船体分段焊接变形控制
探讨船体分段建造的精度管理与控制措施
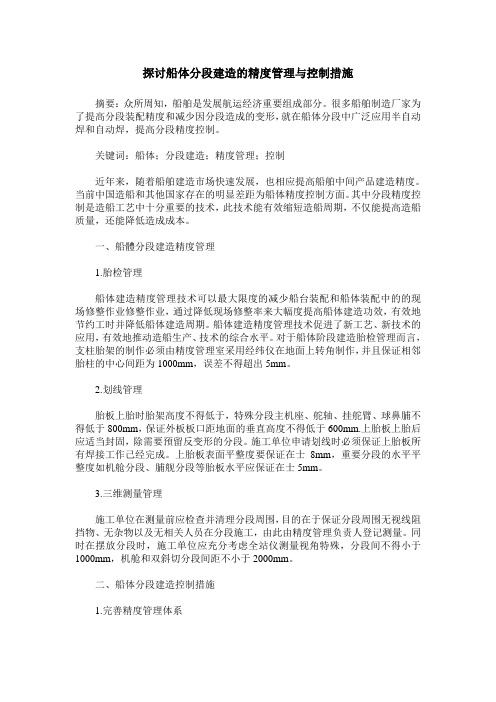
探讨船体分段建造的精度管理与控制措施摘要:众所周知,船舶是发展航运经济重要组成部分。
很多船舶制造厂家为了提高分段装配精度和减少因分段造成的变形,就在船体分段中广泛应用半自动焊和自动焊,提高分段精度控制。
关键词:船体;分段建造;精度管理;控制近年来,随着船舶建造市场快速发展,也相应提高船舶中间产品建造精度。
当前中国造船和其他国家存在的明显差距为船体精度控制方面。
其中分段精度控制是造船工艺中十分重要的技术,此技术能有效缩短造船周期,不仅能提高造船质量,还能降低造成成本。
一、船體分段建造精度管理1.胎检管理船体建造精度管理技术可以最大限度的减少船台装配和船体装配中的的现场修整作业修整作业,通过降低现场修整率来大幅度提高船体建造功效,有效地节约工时并降低船体建造周期。
船体建造精度管理技术促进了新工艺、新技术的应用,有效地推动造船生产、技术的综合水平。
对于船体阶段建造胎检管理而言,支柱胎架的制作必须由精度管理室采用经纬仪在地面上转角制作,并且保证相邻胎柱的中心间距为1000mm,误差不得超出5mm。
2.划线管理胎板上胎时胎架高度不得低于,特殊分段主机座、舵轴、挂舵臂、球鼻脯不得低于800mm,保证外板板口距地面的垂直高度不得低于600mm.上胎板上胎后应适当封固,除需要預留反变形的分段。
施工单位申请划线时必须保证上胎板所有焊接工作己经完成。
上胎板表面平整度要保证在士8mm,重要分段的水平平整度如机舱分段、脯舰分段等胎板水平应保证在士5mm。
3.三维测量管理施工单位在测量前应检查并清理分段周围,目的在于保证分段周围无视线阻挡物、无杂物以及无相关人员在分段施工,由此由精度管理负责人登记测量。
同时在摆放分段时,施工单位应充分考虑全站仪测量视角特殊,分段间不得小于1000mm,机舱和双斜切分段间距不小于2000mm。
二、船体分段建造控制措施1.完善精度管理体系船舶制造企业应在造船过程中编制《分段评级管理方案》、《分段精度管理及奖惩细则》、《流水线分段精度管理》、《内外场划线管理规定》等,同时编制《分段精度作业指导书》中明确规定:“精度管理安全生产规范”、“常见问题分析”、“仪器使用和保养规范”、“划线和完成检测管理及处罚规定”等。
探讨船体结构焊接变形控制方法

探讨船体结构焊接变形控制方法摘要:海洋气候多变,船舶与海洋工程在营运过程中会遭受各种恶劣的自然环境,而船体结构的安全性能是第一先决条件。
焊接工艺的研究和运用,是增加船体结构安全性能的最有效的方法之一。
本文简单的介绍了船舶建造中关于船体结构变形、焊接变形的控制措施和处理方法并对此进行深入研究。
关键词:焊接变形,船体结构,控制措施1引言在造船行业,船体构件的焊接变形,不仅会影响造船工艺流程的正常进行,而且会降低船体结构的承载能力,影响船体结构的尺寸精度与外形。
采用焊后矫正残余变形不但延误了造船的周期,使得制造成本上升,而且会引起整个船体质量的不稳定性等不良后果,因此,对于造船业而言,控制和消除船体结构件的焊接变形十分重要。
对于大型散货船而言,其结构复杂,焊接量大,焊接变形是必须要关注的内容。
2船体结构特点及其变形产生的原因船体结构的主要组成部分以骨架和板架两个结构为主,这两个原本相互独立的结构在通过多个连接和焊接步骤处理后才能够制造出成形的船体结构。
但是,由于不同板架和骨架的区域材料性质各不相同,尤其是材料之前的熔点和传导性质有明显差异,因此在焊接过程中非常容易出现一个骨架或者板架的内部结构有明显的温度不均匀现象分布,这种温度均匀分布直接造成材料出现不均匀热应变,最后导致结构形成塑性变形。
而且,在进行焊接过程中,一般焊接部位的温度都非常高,这种非常高的热量的一旦被输人后就会非常容易造成焊接变形出现,而且这种焊接造成的焊接变形还有不同的种类,出现何种变形种类与热量输人总量、热温度场、焊接结构的约束度三者有直接关系。
3影响焊接变形的因素影响船体焊接变形的主要因素在对船体进行焊接的工作当中缠身国的热应变、塑性应变等因素,是形成船体焊接产生形变的重点因素。
3.1焊接方式与焊接工艺参数分析不同类型的焊接方式实际所产生的收缩量也是不相同的。
当船体焊件的厚度基本相同的时候,单层的焊接从纵向上的收缩量比横向上产生的收缩量更大,这主要是因为在实施多层焊接的时候,先进行焊接的冷却之后阻碍了后续的焊接部分的收缩性。
船体分段常见问题解决措施

常见分段建造精度控制措施分段的建造精度直接影响了分段总组以及合拢时的精度,对于精度造船意义深远,控制好分段的制作精度就为船体的搭建精度打好了基础。
把分段的建造精度提高意味着为后续工作降本增效,增加效益。
因此,把问题在分段阶段处理的更彻底,分段精度质量保证的更好是工作的一个核心。
下面就目前分段问题的现状和控制措施列举如下:1,分段完工后的常见问题1)合拢口缺料控制措施:①合理利用装配公差,均匀偏差,保证满足在装配公差内。
②记录现场尺寸问题,反馈工艺员调查,彻底解决后续船问题。
③提前将超差信息反馈给工艺员,提前制定可行的方案提前解决。
2)结构装配数据超差控制措施:①装配首先要以分段结构图纸为准,其他工艺文件为辅,提前了解图纸信息是否清楚标识装配定位数据。
②出现结构图纸与其他辅助工艺文件不符,及时找工艺员、设计员确认正确的信息,不可没搞清楚就施工。
③装配时加强自检,边装配边检查,确认焊前定位无误再施焊。
检查出偏差提前整改。
3)分段平面度超差控制措施:①分段胎架制作精度要提高。
平面胎架保证水平面;曲面胎架保证胎架线性光顺。
上胎前确认,有问题提前整改。
上胎保证与胎架吻合,固胎。
②胎架反变形的加放落实到位。
工艺文件的内容了解详实清楚。
③分段框架变形、板件变形提前矫正。
④吊装结构注意保护,防止碰撞变形,提前做好定位辅助工装,牵引定位。
⑤框架、板件装配前注意堆放变形,尽量保证前期成品的质量。
⑥框架装焊前利用水带、水平仪检测定位水平。
有问题提前处理到最好状态。
⑦防止定位焊不均匀、不够力而爆焊跑位,严格按工艺执行定位焊(点焊)和全段焊接(焊接要求参数、顺序)。
⑧松胎前,择机进行分段煺火,释放焊接应力。
4)合拢口平齐度超差控制措施:①装配时吊线锤、拉分线,检查结构对正情况,保证定位准度。
装配时加强自检,边装配边检查,确认焊前定位无误再施焊。
检查出偏差提前整改。
合理利用公差保证平齐度。
②划线精度也是控制重点,切割余量保证准确性和质量,切割要考虑切割损耗。
船舶建造分段精度控制之反变形法的应用

船舶建造分段精度控制之反变形法的应用摘要:本文将以船坞搭载精度为目标,反变形方法应用为导向,分段制作阶段实施的路线,来介绍某船厂在8.2万吨散货船上利用反变形法对分段精度控制的研究实施,从而实现在船坞搭载阶段减少结构错位离空,提高船舶精度,缩短船坞周期,增加经济效益的目的。
关键词:精度控制分段建造反变形引言船舶建造中焊接引起的变形是诸多变形中最常见的现象,在变形达到一定程度之后就会超出精度标准范围,需要现场通过额外的弥补措施进行矫正,按照造船行业1:3:9的成本理论,越是后期进行矫正,所付出的代价越大。
通常情况下,焊接的变形我们可以在以下三个阶段进行控制:1、前期设计:合理的焊缝设计及焊接方法的选用;2、施工过程:制定合理的施工工艺,并对施工工艺严格执行,即现场工人按照设计的焊接电流、电压、焊接顺序、焊接速度进行施工;3、后期矫正:即变形后的补救措施,通过机械和火工进行变形矫正。
对于整个船舶建造环节,分段精度的控制是重中之重,分段因焊接产生的变形我们需两方面加以理解和区别对待,从而制定相应的措施进行控制,保证船坞分段搭载顺利进行。
1、分段完工状态目前船厂普遍的精度测量方法基本上是利用全站仪对分段相关点进行数据扫描,收集数据后用专用软件进行处理并与分段理论模型进行对比,尽量做到让实际分段与理论模型吻合。
在船舶实际建造中,常见的分段完工状态应该和理论模型一致,分段的变形需要进行矫正或制作胎架时释放一定反变形,让分段完工后朝着理论模型的方向变化。
另一种是该分段完工后产生的变形,虽然不能与理论模型数据吻合,但正是我们在船坞搭载阶段所需要的状态,或者认为在胎架制作时为让分段完工后达到与理论模型吻合所释放反变形反而不利于船坞搭载。
那么一个分段完工后究竟需要一个什么样的状态呢,这需要我们结合船坞的搭载时分段状态来判断,进而制定分段建造时分段反变形释放的方法。
下面将介绍两种不同分段状态要求下某造船厂分段反变形的释放应用。
船体结构建造精度控制要点
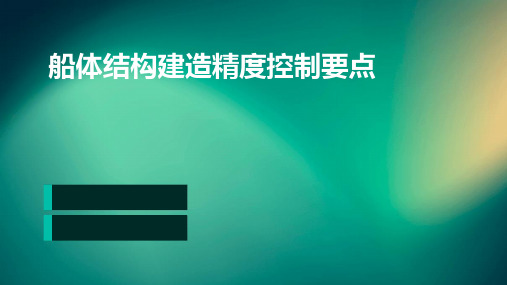
采用先进的加工设备和工艺方法,减 小加工过程中的误差。
组装阶段控制
在船体结构的组装过程中,应按照设 计要求进行组装,确保各部分之间的 相对位置和尺寸精度。
焊接阶段控制
焊接过程中应采用合理的焊接工艺和 参数,减小焊接变形和误差。
检测与调整
在船体结构建造完成后,应进行全面 的检测和调整,确保满足精度要求。
根据船体结构特点和建造工艺,制定合理的搭载精度标准和要求,包括
对齐度、错位量、垂直度等方面的规定。
02
制定搭载工艺流程和方案
根据船体结构特点和施工条件,制定详细的搭载工艺流程和方案,包括
吊装准备、定位测量、焊接方法等,确保搭载精度得到有效控制。
03
实施搭载精度检测
在搭载过程中,对各分段进行定位测量和调整,确保各分段按照精度要
05 船体建造精度检测与评估
建造精度的检测方法
全站仪检测法
激光测距法
利用全站仪对船体各部位进行高精度测量 ,获取各点的坐标值,与理论值进行比较 ,评估建造精度。
使用激光测距仪对船体进行快速、非接触 测量,获取各部位的距离数据,与理论值 进行比较,评估建造精度。
超声波检测法
射线检测法
利用超声波探头对船体内部结构进行无损 检测,获取各部位的尺寸信息,与理论值 进行比较,评估建造精度。
加强结构刚度
03
合理设计船体结构,增加支撑和加强结构,提高整体刚度,减
小变形。
焊接变形的矫正方法
机械矫正法
利用机械力对变形部位进行矫正,如使用矫直机、压力机等设备对 船体板材进行矫平。
火焰矫正法
利用火焰加热对变形部位进行局部加热,使材料产生热膨胀,冷却 后收缩,达到矫正变形的目的。
浅谈船体分段建造的精度管理与控制
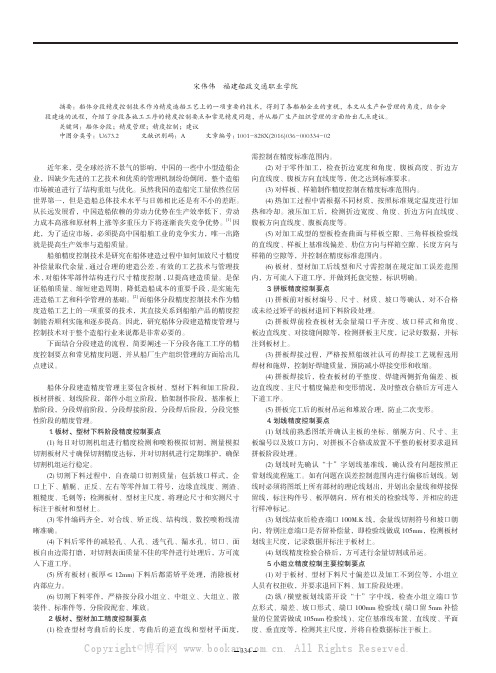
现代经济信息浅谈船体分段建造的精度管理与控制宋伟伟 福建船政交通职业学院摘要:船体分段精度控制技术作为精度造船工艺上的一项重要的技术,得到了各船舶企业的重视,本文从生产和管理的角度,结合分段建造的流程,介绍了分段各施工工序的精度控制要点和常见精度问题,并从船厂生产组织管理的方面给出几点建议。
关键词:船体分段;精度管理;精度控制;建议中图分类号:U673.2 文献识别码:A 文章编号:1001-828X(2016)036-000334-02一、引言近年来,受全球经济不景气的影响,中国的一些中小型造船企业,因缺少先进的工艺技术和优质的管理机制纷纷倒闭,整个造船市场被迫进行了结构重组与优化。
虽然我国的造船完工量依然位居世界第一,但是造船总体技术水平与日韩相比还是有不小的差距。
从长远发展看,中国造船依赖的劳动力优势在生产效率低下、劳动力成本高涨和原材料上涨等多重压力下将逐渐丧失竞争优势。
[1]因此,为了适应市场,必须提高中国船舶工业的竞争实力,唯一出路就是提高生产效率与造船质量。
船舶精度控制技术是研究在船体建造过程中如何加放尺寸精度补偿量取代余量,通过合理的建造公差,有效的工艺技术与管理技术,对船体零部件结构进行尺寸精度控制,以提高建造质量。
是保证船舶质量、缩短建造周期、降低造船成本的重要手段,是实施先进造船工艺和科学管理的基础。
[2]而船体分段精度控制技术作为精度造船工艺上的一项重要的技术,其直接关系到船舶产品的精度控制能否顺利实施和逐步提高。
因此,研究船体分段建造精度管理与控制技术对于整个造船行业来说都是非常必要的。
下面结合分段建造的流程,简要阐述一下分段各施工工序的精度控制要点和常见精度问题,并从船厂生产组织管理的方面给出几点建议。
二、船体分段建造精度管理的控制要点船体分段建造精度管理主要包含板材、型材下料和加工阶段,板材拼板、划线阶段,部件小组立阶段,胎架制作阶段,基准板上胎阶段,分段焊前阶段,分段焊接阶段,分段焊后阶段,分段完整性阶段的精度管理。
船体分段建造的精度管理和控制
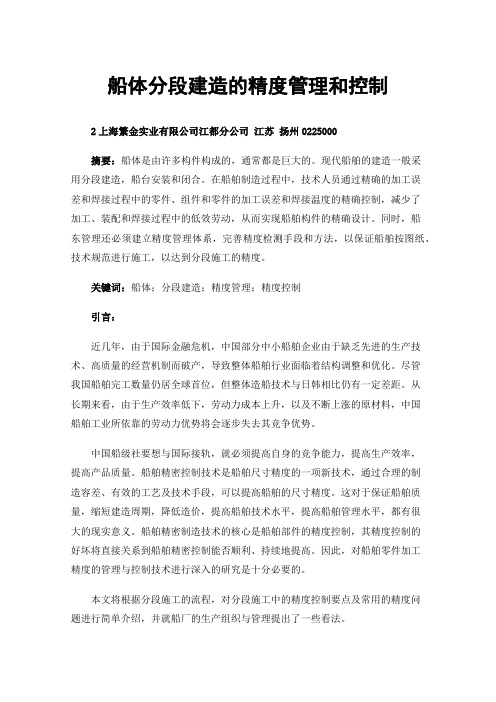
船体分段建造的精度管理和控制2上海繁金实业有限公司江都分公司江苏扬州0225000摘要:船体是由许多构件构成的,通常都是巨大的。
现代船舶的建造一般采用分段建造,船台安装和闭合。
在船舶制造过程中,技术人员通过精确的加工误差和焊接过程中的零件、组件和零件的加工误差和焊接温度的精确控制,减少了加工、装配和焊接过程中的低效劳动,从而实现船舶构件的精确设计。
同时,船东管理还必须建立精度管理体系,完善精度检测手段和方法,以保证船舶按图纸、技术规范进行施工,以达到分段施工的精度。
关键词:船体;分段建造;精度管理;精度控制引言:近几年,由于国际金融危机,中国部分中小船舶企业由于缺乏先进的生产技术、高质量的经营机制而破产,导致整体船舶行业面临着结构调整和优化。
尽管我国船舶完工数量仍居全球首位,但整体造船技术与日韩相比仍有一定差距。
从长期来看,由于生产效率低下,劳动力成本上升,以及不断上涨的原材料,中国船舶工业所依靠的劳动力优势将会逐步失去其竞争优势。
中国船级社要想与国际接轨,就必须提高自身的竞争能力,提高生产效率,提高产品质量。
船舶精密控制技术是船舶尺寸精度的一项新技术,通过合理的制造容差、有效的工艺及技术手段,可以提高船舶的尺寸精度。
这对于保证船舶质量,缩短建造周期,降低造价,提高船舶技术水平,提高船舶管理水平,都有很大的现实意义。
船舶精密制造技术的核心是船舶部件的精度控制,其精度控制的好坏将直接关系到船舶精密控制能否顺利、持续地提高。
因此,对船舶零件加工精度的管理与控制技术进行深入的研究是十分必要的。
本文将根据分段施工的流程,对分段施工中的精度控制要点及常用的精度问题进行简单介绍,并就船厂的生产组织与管理提出了一些看法。
一、船体分段建造过程中的精度管理(一)划线的精度管理在分段施工中,应强化船舶的划线管理。
这就要求设计师精确地控制挂舵臂、主机座、舵轴和胎座,以及确定外板与地板之间的间距。
在所有的胎盘焊接完毕后,技术人员会开始切割。
浅论船体分段建造施工中的施工质量控制

浅论船体分段建造施工中的施工质量控制摘要:船舶分段建造是当前造船企业采用最多的方式之一。
此种造船方式可以明显提高企业生产效率,方便施工、提高构件生产精度,对提高船舶整体制造质量、降低生产成本非常有利。
本文重点介绍船体分段建造方式,分析了船体分段建造过程中影响船体施工质量的主要因素及产生的原因。
提供了质量控制方法和焊接变形的预防措施。
为提高船舶制造业整体水平,提升造船整体质量具有积极意义。
关键词:船体分段;质量控制引言造船精度管理和控制是现代造船领域中的一项关键技术,控制分段的精度与质量是船体大合拢能够顺利实施的基础。
船体分段控制技术在船体建造中属于较为重要的工艺技术,与船体产品是否能够有效实施关系密切。
因此,船体分段建造过程中的精度管理和控制就显得尤为重要。
下文探究了分段建造的精度控制和管理。
1船体分段建造的步骤船体分段建造的信息经过精心设计,分为 4 个步骤:①建造船体分段的小组件,板材的拼接、型材的切割或者弯制、T 型面板的拼装和焊接。
②分段的建造,由小组件和T 型材的组合拼接,形成一定的开放式分段。
③船体总段的建造:由前面完成的小组立、小分段拼装起来,骨架外面的外板挂装,形成相对独立的封闭总段。
④总段上的附属结构,部分小件的安装(桅杆,舱口,门,扶手栏杆等)。
图 1 船体分段建造模型2船体分段建造质量控制分段建造精度的提高,主要有两种方式:一是采取在施工过程中运用检测手段,定期对分段进行检测,校正施工、再检测、循环往复。
以此来提高建造质量。
二是在施工过程中,制定反变形措施,采取各种校正手段,及时修正施工误差,以此提供船舶建造质量。
其中,对每一道工序的精度进行严格的控制,可以尽量减少多道工序误差累加到船体分段上,以达到最大限度地减少各个加工环节形成的的误差对船体质量造成的影响,2.1船体分段中构件的安装质量控制船体分段构件安装的质量控制是船体分段变形控制的重要环节,如果分段构件安装精度若达不到要求可能对船台分段对接及分段局部强度产生非常不利的影响,从而直接造成船体整体质量的下降。
船舶分段装配过程中的焊接变形控制
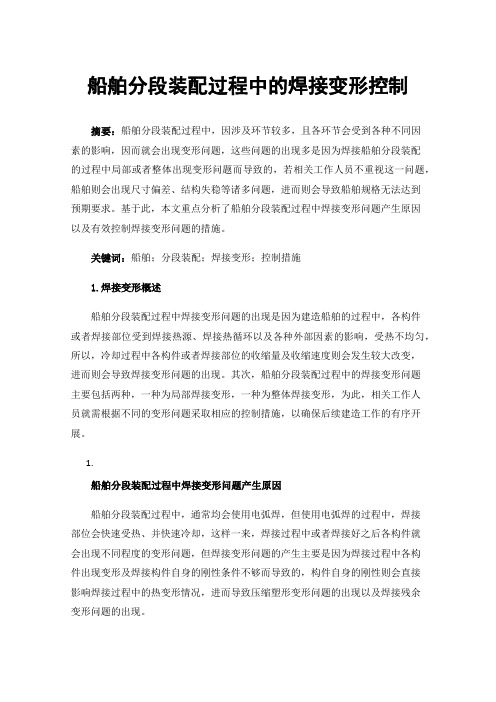
船舶分段装配过程中的焊接变形控制摘要:船舶分段装配过程中,因涉及环节较多,且各环节会受到各种不同因素的影响,因而就会出现变形问题,这些问题的出现多是因为焊接船舶分段装配的过程中局部或者整体出现变形问题而导致的,若相关工作人员不重视这一问题,船舶则会出现尺寸偏差、结构失稳等诸多问题,进而则会导致船舶规格无法达到预期要求。
基于此,本文重点分析了船舶分段装配过程中焊接变形问题产生原因以及有效控制焊接变形问题的措施。
关键词:船舶;分段装配;焊接变形;控制措施1.焊接变形概述船舶分段装配过程中焊接变形问题的出现是因为建造船舶的过程中,各构件或者焊接部位受到焊接热源、焊接热循环以及各种外部因素的影响,受热不均匀,所以,冷却过程中各构件或者焊接部位的收缩量及收缩速度则会发生较大改变,进而则会导致焊接变形问题的出现。
其次,船舶分段装配过程中的焊接变形问题主要包括两种,一种为局部焊接变形,一种为整体焊接变形,为此,相关工作人员就需根据不同的变形问题采取相应的控制措施,以确保后续建造工作的有序开展。
1.船舶分段装配过程中焊接变形问题产生原因船舶分段装配过程中,通常均会使用电弧焊,但使用电弧焊的过程中,焊接部位会快速受热、并快速冷却,这样一来,焊接过程中或者焊接好之后各构件就会出现不同程度的变形问题,但焊接变形问题的产生主要是因为焊接过程中各构件出现变形及焊接构件自身的刚性条件不够而导致的,构件自身的刚性则会直接影响焊接过程中的热变形情况,进而导致压缩塑形变形问题的出现以及焊接残余变形问题的出现。
2.1焊接因素从当前船舶的建造情况来看,船舶建造涉及方面相对较多,在主船体、分段及总段的建造中则会应用各种不同的焊接工艺,其中一些焊接工艺就会导致钢材出现不同程度的变形问题。
钢材出现变形问题是因为焊接分段装配的过程中焊接点产生了较高热量,而导致焊接部位及其周围区域温度存在较大差异,进而则会进一步导致不相容变形问题的出现。
其次,焊接船舶分段装配的过程中,工作人员管理水平的高低及其综合素养也会导致船舶焊接变形问题的出现。
船用钢板焊接变形及控制矫正
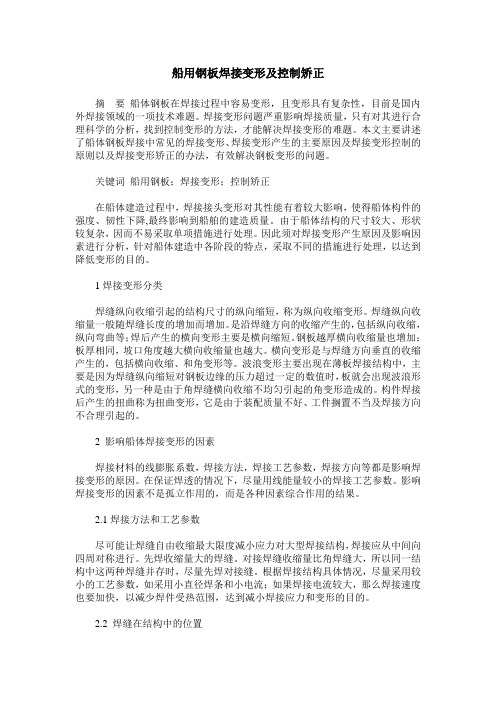
船用钢板焊接变形及控制矫正摘要船体钢板在焊接过程中容易变形,且变形具有复杂性,目前是国内外焊接领域的一项技术难题。
焊接变形问题严重影响焊接质量,只有对其进行合理科学的分析,找到控制变形的方法,才能解决焊接变形的难题。
本文主要讲述了船体钢板焊接中常见的焊接变形、焊接变形产生的主要原因及焊接变形控制的原则以及焊接变形矫正的办法,有效解决钢板变形的问题。
关键词船用钢板;焊接变形;控制矫正在船体建造过程中,焊接接头变形对其性能有着较大影响,使得船体构件的强度、韧性下降,最终影响到船舶的建造质量。
由于船体结构的尺寸较大、形状较复杂,因而不易采取单项措施进行处理。
因此须对焊接变形产生原因及影响因素进行分析,针对船体建造中各阶段的特点,采取不同的措施进行处理,以达到降低变形的目的。
1焊接变形分类焊缝纵向收缩引起的结构尺寸的纵向缩短,称为纵向收缩变形。
焊缝纵向收缩量一般随焊缝长度的增加而增加。
是沿焊缝方向的收缩产生的,包括纵向收缩,纵向弯曲等;焊后产生的横向变形主要是横向缩短。
钢板越厚横向收缩量也增加;板厚相同,坡口角度越大横向收缩量也越大。
横向变形是与焊缝方向垂直的收缩产生的,包括横向收缩、和角变形等。
波浪变形主要出现在薄板焊接结构中,主要是因为焊缝纵向缩短对钢板边缘的压力超过一定的数值时,板就会出现波浪形式的变形,另一种是由于角焊缝横向收缩不均匀引起的角变形造成的。
构件焊接后产生的扭曲称为扭曲变形,它是由于装配质量不好、工件搁置不当及焊接方向不合理引起的。
2 影响船体焊接变形的因素焊接材料的线膨胀系数,焊接方法,焊接工艺参数,焊接方向等都是影响焊接变形的原因。
在保证焊透的情况下,尽量用线能量较小的焊接工艺参数。
影响焊接变形的因素不是孤立作用的,而是各种因素综合作用的结果。
2.1焊接方法和工艺参数尽可能让焊缝自由收缩最大限度减小应力对大型焊接结构,焊接应从中间向四周对称进行。
先焊收缩量大的焊缝。
对接焊缝收缩量比角焊缝大,所以同一结构中这两种焊缝并存时,尽量先焊对接缝。
船体分段装配焊接工艺流程以及变形的预防与矫正
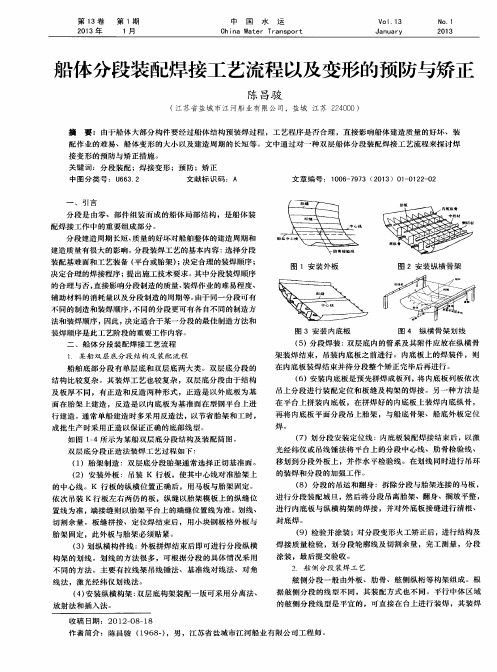
配 作 业 的难 易 、船 体 变 形 的大 小 以及 建 造 周 期 的长 短 等 。文 中 通 过 对 一 种 双 层船 体 分段 装 配 焊 接 工 艺 流 程 来 探 讨 焊 接 变形 的预 防与 矫 正 措 施 。
分段 建 造 周 期 长 短 、 质 量 的好坏 对 船 舶 整 体 的建 造 周 期 和 建 造 质 量 有很 大 的影 响 。 分段 装 焊 工 艺 的基 本 内容 : 选 择 分 段 装 配 基 难 面和 工 艺 装 备 ( 平 台 或胎 架 ) ; 决 定合 理 的装 焊 顺 序 ; 决 定 合 理 的 焊接 程 序 ; 提 出施 工 技 术 要 求 。 其 中分 段 装焊 顺 序 的合 理 与 否 , 直 接 影 响 分段 制 造 的质 量 、 装 焊 作 业 的难 易 程 度 、 辅 助 材 料 的 消 耗量 以及 分 段 制造 的 周期 等 。 由于 同一 分 段 可有 不 同 的制 造 和 装焊 顺 序 , 不 同 的分 段 更 可 有各 自不 同的 制造 方 法和 装 焊 顺 序 , 因此 , 决 定 适合 于 某 一 分 段 的最 佳 制 造 方 法和
的装 焊 和 分 段 的加 强 工 作 。
( 1 )胎 架 制 造 :双 层 底 分段 胎架 通 常 选 择 正 切 基 准 面 。
( 2 )安 装 外 板 : 吊装 K 行 板 ,使 其 中 心线 对 准 胎 架 上
的 中 心 线 。 K 行 板 的纵 横 位 置 正 确 后 ,用 马 板 与 胎 架 固定 。 依 次 吊装 K 行板 左 右 两仍 的板 ,纵 缝 以胎 架 模 板 上 的 纵 缝位 置线为准 , 端 接 缝 则 以胎 架 平 台上 的端 缝 位 置 线 为 准 。划 线 、 切 割 余 量 。板 缝 拼 接 、定 位 焊 结束 后 ,用小 块钢 板 格 外板 与 胎 架 固定 ,此 外 板 与 胎 架 必 须 贴 紧 。 ( 3 )划 纵 横 构件 线 : 外板 拼焊 结束 后 即可 进 行 分 段 纵 横 构 架 的划 线 。划 线 的 方 法 很 多 ,可 根 据 分 段 的具 体 情 况 采 用 不 同 的 方法 。主 要 有 拉 线 架 吊线 锤 法 、 基 准 线 对 线 法 、 对 角
船体分段曲面外板焊接变形控制研究

船体分段曲面外板焊接变形控制研究作者:代能武柳武南来源:《中国科技纵横》2019年第01期摘要:焊接在造船行业过程中起着举足轻重的作用,焊接质量的好坏直接影响船体建造质量。
船体分段结构在焊接时,会不可避免出现焊接变形,目前,多采取预防措施对焊接变形进行控制。
本文探讨了焊接变形的基本形式,产生的主要因素及焊接顺序在控制分段外板焊接变形中的作用。
本文以10000DWT散货船机舱底部舷侧分段外板焊接变形控制为例分析了船体分段外板焊接变形的控制方法。
由于分段外板在曲面胎架上制作,因此本文还介绍了曲面胎架制作及曲面板架制造工艺。
关键词:分段外板焊接;装焊順序;变形控制中图分类号:U671 文献标识码:A 文章编号:1671-2064(2019)01-0077-020 前言随着焊接技术的发展,焊接也成为现代船舶建造中越来越关键的工序,不断研究和改进焊接技术在船舶建造中的应用对提高造船生产效率有很大的意义[2]。
在提高船舶的建造进度的同时,焊接工艺人员和技术人员一直致力于解决在焊接过程中出现的焊接变形问题。
公司在建造13000DWT散货船船体机舱底部舷侧分段外板焊接时采用新的工艺方法控制焊接变形,达到了理想的效果,为后续产品建造积累了经验。
1 焊接变形的定义及影响焊接过程中工件受到不均匀温度场的作用,构件的形状和外形尺寸发生变化称为焊接变形。
由于焊接工件在焊接电弧加热时的膨胀和冷却时的收缩各不相同,这样在构件中就产生了应力和变形。
例如在焊接钢质船体时,会引起船体结构的局部变形和总体变形。
如果焊后构件的变形量超过了精度要求的允许值,就需要进行焊后矫正变形处理。
有的变形经矫正后虽然可以达到精度要求,但是耗资较大,有的干脆无法进行矫正,只好报废,造成浪费。
另一方面,焊后构件的内部还会产生焊接残余应力,这种应力会影响船体结构的承载能力,以及影响焊后机械加工的精度,而且是引起焊接裂纹和脆断的主要因素[5]。
2 焊接变形基本形式焊接变形的基本形式分为:纵向和横向收缩变形、角变形、弯曲变形、扭曲变形、波浪变形。
船体分段合拢施工要领
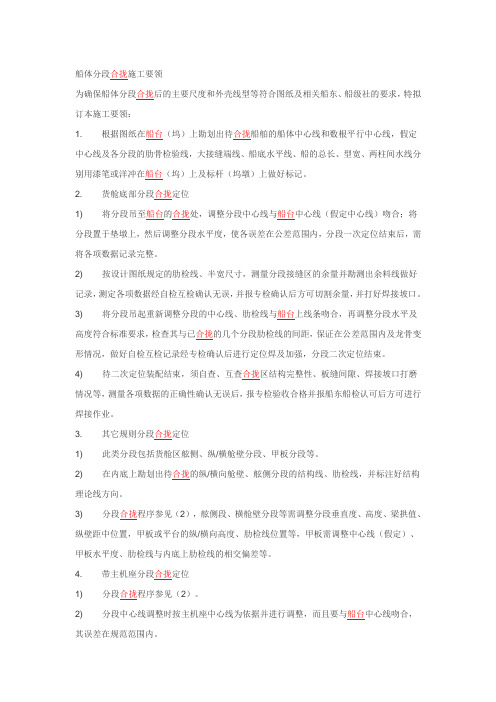
船体分段合拢施工要领为确保船体分段合拢后的主要尺度和外壳线型等符合图纸及相关船东、船级社的要求,特拟订本施工要领:1. 根据图纸在船台(坞)上勘划出待合拢船舶的船体中心线和数根平行中心线,假定中心线及各分段的肋骨检验线,大接缝端线、船底水平线、船的总长、型宽、两柱间水线分别用漆笔或洋冲在船台(坞)上及标杆(坞墩)上做好标记。
2. 货舱底部分段合拢定位1) 将分段吊至船台的合拢处,调整分段中心线与船台中心线(假定中心线)吻合;将分段置于垫墩上,然后调整分段水平度,使各误差在公差范围内,分段一次定位结束后,需将各项数据记录完整。
2) 按设计图纸规定的肋检线、半宽尺寸,测量分段接缝区的余量并勘测出余料线做好记录,测定各项数据经自检互检确认无误,并报专检确认后方可切割余量,并打好焊接坡口。
3) 将分段吊起重新调整分段的中心线、肋检线与船台上线条吻合,再调整分段水平及高度符合标准要求,检查其与已合拢的几个分段肋检线的间距,保证在公差范围内及龙骨变形情况,做好自检互检记录经专检确认后进行定位焊及加强,分段二次定位结束。
4) 待二次定位装配结束,须自查、互查合拢区结构完整性、板缝间隙、焊接坡口打磨情况等,测量各项数据的正确性确认无误后,报专检验收合格并报船东船检认可后方可进行焊接作业。
3. 其它规则分段合拢定位1) 此类分段包括货舱区舷侧、纵/横舱壁分段、甲板分段等。
2) 在内底上勘划出待合拢的纵/横向舱壁、舷侧分段的结构线、肋检线,并标注好结构理论线方向。
3) 分段合拢程序参见(2),舷侧段、横舱壁分段等需调整分段垂直度、高度、梁拱值、纵壁距中位置,甲板或平台的纵/横向高度、肋检线位置等,甲板需调整中心线(假定)、甲板水平度、肋检线与内底上肋检线的相交偏差等。
4. 带主机座分段合拢定位1) 分段合拢程序参见(2)。
2) 分段中心线调整时按主机座中心线为依据并进行调整,而且要与船台中心线吻合,其误差在规范范围内。
刍议船体结构焊接变形控制方法

焊接变形是焊接过程中被焊工件受到不均匀温度场的作用而产生的形状、尺寸变化称为焊接变形。随温度变化而变化的称为焊接瞬时变形;被焊工件完全冷却到初始温度时的改变,称为焊接残余变形;焊接变形对结构安装精度有很大影响,过大的变形将显著降低结构的承载能力。我国的某些研究人员在借鉴了国外研究成果的前提下对船体的焊接变形预测控制进行了全面的研究,同时还有一些研究人员采用固有的应变发对船体分段的焊接变形状况进行了预测,甚至还有一些研究人员他一出了移动热源的方式和自使用有限元网络划分的方法,这对解决结构焊接中变形和应力数值的计算有着十分积极的作用。
引言:
船舶精度建造技术就是通过科学的管理与先进的工艺手段对船体建造进行全过程的精度分析与控制,最大限度地减少现场修正工作量,提高工作效率缩短建造周期,降低建造成本,保证产品质量。影响船舶建造精度的因素很多,如下料、成型、吊装、焊接等。其中,焊接变形是精度控制的关键因素。由于焊接变形对船舶建造质量、成本和周期都具有重要影响,工业界一直对其非常重视,对焊接变形从实验和理论上都进行了大量研究,期望能够对焊接过程进行有效预测和控制。
刍议船体结构焊接变形控制方法
摘要:本文主要对船体结构焊接变形控制方法进一步分析。船体结构的焊接变形控制在造船工程中是非常重要的一个环节,这项工作对于船舰质量以及造船周期的控制都有着十分积极的意义,所以我们一定要采取有效的措施对传统结构焊接变形加以严格的控制。
关键词:船体结构;焊接变形;控制方法;现状;因素;矫正
7.结构设计
船体结构设计过程中是否能够依照结构焊接变形现象采取有效的控制和应对方法,对于焊接变形的控制有极大作用。通常在船体结构变形设计时采取的控制变形方法有:选择合理的施工工艺按照船体结构特点选择合适的工艺;将船体进行分段,分散焊接变形力度;焊缝时尽量选择短的焊缝;选用能够减少焊接次数的结构类型等。
船体分段焊接变形控制

船体分段焊接变形控制摘要:船舶建造过程中焊接工作量极大,因焊接产生的热量所引起的变形是船舶建造过程中始终存在的一项重要的精度难题。
为了提高生产效率和缩短产品周期,就必须控制好焊接变形,以保证分段的精度质量。
关键词:船体分段焊接变形精度焊接顺序对称焊接收缩量1 工艺要求1.1 为控制焊接变形,一般应先焊收缩量大的焊缝,后焊收缩量小的焊缝。
船体结构焊缝的焊接顺序是先焊对接缝,后焊角接缝。
对接缝的焊接顺序是先焊平对接,后焊横对接,最后焊立对接;带坡口的接头先焊,不带坡口的接头后焊。
角接缝的焊接顺序是先焊立角接缝,后焊平角接缝。
1.2 在CO2衬垫多层多道焊时,第一层焊缝焊接电流不允许超过 200 安培;层间温度应控制在 200℃左右,为防止产生裂缝,第一层焊缝结束后,第二层焊缝要立即盖上去,每道焊缝宽度不宜超过 14 毫米。
1.3 特殊分段焊接,如艉轴管与铸钢件及构架焊接时,为控制艉轴管中心线偏移,要派专人进行测量,当出现中心线超公差产生椭圆度时,要及时改变焊接顺序,在椭圆的短轴上先焊,使艉轴管保持正圆。
1.4 分段在设计时,应加放焊接收缩补偿量,具体焊接补偿量按照《船体精度布置图》进行加放。
2 工艺过程2.1 货舱区双层底分段焊接变形控制。
2.1.1 施工方法及状态2.1.1.1建造方案:双层底分段分为内底板部件和外底板部件;内底板部件带内底纵骨、肋板和纵桁,外底板部件只带船底纵骨,分别在平面流水线制作。
最后内底部件翻身扣在外底部件上。
2.1.1.2建造简要程序:a)外底板拼板→焊接→外底纵骨装配→焊接→移出平面流水线平台运输至外场胎架上。
b)内底拼板→焊接→内底纵骨装配→焊接纵骨→肋板、纵桁、管弄板架装配→焊接→移出流水线平台翻身扣在外底板部件上。
c)舭部底板、纵骨→焊接→舭部板架吊在内底分段胎架上合拢→焊接→舭部外板(转圆板)→焊接。
2.1.1.3 分段状态:a)内底板架在平面分段流水线平台上,反造时,内底板为自由状态水平放置在平台上;b)内底板架翻身扣在外板上,为自由状态,对纵、横结构与外板的角焊缝进行焊接。
- 1、下载文档前请自行甄别文档内容的完整性,平台不提供额外的编辑、内容补充、找答案等附加服务。
- 2、"仅部分预览"的文档,不可在线预览部分如存在完整性等问题,可反馈申请退款(可完整预览的文档不适用该条件!)。
- 3、如文档侵犯您的权益,请联系客服反馈,我们会尽快为您处理(人工客服工作时间:9:00-18:30)。
船体分段焊接变形控制
发表时间:2019-09-22T01:13:29.953Z 来源:《基层建设》2019年第19期作者:屈友平赵承平[导读] 摘要:船舶建造过程中焊接工作量极大,因焊接产生的热量所引起的变形是船舶建造过程中始终存在的一项重要的精度难题。
广船国际有限公司 511458
摘要:船舶建造过程中焊接工作量极大,因焊接产生的热量所引起的变形是船舶建造过程中始终存在的一项重要的精度难题。
为了提高生产效率和缩短产品周期,就必须控制好焊接变形,以保证分段的精度质量。
关键词:船体分段焊接变形精度焊接顺序对称焊接收缩量
1 工艺要求
1.1 为控制焊接变形,一般应先焊收缩量大的焊缝,后焊收缩量小的焊缝。
船体结构焊缝的焊接顺序是先焊对接缝,后焊角接缝。
对接缝的焊接顺序是先焊平对接,后焊横对接,最后焊立对接;带坡口的接头先焊,不带坡口的接头后焊。
角接缝的焊接顺序是先焊立角接缝,后焊平角接缝。
1.2 在CO2衬垫多层多道焊时,第一层焊缝焊接电流不允许超过 200 安培;层间温度应控制在 200℃左右,为防止产生裂缝,第一层焊缝结束后,第二层焊缝要立即盖上去,每道焊缝宽度不宜超过 14 毫米。
1.3 特殊分段焊接,如艉轴管与铸钢件及构架焊接时,为控制艉轴管中心线偏移,要派专人进行测量,当出现中心线超公差产生椭圆度时,要及时改变焊接顺序,在椭圆的短轴上先焊,使艉轴管保持正圆。
1.4 分段在设计时,应加放焊接收缩补偿量,具体焊接补偿量按照《船体精度布置图》进行加放。
2 工艺过程
2.1 货舱区双层底分段焊接变形控制。
2.1.1 施工方法及状态
2.1.1.1建造方案:双层底分段分为内底板部件和外底板部件;内底板部件带内底纵骨、肋板和纵桁,外底板部件只带船底纵骨,分别在平面流水线制作。
最后内底部件翻身扣在外底部件上。
2.1.1.2建造简要程序:
a)外底板拼板→焊接→外底纵骨装配→焊接→移出平面流水线平台运输至外场胎架上。
b)内底拼板→焊接→内底纵骨装配→焊接纵骨→肋板、纵桁、管弄板架装配→焊接→移出流水线平台翻身扣在外底板部件上。
c)舭部底板、纵骨→焊接→舭部板架吊在内底分段胎架上合拢→焊接→舭部外板(转圆板)→焊接。
2.1.1.3 分段状态:
a)内底板架在平面分段流水线平台上,反造时,内底板为自由状态水平放置在平台上; b)内底板架翻身扣在外板上,为自由状态,对纵、横结构与外板的角焊缝进行焊接。
2.1.2 焊接顺序
2.1.2.1内外底板拼板示意图
a)焊接方法:横向对接缝采用 CO2衬垫焊+埋弧自动焊
纵向对接缝采用 FCB 法焊接;
b)焊接顺序:如图1,①、②、③为施焊顺序
图1
2.1.2.2纵骨与内底板焊接示意图
a)焊接方法:采用 16 电极 HS-MAG 自动角焊机
b)焊接顺序:如图 2,①、②、③、④、⑤、⑥
图2
2.1.2.3内底分段肋板、纵桁、管弄板架焊接示意图
a)组装焊接方法:采用 CO2半自动和自动角焊机焊接
b)焊接顺序:如图 3,由双数焊工对称同时进行焊接,焊工人数不超过 12 人,焊接方向从中间向前后、左右推进,先焊纵桁与肋板之间的立角焊,再焊纵向肋板与横向肋板之间的立角焊,后焊纵桁肋板与内底板之间的平角焊。
图3
2.1.2.4 舭部底板与纵骨、肘板焊接示意图
a)焊接方法:舭部底板与纵骨之间平角焊采用 16 电极 HS-MAG 自动角焊,肘板与底板采用 CO2半自动焊。
b)焊接顺序:如图 4,肘板与底板间角焊缝由二名焊工从中间向左右、前后方向对称焊接。
图4
2.1.2.5内底板架扣在外底板上与舭部分段合拢焊接按图 5 a)焊接方法:采用 CO2半自动角焊和 CO2半自动衬垫焊 b)焊接顺序:
①焊内底板架扣在外底板上结构焊缝。
由双数焊工同时进行焊接,焊接方向从中间向前后、左右推进。
先焊内底板架纵横构架与外底纵骨之间的立角焊,后焊纵横构架与外底板之间的平角焊。
具体顺序参见图3。
②焊舭部与内底分段合拢焊缝。
先焊内底分段与舭部分段纵向外板对接缝,由二名焊工从中间向艏艉两端焊接;再焊舭部转圆板与舭部底板对接缝(同样由两名焊工从中间向两端焊接);后焊舭部分段大肘板与边纵桁立角焊,最后焊舭部转圆板与肘板平角焊缝。
图5
2.2 机舱底部分段焊接变形控制
2.2.1 施工方法及状态
2.2.1.1 建造方案:以内底平台为基面在胎架上反造。
2.2.1.2 建造简要程序:
a)内底平台拼板→焊接→纵桁、肋板组装→焊接→机舱底部贴外板→焊接→翻身放在曲面胎架上→肋板、纵桁与外板角接缝焊接; b)横隔舱拼板→焊接→T 形件、边水舱通道组装→焊接; c)左(右)舷侧外板拼板→焊接→半隔舱、肋骨组装→焊接; d)机舱底部以自由状态按置在曲面胎架上→隔舱组装→焊接→左右舷外板组装→焊接。
2.2.1.3 分段状态
a)机舱内底板以自由状态放置在平台胎架上,外底贴板接缝焊接结束后移出平台胎架; b)机舱外底板翻身后以自由状态放置在曲面胎架上,按装横隔舱、左(右)舷侧分段及纵横构架,然后进行焊接。
2.2.2 焊接顺序
2.2.2.1 平台板、拼板示意图
a)焊接方法:采用埋弧自动焊和 CO2衬垫焊
b)焊接顺序:如图6,①②③④⑤⑥⑦⑧
图6
2.2.2.2 纵横向构架(纵桁、肋板)组装焊接按图7。
a)组装焊接方法:采用 CO2半自动和自动角焊机焊接;
b)焊接顺序:由双数焊工同时进行焊接,焊接方向从中间向前后、左右推进,先焊中纵桁与肋板之间的立角焊,再焊边纵桁与肋板之间的立角焊最后焊纵桁、肋板与平台板之间的平角焊。
图7
2.2.2.3 机舱底部分段外板装焊示意图
a)焊接方法:采用 CO2衬垫焊和 CO2衬垫焊+埋弧自动焊;
b)焊接顺序:由双数焊工进行对称焊接。
先焊 K 行底板纵缝,后焊边缝,最后焊横向对接缝及纵向边接缝。
具体顺序,见图8。
图8
2.2.2.4 舷侧外板拼板及构架装焊按图9。
a)焊接方法:采用 CO2半自动焊和 CO2衬垫焊由双数焊工进行对称焊接。
先焊舷侧外板对接缝,后焊隔舱、肋骨与舷侧外板角焊缝,最后焊构架与舷外板角焊缝,焊接方向从中间向前后、左右推进。
图9
2.2.2.5 横隔舱拼板及构架装焊按图10。
a)焊接方法:埋弧自动焊、CO2半自动焊及自动角焊
b)焊接顺序:隔舱拼板先焊端接缝①,后焊边接缝②。
加强筋焊接从中间向左、右舷对称焊接。
图10
2.2.2.6 机舱底部分段纵横构架与外板角焊缝焊接按图 11。
机舱底部分段翻身后以自由状态放置在曲面胎架上,采用 CO2半自动焊,焊接纵桁、肋板与外板的角焊缝。
焊接顺序:与 2.1.2.5 双层底构架与外板焊接方法相同。
由双数焊工同时进行焊接。
焊接方向从中间向前后、左右推进。
图 11
2.2.2.7 机舱底部分段组装焊接按图 12。
a)焊接方法:采用 CO2衬垫焊和 CO2半自动焊。
b)焊接顺序:
①先焊横隔舱与内底平台板角焊缝,从中间向左右方向焊接。
后焊隔舱扶强材与平台板角焊缝。
②焊舷部外板纵向对接缝,从中间向艏艉方向焊接。
③焊左、右舷分段部分隔舱与横隔舱垂直对接缝,焊接方向,由下向上焊。
④焊纵横构架与平台板角焊缝。
图12
2.3 艉部分段焊接变形控制
2.3.1 施工方法及状态
2.3.1.1 建造方案:以艉部横舱壁为基面卧造。
2.3.1.2 建造简要程序:
a)艉轴管轧圆合拢→焊接→艉轴管与艉轴毂合拢→焊接;
b)横隔舱拼板→焊接→纵桁、肋板、平台板→焊接→艉轴管插入分段后与前轴毂铸钢件合拢→焊接→贴外板焊接。
2.3.1.3 分段状态
艉部分段卧造时,艉部横隔舱为自由状态水平安置在胎架上。
艉轴管吊入分段为自由状态,与纵横构架焊接。
2.3.2 焊接顺序
2.3.2.1 艉轴管轧圆后,装焊按图 13。
a)焊接方法:采用 CO2衬垫焊+埋弧自动焊;
b)焊接顺序:由 2 名焊工从中间向两端进行焊接。
图13
2.3.2.2 艉轴管与艉轴毂铸钢件装焊按图 14。
a)焊接方法:采用 CO2半自动衬垫焊;
b)焊接顺序:由二名焊工进行对称焊接。
图14
2.3.2.3 横隔舱拼板焊接按图 15。
a)焊接方法:采用埋弧自动焊、CO2半自动焊;
b)焊接顺序:见图 15 中 1、2、3、4、5;
c)拼板焊接结束后,装纵、横构架,焊接构架与隔舱角焊缝,由双数焊工从中间向两端进行焊接。
工从中间向前后、左右方向推进。
c)先焊短焊缝,后焊长焊缝,短焊缝可从下向上焊、长焊缝应采用分段焊。