切屑控制与断屑措施
车削加工中控制断屑的几种方法

车削加工中控制断屑的几种方法当加工产生连绵不断的带状切屑时,不仅容易划伤工件加工表面和损坏刀刃,严重时还会威胁到操作者的安全,所以采取必要的工艺措施,控制屑型和断屑一直是机械加工行业中极为重要的工艺问题。
由于切屑是切屑层变形的产物,所以,改变切削加工条件是改变切屑种类、实现断屑的有效途径,而影响切屑加工条件的因素主要包括工件材料、刀具几何角度及切屑用量等。
一般切屑需要满足以下几个基本条件:1、切屑不得缠绕在刀具、工件及其相邻的工具、装备上;2、切屑不得飞溅,以保证操作者与观察者的安全;3、精加工时,切屑不可划伤工件的已加工表面,影响已加工表面的质量;4、保证刀具预定的耐用度,不能过早磨损并竭力防止其破损;5、切屑流出时,不妨碍切削液的喷注;切屑不会划伤机床导轨或其他部件等。
一、切屑形状的分类由于塑性变形程度的不同,可能会产生不同种类的切屑,如图1所示。
加工塑性材料时,主要形成带状切屑、节状切屑或粒状切屑,加工脆性材料时,一般形成崩碎状切屑。
图11、带状切屑:带状切屑是一种连绵不断的,底面光滑,背面呈毛绒状的切屑,如图1—1a所示。
当采用较大前角的刀具,以较高的切削速度加工塑性金属材料时,容易产生这种切屑。
它是切削层不充分变形的产物。
产生带状切屑时,切削过程平稳,工件表面粗糙度较小,但切屑不易折断,往往引起缠绕,拉毛工件,甚至影响操作,所以不能忽视它的断屑问题。
2、节状切屑:节状切屑是一种底面光滑,背面有明显裂纹,且裂纹较深的切屑,如图1—1b所示。
当采用减小前角的刀具,以较低的切削速度加工塑性材料时,容易产生这种切屑。
它是切屑层较充分变形的产物,已达到了剪裂程度,产生节状切屑时,切屑工作不平稳,工件表面粗糙度较大。
3、粒状切屑:粒状切屑是一种均匀的颗粒状切屑,如图1—1c所示。
当采用小前角刀具,以很低的切削速度加工塑性金属材料时,容易产生这种切屑。
它是切削层充分变形的产物,达到了材料产生剪切破坏,使切屑沿厚度断裂的程度,产生粒状切屑时,切削工作不平稳,工件表面粗糙度较大。
金属切削中的切屑控制技术与策略

金属切削中的切屑控制技术与策略金属切削是制造业中常见的一项工艺,通过切削金属材料来制造零部件和构件。
然而,在这个过程中常常会产生切屑,对于切削加工的稳定性和效率产生负面影响。
因此,切屑控制技术与策略成为了一项重要的研究和应用领域。
切屑是在金属切削过程中由于金属材料在刀具作用下被切割而形成的长薄片,通常以螺旋形或弧形堆积。
它们不仅影响了表面质量和加工精度,还可能引起设备故障、刀具损坏及操作人员伤害等问题。
因此,切屑控制对于提高加工质量、延长设备寿命和保障操作安全具有重要意义。
首先,合理选用刀具材料、形状和涂层是切屑控制的关键。
切削加工过程中,刀具与工件的相互作用会产生高温和高压,不合适的刀具材料和形状会导致切削力过大,从而加剧切屑产生。
合适的刀具涂层能降低摩擦和热量的产生,减少切削力,改善切削过程,避免切削过程中的问题。
其次,良好的切削参数设置也能有效控制切屑的产生。
切削速度、进给速度和切削深度都对切屑形状和数量产生影响。
如果切削速度过高、进给速度过慢或切削深度过大,都会导致切削时金属材料断裂过早,产生大量切屑。
因此,合理设定切削参数是实现切屑控制的重要策略之一。
另外,使用切屑控制装置也是一种有效的方式。
切屑控制装置可以帮助收集和控制切屑的产生,减少切削床上的切屑堆积。
例如,切屑槽、滚花刀具和专用切屑收集设备等,都能够有效收集切屑,并降低对加工过程的干扰。
这些装置可以根据金属切削的特性和需求进行选择和应用,从而实现切屑的有效控制。
此外,定期清理切屑也是重要的措施。
切削过程中产生的切屑若长时间堆积在设备和加工区域,会影响切削加工的稳定性和效率。
因此,操作人员应定期清理切屑,保持工作区域的清洁和整洁,以减少切屑带来的不利影响。
综上所述,金属切削中的切屑控制技术与策略对于提高加工质量、延长设备寿命和保障操作安全具有重要意义。
合理选用刀具材料、形状和涂层,设定合适的切削参数,使用切屑控制装置,以及定期清理切屑,都是实现切屑控制的有效手段。
几种常用的断屑方法
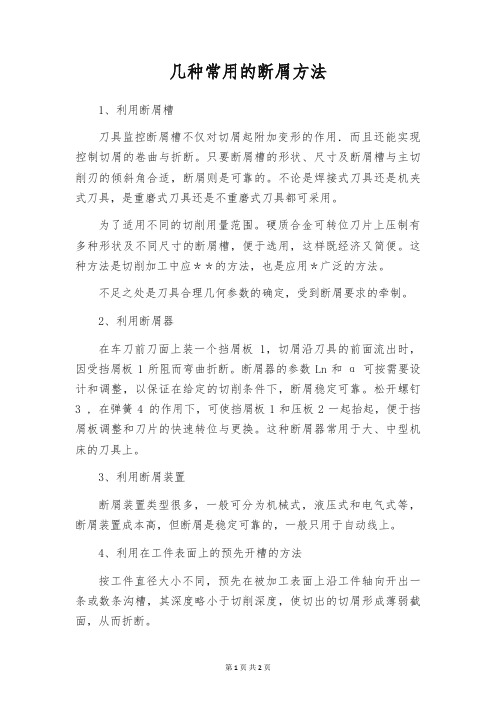
几种常用的断屑方法
1、利用断屑槽
刀具监控断屑槽不仅对切屑起附加变形的作用.而且还能实现控制切屑的卷曲与折断。
只要断屑槽的形状、尺寸及断屑槽与主切削刃的倾斜角合适,断屑则是可靠的。
不论是焊接式刀具还是机夹式刀具,是重磨式刀具还是不重磨式刀具都可采用。
为了适用不同的切削用量范围。
硬质合金可转位刀片上压制有多种形状及不同尺寸的断屑槽,便于选用,这样既经济又简便。
这种方法是切削加工中应**的方法,也是应用*广泛的方法。
不足之处是刀具合理几何参数的确定,受到断屑要求的牵制。
2、利用断屑器
在车刀前刀面上装一个挡屑板1,切屑沿刀具的前面流出时,因受挡屑板1所阻而弯曲折断。
断屑器的参数Ln和α可按需要设计和调整,以保证在给定的切削条件下,断屑稳定可靠。
松开螺钉3 , 在弹簧4 的作用下,可使挡屑板1和压板2一起抬起,便于挡屑板调整和刀片的快速转位与更换。
这种断屑器常用于大、中型机床的刀具上。
3、利用断屑装置
断屑装置类型很多,一般可分为机械式,液压式和电气式等,断屑装置成本高,但断屑是稳定可靠的,一般只用于自动线上。
4、利用在工件表面上的预先开槽的方法
按工件直径大小不同,预先在被加工表面上沿工件轴向开出一条或数条沟槽,其深度略小于切削深度,使切出的切屑形成薄弱截面,从而折断。
这样,既保证了可靠的断屑,又不影响工件已加工表面的粗糙度。
即使加工韧性较大的材料时,断屑效果也很好。
例如在精镗韧性较大的工件材料(如40Cr等)时,在用其他方法很难断屑时,则可在被加工表面上拉削出纵向沟槽,再进行镗削。
采用这种方法能显出其的优点。
切削机床使用中对切屑的要求与防护方法

切削机床使用中对切屑的要求与防护方法切削机床车削时,主刀刃相邻两位置间被切削下一层金属层称切削层,即切屑。
随工件材料、刀具几何形状、切削用量及润滑条件的不同,产生的切屑形状也不同,而不同形状的切屑,对安全的影响也不同。
最常见的切屑形状有:带状屑、C形屑、崩碎屑、卷屑(如螺卷屑、长紧卷屑、头发状卷屑、宝塔状卷屑)等。
其中带状切屑的危害最大,其锋利边缘极易刺伤割伤操作者。
同时由于带状切屑连续不断,有可能缠绕在工件、车刀、刀架、尾架、手柄以及车床的其他部分上。
如不及时清理,有可能损坏机床附件或刀具,甚至使工件飞脱而伤害操作者,这时必须停车清理,否则还可能绞伤或刺伤操作者;在停车清理时,也极易刺伤操作者如割破手指和脚部。
崩碎切屑是加工脆性材料如铸铁、青铜时形成的切屑,也有较大的危害。
这种切屑包括带状切屑折断后的各种形状的切屑,温度可达600—700℃,易烫伤、割伤操作人员的脸部和身体的其他裸露部分。
切屑的体积是工件加工余量的2~9倍,它对劳动生产率、操作安全的影响很大,其危害性与其形状、排除和运输方式有关。
带状屑连绵不断,经常缠绕工件或刀具表面,且不易清除。
不仅划伤工件表面、损坏刀具,而且极易伤人。
因此,除特殊情况下,应尽量避免带状屑。
通常采用断屑的方法,即将带状屑折断成为粒状、半环形状、螺旋状、节状或崩碎切屑等。
直径不大于20~30mm,长度为150—200mm的卷状、管状切屑危险性较小,过长的切屑难以从切屑区清理导出,运输也困难。
断屑的原则是挤压或卷曲切屑,使其剪切或弯曲变形而断裂。
断裂性能主要和切削用量、工件材料、刀具几何形状有关。
切削速度和切削深度愈大,愈不易折断。
而加大进刀量,则有利于断屑。
目前,断屑主要从改变刀具几何形状来解决,大致有以下几种方法:在车刀上磨出断屑槽或台阶;采用断屑器;采用机械夹固不重磨硬质合金刀片等。
常用的断屑措施如下。
1、采用负前角车刀,增加切屑的挤压力,使切屑产生剪切变形而断裂。
关于 钻孔时的切屑控制

钻孔时的切屑控制
转速与进给对切屑的影响
当切屑能够从钻头中顺畅排出时,切屑形成是可以接受的。
对其进行识别的最佳方法是在钻削过程中进行监听。
连续的声音表示排屑良好,断续的声音表示切屑堵塞。
检查进给力或功率监视器。
如果存在异常,则原因可能是切屑堵塞。
查看切屑。
如果切屑长而弯曲,但未卷曲,则表示出现切屑堵塞。
查看孔,如果出现切屑堵塞,则将看到不平整表面。
优秀切屑
良好切屑
异常切屑(堵塞危险)
客户处常见的寿命判断标准为了避免切屑堵塞:
·确保使用正确的切削参数和钻头/刀尖槽形
·检查切屑形状- 调整进给量和速度
进入工件时产生的开始时的切屑总是很长,并不会造成任何问题
可转位刀片钻头(U钻)
中心刀片形成容易识别的锥形切屑。
周边刀片形成类似于车削时形成的切屑
外冷
外冷可在切屑形成良好以及孔深较浅时使用。
由于切削刃温度较高,外冷却液的使用可帮助防止积屑瘤的形成。
切屑的防护和处理范本

切屑的防护和处理范本切屑是在加工过程中产生的金属碎片或碎屑,如果没有正确进行防护和处理,会对机器操作者的安全造成威胁,并且容易导致设备故障。
因此,切屑的防护和处理是非常重要的。
下面将介绍切屑的防护和处理范本。
一、设备的切屑防护1. 安装合适的切屑防护罩:在进行切削、铣削、钻孔等加工时,应该使用合适的切屑防护罩来覆盖机器的切削区域,从而防止切屑溅射。
2. 定期清理废料:对于机床等设备,在加工过程中会产生大量的废料和切屑,必须定期进行清理,以防止积累和堵塞机器。
二、操作者的切屑防护1. 穿戴个人防护装备:操作者在进行加工作业时,应该穿戴个人防护装备,包括防护眼镜、防护手套、防护面罩等,以减少切屑对身体的伤害。
2. 注意站姿和姿势:操作者应该正确站立和采取正确的姿势,保持身体平衡,并尽量做到远离切削区域,以防止切屑溅射到自己身上。
3. 维护和保养工具:操作者在进行加工作业前,应该对工具进行维护和保养,确保工具的切削刃锋利,减少切屑的溅射。
三、切屑的处理1. 使用合适的容器:在清理切屑时,应该使用合适的容器进行收集,以防止切屑飞溅或散落。
2. 定期清理切屑:切屑会堵塞设备和导致设备故障,因此要定期清理切屑,保持设备的正常运转。
3. 将切屑处理为废料:切屑是金属材料的副产品,可以将其处理为废料,以便进行再利用或者妥善处置。
切屑可被送至回收站或经专门处理设备处理。
4. 确保切屑安全处理:在处理切屑时,应该注意安全,避免手部和身体受伤。
使用适当的工具和装备,例如长柄铲子、铲斗等,以防止直接接触切屑。
5. 防止切屑散落:处理后的切屑需要妥善堆放和封存,防止其散落和引发其他安全隐患。
总结:切屑的防护和处理是保障操作者安全和设备正常运转的重要环节。
使用切屑防护罩、穿戴个人防护装备,定期清理废料,注意站姿和姿势,维护和保养工具等都是有效的切屑防护措施。
同时,合理选择容器收集切屑,并定期清理和处理切屑,以保持设备的正常运转。
切屑控制与断屑措施
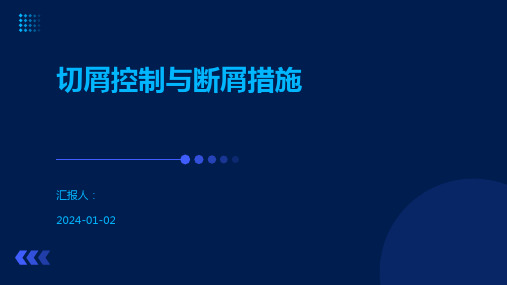
切削液使用中的问题
总结词
切削液在切削加工中起到冷却、润滑和清洗的作用,但在使用过程中也可能出 现泡沫、异味和腐蚀等问题。
详细描述
切削液在使用过程中可能会产生泡沫,影响冷却和润滑效果,同时也会带来异 味和腐蚀等问题。为解决这些问题,可以采取添加消泡剂、更换切削液或加强 切削液管理等措施。
05
未来研究方向与展望
THANKS
谢谢您的观看
选择合适的切削液对于切屑控 制至关重要,应根据加工材料 和刀具材料选择合适的决方案
切屑缠绕问题
总结词
切屑缠绕是切削加工中常见的问题,它可能导致设备损坏、生产效率降低和安全 隐患。
详细描述
切屑缠绕通常发生在铣削、车削和钻孔等加工过程中,当切屑不能及时排出或断 屑不彻底时,切屑会缠绕在刀具或工件上,影响加工质量和效率。为解决这一问 题,可以采取调整切削参数、更换刀具或优化切削液等方式。
02
切削过程中,切削力、切削热和 切削振动等多种因素相互作用, 影响切屑的形成。
切屑的类型
根据切屑的形状和形成机理,切屑可分 为带状屑、节状屑、崩碎屑和锯齿状屑 等类型。
锯齿状屑是由于切削刃上的切削力周期 性变化而形成的,其断面呈锯齿状,容 易产生振动和噪音。
崩碎屑是由于切削刃上的切削力突然变 化而形成的,其断面呈崩碎状,容易飞 溅伤人。
新型切削液的开发与研究
总结词
随着工业技术的不断发展,对切削液的性能要求也越来越高。未来研究将更加注重切削液的环保性、高效性和低 成本化,开发出新型的切削液以满足不断变化的市场需求。
详细描述
新型切削液的开发与研究将注重提高切削液的润滑性、冷却性和防锈性,以减少切削过程中的摩擦和热量,提高 切削效率和刀具寿命。同时,研究将探索切削液的生物降解性和低毒性能,以降低对环境的污染和危害。
断屑的措施

断屑的措施引言断屑是指在加工过程中出现的断裂碎片,通常发生在材料切削、破碎或折弯等工艺中。
断屑的存在对于加工过程和产品质量都有着重要的影响。
在工业生产中,断屑的控制是一个关键问题。
本文将介绍几种措施来有效地控制和减少断屑的生成。
1. 选择合适的刀具和刀具材料刀具的选择对于断屑的控制至关重要。
选择刀具时应考虑材料的切削性能和刃角等因素。
刀具材料应具有足够的硬度和强度,能够承受高切削力和摩擦热。
同时,刀具的形状和刃角也会影响断屑的产生。
较大的刃角会导致断屑容易断裂,减少断屑的生成。
因此,在选择刀具时应根据材料的特性和加工要求来进行合理的选择。
2. 控制切削速度和进给量切削速度和进给量是影响断屑生成的重要因素。
切削速度过高会导致断屑的拉直,增加断屑的长度和断裂概率。
进给量过大会增加切屑的厚度和长度,也会增加断屑的生成。
因此,合理控制切削速度和进给量对于减少断屑的生成至关重要。
3. 使用冷却润滑剂冷却润滑剂的使用可以有效地降低摩擦热和切削温度,减少断屑的粘结和变形。
合适的冷却润滑剂不仅可以降低切屑的摩擦力和切削力,还可以改善切削表面质量。
因此,在加工过程中适时使用冷却润滑剂,可以有效控制断屑的生成和提高加工效率。
4. 使用切屑加工工具切屑加工工具是专门用于处理和回收断屑的工具。
它可以将断屑有效地剥离、收集和清理,减少断屑对加工过程的影响。
常见的切屑加工工具有切屑刀、切屑夹等。
使用切屑加工工具可以有效地减少断屑对加工过程的干扰,提高加工质量。
5. 合理设计工艺参数合理的工艺参数设计是减少断屑生成的关键。
在加工过程中,应根据材料的特性和加工要求来确定合适的切削速度、进给量和切削深度等工艺参数。
合理的工艺参数设计可以减少断屑的生成,提高加工效率和产品质量。
6. 定期维护和保养机械设备机械设备的定期维护和保养对于减少断屑的生成非常重要。
定期检查和更换磨损严重的刀具以及检修磨损严重的机械部件,可以保证设备的工作状态和加工质量。
钻削加工中出现的切屑如何控制

钻头作为孔加工中较为常见、使用较多的刀具,被广泛应用于机械制造中,特别是对于冷却装置、发电设备的管板和蒸汽发生器等零件孔的加工等,应用面尤为广泛和重要。
不过在钻削加工中,如何对切屑进行控制呢?
钻头的切削是在空间狭窄的孔中进行的,切屑必须经过钻头刃沟排出,因此切屑形状对钻头的切削性能影响很大。
其中,片状屑、管状屑、针状屑、锥形螺旋屑、带状屑、扇形屑、粉状屑等都是比较常见的切屑形状。
在进行钻削加工的过程中,出现切屑形状不适当时,还会产生以下问题:
1、细微切屑阻塞刃沟,影响钻孔精度,降低钻头寿命,甚至使钻头折断,例如粉状屑、扇形屑等等。
2、长切屑缠绕钻头,妨碍作业,引起钻头折损或阻碍切削液进入孔内,例如如螺旋屑、带状屑等。
那么,在进行钻削加工的过程中要如何解决切屑形状不适当的问题呢?主要的方法有以下几种:
1、在进行实际加工的过程中,比较常用的方式是分别或联合采用增大进给量、断续进给、
修磨横刃、装断屑器等方法对断屑进行改善,并提高排屑的效果,并消除因切屑引起的一些加工问题。
2、还可以使用专业的断屑钻头打孔。
例如:在钻头的沟槽中增加设计的断屑刃,将切屑打断成为更容易清除的碎屑。
这样一来,碎屑可以顺畅的沿着沟槽排除,不会发生在沟槽内堵塞的现象,有助于切屑的排出。
因而,新型断屑钻获得了比传统钻头流畅许多的切削效果。
同时,短碎的铁屑使冷却液更容易流至钻尖,进一步改善了加工过程中的散热效果和切削性能。
而且因为新增的断屑刃穿了钻头的整个沟槽,经过多次修磨之后依然能够保持其形状和功能。
除了上述功能可以改善外,值得一提的是,这种设计强化了钻体的刚性,显著地增加了单次修磨前钻孔的数量。
切屑的防护和处理(3篇)

切屑的防护和处理是机械加工中非常重要的一项工作。
切屑是机械加工过程中产生的金属或非金属碎片,可能对人员和设备造成伤害。
合理的切屑防护和处理措施可以减少事故发生的概率,提高工作环境的安全性。
本文将详细介绍切屑的防护和处理方法。
一、切屑的防护措施1. 设立围挡或隔离区域在机械加工现场,应设置围挡或隔离区域,将切削区域和其他区域分隔开来,防止切屑飞溅到人员和设备上。
围挡应该具备一定的高度和强度,切削区域的入口处应设置防护门,只有经过允许的人员才可进入切削区域。
2. 使用安全防护装置在机床上,可以安装安全防护装置来保护工作人员的安全。
常见的安全防护装置包括切削液防护罩、钳工防护罩、进给防护罩等。
这些装置可以阻挡切屑的飞溅,减少操作人员被切屑击中的概率。
3. 穿戴个人防护装备所有进入机械加工现场的工作人员都应该穿戴个人防护装备,包括安全帽、护目镜、耳塞或耳罩、防护服等。
安全帽可以保护头部免受切屑伤害,护目镜可以阻挡切屑对眼睛的伤害,耳塞或耳罩可以减少噪音对听力的影响,防护服可以防止切削液溅到身体上。
4. 控制切削速度和进给速度在机械加工过程中,切削速度和进给速度的合理控制可以减少切屑的产生。
如果切削速度过高或进给速度过快,会导致切削过程中产生大量切屑,增加事故发生的风险。
因此,在操作机床时应根据实际情况控制切削速度和进给速度。
5. 定期清理切屑切屑的积累会增加机械设备的故障率,同时也会增加事故发生的概率。
因此,定期清理切屑是非常必要的。
应该确保切屑清理是在机器停机的情况下进行,使用专门的工具或设备清理切屑,防止切屑对清理人员造成伤害。
二、切屑的处理方法1. 分类和回收切屑可以根据材料的不同进行分类,如铝切屑、铁切屑、铜切屑等。
分类后的切屑可以进行回收利用。
回收后的切屑可以用于回炉冶炼或其他加工再利用。
2. 交给专业公司处理如果切屑的数量较大或无法进行分类回收利用,可以将切屑交给专业的废物处理公司进行处理。
切屑的防护和处理.docx

切屑的防护和处理(一)切屑的卷曲和流向车削时,工件每转一转,主刀刃相邻两位置间被切削的一层金属称为切削层。
如图1所示,切削层在刀具的挤压作用下产生沿剪切面的滑移变形后在前刀面上流出。
切屑在流动过程中,由于受前刀面的挤压、摩擦作用,使它进一步产生变形。
切屑底层里的金属变形最严重。
沿前刀面产生滑移,结果使底层的长度比上层长。
于是切屑一边流动。
一边向上卷曲,最后从C点脱离前刀面。
切屑在形成过程中经过较严重的塑性变形后,其硬度提高,塑性下降,性质变脆。
从而为断屑提供了有利的内在条件。
显然,在切削过程中产生的切削变形越大,则切屑越容易折断。
但这不是解决断屑问题的好方法。
在刀具角度和切削用量比较合理的通常情况下,切屑的曲率半径R较大,如不采取适当措施,则难以断屑。
因此,一般常用在前刀面上磨削(或压制)断屑槽或装置断屑板使切屑产生附加卷曲变形的方法来达到断屑之目的。
(二)采取断屑措施车床在切削钢件时,产生的切屑富有韧性,边缘比较锋利,高速车削钢件会形成很长的、具有锋利边缘的带状切屑,它最容易割伤工人的裸露部分,同时还会绕在工件、车刀、手柄等部位,工人在清除时,容易造成割破手或脚跟的事故。
为了消除上述危险,通常采用断屑的方法,即将带状切屑折断成为粒状,半环形状,螺旋状等。
断屑的原则是挤压或卷曲切屑,使其剪刀或弯曲变形而断裂。
断裂性能主要和切削用量、加工材料、刀具几何形状有关。
切削速度和切削深度愈大,愈不易折断,而加大进刀量,则有利于断屑。
目前,断屑主要从改变刀具几何形状来解决,大致有以下几种方法:1.在车刀上磨断屑槽或台阶;2.采用断屑器;3.采用机械夹固不重磨硬质合金刀片。
(三)工作点加防护挡板(罩)在高速切削时,切屑成为碎断形状后,容易崩跳出来伤人,因此操作工人除应戴上防护镜外,还要用防护罩把工件罩住,以免造成伤害,一般使用的防护罩有下列几种:1.玻璃挡屑板;2.车床高速切削防护罩;3.围屏式立式铣床防护罩。
切 屑
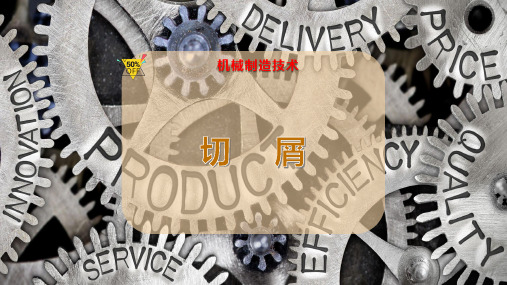
O
180°-σ
δBn γo
lBn γo Rn
γo Rn lBn A γo E
C
折线形
直线圆弧形
全圆弧形
槽的宽度lBn、圆弧半径rBn减小和反屑角δBn增 大,都能使切屑卷曲变形增大,使切屑易折断。但
槽的宽度lBn、圆弧半径rBn太小或反屑角δBn太大, 会造成切屑堵塞,排屑不畅。
机械制造技术
切屑
一、切屑的种类
常见的有带状切屑、节状切屑、粒状切屑和 崩碎切屑四种 ,如下图所示。
带状切屑
节状切屑
粒状切屑
崩碎切屑
1.带状切屑
带状切屑是在切削厚度较小、切削速度较高、 刀具前角较大时得到的一种切屑。带状切屑内表 面由于与前刀面的挤压摩擦而较光滑,外表面呈 毛茸状。
出现带状切屑时,切削力波动小,切削过程 平稳,已加工表面粗糙度较小。
前角γo减小,切削变形变大,也易于断屑。 刃倾角λs能控制切屑的流向。λs为正值时,切屑 卷曲后碰到待加工表面或刀具折断,形成螺旋状切
屑,λs为负值时,切屑卷曲后碰到已加工表面折断 形成C形切屑。
(3)切削用量
切削用量对断屑都有不同程度的影响。 提高切削速度vc,易形成长带状切屑,不易断 屑。 增大进给量f,切屑卷曲应力增大,容易断屑。
槽的宽度lBn一般根据工件材料和切削用量来 决定。例如,切削中碳钢时,lBn=10f;切削合金 钢时,lBn=7f。
一般来说,圆弧半径rBn=(0.4~0.7)lBn,反 屑角δBn=50°~70°。
(2)刀具角度
刀具角度中的主偏角 r、前角γo和刃倾角λs对 断屑影响最明显。
主偏角 r 增大,切削厚度变大,易于断屑。
切屑的防护和处理

切屑的防护和处理是机械加工中非常重要的一项工作。
切屑是机械加工过程中产生的金属或非金属碎片,可能对人员和设备造成伤害。
合理的切屑防护和处理措施可以减少事故发生的概率,提高工作环境的安全性。
本文将详细介绍切屑的防护和处理方法。
一、切屑的防护措施1. 设立围挡或隔离区域在机械加工现场,应设置围挡或隔离区域,将切削区域和其他区域分隔开来,防止切屑飞溅到人员和设备上。
围挡应该具备一定的高度和强度,切削区域的入口处应设置防护门,只有经过允许的人员才可进入切削区域。
2. 使用安全防护装置在机床上,可以安装安全防护装置来保护工作人员的安全。
常见的安全防护装置包括切削液防护罩、钳工防护罩、进给防护罩等。
这些装置可以阻挡切屑的飞溅,减少操作人员被切屑击中的概率。
3. 穿戴个人防护装备所有进入机械加工现场的工作人员都应该穿戴个人防护装备,包括安全帽、护目镜、耳塞或耳罩、防护服等。
安全帽可以保护头部免受切屑伤害,护目镜可以阻挡切屑对眼睛的伤害,耳塞或耳罩可以减少噪音对听力的影响,防护服可以防止切削液溅到身体上。
4. 控制切削速度和进给速度在机械加工过程中,切削速度和进给速度的合理控制可以减少切屑的产生。
如果切削速度过高或进给速度过快,会导致切削过程中产生大量切屑,增加事故发生的风险。
因此,在操作机床时应根据实际情况控制切削速度和进给速度。
5. 定期清理切屑切屑的积累会增加机械设备的故障率,同时也会增加事故发生的概率。
因此,定期清理切屑是非常必要的。
应该确保切屑清理是在机器停机的情况下进行,使用专门的工具或设备清理切屑,防止切屑对清理人员造成伤害。
二、切屑的处理方法1. 分类和回收切屑可以根据材料的不同进行分类,如铝切屑、铁切屑、铜切屑等。
分类后的切屑可以进行回收利用。
回收后的切屑可以用于回炉冶炼或其他加工再利用。
2. 交给专业公司处理如果切屑的数量较大或无法进行分类回收利用,可以将切屑交给专业的废物处理公司进行处理。
车床加工提高断屑的方法

车床加工提高断屑的方法在车床加工中,提高断屑的质量和数量,是保证加工质量和效率的关键之一。
断屑是在车削过程中由切削刀具切削工件时剥离出的金属屑,其质量和数量直接影响着工件表面的光洁度、加工精度和加工效率。
因此,合理选择加工参数和采取有效的方法,提高断屑的质量和数量,对于提升车床加工的质量和效率具有重要意义。
1. 优化刀具和切削参数在车床加工中,选择合适的刀具和切削参数是提高断屑质量和数量的关键。
首先要根据工件材料和加工要求选择合适的切削刀具,确保刀具材料和刀具几何形状适合加工材料的特性。
同时,合理选择切削速度、进给速度和切削深度,避免切削过程中出现过大的切削力和温度,从而影响断屑的形成和排出。
2. 控制冷却润滑在车床加工中,冷却润滑是非常重要的一环。
通过适量的切削液冷却工件和刀具,可以有效减少切削温度,降低切削力,提高加工表面质量和断屑的排出。
此外,良好的冷却润滑还能延长刀具的使用寿命,减少刀具磨损,提高加工效率。
3. 加工去毛刺在车床加工中,去除工件表面的毛刺对于提高断屑质量非常重要。
通过采用合适的去毛刺工艺和工具,可以有效地去除工件表面的毛刺,减少毛刺对切削刀具的干扰,提高断屑的排出和加工表面的光洁度。
4. 保持车床整洁保持车床清洁整洁也是提高断屑质量和数量的关键之一。
定期清理车床上的切屑和油污,保持刀具和工件的清洁,可以有效减少切削过程中产生的摩擦和磨损,提高断屑的排出和加工表面的质量。
通过以上几点方法的有效应用,可以提高车床加工中断屑的质量和数量,进而提升加工质量和效率。
只有不断优化加工工艺,注重细节,才能达到更好的加工效果。
刀具断屑措施

刀具断屑措施1. 引言在加工过程中,尤其是在机械加工中,刀具断屑是一个常见的问题。
刀具断屑不仅会影响加工效率,还会导致工件损坏和加工质量下降。
因此,采取适当的刀具断屑措施是非常重要的。
本文将介绍几种常见的刀具断屑措施,以帮助解决这个问题。
2. 刀具断屑的原因分析在了解刀具断屑措施之前,首先需要分析刀具断屑的原因。
刀具断屑的主要原因包括:•刀具丢失刀屑的能力不足。
•切削力过大。
•刀具材料或刀具形状不合适。
•切削速度过高。
•冷却液不足或不合适。
3. 刀具断屑措施3.1 提高刀具的切削性能在选择刀具时,应根据被加工材料的性质和加工要求来选择合适的刀具。
切削力过大是导致刀具断屑的一个主要原因之一。
因此,选用具有良好切削特性和刚度的刀具能够有效地减少切削力,并降低刀具断屑的风险。
3.2 优化切削参数切削参数的选择对刀具断屑的产生和控制非常重要。
合理的切削速度和进给量能够提高切削效率和刀具寿命,并减少刀具断屑的概率。
切削速度过高会加大切削力,导致刀具断屑的风险增加,因此应适当减小切削速度。
进给量的选择也要根据被加工材料的硬度、切削力等因素进行调整。
3.3 使用适当的刀具冷却液刀具冷却液是刀具断屑控制的重要手段之一。
合适的刀具冷却液可以降低切削温度,改善切削润滑条件,减少刀具磨损和断屑。
同时,刀具冷却液还可以冲刷切削区的切屑和切削热,进一步降低刀具断屑的风险。
在选择刀具冷却液时,应根据被加工材料的性质和加工过程中的切削条件来确定合适的冷却液种类和浓度。
3.4 加工过程中的切削策略优化对于一些特殊的被加工材料和加工要求,采用合适的切削策略也可以改善刀具断屑的控制效果。
例如,对于易断屑的材料,可以采用断屑反弹的策略,通过调整切削方向和进给量来减少切削力和断屑。
此外,采用适当的切削深度和开精度也能够降低刀具断屑的概率。
4. 结论刀具断屑对加工效率和加工质量有着显著的影响,在实际加工过程中必须针对性地采取有效的措施来控制和减少刀具断屑的发生。
切屑形成机理与切屑控制技术

切屑形成机理与切屑控制技术引言:在金属加工过程中,切割金属材料时产生的切屑往往会对加工表面质量、切削力和工具寿命等产生重要影响。
因此,研究切屑的形成机理及采取相应的切屑控制技术,对于提高金属加工的效率和质量具有重要意义。
本文将深入探讨切屑的形成机理,并介绍一些常见的切屑控制技术。
一、切屑形成机理切削过程中,切削刃对工件材料产生剪切作用,使其沿剪切面断裂形成切屑。
切屑形成的主要机理可以总结如下:1. 剪切切屑机制剪切切屑在主要为金属材料由剪切力沿着剪切面发生形变和破坏,最终形成顺着剪切面滑移的切屑。
这种切屑机制在高速切削中最为常见。
2. 挤压切屑机制挤压切屑机制主要适用于某些低可塑性金属材料,例如铸铁、铝合金等。
在切削过程中,由于材料可塑性较低,无法顺利地进行流动,使其在切削区域发生挤压而形成切屑。
3. 破碎切屑机制破碎切屑机制主要适用于一些硬度较高的材料,例如高速钢、硬质合金等。
在切削过程中,由于材料的硬度较大,切削刃与材料发生剪切作用时,材料很难产生滑移,而是发生局部破碎,最终形成破碎切屑。
二、切屑控制技术为了克服切屑对金属加工过程的不利影响,研究人员提出了多种切屑控制技术,并在实践中取得了显著的效果。
以下列举几种常见的切屑控制技术:1. 切向切削切向切削是一种通过增大切削刃的前微倒角来控制切屑形状的技术。
通过增大切削刃的前微倒角,可以使切削刃对工件材料施加的剪切力变小,从而减少切屑的形成。
2. 冷却润滑技术冷却润滑技术是通过在切削过程中对切削区域进行冷却和润滑,减少切削温度和摩擦,从而降低切削力和改善切屑的形成。
常用的冷却润滑技术包括切削液喷射冷却、切削油润滑等。
3. 切屑断裂技术切屑断裂技术是通过在切削过程中断裂切屑来改善切削效果。
在切削过程中,通过添加切削冲击、振动等外力,可以使切屑发生断裂,减少其长度和表面质量,从而提高切削效率。
4. 切削参数优化技术切削参数优化技术是通过调整切削参数,如进给速度、转速、切削深度等,来改善切屑形成和控制效果。
金属切屑的控制方法

车、镗、铣等
(2)增大主偏角
(3)增大倒棱前角负值,适当选择倒棱宽度
(4)适当减小刀尖圆弧半径
选择合适的切削液
选择以冷却为主的切削液及适当的注入方式
各种切削加工
在刀具周围设置障碍,增加切屑撞击的机会,防止缠绕
1、在刀具上设置挡屑板、弹性板等
车、镗
2、在机床或夹具切削区附近设置挡屑块、挡屑罩等
改变前面形状,使切屑流经时产生附件变形
(1)断屑槽(台)
各种切削加工
(2)可转位断屑刀片
(3)成屑槽,使切屑流出时产生三维变形
(4)异形曲面、球面、螺旋面等
改变主切削刃形状
(1)采用曲线切削刃
车、镗、铣、钻
(2)开分屑槽
(3)多齿刀具交错排列刀齿
改变进给运动的状态,使切屑不连续或在薄处折断
(1)断续进给,使切屑不连续
自动机床、数控机床、车、镗、钻、仿形车、自动车难断屑材料、多刀车、自动车
(2)间歇减速进给,使切屑厚度不均匀
(3)振荡进给,使切屑厚度周期变薄
(4)其他改变切屑厚度方法(如双刀切削、均压机构等)
用变吃刀量使切屑在宽度较窄处折断
(1)在工件毛坯表面预切槽,或电火花打坑
车、镗难断屑材料
(2)边开槽,边切削
采用变切削速度
改变主切削刃上各点切削速度,使切屑在薄处折断,如车刀摇动断屑法等
车削
振动切削,使其疲劳折断
(1)在刀具上设置振动切屑装置
车、镗
(2)在机床上设置振动切屑装置
将切削强制切断或破碎
(1)切屑离开前面后,将其强制切断,方法有机械、电花、激光、高压射流等
车、镗难断屑材料
(2)切屑离开前面后,将其破碎(机械破碎法等)
切屑的类型及控制

切屑的类型及控制一、切屑的类型由于工件材料不同,切削条件各异,切削过程中生成的切屑形状是多种多样的。
切屑的形状有带状、节状、粒状和崩碎四种类型。
(1)带状切屑这是最常见的一种切屑,它的内表面是光滑的,外表面呈毛茸状。
加工塑性金属时,在切削厚度较小、切削速度较高、刀具前角较大的工况条件下常形成此类切屑。
(2)节状切屑又称挤裂切屑,它的外表面呈锯齿形,内表面有时有裂纹。
在切削速度较低、切削厚度较大、刀具前角较小时常产生此类切屑。
(3)粒状切屑又称单元切屑。
在切屑形成过程中,如剪切面上的剪切应力超过了材料的断裂强度,切屑单元便从被切材料上脱落,形成粒状切屑。
(4)崩碎切屑切削脆性金属时,由于材料塑性很小、抗拉强度较低,刀具切削时,切削层金属在刀具前刀面的作用下,未经明显的塑性变形就在拉应力作用下脆断,形成形状不规则的崩碎切屑。
加工脆性材料,切削厚度越大越易得到这类切屑。
前三种切屑是加工塑性金属时常见的三种切屑类型。
形成带状切屑时,切削过程最平稳,切削力波动小,加工表面粗糙度较小。
形成粒状切屑时切削过程中的切削力波动最大。
前三种切屑类型可以随切削条件变化而相互转化,例如,在形成节状切屑工况条件下,如进一步减小前角,或加大切削厚度,就有可能得到粒状切屑;反之,加大前角,减小切削厚度,就可得到带状切屑。
二、切屑类型控制在生产实践中,我们会看到不同的排屑情况,有的切屑打成螺卷状,到达一定长度后自行折断;有的切屑折断成C 形、6字形;有的呈发条状卷屑;有的碎成针状或小片,四处飞溅,影响安全;有的带状切屑缠绕在刀具和工件上,易造成事故。
不良的排屑状态会影响生产的正常开展,控制切屑类型和流向具有重要意义,这在自动化生产线上加工时尤为重要。
切屑经第Ⅰ、第Ⅱ变形区的剧烈变形后,硬度增加,塑性下降,性能变脆。
在切屑排出过程中,当碰到刀具后刀面、工件上过渡表面或待加工表面等障碍时,如某一部位的应变超过了切屑材料的断裂极限值,切屑就会折断。
切屑控制与断屑措施

切屑控制与断屑措施汇报人:目录•切屑控制概述•切屑控制原理•切屑控制技术•断屑措施•切屑控制与断屑措施的应用案例01切屑控制概述切屑是金属切削加工过程中从被切削工件上切下来的金属薄片或带状物。
切屑概念在金属切削过程中,刀具对工件进行切削,使工件逐渐被去除,同时产生切屑。
切屑产生切屑的概念及产生连续且不断裂的切屑,通常呈螺旋状。
连续屑短而断续的切屑,通常在刀具后部形成。
短屑由于刀具磨损或切削参数不当导致的崩碎切屑。
崩碎屑过多的切屑会降低生产效率,因为需要经常清理工作区域和更换刀具。
生产效率产品质量刀具寿命切屑可能导致工件表面粗糙,影响产品质量。
切屑过多可能导致刀具磨损加快,缩短刀具寿命。
03020102切屑控制原理切屑控制是指通过采取一定的措施,对切削过程中产生的切屑进行控制,以避免切屑对加工过程和工件产生不良影响。
切屑控制的概念切屑控制对于保证加工过程的稳定性和提高工件的加工质量具有重要意义。
通过对切屑进行控制,可以减少切屑对机床、刀具和工件的损伤,同时提高加工效率和质量。
切屑控制的重要性切屑控制的概念及重要性在切削过程中,刀具对工件进行切削,产生切应力,使工件材料发生变形并形成切屑。
切应力的大小取决于刀具和工件之间的摩擦力、工件材料的力学性质以及切削速度等因素。
切屑形成的过程切屑形成的过程包括工件材料的剪切、挤压、滑移等变形行为,以及切屑与刀具和工件之间的摩擦、散热等物理现象。
通过对切屑形成的力学原理进行分析,可以建立切屑控制的力学模型。
该模型可以描述切屑控制的力学行为,为设计和优化切屑控制措施提供理论支持。
常用切屑控制方法根据切屑控制的力学模型,可以采取不同的方法对切屑进行控制,如改变刀具角度、采用断屑槽或断屑器、使用高压冷却等。
这些方法可以有效控制切屑的形成和排出,提高加工过程的稳定性和工件的加工质量。
03切屑控制技术刀具几何形状控制前角大小01前角的大小直接影响刀具的锋利程度和切削力。
前角越大,切削越轻快,但刀具的强度会降低。
- 1、下载文档前请自行甄别文档内容的完整性,平台不提供额外的编辑、内容补充、找答案等附加服务。
- 2、"仅部分预览"的文档,不可在线预览部分如存在完整性等问题,可反馈申请退款(可完整预览的文档不适用该条件!)。
- 3、如文档侵犯您的权益,请联系客服反馈,我们会尽快为您处理(人工客服工作时间:9:00-18:30)。
① 带状切屑:切塑性金属,Vc较高、 较小、γo较大时 ② 挤裂切屑:切塑性金属,Vc较低、 ③ 单元状切屑:切塑性金属,Vc低、 ④ 崩碎状:切脆性金属时 较大、γo较小时 大、γo小时
屑形细分
(2)断屑措施: ① 在刀具前刀面上磨断屑槽或安装断屑台 槽形:a) 折线形 b) 直线园弧形 c) 全圆弧形
槽向:a) 外斜式→粗加工 b) 平行式→粗加工 c) 内斜式→半精、精加工
(2)断屑措施: ② 改变切削用量:提高f、适当降低Vc
③ 改变刀具角度: ↑Kr、↓γ
设刃倾角改变切屑流向 ④ 适当提高工件材料的脆性→↓εb λs>0 → 切屑流向刀杆、切屑碰后刀面 λs<0 → 切屑流向已加工面 ⑤ 采用振动切削装置
内容提要
1、切屑的流向及卷曲
2、切屑控制与断屑措施
切屑的控制
1、切屑的流向及卷曲
(1)流向
-λs使切屑流向已加工表面 +λs使切屑流向已加工表面
1、切屑的流向及卷曲
(2)卷曲与折断机理: 流经前刀面时的摩擦、滞 留使切屑底层拉长 碰到障碍是受到附加弯曲 力矩作用 断屑的原因:τmax>σb
2、切屑控制与断屑措施