DEFORM楔横轧成形工艺工业应用-安世亚太
【原创】【毕业设计论文】基于DEFORM软件的楔横轧工艺设计模拟与仿真研究
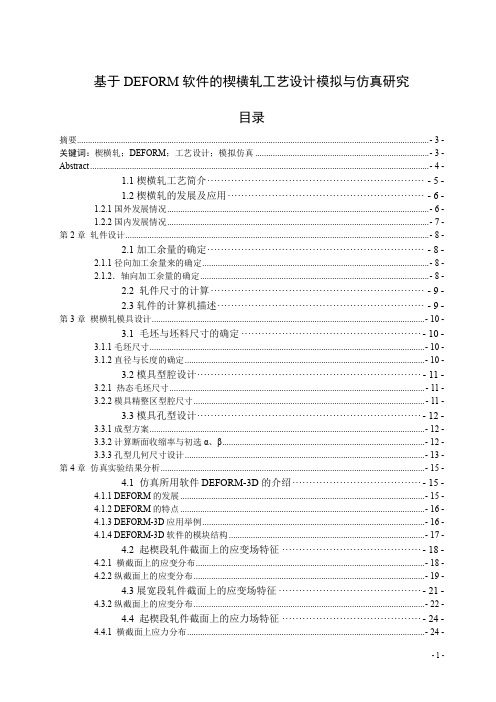
基于DEFORM软件的楔横轧工艺设计模拟与仿真研究目录摘要................................................................................................................................................................ - 3 -关键词:楔横轧;DEFORM;工艺设计;模拟仿真 ............................................................................... - 3 -Abstract .......................................................................................................................................................... - 4 -1.1楔横轧工艺简介································································ - 5 -1.2楔横轧的发展及应用·························································· - 6 -1.2.1国外发展情况....................................................................................................................... - 6 -1.2.2国内发展情况....................................................................................................................... - 7 -第2章轧件设计.......................................................................................................................................... - 8 -2.1加工余量的确定································································ - 8 -2.1.1径向加工余量来的确定....................................................................................................... - 8 -2.1.2.轴向加工余量的确定........................................................................................................ - 8 -2.2 轧件尺寸的计算 ······························································· - 9 -2.3轧件的计算机描述····························································· - 9 -第3章楔横轧模具设计............................................................................................................................ - 10 -3.1 毛坯与坯料尺寸的确定 ·····················································- 10 -3.1.1毛坯尺寸............................................................................................................................. - 10 -3.1.2直径与长度的确定............................................................................................................. - 10 -3.2模具型腔设计··································································- 11 -3.2.1 热态毛坯尺寸.................................................................................................................... - 11 -3.2.2模具精整区型腔尺寸......................................................................................................... - 11 -3.3模具孔型设计··································································- 12 -3.3.1成型方案............................................................................................................................. - 12 -3.3.2计算断面收缩率与初选α、β............................................................................................ - 12 -3.3.3孔型几何尺寸设计............................................................................................................. - 13 -第4章仿真实验结果分析........................................................................................................................ - 15 -4.1 仿真所用软件DEFORM-3D的介绍······································- 15 -4.1.1 DEFORM的发展 ............................................................................................................... - 15 -4.1.2 DEFORM的特点 ............................................................................................................... - 16 -4.1.3 DEFORM-3D应用举例..................................................................................................... - 16 -4.1.4 DEFORM-3D软件的模块结构 ......................................................................................... - 17 -4.2 起楔段轧件截面上的应变场特征 ·········································- 18 -4.2.1 横截面上的应变分布........................................................................................................ - 18 -4.2.2纵截面上的应变分布......................................................................................................... - 19 -4.3展宽段轧件截面上的应变场特征 ··········································- 21 -4.3.2纵截面上的应变分布......................................................................................................... - 22 -4.4 起楔段轧件截面上的应力场特征 ·········································- 24 -4.4.1 横截面上应力分布............................................................................................................ - 24 -4.4.2 纵截面上的应力分布........................................................................................................ - 25 -4.5 展宽段轧件截面上的应力场特征 ·········································- 26 -4.5.1横截面上的应力分布......................................................................................................... - 26 -4.5.2 纵截面上的应力分布........................................................................................................ - 27 -4.6不同工艺参数对空心轴类件轧制力的影响 ······························- 28 -结论.............................................................................................................................................................. - 29 -参考文献...................................................................................................................................................... - 30 -摘要本文主要介绍了楔横轧成形技术与模拟仿真技术,并基于DEFORM分析软件对楔横轧的工艺设计进行了模拟仿真分析研究工作。
DEFORM

资讯· 4 ·IMcadcam@IMCHINA@投稿邮箱GPU为HPC和深度学习提供强大加速动力2015年11月10日,2015年全国高性能计算学术年会在无锡开幕。
NVIDIA 及其GPU 的用户企业带来了近20场演讲报告,针对GPU 的新技术和GPU 在科学计算、大数据分析、深度学习乃至汽车自动驾驶领域的应用和创新,做了解读和分享。
大会首日上午的特邀报告环节,NVIDIA 解决方案工程架构副总裁Marc Hamilton 说:“在NVIDIA 推动下,过去7年间整个加速计算领域获得了10倍的增长,NVIDIA 的GPU 占据了加速器市场85%的份额。
同时在GPU 的驱动下,全球掀起了深度学习热潮,GPU 已成为深度学习研究的首选技术平台。
我们非常高兴地看到GPU 帮助了众多企业和研究机构在HPC 和深度学习领域实现创新应用,相信我们将于明年面世的下一代GPU 架构Pascal 和NVLink 高速互联技术,将为数据中心和深度学习提供更加强大的加速动力。
”Siemens PLM Software获“2015亚洲制造业大奖”在2015年度“亚洲制造业大奖”颁奖礼上,Siemens PLM Software 被授予“最佳CAD/CAM 系统提供商”和“最佳PLM 系统提供商”两项荣誉,这是Siemens PLM Software 连续第三年获此殊荣。
亚洲制造业大奖年度盛事由腾世传媒(Contineo Media)主办,汇聚了亚洲制造业领先企业,旨在表彰那些不断推进亚洲制造业升级转型的技术解决方案。
本次大奖的评委会由国际专家组成,这些资深评委来自不同行业,都致力于推动制造业的不断发展。
Siemens PLM Software 亚太区高级副总裁兼董事总经理Peter Carrier 先生表示:“制造业是亚洲工业复兴的核心,在推动亚洲新兴经济体迈向创新时代的过程中发挥着举足轻重的作用。
DEFORM功能简介与工程应用Deform锻压工艺计算机模拟-安世亚太

电 子 产 品
2015Deform中国用户大会
自由锻
4
体积成形应用——变形分析
挤压过程模拟
T
正
型
挤
带
压
挤
压
2015Deform中国用户大会
5
体积成形应用——变形分析
拉拔过程模拟
梅花棒拉拔
2015Deform中国用户大会
丝材拉拔
6
体积成形应用——缺陷预测
缺陷预测 体积成形过程主要可能产生的缺陷: 折叠 充填不满 开裂(挤压、拉拔等过程) 流线紊乱 飞边
2015Deform中国用户大会
7
体积成形应用——模具应力分析
模具应力分析
2015Deform中国用户大会
8
体积成形应用——模具磨损分析
2015Deform中国用户大会
9
DOE 工艺参数优化
2015Deform中国用户大会
• 具备专业的DOE前后处理界面,可进行粉末成形、切削、锻造和热处理等多工艺的优化;
• 自动优化变量包括毛坯尺寸、模具结构、材料、摩擦、成形速度、成形温度等多种参数类型;
• 场变量输出目标及约束:应力、应变、密度、温度、硬度、体积、材料破坏、磨损、变形量、成形 力、速度、无填充不满、无折叠等;
• 抽样方式:Latin hypercube、Full Factorial、Taguchi、用户自定义
2015Deform中国用户大会
热处理工艺模拟
前 桥 淬 火
扳 手 淬 火
2015Deform中国用户大会
热处理应用——齿轮热处理
• SNC815 钢锥形齿 • 表层硬化 • 渗碳 • 油淬
2015Deform中国用户大会
基于Deform的外轮成形工艺及结构优化
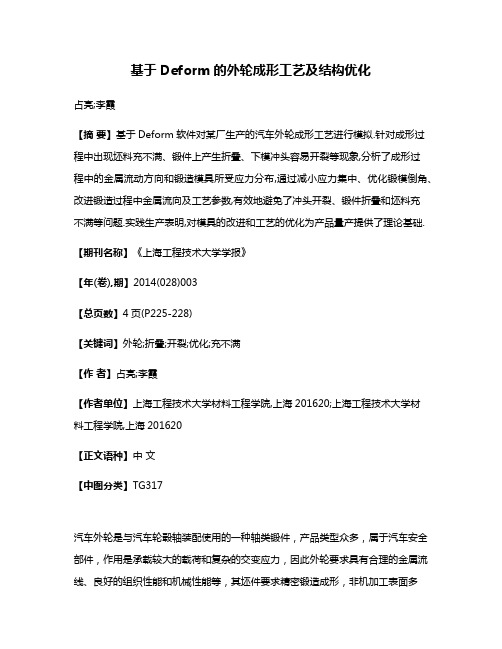
基于Deform的外轮成形工艺及结构优化占亮;李霞【摘要】基于Deform软件对某厂生产的汽车外轮成形工艺进行模拟.针对成形过程中出现坯料充不满、锻件上产生折叠、下模冲头容易开裂等现象,分析了成形过程中的金属流动方向和锻造模具所受应力分布,通过减小应力集中、优化锻模倒角、改进锻造过程中金属流向及工艺参数,有效地避免了冲头开裂、锻件折叠和坯料充不满等问题.实践生产表明,对模具的改进和工艺的优化为产品量产提供了理论基础.【期刊名称】《上海工程技术大学学报》【年(卷),期】2014(028)003【总页数】4页(P225-228)【关键词】外轮;折叠;开裂;优化;充不满【作者】占亮;李霞【作者单位】上海工程技术大学材料工程学院,上海201620;上海工程技术大学材料工程学院,上海201620【正文语种】中文【中图分类】TG317汽车外轮是与汽车轮毂轴装配使用的一种轴类锻件,产品类型众多,属于汽车安全部件,作用是承载较大的载荷和复杂的交变应力,因此外轮要求具有合理的金属流线、良好的组织性能和机械性能等,其坯件要求精密锻造成形,非机加工表面多[1].半封闭式成形技术的提出和发展[2]为复杂零件的精密成形提供了一种非常有意义的方法.采用精密成形的方法成形零部件,是当今成形行业缩短制造过程、提高工作效率的有效途径.在锻造中,精密成形可以得到尺寸和形状精确、内部和表面没有缺陷的产品[3].为获得优质外轮锻件产品,本研究提出采用热模锻加工工艺,其成形工艺为:加热—镦粗—锻造—冲孔—切边.针对实际生产中,一道次模具锻造在试模后出现产品折叠、下模冲头开裂的现象.本研究采用Deform软件模拟成形工艺,找出冲头开裂、产品折叠的原因,并优化模具结构,改进锻造工艺.1 模型建立1.1 工件材料外轮材料为S55C号钢,机械结构用钢,日本工业标准(JIS G 4051—1979)碳素结构钢钢号,其化学成分(质量分数)[4]如表1所示.表1 Parameters of material S55C Table 1 S55C材料参数C Si Mn P S55C0.52~0.58 0.15~0.35 0.60~钢号S Cr Ni Cu S55C 0.035 ≤0.2 ≤0.20 ≤0.300.90 0.03钢号1.2 实验模型某厂轿车外轮图纸见图1,根据实际生产的需要设计加工模具.图1 外轮锻件图Fig.1 Forging diagram of outer hub1.3 参数选取结合实际生产经验,合理选取加工工艺参数,分析工艺参数对外轮成形的影响.依据模具失效形式及失效机理,改进模具结构和优化加工工艺.外轮锻造生产过程中,采用半封闭式锻造工艺进行锻造,节省材料的同时提高了产品表面质量和机械性能[5].依据产品要求选取S55C钢为外轮材料,温度为800~1 200℃,模具材料为H-13钢,上下模模套为5CrNiMo,预热温度约为250℃,具体参数如表2所示,选取1 000t摩擦压力机[6].表2 模拟成形工艺参数Table 2 Parameters of forming simulation坯料材料坯料温度/℃模具温度/℃摩擦因数上模速度/(mm·s-1)S55C 1 100 250 0.3 4502 有限元模拟2.1 几何模型建立用UG软件建立外轮的三维模型.根据体积设计坯料长L=75mm,直径D=55mm,并设计外轮模具,导入到Deform前处理中为模拟做准备.2.2 有限元模型的建立采用有限元模拟软件Deform模拟外轮成形[4].导入外轮几何模型及设计的外轮模具,对导入的几何模型划分网格.采用表2中的成形工艺参数,其他参数采用默认数据,进行模拟分析.2.3 成形模拟模拟锻造过程如图2所示.坯料开始是镦粗的过程,随着上模下行,坯料开始径向充型,填充直至填满整个型腔.分别采用两种方式进行锻造生产.图2 外轮模具锻造模拟Fig.2 Forging simulation of outer hub die方案1:一次锻造成形.坯料直接放在锻模上成形,坯料开始为镦粗过程,随着上模下行,下模填充为挤出拔长过程,轴轮法兰处为镦粗过程.由一次成形模拟结果可以看出,锻件底部倒角区域容易出现折叠.这是由于经过初期的镦粗,坯料在刚进入下模型腔时是向下流动的,随着上模靠拢,成形量达到85%时,下模冲头倒角太小,形成了向下和向上两个方向的流动坯料,在倒角较小的区域形成折叠.折叠是一条线性区域,模拟结果如图3所示.图3 速度场和折叠区域的模拟结果图Fig.3 Simulation result of velocity field and folding area实际生产表明,外轮锻件抛丸后经磁粉探伤,发现锻件底端圆角处出现折叠,折叠区域为一条线性区域,与模拟情况相符合.生产试件约50件时下模冲头出现裂纹,如图4所示.图4 下模冲头开裂及下模模具应力分析Fig.4 Lower punch die crack and stress analysis由下模模具应力分析可以看出:此时下模冲头部分受压应力,在Deform中查看最大压应力处在下模冲头上表面;在整个成形过程中,下模冲头处在压应力和拉应力交互作用下,最大压应力处容易产生应力集中而引起断裂失效.在实际生产中,出现折叠会对产品的装配产生致命的危害,应当重新设计锻造方案.实际产品如图5所示.方案2:一道次锻造成形.坯料锻造之前进行镦粗工艺,减小下模冲头的受力情况,并减小模具应力集中现象.为增大模具寿命,避免出现折叠现象,将下模冲头圆角半径由6mm改为8mm,进行成形模拟.结果显示,折叠现象消失,模具所受应力减小.图5 实际锻件图及折叠出现部位Fig.5 Actual forging picture and folding zone 3 工艺分析及优化通过模拟可以发现,实际锻件上折叠出现在等效应变较大的区域.由材料流动速度可以看出,此处为过渡区.由于过渡圆角同上下两个区域的流动速度差别较大,容易出现折叠.为改进模具结构,将冲头顶端半径由6mm改为8mm,可改善材料流动及缓和应变过渡区域.模具开裂是由于外轮锻造开始时,镦粗过程完全在下模冲头上进行,冲头区域由于应力集中容易产生裂纹;为了方便产品成形,将镦粗比由0.17增大至0.33,有利于减小下模冲头成形初期的压应力,同时增加了模具寿命.优化后的模拟图如图6所示.图6 优化后的等效应变和折叠角Fig.6 Effective strain and folding angle afteroptimization实际生产试锻外轮样件经抛丸处理后,再经过荧光磁粉探伤,发现锻件表面无折叠等其他缺陷.线切割后,经盐浴处理,查看流线较好.优化模具结构和工艺后生产的锻件如图7所示.图7 优化后锻件图及无折叠区域Fig.7 Forging diagram and unfolding area after optimization4 结语本研究采用半闭式锻造,节省了材料,同时具有闭式锻造的优势,提高了材料的机械性能和表面质量,使得模具充型饱满.利用有限元模拟软件Deform对实际生产进行成形模拟分析.对外轮成形过程中速度场、应变场和锻造成形过程中出现的折叠等缺陷进行了分析,结果表明:锻造过程中,在倒角不够大的位置处金属流动出现了混流,从而在过渡位置出现折叠.通过修改锻造工艺和优化模具结构,为实际生产提供了参考.通过改变冲头圆角大小,圆角半径增大至8mm,增大了过渡区,同时镦粗比增大至0.33,减小了下模冲头所受的应力.优化后,锻件折叠问题得到改善,模具冲头寿命得到提高,获得了尺寸精度较高、表面质量较好的外轮锻件. 参考文献:[1]赵德颖,孙惠学,苏升贵.数值模拟在轿车转向节闭塞挤压成形中的应用[J].热加工工艺,2007,36(13):74-77.[2]权国政,王熠昕,周杰.转向节的一种半封闭式挤压成形工艺模拟研究[J].金属铸锻焊技术,2009,38(23):128-130.[3]郭巍,毛华杰,鄢敏,等.基于Deform的轮毂轴承单元精密锻造数值模拟[J].中国水运:下半月,2008,8(6):125-126.[4]林慧国,林钢,吴静雯.袖珍世界钢号手册[M].北京:机械工业出版社,2003.[5]高占民,杨慎华.轻型车左转向节臂锻造工艺分析[J].汽车技术,1999(8):23-24.[6]张海渠.模锻工艺与模具设计[M].北京:化学工业出版社,2009.[7]胡建军,李小平.Deform-3D塑性成形CAE应用教程[M].北京:北京大学出版社,2011.。
基于DEFORM-3D模拟分析钛合金楔横轧微观组织演变规律

基于DEFORM-3D模拟分析钛合金楔横轧微观组织演变规律赵志龙;徐强;万文璐;丁睿
【期刊名称】《现代工业经济和信息化》
【年(卷),期】2022(12)5
【摘要】通过DEFORM-3D有限元软件模拟楔横轧加工TC4钛合金轴类件,将模拟结果与实验结果对比分析,探究初始温度,轧制速度,断面收缩率对轧件微观组织的影响。
结果发现在α+β双相区,轧制促进了动态再结晶的发生,且动态再结晶体积分数随着初始温度和断面收缩率的增大而增大,随着轧制速度的增大而减小;在β单相区,晶粒的平均尺寸随着初始温度的升高而增大,随着轧制速度和断面收缩率的增大而减小。
【总页数】4页(P285-287)
【作者】赵志龙;徐强;万文璐;丁睿
【作者单位】宁波工程学院国际交流学院
【正文语种】中文
【中图分类】TG335.19
【相关文献】
1.挤压式楔横轧小料头轧制的微观组织演变分析
2.楔横轧不同变形阶段的微观组织演变分析
3.楔横轧轴类件热变形时奥氏体微观组织演变的预测
4.无芯棒楔横轧铝合金空心轴微观组织演变规律
5.钛合金楔横轧工艺参数对微观组织演变规律的影响探究
因版权原因,仅展示原文概要,查看原文内容请购买。
DEFORM粉末冶金成形工艺数值模拟技术应用-安世亚太

DEFORM粉末冶金成形工艺数值模拟技术应用安世亚太公司晏建军1 前言金属粉末冶金成形已应用于多种工业机械零部件的成形工艺,包括齿轮、轮盘、汽车连杆等。
粉末冶金成形是将松散的粉末体加工成具有一定尺寸、形状以及一定密度和强度的坯块。
传统的成形方法有模压成形、等静压成形、挤压成形、轧制成形、注浆成形和热压铸成形等。
DEFORM金属粉末成形技术可实现粉末成形工艺过程的计算机数值模拟,预测粉末成形缺陷,优化加工工艺参数。
2 粉末冶金成形工艺优势及面临问题从制作机械零部件方面来看,粉末冶金法制作机械零部件是一种少切削、无切削工艺,可以大量减少切削加工量而节省机床,节约金属材料,提高劳动生产率。
用金属粉末冶金法制作机械结构零件时,比用其他加工方法的材料利用率高、能耗低。
粉末成形工艺过程的实现,涉及到工艺参数及模具结构设计等种种因素,粉末的初始装填密度、压机的锻压速度、压制力等对粉末冶金零件的成形形状、压实密度分布、成形应力应变等具有难以预测的影响,而成形零件的锻压质量又影响到产品的机械性能和使用寿命,因此如何更科学更准确地评估压实成形质量,是汽车齿轮、连杆等金属粉末加工产品的重要方面。
DEFORM塑性成形分析程度的金属粉末成形功能可预测成形过程中产品可能出现的缺陷、分析成形尺寸精度、各部位密度分布等现象,优化成形工艺参数,缩短研发周期。
3 DEFORM粉末冶金成形工艺方案的工业应用粉末冶金成形工艺模拟软件用于精确预测产品最终形状及机械加工件的密度分布,DEFORM数值模拟技术已成为产品及加工工艺设计和优化的有力工具。
在数值模拟计算系统中,可通过快速仿真分析,获得粉末成形模具粉料填充、材料流动、成形吨位、温度场分布、应力应变、能量及裂纹等信息,同时,该数值仿真系统可对粉末成形后的产品进行烧结工艺分析,预测烧结后的产品体积变化及内应力、密度,指导成形模具和工艺参数的优化设计。
在粉末冶金成形领域已获得良好的工业化应用。
高碳钢棒件温楔横轧成形过程的有限元数值模拟

高碳钢棒件温楔横轧成形过程的有限元数值模拟
熊毅;傅万堂;孙淑华;李明;赵文;周维海;孙铁光
【期刊名称】《塑性工程学报》
【年(卷),期】2006(13)5
【摘要】在有限元软件Deform-3D平台上,基于三维刚塑性大变形热/力耦合有限元理论,对一种高碳钢棒件的温楔横轧成形过程进行了数值模拟。
给出了轧制过程中温度、应变及应变速率各场量的分布,并用实际温楔横轧实验进行了验证,模拟结果与实验结果吻合较好。
【总页数】6页(P36-40)
【关键词】高碳钢;棒件;温楔横轧;数值模拟
【作者】熊毅;傅万堂;孙淑华;李明;赵文;周维海;孙铁光
【作者单位】燕山大学亚稳材料制备技术与科学重点实验室;中国第一重型机械集团公司
【正文语种】中文
【中图分类】TG335.19
【相关文献】
1.楔横轧成形小断面收缩率轴类件热力耦合数值模拟 [J], 刘文科;张康生;孟令博;胡正寰
2.楔横轧多楔成形铝合金连杆的数值模拟 [J], 赵小莲;何奥平;曾建民;何克准;刘俊生;肖刚
3.楔横轧三维变形过程的有限元数值模拟研究 [J], 刘桂华;徐春国;任广升
4.高碳钢中珠光体在温楔横轧过程中的组织演变 [J], 熊毅;赵文;孙淑华;吕知清;傅万堂
5.偏心圆截面轴类零件的楔横轧成形数值模拟 [J], 何涛;王宝雨;胡正寰
因版权原因,仅展示原文概要,查看原文内容请购买。
DEFORM软件在环轧方面的应用

DEFORM软件环轧工艺模拟仿真1 背景环轧属于回转塑性成形技术。
与传统的模锻、自由锻、火焰切割工艺相比,由于其具有环件精度高、质量好、生产效率高、节能节材、生产成本低等技术经济优势,成为目前生产各种无缝环形锻件的常用方法,广泛应用于机械、航空、航天等工业领域。
由于环轧是一个多因素作用下的塑性加工过程,具有高度的复杂性,以实验法进行研究时人力物力资源耗费量大,而各种理论分析方法也无法提供环件内部全面精确的应力、应变、温度场等信息。
采用专业的有限元数值模拟软件DEFORM 通过设置合理的参数均可得到接近实际的模拟结果,可以帮助工程师分析研究变形过程中温度场、等效应变场、轧制力的变化规律以及环件变形规律等,获得最佳工艺参数。
2 软件功能环轧工艺过程复杂,控制变量多,专业的工艺仿真软件DEFORM可以实现环轧三维动态全过程数值仿真模拟,可以帮助工程师准确研究轧件金属流动规律,以及对环轧工艺参数进行优化设计。
DEFORM软件环轧工艺仿真功能如下:1)Ring Rolling模块专门为环轧工艺而设计,操作方式流程化,简单易学;环轧专业模板2)环轧模块集成于MO模块中,可以实现多工序模拟仿真;多工序(预成形—环轧—…)模拟仿真3)Ring Rolling模块可以很方便准确实现复杂及多数量模具自动定位;具有普通环轧和车轮环轧专业模板;专业环轧模板4)DEFORM软件具有六面体自动网格划分技术、局部网格密化及网格重划分技术,保证模拟结果的高精度;六面体网格及局部密化技术5)可以实现轧制、温度及微观组织的耦合分析;DEFORM软件除了可以对成形和温度耦合分析外,还可以进行微观组织的耦合分析。
采用JMAK模型可以预测环轧成形过程中微观组织的演变,获得晶粒尺寸的变化。
环轧工艺微观组织预测6)可进行环轧变形过程模拟、模具应力及磨损分析7)可以实现隐式拉格朗日和ALE混合计算及显式求解计算。
DEFORM最新版本V11 隐式求解器对接触算法进行了优化,增强了局部接触处理能力,使得计算结果更加平稳;同时新增了显式求解器,提高了求解速度。
楔横轧技术应用与缺陷分析

楔横轧技术应用与缺陷分析一,楔横轧工作原理:楔横轧工艺是一项少切削,无切削精密轧制技术,它以连续,局部小变形量的成型方式,在台阶轴和回转体轴类零件的制造方面取得了很好的市场效益和社会效益,具有生产效率高,节约材料,劳动条件好等优点,其工作原理为:将加热后的棒材送入两个同向旋转的带有楔形凸起的模具中间,棒材在模具的带动下,作与模具反向的回转运动,同时材料发生径向压缩和轴向延伸,从而轧制成形各种阶梯轴类零件。
应用楔横轧技术可完成各种轴类零件轧制。
其中台阶形状为直角台阶,斜台阶,圆弧台阶和窄凹档台阶等。
既可以是单台阶也可以是组合台阶,轧辊每旋转一周生产两件或多件产品。
其技术工艺流程是:圆钢—棒料—中频感应加热—轧制—热精整校直—超声波探伤—等温正火—抛丸—冷校直—检验—毛坯入库。
二,楔横轧工艺优势:楔横轧与锻造都属零件成形工艺,但成形方式不同:锻造为断续整体成形;楔横轧为连续局部成形。
由于成形方式的不同,它具有显著的优点。
楔横轧既能生产轴类零件,也能给模锻工艺提供精度高的预制坯,为模锻进行高精度材料分配,实现轧锻结合,进行小飞边和无飞边的精密模锻,节约大量原材料。
楔横轧这种零件成形工艺以其连续,局部的成形方式,在阶梯轴和回转体轴类件的制造方面显示出特殊的优势:(1)生产效率高:楔横轧机轧制轴类零件的速度是每分钟6—10件。
(2)产品质量好:楔横轧产品由于金属纤维保持连续,内在组织晶粒细化,均匀,综合机械性能可以提高%20左右。
(3)节省原材料。
由于楔横轧成形轴类零件是精密轧制,加工余量小,单边加工余量1—1.5mm,并且非配合面可实现不加工,因此,材料的利用率较传统的锻造工艺高%10—%20.另外,楔横轧可为精密锻造提供毛坯。
且充分利用轧制产品余热进行等温正火热处理,节约大量电能。
(4)设备投资少,模具寿命长。
楔横轧是局部变形,工作载荷小,因此设备重量轻,体积小,投资省。
由于加工冲击小,模具服役时间长,一次使用寿命可达到10万件以上,容易实现自动化生产,适合大批量生产。
DEFORM 热冲压成形工艺数值模拟技术应用

DEFORM热冲压成形工艺数值模拟技术应用安世亚太公司工艺产品部1 前言热冲压成形工艺可使超高强度钢具有极好的可塑性、良好的成形性能及热加工性能,钣金热冲压成形技术作为钣金件冲压强化的有效途径,已在汽车等领域得到了越来越广泛的应用。
热冲压件可应用于汽车A柱、B柱、边梁、保险杠、顶盖纵梁、门梁、侧栏等重要结构件。
DEFORM金属热冲压成形模拟技术可实现高强度钣金热冲压成形过程的分析,预测冲压缺陷及热冲过程淬火现象,优化热冲工艺参数及热冲模设计。
2 热冲压成形工艺技术及特点热冲压成形是一项专门用来成形超高强度钢板冲压件的新型工艺和技术,是获得超高强度冲压件的有效途径。
热冲压成形部件的抗拉强度可达1500MPa以上,抗疲劳极限可达800MPa,因此硼钢等超高强度钢以其高强度特性已成为汽车重要保护部件用钢的最佳选择。
热冲压成形具有很多优点,如可得到超高强度的车身覆盖件;在保证汽车安全性能得条件下,优化设计以减薄车身零部件,可减轻车身重量,提高车身安全性、舒适性;改善冲压成形性,降低钣金出现易拉伸失稳性,克服传统工艺回弹严重、成形困难容易开裂等诸多难题。
热冲工艺成形技术是将钢板(如硼钢)加热至奥氏体状态,然后进行冲压并同时以20-30摄氏度/秒的冷却速度进行淬火处理,通过一定时间的保压以获得具有均匀马氏体组织的高强度钢钣金件的成形方式。
热冲压工艺包括直接成形(图1)和间接成形(图2),间接成形工艺因增加了设备成本,故现在的热冲压主要以直接热冲压工艺为主。
图1 直接热冲压成形工艺图2 间接热冲压成形工艺3 DEFORM热冲压成形工艺方案的工业应用热冲压成形技术虽具有很多优点,但因较普通冷冲压成形存在热成形及淬火冷却热处理的诸多因素影响,使得如何进行热冲压工艺参数优化及模具冷却结构设计成为需要解决的问题。
影响热冲成形的因素包括板料拉伸性能参数、冲压温度、冲压速度、润滑方案、保压时间、冷却速度及模具冷却水管的结构分布设计等,因此如何在工艺及模具设计阶段优化工艺设计参数,是提高热冲成形效率,降低研发成本的重点。
DEFORM-挤压成形工艺工业应用

DEFORM金属挤压成形工艺数值模拟技术应用安世亚太公司张丹晏建军1 前言金属挤压成形是用压力机和模具对放置在模具腔内的金属坯料施加强大的压力使金属坯料产生定向塑性变形,从挤压模的模孔中挤出而获得所需断面形状、尺寸且具有一定力学性能的零件或半成品的塑性加工方法。
挤压成形的种类很多,例如按照金属塑变流动方向可分为正挤压、反挤压、复合挤压及径向挤压。
按照金属坯料温度分冷挤压、温挤压和热挤压等。
2 挤压成形工艺优势及面临问题挤压成形与其它的金属成形加工方法相比具有明显的优势,可以用少量的工序完成复杂零件的成形加工,例如各种形状复杂的深孔、薄壁和异形截面零。
零件尺寸精度高,表面质量好,生产效率高,挤压零件不需要或仅需要少量的切削加工,大大节约材料。
不过由于挤压成形工艺特点,在生产过程中也有许多需要克服的难点。
对模具的要求较高,要求模具要有较高的强度。
对于冷挤压,坯料一般需要经过软化处理及表面润滑处理,挤压成形后,工件还需消除内应力才能使用;对于被挤压的金属材料要求有较高的塑性及低的屈服极限和冷硬性,目前常用于冷挤压的材料有:有色金属,低碳钢,低合金钢,不锈钢,钛和钛合金等。
除此之外在挤压成形过程中工件经常会出现各种缺陷从而导致零件无法达到实际要求,常见的缺陷有:表面折叠、表面折缝、缩孔和裂纹等。
目前国内企业在面临这些问题时大多采用试错法,也就是完全凭工程师经验进行大量的实际试验,这种方法的弊端在于对工程师经验依赖性大,经验又难以快速进行有效地积累和传承,通过多次的实际试验使得产品的生产周期长,成本增加,质量不高。
因此相关企业需要一种有效地工具来面临挑战,专业金属成形工艺数值模拟工具DEFORM便可以为这些难题提供相应的解决方案。
3 金属成形工艺数值模拟工具DEFORMDEFORM源自塑性有限元程序ALPID(Analysis of Large Plastic Incremental Deformation)。
基于DEFORM的楔横轧无料头轧制过程数值模拟【文献综述】

毕业论文文献综述机械设计制造及其自动化基于DEFORM的楔横轧无料头轧制过程数值模拟摘要:楔横轧是一种高效,低耗,产品质量好的轴类零件成形新工艺,新技术,是当今先进制造技术的组成部分。
理论上某些方面还有待于进一步的探讨和研究。
而有限元模拟技术有助于解决这些问题,但由于有限元模拟技术在楔横轧成形模拟中的应用正处于起步阶段,其研究面较窄,人们对于阶梯轴的楔横轧成形仍采用传统的实践实验法进行研究。
因此,进行楔横轧阶梯轴成形过程的有限元仿真与分析,对于楔横轧的理论发展和技术推广有着重大的意义。
关键词:楔横轧;无料头;有限元一、研究历史及研究现状楔横轧是一种轴类零件成形新工艺,具有高效、节材等优点,在国内外已得到较广泛的应用[10]。
但是,随着楔横轧技术的不断推广和应用范围的增大,对楔横轧技术的要求也就越来越高,如何进一步提高材料利用率是促进楔横轧技术推广的一个关键因素。
尽管目前楔横轧工艺比锻造和切削工艺材料利用率都得以大大提高,但是楔横轧轧制成形,由于目前现有成形技术都必须要有料头,所以材料利用率一般都在90%以下。
如果能够去掉每个零件的料头损失,实现无料头轧制,则零件材料的利用率可达到90%以上,甚至可以实现少或无切削加工要求。
由于楔横轧轧制过程是金属径向压下和轴向延伸的变形过程,轧制端部尺寸时表层金属比心部金属轴向流动要快,如何保证表层流动快的金属能返回而且和心部金属同步,使轧件端部不产生凹心,是辊式楔横轧成形无料头轴类零件技术的一个关键。
在解决如何保证楔横轧轧制轴类件端部轧制不发生凹心,解决无料头轧制关键问题的。
无头轧制的好处是:1.钢材全长以恒定速度进行轧制,生产率有较大提高;2.因对钢材全长施加恒定张力,使钢材断面形状波动减少,钢材质量改善,这点对热轧扁平材生产特别重要;3.由于成品长度不受限制,根据交货状态要求剪切,成品率显著提高;4.由于轧材运行稳定性提高,对热轧带钢来说,有利于生产薄规格带钢;5.和单块轧制不同,钢品啮入次数减少,减小对轧辊冲击,有利于提高轧辊寿命。
基于楔横轧原理的钢球轧制工艺计算机仿真研究

基于楔横轧原理的钢球轧制工艺计算机仿真研究初俊林;袁文生【摘要】The finite element method has been adopted to simulate the ball rolling process on the basis of cross wedge rollingprinciple.The influence of various process parameters of cross wedge rolling on the forming process of steel balls has been studied by DEFORM-3D simulation.The die has been improved according to the metal flow law in the simulation process,which obtains satisfied effect.%钢球在工业中的应用非常广泛,特别是矿山用的球磨机对钢球的应用量更是巨大,由于其形状的特殊性,其大批量生产工艺也越来越得到重视.本文应用有限元方法,并基于楔横轧原理对钢球的轧制成形工艺过程进行模拟仿真,通过DEFORM-3D的模拟过程研究了楔横轧各工艺参数对钢球成形过程的影响,根据模拟过程中金属的流动规律对模具进行改良,获得满意效果.【期刊名称】《锻压装备与制造技术》【年(卷),期】2017(052)006【总页数】4页(P87-90)【关键词】楔横轧;钢球;模具;DEFORM-3D【作者】初俊林;袁文生【作者单位】山东建筑大学,山东济南250101;山东建筑大学,山东济南250101【正文语种】中文【中图分类】TG335.19钢球是重要的基础零部件,尤其是精密工业钢球在国民经济发展中起着巨大的作用。
钢球广泛应用于轴承、五金、电子、铁艺、机械设备、电力、采矿、冶金等领域。
据不完全统计,中国钢球的年消耗量巨大,在百万吨以上,但目前钢球的主要生产工艺为锻造和铸造,生产效率较低。
DEFORM金属成形技术的发展与应用

DEFORM金属成形技术的发展与应用DEFORM是在一个集成环境内综合建模、成形、热传导和成形设备特性进行模拟仿真分析。
适用于金属冷、温、热成形,提供极有价值的工艺分析数据。
如:材料流动、模具填充、锻造负荷、模具应力、晶粒流动、金属微观结构和缺陷产生发展情况等。
金属成形工艺及模具是加工制造业重要的生产方式及装备,随着金属制造业的迅速发展以及金属制品在电子、机械、汽车、航空航天和船舶等工业部门的推广应用,产品的生产质量以及产品对模具设备的要求将越来越高,传统的模具设计方法和靠经验的工艺生产方式已无法适应产品更新换代和提高质量的要求。
一、CAE技术在金属成形市场上的重要性与需求计算机辅助工程CAE技术已成为金属产品开发、模具设计及产品加工中薄弱环节的最有效途径。
同传统的模具设计相比,CAE技术无论在提高生产率、保证产品质量,还是在降低成本、减轻劳动强度等方面,都具有很大优越性。
近些年,CAE技术在汽车、家电、电子通讯、模具制造、日用品等领域逐步地得到了广泛应用。
当今,金属成形工艺及模具的设计不但要采用CAD技术,而且还要采用CAE技术,这是发展的必然趋势。
传统的金属成形方法是在正式生产前,由于设计人员凭经验和直觉设计模具、设定成形工艺,模具加工并装配完毕后,需要多次试模,发现问题后,不仅需要重新设计成形工艺、工艺参数,甚至还需要修改金属制品和模具设计,这种“试错”的研发模式势必增加生产成本,延长产品开发周期。
采用CAE技术,可以通过计算机模拟代替试模,提供了从产品设计到生产的完整解决方案。
在模具制造前,预测产品整个成形过程,帮助研判潜在的问题,有效地防止问题发生,大大缩短了开发周期,降低生产成本,在金属成形时市场上发挥着越来越重要的作用。
二、CAE技术在金属成形领域的重要应用采用CAE技术可以全面解决金属成形过程中出现的问题,指导模具设计。
CAE计算机模拟技术能成功地应用于产品成形工艺优化设计、模具设计开发、成形缺陷预测及热处理等方面。
安世亚太:延伸到制造工艺仿真
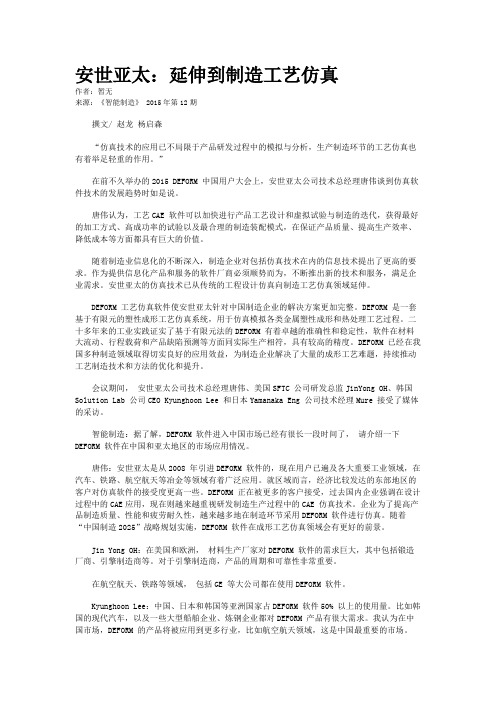
安世亚太:延伸到制造工艺仿真作者:暂无来源:《智能制造》 2015年第12期撰文/ 赵龙杨启森“仿真技术的应用已不局限于产品研发过程中的模拟与分析,生产制造环节的工艺仿真也有着举足轻重的作用。
”在前不久举办的2015 DEFORM 中国用户大会上,安世亚太公司技术总经理唐伟谈到仿真软件技术的发展趋势时如是说。
唐伟认为,工艺CAE 软件可以加快进行产品工艺设计和虚拟试验与制造的迭代,获得最好的加工方式、高成功率的试验以及最合理的制造装配模式,在保证产品质量、提高生产效率、降低成本等方面都具有巨大的价值。
随着制造业信息化的不断深入,制造企业对包括仿真技术在内的信息技术提出了更高的要求。
作为提供信息化产品和服务的软件厂商必须顺势而为,不断推出新的技术和服务,满足企业需求。
安世亚太的仿真技术已从传统的工程设计仿真向制造工艺仿真领域延伸。
DEFORM 工艺仿真软件使安世亚太针对中国制造企业的解决方案更加完整。
DEFORM 是一套基于有限元的塑性成形工艺仿真系统,用于仿真模拟各类金属塑性成形和热处理工艺过程。
二十多年来的工业实践证实了基于有限元法的DEFORM 有着卓越的准确性和稳定性,软件在材料大流动、行程载荷和产品缺陷预测等方面同实际生产相符,具有较高的精度。
DEFORM 已经在我国多种制造领域取得切实良好的应用效益,为制造企业解决了大量的成形工艺难题,持续推动工艺制造技术和方法的优化和提升。
会议期间,安世亚太公司技术总经理唐伟、美国SFTC 公司研发总监JinYong OH、韩国Solution Lab 公司CEO Kyunghoon Lee 和日本Yamanaka Eng 公司技术经理Mure 接受了媒体的采访。
智能制造:据了解,DEFORM 软件进入中国市场已经有很长一段时间了,请介绍一下DEFORM 软件在中国和亚太地区的市场应用情况。
唐伟:安世亚太是从2008 年引进DEFORM 软件的,现在用户已遍及各大重要工业领域,在汽车、铁路、航空航天等冶金等领域有着广泛应用。
凸轮轴板式楔横轧精确成形过程仿真
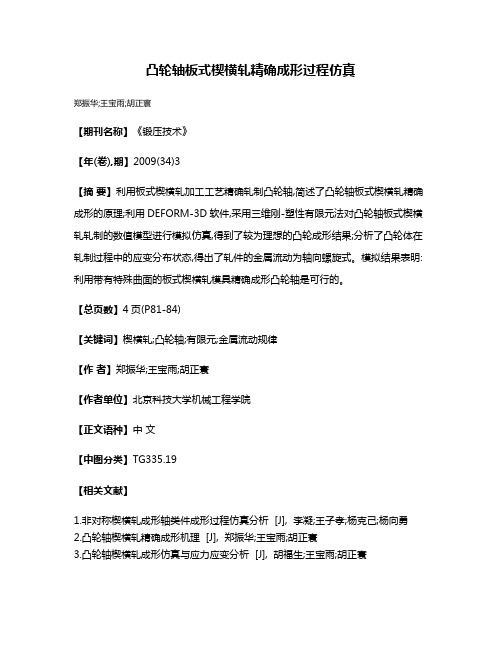
凸轮轴板式楔横轧精确成形过程仿真
郑振华;王宝雨;胡正寰
【期刊名称】《锻压技术》
【年(卷),期】2009(34)3
【摘要】利用板式楔横轧加工工艺精确轧制凸轮轴,简述了凸轮轴板式楔横轧精确成形的原理;利用DEFORM-3D软件,采用三维刚-塑性有限元法对凸轮轴板式楔横轧轧制的数值模型进行模拟仿真,得到了较为理想的凸轮成形结果;分析了凸轮体在轧制过程中的应变分布状态,得出了轧件的金属流动为轴向螺旋式。
模拟结果表明:利用带有特殊曲面的板式楔横轧模具精确成形凸轮轴是可行的。
【总页数】4页(P81-84)
【关键词】楔横轧;凸轮轴;有限元;金属流动规律
【作者】郑振华;王宝雨;胡正寰
【作者单位】北京科技大学机械工程学院
【正文语种】中文
【中图分类】TG335.19
【相关文献】
1.非对称楔横轧成形轴类件成形过程仿真分析 [J], 李凝;王子孝;杨克己;杨向勇
2.凸轮轴楔横轧精确成形机理 [J], 郑振华;王宝雨;胡正寰
3.凸轮轴楔横轧成形仿真与应力应变分析 [J], 胡福生;王宝雨;胡正寰
4.辊式楔横轧和板式楔横轧数值模拟的对比分析 [J], 刘桂华;徐春国;任广升
5.“内燃机凸轮轴毛坯楔横轧精确成形关键技术与应用”项目通过鉴定 [J],
因版权原因,仅展示原文概要,查看原文内容请购买。
- 1、下载文档前请自行甄别文档内容的完整性,平台不提供额外的编辑、内容补充、找答案等附加服务。
- 2、"仅部分预览"的文档,不可在线预览部分如存在完整性等问题,可反馈申请退款(可完整预览的文档不适用该条件!)。
- 3、如文档侵犯您的权益,请联系客服反馈,我们会尽快为您处理(人工客服工作时间:9:00-18:30)。
DEFORM楔横轧成形工艺工业应用
安世亚太公司工艺产品部
1 前言
楔横轧工艺主要适用于带旋转体的阶梯轴类零件的生产,如车辆、内烧机等变速箱中的各种齿轮轴、发动机中的凸轮轴等。
因楔横轧工艺设计不合理产生的成形缺陷如端头凹心、表面螺旋痕、轧件拉缩及缩松与空洞等也是该类产品生产中遇到的常见难题。
DEFORM金属楔横轧成形模拟技术可实现轴类件的成形工艺过程分析,预测轧制缺陷,优化楔横轧工艺参数及轧制模具设计。
2 楔横轧成形工艺技术及特点
楔横轧成形是在两个同向旋转的轧辊模具的楔形凸起作用下带动工件旋转,并使毛坯产生连续局部变形,最终轧制成楔形孔型的各种台阶轴,轧制过程中主要为径向压缩和轴向拉伸变形,如图1所示。
图1 楔横轧成形工艺图
与锻造、铸造成形工艺相比,楔横轧有诸多优点:
1、具有高的生产效率。
每分钟可生产6-25个产品,生产效率平均提高5-20
倍。
2、材料利用率高。
铸锻加工方式,材料利用率一般只有60%左右,楔横轧
成形的每个产品只损失料头,利用率达80%以上。
3、模具寿命较长。
楔横轧过程中,模具受力较小,因此模具寿命较长。
4、加工精度高。
热轧件径向尺寸公差可控制在0.2-0.5mm,长度尺寸公差
可以控制在0.1-1mm。
5、产品质量高。
金属在轧制过程中,晶粒得到细化,产品机械性能得到明
显提高。
3 DEFORM楔横轧成形工艺方案的工业应用
尽管楔横轧工艺具有上述多种优点,但若工艺参数设计、模具结构设计、摩擦条件等不合理则会造成轧件成形尺寸不合格、轧制力过大、出现端部凹心、轧件拉缩、加工过程工具窜动、表面螺旋痕及因曼内斯曼效应造成的缩松及空洞等缺陷,严重影响产品质量。
因此如何进行楔横轧工艺参数优化及模具楔形结构设计成为需要解决的问题。
影响楔横轧成形的因素包括楔展角、成形角、断面缩减率、摩擦系数、旋转速度、轧制温度、轧件尺寸等,因此如何在工艺及模具设计阶段优化工艺设计参数,是提高楔横轧成形精度,降低研发成本的重点。
楔横轧数值模拟技术正逐渐应用于轴类件轧制成形工艺的工业研究,通过楔横轧工艺模拟,可提前预测成形缺陷,获得成形尺寸、应力应变、温度变化、轧制力等各种轧制结果,指导楔横轧工艺及模具结构的设计。
DEFORM楔横轧成形技术可考虑工件在冷、热条件下轧制工艺过程的种种影响因素。
通过精确模拟轧制过程,获得应力应变、温度场、缺陷产生时刻及位置、轧制力曲线等结果,从而优化轧制工艺参数及楔形结构设计,提高生产效率。
图2 轴类件楔横轧成形模拟
3.1 DEFORM楔横轧应力应变分析
楔横轧成形过程中,金属材料受到楔形模具的挤压滚动作用产生塑性变形,变形过程中产生轴向、径向和环向拉压应力,应力的变化和大小可以判断成形裂纹、缩松的潜在产生位置等,应变可以反映局部变形强度及加工硬化区域的分布。
轴类件楔横轧成形变形过程如图所示。
图3 轴类件楔横轧成形变形过程及应变云图
3.2 DEFORM楔横轧成形尺寸
金属材料受到轧辊模具楔形面的挤压,材料向实心或空心轴径向流动的同时也延轴的方向流动,从而使轴轧制成所需长度,阶梯轴各部位成形尺寸可通过DEFORM模拟计算准确获取。
图4 楔横轧成形尺寸图
3.3 DEFORM楔横轧缺陷预测
轧制工艺参数及模具楔形结构的设计,都将影响到楔横轧的成形结果,DEFORM可以预测轧制过程中发生的各种缺陷,并可直观获得缺陷产生时刻及位置,指导成形工艺的优化及模具设计,图5、图6显示了内端面凹心缺陷及拉缩现象。
图5 楔横轧内端面凹心缺陷位置
图 6 楔横轧拉缩缺陷
3.4 DEFORM楔横轧微观组织计算
运用DEFORM结构-热-微观组织耦合计算能力可实现楔横轧成形过程中结构变形、传热、微观组织演变及晶粒长大的模拟,分析轧件晶粒尺寸在不同变形阶段变化的具体原因,通过微观组织模拟,可预测成形回复再结晶的晶粒形核、尺寸长大及晶界等结果,避免粗晶的产生,从而提高成形的总和力学性能。
通过DEFORM的CA算法,可以直观地获取微观组织演变现象。
图7 不同成形阶段微观组织演变及晶粒尺寸细化
4 结论
轴类件楔横轧成形工艺在多种轴类件的生产中得到应用,DEFORM模拟技术可很好地模拟楔横轧成形工艺的各种结果及现象,实现轧制工艺参数优化,指导模具结构设计。