连铸坯在凝固过程中形成裂纹的原因[终稿]
连铸板坯表面纵裂原因探究

连铸板坯表面纵裂原因探究
连铸板坯作为容易变形的金属坯料,在冷却变形过程中容易出现多种裂纹,其中纵裂最为常见。
针对连铸板坯表面纵裂现象,本文就其产生原因进行探究。
首先,表面纵裂常常是由于板坯的表面微细的成形不均匀导致的。
在铸造过程中,由于复杂的铸件形状,往往在表面上凸起或凹陷的微细尺寸会有些出入,并且会加快凝固层的冷却变形,从而使表面裂纹形成。
其次,表面纵裂也可能是由于浇口不合理而出现的。
正常的浇口应该是圆形的,但如果浇口不够均匀,表面纵裂就会产生。
此外,如果浇口太大,会导致板坯储存在浇口中的金属过多,使其凝固太快,从而导致表面纵裂的形成。
再者,当铸件温度过高的时候,表面纵裂也是可能出现的。
当板坯的温度过高时,凝固层会变得很薄,而且会加快凝固变形的过程,从而会出现表面纵裂现象。
最后,表面纵裂也可能是由于模具材料质量不佳导致的。
连铸板坯在流动过程中,会受到模具的影响,因此,模具质量的不佳会直接导致表面纵裂的发生。
总之,连铸板坯表面纵裂的原因多种多样,主要包括表面微细成形不均匀、浇口不合理、板坯温度过高、模具质量不佳等。
因此,为了防止表面纵裂的发生,可以采取一系列技术措施,以确保生产高质量的产品。
连铸坯表面纵裂产生原因及控制对策

连铸坯表面纵裂产生原因及控制对策话说有一天,咱们钢铁厂的李师傅,正对着一块连铸坯发愁呢。
这块坯子表面竟然出现了一道长长的纵裂,就像孩子脸上的泪痕,让人看了心里直痒痒。
李师傅挠了挠头,自言自语道:“这究竟是哪路神仙下凡,给咱这坯子‘美容’了?”玩笑归玩笑,但问题还是要解决的,毕竟这纵裂可不是什么好事,得找出原因,对症下药。
于是,咱们今天就来聊聊这连铸坯表面纵裂的产生原因及控制对策。
一、初探纵裂之谜1.1 原料篇:杂质作祟你想啊,这钢铁原料里要是混进了什么不该有的东西,比如氧化物、硫化物这些调皮的小家伙,它们在高温熔炼时就会闹别扭,导致铸坯在凝固过程中受力不均,从而出现纵裂。
这就好比咱们做菜,食材不新鲜,做出的菜能好吃吗?同理,原料不纯,铸坯的质量自然也好不到哪里去。
1.2 工艺篇:火候难控连铸过程中,温度、速度、冷却强度这些参数可都是关键。
温度高了,坯子容易“上火”,低了又容易“感冒”;速度快了,坯子跟不上节奏,慢了又拖拖拉拉。
这冷却强度也是,太强了坯子受不了,太弱了又不够劲道。
总之,这些参数要是没掌握好,铸坯就容易“闹脾气”,纵裂也就找上门来了。
1.3 设备篇:老胳膊老腿设备要是老化了,比如结晶器磨损严重、润滑不良,那坯子在通过的时候可就遭殃了。
这就像咱们走路,地面不平整,脚就容易扭伤。
同理,设备不“给力”,铸坯也容易受伤,纵裂也就趁机而入。
二、纵裂应对策略2.1 原料净化要想从源头上解决纵裂问题,原料的净化可是必不可少的。
咱们得把原料里的那些“害群之马”给揪出来,比如加强原料的筛选、清洗工作,确保它们干干净净地进入熔炼炉。
这样一来,铸坯的质量就能大大提升啦!2.2 工艺优化工艺参数的调整可是个技术活。
咱们得根据铸坯的实际情况,对温度、速度、冷却强度这些参数进行精细化的控制。
就像厨师炒菜一样,火候得恰到好处,才能炒出美味佳肴。
同理,工艺参数要是调整得当,铸坯的质量自然也能更上一层楼。
2.3 设备升级设备可是咱们生产线的“硬实力”。
板坯内部裂纹的原因与措施

板坯内部裂纹的原因与措施文/胡秋芳 罗莉萍裂纹是连铸板坯常见的质量缺陷,它的存在是发生钢板开裂、断板等质量问题的重要原因。
随着市场经济的深入发展和竞争机制的不断深化,产品质量就显得特别重要。
要想使企业在激烈的市场竞争中常胜不衰,就必须保证产品的质量。
目前二钢厂连铸板坯的质量问题比较突出,其表现为裂纹比较多,即有表面裂纹、表面横裂和表面纵裂,也有内部裂纹。
本文结合二钢厂连铸板坯机的生产实践,从铸机设备与工艺两方面对板坯内部裂纹的形成原因、影响因素等进行的探讨并提出改造措施。
一、板坯连铸机连铸机的机型可分为:立式连铸机、立弯式连铸机、多点弯曲连铸机、全弧形连铸机、多半径弧型(椭圆型)连铸机、水平式连铸机等。
二钢厂板坯连铸机是选用立弯式的连铸机、一机两流单点矫直、火焰切割式、浇注断面为250mm×1800mm,拉坯速度为0.9~1.1m/min,振幅5~8mm,塞棒拉流、浸入式保护浇注,其浇注的钢种为Q215、Q235、Q345。
该铸机设计能力为200万吨/年。
二、连铸坯内部裂纹的类型及形成原因连铸坯内部裂纹的主要类型为:三角区裂纹、中间裂纹、中心裂纹。
连铸坯内部裂纹的形成是铸坯凝固过程中各种外部压力和钢水凝固产生的内部压力作用在液相穴的结果。
液相穴深度是指结晶器内钢水液面连铸坯完全凝固处的长度。
连铸坯的液相穴深度随拉坯的速度而改变,若拉坯的速度快,连铸坯的液相穴深度会延长;反之,连铸坯的液相穴深度会短些。
前沿的凝固交界面及附近区域上当综合压力超过该钢种的固相线温度附近的临界强度时,固液界面处的坯壳已不能抵抗压力作用而产生开裂。
由于钢液已形成半凝固态和固态,使钢水无法外流,因此裂纹得以在坯壳内形成。
从本质上说,内部裂纹的产生是各种压力综合作用的结果,也是该种钢高温力学性能不能抵抗综合力的结果,作用于铸坯壳使之发生变形。
导致产生裂纹的作用力有以下几种:鼓肚力;弯曲或矫直压力;热压力;坯壳与结晶器的摩擦力;意外机械作用力裂纹的出现要经历形成和扩展两个过程。
铸坯角横裂原因分析最终版(2)(1)
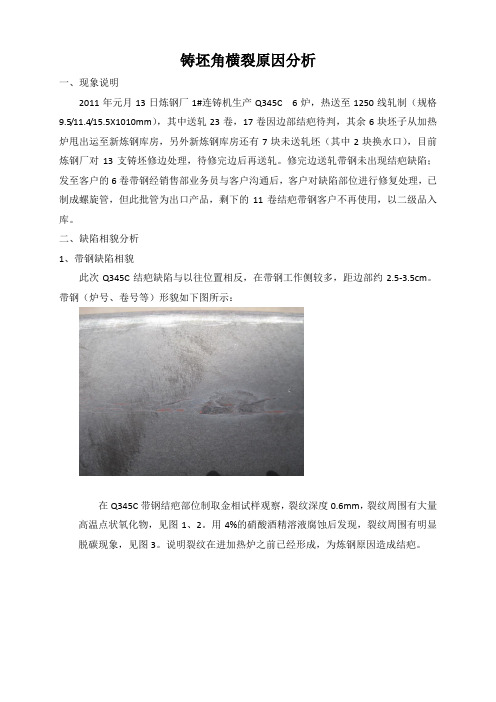
铸坯角横裂原因分析一、现象说明2011年元月13日炼钢厂1#连铸机生产Q345C 6炉,热送至1250线轧制(规格9.5/11.4/15.5X1010mm),其中送轧23卷,17卷因边部结疤待判,其余6块坯子从加热炉甩出运至新炼钢库房,另外新炼钢库房还有7块未送轧坯(其中2块换水口),目前炼钢厂对13支铸坯修边处理,待修完边后再送轧。
修完边送轧带钢未出现结疤缺陷;发至客户的6卷带钢经销售部业务员与客户沟通后,客户对缺陷部位进行修复处理,已制成螺旋管,但此批管为出口产品,剩下的11卷结疤带钢客户不再使用,以二级品入库。
二、缺陷相貌分析1、带钢缺陷相貌此次Q345C结疤缺陷与以往位置相反,在带钢工作侧较多,距边部约2.5-3.5cm。
带钢(炉号、卷号等)形貌如下图所示:在Q345C带钢结疤部位制取金相试样观察,裂纹深度0.6mm,裂纹周围有大量高温点状氧化物,见图1、2。
用4%的硝酸酒精溶液腐蚀后发现,裂纹周围有明显脱碳现象,见图3。
说明裂纹在进加热炉之前已经形成,为炼钢原因造成结疤。
图1裂纹周围有大量的点状氧化物100X 图2 裂纹周围的点状氧化物1000X图3 裂纹周围有明显脱碳现象100X2、钢坯缺陷形貌对炼钢厂库存的Q345C钢坯详细检查,发现在钢坯内弧角部存在明显裂纹缺陷。
缺陷位置如下示意图所示。
为进一步查明钢坯角横裂纹的产生原因,制取钢坯角横裂纹部位的试样进行检验。
Q345C连铸工艺如下:2.1、低倍酸浸检验用1:1的工业盐酸加热后进行低倍酸浸检验,在窄面内弧边部有星状裂纹和网状裂纹,并且在窄面振痕处裂纹扩展,裂纹长度3~10mm;在宽面内弧边部裂纹与窄面振痕处裂纹相连,长度3~9mm,截面裂纹深度2~3mm。
窄面边部裂纹窄面边部振痕处裂纹宽面边部裂纹截面裂纹2.2 高倍金相检验制取角横裂部位的金相试样,观察发现,裂纹周围有大量点状氧化物,部分颗粒较大,裂纹穿晶或沿晶界扩展;表层氧化铁结构疏松,颜色深浅不一,表明成分上有差异,并且氧化铁内层也分布有大量的点状氧化物。
连铸板坯表面裂纹的成因

图1 中间罐温度与拉 速的对应图
图1 中间罐温度与拉 速的对应图
2)浸入式水口对中 2)浸入式水口对中
浸入式水口与结晶器不对中极易产生偏 流冲刷坯壳,还能引起结晶器液面翻腾, 保护渣不能形成均匀渣膜,导致传热不 良,坯壳厚薄不均而引起裂纹的发生。 投产初期采用人工下装式浸人式水口, 水口不易准确对中,尤其热换水口时, 更难保证对中,这些都可能导致裂纹的 发生。
5)保护渣的行为 5)保护渣的行为
现场所用保护渣的流动性不好。研 究表明,保护渣熔融不充分,粘度 过大,使流人坯壳和结晶器间隙的 渣膜不均匀,会导致摩擦力的变化 及坯壳冷却不均匀,造成坯壳厚薄 不均,引起裂纹的发生。
4 采取的措施
1)提高出钢温度的命中率,确保过热度为15℃±5t,重 新制定中间罐温度与拉速的对应表,见表1。 2)拉速升降时必须按每分钟≤0.15m/min的幅度操作,以 保证结晶器液面波动较小。 3)引进浸入式水口快速更换装置,换水口过程仅需3s, 更换水口迅速、准确、平稳及对中良好。 4)改进保护渣,要求保护渣粘度合适,熔化均匀及形成 的渣膜厚度适中。为此,保护渣的熔点由1145℃调为 1 0 7 0 ℃ , 粘 度 由 0 . 2 3 8 Pa·s(1300℃) 调 为 0 . 1 4 2 Pa·s(1300℃)。 5)对Q235等裂纹敏感性强的钢种,结晶器宽面水量由 200m3/h调为185m3/h。
连铸板坯表面裂纹的成因 及防止措施
1 2 3 4 5 前言 铸机状况 铸坯表面裂纹的影响因素 采取的措施 效果
1 前言
连铸板坯裂纹是影响连铸机产量 和铸坯质量的重要缺陷,轻者要 进行精整,重者会导致拉漏或废 品,影响铸机生产率和铸坯质量。 本文就生产中出现的铸坯表面裂 纹进行分析,并提出减少裂纹的 措施。
连铸板坯角部横向裂纹的形成原因与分析
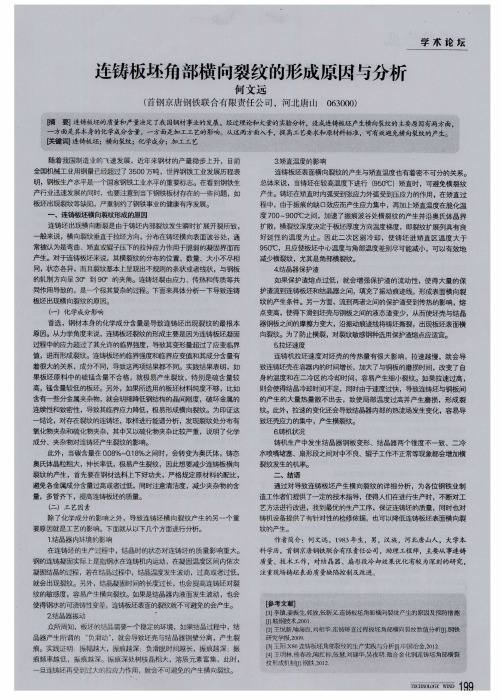
、
连铸板 坯横向裂纹形成的原因
连铸坯 出现横向断裂是由于铸坯内部裂纹发生瞬时扩展开裂所致 ,
—
般来说 , 横向裂纹垂直于拉坯方向,分布在铸坯横向表面波谷 处, 通 常被认为是弯 曲、矫直或辊子压下的拉伸应力作用于脆弱的凝 固界面而 产生。对于连铸板坯来说,其横裂纹的分布的位置 、数量、大小不尽相
9 5 a ℃,且应使板坯中心温度与角部温度差别尽可能减小 ,可以有t 8 8 "  ̄
减 少横裂纹 ,尤其是角部横裂纹 。
4结晶器保护渣
同,状态各异 ,而且裂纹基本上呈现出不规则的条状或者线状 ,与钢板
的轧制 方向呈 3 到9 0 '的夹角。连铸坯裂 由应力、传热和传质等共
如果保护渣熔点过低 ,就会增强保护渣的流动 性,使得大量 的保 护渣流到连铸板坯和结晶器之间,填充了振动痕迹线 , 形成表面横 向裂 纹 的产生条件。另一方面 ,流到两者之间的保护渣受到传热的影响,熔 点 变高,使得下滑到坯 壳与铜板之间的液态渣变少,从而使坯壳与结晶
学 术 论 坛
连铸板坯角部横 向裂纹的形成原因与分析
何文 远
( 首钢 京唐 钢铁 联合 有 限责任公 司 ,河北 唐 l 【 1 0 6 3 0 0 0 )
c } i 笥 蜀 连铸板坯的质量和产量决定了 我国钢材事业的发展,经过理论和大量的实验分析, 造成连铸板坯产生横向裂纹的主要原因有两方面. 方面 是 其本身的化学成分含量,一方面是加 工工艺的影响。从这两方面入手, 提 高工艺要 求和原材料标准 ,可有效避免横向裂纹的产生。 饫镧嗣 ] 连铸板坯;横向裂纹; 化学成分; 加工工艺
连铸方坯中心裂纹成因分析及控制方法
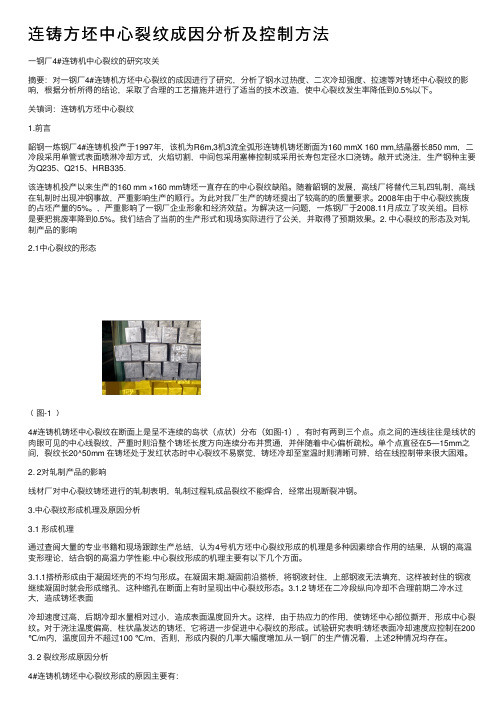
连铸⽅坯中⼼裂纹成因分析及控制⽅法⼀钢⼚4#连铸机中⼼裂纹的研究攻关摘要:对⼀钢⼚4#连铸机⽅坯中⼼裂纹的成因进⾏了研究,分析了钢⽔过热度、⼆次冷却强度、拉速等对铸坯中⼼裂纹的影响,根据分析所得的结论,采取了合理的⼯艺措施并进⾏了适当的技术改造,使中⼼裂纹发⽣率降低到0.5%以下。
关镇词:连铸机⽅坯中⼼裂纹1.前⾔韶钢⼀炼钢⼚4#连铸机投产于1997年,该机为R6m,3机3流全弧形连铸机铸坯断⾯为160 mmX 160 mm,结晶器长850 mm,⼆冷段采⽤单管式表⾯喷淋冷却⽅式,⽕焰切割,中间包采⽤塞棒控制或采⽤长寿包定径⽔⼝浇铸。
敞开式浇注,⽣产钢种主要为Q235、Q215、HRB335.该连铸机投产以来⽣产的160 mm ×160 mm铸坯⼀直存在的中⼼裂纹缺陷。
随着韶钢的发展,⾼线⼚将替代三轧四轧制,⾼线在轧制时出现冲钢事故,严重影响⽣产的顺⾏。
为此对我⼚⽣产的铸坯提出了较⾼的的质量要求。
2008年由于中⼼裂纹挑废的占坯产量的5%。
,严重影响了⼀钢⼚企业形象和经济效益。
为解决这⼀问题,⼀炼钢⼚于2008.11⽉成⽴了攻关组。
⽬标是要把挑废率降到0.5%。
我们结合了当前的⽣产形式和现场实际进⾏了公关,并取得了预期效果。
2. 中⼼裂纹的形态及对轧制产品的影响2.1中⼼裂纹的形态﹙图-1 ﹚4#连铸机铸坯中⼼裂纹在断⾯上是呈不连续的岛状(点状)分布(如图-1),有时有两到三个点。
点之间的连线往往是线状的⾁眼可见的中⼼线裂纹,严重时则沿整个铸坯长度⽅向连续分布并贯通,并伴随着中⼼偏析疏松。
单个点直径在5—15mm之间,裂纹长20^50mm 在铸坯处于发红状态时中⼼裂纹不易察觉,铸坯冷却⾄室温时则清晰可辨,给在线控制带来很⼤困难。
2. 2对轧制产品的影响线材⼚对中⼼裂纹铸坯进⾏的轧制表明,轧制过程轧成品裂纹不能焊合,经常出现断裂冲钢。
3.中⼼裂纹形成机理及原因分析3.1 形成机理通过查阅⼤量的专业书籍和现场跟踪⽣产总结,认为4号机⽅坯中⼼裂纹形成的机理是多种因素综合作⽤的结果,从钢的⾼温变形理论,结合钢的⾼温⼒学性能.中⼼裂纹形成的机理主要有以下⼏个⽅⾯。
连铸小方坯角部纵裂纹及角部纵裂漏钢的成因及防止措施

连铸小方坯角部纵裂纹及角部纵裂漏钢的成因及防止措
施
1.连铸小方坯角部纵裂纹的成因:
①角部罩覆不均匀或罩覆层太厚,使液体钢在连铸过程中受到热应力引起膨胀产生断裂;
②炉内温度分布不均匀;
③小方坯结构极差,钢水温度偏低,造成渣覆盖不均匀;
④小方坯温度过低,且温差大;
⑤冶炼操作不当,料柱受冷凝后,小方坯容易出现纵裂现象;
2.防止措施:
①加强实验室指导料柱的冶炼操作,使小方坯温度和温度分布均匀;
②合理控制罩覆层厚度,使其尽量均匀;
③及时缓和小方坯温度过快下降,尤其是角部;
④检验小方坯投料前后温度梯度,避免温度太大;
⑤增加添加剂,提高液体钢的流动性和结晶性;
⑥检查炉内温度分布是否均匀,及时调整炉内温度控制;
⑦加强铸坯结构的矫正,提高钢水温度及其均匀性,消除结晶缺陷。
连铸坯内部缺陷

连铸坯内部缺陷连铸坯的内部质量,主要取决与其中心致密度。
而影响连铸坯中心致密度的缺陷是各种内部裂纹、中心偏析和中心疏松,以及铸坯内部的宏观非金属夹杂物。
连铸坯的内裂、中心偏析和疏松这些内部缺陷的产生,在很大程度上和铸坯的二次冷却以及自二冷区至拉矫机的设备状态有关。
1)内部裂纹形成的原因各种应力(包括热应力、机械应力等)作用在脆弱的凝固界面上产生的裂纹成为内部裂纹。
通常认为内裂纹是在凝固的前沿发生的,大都伴有偏析的存在,因而也把内裂纹称为偏析裂纹。
还有一种说法是内裂纹是在凝固前沿发生的,其先端和凝固界面相连接,所以内裂纹也可以称为凝固界面裂纹。
除了较大的裂纹,一般内裂纹可在轧制中焊合。
连铸坯的内部裂纹是指从铸坯表面一下直至铸坯中心的各种裂纹,其中包有中间裂纹、对角线裂纹、矫直弯曲裂纹、中心裂纹、角部裂纹。
无论内裂文的类型如何,其形成过程大都经过三个阶段:1拉伸力作用到凝固界面;2造成柱状晶的晶界见开裂;3偏析元素富集的钢液填充到开裂的空隙中。
内裂发生的一般原因,是在冷却、弯曲和矫直过程中,铸坯的内部变形率超过该刚中允许的变形率。
通常在压缩比足够大的情况下,且钢的纯净度较高时,内裂纹可以在轧制中焊合,对一般用途的钢不会带来危害;但是在压缩比小,钢水纯净度较低,或者对铸坯心部质量有严格要求的铸坯,内裂就会使轧制材性能变坏并降低成材率。
2)中心裂纹铸坯中心裂纹在轧制中不能焊合,在钢板的断面上会出现严重的分层缺陷,在钢卷或薄板的表面呈中间波浪形缺陷,在轧制中还会发生断带事故,给成品材的轧制和使用带来影响A裂纹的成因分析铸坯裂纹的形成时传热、传质和应力相互作用的结果。
带液芯的高温铸坯在铸机内运行过程中,各种力的作用是产生裂纹的外因,而钢对裂纹的敏感性是产生裂纹的内因。
铸坯是否产生裂纹决定于钢高温力学性能、凝固冶金行为和铸机运行状态,板坯中心裂纹是由于凝固末端铸坯鼓肚或中心偏析、中心凝固收缩产生的。
1控制铸机的运行状态刚的高温力学性能与铸坯裂纹有直接关系,铸坯凝固过程固、液及诶按承受的应力(如热应力、鼓肚力、矫直力等)和由此产生的塑性变形超过允许的高温强度和临界应变值,则形成树枝晶间裂纹,柱状晶越发达,越有利于裂纹的扩展。
连铸坯表面纵裂纹产生原因及控制措施

左 右 1 00 mm
。
2 3 1 .
.
宽 大 纵 裂 纹 宽 度 深 度 :
丨 0 - 20m m ,
2 0 - 3 0m m ,
长达几米 严重时会贯穿 板坯而报废
,
。
22 .
表 面 纵 裂 纹 原 因 分 析
2 2 .
.1
纵 裂 纹 起 源 于 结 晶 器 的 弯 月 面 区 初 生 凝 固
0 2 -
1
1
> 2 1
钢 液 面 波 动 范 围 mm ,
图 4 液 面 波 动 对 裂 纹 指 数 的 影 响
2 .
2. 4
结 晶 器 冷 却 效 果 及 热 流 的 影 响重 要 纵 裂 纹 一 般 均 发 生 在 结 晶 器 内 部 在 结 晶 器
,
,
结 晶 器 冷 却 效 果 对 连 铸 坯 纵 裂 纹 的 影 响 非 常 内 部 先 形 成 微 裂 纹 进 入 二 冷 区 后 发 展 成 明 显 的 裂 ,
,
晶器
流
于 W M 7 1 .
M2
/
宽面 铜板平 均热 流 为
侧 面 平 均 热 流 M W M 4 6 1 .
-
1.
2 /
,
为
<z>
>
右 1
cr >
i . i
a M
議
图 5 结 晶 器 热 流对 裂 纹 指 数 的 对 应 关 系
板 表 面 纵 裂纹 发 生 率 最 小 M W 3 l .
l- 1.
/ m2 ,
坯
。
经 统 计 分 析 侧 边 铜 板 热 流 与 宽 边 铜 板 热 流 之
连铸坯缺陷及对策
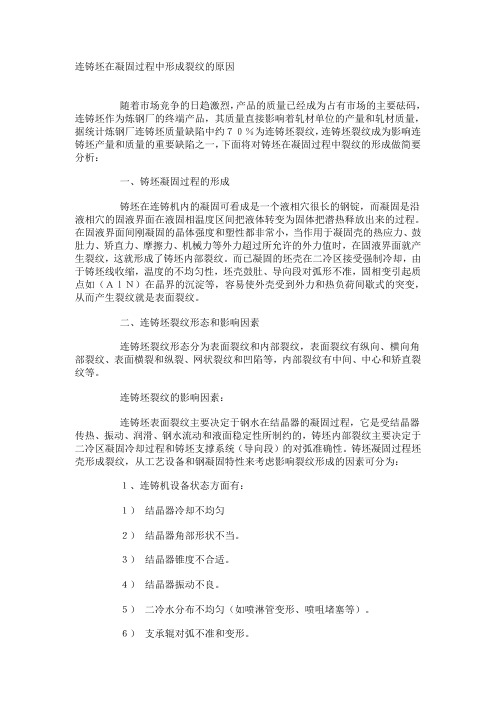
连铸坯在凝固过程中形成裂纹的原因随着市场竞争的日趋激烈,产品的质量已经成为占有市场的主要砝码,连铸坯作为炼钢厂的终端产品,其质量直接影响着轧材单位的产量和轧材质量,据统计炼钢厂连铸坯质量缺陷中约70%为连铸坯裂纹,连铸坯裂纹成为影响连铸坯产量和质量的重要缺陷之一,下面将对铸坯在凝固过程中裂纹的形成做简要分析:一、铸坯凝固过程的形成铸坯在连铸机内的凝固可看成是一个液相穴很长的钢锭,而凝固是沿液相穴的固液界面在液固相温度区间把液体转变为固体把潜热释放出来的过程。
在固液界面间刚凝固的晶体强度和塑性都非常小,当作用于凝固壳的热应力、鼓肚力、矫直力、摩擦力、机械力等外力超过所允许的外力值时,在固液界面就产生裂纹,这就形成了铸坯内部裂纹。
而已凝固的坯壳在二冷区接受强制冷却,由于铸坯线收缩,温度的不均匀性,坯壳鼓肚、导向段对弧形不准,固相变引起质点如(AlN)在晶界的沉淀等,容易使外壳受到外力和热负荷间歇式的突变,从而产生裂纹就是表面裂纹。
二、连铸坯裂纹形态和影响因素连铸坯裂纹形态分为表面裂纹和内部裂纹,表面裂纹有纵向、横向角部裂纹、表面横裂和纵裂、网状裂纹和凹陷等,内部裂纹有中间、中心和矫直裂纹等。
连铸坯裂纹的影响因素:连铸坯表面裂纹主要决定于钢水在结晶器的凝固过程,它是受结晶器传热、振动、润滑、钢水流动和液面稳定性所制约的,铸坯内部裂纹主要决定于二冷区凝固冷却过程和铸坯支撑系统(导向段)的对弧准确性。
铸坯凝固过程坯壳形成裂纹,从工艺设备和钢凝固特性来考虑影响裂纹形成的因素可分为:1、连铸机设备状态方面有:1)结晶器冷却不均匀2)结晶器角部形状不当。
3)结晶器锥度不合适。
4)结晶器振动不良。
5)二冷水分布不均匀(如喷淋管变形、喷咀堵塞等)。
6)支承辊对弧不准和变形。
2、工艺参数控制方面有:1)化学成份控制不良(如C、Mn/S)。
2)钢水过热度高。
3)结晶器液面波动太大。
4)保护渣性能不良。
5)水口扩径。
6)二次冷却水分配不良,铸坯表面温度回升过大。
连铸板坯角部横裂产生的原因及应对措施

铸坯角部横裂产生的原因及应对措施板坯可以在表面上观察到纵向裂纹,在尾部观察到中线裂纹。
要了解板坯中的角裂纹及孔隙,必须用沿板坯边部进行火焰切割处理,切割出50mm宽,2〜3mm深的槽。
在检查板坯的裂纹时,在高强低合金钢(HSLA)、包晶钢、中碳钢中发现了角部横裂,但是在低碳铝镇静钢中却很少发现裂纹。
包晶钢含有Nb,因此,角裂的百分比极高。
虽然在板坯的疏松边发现了角部横裂,但板坯中的大多数裂纹出现在板坯的固定边。
几乎板坯中所有的角部横裂纹与振动痕迹方向一致。
在出厂前,必须对板坯中的角裂纹和针孔进行处理。
处理板坯中出现的裂纹将增加产品成本,降低生产能力,耽误产品出厂日期。
经过火焰切割后的板坯样品送到米塔尔研究实验室进行分析,以便确定其中角部横裂纹的发生原因。
为减少角部横裂纹,米塔尔公司LazaroCardenas(MSLC)的操作人员、维修人员、技术人员组成了一支精干的团队,以降低板坯角部横裂纹的发生。
裂纹起因当铸流表面遭受到热力应变、机械力应变或相变时,若该应变量超过了铸件材料的最大应变值,板坯就会发生横裂。
在下列条件下板坯可能产生裂纹:(1)铸流表面温度下降至低延展区以下,拉伸应变导致铸件产生裂纹。
(2)结晶器上热收缩应变引起板坯内部热断裂,产生裂纹。
(3)结晶器上或结晶器附近所施加的外力引起表面热拉裂。
产品的延展性低是出现裂纹的主要原因。
影响板坯横裂的因素还包括化学作用。
减小温差,降低震动是避免板坯裂隙发生的主要措施。
角部裂分析对板坯切削样本(削痕深度2〜3mm)进行化学成分分析的结果如表1。
在这种钢中发现了严重的角部裂纹,主要原因是该种钢的Nb、V和C含量高,特别是C对包晶钢非常敏感。
理论上讲,Nb(C,N)在1090°C开始析出,当温度下降,析出量快速增长,当温度降低到900C时主要析出物为V(C,N),温度进一步下降到800C时,晶间继续析出。
众所周知,在温度降低过程中,Nb基及V基析出物沿奥氏体晶粒边界析出。
连铸板坯裂纹的可能原因

连铸板坯裂纹的可能原因连铸板坯裂纹是指在连铸过程中,板坯表面或内部出现的裂纹现象。
这种裂纹严重影响了板坯的质量,降低了产品的使用价值,因此了解连铸板坯裂纹的可能原因对于解决该问题具有重要意义。
以下将分析连铸板坯裂纹的可能原因。
连铸板坯裂纹的产生与原材料的质量有关。
原材料中的夹杂物、气孔、硫化物等缺陷会导致板坯的非均匀性和应力集中,从而引发裂纹的产生。
此外,原材料的成分控制也是影响板坯质量的重要因素,过高或过低的含碳量、硫含量等都会增加板坯的脆性,易于产生裂纹。
连铸板坯裂纹的形成与连铸过程中的温度控制有关。
连铸过程中,板坯的冷却速度快,温度梯度大,容易产生应力集中,从而引发裂纹。
在连铸过程中,合理控制板坯的冷却速度和温度梯度,避免过快的冷却或温度梯度过大,能够有效减少裂纹的产生。
第三,连铸板坯裂纹的产生与连铸工艺参数的控制有关。
连铸工艺参数包括浇注速度、结晶器冷却水量、结晶器摇摆频率等。
不合理的工艺参数控制会导致板坯内部应力过大,从而引发裂纹的产生。
例如,过高的浇注速度会使板坯的温度梯度增大,易于产生裂纹;过大的结晶器冷却水量会使结晶器内部的冷却速度过快,也会导致板坯的裂纹。
连铸板坯裂纹的产生还与连铸设备的磨损和维护有关。
设备的磨损会导致连铸过程中的应力不均匀分布,从而引发裂纹。
因此,定期对连铸设备进行检修和维护,保持设备的正常运行状态,对于减少连铸板坯裂纹的产生具有重要作用。
连铸板坯裂纹的产生还与操作人员的技术水平和操作方法有关。
不规范的操作会增加板坯的应力,使其易于产生裂纹。
因此,提高操作人员的技术水平,加强对连铸操作的培训和管理,能够有效减少连铸板坯裂纹的产生。
连铸板坯裂纹的产生与多种因素有关,其中包括原材料质量、连铸过程中的温度控制、连铸工艺参数的控制、设备的磨损和维护以及操作人员的技术水平和操作方法等。
只有全面考虑这些因素,并采取相应的措施,才能有效减少连铸板坯裂纹的产生,提高产品的质量和使用价值。
连铸坯内部裂纹产生的主要原因及解决措施

冶金行为和铸机设备运行状态n 。不同的工厂、 不 同的铸机在不 同的阶段 , 由于条件不 同, 每种因素 对 铸 坯 裂纹 产 生 影 响 的程度 也 不 同。连 铸 过程 是
钢液 的动态 凝 固过程 , 对 连 铸 坯凝 固来 说 , 只要 凝 固壳 一 旦形 成 , 在 固液两 相 区就有 元 素偏 析 , 凝 固 壳 就 承受相 变或 有化合 物 质点 的沉 淀 , 再 加上 外部 应力 的作用 就会产生 裂纹 。 以莱钢 5 0 t 电炉生产 线和新 二 区转 炉炼 钢生产 线 生 产 的铸坯 为 研究 对象 ( 生产 流程 为 : 转 炉/ 电炉 一L F精 炼 一V D真 空 脱 气 _ ÷ 连铸 , 铸 坯 规格 1 8 0 mm×2 2 0 m m、 2 6 0 mm×3 0 0 m m) , 分析 连铸 坯 内裂 纹 的形 成原 因 , 采用 扫描 电镜 和能谱 来分 析裂 纹 的 类型, 并通过 采取相 应措施 , 提 高连铸坯 质量 。
李 广 艳
( 莱芜钢铁集团有限公 司 技术 中心, 山东 莱芜 2 7 1 1 0 4 ) 摘 要: 以莱钢 5 0 t 电炉生产线及新二 区转炉炼钢生产线 生产 的两种 规格的连铸坯作为研究对象 , 分析 了内部裂纹形成 的
原因, 并采用扫描 电镜 和能谱分析 了内部裂纹 的类 型。通过采取恒拉速浇 注、 拉坯 速度与水量合理 匹配 、 实行中间包窄温 度波动控 制、 提 高钢水纯净度等措施 , 连铸坯的质量得到了明显改善 , 低倍 和热顶锻合格率也有 了显著提高 。 关键 词: 连铸坯 ; 内部裂纹 ; 原 因; 措施
中图分类号: T G 1 1 5 . 2 文献标识码 : A 文章编号 : 1 0 0 4 - 4 6 2 0 ( 2 0 1 4 ) 0 2 — 0 0 4 0 — 4 0
连铸板坯裂纹的可能原因

连铸板坯裂纹的可能原因连铸板坯裂纹是指在连铸过程中板坯表面或内部出现的裂纹现象。
连铸板坯是制造板材的重要中间产品,其质量直接关系到最终产品的质量。
因此,了解连铸板坯裂纹的可能原因对于提高板材质量具有重要意义。
连铸板坯裂纹的可能原因主要包括以下几个方面:1. 温度控制不当:温度是连铸过程中最重要的控制参数之一。
如果连铸板坯的冷却速度过快或过慢,都会导致板坯表面或内部的温度梯度过大,从而引起裂纹的产生。
此外,连铸机的冷却水温度和流量的不稳定也会对板坯的温度分布产生影响,进而导致裂纹的形成。
2. 铸造过程中的应力:连铸板坯在冷却过程中由于温度变化而产生应力,如果应力超过了材料的承受能力,就会引起裂纹。
铸造过程中的应力主要包括热应力、冷却应力和收缩应力。
热应力是由于连铸板坯的非均匀冷却引起的,冷却应力是由于冷却水的不均匀冷却引起的,而收缩应力是由于连铸板坯的收缩引起的。
3. 材料质量问题:连铸板坯的质量直接关系到裂纹的产生。
如果原料中存在夹杂物、气孔或其他缺陷,都会在连铸过程中发展为裂纹。
此外,连铸板坯的化学成分和物理性能也会对裂纹的形成起到重要影响。
4. 连铸工艺参数调整不当:连铸过程中的各项工艺参数对于连铸板坯的质量具有重要影响。
如果连铸机的浇注速度、结晶器的冷却强度、结晶器的振动频率等参数调整不当,都会导致连铸板坯出现裂纹。
为了避免连铸板坯裂纹的产生,可以采取以下措施:1. 合理控制连铸过程中的温度,保证板坯的均匀冷却。
2. 优化连铸工艺参数,确保连铸板坯的质量稳定。
3. 加强原料检验,确保原料的质量达标。
4. 定期检查和维护连铸机设备,确保设备的正常运行。
5. 引入先进的控制技术,如自动化控制系统和智能监测设备,提高连铸过程的稳定性和可控性。
连铸板坯裂纹的产生是由多种因素共同作用的结果。
通过合理控制连铸过程中的温度、调整工艺参数、优化原料质量以及加强设备维护,可以有效地避免连铸板坯裂纹的产生,提高板材的质量。
连铸坯横裂产生的原因

连铸坯横裂产生的缘由横裂纹是位于铸坯内弧外表振痕的波谷处,通常是隐蔽看不见的。
经酸洗检查指出,裂纹深度可达 7mm,宽度 0.2mm。
裂纹位于铁素体网状区,而网状区正好是初生奥氏体晶界。
且晶界上有细小质点(如 A1N)的沉淀。
尤其是 C—Mn—Nb(V)钢,对裂纹敏感性更强。
横裂产生的缘由:1)振痕太深是横裂纹的发源地。
2)钢中 A1、Nb 含量增加,促使质点(A1N)在晶界沉淀,诱发横裂纹。
3)铸坯在脆性温度 900~700~C 矫直。
4)二次冷却太强。
防止横裂发生的措施:结晶器承受高频率(200~400 次/分)小振辐(2~4mm)是削减振痕深度的有效办法。
2)二次冷却区承受平稳的弱冷却,使矫直时铸坯外表温度大于900℃。
3)结晶器液面稳定,承受良好润滑性能、粘度较低的保护渣。
4)用火焰清理外表裂纹。
1.连铸坯外表纵裂产生的缘由及其防止方法有哪些?连铸坯外表纵裂纹,会影响轧制产品质量。
如长300mm、深2.5mm 的纵裂纹在轧制板材上留下 1125mm 分层缺陷。
纵裂纹严峻时会造成拉漏和废品。
争论指出:纵裂纹发源于结晶器弯月面初生坯壳厚度的不均匀性。
作用于坯壳拉应力超过钢的允许强度,在坯壳薄弱处产生应力集中导致断裂,出结晶器后在二次冷却区扩展。
纵裂产生的缘由可归纳为:1)水口与结晶器不对中而产生偏流冲刷凝固壳。
2)保护渣熔化性能不良、液渣层过厚或过薄导致渣膜厚薄不均,使局部凝固壳过薄。
液渣层<10mm,纵裂纹明显增加。
3)结晶器液面波动。
液面波动>10 ㎜,纵裂发生几率 30%。
4)钢中 S+P 含量。
钢中S>0.02%,P>0.017%,钢的高温强度和塑性明显降低,发生纵裂趋向增大。
5)钢中 C 在0.12~0.17%,发生纵裂倾向增加。
防止纵裂发生的措施是:1)水口与结晶器要对中。
2)结晶器液面波动稳定在±10mm。
3) 适宜的浸入式水口插入深度。
4)适宜的结晶器锥度。
连铸表面裂纹产生的原因和改进的技术措施3

姓名:陈守汪班级:冶094班学号:0990142142012 年5 月14 日连铸表面裂纹产生的原因和改进的技术措施摘要:连铸坯表面裂纹的产生主要取决于: 钢成分对裂纹敏感性、浇铸工艺条件及连铸机设备状况。
带液芯的连铸坯在连铸机内运行过程中受到外力作用是坯壳产生裂纹的外因, 钢的高温力学行为是产生裂纹的内因, 而设备和工艺因素是产生裂纹的条件。
根据所浇钢种, 对连铸机设备的调整应符合钢水凝固收缩规律, 以坯壳不发生变形为原则。
优化工艺参数, 使其处于能够保证连铸坯不产生裂纹或不足以造成废品的允许范围内, 得到合理的铸坯凝固结构。
关键词:铸坯表面纵裂纹、铸坯表面横裂纹主要内容:铸坯裂纹是影响连铸机产量和铸坯质量的主要缺陷。
据统计, 铸坯各类缺陷中有50%为裂纹缺陷。
铸坯出现裂纹, 轻者需进行精整, 重者会导致漏钢和废品, 既影响连铸坯生产率, 又影响产品质量, 增加生产成本。
1 铸坯表面纵裂纹1. 1 板坯表面纵裂纹特征表面纵裂纹可能在板坯宽面中心区域或宽面到棱边的任一位置产生。
综合分析表明, 纵裂纹有以下特征:( 1) 产生纵裂纹的表面常伴有凹陷( depression), 纵裂纹的严重性与表面凹陷相对应。
( 2) 裂纹沿树枝晶干方向扩展。
( 3) 裂纹内发现有硅、钙、铝等元素的夹杂物。
( 4) 在裂纹周围发现有P, S, Mn 的偏析。
( 5) 裂纹边缘出现一定的脱碳层, 说明裂纹是在高温下形成扩展的。
1. 2 表面纵裂纹产生的原因板坯表面纵裂纹在连铸机内产生原因如下:( 1) 板坯横断面低倍检验表明, 纵裂纹起源于激冷层薄弱处( 约2~3mm) 。
( 2) 结晶器的模拟试验表明, 纵裂纹起源于结晶器弯月面区( 几十毫米到150mm) 周边坯壳厚度薄弱处。
这说明纵裂纹起源于结晶器的弯月面区初生凝固壳厚度的不均匀性。
坯壳受下列所述力的作用:( 1) 板坯凝固壳四周温度不均匀而产生的收缩力;( 2) 板坯收缩时由钢水静压力产生的鼓胀力;( 3) 宽度收缩时受侧面约束产生的弯曲应力。
连铸坯表面纵裂产生原因及控制

连铸坯表面纵裂产生的原因及控制一、表面纵裂的危害1、铸坯表面纵裂纹影响轧制产品质量,长300mm、深2.5mm的表面纵裂纹在轧制板材上留下1125mm分层缺陷,纵裂纹严重时会造成拉漏和废品。
2、表面纵裂经修磨后,由于修磨处铸坯厚度小于其他部位,造成轧制时压缩比偏小,板的表面质量和钢质性能不连续,降低板材的等级和钢材的收得率。
二、铸坯表面纵裂纹形成的机理:铸坯的表面纵裂纹产生于结晶器,由于热流分布不均匀,造成坯壳厚度不均匀,在坯壳薄的地方产生应力集中;结晶器壁与坯表面间的摩擦力使坯壳承受较大的负荷,在牵引坯壳向下运动时产生纵向应力,这种应力与从结晶器窄面,到宽面中心线的距离呈直线增加,最大处在板坯的中间,而钢水静压力随着坯壳往下移动呈直线增加,静压力使得坯壳往外鼓,表面裂纹得到进一步扩大。
三、钢坯表面纵裂纹形成的原因及分析:1、保护渣性能的影响,保护渣的黏度过大或过小,都会使渣膜在坯壳与结晶器壁之间,厚薄不均匀,从而影响结晶器的热流分布,导致坯壳凝固不均匀,从而影响结晶器的热流分布,导致坯凝固不均匀,保护渣的融化速率应与其消耗量平衡,熔化速度和熔点均对保护渣渣层的性能有直接关系,熔化过快或过慢均会影响渣膜的厚度及其均匀性,从而影响结晶器的热流分布。
2、结晶器内钢水行为的影响,钢水在结晶器内的流动状态,对结晶器内钢水卷渣、保护渣对夹杂物的捕捉,铸坯裂纹的形成均有一定关系。
当浸入式水口侧孔直径和角度或是水口的浸入深度和对中程度改变时,钢水流场随之改变,钢水对坯壳的冲刷程度也改变,流场不合理也会造成保护渣的铺展性不良,结晶器液面液渣层厚薄不均匀,使流入气隙的渣厚薄不均,造成热流分布不均匀,坯壳凝固不均,而出现表面纵裂纹。
当下水口外径过大时,结晶器内钢水在口区的内外弧处会出现钢水流动“死区”,造成结晶器液面“搭桥”现象,影响保护渣的熔化性,增加了铸坯中部的摩擦应力。
3、钢水过热度的影响,增加钢水过热度,保护渣熔化速度快,液渣层过厚在空隙内流失过快造成结晶器内热流分布不均匀,坯壳凝固不均匀,表面纵裂纹趋势增大。
- 1、下载文档前请自行甄别文档内容的完整性,平台不提供额外的编辑、内容补充、找答案等附加服务。
- 2、"仅部分预览"的文档,不可在线预览部分如存在完整性等问题,可反馈申请退款(可完整预览的文档不适用该条件!)。
- 3、如文档侵犯您的权益,请联系客服反馈,我们会尽快为您处理(人工客服工作时间:9:00-18:30)。
连铸坯在凝固过程中形成裂纹的原因[终稿] 随着市场竞争的日趋激烈,产品的质量已经成为占有市场的主要砝码,连铸坯作为炼钢厂的终端产品,其质量直接影响着轧材单位的产量和轧材质量,据统计炼钢厂连铸坯质量缺陷中约70%为连铸坯裂纹,连铸坯裂纹成为影响连铸坯产量和质量的重要缺陷之一,下面将对铸坯在凝固过程中裂纹的形成做简要分析:
一、铸坯凝固过程的形成
铸坯在连铸机内的凝固可看成是一个液相穴很长的钢锭,而凝固是沿液相穴的固液界面在液固相温度区间把液体转变为固体把潜热释放出来的过程。
在固液界面间刚凝固的晶体强度和塑性都非常小,当作用于凝固壳的热应力、鼓肚力、矫直力、摩擦力、机械力等外力超过所允许的外力值时,在固液界面就产生裂纹,这就形成了铸坯内部裂纹。
而已凝固的坯壳在二冷区接受强制冷却,由于铸坯线收缩,温度的不均匀性,坯壳鼓肚、导向段对弧形不准,固相变引起质点如(,,,)在晶界的沉淀等,容易使外壳受到外力和热负荷间歇式的突变,从而产生裂纹就是表面裂纹。
二、连铸坯裂纹形态和影响因素
连铸坯裂纹形态分为表面裂纹和内部裂纹,表面裂纹有纵向、横向角部裂纹、表面横裂和纵裂、网状裂纹和凹陷等,内部裂纹有中间、中心和矫直裂纹等。
连铸坯裂纹的影响因素:
连铸坯表面裂纹主要决定于钢水在结晶器的凝固过程,它是受结晶器传热、振动、润滑、钢水流动和液面稳定性所制约的,铸坯内部裂纹主要决定于二冷区凝固冷却过程和铸坯支撑系统(导向段)的对弧准确性。
铸坯凝固过程坯壳形成裂纹,从工艺设备和钢凝固特性来考虑影响裂纹形成的因素可分为:
,、连铸机设备状态方面有:
,)结晶器冷却不均匀
,)结晶器角部形状不当。
,)结晶器锥度不合适。
,)结晶器振动不良。
,)二冷水分布不均匀(如喷淋管变形、喷嘴堵塞等)。
,)支承辊对弧不准和变形。
,、工艺参数控制方面有:
,)化学成份控制不良(如C、Mn\S)。
,)钢水过热度高。
,)结晶器液面波动太大。
,)保护渣性能不良。
,)水口扩径。
,)二次冷却水分配不良,铸坯表面温度回升过大。
,)铸坯带液芯矫直。
,)铸坯在脆性区(700~900?)矫直。
,、钢的凝固特性方面有:
,)凝固冷却过程的相变。
,)铸坯凝固结构(柱状晶与等轴晶的比例)。
,)凝固壳高温力学行为。
,)凝固过程的偏析。
三、连铸坯裂纹形成原因分析
表面裂纹起源于结晶器钢水的凝固过程中,在二冷区加速了裂纹的扩展,而内部裂纹起源液相穴固液交界面并伴随有偏析线。
,、纵裂纹
铸坯裂纹起源于结晶器初生坯壳厚度的不均匀性,是一种严重的表面缺陷。
,)钢中,含量对纵裂纹的影响。
,含量在(0.1~0.2%)时,铸坯表面纵裂趋向严重,且铸坯拉速越高,纵裂越严重。
在结晶器弯月面区,钢水凝固面初生坯壳δFeC=0.1%时进入包晶反应区且伴随较大的线收缩,随着温度下降发生δFe,γFe转变发生线收缩,坯壳与结晶器铜壁脱离过早形成主隙,导致热流最小,坯壳最薄,在表面形成凹陷,凹陷部位冷却和凝固比其它部位慢,组织粗化,对裂纹敏感性强,坯壳出结晶器后受到喷水冷却和钢水静压作用,在凹陷的最薄弱处造成应力集中,加上钢处于高温脆性区而引起裂纹,在二冷区继续扩展。
坯壳表面凹陷越深,坯壳厚度不均匀性就越严重,纵裂出现的机率就越大。
,)钢中S+P含量对纵裂的影响。
钢中S+P含量高,铸坯纵裂发生几率增加,钢中P,0.017%、S,0.025%钢的高温强度和塑性降低,容易发生纵裂,保持Mn/S,20可减少纵裂。
,)保护渣性能对纵裂的影响。
在保护渣各项特性中,粘度对产生表面裂纹影响最大,渣粘度较高时,随拉速增加纵裂加重,渣粘度较小时随拉速增加纵裂减少,保护渣粘度越小,纵裂出现的几率就少。
,)其它影响。
水口与结晶器不应,2mm,水口与结晶器不对中钢流对坯壳产生偏流冲刷,造成坯壳不均匀也增加纵裂纹产生的机率。
结晶器液面波动也对纵裂产生影响。
结晶器液面波动,10mm时纵裂发生机率为30%。
,、横裂纹
横裂纹是位于铸坯内弧表面振痕的波谷处,通常隐藏着看不见,裂纹位于铁素体网状区,而网状区正是初生奥氏结晶界,晶界处有AlN和Nb(CN)的沉淀。
一般是C,Mn钢(Mn,1%),C,Mn,Nb(,)钢(Nb0.03%)容易发生横裂纹,钢中Al和N增加,横裂纹敏感性增加,因为Al、N在,体晶界析出,降低了内聚力,增加了γ?,转变的脆性,使900,700?延性大大降低。
含Nb钢在1050?Nb(CN)已开开始晶界沉淀,使脆化温度区加宽,横向裂纹更严重。
钢中P含量低于0.01%横裂纹增加这是因为P优先在晶界富集,降低了沉淀相在晶界上的适度,但是钢中P一般为不大于0.045%因,含量太高会使中心偏析加重弧形连铸机矫直时,铸坯内弧受到张力,外弧受到压力,在矫直过程中,由于振痕的缺口效应产生应力集中,再加上矫直温度,900?加速成了横裂纹形成,因此二冷区采用软冷却,使铸坯进的表面温度大于950?,可以有效减少横裂纹。
横裂纹是与振痕共生的,要减少横裂纹就是要减少小振痕深度,振动频率增加,振痕深度要减少,采用高振频小振幅的结晶器振动机构,可以有效地减少振痕深度,从而减少横裂的发生。
,、铸坯内部裂纹
包括中间裂纹、中心裂纹、矫直裂纹等,裂纹产生的地点是在液面相穴凝固前沿的固液界面,然后再在固相扩展直到能抵抗裂纹为止。
铸坯内部裂纹的形成与铸坯鼓肚、表面回热和铸坯低倍组织等因素有关。
四、连铸坯裂纹形成机理
,、力学观点
,)临界应力:以凝固过程中坯壳所承受的应力来判断裂纹的形成,如应力超过了固相线温度附近临界强度则产生裂纹。
,)临界应变:当固液界面固相的变量超过了临界应变值时产和断裂。
临界应力和应变值决定于凝固结构,也就是δ相与γ相的比例,全时和韧性较高,δ,γ相凝固和γ相凝固韧性和强度较低,对裂纹敏感性增加。
,、冶金学观点
,)晶界脆化理论。
在凝固前沿大约液相分率10%富集溶质的液体薄膜(如硫化物)包围树枝晶,降低了固相线温度附近钢的延性和强度,当受到外力作用时裂纹就沿晶界发生,致使凝固前沿产生裂纹。
,)柱状晶区的切口效应。
凝固前沿的柱状晶生长的根部相当于一个“切口”,产生应力集中而导致裂纹。
,)硫化物脆性。
硫化物日界分布形成所谓?类硫化物,引起晶间脆性,成为裂
纹优先扩展的地方,这是已凝固坯壳产生裂纹的原因。
,)质点沉淀理论:铸坯在冷却过程中AlN、Nb(CN)等质点在,体晶界面沉淀,增
加晶界脆性与裂纹的敏感性,这是铸坯矫直产生裂纹的主要原因。