2.5连铸坯的凝固及其控制
第三章 连铸坯的凝固与传热
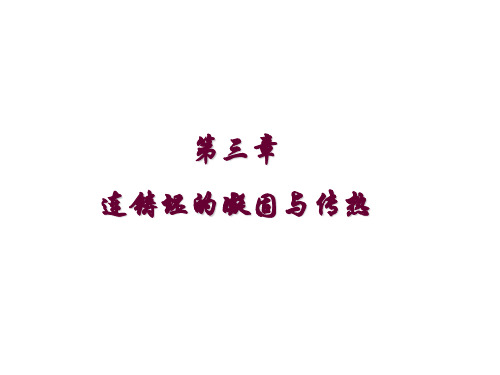
2、坯壳及气隙的形成
注入结晶器的钢液除受结晶器壁的强制冷却外,还通过钢 液面辐射传热及拉坯方向的传导传热,使钢液形成一定厚度的 坯壳。其传出热量的比值大约为30:0.15:0.03。因此,结晶器 内钢水可近似地看作向结晶器壁的单向传热,其散热量的波动
与坯壳表面和结晶器壁的接触状况有关。
钢水热量传出途径:钢水→坯壳→气隙→结晶器铜壁→铜 板与冷却水界面→冷却水。
取24~26 mm/min1/2 ; 板坯取17~22 mm/min1/2 ; 圆坯
取20~25 mm/min1/2 。 小方坯出结晶器下口坯壳厚度8~10 mm,板坯、大方坯大于 15mm。
5、影响结晶器凝固传热的因素
研究指出:气隙热阻占总热阻的 70~90% ,因此改善结 晶器传热最重要的是减小气隙热阻。气隙的形成与演变决定 于凝固壳的收缩、坯壳高温强度、结晶器润滑和结晶器几何 形状等因素。
喷水冷 却 凝固壳
辐射冷 却
铸坯热送热装和连铸连轧等工艺。
连铸机冷却区示意图
2、连铸坯的凝固是沿液相穴在凝固温度区间 将液体转变为固体的加工过程
连铸坯可看成是液相穴很长的钢锭(板坯可达30m),以一定速度
在铸机内运动并凝固,也可看成是在凝固温度区间(TL → TS)把液体转
变为固体的加工过程。 在固—液交界面附近,存在一个凝固脆化区,此处强度、塑性接
从结晶器内凝固传热考虑,应避免高温钢水浇注。
6、确保坯壳出结晶器下口有足够厚度及均匀生 长的措施
① 浇注温度不能过高,保持低温浇注; ② 水口与结晶器严格对中; ③ 结晶器冷却水的水质、流速、水量达到要求,均匀冷却; ④ 合理的结晶器锥度;
⑤ 结晶器液面保持稳定;
⑥ 选择性能良好的结晶器保护渣,以形成均匀的保护渣膜等; ⑦ 合适的浇注速度。
东北大学智慧树知到“冶金工程”《连铸坯凝固与质量控制》网课测试题答案卷4

东北大学智慧树知到“冶金工程”《连铸坯凝固与质量控制》网课测试题答案(图片大小可自由调整)第1卷一.综合考核(共10题)1.连铸坯在凝固过程中出现“小铸锭”凝固,是产生铸坯中心缺陷的重要因素,产生“小铸锭”凝固的原因,下面哪一种分析是正确的?()A.拉速不稳定,二冷不均匀B.结晶焕热过强C.钢的过热度不稳定2.低碳钢在连铸工艺过程中容易出现逐层凝固方式,形成发达的柱状晶,该论述是否正确?()A.论述正确B.论述不正确3.连铸坯的凝固方式有下面哪几种?()A.逐层凝固方式B.快速凝固方式C.中间凝固方式D.体积凝固方式4.高碳钢和低碳钢相比连铸时结晶器内凝固时气隙小、坯壳较厚、拉坯阻力大,要注意使用旧结晶器,稳定拉速,论述是否正确?()A.论述正确B.论述不正确5.一般情况下亚包晶钢连铸时结晶器冷却强度大好?还是小好?()A.冷却强度大好B.冷却强度小好6.适当降低浇铸温度铸坯凝固速度是增加还是减小?()A.凝固速度减小B.凝固速度增加7.连铸坯结晶器凝固传热过程下面哪一种分析是正确的?()A.结晶器凝固传热过程中90%以上热量是通过结晶器的冷却水带走的B.结晶器凝固传热过程中30%以上热量是通过结晶器液面释放的8.大尺寸的铸坯如何增加中心区域的等轴晶比例,下面哪一种工艺是不可行的?()A.慢拉速B.适当降低浇注温度C.变质处理D.提高二冷强度9.高碳钢和低碳钢相比,在结晶器凝固过程中,哪一种钢形成的气隙大一点?()A.低碳钢大一点B.高碳钢大一点10.适当提高铸坯中心等轴晶区的比例,下面哪一种工艺措施的叙述是不正确的?()A.适当降低浇注温度B.采用电磁搅拌技术C.结晶器内的变质处理D.在大包处理钢水第1卷参考答案一.综合考核1.参考答案:A2.参考答案:A3.参考答案:ACD4.参考答案:A5.参考答案:B6.参考答案:B7.参考答案:A8.参考答案:D9.参考答案:A10.参考答案:D。
2205双相不锈钢连铸坯连铸条件的研究
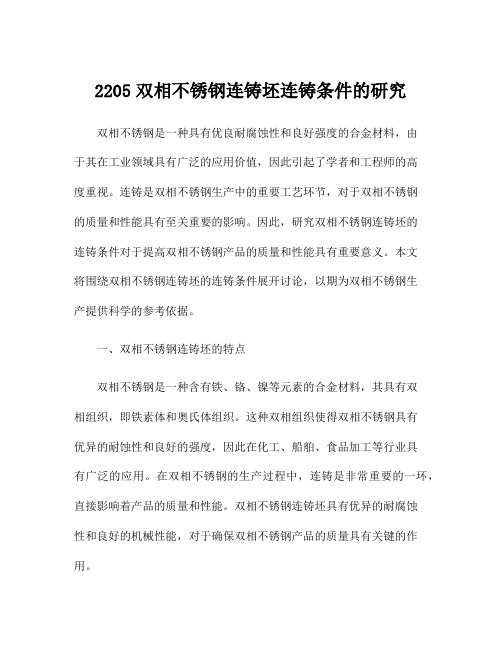
2205双相不锈钢连铸坯连铸条件的研究双相不锈钢是一种具有优良耐腐蚀性和良好强度的合金材料,由于其在工业领域具有广泛的应用价值,因此引起了学者和工程师的高度重视。
连铸是双相不锈钢生产中的重要工艺环节,对于双相不锈钢的质量和性能具有至关重要的影响。
因此,研究双相不锈钢连铸坯的连铸条件对于提高双相不锈钢产品的质量和性能具有重要意义。
本文将围绕双相不锈钢连铸坯的连铸条件展开讨论,以期为双相不锈钢生产提供科学的参考依据。
一、双相不锈钢连铸坯的特点双相不锈钢是一种含有铁、铬、镍等元素的合金材料,其具有双相组织,即铁素体和奥氏体组织。
这种双相组织使得双相不锈钢具有优异的耐蚀性和良好的强度,因此在化工、船舶、食品加工等行业具有广泛的应用。
在双相不锈钢的生产过程中,连铸是非常重要的一环,直接影响着产品的质量和性能。
双相不锈钢连铸坯具有优异的耐腐蚀性和良好的机械性能,对于确保双相不锈钢产品的质量具有关键的作用。
二、双相不锈钢连铸坯的连铸条件(一)浇注温度浇注温度是影响双相不锈钢连铸坯质量的重要因素之一。
过高或者过低的浇注温度都会影响双相不锈钢的组织形貌和化学成分,从而影响产品的性能。
因此,确定合理的浇注温度对于双相不锈钢的生产至关重要。
一般来说,双相不锈钢连铸坯的浇注温度应在合金的固相线以下100~150℃左右。
通过测定合金的凝固曲线和结晶温度,合理控制浇注温度,可以获得理想的双相不锈钢连铸坯。
(二)浇注速度浇注速度是影响双相不锈钢连铸坯凝固过程的重要因素。
合适的浇注速度可以促进均匀的凝固结构,从而获得优良的双相不锈钢连铸坯。
一般来说,较高的浇注速度可以促进块状铁素体的形成,提高产品的强度和硬度;而较低的浇注速度可以促进奥氏体的形成,提高产品的韧性和塑性。
因此,根据产品的要求,合理控制浇注速度对于获得理想的双相不锈钢连铸坯至关重要。
(三)结晶器参数结晶器在双相不锈钢连铸坯的凝固过程中具有非常重要的作用。
合理的结晶器参数可以有效地促进均匀的凝固结构,提高双相不锈钢连铸坯的质量。
连铸圆坯质量控制

连铸圆坯质量控制连铸坯质量检验及控制一、连铸坯的内部结构(凝固组织)的一般特征及检验。
连铸坯的检验方法连铸坯的内部结构:经过酸浸(酸洗)或硫印的方法在连铸坯横断面或纵断面上用肉眼或低倍放大镜看到内部组织结果。
硫印硫印是用感光相纸显示试样上硫偏析(合金中各组成元素在结晶时分布不均匀的现象称为偏析)的方法,主要用于钢铁行业铸坯质量的检验。
从铸坯上取纵向或横向试样,试验面加工的光洁度不应低于6。
使用反差大的溴化银表面相纸,把与试样大小相同的相纸放入稀硫酸中浸泡1-2分钟后取出,将相纸对准检查面轻轻覆盖好,将试样与相纸间气泡赶净,待接触2-5分钟后取下,将相纸在流水中冲洗,然后定影烘干,即完成一张硫印。
印基本原理:硫酸与试样上的硫化物(FeS、MnS)发生反应,生成硫化氢气体,硫化氢气体再与感光相纸上的溴化银作用,生成硫化银沉淀在相纸相应的位置上,形成黑色或褐色斑点。
用硫印试验,可显示钢锭、连铸坯中心裂纹、偏析线、低倍结构和夹杂分布等。
酸洗用酸液洗去基体表面锈蚀物和轧皮的过程。
用酸浸或硫印法所显示的组织结构属于宏观结构,是连铸坯和金属材料检验中最为常见的检验技术。
连铸坯的内部结构连铸坯自表面至中心都是由边缘等轴晶区(激冷区)、柱状晶区和中心等轴晶,区三部分组成。
温度梯度较大时,固液两相区(图1)小,有利于柱状晶的生长,而凝固速度较快,则易于生成枝晶间距小的铸造组织,所以连铸坯具有较发达的柱状晶组织,并具有较小的枝晶间距。
(图1)枝晶间距是指相邻同次枝晶间的垂直距离,它是树枝晶组织细化程度的表征。
枝晶间距越小,组织就越细密,分布于其间的元素偏析范围也就越小,故越容易通过热处理而均匀化。
通常采用的有一次枝晶(柱状晶主干)间距d1,和二次分枝间距d2两种。
连铸坯宏观组织的好坏可以用等轴晶所占的比例多少来衡量,轴晶结构致密,加工性能能好。
柱状晶具有明显的方向性,加工性能差,容易导致中心偏析,中心疏松和中心裂纹等缺陷。
连铸坯的凝固结构及其控制

进入结晶器的钢液在结晶器内凝固,形成坯 壳,出结晶器下口的坯壳厚度应足以承受钢液 静压力的作用
第二阶段
第一阶段
带液芯的铸坯进入二次冷却区继续冷却、坯壳 均匀稳定生长。
坯壳加速生长。根据凝固条件计算三个阶段的凝 固系数(mm.min-0.5)分别为20,25,27~30。
第三阶段——凝固末期
√ 连铸坯从边缘到中心组成: 细小等轴晶带 柱状晶带和
中心等轴晶带组成
√ 出结晶器的铸坯,其液相穴很长。进入二次冷却区后,由于冷却的不均匀,致使铸坯在传热快 的局部区域柱状晶优先发展,当两边的柱状晶相连时,或由于等轴晶下落被柱状晶捕捉,就会出 现“搭桥”现象。
这时液相穴的钢水被“凝固桥”隔开,桥下残余钢液因凝固产生的收缩,得不到桥上钢液的补充,形 成疏松和缩孔,并伴随有严重的偏析。
√ 从铸坯纵断面中心来看,这种“搭桥”是有规律的:每隔5~10cm就会出现一个“凝固桥”及 伴随的疏松和缩孔。
从钢的性能角度看,希望得到等轴晶的凝固结构。等轴晶组织致密,强度、塑性、韧性较 高,加工性能良好,成分、结构均匀,无明显的方向异性。而柱状晶的过分发达影响加工性能 和力学性能。柱状晶有如下特点:
1)柱状晶的主干较纯,而枝间偏析严重; 2)由于杂质(S、P夹杂物)的沉积,在柱状晶交界面构成了薄弱面,是裂纹易扩展的部位,加工时 易开裂; 3)柱状晶过分发达时形成穿晶结构,出现中心疏松,降低钢的致密度。
注意
因此除了某些特殊用途的钢如电工钢、汽轮机叶片等为改善导磁性、耐磨 耐蚀性能而要求柱状晶结构外,对于绝大多数钢种都应尽量控制柱状晶的发展, 扩大等轴晶宽度。
加入形核剂
√ 结晶器内加入形核剂,可以增加结晶器晶核核心数量,扩大等轴晶区。常用的形核剂有 Al2O3,ZrO2,TiO2,V2O5,AlN,ZrN等。
连铸工艺设备连铸坯凝固与传热培训ppt课件

21
21
最大的热阻是来自于坯壳与结晶器 壁之间的气隙。
21
结晶器横向气隙的形成:
结晶器传热示意图:
21
2.影响结晶器传热的主要因素⑴结晶器设计参数对传热的影响 A.结晶器锥度的影响
合适的倒锥度,可以减小下部气隙厚 度,改善传热。
结晶器长度以不增加拉漏为原则。通常为700~900mm。对传热影响不大。
角部成了坯 壳最薄弱的部位。
21
结晶器内气隙的形成过程:
21
坯壳急剧收缩是导致结晶器最大热流减少的原因
21
减轻弯月面区坯壳过度收缩、减少凹陷的形成的措施
21
二.结晶器坯壳生长规律结晶器内坯壳的生长规律服从平方根定律:
21
铸坯表面组织的形成:
21
促进结晶器坯壳均匀生长的操作注意事项
21
三.结晶器传热与热阻
2.弯月面的形成
10
钢液与铜壁弯月面的形成:
10
良好稳定的弯月面可确保初生坯壳的表面质量和坯壳的均匀性。带有夹渣的坯壳是薄弱部位,易发生漏钢。
10
10
4.气隙的形成、稳定及角部气隙
已凝固的高温坯壳发生δ→γ的相变,引起坯壳收缩,收缩力牵引坯壳离开铜壁,气 隙开始形成。周期 性的离合2~3次,坯壳达到一定厚度并完 全脱离铜壁,气隙稳定形成。
二冷区铸坯表面热量传递方式:
37
铸坯二冷传热方式:
37
二.影响二冷区传热的因素
54
表面温度与热流的关系:
54
54
54
三.二冷区凝固坯壳的生长
54
54
四.铸坯的液相穴深度
54
§3—4 连铸坯凝固结构
54
连铸坯的凝固及其控制 ppt课件

PPT课件
24
2.5.3.2连铸板坯的形状缺陷及中心内裂
连铸生产的产品包括:圆钢坯、方坯、板坯以及 各种近终形产品(薄带、异型坯等)。采用连铸 坯取代模铸作轧材,从工艺角度来讲,明显提高 了钢材的收得率,因为连铸工艺完全消除了浇注 系统及冒口切损问题,使得成材率提高约 10%~15%。
PPT课件
9
铸件宏观组织分布示意图
PPT课件
10
一、拉速控制
在保证铸坯质量和安全生产的前提下,拉速主要 受铸坯凝固速度的制约。
500 500 315 约5500
Danieli Somitomo VAI 1)
7
鞍钢第三炼钢连轧厂工艺流程
转炉 LF炉 RH炉
中包
结晶器
连铸机
步进梁式 加热炉
粗轧机
保温罩 飞 剪
精轧机组
层流冷却 卷取 机
除
除
鳞
鳞
PPT课件
8
2.5.2 连铸坯的凝固
要获得性能优良的铸件,首先就要在工艺上进行 控制获得高质量的铸件,同样的道理,连铸坯质 量也是科技工作者研究的重要课题。
连续铸造
2.5 连铸坯的凝固
PPT课件
1
2.5.1 连铸 (continuous casting)
连铸,使金属液由中间包经浸入式水口不断地通 过水冷结晶器,凝成硬壳后从结晶器下方出口连 续拉出,经喷水冷却,全部凝固后切成坯料的一 种铸造工艺。
连铸的设备以弧形连铸机钢坯连铸为例,主要有 钢包支承装置、盛钢桶(钢包)、中间罐、中间罐 车、结晶器(一次冷却装置)、结晶器振动装置、 铸坯导向和二次冷却装置、引锭杆、拉坯矫直装 置(拉矫机)、切割设备和铸坯运出装置(见辊道和 横向移送设备)等。
连铸坯初始凝固控制技术的发展

正弦
Vm
非正弦
t A1
A0
16
3.1 结晶器非正弦振动技术
• 保护渣消耗速率与振动模式的关系
17
3.1 结晶器非正弦振动技术
• 非正弦振动与磨擦阻力的关系
• 非正弦振动与振痕深度的关系
18
3 连铸坯初始凝固控制技术及原理
3.2 结晶器水平振动与垂直正弦振动控制技术 • 该控制技术原理图如下图所示,水平振幅在±0.01 mm内。
• 连铸坯的表面缺陷主要有以下几种: 深振痕、表面凹陷、 裂纹、表面夹渣等。
2.1 连铸坯的深振痕 • 连铸坯的振痕有凹陷形振痕、钩形振痕两种类型。
4
2 连铸初始凝固引起的铸坯质量问题
• 连铸坯深振痕的危害:皮下晶粒粗大、表面横裂的根源。
5
凹陷振痕 钩状振痕
2 连铸初始凝固引起的铸坯质量问题
• 钩状振痕的形成机理
拉坯方向
36
4 结论
• 连铸坯的表面质量与结晶器内初始凝固区域钢液的凝固行 为密切相关,减轻初始凝固坯壳的弯曲变形程度、提高铸 坯初始凝固坯壳厚度的均匀性是提高铸坯表面质量的关键。
• 为减轻初始凝固坯壳弯曲变形程度,冶金工作者采用结晶 器宽面铜板水平振动、电磁软接触连铸等技术以降低结晶 器内保护渣通道的压力;为改善铸坯凝固坯壳厚度均匀性, 冶金工作者采气膜软接触、热顶、导热率低的结晶器等技 术实现结晶器的弱冷。
3.5 弱冷结晶器控制技术
3.5 弱冷结晶器控制技术
18.0 3.9
1
2
3
1-弯月面;2-凝固坯壳;3-镍基718合金结晶器
31
3.5 弱冷结晶器控制技术
高品质钢连铸板坯凝固冷却精益控制关键技术
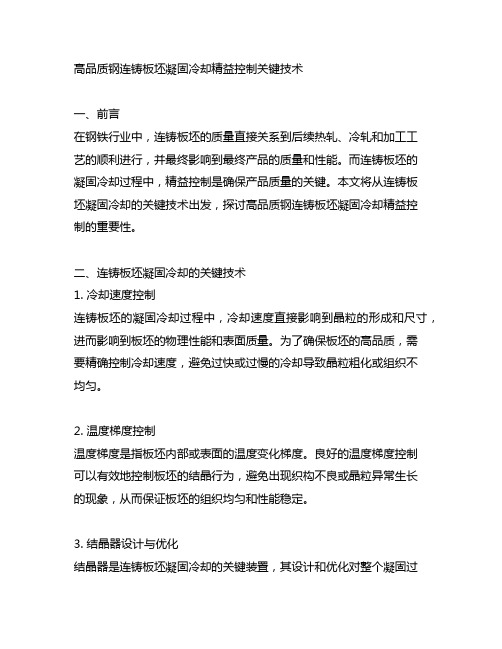
高品质钢连铸板坯凝固冷却精益控制关键技术一、前言在钢铁行业中,连铸板坯的质量直接关系到后续热轧、冷轧和加工工艺的顺利进行,并最终影响到最终产品的质量和性能。
而连铸板坯的凝固冷却过程中,精益控制是确保产品质量的关键。
本文将从连铸板坯凝固冷却的关键技术出发,探讨高品质钢连铸板坯凝固冷却精益控制的重要性。
二、连铸板坯凝固冷却的关键技术1. 冷却速度控制连铸板坯的凝固冷却过程中,冷却速度直接影响到晶粒的形成和尺寸,进而影响到板坯的物理性能和表面质量。
为了确保板坯的高品质,需要精确控制冷却速度,避免过快或过慢的冷却导致晶粒粗化或组织不均匀。
2. 温度梯度控制温度梯度是指板坯内部或表面的温度变化梯度。
良好的温度梯度控制可以有效地控制板坯的结晶行为,避免出现织构不良或晶粒异常生长的现象,从而保证板坯的组织均匀和性能稳定。
3. 结晶器设计与优化结晶器是连铸板坯凝固冷却的关键装置,其设计和优化对整个凝固过程至关重要。
合理的结晶器设计可以有效地控制板坯的凝固行为,确保板坯表面和内部的温度和结晶行为均匀稳定。
4. 液相区控制在板坯凝固过程中,液相区的存在对板坯的质量和性能有着重要影响。
精益控制液相区的形成和移动,可以有效地避免板坯表面和内部出现缺陷和损伤,确保板坯的质量。
5. 温度监测与控制系统温度监测与控制系统是实现连铸板坯凝固冷却精益控制的关键工具。
通过对板坯表面和内部温度的实时监测和控制,可以及时发现和解决凝固过程中的异常情况,确保板坯的质量和形态稳定。
三、高品质钢连铸板坯凝固冷却精益控制的重要性1. 保证产品质量精益控制连铸板坯的凝固冷却过程,可以有效地避免板坯表面和内部出现缺陷和损伤,保证产品的质量稳定。
2. 提高生产效率精益控制连铸板坯的凝固冷却过程,可以减少生产过程中的废品率和质量事故率,提高生产效率。
3. 降低生产成本精益控制连铸板坯的凝固冷却过程,可以减少能源和原材料的浪费,降低生产成本,提高企业的竞争力。
连铸坯的工艺和质量控制

连铸坯的工艺和质量控制碳含量小于或等于0.12%时,碳当量应采用CE(Pcm)公式计算:CE(Pcm)=C+Si/30+Mn/20+Cn/20+Ni/60+Cr/20+Mo/15+V/10+5B当碳含量大于0.12%时,碳当量应采用CE(IIW)公式计算:C E(I I W)=C+M n/6+(C r+M o+V)/5+(N i+C u)/15各国碳当量计算公式文字1、碳(C):钢中含碳量增加,屈服点和抗拉强度升高,但塑性和冲击性降低,当碳量0.23%超过时,钢的焊接性能变坏,因此用于焊接的低合金结构钢,含碳量一般不超过0.20%。
碳量高还会降低钢的耐大气腐蚀能力,在露天料场的高碳钢就易锈蚀;此外,碳能增加钢的冷脆性和时效敏感性。
2、硅(Si):在炼钢过程中加硅作为还原剂和脱氧剂,所以镇静钢含有0.15-0.30%的硅。
如果钢中含硅量超过0.50-0.60%,硅就算合金元素。
硅能显著提高钢的弹性极限,屈服点和抗拉强度,故广泛用于作弹簧钢。
在调质结构钢中加入 1.0-1.2%的硅,强度可提高15-20%。
硅和钼、钨、铬等结合,有提高抗腐蚀性和抗氧化的作用,可制造耐热钢。
含硅1-4%的低碳钢,具有极高的导磁率,用于电器工业做矽钢片。
硅量增加,会降低钢的焊接性能。
3、锰(Mn):在炼钢过程中,锰是良好的脱氧剂和脱硫剂,一般钢中含锰0.30-0.50%。
在碳素钢中加入0.70%以上时就算“锰钢”,较一般钢量的钢不但有足够的韧性,且有较高的强度和硬度,提高钢的淬性,改善钢的热加工性能,如16Mn钢比A3屈服点高40%。
含锰11-14%的钢有极高的耐磨性,用于挖土机铲斗,球磨机衬板等。
锰量增高,减弱钢的抗腐蚀能力,降低焊接性能。
4、磷(P):在一般情况下,磷是钢中有害元素,增加钢的冷脆性,使焊接性能变坏,降低塑性,使冷弯性能变坏。
因此通常要求钢中含磷量小于0.045%,优质钢要求更低些。
5、硫(S):硫在通常情况下也是有害元素。
连铸坯的凝固结构及控制
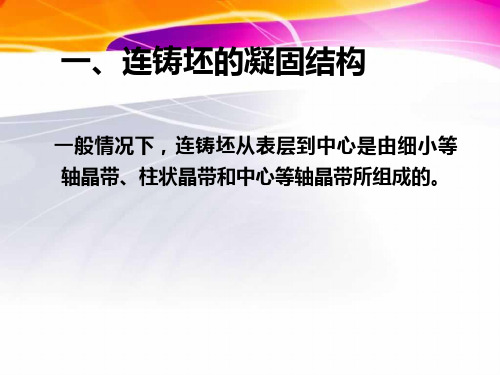
三、铸坯结构的控制
为扩大等轴晶带可采取以下措施:
(1)加速凝固工艺。 (2)喷吹金属粉粉剂。 (3)控制二冷区冷却水量。 (4)加入形核剂。 (5)电磁搅拌技术。
对形核剂要求是: 1)在钢液温度下为固态; 2)在钢液温度下不分解为元素而进入钢中; 3)能稳定地存在于凝固前沿而不上浮; 4)形核剂尽可能与钢液润湿,晶格彼此接近,使形核 剂与钢液间有粘附作用。
二、“小钢锭”结构
柱状晶开始时为均匀生长。但由于二冷区喷水冷却的不均匀 性,将会使冷却快的局部区域的柱状晶优先生长,当某一 局部区域两边相对生长的柱状晶相连接或等轴晶的下落被 柱状晶所捕集时,就会出现“搭”现象,形成“凝固 桥”,将液相穴内的钢液分隔开来。这祥,“桥”下面残 余钢液固收缩将得不到上面钢液的补充,凝固后就会形成 明显的疏松或缩孔,并伴随有严重前中心偏析。
一、连铸坯的凝固结构
一般情况下,连铸坯从表层到中心是由细小等 轴晶带、柱状晶带和中心等轴晶带所组成的。
连铸坯凝固结构示意图 1—中心等轴晶带;2—柱状晶带;
3—细小等轴晶带
(1)细小等轴晶带。表层细小等轴晶带也叫激冷层。它是表层钢液在 结晶器弯月面处冷却速度并在连续向下的运动中形成的。
(2)柱状晶带。激冷层形成过程中的收缩,使坯壳与结晶器壁间产 生了气隙,增加了热阻,降低下传热速度,不再生成新的晶核, 而表现为已有晶核的继续长大。此时,钢液的过热热量和结晶潜 热主要通过凝固层传出,产生了向结晶器壁的定向传热。
浇注温度、冷却条件等对柱状晶生长均有影响。浇注温度高,柱 状晶带就宽;二冷区冷却强度加大,将增加温度梯度,也促进柱 状晶发展;铸坯断面加大,则减小温度梯度,从而减小柱状晶的 宽度。
(3)中心等轴晶带。此时心部传热的单向性已很不明显,并且此时 传热的途径长,传热受到限制,晶粒长大缓慢,故形成晶粒比激 冷层粗大的等轴晶。
第五讲-连铸坯内部质量控制

第六讲连铸坯内部质量的控制北京科技大学课程主要内容1.绪论2.连铸技术的发展3.凝固理论(形核、长大、凝固组织控制)4.钢液的凝固原理(结晶器、二次冷却)5.连铸坯表面质量控制6.连铸坯内部质量控制7.连铸新技术主要内容1 连铸坯中心缺陷概念2 影响连铸坯中心缺陷形成因素3 防止铸坯中心缺陷的对策4 铸坯中心缺陷形成机理5 结语前言从结晶器拉出来带有液芯的坯壳,在连铸机内边传热、边凝固、边运行而形成很长液相穴的铸坯(少则几米多则十几或二十几米),由于受凝固、传热、传质和工艺的限制,沿液相穴路径常常发生钢水补缩不好,在铸坯完全凝固后,沿铸坯轴向(拉坯方向)某些局部区域常常发现疏松、缩孔和偏析,常称为中心缺陷。
根据钢种和产品用途不同,对连铸坯中心缺陷有严格要求,板坯中心缺陷严重会引起中厚板横向性能尤其是冲击韧性不合格,管线钢抵抗,氢脆(HIC)裂纹能力恶化。
对于中高碳大方坯轧制棒材或线材产品常常会因中心缺陷严重使大方坯低倍检验不合格而导致产品合格率降低。
因此减轻铸坯中心缺陷至不使产品产生废品,这是提高连铸坯内部质量的一个重要任务。
1 连铸坯中心缺陷概念1.1 铸坯中心缺陷形貌沿铸坯横向或纵向轴线剖开经硫印或酸浸后,可显示出低倍结构,(图1-1)沿铸坯纵剖面中心轴线可发现:y中心疏松y中心缩孔y中心偏析(宏观偏析,它与疏松缩孔伴生)y点状或V形偏析(半宏观偏析)沿铸坯横剖面,则中心区有点状疏松或缩孔。
图1-1 铸坯低倍形貌1.2 铸坯中心缺陷评价(1)宏观评级零级相当于中心结构致密,5级为中心疏松尺寸大且连续。
在高过热度浇铸时,约80%铸坯相当于1、2、3级,而20%铸坯相当于4、5级。
(3)化学元素分布从铸坯横断面从内弧到外弧隔一定距离钻样,分析C、Si、Mn、S、P元素以表征铸坯表面至中心的成分差异(图1-3)。
图1-3 铸坯横断面成分分布从铸坯纵向轴线剖开沿中心线隔一定距离钻样,分析C、Si、Mn、S、P成分,以表征铸坯中心线区域成分差异(图1-4)图1-4 铸坯中心成分分布表1-1 铸坯偏析比也可用SEM(Scanning Electron Microscope) 来描述铸坯或轧材试样上Mn偏析图谱,以表征微观偏析状况。
连铸坯质量及控制方法

连铸坯质量及控制方法1、连铸坯质量的含义是什么?最终产品质量决定于所供给的铸坯质量。
从广义来说,所谓连铸坯质量是指得到合格产品所允许的铸坯缺陷的严重程度。
它的含义是:——铸坯纯净度(夹杂物数量、形态、分布、气体等)。
——铸坯表面缺陷(裂纹、夹渣、气孔等)。
——铸坯内部缺陷(裂纹、偏析、夹杂等)。
铸坯纯净度主要决定于钢水进入结晶器之前处理过程。
也就是说要把钢水搞“干净”些,必须在钢水进入结晶器之前各工序下功夫,如冶炼及合金化过程控制、选择合适的炉外精炼、中间包冶金、保护浇注等。
铸坯的表面缺陷主要决定于钢水在结晶器的凝固过程。
它是与结晶器坯壳形成、结晶器液面波动、浸入式水口设计、保护渣性能有关的。
必须控制影响表面质量各参数在目标值以内,以生产无缺陷铸坯,这是热送和直接扎制的前提。
铸坯的内部缺陷主要决定于在二次冷却区铸坯冷却过程和铸坯支撑系统。
合理的二次冷却水分布、支承辊的对中、防止铸坯鼓肚等是提高铸坯内部质量的前担。
因此,为了获得良好的铸坯质量,可以根据钢种和产品的不同要求,在连铸的不同阶段如钢包、中间包、结晶器和二次冷却区采用不同的工艺技术,对铸坯质量进行有效控制。
2、提高连铸钢种的纯净度有哪些措施?纯净度是指钢中非金属夹杂物的数量、形态和分布。
要根据钢种和产品质量,把钢中夹杂物降到所要求的水平,应从以下五方面着手:——尽可能降低钢中[O]含量;——防止钢水与空气作用;——减少钢水与耐火材料的相互作用;——减少渣子卷入钢水内;——改善钢水流动性促进钢水中夹杂物上浮。
从工艺操作上,应采取以下措施:(1)无渣出钢:转炉采用挡渣球(或挡渣锥),防止钢渣大量下到钢包。
(2)钢包精炼:根据钢种选择合适的精炼方法,以均匀温度、微调成分、降低氧含量、去除气体夹杂物等。
(3)无氧化浇注:钢水经钢包精炼处理后,钢中总氧含量可由130ppm下降到20ppm以下。
如钢包→中间包注流不保护或保护不良,则中间包钢水中总氧量又上升到60~100ppm范围,恢复到接近炉外精炼前的水平,使炉外精炼的效果前功尽弃。
连铸坯的凝固与传热

6、确保坯壳出结晶器下口有足够厚度及均匀生 长的措施
① 浇注温度不能过高,保持低温浇注; ② 水口与结晶器严格对中; ③ 结晶器冷却水的水质、流速、水量达到要求,均匀冷却; ④ 合理的结晶器锥度; ⑤ 结晶器液面保持稳定; ⑥ 选择性能良好的结晶器保护渣,以形成均匀的保护渣膜等; ⑦ 合适的浇注速度。
连铸机冷却区示意图
2、连铸坯的凝固是沿液相穴在凝固温度区间 将液体转变为固体的加工过程
连铸坯可看成是液相穴很长的钢锭(板坯可达30m),以一定速度 在铸机内运动并凝固,也可看成是在凝固温度区间(TL → TS)把液体转 变为固体的加工过程。
在固—液交界面附近,存在一个凝固脆化区,此处强度、塑性接 近零,为裂纹敏感区,如应变超过临界应变值就会产生裂纹。
液相穴内液体流动对铸坯结构、夹杂分布、溶质元素偏析和坯壳的 生长有重要作用。
4、已凝固坯壳的冷却可看成是经历“形变热处 理”过程
已凝固坯壳在连铸机内运行的过程中,从力的方面看,它承受 热应力和机械力的作用,使坯壳发生不同程度的变形;从冶金方面 看,随温度的下降,坯壳发生δ→γ→α的相变,特别是二冷区,坯 壳温度的反复下降和回升,使铸坯组织发生变化,这就相当于“热 处理”过程。
水冷结 晶器
水冷却区,喷水加速铸坯内部热量的传递,
使铸坯完全凝固; ③三次冷却区 铸坯向周围空气中辐射传热,
喷水冷 却
使铸坯内外温度均匀一致。
凝固壳
调查表明:铸坯在切割之前放出热量约
50%;切割之后还有50%的热量放出,为 利用这部分能量,节约能源,成功开发了
- 1、下载文档前请自行甄别文档内容的完整性,平台不提供额外的编辑、内容补充、找答案等附加服务。
- 2、"仅部分预览"的文档,不可在线预览部分如存在完整性等问题,可反馈申请退款(可完整预览的文档不适用该条件!)。
- 3、如文档侵犯您的权益,请联系客服反馈,我们会尽快为您处理(人工客服工作时间:9:00-18:30)。
分。
结束
连铸凝固进程数值模拟的数学模型
1.连铸过程基本方程
三维直角坐标系下连铸过程的控制方程为
c T T T T T (k ) (k ) (k ) CVc q t x x y y z z z
2 单元传热模型及基本方程的差分化
(i, j, k-1)
2.5.3.4 连铸圆坯的形状缺陷
连铸圆坯用于生产无缝钢管、钢轨、锻造用钢半 成品、特殊钢和滚珠钢。连铸圆坯容易产生纵向 裂纹,纵裂发展的一定程度时还会引起漏钢。连 铸圆坯和板坯的铸坯表面还可能产生星形裂纹。 星形裂纹是由于铜结晶器内无镀层,铜进入钢水 中浸入晶界产生。
2.5.4 改善连铸坯组织的新技术
优化铸造工艺。
开始 几何模型建立,初始 化信息输入 网格划分,单元信息输 入 工艺参数
钢锭凝固温
度场数值模
拟。模拟分 为前处理、 计算体和后 处理三大部
前 处 理 preprocessing
计算体 computation
潜热处理 计算温度场及其它参数
凝固进程动态显示 后 处 理 postprocessing 铸表面的温度分布 铸坯中心的温度分布
2.5.3.1连铸小方坯的脱方和角裂
脱方:小方坯横截面上两个对角线长度不
相等时称脱方。脱方将对铸坯质量产生影 响。
a=b
a<b
a b
a
b
小方坯脱方前后铸坯截面示意图
与脱方同时出现的现象
部位 钝角 热导 出 少 角部 温度 高 出结晶器时 裂纹(角裂) 坯壳厚度 倾向 薄 偏离角纵向凹 陷、内裂,对 角线内裂倾向 大 角部横裂倾向 大 折痕深 度 深
板坯偏离角皮下裂纹的产生与板坯窄面凸出有关。
板坯窄面凸出与偏离角皮下裂纹的关系
偏离角纵裂与结晶器窄面铜板锥度小或在使用过 程中锥度丧失有关(即窄面凸出)。 防止窄面凸出的措施有: (1)增加窄面铜板锥度; (2)将足辊移到结晶器锥度线以内,并将窄面足 辊由3增至4个; (3)窄面采用抛物线型锥度。 还有的可根据所生产钢种对宽面和窄面的冷却强 度进行控制、对液面稳定性进行控制。
根据结晶器的传热特点,建立了小方坯及其结晶器的计算模 型。由对称性,选取结晶器的四分之一进行计算。
(b)结晶器网格剖分及截面
(a)方坯及结晶器模型
小方坯连铸结晶器模型及其网格剖分
温度场数值模拟输出结果
(a) 结晶器出口处横截面温度场分布
(b) 弯月面处横截面温度分布
连铸钢坯结晶器的横剖面温度显示及等温线分布
连续铸造简图
核心设备:结晶器,二冷设备
钢包
中间包
结晶器 二冷段
空冷段
矫直段
一机四流、一机两流 连铸小方坯
连续铸钢的发展
连续铸钢技术经历了20世纪40年代的试验开发, 50年代开始步入工业生产阶段,60年代出现弧形 连铸机,经过70年代的大发展,80年代日趋成熟 和90年代的一场新的变革,直到今天,经历了70 年的发展历程。众多专家学者致力于连铸技术及 连铸坯质量的研究。当前,连续铸钢已向薄板坯 连铸连轧、异形坯连铸和高速连铸等高效节能的 高附加值产品的方向发展。
连续铸造
2.5 连铸坯的凝固
2.5.1 连铸 (continuous casting)
连铸,使金属液由中间包经浸入式水口不断地通 过水冷结晶器,凝成硬壳后从结晶器下方出口连 续拉出,经喷水冷却,全部凝固后切成坯料的一 种铸造工艺。
连铸的设备以弧形连铸机钢坯连铸为例,主要有 钢包支承装置、盛钢桶(钢包)、中间罐、中间罐 车、结晶器(一次冷却装置)、结晶器振动装置、 铸坯导向和二次冷却装置、引锭杆、拉坯矫直装 置(拉矫机)、切割设备和铸坯运出装置(见辊道和 横向移送设备)等。
连续铸造电磁搅拌的形式
M-EMS: Mold Electromagnetic Stirring 结晶器电磁搅拌 S-EMS: Secondary EMS 二冷区电磁搅拌 F-EMS: Final EMS 凝固末端电磁搅拌
电磁铸造铸坯
电磁铸造的优点:
20MnSi小方坯 • 铸坯表面光洁 • 铸坯内部晶粒细化 • 强度和塑性提高3040%。
K r t Cxi ( xi 1 xi )
Ab
K b t Cy j ( y j 1 y j )
Af
K f t Cy j ( y j 1 y j )
Au
K u t Cz k ( z k 1 z k )
Ad
K d t Cz k ( z k 1 z k )
中心内裂的产生与拉坯速度Vc有关:
Δv≤0.10m/min时,危险拉速Vc=0.87m/min Δv ≥0.30m/min时,危险拉速Vc=0.93m/min
要避开危险拉速范围,即应使在矫直点处,未凝钢 水层厚度大于6mm。
此外,矫直辊偏心或矫直辊间隙过大(间隙过大, 铸坯将产生鼓肚)也对中心内裂产生影响。
A f (Ti ,pj 1, k Ti ,pj , k ) Au (Ti ,pj , k 1 Ti ,pj , k ) Ad (Ti ,pj , k 1 Ti ,pj , k )
qt c
式中:
Al
K l t Cxi ( xi 1 xi )
Ar
铸件宏观组织分布示意图
一、拉速控制
在保证铸坯质量和安全生产的前提下,拉速主要 受铸坯凝固速度的制约。 其关系式为:s=K t1/2
式中s为钢凝固层厚度(毫米),s为凝固时间(分) 一定的s值应保证硬壳不破裂和安全生产,K值为 23~32,视钢种、断面、钢水温度和拉速变化而定。 以普通碳钢为例,拉坯速度:板坯0.5~1.8米/分, 大方坯0.6~1.5米/分,小方坯1.5~3.5米/分,CSP 4.5~6米/分。
三、连铸结晶器内的传热与坯壳厚度
连铸过程中,熔融金属放出的总热量(Qsum)从结 晶器边界到冷却水的传输过程非常复杂,在熔融 金属与结晶器边界同时有几种传热方式,保护渣 和气隙形成边界热阻,阻碍熔融金属和结晶器边 界传热。
在稳定生产条件下,结晶器内部,熔融金属放出 的总热量Qsum 可以估算,这部分热量由冷却水带 走。
连铸板坯的形状缺陷是宽面鼓肚和窄面凸出。连 铸板坯的粘结漏钢、宽面纵裂(随板宽增加而增 加)和偏离角纵裂漏钢都与板坯形状缺陷有关。 连铸板坯偏离角纵裂的产生其机理与小方坯使用 单锥度结晶器时产生偏离角纵向凹陷和裂纹的机 理相近,即在弯月面处锥度太小,结晶器出口处 锥度太大有关。
偏离角纵向凹陷的形成机理
铝合金电磁铸造扁锭,断面尺寸520130mm
轻压下示意图
轻压下的作用
(1) 破碎“晶桥” (2) 补偿冷却收缩 (3) 减小“鼓肚”量
2.5.5 数值模拟技术在连铸中的应用
铸件凝固数值模拟:
结合计算机技术和数值计算方法来定量描述铸件的 凝固传热过程,从而揭示金属凝固的真实行为和 规律,为预测铸造应力、微观及宏观偏析、铸件 性能等提供必要的依据和分析计算的基础数据并
到2.5以上就可以满足要求。
目前全球已有包括生产和少数在建项目的薄板坯 连铸连轧生产线统计结果。
工艺 CSP (其中ISP)
生产线 数/条 26
(5)
铸机流 数/条 42
(7) 5 4 3 54
生产能力/ 万t﹒a-1 4200
(765) 500 500 315 约5500
技术供应 厂商 SMSDemag
现代科学技术的发展,特别是航天、航空及核能 等高技术的发展,对材料提出了越来越高的要求。 在材料科学的领域中,控制材料的凝固过程已成 为提高材料性能和开发新兴材料的重要途径之一。
材料电磁加工(EPM) 技术已成为提高材料质量、 节能、改善环境的重要途径;连铸坯凝固末端轻 压下技术的应用也逐渐引起了关注,并在凝固末 端组织控制方面优于电磁搅拌。
普通连铸板坯的厚度为150~300mm,而连铸薄板
坯的厚度已经减薄至50~90mm,双辊薄带连铸铸
出的镁合金薄带厚度可达1.0~3.5mm。为保证板 带钢的性能和表面质量的要求,一般要求板带钢 压缩比4~6就可以满足,对于要求高性能和对表 面缺陷敏感的钢种,要求有更大的压缩比。但实
际表明因快速凝固对细化晶粒的影响,压缩比达
(1)对结晶器钢液面绝热保温;
(2)使钢液面不受空气二次氧化;
(3)吸收钢液中上浮的夹杂物;
(4)润滑运动的铸坯,在结晶器与坯壳之间起着 良好的润滑作用,从而减少拉坯阻力,防止“粘 结”现象的发生。
(5)均匀和调节凝固坯壳向结晶器的传热,使坯 壳均匀生长,形成足够厚度的坯壳,防止裂纹的 产生。
2.5.3 连铸坯的形状缺陷
冷却水
结晶器 壁
气隙 保 坯壳 护渣
Tc Ti To 热流
Th
Tg
Tf
Ts
结晶器边界传热模型
1 热面温度与平均热流密度与距结晶器上口 距离的关系
2 拉速和碳含量对热流密度的影响
3 拉速和碳含量对结晶器出口处坯壳厚度 的影响
4 碳含量(钢种)对漏钢率的影响
5 连铸保护渣的选用
保护渣的冶金作用
X
Y
Z
(j-1, j, k)
(i, i-1, k)
(i, j, k)
(i, i+1, k)
(j+1, j, k) (i, j, k+1)
1 p p Ti ,pjk Ti ,pj , k Al (Ti 1, j , k Ti ,pj , k ) Ar (Ti 1, j , k Ti ,pj , k ) Ab (Ti ,pj 1, k Ti ,pj , k ) ,