涂装线设计方案
涂装线设计方案

喷烤漆设备设计方案山东亮光涂装科技有限公司二0一一年十一月方案一一、设计依据1.工件名称:机械管件2.最大工件尺寸:长5米×直径0.5米最大工件重量:800公斤左右3.加热方式:电加热或燃气型(天然气)4.工作温度:60℃左右5.漆雾处理方式:干式处理6.废气处理方式:干式(湿式)7.送风形式:上送风下回风8.热量利用方式:循环式利用9.输送形式:根据工件和客户所需由地面道轨平车和轻型悬挂输送机相结合。
10.设备尺寸:内径,喷涂部,6米×3.5米×2.5米,烘干部长8米×2.5米×2.5米二、设计目标主要承担工件的喷漆和烘干工作,使工件表面形成致密的耐蚀膜层,并具有良好的外观质量,以提高产品的防腐性能和装饰性能。
喷烤漆室具备通风、照明、空气净化、加热、升温和保温、漆雾处理功能,同时还具备故障报警和废气治理功能。
三、设计思想概述及原则1、喷烤漆室在设计时严格按照国家有关劳动、卫生、消防及环保等方面的标准进行,如:涂装作业安全性方面符合GB6514-1995、GB14444-93《涂装作业安全规程喷漆室、烘干室安全技术规定》;涂装作业卫生性方面符合TJ36-2002《涂装作业安全规程》;环保方面符合GB16297-2002《大气污染物综合排放标准》。
2、设备美观大方,满足产品使用要求,运行可靠,操作简便,维护保养方便易行。
3、选用的配套件、材料及电器元件均质量可靠,技术领先,其中关键配套件和材料(如:顶部过滤棉、燃烧器和电器主控件)均选用国内外知名品牌,确保设备的整体性能和质量。
4、控制系统充分考虑系统相互之间的连锁性,系统阻力都采取了保护措施,避免设备事故发生。
5、我们的设备是全新设备,包括室体、过滤材料,风机及所有零部件。
四、输送形式1.根据需方工件的形状和大小、重量及生产的需求,设计两套输送形式:(1)地面道轨平车输送方式(输送大型管件)。
(2)上吊链式轻型悬挂输送式。
涂装生产线项目设计方案
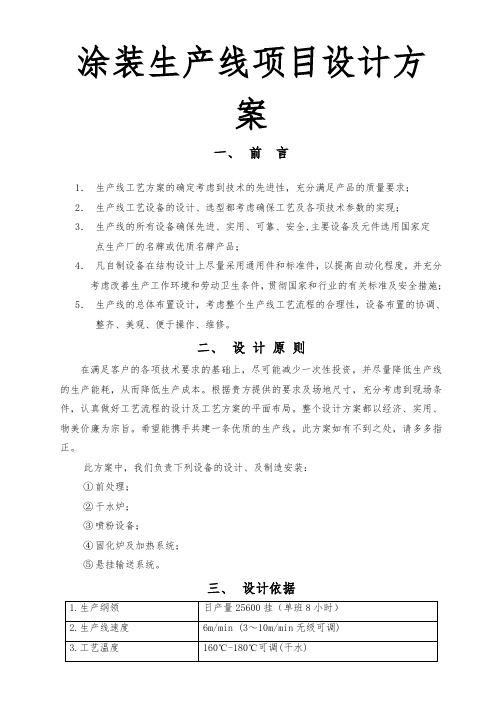
涂装生产线项目设计方案一、前言1.生产线工艺方案的确定考虑到技术的先进性,充分满足产品的质量要求;2.生产线工艺设备的设计、选型都考虑确保工艺及各项技术参数的实现;3.生产线的所有设备确保先进、实用、可靠、安全,主要设备及元件选用国家定点生产厂的名牌或优质名牌产品;4.凡自制设备在结构设计上尽量采用通用件和标准件,以提高自动化程度,并充分考虑改善生产工作环境和劳动卫生条件,贯彻国家和行业的有关标准及安全措施;5.生产线的总体布置设计,考虑整个生产线工艺流程的合理性,设备布置的协调、整齐、美观、便于操作、维修。
二、设计原则在满足客户的各项技术要求的基础上,尽可能减少一次性投资,并尽量降低生产线的生产能耗,从而降低生产成本。
根据贵方提供的要求及场地尺寸,充分考虑到现场条件,认真做好工艺流程的设计及工艺方案的平面布局。
整个设计方案都以经济、实用、物美价廉为宗旨。
希望能携手共建一条优质的生产线。
此方案如有不到之处,请多多指正。
此方案中,我们负责下列设备的设计、及制造安装:①前处理;②干水炉;③喷粉设备;④固化炉及加热系统;⑤悬挂输送系统。
三、设计依据4.加热方式 柴油燃烧机加热5.燃 料 柴油6.主要工件 钢铁管件7.工件尺寸 最大:L1800mm ×φ6 0mm ×δ0.7~1.8mm 8.喷涂种类 粉体 9.车间高度 Hmin=7.0米 10.输送形式悬挂输送四、 生产线工艺流程主脱脂(浸3min,50~60℃)预脱脂(喷2min)上 件中和(喷1min)固化(19min,200~220℃)水洗(喷1min)工艺流程水洗(喷1min)磷化(浸2min)除锈(浸2min,45~50℃)水洗(浸1min)水洗(喷1min)纯水洗(喷1min)滴 水冷却(5min)自动喷粉手动补粉水洗(浸1.5min)表调(喷1min)干水(9min,160~180℃)冷 却下 件五、 生产线各设备的组成一)前处理前处理规格:L59.1m W1.1H5.35m (喷淋) L108.2mW1.1H2.7m (浸泳)前处理工艺采用常温工艺,主体全部采用不锈钢板,喷淋管采用PVC 管,骨架采用普通型材。
涂装生产流水线制造方案
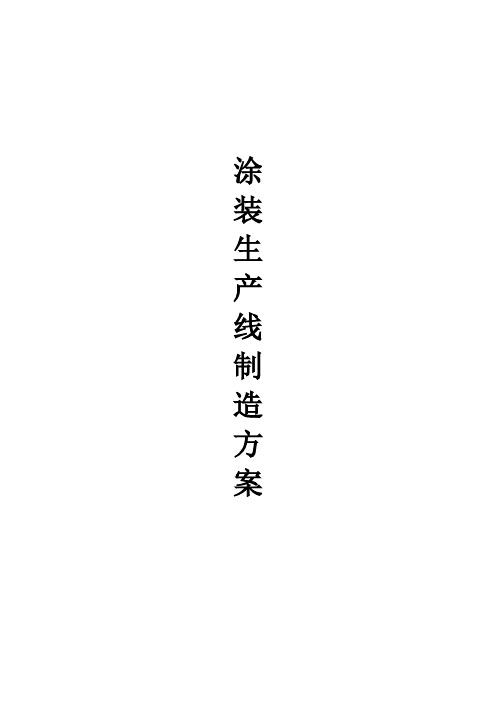
涂装生产线制造方案第一篇粉末涂装生产设计基本条件总体设计方案●涂装工件要求:●设计要求:●动力能源条件(用户负责提供)●业务范围:A.整套涂装线平面图纸B.厂内设备制作C.现场设备安装D.设备调试E.设备维护保养●粉体线涂装工艺流程:喷塑线:人工上件→喷淋前处理→预烘干→喷塑→固化→自然冷却→人工下件●流水线工艺参数表:●所需涂装设备:第二篇:前处理系统数量:1套 工艺参数表: V=2.5m/min联合前处理生产线制作规范:1前处理设备总成约为:42m×1.4m×8m(L×W×H)。
2为防止窜液,各工艺段之间有滴液区设计合理,各工序间的进出口设有可调节隔断板,以确保各不同工序段之间不窜液。
3液槽采用主、副结构,不锈钢双层过滤网,以除去液槽申的杂质,从而减少喷嘴和水泵的堵塞,为保持液槽的美观和易于清洁,槽沿和槽盖均采用不锈钢材料制作;4液槽底部做成倾斜结构,便清除槽内的溶液及槽底部沉积的污垢;液槽槽底克服焊缝腐蚀和漏液问题。
5喷淋装置由喷淋泵、开启阀门、调节阀门、压力表、喷淋主管、立喷管和万向球头喷嘴所组成。
主管——主管---- 阀门——泵(不锈钢)立管——主管(不锈钢)喷嘴一一立管(PP)●前处理工艺流程及参数流程:预脱脂——主脱脂——水洗——磷化——水洗●脱脂段第三篇:烘道系统●脱水烘道:数量:1套●脱水烘道设计参数:脱水烘道热能系统规范:脱水烘道炉体明细表:烘道结构特征:1炉体脱水烘道采用手工岩棉拼装板结构,散热面积小,保温性能好,焦炭加热,使炉内得到清洁的热空气,使整个炉体结构严谨、美观。
2送风系统热风经过循环风管,在引风机的作用下,将热风从烘道底部送入,均匀分布在整个炉内,从顶部抽风,再从烘道底部送入,实现内置式的热风循环结构。
3温控系统炉体的热风循环系统采用负抽风送风,在风管上设置均布的出风口,使炉内部温度分布均匀。
当温度低于设定温度时,循环风机开始工作,当温度高于设定温度时,循环风机停止工作。
涂装线改造工程方案
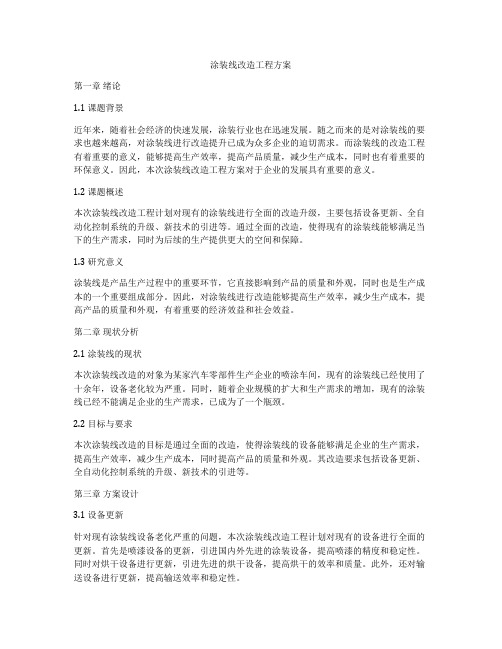
涂装线改造工程方案第一章绪论1.1 课题背景近年来,随着社会经济的快速发展,涂装行业也在迅速发展。
随之而来的是对涂装线的要求也越来越高,对涂装线进行改造提升已成为众多企业的迫切需求。
而涂装线的改造工程有着重要的意义,能够提高生产效率,提高产品质量,减少生产成本,同时也有着重要的环保意义。
因此,本次涂装线改造工程方案对于企业的发展具有重要的意义。
1.2 课题概述本次涂装线改造工程计划对现有的涂装线进行全面的改造升级,主要包括设备更新、全自动化控制系统的升级、新技术的引进等。
通过全面的改造,使得现有的涂装线能够满足当下的生产需求,同时为后续的生产提供更大的空间和保障。
1.3 研究意义涂装线是产品生产过程中的重要环节,它直接影响到产品的质量和外观,同时也是生产成本的一个重要组成部分。
因此,对涂装线进行改造能够提高生产效率,减少生产成本,提高产品的质量和外观,有着重要的经济效益和社会效益。
第二章现状分析2.1 涂装线的现状本次涂装线改造的对象为某家汽车零部件生产企业的喷涂车间,现有的涂装线已经使用了十余年,设备老化较为严重。
同时,随着企业规模的扩大和生产需求的增加,现有的涂装线已经不能满足企业的生产需求,已成为了一个瓶颈。
2.2 目标与要求本次涂装线改造的目标是通过全面的改造,使得涂装线的设备能够满足企业的生产需求,提高生产效率,减少生产成本,同时提高产品的质量和外观。
其改造要求包括设备更新、全自动化控制系统的升级、新技术的引进等。
第三章方案设计3.1 设备更新针对现有涂装线设备老化严重的问题,本次涂装线改造工程计划对现有的设备进行全面的更新。
首先是喷漆设备的更新,引进国内外先进的涂装设备,提高喷漆的精度和稳定性。
同时对烘干设备进行更新,引进先进的烘干设备,提高烘干的效率和质量。
此外,还对输送设备进行更新,提高输送效率和稳定性。
3.2 全自动化控制系统的升级为了提高涂装线的生产效率和稳定性,本次涂装线改造工程计划对全自动化控制系统进行升级。
(完整版)涂装生产线设计方案
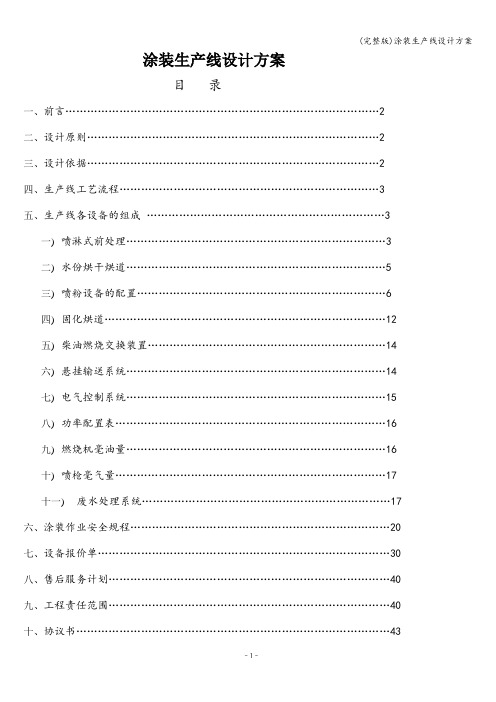
涂装生产线设计方案目录一、前言 (2)二、设计原则 (2)三、设计依据 (2)四、生产线工艺流程 (3)五、生产线各设备的组成 (3)一)喷淋式前处理 (3)二)水份烘干烘道 (5)三)喷粉设备的配置 (6)四)固化烘道 (12)五)柴油燃烧交换装置 (14)六)悬挂输送系统 (14)七)电气控制系统 (15)八)功率配置表 (16)九)燃烧机毫油量 (16)十)喷枪毫气量 (17)十一)废水处理系统 (17)六、涂装作业安全规程 (20)七、设备报价单 (30)八、售后服务计划 (40)九、工程责任范围 (40)十、协议书 (43)一、前言1.生产线工艺方案的确定考虑到技术的先进性,充分满足产品的质量要求;2.生产线工艺设备的设计、选型都考虑确保工艺及各项技术参数的实现;3.生产线的所有设备确保先进、实用、可靠、安全,主要设备及元件选用国家定点生产厂的名牌或优质名牌产品;4.凡自制设备在结构设计上尽量采用通用件和标准件,以提高自动化程度,并充分考虑改善生产工作环境和劳动卫生条件,贯彻国家和行业的有关标准及安全措施;5.生产线的总体布置设计,考虑整个生产线工艺流程的合理性,设备布置的协调、整齐、美观、便于操作、维修。
二、设计原则在满足客户的各项技术要求的基础上,尽可能减少一次性投资,并尽量降低生产线的生产能耗,从而降低生产成本.根据贵方提供的要求及场地尺寸,充分考虑到现场条件,认真做好工艺流程的设计及工艺方案的平面布局。
整个设计方案都以经济、实用、物美价廉为宗旨.希望能携手共建一条优质的生产线。
此方案如有不到之处,请多多指正.此方案中,我们负责下列设备的设计、及制造安装:①前处理;②干水炉;③喷粉设备;④固化炉及加热系统;⑤悬挂输送系统。
三、设计依据2。
生产线速度 6m/min (3~10m/min 无级可调) 3.工艺温度 160℃—180℃可调(干水) 4。
加热方式 柴油燃烧机加热 5。
燃 料 柴油 6.主要工件 钢铁管件7。
涂装生产流水线制造方案
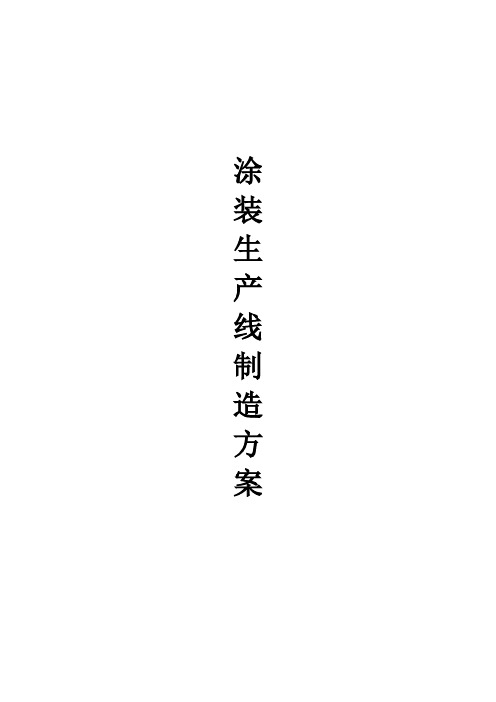
涂装生产线制造方案第一篇粉末涂装生产设计基本条件总体设计方案●涂装工件规定:●设计规定:●动力能源条件(用户负责提供)●业务范围:A.整套涂装线平面图纸B.厂内设备制作C.现场设备安装D.设备调试E.设备维护保养●粉体线涂装工艺流程:喷塑线:人工上件→喷淋前解决→预烘干→喷塑→固化→自然冷却→人工下件●流水线工艺参数表:●所需涂装设备:第二篇:前解决系统数量:1套 工艺参数表: V=2.5m/min联合前解决生产线制作规范:1前解决设备总成约为:42m×1.4m×8m(L×W×H)。
2为防止窜液,各工艺段之间有滴液区设计合理,各工序间的进出口设有可调节隔断板,以保证各不同工序段之间不窜液。
3液槽采用主、副结构,不锈钢双层过滤网,以除去液槽申的杂质,从而减少喷嘴和水泵的堵塞,为保持液槽的美观和易于清洁,槽沿和槽盖均采用不锈钢材料制作;4液槽底部做成倾斜结构,便清除槽内的溶液及槽底部沉积的污垢;液槽槽底克服焊缝腐蚀和漏液问题。
5喷淋装置由喷淋泵、启动阀门、调节阀门、压力表、喷淋主管、立喷管和万向球头喷嘴所组成。
主管——主管---- 阀门——泵(不锈钢)立管——主管(不锈钢)喷嘴一一立管(PP)●前解决工艺流程及参数流程:预脱脂——主脱脂——水洗——磷化——水洗●脱脂段第三篇:烘道系统●脱水烘道:数量:1套●脱水烘道设计参数:脱水烘道热能系统规范:脱水烘道炉体明细表:烘道结构特性:1炉体脱水烘道采用手工岩棉拼装板结构,散热面积小,保温性能好,焦炭加热,使炉内得到清洁的热空气,使整个炉体结构严谨、美观。
2送风系统热风通过循环风管,在引风机的作用下,将热风从烘道底部送入,均匀分布在整个炉内,从顶部抽风,再从烘道底部送入,实现内置式的热风循环结构。
3温控系统炉体的热风循环系统采用负抽风送风,在风管上设立均布的出风口,使炉内部温度分布均匀。
当温度低于设定温度时,循环风机开始工作,当温度高于设定温度时,循环风机停止工作。
汽车涂装生产线设计方案
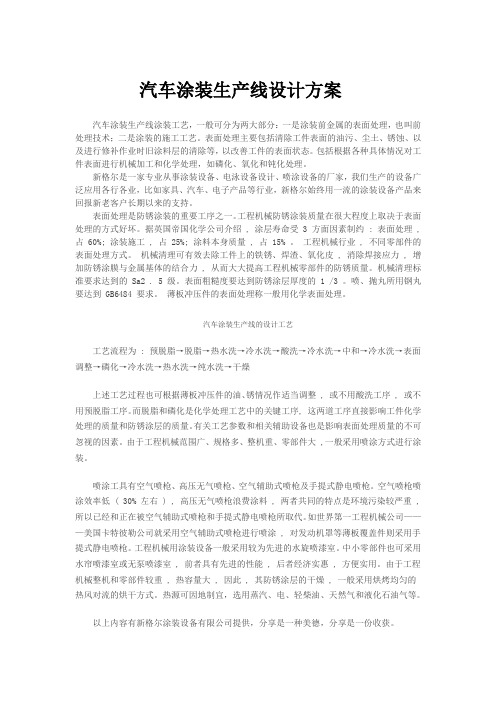
汽车涂装生产线设计方案汽车涂装生产线涂装工艺,一般可分为两大部分:一是涂装前金属的表面处理,也叫前处理技术;二是涂装的施工工艺。
表面处理主要包括清除工件表面的油污、尘土、锈蚀、以及进行修补作业时旧涂料层的清除等,以改善工件的表面状态。
包括根据各种具体情况对工件表面进行机械加工和化学处理,如磷化、氧化和钝化处理。
新格尔是一家专业从事涂装设备、电泳设备设计、喷涂设备的厂家,我们生产的设备广泛应用各行各业,比如家具、汽车、电子产品等行业,新格尔始终用一流的涂装设备产品来回报新老客户长期以来的支持。
表面处理是防锈涂装的重要工序之一。
工程机械防锈涂装质量在很大程度上取决于表面处理的方式好坏。
据英国帝国化学公司介绍 , 涂层寿命受 3 方面因素制约 : 表面处理 , 占 60%; 涂装施工 , 占 25%; 涂料本身质量 , 占 15% 。
工程机械行业 , 不同零部件的表面处理方式。
机械清理可有效去除工件上的铁锈、焊渣、氧化皮 , 消除焊接应力 , 增加防锈涂膜与金属基体的结合力 , 从而大大提高工程机械零部件的防锈质量。
机械清理标准要求达到的Sa2 . 5 级。
表面粗糙度要达到防锈涂层厚度的 1 /3 。
喷、抛丸所用钢丸要达到 GB6484 要求。
薄板冲压件的表面处理称一般用化学表面处理。
汽车涂装生产线的设计工艺工艺流程为 : 预脱脂→脱脂→热水洗→冷水洗→酸洗→冷水洗→中和→冷水洗→表面调整→磷化→冷水洗→热水洗→纯水洗→干燥上述工艺过程也可根据薄板冲压件的油、锈情况作适当调整 , 或不用酸洗工序 , 或不用预脱脂工序。
而脱脂和磷化是化学处理工艺中的关键工序, 这两道工序直接影响工件化学处理的质量和防锈涂层的质量。
有关工艺参数和相关辅助设备也是影响表面处理质量的不可忽视的因素。
由于工程机械范围广、规格多、整机重、零部件大 ,一般采用喷涂方式进行涂装。
喷涂工具有空气喷枪、高压无气喷枪、空气辅助式喷枪及手提式静电喷枪。
整机补漆涂装线设计方案书
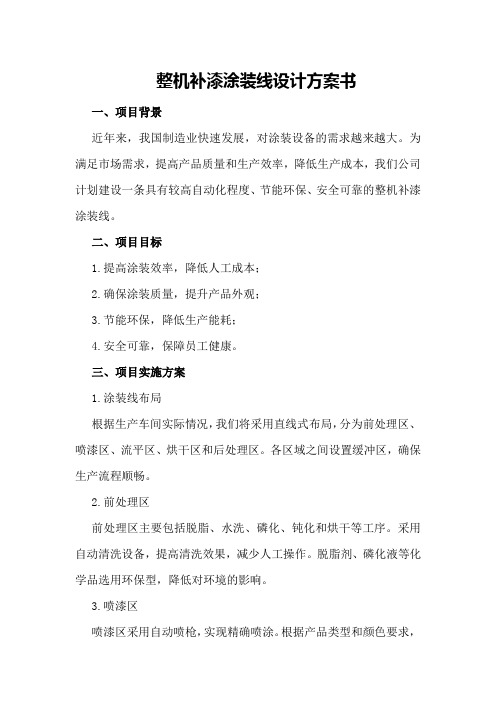
整机补漆涂装线设计方案书一、项目背景近年来,我国制造业快速发展,对涂装设备的需求越来越大。
为满足市场需求,提高产品质量和生产效率,降低生产成本,我们公司计划建设一条具有较高自动化程度、节能环保、安全可靠的整机补漆涂装线。
二、项目目标1.提高涂装效率,降低人工成本;2.确保涂装质量,提升产品外观;3.节能环保,降低生产能耗;4.安全可靠,保障员工健康。
三、项目实施方案1.涂装线布局根据生产车间实际情况,我们将采用直线式布局,分为前处理区、喷漆区、流平区、烘干区和后处理区。
各区域之间设置缓冲区,确保生产流程顺畅。
2.前处理区前处理区主要包括脱脂、水洗、磷化、钝化和烘干等工序。
采用自动清洗设备,提高清洗效果,减少人工操作。
脱脂剂、磷化液等化学品选用环保型,降低对环境的影响。
3.喷漆区喷漆区采用自动喷枪,实现精确喷涂。
根据产品类型和颜色要求,选用合适的喷枪和涂料。
喷漆室采用封闭式设计,确保喷漆过程中产生的废气得到有效处理。
4.流平区流平区设置在喷漆区与烘干区之间,用于确保涂料在烘干前达到一定的流平效果。
采用红外线加热,提高流平效果。
5.烘干区烘干区采用高温烘干设备,确保涂料在短时间内固化。
烘干设备选用节能型,降低能耗。
6.后处理区后处理区主要包括打磨、抛光、检验等工序。
采用自动打磨设备,提高打磨效果。
检验合格后,产品进入包装环节。
7.自动化控制系统涂装线采用自动化控制系统,实现各工序的自动化控制。
系统具备故障诊断、数据采集、生产调度等功能,提高生产效率。
8.环保措施(1)选用环保型涂料;(2)采用高效节能烘干设备;(3)设置废气处理设施,确保废气排放符合国家标准;(4)定期检测生产现场空气质量,保障员工健康。
9.安全措施(1)设置防护栏、安全警示标志;(2)定期进行安全培训,提高员工安全意识;(3)配备消防设备,制定应急预案;(4)加强生产现场管理,确保生产秩序。
四、项目实施计划1.项目筹备阶段:完成项目可行性研究、方案设计、设备采购等前期工作;2.设备安装阶段:完成设备安装、调试、验收等工作;3.生产调试阶段:完成生产线试运行、优化生产流程等工作;4.正式生产阶段:进入批量生产,实现生产目标。
自动化涂装线的设计及控制
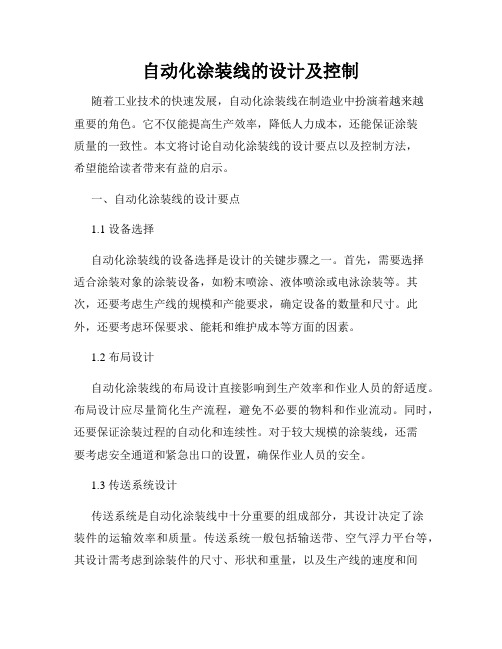
自动化涂装线的设计及控制随着工业技术的快速发展,自动化涂装线在制造业中扮演着越来越重要的角色。
它不仅能提高生产效率,降低人力成本,还能保证涂装质量的一致性。
本文将讨论自动化涂装线的设计要点以及控制方法,希望能给读者带来有益的启示。
一、自动化涂装线的设计要点1.1 设备选择自动化涂装线的设备选择是设计的关键步骤之一。
首先,需要选择适合涂装对象的涂装设备,如粉末喷涂、液体喷涂或电泳涂装等。
其次,还要考虑生产线的规模和产能要求,确定设备的数量和尺寸。
此外,还要考虑环保要求、能耗和维护成本等方面的因素。
1.2 布局设计自动化涂装线的布局设计直接影响到生产效率和作业人员的舒适度。
布局设计应尽量简化生产流程,避免不必要的物料和作业流动。
同时,还要保证涂装过程的自动化和连续性。
对于较大规模的涂装线,还需要考虑安全通道和紧急出口的设置,确保作业人员的安全。
1.3 传送系统设计传送系统是自动化涂装线中十分重要的组成部分,其设计决定了涂装件的运输效率和质量。
传送系统一般包括输送带、空气浮力平台等,其设计需考虑到涂装件的尺寸、形状和重量,以及生产线的速度和间距要求。
为了保证涂装质量,传送系统还应设计成稳定可靠,避免产生颤动和碰撞。
二、自动化涂装线的控制方法2.1 PLC控制自动化涂装线的控制通常采用可编程逻辑控制器(PLC)作为核心控制器。
PLC能够根据预设的程序和逻辑条件自动控制设备的运行和涂装过程。
通过PLC,可以实现对传送系统、喷涂设备、温度控制装置等的统一控制和调度,确保整个涂装过程的自动化和稳定性。
2.2 人机界面为了方便操作和监控自动化涂装线的运行,人机界面成为必不可少的一部分。
通过人机界面,操作员可以实时了解设备状态、涂装过程参数和报警信息,同时还可以进行参数调整和设备故障排除。
人机界面设计应简洁清晰,使操作员能够轻松掌握涂装线的运行情况。
2.3 传感器技术传感器技术在自动化涂装线中起到了至关重要的作用。
(完整版)涂装流水线方案设计指引

※方案设计指引※一、设计数据:1. 工件名称:2. 工件材质:3. 标准工件尺寸: mm(L) * mm(W) * mm(H)4. 最大工件尺寸: mm(L) * mm(W) * mm(H)5. 运输带标准速度: mm/min( ~ m/min可调)6. 吊挂节距: mm7. 设计产量:件/小时(通常我们按标准工件计算,最大工件只考滤通过,是不计产量)注:以上1~6项客户必须提供第3项标准工件尺寸及第4项最大工件尺寸第5项设计线速与第7项设计产量客户必须提供其中的一项第1项工件名称与第2项工件材质尽量让客户提供第6项吊挂节距由我们根据工件大小,模拟而定出(链条的最小节距后有详细资料)所用到的公式:设计线速(mm/min)= 设计产量(件/h)/60/n(件/挂)* 节距(mm)设计产量(件/h)= 设计线速(mm/min)/节距(mm)* 60 * n(件/挂)二、工艺流程:尽量让客户提供,我们也有标准工艺(见标准报价)三、设备设计要求:1.喷淋式前处理:1.1长度计算:A.工式艺段长度= 设计线速(mm/min)* 工艺时间(min)+ 900mmB.出入口段长:1)当工件长度≦1,500mm时,长度为1,500mm2)当工件长度≧1,500mm时,长度为≧工件长度C.滴水段长度:1)当工件长度≦1,500mm时,长度为1,000~1,500mm2)当工件长度≧1,500mm时,长度为≧工件长度D. 棚体宽度= 工件宽度+1,000mmE. 棚体高度= 工件高度+2,600mm(水缸高+挂具+工件到喷嘴间隙),仅供参考!F. 每排喷嘴个数= (工件高度/300)*2+(工件宽度/300)*2(取整数)G. 喷管排数= 线速*工艺时间/300+1(取整数)H. 水泵流量= 喷嘴个数*喷嘴流量(注:超过水泵最大流量就要多加一台)I. 水缸大小= 水泵流量*水泵个数*1.5倍(药齐缸)水泵流量*水泵个数*2倍(水洗缸)1.2配置要求:A. 加热段棚体要配抽气风机B. 直喷直排有水缸,直喷无水缸C. 铁磷化必须配沉渣缸,大小同磷化缸,锌磷化无须配沉渣缸D. 酸洗一般不要放在在线处理1.3设计公式:A. 水缸加热功率:1.轻柴油及电加热热功率(KW)={水缸容积(USGAL)*1.0(系数)*8.35(系数)*温差[升温(华氏)-室温(华氏)]}÷[3412(系数)*升温时间(小时)]2.蒸氯加热热耗量(KG/H)={水缸容积(L)*4.2(系数)*温差[升温(摄氏)-室温(摄氏)]}*1.15÷[2100(系数)*升温时间]2. 浸入式前处理(运输带式):1.1工艺段长度计算:两端斜坡长度(mm)+设计线速(mm/min)*时间(min)(斜坡长度需模拟工件爬坡,运输带爬坡角度为30度)1.2水缸高度计算:工件高度+650mm(工件到缸底+工件到缸面+水缸厚度) ,仅供参考!1.3设计公式:A. 水缸加热功率:1.轻柴油及电加热热功率(KW)={水缸容积(USGAL)*1.0(系数)*8.35(系数)*温差[升温(华氏)-室温(华氏)]}÷[3412(系数)*升温时间(小时)]2.蒸氯加热热耗量(KG/H)={水缸容积(L)*4.2(系数)*温差[升温(摄氏)-室温(摄氏)]}*1.15÷[2100(系数)*升温时间]3. 浸入式前处理(吊葫芦及龙门式):1.1:A 吊篮装件个数=产量(件/小时)/60 * 周期(根据工艺流程及时间而定)B 吊篮大小为工件在吊篮叠放大小C 设计产量=吊篮装件个数/周期*601.2水缸长宽计算:吊篮长宽各加150~200mm1.3水缸高度计算:吊篮高度+650mm(吊篮到缸底+吊篮到缸面+水缸厚度) ,仅供参考!1.4设计公式:A. 水缸加热功率:1.轻柴油及电加热热功率(KW)={水缸容积(USGAL)*1.0(系数)*8.35(系数)*温差[升温(华氏)-室温(华氏)]}÷[3412(系数)*升温时间(小时)]2.蒸氯加热热耗量(KG/H)={水缸容积(L)*4.2(系数)*温差[升温(摄氏)-室温(摄氏)]}*1.15÷[2100(系数)*升温时间]4. 烘干/固化炉:1.1长度计算:设计线速(mm/min)* 时间(min)/n轨(注:要模拟工件在炉内不碰撞)1.2高度计算:A.桥式炉:工件高度(mm)+桥体高度(一般2.6米到3米)+扣板厚度*2(上下)+挂具长度(一般为1米)+风槽(250mm~300mm)+工件到风槽间距(250mm)B.座地式炉:工件高度(mm)+炉脚(250mm)+扣板厚度*2(上下)+挂具长度(一般为1米)+风槽(250mm~300mm)+工件到风槽间距(250mm)C.支承式炉:工件高度(mm)+支承杆及路轨(550mm)+工件到炉顶(300mm)+扣板厚度*2(上下)+炉脚(600mm)1.3 扣板厚度(mm)= 根据温度而定,A.温度≦80℃,扣板厚度为50mmB. 80℃<温度≦150mm,扣板厚度为100mmC. 150℃<温度≦250mm,扣板厚度为100mmD. 250℃<温度≦600mm,一般用框架式,炉厚300mm1.4 烘炉功率计算(KW)= 炉内胆体积(包括炉内风槽)*25或18*温度*1.15*1.15/860注:炉内胆体积超过100m3时总功率*70%,25指天然气、轻柴油等燃值,18指电、蒸气等燃值5. 喷粉柜:1.1 粉柜的长度根据线速及工件的长度而定1.2 粉柜的宽度根据工件的宽度而定1.3 粉柜的高度=脚(700mm)+开口斜度(300mm*2)+开口高度,数值仅供参考!1.4 单面自动喷枪数量= 线速度(英尺/分)* 工件高度(英尺)A系数(参考数27) * 23系数A=192.3*上粉率(50%) =27(参考数)1.5*膜厚(2.36mil)1.5 滤芯个数(=[(手喷位截面*个数)+出入口截面*2个+顶开口截面]*10.7639*120500cfm(注:滤芯个数为双整数)6.水濂喷房:1.1 水濂喷房的长度根据线速及工件的长度及工位要求而定1.2 水濂喷房工件到水幕的距离为1,500mm左右1.3 恒压室的高度一般在700~1,800mm之间(视客户的厂房高度及供风精度而定)1.4 抽风量:工件截面面积*风速(0.5~0.8m/s)*3,600*0.589= cfm7.中央供风系统:1.1 中央供风系统大小根据风量大小及温湿度要求而定1.2 供风量计算:所有设备抽风量+其他区域空间体积 * 换气次数一些区域换气频率:调油、供油房换气频率 50~60次/h烘炉换气频率10~20次/h流平室换气频率20~30次/h上下货区等换气频率20次/h1.3 研磨线抽风量(20个工位):7,000m3/h1.4 冰水机功率计算有附表1.5 隔间柜式空调大小计算:隔间体积(m3)/50 = x HP空调1.6 一体化风箱(外购):尺寸(760mm*760mm),过风量(1,000m3/h)8.运输链条:1.1 支承链目前我们常用的有三款:A.双层基链 B.长寿链 C.滑撬式(最新款)A双层基链:最小节距76.2mmB长寿链: 最小节距76.2mmC滑撬式: 最小节距25.4mm1.2 吊挂链目前我们常用的有五款:A. 5T吊挂链 B. 5T吊挂加重型 C. 7T吊挂链D. X-348型E. X-458型A.5T吊挂链:最小节距150mm,单点最大吊重25KgB.5T吊挂加重型:最小节距150mm,单点最大吊重35KgC.7T吊挂链:最小节距200mm,单点最大吊重50Kg(路轨开口向上)D.X-348型:最小节距76.6mm,单点最大吊重100KgE.X-458型:最小节距102.4mm,单点最大吊重200Kg1.3 支承线运输带长超过150m就要加一组起动、拉紧1.4 吊挂线运输带长超过200m就要加一组起动、拉紧9.设计常用单位换算:1M3=1,000L 1L=1,000ML 1加仑= 4,54609 L 1英尺=12英寸1英寸=25.4mm 1英尺= 305mm1KW=860Kcal/h 1美国冷吨(USRT)=3.517KW 1cfm=0.589m3/h1美国冷吨(USRT)=3024大卡/时1KW=3412BTU/h(英热/h)1KW=0.28434美国冷吨(USRT) 1Kcal/h=0.001163KW1摄氏度(℃)=(华氏°F-32)/1.8。
涂装流水线技术方案

江苏丹阳金城配件有限公司汽车塑料件涂装生产线技术规划书南京达克罗机械设备工程有限公司汽车塑料件涂装生产线技术规划书总目录第壹部分:设计原则第贰部分:设计依据第叁部分:设备描述一、喷漆生产线1、设计纲领2、设备清单2.1风淋室2.2手自动一体式静电除尘室2.3喷漆室2.4烘干炉2.5地面反向输送机2.6集中净化送风装置2.7彩板隔离间二、流平室、整厂净化隔离板1、设计纲领2、设备描述三、电控系统1、设计纲领2、设备清单第肆部分:备品备件清单第伍部分: 售后服务计划第陆部分:责任界定第柒部分:所提供技术资料第捌部分:双方施工范围分工第玖部分:培训计划第拾部分:设备验收单第拾壹部分:部分客户目录第壹部分:设计原则1、本自动化涂装线设计原则本着贵公司的品牌定位和发展战略为基础,生产线设备以经济、实用、环保为基本设计原则,努力提高性价比,设计科学合理,可持续发展为设计准则:2、满足汽车塑料件的高品质喷涂生产所需设备及环境的要求;3、设备整体外观设计、制造体现美观大方,富于时代感,能体现现代企业的风貌,汽车内饰件生产企业的典范喷涂线;4、整厂生产线的整体布局流畅,布局空间分割合理、物流通畅、操作维护方面简便等特点。
5、整厂设计能满足自动化程度高、能耗低的要求,低成本运行的特点;6、整厂涂装生产线工序完善,工艺设备先进;操作条件安全,良好,车间环境清洁;按同期同行业产品先进水平设计制造。
第贰部分:设计依据1、喷涂工件:汽车保险杠及内侧板2、工件尺寸:最大综合工件L2100 mm×W1000mm×H950mm3、工件重量:最大30kg4、工件材质:ABS,PP5、产能:400件/年,10h/天,6、厂房尺寸:详见平面图7、供风要求:喷房内三级无尘供风(初效+中效+顶棚过滤棉)8、温湿度要求:无要求9、喷涂输送方式:地面反向工艺链;手动线10、生产节拍:喷涂时间:1-2min11、工艺链运行速度:2m/min,变频控制12、电源电压:三相五线AC380V±5%,50HZ±2%;13、工艺:上件→自动除尘→手动除尘→手动喷底漆→底漆流平(8min)→手动喷面漆→面漆流平(8min)→固化烘干(RT-80℃, 35min)→冷却→下件第叁部分:设备描述一、喷漆生产线:1、设计纲领:1.1本涂装生产线整体布局合理美观,物流、参观、维修通道畅通,车间无二次污染,气流通畅,操作环境舒适,改善涂装环境,可充分满足高品质喷涂生产要求。
涂装线整体方案规划要求

涂装线整体方案规划要求引言涂装线是一种用于工业生产中的重要设备,广泛应用于汽车制造、家具制造、机械制造等领域。
涂装线的设计和规划直接影响到生产效率和产品质量。
因此,制定一套合理的涂装线整体方案规划要求对于企业的发展至关重要。
本文将深入探讨涂装线整体方案规划要求的关键要点,并提供一些建议。
环境要求涂装线的运行环境是其正常运行的基础。
因此,首先需要考虑涂装车间的环境要求。
涂装车间应具备以下特点:1. 温度和湿度控制:涂料施工过程对环境的温湿度要求较高,应保持在理想的温湿度范围内,以确保涂料的施工质量。
2. 通风设施:涂装车间应具备良好的通风设施,排除涂料挥发性有机物的气味和有害气体,保证员工健康和车间的安全。
3. 防尘设施:涂装车间应采取措施防止尘土和杂质进入涂装线,以确保产品表面光滑和强度。
设备要求涂装线的设备是实现产品涂装过程的核心。
因此,良好的设备要求是涂装线整体方案规划的重要部分。
以下是涂装线设备的一些基本要求:1. 自动化程度高:在涂装线的规划中,应优先考虑实现自动化的程度,减少人工操作的需求,提高生产效率和产品质量。
2. 稳定可靠:涂装线设备应具备稳定可靠的特点,能够长时间持续运行,降低设备故障和停机的可能性。
3. 环保节能:涂装线设备应具备节能环保的特点,降低能耗和环境污染,符合可持续发展的要求。
4. 操作方便:涂装线的设备操作应简单方便,提高操作者的工作效率,降低操作错误的可能性。
工艺要求涂装线的工艺要求直接关系到涂装效果的好坏。
在制定涂装线整体方案规划时,应考虑以下工艺要求:1. 施工质量:涂装线的整体方案规划应确保施工质量达到要求,包括涂层的厚度、附着力、表面光滑度等。
2. 工艺流程:涂装线的规划要符合工艺流程的要求,包括预处理、涂装、烘干等环节,以确保每个环节的顺利进行。
3. 涂装材料选择:涂装线的整体方案规划要求考虑涂装材料的选择,包括涂料的种类、颜色、质量等。
4. 涂装周期控制:涂装线的整体方案规划要求合理控制涂装周期,避免生产周期过长或过短,以满足市场需求。
自动化涂装生产线设计
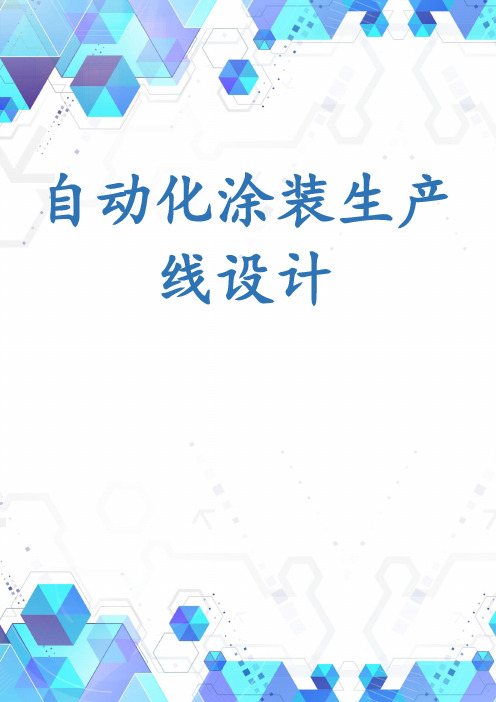
自动化涂装生产线设计自动化涂装生产线设计自动化涂装生产线是一种高效、精确且可持续的制造技术,广泛应用于各个行业。
本文将按照逐步思考的方式,为你介绍自动化涂装生产线的设计。
第一步:确定涂装需求在设计自动化涂装生产线之前,需要明确涂装的需求。
这包括确定所需涂装的材料、颜色、涂布厚度以及涂装表面的形状和尺寸等。
这些信息将有助于确定所需的涂装设备和涂装工艺。
第二步:选择涂装设备基于涂装需求,可以选择适合的涂装设备。
常见的涂装设备包括涂布机、喷涂机、电泳涂装机等。
选择涂装设备时,需要考虑设备的处理能力、涂布均匀度、节能性能以及设备的可靠性等因素。
第三步:设计生产线布局自动化涂装生产线的布局设计是关键。
布局设计应考虑到涂装设备的相对位置、物料的流动路径以及工人的工作空间。
合理的布局设计可以提高涂装效率、降低物料运输成本,并确保工人的安全和舒适。
第四步:确定自动化控制系统自动化涂装生产线需要一个可靠的自动化控制系统来监控和控制涂装过程。
这个系统可以根据预设的参数和要求,自动调整涂装设备的运行状态,确保涂装的质量和效率。
自动化控制系统还可以实现设备的远程监控和故障诊断,提高设备的可靠性和维护效率。
第五步:优化涂装工艺涂装工艺的优化是提高涂装效率和质量的关键。
通过分析涂装过程中的关键参数和环节,可以找到改进涂装工艺的方法。
例如,在涂装前对物料进行预处理,优化喷涂角度和喷涂速度,使用高效的干燥设备等。
这些改进措施可以提高涂装的一致性和降低涂装的成本。
第六步:进行测试和调试在正式投产之前,需要对自动化涂装生产线进行测试和调试。
这包括验证涂装设备的运行状态和自动化控制系统的性能,以及检查产品的涂装效果和质量。
通过测试和调试,可以及时发现和解决问题,确保生产线的正常运行。
第七步:培训和运营当自动化涂装生产线正式投入运营后,需要对工人进行培训,使其熟悉设备的操作和维护。
同时,需要建立起设备的定期维护和保养机制,确保生产线的长期稳定运行。
涂装车间技术方案

技术方案项目单位:xx—喷涂车间涂装线喷涂车间涂装线方案描述一项目整体设计原则涂装生产线方案的设计充分考虑到技术的先进性,充分满足喷涂产品的质量、产能要求,确保工艺及各项技术参数的实现,并力求实用、安全、可靠,可以有效控制及提高产品涂装质量。
涂装生产线上凡自制设备在结构设计上,尽量采用通用件和标准件,以提高自动化程度;涂装生产线的总体布置设计,充分考虑工艺流程系统的合理性,设备布置协调、整齐、美观,便于操作、维修。
在满足各项技术要求的基础上,尽量减少一次性投资成本;并尽可能降低涂装生产线的能耗。
1.1 根据既定的车间面积,使产能最大、质量最佳化。
1.2 设备是全新设备(包括所有零部件、元器件和各种附件)。
1.3 工件经过抛丸处理后,表面抛丸质量为Sa2.5级、粗糙度为Rz=25~40。
1.4 喷漆在喷漆室进行,喷漆室采用水旋式漆雾净化装置净化漆雾,喷漆室采用上送风、下抽风的气流组织形式,保证喷漆室内各处的气流成均匀层流状态,各室体内的送、排风电器带变频功能,可以用于调整室体内的气压平衡。
1.5 烘干室采用燃气四元体间接加热,烘干室采用直通式结构。
1.6 喷漆室废气通过水旋漆雾净化后直接高空排放;烘干室废气通过四元体处理后高空排放。
1.7 所有室体两端设电动对开门,供工件出入;室体两侧面各开有两扇安全作业门,供操作工人出入及设备人员检修。
电动门与输送系统连锁自动开关。
1.8 设备外观颜色,符合甲方指定颜色的要求、或在验收前涂装成甲方指定颜色。
1.9 室体骨架与输送骨架必须使用同一骨架系统,所有骨架材料均做防锈处理,骨架之间采用焊接或螺栓连接。
二设计依据2.1. 设备用途工件的喷涂,烘干等处理。
2.3. 工件涂装前表面质量抛丸后达Sa2.5~3.0级,粗糙度Rz=25~452.4. 输送方式葫芦+地面台车2.5. 涂装材料溶剂型油漆2.6. 涂装部位工件外表面2.7. 固化条件30min/80~100℃2.8. 厂房 150×482.9. 产能自动喷漆线一 100件/班自动喷漆线二 1111件/班大件喷漆室 10件/班大件烘干室 10件/班伸缩式喷漆室 10件/班三工艺流程方案四涂装线主要设备设备包含喷丸室、喷丸清理室、自动和人工喷漆室、烘干室、强冷室、空调风机、排风风机、漆雾处理系统、电控系统。
(完整版)涂装流水线方案设计指引
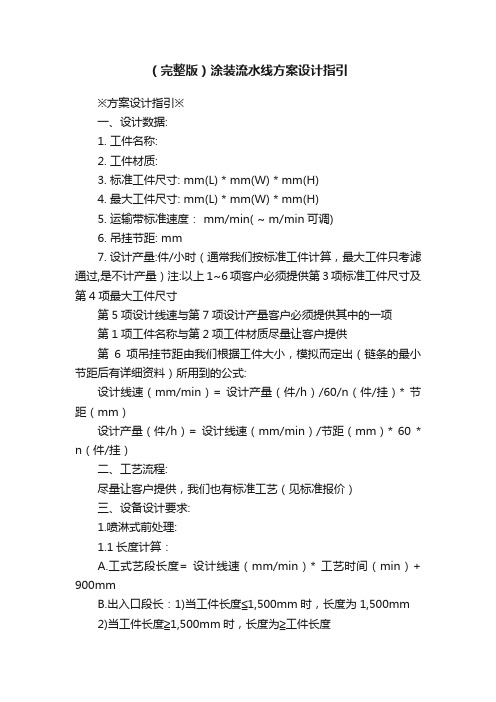
(完整版)涂装流水线方案设计指引※方案设计指引※一、设计数据:1. 工件名称:2. 工件材质:3. 标准工件尺寸: mm(L) * mm(W) * mm(H)4. 最大工件尺寸: mm(L) * mm(W) * mm(H)5. 运输带标准速度: mm/min( ~ m/min可调)6. 吊挂节距: mm7. 设计产量:件/小时(通常我们按标准工件计算,最大工件只考滤通过,是不计产量)注:以上1~6项客户必须提供第3项标准工件尺寸及第4项最大工件尺寸第5项设计线速与第7项设计产量客户必须提供其中的一项第1项工件名称与第2项工件材质尽量让客户提供第6项吊挂节距由我们根据工件大小,模拟而定出(链条的最小节距后有详细资料)所用到的公式:设计线速(mm/min)= 设计产量(件/h)/60/n(件/挂)* 节距(mm)设计产量(件/h)= 设计线速(mm/min)/节距(mm)* 60 * n(件/挂)二、工艺流程:尽量让客户提供,我们也有标准工艺(见标准报价)三、设备设计要求:1.喷淋式前处理:1.1长度计算:A.工式艺段长度= 设计线速(mm/min)* 工艺时间(min)+ 900mmB.出入口段长:1)当工件长度≦1,500mm时,长度为1,500mm2)当工件长度≧1,500mm时,长度为≧工件长度C.滴水段长度:1)当工件长度≦1,500mm时,长度为1,000~1,500mm2)当工件长度≧1,500mm时,长度为≧工件长度D. 棚体宽度= 工件宽度+1,000mmE. 棚体高度= 工件高度+2,600mm(水缸高+挂具+工件到喷嘴间隙),仅供参考!F. 每排喷嘴个数= (工件高度/300)*2+(工件宽度/300)*2(取整数)G. 喷管排数= 线速*工艺时间/300+1(取整数)H. 水泵流量= 喷嘴个数*喷嘴流量(注:超过水泵最大流量就要多加一台)I. 水缸大小= 水泵流量*水泵个数*1.5倍(药齐缸)水泵流量*水泵个数*2倍(水洗缸)1.2配置要求:A. 加热段棚体要配抽气风机B. 直喷直排有水缸,直喷无水缸C. 铁磷化必须配沉渣缸,大小同磷化缸,锌磷化无须配沉渣缸D. 酸洗一般不要放在在线处理1.3设计公式:A. 水缸加热功率:1.轻柴油及电加热热功率(KW)={水缸容积(USGAL)*1.0(系数)*8.35(系数)*温差[升温(华氏)-室温(华氏)]}÷[3412(系数)*升温时间(小时)]2.蒸氯加热热耗量(KG/H)={水缸容积(L)*4.2(系数)*温差[升温(摄氏)-室温(摄氏)]}*1.15÷[2100(系数)*升温时间]2. 浸入式前处理(运输带式):1.1工艺段长度计算:两端斜坡长度(mm)+设计线速(mm/min)*时间(min)(斜坡长度需模拟工件爬坡,运输带爬坡角度为30度)1.2水缸高度计算:工件高度+650mm(工件到缸底+工件到缸面+水缸厚度) ,仅供参考!1.3设计公式:A. 水缸加热功率:1.轻柴油及电加热热功率(KW)={水缸容积(USGAL)*1.0(系数)*8.35(系数)*温差[升温(华氏)-室温(华氏)]}÷[3412(系数)*升温时间(小时)]2.蒸氯加热热耗量(KG/H)={水缸容积(L)*4.2(系数)*温差[升温(摄氏)-室温(摄氏)]}*1.15÷[2100(系数)*升温时间]3. 浸入式前处理(吊葫芦及龙门式):1.1:A 吊篮装件个数=产量(件/小时)/60 * 周期(根据工艺流程及时间而定)B 吊篮大小为工件在吊篮叠放大小C 设计产量=吊篮装件个数/周期*601.2水缸长宽计算:吊篮长宽各加150~200mm1.3水缸高度计算:吊篮高度+650mm(吊篮到缸底+吊篮到缸面+水缸厚度) ,仅供参考!1.4设计公式:A. 水缸加热功率:1.轻柴油及电加热热功率(KW)={水缸容积(USGAL)*1.0(系数)*8.35(系数)*温差[升温(华氏)-室温(华氏)]}÷[3412(系数)*升温时间(小时)]2.蒸氯加热热耗量(KG/H)={水缸容积(L)*4.2(系数)*温差[升温(摄氏)-室温(摄氏)]}*1.15÷[2100(系数)*升温时间]4. 烘干/固化炉:1.1长度计算:设计线速(mm/min)* 时间(min)/n轨(注:要模拟工件在炉内不碰撞)1.2高度计算:A.桥式炉:工件高度(mm)+桥体高度(一般2.6米到3米)+扣板厚度*2(上下)+挂具长度(一般为1米)+风槽(250mm~300mm)+工件到风槽间距(250mm)B.座地式炉:工件高度(mm)+炉脚(250mm)+扣板厚度*2(上下)+挂具长度(一般为1米)+风槽(250mm~300mm)+工件到风槽间距(250mm)C.支承式炉:工件高度(mm)+支承杆及路轨(550mm)+工件到炉顶(300mm)+扣板厚度*2(上下)+炉脚(600mm)1.3 扣板厚度(mm)= 根据温度而定,A.温度≦80℃,扣板厚度为50mmB. 80℃<温度≦150mm,扣板厚度为100mmC. 150℃<温度≦250mm,扣板厚度为100mmD. 250℃<温度≦600mm,一般用框架式,炉厚300mm1.4 烘炉功率计算(KW)= 炉内胆体积(包括炉内风槽)*25或18*温度*1.15*1.15/860注:炉内胆体积超过100m3时总功率*70%,25指天然气、轻柴油等燃值,18指电、蒸气等燃值5. 喷粉柜:1.1 粉柜的长度根据线速及工件的长度而定1.2 粉柜的宽度根据工件的宽度而定1.3 粉柜的高度=脚(700mm)+开口斜度(300mm*2)+开口高度,数值仅供参考!1.4 单面自动喷枪数量= 线速度(英尺/分)* 工件高度(英尺)A系数(参考数27) * 23系数A=192.3*上粉率(50%) =27(参考数)1.5*膜厚(2.36mil)1.5 滤芯个数(=[(手喷位截面*个数)+出入口截面*2个+顶开口截面]*10.7639*120500cfm(注:滤芯个数为双整数)6.水濂喷房:1.1 水濂喷房的长度根据线速及工件的长度及工位要求而定1.2 水濂喷房工件到水幕的距离为1,500mm左右1.3 恒压室的高度一般在700~1,800mm之间(视客户的厂房高度及供风精度而定)1.4 抽风量:工件截面面积*风速(0.5~0.8m/s)*3,600*0.589= cfm7.中央供风系统:1.1 中央供风系统大小根据风量大小及温湿度要求而定1.2 供风量计算:所有设备抽风量+其他区域空间体积 * 换气次数一些区域换气频率:调油、供油房换气频率 50~60次/h烘炉换气频率10~20次/h流平室换气频率20~30次/h上下货区等换气频率20次/h1.3 研磨线抽风量(20个工位):7,000m3/h1.4 冰水机功率计算有附表1.5 隔间柜式空调大小计算:隔间体积(m3)/50 = x HP空调1.6 一体化风箱(外购):尺寸(760mm*760mm),过风量(1,000m3/h)8.运输链条:1.1 支承链目前我们常用的有三款:A.双层基链B.长寿链C.滑撬式(最新款)A双层基链:最小节距76.2mmB长寿链: 最小节距76.2mmC滑撬式: 最小节距25.4mm1.2 吊挂链目前我们常用的有五款:A. 5T吊挂链 B. 5T吊挂加重型C. 7T吊挂链D. X-348型E. X-458型A.5T吊挂链:最小节距150mm,单点最大吊重25KgB.5T吊挂加重型:最小节距150mm,单点最大吊重35KgC.7T吊挂链:最小节距200mm,单点最大吊重50Kg(路轨开口向上)D.X-348型:最小节距76.6mm,单点最大吊重100KgE.X-458型:最小节距102.4mm,单点最大吊重200Kg1.3 支承线运输带长超过150m就要加一组起动、拉紧1.4 吊挂线运输带长超过200m就要加一组起动、拉紧9.设计常用单位换算:1M3=1,000L 1L=1,000ML 1加仑= 4,54609 L 1英尺=12英寸1英寸=25.4mm 1英尺= 305mm1KW=860Kcal/h 1美国冷吨(USRT)=3.517KW 1cfm=0.589m3/h1美国冷吨(USRT)=3024大卡/时1KW=3412BTU/h(英热/h) 1KW=0.28434美国冷吨(USRT) 1Kcal/h=0.001163KW1摄氏度(℃)=(华氏°F-32)/1.8。
涂装生产线方案

涂装生产线方案引言涂装生产线是现代工业中广泛应用的一种生产方式,它能够高效地完成产品表面的涂装任务,提高产品质量和生产效率。
本文将针对涂装生产线的设计、布置和优化等方面进行详细阐述。
设计方案生产线布置在设计涂装生产线时,需考虑以下几个主要因素: 1. 产品尺寸和形状:根据不同产品的尺寸和形状,合理规划生产线的长度和宽度,确保产品能够顺利通过涂装生产线。
2. 工艺流程:根据涂装工艺流程,确定每个工位的位置和顺序,确保产品在每个工位上都能得到相应的涂装处理。
3. 作业效率:合理安排每个工位的距离和人员配置,最大程度地提高生产效率。
4. 安全性:确保生产线的安全性,提供紧急停机装置和防护措施。
设备选择选择适合的涂装设备对于涂装生产线的高效运作至关重要。
常用的涂装设备有:- 喷涂设备:如手动喷枪、自动喷涂机器人等 - 涂胶设备:如涂胶机、涂胶机器人等 - 烘干设备:如烘干炉、烘干室等 - 气体处理设备:如除尘器、废气处理设备等选择设备时,需根据产品材质、涂装工艺和产能要求进行综合评估,确保设备的稳定性、可靠性和适用性。
运营管理涂装生产线的运营管理对于保证生产线的正常运行和提高生产效率至关重要。
以下是几个重要的运营管理要点: 1. 供应链管理:确保原材料和涂装剂的供应充足,并与供应商建立良好的合作关系。
2. 质量控制:建立涂装产品质量控制体系,确保涂装质量符合要求。
3. 设备维护:定期对涂装设备进行维护和保养,确保设备的正常运行和使用寿命。
4. 培训与人员管理:针对涂装生产线操作人员进行培训,提高操作技能和工作效率。
优化措施为了提高涂装生产线的效率和降低生产成本,可以采取以下优化措施: 1. 自动化技术应用:引入自动化设备,如喷涂机器人、自动输送线等,减少人力投入,提高生产效率。
2. 进行流程优化:通过研究涂装生产线中每个环节的工艺参数和操作步骤,找出优化空间,并调整相应的工艺参数和操作步骤,提高生产效率和涂装质量。
喷粉喷塑涂装线设计方案
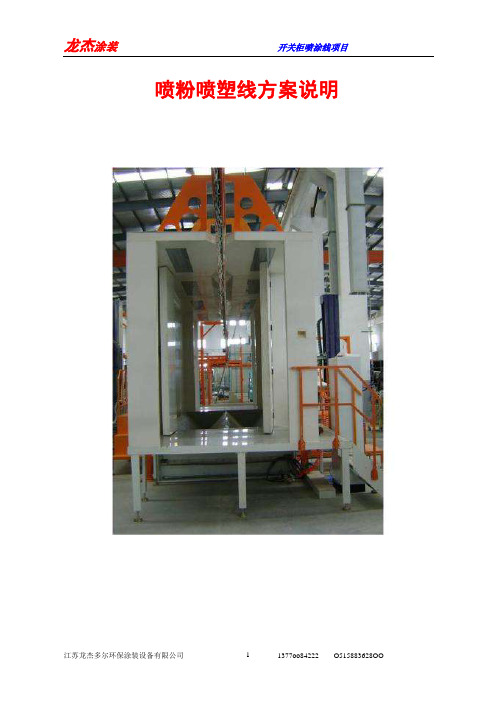
喷粉喷塑线方案说明一、项目名称开关柜喷涂线二、项目内容全线由前处理、水分烘干、喷粉系统、喷、喷漆系统、固化炉、输送设备及相关设备的电控系统组成。
以上工程量均为设计、制造、安装、调试以及包括人员培训和技术服务的“交钥匙”工程,并且保证与用户做好相应的配合工作。
三、设计思想根据用户要求及提供的条件,充分应用国内外先进的技术和工艺,精心选用国内外名优配套设备,在确保质量的前提下降低投资成本,使该喷涂线居国内同行业的先进水平,涂装产品达国标或企标。
二、设计依据1、工件参数:⑴工件名称:开关柜⑵工件材质:Q235A⑶工件最大尺寸:3000L×1800W×2400H⑷工件最大重量:60Kg1、生产纲领:最大工件≥50件/月2、喷涂要求:⑴内、外喷涂;⑵考虑喷粉和喷漆;⑶喷漆后自然干燥;3、输送方式:前处理用电动葫芦,脱水烘干后用人工输送;4、吊挂方式:前处理大工件工件双点吊挂,小工件用框盛装处理;喷漆和喷粉时大件放在台车上喷涂,操作高位时人站在操作台上喷涂;喷小件时吊挂在轨道上喷涂后放在台车上进行烘干。
5、加热方式:电6、使用区域:见平面布置图三、工艺方案设计1、工艺流程:工艺流程表2、生产速度:因生产量较小,此线选用间歇式生产方式,可节约投入,降低运行成本。
四、设备设计说明1、前处理设备:前处理由槽体、抽风装置、搅拌装置、电动葫芦、输送装置、立柱及相关电控等部分组成。
槽体采用水泥及砖砌结构,同时在酸洗及磷化内加设玻璃钢做内胆。
槽体底部最低处设有排污口,方便废液排污之用,离槽边150mm左右设有溢流口,便于液体过多时溢流。
(其中槽体由用户自制)抽风装置采用玻璃钢防腐风机固定在车间之外,确保脱脂槽液、磷化槽液、酸洗槽液,挥发的蒸汽不扩散到车间中,直接由抽风机排出室外。
前处理药液选用常温药液无需加热。
搅拌系统:在脱脂、表调、磷化槽内设有搅拌装置,搅拌采用压缩空气搅拌,确保溶液均匀,不产生沉淀。
工程机械涂装线设计方案浅析

工程机械涂装线设计方案浅析hc360慧聪网涂装与表面处理行业频道2004-07-08 14:31:521刖言涂装质量是影响产品竞争力的重要一环,在生产制造过程中起着举足轻重的地位。
利用该“双高一优”项目向开发区搬迁的契机,计划上一条现代化的涂装流水线。
在调研了部分工程机械厂家涂装线后,本着保证质量、满足能力需求、追求先进性和实用性相统一的原则,规划设计了该厂的大件涂装流水线方案。
2方案设计原则(1 )生产纲领:年产装载机5000台;(2 )每台整机折合成 4.5件结构大件计算;(3 )结构件产品特点:外形尺寸大、质量重、结构复杂;(4)双班制,全年工作日251天;3设计中具体问题的考虑3.1关于输送方式大件涂装线一般有三种输送方式:普通悬挂链、自行自动葫芦链和平台小车。
遵循能吊着不平放着的原则,此前常用的台车输送有以下两点不便:支撑点需补喷台车较矮,工件底面不易喷普通悬挂链输送的动力消耗小、维修方便,适用于大批量流水线作业,但其吊架链节是固定的,自由度小,不能针对单个工件进行升降运动。
采用自行电动葫芦输送方式,即无支撑点,且能升能降,方便喷涂,对年产5000台大型结构件涂装线,综合性能价格比最佳。
3.2前处理方法前处理方法主要有化学前处理法和喷抛丸法。
目前工程机械行业一般采用化学前处理法(如酸洗磷化)对小件进行前处理,而用喷抛丸法对大件进行前处理。
该厂主要是针对大件进行前处理,且处理量较大(按日产20台装载机,需处理的结构件有90件),采用喷丸处理存在工序能力不足的问题,因此选用通过式自动抛丸进行处理,由于工件较长,如采用工件静止在抛丸室中抛丸的方式,抛丸器个数会很多,采用电动葫芦吊着工件以慢速连续运行通过抛丸室的方式,在抛丸室工位电动葫芦自动变频,速度变为1.5-2m/mi n,从而保证工件的抛丸处理质量。
3.3涂料的选择当前工程机械涂料一般有两种类型,一类是使用耐候性很好的聚氨酯作为面漆,配以环氧富锌底漆,其整体防锈性能好,装饰性好,耐光、耐候、抗石击。
- 1、下载文档前请自行甄别文档内容的完整性,平台不提供额外的编辑、内容补充、找答案等附加服务。
- 2、"仅部分预览"的文档,不可在线预览部分如存在完整性等问题,可反馈申请退款(可完整预览的文档不适用该条件!)。
- 3、如文档侵犯您的权益,请联系客服反馈,我们会尽快为您处理(人工客服工作时间:9:00-18:30)。
喷烤漆设备设计方案山东亮光涂装科技有限公司二0一一年十一月方案一一、设计依据1.工件名称:机械管件2.最大工件尺寸:长5米×直径0.5米最大工件重量:800公斤左右3.加热方式:电加热或燃气型(天然气)4.工作温度:60℃左右5.漆雾处理方式:干式处理6.废气处理方式:干式(湿式)7.送风形式:上送风下回风8.热量利用方式:循环式利用9.输送形式:根据工件和客户所需由地面道轨平车和轻型悬挂输送机相结合。
10.设备尺寸:内径,喷涂部,6米×3.5米×2.5米,烘干部长8米×2.5米×2.5米二、设计目标主要承担工件的喷漆和烘干工作,使工件表面形成致密的耐蚀膜层,并具有良好的外观质量,以提高产品的防腐性能和装饰性能。
喷烤漆室具备通风、照明、空气净化、加热、升温和保温、漆雾处理功能,同时还具备故障报警和废气治理功能。
三、设计思想概述及原则1、喷烤漆室在设计时严格按照国家有关劳动、卫生、消防及环保等方面的标准进行,如:涂装作业安全性方面符合GB6514-1995、GB14444-93《涂装作业安全规程喷漆室、烘干室安全技术规定》;涂装作业卫生性方面符合TJ36-2002《涂装作业安全规程》;环保方面符合GB16297-2002《大气污染物综合排放标准》。
2、设备美观大方,满足产品使用要求,运行可靠,操作简便,维护保养方便易行。
3、选用的配套件、材料及电器元件均质量可靠,技术领先,其中关键配套件和材料(如:顶部过滤棉、燃烧器和电器主控件)均选用国内外知名品牌,确保设备的整体性能和质量。
4、控制系统充分考虑系统相互之间的连锁性,系统阻力都采取了保护措施,避免设备事故发生。
5、我们的设备是全新设备,包括室体、过滤材料,风机及所有零部件。
四、输送形式1.根据需方工件的形状和大小、重量及生产的需求,设计两套输送形式:(1)地面道轨平车输送方式(输送大型管件)。
(2)上吊链式轻型悬挂输送式。
2.地面轻轨平车输送主要是以在喷漆室底部和烘干室底部铺设15道轨两条,长度超出进出货门各6米,道轨与道轨之间的间距为0.8米,铺设完毕与地面平行,小车离地面0.5米,长度4米,承重能力2吨,人工输送,带扶手支撑。
3.轻型悬挂输送机:是由上面工字钢轨道悬挂下来的滑架,用牵引链条连接起来并由之驱动、输送的,载荷一般用吊具从滑架上悬挂下来,随着链子运转,悬挂输送机可安排在一个平面或多个平面上工作。
整体主要由驱动装置、牵引链条、张紧装置、滑架、轨道、电控柜、温度伸缩接头等组成。
4″道轨和458号链条普链,用于中等载荷的输送,每驱动装置的链条牵引力不超过1600,一般最大可定为1150。
单车承载600。
主要部件:链条、滑架、吊具、轨道(包括弯曲段)、张紧装置、驱动装置等分述如下:(1)链条:在悬挂输送机中,链条是传递动力的构件,链条选择是否得当直接影响输送机的使用寿命及性能。
(2)滑架:滑架的作用是承受物件、吊具及链条的重量。
在垂直弯曲段上还要承受链条张力的合力,并能够保证链条按轨道的线路运行。
滑架可分为空载、负载及重载。
滑架由滑架轮、轴承、压力式加油嘴、滑架支架、中间链片、连接螺栓、滑架附件等组成。
为了适应各工作条件,如冷、热、潮湿、污染等等和适应各种载荷的性质,如重量大小,体积大小等,选择最佳的滑架,来以最经济的和最安全可靠的手段,完成最大的工作量。
(3)常用吊具有“H”型、“T”型、挂钩型、挂环型等。
(4)轨道:轨道是输送机最重要的部件之一,因为它除了负担载荷的重量外,还要经受住滑架的摩擦,轨道分为直线段、水平弯曲段和垂直弯曲段。
直线轨段的标准长度为6m,4″悬挂输送机轨道为110,它是由中碳、中锰钢轧制而成,以保证有较高的强度和较好的耐磨性能。
固定接头的焊接强度不低于原强度,通过高混和业区的轨道要高温度伸缩接头。
由于轨道在加热炉或温度变化环境中易线膨胀,在这些地方安装轨道温度伸缩接头加以解决是必要的。
水平旋转段,必须使用一个光轮或一个滚子组转弯总成来将链条拉紧于轨道之下,这种方法特别适用于90或小于90的转弯,转弯大于90时,只要直径不过大,一般选用光轮为好。
当需要维修容易和摩擦损失最少时,应首选光轮转弯段,特别是在转弯段装在污秽和腐蚀严重的地方时。
由于链子在光轮上是被带着环绕转弯段而不像在滚子组转弯段时要逐节环绕固定的滚子移动,它使链条磨损减少,输送机运行平稳,这在输送机运行速度较高时,表现更为明显,光轮的集中润滑和间隔大的圆锥滚子轴承有较大的油脂腔和防止外物或污物进入的密封,使维修工作和磨擦损失减少到最低程度。
(5)张紧装置机:输送机都要张紧装置来保证链条张紧,补偿安装误差和链条拉力作用下的磨损及温差作用下引起的伸缩,保证驱动装置绕出点有一个初张力,在只有一台驱动装置的输送机中,也可以不用张紧装置我们将一个下降段安排在靠近驱动的地方而它又有足够的度差,保证随时能从驱动装置把松弛的链条拉紧。
人工调节张紧装置即螺杆型,它是调节输送机松驰链条的一种经济的方法,它可装用滚子组转弯或光轮转弯,结构上,除调节部分外,其余均与其它张紧装置一样。
(6)驱动装置:直线驱动装置可以安装于输送机系统上的任何地点,所以比一般角驱动装置有较大的灵活性。
一般来说,直线驱动装置的安装位置能更方便和有效地与张紧装置配合。
能使输送机载荷的分布更好。
工作条件:工作环境温度适用于60℃—+360℃,特殊要求时应加特殊润滑剂,设备在有粉尘环境中工作时应定期进行清理。
运行速度:0.15 -1.5,可调整,输送机功率 1.5。
五、设备组成系统说明1、设备目的:用于工件外表面喷漆。
2、工作原理:喷漆时,外部空气经进风口初级过滤棉过滤后送人漆房静压室内,再经过顶部过滤棉二次过滤净化后进入漆房作业空间,气流由上向下在工件周围形成风幕。
这时漆房内平均空载风速达0.25左右。
喷漆时产生的漆雾微粒不会在操作者呼吸带处停留,而随气流迅速下降,之后在排风机的作用下,气流经底部环保处理后由排风道高空排放,并且排出的气体符合GB16297-2002《大气污染物综合排放标准》。
烘干时,通过风机将外部新鲜空气经初级过滤网过滤后,通过电热远红外线与热交换器产生换热送入到漆房顶部,再经过过滤网二次过滤净化,热空气进入到烤房内,经底部的内循环作用,除吸进少量新鲜空气外,绝大部分热空气又被继续加热利用,送入到漆房内部,使得漆房内温度逐步升高,当温度达到设定温度时,加热器自动停止工作,当温度下降到设定温差时,又自动工作,使烤漆房温度保持恒定。
最后当烤漆时间达到设定的时间时,烤房自动关机,烤漆结束。
3、设备组成:本喷漆室用于工件喷漆和升温喷漆时扑捉漆雾、处理漆雾和废气治理功能,且严格按照国家有关劳动安全、卫生、消防及环保等方面的标准进行设计,通排风根据喷漆的工艺要求实施。
该设备主要由:室体、送风系统、排风系统、加热系统、空气过滤系统、照明系统、漆雾、废气处理系统、电控系统地轨平车输送和轻型悬挂输送系统等组成。
室体主要由:骨架、壁板、顶板、静压室、工件进出入门、安全门和地板格栅等系统组成。
骨架:由方钢管骨架、U型槽、纵横卡槽和顶梁等折弯焊接加工而成,以保证房体的牢固和可靠性。
壁板:采用保温板,保温板的内外壁板均为彩色镀锌钢板,中间层填充保温材料,内外板与保温材料整体压制而成一体,总厚度为75.根据工件尺寸5*0.5米,再考虑喷漆时操作空间,则喷漆室内尺寸(长*宽*高)6*3.5*2.5,烤漆室全部壁板采用拼装配式结构。
同时此板材已获得山东省消防产品登记备案证书,阻燃保温,请用户放心。
顶板:采用50厚保温板,结构同壁板说明。
静压室:室顶设有静压室,高600。
从供风系统送来的新鲜空气进入静压室,在静压室与操作室之间,铺有漆房专用C型钢顶网(能更好地防止灰尘掉落)及意大利2-600精密级亚高效过滤棉(详细参见空气过滤系统说明),风经过此棉后,气流流向操作间更平稳,避免了紊流现象的产生。
工件出入门:1套设备大门结构形式为手动折叠门,每扇门上均配装钢化玻璃观察窗,玻璃四周采用大门压条密封,每扇门之间用铸钢铰链连接,开启灵活,内侧配有大门插销和插销总成,操作方便,大门尺寸为(宽*高):2米*2.4米。
安全门:在室体纵向两侧各设安全门1套,以方便人员进出,安全门尺寸(宽×高):650×1850,安全门带机械压力锁,保证自动打开卸压。
地网格栅,为便于工件两侧、前后端面的喷涂,在室体底部设有格栅板,格栅板采用4*30扁钢和δ8圆钢焊接而成。
格栅有我公司根据W323型号自制,加工形成后全部热浸锌,这样可避免工件喷漆时装饰带划线、贴报纸产生的废报纸废胶带等进入地下构筑物部分。
格栅沉积的过喷涂泥清理建议可用脱漆剂进行化学脱除,然后清理,也可采用焚烧炉焚烧处理。
拖网:为方便底部玻璃纤维铺设,在地网格栅下设置拖网,用镀锌钢板和网片焊接而成。
送风系统:由新风段、初效过滤段、送风机段组成。
新风段:采用镀锌板组合而成,设置手动调节阀,可进行风量调节。
初效过滤段:设片式过滤器,过滤材料选用意大利进口材料,压框采用镀锌板制作,安装更换方便,并可重复使用。
送风机段:送风量的计算:根据国家有关标准,干式喷漆室空载风速一般要求在0.2-0.3左右,故*3600 式中:送风量,单位:m3送风截面积,单位:m2送风断面风速:单位:,取0.25则送风区截面积:6*3.5*0.25*3600=18900 m3,使室内有载空气流速达0.30 以上。
风机型号的确定:根据风量配置1组送风系统,每组配1台涂装专用节能环保降温型冷风机,使工作环境舒适,具体风机参数如下:风量:18900 m3,全压140,功率1.1排风系统:主要由环保箱、排风机箱、排风机、排风风道和排风风阀等组成。
喷漆时,为了将过滤后的空气高空排放,其风量计算如下:0.80.8*18900=15120 m3,因此本漆房配置1组排风系统,总排风量为17500 m3,从而保证喷漆质量。
环保箱:由槽钢焊接而成,内装M型活性炭。
详细见漆雾处理系统和废气系统说明。
排风机箱:由槽钢、角钢和镀锌板焊接而成,能够承载风机的重量。
排风机:配置1台轴流防爆排风机,功率 2.2,不粘漆,使用维修周期长,工作效率高。
同时也避免了漆雾经常堵塞风机现象的产生。
排风风道:管道高10米,以超出车间高度为准,由镀锌板和法兰组合而成。
排风风阀:在排风风管上设置手动调节阀,来调整风量的大小。
烘干室加热系统:采用电远红外线加热的方式。
根据最高温度60℃和温升要求,给此喷漆配置1组加热系统,每套采用56电远红外线管加热器,发热量为260000大卡/小时,和1台不锈钢板制作的热交换器,热交换率可达90%。
其中热风部分采用优质镀锌钢板和反光铝板,并内填岩棉保温材料,阻止热量损失。