波音787飞机装配技术及其装配过程
飞机的装配过程和装配方法

2.1 部件气动力外形准确度
•
飞机外形准确度:飞机装配后实际外形
超音速歼击机外形准 确度要求
偏离设计给定的理论外形的程度。
• 飞机外形波纹度要求:外形波纹度误差
是两相邻波峰波谷的高度差H和波长L
的比值。 h
L
h
y n 1
yn
yn2 2
•外形表面平滑度:表面局部凸起和凹陷,包括铆钉、螺 钉、焊点处的局部凸凹缺陷,蒙皮口盖对缝间隙和阶差等。 通常顺气流和垂直气流方向的偏差有不同要求。
• 常用方法:按划线定位;按基准件定位;按装配夹 具(型架)定位;按装配孔定位
39/144
3.1 划线定位
40/144
41/144
• 在飞机上我们对划线工具有要求,对零件表面保护层有破坏 的划线工具及对飞机材料有影响的划线工具不能使用。
– 例如:如果用含碳的笔在钛合金材料的工件上划线,活性碳会渗透到工 件内,而我们的钛合金材料的工件一般安装在高温受热地方,如果活 性碳与工件结合就会造成工件受热不均匀而使材料开裂,所以在飞机 上划线工具有要求。
一般规定梁轴线允许的位置误差和不平度不超过±0.5~ 1.0mm,普通肋轴线的位置误差是±1~2mm,长桁位置误 差在±2.0mm以内
28/144
2.3 部件之间接头配合的准确度 结构件间配合准确度
叉耳式接头配合要求:
围框接头配合要求:
• 孔与螺栓之间为H8/h7或H9/f9 • 孔与螺栓配合间隙0.1~0.25mm
• 二者界限不是绝对的,可以互相转化。
38/144
3 装配定位方法
• 装配 定位、夹紧、连接 • 在装配过程中,首先要确定零件、组合件、板件、
段件之间的相对位置,这就是装配定位。 • 在装配工作中,对定位的要求是:
飞机装配的基本过程

部件的板件化程度是评价结构工艺性的重要 指标。 因此在结构设计中应尽量提高板件化程度。
一般来说在飞机设计阶段不仅应该确定设 计分离面,也应该充分考虑工艺分离面, 如果考虑不充分或者存在一些问题,就会 给制造带来很大影响; 但很多情况由于设计人员对制造的认识不 足而导致结构设计不合理,这就需要工艺 人员综合多方面因素考虑合理设置工艺分 离面。
1 定位准确度高 2 限制装配变形或强 迫低刚性结构件符合工 装 3 能保证互换部件的 协调 4 生产准备周期长
应用广泛的定位方法, 能保证各类结构件的 装配准确度要求
四、提高装配准确度的补偿方法
在飞机的一些结构复杂、协调尺寸较多的部位, 或是零件、组合件刚度较小其装配变形无法预先 估计的情况下,过分提高制造准确度和协调准确 度,在经济上不合理,在技术上难以达到,因此, 采用补偿方法。 补偿方法就是零件、组合件或部件的某些准确度 要求高的尺寸,在装配时或装配后,通过修配、 补充加工或调整,部分消除零件制造和装配误差, 最后达到规定的准确度要求。
(1)划线定位
手工划线;接触照像法
(2)装配孔定位
模线样板法,型架,工艺装配凸 台
(3)装配夹具(型架)定位
装配,校形(利用超六点定位)
划线定位
装配孔定位
装配孔定位
装配孔定位
装配夹具(型架)定位
装配夹具(型架)定位
采用装配型架定位是飞机装配的主要方式。 保证了零件、组件在空间具有准确的位置;
⑴定位基准-确定结构件在工装上的相对位置; ⑵装配基准-确定结构件之间的相对位置; ⑶测量基准-测量结构件装配位置尺寸的起始位置。
在装配过程中, 使用两种装配 基准:
以骨架为基准
飞机部装总装过程和装配新技术(新)word版本
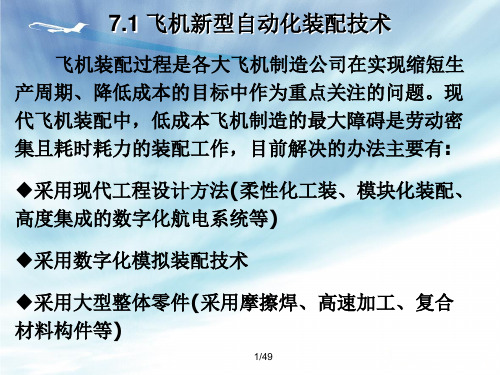
•
(如波音717、777总装线)
• 2、并行式飞机总装线布局
•线布局
•
(如波音787总装线)
8/49
7.3 新型飞机自动化装配技术
波音717总装线
串行式
9/49
7.3 新型飞机自动化装配技术
波音777总装线
串行式
10/49
7.3 新型飞机自动化装配技术
5/49
7.3 新型飞机自动化装配技术
飞机总装配工作过程
总装配过程示意图
6/49
7.3 新型飞机自动化装配飞技术机总装配生产线布局
串行式
并行式
斜排式
成批生产中,飞机总装配采用流水生产的组织形式 流水线上歼击机的布置方案7/49
7.3 新型飞机自动化装配技术
国外大飞机总装线布局
• 1、串行式飞机总装线布局
• 目前,B717、B737、B747、B757、B767和B777飞机已全部采用 了这一先进的制造技术,并在提高产品质量、降低成本的同时,缩短 向客户交付飞机的时间。波音公司的总装移动生产线具有如下的特点:
• (1)一条连续移动的总装生产线将飞机从一个总装小组缓慢地移至另 一个总装小组;
• (2)在整个装配过程中,飞机始终以平稳的速度移动,便于工人们准 确地把握制造流程,
13/49
•13
7.3 新型飞机自动化装配技术
波音飞机装配移动生产线的应用
飞机装配移动生产线的概念是由位于加利福尼亚 长滩生产波音717的波音分部最先提出的。波音生产 部门最初想象的移动装配生产线为:
7架飞机在牵引力作用下利用各自的起落架轮沿着 一条直线通过厂房,每架飞机及各自的保障设备和工 作站由一个动力车牵引前进。
7.1 飞机新型自动化装配技术
大飞机装配方法概述

•
相信相信得力量。20.10.292020年10月 29日星 期四6时34分45秒20.10.29
谢谢大家!
特种铆接
一、单面铆接
特种铆接
二、环槽铆钉(虎克钉)铆接
2.螺栓连接
•现代飞机的零件连接方法以铆钉连接为主,在 重要接头处还应用螺栓连接。 •.提高螺栓连接件疲劳寿命的方法
1. 提高螺栓和螺栓孔的精度和光洁度; 2. 采用干涉配合; 3. 采用挤压孔壁的方法。
锥形螺栓连接
四、组合件、板件装配
• 组合件和板件装配过程
1. 零件的定位及定位铆接; 2. 钻孔锪窝和铆接; 3. 补偿铆接及安装工作。
五、段件、部件装配
• 段件和部件装配过程 第一阶段,型架内装配; 第二阶段,型架外装配及安装工件; 第三阶段,最后精加工,检验及移交。
六、胶接和胶接结构装配
• 胶接的优点:不削弱结构材料,应力集中最小 ,疲劳强度高;密封性好;表面光滑,气动性 能好。
胶接工艺过程
预装配
胶接表面制备和密封
试验和检验
七、焊接装配
• 焊接(点焊)的优点:生产率高、成本低 ;比铆接结构重量轻;表面光滑;劳动条 件好。
• 焊接(点焊)的缺点:集中应力大,疲劳 强度低;可焊性差;不同材料不能点焊, 零件厚度相差太大或三层以上的结构不能 进行点焊。
• 2飞机装配使用了许多复杂的装配型架,飞机制造 的准确度很大程度上取决与装配的准确度,而一 般机械主要取决于零件制造的准确度。
一、装配基准
• 在装配过程中,使用两种装配基准:以骨架 外形为基准和以蒙皮外形为基准的装配。
二、装配定位
• 装配定位--在装配过程中,确定零件、组合件 、板件、 段件之间的相对位置。
飞机装配工艺(二)

最后精加工,检验及提交
1、最后精加工
满足部件对接的互换、协调要求,保证各部件之间相
对位置的准确度。 主要对接接头、配合面的精加工。
目的
工作内容
设备
单独的精加工型架 部件装配型架内的精加工设备(专用钻模、靠模)
最后精加工,检验及提交
2、检验、移交
1、对接接头或对接面的准确度的检验;
2、外形准确度的检验;
1 、有些不必要在型架上或自动铆接机上铆接的工作(结
工作内容
构件已形成一定的刚性); 2、有些铆钉难于在铆接机上铆接的工作;
3、一些安装工作(如小支架、口盖、卡箍等)。
要求
尽量减少架内的铆接工作,移至架外补充铆接和安装。
段件、部件的装配
段件、部件的特点:
结构较复杂,比较封闭,开敞性差; 一般带有全部的气动外形和重要的对接接头,准确度要求高; 一般都采用型架装配,工作量大; 劳动生产率低,装配周期长。
产品设计需要建立的基准。如:飞机水平基准线、对称
设计基准
轴线、翼弦平面、弦线、梁轴线、长桁轴线、框轴线、
肋轴线等。
设计基准的特点
一般都不存在于结构表面上的点、线、面,在生产 上往往无法直接利用。
装配基准
工艺基准
装配过程中需要建立的工艺基准。
工艺基准分类 (按功能分) 定位基准:用于确定结构件在设备或工艺装备上的相对位置。 装配基准:用于确定结构件之间的相对位置。
机身的段、部件总装型架。
根据飞机结构的使用功能、维护修理、运输方便等方面
Hale Waihona Puke 设计分离面的需要,设计人员将整架飞机在结构上划分为许多部件、
段件和组件,所形成的分离面。
主要特点
波音787:全球协作的梦想
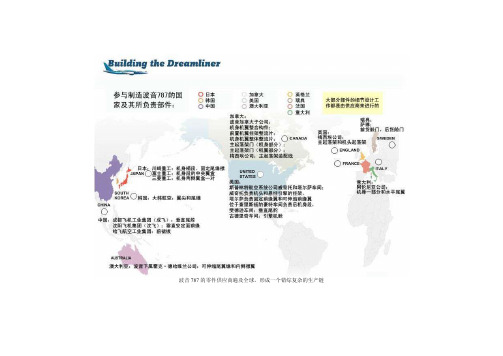
波音787的零件供应商遍及全球,形成一个错综复杂的生产链供应商们各自按照波音下发的统一规格生产零件,再将各自完成的部分经由令人眼花缭乱的物流渠道中转最终汇集到波音总装厂的只有已经完成组装的六大块主要构件,这样做理论上可以极大提高飞机的生产效率。
使用电脑进行无纸设计是波音自777以来的技术创新,波音在787的研制中也继续使用计算机无纸化作业生产制造机身所使用的碳纤维,波音787有61%重量使用碳纤维,所占比例居世界客机之最。
在日本制造的碳纤维机翼构件日本川崎重工拥有世界最大的热压机,用于制造787的翼盒结构在美国完成制造的垂直尾翼,稍后将送到下一处厂房与来自中国的尾舵等零件对接为了快速完成零件全球运输,波音改装了4架747专门用于空运大型组件波音747“梦想搬运工”采用了怪模怪样的机身铰接式舱门,从机身中间像折刀一样开启这是从日本空运完成的机翼主体;机身,主翼,机头......机身的各大组成部分从分布于世界各地的制造商手中发货,向负责下一级制造程序的工厂前进进入波音总装车间的零件都是已经接近完成的大型整体构件,这里的工人要做的就是将这些大件进行拼接对接机头与机身世界各地的供应商需要严格按照时间表完成任务,以确保这个世界最大的“流水线”不间断运行,波音787延迟试飞长达两年的问题之一,也是出在这个流水线尚无法顺利运转上。
毕竟这是一个前人从未尝试过的复杂生产过程。
最终787的原型机于2007年面世,但这时它还存在很多问题。
由于下游制造商的制造误差,许多零件无法顺利拼接,根本无法飞行,稍后就被拖回厂房“回炉再造”。
经过一系列整合,波音787终于度过了最艰难的时期,接下来将迎来为期9个月的全面飞行测试。
如果一切顺利,最终将于2010年全面投向市场。
建造梦想:波音787诞生记核心提示:美国西部时间12月15日上午10时27分,波音787梦想客机从埃弗雷特潘恩机场腾空而起,一个由遍布全球的生产者们共同建造的“梦想”终于走进了现实。
飞机装配的基本过程(课堂PPT)

使用两种装配 误差积累由内向外:
基准:
✓ 骨架零件外形制造误差
✓ 骨架的装配误差
✓ 蒙皮的厚度误差
✓ 蒙皮和骨架贴合误差
✓ 装配后变形
11
翼肋
铆接
桁条
铆接
骨架
蒙皮
铆接
大梁
12
以蒙皮外形为基准
误差积累由外向内: ✓装配型架卡板外形误差 ✓蒙皮和骨架贴合误差 ✓装配后变形
13
半肋
机翼
半肋
桁条
蒙皮
2 基准件必须具有较 好的刚性和位置准确度
在相互连接的零件 (组合件)上,按一 定的协调路线分别制 出孔,装配时零件以 对应的孔定位来确定 零件(组合件)的相 互位置 利用型架定位确定结 构件的装配位置或加 工位置(如精加工台)
1 定位迅速、方便 2 不用或仅用简易 的工装 3 定位准确度比工 装定位的低,比划线 定位的高
4
即使飞机被划分成多个部件,这样的部件 还是十分复杂的,由于部件的划分是按照 功能、实用等划分的,因此在部件装配的 时候还需要将部件进一步划分从而形成更 小的板件、段件、组合件等等;
这些组合件在装配时一般采用不可拆卸的 连接,他们之间的分离面称为工艺分离面;
5
6
合理的划分工艺分离面,也就是合理地对 部件进行剖分,对制造是极有好处的。
19
划线定位
20
装配孔定位
21
装配孔定位
22
装配孔定位
23
装配夹具(型架)定位
24
装配夹具(型架)定位
25
采用装配型架定位是飞机装配的主要方式。 ➢ 保证了零件、组件在空间具有准确的位置; ➢ 校正零件形状和限制装配变形的作用。 飞机装配中一般可不遵守六点定位原则,而采用
飞机装配工艺
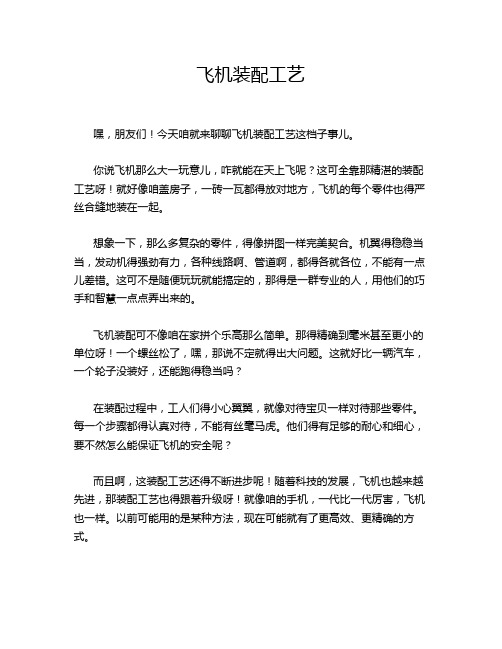
飞机装配工艺嘿,朋友们!今天咱就来聊聊飞机装配工艺这档子事儿。
你说飞机那么大一玩意儿,咋就能在天上飞呢?这可全靠那精湛的装配工艺呀!就好像咱盖房子,一砖一瓦都得放对地方,飞机的每个零件也得严丝合缝地装在一起。
想象一下,那么多复杂的零件,得像拼图一样完美契合。
机翼得稳稳当当,发动机得强劲有力,各种线路啊、管道啊,都得各就各位,不能有一点儿差错。
这可不是随便玩玩就能搞定的,那得是一群专业的人,用他们的巧手和智慧一点点弄出来的。
飞机装配可不像咱在家拼个乐高那么简单。
那得精确到毫米甚至更小的单位呀!一个螺丝松了,嘿,那说不定就得出大问题。
这就好比一辆汽车,一个轮子没装好,还能跑得稳当吗?在装配过程中,工人们得小心翼翼,就像对待宝贝一样对待那些零件。
每一个步骤都得认真对待,不能有丝毫马虎。
他们得有足够的耐心和细心,要不然怎么能保证飞机的安全呢?而且啊,这装配工艺还得不断进步呢!随着科技的发展,飞机也越来越先进,那装配工艺也得跟着升级呀!就像咱的手机,一代比一代厉害,飞机也一样。
以前可能用的是某种方法,现在可能就有了更高效、更精确的方式。
咱再想想,飞行员们在天上飞,他们的生命可都系在这装配工艺上啊!要是装配得不好,那后果简直不堪设想。
所以说,这飞机装配工艺可真是太重要啦!它关系着无数人的生命安全,也关系着我们的蓝天梦想。
那些从事飞机装配的工人们,真的是了不起的人呐!他们在背后默默付出,用自己的双手打造出一架架安全可靠的飞机。
他们的工作可不简单,得掌握各种技能和知识,还得有高度的责任感。
所以啊,下次当你看到飞机在天空中翱翔的时候,别忘了想想背后的这些故事,想想那些为飞机装配工艺默默奉献的人们。
让我们一起为他们点赞,为这神奇的飞机装配工艺喝彩吧!飞机装配工艺,真的是一门了不起的艺术!。
飞机装配工艺设计及其BOM重构过程探讨

飞机装配工艺设计及其 BOM重构过程探讨摘要本文对飞机总装配、部件装配工艺设计的内容和工作程序、部件对接各种形式的特点及其以模型为核心的装配工艺规划进行介绍;在协同制造系统中BOM划分由顶向下进行,先进行总体规划,再进行详细设计的BOM重构过程进行了研究探讨。
关键词:飞机装配;工艺设计;构型;BOM重构数字化技术应用使飞机设计制造模式产生巨大变革,美国波音公司在787 新型客机研制过程中,全面采用了将三维产品制造信息与三维设计信息共同定义到产品的三维数模型中,建立了三维数字化设计制造一体化集成应用体系,开创了飞机数字化设计制造的崭新模式,保证了波音787 客机的研制周期和质量[1]。
经过多年的努力,飞机数字化三维装配工艺设计技术研究也取得较快进展,实现的主要技术途径可以概括为二类:一类是以DELMIA软件为主进行定制开发,结合三维轻量化软件实现基于轻量化模型的工艺设计及现场可视化装配;另一类是基于协同平台开发以模型为核心的三维数字化工艺设计。
构型是产品某特定构型在产品生命周期中不断演变的动态过程,并以不同的视图展现出来,不管是EBOM, PBOM 还是MBOM,它们均是同一产品构型的不同的视图表示形式[2],BOM重构与三维数字化工艺设计密切相关。
1 总装配工艺设计1.1内容:飞机总装配是把已制成的飞机结构部件进行对接,在机上进行各种功能装置和功能系统的安装、调整、实验及检测,使飞机成为具有飞行功能和使用功能的完整的整体。
1)飞机结构部件的对接及对接后整流部分的安装,功能装置的安装、调整,各功能系统的安装;2)各功能系统和装置的调整试验及检测。
1.2特点飞机总装配的特点是:1)手工操作是飞机总装配作业基本方法,工厂已采用机器人进行机翼和机身对接工作,但自动化、智能化仍是努力的方向;2)飞机总装配涉及的工种多、专业性强,而且专业间接口多、交叉多、综合程度高、技术复杂,要有不同专业的人共同完成系统的安装、调试、检测和联试工作;3)协调关系复杂是飞机总装配的技术难点,可采用三维仿真解决空间协调问题;4)功能调试是总装配工作的重点;5)高完整性要求是飞机总装配的基本任务。
飞机结构装配,详细的解说过程,科普时间到

飞机结构装配,详细的解说过程,科普时间到飞机制造过程的主要环节是装配,包括机体部件的装配和各系统在机体内的安装(飞机总装);飞机装配过程是将大量的飞机零件按图纸、技术要求进行组合、连接的过程;飞机装配的最终目的是生产出具有合格质量的飞机产品;对于批量生产的飞机,还要尽可能保证飞机具有较好的互换性,这样才能大幅降低成本、提高飞机的可靠性以及保证较好的维修性。
一设计分离面和工艺分离面从系统论的角度出发,需要将飞机划分成若干功能相对独立的子系统;这种方法可以使整个研发、制造过程易于并行实施、便于管理……;对飞机结构来说,根据使用、运输、维护等方面的需要将整架飞机在结构上进行划分多个部件、段件和组件;这些部件、段件和组件之间一般采用可拆卸的连接,这样所形成的可拆卸的分离面就是设计分离面。
即使飞机被划分成多个部件,这样的部件还是十分复杂的,由于部件的划分是按照功能、实用等划分的,因此在部件装配的时候还需要将部件进一步划分从而形成更小的板件、段件、组合件等等;这些组合件在装配时一般采用不可拆卸的连接,他们之间的分离面称为工艺分离面;合理的划分工艺分离面,也就是合理地对部件进行剖分,对制造是极有好处的。
1. 增加了平行装配工作面,提高了装配工作的机械化和自动化;2. 改善了装配工作的开放性,有利于提高产品的装配质量;3. 部件的板件化程度是评价结构工艺性的重要指标。
因此在结构设计中应尽量提高板件化程度。
一般来说在飞机设计阶段不仅应该确定设计分离面,也应该充分考虑工艺分离面,如果考虑不充分或者存在一些问题,就会给制造带来很大影响;但很多情况由于设计人员对制造的认识不足而导致结构设计不合理,这就需要工艺人员综合多方面因素考虑合理设置工艺分离面。
二、飞机装配过程基准:确定结构件之间位置的一些点、线、面。
飞机的设计基准包括飞机水平基准线、对称轴线、翼弦平面、梁轴线、长桁轴线、框轴线、肋轴线等。
设计基准一般是不存在于结构件表面的点、线、面,为制造和装配需要,设立(装配)工艺基准。
飞机装配工艺学

飞机装配工艺学绪言飞机制造过程可划分为毛坯制造、零件加工、装配安装和试验四个阶段。
飞机装配过程:零件—组合键—板件—锻件—部件—机体—飞机。
安装是将发动机、仪表、操纵系统和附件等安装在机体中。
从构造和工艺上讲,飞机的各部分差别很大,发动机、机载电子设备、仪表、液压系统等都有专门厂家生产。
通常飞机制造仅指飞机机体零件制造、部件装配和整机总装。
飞机制造厂完成的是飞机机体的制造和各个系统的安装。
飞机装配的连接技术包括铆接、螺接(螺栓和螺钉)、胶接和焊接(胶焊)。
以机械连接(铆接和螺接)为主,大量采用铆接,并使用一部分螺栓连接。
尤其是复杂和受力较大的地方主要采用铆接和螺接。
第一章飞机装配过程和装配方法第一节飞机结构的分解零件:由整块材料制造的工件的基本部分称为零件。
组合件:几个骨架零件彼此连接起来的装配件称为组合件,如大梁、翼肋、隔框、翼尖等。
板件:一些骨架零件和蒙皮连接起来的装配件称为板件。
(由蒙皮、长桁和翼肋或隔框的一部分组成的独立单元)部件:由板件、组合件和零件构成的,在构造上和工艺上完整的机体部分。
段件:部件的一部分。
飞机结构划分成许多部件和可卸件后,在部件与部件间、部件与可卸件之间在结构上形成了分离面,因这种分离面是为结构和使用需要而取的,故称为设计或使用分离面。
飞机仅划分为部件,不能满足装配过程的要求。
为了生产需要,需将飞机结构进一步划分。
即将部件进一步划分为段件,段件进一步划分为板件及组合件等各种装配单元。
这种为满足生产需要而划分的分离面称工艺分离面。
●合理划分工艺分离面,有显著的技术经济效果:(一)增加了平行装配工作面,可缩短装配周期;(二)减少了复杂的部件装配型架数量;(三)由于改善了装配工作的开敞性,因而提高装配质量。
●部件、段件划分为板件后,具有重要的经济意义:(一)为提高装配工作的机械化和自动化程度创造了条件,板件化程度已成为评定结构工艺性的重要指标之一;(二)有利于提高连接质量。
飞机装配工艺设计的主要内容

飞机装配工艺设计的主要内容嘿,朋友!你知道飞机装配工艺设计是咋回事不?这可不像搭积木那么简单,里面的门道多着呢!先来说说装配方案的确定。
这就好比你要盖一座房子,得先想好是盖成小木屋还是大别墅,是一层还是多层。
飞机也一样,是选择分段装配然后总装,还是直接整体装配?这得根据飞机的结构、生产批量、技术水平等好多因素来决定。
你想想,如果不精心设计装配方案,那飞机能飞得稳当吗?接着是装配顺序的规划。
这就像是安排一场精彩的演出,哪个节目先上,哪个节目后上,都有讲究。
在飞机装配中,先装机翼还是机身?先装发动机还是起落架?顺序错了,那可就乱套啦!就好比你先穿鞋子再穿裤子,能舒服吗?还有装配型架的设计。
型架就像是给飞机零件安个“家”,让它们各就各位。
这个“家”得舒适、合适,不然零件可就“造反”啦!型架的结构、精度,都得精心琢磨。
你说,要是型架不靠谱,零件能乖乖听话吗?装配连接方法的选择也很关键。
是用铆钉连接,还是用螺栓?是焊接还是粘接?这就好比你选择走路去上班还是骑车去上班,不同的方法效果可大不一样。
选对了连接方法,飞机才能坚固耐用。
再讲讲装配工装设备的选用。
这就像是给工人师傅们挑选称手的工具,好工具能让工作事半功倍。
如果工具不好使,那不是耽误事儿嘛!还有装配精度的控制。
飞机可不是差不多就行的东西,精度要求那是相当高。
一丝一毫的偏差都可能带来大麻烦。
这就像你射箭,差一点就脱靶啦!最后是装配工艺的优化。
不断改进工艺,提高效率,降低成本。
就像你学习,不断找到更好的学习方法,才能学得又快又好。
总之,飞机装配工艺设计是一项极其复杂又极其重要的工作。
每一个环节都得精心设计,容不得半点马虎。
只有这样,咱们才能造出安全可靠、性能优越的飞机,让它在蓝天中自由翱翔!你说是不是这个理儿?。
波音787制造

波音787飞机生产所体现的先进制造技术波音787复材机身段的制造技术碳纤维合成技术已有数十年的历史,自20世纪80年代以来,广泛应用于试验飞行和军事航空领域。
不过,波音787是第一种主要采用碳纤维材料制造的商业客机:70%机体使用合成材料制造。
碳纤维丝被植入树脂中,然后将一层层的碳纤维夹在别的材料之间,以便令碳纤维丝处于不同方位。
利用这种技术制造的材料既轻又坚硬——强度至少是钢材的四倍。
金属机身一般由长方形金属板构成,然后用成千上万个铆钉固定,使用合成材料,整个机身的管状截面可以作为整体制造出来——基本上是在一个巨型炉子(称为高压釜)烧制碳合成材料。
接着,只要通过更少的扣件就能将更少的部件固定。
这使得波音公司可以重新考虑整个制造过程。
波音不是像以前那样,将机身结构组装完毕,然后再安装所有的布线、管线和其他机载系统,而是将机身整个部分外包,造好以后再在埃弗雷特进行组装。
由于复合材料结构有着许多众所周知的优点,在对复材结构做了大量成功的研究试验基础上,波音公司决定787机体主要结构大规模地采用复合材料。
由777飞机复材用量的12%一步跨越到50%,即机身和机翼壳体几乎都由碳纤维增强。
由于复合材料结构有着许多众所周知的优点,在对复材结构做了大量成功的研究试验基础上,波音公司决定787机体主要结构大规模地采用复合材料。
由777飞机复材用量的12%一步跨越到50%,即机身和机翼壳体几乎都由碳纤维增强复合材料制成,仅少数机体部位应用铝合金或其他材料。
而空客公司原来的A350设计方案是在A330飞机基础上进行的,机身仍是以铝合金的铆接结构为主,复材用量仅为35%,这样,波音787就大幅度地拉大与A350复材用量的差距。
对于波音的竞争对手空客公司来说,客机的超大型机身复材部件的制造技术是一个难于逾越的巨大挑战。
这种由复材组成机身的787客机,是全球第一款利用高科技碳纤维复合材料打造的客机,机身段省去1500块铝合金钣料零件和4~5万个连接件,使机体结构件尺寸变小,但更轻盈坚固。
大型飞机装配方法及其机翼装配技术

大型飞机装配方法及其机翼装配技术作者:朱吉祥来源:《科学与财富》2018年第05期摘要:大型飞机的装配是比较困难的,特别是民用飞机,波音型民用飞机整体机型上很大,零部件很多,本文研究大型民用飞机的自动化装配方法波音飞机的装配方法,探讨飞机机翼的装配技术,通过怎样的自动化装配技术保证大型飞机的使用寿命和装配效率。
关键词:自动化装配;波音飞机装配方法;机翼装配技术1.自动化装配大型民用飞机典型特点就是飞机整体结构大,质量大,可靠性高,寿命要长,但是大型飞机的制造却困难,实现大型飞机自动化制造是提高飞机装配质量和提高飞机寿命的有效途径,虽然大型飞机的结构件大提高飞机装配难度,但是又是由于飞机结构大的原因,易于实现大型飞机自动化装配,对自动化装配的要求如下:(1)自动化装配要保证飞机结构件和零件的质量,寿命;(2)自动化程度要高,避免人工的需求;(3)自动化装配与数字化结合,实现装配过程中的数字化监控,消除装配误差;(4)要适应飞机任何材料的装配,包括复合材料,并确保复合材料的装配质量;(5)自动化装配技术还要实现柔性化,降低研发成本,减小空间使用,缩短飞机制造周期。
以上反应的是飞机装配成本、飞机产量、装配效率、装配精度等之间的关系图,图中反应飞机半自动化装配,自动化装配、手工装配、大批量生产以及单机装配的关系图,所以自动化装配是大型飞机装配的必要方法,也是最有效的方法。
2.波音飞机装配方法波音飞机的装配采用的是柔性翼梁装配系统,这项技术属于大型飞机自动化装配计划,这项技术的核心是柔性装配工装和自动铆接技术的使用,可以使用与飞机任何规格与尺寸的装配,具体分析如下:决定性柔性装配方法:这种装配技术是将零件设计成预先定义的截面进行装配,在这个装配过程中,不需要定位与检测技术,波音飞机的装配利用飞机零件之间的关系和主要关键特征进行数字化设计,零件的装配不是按照工装进行装配,是根据设计进行装配,将工装代替掉。
以骨架为基准的自动化装配:对于大型民用飞机的装配,利用骨架为装配基准进行装配,优点是装配精度能保证,壁板和蒙皮可用束紧带进行压紧,简化装配,避免装配误差的产生。
波音787飞机装配技术及其装配过程

波音787飞机装配技术及其装配过程波音787飞机装配技术及其装配过程波音公司基于全球协同环境GCE研制的787“绿色”环保客机,虽然尚未试飞,但它的一系列全新的飞机装配理念、方法和技术,就已经引起航空制造业界的极大关注。
这些大型飞机装配的新技术,如全球协同研制的理念和方法、基于模型定义(MBD)的装配技术、利用室内GPS系统的飞机对接总装过程以及复材机体的装配连接技术的应用等更是业内关注的焦点。
787客机结构及其全球协同研制模式由于复合材料结构有着许多众所周知的优点,波音公司在对复材结构做了大量成功研究试验的基础上,决定787机体主要结构大规模地采用复合材料,由777飞机复材用量占整机材料用量的12%一步跨越到现在的50%,即机身和机翼外壳几乎都由碳纤维增强复合材料制成,仅少数机体部位应用铝合金或其他材料。
这种机身由复材组成的787客机,是波音公司全新研制的机型,与之前的机型相比,它的维修成本可节省30%,飞行的舒适性也有很大提高,所以得到很多航空公司的欢迎。
因此,国际上各航空公司都期望着这一“绿色”客机能给空中旅行带来革命性的变化。
与此同时,787客机的出现也使这种飞机的制造和装配技术发生了根本性变革。
在过去,波音标准的研制方法是先在公司内设计好飞机(Design the PlaneIn-House),然后把飞机的零部件或一整段机体的图纸送到它们的制造伙伴工厂去生产。
而这次在研制787客机中,波音彻底地改变了研制方法,也改变了研制流程。
它利用Dassault的PLM套件创建了全球协同平台,与合作伙伴协同研制787客机。
最重要的是,全世界大约6000余名工程师联合起来共同设计和工程化787客机。
波音787机体分段及分工情况:意大利的阿里尼亚航空制造公司,负责制造主机身48段;日本的富士重工、川崎重工和三菱重工等公司,负责制造机翼12段、主起舱45、中央翼盒11段和机身13段;北美的古得里奇公司负责制造发动机短舱和反向装置;美国的Spirit公司负责制造机身43段,沃特公司负责制造机身47段;全球航空公司负责机尾47段和48段对接装配等工作。
- 1、下载文档前请自行甄别文档内容的完整性,平台不提供额外的编辑、内容补充、找答案等附加服务。
- 2、"仅部分预览"的文档,不可在线预览部分如存在完整性等问题,可反馈申请退款(可完整预览的文档不适用该条件!)。
- 3、如文档侵犯您的权益,请联系客服反馈,我们会尽快为您处理(人工客服工作时间:9:00-18:30)。
波音787飞机装配技术及其装配过程波音公司基于全球协同环境GCE研制的787“绿色”环保客机,虽然尚未试飞,但它的一系列全新的飞机装配理念、方法和技术,就已经引起航空制造业界的极大关注。
这些大型飞机装配的新技术,如全球协同研制的理念和方法、基于模型定义(MBD)的装配技术、利用室内GPS系统的飞机对接总装过程以及复材机体的装配连接技术的应用等更是业内关注的焦点。
787客机结构及其全球协同研制模式由于复合材料结构有着许多众所周知的优点,波音公司在对复材结构做了大量成功研究试验的基础上,决定787机体主要结构大规模地采用复合材料,由777飞机复材用量占整机材料用量的12%一步跨越到现在的50%,即机身和机翼外壳几乎都由碳纤维增强复合材料制成,仅少数机体部位应用铝合金或其他材料。
这种机身由复材组成的787客机,是波音公司全新研制的机型,与之前的机型相比,它的维修成本可节省30%,飞行的舒适性也有很大提高,所以得到很多航空公司的欢迎。
因此,国际上各航空公司都期望着这一“绿色”客机能给空中旅行带来革命性的变化。
与此同时,787客机的出现也使这种飞机的制造和装配技术发生了根本性变革。
在过去,波音标准的研制方法是先在公司内设计好飞机(Design the PlaneIn-House),然后把飞机的零部件或一整段机体的图纸送到它们的制造伙伴工厂去生产。
而这次在研制787客机中,波音彻底地改变了研制方法,也改变了研制流程。
它利用Dassault的PLM套件创建了全球协同平台,与合作伙伴协同研制787客机。
最重要的是,全世界大约6000余名工程师联合起来共同设计和工程化787客机。
波音787机体分段及分工情况:意大利的阿里尼亚航空制造公司,负责制造主机身48段;日本的富士重工、川崎重工和三菱重工等公司,负责制造机翼12段、主起舱45、中央翼盒11段和机身13段;北美的古得里奇公司负责制造发动机短舱和反向装置;美国的Spirit公司负责制造机身43段,沃特公司负责制造机身47段;全球航空公司负责机尾47段和48段对接装配等工作。
最后,由波音公司利用超大型运输机LCA把世界各地制造的十几个大部件运到波音进行对接总装、试飞和最后的交付工作。
基于模型定义(MBD)的装配技术波音公司在研制装配787客机的过程中,采用了全新的基于模型定义(Model Based Definition,MBD)的技术。
美国机械工程师协会于1997年在波音公司的协助下开始有关MBD标准的研究和制定工作,并于2003年成为美国国家标准。
随后CAD软件公司把此标准设计到软件中,使波音公司才有可能在2004年开始的787客机设计中,全面采用基于模型定义的新技术。
该技术将三维制造信息PMI(3D Product Manufacturing Information)与三维设计信息共同定义到产品的三维数字化模型中,使CAD和CAM(加工、装配、测量、检验)等实现真正的高度集成,数字化技术的应用有了新的跨越式发展,可不再使用二维图纸,将工程技术人员从百年来的二维文化中解放出来。
同时使数字化技术在飞机装配中的应用有了革命性的进展。
在此过程中,其主导思想不只是简单地将二维图纸的信息反映到三维数据中,而是充分利用三维模型所具备的表现力,去探索便于用户理解且更具效率的设计信息表达方式。
其中,最为艰难的是“要从二维图纸文化这种现有概念中跳出来,从零开始研究新的信息表达方式”。
同时,波音公司进一步把MBD技术深入应用到787数字化装配的各个方面。
数字化协调方法——阵列式装配(DA)技术由于现代大型飞机的结构尺寸大、刚性差、定位精度要求严,同时还有制造成本低、装配速率高的要求。
这就造成飞机装配工艺及其工装的设计和制造难度大,装配协调困难。
使得传统的装配工艺及其工装难以胜任,需要用新的方法和技术来支持部件之间的精确装配关系。
在这种条件下,基于产品的三维数字化定义和精确CNC加工技术的数字化协调方法,即阵列式装配(Determinate Assembly,DA)技术应运而生了。
一般来说,装配工装大于产品本身,工装的设计与产品设计、工装制造和装配的速率密切相关,而且飞机产品的设计还在不断的变化之中。
所以需要新的装配工艺及其工装设计和制造方法——基于数字化协调的阵列式装配方法来解决这个问题。
数字化阵列式装配是一个术语,用来描述实际的设计零部件在预先定义的界面上,能精确地装配在一起,而不需要实物标准样件或其他复杂的测量和调整技术,其实质上是数字化协调方法的具体体现。
也就是通常说的,为了制造和装配的设计(DFMA),这样大幅度地减少了工装的设计和制造工作。
空客A340-600的壁板制造单元就是典型实例。
这一壁板制造单元用来把铝合金的长桁定位和连接到机加的壁板上,这是一个很大的装配件,高几米、长30多米。
传统的方法是采用夹具来定位长桁和壁板,设计了长桁各细部的定位件,现场用激光跟踪仪来安装。
这样现场就需要用激光跟踪仪来确定超过2000个定位点,这是件极其费工费时、劳动量也极大的困难工作。
空客公司采用的数字化阵列式装配方法很好地解决了这个问题,不仅能将长桁和壁板快速而准确地装配到一起,还有利于并行协同研制工作的展开。
随后,空客公司还把这一先进技术应用到了大型客机A380机翼的主要工装设计和制造中。
在20世纪90年代中期,波音公司在新的大型飞机747的制造中,开展了机身装配改进团队(Fuselage Assembly Improvement Team, FAIT)项目,也将先进的阵列式装配方法应用于机身的装配中。
其原理是:由于飞机机身是在飞机坐标系中进行数字化定义的,机身壁板的定位点也在飞机坐标系中定义。
在壁板的装配型架上有用数字化方法安装的定位点的定位器,在机身装配工装上的壁板定位器用激光跟踪仪确定它们在飞机坐标系中的位置,这样就保证了多块机身壁板在机身坐标系里是相互协调的,可以使壁板能装配到机身的准确位置上。
波音公司在研制787客机中进一步应用基于数字化协调的阵列式装配技术于部件装配和全机的对接总装中,如部件装配中应用了DA孔(通称协调孔)的定位方法,也是基于上述定位原理的数字化协调方法。
室内GPS系统在787客机总装中的应用激光跟踪仪在我国飞机装配工装的制造和安装中已广泛使用,但我们对室内GPS系统(也称作局域GPS精密测量系统)在飞机装配中的应用还比较陌生。
室内GPS系统是数字化装配技术最重要的技术手段之一。
室内GPS系统与激光跟踪仪相比较,主要优势体现在如下几点:首先,在室内GPS系统中进行测量不会因为掉光而影响工作进程,这是由室内GPS系统的原理决定的。
它是由发射器以水平270°、垂直60°的覆盖范围从3个方向无线发射信号,传感器和接收器只要在这个信号的覆盖范围内,就能接收到光信号,并无线传播到中央控制电脑。
在这个过程中,传感器只要能同时接收到2个发射器发射出的信号就能测出点的三维坐标值。
如果能同时接收到3~4个发射器发射出的信号就是增加了自由度和精度。
由此可见,在测量时即使有人走过,挡住了一个发射器发射的信号,也不会影响这一点坐标的测量。
即使所有的发射器信号被遮挡也没有关系,只要增加测量杆的长度就可以正常测量。
其次,室内GPS系统能够满足多用户同时使用。
在一个装配车间内,常常需要同时监控被测部件的几个关键点和面的位置关系。
这种情况下,我们只需要在车间的墙壁和天花板上固定一定数量的发射器,一般建议在30m×30m的空间内放置6个发射器,信号就会全部覆盖这个范围,被测部件的关键点和面的位置就都会被监控。
我们可以在不同的被测部件上放置不同的传感器和接收器,那样它们的位置就会被实时监控。
也可以用几个测量杆组件,由不同的工作人员同时测量部件的各个关键点和面的位置关系,互不干扰。
也就是说,系统建立起来后,只要增加传感器和接收器就可以增加用户了。
中央电脑可以同时处理这些数据并传递给不同的终端用户(比如掌上电脑),给用户的工作带来很大方便。
第三,当整个系统进行一次固定装配标定后,就可以无限次数的使用。
所有进入这个区域的待测物都可以马上测量,无需建立坐标系。
唯一要做的工作就是打开发射器的电源开关,待它预热5min之后,就可以马上开始测量工作。
第四,室内GPS系统最为突出的特点是可以进行大尺度的测量。
在10m的测量空间中精度能达到0.1mm,这大大高于激光跟踪仪,而且测量范围可以无限增加,只要增加发射器即可。
可以实现自动装配测量,实时监控移动物体的运动曲线,比如飞机机翼与机身的自动对接过程。
第五,室内GPS系统可以对系统自身进行监控。
如果有发射器出现位移或出现问题的情况,系统会自动报警,这样就可以在最短的时间内发现系统的问题。
局域GPS精密测量系统不受温度影响,它的工作范围为-10~50℃。
基于上述原因,波音在研制787客机的总装过程中采用了集成的室内GPS系统环境进行装配。
复材结构的数字化钻孔和连接技术在复材部件的装配中,一般采用机械连接或胶接的方法将复合材料构件或复合材料构件与金属零件装配在一起形成部件。
由于复合材料构件的特殊性,它的连接方法与金属零件的装配方法也有所不同。
787客机的结构材料有50%是复合材料,机身的大部段壳体基本上都是复合材料的。
考虑到复材机体结构的特殊性,钻孔时材料层间容易劈裂,而且又不适宜敲打,所以它们的连接不能用一般的铆接技术来实现;另一方面,考虑到787客机的生产批量大,有数量巨大的孔需要钻制,所以波音和合作伙伴研制了专用的自动化钻孔铆接设备和相关的工艺技术,以此来确保787客机的装配连接质量和速率,同时保持低的成本部件制造与装配过程以787客机的机头41段部件为例,说明其制造和装配的过程。
1 机头41段部件的制造首先,构建复材部件壁板(包括长桁)的成型模具(型胎),这型胎是组合式的,便于装拆。
其上有长桁内槽,先把预制好的复材长桁放到内槽里,然后进行缠绕操作。
再进入固化炉成型,成型后再进行切边钻孔等机械加工,最后喷漆。
2 机头41段部件的装配以上的制造过程仅完成了此部件的复材壳体制造工作,里面还需安装机身隔框等其他组件。
部件装配不仅要完成结构的安装工作,而且要把此部件内的所有仪表、电缆和管路等航电设备也都安装好,充分体现了飞机产品模块化设计和装配的思想。
波音最后仅需进行十几个大部件的对接总装配工作,保证3天之内能总装出一架787客机。
全机对接总装配过程由于787客机的结构和材料与一般的大型客机不同,所以其装配方法也有重大的变革。
通常复杂而笨重的装配型架(激光跟踪仪和厂房内的巨大起重机)不见了,取而代之的是轻巧的型架式起重运输系统(Jig-Crane-Style Materials Handling System)和厂房天花板上装有的一排排的室内GPS系统,用来定位飞机部件装配型架。