铸造合金原理及熔炼
低压铝合金铸造工艺
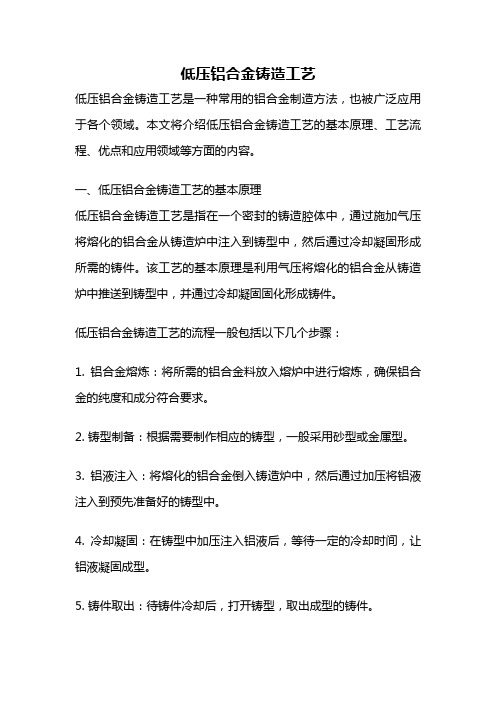
低压铝合金铸造工艺低压铝合金铸造工艺是一种常用的铝合金制造方法,也被广泛应用于各个领域。
本文将介绍低压铝合金铸造工艺的基本原理、工艺流程、优点和应用领域等方面的内容。
一、低压铝合金铸造工艺的基本原理低压铝合金铸造工艺是指在一个密封的铸造腔体中,通过施加气压将熔化的铝合金从铸造炉中注入到铸型中,然后通过冷却凝固形成所需的铸件。
该工艺的基本原理是利用气压将熔化的铝合金从铸造炉中推送到铸型中,并通过冷却凝固固化形成铸件。
低压铝合金铸造工艺的流程一般包括以下几个步骤:1. 铝合金熔炼:将所需的铝合金料放入熔炉中进行熔炼,确保铝合金的纯度和成分符合要求。
2. 铸型制备:根据需要制作相应的铸型,一般采用砂型或金属型。
3. 铝液注入:将熔化的铝合金倒入铸造炉中,然后通过加压将铝液注入到预先准备好的铸型中。
4. 冷却凝固:在铸型中加压注入铝液后,等待一定的冷却时间,让铝液凝固成型。
5. 铸件取出:待铸件冷却后,打开铸型,取出成型的铸件。
三、低压铝合金铸造工艺的优点低压铝合金铸造工艺相比其他铸造方法具有以下优点:1. 成品质量高:低压铝合金铸造工艺可以实现较高的铸件准确性和表面质量,铸件的尺寸精度、表面光洁度和机械性能都能够满足要求。
2. 生产效率高:低压铝合金铸造工艺具有快速生产的特点,一次注塑可以得到多个铸件,生产效率较高。
3. 设备投资少:低压铝合金铸造工艺相对于其他铸造方法,设备投资相对较少,维护成本也较低。
4. 适用范围广:低压铝合金铸造工艺适用于各种铝合金铸件的制造,例如汽车零部件、航空航天零部件等。
四、低压铝合金铸造工艺的应用领域低压铝合金铸造工艺广泛应用于各个领域,特别是在汽车、航空航天、电子、机械等行业中得到了广泛的应用。
它可以制造各种复杂形状的铝合金零部件,如汽车发动机缸体、飞机发动机壳体、电子设备外壳等。
低压铝合金铸造工艺是一种高效、高质量的铸造方法,具有成本低、生产效率高、适用范围广等优点,被广泛应用于各个领域。
铸造合金及其熔炼(铸铁熔炼)
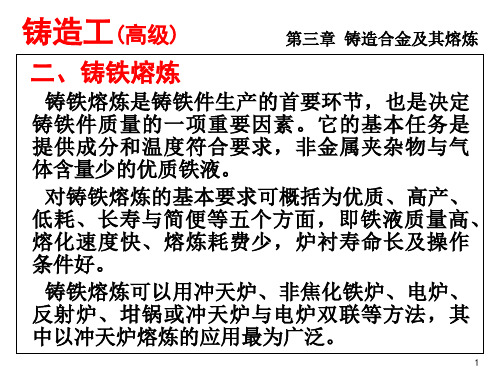
第三章 铸造合金及其熔炼
以上均为氧化放热反应,根据上述反应及 图3-13可见,在氧化带内:
①焦炭燃烧生成的炉气,既有二氧化碳,也有一 氧化碳,但主要是二氧化碳。
②从主排风口开始,随着炉气的上升,反应不断 进行,炉气中的氧逐渐减少,二氧化碳不断增 加。当上升到氧化带顶面时,炉气的氧基本耗 尽,氧化反应终止,二氧化碳达到最高值。
图3-13 冲天炉熔炼过程原理图
25
铸造工(高级)
第三章 铸造合金及其熔炼
1)预热区 从加料口下沿料面到铁料开始熔化这 段高度为预热区。预热区的炉料在下降过程中, 与上升的炉气之间的热交换方式以对流为主,金 属料逐渐被加热至熔化温度。
预热区高度受有效高度、底焦高度、炉内料面的 实际位置、炉料块度、炉料下落速度、炉气分布、 铁焦比等许多因素的影响,波动很大。其中金属 料的块度特别重要。金属料的块度愈大,预热所 需的时间愈长,预热区高度愈大,严重时金属料 块可能进入风口区,造成“落生”现象,妨碍冲 天炉的正常操作。因此应限制金属料的块度。但 金属料的块度也不能过小,以免造成严重氧化。
铸铁熔炼可以用冲天炉、非焦化铁炉、电炉、 反射炉、坩锅或冲天炉与电炉双联等方法,其 中以冲天炉熔炼的应用最为广泛。
1
铸造工(高级)
第三章 铸造合金及其熔炼
1. 冲天炉的结构(图3-12)
冲天炉的类型很多,但基本结构大体相 同。常用的冲天炉由四部分组成:炉底部 分、炉身部分(包括送风系统)、前炉部 分、炉顶部分(烟囱及除尘系统)。
修炉完毕,用木柴或烘干器慢火充分烘干前、后 炉。前炉必须烘透,以保证铁液温度。
6
铸造工(高级)
第三章 铸造合金及其熔炼
(3)点火与加底焦 烘炉后,加入木柴,引
铝合金的熔炼与铸造
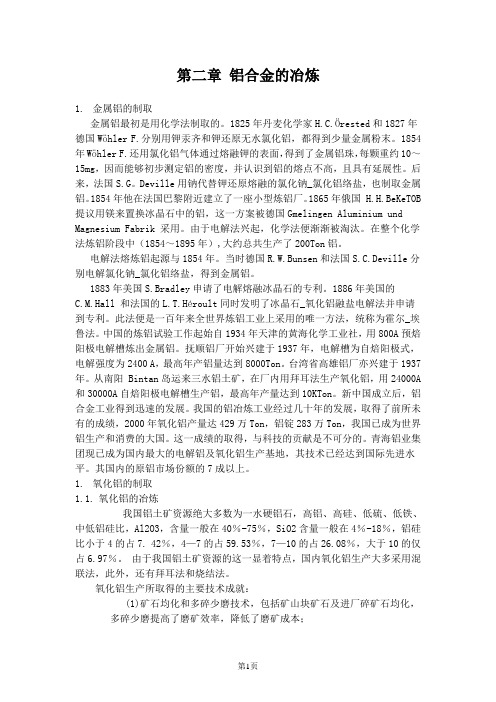
第二章铝合金的冶炼1.金属铝的制取金属铝最初是用化学法制取的。
1825年丹麦化学家H.C.Örested和1827年德国Wöhler F.分别用钾汞齐和钾还原无水氯化铝,都得到少量金属粉末。
1854年Wöhler F.还用氯化铝气体通过熔融钾的表面,得到了金属铝珠,每颗重约10~15mg,因而能够初步测定铝的密度,并认识到铝的熔点不高,且具有延展性。
后来,法国S.G。
Deville用钠代替钾还原熔融的氯化钠_氯化铝络盐,也制取金属铝。
1854年他在法国巴黎附近建立了一座小型炼铝厂。
1865年俄国 H.H.BeKeTOB 提议用镁来置换冰晶石中的铝,这一方案被德国Gmelingen Aluminium und Magnesium Fabrik 采用。
由于电解法兴起,化学法便渐渐被淘汰。
在整个化学法炼铝阶段中(1854~1895年),大约总共生产了200Ton铝。
电解法熔炼铝起源与1854年。
当时德国R.W.Bunsen和法国S.C.Deville分别电解氯化钠_氯化铝络盐,得到金属铝。
1883年美国S.Bradley申请了电解熔融冰晶石的专利。
1886年美国的C.M.Hall 和法国的L.T.Héroult同时发明了冰晶石_氧化铝融盐电解法并申请到专利。
此法便是一百年来全世界炼铝工业上采用的唯一方法,统称为霍尔_埃鲁法。
中国的炼铝试验工作起始自1934年天津的黄海化学工业社,用800A预焙阳极电解槽炼出金属铝。
抚顺铝厂开始兴建于1937年,电解槽为自焙阳极式,电解强度为2400 A,最高年产铝量达到8000Ton。
台湾省高雄铝厂亦兴建于1937年。
从南阳 Bintan岛运来三水铝土矿,在厂内用拜耳法生产氧化铝,用24000A 和30000A自焙阳极电解槽生产铝,最高年产量达到10KTon。
新中国成立后,铝合金工业得到迅速的发展。
我国的铝冶炼工业经过几十年的发展,取得了前所未有的成绩,2000年氧化铝产量达429万Ton,铝锭283万Ton,我国已成为世界铝生产和消费的大国。
熔炼、铸造和均质的基础理论

有色金属熔炼和铸造一. 基本原理1.熔炼和铸造的定义:熔炼的含义:就是将各种胚锭通过加温重熔的方法,实现由固态向液态转变的同时,进行合金化的过程.在熔炼的过程中,将实现净化除杂的目的.铸造的含义:将符合铸锭要求的金属熔体通过转注工具浇入到具有一定形状的铸模 中,使熔体在重力场或外力场的作用下充满模腔,冷却并凝固成型的工艺过程.它不仅要实现外部定型,而且还要实现对内部的微观组织结构的调控.二. 铝及其合金的熔炼1.熔炼的传热过程铝的熔点虽然很低(660℃),但由于熔化潜热(395.56kJ/kg)、固态热容(1.1386kJ/kg. ℃)和液态热容(1.046kJ/kg. ℃)都较高,而铝的黑度是铜铁的1/4,所以铝熔炼耗能大,很难实现理想的热效率。
热的传递方式有三种,传导、对流和辐射。
要提高金属的受热量,一方面提高炉温,这对炉体和熔体都不利,另一方面铝的黑度小,故提高辐射传热也是有限的,因此只能着眼于增大对流的传热系数(αc),它与气流速度的关系:αc=5.3+3.6v[kJ/(m2 h.℃)] V<5m/s时αc=647+v0.78 [kJ/(m2 h.℃)] V>5m/s时可见提高燃烧的气流速度是有效的。
2.合金元素的溶解和蒸发熔炼温度下(700℃)几种元素在铝中的扩散系数为(cm2/s):Ti:0.66,Mo:1.38(760℃),Co:0.79,Ni:1.44,Si:14.4,通常情况下,与铝形成易熔共晶的元素,一般较易熔解,与铝形成包晶转变的,特别是熔点相差大的元素较难于溶解。
在相同溶解条件下,一般蒸气压高的元素容易挥发,可把常用的铝合金分为两组:Cu、Cr、Fe、Ni、Ti、Si、V、Zr等元素的蒸气压比铝的小,蒸发慢,Mn、Li、Mg、Zn、Na、Cd等元素蒸气压比铝的大,容易蒸发,在熔炼过程中损失较大。
3.熔炼的吸气过程铝—氧反应金属以熔融态或半熔融态暴露于炉气中并与之相互作用时间越长,往往造成金属大量吸气,氧化和形成其它非金属夹杂,其反应分为:吸附、界面反应和熔解(扩散)。
brc20铸造 原理
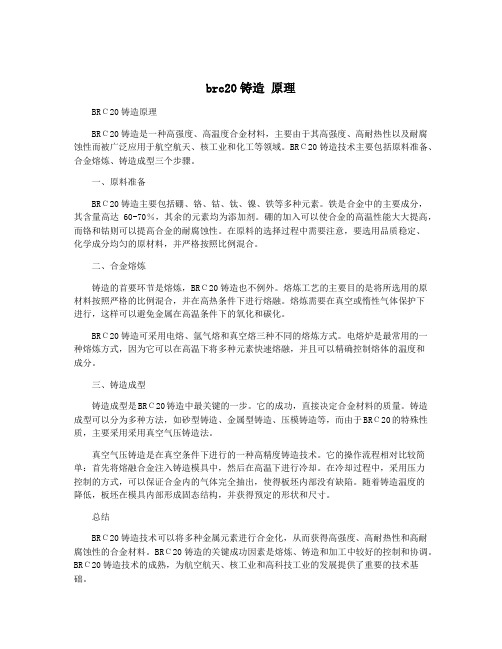
brc20铸造原理BRС20铸造原理BRС20铸造是一种高强度、高温度合金材料,主要由于其高强度、高耐热性以及耐腐蚀性而被广泛应用于航空航天、核工业和化工等领域。
BRС20铸造技术主要包括原料准备、合金熔炼、铸造成型三个步骤。
一、原料准备BRС20铸造主要包括硼、铬、钴、钛、镍、铁等多种元素。
铁是合金中的主要成分,其含量高达60-70%,其余的元素均为添加剂。
硼的加入可以使合金的高温性能大大提高,而铬和钴则可以提高合金的耐腐蚀性。
在原料的选择过程中需要注意,要选用品质稳定、化学成分均匀的原材料,并严格按照比例混合。
二、合金熔炼铸造的首要环节是熔炼,BRС20铸造也不例外。
熔炼工艺的主要目的是将所选用的原材料按照严格的比例混合,并在高热条件下进行熔融。
熔炼需要在真空或惰性气体保护下进行,这样可以避免金属在高温条件下的氧化和碳化。
BRС20铸造可采用电熔、氩气熔和真空熔三种不同的熔炼方式。
电熔炉是最常用的一种熔炼方式,因为它可以在高温下将多种元素快速熔融,并且可以精确控制熔体的温度和成分。
三、铸造成型铸造成型是BRС20铸造中最关键的一步。
它的成功,直接决定合金材料的质量。
铸造成型可以分为多种方法,如砂型铸造、金属型铸造、压模铸造等,而由于BRС20的特殊性质,主要采用采用真空气压铸造法。
真空气压铸造是在真空条件下进行的一种高精度铸造技术。
它的操作流程相对比较简单:首先将熔融合金注入铸造模具中,然后在高温下进行冷却。
在冷却过程中,采用压力控制的方式,可以保证合金内的气体完全抽出,使得板坯内部没有缺陷。
随着铸造温度的降低,板坯在模具内部形成固态结构,并获得预定的形状和尺寸。
总结BRС20铸造技术可以将多种金属元素进行合金化,从而获得高强度、高耐热性和高耐腐蚀性的合金材料。
BRС20铸造的关键成功因素是熔炼、铸造和加工中较好的控制和协调。
BRС20铸造技术的成熟,为航空航天、核工业和高科技工业的发展提供了重要的技术基础。
《铸造合金及其熔炼》总结

《铸造合金及其熔炼》总结前言:全书一共有三部分组成第一篇铸造及其熔炼主要讲的是几种铸铁和铸铁的熔炼重点在第一章,主要内容为铸铁的凝固剂组织形成的基本理论;熔炼部分重点为冲天炉熔炼。
第二篇铸钢及其熔炼,主要讲的是各种铸钢和铸钢的熔炼重点为铸造低合金钢、电弧刚及钢液的炉外精炼。
第三篇铸造非铁合金及其熔炼主要的内容是铝铜等其他非铁合金的性能及其熔炼方法,重点为铸造铝合金及其变质、精炼。
第一篇铸造及其熔炼合金相图是分析合金相组织的有用工具。
通过铁碳合金相图可以知道各种相得相变温度,合金成分含量,为热加工等工艺提供基础2。
铸铁的生产主要讲解了灰铸铁、强韧铸铁、以及其他特种性能铸铁(减摩铸铁,冷硬铸铁,抗磨铸铁,耐热的铸铁,耐腐蚀铸铁)的力学性能特点机械性能特点,金相组织的性能特点,以及铸铁的生产、分类和牌号。
(1)影响铸态组织的因素冷却速度的影响化学成分的影响铁液的过热和高温静止的影响孕育的影响炉料的影响3 铸铁的熔炼--- 冲天炉熔炼1 、冲天炉熔炼基本原理(1)底焦燃烧:冲天炉底焦燃烧可以划分为两个区带:A 、氧化带:从主排风口到自由氧基本耗尽,二氧化碳浓度达到最大值的区域。
B 、还原带:从氧化带顶面到炉气中[CO2]/[CO] 浓度基本不变的区域,从风口引入的风容易趋向炉壁,形成炉壁效应,形成一个下凹的氧化带和还原带,对熔化造成不利影响。
①不易形成一个集中的高温区,不利于铁水过热;②加速了炉壁的侵蚀;③铁料熔化不均匀,铁液不易稳定下降, 影响化学成分。
解决方法:①采用较大焦炭块度,使风均匀送入;②采用插入式风嘴;③采用曲线炉膛;④采用中央送风系统;⑤熔炼过程中为使焦炭不易损耗,送风量要与焦炭损耗相适应。
根据炉气、炉料、铁水浓度和温度,炉身分为4 个区域:(1)预热区(2)熔化区(3)过热区4)炉缸区。
:冲天炉熔炼过程在熔化过程中底焦燃烧而消耗,为了保证整个熔炼过程连续正常进行就必须及时得补充底焦,以此来始终保持底焦的高度。
铝合金熔炼与铸造

铝合金熔炼与铸造铝合金是一种常见且广泛使用的金属材料,具有较低的密度、良好的导热性和耐腐蚀性,因此在许多行业中得到了广泛的应用。
铝合金的熔炼和铸造是制造铝合金制品的关键步骤。
本文将介绍铝合金熔炼和铸造的基本原理、工艺和注意事项。
一、铝合金熔炼1.1 熔炼原理铝合金熔炼的主要原理是将铝及其他合金元素加热至其熔点,使其融化成液态,以便进行后续的铸造工艺。
铝的熔点较低,约为660°C,因此相对较容易熔化。
而其他合金元素的加入可以改变铝合金的性质,例如提高其强度、耐腐蚀性或者改善加工性能。
1.2 熔炼工艺铝合金熔炼工艺一般分为两种:批量熔炼和连续熔炼。
批量熔炼是将一定量的铝和其他合金元素加入炉内,通过加热熔化成液态,并进行充分混合。
这种方法适用于小规模生产,常用的炉型有电阻炉和燃气炉。
而连续熔炼是将铝合金材料加入熔炉的顶部,通过炉内的加热和熔化过程,使得底部的液态铝合金不断流出。
这种方法适用于大规模生产,常用的炉型有回转炉和隧道炉。
1.3 熔炼注意事项在铝合金的熔炼过程中,需要注意以下几个方面。
首先,炉内的温度需要控制在适当的范围内,以避免过度燃烧或者过度冷却。
其次,需要保持良好的熔炼环境,防止氧气、水分或杂质等对炉内材料的影响。
最后,在加入其他合金元素时,需要根据配比和工艺要求进行准确的添加,以保证最终铝合金的性能。
二、铝合金铸造2.1 铸型设计铝合金铸造的第一步是进行铸型设计。
铸型设计的目的是根据最终产品的形状和要求,确定合适的铸造方法和材料,以及适当的铸型结构。
常见的铸型结构有砂型、金属型和陶瓷型等。
其中砂型是最常用的铸造方法,可以应用于各种形状和尺寸的产品。
2.2 铸造工艺铝合金的铸造工艺可以分为传统铸造和压铸两种。
传统铸造是将熔融的铝合金液体倒入铸型中,并通过自然冷却形成最终产品。
这种方法适用于小批量生产,但精度和表面光滑度相对较低。
压铸是将高压液压机将铝合金液体注入铸型中,通过压力传递和快速冷却,实现快速成型。
铸造镁合金熔炼

汽车工业
汽车工业对轻量化材料的需求越来越 大,镁合金作为一种轻质材料,在汽 车领域的应用前景广阔。
THANKS
感谢观看
在加热过程中,应确保炉温均 匀,避免局部过热,以防止镁 合金在熔化前就发生氧化燃烧。
熔化后的镁合金应保持液态稳 定,以便进行后续的精炼和除 气处理。
镁合金的精炼与除气
为了去除镁合金中的杂质和气体,需要 进行精炼和除气处理。常用的精炼剂包
括氯化物、氟化物和氯氟化物等。
在精炼过程中,应控制精炼剂的加入量 和加入速度,以避免产生大量烟雾和溅 出。同时,应保持熔液的搅拌,以便使
熔炼设备的选择与准备
01
02
03
熔炼炉
根据生产需求选择合适的 熔炼炉,如坩埚式、感应 式等,并确保其完好无损。
炉衬材料
选用合适的耐火材料作为 炉衬,以承受高温和化学 侵蚀,延长熔炼炉的使用 寿命。
设备调试
对熔炼设备进行调试,确 保其正常运行,并符合安 全规范。
安全防护措施的准备
安全操作规程
制定并遵守安全操作规程, 确保操作人员熟悉安全操 作要求。
精炼剂充分混合。
除气是精炼过程中的一个重要环节,可 以通过在熔液中通入惰性气体或加入除 气剂来实现。通入惰性气体可以排出熔 液中的气体,而加入除气剂则可以吸附
熔液中的气体。
镁合金的成分调整与细化组织
根据产品要求,可以对镁合金的成分进行调整,如添加合金 元素、调整元素含量等。成分调整可以提高镁合金的力学性 能和耐腐蚀性。
质量检测与控制
外观检测
对铸造完成的镁合金进行外观检查, 确保表面光滑、无缺陷,尺寸符合要 求。
内部检测
通过X射线、超声波等无损检测方法 对镁合金内部进行检测,以确保无气 孔、夹渣等缺陷。
铸造工程学-铸造合金及熔炼
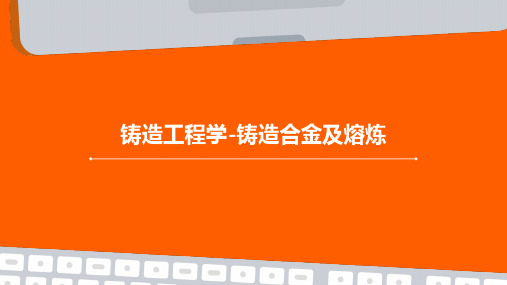
在铸造过程中,由于合金的收缩特性以及模具结构设计不当等原因,容易导致铸件出现缩孔与缩松缺 陷。这些缺陷会导致铸件局部强度和致密度下降,影响其机械性能和耐腐蚀性。
裂纹与变形
总结词
裂纹与变形是铸造合金冷却和加工过程中常见的问题,会导致铸件报废。
详细描述
在铸造过程中,由于冷却速度过快、模具设计不合理、浇注系统不当等因素,容易导致 铸件出现裂纹与变形缺陷。裂纹会导致铸件强度下降,变形则会使铸件无法满足精度要
熔炼的基本原理
熔炼是指将金属材料加热至熔点以上,使其成为液态,并加入所需的合金元素,通 过搅拌和化学反应等手段,使合金成分均匀混合的过程。
熔炼过程中,金属材料的熔点、密度、粘度等物理性质和化学性质都会发生变化, 这些变化对熔炼过程和产品质量产生重要影响。
熔炼过程中需要控制温度、压力、气氛等工艺参数,以确保合金成分的准确性和均 匀性,以及避免金属氧化、吸气等不良现象。
熔炼温度控制
严格控制熔炼温度,以保 证合金成分的均匀性和避 免烧损。
合金的熔炼与搅拌
通过搅拌和合金化处理, 确保合金成分均匀分布, 提高合金性能。
精炼与除渣
精炼
通过除气、去除非金属夹杂物等手段,提高合金的纯净度。
除渣
去除熔融金属中的熔渣和杂质,以保证铸件的质量和性能。
浇注与冷却
浇注
将熔融金属浇注入铸型中,形成符合要求的铸件。
熔炼技术的创新与改进
真空熔炼技术
利用真空技术进行合金熔炼,可 去除有害气体和杂质,提高合金
的纯净度和质量。
电渣重熔技术
通过电流作用下的熔渣进行二次熔 炼,使金属更加纯净和致密,提高 材料的机械性能。
定向凝固技术
使合金在凝固过程中保持一定的结 晶方向,提高材料的定向性能和机 械强度。
铝合金铸铝工艺

铝合金铸铝工艺一、铝合金铸铝工艺概述铝合金铸造是一种常用的制造工艺,其主要原理是通过熔化铝合金,将其注入模具中进行冷却凝固,最终得到所需的零件或产品。
在此过程中,需要考虑多个因素,如模具设计、熔炼温度、注液速度等。
二、模具设计1. 模具材料选择:通常使用的模具材料有钢、铜合金等,需要根据所需产品的材质和形状来选择。
2. 模具结构设计:根据产品形状和尺寸确定模具结构,并考虑到浇口、排气孔等因素。
3. 模具加工精度:为了保证产品的精度和表面质量,需要对模具进行高精度加工。
三、熔炼与浇注1. 铝合金选择:根据产品性能要求选择适当的铝合金。
2. 熔炼温度控制:根据不同的铝合金种类和配方确定熔点,并控制在适当范围内以保证成品质量。
3. 浇注温度控制:决定了铸件内部组织和外观质量,需要根据模具材料和产品形状确定最佳浇注温度。
4. 注液速度控制:过快或过慢都会影响产品质量,需要根据产品形状和模具结构确定最佳注液速度。
四、冷却凝固1. 冷却方式:常用的冷却方式有自然冷却、水淬和沙包淬火等,需要根据不同的铝合金种类和产品形状选择适当的冷却方式。
2. 冷却时间:直接影响到产品内部组织和外观质量,需要根据铝合金种类、产品形状和模具材料等因素确定最佳冷却时间。
五、后处理1. 去除毛刺:通过打磨或切割等方式去除铸件表面的毛刺。
2. 热处理:常用的热处理方法有退火、时效处理等,可以改善铸件的力学性能。
3. 表面处理:如喷漆、电泳涂装等,可以提高铸件表面质量和耐腐蚀性能。
六、注意事项1. 熔炼时要注意保持干燥,避免水分进入铝合金中。
2. 浇注时要注意浇口和排气孔的设计,避免气泡和缺陷的产生。
3. 冷却凝固时要注意控制温度和时间,避免过快或过慢导致质量问题。
4. 后处理时要注意安全,如切割时戴好防护眼镜等。
七、总结铝合金铸造工艺是一项复杂的制造工艺,需要综合考虑多个因素来保证产品质量。
模具设计、熔炼与浇注、冷却凝固和后处理都是重要环节,需要精细控制。
铸造熔炼实验报告
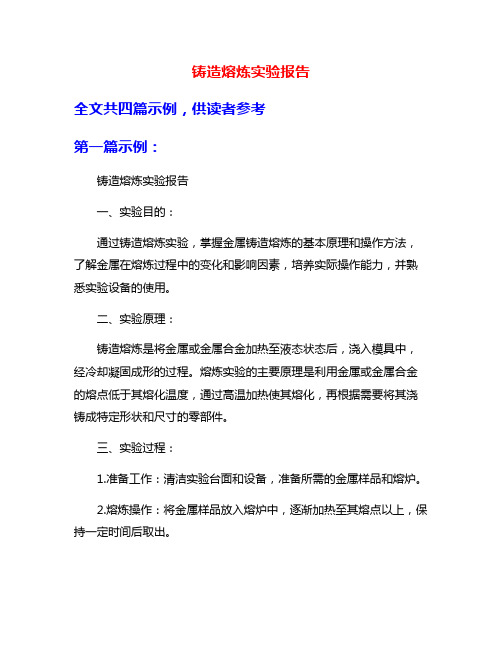
铸造熔炼实验报告全文共四篇示例,供读者参考第一篇示例:铸造熔炼实验报告一、实验目的:通过铸造熔炼实验,掌握金属铸造熔炼的基本原理和操作方法,了解金属在熔炼过程中的变化和影响因素,培养实际操作能力,并熟悉实验设备的使用。
二、实验原理:铸造熔炼是将金属或金属合金加热至液态状态后,浇入模具中,经冷却凝固成形的过程。
熔炼实验的主要原理是利用金属或金属合金的熔点低于其熔化温度,通过高温加热使其熔化,再根据需要将其浇铸成特定形状和尺寸的零部件。
三、实验过程:1.准备工作:清洁实验台面和设备,准备所需的金属样品和熔炉。
2.熔炼操作:将金属样品放入熔炉中,逐渐加热至其熔点以上,保持一定时间后取出。
3.浇铸过程:将熔化的金属快速倒入模具中,待冷却后取出铸件,清理去除砂砾。
4.分析检测:对铸件进行外观和内部组织的观察和分析,检测金属成分和性能。
四、实验结果:通过本次铸造熔炼实验,成功熔炼了金属样品并浇铸成铸件。
铸件表面光洁,无气孔和夹渣现象,内部组织紧密,无裂纹和夹杂。
经过检测,铸件成分和性能符合设计要求,达到预期效果。
五、实验体会:1.熟练掌握金属熔炼的基本操作技能和安全注意事项。
2.加强了对金属熔炼过程的理解和认识,对金属成分和熔点的关系有了更深入的了解。
3.培养了实际操作和解决问题的能力,提高了团队合作和沟通能力。
六、实验总结:通过铸造熔炼实验,我们深入了解了金属铸造熔炼的基本原理和操作方法,掌握了金属熔点的控制和铸造过程的技巧。
在实践中不断积累经验,提高了对金属材料处理的能力和水平。
希望今后能结合更多实际案例和问题进行进一步研究和探讨,为工程技术领域的发展贡献自己的力量。
以上为本次铸造熔炼实验报告内容,谢谢!第二篇示例:实验名称:铸造熔炼实验报告一、实验目的本实验旨在通过铸造熔炼的操作,使学生了解铸造熔炼的基本原理和方法,掌握铸造熔炼的实验操作技能,提高学生的实际动手能力和实验设计能力。
二、实验原理铸造熔炼是利用高温将金属或合金熔化后,借助一定的模具将熔化金属或合金浇铸到模具中,通过凝固形成所需的零件或器件的一种加工工艺。
铝合金熔炼与铸造简介课件

目录
• 铝合金熔炼基础 • 铝合金熔炼工艺 • 铝合金铸造技术 • 铝合金的应用 • 铝合金熔炼与铸造的挑战与未来发展
01
铝合金熔炼基础
铝合金的特性
01
02
03
物理特性
铝合金具有优良的导电性 、导热性和耐腐蚀性。
化学特性
铝合金易于氧化形成致密 的氧化膜,具有良好的耐 腐蚀性。
熔炼设备
常用的熔炼设备有坩埚炉 、电炉、感应炉等。
熔炼工艺参数
包括熔炼温度、熔炼时间 、熔炼气氛等,这些参数 对铝合金的性能和成分有 重要影响。
02
铝合金熔炼工艺
熔炼前的准备
原材料选择
配料计算
选择高质量的原材料,如铝锭、合金 元素和添加剂,以确保熔炼出的铝合 金具有所需的性能。
根据产品要求,计算所需的原材料配 比,以获得所需的化学成分和性能。
理。
热处理
根据需要,对铸件进行 热处理以提高其机械性
能。
铸造后处理
清理
去除铸件表面的毛刺、飞边等杂质,确保表 面质量。
质量检测
对铸件进行质量检测,确保其符合相关标准 和客户要求。
机械加工
对铸件进行机械加工,以满足其使用要求。
包装运输
对铸件进行包装,并选择合适的运输方式将 其送达目的地。
04
铝合金的应用
THANK YOU
感谢观看
模具准备
设计和制作铸造模具,确保其 结构合理、尺寸精确。
设备检查
对熔炼炉、浇注机等设备进行 检查和调试,确保其正常运转
。
工艺准备
制定合理的铸造工艺流程,明 确各环节的技术要求和操作规
范。
铸造过程
铸造合金熔炼原理
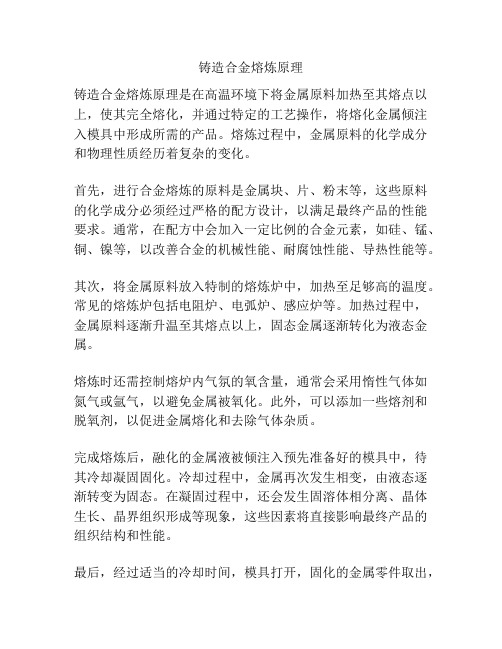
铸造合金熔炼原理
铸造合金熔炼原理是在高温环境下将金属原料加热至其熔点以上,使其完全熔化,并通过特定的工艺操作,将熔化金属倾注入模具中形成所需的产品。
熔炼过程中,金属原料的化学成分和物理性质经历着复杂的变化。
首先,进行合金熔炼的原料是金属块、片、粉末等,这些原料的化学成分必须经过严格的配方设计,以满足最终产品的性能要求。
通常,在配方中会加入一定比例的合金元素,如硅、锰、铜、镍等,以改善合金的机械性能、耐腐蚀性能、导热性能等。
其次,将金属原料放入特制的熔炼炉中,加热至足够高的温度。
常见的熔炼炉包括电阻炉、电弧炉、感应炉等。
加热过程中,金属原料逐渐升温至其熔点以上,固态金属逐渐转化为液态金属。
熔炼时还需控制熔炉内气氛的氧含量,通常会采用惰性气体如氮气或氩气,以避免金属被氧化。
此外,可以添加一些熔剂和脱氧剂,以促进金属熔化和去除气体杂质。
完成熔炼后,融化的金属液被倾注入预先准备好的模具中,待其冷却凝固固化。
冷却过程中,金属再次发生相变,由液态逐渐转变为固态。
在凝固过程中,还会发生固溶体相分离、晶体生长、晶界组织形成等现象,这些因素将直接影响最终产品的组织结构和性能。
最后,经过适当的冷却时间,模具打开,固化的金属零件取出,
经过后续的加工处理(如去毛刺、研磨、抛光等),即可得到最终的铸造合金产品。
总结起来,铸造合金熔炼原理是通过将金属原料熔化、倾注模具、冷却凝固等步骤,控制金属的组织结构和化学成分,制备出具有所需性能的铸造合金产品。
熔铸知识点总结
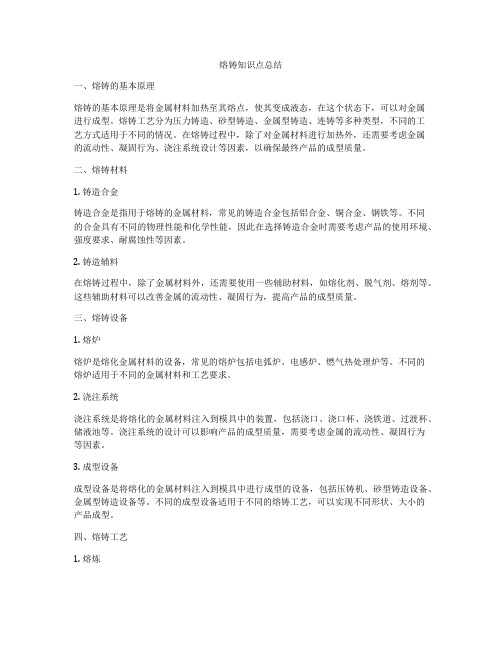
熔铸知识点总结一、熔铸的基本原理熔铸的基本原理是将金属材料加热至其熔点,使其变成液态,在这个状态下,可以对金属进行成型。
熔铸工艺分为压力铸造、砂型铸造、金属型铸造、连铸等多种类型,不同的工艺方式适用于不同的情况。
在熔铸过程中,除了对金属材料进行加热外,还需要考虑金属的流动性、凝固行为、浇注系统设计等因素,以确保最终产品的成型质量。
二、熔铸材料1. 铸造合金铸造合金是指用于熔铸的金属材料,常见的铸造合金包括铝合金、铜合金、钢铁等。
不同的合金具有不同的物理性能和化学性能,因此在选择铸造合金时需要考虑产品的使用环境、强度要求、耐腐蚀性等因素。
2. 铸造辅料在熔铸过程中,除了金属材料外,还需要使用一些辅助材料,如熔化剂、脱气剂、熔剂等。
这些辅助材料可以改善金属的流动性、凝固行为,提高产品的成型质量。
三、熔铸设备1. 熔炉熔炉是熔化金属材料的设备,常见的熔炉包括电弧炉、电感炉、燃气热处理炉等。
不同的熔炉适用于不同的金属材料和工艺要求。
2. 浇注系统浇注系统是将熔化的金属材料注入到模具中的装置,包括浇口、浇口杯、浇铁道、过渡杯、储液池等。
浇注系统的设计可以影响产品的成型质量,需要考虑金属的流动性、凝固行为等因素。
3. 成型设备成型设备是将熔化的金属材料注入到模具中进行成型的设备,包括压铸机、砂型铸造设备、金属型铸造设备等。
不同的成型设备适用于不同的熔铸工艺,可以实现不同形状、大小的产品成型。
四、熔铸工艺1. 熔炼熔炼是将固态金属材料加热至液态的过程,常见的熔炼工艺包括电弧炉熔炼、感应炉熔炼、气氛炉熔炼等。
在熔炼过程中,需要考虑金属材料的成分、温度控制、气氛保护等因素。
2. 浇注浇注是将熔化的金属材料注入到模具中进行成型的过程,浇注过程需要控制浇注速度、浇注温度、浇注位置等参数,以确保产品的成型质量。
3. 凝固凝固是指熔化的金属材料从液态变成固态的过程,凝固过程会影响产品的晶粒结构、机械性能、缺陷形成等因素。
- 1、下载文档前请自行甄别文档内容的完整性,平台不提供额外的编辑、内容补充、找答案等附加服务。
- 2、"仅部分预览"的文档,不可在线预览部分如存在完整性等问题,可反馈申请退款(可完整预览的文档不适用该条件!)。
- 3、如文档侵犯您的权益,请联系客服反馈,我们会尽快为您处理(人工客服工作时间:9:00-18:30)。
铸造合金原理及熔炼一、名词解释l.铸铁:是C的含量大于2.14%或者组织中具有共晶组织,并含有较多Si.Mn.P.S杂质元素的铁碳合金。
2.白口铸铁:少数C固溶于铁素体,其他以碳化物存在。
3.灰口铸铁:c主要结晶成石墨,并呈片状形式存在于铸铁中,断口为暗灰色。
4.球墨铸铁:铁水在浇注前经球化和孕育处理,C主要以球状形式存在于铸铁中。
5.球化处理:向铁水中加入稀土镁合金(球化剂)。
(其中镁是具有很强球化能力的元素)。
球化剂的作用是使石墨呈球状析出。
我国应用最广的球化剂是稀土镁合金。
6.孕育处理:向铁水中加入硅铁合金(孕育剂)颗粒。
孕育剂的作用是促进铸铁石墨化,防止产生白口,细化石墨。
常用的孕育剂为硅的质量分数75%硅铁。
7.蠕墨铸铁;是液态铁水经蠕化处理和孕育处理得到的.由金属基体和蠕虫状石墨构成。
8.可锻铸铁:是由白口铁经过退火而制得的一种高强度铸铁,白口铸铁中的渗碳体分解成团絮状石墨的灰口铸铁,性能优于灰铸铁,耐磨性和减震性优于普通碳索钢,可部分代替碳钢,合金钢和有色金属。
9.奥氏体(A或γ):碳溶于γ-Fe中所形成的间隙固溶体。
晶格结构:面心立方晶格fcc。
10.铁素体(F或α):碳溶于α-Fe中所形成的间隙固溶体,晶格结构:体心立方晶格bcc。
11.δ-铁素体:碳溶于δ-Fe中所形成的间隙固溶体。
12.碳当量定义:将合金元素对共晶点碳量的影响折算成铸铁碳量的增减,折算后的值称之为碳当量,以CE表示。
碳当量:CE=C+1/3(Si+p)13.共晶度:铁液实际含碳量和共晶点的实际碳量的比值为共晶度,以sc表示。
共晶度:Sc=C/[4.26%-(Si+p)l/3l 14.钢的腐蚀金属表面在周围介质的作用下逐渐被破坏的现象称为金属的腐蚀。
15.化学腐蚀是指金属表面与周围介质发生化学反应而引起的破坏,如高温下金属的氧化等。
16.电化学腐蚀是指金属与电解质溶液发生电化学作用而使金属破坏的现象。
17.耐热钢是指在高温下对氧化性气体具有抗氧化性的钢种。
18.黑色金属:在工业生产中,通常把铁及其合金称为黑色金属。
19.有色金属:把其他非铁金属及其合金称为有色金属。
20.固溶强化:通过合金元素固溶于金属基体中,使晶格发生畸变,从而使塑性变形的抗力增加,合金强度和硬度提高的过程叫做固溶强化。
21.时效强化(沉淀强化):时效处理,又称低温回火。
时效强化是指在网溶度随温庋降低而减少的合金系中,当合金元素含量超过一定限量后,淬火可获得过饱和固溶体。
在较低的温度加热(时效),过饱和固溶体将发生分解并析出弥散相,引起合金强度、硬度升高而塑性下降的过程。
它也被称为沉淀强化。
22.自然时效是指时效强化在室温下进行的时效,通常需要较长的时间。
23.人工时效又分为不完全人工时效、完全人工时效和过时效3种。
24.过剩相强化:当过量的合金元素加人到基体中时,一部分溶人固溶体,而超过极限溶解度的部分则不能溶入,形成过剩的第二相,如铝硅合金中的硅相。
过剩相强化主要利用较硬的过剩相来阻碍基体的变形,从而使合金强化,与时效强化有相似之处。
25.变质处理:铸造合金的组织细化亦常称为变质处理26.淬火:工艺是将工件加热到足够高的温度,并保温足够长的时间,使强化相充分溶人固溶体,随后快速冷却(淬人水中或油中)的过程。
27.时效:当铝合金通过高温下淬火形成过饱和固溶体后,再在一定温度下保温(或室温长时间放置)而使其强度、硬度升高的过程称为时效。
28.紫铜:纯铜呈紫红色,故又称紫铜,具有面心立方晶格,无同素异构转变,无磁性。
29.青铜主要是CuSn台金,后来发展出一些代锡的铜合金,其组织和性能仍与锡青铜类似,称为无锡青铜,如铝青铜、铅青铜等。
30.黄铜:以锌为主加元素的铜合金称为黄铜31.特殊黄铜:通常,Cu-Zn二元合金称为普通黄铜。
以铜、锌为主要组元,再加人其他元素构成的合金,称为特殊黄铜32.锡汗:锡青铜有很强的枝晶偏析和反偏析现象,常在铸件表面渗出许多灰白色颗粒(富锡分泌物人在加工表面也常见到一些灰白色小点,俗称“锡汗”。
33.焦炭:是将配制的煤在隔绝空气条件下,长时间(20h左右)高温(最高达1300℃左右)加热炼制而成的人工燃料。
34.冲天炉熔化区:是指金属料块从开始熔化到熔化完毕这一段炉身高度范围。
35.双联熔炼,即将冲天炉与电炉等其他熔化炉组合,冲天炉铁水经过其他熔炼炉升温及成分调接后才浇注。
三、填空题1.蠕墨铸铁的蠕化剂为镁钛合金、稀土镁钛合金或稀土镁钙合金等。
2.灰铸铁的金相组织由金属基体和片状石墨组成。
主要的金属基体形式有珠光体、铁索体及珠光体加铁素体三种。
3.可锻铸铁种类;1)黑心可锻铸铁:KTH300 - 06:2)珠光体可锻铸铁KTZ450-06: 3)白心可锻铸铁KTB380-124.获得合乎要求的白口铸铁是生产可锻铸铁的前提,所以选择好化学成分,保证铸铁浇铸后获得白口铁组织非常重要。
5.石墨形态因结晶条件不同而有七种基本类型,即球状、团状、团絮状、蠕虫状、水草状、开花状和片状。
在片状石墨中又可分为A、B、C、D、E、F六种形状。
6.珠光体:奥氏体冷却到共析点以下即发生共析发应,一方面析出共析渗碳体,一方面转变为α-Fe,二者共同组成的共析体就是珠光体。
7.渗碳体:由一个C原子和三个Fe原子组成的化合物Fe3C称为渗碳体。
晶格结构:复杂正交。
8.莱氏体:共晶反应时与奥氏体同时生长的渗碳体称为共晶渗碳体,它和共晶奥氏体形成的机械混合物称为莱氏体8.高温莱氏体:727℃以上,奥氏体与渗碳体,以Le表示。
低温莱氏体:727℃以下,珠光体与渗碳体,以L'e表示。
9.二元磷共晶:Fe3P+α-Fe:三元磷共晶:Fe3P+Fe3C +α-Fe。
10.强化孕育条件,细化共晶团,控制磷共晶数量有可能得到断续网状磷共晶结构,既保持较高的强度又有较好的耐磨性。
11.奥氏体中碳的脱溶:普通成分的铸铁,共晶转变后组织为含碳约2.10%的奥氏体加石墨。
如继续冷却,奥氏体中的含碳量将减小,卧二次石墨的形式析出。
12.目前各国使用的商业孕育剂和专利孕育剂的品种繁多,归纳起来可分两大类:石墨化孕育剂和稳定化孕育剂。
13.现在我国生产的球墨铸铁普通用稀土硅铁镁合金作为球化剂,所以也称稀土镁球墨铸铁14.磷在球墨铸铁中有严重的偏析倾向,易在晶界处形成磷共晶,严重降低球墨铸铁的韧性。
磷还增大球墨铸铁的缩松倾向。
15.适用于球墨铸铁生产的优质铁液应该是高温,低硫、磷含量和低的杂质含量(如氧及反球化元素含量等)。
16.在球墨铸铁生产中,除会产生一般的铸造缺陷外,还经常会产生一些特有的缺陷。
主要有:缩孔及缩松、夹渣、皮下气孔、石墨漂浮及球化衰退等。
17.根据铸态组织中有无自由渗碳体,而可分别采取高温石墨化退火和低温石墨化退火的两种方式。
18.根据正火温度的不同,可分为高温完全奥氏体化正火以及部分奥氏体化正火。
19.蠕虫状石墨是介于片状石墨及球状石墨之间的中问状态类型石墨,它既有在共晶团内部石墨互相连续的片状石墨的组织特征,又有石墨头部较圆、其位向特点和球状石墨相似的特征。
20. 蠕墨铸铁的化学成分与球墨铸铁的成分要求基本相似,即高碳、低磷。
低硫,一定的硅、锰含量21.铸铁中石墨的润滑能力,与金属基体有关,与石墨的形状、尺寸和分布有关,还与摩擦面承载大小有关。
22.一种优质抗磨材料应该在保证不破裂的前提下尽量提高耐磨性,因此要求材料有强韧性好的基体和足够数量的硬化相。
23.材料在巨大的局部载荷作用下不损坏的关键是金属基体,只有强韧性特别好的基体才能够承受恶劣的工作条件,如马氏体、奥氏体,贝氏体都属于抗磨铸铁选择的基体。
要避免铁索体、珠光体、石墨等显微组织存在。
其次,要有足够数量的硬化相。
24.铸钢材料的品种从普通碳钢、低合金钢至高合金钢。
25.碳钢铸件热处理的目的是细化晶粒,消除魏氏体(或网状组织)和消除铸造应力。
热处理方法有退火、正火或正火加回火。
26.纯铝具有银白色金属光泽,密度小(2.72),熔点低(660.4℃),导电、导热性能优良。
27. Al-Si系铸造铝合金,称硅铝明。
其中ZL102(ZAlSi12)是含12%Si的铝硅二元合金,称为简单硅铝明.加入其他合金元素的铝硅铸造合金称复杂(或特殊)硅铝明。
28.时效处理又分为自然时效及人工时效两大类。
29.金属镁的密度(约 1.7 g/cm3小于铝,镁合金也比铝合金轻,密度约为锅台金的 2/3。
镁合金具有很高的比强度、比剐度和比弹性模量,且切削加工性能极好。
30.影响冲天炉内焦炭燃烧过程的因素,主要是送人炉内空气的数量和质量用温度、含氧量等人焦炭的质量(灰分、块度)等。
31. 焦炭灰分含量不仅影响焦炭中固定碳含量及发热值大小,而且影响焦炭的燃烧速度。
32.一般随焦炭块度增大,氧化带扩大,燃烧温度增高。
33.空气温度对燃烧过程的影响一方面是空气带人的物理热,使反应的热量增大,从而提高燃烧温度。
34。
若风量不变、层焦用量增加时(焦耗增大)原来熔化一批金属炉料消耗的底焦少于补充的层焦,使底焦高度上升,但这样并不会造成底焦高度无限升高,经过3~5批料后,底焦高度会在一个新的高度上稳定下来,原因是层焦增多会使还原带增高,并使还原反应更充分,造成C2。
含量降低,CO含量升高,燃烧系数ηv下降。
35.当送风量增加时,燃烧速度加快,熔化一批料所消耗的底焦量增多,若层焦量不变时,必然造成底焦高度逐渐下降36.当送风量减少时,由于消耗的底焦量少于层焦补充量,底焦高度就会逐渐升高37. 当底焦高度过低,使还原带高度减少到零时,这种平衡过程就无法再进行,冲天炉的熔炼过程就无法继续进行下去,生产中若出现这种情况时,必须立即打炉,否则会出现冻炉或结渣等严重事故。
38.当焦耗过高而风量又不足时,可能出现底焦高度太高,使得还原带上部的温度低于还原反应的温度(1200℃)这时底焦顶面以上的金属炉料无法熔化,冲天炉的熔炼过程便出现暂时中断现象。
39.预热区是指从加料口到金属炉料加热到平均熔点(一般取1200℃)为止的区间。
40.过热区是冲天炉热交换最薄弱的环节。
冲天炉的总热效率为35%左右,其中预热带热效率为50%—60%,熔化带为50%左右,但过热带的热效率仅为6%~8%。
41.酸性冲天炉熔炼可能出现增硅现象,不可能出现增锰现象。
42.碳作为铸铁的重要元素,在冲大炉熔炼过程中,既被O2,CO2和FeO氧化损失,又因焦炭中的碳向铁水溶解而增加。
43.水冷冲大炉的关键结构是在冲天炉底焦区的钢板炉壳加冷却水套,形成水冷炉壁,其结构有内冷式和外冷式两种44.常用的双联熔炼有冲天炉一电炉(包括电弧炉、有芯工频妒、无芯工频炉)熔炼。
45.冲天炉的预热及熔化的热效率高(约60%)但过热效率低(约7%)而电炉的过热效率高(>60%)故冲天炉一电炉双联熔炼可晟大限度地降低能耗和成本,并获得高质量的铁水。