质量体系不合格项判断
审核不符合项标准
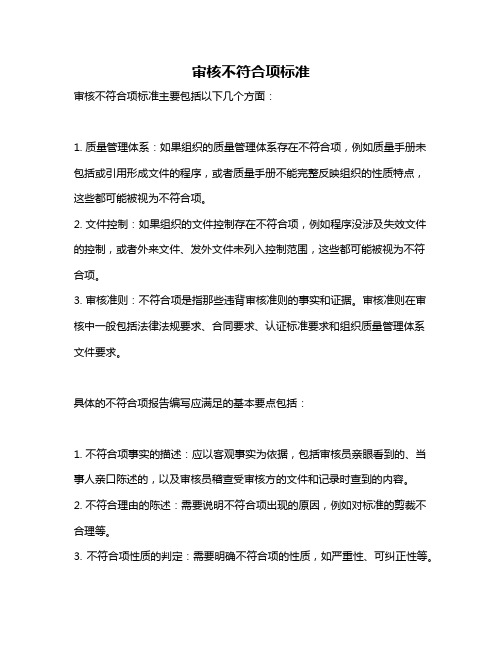
审核不符合项标准
审核不符合项标准主要包括以下几个方面:
1. 质量管理体系:如果组织的质量管理体系存在不符合项,例如质量手册未包括或引用形成文件的程序,或者质量手册不能完整反映组织的性质特点,这些都可能被视为不符合项。
2. 文件控制:如果组织的文件控制存在不符合项,例如程序没涉及失效文件的控制,或者外来文件、发外文件未列入控制范围,这些都可能被视为不符合项。
3. 审核准则:不符合项是指那些违背审核准则的事实和证据。
审核准则在审核中一般包括法律法规要求、合同要求、认证标准要求和组织质量管理体系文件要求。
具体的不符合项报告编写应满足的基本要点包括:
1. 不符合项事实的描述:应以客观事实为依据,包括审核员亲眼看到的、当事人亲口陈述的,以及审核员稽查受审核方的文件和记录时查到的内容。
2. 不符合理由的陈述:需要说明不符合项出现的原因,例如对标准的剪裁不合理等。
3. 不符合项性质的判定:需要明确不符合项的性质,如严重性、可纠正性等。
以上信息仅供参考,如果您还有疑问,建议咨询专业人士。
ISO 质量管理体系常见的不合格项

ISO9001:2000 7.6监视和测量装
置的控制
1.监视和测量活动不能确保符合性和实施改进;
2.未采用统计技术的需求; 3.统计技术使用中有错误,可能是缺乏培训,也可能是无相应的作 业指导书; 4.数据收集不规范;
ISO9001:2000 8.1总则
ISO9001:2000 标准条款8
测量分析改进
1.没有程序或程序不适用; 2.出了不合格品不标识; 3.出了不合格品不进行处理,或处理的权限不清; 4.返工/返修的产品没有再次验证; 5.返工与返修两者之间区分模糊不清,让步接收未经顾客和/或授 权人员批准; 6.组织没有对售后的产品出现不合格时不处理措施;
ISO9001:2000 8.2.4产品的监视
1.没有规定收集,分析,利用顾客满意程度信息的方法; 2.顾客满意度下降时,未采取改进措施;
ISO9001:2000 8.2.1顾客满意
质量管理体系常见的不合格项
不合格项描述
不符合条款 体系范围
1.未进行审核策划或策划的内容不完整;
2.每次审核时未编制审核计划;
3.内审员未经培训或资格证实;
4.内审后纠正措施的跟踪验证缺乏记录,或验证记录未报告相关部 门及人员;
1.不明确沟通的目的; 2.沟通的工具不明确;
ISO9001:2000 5.5.3内部沟通
1.管理评审未保存记录; 2.管理评审内容不符合要求; 3.管理评审不是由最高管理者执行;
ISO9001:2000 5.6管理评审
1.资源提供的途径不明确; 2.资源配置不充分;
ISO9001:2000 6.1资源提供
5.内审员与被审核部门有直接责任关系;
ISO9001:2000 8.2.2内部审核
质量管理体系内审不符合项及其判定原则
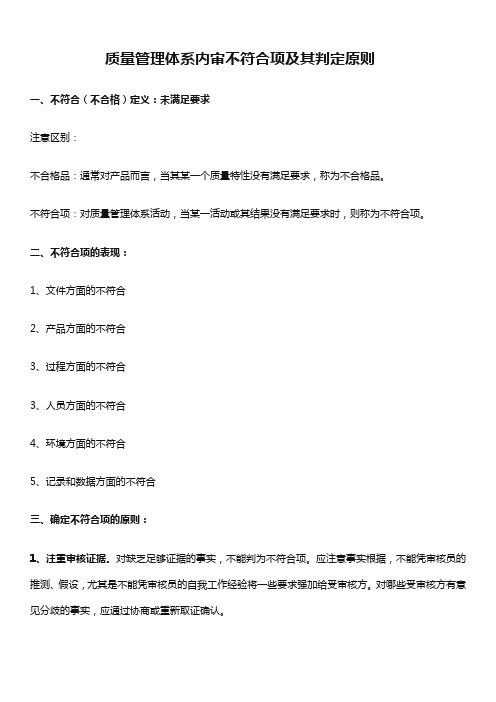
质量管理体系内审不符合项及其判定原则一、不符合(不合格)定义:未满足要求注意区别:不合格品:通常对产品而言,当其某一个质量特性没有满足要求,称为不合格品。
不符合项:对质量管理体系活动,当某一活动或其结果没有满足要求时,则称为不符合项。
二、不符合项的表现:1、文件方面的不符合2、产品方面的不符合3、过程方面的不符合3、人员方面的不符合4、环境方面的不符合5、记录和数据方面的不符合三、确定不符合项的原则:1、注重审核证据。
对缺乏足够证据的事实,不能判为不符合项。
应注意事实根据,不能凭审核员的推测、假设,尤其是不能凭审核员的自我工作经验将一些要求强加给受审核方。
对哪些受审核方有意见分歧的事实,应通过协商或重新取证确认。
2、坚持亲自核实。
如在审核现场,审核员听取一个检验员说,企业未对最终出厂产品进行检验就发运出厂。
3、严格依据审核准则。
不符合项的判定应以ISO9001:2015标准明示的要求为依据,超出规定范围的,不宜提出不符合项。
如发现受审核方亏本销售产品,不能提出关于质量成本方面的不符合项。
四、不符合项的种类:(一)、按不合格程度分1、严重不符合项A.与审核准则、要求严重不符合(缺少或删减要求)B.结果可导致质量管理体系失效(未校准)C.不能确保所提供产品(服务)的质量符合要求,已导致了或可能导致严重后果(产品出厂时产品安全指标超标、顾客使用产品造成了人身伤害、故意发运不合格品给顾客等)D.一般不符合项数量太多,集中反映出组织内某个区域或某个过程的失效。
2、一般不符合项A.与审核准则、要求轻微不符合(文件更改未经审批、顾客投诉没有处理);B.违反质量管理体系要求的孤立的、偶然的、轻微的事件(生产设备出现故障、经检验后的半成品无标识);C.可能或已经造成的后果不严重,影响不大等。
3、观察项证据不够充分、不足以确认是否构成不符合项,但可能会造成不良后果的事实。
如内部审核计划没有考虑上次的审核结果。
(二)、按不合格产生的原因分1、体系性不符合项质量管理体系文件与适用的法律法规、标准、合同等的要求不符。
质量管理体系审核中常见的不合格项 介绍
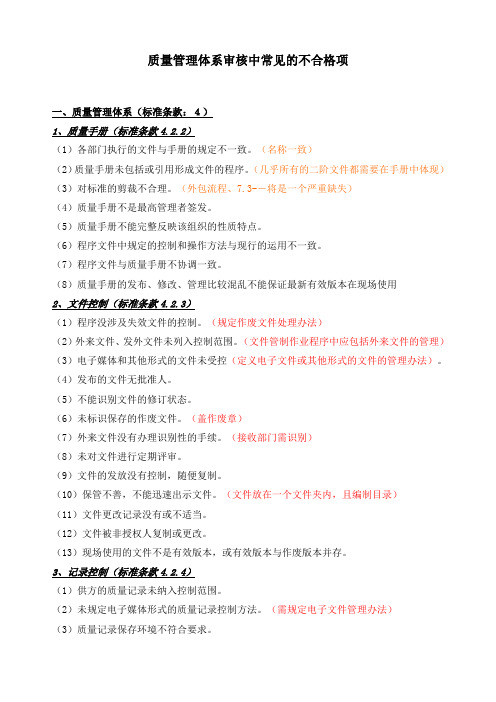
质量管理体系审核中常见的不合格项一、质量管理体系(标准条款:4)1、质量手册(标准条款4.2.2)(1)各部门执行的文件与手册的规定不一致。
(名称一致)(2)质量手册未包括或引用形成文件的程序。
(几乎所有的二阶文件都需要在手册中体现)(3)对标准的剪裁不合理。
(外包流程、7.3--将是一个严重缺失)(4)质量手册不是最高管理者签发。
(5)质量手册不能完整反映该组织的性质特点。
(6)程序文件中规定的控制和操作方法与现行的运用不一致。
(7)程序文件与质量手册不协调一致。
(8)质量手册的发布、修改、管理比较混乱不能保证最新有效版本在现场使用2、文件控制(标准条款4.2.3)(1)程序没涉及失效文件的控制。
(规定作废文件处理办法)(2)外来文件、发外文件未列入控制范围。
(文件管制作业程序中应包括外来文件的管理)(3)电子媒体和其他形式的文件未受控(定义电子文件或其他形式的文件的管理办法)。
(4)发布的文件无批准人。
(5)不能识别文件的修订状态。
(6)未标识保存的作废文件。
(盖作废章)(7)外来文件没有办理识别性的手续。
(接收部门需识别)(8)未对文件进行定期评审。
(9)文件的发放没有控制,随便复制。
(10)保管不善,不能迅速出示文件。
(文件放在一个文件夹内,且编制目录)(11)文件更改记录没有或不适当。
(12)文件被非授权人复制或更改。
(13)现场使用的文件不是有效版本,或有效版本与作废版本并存。
3、记录控制(标准条款4.2.4)(1)供方的质量记录未纳入控制范围。
(2)未规定电子媒体形式的质量记录控制方法。
(需规定电子文件管理办法)(3)质量记录保存环境不符合要求。
(4)质量记录未规定标识、贮存、保护、保存期、处置的方法。
(规定每一种表单保存多久,未规定的列入其他)(5)质量记录填写不全,质量记录上无记录者签名。
二、管理职责(标准条款:5)1、管理承诺(标准条款5.1)(1)最高管理者不知道对管理承诺应提供哪些证据。
质量体系认证内部审核不合格项报告编制方法与末次会议内容
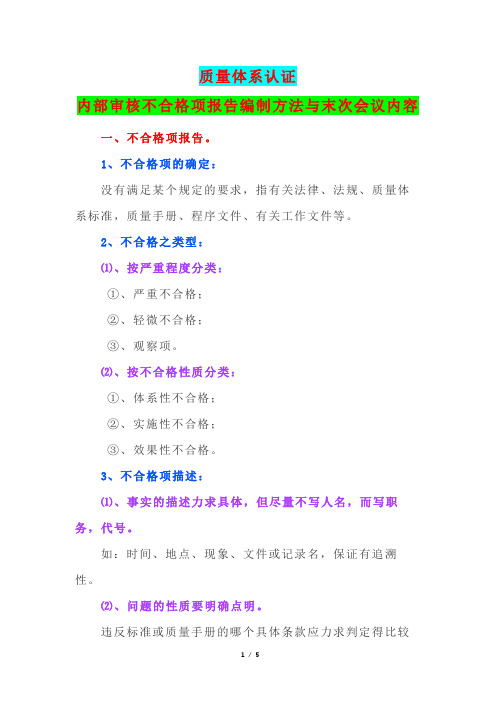
质量体系认证
内部审核不合格项报告编制方法与末次会议内容
一、不合格项报告。
1、不合格项的确定:
没有满足某个规定的要求,指有关法律、法规、质量体系标准,质量手册、程序文件、有关工作文件等。
2、不合格之类型:
⑴、按严重程度分类:
①、严重不合格;
②、轻微不合格;
③、观察项。
⑵、按不合格性质分类:
①、体系性不合格;
②、实施性不合格;
③、效果性不合格。
3、不合格项描述:
⑴、事实的描述力求具体,但尽量不写人名,而写职务,代号。
如:时间、地点、现象、文件或记录名,保证有追溯性。
⑵、问题的性质要明确点明。
违反标准或质量手册的哪个具体条款应力求判定得比较
确切。
二、末次会议。
1.签到。
2.总结审核过程。
3.总结不合格项的数量和分类。
4.宣读不合格报告,并要求各部门提出改善措施。
5.澄清和回答各部门提出的问题。
6.说明审核是一个抽样过程,内审员仅对看到的证据负责,其他地方可能还有不合格项。
质量管理体系审核中常见的不合格项【最新范本模板】

质量管理体系审核中常见的不合格项一、质量管理体系(标准条款:4)1、质量手册(标准条款4。
2.2)(1)各部门执行的文件与手册的规定不一致。
(2)质量手册未包括或引用形成文件的程序。
(3)对标准的剪裁不合理.(4)质量手册不是最高管理者签发。
(5)质量手册不能完整反映该组织的性质特点。
(6)程序文件中规定的控制和操作方法与现行的运用不一致。
(7)程序文件与质量手册不协调一致.(8)质量手册的发布、修改、管理比较混乱不能保证最新有效版本在现场使用2、文件控制(标准条款4。
2。
3)(1)程序没涉及失效文件的控制.(2)外来文件、发外文件未列人控制范围。
(3)电子媒体和其他形式的文件未受控.(4)发布的文件无批准人。
(5)不能识别文件的修订状态。
(6)未标识保存的作废文件。
(7)外来文件没有办理识别性的手续。
(8)未对文件进行定期评审.(9)文件的发放没有控制,随便复制。
(10)保管不善,不能迅速出示文件。
(11)文件更改记录没有或不适当。
(12)文件被非授权人复制或更改。
(13)现场使用的文件不是有效版本,或有效版本与作废版本并存.3、记录控制(标准条款4。
2.4)(1)供方的质量记录未纳人控制范围。
(2)未规定电子媒体形式的质量记录控制方法。
(3)质量记录保存环境不符合要求。
(4)质量记录未规定标识、贮存、保护、保存期、处置的方法.(5)质量记录填写不全,质量记录上无记录者签名。
二、管理职责(标准条款:5)1、管理承诺(标准条款5。
1)(1)最高管理者不知道对管理承诺应提供哪些证据。
(2)组织成员对质量方针、质量目标各有各的理解.(3)资源配置不足,检验人员素质差,内审人员未经培训。
2、以顾客为关注焦点(标准条款5。
2)(1)拿不出文件证实顾客的要求已得到确定。
3、质量方针(标准条款5.3)(1)质量方针空洞,体现不出企业特色,与质量目标的关系不明确。
(2)下级人员不清楚质量方针。
(3)拿不出对质量方针的评审证据。
ISO质量管理体系审核中常见的不合格项

ISO质量管理体系审核中常见的不合格项一、质量管理体系(标准条款:4)1、质量手册(标准条款4.2.2)(1)各部门执行的文件与手册的规定不一致。
(2)质量手册未包括或引用形成文件的程序。
(3)对标准的剪裁不合理。
(4)质量手册不是最高管理者签发。
(5)质量手册不能完整反映该组织的性质特点。
(6)程序文件中规定的控制和操作方法与现行的运用不一致。
(7)程序文件与质量手册不协调一致。
(8)质量手册的发布、修改、管理比较混乱不能保证最新有效版本在现场使用2、文件控制(标准条款4.2.3)(1)程序没涉及失效文件的控制。
(2)外来文件、发外文件未列人控制范围。
(3)电子媒体和其他形式的文件未受控。
(4)发布的文件无批准人。
(5)不能识别文件的修订状态。
(6)未标识保存的作废文件。
(7)外来文件没有办理识别性的手续。
(8)未对文件进行定期评审。
(9)文件的发放没有控制,随便复制。
(10)保管不善,不能迅速出示文件。
(11)文件更改记录没有或不适当。
(12)文件被非授权人复制或更改。
(13)现场使用的文件不是有效版本,或有效版本与作废版本并存。
3、记录控制(标准条款4.2.4)(1)供方的质量记录未纳人控制范围。
(2)未规定电子媒体形式的质量记录控制方法。
(3)质量记录保存环境不符合要求。
(4)质量记录未规定标识、贮存、保护、保存期、处置的方法。
(5)质量记录填写不全,质量记录上无记录者签名。
二、管理职责(标准条款:5)1、管理承诺(标准条款5.1)(1)最高管理者不知道对管理承诺应提供哪些证据。
(2)组织成员对质量方针、质量目标各有各的理解。
(3)资源配置不足,检验人员素质差,内审人员未经培训。
2、以顾客为关注焦点(标准条款5.2)(1)拿不出文件证实顾客的要求已得到确定。
3、质量方针(标准条款5.3)(1)质量方针空洞,体现不出企业特色,与质量目标的关系不明确。
(2)下级人员不清楚质量方针。
(3)拿不出对质量方针的评审证据。
质量管理体系不符合项报告项
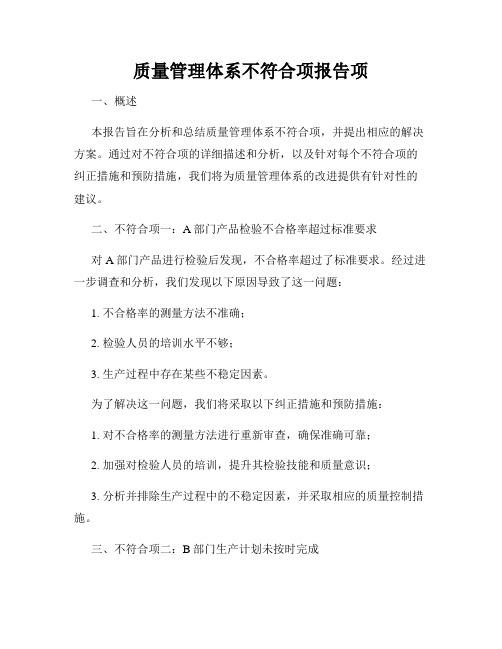
质量管理体系不符合项报告项一、概述本报告旨在分析和总结质量管理体系不符合项,并提出相应的解决方案。
通过对不符合项的详细描述和分析,以及针对每个不符合项的纠正措施和预防措施,我们将为质量管理体系的改进提供有针对性的建议。
二、不符合项一:A部门产品检验不合格率超过标准要求对A部门产品进行检验后发现,不合格率超过了标准要求。
经过进一步调查和分析,我们发现以下原因导致了这一问题:1. 不合格率的测量方法不准确;2. 检验人员的培训水平不够;3. 生产过程中存在某些不稳定因素。
为了解决这一问题,我们将采取以下纠正措施和预防措施:1. 对不合格率的测量方法进行重新审查,确保准确可靠;2. 加强对检验人员的培训,提升其检验技能和质量意识;3. 分析并排除生产过程中的不稳定因素,并采取相应的质量控制措施。
三、不符合项二:B部门生产计划未按时完成对B部门的生产计划进行检查后发现,其未能按时完成。
经过调查和分析,我们确定了以下原因:1. 生产计划制定不合理,没有考虑到实际生产情况;2. 生产资源分配不均衡,导致生产进度滞后;3. 员工技能和工作效率不足。
为了解决这一问题,我们将采取以下的纠正措施和预防措施:1. 对B部门的生产计划进行重新制定,合理安排生产任务和时间节点;2. 调整生产资源的分配,确保生产进度的顺利进行;3. 提升员工的技能和工作效率通过培训和激励等方式。
四、不符合项三:C部门工艺流程存在缺陷对C部门的工艺流程进行评估后发现,存在一些缺陷和不足。
经过深入分析,我们得出以下结论:1. 工艺流程不够清晰明确,导致操作人员容易出错;2. 工艺参数设置不合理,影响产品质量;3. 工艺流程的改进和优化不及时。
为了解决这一问题,我们将采取以下的纠正措施和预防措施:1. 重新设计和优化C部门的工艺流程,确保其清晰明确可操作性强;2. 优化工艺参数的设置,提升产品质量;3. 建立起工艺改进的机制,定期对工艺流程进行评估和优化。
ISO9000内审不符合(不合格)项判断参考条款

ISO9000内审不符合(不合格)项判断参考条款1. 质量方针与质量目标没有框架关系――5.32. 质量方针、目标不能被各级人员所理解和贯彻――5。
33。
质量目标没有展开到职能部门,实现不能提供证据――5。
4。
14。
管理评审未进行――5.65. 管理评审未保存原始记录――5。
6.16. 管理评审的输出没有包括与顾客要求有关的产品的改进――5.6.37。
职责和权限不清――5。
5。
18。
资源配置不足――69。
外来文件和资料不受控――4.2。
3 f)10。
电子媒体和其他形式的文件未受控――4。
2。
311. 现场不能得到相应文件有效版本,或使用不受控文件――d)12. 现场有效版本和作废版本并存--4.2.3 g)13。
现场只有作废版本--4.2.3 g)14. 文件的现行修订状态不能识别―― 4。
2.3 c)15。
文件和资料在发布前未经授权人审批其适宜性――4。
2。
3 a)16。
文件发放范围未经审批――4.2。
3 d)17。
对文件未进行必要的评审和修订――4.2。
3 b)18。
工作现场没有可依据的文件,导致了工作质量的不一致――7。
119. 质量手册对删减的细节和合理性描述不充分――4。
2.2 a)20. 质量手册对体系过程之间的相互作用没有表述-4.2。
2 c)21。
供方的产品质量记录未保存在组织--7.4或者4。
2.422。
其他各种记录按就近不就远原则处理.如合同评审无记录--7.2.223. 未规定电子媒体形式的质量记录控制方法--4.2。
424. 质量记录未规定编目、标识、归档、处理办法――4.2。
425. 没有确定从事影响产品质量工作人员所必要的能力-6。
2.2 a)26. 培训需求未确定――6.2.2 b)27. 没有保持教育、培训、技能、经验的适当记录--6。
2.2 e)28。
不能提供培训有效性评价的证据――6.2。
2 c)29. 特殊工序的操作工人资格、培训、考察、考核不符合要求--7.5。
ISO9001-2015质量管理体系判标技巧

ISO9001质量管理体系判标技巧现场审核时,审核员要经常及时地对所收集到的客观证据和形成的审核发现进行符合性判断.如何正确判断,除深刻理解标准要求外,还需掌握一些技巧,现以ISO9001:2015为例,将条款判断的一些技巧介绍如下:一、判标基本原则(各体系通用)1) 能细则细,不能细则粗;对上的则细,对不上的则粗原则:如7.5.3成文信息的控制,而不具体到其下小条款7.5.3.1、7.5.3.2.2) 最贴近原则在标准中找不到完全能"对号入座"条款时就判最为接近的条款。
3) 最有效原则当存在多种判断时按最有利改进可改进最易见效的条款处判。
4) 最关键原则当同时存在多个问题时,应寻找关键词或关键客观证据或关键问题进行判断。
5) 最密切联系原则有些问题应透过现象看本质,应与问题的产生有最紧密关系的原因处判。
6) 合并同类项原则相同的轻徽不合格项可采取合并同类项的方法,如文件控制中一些标识等。
7) 具体分析审核对象,切忌望文生义。
二、ISO9001:2015标准判标指引1) 最高管理者标准中直接涉及到最高管理者要求的条款有:5.1.1领导作用和承诺总则、5.1.2以顾客为关注焦点、5.2.1制定质量方针、5.3组织的岗位、职责和权限、9.3管理评审等,如判断上述条款有不合格项,往往意味着系统失效,且主要责任者是最高管理者,其不合格项所引起的随后措施,可能会涉及整个质量管理体系,所以应慎判。
2) 更改•对设计开发要求及相关文件的更改问题,应判8.3.6设计和开发更改;•对来自顾客产品要求相关文件的更改问题应判8.2.3产品和服务要求的评审;•对质量管理体系变更的策划问题应判6.3变更的策划PS:质量管理体系变更有哪些情况?①质量管理体系建立和实施的初始阶段;②组织结构、生产工艺发生了重大变化、需要对质量管理体系进行调整时;③有了新的要求时;④多个管理体系整合时。
•对除上述判断外,质量管理体系文件的更改部均可判到7.5.2创建和更新。
质量管理体系常见的不合格项
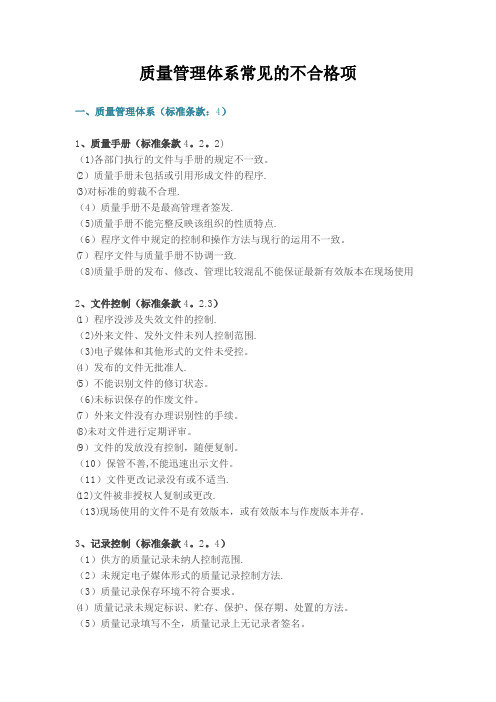
质量管理体系常见的不合格项一、质量管理体系(标准条款:4)1、质量手册(标准条款4。
2。
2)(1)各部门执行的文件与手册的规定不一致。
(2)质量手册未包括或引用形成文件的程序.(3)对标准的剪裁不合理.(4)质量手册不是最高管理者签发.(5)质量手册不能完整反映该组织的性质特点.(6)程序文件中规定的控制和操作方法与现行的运用不一致。
(7)程序文件与质量手册不协调一致.(8)质量手册的发布、修改、管理比较混乱不能保证最新有效版本在现场使用2、文件控制(标准条款4。
2.3)(1)程序没涉及失效文件的控制.(2)外来文件、发外文件未列人控制范围.(3)电子媒体和其他形式的文件未受控。
(4)发布的文件无批准人.(5)不能识别文件的修订状态。
(6)未标识保存的作废文件。
(7)外来文件没有办理识别性的手续。
(8)未对文件进行定期评审。
(9)文件的发放没有控制,随便复制。
(10)保管不善,不能迅速出示文件。
(11)文件更改记录没有或不适当.(12)文件被非授权人复制或更改.(13)现场使用的文件不是有效版本,或有效版本与作废版本并存。
3、记录控制(标准条款4。
2。
4)(1)供方的质量记录未纳人控制范围.(2)未规定电子媒体形式的质量记录控制方法.(3)质量记录保存环境不符合要求。
(4)质量记录未规定标识、贮存、保护、保存期、处置的方法。
(5)质量记录填写不全,质量记录上无记录者签名。
二、管理职责(标准条款:5)1、管理承诺(标准条款5。
1)(1)最高管理者不知道对管理承诺应提供哪些证据。
(2)组织成员对质量方针、质量目标各有各的理解。
(3)资源配置不足,检验人员素质差,内审人员未经培训.2、以顾客为关注焦点(标准条款5.2)(1)拿不出文件证实顾客的要求已得到确定。
3、质量方针(标准条款5.3)(1)质量方针空洞,体现不出企业特色,与质量目标的关系不明确。
(2)下级人员不清楚质量方针。
(3)拿不出对质量方针的评审证据.(4)有的部门也制订了质量方针。
质量体系不合格项判断

质量体系不合格项判断质量体系概述质量体系是指为规范企业产品设计、开发、生产和服务过程,保证产品质量稳定的组织形式、方法、程序和规范文件等总和。
质量体系在企业中扮演着至关重要的角色,是企业真正重视产品质量、提高竞争力的重要组成部分。
质量体系可以保证产品的质量稳定,从而提高企业产品的市场竞争力和形象,也是企业获得ISO9001国际认证的关键。
质量体系不合格项尽管质量体系对于企业的重要性毋庸置疑,但是在实际的企业生产过程中难以避免出现质量体系不合格的情况。
下面列举了一些企业质量体系不合格的主要原因:1.确定的标准不够明确,无法准确检查,导致生产品质无法保证。
2.生产过程中的数据量太大,造成后期无法快速定位问题,并解决问题。
3.生产过程中,工厂员工意识培训不足,导致产品质量的控制不佳。
4.企业缺乏有效的质量管理流程,缺乏完整的管理体系,以及质量信息不良档案管理、产品质量的分析和监控等控制措施。
如何判断质量体系不合格项在企业生产过程中,如何判断产品出现的质量体系的不合格项呢?一般来说,可以通过以下几项来进行判断:1.产品质量问题分析在产品质量出现的问题的分析过程中,经常会涉及到质量体系不合格的原因。
如果出现的问题与质量体系有关,则往往需要调整质量管理流程;如果是其他问题,则需要采取其他对策来解决问题。
2.质量体系审核和评估企业需要对质量体系进行审核和评估,以发现质量体系存在的问题和风险。
一旦发现问题,企业应该进行整改和改进,以保证质量体系变得更加完善。
3.检查质量体系文档在实际操作中,要不断审查、分析、改进质量体系,发现和深究产生问题的根源,防止不良质量事件重复发生,避免出现不合格项。
如何防止质量体系不合格项围绕于以上出现质量体系不合格项的主要原因,建议企业可以采取以下对策,避免不合格项的产生:1.加强对标准规范的定义,尤其对关键点强化管理。
2.设计和运营新的数据管控机制,把握趋势走向。
3.对员工意识加强培训,提高工作流程管理水平。
质量管理体系审核中常见的不合格项

质量管理体系审核中常见的不合格项一、质量管理体系(标准条款:4.4)1、质量手册(标准条款:2015新版无明确要求需形成质量手册)(1)各部门执行的文件与手册的规定不一致。
(2)质量手册未包括或引用形成文件的程序。
(3)对标准的剪裁不合理。
(4)质量手册不是最高管理者签发。
(5)质量手册不能完整反映该组织的性质特点。
(6)程序文件中规定的控制和操作方法与现行的运用不一致。
(7)程序文件与质量手册不协调一致。
(8)质量手册的发布、修改、管理比较混乱不能保证最新有效版本在现场使用 2、文件控制(标准条款7.5.3)(1)程序没涉及失效文件的控制。
(2)外来文件、发外文件未列人控制范围。
(3)电子媒体和其他形式的文件未受控。
(4)发布的文件无批准人。
(5)不能识别文件的修订状态。
(6)未标识保存的作废文件。
(7)外来文件没有办理识别性的手续。
(8)未对文件进行定期评审。
(9)文件的发放没有控制,随便复制。
(10)保管不善,不能迅速出示文件。
(11)文件更改记录没有或不适当。
(12)文件被非授权人复制或更改。
(13)现场使用的文件不是有效版本,或有效版本与作废版本并存。
3、记录控制(标准条款7.5.3)(1)供方的质量记录未纳人控制范围。
(2)未规定电子媒体形式的质量记录控制方法。
(3)质量记录保存环境不符合要求。
(4)质量记录未规定标识、贮存、保护、保存期、处置的方法。
(5)质量记录填写不全,质量记录上无记录者签名。
二、领导作用(标准条款:5)1、领导作用与承诺(标准条款5.1)(1)最高管理者不知道对管理承诺应提供哪些证据。
(2)组织成员对质量方针、质量目标各有各的理解。
(3)资源配置不足,检验人员素质差,内审人员未经培训。
2、以顾客为关注焦点(标准条款5.1)(1)拿不出文件证实顾客的要求已得到确定。
3、质量方针(标准条款5.2)(1)质量方针空洞,体现不出企业特色,与质量目标的关系不明确。
(2)下级人员不清楚质量方针。
质量管理体系审核中常见的不合格项

质量管理体系审核中常见的不合格项一、质量管理体系(标准条款:4.4)1、质量手册(标准条款:2015新版无明确要求需形成质量手册)(1)各部门执行的文件与手册的规定不一致。
(2)质量手册未包括或引用形成文件的程序。
(3)对标准的剪裁不合理。
(4)质量手册不是最高管理者签发。
(5)质量手册不能完整反映该组织的性质特点。
(6)程序文件中规定的控制和操作方法与现行的运用不一致。
(7)程序文件与质量手册不协调一致。
(8)质量手册的发布、修改、管理比较混乱不能保证最新有效版本在现场使用 2、文件控制(标准条款7.5.3)(1)程序没涉及失效文件的控制。
(2)外来文件、发外文件未列人控制范围。
(3)电子媒体和其他形式的文件未受控。
(4)发布的文件无批准人。
(5)不能识别文件的修订状态。
(6)未标识保存的作废文件。
(7)外来文件没有办理识别性的手续。
(8)未对文件进行定期评审。
(9)文件的发放没有控制,随便复制。
(10)保管不善,不能迅速出示文件。
(11)文件更改记录没有或不适当。
(12)文件被非授权人复制或更改。
(13)现场使用的文件不是有效版本,或有效版本与作废版本并存。
3、记录控制(标准条款7.5.3)(1)供方的质量记录未纳人控制范围。
(2)未规定电子媒体形式的质量记录控制方法。
(3)质量记录保存环境不符合要求。
(4)质量记录未规定标识、贮存、保护、保存期、处置的方法。
(5)质量记录填写不全,质量记录上无记录者签名。
二、领导作用(标准条款:5)1、领导作用与承诺(标准条款5.1)(1)最高管理者不知道对管理承诺应提供哪些证据。
(2)组织成员对质量方针、质量目标各有各的理解。
(3)资源配置不足,检验人员素质差,内审人员未经培训。
2、以顾客为关注焦点(标准条款5.1)(1)拿不出文件证实顾客的要求已得到确定。
3、质量方针(标准条款5.2)(1)质量方针空洞,体现不出企业特色,与质量目标的关系不明确。
(2)下级人员不清楚质量方针。
iatf16949质量体系内审不合格项

IATF16949质量体系内审不合格项随着汽车行业的不断发展,汽车零部件供应商面临着越来越严格的质量要求。
为了满足客户的需求,提高产品质量和服务水平,越来越多的汽车零部件供应商选择引入IATF16949质量体系,以确保其质量管理体系的稳定性和有效性。
而在IATF16949质量体系内审中,不合格项的存在会成为影响供应商声誉和持续经营的一大隐患。
一、IATF16949质量体系内审的重要性1. 了解质量管理体系运行情况。
IATF16949要求汽车零部件供应商建立并持续改进其质量管理体系,内审是了解质量管理体系运行情况、发现问题和提出改进建议的重要手段。
2. 发现问题、预防风险。
内审可以从体系运行的全过程中找出问题,为供应商避免违规,提前预防和解决可能发生的风险。
3. 提高管理效能,持续改进。
内审可以发现组织运作的不足之处,为提高管理效能,推动供应商持续改进提供有效的信息和数据支持。
二、IATF16949质量体系内审不合格项的原因1. 文件控制不严。
包括文件不适用、文件版本混乱、文件变更未及时更新等问题。
2. 流程与程序未得到遵循。
很多时候,流程与程序都是不存在的,员工违背流程与程序,导致质量事故的发生。
3. 基础设施和环境条件不符合要求。
包括生产场地、工艺设备、清洁和卫生条件等。
4. 测量和检验设备不符合要求。
测量和检验设备不合格会直接影响产品质量和供应商的可靠性。
5. 持续改进不够。
持续改进是IATF要求的核心要求之一,如果持续改进不够,将难以满足IATF体系的要求。
三、IATF16949质量体系内审不合格项的处理方法1. 分析原因,定责。
对于发现不合格项,供应商需要进行深入分析,明确不合格项的原因,并且及时确定责任人。
2. 制定纠正措施。
一旦发现不合格项,供应商需要制定纠正措施,并确定纠正措施的实施时间表和责任人。
3. 改进体系。
不合格项的存在是体系运行的问题,供应商需要对体系进行全面的检讨,确定存在的问题并加以改进。
QMS质量管理体系不合格项的判断技巧

序号
不合格项
判标说明
第 1 据识别场合、时机、对象、 目的、范围寻找标准中直接涉及到“识别”要求的相应条款。 4.1
总要求 文件控制 记录控制 设计和开发评审 设计和开发更改的控制 标识和可追溯性 顾客财产 监视和测量装置的控制 不合格品控制 数据分析 管理承诺 以顾客为关注焦点 与顾客有关的要求的确定 能力、意识和培训 设计和开发输入 设计和开发评审 管理评审 与产品有关的要求的评审 设计和开发评审 内部审核 总要求 管理承诺 评审输出 资源管理 产品实现的策划 资源的提供 管理承诺 质量方针 职责和权限 管理者代表 内部沟通 顾客沟通 设计和开发策划 采购信息 管理评审 内部审核 不合格品控制 纠正措施 预防措施 产品实现的策划 与产品有关的要求的评审 设计和开发策划 设计和开发确认
没有相应条款可判时,均可判到6.1条。
12 沟通
在对“沟通”问题进行判断时,应根据沟通对象、过程、目的寻 找直接涉及到“沟通”要求的相应条款。
13 改进
针对质量管理体系问题所采取的措施问题,宜判5.6条。 针对审核发现所采取的措施问题,宜判8.2.2条。 针对不合格产品本身所采取的措施问题,应判8.3条。
能力、意识和培训 总则 4.2.3 设计和开发输出 设计和开发更改的控制
生产和服务提供过程的确认 生产和服务提供过程的确认
产品的监视和测量 不合格品控制
23 能细则细 24 最贴近原则 25 最有效原则 26 最关键原则 27 最密切联系
原则
28 合并同类项
原则 对象
29 具体分析审核 具体分析审核对象,切忌望文生义。
对 标
10 法律
向组织传达遵守法律的问题 对组织知法的问题可根据涉及对象、范围分别判相关条款。
质量管理体系审核中常见的不合格项(精选)
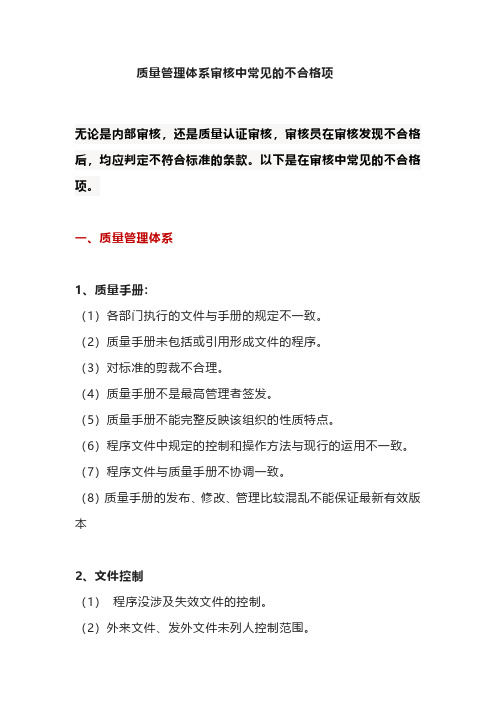
质量管理体系审核中常见的不合格项无论是内部审核,还是质量认证审核,审核员在审核发现不合格后,均应判定不符合标准的条款。
以下是在审核中常见的不合格项。
一、质量管理体系1、质量手册:(1)各部门执行的文件与手册的规定不一致。
(2)质量手册未包括或引用形成文件的程序。
(3)对标准的剪裁不合理。
(4)质量手册不是最高管理者签发。
(5)质量手册不能完整反映该组织的性质特点。
(6)程序文件中规定的控制和操作方法与现行的运用不一致。
(7)程序文件与质量手册不协调一致。
(8)质量手册的发布、修改、管理比较混乱不能保证最新有效版本2、文件控制(1) 程序没涉及失效文件的控制。
(2)外来文件、发外文件未列人控制范围。
(3)电子媒体和其他形式的文件未受控。
(4)发布的文件无批准人。
(5)不能识别文件的修订状态(6)未标识保存的作废文件。
(7)外来文件没有办理识别性的手续。
(8)未对文件进行定期评审。
(9)文件的发放没有控制,随便复制。
(10)保管不善,不能迅速出示文件。
(11)文件更改记录没有或不适当。
(12)文件被非授权人复制或更改。
(13)现场使用的文件不是有效版本,或有效版本与作废版本并存。
3、记录控制(1)供方的质量记录未纳人控制范围。
(2)未规定电子媒体形式的质量记录控制方法。
(3)质量记录保存环境不符合要求。
(4)质量记录未规定标识、贮存、保护、保存期、处置的方法。
(5)质量记录填写不全,质量记录上无记录者签名。
二、管理职责1、管理承诺(1)最高管理者不知道对管理承诺应提供哪些证据。
(2)组织成员对质量方针、质量目标各有各的理解。
(3)资源配置不足,检验人员素质差,内审人员未经培训。
2、以顾客为关注焦点(1)拿不出文件证实顾客的要求已得到确定。
3、质量方针(1)质量方针空洞,体现不出企业特色,与质量目标的关系不明确。
(2)下级人员不清楚质量方针。
(3)拿不出对质量方针的评审证据。
(4)有的部门也制订了质量方针。
- 1、下载文档前请自行甄别文档内容的完整性,平台不提供额外的编辑、内容补充、找答案等附加服务。
- 2、"仅部分预览"的文档,不可在线预览部分如存在完整性等问题,可反馈申请退款(可完整预览的文档不适用该条件!)。
- 3、如文档侵犯您的权益,请联系客服反馈,我们会尽快为您处理(人工客服工作时间:9:00-18:30)。
质量管理体系审核不合格项判断参考
福建省质量协会副秘书长
福州森海企业顾问有限公司总经理
无论是内部审核,还是质量认证审核,审核员在审核发现不合格后,均应判定不符合GB/T19001标准的条款。
本文系笔者总结了在审核中遇到的各种情况,归纳出下列的参考意见。
1.质量方针不能成为质量目标的框架――5.3
2.质量方针、目标不能被各级人员所理解和贯彻――5.3
3.质量目标没有展开到职能部门,实现情况不能提供证据――5.
4.1
4.管理评审未进行――
5.6
5.管理评审未保存原始记录――5.
6.1
6.管理评审的输出没有包括与顾客要求有关的产品的改进――5.6.3
7.职责和权限不清――5.5.1
8.资源配置不足――6
9.质量手册对删减的细节和合理性描述不充分――4.2.2a)
10.质量手册对体系过程之间的相互作用没有表述-4.2.2c)
11.外来文件不受控――4.2.3f)
12.电子媒体和其他形式的文件未受控――4.2.3
13.现场不能得到相应文件有效版本,或使用不受控文件――d)
14.现场有效版本和作废版本并存--4.2.3g)
15.现场只有作废版本--4.2.3g)
16.文件的现行修订状态不能识别――4.2.3c)
17.文件在发布前未经授权人审批其适宜性――4.2.3a)
18.文件发放范围未经审批――4.2.3d)
19.对文件未进行必要的评审和修订――4.2.3b)
20.工作现场没有可依据的文件,导致了工作质量的不一致――7.1
21.供方的产品质量记录未保存在组织--7.4或者4.2.4
22.其他各种记录按就近不就远原则处理。
如合同评审无记录--7.2.2
23.未规定电子媒体形式的质量记录控制方法--4.2.4
24.质量记录未规定编目、标识、归档、处理办法――4.2.4
25.质量记录查找不方便。
――4.2.4
26.没有确定从事影响产品质量工作人员所必要的能力-6.2.2a)
27.培训需求或采取其他措施(如招聘)的要求未确定――6.2.2b)
28.没有保持教育、培训、技能、经验的适当记录--6.2.2e)
29.不能提供培训有效性评价的证据――6.2.2c)
30.特殊工序的操作工人资格、培训、考察、考核不符合要求--7.5.2
31.检验人员、内审人员、计量人员不能胜任工作,未取得培训合格资格――6.2.1
32.没有对与产品有关的四个方面要求进行确定――7.2.1
33.未在合同签订前进行合同评审――7.2.2
34.只对重要、大宗订货合同进行评审,未对零星、口头合同进行评审――7.2.2
35.未对顾客特殊要求进行识别――7.2.1
36.交货后发现组织没有履行合同能力――7.2.2
37.合同更改未按程序进行――7.2.2
38.合同更改后未传递到有关职能部门――7.2.2
39.没有保存合同评审结果或所引起措施的记录――7.2.2
40.没有进行设计和开发的策划――7.3.1
41.设计输入未确定,未作评审,或未包括适用的法规和法律――7.3.2
42.设计输出不符合输入要求或文件不完整或发放前未经评审和得到批准――7.3.3
43.设计未验证或样机不合格仍投产――7.3.5
44.样机合格性确认不符合要求仍投产――7.3.6
45.可进行确认但未做――7.3.6
46.设计修改(含笔误)不按规定程序――7.3.7
47.未根据满足合同要求能力评价和选择分承包方――7.4.1
48.需方指定采用某供方产品,供方对该分供方不评定也不检验其产品――7.4
49.未明确规定对供方实行控制的方式和程度――7.4.1
50.采购资料中未规定产品的技术指标和检验规程――7.4.2
51.对采购产品的验证方式未在采购文件中规定――7.4.3
52.不在合格供方名单中采购,也未按程序规定办理手续――7.4.1
53.委托检验或委托搬运等活动,未对分承包方进行评审――7.4.1
54.顾客提供的产品(元器件、材料),未验证,也未保管好--7.5.4
55.顾客提供的产品不适用或损坏时未记录并向顾客报告--7.5.4
56.生产中产品无证明其身份的标志(过程卡、路线卡、随工单等),出了问题无法追溯- 7.5.3
57.一批产品,生产中再分批未复制或增加过程卡等标识-7.5.3
58.产品标志在加工中消失而未补加标志-7.5.3
59.原材料未能检验紧急使用前未加标志――7.5.3
60.半成品未能检验紧急转序未加标志――7.5.3
61.包装标志不符合要求-7.5.5
62.不合格品未加标志-7.5.3
63.未获得表述产品特性的信息――7.5.1a)
64.由于未能获得作业指导书而影响产品质量-7.5.1b)
65.有章(操作规程、工艺规程等)不循,即使合理也不合法-7.5.1
66.几种规定都有效,互相矛盾,难以控制工序--7.1
67.操作人员不知道按操作规程做--6.2.2
68.操作人员做假记录7.5.1e)
69.生产现场没有配置监视和测量装置。
7.5.1d)
70.设备的维护没有计划、也没有记录。
--6.3
71.现场环境不符合规定-6.4
72.领用的原材料没有标识或检验状态――7.5.3
73.未编制检验程序或检验计划或检验操作规程--7.1
74.未按检验程序、质量计划、规范检验--8.2.4
75.对进货没有进行验证――7.4.3
76.规定应专人检验,而擅自改为自检--8.2.4
77.进料、工序检验未完成或不合格就作成品检验--8.2.4
78.检验员因工作量太大而简化、或减少检验次数。
--8.2.4
79.检验记录未建立或未保存或未按规定做--8.2.4
80.返工返修后未复检--8.3
81.检验规范规定的统计抽样检验方法不合理--7.1
82.标准溶液未规定有效期或已经失效――7.6
83.试验软件作为检验手段而未作检查--7.6
84.不对检测设备校验。
只对设备中的计量器具进行校验,如只对水浴锅中的温度计进行校验--7.6
85.对难以校验的检测设备无自校规程--7.6
86.因为有了设备的出厂合格证,就没有进行校准或检定――7.6
87.监视和测量装置无有效校准状态标志--7.6
88.对检验和试验状态的标识没有作出规定--7.5.3
89.现场产品检验状态标志错误--7.5.3
90.现场产品无检验状态标识--7.5.3
91.出了不合格品不标识、不隔离--8.3
92.出了不合格品不评审、不处置--8.3
93.出了不合格品不通知有关部门或由无资格(无权)人员处理--8.3
94.让步接收不合格品未经有关授权人员批准--8.3
95.返修/返工后产品未进行重新检验--8.3
96.没有保持不合格的性质以及随后所采取任何措施的记录――8.3
97.多次出了不合格品,不分析原因,不采取纠正措施--8.5.2
98.内审发现不合格,不采取治本的纠正措施--8.2.2
99.纠正措施实施了但未记录其结果或记录不详细--8.5.2
100.对顾客的报怨、投诉,不分析、不处理--8.5.2a)
101.未将预防和纠正措施的状况提交管理评审――5.6.2d)
102.厂内搬运不符合要求--7.5.5
103.交付搬运不符合要求--7.5.5
104.擅自修改包装图纸设计--7.3.7
105.不按包装设计包装--7.5.5
106.包装车间工序失控--7.5.1
107.未规定授权接收和发放的管理办法--7.5.5
108.仓库管理办法中未规定定期检查库存品状况,帐、物、卡不符--7.5.5
109.仓库条件不符合规定-7.5.5
110.未按保管程序(如先进先出、隔离存放)进行--7.5.5
111.未能确定对获取顾客满意信息的方法--8.2.1
112.未能利用对获取的顾客满意信息--8.2.1
113.内部审核未编制计划,未按内审程序进行--8.2.2
114.内审员未经培训或任命资格证实――6.2.2
115.内审后未采取纠正措施--8.2.2
116.内审员与被审核工作有直接责任关系--8.2.2
117.不能提供内审结果纠正措施的跟踪验证记录--8.2.2
118.没有开展对质量管理体系过程进行监视和测量的活动--8.2.3
119.未规定公司应该提供的服务内容--7.2.3
120.合同规定要服务而不执行--7.2.3
121.未确定数据分析的需求--8.4
122.没有开展数据分析分析活动--8.4
123.未开展对统计技术的培训,选错统计方法或应用错误-6.2.2。