顶出机构及其基本形式
二次顶出机构(图文教程,经典案例)
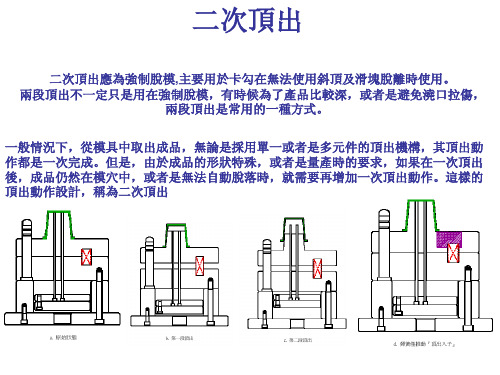
延时頂出
但是由于成品的形狀特殊或者是量產時的要求如果在一次頂出後成品仍然在模穴中或者是無法自動脫落時就需要再增加一次頂出動作
二次頂出
二次頂出應為強制脫模,主要用於卡勾在無法使用斜頂及滑塊脫離時使用。 兩段頂出不一定只是用在強制脫模,有時候為了產品比較深,或者是避免澆口拉傷, 兩段頂出是常用的一種方式。 一般情況下,從模具中取出成品,無論是採用單一或者是多元件的頂出機構,其頂出動 作都是一次完成。但是,由於成品的形狀特殊,或者是量產時的要求,如果在一次頂出 後,成品仍然在模穴中,或者是無法自動脫落時,就需要再增加一次頂出動作。這樣的 頂出動作設計,稱為二次頂出
頂出時,左側的頂針會 先動作,直到下固定板頂 到右側頂針下方以紅色線 條圈起來的頂針頭時,右 側的頂針才會開始動作。 這樣的二次頂出結構, 可以避免潛伏式澆口在頂 出時,澆口拉離成品時將 成品拉傷。 側澆口也可以利用類似 的方式頂出,避免在澆口 位置拉傷成品。
當然,這種頂出方式不僅是 用在澆口附近的頂出。由於 其第二段頂出行程的起使位 置僅需要更改頂針下方的柱 狀長度就可以達成,而且在 模具製作上的費用又較為低 廉,這種頂出方式,也很適 合之前所提到的較深的盒狀 物的頂出。
二次頂出
或者为获得可靠的脱模效果,分解胶件脱模阻力,经二次脱模动作,来。
胶件凹凸位被型芯包紧
第一次脱模出内芯,为胶件提供变形空间
第二次脱模,胶件凹凸位变形后强脱出模
图8.5.1
二次頂出
顶针
二次脱模机构示例: (1)胶件如图8.5.2 所示,两骨间有半圆凹 陷,被后模 型腔包紧。脱模机构如图8.5.3 所示,第一 次脱模使胶件脱 出后模型腔,为强脱变形提供空间;第二 次脱模,由顶针脱 模,胶件半圆凹陷位强脱出型芯推块。该 机构运动过程:第 一次脱模四块顶针板都运动,带着顶针、 型芯推块同时运动, 脱模距离/ h,使胶件脱出后模型腔,一次 脱模完成。当继续 运动至摆块碰上限位面后,摆块摆动使上 面两块针板快速运动, 带动顶针脱出胶件,完成二次脱模。此机 构须注意: h1 > h, H > 10mm1 h11 (二次脱模运动距离)。
模具行位和斜顶的设计经验要点
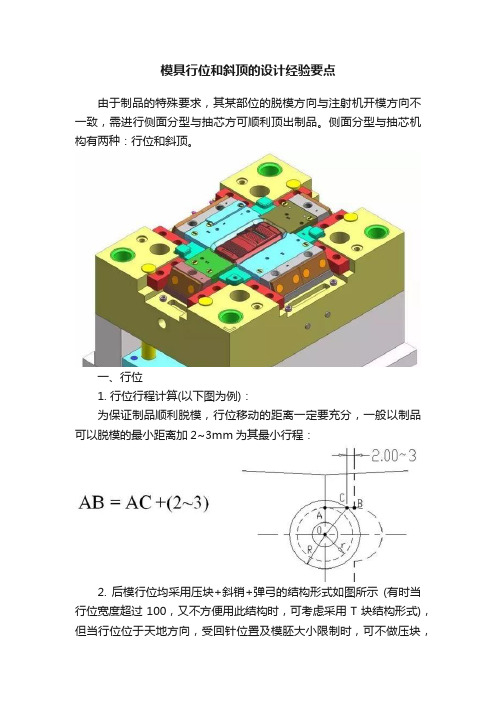
模具行位和斜顶的设计经验要点由于制品的特殊要求,其某部位的脱模方向与注射机开模方向不一致,需进行侧面分型与抽芯方可顺利顶出制品。
侧面分型与抽芯机构有两种:行位和斜顶。
一、行位1. 行位行程计算(以下图为例):为保证制品顺利脱模,行位移动的距离一定要充分,一般以制品可以脱模的最小距离加2~3mm为其最小行程:2. 后模行位均采用压块+斜销+弹弓的结构形式如图所示(有时当行位宽度超过100,又不方便用此结构时,可考虑采用T块结构形式),但当行位位于天地方向,受回针位置及模胚大小限制时,可不做压块,由模板原身出。
3. 行位底面、顶面与前后模底、顶面的关系,见图:4. 不论行位侧面是否有封胶,其两侧均要做斜度,一般值为单边3~5°,但当两个运动方向垂直的行位贴合时,角度为45°。
若产品四面均有行位互相贴合,设计时应考虑将其中一个行位伸出一耳朵,以保证准确定位。
5. 行位高度与厚度的比值最大为1,否则行位运动时会受翻转力矩影响,造成运动失效,一般要求L≧1.5H。
6. 行位斜销角度一般为15°~25°,最大不能超过25°,斜销角度比行位小2°,一般尽量不采用细小的斜销,以保证行位运动的顺利。
7. 斜销孔比斜销单边大1/64",约0.4,当斜销穿过行位时,需在模板上为其留出足够的让位空间。
8. 斜销在行位中位置的确定:斜销尽量置于行位的中间位置,具体尺寸要求如图:9. 铲鸡与行位的配合面要求超过行位高度的2/3,并且用于铲鸡的螺丝应尽量大,下图为两种不同结构的铲鸡,尽量避免采用图b的结构。
10. 行位弹弓长度的确定,应保证弹弓空间足够,防止弹弓失效。
设定行位行程为M,弹弓总长为L,设弹簧压缩40%,行位完全退出后,弹弓仍预压10%,则有:(40%-10%)L=ML=(10/3)M弹弓空间为0.6L但当L过小时,为了防止弹弓失效,往往要加大弹弓长度。
模具系列7-模具顶出系统

一.使产品冷却固化后从模具上脱落的机构称为顶出系统,顶出系统要求安全可靠闭合时不能与其它机构发生干涉。
二.我们最常用的是机械顶出,其运用啤机机械力控制模具的闭合及顶出,另外还有气动顶出,液压顶出。
三.常用机械顶出类型A,圆顶针(推杆)<1>加工简便价格相对低廉,用得最广最多。
<2>分有托(双托)及无托(单托)我们厂通常直径2MM以下用有托(见图1)B,扁顶<1>加工比较复杂,要做镶件或者线割。
<2>主要用在深骨位置,透明产品上有骨位的地方,手机类骨状结构(见图2)<3>自制大扁顶(直顶),用在大面积深骨位置和透明类产品整个外形的顶出(见图3)C,司筒(推管)<1>价格相对比较高,主要用于空心柱子的顶出。
<2> A尺寸(司筒管壁厚)尽量取大否则易损坏, A≥0.8MM(见图4)<3>15MM以上的空心柱或者15MM以下但旁边不能下顶针的空心柱用司筒,透明类产品上有空心柱用司筒,细长圆形制品用司筒.<4>分有托及无托.<5>不能和顶棍孔干涉.<6>司筒针固定方式:我们厂规定用压板.没办法时可用基米镙丝.(见图4).D,推方(推块)<1>方式:a原身b镶件+顶针.<2>一般用在比较高并且其中间有大孔又不适合做推板的制品或制品后模边缘是大斜面或大弧面下顶针效果不好时,还有就是大面积深骨位置(和直顶相似)(见图5).E,推板<1>推呵(推后模料)深度较高或者产品内侧不能下顶针时(见图6)<2>推板和推呵相同,用有推板的模架.(桶状深长制品)四.注意事项A复位装置: 黄弹弓+回针B管位(定位),圆顶针或司筒上面不是平面的为了防转动而做定位装置,形式主要有两种(见图7)一种穿针,另一种把顶针头磨一角成”D”字形.我们厂要求所有顶针做”D”字头.(见图7b).C顶针处在大弧面或角度大的斜面上时要做”十”字防滑槽或晒格子纹(图8).D顶针等必须把产品顶离模具5~15MM,某些特别深的产品由于顶出行程的限制可以不用全部顶离模具,但其上面的骨位,柱位尽量顶离模具然后人工取出.E骨位,柱位及对内模有包紧力的地方(产品边缘等)是顶针布置集中区域F不能与其它机构干涉:离镶件,镶针边要有1~3MM;离运水要≥4MM;离镙丝牙≥2MM; 不能与推方相撞.G行位下面有顶针必须做先复位机构或做咭制.H有做”Z”形拉料的顶针其Z方向必须一致,方便取出(图9)I产品薄壁处不能下顶针(易顶高顶白)J注意某些禁设顶针区域(镜面要求,装配紧密,要滑动区等)K在产品有相互配合的地方下顶针,顶针要高出模面0.3~0.5MM.L原则上每套模具都要做顶针板限位块(一来防止弹弓过分压缩,二来防有托顶针避空不足撞断顶针)(见图10)五.顶针的一些下法A透明类常用垃圾水口顶出,它上面有筋骨考虑扁顶;上面有实心柱考虑圆顶;上面有空心柱考虑司筒;或者考虑整个外形的顶出.B主流道分流道处下圆顶C每一个或每一组潜水必须要有1支以上的水口针.D深实心柱子,下在其下面(图9b)短实心柱下在其旁边(图9C)E镶件,镶针旁边(图9def).F前模镶针碰后模顶针(图9gh)G骨位交叉位置(CASIO面,学习机面等(见图11).H围骨旁边(见图12).I深骨位旁边(见图13).J产品边缘.六.下顶针步骤A原则:圆顶优先,选大去小(面积足够)规格要少,分布平行—做到快速顶出,不顶白不顶高,顶针不倾斜不易断.B下法:,<1>对柱子先确认镶件还是司筒,镶针旁边要下顶针<2>深骨位置或凸凹台旁边下顶针或推方.<3>产品边缘下顶针.<4>对于对称产品可先下一边再镜像.<5>调整顶针位置达到均衡美观.。
塑料模具顶出系统设计
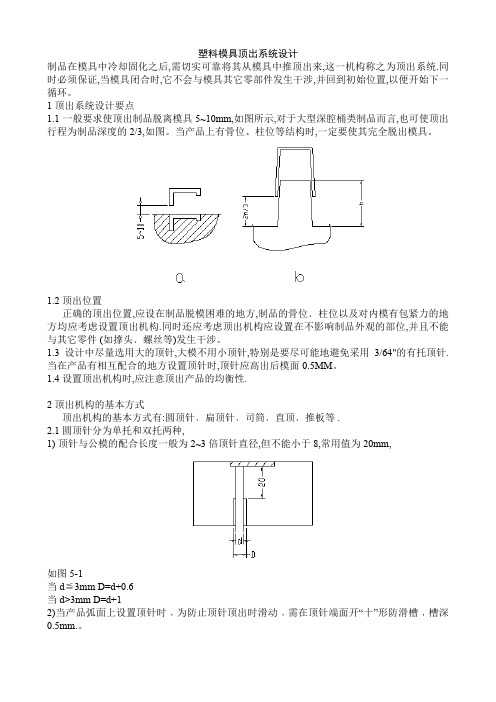
塑料模具顶出系统设计制品在模具中冷却固化之后,需切实可靠将其从模具中推顶出来,这一机构称之为顶出系统.同时必须保证,当模具闭合时,它不会与模具其它零部件发生干涉,并回到初始位置,以便开始下一循环。
1 顶出系统设计要点1.1一般要求使顶出制品脱离模具5~10mm,如图所示,对于大型深腔桶类制品而言,也可使顶出行程为制品深度的2/3,如图。
当产品上有骨位、柱位等结构时,一定要使其完全脱出模具。
1.2 顶出位置正确的顶出位置,应设在制品脱模困难的地方,制品的骨位﹑柱位以及对内模有包紧力的地方均应考虑设置顶出机构.同时还应考虑顶出机构应设置在不影响制品外观的部位,并且不能与其它零件 (如撑头﹑螺丝等)发生干涉。
1.3设计中尽量选用大的顶针,大模不用小顶针,特别是要尽可能地避免采用3/64"的有托顶针.当在产品有相互配合的地方设置顶针时,顶针应高出后模面0.5MM。
1.4设置顶出机构时,应注意顶出产品的均衡性.2 顶出机构的基本方式顶出机构的基本方式有:圆顶针﹑扁顶针﹑司筒﹑直顶﹑推板等 .2.1圆顶针分为单托和双托两种,1) 顶针与公模的配合长度一般为2~3倍顶针直径,但不能小于8,常用值为20mm,如图5-1当d≦3mm D=d+0.6当d>3mm D=d+12)当产品弧面上设置顶针时﹐为防止顶针顶出时滑动﹐需在顶针端面开“十”形防滑槽﹐槽深0.5mm.。
3)顶针与周边零件的位置关系。
顶针边与骨位﹑镶件的最小距离为2.0mm,与产品边﹑水道最小距离为3.0mm。
.4)当产品中柱位孔为前模碰穿方式,其下放置顶针时,处理方式如图:5)顶针的管位.当顶针位于圆弧面或者当顶针和司筒受胶位方向限制时,往往要设置管位装置,管位方式有下列三种:见图,其中图a为设置管位钉,较常用;图b为加一管位块;图c为将顶针头部加工为直边,此方式较常用于大顶针的场合。
6)镜类产品不允许产品上有顶出痕迹,常采用垃圾钉顶出,产品有扣时,顶针边距产品边2mm,无扣时为3mm,如图:7)有时,将顶针顶端加工成”z”形头,达到制品留后模的目的,此时应保证,使”z”形头方向一致。
注塑模具结构及设计-5(导向_定位_顶出_复位)
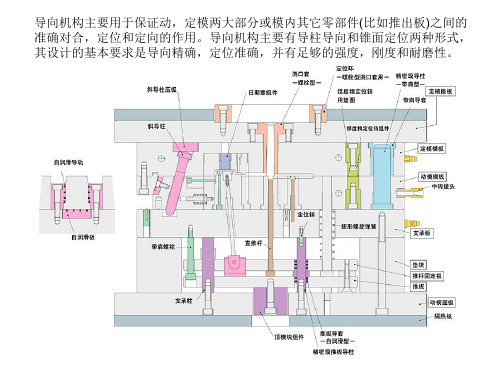
3,导柱的端部通常设计成锥形或半球形,以便导柱顺利进入导向孔。
导柱的端部分别为锥形,半球形,R角,斜角
4,导柱与导向孔通常采用间隙配合,导柱与安装孔通常采用过渡配合。
5,导柱的固定形式 普通导柱的固定形式:
推板导柱的两端都要固定,这样才能 更好的起导向作用。
挂台固定 (通孔)
螺钉固定(盲孔) 导柱配合面研伤更换 时可避免损坏固定孔
定位: 1,在模架上通常增加一些精定位来帮助动, 定模之间更准确的定位。这些精定位的位置 选择要注意关于中心对称,以使受力平衡。 定模 动模
右边为常用的几种 精定位形式(圆锥 面定位型,侧面安 装无锥度型,嵌入 安装锥面定位型)
2,在动,定模芯之间,为了达到更好的定位效果,防止动,定模芯之 间错位,需要增设定位。 动模定位 定模定位
定位到型腔边的距离不 等可能定位效果不理想
4,侧向受力不均匀的 塑件对模具往往有较 大的侧向力,该压力 可能引起型芯和型腔 的偏移,如果传递到 导柱上,将使导柱发 生卡住或损坏的现象, 需要采用定位的形式。
5,有些分型面坡 度过大,合模时受 力不平衡,为了抵 消这些不平衡力, 防止动,定模之间 错位,要设置定位。
动,定模合在一起
定位需带有斜度,合上之后没有间隙
动定模错位导致壁厚不均匀 3,对于成型大型深腔, 高精度或薄壁制品的模具, 型腔可能因为受到大的侧 向压力而向外变形,为消 除动定模之间的断差确保 壁厚均匀需要设置定位。
定 模 涨 开 导 致 动 定 模 之 间 断 差
大型腔或要求壁厚均匀的薄壁塑件的分型面上设置的 定位要随着型腔的外形走
推管顶出后
推管与推管芯的通常固定形式:
3,推块
推块可以有效的增加顶出面积
塑胶模具结构详解

塑胶模具结构详解塑胶模具是塑胶制品生产中必不可缺的工具,主要用于将熔融状态的塑胶物料注入模具中,通过冷却固化后得到所需要的塑胶制品。
塑胶模具的结构设计直接影响着塑胶制品的成型质量和生产效率,因此塑胶模具的结构设计非常重要。
下面我将详细介绍塑胶模具的结构。
首先,塑胶模具的结构主要包含以下几个部分:模具座、模腔、模芯、导向机构和顶出机构。
1.模具座:模具座是塑胶模具的支撑结构,通常采用钢板焊接而成。
模具座上装有模腔和模芯,通过模具座上的定位孔与注塑机上的模板定位销相连接,保证模具的准确定位。
2.模腔:模腔是塑胶模具中用于成型的腔体部分,它的形状和尺寸与最终产品的形状和尺寸一致。
模腔一般由高硬度、高耐磨的钢制成,以保证模具的耐用性。
模腔表面经过抛光和处理,以保证成型产品的光洁度。
3.模芯:模芯是模腔的补充部分。
在注塑过程中,塑胶材料被注入到模腔中,模芯起到的作用是使模腔中的塑胶材料在注射后能够顺利排出,并保证成型产品的尺寸和形状的准确性。
模芯一般用低硬度、低摩擦系数的钢制成,以减少与模腔的磨损。
4.导向机构:导向机构用于保证模腔和模芯的准确定位,以防止注塑过程中的偏移和动作不平衡。
通常采用导柱和导套的组合形式,导柱固定在模具座上,导套安装在模腔和模芯上,实现模腔和模芯的相对运动。
5.顶出机构:顶出机构用于将成型后的产品从模具中弹出,通常采用弹簧和顶出杆的组合形式。
顶出机构应设计合理,力度适中,以保证成型产品的完整和表面的光洁度。
除了上述主要部分之外,塑胶模具还可以根据具体的产品要求加上一些辅助结构,如冷却系统、进胶口和排气口等。
冷却系统用于将模具中的热量迅速带走,以保证模具的温度恒定,提高生产效率;进胶口用于塑胶材料的注入,排气口用于排除模腔内的气体。
总之,塑胶模具是实现塑胶制品生产的关键工具,其结构设计需要综合考虑成型质量、生产效率和模具耐用性等方面的因素。
上述介绍的塑胶模具结构是基础的结构设计,具体的模具结构设计还需要根据不同产品的具体要求进行调整和优化。
4.7脱模机构解析
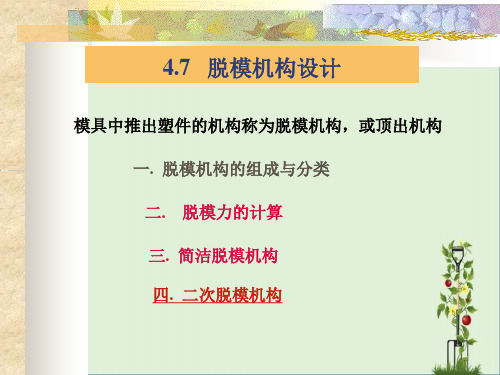
模具中推出塑件的机构称为脱模机构,或顶出机构 一. 脱模机构的组成与分类 二. 脱模力的计算 三. 简洁脱模机构 四. 二次脱模机构
一. 脱模机构的组成与分类
组成
脱模机构一般由三局部组成:推出部件,导向部件,复位部件 推出部件:推杆、拉料杆、推杆固定板,推板等
导向部件:导柱、导套 复位部件:复位杆
3〕直径和数量
保证足够的刚度。可设计成阶梯形
数量应保证顺当脱模且不损伤塑件表观
4〕推杆材料及热处理要求
材料常用T8A,T10A或65Mn,碳素工具钢热处理要求硬度HRC50~54,
弹簧钢热处理硬度要求HRC50~54。
5〕推杆固定形式
推杆
推杆
推杆
推杆
推杆
推杆
(a)
(b)
(c)
(d)
(e)
(f)
图4-79 推杆的固定形式
3〕气动脱模: 利用压缩空气将塑件吹出。
2、按模具构造分
一次推出脱模〔简洁脱模〕、二次推出脱模、动定模双向推出脱模、 挨次脱模、带螺纹塑件脱模塑件不变形损坏 机构推出中心与脱模力中心相重合,推出力分布均匀,
作用点尽可能靠近型芯防止塑件脱模后变形;推出力施于 塑件刚性和强度最大的地方〔如凸缘、加强筋等〕。
留有0.2~025mm的间隙 锥面 协作
推件板常用材料为45钢,热处理要求28~32HRC
四. 二次脱模机构
作用:由于塑件的特殊外形或生产自动化的需要;为避 开一次脱模塑件受力过大。
单推板
摆块拉板式二级脱模机构
双推板
三角滑块式双推板二次脱模机构
螺纹的脱模
强制脱出:弹性较好或较松软的塑件,用于精 度不高和小批量生产的塑件 模外脱出:活动螺纹镶块
注塑模具设计:第三章:顶出系统
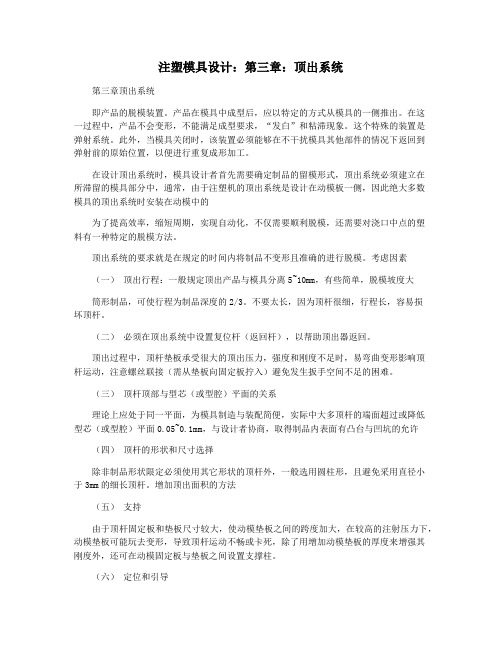
注塑模具设计:第三章:顶出系统第三章顶出系统即产品的脱模装置。
产品在模具中成型后,应以特定的方式从模具的一侧推出。
在这一过程中,产品不会变形,不能满足成型要求,“发白”和粘滞现象。
这个特殊的装置是弹射系统。
此外,当模具关闭时,该装置必须能够在不干扰模具其他部件的情况下返回到弹射前的原始位置,以便进行重复成形加工。
在设计顶出系统时,模具设计者首先需要确定制品的留模形式,顶出系统必须建立在所滞留的模具部分中,通常,由于注塑机的顶出系统是设计在动模板一侧,因此绝大多数模具的顶出系统时安装在动模中的为了提高效率,缩短周期,实现自动化,不仅需要顺利脱模,还需要对浇口中点的塑料有一种特定的脱模方法。
顶出系统的要求就是在规定的时间内将制品不变形且准确的进行脱模。
考虑因素(一)顶出行程:一般规定顶出产品与模具分离5~10mm,有些简单,脱模坡度大筒形制品,可使行程为制品深度的2/3。
不要太长,因为顶杆很细,行程长,容易损坏顶杆。
(二)必须在顶出系统中设置复位杆(返回杆),以帮助顶出器返回。
顶出过程中,顶杆垫板承受很大的顶出压力,强度和刚度不足时,易弯曲变形影响顶杆运动,注意螺丝联接(需从垫板向固定板拧入)避免发生扳手空间不足的困难。
(三)顶杆顶部与型芯(或型腔)平面的关系理论上应处于同一平面,为模具制造与装配简便,实际中大多顶杆的端面超过或降低型芯(或型腔)平面0.05~0.1mm,与设计者协商,取得制品内表面有凸台与凹坑的允许(四)顶杆的形状和尺寸选择除非制品形状限定必须使用其它形状的顶杆外,一般选用圆柱形,且避免采用直径小于3mm的细长顶杆。
增加顶出面积的方法(五)支持由于顶杆固定板和垫板尺寸较大,使动模垫板之间的跨度加大,在较高的注射压力下,动模垫板可能玩去变形,导致顶杆运动不畅或卡死,除了用增加动模垫板的厚度来增强其刚度外,还可在动模固定板与垫板之间设置支撑柱。
(六)定位和引导在制品产量大,或顶出行程长,同时使用较细的顶杆,以及使用顶管顶出并在动模固定板装有细长芯子时,为保护顶杆(或长芯子)使其运动平稳,顶出系统需要设置导向装置,并且在动模板与垫条以及动模固定板之间装有定位销钉,以保证位置精度(七)弹射位置制品凡是有塑料包围钢件的地方,脱模都会困难,这是因为塑料熔体冷却后的收缩应力而产生对钢件的“抱紧”现象所导致的,故这些地方(筋、柱)都应重点考虑喷射器的分类一、圆顶杆,易加工,最普通,最简单的标准件,顶杆需淬火处理,获得足够的轻度和耐磨性。
模具设计二次顶出机构
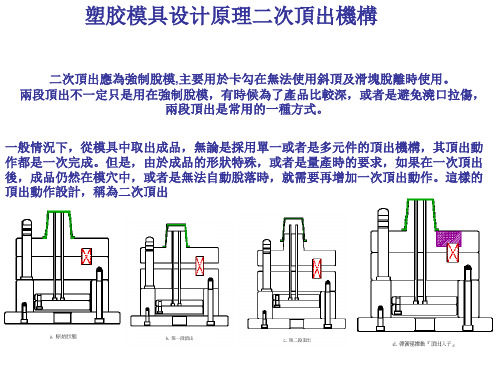
二次頂出
或者为获得可靠的脱模效果,分解胶件脱模阻力,经二次脱模动作,来完成胶件出模的 机构称二次脱模机构 如图8.5.1所示。
胶件凹凸位被型芯包紧
第一次脱模出内芯,为胶件提供变形空间
第二次脱模,胶件凹凸位变形后强脱出模
图8.5.1
二次頂出
顶针
二次脱模机构示例: (1)胶件如图8.5.2 所示,两骨间有半圆凹 陷,被后模 型腔包紧。脱模机构如图8.5.3 所示,第一 次脱模使胶件脱 出后模型腔,为强脱变形提供空间;第二 次脱模,由顶针脱 模,胶件半圆凹陷位强脱出型芯推块。该 机构运动过程:第 一次脱模四块顶针板都运动,带着顶针、 型芯推块同时运动, 脱模距离h,使胶件脱出后模型腔,一次脱 模完成。当继续 运动至摆块碰上限位面后,摆块摆动使上 面两块针板快速运动, 带动顶针脱出胶件,完成二次脱模。此机 构须注意: h1 > h, H > 10mmh1(二次脱模运动距离)。
二次頂出
拉料杆
拉料杆 斜顶行 位块 顶针
潜浇道放 大图
二次頂出
延时頂出
延时頂出是解决产品与浇口 不能自动断开的问题 (浇口形式。搭接式或侧浇口) 延时顶出只顶在流道上
延时頂出,可以 利用頂針的變化來 完成。
延时頂出
至於頂針採用兩截式頂 針,只是在於增加頂針的 強度,避免頂出時發生撓 曲變形。 採用這種頂針來完成兩 段式頂出,在模具結構上 是最簡單的,只要在頂針 板上動手腳就行了。 此處舉的例子,是利用 這種機構,來進行潛伏式 澆口的切斷。
塑胶模具设计原理二次頂出機構
二次頂出應為強制脫模,主要用於卡勾在無法使用斜頂及滑塊脫離時使用。 兩段頂出不一定只是用在強制脫模,有時候為了產品比較深,或者是避免澆口拉傷, 兩段頂出是常用的一種方式。
顶出机构及其基本形式

顶出机构及其基本形式顶出机构的设计原则1.顶出机构应设置在动模一侧;因塑件一般均留在动模一侧以便顶出。
2.顶出时与塑件的接触面应为塑件内表面及其他不显眼的位置,以保证塑件外观。
3.顶出装置均匀分布,顶出力作用在塑件承受力最大的部位。
以防变形和损伤。
4.顶出机构应平稳顺畅,灵活可靠,足够的强度、耐磨性,平稳顺畅无卡滞,并且制造方便,易于维修。
顶杆的结构形式和固定形式①顶杆的结构形式,如图6-5所示②顶杆的固定方式,如图6-6所示。
顶杆的组装精度,如图6-7所示。
ⅰ)配合长度L:当d<6㎜时, L=2d;当d =6~10㎜时,L<1.5d。
ⅱ)配合精度:理论上,单边间隙不大于塑料的允许溢边值即可。
实际上要求总间隙不大于塑料的允许溢边值。
因各种塑料的溢边值不同,故顶杆和顶杆孔的配合精度为一范围H8/f8~H9/f9(流动性好→小;流动性差→大)ⅲ)顶杆和顶杆孔的配合间隙在注射时起排气作用,间隙大则排气功能好。
故选择间隙时需兼顾排气和溢料两方面。
顶杆顶出机构的设计要点:a. 设在脱模阻力较大部位:成型件侧壁、边缘、拐角等处。
如图6-8所示(形芯强度,为修复、扩孔留余地)b. 设在塑件承受力较大的部位:较厚处、立壁、加强筋、凸缘上。
以防顶出变形。
c. 位置布局合理,顶出受力平衡以避免塑件变形。
d. 在确保顶出的前提下,数量尽量少以简化模具结构,减少顶出对塑件表面影响。
e. 对有装配要求的塑件,顶杆端面应高出形芯h=0.1~0.5㎜,以免影响塑件装配,但不能太高。
f. 顶杆应尽量短以保证顶出时的刚度、强度。
g. 不易过细,Φ<3㎜时,应采用阶梯形提高刚度。
h. 必须在塑件斜面设置顶杆时,为防止顶出过程中滑动,再顶杆部斜面上开横槽。
图6-8 d)i. 当薄、平塑件上不允许有顶出痕迹时,将顶杆设在浇口附近。
图6-8 e)j. 在带侧抽机构的模具中,顶杆位置尽量避免与活动型芯发生运动干扰。
图6-8 f)k. 避开冷却水路l.材料:T8A、T10A,头部淬硬HRC50~55。
塑料模具6大系统

试模和量产的成败以及成本的高低,80%決定于设计阶段。
我们的目标应当是让设计部门担负起试模和量产成败的责任,设计工程师要清楚的知道自己设计的产品和模具是如何历经酸甜苦辣之途,才完成任务的,这样设计水平才能不断精进。
设计工程师也应在最短的时间內将最新的更正设计反映在设计图面和文档上,这样知识和经验才能累积、分享和传承。
加工、钳工和品管的责任是按图施工和品管,並且反馈设计合理化的意见。
这样经年累月下來,竞争力不断增强的模具/注塑厂將脱颖而出。
模具结构----六大系统之一:模具成型零件(排位与订料)概述:模具成型零件----由上下内模(包括行位/镶件)组成,它们形成一个封闭的型腔。
通俗来说,凡是有产品胶位的地方都称为模具成型零件。
排位与订料:1:产品在模仁(内模)的排位以最佳效果形成排放位置,要充分考虑进胶的平衡性,流道尽短地流入型腔,要充分考虑进胶位置和分型面因素,要与制品的外形大小,深度成比例。
2:产品到模仁边的距离与产品之间的距离:小件制品距离一般为15-25MM之间,成品之间一般为15-20MM,如有镶呵则一般为25MM 左右,成品间有主流道的最少要有15MM,大件制品距离边一般为30-50MM,有镶呵最小为35,镶呵出多件产品,刚其之间距离为10-15MM左右,成品长度在200MM以上,宽度在150MM 以上其产品距离应不小于30MM;3:模仁到模胚边距离:300MM以内,模胚为50-60MM之间;330-350MM以内,模胚为60-70MM之间;550MM 以上,模胚一般要在75MM以上。
4:模仁底部到模胚底部距离;公模300MM以内,模胚为40-50MM之间;330以上,模胚为50-70MM之间;母模300MM 以内,模胚为25-30MM之间;330MM以上模胚为25-35MM。
5:模仁用料,母模一般模具国产NAK80,较高要求,则用进口NAK80,有特殊或批量大模具选用热处理材料,有腐蚀性胶料如PVC,POM,NL或透明PMMA,PC等则选择不锈钢系列,如2316,S136,S136H等,公模仁一般选用德国P20,有腐蚀性胶料如PVC,POM,NL或透明PMMA,PC等亦要选择不锈钢系列,斜顶一般选用进口718,法兰一般选用王牌,散热要求高的镶件用铍铜。
模具行位系统

模具行位系统由于制品的特殊要求﹐其某部位的脱模方向与注射机开模方向不一致﹐需进行侧面分型与抽芯方可顺利顶出制品。
侧面分型与抽芯机构有两种:行位和斜顶。
1.行位1.1行位行程计算(以两辨合模为例):为保证制品顺利脱模,行位移动的距离一定要充分,一般以制品可以脱模的最小距离加2~3mm为其最小行程:AB = AC+(2~3)1.2.后模行位均采用压块+斜销+弹弓的结构形式如图所示(有时当行位宽度超过100,又不方便用此结构时,可考虑采用T块结构形式),但当行位位于天地方向,受回针位置及模胚大小限制时,可不做压块,由模板原身出。
其压块采用公司自制标准件,规格参照附表3-1.2,并且压块均需加定位销定位。
1.3.行位底面﹑顶面与前后模底﹑顶面的关系,见图:a .b≧15mma .b=01.4.不论行位侧面是否有封胶﹐其两侧均要做斜度,一般值为单边3~5o,但当两个运动方向垂直的行位贴合时,角度为.45o。
若产品四面均有行位互相贴合,设计时应考虑将其中一个行位伸出一耳朵,以保证准确定位。
1.5.行位高度与厚度的比值最大为1,否则,行位运动时会受翻转力矩影响,造成运动失效。
一般要求L≧1.5H。
1.6.行位斜销角度一般为15o~25o,最大不能超过25o,斜销角度比行位小2o,一般尽量不采用细小的斜销,以保证行位运动的顺利。
1.7.斜销孔比斜销单边大1/64",约0.4,当斜销穿过行位时,需在模板上为其留出足够的让位空间。
1.8.斜销在行位中位置的确定﹕斜销尽量置于行位的中间位置,具体尺寸要求如图:1.9.铲鸡与行位的配合面要求超过行位高度的2/3,并且用于铲鸡的螺丝应尽量大,下图为两种不同结构的铲鸡,尽量避免采用图b的结构。
1.10.行位弹弓长度的确定,应保证弹弓空间足够,防止弹弓失效。
设定行位行程为M,弹弓总长为L,设弹簧压缩40%,行位完全退出后,弹弓仍预压10%,则有(40%﹣10%)L=ML=(10/3)M弹弓空间为0.6L.但当L过小时,为了防止弹弓失效,往往要加大弹弓长度。
模具顶出方式的种类

顶出装置•成形品之顶出•有螺纹之成形品取出方法•点状浇口之主注到道一流道之顶出•两段顶出•顶出板超前退回机构为使射出成形能率及成形品质量提高﹐亦有必要施行自动运转﹐为此必需能使注道﹐流道及成形品自动而确实脱模﹒再者﹐少量生产之制品﹐型模制作日数及价格有所限制﹐亦由于成形品形状及浇口之种类不能自动脱模之场合﹐此际可决定成形品及注道﹐流道最容易脱模之顶出机构﹒同一形状之成形品亦由于材料种类及浇口形式之不同顶出方法亦随之异﹐必需将最适当之方法组合使用﹒成形品之顶出成形品顶出方法之决定﹐当然受成形品材料及形状等所左右﹐但原则上在成形品上制成缺口﹐阶层等﹐使能形成最确实之脱模﹐并且故障较少﹐再都故障发生之场合必需能简单补修﹒同一形状之成形品亦因由于外表﹐精度﹐成形性不同﹐而变化使用之顶出方法﹒顶出方法一般使用顶出梢(直梢﹐阶段梢)﹐筒套﹐刮料板﹐空气等﹐单独使用或组合使用﹐则视型模之寿命长短,型模加工之难易选定之﹒(1)顶出之种类1)顶出梢梢之加工最为容易﹐必需硬度之场合﹐施行淬火磨削等亦较其它方法为容易﹐可在成形品之任意位置上配置﹐为使用最多者﹒孔之加工容易﹐精度亦能达规定﹐滑动抵抗最小﹐契住发生少﹒因之型模寿命长﹐互换性使在破损之际﹐补修可以容易﹒然而在小面积上顶出﹐顶出应力集中于成形品之局部﹐杯类及箱形物品之退缩倾斜小﹐脱模抵抗大之成形品上﹐将发生压陷及顶穿等﹐此种场合﹐使用顶出梢大多不适当﹒2)方形或板状顶出梢板状顶出板等件之加工﹐热处理等并无困难点﹐但孔之加工困难﹐需要使用放电加工等特殊加工﹒将型范本及心型部份分割﹐形成组合型﹐加工变为容易﹐但制造工时增加﹐成形品由于有分割线﹐对透明件之外观有不良影响﹐亦有不允许之场合﹒再者﹐滑动抵抗亦较,圆梢为多﹐板之厚度较薄﹐容易引起弯折及挫屈﹐在可能限度中避免使用﹒3)套筒套筒之加工性比较良好﹐但套筒内径小而长度长者﹐加工较难﹐使用于肉薄件容易发生开裂﹒由于套筒之端面全面顶出﹐成形品顶出均一﹐能形成确实脱模﹐成形品开裂较少发生﹒4)刮料板刮料板及心型之加工并不比顶出梢为难﹐滑动面机械加工及配合则需要较多时间﹐滑动面契合部必需淬火﹐热处理为困难﹒再者﹐互换性亦趋向不良﹐修补必需较多人工﹒刮料板与心型配合面形状为圆形或方形者﹐机械加工及配合加工比较容易﹐但如为连续变化之曲线形者﹐则变为困难﹒再者﹐为使施行淬火后仍保有互换性﹐使用衬套嵌入﹐使补修容易﹐特别有数个型穴者﹐可仅将破损单件换调﹒刮料板与其它顶出方法比较﹐为顶出面积广大﹐成形品能确实脱模﹐对脱模抵抗较大之杯类及帽类之成形品脱模有效﹐广泛应用﹒再者﹐外观上几无顶出痕迹显示﹐此亦为优点之一﹒5)空气压出方法空气压出方法为设置阀等﹐将空气通入隙间﹐加工较为简单﹐对杯类及箱形等深度较大之成形品之脱模为极有效之方法﹒(2)顶出机构之实例图1为仅使用顶出梢之场合﹒顶出梢位置应配置于脱模抵抗强度较大之处﹐如脱模抵抗强度均一之场合﹐则应均等配置﹒图中所示之杯类及箱形成成形品﹐其侧面抵抗最大﹐最佳情形将顶出梢配置于此﹐再者﹐如于内侧面设置顶出梢场合﹐配置于侧壁附近较优于中央部份﹐否则将使顶出时容易引起开裂﹒图2为含有细而深之凸毂及加强肋之场合﹐使用顶出梢在其周围顶出﹐则发生开裂﹐容易使成形品破损报废﹐顶出梢必需设置于凸毂及加强肋底部﹐使能确实脱模﹒图3为阶层顶出梢之使例﹐由于无法使用细小顶出梢于小型成形品之场合﹐由于中段较粗﹐挫屈降低﹒图4为顶出梢与刮料板并用之一例﹐心型内面脱模抵抗较大部份﹐如仅用刮料板脱模﹐可能有列为断残留﹐为防止此种疵病发生﹐设置顶出梢﹐成为刮料板为主﹐顶出梢为补助之场合﹒此种场合﹐顶出梢设置于心型之内﹐形成心型冷却故障﹐使用小直径心型可作直接冷却﹐能消除此项缺点﹐必需考虑成形品之形状﹐使设置顶出梢之可能性消除﹐亦且能脱模﹒图5所示为部份之脱模抵抗较强(退缩倾斜少而深),如管状凸起场合﹐使用顶出梢在其周缘部及内面顶出时﹐成形品亦有开裂﹐皮用套筒顶出﹐以顶出梢为主﹐套筒为补助之机构﹒图6与图4﹒图5作相同之考虑﹐为刮料板及套筒并用之例﹒图7为深管状成形品之内外周具嵌入于可动侧之场合﹐在成形品端面使用用套筒顶出最为有效﹒图8示长套筒加工困难﹐短套套筒加工容易之例﹒一般情形﹐对盆形成形品顶出﹐大多使用图9之刮料板顶出﹐如使用图10所示之斜盆端顶出梢则加工简单﹒并且使用刮料板对心型冷却﹐亦如图4.图5之情形相同﹒有缺点存在﹒图11﹒图12为利用空气压出之情形﹒对大平面﹐深﹐肉薄之成形品(箱﹐杯等)使用刮料板顶出时﹐成形品可能引起挫屈﹐再者﹐成形品与心型间形成真空﹐使成形品破碎﹒使用于聚乙烯等软质材料场合破碎程度更为显著﹐此种场合使用空气压出最为有效﹐图11为仅使用空气者﹐图12为使用刮料板并在心型间有气压出方法之一例﹒有螺纹之成形品取出方法成形品有螺纹场合﹐脱模方法有下列三种﹒1) 型模螺纹部分模2)型模螺纹部置入嵌入件﹒3)成形品在型模螺纹部回转﹒(1)型模螺纹部分模此种方法适合于外螺纹(阳螺纹之型模构造﹐制造亦较简单﹐能确实脱模)﹒但成形品螺纹部有挤入分模线之废边产生﹐成形品之后加工﹐与契合件之配合形成故障﹒(2)型模螺纹部置入嵌入件型模构造不能使用分模及回转旋出者﹐型模构造简单之场合可使用置入嵌合件法﹒但使用此法时﹐成形品顶出后﹐必需将嵌入件取下﹐成形品为外螺纹之场合﹐由于收缩﹐取出容易﹐但如为内螺纹之场合﹐则置入之嵌入件与成形品之接角面积大﹐取出不易﹐由于成形品之材料及接触面积大取出困难﹒(3)成形品在型模螺纹部回转之场合一般盖件等为有内螺纹之成型品﹐大多使用回转自动旋出﹒此咱场合﹐成形品与型模任一件回转﹐并作退出运动﹐或一件仅作回转﹐他件退出运动﹐但对成形品必需有滑动定位(回转止动).成形品外周滑动定位﹐有点状浇口之型模﹐开模同时开始回转之场合﹐成形品与型模螺纹部之脱模﹐由于分模面之压开﹐分模面脱模抵抗大﹐成形品螺纹发生破断﹒为使能防止此项疵病﹐螺纹退出作用之速度﹐必需设计与分模线开模机构之速度相同﹒再者﹐在成形品螺纹部以外有脱模抵抗较强处所之场合﹐与回转开始之同时﹐必需有相同速度之顶出作用﹒回转伤虽在型模之固定侧及可动侧中俱可设置﹐但一般成形机设置于喷嘴及顶出机构之反对侧﹐由于注道﹐流道之配置及顶出关系﹐回转机构设置于可动侧﹐在型模构造上及成形能率上具属有利﹒1)成形品外周有滑动定位之场合图13为外点状浇口﹐图14为内点状浇口﹐俱使用特殊之顶出梢﹐刮料板等将其顶出﹐于开模间螺纹(a)回转纹数次后﹐在型穴中或心型上脱离﹐成形品自然落下﹒图15为成形品滑动定位及型模心型等位置于可动侧之场合﹐回转终了﹐成形品顶出H及h段﹐脱模落下﹒如图所示﹐H>h之场合﹐必需装置顶出梢(b)之顶出机构﹒图13~15所示适用于脱模时﹐浇口自动切断者﹐侧向浇口之场合﹐流道与成形品同时移动﹐必需设置同速之顶出机构﹒2)成形品内面有滑动定位之场合图16为内侧平面部有滑动定位﹐(a)一面回转﹐一面移动﹐当螺纹模之后﹐滑动定位仍然附着﹐必需另装除去装置﹐使成形件能自行落下﹒图17为内侧面有滑动定位之外螺纹场合﹐(a)回转﹐依成形品螺纹之螺距﹐将螺纹旋出﹐然后必需使用顶出梢(b)将其顶出﹒图18﹐图19内侧面有滑动定位﹐仅有(a)回转而(b)固定, 螺纹旋出脱模后,经由刮料板将其顶出. 刮料板之作用,有使用顶出梢, 弹簧等各种方法.3)成性形品端面有滑动定位之场合图20, 图21所示之成形品端面俱有滑动定位上, 为使其能自然落下, 必需另装顶出装置(a). 小型成形品而有侧向浇口之场合, 不能将成形品直接顶出, 需与流道一并顶出,再者无不需特别设置滑动定位, 可用浇口作为端面设置之滑动定位. 但对软质材料之场合, 如无相当大之浇口, 有剪断之可能.4)一面回转,一面作往复运动之小齿轮连结方法图22 示一面回转一面作往复运动之心型@与小齿轮直接连结, 图23示@与使用间接连结. 往复运动之滑动扺抵抗, 图23 者较小, 能圆滑作用,往复冲程较大, 图22中则强度较为良好, @中设质有心型梢之场合,与图22 所用者并物无差异.5)螺纹心型之驱动方法图24, 25利用开模冲程者.图26, 图27设置有油压及电动机等各别之动力者, 其优点为回转开始,停止等之时点能自由控制, 但必需有动力操纵装置. 成形品螺栓回转数多之场合, 图27 所示之驱动方法为最良好者.点状浇口之主注到道一流道之顶出侧向浇口在成形面中有流道一浇口之场合, 成形品可与之同时脱落,自然脱落容易,但点状浇口等场合, 自然脱落困难.图28 所示无流道剥离机构之场合, 必需以手工脱模. 型模构造最为简单, 但成形能率低, 少量生产以外场合不予使用.图29 为设置有流道刮料板, 但在剥离状态, 注道部分悬挂于流道刮料板孔中, 不能自然脱落, 此种情形应在A部设置顶出稍, 必要时使用空气压力将其压脱.图30 所示为较简单之构造,完成加工工数较少,流道长L比l为大,如l 深于以上场合,流道浮起时,形成嵌入于型范本策侧状态,不能自然脱落.再者,冷却时间长之场合,流道一部分弯折,一都度浮起之浇口部颁,仍将弹回退入于型范本侧.再者, A部颁有纵向庞旁边发生, 此等处所附着而不脱落. 此外, 成形品配置于注道之直下者, 注道定位稍不能装置, 使不适使用. 但无需使用弹簧及引长装置等装置, 并于开模同时, 浇口即可切断等利点.图31之优点及缺点大致相同,使图30中之A部不附着,流道之一部嵌入于型范本侧,亦能体度浮起脱落.但是注道顶出稍较可动侧装接板为长甚大,不能使用于无中心部顶出杆孔之成形机, 及中心顶出孔不够深之成形机上.图32 为钢笔套等细长成形品所用者, 在固定侧型模板内设置顶出板, 经由顶出梢将流道顶出, 此仅使用于限定之成形品形状.两段顶出(1)用途使用刮料板顶出场合, 刮料板内侧将成形品凸缘部顶出, 此部份仍与刮料板粘着, 必需更有任何方法将此自成形品上去除. 此种情形时, 为时能形成自动脱模, 必需有两段顶出机构.图33示刮料板与顶出梢之方法, 图34为将有凹陷之成形品, 使用两组出板, 作两段顶出, 使形成强制顶出之例.两段顶出之场合, 两组顶出冲程必需有所差异, 冲程大侧同同时或较迟作用.成性机顶出机构为压力缸及其附件, 以及定位杆及其附件, 前者之场合, 一方由固定侧, 使用螺杆,炼条及环等, 依开模冲程引长, 另一方由成形机之顶出机构作用, 能形成两段顶出作用.但后者场合, 两组必需由同一方向作两段顶出, 两组顶出机构必需有顶出冲程定时及冲程调节机构.(2)两段顶出之定位及冲程调节机构1)弹簧法图35为顶出之一方经由弹簧作用者,制造容易,安装位置小,为最简单之机构. 但不能承受过大之力,作用不确实.2)压力缸法图36 为使用压力缸代替弹簧, 作用确实, 定时能自由调节. 但安装位置较大, 成形机及型模较小时不能使用, 再者, 油压泵及空气压缩机必需有专用之控制设施.3)凸轮法图37示使用凸轮代替弹簧及压力缸, 作用确实,无须需其它附属设施.但由固定侧伸出之凸轮挺杆,必需安装对成形品取出无妨碍处所.4)夹颚法图38示(a), (b)两组顶出板, (a)组直接由(c)顶出, (a)组以夹颚(d)与(a)连结, 在作用行程中经(d)施行两段顶出.5)设置滑动件之顶出板图39为刮料板与顶出梢同时作用, (a)之直下方有滑动件, 由于此滑动件之移动, 顶出板在作用过程中, 刮料板停止作用,施行两段顶出.再者,(a)及(b)之接触面必需光滑.顶出板超前退回机构使用分模及侧向心型之型模中, 装有顶出梢者, 开模之际, 顶出梢必需在滑动件退回之前确实先行退回,否则两者发生冲突而破损.1)弹簧法图40为应用弹簧作顶出板之超前退回机构, 此种场合型模构造及加工最为简单, 装置位置亦小.但顶出梢者有发生住之场合, 使超前退回作用不确实, 滑动件与顶出梢冲突, 型模破损. 再者, 顶出冲程大者, 弹簧压缩比变大, 使用相当强度之弹簧, 顶出板在作用过程中亦不超前退回, 尽量避免作用.2)环节法图41示使用环节,作用确实,不致发生故障,但由固定侧伸出之作用杆(a)长度长,必需装置于成形品取出无妨碍之处所.3)游戏杆法图42示使用游戏杆之场合,起其优点及缺点与使用环节者相同.但当顶出板复归完了时,及必需解脱,.更需对定时调节注意.4)齿轮法图43所示使用齿轮之场合,作用确实,与环节法相同,有关成形品之取出考虑,必需与环节法及游戏杆法相同,与其它方法相异点为顶出板之作用,往复运动等由齿条实施,必需考虑顶出板顶出作用之稳定.5)油压缸法此种方法之机构之优点及缺点为:在两段顶出场合,作用确实,定时亦可自由调节; 缺点为装置复杂.。
模具顶出机构概要
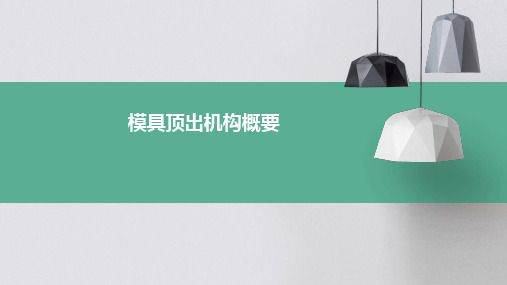
某铝合金门窗生产企业采用压铸模具生产铝合金型材,通过改进顶出机构,减少了残次品率。
冲压模具案例
某不锈钢厨具生产企业采用冲压模具生产厨具部件,优化顶出机构后,提高了生产效率和材料利 用率。
未来发展趋势
01
智能化
随着工业4.0和智能制造的推进,模具顶出机构的智能化将成为未来发
展的趋势。通过引入传感器、执行器和控制系统,实现顶出机构的自动
模具顶出机构概要
$number {01}
目 录
• 模具顶出机构简介 • 模具顶出机构设计 • 模具顶出机构制造工艺 • 模具顶出机构应用与案例 • 模具顶出机构常见问题与解决方
案
01
模具顶出机构简介
定义与作用
定义
模具顶出机构是指在塑胶模具中 ,将成型后的产品从模具型腔中 顶出的装置。
作用
在塑胶模具中,顶出机构的主要 作用是将成型后的产品从模具型 腔中顶出,以便进行后续的脱模 操作。
制造流程
设计
根据模具的需求和设计要求,进 行顶出机构的结构设计、尺寸计 算和零件排布。
热处理
对顶出机构的各个零件进行热处 理,以提高其机械性能和使用寿 命。
粗加工
对顶出机构的各个零件进行粗加 工,包括切割、打孔、铣削等, 以满足后续装配的需求。
精加工
对顶出机构的各个零件进行精加 工,包括研磨、抛光等,以获得 所需的尺寸和表面质量。
加强操作人员的培训和指导
确保操作人员熟悉模具的操作和维护要求,正确 使用和保养模具。
THANKS
模具顶出机构制造工艺
制造材料
1 3
钢材
钢材是制造模具顶出机构的主要材料,具有高强度、耐磨性 和耐腐蚀性。常用的钢材有碳素钢、合金钢和不锈钢等。
- 1、下载文档前请自行甄别文档内容的完整性,平台不提供额外的编辑、内容补充、找答案等附加服务。
- 2、"仅部分预览"的文档,不可在线预览部分如存在完整性等问题,可反馈申请退款(可完整预览的文档不适用该条件!)。
- 3、如文档侵犯您的权益,请联系客服反馈,我们会尽快为您处理(人工客服工作时间:9:00-18:30)。
顶出机构的设计原则
1.顶出机构应设置在动模一侧;因塑件
一般均留在动模一侧以便顶出。
2.顶出时与塑件的接触面应为塑件内表
面及其他不显眼的位置,以保证塑件外观。
3.顶出装置均匀分布,顶出力作用在塑
件承受力最大的部位。
以防变形和损伤。
4.顶出机构应平稳顺畅,灵活可靠,足
够的强度、耐磨性,平稳顺畅无卡滞,并且制造方便,易于维修。
顶杆的结构形式和固定形式
①顶杆的结构形式,如图6-5所示
②顶杆的固定方式,如图6-6所示。
顶杆的组装精度,如图6-7所示。
ⅰ)配合长度L:当d<6㎜时, L=2d;
当d =6~10㎜时,L<。
ⅱ)配合精度:理论上,单边间隙不大于塑料的允许溢边值即可。
实际上要求总间隙不大于塑料的允许溢边值。
因各种塑料的溢边值不同,故顶杆和顶杆孔的配合精度为一范围H8/f8~H9/f9(流动性好→小;流动性差→大)
ⅲ)顶杆和顶杆孔的配合间隙在注射时起排气作用,间隙大则排气功能好。
故选择间隙时需兼顾排气和溢料两方面。
顶杆顶出机构的设计要点:
a. 设在脱模阻力较大部位:
成型件侧壁、边缘、拐角等处。
如图6-8所示(形芯强度,为修复、扩孔留余地)
b. 设在塑件承受力较大的部位:较厚
处、立壁、加强筋、凸缘上。
以防顶出变形。
c. 位置布局合理,顶出受力平衡以避免
塑件变形。
d. 在确保顶出的前提下,数量尽量少以
简化模具结构,减少顶出对塑件表面影响。
e. 对有装配要求的塑件,顶杆端面应高
出形芯h=~㎜,以免影响塑件装配,但不能太高。
f. 顶杆应尽量短以保证顶出时的刚度、强度。
g. 不易过细,Φ<3㎜时,应采用阶梯形提高刚度。
h. 必须在塑件斜面设置顶杆时,为防止顶出过程中滑动,再顶杆部斜面上开横槽。
图6-8 d)
i. 当薄、平塑件上不允许有顶出痕迹时,将顶杆设在浇口附近。
图6-8 e)j. 在带侧抽机构的模具中,顶杆位置尽量避免与活动型芯发生运动干扰。
图6-8 f)
k. 避开冷却水路
l.材料:T8A、T10A,头部淬硬HRC50~55。
2.顶管顶出机构
用于中心有圆孔的塑件及环形轴套类塑件。
顶出时周边接触塑件,动作稳定可靠,塑件顶出均匀不变形,无明显痕迹,但精度要求高。
材料T8A、T10A,经淬硬处理HRC50~55。
加工较难,应尽量采用标准件。
(1)顶管顶出机构的基本形式
形式一:型芯固定在动模座板上,顶管固定在顶杆固定板上。
固定方式有图6-9a)~d)四种。
特点:结构可靠,但型芯和顶管太长,制造、装配、调整均困难。
形式二:型芯固定在动模板上,顶管和顶管座成为一体。
另有一辅助顶杆。
辅助顶杆在顶出板的作用下推动顶管座和顶管在型腔板内滑动。
这可使顶管和型芯长度缩短,但型腔板厚度增大。
图6-10
实例:双顶板顶管顶出结构实例图6-11。
详解各件名称、动作过程、顶出特点。
(2)顶管顶出的设计要点
①用于顶出塑件的厚度不小于㎜,否则强度难保证。
②顶管的组装精度与顶杆的组装精度相同。
③顶管与型芯保持同心,允差不超过~㎜。
其内孔末端应有㎜的空刀间隙以减少与型芯的摩擦磨损,利于排气、利于加工。
④都应设置复位装置,必要时还设导向零件,尤其是顶管直径较小时。
⑤材料:T8A、T10A。
端部淬硬HRC50~55。
最小淬硬长度大于顶管/型腔板的配合长度与顶出距离之和。
3.推板顶出机构
深腔、薄壁塑件如壳体、筒形件或形状复杂的塑件,不允许有顶出痕时采用推板顶出。
即在型芯根部安装一块与之形状相同的、滑动配合的顶板。
顶出时,顶板沿型芯周边平移。
(1)特点:
①顶出位置在脱模力较大的塑件底部边缘区,顶出面积大,顶出力大且无明显顶出痕迹。
②运动平稳,顶出力均匀,塑件不变形。
③无需设顶出机构的复位装置,合模时,推板靠合模力的作用带动顶出机构复位。
(2)推板顶出的结构形式图6-12a)~e)
(3)推板与形芯的配合形式
应避免因相对移动产生的摩擦、磨损。
若采用孔径配合,虽加工简单,但弊病
如下:
①顶出移动时,产生滑动摩擦,造成彼此磨损;且推件板一旦磨损或磨耗,很难修复。
②合模复位时,易于在形芯上的尖角发生碰撞而损伤。
③垂直配合易因制造误差而产生定位的偏移,使单边的配合间隙过大产生溢料飞边。
故通常推板与型芯均采用斜面配合的形式。
如图6-13所示。
4)推板顶出的设计要点
①推动推板的推杆应以顶出力为中心均匀分布,以使推板受力平衡,平行移动。
推杆兼起推板的导向作用。
图6-12(c)尽量加大顶杆直径,同时采用H7/f7配合精度。
②推板与形芯间采用H8/f8的间隙配合。
即不溢料飞边,又可较好定位。
③推板的顶出距离不得大于导柱的有效导向长度。
④推板的配合部分做淬硬处理,常用镶件。
(5)推板顶出实例:图6-14详解各件名称、动作过程。
4.顶块顶出机构
用于平面度要求较高的平板状塑件或表面不许有顶出痕迹的塑件。
特点:
①顶块推顶整个塑件表面,顶出面积大,顶出力均衡,塑件不变形。
②制作方便。