钣金件表面处理
钣金件表面处理工艺

钣金件表面处理工艺
钣金件表面处理工艺主要有以下几种:
1. 涂装:采用涂料对钣金件进行表面处理,可防止氧化、腐蚀和磨损,同时还能美化表面。
2. 镀层处理:在钣金件表面电解镀上一层金属或合金,如镀铬、镀锌、镀镍等,可增加钣金件的耐腐蚀性和硬度。
3. 喷砂:使用高压压缩空气将砂粒喷射到钣金件表面,去除表面粗糙度和氧化层。
4. 电化学抛光:通过电化学原理,将钣金件表面金属离子还原成金属,并清除氧化物和杂质。
5. 氧化:将钣金件表面暴露在氧化气氛中,使其表面产生一层氧化膜,可增强钣金件的耐腐蚀性和硬度。
6. 喷涂:采用高压喷涂技术将漆料喷涂到钣金件表面,可美化表面并增加其耐久性。
7. 磨光:使用研磨工具对钣金件表面进行打磨和抛光,可去除表面毛刺和粗糙
度,使其表面光滑亮丽。
钣金件表面处理主要工艺方法介绍

表面处理工艺表面处理技术介绍一、什么叫做表面处理表面处理:以最经济和最有效的方法改变产品表面及近表面区的形态、化学成分和组织结构,有效地改善和提高产品的装饰性能、耐腐蚀性能和耐磨性能,延长产品的使用寿命。
常见的表面处理:电镀,化学镀,转化膜技术,物理气相沉积,化学气相沉积,热喷涂,热浸镀,喷砂,化学转化,阳极氧化,涂装等;表面处理技术还能赋予材料表面各种光、电、磁、热、声、化学以及功能转换等特性。
1.各种光的表面技术:镜子;防反光;2.各种电的表面技术:绝缘的镀银,金,铜;导电的用塑料保护3.各种磁的表面技术:隐身技术(重点)4.热的表面技术:红外,吸收红外,防热;5.声的表面技术:防声纳6.化学:钢材镀锌表面处理的种类表面处理根据产品的使用要求可以分为:防护型表面处理,如电镀、氧化(化学氧化、电化学氧化)、装饰型表面处理(如涂装、、功能型表面处理,总的来说,没有明显的划分界限,其主要目的是延长产品的使用寿命,最大程度的节省和利用资源。
二、钣金加工中为什么要进行表面处理?1.钣金加工所用的材料多为冷轧板、热轧板、电解板、白口铁、不锈钢、铝合金板及型材、铜材等,这些材料暴露在大气中,与空气中的水分和氧充分接触后,会发生电化学反应,从而造成材料表面腐蚀,同时物理及化学性质不同的材料间相互接触也会由于彼此间的电位差而形成原电池,从而造成接触腐蚀。
为避免钣金加工中材料在各加工工序间及成品在存放及使用中发生腐蚀,生产中通过对材料进行表面处理方式来控制腐蚀的产生或延缓腐蚀的产生,从而减少由于腐蚀的产生而造成产品返修或报废,尽可能地节约资源及生产成本。
2.各种材料经过钣金加工转化为商品时,为了满足顾客的需求及商品给予人视觉上的美感,就对产品外观作各种表面处理,如电镀、氧化着三、在钣金加工业中铝合金材料通常需进行哪些表面处理?在钣金加工业中,铝合金材料通常需进行以下表面处理:无色化学氧化、黑色化学氧化、金黄色化学氧化、拉丝无色化学氧化、喷砂无色化学氧化、光亮无色化学氧化、喷砂光亮阳极氧化、化学氧化着色、化学氧化后涂装(喷漆、喷粉),其中氧化层有导电与绝缘两种;硬质、耐磨等;前处理四、磷化工艺A、磷化工艺流程:预脱脂----脱脂----流动水洗----流动水洗----表调----磷化----流动水洗----流动水洗----纯水洗----烘干B、前处理生产线喷淋线、浸泡线装生产前为何要进行磷化处理?1、磷化是通过化学的方法使铁基材或锌基材与磷酸盐发生反应而生成一层致密的化学转化膜的过程。
钣金件制作中的选材以及表面处理加工工艺探讨

钣金件制作中的选材以及表面处理加工工艺探讨【摘要】钣金件制作是制造业中常见的加工方式,选材和表面处理是该过程中至关重要的环节。
选材的考虑因素包括强度、硬度、耐腐蚀性等,常见的材料有铁、铝、不锈钢等。
表面处理工艺可以提高产品的美观度和耐用性,常见方法包括喷涂、电镀、镀锌等。
选材与表面处理密切相关,合理的选材能够提升表面处理效果,而优质的表面处理也能够保护选材材料。
在钣金件制作中,选材和表面处理的重要性不可忽视,它们直接影响产品的质量和使用寿命。
未来,随着技术的发展和市场需求的变化,钣金件选材和表面处理也将不断创新,以满足不同领域的需求。
选材和表面处理在钣金件制作中扮演着重要的角色,值得重视和研究。
【关键词】钣金件制作、选材、表面处理、工艺、考虑因素、常见选材、表面处理方法、关系、重要性、发展趋势、总结。
1. 引言1.1 钣金件制作简介钣金件是一种常见的零部件,在许多机械设备和汽车中都有广泛的应用。
它们通常用于外壳、固定支架、连接件等部件的制作。
钣金件的制作工艺主要包括材料的选取、模具设计、冲压成型、焊接和表面处理等环节。
钣金件制作的首要任务是根据设计要求选择合适的材料。
材料的选取直接影响到钣金件的性能和质量。
一般来说,钣金件材料应具有良好的成形性、强度和耐腐蚀性。
常用的钣金件制作材料包括冷轧钢板、不锈钢、铝合金等。
在钣金件制作过程中,表面处理是必不可少的环节。
表面处理可以提高钣金件的耐腐蚀性、装饰性和机械性能,延长其使用寿命。
常见的表面处理方法包括喷涂、电镀、镀锌、喷砂等。
钣金件的选材和表面处理工艺是制作过程中至关重要的环节。
只有选材合理、表面处理到位,才能确保钣金件的质量和性能达到设计要求。
在未来的发展中,钣金件制作技术将不断创新,追求更高的精度和品质。
1.2 选材的重要性选材在钣金件制作中扮演着至关重要的角色。
选用合适的材料可以直接影响到钣金件的质量、性能和耐用性。
选材要考虑到钣金件的使用环境和要求,不同的材料有不同的物理和化学性质,选择合适的材料可以确保钣金件在各种条件下都能正常工作。
钣金件表面处理主要工艺方法介绍

表面处理工艺表面处理技术介绍一、什么叫做表面处理表面处理:以最经济和最有效的方法改变产品表面及近表面区的形态、化学成分和组织结构,有效地改善和提高产品的装饰性能、耐腐蚀性能和耐磨性能,延长产品的使用寿命。
常见的表面处理:电镀,化学镀,转化膜技术,物理气相沉积,化学气相沉积,热喷涂,热浸镀,喷砂,化学转化,阳极氧化,涂装等;表面处理技术还能赋予材料表面各种光、电、磁、热、声、化学以及功能转换等特性。
1.各种光的表面技术:镜子;防反光;2.各种电的表面技术:绝缘的镀银,金,铜;导电的用塑料保护3.各种磁的表面技术:隐身技术(重点)4.热的表面技术:红外,吸收红外,防热;5.声的表面技术:防声纳6.化学:钢材镀锌表面处理的种类表面处理根据产品的使用要求可以分为:防护型表面处理,如电镀、氧化(化学氧化、电化学氧化)、装饰型表面处理(如涂装、、功能型表面处理,总的来说,没有明显的划分界限,其主要目的是延长产品的使用寿命,最大程度的节省和利用资源。
二、钣金加工中为什么要进行表面处理?1.钣金加工所用的材料多为冷轧板、热轧板、电解板、白口铁、不锈钢、铝合金板及型材、铜材等,这些材料暴露在大气中,与空气中的水分和氧充分接触后,会发生电化学反应,从而造成材料表面腐蚀,同时物理及化学性质不同的材料间相互接触也会由于彼此间的电位差而形成原电池,从而造成接触腐蚀。
为避免钣金加工中材料在各加工工序间及成品在存放及使用中发生腐蚀,生产中通过对材料进行表面处理方式来控制腐蚀的产生或延缓腐蚀的产生,从而减少由于腐蚀的产生而造成产品返修或报废,尽可能地节约资源及生产成本。
2.各种材料经过钣金加工转化为商品时,为了满足顾客的需求及商品给予人视觉上的美感,就对产品外观作各种表面处理,如电镀、氧化着三、在钣金加工业中铝合金材料通常需进行哪些表面处理?在钣金加工业中,铝合金材料通常需进行以下表面处理:无色化学氧化、黑色化学氧化、金黄色化学氧化、拉丝无色化学氧化、喷砂无色化学氧化、光亮无色化学氧化、喷砂光亮阳极氧化、化学氧化着色、化学氧化后涂装(喷漆、喷粉),其中氧化层有导电与绝缘两种;硬质、耐磨等;前处理四、磷化工艺A、磷化工艺流程:预脱脂----脱脂----流动水洗----流动水洗----表调----磷化----流动水洗----流动水洗----纯水洗----烘干B、前处理生产线喷淋线、浸泡线装生产前为何要进行磷化处理?1、磷化是通过化学的方法使铁基材或锌基材与磷酸盐发生反应而生成一层致密的化学转化膜的过程。
钣金表面处理通用检验标准

检验标准名称:表面处理通用检验标准图号:DMBM0.402. 003拟制:***审核:***标准化:***IQC会签:***批准:***目次○、总则................................................................................................................................. 1一、电镀镍检验标准............................................................................................................. 11.1 试样要求.................................................................................................................. 11.2 外观.......................................................................................................................... 11.3 镀层厚度.................................................................................................................. 21.4 结合强度.................................................................................................................. 21.5 耐蚀性...................................................................................................................... 2二、电镀锌检验标准............................................................................................................. 32.1 试样要求.................................................................................................................. 32.2 外观.......................................................................................................................... 32.3 镀层厚度.................................................................................................................. 42.4 结合强度.................................................................................................................. 42.5 耐蚀性...................................................................................................................... 42.6 白色钝化膜的存在性试验...................................................................................... 4三、装饰镀铬检验标准......................................................................................................... 53.1试样要求................................................................................................................... 53.2 外观.......................................................................................................................... 53.3 镀层厚度.................................................................................................................. 53.4 结合强度.................................................................................................................. 63.5 耐蚀性...................................................................................................................... 6四、喷漆检验标准................................................................................................................. 74.1 试片要求.................................................................................................................. 74.2 颜色.......................................................................................................................... 74.3 光泽.......................................................................................................................... 74.4 外观.......................................................................................................................... 74.5 漆层厚度.................................................................................................................. 84.6 附着力...................................................................................................................... 84.7 抗冲击性.................................................................................................................. 84.8 耐溶剂(无水乙醇)性.......................................................................................... 8五、粉末喷涂检验标准......................................................................................................... 95.1 试片要求.................................................................................................................. 95.2 颜色.......................................................................................................................... 95.3 光泽.......................................................................................................................... 95.4 外观.......................................................................................................................... 95.5 涂层厚度.................................................................................................................. 95.6 附着力.................................................................................................................. 105.7 抗冲击性.............................................................................................................. 105.8 耐溶剂(无水乙醇)性...................................................................................... 10六、铝合金化学氧化检验标准......................................................................................... 116.1 试片要求.............................................................................................................. 116.2 外观...................................................................................................................... 116.3 耐蚀性.................................................................................................................. 11七、铝合金喷砂光亮阳极化检验标准............................................................................. 127.1 试片要求.............................................................................................................. 127.2 外观...................................................................................................................... 127.3 氧化膜厚度.......................................................................................................... 127.4 耐蚀性.................................................................................................................. 127.5 封闭质量.............................................................................................................. 12八、喷砂及拉丝检验标准................................................................................................. 138.1 拉丝件.................................................................................................................. 138.2 喷砂件.................................................................................................................. 13表面处理通用检验标准○、总则0.1 零部件表面处理前应去除毛刺、飞边、划痕、氧化层等缺陷,锐边棱角倒钝。
冲压及钣金件制造中的表面处理技术研究进展

冲压及钣金件制造中的表面处理技术研究进展【引言】冲压及钣金件制造在现代工业中起着重要的作用,广泛应用于汽车、电子、家电等领域。
为提高产品的质量和使用寿命,表面处理技术在冲压及钣金件制造中显得尤为重要。
本文将从表面处理工艺、新技术和未来发展方向三个方面,探讨冲压及钣金件制造中的表面处理技术研究进展。
【表面处理工艺】1. 酸洗工艺:酸洗是冲压及钣金件制造中常用的表面预处理方法之一。
它通过酸溶液对材料表面进行清洁和除氧化处理,以提高后续涂装和镀层的附着力。
目前,氢氟酸酸洗、硝酸酸洗、盐酸酸洗等酸洗工艺被广泛应用。
然而,酸洗过程中产生的废液对环境造成污染,需要进一步改进。
2. 电镀工艺:电镀是将金属涂覆在冲压件或钣金件表面的一种表面处理技术。
镀金、镀银、镀铬等电镀工艺可以提高产品的装饰性和防锈性能。
并且,通过选择不同的电镀材料,可以实现不同颜色和表面效果。
然而,传统的电镀过程消耗大量的能源和化学药剂,并产生大量废液,对环境造成负担。
因此,近年来,研究人员开始探索更加环保的电镀替代技术。
【新技术】1. 离子注入技术:离子注入技术是一种将离子注入到基材表面的新型表面处理技术。
通过离子注入,可以提高冲压件和钣金件表面的硬度、耐磨性和腐蚀性能,同时不改变其它物性。
离子注入技术具有高效、节能、无污染等优点,因此受到了广泛关注。
2. 高能束分子矩阵注入技术:高能束分子矩阵注入技术利用高能束分子矩阵注入到基材表面,形成多孔纳米结构。
这种纳米多孔结构可以提高冲压及钣金件表面的吸附性能和润滑性能,从而改善产品在装配和使用过程中的摩擦性能。
【未来发展方向】1. 绿色环保化:随着环保意识的增强,冲压及钣金件制造中的表面处理技术也将朝着更加环保化的方向发展。
研究人员们将致力于寻找更加环境友好的表面处理材料、工艺和设备。
2. 智能化:随着科技的发展,智能制造正在逐渐改变冲压及钣金件制造领域的生产方式。
表面处理领域也将加速向智能化发展,通过智能设备和系统,实现表面处理过程自动化、高效化和信息化。
钣金件常见表面处理介绍

磷酸鋅
4A 4B 4C 4D 4E
1.3磷酸監化成工藝過程及監控
脫脂→水洗→(除銹) →表面調整→化成→水洗→封閉處理 或烤漆 化成工序的監控參數:游離酸度, 全酸度, 雜質含量. 脫脂工序的監控參數:游離鹼度,全鹼度. 表面調整:由於脫脂溶液中的硅酸監使膜結晶粗糙,膜重增 加,不適合涂裝;同時強鹼溶液如NaOH也使鋅監磷化膜 粗糙變厚,並且低磷化膜的耐蝕性和柔韌性.活化晶核由 於生成氫氧化物或氧化物的薄膜而減少,因此用弱鹼性 的磷酸鈦監溶液或草酸溶對鋼鐵表面進行處理,可使大 多數的晶核重新活化和復原,細化晶粒,增加晶粒數.
1.2.鄰酸監膜成機理和構成
1.2.1分類 :
鋼鐵用化成處理劑 鋁用化成處理劑 鋅用化成處理劑 不銹鋼用化成處理劑 銅用化成處理劑 鎂用化成處理劑 其他化成處理劑 涂裝打底用的化成處理劑 塑性加工用化成處理劑 防銹用化成處理劑 耐磨用化成處理劑 絕緣用化成處理劑 塑膠疊片用化成處理劑
1.2.2涂裝打底用皮膜特點:
3.2 通電電鍍(1通過導電使產品上達到一定厚度的金屬鍍層
(2)可以得到全光亮的鍍層 (3) 相對於化學鍍.有較好的軔性.
4.噴砂
使工件表面受到噴射砂粒的沖擊而進行清 理,除鏽或粗化的過程. 目前公司使用的砂子規格:玻璃珠 (ROHS)#220金剛砂(ROHS)#180 技朮要求: 1.噴砂表面紋路均勻,無划痕,污染,大理石花 紋,腐蝕痕跡或疏松粉末.不可出現明顯色 差 2.如有客戶“噴砂”標准樣板,噴砂表面的 外觀必須與樣板一致.
五金件常見表面處理介紹
Daniel TU 2005.12.10
常見表面處理種類
一.鄰化處理(皮膜) 二.陽極氧化 三.電鍍. 四.噴砂 五.拉絲
電化學及化學轉化學
钣金表面处理和丝印
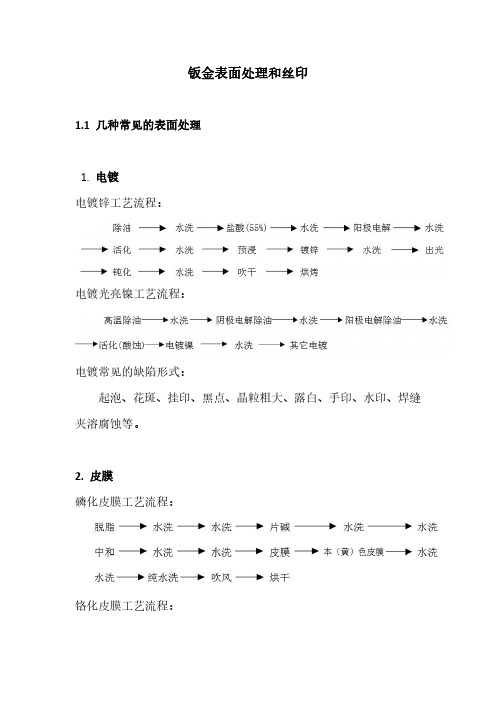
钣金表面处理和丝印1.1几种常见的表面处理1.电镀电镀锌工艺流程:电镀光亮镍工艺流程:电镀常见的缺陷形式:起泡、花斑、挂印、黑点、晶粒粗大、露白、手印、水印、焊缝夹溶腐蚀等。
2.皮膜磷化皮膜工艺流程:铬化皮膜工艺流程:皮膜常见的缺陷形式:露白、针孔、麻点、花斑、水印、残液留痕、深划伤、变形、哑淡等。
1.2表面处理注意事项1.所有电化学处理都应在零件状态下进行,因为处理过程中的化学溶液会被截留在组合件的缝隙之中而引起腐蚀;2.点焊的零件可进行化学处理,但不能进行电化学处理(包括电镀、阳极化);3.铝合金铸件不能进行硫酸阳极氧化处理;4.细而长的管形(其长度大于2倍直径)零件一般不宜进行电化学处理,因为其内表面将没有膜层;(特殊情况下可采取特别措施来满足要求)5.有较深凹槽或细孔(一般指深度大于2倍直径或开口宽度,但优良的工艺可不受此限)的零件电镀后,其内表面将不能完全覆盖镀层;6.钢铁件喷涂前好先进行磷化处理,以增加涂层的附着力;7.镀亮镍的钢件为提高其耐蚀性,可先镀铜或镀暗镍打底;8.锌基合金一般采用电镀层作防护装饰,为提高其镀层的结合力,一般需先预镀铜或镍;9.因多数有机气体对锌有腐蚀作用,故在设计中应谨慎选用镀锌层与有机材料接触或组装在同一密闭体内;10.对有铆接要求的电镀(氧化)件,其加工工序必须是先电镀(或氧化)、然后再铆接。
1.3丝印为保证产品整体形象的统一,产品的丝印设计需按以下原则进行:1.系列产品的丝印形式必须保持一致;2.同一产品的不同模块的丝印形式必须保持一致;3.丝印内容(文字或标记)的排列,根据功能和具体结构形式,结合平面设计的美学法则进行组织,在视觉上达到美观,整齐一致;4.丝印内容的定位一般以零件外边缘作为基准,为了丝印时更换基准的方便,丝印图好将外形尺寸标上;5.用于指示某一器件功能的丝印内容可位于该器件的上、下、左或右适当位置,位于器件上或下时丝印内容以中心定位,位于器件左边时丝印内容以右边定位,位于器件右边时丝印内容以左边定位。
钣金件表面处理主要工艺方法介绍

表面处理工艺表面处理技术介绍一、什么叫做表面处理表面处理:以最经济和最有效的方法改变产品表面及近表面区的形态、化学成分和组织结构,有效地改善和提高产品的装饰性能、耐腐蚀性能和耐磨性能,延长产品的使用寿命。
常见的表面处理:电镀,化学镀,转化膜技术,物理气相沉积,化学气相沉积,热喷涂,热浸镀,喷砂,化学转化,阳极氧化,涂装等;表面处理技术还能赋予材料表面各种光、电、磁、热、声、化学以及功能转换等特性。
1.各种光的表面技术:镜子;防反光;2.各种电的表面技术:绝缘的镀银,金,铜;导电的用塑料保护3.各种磁的表面技术:隐身技术(重点)4.热的表面技术:红外,吸收红外,防热;5.声的表面技术:防声纳6.化学:钢材镀锌表面处理的种类表面处理根据产品的使用要求可以分为:防护型表面处理,如电镀、氧化(化学氧化、电化学氧化)、装饰型表面处理(如涂装、、功能型表面处理,总的来说,没有明显的划分界限,其主要目的是延长产品的使用寿命,最大程度的节省和利用资源。
二、钣金加工中为什么要进行表面处理?1.钣金加工所用的材料多为冷轧板、热轧板、电解板、白口铁、不锈钢、铝合金板及型材、铜材等,这些材料暴露在大气中,与空气中的水分和氧充分接触后,会发生电化学反应,从而造成材料表面腐蚀,同时物理及化学性质不同的材料间相互接触也会由于彼此间的电位差而形成原电池,从而造成接触腐蚀。
为避免钣金加工中材料在各加工工序间及成品在存放及使用中发生腐蚀,生产中通过对材料进行表面处理方式来控制腐蚀的产生或延缓腐蚀的产生,从而减少由于腐蚀的产生而造成产品返修或报废,尽可能地节约资源及生产成本。
2.各种材料经过钣金加工转化为商品时,为了满足顾客的需求及商品给予人视觉上的美感,就对产品外观作各种表面处理,如电镀、氧化着三、在钣金加工业中铝合金材料通常需进行哪些表面处理?在钣金加工业中,铝合金材料通常需进行以下表面处理:无色化学氧化、黑色化学氧化、金黄色化学氧化、拉丝无色化学氧化、喷砂无色化学氧化、光亮无色化学氧化、喷砂光亮阳极氧化、化学氧化着色、化学氧化后涂装(喷漆、喷粉),其中氧化层有导电与绝缘两种;硬质、耐磨等;前处理四、磷化工艺A、磷化工艺流程:预脱脂----脱脂----流动水洗----流动水洗----表调----磷化----流动水洗----流动水洗----纯水洗----烘干B、前处理生产线喷淋线、浸泡线装生产前为何要进行磷化处理?1、磷化是通过化学的方法使铁基材或锌基材与磷酸盐发生反应而生成一层致密的化学转化膜的过程。
钣金加工中的表面处理应该注意什么

钣金加工就是对金属板材实施加工的技术,它既包括传统的切割下料、冲裁加工、弯压成形等方法及工艺参数,又包括各种冷冲压模具结构及工艺参数、各种设备工作原理及操纵方法,还包括一些新冲压技术及新工艺。
越来越多的钣金加工企业认识到,适当的表面处理可以对产品表面起到很好的装饰和防护作用,提高产品的“颜值”,进而提高市场竞争力。
钣金加工中常用的表面处理方式:钣金加工中最常用的表面处理方式有电镀、喷涂两种。
电镀分为镀锌、镀镍、镀铬等,主要目的是利用电解原理,在钣金工件表面形成一层金属或合金防护层,起到保护和装饰的作用。
喷涂分为喷漆和喷粉两种,是将料件经过前处理以后,用喷枪气体把涂料分散成均匀而微细的雾滴,并喷到钣金工件表面上,使涂料在工件表面形成涂层,再加热烘干。
喷涂能够对工件起到防护的作用。
除了以上两种方式外,还有一些其他的表面处理方式,如阳极氧化、铬酸盐、拉丝、喷砂和氧化等,在这里就不做具体的介绍了。
钣金工件表面处理的注意事项:首先要注意的是工件的状态,所有的电化学处理都必须在工件的散件状体下进行,组合件觉得不能进行电化学处理。
因为在处理过程中,溶液会被截留在组合件的缝隙中而对工件造成腐蚀。
其次要注意加工顺序问题,比如经过点焊的零件可以进行化学处理,但是千万不能进行电化学处理,包括电镀、阳极氧化在内的电化学处理都会对点焊质量造成影响。
对于一些有铆接要求的电镀或氧化件,其加工工序必须遵循先电镀或氧化,然后再进行铆接。
第三要注意表面处理前的预处理,比如钢件在进行喷涂以前,有必要先经过磷化处理,这样可以增加涂层的附着力。
镀亮镍的钢件,为了提高其耐腐蚀性,可以先镀一层铜或暗镍打底。
锌基合金也存在这个问题,在电镀之前同样需要预先镀一层铜或暗镍打底,这样可以提高电镀层的结合力。
第四要注意工件材料与处理方法不能发生冲突,铝合金铸件就绝不允许进行硫酸阳极氧化处理。
第五,应该根据零件的形状判断其是否适合电化学加工,比如长度大于两倍直径的细长管就不宜进行电化学处理,因为其内表面无法形成高质量的膜层;而具备较深凹槽或者是深度大于两倍直径细孔的零件,在电镀之后,内表面也没法被镀层完全覆盖到。
钣金常用表面处理技术介绍

4.2.1.2化学镀镍的沉积机理
以次磷酸盐镀液为例﹐首先是次磷酸根在固体催化表面上氧化脱氢﹐并生成亚磷酸根﹐反应为﹕
H2PO2-+H2O→H++H3PO2-+2H
吸附于催化表面上的活泼氢原子使镍离子还原成金属镍﹐而本身则氧化为氢离子﹐
Ni2++2H→Ni+2H+
同时溶液中的部分次磷酸根也被吸附在催化表面上的活泼氢原子还原成单质磷﹐
5.3防锈油应具备的性能
(1)防锈性能良好
(2)无腐蚀性﹐与其所接触的金属或非金属部件不其作用。
(3)对人体无害﹑无特殊臭味或其它刺激性气味
(4)具有很好的化定性﹐在长期储存中不变质﹑不氧化﹑效果恒定。能有效防止有害气体和水扩散到金属表面﹐同时对手汗有一定的置换性
(5)涂层不因温度变化而流失或龟裂﹔涂层应有一定的强度﹔涂层要薄﹐且除膜性好﹐并能适应多种包装材料的包装。
在大气条件下很稳定﹐在有机油类﹐苯﹐甲苯及各种气体燃料中有很好的耐蚀性。但磷酸盐皮膜不耐酸﹐碱﹐氨﹐海水及水蒸气等。磷酸盐膜经过封闭处理后能大大提高其耐蚀性。
磷酸盐皮膜的耐蚀性高于发蓝膜。
(2)吸附性
磷酸盐膜具有多孔构﹐有很好的吸附性﹐因此常用作油漆的底层和吸附润滑油后作为减摩层和润滑层。
(3)电绝缘性
表面调整﹕由于脱脂溶液中的硅酸盐使膜结晶粗糙﹐膜重增加﹐不适合涂装﹔同时强碱溶液如NaOH也使锌盐磷化膜粗糙变厚﹐并且降低磷化膜的耐蚀性和柔韧性。活化晶核由于生成氢氧化物或氧化物的薄膜而减少﹐因此用弱碱性的磷酸钛盐溶液或稀草酸溶液对钢铁表面进行处理﹐可使大多数的晶核重新活化和复原﹐细化晶粒﹐增加晶粒数。
4.化学镀
4.1化学镀的特性
常见钣金件加工的工艺流程及表面处理

常见钣金件加工的工艺流程及表面处理工的工艺流程及表面处理导读:常见钣金件加工的工艺流程及表面处理钣金加工是钣金技术人员需要掌握的关键技术,也是钣金制品成形的重要工序,它既包括传统的切割下料、冲裁加工、弯压成形等方法及工艺参数,又包括各种冷冲压模具结构及工艺参数、各种设备工作原理及操作方法,还包括新冲压技术及新工艺,钣金加工一般用到的材料有冷轧板(SPCC)、热轧板(SHCC)、镀锌板(SECC,N料主要不作表面处理,其表面处理是镀镍、镀铬,或不作处理,一常见钣金件加工的工艺流程及表面处理钣金加工是钣金技术人员需要掌握的关键技术,也是钣金制品成形的重要工序。
它既包括传统的切割下料、冲裁加工、弯压成形等方法及工艺参数,又包括各种冷冲压模具结构及工艺参数、各种设备工作原理及操作方法,还包括新冲压技术及新工艺。
一、材料的选用钣金加工一般用到的材料有冷轧板(SPCC)、热轧板(SHCC)、镀锌板(SECC、SGCC),铜(CU)黄铜、紫铜、铍铜,铝板(6061、6063、硬铝等),铝型材,不锈钢(镜面、拉丝面、雾面),根据产品作用不同,选用材料不同,一般需从产品其用途及成本上来考虑。
1.冷轧板SPCC,主要用电镀和烤漆件,成本低,易成型,材料厚度≤3.2mm。
2.热轧板SHCC,材料T≥3.0mm ,也是用电镀,烤漆件,成本低,但难成型,主要用平板件。
3.镀锌板SECC、SGCC。
SECC电解板分N料、P料,N料主要不作表面处理,成本高, P料用于喷涂件。
4.铜;主要用导电作用料件,其表面处理是镀镍、镀铬,或不作处理,成本高。
5.铝板;一般用表面铬酸盐(J11-A),氧化(导电氧化,化学氧化),成本高,有镀银,镀镍。
6.铝型材;截面结构复杂的料件,大量用于各种插箱中。
表面处理同铝板。
7.不锈钢;主要用不作任何表面处理,、成本高。
二、图面审核要编写零件的工艺流程,首先要知道零件图的各种技术要求;则图面审核是对零件工艺流程编写的最重要环节。
钣金件表面处理常见缺陷
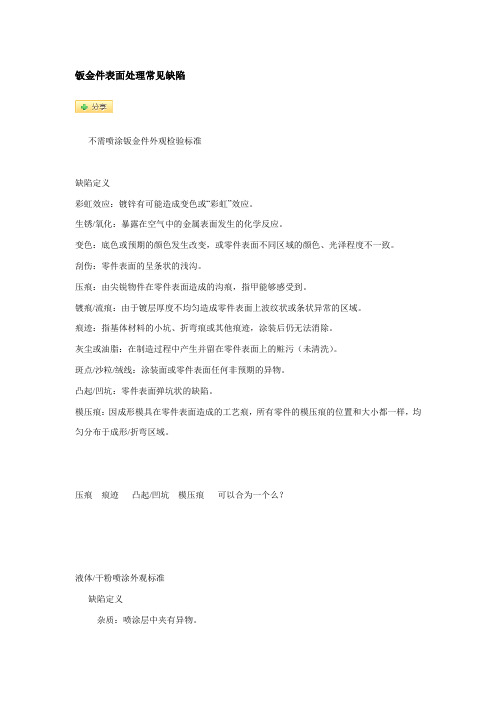
钣金件表面处理常见缺陷不需喷涂钣金件外观检验标准缺陷定义彩虹效应:镀锌有可能造成变色或“彩虹”效应。
生锈/氧化:暴露在空气中的金属表面发生的化学反应。
变色:底色或预期的颜色发生改变,或零件表面不同区域的颜色、光泽程度不一致。
刮伤:零件表面的呈条状的浅沟。
压痕:由尖锐物件在零件表面造成的沟痕,指甲能够感受到。
镀痕/流痕:由于镀层厚度不均匀造成零件表面上波纹状或条状异常的区域。
痕迹:指基体材料的小坑、折弯痕或其他痕迹,涂装后仍无法消除。
灰尘或油脂:在制造过程中产生并留在零件表面上的赃污(未清洗)。
斑点/沙粒/绒线:涂装面或零件表面任何非预期的异物。
凸起/凹坑:零件表面弹坑状的缺陷。
模压痕:因成形模具在零件表面造成的工艺痕,所有零件的模压痕的位置和大小都一样,均匀分布于成形/折弯区域。
压痕痕迹凸起/凹坑模压痕可以合为一个么?液体/干粉喷涂外观标准缺陷定义杂质:喷涂层中夹有异物。
凹痕:基体材料压痕(包括接刀痕,模压痕,折弯压痕)造成的喷涂面局部凹陷。
剥离:噴涂表面局部脫落。
刮伤:喷涂表面划伤,且已伤至底层,露出金属底材颜色。
桔皮:喷涂面因涂料附着力差而导致起皱,局部堆积凸起,象桔子皮样的外观或皱纹状(皱纹粉除外)。
流痕:喷涂表面有液体流淌状的突起,顶端呈圆珠状。
变色:喷涂面颜色(深浅)不一致。
针孔:涂层表面可看见类似针刺形成的微小孔(不能露出金属底材,如露出则视为剥离)。
气泡:喷涂层局部粘附不良引起涂膜凸起。
污迹:由于基体材料缺陷或不干净而导致零件喷涂表面有污迹或颜色不规则。
挂具印:因装挂用辅助工具的遮挡在喷涂表面留下的印记(不能露出金属底材,如露出则视为剥离)。
擦伤:喷涂表面划伤,但未伤至金属底材。
开裂:喷涂表面有细的裂纹。
麻点(缩孔/鱼眼):涂层干燥后仍滞留的若干大小不等、分布各异的圆形小坑等(不能露出金属底材,如露出则视为剥离)。
厚边:喷涂时在产品边缘或内折弯角处的涂料堆积现象。
色差:喷涂颜色与标准色板样的颜色不一致,不均匀。
钣金表面处理的方式都有哪些

钣金件的表面处理也是钣金加工过程非常重要的一环,因为它有防止零件生锈,美化产品的外观等作用。
由于某些钣金材料表面不具备防锈防腐蚀的能力,所以进行有效的表面处理是十分必要的。
对钣金件进行表面处理可以提高产品在恶劣环境下的使用寿命,或者为了达到特定的表面效果或功能。
钣金常见的几种表面处理方式为:拉丝、喷砂、烤漆、喷粉、电镀、阳极氧化。
这几种1.拉丝
主要作用是美化外观.一般都是铝材才考虑用拉丝的表面处理方式。
2.喷砂
主要作用是去除工件表面的脏污,增加工件表面的附着力,为后续表面处理方式做准备。
3.烤漆
通过喷涂,高温烘烤等方式,在材料表面喷上一层各种颜色的涂料,用来美化外观,且能增加材料的防腐蚀性能.是常用的表面处理方式(一般有液体烤漆和粉体烤漆两种)。
4.电镀
通过化学反应,在材料表面附上一层其他金属,用来增加金属的防腐蚀性能,且能达到一定的美化外观作用,是常用的一种表面处理方式,如:电镀锌,电镀镍等。
5.阳极氧化
将工件表面的金属氧化,在工件表面形成一层致密的保护膜,增加工件的防腐蚀性.一般有化学氧化和阳极氧化两种方式。
钣金件表面前处理的作用主要是去油污,氧化皮,铁锈等,它为表面后处理作准备;而后处理主要是喷(烤)漆,喷塑以及镀防锈层等。
钣金件制作中的选材以及表面处理加工工艺探讨

钣金件制作中的选材以及表面处理加工工艺探讨钣金件是指利用薄板、带材等金属材料经过剪切、折弯、冲压、焊接等加工工艺制作成的零件。
它广泛应用于电子、通信、家电、汽车、机械设备等领域,是现代制造业中不可或缺的一部分。
在钣金件的制作过程中,选材和表面处理加工工艺是两个非常重要的环节,直接关系到产品的质量和性能。
本文将就钣金件制作中的选材以及表面处理加工工艺进行探讨,希望能为相关行业提供一些参考。
一、选材1.金属材料在钣金件的制作中,常用的金属材料主要有冷轧板、热轧板、镀锌板、铝合金板等。
不同材料的特性决定了其适用的领域和加工工艺,因此在选材时需要考虑以下几个方面:(1)强度和硬度强度和硬度是衡量材料抗拉伸、抗压和抗划伤能力的重要指标,选择适当的强度和硬度可以保证钣金件在使用过程中不易发生变形和损坏。
(2)可加工性材料的可加工性指的是其在加工过程中的可塑性、可焊性和可切削性等能力,不同的材料在加工性能上有所差异,因此需要根据具体的工艺要求来选择适宜的材料。
(3)耐腐蚀性耐腐蚀性是指材料在不同环境条件下抵抗腐蚀的能力,特别是在一些特殊环境下,如海洋、酸雨等腐蚀环境下,需要选择具有良好耐腐蚀性的材料。
除了金属材料外,还有一些非金属材料在钣金件制作中也有着重要的作用,比如塑料、橡胶、纤维复合材料等。
这些材料通常用于钣金件的密封、绝缘、减震等功能,需要根据具体的使用要求选择适宜的非金属材料。
选材时需要根据钣金件的具体用途、工艺要求和环境条件等因素来综合考虑,选择适宜的金属和非金属材料,以确保产品具有良好的性能和稳定的质量。
二、表面处理加工工艺表面处理是钣金件制作中非常重要的一环,它直接影响着产品的外观、耐腐蚀性和耐磨性等性能。
常用的表面处理加工工艺主要包括镀锌、喷涂、阳极氧化、电泳涂装等,下面将对几种常用的表面处理加工工艺进行介绍:1.镀锌镀锌是将锌层覆盖在钢铁制品表面的一种防腐处理方式,可以有效提高钣金件的耐腐蚀性。
钣金零件表面处理设备环保清洗技术的标准与规范
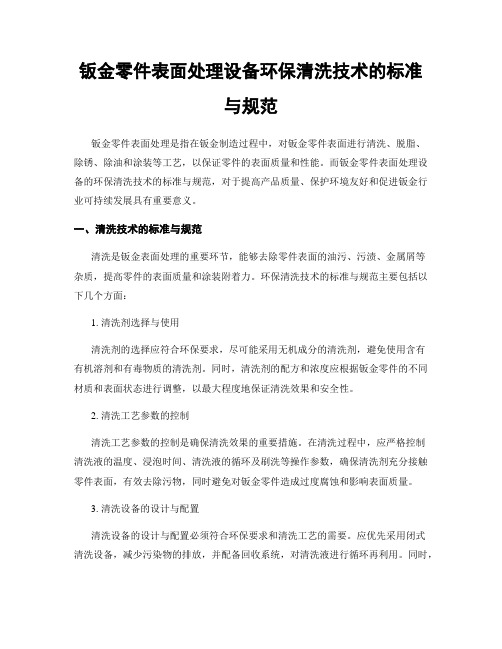
钣金零件表面处理设备环保清洗技术的标准与规范钣金零件表面处理是指在钣金制造过程中,对钣金零件表面进行清洗、脱脂、除锈、除油和涂装等工艺,以保证零件的表面质量和性能。
而钣金零件表面处理设备的环保清洗技术的标准与规范,对于提高产品质量、保护环境友好和促进钣金行业可持续发展具有重要意义。
一、清洗技术的标准与规范清洗是钣金表面处理的重要环节,能够去除零件表面的油污、污渍、金属屑等杂质,提高零件的表面质量和涂装附着力。
环保清洗技术的标准与规范主要包括以下几个方面:1. 清洗剂选择与使用清洗剂的选择应符合环保要求,尽可能采用无机成分的清洗剂,避免使用含有有机溶剂和有毒物质的清洗剂。
同时,清洗剂的配方和浓度应根据钣金零件的不同材质和表面状态进行调整,以最大程度地保证清洗效果和安全性。
2. 清洗工艺参数的控制清洗工艺参数的控制是确保清洗效果的重要措施。
在清洗过程中,应严格控制清洗液的温度、浸泡时间、清洗液的循环及刷洗等操作参数,确保清洗剂充分接触零件表面,有效去除污物,同时避免对钣金零件造成过度腐蚀和影响表面质量。
3. 清洗设备的设计与配置清洗设备的设计与配置必须符合环保要求和清洗工艺的需要。
应优先采用闭式清洗设备,减少污染物的排放,并配备回收系统,对清洗液进行循环再利用。
同时,清洗设备的结构应合理,易于清洗剂的更换和设备的维护,以保证设备的长期稳定运行和提高清洗效率。
二、环保清洗技术的优势环保清洗技术对于钣金行业的发展具有许多重要优势,如下所示:1. 减少污染物排放传统的清洗工艺中常采用有机溶剂等化学物质,会导致大量的挥发性有机物排放,对环境造成严重的污染。
而环保清洗技术采用水性清洗剂或无机清洗剂,能够有效减少污染物排放,降低对环境的影响。
2. 节约能源和资源环保清洗技术在设计和操作上更加合理高效,能够减少能源的消耗和资源的浪费。
例如,采用封闭式清洗设备,并配备回收系统,能够实现清洗剂的循环利用,减少清洗剂的消耗和成本。
钣金表面处理工艺

四、热处理的工艺性
热处理时机的确定: 预备热处理一般安排在毛坯生产之后,切
削加工之前 正火和退火:消除热加工时毛坯的内应力、
细化晶粒、调整组织、改善切削加工性 调质:提高零件综合性能,为最终热处理
做组织上的准备
钣金表面处理工艺
最终热处理(淬火+回火或化学热处理): 一般放在半精加工之后,磨削加工之前。 热处理工艺对零件结构的要求
多弧离子镀膜机
钣金表面处理工艺
物理气相沉积具有适用的基体材料和膜层材料广泛;工艺简 单、省材料、无污染;获得的膜层膜基附着力强、膜层厚度 均匀、致密、针孔少等优点。
广泛用于机械、航空航天、电子、光学和轻工业等领域制备 耐磨、耐蚀、耐热、导电、绝缘、光学、磁性、压电、滑润、 超导等薄膜。
钣金表面处理工艺
⑶ 激光热处理: 利用高能量密度的 激光对工件表面进行加热的方法。 效率高,质量好。
火焰加热表面淬火
激光表面热处理
钣金表面处理工艺
火焰加热表面淬火示意图
钣金表面处理工艺
一、表面热处理
2、化学表面热处理
化学热处理是将工件置于特定介质中加热保温,使 介质中活性原子 渗入工件表层从 而改变工件表层 化学成分和组织, 进而改变其性能 的热处理工艺。
火轴 感连
感应加热表面淬火齿轮的截面图
钣金表面处理工艺
中频感应加热 频 率 为 25008000Hz,淬硬层深 度2-10mm。
中频感应加热表面淬火的机车凸轮轴
钣金表面处理工艺
各种感应器
工频感应加热 频率为50Hz,淬硬层
深度10-15 mm
感应穿透加热
各种感应器
钣金表面处理工艺
⑵ 火焰加热: 利用乙炔火焰直接加 热工件表面的方法。成本低,但质 量不易控制。
钣金件制作中的选材以及表面处理加工工艺探讨

钣金件制作中的选材以及表面处理加工工艺探讨钣金件是一种重要的机械零部件,广泛应用于各种机械设备中。
钣金件制作中的选材以及表面处理加工工艺对于产品的质量和性能有着重要的影响。
本文将探讨钣金件制作中的选材和表面处理加工工艺的相关问题。
选材是钣金件制作过程中的关键一步。
选材应首先满足产品的使用要求,例如要求耐腐蚀、耐高温、耐磨损等。
常用的钣金材料有冷轧板、热轧板、镀锌板、不锈钢板等。
冷轧板由于具有较好的成型性能和表面质量,广泛应用于一般工业产品上。
不锈钢板因具有较好的耐腐蚀性能和美观性,被广泛应用于高档家电和厨具等产品。
根据不同的需求选择合适的材料有助于提高产品的质量和性能。
表面处理是钣金件制作中的重要一环。
表面处理可以提高产品的防腐性能、美观性能和附着性能。
常用的表面处理加工工艺有喷涂、电镀、喷砂等。
喷涂是一种常用的表面处理方法,可以保护钣金件表面不受外界因素的侵蚀,例如防腐、防潮、防氧化等。
电镀是一种常用的提高钣金件外观质量和耐腐蚀性能的方法,例如镀铬、镀锌等。
喷砂是通过喷射高速喷砂流将砂粒冲击到钣金件表面,达到去除表面氧化皮和清洁的效果,从而提高粉涂附着力和表面质量。
钣金件制作中的选材和表面处理加工工艺对产品的质量和性能有着重要的影响。
选材应根据产品的使用要求选择适合的材料,以提高产品的使用寿命和性能。
表面处理加工工艺应结合产品的使用环境和要求选择合适的方法,以提高产品的防腐性能、美观性能和附着性能。
在实际的制作过程中,还需要根据不同材料和工艺的特点,选择合适的加工设备和工艺参数,保证产品的质量和性能。
制作过程中还需要注意操作规范和质量控制,以确保产品的质量和性能符合要求。
- 1、下载文档前请自行甄别文档内容的完整性,平台不提供额外的编辑、内容补充、找答案等附加服务。
- 2、"仅部分预览"的文档,不可在线预览部分如存在完整性等问题,可反馈申请退款(可完整预览的文档不适用该条件!)。
- 3、如文档侵犯您的权益,请联系客服反馈,我们会尽快为您处理(人工客服工作时间:9:00-18:30)。
钣金件就是薄板五金件,也就是可以通过冲压,弯曲,拉伸等手段来加工的零件,一个大体的定义就是在加工过程中厚度不变的零件. 相对应的是铸造件,锻压件,机械加工零件等.
SPCC 一般用钢板,表面需电镀或涂装处理
SECC 镀锌钢板,表面已做烙酸盐处理及防指纹处理
SUS 301 弹性不锈钢
SUS304 不锈钢
镀锌钢板表面的化学组成------基材(钢铁),镀锌层或镀镍锌合金层,烙酸盐层和有机化学薄膜层。
有机化学薄膜层能表面抗指纹和白锈,抗腐蚀及有较佳的烤漆性。
SECC的镀锌方法
热浸镀锌法:
连续镀锌法,成卷的钢板连续浸在溶解有锌的镀槽中;
板片镀锌法,剪切好的钢板浸在镀槽中,镀好后会有锌花。
电镀法: 电化学电镀,镀槽中有硫酸锌溶液,以锌为阳极,原材质钢板为阴极。
(1)产品种类介绍
1.品名介绍
材料规格后处理镀层厚度
S A B C * D * E
S for Steel
A:
EG (Electro Galvanized Steel)电气镀锌钢板---电镀锌
一般通称 JIS
镀纯锌 EG SECC (1)
铅和镍合金合金EG SECC (2)
GI (Galvanized Steel) 溶融镀锌钢板------热浸镀锌
非合金化 GI, LG SGCC (3)
铅和镍合金 GA, ALLOY SGCC (4)
裸露处耐蚀性 2>3>4>1
熔接性 2>4>1>3
涂漆性 4>2>1>3
加工性 1>2>3>4
B:所使用的底材
C (Cold rolled) : 冷轧
H (Hot rolled): 热轧
C:底材的种类
C:一般用
D:抽模用
E:深抽用
H:一般硬质用
D:后处理
M:无处理
C:普通烙酸处理---耐蚀性良好,颜色白色化
D:厚烙酸处理---耐蚀性更好,颜色黄色化
P:磷酸处理---涂装性良好
U:有机耐指纹树脂处理(普通烙酸处理)--- ---耐蚀性良好,颜色白色化,耐指纹性很好
A:有机耐指纹树脂处理(厚烙酸处理)---颜色黄色化,耐蚀性更好
FX:无机耐
指纹树脂处理---导电性
FS:润滑性树脂处理---免用冲床油
E:镀层厚
(2)物理特性
膜厚---含镀锌层,烙酸盐层及有机化学薄膜层,最小之膜厚需0.00356mm以上。
测试方法有磁性测试(ASTM B499),电量分析(ASTM B504),显微镜观察(ASTM B487)。
表面抗电阻---一般应该小于0.1欧姆/平方公分。
(3)
盐雾试验----试片尺寸100mmX150mmX1.2mm,试片需冲整捆或整叠铁材中取下,必须在镀烙酸盐后24小时,但不可超过72小时才可以用于测试,使用5%的盐水,用含盐的水汽充满箱子,试片垂直倒挂在箱子中48小时。
测试后试片的镀锌层不可全部流失,也不能看到底材或底材生锈,但是离切断层面6mm范围有生锈情况可以忽略。
(4) 镀锌钢板的一般问题点
1.白锈---因结露或被水沾湿致迅速发生氢氧化锌为主要成分的白色粉末状的锈。
(会导致产品质量劣化)
2.红锈---因结露或被水沾湿致迅速发生氢氧化铁为主要成分的红茶色粉末状的锈。
3.烙酸不均匀---黄茶色的小岛形状或线形状的花纹,但耐蚀性没有问题。
4.替代腐蚀保护---在锌面割伤而,露出钢板基体表面的情况下,我们也不必担心镀锌钢板切边生锈问题。
(5) 镀锌钢板之烤漆处理
1.前处理
由于锌是一种高活性金属,在烤漆前需要适当的化学转化处理如磷酸盐处理。
磷酸盐处理剂有两种,一种是处理铁的,一种是处理锌的。
2.脱脂
采用弱碱,有机溶剂及中性乳液或洗涤剂,避免用酸或强碱脱脂剂。
可用水膜试验(Water lreakage test)来确认,观察试验后的水是否受到污染,以及试品表面的水膜是否均匀。
3.烤漆
电镀锌钢片对漆的选择性比冷轧钢片为严。
使用水性底漆(Water promer)可以确保有较强的油漆附着性。