连铸工艺、设备-连铸坯凝固与传热培训课件
连铸工艺设备连铸坯凝固与传热培训

连铸机故障排除与维修:针对设备出现的故障,及时进行排除和维修,确保生产顺利进行。
连铸机安全操作规程:诊断技术
连铸机设备故障排除流程
连铸机设备故障排除案例分析
连铸机设备故障预防措施
掌握连铸工艺设备的基本原理和操作方法
了解连铸工艺设备的维护和保养知识
连铸坯出结晶器后继续凝固传热
传热过程对连铸坯质量的影响:传热是连铸过程中不可或缺的环节,通过控制传热速率和温度梯度,可以优化连铸坯的凝固组织和晶粒结构,提高其热塑性和韧性。
培训在提高连铸坯质量中的作用:通过培训,使操作人员掌握连铸工艺设备的基本原理和操作技能,了解凝固与传热对连铸坯质量的影响,从而在实际生产中更好地控制工艺参数,提高连铸坯的质量和产量。
培训方式:理论授课、实践操作、案例分析、互动讨论
培训时间与地点:根据实际情况安排时间和地点
培训前后对比:评估学员在培训前后的知识、技能和态度等方面的变化
培训目标达成度:评估学员是否达到了培训目标的要求
学员反馈:收集学员对培训的意见和建议,以便改进后续培训
培训效果跟踪:对学员在工作中应用所学知识和技能的情况进行跟踪和评估
凝固与传热的交互作用对连铸坯质量的影响:凝固和传热过程相互影响,通过调整工艺参数和控制技术,可以优化两者之间的交互作用,进一步提高连铸坯的质量和性能。
凝固过程对连铸坯质量的影响:凝固是连铸坯形成的关键过程,控制好凝固速率、温度场分布和结晶器内液面的稳定性等因素,可以减少裂纹、夹杂物等缺陷的产生,提高连铸坯的致密性和强度。
高效性:连铸机具有高效的生产能力,能够实现连续、快速地生产铸坯。
单击此处输入你的智能图形项正文,文字是您思想的提炼,请尽量言简意赅的阐述观点
灵活性:连铸机可以根据不同的工艺要求和产品规格,进行灵活的调整和改造。
连铸坯凝固与传热

连铸坯凝固与传热连铸过程中铸坯的凝固和传热是连铸设备设计工艺、工艺控制和质量控制的基础,是连铸工作必须掌握的知识。
第1节连铸坯凝固传热的特点钢液在连铸过程中的凝固是一个热量释放和传递的过程,有两个特点。
*在运动(动态)过程中凝固放热*在不同时期散热和传热的方式是不同的一、连铸坯的凝固过程实质上是一个传热的过程。
钢液在转变成固态过程中是分为几个过程。
热量Q包括:1.过热:从浇注温度T C冷却到液相线温度T L放出的热量,C1(T C-T L);2.潜热:从液相线温度T L冷却至固相线温度T S放出的热量以L f表示;3.显热:从固相线温度T S冷却到环境温度To放出的热量C S(Y S-T O);大约有1/3的热量是从液态→固态放出的, 而其余热量是完全凝固后冷却放出的。
连铸过程中钢液凝固可分三个传热冷却区。
*一次冷却区:形成足够厚度的坯壳以保证铸坯出结晶器不漏钢。
*二次冷却区:使铸坯完全凝固。
*三次冷却区:空冷区。
从热平衡来看*钢水结晶器→二冷区→空冷区大约有60%的热量放出来,铸坯才能完全凝固。
这部分热量放出的速度决定了铸机的生产率和铸坯的质量。
*铸坯切割后还有40%热量要放出来,为了利用这部分热量,节约能源,采用热装直轧或连浇连轧工艺。
二钢热凝固过程是液体转变固体的加工过程凝固是发生在铸坯传热过程中的主要现象,铸坯在运动过程中凝固,实质是固——液交界面潜热的释放和传递过程。
1.凝固温度区间(T L-T S)将液体转变成固体加工过程。
这时在固——液交界面有个脆性区,其强度σ=0;收缩率ψ=0。
极易在此区产生裂纹,因此称裂纹敏感区。
固——液界面糊状区。
晶体强度和塑性都非低或称临界强度,如这时受到外力作用。
如热应力,鼓肚应力,矫直力等超上述临界值(ó为1-3N/mm2,由应变到断裂的临界应变为0.2-0.4%)产生裂纹和偏析裂纹。
2.在二冷区受喷水冷却时在这个区已凝固坯壳不断进行线收缩和坯壳温度分布不均匀性及坯壳鼓胀和夹辊不完全对中等原因,是坯壳受到机械和热应力的作用(有时是反复的)也易使铸坯产生裂纹。
连铸理论与工艺板坯连铸资料课件

拉坯速度的不稳定可能导致连铸坯质量波动。为确保拉坯速度稳定,应定期对拉坯设备进行维护,优化 连铸工艺参数,以减小速度波动范围,提高连铸过程势与展 望
连铸技术的前沿研究动态
高效连铸技术
提高连铸机的生产效率,减少能源消耗和环境污染是当前研究的重点。例如, 开发新型结晶器、优化二冷制度等都能有效提高连铸效率。
连铸工艺优点
与传统模铸相比,连铸具有高效、节能、提高金属收得率和产品质量等 优点。
03
连铸工艺类型
根据连铸机的结构和铸坯的运出方式,连铸工艺主要分为立式、立弯式
、弧形和水平连铸等。
连铸过程中的传热与凝固
传热机制
连铸过程中的传热主要包括钢水与结晶器壁之间的对流换热、结 晶器壁的导热以及坯壳与冷却水之间的对流换热。
连铸理论与工艺板坯连铸资料课 件
contents
目录
• 连铸理论基础 • 板坯连铸工艺与技术 • 连铸过程中的问题与解决方案 • 连铸工艺的未来发展趋势与展望
01
连铸理论基础
连铸工艺概述
01 02
连铸工艺定义
连铸工艺是将钢水直接连续倒入特定形状的结晶器中,通过强制冷却使 钢水在结晶器中快速凝固成具有一定形状、尺寸和内部质量的连铸坯的 工艺过程。
在保证产品质量和生产效率的前提下,降 低原料、能源、人力等方面的成本,提高 企业经济效益。
03
连铸过程中的问题与解决方案
连铸坯表面质量缺陷及预防措施
裂纹
连铸坯表面裂纹是常见的缺陷,主要源于铸坯在凝固过程中的内部应力。预防措施包括优 化连铸工艺参数,如浇注温度、拉坯速度,以及改善二冷区冷却制度等。
凝固前沿与坯壳生长
随着热量的传递,钢水在结晶器内逐渐形成凝固前沿,坯壳从凝固 前沿向外生长,直至完全凝固。
(ppt版)连铸工艺技术培训课程

律调查的根底上,根据每个钢种所要经过的工艺路线
(lùxiàn)来确定。
第十六页,共七十页。
㈢ 钢水温度控制要点 1、出钢温度控制: ①提高终点温度命中率
②确保从出钢到二次精炼( jīngliàn)站,钢包钢水温度处于目 标范围之内
2、充分发挥钢包精炼的温度与时间的协调作用
3、控制和减少从钢包到中间包的温度损失
(0.5~1.2℃/min〕;
△T5 钢水从钢包注入中间包的温降。
第十页,共七十页。
• 1温、降△T1 钢水从炼钢炉的出钢口流入钢包(gāngbāo)这个过程的 分析:
• 热量损失形式:钢流辐射热损失、对流热损失、钢包吸热 。
• 影响因素:出钢时间、出钢温度及钢包的使用状况。 • 降低热量损失的措施:
③非金属夹杂不易上浮,影响铸坯内在质量。
第六页,共七十页。
第二节 中间包钢水温度(wēndù)的控制
一、浇铸温度(wēndù)确实定 〔浇铸温度也称目标浇铸温度〕:
T浇=TL+△T 式中: TL——液相线温度
△T ——钢水过热度
第七页,共七十页。
1、液相线温度TL
液相线温度,即开始凝固(nínggù)的温度, 就是确定浇铸温度的根底。推荐一个计算 公式:
第五节 连铸过程检测(jiǎn 与自动 cè) 控制
• 一、连铸过程(guòchéng)自动检测
〔一〕中间(zhōngjiān)包钢液温度测定
1、中间包钢液温度的点测
第二十九页,共七十页。
用快速测温头
及数字显示二次 仪测量(cèliáng)温 度。
第三十页,共七十页。
2、中间(zhōngjiān)包钢液温度的连续测定
第四十三页,共七十页。
连铸坯质量及其控制基础知识培训(PowerPoint 69页)

1.钢水中常见元素及基本概念
• 硼(B):钢中加入微量的硼就可改善钢的致 密性和热轧性能,提高强度。
• 氮(N):一般认为,钢中的氮是有害元素,但是 氮作为钢中合金元素的应用,已日益受到重 视。氮能提高钢的强度,低温韧性和焊接 性,增加时效敏感性。
1.钢水中常见元素及基本概念
• 稀土(Xt):稀土元素是指元素周期表中原子 序数为57-71的15个镧系元素。这些元素都 是金属,但他们的氧化物很象“土”,所 以习惯上称稀土。钢中加入稀土,可以改 变钢中夹杂物的组成、形态、分布和性质, 从而改善了钢的各种性能,如韧性、焊接 性,冷加工性能。在犁铧钢中加入稀土, 可提高耐磨性。
1.钢水中常见元素及基本概念
铌(Nb):铌能细化晶粒和降低钢的过热敏感性及回 火脆性,提高强度,但塑性和韧性有所下降。在普 通低合金钢中加铌,可提高抗大气腐蚀及高温下抗 氢、氮、氨腐蚀能力。铌可改善焊接性能。在奥氏 体不锈钢中加铌,可防止晶间腐蚀现象。
钴(Co):钴是稀有的贵重金属,多用于特殊钢和合 金中,如热强钢和磁性材料。
结晶器与冷却水界面传热可能有三种情况: ①强制对流区:传热良好 ②核态沸腾区:当铜壁温度夜125—130℃时,水开始在表 面蒸发,水中凝聚有气泡。热流值增加很快,铜壁有过热现象。 ③膜态沸腾区:热流越过某一极限值,导致铜壁表面温度突然 升高,这对结晶器是不允许的,会使结品器永久变形
结晶器内凝固示意图
1.钢水中常见元素及基本概念
钒(V):钒是钢的优良脱氧剂。钢中加0.5%的钒可 细化组织晶粒,提高强度和韧性。钒与碳形成的碳 化物,在高温高压下可提高抗氢腐蚀能力。
钨(W):钨熔点高,比重大,是贵生的合金元素。 钨与碳形成碳化钨有很高的硬度和耐磨性。在工具 钢加钨,可显著提高红硬性和热强性,作切削工具 及锻模具用。
连铸技术基本原理-1凝固与传热
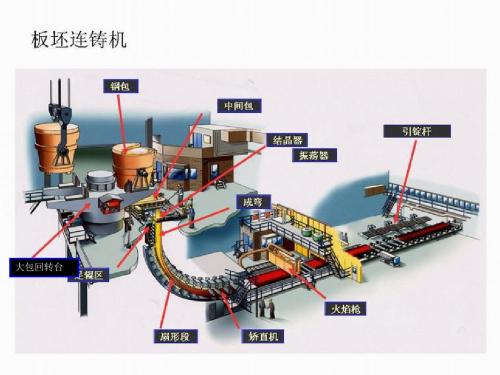
56
二次冷却与铸坯质量
铸坯质量对二冷要求
铸坯表面温度符合钢种的高温延性曲线,矫直 时避开脆性区 控制铸坯表面冷却速率小于200℃/m 控制铸坯温度回升速率小于100℃/m
15
6.1.1 连铸坯凝固与传热特点
坯壳经历“形变热处理”过程
随温度降低,坯壳发生δγα的相变
坯壳发生形变
16
6.1.2 结晶器传热与凝固
结晶器平均散热量
Q WC (2 1 )
式中, Q-结晶器总散热量, KJ/min W-结晶器冷却水量,L/min
C-水的比热, KJ/(Kg.℃)
39
影响结晶器传热的因素
结晶器设计
结晶器长度 结晶器铜板厚度 结晶器材质
结晶器冷却 钢水过热度
40
6.1.3 二冷区传热与凝固
二冷区传热方式
连铸机各区散热比例
结晶器 二冷区 辐射区 16%-20% 23%-28% 50%—60%
二冷区铸坯表面热量传递方式
9
T cT l T l T s T s T o
6.1.1 连铸坯凝固与传热特点
• 钢液在连铸机中凝固: • 是液体钢转化为固体钢的加工过程 • 是热量释放的过程 • 凝固过程中,传输的热量包括: • 钢水过热:进入结晶器的钢水温度冷却到钢 的液相线温度放出的热量 • 凝固潜热:钢水从液相线冷却到固相线所放 出的热量 • 物理显热:凝固以后的高温铸坯冷却至送出 连铸机所放出的热量
55
二次冷却与铸坯质量
某厂Q195高温力学性能曲线
100 90 80 70 60 50 40 30 20 10 0 600 650 700 750 800 850 900 950 1000 1050 1100 1150 1200 1250 1300 1350 1400 1450 1500 温度,℃
连铸工艺设备连铸坯凝固与传热培训ppt课件

21
21
最大的热阻是来自于坯壳与结晶器 壁之间的气隙。
21
结晶器横向气隙的形成:
结晶器传热示意图:
21
2.影响结晶器传热的主要因素⑴结晶器设计参数对传热的影响 A.结晶器锥度的影响
合适的倒锥度,可以减小下部气隙厚 度,改善传热。
结晶器长度以不增加拉漏为原则。通常为700~900mm。对传热影响不大。
角部成了坯 壳最薄弱的部位。
21
结晶器内气隙的形成过程:
21
坯壳急剧收缩是导致结晶器最大热流减少的原因
21
减轻弯月面区坯壳过度收缩、减少凹陷的形成的措施
21
二.结晶器坯壳生长规律结晶器内坯壳的生长规律服从平方根定律:
21
铸坯表面组织的形成:
21
促进结晶器坯壳均匀生长的操作注意事项
21
三.结晶器传热与热阻
2.弯月面的形成
10
钢液与铜壁弯月面的形成:
10
良好稳定的弯月面可确保初生坯壳的表面质量和坯壳的均匀性。带有夹渣的坯壳是薄弱部位,易发生漏钢。
10
10
4.气隙的形成、稳定及角部气隙
已凝固的高温坯壳发生δ→γ的相变,引起坯壳收缩,收缩力牵引坯壳离开铜壁,气 隙开始形成。周期 性的离合2~3次,坯壳达到一定厚度并完 全脱离铜壁,气隙稳定形成。
二冷区铸坯表面热量传递方式:
37
铸坯二冷传热方式:
37
二.影响二冷区传热的因素
54
表面温度与热流的关系:
54
54
54
三.二冷区凝固坯壳的生长
54
54
四.铸坯的液相穴深度
54
§3—4 连铸坯凝固结构
54
连铸坯的凝固及其控制 ppt课件

PPT课件
24
2.5.3.2连铸板坯的形状缺陷及中心内裂
连铸生产的产品包括:圆钢坯、方坯、板坯以及 各种近终形产品(薄带、异型坯等)。采用连铸 坯取代模铸作轧材,从工艺角度来讲,明显提高 了钢材的收得率,因为连铸工艺完全消除了浇注 系统及冒口切损问题,使得成材率提高约 10%~15%。
PPT课件
9
铸件宏观组织分布示意图
PPT课件
10
一、拉速控制
在保证铸坯质量和安全生产的前提下,拉速主要 受铸坯凝固速度的制约。
500 500 315 约5500
Danieli Somitomo VAI 1)
7
鞍钢第三炼钢连轧厂工艺流程
转炉 LF炉 RH炉
中包
结晶器
连铸机
步进梁式 加热炉
粗轧机
保温罩 飞 剪
精轧机组
层流冷却 卷取 机
除
除
鳞
鳞
PPT课件
8
2.5.2 连铸坯的凝固
要获得性能优良的铸件,首先就要在工艺上进行 控制获得高质量的铸件,同样的道理,连铸坯质 量也是科技工作者研究的重要课题。
连续铸造
2.5 连铸坯的凝固
PPT课件
1
2.5.1 连铸 (continuous casting)
连铸,使金属液由中间包经浸入式水口不断地通 过水冷结晶器,凝成硬壳后从结晶器下方出口连 续拉出,经喷水冷却,全部凝固后切成坯料的一 种铸造工艺。
连铸的设备以弧形连铸机钢坯连铸为例,主要有 钢包支承装置、盛钢桶(钢包)、中间罐、中间罐 车、结晶器(一次冷却装置)、结晶器振动装置、 铸坯导向和二次冷却装置、引锭杆、拉坯矫直装 置(拉矫机)、切割设备和铸坯运出装置(见辊道和 横向移送设备)等。
(四)连铸工艺与操作课件.ppt

三、连铸生产工艺
上引锭杆 开浇 启车拉矫 脱引锭杆 切割 钢包更换 中间包更换
精品
停车
1.上引锭杆
油缸驱动→引 锭杆放到中间轨道→ 送入拉矫机引锭杆经 二冷段→入结晶器上 100-150mm→ 反 向 至结晶器下口 150mm 处 → 拉 矫 机 引锭杆夹紧定位→完 成安装操作.
精品
2.开 浇
连铸连轧新技术
第二讲 连铸工艺与操作
精品
主要内容
一、概 述 二、生产模拟 三、生产工艺 四、连铸设备 五、工艺参数
精品
一、概 述 1.连铸的发展概况 2.连铸机的特点 3.连铸机的机型
精品
1.连铸的发展概况
连续铸钢(连铸)是将钢水通过连铸机直接铸成钢坯 ,从而取代模铸和初轧开坯的一种钢铁生产先进 工艺。世界各国都以连铸比(连铸坯产量占钢总产 量比例)的高低来衡量钢铁工业生产结构优化的程 度和技术水平的高低。连铸的好处在于节能和提 高金属收得率。
精品
弧型连铸机:
设备高度明显下降,能够 适应提高拉速和加大断面的要 求
又分为:
直弧型连铸机:
采用直结晶器从结晶器下 保留2m直线段,然后为弧型段, 铸坯由直变弯,最后通过拉矫机 将弧形坯矫直; 优点:夹杂物易上浮,且比立弯式 高度低;
全弧型连铸机:
铸坯的运动轨迹是一条弧 线.结晶器,二冷段全为弧型,拉 矫机、切割机和出坯系统布置 在水平线上.
连轧为代 表,钢厂向紧凑化发展。
精品
2、 21世纪钢铁工业发展趋势
(1) 产品更加纯洁化 (2) 生产工艺更加高效低耗 (3) 生产过程对环境更加友好
精品
•
连铸液体金属是19世纪提出的。最初只能用
于浇铸低熔点的有色金属。1933年现代连铸之父
《连铸工艺与设备》PPT课件
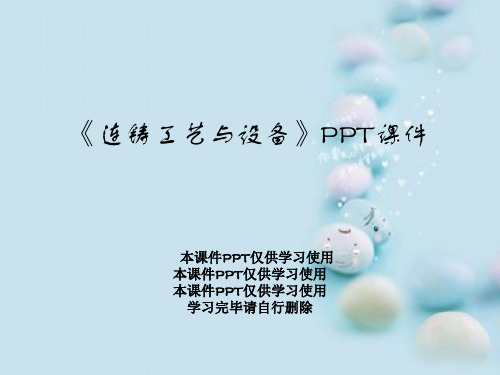
2.2.9 结晶器
➢在连续铸造、真空吸铸、单向结晶等铸造方法中, 使铸件成形并迅速凝固结晶的特种金属铸型。结晶 器是连铸机的核心设备之一,直接关系到连铸坯的 质量。
31
2.2.10 事故保护装置
➢功能 收集和存放渣以及从中间包溢流出来的钢水。保护钢 包回转台,中间包车,结晶器。 ➢ 位置 在浇铸平台上。 ➢结构 溢流箱位置靠近浇铸时的中间包,收集从中间包溢流 槽中流出的钢水。两个渣箱位于中间包停放位置的下 面,收集渣和滴下来的钢液。溜槽放置在钢包事故旋 转的范围中,收集从钢包滑动水口流出的钢水。这三 个设备都由钢板焊接成,内衬耐火材料。
7
连铸工艺和设备
8
2.2.1 钢包回转台(数量1台)
➢钢包回转台:设在连铸机浇铸位置上方用于运载钢 包过跨和支承钢包进行浇铸的设备。由底座、回转臂、 驱动装置、回转支撑、事故驱动控制系统、润滑系统 和锚固件6部分组成(回转部分、固定部分、润滑系统 和电控系统)。 ➢回转部分由回转环、“H”型回转臂、钢包升降装置、 加保温盖装置以及回转驱动装置所组成。由于回转速 度较低~1r/min),速比大,所以回转驱动的大齿轮广 泛采用柱销齿圈,它结构简单、维修方便、造价低廉。
6
2.2 连铸设备组成简介
连续铸钢设备必须适应高温钢水由液态变成液固态,又变成固态的全过程。其间进行着一系列比 较复杂的物理与化学变化。显然,连续铸钢具有连 续性强、工艺难度大和工作条件差等特点。因此生 产工艺对机械设备提出了较高的要求,主要有:设 备应具有抗高温、抗疲劳强度的性能和足够的刚度, 制造和安装精度要高,易于维修和快速更换,要有 充分的冷却和良好的润滑等。
2.2.2 中间包
4) 保护作用。通过中间包液面的覆盖剂,长水口以 及其他保护装置,减少中间包中的钢液受外界的污 染。 5) 清除杂质作用。中间包作为钢液凝固之前所经 过的最后一个耐火材料容器,对钢的质量有着重要 的影响,应该尽可能使钢中非金属夹杂物的颗粒在 处于液体状态时排除掉。 中间包烘烤上升下降,中包车右行,前后,上下
连铸ppt-6-7

图3.1.水结晶冷却曲线 水结晶冷却曲线 1—水理论结晶曲线; 水理论结晶曲线; 2—水实际结晶曲线 水理论结晶曲线 水实际结晶曲线
(2)形核、长大(动力学条件) )形核、长大(动力学条件) 形核过程 A.均质形核,又称自发形核 液态金属中存在很多与固态金属结构相似、体积很小、 液态金属中存在很多与固态金属结构相似、体积很小、近程 有序排列的原子集团,在很大的过冷度(通常 通常∆T=(0.15~ 有序排列的原子集团,在很大的过冷度 通常 ~ 0.20)Tl, 实验室测定纯铁 实验室测定纯铁∆T=0.16Tl=295℃。)条件下,这些 条件下, ℃ 条件下 原子集团变成规则排列,并稳定下来而成为晶核,这一过程 原子集团变成规则排列,并稳定下来而成为晶核, 即为均质形核。 即为均质形核。 B.非均质形核,又称非自发形核,也称异质形核 又称非自发形核, 在金属液相中已存在的固相质点和表面不光滑的器壁均可作 为形成核心的“依托”而发展成初始晶核。 为形成核心的“依托”而发展成初始晶核。非均质形核需要 的过冷度则很小,只要过冷度到20℃就能形成晶核。 的过冷度则很小,只要过冷度到 ℃就能形成晶核。 钢液内部含有熔点不同的杂质, 钢液内部含有熔点不同的杂质,因此钢液的结晶主要为非均 质形核。
4.铸坯凝固冷却过程分为四个阶段: .铸坯凝固冷却过程分为四个阶段: 1)钢液在结晶器中快速冷却,形成薄的坯壳,坯壳与结晶 )钢液在结晶器中快速冷却,形成薄的坯壳, 器壁紧密接触,此时冷却较快,铸坯表面温度明显下降; 器壁紧密接触,此时冷却较快,铸坯表面温度明显下降; 2)随着凝固壳增厚,铸坯收缩,坯壳与结晶器壁间产生气 )随着凝固壳增厚,铸坯收缩, 隙,铸坯冷却速度减慢; 铸坯冷却速度减慢; 3)铸坯从结晶器中拉出,在二冷区受到强烈的喷水冷却, )铸坯从结晶器中拉出,在二冷区受到强烈的喷水冷却, 中心逐渐凝固; 中心逐渐凝固; 4)铸坯在空气中较缓慢的冷却,铸坯中心的热量传导给外 )铸坯在空气中较缓慢的冷却, 层使铸坯外层变热,表面温度回升。 层使铸坯外形成的细小等轴晶的基础上, 在已形成的细小等轴晶的基础上, 一些在散热方向上具有优先成长 方位的晶体将继续长大。 方位的晶体将继续长大。如果在 结晶前沿液相中成分过冷很大, 结晶前沿液相中成分过冷很大, 则晶体呈树枝状发展, 则晶体呈树枝状发展,从而形成 了大体上平行于散热方向的树枝 晶集合组织(柱状晶)。 晶集合组织(柱状晶)。
小方坯连铸机工艺培训课件

精心整理方坯连铸工艺培训课件一、方坯连铸工艺流程简图二、方坯连铸基本参数铸坯断面:150×150mm定尺长度:6~12m(实际最短生产过9.25的,拉速2.1m/min)55Q4.1钢包汇总台4.1钢包回转台功能支承钢包并将满包从受包位旋转到中间罐上方的浇4.2中间罐功能保证连浇;均匀分配钢流到结晶器;促使夹杂物上浮。
结构型式中间罐为梯形带盖式,主要技术参数中间罐最大容量20t钢水液面高度工作液面:800mm主要技术参数烘烤时间180min烘烤温度~1000℃4.5结晶器功能将钢水凝结成型,使浇入其中的钢水快速冷却。
在引锭头拉出结晶器铜管后,凝结的钢水坯壳能承受内部还未凝固的钢水静压力。
结构型式结晶器为套管式,主要由内壁镀铬的三维立体锥度铜管、精密加工成型的整体铜水套、钢结构外壳、上下法兰、卡板及密封件等部分组成。
铜管材质为磷脱氧铜。
主要技术参数铜管长度900mm托架等组成,喷淋管沿弧线纵向布置。
主要技术参数冷却段数3(含喷淋环)喷淋管长度~4.5m喷嘴型号3/8PZ17080QZ5*12PZ8065QZ5*28PZ8047QZ5*284.8导向段功能开浇时引导引锭杆进入结晶器并在浇铸时支承铸坯。
结构型式导向段位于喷淋集管组与拉矫机之间,主要由导向辊、支座、侧导辊、压辊及侧导板等组成。
功能开浇时引锭头堵住结晶器下口,把初步凝固的铸坯拉出结晶器,引入拉矫机。
结构型式主要由自适应型引锭头、刚性杆身、链条及联接件、传动系统、导向轮及安全装置所组成。
铸机开浇前,启动存放装置电动机使引锭杆下降至拉矫机内。
引锭结束后,引锭杆运行至存放位置。
主要技术参数引锭杆外弧半径R8m引锭杆长度(弧度)~87°送引锭杆速度1~4.0m/min4.11切前/输送/出坯辊道坯。
主要技术参数行程~20000mm(工作行程)轨距~13000mm轮距/轮径~2100mm/D300mm4.13翻转冷床功能翻转冷却铸坯,防止铸坯变形结构型式冷床为液压传动、步进翻转式。
连铸连轧原理课件4
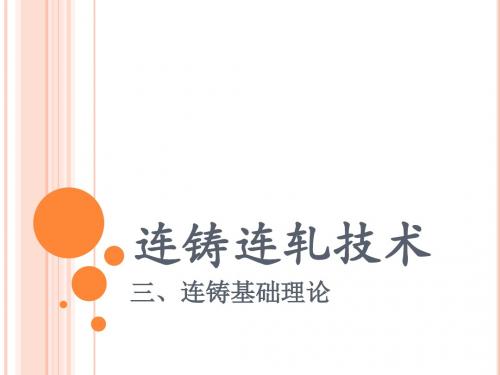
3.3 结晶器传热与凝固
结晶器弯月面渣子行为 在结晶器钢液面上加入保护渣,吸收 钢水热量渣子熔化,在结晶器钢液面 上形成液渣层、烧渣层和粉渣层的三 层结构的渣层。由于液渣与水冷铜壁 接触的温度梯度高。在结晶器周边形 成了固体渣围并黏附在结晶器壁上。
3.3 结晶器传热与凝固
渣圈的作用: 在浇注过程中一旦形成渣圈,由于液 渣和钢水与铜壁润湿程度有差异,在 结晶器四周弯月面渣圈与初生坯壳会 形成一个垂直向下的毛细管通道,由 于结晶器振动和毛细现象的作用,把 弯月面上的液体渣源源不断地吸人坯 壳与铜壁的气隙中形成渣膜,从而起 到润滑作用,结晶器振动的一个周期 内,液渣的渗漏量除了与钢液面液渣 层厚度有关外,还与结晶器周边形成 的渣圈形状有关。如果渣圈不断长大 ,会阻碍液渣的渗漏。渣圈可能破裂 ,特别是浸入式水口壁与铜板之间渣 圈有的可以搭桥,严重时会导致板坏 裂纹和漏钢。
3.3 结晶器传热与凝固
凝固钩(Hook),其形貌基本类似于弯月面形状,弧线自表面向钢液侧弯 曲深度达1.42mm,此时振痕深度0.26mm。
3.3 结晶器传热与凝固
在弯月面凝固形成的弧形凝固钩,其形状是由在弯月面区钢水表面张力和 钢水静压力的平衡决定的。凝固钩形成过程如图所示。
(a)弯月面钢水与铜板接触点是凝固钩 开始点,然后呈弧形线离开铜壁。凝 固沿弧形线横向生长,形成初生坯壳 厚度。 (b)结晶器向下运动处于负滑脱期间, 弯月面钢水溢出凝固钩弧线,此时流 体惯性力超过钢水表面张力,把弯月 面液渣泵入到坯壳与铜板气隙中作润 滑剂。同时溢过凝固钓弧线的钢水靠 近模壁迅速凝固。高温的钢水也把附 着铜壁的固体渣(0.16mm厚)再熔化, 使横向传热加快,坯壳增厚。
金属凝固及连铸连铸坯的凝固传热资料PPT课件

2012.10.19
仿真软件的参数输入界面
31
第31页/共43页
选择钢种界面
2012.10.19
32
第32页/共43页
铸机参数界面
2012.10.19
33
第33页/共43页
二冷水量等参数输入界面
2012.10.19
34
第34页/共43页
2012.10.19
水流密度、传热系数关系式输入界面
35
2012.10.19
42
第42页/共43页
感谢观看!
2012.10.19
43
第43页/共43页
变以及铸坯温度分布的不均匀性等。
2012.10.19
21
第21页/共43页
铸坯冷却冶金准则:
1)极限冶金长度 H<H0
2)出结晶器处最小坯壳厚度 e≥e0
3)铸坯鼓肚极限 Ti≤T0 4)铸坯表面回热限制 一般为100℃/m T2 T1 C
Z
5)避开脆性区温度区间 TS≥Tsup TS≤Tint
2012.10.19
二冷区: h(TS TW)
辐射区: (TS4 T04) 25
第25页/共43页
2、离散化方程的建立(差分方程)
以板坯为例,由于板坯连铸冷却具有对称性的特点,模拟计算中 只取铸坯断面的二分之一。进行显式差分后可以化成九个差分方程 。
铸坯断面差分网格的划分
2012.10.19
2012.10.19
e
Q
Lvm[cl (Tc Tl ) L f cs (Ts T0 )]
11
第11页/共43页
影响结晶器传热因素
1)锥度的影响 2)结晶器润滑 3)结晶器材质 4)结晶器参数 5)冷却强度; 6)冷却水质 7)钢水成分。
- 1、下载文档前请自行甄别文档内容的完整性,平台不提供额外的编辑、内容补充、找答案等附加服务。
- 2、"仅部分预览"的文档,不可在线预览部分如存在完整性等问题,可反馈申请退款(可完整预览的文档不适用该条件!)。
- 3、如文档侵犯您的权益,请联系客服反馈,我们会尽快为您处理(人工客服工作时间:9:00-18:30)。
减轻弯月面区坯壳过度收缩、减少凹陷的 形成的措施
A.结晶器采用弱冷却,以降低局部热流,延 缓弯月面附近坯壳生长
B.在弯月面区域镶入低导热性的材料(如不 锈钢)组成复合热顶结晶器;
C.整个结晶器高度上镀层以降低导热性;
D.稳定浇注,如减小结晶器液面波动、结晶 器液渣层稳定等。
实际生产中,正常情况是处于第一种情况, 应尽力避免第二种情况发生,绝对禁止第 三种情况发生。
结晶器水流速一般在6~12m∕s范围,进出 水温差应控制在5~6℃,不大于10℃。结晶 器最大供水量,对于板坯和大方坯,每流 为500~600m3∕h,对于小方坯为100~150 m3∕h。
B.冷却水质的影响
在液相穴下部液体的流动主要是坯壳的收 缩和晶体下沉所引起的自然对流,或者是 由于铸坯鼓肚所引起的液体流动。
液相穴内液体流动对铸坯结构、夹杂物分 布、溶质元素的偏析和坯壳的生长有重要 作用。
四.在连铸机内运行的已凝固坯壳的冷却可看 成是经历“形变热处理”过程
1.从受力的方面看,铸坯承受热应力和机械应 力的作用பைடு நூலகம்使坯壳发生不同程度的变形;
D.结晶器材质的影响
正常通水情况下,结晶器内壁使用温度为 200~300℃。特殊情况时,最高处可达 500℃。要求结晶器材质导热性好,抗热 疲劳,强度高,高温下膨胀小,不易变形。 纯铜导热性最好,但弹性极限低,易产生 也就变形。所以多采用强度高的铜合金, 如Cu—Cr,Cu—Ag合金等。这些合金高 温下抗磨损能力强,使结晶器壁寿命比纯 铜高几倍。
下过程: ⑴钢水向坯壳的对流传热; ⑵凝固坯壳中的传导传热; ⑶凝固坯壳与结晶器壁传热; ⑷结晶器壁传导传热; ⑸冷却水与结晶器壁的强制对流传热,热量
被通过水缝中高速度流动的冷却水带走。
结晶器内钢水热量传给冷却水的总热阻可表示为:
1 1 em 1 eCu 1
式中 h h1 m h0 Cu hW h—总的传热系数; hl—钢水与坯壳的对流传热系数,估算hl= 1W∕cm2·℃; em—凝固坯壳厚度。坯壳内温度梯度可达 550℃∕cm; λm—钢的导热系数;
钢液与铜壁弯月面的形成:
在弯月面的根部,钢液与水冷铜壁接触, 立即受到铜壁的激冷作用,初生坯壳迅速 形成。良好稳定的弯月面可确保初生坯壳 的表面质量和坯壳的均匀性。当钢水中上 浮的夹杂物被保护渣吸附时,会降低钢液 表面张力,弯月面半径减小,从而破坏了 弯月面的薄膜性能,弯月面破裂,这时夹 杂物随同钢液在破裂处和铜壁形成新的凝 固层,夹杂物牢牢地粘附在这层凝固层上 而形成表面夹渣。带有夹渣的坯壳是薄弱 部位,易发生漏钢。
结晶器内气隙的形成过程:
接近紧密接触区的部分坯壳,实际上是处于气隙形 成和消失的动态平衡过程中。只有当坯壳厚度达到 足以抵抗钢液静压力的作用时,气隙才能稳定存在。
坯壳急剧收缩是导致结晶器最大热流减少的 原因
A.弯月面区域冷却强度太大,局部坯壳“过 冷”引起过度收缩;
B.随温度下降,坯壳发生δ→γ转变引起局部 收缩最大(0.38%);
C.结晶器润滑的影响
结晶器润滑可以减小拉坯阻力,并可由于 润滑剂充满气隙而改善传热。通常敞开浇 注时用油做润滑剂。油在高温下裂化分解 为C—H化合物。它充满气隙对传热有利。 采用保护浇注时,保护渣加在结晶器钢液 面上,形成液渣层,结晶器振动时,在弯 月面处液渣被带入气隙中,坯壳表面形成 均匀的渣膜,既起润滑作用,又由于填充 气隙而改善传热。
零强度温度TRN:强度σ=0的温度。 零塑性温度TDN:断面收缩率φ=0的温度。 在TRN和TDN温度区间是一个裂纹敏感区。
钢高温性能示意图:
TRN =TS+(20 ~30℃) TDN =TS-(30 ~50℃)
固—交界面的糊状区晶体强度和塑性 都非常小,(临界强度1~ 3N∕mm2,,由变形至断裂的临界应 变为0.2% ~0.4%)。当作用于凝固 坯壳的外部应力(如热应力、鼓肚力、 矫直力)使其变形超过上述临界值时, 铸坯就在固—交界面产生裂纹,形成 偏析线裂纹。
三.铸坯凝固是分阶段的凝固过程 在连铸机内铸坯的凝固经历三个阶段: 1.钢水在结晶器内形成初生坯壳,出结晶器下
口的铸坯安全厚度应足以抵抗钢液的静压 力的作用; 2.带有液芯的坯壳在二冷区稳定生长; 3.临近凝固末期的坯壳加速增长。
液相穴上部为强制对流循环区,循环区高 度决定于注流方式、浸入式水口类型和铸 坯断面。
④ 铸坯切割后大约还有40%热量放出来,为 了利用这部分热量,节约能源,成功地开 发了铸坯热装和连铸—连轧等工艺。
二.连铸坯凝固是沿液相穴在凝固温度区间把 液体转变为固体的加工过程
铸坯在运动中的凝固,实质上是沿液相穴 固—液交界面潜热的释放和传递过程。也 可看成是在凝固温度区间(TL→TS)把液体 转变为固体的加工过程。在固—液交界面 附近,存在一个凝固脆化区:
由于坯壳温度的回升,其强度降低,在钢 水静压力作用下使其再次帖紧铜壁,传热 条件有所改善,坯壳增厚,于是又产生冷 凝收缩,牵引坯壳再次离开铜壁,这样周 期性的离合2~3次,坯壳达到一定厚度并完 全脱离铜壁,气隙稳定形成。
结晶器角部区域,由于是二维传热,最先 形成坯壳,收缩力大,随后形成的气隙也 最大。由于钢水的静压力无法将角部的坯 壳压向铜壁,因而角部一开始就形成了永 久性的气隙。所以初生坯壳形成后,角部 区域地方传热变得比边部更差,角部成了 坯壳最薄弱的部位。
热量,以LP表示; ⑶显热:从固相线温度TS冷却到环境温度TO放出的
热量,CS(TS-TO)。
2.连铸机的三个传热冷却区 ① 一次冷却区。 钢水在水冷结晶器中形成足够厚均匀的坯
壳,以保证铸坯出结晶器不拉漏; ② 二次冷却区。 向铸坯表面喷水以加速铸坯内部热量的传
递,使铸坯完全凝固; ③ 三次冷却区。 铸坯向空气中辐射传热,使铸坯内外温度
2.从冶金方面看,随着温度的下降,坯壳发生 δ→γ→α的相变,特别是二冷区,坯壳温度 的反复下降和回升,使铸坯组织发生变化, 就相当于“热处理”过程。同时由于溶质 元素的偏析作用,可能发生硫化物、氮化 物质点在晶界沉淀,增加了钢的高温脆性, 对铸坯质量有重要影响。
§3—2 钢液在结晶器内的凝固与传热
3.紧密接触区
弯月面下部的初生坯壳由于不足以抵抗钢液 静压力的作用,与铜壁紧密接触。在该区域 坯壳以传导传热的方式将热量传输给铜壁, 愈往接触区的下部,坯壳也愈厚。
4.气隙的形成、稳定及角部气隙
已凝固的高温坯壳发生δ→γ的相变,引起坯 壳收缩,收缩力牵引坯壳离开铜壁,气隙 开始形成。由于气隙的热阻很大,气隙的 形成使坯壳向铜壁的传热迅速减少,离开 铜壁的坯壳回热升温,甚至凝固前沿部分 初生坯壳重新熔化。
铜壁局部区域处于高温状态,靠近铜壁表面过热 的水层中,有水生成蒸汽并产生沸腾。在这种情 况下,结晶器与冷却水之间热交换不决定于水流 速,而主要决定于铜壁表面的过热和水的压力。
c.膜态沸腾:
温度超过某一极限值时,靠近铜壁表面的 水形成蒸汽膜,热阻增大,热流减小,导 致铜壁表面温度升高,造成结晶器损坏。
一.结晶器内坯壳的形成 1.坯壳表面与铜壁之间的接触状况 ⑴钢液弯月面区; ⑵坯壳与铜壁紧密接触区; ⑶坯壳收缩与铜壁脱开产生的气隙区。
2.弯月面的形成 由于钢液与结晶器铜壁的润湿作用,钢液与铜
壁接触形成了一个半径很小的弯月面。其半径:
r =5.43×10-2 m
m
式中 σm—钢液表面张力; ρm—钢水密度。
C=ΔTβ×100%
B.结晶器长度的影响
结晶器内钢水热量导出给铜壁,上半部占 50%以上,当气隙形成后,结晶器下部导 出热量减少,结晶器下部主要起支承坯壳 的作用,结晶器长度以不增加拉漏为原则。 通常为700~900mm。
C.结晶器铜壁厚度的影响
铜壁厚度在一定范围内对传热影响不大。 方坯结晶器铜壁厚度在8~15mm范围,热 流变化很小,板坯结晶器铜壁厚度由40mm 减薄到20mm时,热流仅增加10%。
均匀化。
连铸坯冷凝示意图:
3.连铸机热平衡
① 钢水从结晶器→二冷区→辐射区大约有60 %热量放出来铸坯才能完全凝固。这部分 热量的放出速度决定了铸机生产率和铸坯 质量
② 铸机范围内主要依靠结晶器和二次冷却系 统散热,其中二冷区散出热量最多。
③ 通过结晶器在一分钟内要散出的热量,最 高时可占总需散热量的20%左右。可见保证 结晶器有足够的冷却能力十分重要,它对 初期坯壳的形成具有决定性的影响。
a— 坯壳与铜壁紧密接触;b—坯壳产生气 隙
促进结晶器坯壳均匀生长的操作注意事项 ⑴低的浇注温度; ⑵水口注流与结晶器断面严格对中; ⑶结晶器冷却水缝中水流均匀分布; ⑷合理的结晶器倒锥度; ⑸结晶器液面的稳定性; ⑹防止结晶器变形; ⑺坯壳与结晶器壁之间均匀的保护渣膜。
三.结晶器传热与热阻 1.结晶器热阻 结晶器中钢水沿周边即水平方向传热有以
h0—坯壳与结晶器间传热系数。它取决于坯 壳与铜壁的接触状态,若形成了气隙,热 阻显著增大。气隙中的传热系数h0 =0.2 W∕cm2·℃;
eCu—T铜壁厚度;
λCu—铜的导热系数;
hw—强制对流时水的传热系数。研究表明, 当水流速达6m∕s时,传热系数hw=4 W∕cm2·℃;
可见,最大的热阻是来自于坯壳与结晶器 壁之间的气隙。气隙热阻占总热阻84%以 上。因此坯壳的生长决定于气隙形成动力 学,而气隙的大小是决定于坯壳的收缩和 坯壳抵抗钢水鼓胀的能力。结晶器断面气 隙的形成是不均匀的,由于角部是二维传 热,冷却最快收缩最早,产生气隙后向中 心面扩展,结晶器宽面气隙宽度比角部小, 角部坯壳厚度最薄,常常会出现角部裂纹, 甚至造成漏钢。
水垢沉积在铜壁表面形成绝热层,增加热 阻,热流下降,导致铜壁温度升高,加速 了水的沸腾。所以,结晶器必须使用软水。 要求其总盐含量≯400mg∕l,硫酸盐≯150 mg∕l,氯化物≯50mg∕l,硅酸盐 ≯40mg∕l,悬浮质点<50mg∕l,质点尺 寸≯0.2mm,碳酸盐硬度≯1~2°Dh, pH 值为7~8。