膜片弹簧课程了设计说明书
膜片弹簧离合器设计说明书

关键词:离合器;膜片弹簧;从动盘; 压盘 ;摩擦片
1离合器概述
1.1离合器的组成
对于以燃机为动力的汽车,离合器在机械传动系中是作为一个独立的总成而存在的。它是汽车传动系中直接与发动机相连的总成。目前,各种汽车广泛采用的摩擦离合器是一种依靠主、从动部分之间的摩擦来传递动力且能分离的装置。它主要包括主动部分、从动部分、压紧机构和操纵机构等四部分。主动部分由飞轮、离合器盖和压盘等组成;从动部分由从动盘等组成;压紧机构由压紧弹簧组成;操纵机构由分离叉、分离轴承、离合器踏板和传动部分等组成。
1.2离合器的功用
1)在汽车起步时,通过离合器主动部分(与发动机曲轴相联)和从动部分(与变速器第一轴相接)之间的滑磨、转速的逐渐接近,使旋着的发动机和原为静止的传动系平稳地接合,以保证汽车平稳起步;
2)当变速器换挡时,通过离合器主、从动部分的迅速分离来切断动力传递,以减轻换挡时轮齿间的冲击,便于换挡;
1—飞轮; 2—摩擦片; 3—离合器盖; 4—分离轴承; 5—压盘; 6—膜片弹簧; 7—支撑环
4)离合器从动部分转动惯量要小,以减轻换挡时变速器换挡齿轮之间的冲击,便于换挡和减小同步器的磨损;
5)能避免和衰减传动系的扭振,具有吸收振动、冲击和降低噪声的能力;
6)应有足够的吸热能力和良好的通风散热效果,以保证工作温度不致于过高,延
长其使用寿命;
7)操纵轻便、准确,以减轻驾驶员的疲劳;
8)具有足够的强度和动平衡,以保证其工作可靠、使用寿命长;
1.5膜片弹簧离合器
膜片弹簧是一种由弹簧钢制成的具有特殊结构的蝶形弹簧,主要由碟簧部分和分离指部分组成。在膜片弹簧离合器中膜片弹簧有压紧弹簧和分离杠杆的双重作用,所以膜片弹簧离合器的结构设计主要是包括从动盘总成、膜片弹簧和压盘总成三个部分。膜片弹簧为碟形,其上开有若干个径向开口,形成若干个弹性杠杠。弹簧中部有钢丝支承圈,用铆钉将其安装在离合器盖上。在离合器盖未固定到飞轮上时,膜片弹簧处于自由状态,离合器盖与飞轮接合面间有一距离L。 用螺栓将离合器盖固定到飞轮上时,离合器盖通过后钢丝支承圈把膜片弹簧中部向前移动了一段距离。由于膜片弹簧外端位置没有变化,所以膜片弹簧被压缩变形。膜片弹簧外缘通过压盘把从动盘压靠在飞轮后端面上,这时离合器为接合状态。在分离离合器时,分离轴承前移,膜片弹簧将以前钢丝支承圈为支点,其外缘向后移动,在分离钩的作用下,压盘离开从动盘后移,离合器就变为分离状态了。
中型载重车膜片弹簧离合器设计(后备功率小)课程设计说明书

中型载重车膜片弹簧离合器设计(后备功率小)课程设计说明书汽车设计课程设计任务书学院名称:交通与汽车工程学院课程代码:__ ____ 专业:车辆工程年级: 2008一、设计题目:中型载重车膜片弹簧离合器设计(后备功率小)二、主要内容:1.离合器基本参数及尺寸确定;2.离合器主要部件设计计算;3.离合器操纵机构设计计算;4.绘制膜片弹簧零件图;5.绘制膜片弹簧离合器装配图。
三、具体要求及应提交的材料1.每一位同学按照指定的参数进行设计;2.膜片弹簧设计计算编制程序完成,并打印出膜片弹簧特性曲线图(图必须标明六个点及主要参数);3.说明书不得抄袭,必须独立完成;4.必须按时完成;5.设计说明书按规定格式书写;6.完成应提交的材料:设计说明书一份、离合器装配总图一张(1:1)、膜片弹簧零件图一张(1:1)。
四、主要技术路线提示1.根据已知数据初算摩擦片尺寸,然后根据相关约束条件进行验算;2.根据摩擦片外径初步确定膜片弹簧外径;3.初步确定膜片弹簧有关参数及用程序进行对参数调整直到满足要求为止;4.压盘传动及定中方式确定;5.操纵机构设计计算。
五、进度安排1.准备及任务布置1天;2.离合器基本参数及尺寸确定1天;3.离合器主要部件设计计算4天;4.离合器操纵机构设计计算1天;5.绘制膜片弹簧零件图1.5天;6.绘制膜片弹簧离合器装配图4天;7.编写设计说明书2天;8.机动时间0.5天。
六、推荐参考资料不少于3篇1. 王望予主编主编主编吴宗泽主编摘要 2引言 31摩擦离合器基本结构尺寸、参数的选择 41.1离合器基本性能关系式41.2摩擦片外径D与内径d的选择 41.3 离合器后备系数的确定 61.4 单位压力P的确定61.5 离合器基本参数的约束条件72离合器从动盘总成设计92.1摩擦片设计92.2从动盘毂设计92.3从动片设计122.4扭转减振器设计123 膜片弹簧设计163.1 膜片弹簧的概念163.2 膜片弹簧的弹性特性163.3 膜片弹簧主要参数的选择164 压盘和离合器盖的设计234.1 压盘设计234.2离合器盖设计245 离合器操纵机构设计265.2 操纵机构结构形式选择265.3 离合器操纵机构的设计计算26摘要本次课程设计的是中型载重车膜片弹簧离合器,根据所给汽车发动机的最大扭矩、最大转速、最大功率等基本参数等基本参数确定离合器基本参数。
膜片弹簧说明书
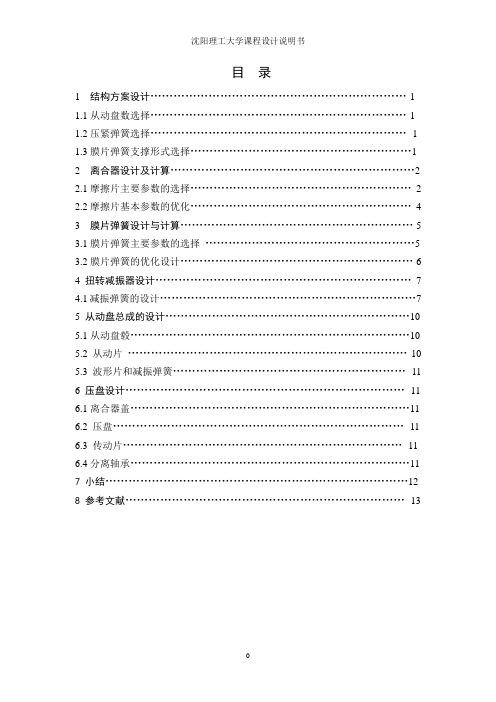
目录1 结构方案设计 (1)1.1从动盘数选择 (1)1.2压紧弹簧选择 (1)1.3膜片弹簧支撑形式选择 (1)2 离合器设计及计算 (2)2.1摩擦片主要参数的选择 (2)2.2摩擦片基本参数的优化 (4)3 膜片弹簧设计与计算 (5)3.1膜片弹簧主要参数的选择 (5)3.2膜片弹簧的优化设计 (6)4 扭转减振器设计 (7)4.1减振弹簧的设计 (7)5 从动盘总成的设计 (10)5.1从动盘毂 (10)5.2 从动片 (10)5.3 波形片和减振弹簧 (11)6压盘设计 (11)6.1离合器盖 (11)6.2 压盘 (11)6.3 传动片 (11)6.4分离轴承 (11)7 小结 (12)8 参考文献 (13)1结构方案设计1.1从动盘数选择选择单片离合器。
本车型为宝马,汽车总质量为1335kg,发动机最大转矩为200N·m。
对于乘用车,发动机的最大转矩一般不大,在布置尺寸允许条件下,通常离合器只设有一片从动盘。
盘片离合器结构简单,轴向尺寸紧凑,散热良好,维修调整方便,从动部分转动惯量小,在使用时能保证分离彻底,采用轴向有弹性的从动盘可保证结合平顺。
1.2压紧弹簧选择选择拉式膜片弹簧离合器选择膜片弹簧的原因:1)膜片弹簧的轴向尺寸小而径向尺寸很大,有利于提高离合器传递转矩能力的情况下减小离合器轴向尺寸。
2)不需要专门的分离杠杆,使离合器结构简化,零件数目少,质量轻。
3)可适当增加压盘厚度提高热容量;还可以在压盘上增设散热筋及离合器盖上开设较大的通风孔来改善散热条件。
4)主要部件形状简单,大批量生产可降低生产成本。
选择拉式膜片弹簧的原因:1)由于拉式膜片弹簧是以其中部压紧压盘,在压盘大小相同的条件下课使用直径相对较大的膜片弹簧,从而实现在不增加分离时的操纵力的前提下,提高压盘的压紧力和传递转矩的能力;或在传递转矩相同的条件,减小压盘的尺寸。
2)零件数目少,其结构简单、紧凑、质量轻。
膜片弹簧说明书
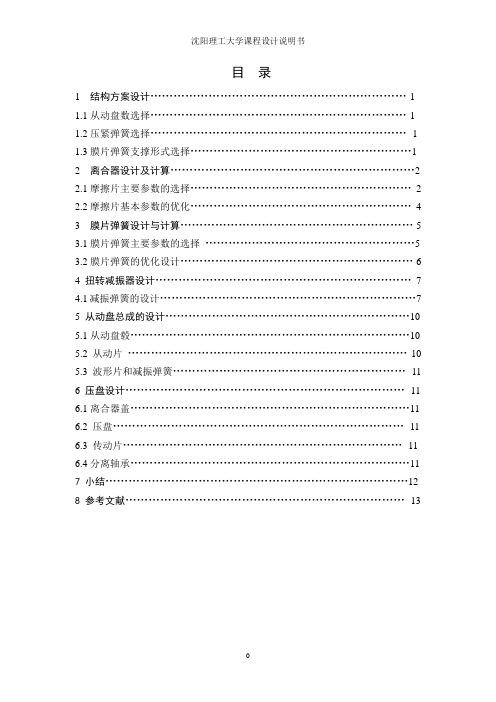
目录1 结构方案设计 (1)1.1从动盘数选择 (1)1.2压紧弹簧选择 (1)1.3膜片弹簧支撑形式选择 (1)2 离合器设计及计算 (2)2.1摩擦片主要参数的选择 (2)2.2摩擦片基本参数的优化 (4)3 膜片弹簧设计与计算 (5)3.1膜片弹簧主要参数的选择 (5)3.2膜片弹簧的优化设计 (6)4 扭转减振器设计 (7)4.1减振弹簧的设计 (7)5 从动盘总成的设计 (10)5.1从动盘毂 (10)5.2 从动片 (10)5.3 波形片和减振弹簧 (11)6压盘设计 (11)6.1离合器盖 (11)6.2 压盘 (11)6.3 传动片 (11)6.4分离轴承 (11)7 小结 (12)8 参考文献 (13)1结构方案设计1.1从动盘数选择选择单片离合器。
本车型为宝马,汽车总质量为1335kg,发动机最大转矩为200N·m。
对于乘用车,发动机的最大转矩一般不大,在布置尺寸允许条件下,通常离合器只设有一片从动盘。
盘片离合器结构简单,轴向尺寸紧凑,散热良好,维修调整方便,从动部分转动惯量小,在使用时能保证分离彻底,采用轴向有弹性的从动盘可保证结合平顺。
1.2压紧弹簧选择选择拉式膜片弹簧离合器选择膜片弹簧的原因:1)膜片弹簧的轴向尺寸小而径向尺寸很大,有利于提高离合器传递转矩能力的情况下减小离合器轴向尺寸。
2)不需要专门的分离杠杆,使离合器结构简化,零件数目少,质量轻。
3)可适当增加压盘厚度提高热容量;还可以在压盘上增设散热筋及离合器盖上开设较大的通风孔来改善散热条件。
4)主要部件形状简单,大批量生产可降低生产成本。
选择拉式膜片弹簧的原因:1)由于拉式膜片弹簧是以其中部压紧压盘,在压盘大小相同的条件下课使用直径相对较大的膜片弹簧,从而实现在不增加分离时的操纵力的前提下,提高压盘的压紧力和传递转矩的能力;或在传递转矩相同的条件,减小压盘的尺寸。
2)零件数目少,其结构简单、紧凑、质量轻。
毕业设计(论文)-拉式膜片弹簧离合器设计说明书[管理资料]
![毕业设计(论文)-拉式膜片弹簧离合器设计说明书[管理资料]](https://img.taocdn.com/s3/m/4ae36307ba0d4a7302763af9.png)
拉式膜片弹簧离合器设计第1章绪本次设计,我力争把离合器设计系统化,为离合器设计者提供一定的参考价值。
抛弃传统的推式膜片弹簧离合器,设计新式的拉式膜片弹簧离合器是本次设计的主要特点。
近年来各国政府都从资金、技术方面大力发展汽车工业,使其发展速度明显比其它工业要快的多,因此汽车工业迅速成为一个国家工业发展水平的标志。
对于内燃机汽车来说,离合器在机械传动系中作为一个独立的总成而存在,它是汽车传动系中直接与发动机相连接听总成。
目前,各种汽车广泛采用的摩擦式离合器主要依靠主、从动部分之间的摩擦来传递动力且能分离的装置。
在早期研发的离合器中,锥形离合器最为成功。
现今所用的盘片式离合器的先驱是多片盘式离合器,它是直到1925年以后才出现的。
20世纪20年代末,直到进入30年代时,只有工程车辆、赛车和大功率的轿车上才采用多片离合器。
多年的实践经验和技术上的改进使人们逐渐趋向于首选单片干式离合器[1]。
近来,人们对离合器的要求越来越高,传统的推式膜片弹簧离合器结构正逐步地向拉式膜片弹簧离合器结构发展,传统的操纵形式的操纵形式正向自动操纵的形式发展。
因此,提高离合器的可靠性和延长其使用寿命,适应发动机的高转速,增加离合器传递转矩的能力和简化操纵,已成为离合器的发展趋势。
随着汽车发动机转速、功率不断提高和汽车电子技术的高速发展,人们对离合器的要求越来越高。
从提高离合器工作性能的角度出发,传统的推式膜片弹簧离合器结构正逐步地向拉式膜片弹簧离合器结构发展,传统的操纵形式正向自动操纵的形式发展。
因此,提高离合器的可靠性和延长其使用寿命,适应发动机的高转速,增加离合器传递转矩的能力和简化操纵,已成为离合器的发展趋势。
随着计算机的发展,设计工作已从手工转向电脑,包括计算、性能演示、计算机绘图、制成后的故障统计等等。
按动力传递顺序来说,离合器应是传动系中的第一个总成。
顾名思义,离合器是“离”与“合”矛盾的统一体。
离合器的工作,就是受驾驶员操纵,或者分离,或者接合,以完成其本身的任务。
吨商用车膜片弹簧离合器设计说明书

目录1 离合器概述..................................... 错误!未定义书签。
离合器的简介. (2)汽车离合器的主要功用............................ 错误!未定义书签。
2膜片弹簧离合器结构分析与计算.. (3)膜片弹簧离合器的结构 (3)设计变量 (4)目标函数........................................ 错误!未定义书签。
约束条件.. (6)3 膜片弹簧的设计 (8)膜片弹簧的基本参数的选择........................ 错误!未定义书签。
膜片弹簧的弹性特性曲线.. (15)强度校核 (15)4扭转减振器的设计 (15)扭转减振器主要参数 (15)减振弹簧的计算 (15)5 从动盘总成的设计 (16)盘总成零件功能介绍 (17)从动盘毂 (18)从动片 (18)波形片和减振弹簧 (18)6 压盘设计 (19)离合器盖 (19)压盘 (20)传动片 (18)分离轴承 (19)7 总结 (20)参考文献 (21)1 离合器概述离合器的简介:联轴器、离合器和制动器是机械传动系统中重要的组成部分,共同被称为机械传动中的三大器。
它们涉及到了机械行业的各个领域。
广泛用于矿山、冶金、航空、兵器、水电、化工、轻纺和交通运输各部门。
离合器是一种可以通过各种操作方式,在机器运行过程中,根据工作的需要使两轴分离或结合的装置。
对于以内燃机为动力的汽车,离合器在机械传动系中是作为一个独立的总成而存在的,它是汽车传动系中直接与发动机相连的总成。
目前,各种汽车广泛采用的摩擦离合器是一种依靠主从动部分之间的摩擦来传递动力且能分离的装置。
它主要包括主动部分、从动部分、压紧机构、和操纵机构等四部分。
离合器作为一个独立的部件而存在。
它实际上是一种依靠其主、从动件之间的摩擦来传递动力且能分离的机构,见图1-1离合器工作原理图图1-1离合器工作原理图1—飞轮;2—从动盘;3—离合器踏板;4—压紧弹簧;5—变速器第一轴;6—从动盘毂汽车离合器的主要的功用:1.保证汽车平稳起步:起步前汽车处于静止状态,如果发动机与变速箱是刚性连接的,一旦挂上档,汽车将由于突然接上动力突然前冲,不但会造成机件的损伤,而且驱动力也不足以克服汽车前冲产生的巨大惯性力,使发动机转速急剧下降而熄火。
中型载重车膜片弹簧离合器设计(后备功率小)课程设计说明书

中型载重车膜片弹簧离合器设计(后备功率小)课程设计说明书汽车设计课程设计任务书学院名称:交通与汽车工程学院课程代码:__ ____ 专业:车辆工程年级: 2008一、设计题目:中型载重车膜片弹簧离合器设计(后备功率小)二、主要内容:1.离合器基本参数及尺寸确定;2.离合器主要部件设计计算;3.离合器操纵机构设计计算;4.绘制膜片弹簧零件图;5.绘制膜片弹簧离合器装配图。
三、具体要求及应提交的材料1.每一位同学按照指定的参数进行设计;2.膜片弹簧设计计算编制程序完成,并打印出膜片弹簧特性曲线图(图必须标明六个点及主要参数);3.说明书不得抄袭,必须独立完成;4.必须按时完成;5.设计说明书按规定格式书写;6.完成应提交的材料:设计说明书一份、离合器装配总图一张(1:1)、膜片弹簧零件图一张(1:1)。
四、主要技术路线提示1.根据已知数据初算摩擦片尺寸,然后根据相关约束条件进行验算;2.根据摩擦片外径初步确定膜片弹簧外径;3.初步确定膜片弹簧有关参数及用程序进行对参数调整直到满足要求为止;4.压盘传动及定中方式确定;5.操纵机构设计计算。
五、进度安排1.准备及任务布置1天;2.离合器基本参数及尺寸确定1天;3.离合器主要部件设计计算4天;4.离合器操纵机构设计计算1天;5.绘制膜片弹簧零件图1.5天;6.绘制膜片弹簧离合器装配图4天;7.编写设计说明书2天;8.机动时间0.5天。
六、推荐参考资料不少于3篇1. 王望予主编主编主编吴宗泽主编摘要 2引言 31摩擦离合器基本结构尺寸、参数的选择 41.1离合器基本性能关系式41.2摩擦片外径D与内径d的选择 41.3 离合器后备系数的确定 61.4 单位压力P的确定61.5 离合器基本参数的约束条件72离合器从动盘总成设计92.1摩擦片设计92.2从动盘毂设计92.3从动片设计122.4扭转减振器设计123 膜片弹簧设计163.1 膜片弹簧的概念163.2 膜片弹簧的弹性特性163.3 膜片弹簧主要参数的选择164 压盘和离合器盖的设计234.1 压盘设计234.2离合器盖设计245 离合器操纵机构设计265.2 操纵机构结构形式选择265.3 离合器操纵机构的设计计算26摘要本次课程设计的是中型载重车膜片弹簧离合器,根据所给汽车发动机的最大扭矩、最大转速、最大功率等基本参数等基本参数确定离合器基本参数。
膜片弹簧离合器课程设计报告书
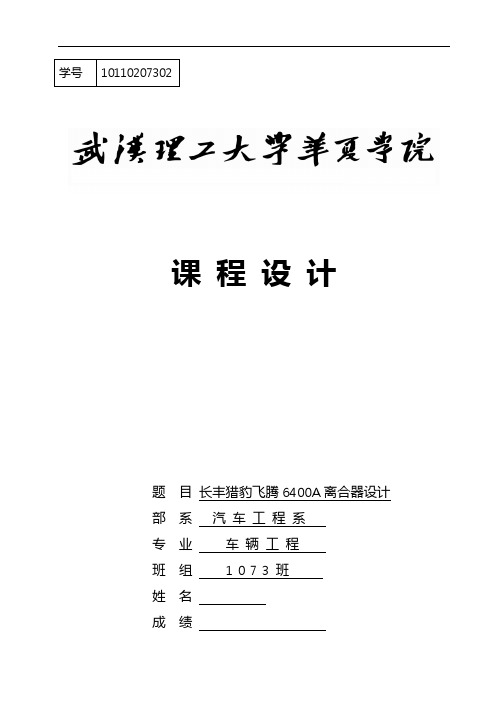
学号***********课程设计题目长丰猎豹飞腾6400A离合器设计部系汽车工程系专业车辆工程班组 1 0 7 3 班姓名成绩指导教师2010年11月25日课程设计任务书学生姓名:专业班级:车辆工程指导教师:甘泉工作单位:汽车工程系车辆教研室题目:汽车设计课程设计一、设计车型本设计针对的车型是长丰猎豹飞腾6400A ,其基本参数为:最大扭矩:168 (N·m)最高转速:4500 (r/min)二、主要任务:1.设计说明书要求:完成5千字设计说明书。
2.图纸要求完成1号手绘装配图纸一张,零件图纸三张(可用CAD绘制)。
3.图纸比例需选取合理,序号为单号的同学画主动件,双号的同学画从动件。
三、时间安排:设计时间共2周,具体时间安排如下:指导教师签名:年月日教研室主任签名:年月日目录摘要 (1)1 绪论 (2)1.1 离合器概论 (2)1.2 离合器的功用 (2)1.3 离合器的工作原理 (3)1.4 膜片弹簧离合器的概论 (4)1.5 拉式膜片弹簧离合器的优点 (5)2 离合器结构方案选取 (6)2.1 离合器车型的选定 (6)2.2 离合器设计的基本要求 (6)2.3 离合器结构设计 (7)2.3.1 摩擦片的选择 (7)2.3.2 压紧弹簧布置形式的选择 (7)2.3.3 压盘的驱动方式 (7)2.3.4 分离杠杆、分离轴承 (8)2.3.5 离合器的散热通风 (8)3 离合器基本结构参数的确定 (9)3.1 摩擦片主要参数的选择 (9)3.2 离合器后备系数β的确定 (10)3.3 单位压力P的确定 (10)4 离合器从动盘设计 (11)4.1 从动盘结构介绍 (11)4.2 从动盘设计 (12)4.2.1 从动片的选择和设计 (12)4.2.2 从动盘毂的设计 (13)4.2.3 摩擦片的材料选取及与从动片的固紧方式 (14)5 离合器压盘设计 (15)5.1 压盘的传力方式选择 (15)5.2 压盘的几何尺寸的确定 (15)5.3 压盘传动片的材料选择 (15)5.4 离合器盖的设计 (16)6 离合器分离装置设计 (17)6.1 分离杆的设计 (17)6.2 离合器分离套筒和分离轴承的设计 (17)7 离合器膜片弹簧设计 (19)7.1 膜片弹簧的结构特点 (19)7.2 膜片弹簧的变形特性和加载方式 (19)7.3 膜片弹簧的弹性变形特性 (20)7.4 膜片弹簧的参数尺寸确定 (21)7.4.1 H/h比值的选取 (22)7.4.2 R及R/r确定 (22)7.4.3 膜片弹簧起始圆锥底角α (22)7.4.4 膜片弹簧小端半径r f及分离轴承的作用半径r p (22)7.4.5 分离指数目n、切槽宽1δ、窗孔槽宽2δ、及半径r e (22)8 扭转减震器设计 (23)9 离合器壳设计 (23)结论 (24)参考文献 (25)致谢 (26)摘要离合器是汽车传动系中的重要部件,主要功用是是切断和实现发动机对传动系的动力传递,保证汽车平稳起步,保证传动系统换挡时工作平顺以及限制传动系统所承受的最大转矩,防止传动系统过载。
膜片弹簧离合器设计说明书

汽车设计课程设计说明书题目:乘用车膜片弹簧离合器设计(3)系别:机电工程系专业:车辆工程班级:本汽设091姓名:刘祥君学号:2009030643124指导教师:胡春平、谭滔日期: 2012年7月广东技术师范学院天河学院汽车设计课程设计说明书乘用车膜片弹簧离合器设计摘要汽车离合器位于发动机和变速箱之间的飞轮壳内,用螺钉将离合器总成固定在飞轮的后平面上,离合器的输出轴就是变速箱的输入轴。
在汽车行驶过程中,驾驶员可根据需要踩下或松开离合器踏板,使发动机与变速箱暂时分离和逐渐接合,以切断或传递发动机向变速器输入的动力。
其功用为:(1)使汽车平稳起步;(2)中断给传动系的动力,配合换档;(3)防止传动系过载。
膜片弹簧离合器是近年来在轿车和轻型汽车上广泛采用的一种离合器,膜片弹簧离合器本身兼压紧弹簧和分离杠杆的作用,使离合器结构大大简化并缩短了离合器的轴间尺寸;再者,膜片弹簧具有良好的非线性特性,设计合适可使摩擦片磨损到极限,压紧力仍能维持很少改变,且减轻分离离合器时的踏板力,使操纵轻便。
由于膜片弹簧与压盘的整个圆周接触,使压力分布均匀,摩擦片接触良好,磨损均匀;膜片弹簧是一种旋转对称零件,平衡性好,在高速下,其压紧力降低很小;易于实现良好的通风散热。
因此对于它的研究已经变得越来越重要,此设计说明书对乘用车膜片弹簧离合器的结构形式、参数选择与及计算过程进行了详细说明。
本文主要是对乘用车的膜片式弹簧离合器进行设计。
根据车辆使用条件和车辆参数,按照离合器系统的设计步骤和要求,进行了相关参数的选择与计算并进行了总成设计等。
关键词:离合器;膜片弹簧;从动盘;压盘;摩擦片目录1离合器概述 (1)1.1离合器的组成 (1)1.2离合器的功用 (1)1.3离合器的要求 (1)1.4离合器的工作原理 (2)1.5膜片弹簧离合器 (2)1.5.1膜片弹簧离合器的优点 (3)1.5.2拉式膜片弹簧离合器的优点 (4)2离合器结构方案选取 (6)2.1离合器的结构设计 (6)2.1.1从动盘数的选择 (6)2.1.2膜片弹簧布置形式的选择 (6)2.1.3膜片弹簧的支承形式选择 (6)2.1.4压盘的驱动方式选择 (7)2.1.5分离杠杆、分离轴承 (8)2.1.6离合器的散热通风 (8)3离合器主要参数的选择 (9)3.1后备系数β的取值 (9)P的选择 (9)3.2单位压力3.3摩擦因数f、摩擦面数z和离合器间隙t∆的选取 (10)3.4摩擦片外径D、内径d和厚度b的选择 (11)3.5离合器参数的约束条件的计算 (12)4膜片弹簧的设计 (15)4.1膜片弹簧基本参数的选择 (15)4.1.1比值hH/和h的选择 (16)R/的比值和R、r的选择 (16)4.1.2r广东技术师范学院天河学院汽车设计课程设计说明书4.1.3α的选择 (17)4.1.4分离指数目n 的选取 (17)4.1.5膜片弹簧小端内半径0r 及分离轴承作用半径f r 的确定 (17)4.1.6切槽宽度1δ、2δ及半径e γ的确定 (18)4.1.7压盘加载点半径1R 和支承环加载点半径1r 的确定 (18)4.1.8膜片弹簧工作点位置的选择 (18)5离合器从动盘设计 (21)5.1从动盘的结构组成与选择 (21)5.2从动盘总成设计 (21)5.2.1从动片的设计 (21)5.2.2从动盘毂的设计 (22)5.2.3摩擦片的设计 (22)6离合器压盘设计 (24)6.1压盘的传力方式选择 (24)6.2压盘的几何尺寸设计 (25)7离合器盖的设计 (26)8离合器分离装置设计 (27)8.1膜片弹簧与离合器盖的连接方式的确定 (27)8.2分离轴承与分离套筒设计 (27)9扭转减振器的设计 (29)9.1扭转减振器的结构类型及材料的选择 (29)9.2扭转减振器主要参数及减振弹簧的选择计算 (30)9.2.1极限转速j T 的设计计算 (30)9.2.2减振弹簧个数j Z 的设计选取 (30)9.2.3扭转角刚度ϕk 的设计计算 (30)9.2.4阻尼摩擦转矩μT 的设计计算 (31)9.2.5预紧转矩T 的设计计算 (31)9.2.6减振弹簧的位置 (31)9.2.7减振弹簧总压力F的设计计算 (31)∑ϕ的设计选取 (32)9.2.8极限转角j9.2.9减振弹簧的尺寸 (32)10总结 (33)参考文献 (34)致谢 (35)乘用车膜片弹簧离合器设计1离合器概述1.1离合器的组成对于以内燃机为动力的汽车,离合器在机械传动系中是作为一个独立的总成而存在的。
上海通用雪佛兰赛欧膜片弹簧离合器设计说明书大学论文

目录1 概述 (2)1.1组成 (2)1.2功用 (2)1.3 设计基本要求 (2)2 结构方案选择 (4)2.1从动盘数的选择 (4)2.2压紧弹簧和布置形式的选择:推式膜片弹簧离合器 (4)2.3膜片弹簧的支撑形式选择:双支承环形式 (5)2.4 压盘的驱动方式:杠杆分离传动片式 (6)3 主要参数选择 (6)3.1后备系数β初值 (6) (7)3.2 单位压力初值P3.3 离合器摩擦片外径D、内径d和厚度b (7)3.4 摩擦因数f、摩擦面数Z和离合器间隙△t (9)4 离合器基本参数的优化 (10)4.1 离合器摩擦片外径D (10)4.2 摩擦片的内、外径比c (10)4.3 后备系数β (10)4.4 摩擦片的内径d (10)4.5单位摩擦面积传递的转矩Tco (10)4.6离合器单位摩擦面积滑磨功ω (11)5 离合器盖总成设计 (12)5.1 膜片弹簧的设计 (12)5.1.1 膜片弹簧基本参数的选择 (12)5.1.2膜片弹簧基本参数约束条件的检验 (13)5.1.3 膜片弹簧材料及制造工艺 (13)5.2 压盘设计 (14)5.3 离合器盖设计 (15)5.4离合器分离装置设计 (15)6 从动盘总成设计 (17)6.1 扭转减振器设计 (17)6.1.1 扭转减振器的功用 (17)6.1.2减振器的结构设计 (17)6.2 从动盘毂的设计 (18)6.3 从动盘总成的结构型式的选择 (20)6.4 从动片结构型式的选择 (20)7 操纵机构设计 (21)7.1 操纵机构设计要求 (21)7.2离合器操纵机构选择 (21)8 总结 (22)参考文献 (23)1 概述我国的车辆工业与世界其他先进国家相比,还是比较落后的,虽然已经从国外引进了许多新的产品和新的技术,但是要全面掌握核心的技术还是有很长的差距的。
本次的设计主要是以当前比较常见的小轿车的汽车技术参数作为依据的,对其进行了膜片弹簧离合器的设计。
基于UG的汽车膜片弹簧建模与设计毕业设计说明书

毕业设计说明书学生姓名: X X X 学号: XXXXXXXX 学院: XXXXXXXX学院专业年级: 201X级 XXXXXXX班题目:基于UG的汽车膜片弹簧建模与设计指导教师: X X X 教授评阅教师:201X 年05 月摘要离合器是汽车传动系中直接与发动机相连接的总成,其主要功用是切断和实现对传动系的动力传递,以保证汽车起步时将发动机与传动系平顺地接合,确保汽车平稳起步;在换挡时将发动机与传动系分离,减少变速器中换挡齿轮之间的冲击;在工作中受到大的动载荷时;能限制传动系所承受的最大转矩,防止传动系各零件因过载而损坏;同时,由于离合器避免了发动机与变速箱的刚性连接,能有效地降低传动系中的振动和噪声。
因此,离合器在使用过程中,故障率极高,其中以因压紧力不足而出现难挂挡而导致异常磨损或烧蚀以及踏板力沉重为主。
膜片弹簧是离合器中最关键的部件,离合器的工作压力以及踏板力、压盘升程和分离行程都与膜片弹簧相关。
因此,研究膜片弹簧的力学性能对查找离合器故障原因以及提出优化方案不仅具有理论意义,也具有巨大的现实利益。
本论文的重点有三方面的内容:一、离合器的工作原理与结构;二、膜片弹簧的数学模型的建立以及理论推导;三、基于UG对于膜片弹簧的建模设计。
首先,分析了离合器的国内外发展现状,并提出本文的研究内容,目的和意义。
其次,分析离合器工作原理与结构,离合器的关键零部件在离合器工作中的作用,并提出膜片弹簧对离合器技术参数的影响。
接着对膜片弹簧进行数学建模,强度校核等,并基于UG进行建模。
最后结合前面所有的研究成果,总体宏观把握,提出了工作总结与展望。
关键词:膜片弹簧;建模与设计;UG;汽车离合器Title Modeling and design of automobile diaphragm spring based on UGAbstractClutch of automobile driving system is directly connected with the engine assembly and its main function is cut off and the transmission power of the transmission line, to ensure the car started the engine and transmission line joins smoothly and ensure a smooth start car; the shifting of the engine and the transmission line separation, reduce the impact between the shift gears of the transmission; in the work by the large dynamic load; to limit the transmission under the maximum torque to prevent transmission parts from being damaged due to overloading; at the same time, due to the clutch to avoid the rigid connection of the engine and the gearbox, effectively reduce the vibration and noise of the transmission system. Therefore, the clutch in the use of the process, the high failure rate, which in due to the lack of compression force and the difficulty of the suspension caused by abnormal wear or erosion and heavy pedal force.Diaphragm spring is the key part in the clutch, clutch working pressure and pedal force, pressure plate rise and separating stroke are and the diaphragm spring. Therefore, the study of the mechanical properties of the diaphragm spring for finding the clutch failure reasons and the proposed optimization scheme not only has the theoretical significance, but also has huge real benefits.This paper focuses on three aspects of content:, clutch working principle and structure; second, the mathematical model of the diaphragm spring is established and the theoretical derivation; third, based on the UG modeling and design of diaphragm spring.Firstly, the paper analyzes the development of the clutch at home and abroad, and puts forward the research content, purpose and significance of this paper..Secondly, it analyzes the working principle and structure of the clutch, the key partsof the clutch in the clutch work, and puts forward the influence of diaphragm springon the clutch technical parameters..Then, the mathematical modeling of diaphragm spring, strength checking, etc., and based on UG modeling.In the end, the overall macro grasp of the research results, and the summary and Prospect of the work is presented.Keywords : Diaphragm spring; Modeling and design; UG; Automobile clutch目录1 绪论.............................................................1 1.1 研究背景.......................................................1 1.2 课题的研究内容和目的...........................................2 1.3 汽车膜片弹簧的研究和发展现状...................................2 1.3.1 汽车离合器的发展.............................................2 1.3.2 国内外汽车膜片弹簧研究现状...................................6 2 膜片弹簧离合器结构分析...........................................8 2.1 膜片弹簧离合器工作要求.........................................8 2.2 膜片弹簧离合器的工作原理.......................................8 2.3 膜片弹簧离合器结构............................................10 3 膜片弹簧的设计..................................................12 3.1 车型选择......................................................12 3.2 膜片弹簧的概念及弹性特性......................................12 3.3 膜片弹簧的结构特点............................................14 3.4 膜片弹簧基本参数的选择........................................14 3.4.1 比值/H h 和h 的选择........................................14 3.4.2 /R r 比值和R 、r 的选择......................................14 3.4.3 膜片弹簧起始圆锥底角......................................15 3.4.4 分离指数目n 、切槽宽1、窗孔槽宽2、及半径e r ................15 3.4.5 膜片弹簧小段内半径0r 及分离轴承作用半径f r 的确定..............15 3.4.6 压盘加载点半径1R 和支承环加载点半径1r 的确定................15 3.5 膜片弹簧的优化设计............................................15 3.6 弹簧材料及制造工艺............................................16 4 基于UG 对膜片弹簧的建模.........................................18 4.1 UG 软件介绍...................................................18 4.2 UG 模型绘制...................................................19 结论...............................................................21 致谢...............................................................22 参考文献 (23)1 绪论1.1 研究背景汽车是重要的交通运输工具,是科学技术发展水平的标志,随着现代生活的节奏越来越快,人们对交通工具的要求也越来越高。
汽车膜片弹簧离合器设计---设计说明书

课程设计汽车膜片弹簧离合器设计姓名:学号:指导教师:专业班级:汽车膜片弹簧离合器设计---课程设计任务书汽车离合器是发动机与变速箱之间的连接装置,起连接或断开动力的作用。
离合器类型有多种,本课程设计要求设计膜片弹簧离合器,这种离合器是目前汽车上应用最多的一类离合器。
要求通过学习掌握汽车膜片弹簧离合器的原理,结构和设计知识,用所给的基本设计参数进行汽车膜片弹簧离合器设计,绘制主要的零部件图纸,写出内容详细的设计说明书。
一、基本设计参数:1.发动机型号: TJ370Q2.发动机最大扭矩: 58.8/3200 Nm/(r/min)3.传动系统传动比: 1挡:3.966主减速比:5.1254.驱动轮类型与规格:5.00-12-8PR 145/70SR125.汽车总质量: 1429KG二、设计内容及步骤1、离合器主要参数的确定(1)根据基本设计参数确定离合器主要参数:①后备系数;②单位压力;③摩擦片内外径D、d和厚度b;④摩擦因素f、摩擦面数Z等。
(2)摩擦片尺寸校核与材料选择。
2、扭转减震器的设计(1)确定扭转减震器结构(2)确定扭转减震器主要参数(3)确定减震弹簧尺寸3、从动盘总成设计(1)从动片设计(2)从动盘毂设计(3)确定从动盘摩擦材料4、离合器盖总成的设计(1)选择压盘内外径、厚度及材料,并进行校核(2)离合器盖设计(3)支撑环设计5、膜片弹簧的设计(1)膜片弹簧基本参数选择(2)膜片弹簧强度计算三、设计成果要求1、设计计算说明书(1)设计计算说明书要包括:封面、课程设计任务书、目录、中英文摘要、正文、参考文献等。
(2)正文主要体现:进行各零部件的参数选择与计算时的理论依据、计算步骤及对计算结果合理性的阐述。
(3)课程设计说明书统一用A4纸打印或撰写,要求排版整洁合理,字迹工整,图文并貌。
2、设计图纸(1)零件图纸包括: 磨擦片、从动片、从动盘毂、压盘、膜片弹簧图(2)离合器总成结构装配图尺寸标注、公差标注、技术要求、明细栏等完整。
基于捷达轿车膜片弹簧式离合器的设计_课程设计说明书
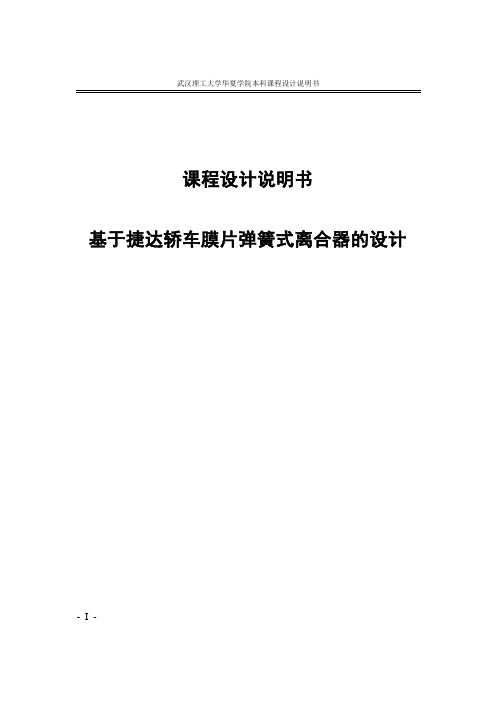
武汉理工大学华夏学院本科课程设计说明书- I - 课程设计说明书基于捷达轿车膜片弹簧式离合器的设计武汉理工大学华夏学院本科课程设计说明书- II - 摘要离合器装在发动机与变速器之间,汽车从启动到行驶的整个过程中,经常需要使用离合器。
它的作用是使发动机与变速器之间能逐渐接合,从而保证汽车平稳起步;暂时切断发动机与变速器之间的联系,以便于换档和减少换档时的冲击;当汽车紧急制动时能起分离作用,防止变速器等传动系统过载,起到一定的保护作用。
离合器类似开关,接合或断离动力传递作用,因此,任何形式的汽车都有离合装置,只是形式不同而已。
在现代汽车设计中,膜片弹簧式离合器应用越来越广泛。
本设计基于05款捷达GDF的设计要求和设计参数,确定了以拉式膜片弹簧离合器作为设计目标。
根据拉式膜片弹簧离合器工作原理和使用要求,采用系统化设计方法,把离合器分为主动部分、从动部分、操纵机构。
通过对各个部分设计方案的原理阐释和优缺点的比较,确定了相关部分的基本结构及其零部件的制造材料。
根据车辆使用条件和车辆参数,按照离合器系统的设计步骤和要求,主要进行了以下工作:选择相关设计参数主要为:摩擦片外径D的确定,离合器后备系数β的确定,单位压力P的确定。
并进行了总成设计主要为:分离装置的设计,以及从动盘设计(从动盘毂的设计)和膜片弹簧设计等。
关键词离合器设计膜片弹簧从动盘摩擦片武汉理工大学华夏学院本科课程设计说明书- III - 目录摘要 (I)第1章绪论 (5)1.1 课题背景 (5)1.2 离合器的发展 (5)1.3 离合器的概述 (7)1.4 离合器的功用 (7)1.5 离合器的工作原理 (8)1.6 膜片弹簧离合器的结构及其优点 (9)第2章离合器结构方案选取 (11)2.1 离合器车型的选定 (11)2.2 离合器设计的基本要求 (11)2.3 离合器结构设计 (12)2.3.1 摩擦片的选择 (12)2.3.2 压紧弹簧布置形式的选择 (12)2.3.3 压盘的驱动方式 (13)2.3.4 分离轴承的类型 (13)2.3.5 离合器的散热通风措施 (14)2.4 本章小结 (14)第3章离合器基本参数的确定 (14)3.1 摩擦片主要参数的选择 (14)3.2离合器后备系数β的确定 (16)3.3单位压力P和摩擦因数f的确定 (16)3.4 摩擦片基本参数的优化 (17)3.5 本章小结 (20)第4章离合器从动盘设计 (20)4.1从动盘结构介绍 (20)4.2从动盘设计 (21)4.2.1 从动片的选择和设计 (22)4.2.2从动盘毂的设计 (22)4.2.3摩擦片的材料选取及与从动片的固紧方式 (23)武汉理工大学华夏学院本科课程设计说明书- IV -4.3 本章小结 (24)第5章 离合器压盘设计 (25)5.1 压盘的传动方式的选择 (25)5.2 压盘的几何尺寸的确定、 (25)5.3 压盘传动片的材料选择 (26)5.4 离合器盖的设计 (26)5.5 本章小结 (26)第6章 离合器分离装置设计 (27)6.1 分离杆的设计 (27)6.2 离合器分离套筒和分离轴承的设计 (27)6.3 本章小结 (28)第7章 离合器膜片弹簧设计 (29)7.1 膜片弹簧的结构特点 (29)7.2 膜片弹簧的变形特性和加载方式 (29)7.3 膜片弹簧的弹性变形特性 (30)7.4 膜片弹簧的参数尺寸确定 (31)7.4.1 H/h 比值的选取 (32)7.4.2 R 及R/r 确定 (32)7.4.3 膜片弹簧起始圆锥底角α (32)7.4.4 分离指数目n 、切槽宽1δ、窗孔槽宽2δ、及半径r e (32)7.5 膜片弹簧的优化设计 (33)7.6 膜片弹簧强度计算 (34)7.6.1 F-λ图 (34)7.6.2 应力计算 (35)7.7 本章小结 (38)第8章 扭转减振器的概述 (38)8.1 扭转减振器的组成 (38)8.2 扭转减振器的功用 (39)8.3 本章小结 (39)第9章 离合器壳设计 (39)结束语 (40)参考文献 (41)武汉理工大学华夏学院本科课程设计说明书- V - 第1章绪论1.1课题背景对于内燃机为动力的汽车,离合器在机械传动系中是作为一个独立的总成而存在的,按动力传递顺序来说,离合器应是传动系中的第一个总成。
膜片弹簧离合器设计说明书
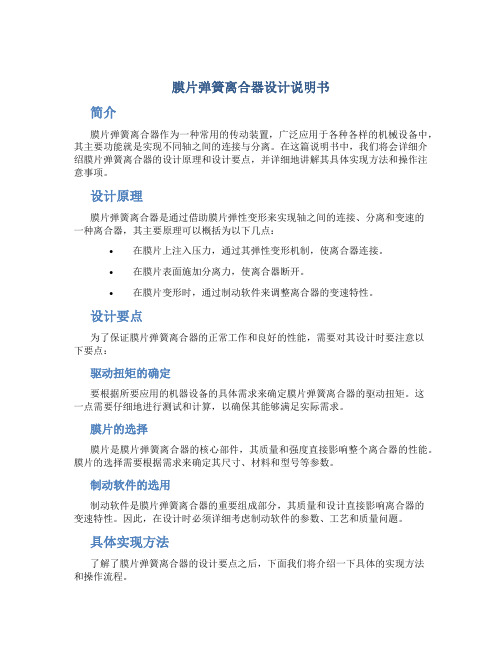
膜片弹簧离合器设计说明书简介膜片弹簧离合器作为一种常用的传动装置,广泛应用于各种各样的机械设备中,其主要功能就是实现不同轴之间的连接与分离。
在这篇说明书中,我们将会详细介绍膜片弹簧离合器的设计原理和设计要点,并详细地讲解其具体实现方法和操作注意事项。
设计原理膜片弹簧离合器是通过借助膜片弹性变形来实现轴之间的连接、分离和变速的一种离合器,其主要原理可以概括为以下几点:•在膜片上注入压力,通过其弹性变形机制,使离合器连接。
•在膜片表面施加分离力,使离合器断开。
•在膜片变形时,通过制动软件来调整离合器的变速特性。
设计要点为了保证膜片弹簧离合器的正常工作和良好的性能,需要对其设计时要注意以下要点:驱动扭矩的确定要根据所要应用的机器设备的具体需求来确定膜片弹簧离合器的驱动扭矩。
这一点需要仔细地进行测试和计算,以确保其能够满足实际需求。
膜片的选择膜片是膜片弹簧离合器的核心部件,其质量和强度直接影响整个离合器的性能。
膜片的选择需要根据需求来确定其尺寸、材料和型号等参数。
制动软件的选用制动软件是膜片弹簧离合器的重要组成部分,其质量和设计直接影响离合器的变速特性。
因此,在设计时必须详细考虑制动软件的参数、工艺和质量问题。
具体实现方法了解了膜片弹簧离合器的设计要点之后,下面我们将介绍一下具体的实现方法和操作流程。
装配前的准备工作在进行装配工作之前,我们需要对膜片弹簧离合器的各个部件进行检查和清洁,以确保其质量和工作安全。
同时,也需要对装配环境进行清洁和消毒,以保证零部件不受到污染。
确定膜片的安装位置膜片的安装位置必须要确定,一般是在离合器盘板的中心位置。
在安装之前,需要将膜片按照设计要求进行预弯曲处理。
检查膜片的合适性在安装膜片之前,需要检查膜片的质量和合适性。
在检查时,需要检查其外观、尺寸、弹性检测等行为。
安装制动软件安装制动软件是整个装配过程中非常关键的一个环节,需要认真按照设计要求进行操作。
在安装制动软件时,需要掌握正确的操作方法,以确保制动软件安装的稳定性和可靠性。
推式膜片弹簧
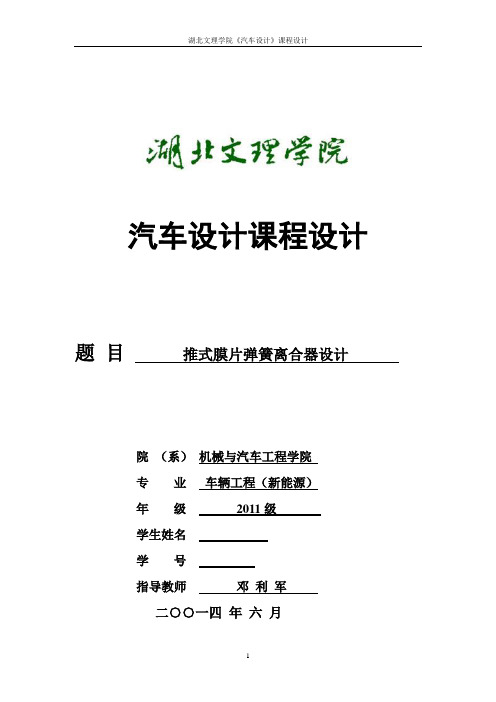
汽车设计课程设计题目推式膜片弹簧离合器设计院(系)机械与汽车工程学院专业车辆工程(新能源)年级2011级学生姓名学号指导教师邓利军二○○一四年六月前言离合器是汽车传动系中直接与发动机相连接的总成,其主要功用是切断和实现对传动系的动力传递,以保证汽车起步时将发动机与传动系平顺地接合,确保汽车平稳起步;在换挡时将发动机与传动系分离,减少变速器中换挡齿轮之间的冲击;在工作中受到大的动载荷时,能限制传动系所承受的最大转矩,防止传动系各零件因过载而损坏;有效地降低传动系中的振动和噪声。
摩擦离合器主要由主动部分(发动机飞轮、离合器盖和压盘等)、从动部分(从动盘)、压紧机构(压紧弹簧)和操纵机构(分离叉、分离轴承、离合器踏板及传动部件等)四部分组成。
主、从动部分和压紧机构是保证离合器处于接合状态并能传递动力的基本结构,操纵机构是使离合器主、从动部分分离的装置。
本课题来源于生产实际,为保证离合器具有良好的工作性能,依据经济、可靠、操作方便的原则,对汽车离合器设计提出如下基本要求:a.在任何行驶条件下,能可靠地传递发动机的最大转矩。
b.接合时要平顺柔和,以保证汽车起步时没有抖动和冲击。
c.分离时要迅速、彻底。
d.从动部分转动惯量小,减轻换挡时变速器齿轮间的冲击。
e.有良好的吸热能力和通风散热效果,保证离合器的使用寿命。
f.操纵轻便、准确,以减轻驾驶员的疲劳。
g.作用在从动盘上的压力和摩擦材料的摩擦因数在使用过程中变化要尽可能小,以保证有稳定的工作性能。
h.应有足够的强度和良好的动平衡,以保证其工作可靠、寿命长。
目录第1章概述 (5)第2章离合器的结构和基本参数的确定 (6)2.1离合器结构型式的确定 (6)2.2离合器基本参数的确定 (6)第3章离合器的设计 (9)3.1从动盘总成 (9)3.1.1 从动盘毂 (9)3.1.2 从动片设计 (10)3.1.3 从动盘摩擦片 (10)3.1.4 波形片和减振弹簧 (10)3.2膜片弹簧设计 (11)3.2.1膜片弹簧设计计算的基本公式 (11)3.2.2膜片弹簧基本参数的确定 (11)3.2.3 强度校核 (15)3.3离合器盖及压盘总成的设计 (15)3.3.1离合器盖设计 (15)3.4压盘结构设计 (16)3.4.1压盘结构设计 (16)3.4.2压盘几何尺寸的确定 (16)3.4.3传力方式的选择 (17)3.5分离轴承总成 (17)3.6操纵机构设计 (17)参考文献 (18)推式膜片弹簧离合器设计任务书推式膜片弹簧离合器设计一、任务:1、确定推式膜片弹簧离合器的总体方案。
膜片弹簧说明书
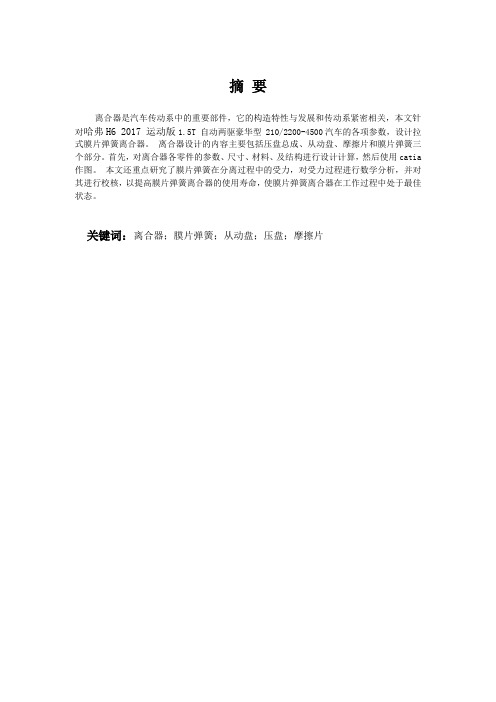
摘要离合器是汽车传动系中的重要部件,它的构造特性与发展和传动系紧密相关,本文针对哈弗H6 2017 运动版1.5T 自动两驱豪华型 210/2200-4500汽车的各项参数,设计拉式膜片弹簧离合器。
离合器设计的内容主要包括压盘总成、从动盘、摩擦片和膜片弹簧三个部分。
首先,对离合器各零件的参数、尺寸、材料、及结构进行设计计算,然后使用catia 作图。
本文还重点研究了膜片弹簧在分离过程中的受力,对受力过程进行数学分析,并对其进行校核,以提高膜片弹簧离合器的使用寿命,使膜片弹簧离合器在工作过程中处于最佳状态。
关键词:离合器;膜片弹簧;从动盘;压盘;摩擦片第一章离合器介绍1.1离合器的概述按动力传递顺序来说,离合器应是传动系中的第一个总成。
顾名思义,离合器是“离”与“合”矛盾的统一体。
离合器的工作,就是受驾驶员操纵,或者分离,或者接合,以完成其本身的任务。
离合器是设置在发动机与变速器之间的动力传递机构,其功用是能够在必要时中断动力的传递,保证汽车平稳地起步;保证传动系换档时工作平稳;限制传动系所能承受的最大扭矩,防止传动系过载。
为使离合器起到以上几个作用,目前汽车上广泛采用弹簧压紧的摩擦式离合器,摩擦离合器所能传递的最大扭矩取决于摩擦面间的工作压紧力和摩擦片的尺寸以及摩擦面的表面状况等。
即主要取决于离合器基本参数和主要尺寸。
膜片弹簧离合器在技术上比较先进,经济性合理,同时其性能良好,使用可靠性高寿命长,结构简单、紧凑,操作轻便,在保证可靠地传递发动机最大扭矩的前提下,有以下优点:(1)结合时平顺、柔和,使汽车起步时不震动、冲击;(2)离合器分离彻底;(3)从动部分惯量小,以减轻换档时齿轮副的冲击;(4)散热性能好;(5)高速回转时只有可靠强度;(6)避免汽车传动系共振,具有吸收震动、冲击和减小噪声能力;(7)操纵轻便;T和后备系数 保持稳定);(8)工作性能(最大摩擦力矩emax(9)使用寿命长。
图1-11.2离合器的功用离合器可使发动机与传动系逐渐接合,保证汽车平稳起步。
乘用车膜片弹簧课程设计

乘用车膜片弹簧课程设计一、课程目标知识目标:1. 让学生掌握乘用车膜片弹簧的基本结构、工作原理及功能;2. 了解乘用车膜片弹簧在汽车悬挂系统中的作用,及其对汽车行驶稳定性的影响;3. 掌握相关术语和概念,如弹性特性、刚度、预紧力等。
技能目标:1. 培养学生运用所学知识分析乘用车膜片弹簧性能的能力;2. 能够利用工具和技术资料,对乘用车膜片弹簧进行简单的故障诊断和性能评估;3. 提高学生团队协作和动手实践的能力,通过实验和案例研究,加深对膜片弹簧的理解。
情感态度价值观目标:1. 培养学生对汽车工程技术的兴趣和热情,激发学生探索汽车悬挂系统奥秘的欲望;2. 强化学生的安全意识,让学生认识到乘用车膜片弹簧在汽车行驶安全中的重要性;3. 培养学生严谨的科学态度,通过实践操作和数据分析,提高学生解决问题的能力。
课程性质:本课程为汽车维修与检测专业课程,侧重于理论与实践相结合,注重培养学生的动手能力和实际问题解决能力。
学生特点:学生为中职二年级,已具备一定的汽车基础知识,对汽车维修与检测有一定了解,但实践经验不足。
教学要求:结合学生特点和课程性质,采用案例教学、实验操作、小组讨论等教学方法,注重理论与实践相结合,提高学生的综合素养。
通过本课程的学习,使学生能够更好地适应汽车维修行业的发展需求。
二、教学内容1. 乘用车膜片弹簧的结构与原理- 膜片弹簧的组成、材料及制造工艺;- 弹簧的弹性特性、刚度计算;- 膜片弹簧在汽车悬挂系统中的作用及其工作原理。
2. 乘用车膜片弹簧的性能与检测- 弹簧预紧力、自由长度的测量方法;- 膜片弹簧的故障类型及原因分析;- 常用检测工具及设备的使用。
3. 乘用车膜片弹簧的故障诊断与排除- 故障诊断流程及方法;- 典型故障案例分析;- 故障排除技巧及注意事项。
4. 乘用车膜片弹簧的维护与保养- 膜片弹簧的日常检查与维护;- 更换周期及注意事项;- 提高弹簧使用寿命的方法。
教学内容按照以上四个方面进行组织,结合教材相关章节,确保教学内容的科学性和系统性。
- 1、下载文档前请自行甄别文档内容的完整性,平台不提供额外的编辑、内容补充、找答案等附加服务。
- 2、"仅部分预览"的文档,不可在线预览部分如存在完整性等问题,可反馈申请退款(可完整预览的文档不适用该条件!)。
- 3、如文档侵犯您的权益,请联系客服反馈,我们会尽快为您处理(人工客服工作时间:9:00-18:30)。
此设计为矿用自卸车离合器上的膜片弹簧。
在下面的第一部分中,分别对该车的最大起步坡度和最大爬坡度进行计算和比较。
后面的部分是对该车膜片弹簧的设计及校核。
1、滑磨功与温升校核
1.1用矿用自卸车的行驶阻力系数表示滑磨功L(N·m)
L=
式中,:发动机最大转矩时转速,取1400;
:汽车总质量换算后得到的相对转动惯量,==3.687kg·;
:发动机旋转部件及离合器主动部分的转动惯量,取2.983kg·;
:汽车阻力矩,=·,N·m;
:发动机最大转矩,取1400N·m;
:离合器最大静摩擦力矩,取2100N·m;
:离合器后备系数,=;
:汽车总质量,取65t;
:传动系效率,取0.8;
:车轮滚动半径,取0.536m;
:主传动比,取5.73;
:变速器一档速比,取12.42;
g:重力加速度,取9.8;
f:滚动阻力系数,取0.01;
:汽车行驶阻力系数,取=·f+;
得:L=
1.2压盘温升T及矿用自卸车最大起步坡度
T=
式中,T:压盘温升,20;
:传到压盘的热量所占的比例,单盘离合器=0.5;
L:滑磨功,L=N·m;
m:单盘离合器压盘质量,取30kg;
c:压盘的比热容,铸铁取481.4;
因为在一次离合器接合过程中产生的温升不允许超过20,所以估计一辆矿用自卸车的最大起步坡度=。
1.3矿用自卸车最大爬坡度
=
式中,:汽车的驱动力,N;
:作用于驱动轮上的转矩,==79.707N·m;
:车轮半径,0.536m;
:发动机最大转矩,取1400N·m;
:变速器一档速比,取12.42;
:主传动比,取5.73;
:传动系效率,取0.8;
在计算矿用自卸车最大爬坡度时,只考虑滚动阻力和坡度阻力所引起的阻力,则有下式:
=
式中,:矿用自卸车的行驶阻力N;
:汽车总质量,取65t;
g:重力加速度,取9.8;
f:滚动阻力系数,取0.01;
令与相等,可以计算出矿用自卸车的最大爬坡度=。
2、膜片弹簧基本参数的选择
选取60Si2MnA高精度钢板材料为膜片弹簧材料。
2.1比值的选择
为了保证离合器压紧力变化不大和操纵轻便,汽
车离合器用膜片弹簧的一般为1.5~2.0,板厚h
为2~4mm。
故初选h=4mm,=2.0,则H=2.0h=8.0mm。
图1
2.2 R、r的选择
对于气和离合器膜片弹簧,设计上并不要求储存大量的弹性能,而是根据结构布置
与分离的需要来确定,一般的取值为1.2~1.3。
对于R,膜片弹簧大端外径R应满足结构上的要求而和摩擦片上的外径尺寸相适应,大于摩擦片内径,近于摩擦片外径。
根据该设计数据及《汽车离合器》(徐石安,江发潮编著)中表3.2.1可以确定离合器摩擦片内、外径分别为220mm和405mm。
所以取R=200mm,再结合实际情况取=1.3,则r=160mm。
2.3锥角的选择
==≈,满足膜片弹簧处于自由状态时的圆锥底角一般在左右的要求。
2.4分离指数目n及形状的选择
汽车离合器膜片弹簧的分离指数n﹥12,一般取18,采用偶数,便于制造时模具的分离。
分离指与碟簧部分交界处的径向槽较宽,呈长方圆形孔。
这样做的目的一方面可以减少分离指根部的应力集中,另一方面又可用来安置销钉固定膜片弹簧。
2.5膜片弹簧小端内半径及分离轴承作用半径的确定
值主要由结构决定,其最小值应大于变速器第一轴花键的外径以便安装。
分离轴承作用半径大于。
根据《汽车设计》(吉林工业大学.王望予编著)第二章离合器设计可知,弹簧各部分有关尺寸比值应符合一定的范围,即
1.20≤R/r≤1.35
70≤2R/h≤100
3.5≤≤5.O
由离合器的结构决定,其最小值应大于变速器第一轴花键的外径
=k·=4×mm=44.75mm,则取=50mm
根据弹簧结构布置的要求,与R、与r、与之差应在一定范围内,即
1≤R-≤7,0≤-r≤6,0≤-≤4
取分离轴承=54mm。
2.6切槽宽度δ1、δ2及半径
切槽宽=4mm(取值约为4mm),≈(2.5~
4.5)=3×4=12mm,满足r-≥,则≤r-
=160-12=148mm,
故取=148mm。
2.7压盘加载点半径和支承环加载点半径的确定图2
根据《汽车设计》(王望予编著,机械工业出版社出版)知,和需满足下列条件:1≤R-≤7,0≤-r≤6
故选择=195mm,=165mm。
2.8膜片弹簧工作点位置的选择
自由状态压紧状态分离状态
图3 膜片弹簧不同工作状态下的变形
图4
B点:通常为=(0.8~1.0),即处在工作位置时,其大端变形量为:=(0.7~0.85)H
A点:主要确保摩擦片磨损后达到极限位置时,仍然能提供足够的压紧力,可按下式估算:=Z×
式中:Z为摩擦面数,单片离合器Z=2,双片离合器Z=4;
为摩擦片允许的极限磨损量,一般取0.65~1.1mm。
为彻底分离时摩擦副间的间隙,一般取0.75~1.0mm。
3、膜片弹簧的弹性特性
工作压力和膜片弹簧在压盘接触点处的轴向变形关系式
=·{(H-)[H-()]+}
式中,E:弹性模数,钢材取E=2.1×M;
:泊松比,钢材取=0.3;
:弹簧片厚,=4mm;
H:碟簧部分内截锥高,H=8mm;
:大端变形,=0.8×8mm=6.4mm;
R:碟簧部分外半径(大端半径),R=200mm;
r:碟簧部分内半径,r=160mm;
L:膜片弹簧与压盘接触半径,L=195mm;
l:支承环平均半径,l=165mm。
=10227.100N
4、强度校核
离合器接合时膜片弹簧的大端变形量为=0.8H=0.8×8.0mm=6.4mm
离合器彻底分离时,膜片弹簧大端的变形量为=+(即为)压盘行程
为=2×0.8mm=1.6mm,故=6.4mm+1.6mm=8.0mm。
4.1计算
=1-=0.777
4.2求离合器彻底分离时分离轴承作用的载荷
={(H-)[H-]+}=2116.068N
4.3强度校核
=··+[(-1)×(-·)×
+·]=1310.059M﹤1700~1900 M,符合要求。
5、膜片弹簧的制造工艺及热处理
本次设计中膜片弹簧采用60Si2MnA高精度钢板材料。
为了提高膜片弹簧的承载能力,要对膜片弹簧进行强压处理。
另外,对膜片弹簧的凹面或双面进行喷丸处理以起到冷作硬化的作用,同样也可以提高承载能力的疲劳强度。
为了提高分离指的耐磨性,可对其端部进行高频淬火、喷镀铬合金和镀镉或四氟乙烯。
在膜片弹簧与压盘接触圆形处,为了防止由于拉应力的作用而产生裂纹,可对该处进行挤压处理,以消除应力源。
膜片弹簧表面不得有毛刺、裂纹、划痕、锈蚀等缺陷。
碟簧部分的硬度一般为45~50HRC,分离指端硬度为55~62HRC,在同一片分离指上同一范围内的硬度差不大于3个单位。
膜片弹簧的内、外半径公差一般为H11和h11,厚度公差为±0.025mm,初始底锥角公差为±10分。
膜片弹簧上下表面的表面粗糙度为1.6μm,底面的平面一般要求小于0.1mm。
膜片弹簧处于接合状态时,其分离指端的相互高度差一般要求小于0.8~1.0mm。
6、课程设计心得
(1)在做任何事情时,都应该有个认真的态度;
(2)做设计时要多查资料,再小的地方也要有事实依据;
(3)画图时仔细查阅相关资料,尽量将部件清楚的表达出来;
(4)了解了膜片弹簧设计的基本步骤和计算方法。
参考资料
(1)计算机绘图实验指导书
(2)程军李虹.画法几何级机械制图.北京:国防工业出版社,2005.8 (3)徐石安江发潮.汽车离合器.北京:清华大学出版社,2005.8 (4)王宵峰.汽车底盘设计.北京:清华大学出版社,2010.4
(5)王予望.汽车设计.吉林:吉林工业大学出版社。