折弯形状与模具选择
折弯机模具选材及模具性能特点

折弯机模具选材及模具性能特点在金属加工领域,折弯机是一种常用的设备,而折弯机模具则是决定折弯效果和产品质量的关键因素。
正确选择折弯机模具的材料以及了解其性能特点,对于提高生产效率、保证产品质量、降低成本都具有重要意义。
一、折弯机模具的分类折弯机模具通常可以分为上模和下模。
上模一般是凸模,下模则是凹模。
根据不同的折弯需求,模具的形状和尺寸也会有所不同。
常见的有直刀模具、弯刀模具、R 形模具等。
二、折弯机模具选材的重要性合适的模具材料能够确保模具在长期的使用过程中保持良好的性能和精度。
首先,它影响模具的使用寿命。
优质的材料能够承受更多的折弯次数和更大的压力,减少磨损和变形,从而延长模具的使用寿命。
其次,选材直接关系到折弯产品的质量。
材料的硬度、韧性等性能会影响折弯的精度和表面质量。
此外,好的材料还能提高生产效率,减少模具更换和维修的时间。
三、常见的折弯机模具材料1、碳素工具钢碳素工具钢价格相对较低,具有一定的硬度和耐磨性。
但其韧性较差,容易在使用过程中出现崩刃和断裂的情况,适用于一些简单、小批量的折弯加工。
2、合金工具钢合金工具钢在碳素工具钢的基础上加入了一些合金元素,如铬、钼、钨等,提高了材料的硬度、耐磨性和韧性。
这种材料的综合性能较好,能够满足大多数折弯加工的需求,是比较常用的模具材料之一。
3、高速钢高速钢具有较高的硬度、耐磨性和红硬性,即在高温下仍能保持较高的硬度。
但高速钢的价格较高,一般用于对精度和表面质量要求较高的折弯模具。
4、硬质合金硬质合金是一种硬度极高、耐磨性极好的材料。
它能够在恶劣的工作条件下保持良好的性能,但由于其脆性较大,加工难度较高,成本也较高,通常用于特殊要求的折弯模具。
四、折弯机模具材料的选择因素1、折弯材料不同的折弯材料对模具的磨损程度不同。
例如,不锈钢等硬度较高的材料需要选用硬度更高的模具材料,以防止模具过早磨损。
2、折弯厚度折弯材料的厚度越大,所需的模具强度和耐磨性就越高。
开槽折弯模具设计方案
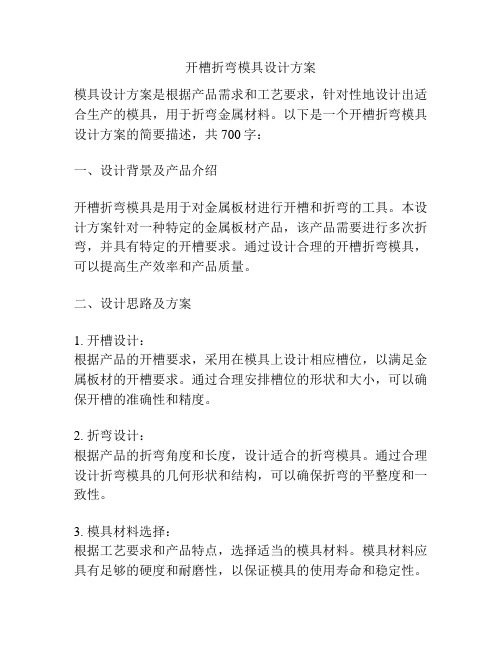
开槽折弯模具设计方案模具设计方案是根据产品需求和工艺要求,针对性地设计出适合生产的模具,用于折弯金属材料。
以下是一个开槽折弯模具设计方案的简要描述,共700字:一、设计背景及产品介绍开槽折弯模具是用于对金属板材进行开槽和折弯的工具。
本设计方案针对一种特定的金属板材产品,该产品需要进行多次折弯,并具有特定的开槽要求。
通过设计合理的开槽折弯模具,可以提高生产效率和产品质量。
二、设计思路及方案1. 开槽设计:根据产品的开槽要求,采用在模具上设计相应槽位,以满足金属板材的开槽要求。
通过合理安排槽位的形状和大小,可以确保开槽的准确性和精度。
2. 折弯设计:根据产品的折弯角度和长度,设计适合的折弯模具。
通过合理设计折弯模具的几何形状和结构,可以确保折弯的平整度和一致性。
3. 模具材料选择:根据工艺要求和产品特点,选择适当的模具材料。
模具材料应具有足够的硬度和耐磨性,以保证模具的使用寿命和稳定性。
4. 模具加工工艺:根据模具设计要求,采用合适的加工工艺制造模具。
通过合理安排加工工序和控制加工精度,确保模具的准确性和可用性。
5. 模具调试和优化:在模具加工完成后,进行模具调试和优化。
通过合理调整模具的参数和结构,可以提高模具的使用效果和生产效率。
三、设计特点及优势1. 适应性强:本设计方案可以根据产品需求进行灵活调整和优化,适应不同规格和尺寸的金属板材产品的生产需求。
2. 精度高:通过合理设计和优化,可以确保开槽和折弯的精度和一致性,提高产品质量和生产效率。
3. 可靠性好:通过合理选择模具材料和加工工艺,并采用适当的模具调试和优化措施,可以确保模具的稳定性和长期可靠性。
四、总结本开槽折弯模具设计方案通过合理的设计思路和方案,可以满足金属板材产品的开槽和折弯需求。
通过适应性强、精度高、可靠性好等特点和优势,可以提高生产效率和产品质量,促进企业的发展。
第3章 弯曲工艺与模具设计

3.2.2、影响回弹的因素 材料的机械性能 相对弯曲半径 弯曲中心角 模具间隙 弯曲件的形状 弯曲力
3.2.3、回弹值的确定 目的:作为修正模具工作部分参数的 依据。 经验公式: 1.小半径弯曲的回弹( r / t 5 ~ 8 )
0 t
rt r 1 3
90
90
6)弹性材料的准确回弹值需要通过试模对凸、 凹模进行修正确定,因此模具结构设计要便于拆 卸。 7)由于U形弯曲件校正力大时会贴附凸模,所以 在这种情况下弯曲模需设计卸料装置。 8)结构设计应考虑当压力机滑块到达下极点时, 使工件弯曲部分在与模具相接触的工作部分间得 到校正。 9)设计制造弯曲模具时,可以先将凸模圆角半 径做成最小允许尺寸,以便试模后根据需要修整 放大。
当工件局部边缘部分需弯曲时,为防 止弯曲部分受力不均而产生变形和裂纹, 应预先切槽或冲工艺孔(如图所示) 5.弯曲件的几何形状 如果弯曲件的形状不对称或者左右弯 曲半径不一致,弯曲时板料将会因摩擦阻 力不均匀而产生滑动偏移(如图所示), 为了防止这种现象的发生,应在模具上设 置压料装置,或利用弯曲件上的工艺孔采用 定位销定位(如图所示)
第 3 章 弯曲工艺与模具设计
3.1
3.2
弯曲的基本原理 应变中性层位置、最小弯曲半径的确定及回弹现象 弯曲力和弯曲件的毛坯尺寸计算 弯曲件的工艺性 弯曲模具的设计
3.3 3.4
3.5
3.1 弯曲的基本原理
弯曲是使材料产生塑性变形,形成一 定曲率和角度零件的冲压工序(如图所示) 弯曲材料:板料、棒料、型材、管材 弯曲方法:压弯、折弯、拉弯、滚弯、 辊弯
3.1.1 弯曲变形过程 (图3.1.1) 1、变形毛坯的受力情况 从力学角度,弯曲分为: 弹性弯曲 弹塑性弯曲 纯塑性弯曲 无硬化弯曲
折弯常见问题处理方法

3) 加工的先后顺序一定要正确。
4)针对特殊的加工﹐可用如下方法加工﹕
-------中心线分离法(偏心加工)
-------小V加工(需增大折弯系数)
-------易模成形
-------修磨下模
4﹐反折压平
反折压平又称压死边。
1)死边的加工步骤为:先折弯插深至35度左右﹐再用压平模压平至贴平贴紧。
2>﹐卯不紧是由于抽孔胀开不到位。
3>﹐变形存在孔错位或卯合方式不对造成。
解决方法﹕
1>﹐改选用大R角的冲子。
注意抽孔翻边时孔周围的毛刺。
2>﹐加大压力
色拉孔加大加深
改用大R角的冲子。
3>﹐改变卯合方式及孔错位的原因法掘。
10﹐螺柱压卯歪斜或压卯后工件变形
原因分析﹕
1>﹐加工产品时没有断平工件。
2>﹐工件下表面受力不均匀或压力过大。
6﹐大高度抽桥易断裂
原因分析﹕
1>﹐由于抽桥高度太高﹐材料拉伸严重导致断裂。
2>﹐易模棱角未修磨或修磨不够。
3>﹐材料的韧性太差或桥体太窄。
解决方法﹕
1>﹐在断裂的一边加长工艺孔。
2>﹐增大抽桥宽度。
3>﹐修磨易模R角﹐增大圆弧过渡。
4>﹐加润滑油于抽桥处。(因此种方法会使工件表面脏污﹐故对AL件等无法采用)
1.目的.
了解易模加工的范围及性能
2.适用范围.
工艺部
3.引用文件.
无
4.主要内容.
一﹐折床加工内容
1﹐L折
按角度分为90˚折和非90˚折。
按加工分一般加工(L>V/2)和特殊加工(L<V/2)。
折弯机上下模选用标准
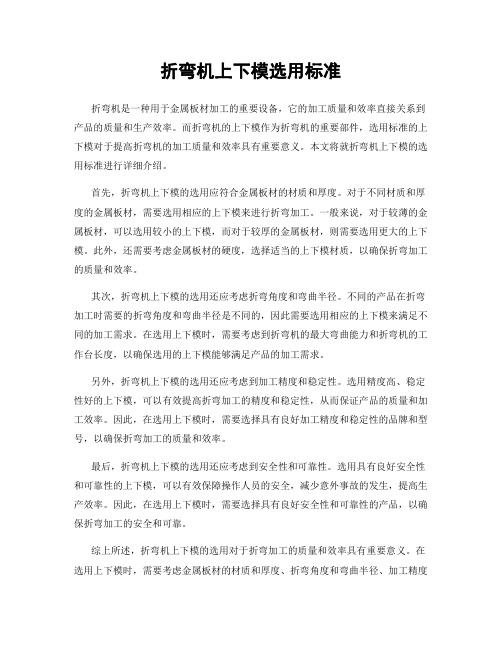
折弯机上下模选用标准折弯机是一种用于金属板材加工的重要设备,它的加工质量和效率直接关系到产品的质量和生产效率。
而折弯机的上下模作为折弯机的重要部件,选用标准的上下模对于提高折弯机的加工质量和效率具有重要意义。
本文将就折弯机上下模的选用标准进行详细介绍。
首先,折弯机上下模的选用应符合金属板材的材质和厚度。
对于不同材质和厚度的金属板材,需要选用相应的上下模来进行折弯加工。
一般来说,对于较薄的金属板材,可以选用较小的上下模,而对于较厚的金属板材,则需要选用更大的上下模。
此外,还需要考虑金属板材的硬度,选择适当的上下模材质,以确保折弯加工的质量和效率。
其次,折弯机上下模的选用还应考虑折弯角度和弯曲半径。
不同的产品在折弯加工时需要的折弯角度和弯曲半径是不同的,因此需要选用相应的上下模来满足不同的加工需求。
在选用上下模时,需要考虑到折弯机的最大弯曲能力和折弯机的工作台长度,以确保选用的上下模能够满足产品的加工需求。
另外,折弯机上下模的选用还应考虑到加工精度和稳定性。
选用精度高、稳定性好的上下模,可以有效提高折弯加工的精度和稳定性,从而保证产品的质量和加工效率。
因此,在选用上下模时,需要选择具有良好加工精度和稳定性的品牌和型号,以确保折弯加工的质量和效率。
最后,折弯机上下模的选用还应考虑到安全性和可靠性。
选用具有良好安全性和可靠性的上下模,可以有效保障操作人员的安全,减少意外事故的发生,提高生产效率。
因此,在选用上下模时,需要选择具有良好安全性和可靠性的产品,以确保折弯加工的安全和可靠。
综上所述,折弯机上下模的选用对于折弯加工的质量和效率具有重要意义。
在选用上下模时,需要考虑金属板材的材质和厚度、折弯角度和弯曲半径、加工精度和稳定性、安全性和可靠性等因素,以确保选用的上下模能够满足产品的加工需求,提高折弯加工的质量和效率。
折弯模具标准

折弯模具标准折弯模具标准主要包括以下几个方面:1. 材质选择:折弯模具通常采用T8、T10、42CrMo等材质制成。
其中,T8和T10适用于一般需求,42CrMo则适用于高强度、高韧性及良好的耐磨性能的要求。
2. 淬火硬化:模具淬火后的硬度一般在HRC52-60之间。
不同的模具类型和应用场景对硬度要求可能有所不同。
3. 模具分段:折弯模具通常分为上模、下模、导轨等部件。
上模和下模根据工件的形状和折弯角度有所不同,常见的有直角折弯、圆弧折弯、U型折弯等。
导轨则用于引导工件在折弯过程中的运动。
4. 模具尺寸:标准折弯模具的长度通常为835mm、800mm、550mm 等。
此外,根据工件尺寸和折弯机类型,模具尺寸也可以定制。
5. 模具形状:根据工件形状和折弯角度,折弯模具有多种形状,如90度、88度、86度、60度、45度、30度等。
6. 尖端R角和尖端角度:尖端R角有0.2R、0.6R、0.8R、1.5R、3.0R等不同选择。
标准尖端角度有90度、88度、86度、60度、45度、30度等。
7. 模具组合:根据不同工件的形状和折弯顺序,折弯模具可以组合使用。
例如,在折弯锐角或压死角时,应选用30度上模,先折锐角,后压死边。
在折弯R角时,应选用R上模和R下模进行。
8. 适用范围:折弯模具适用于各种品牌折弯机床,如阿玛达(Amada)、天田(Tokyo)、小松(Komatsu)、东洋(Toyokoki)、比利时(LVD)、贝勒(Beyeler)、村田(Murata)、德国通快(Trumpf)、德国海穆勒(Hammerle)、瑞士百超(Bystronic)、芬兰芬宝(Finn-Power)、爱克(AccurPress)等。
9. 非标定制:根据客户提供的图纸要求,可以定制非标准折弯模具。
例如,特殊形状的折弯模具、段差模、无压痕模、集装箱模、铰链模等。
折弯模具标准涵盖了材质、尺寸、形状、角度、组合等多个方面,根据工件需求和折弯机类型选择合适的模具,可以实现高效、高质量的折弯加工。
折弯规范管理

折弯规范管理折弯规范管理是指在工业生产过程中,针对金属板材的折弯加工操作进行规范化管理的一种方法。
折弯是将金属板材按照一定的角度和形状弯曲的工艺,常用于创造各种金属制品,如汽车零部件、家具、电子设备等。
为了确保折弯加工的质量和效率,折弯规范管理需要包括以下几个方面的内容:1. 技术规范:制定和执行符合国家标准和行业规范的折弯技术规范。
这些规范应包括折弯角度、弯曲半径、板材厚度、模具选择、折弯工艺参数等方面的要求。
通过制定统一的技术规范,可以确保不同操作人员在进行折弯操作时遵循相同的标准,提高产品的一致性和稳定性。
2. 设备管理:对折弯设备进行定期维护和检修,确保设备的正常运行和准确性。
包括保持设备的清洁、润滑、校准等工作。
同时,应对设备进行定期的性能检测,以确保其在折弯过程中的准确度和稳定性。
3. 模具管理:对折弯过程中使用的模具进行管理和维护。
模具是决定折弯形状和尺寸的重要因素,需要保持模具的完好和准确性。
定期检查模具的磨损情况,及时更换损坏的模具,避免因模具问题导致的折弯质量问题。
4. 操作人员培训:对折弯操作人员进行专业培训,提高其折弯技术和操作技能。
培训内容包括折弯工艺知识、设备操作技巧、模具使用和维护等方面。
通过培训,使操作人员具备良好的专业素质和操作技能,能够准确、高效地完成折弯任务。
5. 质量控制:建立完善的折弯质量控制体系,包括对折弯产品进行抽样检验、尺寸测量、外观检查等。
通过严格的质量控制,确保折弯产品符合设计要求和客户需求,提高产品质量和客户满意度。
6. 数据记录和分析:对折弯过程中的关键数据进行记录和分析,包括折弯角度、弯曲力度、板材厚度等参数。
通过数据分析,可以及时发现折弯过程中的问题和不良趋势,并采取相应的改进措施,提高折弯工艺的稳定性和可控性。
7. 持续改进:定期评估和改进折弯规范管理的效果和成效,及时调整和优化管理措施。
通过持续改进,不断提高折弯工艺的质量和效率,降低生产成本,提高企业竞争力。
折弯上模r角选用标准

折弯上模r角选用标准一、模具结构模具结构应设计合理,符合折弯工艺要求,能够满足R角的形成和变化。
模具结构应简洁、易于维护和操作,能够保证生产的稳定性和效率。
二、材料选择材料选择应考虑到耐磨性、抗压强度、抗冲击性等因素。
常用的材料有高速钢、合金钢、不锈钢等,可以根据不同的工艺要求和生产需求进行选择。
三、模具硬度模具硬度是影响折弯上模R角选用的重要因素之一。
硬度过高会导致模具脆性增加,容易开裂;硬度过低则会导致模具耐磨性下降,寿命缩短。
因此,在选择模具时,应根据使用要求和生产条件合理选择硬度范围。
四、加工精度折弯上模R角的加工精度对其选用的影响也很大。
精度高的模具能够保证R角的尺寸和形状精度,提高生产效率和产品质量;精度低的模具则会影响到R角的形成和变化,导致生产效率下降和产品质量不稳定。
五、表面处理表面处理对折弯上模R角的选用也有一定的影响。
表面处理可以改变模具表面的物理和化学性能,提高模具的耐磨性、抗冲击性和使用寿命。
常见的表面处理方法有渗碳、渗氮、镀铬等。
六、尺寸稳定性尺寸稳定性是衡量折弯上模R角选用是否合理的重要指标之一。
尺寸稳定性好的模具能够保证R角的尺寸和形状稳定,提高生产效率和产品质量;尺寸稳定性差的模具则会导致R角的尺寸和形状变化不定,影响生产效率和产品质量。
七、抗冲击性抗冲击性是折弯上模R角选用的重要因素之一。
抗冲击性好的模具能够承受较大的冲击载荷,提高产品的质量和稳定性;抗冲击性差的模具则会导致开裂、崩角等问题,影响产品的质量和稳定性。
八、使用寿命使用寿命是衡量折弯上模R角选用是否合理的重要指标之一。
使用寿命长的模具能够提高生产效率和降低成本;使用寿命短的模具则需要频繁更换,增加生产成本和时间成本。
玻璃折弯的技巧

玻璃折弯的技巧
玻璃折弯是一项需要专业技巧和设备的工艺,以下是一些常用的技巧:
1.选择适合折弯的玻璃:玻璃的类型、厚度和质量都会影响折弯的效果。
一般来说,钢化玻璃和热弯玻璃更容易折弯。
2.控制温度:玻璃折弯需要加热至高温软化状态,然后再使其快速冷却以保持所需的形状。
因此,控制加热和冷却的温度非常重要,需要根据玻璃的类型和厚度来确定合适的温度范围。
3.使用模具:为了得到所需的形状,通常需要在折弯过程中使用模具。
模具可以是金属的或者是基于玻璃形状的木制模具。
使用模具可以使玻璃保持所需的形状,并防止在折弯过程中变形或破裂。
4.掌握折弯技巧:玻璃折弯需要一定的经验和技巧。
操作时需要掌握适当的力度和速度,避免过度施力或过快移动导致玻璃破损。
5.安全措施:由于玻璃折弯需要高温处理,操作过程中必须要注意安全。
穿戴专业的防护设备,如耐高温手套、防护眼镜和工作服,以保护自己的安全。
总的来说,玻璃折弯技巧需要结合经验和专业设备,并且需要注意安全,这样才能顺利完成折弯过程。
建议在进行玻璃折弯之前咨询专业人士或相关工艺师进行
指导。
弯曲模具设计

弯曲模具的结构设计是在弯曲工序确定后的基础上进行的,设计时应考虑弯曲件的形状、精度要求、材料性能以及生产批量等因素,下面分析常见各类型弯曲模的结构和特点。
一. V 形件弯曲模V 形件即为单角弯曲件,形状简单,能够一次弯曲成形。
这类形状的弯曲件可以用两种方法弯曲:一种是沿着工件弯曲角的角平分线方向弯曲,称为V 形弯曲;另一种是垂直于工件一条边的方向弯曲,称为 L 形弯曲。
1-顶杆;2定位钉;3-模柄; 4-凸模;5-凹模;6-下模座;3.4.1 有压料装置的V形件弯曲模V 形件弯曲模的基本结构如图 3.4.1 所示,图中弹簧顶杆 1 是为了防止压弯时板料偏移而采用的压料装置。
除了压料作用以外,它还起到了弯曲后顶出工件的作用。
这种模具结构简单,对材料厚度公差的要求不高,在压力机上安装调试也较方便。
而且工件在弯曲冲程终端得到校正,因此回弹较小,工件的平面度较好。
如果弯曲件精度要求不高,为简化模具结构,压料装置也可以省略不用。
图 3.4.2 所示为无压料装置的 V 形件弯曲模。
1-模柄;2-上模座;3-导柱、导套;4、7-定位板;5-下模座;6-凹模;7-凸模3.4.2 无压料装置的V形件弯曲模当弯曲相对宽度很大的细长 V 形件时,会产生明显的翘曲现象,这种情况下可以采用带侧板结构的弯曲模,以阻碍材料沿弯曲线方向的流动(见图3.4.3a );也可以改变弯曲凸、凹模形状,将翘曲量设计在与翘曲方向相反的方向上(见图 3.4.3b )。
图3.4.3 减少弯曲件翘曲的模具结构L 形弯曲模常用于两直边相差较大的单角弯曲件,如图 3.4.4a 所示。
弯曲件的长边被夹紧在压料板和凸模之间,弯曲件过程中另一边竖立向上弯曲。
由于采用了定位销定位和压料装置,压弯过程中工件不易偏移。
但是,由于弯曲件竖边无法受到校正,因此工件存在回弹现象。
a〕1-凸模;2-凹模;3-定位销;4-压料板;5-挡块 b〕1-凸模;2-压料板 3-凹模;4-定位板;5-挡块图3.4.4 L形弯曲模图 3.4.4b 为带有校正作用的 L 形弯曲模,由于压弯时工件倾斜了一定的角度,下压的校正力可以作用于原先的竖边,从而减少了回弹。
折弯机的工艺技术要求
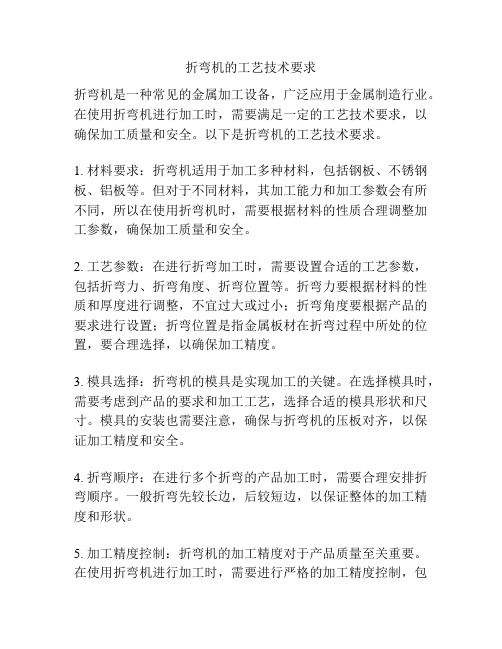
折弯机的工艺技术要求折弯机是一种常见的金属加工设备,广泛应用于金属制造行业。
在使用折弯机进行加工时,需要满足一定的工艺技术要求,以确保加工质量和安全。
以下是折弯机的工艺技术要求。
1. 材料要求:折弯机适用于加工多种材料,包括钢板、不锈钢板、铝板等。
但对于不同材料,其加工能力和加工参数会有所不同,所以在使用折弯机时,需要根据材料的性质合理调整加工参数,确保加工质量和安全。
2. 工艺参数:在进行折弯加工时,需要设置合适的工艺参数,包括折弯力、折弯角度、折弯位置等。
折弯力要根据材料的性质和厚度进行调整,不宜过大或过小;折弯角度要根据产品的要求进行设置;折弯位置是指金属板材在折弯过程中所处的位置,要合理选择,以确保加工精度。
3. 模具选择:折弯机的模具是实现加工的关键。
在选择模具时,需要考虑到产品的要求和加工工艺,选择合适的模具形状和尺寸。
模具的安装也需要注意,确保与折弯机的压板对齐,以保证加工精度和安全。
4. 折弯顺序:在进行多个折弯的产品加工时,需要合理安排折弯顺序。
一般折弯先较长边,后较短边,以保证整体的加工精度和形状。
5. 加工精度控制:折弯机的加工精度对于产品质量至关重要。
在使用折弯机进行加工时,需要进行严格的加工精度控制,包括角度精度、尺寸精度等。
在设备调试和正式加工中,需要通过调整工艺参数和模具,以及对加工工艺的不断优化,来提高加工精度。
6. 安全操作:折弯机是一种大功率设备,操作时需要注意安全。
操作人员需要熟悉设备的安全操作规程,保持机器周围的清洁和整齐,佩戴个人防护设备,避免操作过程中发生事故。
总之,折弯机的工艺技术要求是为了保证加工质量和安全。
在使用折弯机进行加工时,需要合理选择材料、设置工艺参数、选择合适的模具、安排折弯顺序、控制加工精度,并注意安全操作规程。
通过合理的工艺技术要求的控制和优化,可以提高折弯机加工的效率和质量。
厚板折弯冲压注意事项
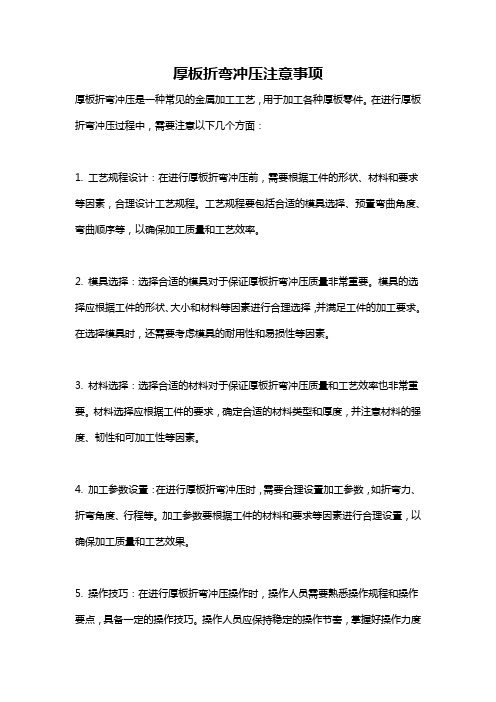
厚板折弯冲压注意事项厚板折弯冲压是一种常见的金属加工工艺,用于加工各种厚板零件。
在进行厚板折弯冲压过程中,需要注意以下几个方面:1. 工艺规程设计:在进行厚板折弯冲压前,需要根据工件的形状、材料和要求等因素,合理设计工艺规程。
工艺规程要包括合适的模具选择、预置弯曲角度、弯曲顺序等,以确保加工质量和工艺效率。
2. 模具选择:选择合适的模具对于保证厚板折弯冲压质量非常重要。
模具的选择应根据工件的形状、大小和材料等因素进行合理选择,并满足工件的加工要求。
在选择模具时,还需要考虑模具的耐用性和易损性等因素。
3. 材料选择:选择合适的材料对于保证厚板折弯冲压质量和工艺效率也非常重要。
材料选择应根据工件的要求,确定合适的材料类型和厚度,并注意材料的强度、韧性和可加工性等因素。
4. 加工参数设置:在进行厚板折弯冲压时,需要合理设置加工参数,如折弯力、折弯角度、行程等。
加工参数要根据工件的材料和要求等因素进行合理设置,以确保加工质量和工艺效果。
5. 操作技巧:在进行厚板折弯冲压操作时,操作人员需要熟悉操作规程和操作要点,具备一定的操作技巧。
操作人员应保持稳定的操作节奏,掌握好操作力度和速度,注意保持机床和模具的清洁和润滑,以提高加工质量和工艺效率。
6. 安全防护:在进行厚板折弯冲压时,要严格遵守相关的安全操作规程和安全防护要求。
操作人员应戴好个人防护用品,如手套、护目镜等,保护好自己的人身安全。
同时,还应定期对机床设备和模具进行维护和保养,确保设备的安全可靠性。
7. 质量检验:在完成厚板折弯冲压后,需要进行质量检验,以确保加工质量达到要求。
质量检验可以通过目测、量测和使用检测设备等多种方法进行,对于不合格的工件需要及时予以整改。
总之,厚板折弯冲压是一项较为复杂的金属加工工艺,需要注意上述事项,方能保证加工质量和工艺效率。
同时,还需加强员工培训和技术储备,提高工艺水平和操作能力,以适应市场需求的不断变化。
钣金折弯注意事项

钣金折弯注意事项钣金折弯是一种常见的金属加工方法,用于将金属板材折弯成所需的形状和角度。
在进行钣金折弯操作时,需要注意以下几点:1. 材料选择:钣金折弯可以适用于各种金属材料,如不锈钢、铝合金、铜等。
在选择材料时,需考虑其机械性能和成本因素,以确保折弯后的零件满足设计要求。
2. 厚度和硬度:钣金折弯的材料厚度和硬度对折弯工艺和设备要求有一定影响。
通常,较大的板厚和硬度会增加折弯力和设备要求,因此需要根据具体情况进行调整。
3. 折弯工艺:根据所需折弯角度和形状,选择合适的工艺方法,如V型模具折弯、U型模具折弯等。
在折弯过程中,需要合理安排模具的位置和角度,以确保折弯后的零件尺寸和形状准确。
4. 设备选择:钣金折弯通常使用折弯机进行操作。
在选择设备时,需考虑板材的尺寸、厚度和折弯角度要求,选择合适的折弯机型号和模具。
5. 边料处理:在钣金折弯过程中,会产生一定数量的边料。
对于边料的处理,可以选择切割、破碎或回收利用,以减少材料浪费。
6. 技术要求:钣金折弯需要操作人员具备一定的技术知识和经验。
操作人员应熟悉折弯机的操作规程和安全要求,掌握折弯工艺和操作技巧,以确保折弯过程的安全和质量。
7. 零件设计:在进行钣金折弯前,需要进行零件的设计和排样。
设计要考虑到折弯后的零件形状和尺寸变化,合理安排折弯位置和顺序,以确保最终零件满足设计要求。
8. 折弯角度控制:钣金折弯过程中,需要控制折弯角度的准确性。
可以通过调整折弯机的参数、模具的位置和角度等手段,来控制折弯角度的精度。
9. 表面保护:钣金折弯后的零件表面可能会出现划痕或变形。
为了保护零件表面的完整性,可以采取适当的措施,如使用保护膜、添加胶垫等。
10. 质量检验:钣金折弯完成后,需要进行质量检验。
可以使用量具、投影仪等设备来检测折弯角度、尺寸精度和表面质量,以确保零件的质量符合要求。
总结起来,钣金折弯是一项需要技术和经验的金属加工方法。
通过合理选择材料、工艺和设备,严格控制折弯角度和质量要求,可以得到满足设计要求的优质零件。
折弯规范管理

折弯规范管理标题:折弯规范管理引言概述:折弯是金属加工中常见的一种工艺,通过对金属板材进行折弯加工,可以制作出各种形状的零部件。
然而,折弯工艺需要严格的规范管理,以确保产品质量和生产效率。
本文将介绍折弯规范管理的重要性和具体实施方法。
一、工艺参数的确定1.1 确定折弯角度:根据设计图纸和产品要求确定每个零件的折弯角度,避免出现偏差。
1.2 确定折弯半径:根据金属板材的厚度和材质确定合适的折弯半径,避免出现开裂或变形。
1.3 确定折弯顺序:根据零件的结构和形状确定折弯的顺序,避免出现错位或重叠。
二、模具的选择和维护2.1 选择合适的模具:根据零件的形状和尺寸选择合适的模具,确保折弯的准确性和稳定性。
2.2 定期维护模具:定期清洁和润滑模具,检查模具的磨损和损坏情况,及时更换或修复损坏的模具。
2.3 标记和存放模具:对模具进行标记,避免混淆和错误使用,并妥善存放,防止损坏和丢失。
三、操作员的培训和监督3.1 培训操作员:对折弯工艺进行培训,包括操作技巧、安全注意事项和质量要求,确保操作员具备必要的技能。
3.2 监督操作员:定期对操作员进行监督和检查,及时纠正错误和不良习惯,确保操作规范和质量稳定。
3.3 奖惩机制:建立奖惩机制,激励操作员遵守规范操作,提高工作效率和产品质量。
四、质量检验和反馈4.1 折弯后的质量检验:对每个零件进行折弯后的质量检验,包括尺寸、角度和外观等方面,确保产品符合要求。
4.2 异常处理和反馈:对于出现的质量问题和异常情况,及时处理和记录,并进行反馈,找出问题的原因并采取改进措施。
4.3 持续改进和优化:根据质量检验和反馈结果,持续改进折弯工艺和管理措施,提高产品质量和生产效率。
五、设备维护和保养5.1 定期保养设备:对折弯设备进行定期保养和检查,确保设备运行稳定和正常。
5.2 检查润滑和冷却系统:定期检查润滑和冷却系统的工作情况,确保设备的正常运转和保护。
5.3 预防性维护:采取预防性维护措施,延长设备的使用寿命,减少故障和停机时间。
钣金折弯人员必备知识【集锦】

对于在工作中折弯工艺的学习,首先应该从基础知识先了解。
1、折弯模具的选择折弯模具按折弯工艺分为标准模具和特殊折弯模具。
在标准的折弯情况下(直角和非直角折弯)折弯时一般都是用标准模具,折弯一些特殊的结构件(如:段差折弯、压死边等)时采用特殊模具。
另外折弯不同厚度板料时,对折弯下模具的开口尺寸“V”形槽尺寸选择有所不同。
一般所选用“V”形槽开口尺寸为板材厚度的6-10倍(0.5~2.6mm为6t、3~8mm 为8t、9~10mm为10t、12mm以上为12t)。
当板材较薄时选择取向于小数,板材较厚时取向于大数。
如:折弯2mm板时可选用12mmV槽即可。
标准的折弯一般所弯的角度不小于90度,标准的折弯机模具上模和下模的尖角通常为88度。
在不标准的折弯情况下,可选择不同的上模具形状,可折弯板材不同的角度和形状。
若特殊的形状板金件,可要选择特殊的折弯模具成形折弯。
特殊模具折弯图2、模具的分段通常折弯机模具标准长度为835mm一段,原则上只可折弯大尺寸的工。
如果将模具分割为长短不同的小段,通过不同的模具长度自由组合,就可方便于不同长短的盒形工件或箱体等折弯。
在行业内对折弯模具的分段有一个标准的分割尺寸,如:标准分割835分段:100(左耳),10,15,20,40,50,200,300,100(右耳)=835mm。
当然也可按用户的要求分割。
折弯模具分段图3、折弯力的计算如果我们要折弯一件比较大以及板材比较厚的板材时,先要了解所需的折弯吨位力。
那么我们可以通过计算得出折弯所需的吨位(建议工件折弯的所需压力在设备额定吨位的80%以内),通过计算我们也可确定折弯所需的吨位设备,模具V槽合理的选择而对折弯力也有影响。
计算方法如下:计算公式:P=折弯力(KN)L=板料长度(M)T=材料抗拉力(软钢:45Kg/mm2) S=板材厚度(mm)V=下模宽度(mm)■例:以折弯2米长,3毫米厚的软钢板为例计算它的折弯力:T=材料抗拉力(软钢:45KN/mm2)P=1.42xLxTxs2/1000xV=1.42x2000x450x9/1000x24=11502000/24000=479.25KN=48吨在折弯的过程中,除了我们标准的折弯方法外,还会经常遇到一些特殊的折弯工艺要求。
折弯作业指导书

折弯作业指导书一、引言在金属加工领域,折弯是常用的一种工艺,用于将金属材料弯曲成所需形状。
本指导书旨在提供折弯作业的详细步骤和注意事项,以帮助操作人员正确而高效地完成折弯工作。
二、材料准备1. 工件材料:确保所选用的金属材料适合折弯工艺,并具备所需的弯曲性能。
2. 工具准备:准备好适当类型和规格的折弯模具和折弯设备。
3. 安全装备:佩戴所需的安全护具,如手套、护目镜和防护服等,以确保操作人员的安全。
三、折弯作业步骤1. 设定折弯参数:确定所需的折弯角度、弯曲半径和折弯顺序,并在折弯设备上进行相应的参数设置。
2. 工件定位:将工件放置在折弯设备上,根据需要进行定位,确保工件的稳定性和准确性。
3. 装夹工件:使用合适的装夹工具将工件固定在折弯设备上,确保工件与折弯模具之间的压力均匀分配。
4. 进行折弯操作:在严格遵守安全操作规程的前提下,根据设定的折弯参数,进行折弯操作。
可采用手动或机械化方式进行折弯。
5. 检验折弯效果:完成折弯后,使用测量工具(如卡尺或量规)检验折弯的角度和尺寸是否符合要求。
6. 调整修正:若折弯效果不符合要求,可根据需要调整折弯参数或重新进行折弯操作,直至达到所需的效果。
7. 完成折弯作业:当所有工件完成折弯操作且满足要求时,将其取下并进行必要的后续处理。
四、注意事项1. 安全第一:在进行折弯作业时,必须严格遵守相关的安全规定和操作要求,确保人员的安全。
2. 材料选择:根据工件的使用环境和要求,选择合适的金属材料,确保其具备足够的韧性和弯曲性能。
3. 折弯模具选择:根据工件的尺寸、形状和折弯要求,选择合适类型和规格的折弯模具,以确保折弯效果的准确性和一致性。
4. 技术培训:操作人员应接受相关折弯技术培训,了解折弯设备的操作原理和注意事项,熟悉不同材料的折弯特性。
5. 质量控制:定期检查折弯设备的运行状态和精度,保持设备的良好性能,确保折弯作业的质量和准确性。
6. 工件处理:除了折弯操作外,还需根据需要进行后续的处理,如焊接、打磨和喷涂等,以满足最终产品的要求。
折弯作业危险源辨识:模具选择、安装、操作、人员安排及材料选择等

折弯作业危险源辨识:模具选择、安装、操作、人员安排及材料选择等折弯危险源辨识在折弯作业过程中,存在许多潜在的危险源,如果不加注意或控制不当,可能会导致事故发生。
本文将就折弯作业中可能存在的危险源进行辨识,并分别进行简要分析。
1.模具选择不当在折弯作业中,模具选择不当可能会导致以下事故:●模具承载能力不足,导致弯曲件损坏或模具断裂。
●模具的形状、尺寸与弯曲件不匹配,造成成型不良或弯曲件损坏。
●模具材料不当,导致弯曲件表面划伤或模具过早磨损。
为避免类似事故发生,应选择与弯曲件相适应的模具,并确保模具的承载能力和材料符合要求。
1.模具安装不当模具安装不当可能导致以下危险:●模具安装不牢固,导致折弯过程中模具脱落或断裂。
●上下模具对中不良,导致弯曲件成型不良或损坏。
为避免事故发生,应按照规定的步骤正确安装模具,同时确保上下模具的对中性。
1.折弯角度过大折弯角度过大可能会导致以下事故:●弯曲件内侧材料拉伸过度,导致弯曲件变形或开裂。
●弯曲件外侧材料压缩过度,导致弯曲件外侧起皱或开裂。
为避免类似事故发生,应控制折弯角度在合适的范围内,并确保弯曲件的材料和厚度与折弯角度相适应。
1.操作失误操作人员在折弯过程中可能会出现以下问题:●操作不熟练或技能不足,导致弯曲件成型不良或损坏。
●未经过培训或安全教育不足,不了解操作规程和安全注意事项。
●粗心大意或疲劳作业,导致意外事故的发生。
为减少由于人为错误导致的事故,应加强对操作人员的培训和技能考核,确保他们熟悉操作规程和安全注意事项。
同时,应加强安全教育和宣传,提高操作人员的安全意识。
1.折弯速度过快折弯速度过快可能会导致以下问题:●材料去除速度过快,导致弯曲件表面粗糙或开裂。
●模具磨损加快,导致模具过早损坏。
●弯曲件成型不良,导致弯曲件质量下降。
为避免上述问题,应控制折弯速度在合适的范围内,并确保折弯机的转速与弯曲件的材料和厚度相适应。
1.人员安排不当2.多人操作时如若人员安排不当可能会发生推搡事故;或者工作疏忽可能会导致工件砸伤操作员工的情况;应该合理安排人员的工作,实行定人定机制度。
折弯基本知识
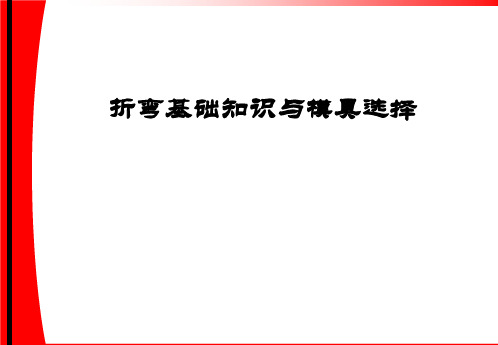
V 折弯压力与
① 折弯线长度(L)正比关系 ② 材料的拉伸强度(σb)正比关系 ③ 板厚(t)平方关系 ④ 下模V宽反比关系。
C(补偿系数)的值为1.5,σb为45
P=68 × 板厚 × 板厚 ÷V 槽宽度
简化后为1m的折弯吨数公式:
*
模具一定有耐压值。模具形状决定耐压大小。 一定要确认耐压必须大于折弯所需吨数。
加力状态 Θ
消除力的状态 Θ’
Θ’
Δ Θ/2
★材质不同回弹量不同 ★板厚不同回弹量不同 ★要求折弯角度不同回弹量不同 因此 ● SPCC<SUS ●板厚越薄回弹量越大
回弹的原因
1 由于折弯是一种塑性变形加工,当压力消除后,材料将发生一定的弹性回弹. 2 折弯的内应力的回弹
与一般的R折弯模具相比有以下优点:①无滑动折弯痕迹②不会有多段折曲现象发生,可以获得较好的圆弧面。③折弯回弹量小。 缺点是折弯压力大。
成本比较
低价
高价
高价
中价
中价
*
26
18
120
100
100
39
100
280mm
420
使用模具
深箱形状折弯中间板规格(注意机器开口高度)
长度有限制
*
取出
取不出
单纯的箱体形状
下模耐压刻印
上模耐压刻印
刻印必须表示每米的吨数。 请注意折弯吨数会随产品的长度变化。
例 产品长度200mm,使用的模具刻印1000kN/m,只需施加 1000kN/m×0.2=200kN/m(20ton)。
耐压40ton/m
折弯压力与模具耐压
回弹的定义
所谓回弹就是在消除折弯力后,折弯角度的返回。
电气控制柜设计制作-机柜制作-折弯设备-折弯模具的选择

折弯模具的选择1)折弯模具的类型折弯模具有L型、R型、U型、Z型等折弯类型。
上模主要有90°、88°、45°、30°、20°、15°等不同角度。
下模有4~18V不同槽宽的双槽和单槽,有R下模、锐角下模、压平模等。
上下模分为分段和整体。
上模分段一般为:300mm、200mm、100mm、50mm、40mm、20mm、15mm、10mm,整体为835mm。
下模分段一般分为:400mm、200mm、100mm、50mm、40mm、20mm、15mm、10mm,整体为835mm。
2)绝对不能超过模具所标注的压力折弯模具采用优质钢材,经特殊热处理制作而成,具有硬度高、不易磨损、承受压力大等特点,但每套模具都有它承受的极限压力,所以在使用模具时要正确选用模具的长度,即考虑每米要加多少压力,绝对不能超过模具所标注的压力。
模具标识的耐压是单位长度上的负荷。
模具能够承受的最大负荷=模具上标识的耐压×加压部分的长度。
超过模具耐压最大负荷的话,模具破裂飞散的可能性非常大,是极其危险的违规使用。
如果上模与下模耐压的标识不同,那么应该以耐压低的一方作为标准,来计算模具的最大耐压负荷。
举例如下:模具上的耐压标识为MAXTONS 50/METER时:加压部分的长度是0.835m的情况下,模具可以使用的最大负荷是50t/m×0.835m=41.75t;加压部分的长度是0.415m的情况下,模具可以使用的最大负荷是50t/m×0.415m=20.75t。
3)根据工件的材质硬度、厚度、长度来选用上、下模在使用模具时,要根据金属板料的材质硬度、厚度、长度来选用上、下模,一般按照56T的标准使用下模,长度要比板料长一些。
材质越硬、厚度越大的料,应用槽较宽的下模。
4)有角度要求时在作为锐角或压死角时,应选用30°模具,先折锐角,后压死边。
dp980折弯标准

DP980折弯标准1. 材料选择DP980是一种高强度、高硬度、高耐腐蚀性的不锈钢材料,适用于各种机械零件的制造。
在选择材料时,应优先考虑使用DP980,以确保零件的强度和耐腐蚀性。
2. 板材厚度DP980板材的厚度应符合折弯加工的要求。
一般来说,板材厚度应在0.5mm以上,以确保折弯过程中不会出现破裂或变形。
3. 折弯半径折弯半径是指板材在折弯过程中弯曲部分的半径。
DP980的折弯半径应不小于板材厚度的1.5倍,且最小折弯半径不应小于2mm。
4. 折弯角度折弯角度是指板材在折弯过程中形成的角度。
DP980的折弯角度应控制在90°至180°之间,以保证零件的稳定性和强度。
5. 模具选择在折弯过程中,模具的选择对零件的质量和精度有很大影响。
应根据DP980的材料特性选择合适的模具,以保证折弯过程的顺利进行。
6. 折弯压力折弯压力是指在折弯过程中施加在板材上的压力。
DP980的折弯压力应根据板材厚度、折弯半径和折弯角度等因素来确定。
适当的折弯压力可以保证零件的形状和质量。
7. 表面质量DP980的表面质量应达到一定的标准,以确保零件的使用性能。
在折弯过程中,应注意防止划痕、压痕等表面缺陷的产生。
8. 尺寸精度DP980的尺寸精度对零件的使用性能有很大影响。
在折弯过程中,应控制好各部分的尺寸精度,以保证零件的稳定性和强度。
9. 折弯顺序在折弯过程中,应按照一定的顺序进行折弯操作,以避免零件变形或产生裂纹。
一般来说,应先进行小角度的折弯操作,再逐渐进行大角度的折弯操作。
10. 质量控制在折弯过程中,应进行严格的质量控制,以确保零件的质量和精度符合要求。
质量控制包括对各工序的操作进行检查、对零件的质量进行检测等。
如发现质量问题,应及时采取措施进行处理。