机械结构优化设计概述
机械结构优化设计方法及其在产品开发中的应用
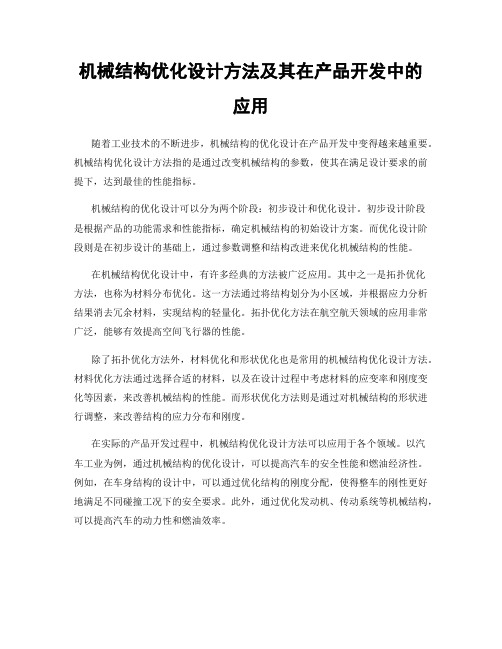
机械结构优化设计方法及其在产品开发中的应用随着工业技术的不断进步,机械结构的优化设计在产品开发中变得越来越重要。
机械结构优化设计方法指的是通过改变机械结构的参数,使其在满足设计要求的前提下,达到最佳的性能指标。
机械结构的优化设计可以分为两个阶段:初步设计和优化设计。
初步设计阶段是根据产品的功能需求和性能指标,确定机械结构的初始设计方案。
而优化设计阶段则是在初步设计的基础上,通过参数调整和结构改进来优化机械结构的性能。
在机械结构优化设计中,有许多经典的方法被广泛应用。
其中之一是拓扑优化方法,也称为材料分布优化。
这一方法通过将结构划分为小区域,并根据应力分析结果消去冗余材料,实现结构的轻量化。
拓扑优化方法在航空航天领域的应用非常广泛,能够有效提高空间飞行器的性能。
除了拓扑优化方法外,材料优化和形状优化也是常用的机械结构优化设计方法。
材料优化方法通过选择合适的材料,以及在设计过程中考虑材料的应变率和刚度变化等因素,来改善机械结构的性能。
而形状优化方法则是通过对机械结构的形状进行调整,来改善结构的应力分布和刚度。
在实际的产品开发过程中,机械结构优化设计方法可以应用于各个领域。
以汽车工业为例,通过机械结构的优化设计,可以提高汽车的安全性能和燃油经济性。
例如,在车身结构的设计中,可以通过优化结构的刚度分配,使得整车的刚性更好地满足不同碰撞工况下的安全要求。
此外,通过优化发动机、传动系统等机械结构,可以提高汽车的动力性和燃油效率。
在工程机械领域,机械结构的优化设计也起到了重要的作用。
例如,在挖掘机的臂杆结构设计中,通过优化材料分布和结构形状,可以提高挖掘机的工作效率和稳定性。
通过减少结构的自重,还可以减小机械的能耗和环境负荷。
此外,机械结构优化设计方法还可以应用于航空航天、能源等领域。
例如,在航空发动机的结构设计中,通过优化轴承和叶轮的结构,可以提高发动机的性能和可靠性;在风力发电机的叶片设计中,通过优化叶片结构的材料和几何形状,可以提高发电机的转化效率。
机械设计中的结构优化与几何优化

机械设计中的结构优化与几何优化在机械设计领域,为了提高产品的性能和效率,结构优化和几何优化是必不可少的过程。
结构优化旨在通过调整和改进机械结构的布局和材料分布,以达到最佳的结构性能。
而几何优化则通过调整机械零部件的外形和尺寸来优化其工作性能。
本文将介绍机械设计中的结构优化和几何优化的基本原理和方法。
一、结构优化结构优化是通过调整结构布局和材料分布来改进机械系统的性能。
在进行结构优化之前,需要先确定设计目标和设计约束。
设计目标可以是最小重量、最大刚度、最小变形等,而设计约束则包括尺寸限制、工艺要求、应力和应变的约束等。
常用的结构优化方法包括拓扑优化、参数优化和拟合优化。
拓扑优化是通过改变部件的形状和材料分布,来实现结构的最优化。
参数优化是在给定结构形状的基础上,通过改变参数的数值来优化结构性能。
拟合优化则是通过寻找合适的拟合曲线或曲面,以达到最佳的设计目标。
二、几何优化几何优化是通过调整机械零部件的外形和尺寸,来优化其工作性能。
几何优化旨在改变零部件的曲率、角度和尺寸,以提高其刚度、强度和流体动力性能等。
几何优化常用于飞行器、汽车和船舶等领域,以提高其运动性能和气动性能。
几何优化的方法主要包括形状优化、参数化优化和拓扑优化。
形状优化是通过改变零部件的曲率和角度,以改进其工作性能。
参数化优化则是在给定的几何模型上,通过改变参数的数值来优化零部件的形状和尺寸。
拓扑优化是通过拓扑结构的变化,来优化零部件的外形和分布。
三、结构优化和几何优化的应用结构优化和几何优化在机械设计中有着广泛的应用。
它们可以应用于飞行器设计中的翼型优化,以提高其升力和阻力性能;在汽车设计中的车身优化,以提高其安全性和运动性能;在船舶设计中的船体优化,以提高其稳定性和航行性能。
此外,结构优化和几何优化还可以应用于机械系统的动力学分析和热力学分析中。
通过优化结构和几何,在满足约束条件的前提下,可以使机械系统的动力学响应更加平稳且能量损失更小;在热力学分析中,优化后的结构和几何可以提高机械系统的热传导性能和热稳定性。
机械结构的优化设计

机械结构的优化设计1. 引言机械结构的优化设计是在满足特定功能和性能要求的前提下,通过改进结构形状、减轻重量、提高刚度等方式来提高机械产品的综合性能和竞争力。
优化设计能够有效降低产品制造成本、提高生产效率,并能够延长产品使用寿命,受到了广泛的关注和研究。
2. 优化设计的基本原理机械结构的优化设计基于优化理论和方法,主要包括以下几个方面的内容:2.1. 设计目标通过调整结构形状、材料选择、力学特性等因素,实现机械产品在性能、重量、刚度、安全性、可靠性等方面的优化目标。
设计目标的确定是进行优化设计的第一步,也是最关键的一步。
2.2. 设计变量设计变量是指可以在设计中进行调整和改变的参数,如材料的选择、结构的尺寸和形状等。
设计变量的选择需要考虑到各种约束条件和目标函数,以实现最佳的设计效果。
2.3. 约束条件约束条件是指设计中需要满足的各种限制条件,如结构的强度、刚度、稳定性、可制造性等。
在优化设计过程中,需要考虑约束条件的影响,以保证设计结果的可行性。
2.4. 目标函数目标函数是指优化设计中需要优化的性能指标,如重量、刚度、安全系数等。
目标函数的选择需要考虑到产品的实际使用情况和市场需求,以实现最佳的设计效果。
3. 优化设计方法机械结构的优化设计涉及到复杂的数学模型和计算方法,常用的优化设计方法包括以下几种:数值优化方法是目前应用最广泛的优化设计方法之一,主要包括遗传算法、粒子群算法、模拟退火算法等。
这些方法可以通过数学模型的计算和迭代,寻找最优解或近似最优解。
3.2. 拓扑优化方法拓扑优化方法是一种基于物理模型和材料力学原理的优化设计方法。
通过对结构的材料分布进行优化,实现结构的轻量化和刚度的提高,可以提高产品的性能和效果。
3.3. 多目标优化方法多目标优化方法是一种针对多个优化目标的设计方法,通过确定不同目标的权重和优先级,寻找多个目标的平衡点。
这种方法可以综合考虑多个性能指标,达到在各方面都取得较好效果的设计。
机械工程中的结构优化设计方法
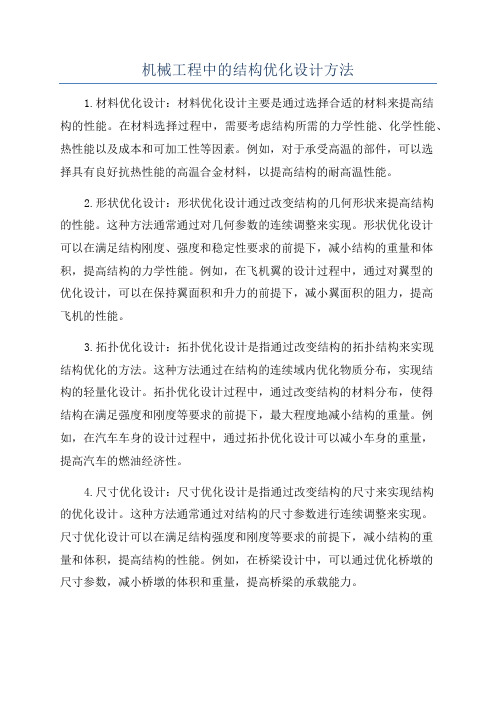
机械工程中的结构优化设计方法1.材料优化设计:材料优化设计主要是通过选择合适的材料来提高结构的性能。
在材料选择过程中,需要考虑结构所需的力学性能、化学性能、热性能以及成本和可加工性等因素。
例如,对于承受高温的部件,可以选择具有良好抗热性能的高温合金材料,以提高结构的耐高温性能。
2.形状优化设计:形状优化设计通过改变结构的几何形状来提高结构的性能。
这种方法通常通过对几何参数的连续调整来实现。
形状优化设计可以在满足结构刚度、强度和稳定性要求的前提下,减小结构的重量和体积,提高结构的力学性能。
例如,在飞机翼的设计过程中,通过对翼型的优化设计,可以在保持翼面积和升力的前提下,减小翼面积的阻力,提高飞机的性能。
3.拓扑优化设计:拓扑优化设计是指通过改变结构的拓扑结构来实现结构优化的方法。
这种方法通过在结构的连续域内优化物质分布,实现结构的轻量化设计。
拓扑优化设计过程中,通过改变结构的材料分布,使得结构在满足强度和刚度等要求的前提下,最大程度地减小结构的重量。
例如,在汽车车身的设计过程中,通过拓扑优化设计可以减小车身的重量,提高汽车的燃油经济性。
4.尺寸优化设计:尺寸优化设计是指通过改变结构的尺寸来实现结构的优化设计。
这种方法通常通过对结构的尺寸参数进行连续调整来实现。
尺寸优化设计可以在满足结构强度和刚度等要求的前提下,减小结构的重量和体积,提高结构的性能。
例如,在桥梁设计中,可以通过优化桥墩的尺寸参数,减小桥墩的体积和重量,提高桥梁的承载能力。
总而言之,机械工程中的结构优化设计方法包括材料优化设计、形状优化设计、拓扑优化设计和尺寸优化设计。
这些方法可以在满足结构强度和刚度等要求的前提下,减小结构的重量和体积,提高结构的性能。
机械结构优化设计的应用及趋势探究
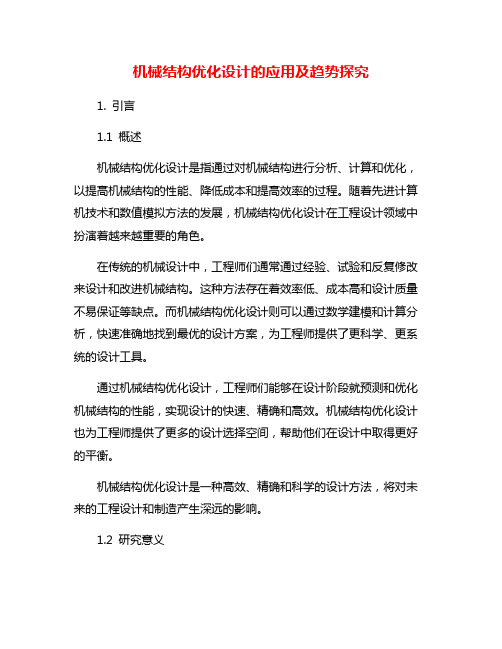
机械结构优化设计的应用及趋势探究1. 引言1.1 概述机械结构优化设计是指通过对机械结构进行分析、计算和优化,以提高机械结构的性能、降低成本和提高效率的过程。
随着先进计算机技术和数值模拟方法的发展,机械结构优化设计在工程设计领域中扮演着越来越重要的角色。
在传统的机械设计中,工程师们通常通过经验、试验和反复修改来设计和改进机械结构。
这种方法存在着效率低、成本高和设计质量不易保证等缺点。
而机械结构优化设计则可以通过数学建模和计算分析,快速准确地找到最优的设计方案,为工程师提供了更科学、更系统的设计工具。
通过机械结构优化设计,工程师们能够在设计阶段就预测和优化机械结构的性能,实现设计的快速、精确和高效。
机械结构优化设计也为工程师提供了更多的设计选择空间,帮助他们在设计中取得更好的平衡。
机械结构优化设计是一种高效、精确和科学的设计方法,将对未来的工程设计和制造产生深远的影响。
1.2 研究意义通过开展机械结构优化设计研究,可以推动我国机械制造技术的发展,提高我国制造业的整体水平和竞争力。
通过优化设计,可以减少产品的材料损耗,降低生产成本,提高产品的质量和性能,满足人们对产品品质的需求。
研究机械结构优化设计的意义重大,有助于推动我国工程技术的发展,促进工程实践的创新和进步。
2. 正文2.1 机械结构优化设计的相关概念机械结构优化设计是指通过应用现代设计理论、数学优化方法和计算机辅助设计技术,对机械结构进行优化设计,以提高结构的性能和效率。
其核心目标是在满足结构强度、刚度、稳定性等基本功能要求的前提下,尽可能减轻结构重量、降低成本、提高工作效率。
在机械结构优化设计中,需要考虑的因素包括结构形状、材料性质、载荷情况、工作环境等多个方面。
通过合理选择设计变量和约束条件,结合数学优化方法如有限元分析、遗传算法、模拟退火算法等,可以实现对机械结构进行全面、高效的优化设计。
机械结构优化设计的关键是要充分理解结构的工作原理和设计要求,同时要熟练掌握现代设计软件和优化算法,以达到设计效率和性能的最佳平衡。
机械设计中的结构优化方法综述

机械设计中的结构优化方法综述引言:机械设计是一门综合性的学科,涉及到材料科学、力学、工程力学等多个领域。
在机械设计中,结构优化是一个重要的环节,通过优化设计可以提高机械产品的性能和效率。
本文将综述机械设计中的结构优化方法,包括传统的优化方法和近年来发展起来的基于人工智能的优化方法。
一、传统的结构优化方法1.1 材料选择和设计准则在机械设计中,材料的选择对结构的优化起着至关重要的作用。
不同材料的物理性能和力学性能各有优劣,根据机械产品的使用环境和要求,选择合适的材料可以提高产品的性能和寿命。
同时,设计准则也是结构优化的基础,如强度、刚度、稳定性等要求,需要在设计过程中合理考虑。
1.2 拓扑优化拓扑优化是一种常用的结构优化方法,通过改变材料的分布来优化结构的性能。
这种方法可以通过数学模型和计算机仿真来实现。
拓扑优化可以帮助设计人员在不改变结构形状的前提下,找到最佳的材料分布方式,以实现最佳的结构性能。
1.3 尺寸优化尺寸优化是指通过改变结构的尺寸来优化结构的性能。
这种方法需要根据结构的受力情况和设计要求,对结构的尺寸进行调整。
尺寸优化可以通过数学模型和计算机仿真来实现,通过优化结构的尺寸,可以提高结构的强度和刚度。
二、基于人工智能的结构优化方法近年来,随着人工智能技术的发展,基于人工智能的结构优化方法也逐渐兴起。
这些方法利用机器学习和深度学习等技术,通过大量的数据和算法模型来实现结构的优化。
2.1 遗传算法遗传算法是一种模拟生物进化过程的优化方法。
通过模拟自然选择、交叉和变异等过程,来寻找最优解。
在结构优化中,遗传算法可以通过不断迭代和优化,找到最佳的结构设计。
2.2 神经网络神经网络是一种模拟人脑神经元工作原理的优化方法。
通过训练神经网络模型,可以实现结构的优化。
神经网络可以学习和记忆大量的数据和模式,通过不断的训练和调整,可以找到最佳的结构设计。
2.3 深度学习深度学习是一种基于神经网络的机器学习方法,通过多层次的神经网络结构来实现结构的优化。
机械结构优化设计的应用及趋势探究
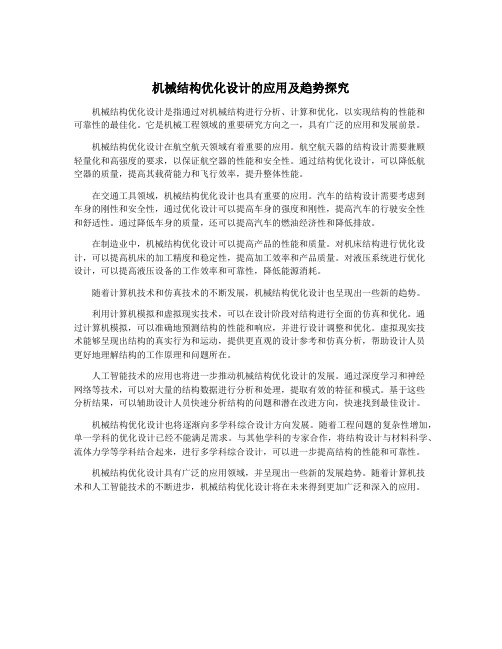
机械结构优化设计的应用及趋势探究机械结构优化设计是指通过对机械结构进行分析、计算和优化,以实现结构的性能和可靠性的最佳化。
它是机械工程领域的重要研究方向之一,具有广泛的应用和发展前景。
机械结构优化设计在航空航天领域有着重要的应用。
航空航天器的结构设计需要兼顾轻量化和高强度的要求,以保证航空器的性能和安全性。
通过结构优化设计,可以降低航空器的质量,提高其载荷能力和飞行效率,提升整体性能。
在交通工具领域,机械结构优化设计也具有重要的应用。
汽车的结构设计需要考虑到车身的刚性和安全性,通过优化设计可以提高车身的强度和刚性,提高汽车的行驶安全性和舒适性。
通过降低车身的质量,还可以提高汽车的燃油经济性和降低排放。
在制造业中,机械结构优化设计可以提高产品的性能和质量。
对机床结构进行优化设计,可以提高机床的加工精度和稳定性,提高加工效率和产品质量。
对液压系统进行优化设计,可以提高液压设备的工作效率和可靠性,降低能源消耗。
随着计算机技术和仿真技术的不断发展,机械结构优化设计也呈现出一些新的趋势。
利用计算机模拟和虚拟现实技术,可以在设计阶段对结构进行全面的仿真和优化。
通过计算机模拟,可以准确地预测结构的性能和响应,并进行设计调整和优化。
虚拟现实技术能够呈现出结构的真实行为和运动,提供更直观的设计参考和仿真分析,帮助设计人员更好地理解结构的工作原理和问题所在。
人工智能技术的应用也将进一步推动机械结构优化设计的发展。
通过深度学习和神经网络等技术,可以对大量的结构数据进行分析和处理,提取有效的特征和模式。
基于这些分析结果,可以辅助设计人员快速分析结构的问题和潜在改进方向,快速找到最佳设计。
机械结构优化设计也将逐渐向多学科综合设计方向发展。
随着工程问题的复杂性增加,单一学科的优化设计已经不能满足需求。
与其他学科的专家合作,将结构设计与材料科学、流体力学等学科结合起来,进行多学科综合设计,可以进一步提高结构的性能和可靠性。
机械结构优化设计具有广泛的应用领域,并呈现出一些新的发展趋势。
机械结构优化设计与性能分析

机械结构优化设计与性能分析一、引言机械结构的设计和优化是现代制造业中非常重要的工作。
越来越多的制造企业意识到了机械结构优化设计对于产品质量和生产效率的重要性。
本文将从机械结构优化设计和性能分析两个方面进行探讨。
二、机械结构优化设计机械结构优化设计指的是利用先进的设计技术和优化算法,通过改变结构形状、结构参数、材料等方面的因素,使结构的性能得到提升或优化。
优化设计的流程主要分为以下几个步骤:(1)确定设计目标和约束条件在进行优化设计之前,需要明确设计目标和约束条件。
设计目标可以是优化结构的强度、刚度、重量等性能指标。
约束条件可以包括结构的最大尺寸、最小重量、最大载荷等限制条件。
(2)建立数学模型将机械结构转化为可以计算的数学模型,通常使用有限元分析方法进行建模。
在建模过程中需要考虑结构的材料力学性质、载荷情况、约束条件等。
(3)优化算法选择根据设计目标和约束条件选择适合的优化算法。
常用的算法有遗传算法、粒子群算法、模拟退火算法等。
(4)参数优化和结构改进在进行优化计算之前,需要确定待优化的参数。
根据优化算法的特点和问题的具体情况,进行参数优化和结构改进。
(5)优化结果评估根据优化结果进行评估,包括优化目标的优化程度、结构变化的程度、优化结果的可行性等。
三、机械结构性能分析机械结构性能分析主要是针对优化设计后的结构进行性能检测和验证。
性能分析主要包括两个方面:(1)结构强度分析通过有限元分析方法等来评估结构强度。
强度分析可以分为静载和动载两种情况,静载包括拉伸、压缩、弯曲等力学指标,动载包括冲击、振动、疲劳等指标。
(2)结构稳定性分析结构的稳定性分析是指对结构进行稳定性评估。
结构的稳定性常常与结构的材料、形状、尺寸等因素有关。
四、结论机械结构的优化设计和性能分析是机械制造领域中非常重要的工作。
为了实现结构的优化设计,需要考虑设计目标、约束条件、数学模型、优化算法和参数优化等因素。
对于机械结构的性能分析,则需要进行包括强度分析和稳定性分析等在内的多个方面的测试和评估。
机械结构的优化设计

机械结构的优化设计在工程领域中,机械结构的优化设计是一个关键的环节。
通过对机械结构的合理设计和优化,可以提高装置的性能、减少能源的损失,并延长其使用寿命。
本文将从机械结构的设计原则、优化方法以及现代技术应用等多个方面来探讨机械结构的优化设计。
首先,机械结构的设计原则是优化设计的基础。
在机械结构的设计过程中,需要根据工作环境和工作条件,确定合理的设计参数。
设计原则包括结构合理性、材料选择、强度和刚度等因素的综合考虑。
例如,在设计高速旋转机械时,需要考虑结构的平衡性和动平衡性,以减少振动和噪音;在设计承受大载荷的机械结构时,需要选择高强度材料,并进行强度和刚度的计算。
其次,机械结构的优化方法有多种。
常见的优化方法包括有限元分析法、参数化设计法和演化算法等。
有限元分析法可以模拟机械结构在工作过程中的应力和变形情况,以评估结构的稳定性和安全性。
参数化设计法可以通过对设计参数的合理选择,对机械结构进行优化。
演化算法则是一种启发式搜索算法,通过对机械结构进行不断变异和选择,以优化设计结果。
这些优化方法可以互相结合,形成多层次、多尺度的优化设计。
此外,现代技术的应用对机械结构的优化设计起到了巨大的推动作用。
随着计算机技术和虚拟仿真技术的发展,设计师可以使用各种软件和工具进行机械结构的模拟分析和优化设计。
例如,使用CAD软件进行结构三维建模和可视化设计,使用CAE软件进行有限元分析和结构优化,使用CFD软件进行流体动力学仿真等。
这些技术的应用不仅可以提高设计效率,还可以减少试验和制造成本,为机械结构的优化设计提供了新的途径。
在实际应用中,机械结构的优化设计需要考虑多个因素的综合。
除了结构的强度和刚度之外,还需要考虑结构的重量、成本、可靠性和可维护性等因素。
例如,在航空航天领域,对飞机的机身结构进行优化设计时,需要考虑满足足够强度和刚度的前提下,尽可能减小其重量,以提高飞机的燃油效率和载重能力。
总之,机械结构的优化设计是一项复杂而关键的任务。
机械结构优化设计与性能分析

机械结构优化设计与性能分析现代制造业对机械结构设计的需求越来越高,要求其在保持稳定性和可靠性的同时,能够实现更高的工作效率和安全性。
机械结构优化设计与性能分析成为了研究热点。
本文将从机械结构优化设计的原理与方法、性能分析的指标以及相关应用等方面进行探讨。
一、机械结构优化设计的原理与方法机械结构优化设计的目标是通过改变结构的参数和形状,使机械结构在给定的工作条件下,具有最佳的性能和最小的重量、成本和能耗。
其核心原理是结构与性能之间的相互关系。
常用的机械结构优化设计方法包括参数法、构型法和材料法等。
参数法是在设计中固定某些参数,通过调整其他参数的取值,来优化结构设计。
构型法是改变结构的形状,通过不同的设计方案进行比较,找到最佳的结构形式。
材料法是通过改变材料的性质和组成,来优化结构的设计。
二、性能分析的指标在机械结构优化设计过程中,需要对结构的性能进行分析和评估。
常用的性能指标包括强度、刚度、稳定性和动态响应等。
强度是指结构在外部载荷作用下抵抗变形和破坏的能力。
在机械结构设计中,需要保证结构的强度能够满足工作条件下的安全要求。
刚度是指结构对外部力学变量变化的响应能力。
刚度越大,结构在受力时变形越小,对外部载荷的变化越敏感。
稳定性是指结构在受到外部载荷作用时,能够保持稳定的能力。
对于长条形结构或高塔等,稳定性的分析尤为重要。
动态响应是指结构在受到动力载荷作用时的振动情况。
需要分析结构的固有频率和模态形态,以保证结构在工作过程中不会发生共振。
三、机械结构优化设计与性能分析的应用机械结构优化设计与性能分析在各个领域都有广泛的应用。
以航空航天领域为例,机身、发动机和机翼等机械结构的优化设计和性能分析对于飞机的性能和安全至关重要。
通过优化设计,可以减轻重量,提高航空器的性能和燃油效率。
在交通运输领域,汽车的车身结构和悬挂系统的优化设计可以提高行驶的稳定性和舒适性。
对高速列车和地铁等轨道交通的轨道结构和车辆结构进行优化设计和性能分析,可以提高列车的速度和牵引力。
机械优化设计概念

机械优化设计概念机械优化设计是指在机械设计过程中,通过对机械结构、材料、工艺等方面的优化,以达到提高机械性能、降低成本、提高生产效率等目的的设计方法。
机械优化设计是机械设计中的重要环节,它可以提高机械的可靠性、稳定性和安全性,同时也可以提高机械的经济性和竞争力。
机械优化设计的概念包括以下几个方面:1. 结构优化设计:结构优化设计是指通过对机械结构的优化,以达到提高机械性能、降低成本、提高生产效率等目的的设计方法。
结构优化设计可以通过改变机械结构的形状、尺寸、材料等方面来实现。
2. 材料优化设计:材料优化设计是指通过对机械材料的优化,以达到提高机械性能、降低成本、提高生产效率等目的的设计方法。
材料优化设计可以通过选择合适的材料、改变材料的组成、制备工艺等方面来实现。
3. 工艺优化设计:工艺优化设计是指通过对机械制造工艺的优化,以达到提高机械性能、降低成本、提高生产效率等目的的设计方法。
工艺优化设计可以通过改进制造工艺、优化加工工艺等方面来实现。
4. 综合优化设计:综合优化设计是指将结构优化设计、材料优化设计和工艺优化设计等方面进行综合考虑,以达到最优化的设计效果。
综合优化设计可以通过建立机械优化设计模型、进行多目标优化等方法来实现。
机械优化设计的实现需要遵循以下原则:1. 综合考虑机械性能、成本和生产效率等因素,以达到最优化的设计效果。
2. 采用先进的设计方法和工具,如计算机辅助设计、有限元分析等,以提高设计效率和准确性。
3. 与制造工艺和生产实际相结合,以确保设计方案的可行性和实用性。
4. 不断进行优化和改进,以逐步提高机械的性能和竞争力。
总之,机械优化设计是机械设计中的重要环节,它可以提高机械的可靠性、稳定性和安全性,同时也可以提高机械的经济性和竞争力。
在实现机械优化设计的过程中,需要遵循一定的原则和方法,以达到最优化的设计效果。
机械设备的结构优化设计

机械设备的结构优化设计随着科技的不断进步,机械设备在工业生产和日常生活中扮演着极为重要的角色。
而机械设备的结构优化设计则是提高机械设备性能和效率的关键。
本文将从结构优化设计的概念、优化的方法和具体案例等方面进行探讨。
一、结构优化设计的概念结构优化设计是指通过改变机械设备的结构形式,使其在给定的条件下达到最佳的性能和效率。
结构优化设计的目标是在满足机械设备的功能和性能要求的前提下,尽可能地减少材料的使用量,降低成本,提高可靠性和安全性。
它涉及到材料的选择、零部件的布局和连接等方面的考虑,需要综合考虑各种因素的影响。
二、结构优化设计的方法1. 材料优化:选择合适的材料是结构优化设计的基础。
不同的材料具有不同的物理性质和机械性能,因此需要根据具体的应用需求选择合适的材料。
在材料的选择过程中,需要考虑机械强度、耐磨性、导热性等因素的影响。
2. 拓扑优化:拓扑优化是一种常用的结构优化设计方法。
它通过改变结构的形状和布局来达到优化的效果。
通常会利用计算机辅助设计软件进行拓扑优化分析,通过数学模型和算法确定最佳的结构形式。
拓扑优化方法可以帮助设计师提供一些意想不到的形状和结构,以提高机械设备的性能和效率。
3. 参数优化:参数优化是指在给定的结构形式下,通过对结构参数的调整来实现最佳的设计效果。
在参数优化过程中,需要根据具体的设计需求确定设计目标和约束条件,通过数学模型和优化算法寻找最佳的参数组合。
三、结构优化设计的案例1. 案例一:某汽车发动机气缸头的结构优化设计某汽车发动机气缸头在原设计上存在材料消耗过大、重量较重等问题。
通过拓扑优化分析,设计师确定了气缸头的最佳形状,并采用了轻量化材料进行制造。
经过优化设计后,气缸头的重量减少了20%,材料消耗减少了30%,同时保持了原有的功能和性能。
2. 案例二:某工业机器人的结构优化设计某工业机器人在原设计上存在结构不稳定、承载能力不足等问题。
通过参数优化分析,设计师对机器人的关键结构参数进行了调整,并增加了加固结构。
机械工程中的结构优化设计
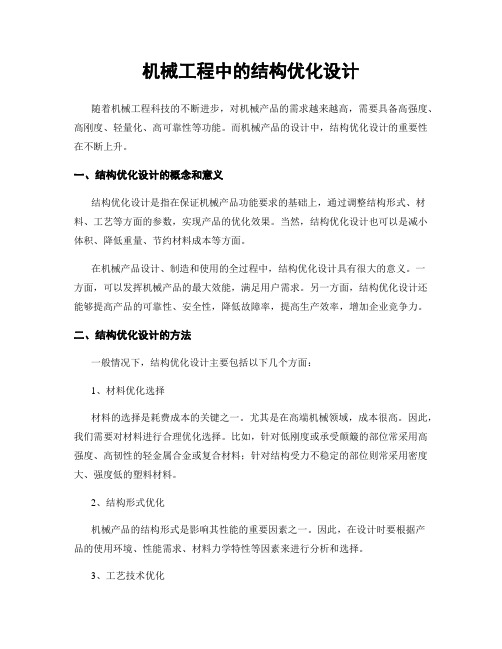
机械工程中的结构优化设计随着机械工程科技的不断进步,对机械产品的需求越来越高,需要具备高强度、高刚度、轻量化、高可靠性等功能。
而机械产品的设计中,结构优化设计的重要性在不断上升。
一、结构优化设计的概念和意义结构优化设计是指在保证机械产品功能要求的基础上,通过调整结构形式、材料、工艺等方面的参数,实现产品的优化效果。
当然,结构优化设计也可以是减小体积、降低重量、节约材料成本等方面。
在机械产品设计、制造和使用的全过程中,结构优化设计具有很大的意义。
一方面,可以发挥机械产品的最大效能,满足用户需求。
另一方面,结构优化设计还能够提高产品的可靠性、安全性,降低故障率,提高生产效率,增加企业竞争力。
二、结构优化设计的方法一般情况下,结构优化设计主要包括以下几个方面:1、材料优化选择材料的选择是耗费成本的关键之一。
尤其是在高端机械领域,成本很高。
因此,我们需要对材料进行合理优化选择。
比如,针对低刚度或承受颠簸的部位常采用高强度、高韧性的轻金属合金或复合材料;针对结构受力不稳定的部位则常采用密度大、强度低的塑料材料。
2、结构形式优化机械产品的结构形式是影响其性能的重要因素之一。
因此,在设计时要根据产品的使用环境、性能需求、材料力学特性等因素来进行分析和选择。
3、工艺技术优化在机械制造中,工艺的优化可以极大地提高生产效率,同时还可降低成本。
在结构优化设计中,选用合理的工艺方案则可以提高产品性能、优化产品结构,从而达到更好的客户体验。
三、结构优化设计的应用案例结构优化设计在实际生产中有着广泛的应用。
笔者这里举一个最近亲身经历的案例进行说明:我所在公司的一个新产品设计初期,经常出现陨石着陆模拟测试时部分构件断裂、变形的问题。
我们最终采用了如下的结构优化设计方法:1、材料优化选择:选用了密度相对较小,韧度又相对较高的合金材料;2、结构形式优化:优化三角板间距和尺寸比例,以减少受力不均等因素;3、工艺技术优化:通过对工艺流程、工艺参数进行优化,提高产品的成形精度和强度。
机械结构的优化设计与性能分析

机械结构的优化设计与性能分析机械结构的设计与性能分析在工程领域中起着至关重要的作用。
一台优秀的机械设备不仅需要满足性能要求,还需要在经济、可靠性和使用寿命等方面具有较高的优势。
本文将从机械结构的优化设计和性能分析两个方面探讨其重要性和方法,以提供一些有益的思路和方法。
一、机械结构的优化设计机械结构的优化设计是指通过对结构的形状、材质、尺寸和布局等参数进行合理调整和优化,以使得机械设备在满足性能要求的同时,也能够达到经济、可靠、轻量化等目标。
首先,在优化设计中,需要明确机械设备的使用环境和工作条件。
比如,对于一台用于工业生产的机床,需要考虑到其所承受的力和振动等外界因素。
而对于一台用于交通运输的机械设备,需要关注其在高速运行和复杂道路条件下的可靠性和安全性。
其次,优化设计过程中需要充分考虑材料的选择和应用。
不同材料具有不同的力学性能和耐用性,因此,根据实际要求选用适合的材料可以有效地提高机械结构的性能。
例如,对于需要承受重负荷和高温的零件,合金钢是一种理想的选择;而对于需要轻量化和高刚度的结构,复合材料则是一个不错的替代品。
最后,优化设计需要运用先进的计算手段和方法。
利用计算机辅助设计软件和有限元分析等工具,可以对机械结构进行模拟和仿真,快速地评估不同方案的性能和可行性,并找到最佳设计方案。
二、机械结构的性能分析机械结构的性能分析是指通过实验和计算的方式,对机械结构的强度、刚度、动态响应等性能进行评估和分析。
在性能分析中,强度是一个关键的指标。
通过应力分析和疲劳寿命预测等方法,可以评估机械结构在工作过程中承受外部载荷的能力。
强度不足可能导致机械零部件的破坏和事故的发生,因此,需要在设计阶段充分考虑和评估结构的强度问题。
刚度是另一个重要的性能指标。
刚度决定了机械结构的稳定性和动态响应。
在高速运行和复杂工况下,结构的刚度对于保证机械设备的精度和性能至关重要。
因此,在设计阶段需要进行刚度分析和优化,以满足要求。
机械结构优化设计

机械结构优化设计机械结构的优化设计一直是工程领域中关注的焦点之一。
随着科技的发展,机械结构在工业制造领域的重要性日益凸显。
优化设计可以帮助提高机械结构的性能,减少生产成本,提高生产效率。
本文将探讨机械结构优化设计的意义、方法和应用。
机械结构的优化设计对于提升机械产品的质量和可靠性至关重要。
优化设计可以通过改善结构的强度和刚度,优化零部件的尺寸和形状,提高机械结构的寿命和耐久性。
此外,优化设计还可以减少机械结构的重量和体积,降低生产成本。
通过运用先进的设计工具和方法,可以实现机械结构的性能和可靠性的最大化。
机械结构优化设计的方法有很多种,其中最常用的是基于仿真的优化设计。
通过建立数学模型和使用计算机模拟技术,可以快速评估不同设计方案的性能,并选择最佳方案。
常用的仿真软件有有限元分析软件、计算流体力学软件等。
通过这些软件,可以对机械结构的热力学行为、力学特性和流体运动等进行模拟,从而找到最优化的设计方案。
除了仿真技术,优化设计还可以运用人工智能技术。
通过机器学习和深度学习算法,可以从海量数据中发现模式和规律,并根据这些规律辅助设计出更优化的结构方案。
此外,遗传算法和蚁群算法等进化算法也被广泛应用于机械结构优化设计。
这些算法可以模拟自然界的进化过程,通过不断地迭代和进化,找到最优化的设计解。
机械结构优化设计不仅仅局限于产品设计阶段,也可以应用于产品的改进和升级。
通过对已有机械结构的分析和评估,可以找到问题所在,并提出改进措施。
例如,通过优化改进某些零部件的形状,减少材料损失和重量,提高整个机械结构的性能。
此外,还可以运用拓扑优化设计方法,通过剔除不必要的材料,减少结构的重量和体积,提高结构的强度和刚度。
当然,机械结构优化设计也面临着一些挑战和限制。
首先,优化设计过程需要大量的计算资源和时间。
其次,优化设计还受到材料和加工工艺的限制,必须考虑到实际生产的可行性和成本效益。
另外,机械结构的优化设计还需要与其他学科领域的知识相融合,如工程力学、材料学、控制论等。
机械结构的优化设计
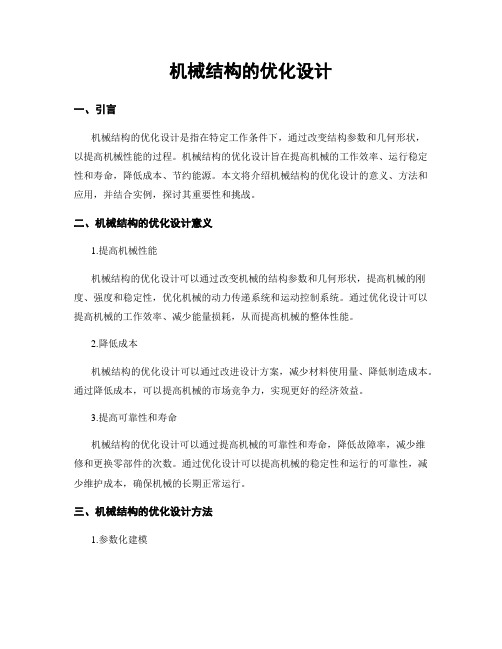
机械结构的优化设计一、引言机械结构的优化设计是指在特定工作条件下,通过改变结构参数和几何形状,以提高机械性能的过程。
机械结构的优化设计旨在提高机械的工作效率、运行稳定性和寿命,降低成本、节约能源。
本文将介绍机械结构的优化设计的意义、方法和应用,并结合实例,探讨其重要性和挑战。
二、机械结构的优化设计意义1.提高机械性能机械结构的优化设计可以通过改变机械的结构参数和几何形状,提高机械的刚度、强度和稳定性,优化机械的动力传递系统和运动控制系统。
通过优化设计可以提高机械的工作效率、减少能量损耗,从而提高机械的整体性能。
2.降低成本机械结构的优化设计可以通过改进设计方案,减少材料使用量、降低制造成本。
通过降低成本,可以提高机械的市场竞争力,实现更好的经济效益。
3.提高可靠性和寿命机械结构的优化设计可以通过提高机械的可靠性和寿命,降低故障率,减少维修和更换零部件的次数。
通过优化设计可以提高机械的稳定性和运行的可靠性,减少维护成本,确保机械的长期正常运行。
三、机械结构的优化设计方法1.参数化建模参数化建模是机械结构优化设计的基础。
通过将机械结构转化为可调整参数的数学模型,可以对机械的结构参数进行变量化表示,为优化设计提供基础。
2.多目标优化机械结构的优化设计通常涉及多个指标,如强度、刚度、轻量化等,这些目标往往相互制约。
多目标优化方法可以综合考虑多个目标指标,通过建立适当的数学模型和优化算法,找到最优解。
3.拓扑优化设计拓扑优化是机械结构优化设计的重要方法之一。
通过改变机械结构的拓扑形状,使其在满足约束条件的前提下,获得更好的性能。
拓扑优化设计可以通过增加或减少材料在结构中的分布,以改变结构的刚度、强度和重量。
四、机械结构的优化设计应用1.飞机结构设计飞机是一个复杂的机械系统,其结构设计的优化在航空工业中具有重要意义。
通过优化设计可以减轻飞机的重量,提高载荷能力,降低能耗,提高机动性能和飞行安全性。
2.汽车结构设计汽车工业是机械结构优化设计的另一个重要领域。
机械结构的紧凑性优化设计
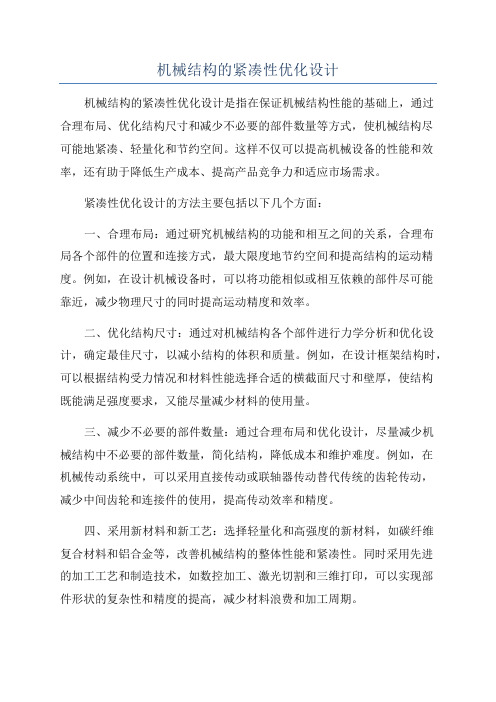
机械结构的紧凑性优化设计机械结构的紧凑性优化设计是指在保证机械结构性能的基础上,通过合理布局、优化结构尺寸和减少不必要的部件数量等方式,使机械结构尽可能地紧凑、轻量化和节约空间。
这样不仅可以提高机械设备的性能和效率,还有助于降低生产成本、提高产品竞争力和适应市场需求。
紧凑性优化设计的方法主要包括以下几个方面:一、合理布局:通过研究机械结构的功能和相互之间的关系,合理布局各个部件的位置和连接方式,最大限度地节约空间和提高结构的运动精度。
例如,在设计机械设备时,可以将功能相似或相互依赖的部件尽可能靠近,减少物理尺寸的同时提高运动精度和效率。
二、优化结构尺寸:通过对机械结构各个部件进行力学分析和优化设计,确定最佳尺寸,以减小结构的体积和质量。
例如,在设计框架结构时,可以根据结构受力情况和材料性能选择合适的横截面尺寸和壁厚,使结构既能满足强度要求,又能尽量减少材料的使用量。
三、减少不必要的部件数量:通过合理布局和优化设计,尽量减少机械结构中不必要的部件数量,简化结构,降低成本和维护难度。
例如,在机械传动系统中,可以采用直接传动或联轴器传动替代传统的齿轮传动,减少中间齿轮和连接件的使用,提高传动效率和精度。
四、采用新材料和新工艺:选择轻量化和高强度的新材料,如碳纤维复合材料和铝合金等,改善机械结构的整体性能和紧凑性。
同时采用先进的加工工艺和制造技术,如数控加工、激光切割和三维打印,可以实现部件形状的复杂性和精度的提高,减少材料浪费和加工周期。
紧凑性优化设计在机械结构的研发和生产中具有重要的意义。
首先,紧凑的结构可以减小机械设备的占地面积,提高资源利用效率和产能密度,无论是在生产车间还是在现场使用,都能节约生产成本和空间。
其次,紧凑的结构可以减少部件之间的摩擦和能量损失,提高机械设备的效率和工作稳定性。
最后,紧凑的结构可以降低机械设备的重量和运输成本,提高设备的便携性和安装效率,适应市场快速变化的需求。
总之,机械结构的紧凑性优化设计是一项复杂而重要的工作。
机械结构工程优化方案设计

机械结构工程优化方案设计一、背景介绍机械结构工程优化是指对机械结构进行综合分析、设计和改进,以提高其性能、降低成本、延长使用寿命和提高可靠性。
在机械制造领域,优化设计在提高产品竞争力和降低生产成本方面发挥着重要作用。
本文将结合实际案例,介绍机械结构工程优化方案设计的具体步骤和方法。
二、优化目标和指标优化目标:通过对机械结构进行优化设计,提高产品性能、降低成本、提高可靠性、降低制造难度和提高制造效率。
优化指标:1. 产品性能指标:包括运行速度、压力、扭矩、位移、噪音等;2. 成本指标:包括材料、加工工艺、装配成本等;3. 可靠性指标:包括寿命、故障率、维修性等;4. 制造难度指标:包括工艺性、可制造性、装配性等;5. 制造效率指标:包括生产周期、吞吐量、生产效率等。
三、优化方案设计步骤1. 原始结构分析首先对机械结构的原始设计进行详细分析,包括结构形式、材料选择、工艺工程等,了解其优点和不足,确定需求和目标。
2. 机械结构仿真建模在进行优化设计前,需要对机械结构进行三维建模和有限元分析,以确定其受力状态和不同工况下的性能表现。
有限元分析可以为优化设计提供准确的数据支持,从而避免盲目改动造成不良影响。
3. 优化设计方案制定根据仿真分析结果和优化目标,制定具体的优化设计方案,包括材料改良、结构优化、加工工艺改进等。
同时,还需考虑到设计的可行性和实施的难易程度,确保方案能够有效地实施。
4. 优化设计方案验证将优化设计方案进行仿真验证,检验其在设计要求下的性能、成本、可靠性等指标的改进效果,并根据仿真结果调整优化设计方案,直至满足优化目标。
5. 方案实施和验证在优化设计方案得到验证后,需要将其实施到实际生产中,并通过实际测试验证其性能、成本、可靠性等指标的改进效果,并为下一轮设计工作提供经验和教训。
四、案例分析以一个某公司生产的变速箱为例,该变速箱在实际使用中存在换挡不顺畅、噪音大、寿命短等问题,需要进行优化设计。
机械工程中的结构优化设计
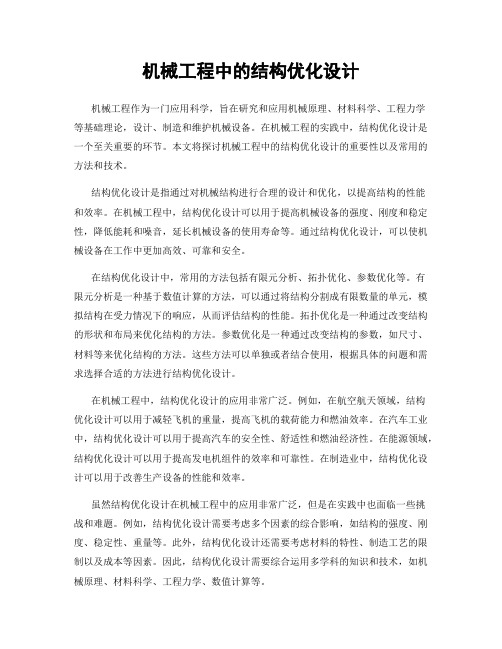
机械工程中的结构优化设计机械工程作为一门应用科学,旨在研究和应用机械原理、材料科学、工程力学等基础理论,设计、制造和维护机械设备。
在机械工程的实践中,结构优化设计是一个至关重要的环节。
本文将探讨机械工程中的结构优化设计的重要性以及常用的方法和技术。
结构优化设计是指通过对机械结构进行合理的设计和优化,以提高结构的性能和效率。
在机械工程中,结构优化设计可以用于提高机械设备的强度、刚度和稳定性,降低能耗和噪音,延长机械设备的使用寿命等。
通过结构优化设计,可以使机械设备在工作中更加高效、可靠和安全。
在结构优化设计中,常用的方法包括有限元分析、拓扑优化、参数优化等。
有限元分析是一种基于数值计算的方法,可以通过将结构分割成有限数量的单元,模拟结构在受力情况下的响应,从而评估结构的性能。
拓扑优化是一种通过改变结构的形状和布局来优化结构的方法。
参数优化是一种通过改变结构的参数,如尺寸、材料等来优化结构的方法。
这些方法可以单独或者结合使用,根据具体的问题和需求选择合适的方法进行结构优化设计。
在机械工程中,结构优化设计的应用非常广泛。
例如,在航空航天领域,结构优化设计可以用于减轻飞机的重量,提高飞机的载荷能力和燃油效率。
在汽车工业中,结构优化设计可以用于提高汽车的安全性、舒适性和燃油经济性。
在能源领域,结构优化设计可以用于提高发电机组件的效率和可靠性。
在制造业中,结构优化设计可以用于改善生产设备的性能和效率。
虽然结构优化设计在机械工程中的应用非常广泛,但是在实践中也面临一些挑战和难题。
例如,结构优化设计需要考虑多个因素的综合影响,如结构的强度、刚度、稳定性、重量等。
此外,结构优化设计还需要考虑材料的特性、制造工艺的限制以及成本等因素。
因此,结构优化设计需要综合运用多学科的知识和技术,如机械原理、材料科学、工程力学、数值计算等。
总之,结构优化设计在机械工程中具有重要的意义。
通过合理的设计和优化,可以提高机械设备的性能和效率,降低能耗和噪音,延长使用寿命,从而推动机械工程的发展和进步。
- 1、下载文档前请自行甄别文档内容的完整性,平台不提供额外的编辑、内容补充、找答案等附加服务。
- 2、"仅部分预览"的文档,不可在线预览部分如存在完整性等问题,可反馈申请退款(可完整预览的文档不适用该条件!)。
- 3、如文档侵犯您的权益,请联系客服反馈,我们会尽快为您处理(人工客服工作时间:9:00-18:30)。
线性问题
最优化问题动静态态问问题题约无 约无束约 束约束 问束题问题非线线非性性规线规性划划问题一n维维问问题题
还有其它的一些划分方法: 如按设计变量的性质分:连续变量、离散变量、整数变量
规划问题: 二次规划、几何规划、随机规划等。
© XUJI POWER 4/23/2020 v1.0
方法简介
1.简单解法
实践证明,最优化设计是保证产品具有优良的性能,减轻 自重或体积,降低产品成本的一种有效设计方法。同时也可使 设计者从大量繁琐和重复的计算工作中解脱出来,使之有更多 的精力从事创造性的设计,并大大提高设计效率。
© XUJI POWER 4/23/2020 v1.0
§1-2 优化设计问题的示例
优化设计就是借助最优化数值计算方法与计算 机技术,求取工程问题的最优设计方案。
当优化问题的变量较少时,可用下列简单解法。
(1)图解法。在设计空间中作出可行域和目标函数等值面,再从图形上找出既在可行 域内(或其边界内),又使目标函数值最小的设计点的位置。
(2)解析法。当问题比较简单时,可用解析法求解。
2.准则法
准则法是从工程和力学观点出发,提出结构达到优化设计时应满足的某些准则 (如同步失效准则、满应力准则、能量准则等),然后用迭代的方法求出满足这些 准则的解。该方法的主要特点是收敛快,重分析次数与设计变量数目无直接关系, 计算量不大,但适用有局限性,主要适用于结构布局及几何形状已定的情况。尽管 准则法有它的缺点,但从工程应用的角度来看,它比较方便,习惯上易于接受,优 点仍是主要的。最简单的准则法有同步失效准则法和满应力准则法。
优化设计包括: (1)必须将实际问题加以数学描述,形成数学 模型; (2)选用适当的一种最优化数值方法和计算程 序运算求解。
© XUJI POWER 4/23/2020 v1.0
箱盒的优化设计
已知:制造一体积为100m3,长度不小于5m,不带上盖的
箱盒,试确定箱盒的长x1,宽x2,高x3,使箱盒用料最省。 分析:
© XUJI POWER 4/23/2020 v1.0
结构设计——设计满足工作需要的结构
© XUJI POWER 4/23/2020 v1.0
© XUJI POWER 4/23/2020 v1.0
© XUJI POWER 4/23/2020 v1.0
结构优化设计
© XUJI POWER 4/23/2020 v1.0
(1)箱盒的表面积的表达式;
(2)设计参数确定:长x1,宽x2,高x3 ; (3)设计约束条件:
(a)体积要求; (b)长度要求;
x2 x1
x3
© XUJI POWER 4/23/2020 v1.0
设计参数: 设计目标:
数学模型
x1x,1x,2 ,xx23,x3
min S =x1x2+2(x1x3+x2x3)
2)对结构诸参数进行分析,以确定设计的原始参数、设计常 数和设计变量。 3)根据设计要求,确定并构造目标函数和相应的约束条件, 有时要构造多目标函数。
4)必要时对数学模型进行规范化,以消除诸组成项间由于量 纲不同等原因导致的数量悬殊的影响。
© XUJI POWER 4/23/2020 v1.0
对于最优化问题一般可作如下分类:
(2)性态约束条件。即对结构的工作性态所施加的一些 限制。如构件的强度、稳定约束以及结构整体的刚度和 自振频率等方面的限制。
© XUJI POWER 4/23/2020 v1.0
建立优化设计问题的数学模型一般步骤:
1)根据设计要求,应用专业范围内的现行理论和经验等,对 优化对象进行分析。必要时,需要对传统设计中的公式进行改 进,并尽可以反映该专业范围内的现代技术进步的成果。
© XUJI POWER 4/23/2020 v1.0
机械优化设计 就是把机械设计与优化设计理论及方法相结合, 借助电子计算机,自动寻找实现预期目标的最优设计方案和 最佳设计参数。
常规设计流程
© XUJI POWER 4/23/2020 v1.0
优化设计流程
机械优化设计应用实例
美国波音飞机公司对大型机翼用138个设计变量进行结构 优化,使重量减少了三分之一;大型运输舰用10个变量进行优 化设计,使成本降低约10%。
机械结构优化设计概述
丁习坤 2013年2月26日
优化设计的基本概念
§1-1 绪论 §1-2 优化设计问题的示例 §1-3 优化设计的数学模型
© XUJI POWER 4/23/2020 v1.0
§1-1 绪论 结构优化设计:
© XUJI POWER 4/23/2020 v1.0
§1-1 绪论
© XUJI POWER 4/23/2020 v1.0
约束条件:
x1 ≥ 5
x2 ≥ 0
x3 ≥ 0 x1.x2.x3=100xA, xB
© XUJI POWER 4/23/2020 v1.0
§1-3 优化设计的数学模型
1.结构优化设计的数学模型 结构优化设计可定义为:对于已知的给定参数,求出满足全部 约束条件并使目标函数取最小值的设计变量的解。 2.设计变量 设计变量指在设计过程中所要选择的描述结构特性的量,它的 数值是可变的。设计变量可以是各个构件的截面尺寸、面积、 惯性矩等设计截面的几何参数,也可以是柱的高度、梁的间距、 拱的矢高和节点坐标等结构总体的几何参数。设计变量通常有 连续设计变量和离散设计变量两种类型。 (1)连续设计变量。这类变量在优化过程中是连续变化的, 如拱的矢高和节点坐标等。 (2)离散设计变量。这类变量在优化中是跳跃式变化的,如 可供选用的型钢的截面面积和钢筋的直径都是不连续的。
(1)同步失效准则法。其基本思想可概括为:在荷载作用下,能使所有可能发生的破 坏模式同时实现的结构是最优的结构。同步失效准则设计有许多明显的缺点。由于 要用解析表达式进行代数运算,同步失效设计只能用来处理非常简单的元件优化; 当约束数大于设计变量数时,必须设法确定那些破坏模式应当同时发生才给出最优 设计,这通常是一件十分困难的工作;当约束数和设计变量数相等时,并不能保证 这样求得的解是最优解。
© XUJI POWER 4/23/2020 v1.0
3.目标函数
目标函数是用来衡量设计好坏的指标。采用何种指标来 反映设计好坏与结构本身的技术经济特性有关。通常采 用的目标函数有:结构重量、结构体积、结构造价三种
4.约束条件
结构优化的约束条件一般有几何约束条件和性态约束条 件两种。
(1)几何约束条件。即在几何尺寸方面对设计变量加以 限制。如工字型截面的腹板和翼缘的最小厚度限制。