对切削力的影响
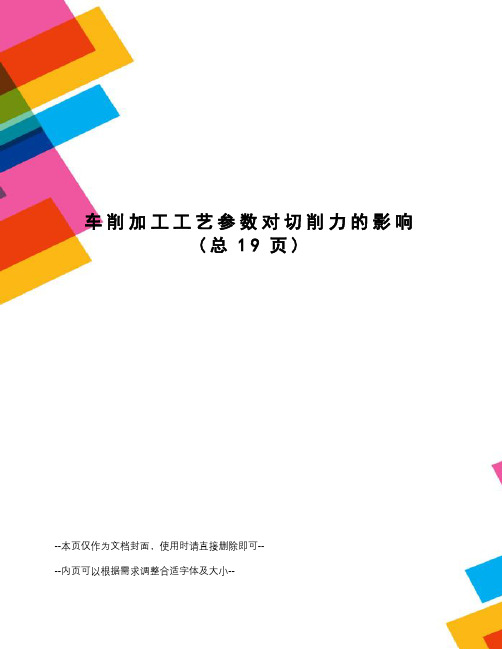
车削加工工艺参数对切削力的影响(总19页)--本页仅作为文档封面,使用时请直接删除即可----内页可以根据需求调整合适字体及大小--基于DEFORM3D的车削有限元模拟摘要:本文在建立了车削三维有限元模型基础上,运用有限元法对45钢的车削过程中切削用量对切削力影响进行了模拟,并对结果进行了分析讨论。
该模拟对现实工程应用有较大的作用。
关键字:车削模拟 DEFORM3D1 引言金属零件的加工方式可分为塑性加工、热成形或压力成形加工、机械加工、高能加工、电及化学加工等几大类。
在上述各种加工方法中,在机械制造过程所占比重最大的是机械加工中的切削加工和磨削加工;而车削加工作为切削加工中应用最广泛的加工形式,其加工过程中的工艺参数一直成为研究的对象。
本文利用STFC公司的DEFORM3D软件对车削过程进行模拟,并分析了不同的切削用量对切削力的影响。
车削加工过程中切削力的来源与分解切削力的来源刀具总切削力是刀具上所有参与切削的各切削部分所产生的总切削力的合力。
而一个切削部分的总切削力F是一个切削部分切削工件时所产生的全部切削力。
它来源于两个方面:三个变形区(剪切区、摩擦区、挤压区)内产生的弹、塑性变形抗力和切屑、工件与刀具之间的摩擦力。
切削时金属的塑性变形如图1所示,其中第Ⅰ变形区为剪切区,第Ⅱ变形区为摩擦区,第Ⅲ变形区为挤压区。
图1 切削时金属的塑性变形总切削力的几何分力刀具切削部分的总切削力是个大小、方向不易测量的力。
为方便分析,常将总切削力沿选定轴系作矢量分解来推导出各分力,即总切削力的几何分力。
图2 外圆车削时力的分解(1) 切削力F。
CF是F在主运动方向上的正投影。
在各分力中它最大,要消耗机床功率的C95%以上。
它是计算机床功率和主传动系统零件强度和刚度的主要依据。
(2) 进给力F。
fF是F在进给运动方向上的正投影,是设计或校核进给系统零件强度和刚f度的依据。
(3) 背向力FpF是F在垂直于工作平面上的分力。
轴承钢车削参数

轴承钢车削参数
轴承钢是一种用于制造轴承的高强度钢材,具有耐磨、耐腐蚀、耐高温等特点。
在进行轴承钢车削时,需要合理设置车削参数,以保证加工精度和表面质量。
一般而言,轴承钢车削参数应包括以下几个方面:
1. 速度:轴承钢车削速度一般较慢,一般在60~80m/min范围内。
过高的车削速度会导致刀具过热、刃口失效等问题。
2. 进给:轴承钢车削进给量一般较小,一般在0.1~0.25mm/r 范围内。
过大的进给量容易导致刀具磨损加剧,同时也会影响加工精度和表面质量。
3. 刀具:选择合适的刀具对于轴承钢车削至关重要,一般建议使用硬质合金刀具或陶瓷刀具,以确保切削性能和刀具寿命。
4. 冷却液:轴承钢车削一般需要使用冷却液进行冷却和润滑,常用的冷却液有水溶性切削油、乳化液、合成切削油等。
5. 车削深度:轴承钢车削深度一般较小,一般在0.2~2mm范围内。
过大的车削深度容易导致刀具过热、加工精度下降等问题。
总之,合理设置轴承钢车削参数是保证加工质量和提高效率的关键,需要根据实际情况进行调整和优化。
2.5m立车粗加工参数

2.5m立车粗加工参数1.引言本文将为您介绍2.5m立车粗加工参数的相关信息。
立车是一种常用的金属加工设备,用于加工大型工件和零件。
了解正确的粗加工参数对于保证加工效果和提高生产效率至关重要。
本文将讨论立车的切削速度、进给速度和切削深度等关键参数。
2.切削速度切削速度是指立车车刀在加工过程中切削过工件表面的速度。
切削速度的选择与工件材料的硬度、车刀材料和车刀尺寸等因素有关。
一般来说,硬度高的工件,切削速度应适当降低,以避免车刀过热和磨损过快。
切削速度的单位通常是米每分钟(m/mi n)。
3.进给速度进给速度指的是立车车刀在单位时间内移动的距离。
进给速度的选择与工件的尺寸和要求的加工精度有关。
一般来说,对于大型工件,进给速度应适当降低,以确保加工精度和安全性。
进给速度的单位通常是毫米每转(mm/r ev)。
4.切削深度切削深度是指立车车刀在一次切削中进入工件的深度。
切削深度的选择应根据工件的材料性质、切削效果和机床刚性等因素进行合理调整。
一般来说,切削深度不宜过大,以避免车刀过载和工件变形。
切削深度的单位通常是毫米(m m)。
5.切削力切削力是指立车车刀在切削过程中对工件施加的力。
切削力的大小直接影响到设备的稳定性和加工质量。
为了保证加工效果和设备安全,需要控制切削力在合理范围内。
切削力的单位通常是牛顿(N)。
6.补偿及调整在实际加工过程中,根据加工效果和工件要求可能需要进行补偿和调整。
例如,根据加工后的尺寸偏差情况,可以进行工件尺寸的微调。
此外,根据机床刚性和切削力的变化,可能需要调整切削参数以提高生产效率和加工质量。
7.粗加工参数的优化为了获得更好的加工效果和提高生产效率,需要进行粗加工参数的优化。
通过合理选择切削速度、进给速度和切削深度等参数,可以最大程度地发挥设备的性能和加工能力。
同时,合适的切削参数还可以降低工具磨损和工件变形的风险。
8.总结本文简要介绍了2.5m立车粗加工参数的相关内容,包括切削速度、进给速度、切削深度和切削力等关键参数。
车削加工最大回转直径

车削加工最大回转直径
车削加工时,工件的最大回转直径是需要考虑的一个重要参数。
回转直径越大,工件的刚性越差,加工精度难以保证。
同时,大直径工件的驱动扭矩也较大,对主轴和传动系统的要求较高。
一般来说,车削加工时工件最大回转直径不应超过250mm。
对于一般车削加工机,最大回转直径在200-250mm之间。
超过这个范围,就需要选用专门的大直径车削加工机床。
工件回转直径过大时,会产生较大的离心力,需要加大尾端中心,增大工件的刚性。
此外,应合理选择切削参数,采取对称切削,避免过大切削力产生偏心等问题。
还可以考虑采用滚刀车削来改善加工精度。
综上,车削加工时,工件最大回转直径直接影响加工质量和加工能力。
只有合理选择加工设备,制定切削参数,才能确保大直径车削加工的精度。
- 1、下载文档前请自行甄别文档内容的完整性,平台不提供额外的编辑、内容补充、找答案等附加服务。
- 2、"仅部分预览"的文档,不可在线预览部分如存在完整性等问题,可反馈申请退款(可完整预览的文档不适用该条件!)。
- 3、如文档侵犯您的权益,请联系客服反馈,我们会尽快为您处理(人工客服工作时间:9:00-18:30)。
车削加工参数
1切削用量选定原则
选择机械加工切削用量就是指具体确定切削工序的切削深度、进给量、切削速度及刀具耐用度。
选择切削用量时,要综合考虑生产率、加工质量和加工成本。
从切削加工生产率考虑:切削深度、进给量、切削速度中任何一个参数增加一倍,都可提高生产率一倍。
从刀具耐用度考虑:应首先采用最大的切削深度,再选用大的进给量,然后根据确定的刀具耐用度选择切削速度。
从加工质量考虑:精加工时,采用较小的切削深度和进给量,采用较高的切削速度。
2车削加工参数
2.1车削要素
切削速度v:工件旋转的线速度,单位为m/min。
进给量f:工件每旋转一周,工件与刀具相对位移量,单位为mm/r。
切削深度ap:垂直于进给运动方向测量的切削层横截面尺寸,单位为mm。
Ra :以轮廓算术平均偏差评定的表面粗糙度参数,单位为^m。
dw :工件直径,单位为mm。
切削速度与转速关系:
jsin nd
1000 318_3 m/min
lOOOv 3183v
H - -- -= ---
就』r/min
v:切削速度,工件旋转的线速度,单位为m/min。
n:工件的转速,单位为r/min。
d:工件观察点直径,单位为mm。
2.2车削参数
45钢热轧状态(硬度:187HB)外圆车削
钢调质状态(硬度:28〜32HRC)外圆车削
45
40Cr钢热轧状态(硬度:212HB)外圆车削
28〜32HRC)外圆车削
40Cr钢调质状态(硬度:
28〜32HRC)内圆车削
TC4固溶处理并时效状态(硬度:320〜380HB)外圆车削
TC4固溶处理并时效状态(硬度:320〜380HB)内圆车削。