镁合金制程介绍(压铸件)
镁合金压铸工艺介绍

AS41B
3.5~5.0 0.35~0.7 0.12 max 0.5~1.5 0.02 max 0.002 max 0.0035 max 0.02
单位:%
特性介绍:AZ91-机械性质及铸造性极佳 AM60-延性及冲击强度佳 AS41-高温强度及抗潜变能力优
机械 性质
材料 名称
unit AZ91D AM60B AS41B
热室机-柱塞速度:3~ 5 m/sec熔汤于浇口速度:30~ 40 m/sec 冷室机-柱塞速度:5~10 m/sec熔汤于浇口速度:90~120 m/sec
2.高压-压铸机于熔汤充满模穴后再施予之压力。 热室机-170~280kg/cm2
冷室机-350~550kg/cm2
3.冷却速度极快 4.充填时间极短-Notebook LCD Cover之铸件充填时间仅7ms (0.007sec)
抗拉 强度
MPa 230 220 215
常用镁合金之 机械特性
降伏 强度
压降伏 强度
剪强度
疲劳 强度
MPa 160 120 140
MPa 165 130 140
MPa 140 N/A N/A
MPa 70 70 N/A
冲击 强度
伸长率 (51mm)
硬度
J
%
BHN
2.2
3
75
6.1
6~8
62
4.1
6
75
8.与钢之亲和性小
模具壽命Байду номын сангаас,切削加工性佳
9.机械加工性佳
切削加工性佳
10.镁金属蕴藏丰富
地球上第三豐富之構造用金屬材料,第八大豐富元素,主要蘊藏於菱鎂礦、白雲石及海水中
(完整版)镁合金压铸工艺

(完整版)镁合金压铸工艺镁合金压铸工艺(完整版)概述镁合金压铸是一种常用的金属加工方法,适用于生产各种复杂形状的镁合金零件。
本文档将介绍镁合金压铸工艺的完整过程。
原材料镁合金压铸的原材料主要是镁合金。
镁合金具有低密度、高强度和良好的机械性能,因此在航空航天、汽车和电子等领域得到广泛应用。
模具设计在镁合金压铸过程中,模具起着关键的作用。
合理的模具设计可以确保产品的质量和生产效率。
模具应考虑产品形状、尺寸和冷却系统等因素。
铸造工艺1. 预热模具:在进行镁合金压铸之前,需要将模具进行预热,以提高铸造品质和延长模具寿命。
2. 熔化镁合金:将镁合金加热至熔点,形成液态金属。
3. 液态金属注入模具:将液态镁合金迅速注入预热的模具中,填充模具腔体。
4. 压力施加:通过压铸机施加高压,使液态金属充分填充模具腔体,并确保产品的致密性和表面平整度。
5. 冷却固化:待金属冷却固化后,取出模具中的镁合金零件。
加工和表面处理冷却固化后的镁合金零件需要进行加工和表面处理,以达到设计要求和外观要求。
加工过程可以包括切割、打磨、钻孔等操作。
表面处理可以采用喷涂、阳极氧化等方法。
质量检验镁合金压铸工艺中,质量检验是不可或缺的环节。
质量检验可以包括外观检查、尺寸测量、力学性能测试等。
通过质量检验,可以确保产品达到设计要求和客户需求。
结论镁合金压铸工艺是一种高效的金属加工方法,广泛应用于工业生产中。
合理的工艺设计和严格的质量检验是保证产品质量的关键因素。
希望本文档对了解镁合金压铸工艺的完整过程有所帮助。
参考文献- 张三, 镁合金压铸工艺研究, 《金属加工》, 2018.。
最新 绝对实用 镁合金压铸技术
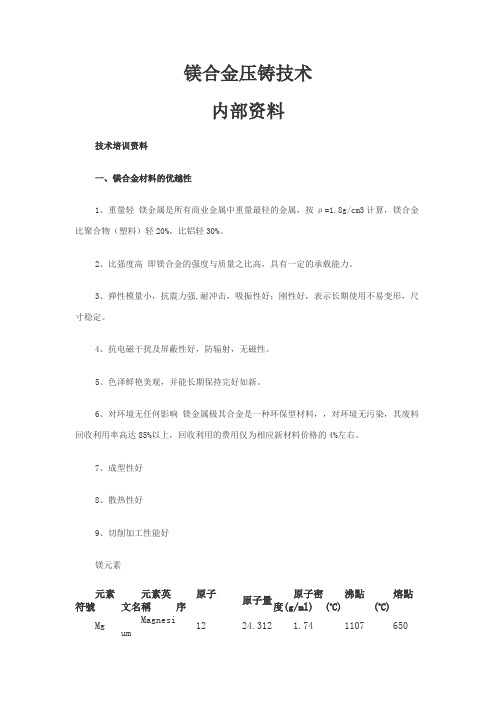
镁合金压铸技术内部资料技术培训资料一、镁合金材料的优越性1、重量轻镁金属是所有商业金属中重量最轻的金属,按ρ=1.8g/cm3计算,镁合金比聚合物(塑料)轻20%,比铝轻30%。
2、比强度高即镁合金的强度与质量之比高,具有一定的承载能力。
3、弹性模量小,抗震力强,耐冲击,吸振性好;刚性好,表示长期使用不易变形,尺寸稳定。
4、抗电磁干扰及屏蔽性好,防辐射,无磁性。
5、色泽鲜艳美观,并能长期保持完好如新。
6、对环境无任何影响镁金属极其合金是一种环保型材料,,对环境无污染,其废料回收利用率高达85%以上,回收利用的费用仅为相应新材料价格的4%左右。
7、成型性好8、散热性好9、切削加工性能好镁元素元素符號元素英文名稱原子序原子量原子密度(g/ml)沸點(o C)熔點(o C)MgMagnesium12 24.312 1.74 1107 650二、镁合金压铸的优势模具寿命和生产效率钢模具型腔的热裂和热冲击,是多年来一直困扰压铸工作人员的两个问题。
在压铸铝合金时,在压射了10.000次后,就发现冲击的痕迹和热裂,这并不少见。
只要模具一开始投入使用,它型腔的钢材就慢慢被损伤;当压铸了150.000-200.000次以后,就要更换模具了。
有的时候,模具的寿命可能更短些。
镁合金与铝合金不同,它不像铝合金那样侵袭型腔的钢材。
根据实际的资料,压铸镁合金的模具的寿命约为铝合金模具的3-4倍。
有许多镁合金压铸模,在压铸了500000次以后,现在还在生产中正常使用。
许多这样的模具还在用于生产薄壁件,其表面质量要求很高。
由于镁的凝固很快,以及它不易粘结,所以可以比铝有更高的生产效率,而仃机和喷雾的时间更少。
与铝合金相比,镁合金的压铸周期时间可以比铝合金缩短25%到50%。
由于镁合金本身固有的特性,因而能有较快的压铸速率。
与铝合金相比,其压铸速率可以提高50%。
可以减轻重量是镁合金的另一重要优点,但与铝合金,锌合金作精确的减轻重量的比较,还要根据图纸作全面的考虑。
镁合金压铸工艺
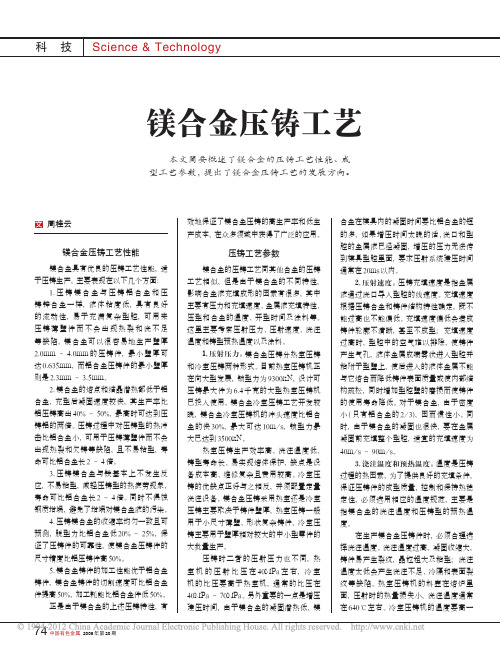
科 技Science & Technology镁合金压铸工艺本文简要概述了镁合金的压铸工艺性能、成型工艺参数,提出了镁合金压铸工艺的发展方向。
文 周桂云镁合金压铸工艺性能镁合金具有优良的压铸工艺性能,适于压铸生产,主要表现在以下几个方面:1.压铸镁合金与压铸铝合金和压铸锌合金一样,液体粘度低,具有良好的流动性,易于充满复杂型腔,可用来压铸薄壁件而不会出现热裂和浇不足等缺陷。
镁合金可以很容易地生产壁厚2.0mm~4.0mm的压铸件,最小壁厚可达0.635mm,而铝合金压铸件的最小壁厚则是2.3mm~3.5mm。
2.镁合金的熔点和结晶潜热都低于铝合金,充型后凝固速度较快,其生产率比铝压铸高出40%~50%,最高时可达到压铸铝的两倍。
压铸过程中对压铸型的热冲击比铝合金小,可用于压铸薄壁件而不会出现热裂和欠铸等缺陷,且不易粘型,寿命可比铝合金长2~4倍。
3.压铸镁合金与铁基本上不发生反应,不易粘型,减轻压铸型的热疲劳现象,寿命可比铝合金长2~4倍。
同时不侵蚀钢质坩埚,避免了坩埚对镁合金液的污染。
4.压铸镁合金的收缩率均匀一致且可预测,脱型力比铝合金低20%~25%,保证了压铸件的可靠性,使镁合金压铸件的尺寸精度比铝压铸件高50%。
5.镁合金铸件的加工性能优于铝合金铸件,镁合金铸件的切削速度可比铝合金件提高50%,加工耗能比铝合金件低50%。
正是由于镁合金的上述压铸特性,有效地保证了镁合金压铸的高生产率和低生产成本,在众多领域中获得了广泛的应用。
压铸工艺参数镁合金的压铸工艺同其他合金的压铸工艺相似,但是由于镁合金的不同特性,影响合金液充填成形的因素有很多,其中主要有压力和充填速度、金属液充填特性、压型和合金的温度、开型时间及涂料等。
这里主要考察压射压力、压射速度、浇注温度和铸型预热温度以及涂料。
1.压射压力。
镁合金压铸分热室压铸和冷室压铸两种形式。
目前热室压铸机正在向大型发展,锁型力为9300kN,设计可压铸最大件为6.4千克的大型热室压铸机已投入使用。
镁合金压铸工艺、安全操作要点

镁合金压铸工艺、安全操作要点1、压铸工艺镁合金的压铸工艺同其他合金的压铸工艺相似,但是由于镁合金的不同特性,在压力、速度、温度及涂料的应用上又有着不同的地方。
1.1压力镁合金压铸分热室和冷室两种形式,压铸时压力也不同,热室机的压射比压在40MPa左右,冷室机的比压要高于热室机,通常的比压在40-70MPa.另外重要的一点是增压建压时间,由于镁合金的凝固潜热低,镁合金在模具内的凝固时间要比铝合金的短的多,如果增压时间太晚的话,浇口和型腔的金属液已经凝固,增压也就失去意义.所以建压时间是衡量镁合金压铸机性能的一个重要因素,大部分压铸机的增压建压时间都在60ms以上,这时浇口的镁合金已经凝固,增压的压力无法传到模具型腔里面,优秀的压射系统建压时间通常在20ms以内.1.2速度镁合金由于密度小(只有铝合金的2/3),因而惯性小。
同时,由于镁合金的凝固也很快,要在金属凝固前充填整个型腔,因此,镁合金的压射速度要快。
热室镁合金的压射速度可达6m/s,冷室压铸机的速度要更高一些,达到8 m/s。
高的压射速度也产生高的浇口速度。
举例来说,锌合金和铝合金的压铸模浇口速度大约在40 m/s至60 m/s之间,否则可能出现模具烧蚀现象,薄壁镁合金铸件的浇口速度很多要超过80m/s,由于镁合金的低热性和对模具钢的低焊合性,对压铸模具的烧蚀也没有铝合金般严重。
1.3温度温度是压铸过程的热因素,为了提供良好的充填条件,保证压铸件的成型质量,控制和保持热稳定性,必须选用相应的温度规范,主要是指合金的浇注温度的模具温度。
热室压铸机的料壶在熔炉里面,压射时的热量损失小,因此,热室机压铸是镁合金的温度要低一些,通常在640℃左右。
冷室压铸机的温度要高一些,一般在680℃左右。
对于镁合金压铸有一点值得注意,就是如果产品的成型不太理想,可以从其它方面,比如压射速度、模具温度等方面改善,不可一味提高合金浇注温度,因为现在镁合金熔炉用的保护气体,在温度过高(超过710℃时)会失去效用。
镁合金压铸技术
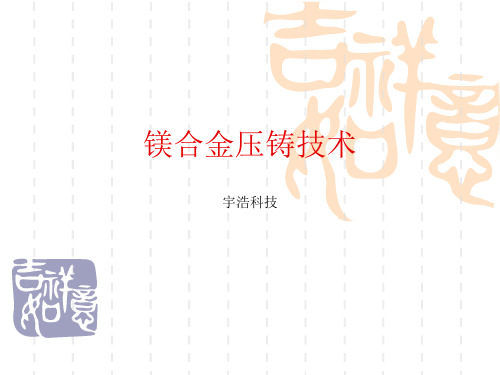
检查溢流位和排气
大小正确 排气孔打开 位于填充的末端 利用计算机模拟
常见缺陷的解决措施
3)缩水(从液体到固 体收缩4%-6%)
增加注射压力 检查锤头问题是否傅压 力降低(锤头或鹅颈磨 损) 增加问题点的入水
考虑在问题点可否使用 单独的水口
检查模具温度
加热冷点 冷却热点 检查动模和静模的温度 差异
检查金属的温度波动 使信件有方向的凝固
顶针顶出力不均匀
长度不一致 位置不正确
6.镁合金压铸的安全问题
Mg和氧及氧化物反应
燃烧/氧化 2Mg+O2=2MgO 液体镁合金中的水份迅速气化 Mg(液)+H2O(液)=H2O(气)+Mg(微小颗粒) 和水反应/氢气爆炸 Mg+H2O=MgO+H2 2H2+O2=2H2O 和氧化铁反应 3Mg+Fe2O3=3MgO+2Fe 和氧化硅反应 2Mg+SiO2=2MgO+Si
镁合金的主要性能
重量轻、强度好,比重只有钢的1/4,壁厚 可以比塑料更薄 良好的压铸性能 好的抗腐蚀性能 良好的减震性能 抗电磁波干扰性能 长模具寿命 优良的机械加工性能
2.镁合金压铸件的发展前景
镁合金材料1808年面世,1886年始用于工业生产。镁合 金压铸技术从1916年成功地将镁合金用于压铸件算起, 至今也经历了八十余年的发展。人类在认识和驾驭镁合 金及其制品的生产技术方面,经历了漫长的探索历程。 从1927年推出高强度MgAl9Zn1开始,镁合金的工业应用 获得了实质性的进展。1936年德国大众汽车公司开始用 压铸镁合金生产“甲壳虫”汽车的发动机传动系统零件, 1946年单车使用镁合金量达18kg左右。美国在1948~ 1962年间用热室压铸机生产的汽车用镁合金压铸件达数 百万件。
镁合金压铸零件的加工

镁合金压铸零件的加工镁合金密度较小,同等体积下比铝合金轻36%、比锌合金轻73%、比钢轻77%,被公认为是质量最小的结构金属材料,因此在航空航天产品上应用较多,在我们加工的产品中,就有部分镁合金压铸零件。
由于镁合金材料的机械性能与钢及铝合金有所不同,因此在加工过程中加工工艺、刀具、切削参数的选择也有区别。
因此,本文将对镁合金压铸零件的机械加工工艺及安全操作规程进行了概括性的介绍,以供参考。
1 镁合金的机械加工性能分析由于镁合金导热性好、切削力小,故在加工过程中的散热速度很快,因而刀具寿命长,粘刀量少,从而可以降低刀具费用。
因为镁合金易切削,其断屑性能十分良好,一般清况下只需经过一次精加工便可达到所要求的最终表面粗糙度。
同时由于镁的比热高、导热性良好,摩擦产生的热量会迅速地扩散到零件的各个部分,因此对镁合金进行切削加工时并不会产生较高的温度。
但是,在高切削速度和大进给量的情况下,零件所产生的热量也是相当高的,很可能因为温度过高而发生扭曲变形。
如果对成品零件的尺寸公差要求比较严格,则在设计中必须考虑到镁的热膨胀系数这一影响因素。
如果在上述加工条件下产生了相当多的热量,则很可能会影响到零件的加工精度。
镁的热膨胀系数略高于铝,明显高于钢。
在机械加工过程中,镁合金零件很少发生因为冷变形引起的扭曲变形或翘曲。
但刀具太钝、进给速度太慢以及刀具在加工过程中有停顿等不利因素时,也可能造成扭曲变形或翘曲。
2.刀具的选择加工钢和铝的刀具通常也适合于镁合金的加工。
但是,由于镁的切削力小,热容量也相当低,故其加工刀具应当具有较大的外后角、较大的走屑空隙、较少的刀刃数和较小的前角。
另外,保证刀具的各个表面很平滑也是十分重要的。
对镁合金进行机械加工的一条重要原则是,应当使刀具保持尽可能高的锋利和光滑程度,必须没有划伤、毛刺和卷刃。
如果刀具切削过其他金属,即使切削角没有改变,也应进行重新刃磨和晰磨。
3.切削液的选用由于镁的散热速度很快,可使被加工表面保持在较低的温度水平上,此外镁的易切削性使其不易与钢发生胶合,切削加工时一般不需要冷却液,但使用微小切削量时,要使用矿物油冷却液来降温。
镁合金制程详解

噴面漆 保護作用
面漆噴塗
1.按照標准參數表上要求把噴槍設定到預定參數. 2.把噴槍調到最佳噴塗狀態. 3.保証塗膜均勻到位.
流平
1.流平間溫度要適中﹐溫度太高和太低都會改變溶劑揮發 速度影響流平效果.
乾燥面漆 PU漆
二者選一 乾燥面漆 UV漆
面漆烘烤
1.按照標准參數表上要求把烤爐設定到規定溫度. 2.塗膜要烤干﹐否則會影響耐磨﹑硬度等性能測試.
射出機
機加主要生產制程
沖模
上下沖並含側沖
側沖滑塊
機加
機加
機加
簡介
• 化成這一製程主要是讓鎂鋁工件於表面上生成一層皮膜(氧化鎂) 主要用途有三: 1.可增加工件的耐蝕能力 2.增加成品防磁波的能力 3.增加與漆的密著度 此一製程約花70分鐘完成,每約隔十分鐘中會有新的一籠物料開始進行化成 化成處理可分為酪酸處理與非酪酸處理(磷酸鹽與釩酸鹽法,過錳酸鉀法)
二. 工藝流程
壓鑄成型
1) 2) 預熱:除去鎂合金水份,在密封狀態下不會因大量的水蒸氣而引起爆炸,適用于大件(電腦機 殼…),小件(手機前蓋…)不需要預熱 壓鑄成型:鎂合金高溫熔融﹐高壓鑄塑成型. 粗沖 –– 去毛邊﹑打孔 精沖(CNC銑床)–– 整形﹐銑凹槽 研磨 1) 磁力研磨 –– 優點:不會使產品變形 2) 震動研磨 –– 優點:產量大 3) 手工研磨 –– 沙紙打磨 刮刀 1) 手工用刀片刮除產品多余部分
制程特性
1) 2) 產品電鍍層均勻分布 防止產品導電
二. 工藝流程
產品表面清潔 去靜電
噴底漆
UV,透明無色,吸附VM
1.5H
烘烤底漆
噴中漆
烘烤中漆
上色
VM 真空鍍膜
電鍍
镁合金压铸技术

镁合金压铸技术发布日期:10-04-03 10:03:08 浏览人次:367向柱;汽门盖;方向盘;仪表板总成;灯罩底座..离合器箱体;歧管盖;轮毂;保险杠2摩托车类:曲轴箱;轮毂;汽缸罩;曲轴箱盖3自行车类:车架;前车架用镁合金AM60;AM50制成机车结构件和运动部件就可最大限度降低车的重量和能耗;提高整车加速制动性;降低行驶振动和噪声;提高驾驶舒适度..这些构件绝大多数用AM60; AM50经过压铸+微弧氧化即可使用电动工具;气动工具类外壳件对材料的设计要求1. 重量轻;刚性好;长期使用不变形2. 吸振性佳;耐冲击3.散热性佳4. 易成型易加工5. 符合环保总结:用AM60;AM50合金;压铸+烤漆镁合金特性化学性能合金的化学性能是它们在各种介质中与其它元素起化学反应的能力;主要是耐蚀性..① 机械性能合金的机械性能是指它抵抗外力作用而表现出来的特性;也称为力学性能;如强度;硬度;塑性;弹性;和冲击韧性;一般以抗拉强度;屈服强度;塑性;延伸率;断面收缩率;硬度来衡量和反映金属和合金的机械性能..② 工艺性能合金的工艺性能是指它们是否易于加工成形的性能;它包括:可铸性;可锻性;可焊性;切削加工性;电镀性和热处理性等..合金的铸造性:流动性;收缩性;热裂;铸造应力..偏析;吸气;杂质..a. 流动性:指合金液充填型腔的能力;影响因素:浇注温度;模具温度;压力;压射速度;铸件结构..b. 收缩性:合金从液态到凝固完毕直至常温过程中所产生的体积和尺寸的变化;总称为收缩;可分三个阶段:液态;收缩;凝固收缩和固态收缩..压铸件收缩的大小;主要取决于合金种类;化学成分;浇注温度;压射比压;持压及留模时间;模具温度及铸件结构等..c. 热裂:是指合金在高温状态形成的裂纹..影响因素:铸型阻力;铸件结构;浇注温度..d. 铸造应力:根据应力产生原因分热应力;相变应力和收缩应力..防止铸件产生裂纹或变形;除铸件结构设计合理即具有良好的压铸工艺性外;在压铸工艺上应采取妥善措施;使合金同时结晶凝固;并尽可能使铸件壁厚均匀..避免合金局部积聚;转折处避免尖角;选择合理的浇注系统和溢流系统;以减少铸件各部分的温度差..总的目的是减免铸造应力产生..e. 偏析:铸件化学成分不均匀的现象称为偏析..成分不一致势必会影响其机械及物理性能..f. 吸气:各种铸造有色合金都有吸收气体的特性;尤其在合金达到熔点时气体的溶解度剧烈增加..g. 气密性:合金的气密性是指铸件承受高压气体或液体的作用而不渗漏的能力;它通常反映着铸件内部的致密程度;一般规律是合金的凝固温度范围愈窄;铸件产生疏松的倾向愈小;因而气密性愈高..物理特性:机械特性:五、应用领域1、汽车零部件采用镁合金制造汽车零部件;可显着减轻汽车整车重量;而汽车所用燃料的60%消耗于汽车自重;车重每减轻10%;可节约燃料5.5%;因此;国外近年来镁合金在汽车制造中的应用逐步增长..但我国在这方面的开发刚刚起步..2、通讯器材如手机外壳、便携机外壳等3、高档建筑装饰材料由于镁合金的许多独特性能比铝合金更优越;因此国外出现了采用镁合金制造高档豪华型建筑装饰材料的趋势;国内一些镁合金生产厂家强烈要求开发镁合金型材的成型加工技术;国家科技部也希望尽快开发这方面的高新技术;并列为国家“十五”攻关项目..六、技术工艺路线工艺视不同产品略有区别;典型的镁合金压铸工艺流程如下图所示:七、热室压铸机和冷室压铸机压铸机是压铸生产的最基本的设备;是压铸生产中提供能源和选择最佳压铸工艺参数的条件;是实现高速高压压铸特点而获得压铸件的保证基础..压铸机分类及型号规格压铸机通常按压室的受热条件的不同分为冷室压铸机和热室压铸机两大类..冷室压铸机又因压室和模具放置的位置和方向不同分为卧式;立式和全立式三种..热室压铸机的主要特点是在压室和压射冲头浸在熔融金属液中.冷室压铸机的主要特点是压室内和压射冲头不浸在熔融的金属中;冷室压铸机的卧式最为常见压铸机基本结构压铸机的基本结构由以下八个部分组成:1.合模机构;2.压射机构;3.液压传动系统;4.控制、操纵系统;5.机座与油箱;6.顶出器及液压抽芯器;7.冷却、润滑系统;8.安全防护装置..合模机构压铸机的开合模机构称合模机构;是带动压铸模式的动模部分;使模具分或合拢的机构;同时这一机构还具有锁紧模具的功能..近年来;在合模机构上发展了合模安全装置;合模力量示装置;合模力自动调节等腰新装置..压射机构压铸机的压射机构是将熔融金属推送进模具型号腔填充成形为铸件的机构;压射过程的压力、速度等主要工艺参数都必须是由安而产生..现代压铸机的压射结构的主要特点是三级压射..也就是低速排除压射室中的气体;高速填充型腔机不间断地给出液态合金施以稳定的高压即两级速度一级增压..为实现三级压射的目的;对压射机构提出来出了如下的原则和要求:1.慢速压射速度应无级可调;2.快速压射速度应大于4米/秒镁合金机应大于6m/s;3.从慢速压射到快速压射的过渡转换距离应在30~50毫米以下;4.建压时间应低于30毫秒;5.压射及增压压力冲击峰值不应超过额定压力的30%;6.各压射工艺参数应能独立调节器节而互不干扰..液压传动系统压铸机的运行是由液压传动系统来进行的;液压传动系统由动力设备及管路网等构成;其主要组成部分如下:1.动力设备--------驱动电机、液压泵和贮能器等;2.压力控制器件-------溢流阀、卸压阀、减压阀、顺序阀以及压力继电器等;3.测量控制元件-------节流阀、调速阀、行程阀等;4.方向控制元件-------电磁换向阀、电液换向阀、手动换向阀;5.管路系统---------液压管道、油箱、油缸等;6.净化装置--------滤油器;7.冷却加热装置-------冷却器、加热器等;8.安全保护器件-------安全阀、压力继电器及温度控制器;9.传递介质-------压力油..控制、操纵系统压铸机的控制、操纵系统大都采用液压操纵与电器控制..其控制、操纵系统应能满足以下三个基本要求:1.保证压铸件的工艺规范得以顺利实施;2.机器及人身安全均有可靠的保证;3.操作方便、易于监视..压铸机的工作程序一般有:1.有点动调整程序 2.程序手动 3.半自动 4.全自动等..机座与油箱机座是整个压铸机的各种机构和系统的支承体、合模机构和压射机构通过拉力柱连成一个牢固的整体;并一同固定在机座上..油箱是压铸机工作液压力油存置的容器..现代的压铸机为减小机器的体积;将机座设计成箱体式;机座箱体内部即构成贮油的油箱..顶出器和液压抽芯器压铸机的合模机构上都附有顶出铸件的装置;这一装置称为顶出器..为了满足铸件特殊部位抽芯的需要;压铸机的动型板和定型板上都附有液压抽芯器;以供压铸模具设计液压压插芯之间..冷却、润滑系统压铸机上都设有冷却和润滑系统..冷却系统由冷却水管和回水管等组成;它的作用是输送、冷却水供压铸模、型板冷却之用;同时也供给液压油冷却器冷却之用..润滑系统由润滑油泵、油压表、输油管、电器元件等组成..其作用主要润滑曲肘机构中的回转副;减少摩擦..安全防护装置压铸机安全防护装置有:防护门、安全液压压力、滤油器堵塞、油温过高、报警等电气控制装置..压铸模压铸模式在生产中的作用..压铸模是压铸生产中的重要工艺装备;它对生产能否顺利进行;铸件质量的优劣合格率的高低、作业循环的快慢起着极为重要的作用..1.决定着铸件的形状和尺寸公差等级;2.其浇注系统特别是浇口位置决定了熔融金属的填充状况..3.溢流排气系统影响着熔融金属的溢渣排气条件..4.控制和调节压铸过程的热平衡..5.决定了铸件的表面质量及变形程度..6.模具的强度限制了压射比压的最大限度..7.影响生产效益..压铸模结构压铸模构成:压铸模式是由定模和动模两个主要部分组成的;定模与机器压射部分连接;并固定于其上;浇注系统压室内相通..动模则安装在机器的动模型板上;并随机器型板的移动而与定模式合拢或分开..八、压铸原理1.压铸概念熔融金属在高压高速下充填铸型;并在高压下结晶凝固形成铸件.特征:高速;高压.2. 金属填充型腔的流态介绍三种填充理论① 喷射填充填充分二个阶段:冲击阶段和涡流阶段a. 冲击阶段:在速度;压力保持不变的前提下;金属液进入内浇口后;仍保持着内浇口的截面形状;冲击到正对面的型壁处.b. 涡流阶段:向着内浇口反向填充这种理论比较适用于薄壁内浇口;高速填充的长方形铸件② 全壁厚填充理论由德国学者在1937年提出;内浇口厚度值取0.5~2mm; 内浇口与铸件的厚度比值为f/F 在0.1~0.6范围内.这种理论认: 金属液通过内浇口进入型腔后;即扩张到型壁;然后沿着整个型腔截面向前填充;直到整个型腔充满为止.③ 三阶段填充由英国学者1944年提出a. 第一阶段:液态金属射入型腔冲击型壁后;沿着型腔各方向扩展;在正常的传热条件下;与型腔壁面相接触的部位形成一层凝固层;亦即铸件的表面层.b. 第二阶段: 铸件表面成壳后;型腔继续受到液体金属的填充;凝固层逐渐增厚;此时合金的粘度亦增;而处于中心部位的液体金属;在第二阶段结束时;尚处于液态;除了继续得到液体金属的补充外;仍可承受来自压室的压射压力..c. 第三阶段: 金属液全部充满型腔;连同浇注系统及压室形成一个封闭的水力系统;在这个系统中各处的压力均等;压射力仍可通过尚未凝固的内浇口作用于铸件;达到进一步增压的目的..3. 金属液在不同条件下的流态分析① 不同厚度内浇口所出现的流态改变内浇口厚度与铸件厚度之比;除了影响填充的速度和时间外;也影响金属液在型腔内的流态..如下图:② 内浇口开在型腔一侧的流态金属液沿侧壁填充向前;到达顶端后包围;聚集;向反方向填充;聚集处有旋涡包气..③ 薄壁型腔填充流态金属流的厚度接近型腔的厚度;金属流入是的飘动;与型腔一侧或两侧相接触..④ 型腔转角处的流态金属液入型腔转角处会产生旋涡b⑤ 圆弧面处的流态注:1金属液 2包气4. 压铸过程中的主要参数说明5. 压铸过程中的主要参数说明1起始阶段金属液浇入压室;2345一般希望在系统压力建立以后立即增压;以便达到紧实铸件;压缩消除内部气孔和缩孔的目的;增压时间T4一般在0.01~0.03秒范围内为佳;增压延时t2过长或增压建立时间t3太长都会造成整个增压时间T4延长;这对铸件的质量十分不利..冲头行程;各行程压力;各行程时间等解说6. 压铸件的检验检验项目:① 尺寸与形状② 合金成分③ 表面质量④ 内部质量⑤ 渗漏九、研磨研磨目的:为化成;烤漆作准备;包括去除毛刺;打圆角;清洗油污;表面抛光..一. 研磨内容:①毛刺;毛边去除②表面抛光③喷砂1. 毛刺;毛边去除方式:人工;机床冲切;喷砂;振动研磨人工去除要注意:锉刀目数及大小选用顺序2. 抛光分:人工打磨和震动研磨人工打磨的效果较好二. 震动研磨工艺1. 工艺内容:震动速度;振幅;振动时间;磨石种类;磨石粗幼磨石形状;工件和磨石比例;磨液..2. 研磨机分类:① 标准圆型:工件易相互碰撞② 桶型:适合大件及较长件此机振动强度大;要防止变形③ 离心型:适合小件工件少碰撞3. 磨石分类:棕刚玉;石英砂;高铝瓷;氧化铝粗幼:棕刚玉石英砂150目;高铝瓷800目;氧化铝1000目形状:磨石形状的选择与工件形状有关4. 工件和磨石比例:工件和磨石混合比例对效率有极大影响磨石若太多;会引起工件碰撞;其比例应参考以下因素:① 工件原料:如:软质材料……少量工件② 需要效果:如:抛光效果……少量工件③ 工件形状:如:是否会在工序中互相缠绕……少量工件④ 工件重量;尺寸以下是由重量所计算出的比例;只作为参考:每100升容量的溶液可处理工件4. 磨液① 功能:a.石和工件之间有一层液体作界面;以面磨石粉屑附在工件上b.水溶性液体可以软化硬水;清洁磨石和工件;工件抛光;防腐蚀及除锈等② 磨液选择遵循:a. 清洁磨石;工件表面.b.抑制工件氧化c.可循环使用③ 磨液浓度:每100公升容量的水 10公斤/小时的流量5. 时间:一般30分钟延长时间可令抛光和磨毛边效果改善;但会增加成本和工件碰伤的机会..三. 镁合金件表面喷砂1. 喷砂原理:将加速的磨料颗粒向金属表面撞击而达到除锈;去毛刺;去氧化层或作表面处理;改变金属表面光洁度和应力状态;及表面附着力2. 工艺因素:磨料种类;磨料颗粒;喷射距离;喷射角度及速度喷枪与工件距离150~200mm;处理直径范围30mm① 磨料分固体和流体两种..固体又分两种:金属黑色金属及有色金属非金属矿物与有机合成类镁合金件的喷砂磨料选铝丸;玻璃丸;陶瓷砂及氧化铝型腔材料尽可能不用钢板;用聚安只脂或橡胶内衫;避免产生静电或火花..十、表面处理和涂装一.镁合金制品的前处理工程为实现防护与装饰的目的;涂装作为一种重要的表面处理手段镁合金的表面处理主要有化学氧化;阳极氧化;皮膜化成;电镀;化学镀;涂装等方法;广泛地应用于镁合金制品的加工制作过程..但因镁合金活性高;容易腐蚀;涂装的化成处理工程及其后喷漆工程中的涂料选择有较大的难度..目前德国的BONDER公司及日本的帕卡在前处理方面做的较好;日本的久保孝公司和日本油脂公司在涂料领域做得较好..下面以成熟的Gr系化成为例浅谈镁合金的化成处理过程..A.镁合金化成处理工艺流程B.各工程的作用预脱脂/脱脂:利用皂化反应和乳化作用;浸润清理制品表面的加工油;周转过程造成的脏污;打磨未清理干净的离型剂热水/冷水洗:清理工件表面的油污转化物化学反应使不溶性的油脂转化为亲水物质..表调:活化制品表面;清除前工程未清理干净的油污及离型剂;清除工件表面的氧化物化成:形成化成皮膜;提高制品的防护性能;皮膜疏松多孔;可作为良好的涂层基底;纯水洗:消除制品表面的电解质离子;提高制品涂镀层的防护性..C.化成皮膜的性能要求及测试方法1.耐盐雾性能JIS9级以上→盐雾实验机2.阻抗0.3~0.6→阻抗测试仪D.化成工程中常见的问题点及解决对策常见问题点:1.耐盐雾性能差2.阻抗太高3.外观发花或结晶粗糙解决对策:分析槽液参数;调整到合理的工艺范围内二.镁合金制品的涂装工程从经验的角度来开;镁合金制品涂装的成功与否;和选择的涂料有较大的关系..底漆离型剂耐性好;和底材附着力好是最重要的条件..此外;面漆重涂性的好坏rework不会影响附着力也是一个较为重要的条件..A.镁合金涂装处理工艺流程B.涂装各工程的作用遮蔽: 产品局部导电区域及装配boss的保护底漆:填平素材表面的轻微缺陷;提高产品的耐腐蚀性;二底:找平;填补缺陷;提高涂层的外观装饰性;刮灰:消除漆面缺陷;提高涂层的外观装饰性研磨:消除漆面缺陷;提高层间附着力;面漆:赋予产品清新亮丽的外观;增进销售;装饰与防护B.镁合金产品的涂装性能要求及测试方法涂层性能要求:1.光泽 2.色差 3. 附着力 4.硬度 5. 耐磨耗 6.耐酒精7.耐人工汗 8.高温高湿测试方法:光泽计色差计附着力测试仪硬度计磨耗测试仪器高温高湿实验机C.涂装工程常见的品质问题及改善对策1.杂质工件清洁不干净;喷房环境差改善对策:A..加强打磨后的除尘工作B..加强上挂前的静电除尘作业2.油点空气过滤不好;涂料施工粘度偏低;裸手作业改善对策:A..涂装的整个流程严禁裸手触摸工件;B..检查油水分离系统的作业状态;以确保状态良好C..依据环境温度适当的调整施工粘度3.积漆堆漆治具欠合理;治具未按规定要求更换或清理改善对策:合理设计治具;严格遵守治具的更换周期4.过磨打磨本工程或前工程不当造成;改善打磨的方法5.刀痕素材研磨;机械加工等工程造成..改善对策:加强来料检验;避免人工及材料的浪费;知会前工程并敦促其改善从同业的经验来看;镁合金产品涂的涂装较为困难一次直通率不大于70%..除本工程的问题外;其他工程对涂装产生的影响也很多;如机械加工的过切;素材研磨的过磨;压铸工程的冷裂纹;缩陷;针孔等;而这些问题涂装工程是无能为力的..因此;只有压铸;机加;素材研磨;化成烤漆等工程共同努力;才能将镁合金产品做好..四、表面处理转化技术化学转化膜:金属表面与溶液界面发生化学反应或电化反应形成的薄膜;其特点是与底材结合良好;膜层薄、结晶细腻;拥有一定的孔隙;可与薄膜形成良好的结合..按膜的主要组成物的类型..化学转化膜可分为:氧化物膜;铬酸盐膜;磷酸盐膜和草酸盐膜等不同类别..化学转化膜作为金属制件防护层;其防护功能是依靠降低金属本身的化学活性;以提高它在环境介质中的热力学稳定性..化学转化膜的防护功效取决于下面的因素:① 受转化金属的本性..②膜的类型;组成和结构..③ 膜的性能同基底金属的结合强度;孔隙率等④ 环境条件电化学氧化阳极氧化:铝和铝合金在相应的电解液和特定的工艺条件下;施加外加电流;在其表面上形成一层氧化膜的过程..阳极化膜的厚度约为3—15丝;经硫酸阳极化处理后零件尺寸稍有增大..零件表面粗糙度也稍受影响;如果阳极化前进行抛光处理;可以得到弥补..阳极化膜层多孔;孔隙率约为35%..为了提高阳极化膜层的耐蚀性;可以采用下述方法进行封闭处理;可提高耐蚀性..① 沸水封闭:阳极化后;即进入90—98℃水中进行封闭处理;可提高耐蚀性..② 高压:蒸汽封闭;与热水封闭效果相当..③ 重铬酸盐封闭;由于膜孔中吸附了铬酸盐;具有缓蚀作用;进一步提高了耐蚀性..④ 二次封闭;用含有镍盐或钴盐的重铬酸盐封闭后;再浸封聚合物;使阳极化膜具有极高的抗腐蚀能力..第二次封闭时所使用的封闭工艺不同;膜层耐腐蚀能力也不尽相同;用某些聚合物封闭后;阳极化膜的耐腐蚀性比单独重铬酸盐封闭的高几倍..铬酸氧化膜不透明;为浅灰色或乳白色;氧化膜厚度只有2—5丝;膜层软、弹性好、松孔率低、不易染色;经过铬酸阳极化的制件能保持原来的精度和表面粗糙度..氧化膜与基体有很好的结合力;但膜性脆;并随膜层厚度的增加而脆性加大;因此经硬质阳极化处理的铝合金零件;不能承受冲击、弯曲和变形..而且膜层超过一定厚度时;会使合金的疲劳强度降低..因此;承受疲劳载荷的零件采用阳极化处理时应十分慎重..微弧氧化是零件在电解质水溶液中;置于阳极;利用电化学方法使铝、镁、钛、钽、镐或铌等材料的表面微孔中产生火花或微弧放电;在金属表面生成陶瓷膜层的表面该性处理技术..优点:①耐蚀性能高;承受5%盐雾实验的耐蚀能力在1000h以上..②硬度高、耐磨性好③电绝缘性能好④外观装饰性能好镁合金的阳极化镁合金的阳极化除对基体具有一定的防护作用外;而且是油漆的良好低层;经阳极化得到的转化膜;其耐蚀性、耐磨性和硬度一般都比化学法所得者高..其缺点是对复杂的制件难以得到均匀的膜层;膜的脆性较大..镁合金既可在酸性也可在碱性溶液中进行阳极化;镁合金在只含苛性碱的溶液中是十分容易阳极化成膜的;膜的主要组成为氢氧化镁;但膜层结构疏松;同基底金属的结合力和防护性能都十分差;所以要在电解液中添加碳酸盐、硼酸盐、硅酸盐、磷酸盐和氟化物以及某些有机物..其中;以氟化物为添加物的电解液已取得实际应用..镁合金阳极化所用的酸性溶液由铬酸盐、磷酸盐和氟化物等无机盐组成;所得的阳极化膜含有这些盐的酸根;其对应的镁盐在酸性介质中均相应稳定..十一压铸件的缺陷分析及检验16.1缺陷分类及产生原因:1 几何缺陷:压铸件形状、尺寸与技术要求有偏离;尺寸超差、扰曲、变形等..2 表面缺陷:压铸件外观不良;出现花纹、流痕、冷隔、斑点、缺肉、毛刺、飞边..3 内部缺陷:气孔、缩孔、缩松、裂纹、夹杂等;内部组织、机械性能不符要求..A:产生原因及影响因素1 压铸机引起:压铸机性能;所提供的能量能否满足所需要的压射条件:压射力、压射速度..锁模力是否足够..压铸工艺参数选择及调控是否合适;包括压力、速度、时间、冲头行程等..2 压铸模引起:A:模具设计:模具结构、浇口尺寸及位置、排溢系统及位置、顶杆及布局、冷却系统..B:模具加工:模具表面粗糙度;加工精度、硬度..C:模具使用:温度控制、表面清理、保养..3 压铸件设计引起:压铸件壁厚、弯角位、拔模斜度、热节位、深凹位等..4 压铸操作引起:合金浇注温度、熔炼温度、涂料及喷涂量、生产周期..5 合金料引起:原材料及回炉的成分、干净程度、配比;熔炼工艺等..以上任何一个因素的不正确;都有可能导致缺陷的产生..常见缺陷分析1表面缺陷2内部缺陷4解决缺陷的思路由于每一种缺陷的产生原因来自多个不同的影响因素;因此在实际生产中要解决问题;面对众多原因到底是先调机还是先换料或先修改模具建议按难易程度;先简后复杂去处理;其次序:。
镁合金的压铸方法及压铸制品与制作流程

本技术将使用冷室式压铸机的情况下为了达成薄壁化所需的注射条件、金属模条件、镁合金的熔化条件、冷室式压铸机的浇口部的镁合金的熔液温度及金属熔液保温锅中的金属熔液温度与浇口部的金属熔液温度之差的条件、以及金属模的模腔侧内面的涂层的条件加以特定化,便可使用在以往技术中被视为不适合于镁合金的薄壁铸造,但却具高注射能力的冷室式压铸机来制造高品质薄壁铸造品,尤其是,即使具有如同笔记本型个人电脑的框体般的大面积者,也可铸造出在以往技术中是困难的制品最小壁厚1.5mm以下,较理想为1.2mm以下的压铸制品。
技术要求1.一种镁合金的压铸方法,它是使用冷室式压铸机从镁合金铸造制品最小壁厚为1.5mm以下,且无铸件皱纹、表面裂纹、填充不良、金属模粘砂的压铸制品的方法,其特征在于,a)将镁合金的熔液温度保持在650至750℃;b)将向模腔的填充速度设定为1/100至10/100秒钟;且c)将填充后的增压设定为200kgf/cm2以上。
2.一种镁合金的压铸方法,它是使用冷室式压铸机从镁合金铸造制品最小壁厚为1.5mm以下,且无铸件皱纹、表面裂纹、填充不良、金属模粘砂的压铸制品的方法,其特征在于,d)将金属模温度保持在150~350℃;e)使容易在压铸铸造器上造成缩裂的模腔部位的金属模表面温度较的周边部降低10K以上;f)将压铸铸造时的金属模内的空气压力设定为100mmHg以下;且g)作为对涂布于金属模内面的脱模剂的添加剂,使用选自由石墨、氮化硼(BN)、水玻璃、云母、硅胶、氢氧化镁及氧化镁组成的组中的至少一种。
3.一种镁合金的压铸方法,它是使用冷室式压铸机从镁合金铸造制品最小壁厚为1.5mm以下,且无铸件皱纹、表面裂纹、填充不良、金属模粘砂的压铸制品的方法,其特征在于,h)使用在镁合金熔液的表面形成有防止燃烧、氧化的保护气氛的密闭式熔化炉;且i)从距该镁合金熔液的表面100mm以上的位置,吸出该镁合金熔液,借此抑制镁合金熔液的氧化,改善流动性,并抑制氧化物的混入及铸件皱纹的发生。
镁合金生产制程管制重点
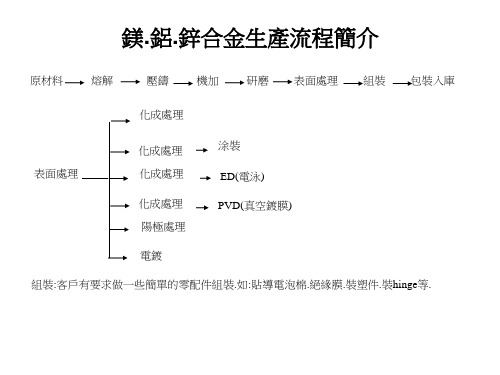
此種裂紋發生部位在產品的結構變化較大的部位,如肉厚不均. 冷卻收縮力 均的rib.boss根部.也有發生在模具局部溫度變化大的部位.
b.受出模力.拉模力產生的裂紋
一般是在產品的結構較復雜.模具頂出力不均衡,有拉模現象的受力部位.
c.受后制程外力影響產生的裂紋 在去除gate.overflow.校形過程中,也會產生裂紋.需要在SIP中指出這些可 能產生裂紋的部位,作為檢查重點.
標示*記號的檢驗頻率一 般不需要設定的.除非產品 有特殊性的要求. 如:1.制 程穩定性差,難以保障. 2.客戶在圖面有重點要求
8.外觀
鎂.鋁.鋅合金生產制程管制重點
二.機加段制程管控重點. 1.機加孔尺寸(孔徑.孔深.孔位) 2.機加卡勾尺寸(位置.深度) 3.偷肉尺寸(長.寬.深.形狀) 4.螺紋孔的扭力測試 5.去除gate/overflow及搭橋等機加工尺寸(形狀.殘留量的控制) 6.外觀
機加段制程管控重點
F.外觀檢查 針對機加後的產品外觀,原則上凡是刀具加工過的部位都要比對工程樣品來 管制.確認有無異常變化發生.工程樣品須在機加動過刀的部位用色筆標示 出來. 在SIP上.要突出重點管制以下幾點:
1.卡勾處有無裂紋.
2.螺紋孔內有無切屑殘留,有無砂孔 3.偷肉處的背面,有無影響到外觀品質的凸起.印痕.
化成段制程管控重點
D.平面度. 1.化成制程有烘烤作業.產品會出現應力釋放而變形. 2.前段來料本身就有變形,流到化成段來做最終校形作業. 3.若是產品以化成品方式出貨,則須管控平面度.若是還要進行涂裝后制 程作業,一般是不要管制平面度.除非化成段的變形已嚴重影響了涂裝 后的校形作業. E.外觀檢查 1).化成品外觀不良主要是以下几種: 1.氧化腐蝕 2.殘留白灰 /黑灰 3.殘留毛邊 4.裂紋 5.斷柱 6.缺料 7.變形 8.充填不良 9.露底材.
压铸制程简介
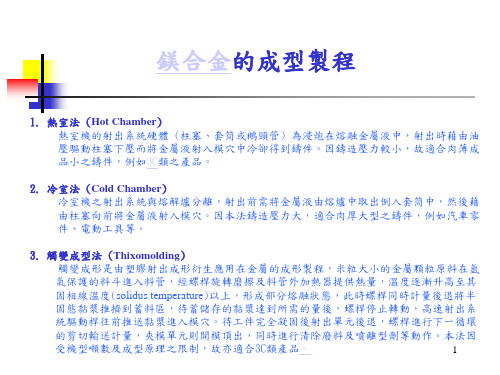
1. 熱室法 (Hot Chamber) 熱室機的射出系統硬體 (柱塞、套筒或鵝頸管) 為浸炮在熔融金屬液中,射出時藉由油 壓驅動柱塞下壓而將金屬液射入模穴中冷卻得到鑄件。因鑄造壓力較小,故適合肉薄成 品小之鑄件,例如3C類之產品。
2. 冷室法 (Cold Chamber) 冷室機之射出系統與熔解爐分離,射出前需將金屬液由熔爐中取出倒入套筒中,然後藉 由柱塞向前將金屬液射入模穴。因本法鑄造壓力大,適合肉厚大型之鑄件,例如汽車零 件、電動工具等。
4
5
壓鑄概論
❖ 壓力鑄造概念: (鋁,錫,鋅,镁,鉛,銅,合金) 即將溶融合金在高壓,高速條件下充型並在高壓下冷卻凝固成型的一 種精密鑄造方法, 簡稱壓鑄,其最終產品是壓鑄件.
❖ 壓力鑄造特性: 1. 高速充填:通常澆口速度達30~60m/s之間. 2. 充填時間很短:中小型件通常為0.02~0.2s之間. 3. 高壓充填:熱室機壓力通常為70~350kg/c㎡ 4. 溶湯的冷卻速度快
25
12.產品後工程量產性評估難易度,工時…..
15
成型工藝
(一)壁厚
最大壁厚與最小壁厚之比不要大于3﹕1(應設計壁厚均勻﹐保証足夠強度與剛度的前提)
(二)加強肋,大于或等于2.5MM﹐會降低抗拉強度﹐易產生氣孔﹐縮孔。
設計原則﹕1﹐受力大﹐減小壁厚﹐改善強度.
2﹐對稱布置﹐壁厚均勻﹐避免縮孔氣孔.
3﹐與料流方向一致﹐避免亂流.
統驅動桿往前推送黏漿進入模穴。待工件完全凝固後射出單元後退,螺桿進行下一循環
的剪切輸送計量,夾模單元則開模頂出,同時進行清除廢料及噴離型劑等動作。本法因
受機型噸數及成型原理之限制,故亦適合3C類產品。
1
熱室法 (Hot Chamber)
镁合金壳体压铸件生产工艺流程
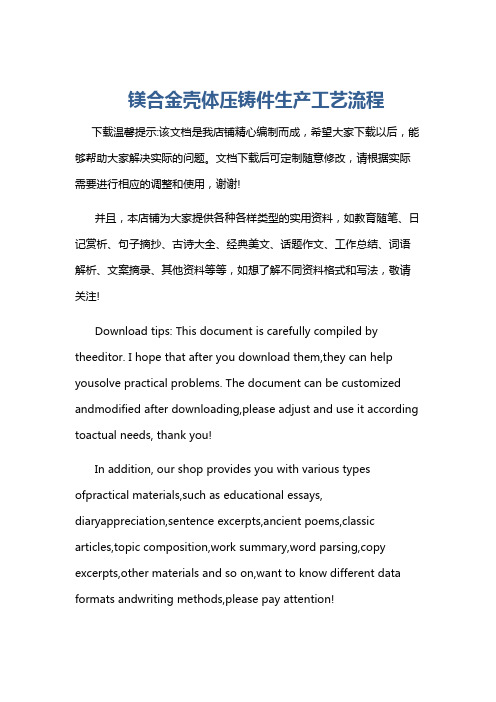
镁合金壳体压铸件生产工艺流程下载温馨提示:该文档是我店铺精心编制而成,希望大家下载以后,能够帮助大家解决实际的问题。
文档下载后可定制随意修改,请根据实际需要进行相应的调整和使用,谢谢!并且,本店铺为大家提供各种各样类型的实用资料,如教育随笔、日记赏析、句子摘抄、古诗大全、经典美文、话题作文、工作总结、词语解析、文案摘录、其他资料等等,如想了解不同资料格式和写法,敬请关注!Download tips: This document is carefully compiled by theeditor. I hope that after you download them,they can help yousolve practical problems. The document can be customized andmodified after downloading,please adjust and use it according toactual needs, thank you!In addition, our shop provides you with various types ofpractical materials,such as educational essays, diaryappreciation,sentence excerpts,ancient poems,classic articles,topic composition,work summary,word parsing,copy excerpts,other materials and so on,want to know different data formats andwriting methods,please pay attention!镁合金壳体压铸件生产工艺流程镁合金壳体压铸件是一种常见的轻量化材料,广泛应用于汽车、电子、航空航天等领域。
镁合金压铸成型

环保与可持续发展
环保材料的应用
为了满足日益严格的环保要求,镁合金作为一种可再生资源,其 应用越来越广泛,有助于减少对有限金属资源的依赖。
节能减排技术
在镁合金压铸成型过程中,通过采用先进的节能技术和减排措施, 降低能耗和减少环境污染。
循环经济与资源回收
发展循环经济,推动镁合金废料的回收和再利用,实现可持续发展。
THANK YOU
感谢聆听
06
实际应用案例分析
汽车制造业中的应用
镁合金压铸成型在汽车制造业 中广泛应用于发动机、变速器 等零部件的制造。
由于镁合金具有轻量化、高强 度、高刚性等特点,使用镁合 金压铸成型能够显著降低汽车 重量,提高燃油经济性和动力 性能。
镁合金压铸成型还具有生产效 率高、成本低等优势,因此在 汽车制造业中具有广阔的应用 前景。
随着科技的不断进步,镁合金压铸成型技术也在不断创新,如研究 开发出高能效、高精度的压铸设备,提高生产效率和产品质量。
模具设计与制造技术
模具是压铸成型的关键,通过优化模具设计和制造技术,可以提升 镁合金压铸件的精度和表面质量,满足更高端产品的需求。
自动化与智能化生产
随着工业4.0的推进,镁合金压铸成型将逐步实现自动化和智能化生 产,提高生产效率和降低人工成本。
电子产品外壳制造中的应用
02
01
03
随着电子产品向轻薄化、小型化方向发展,镁合金压 铸成型在电子产品外壳制造中越来越受到青睐。
镁合金具有良好的电磁屏蔽性能和散热性能,能够满 足电子产品对外观、性能和轻量化的要求。
通过镁合金压铸成型,可以快速、高效地生产出高品 质的电子产品外壳,提高产品市场竞争力。
镁合金压铸成型
目
镁合金压铸工艺流程

镁合金压铸工艺流程镁合金压铸工艺流程:镁合金压铸工艺是一种将镁合金熔液注入压铸模具中,通过压力使熔液在模具中凝固得到产品的加工过程。
以下是一般的镁合金压铸工艺流程。
第一步:材料准备。
首先需要准备好所需的镁合金材料,通常镁合金是由镁及其合金元素组成的。
然后将镁合金材料加热至熔点,并将熔液进行过滤以去除杂质和气泡。
第二步:模具准备。
根据产品的形状和尺寸要求,制作相应的压铸模具。
模具通常由两部分组成,上模和下模。
上模和下模分别有对应的镂空内腔,当两个模具合上时,内腔形成一个封闭的空间用于注入熔液。
第三步:注入熔液。
将熔液倒入特定的容器中,通过铸造设备将熔液注入模具的内腔中。
注入时要注意控制好注入速度和温度,以确保熔液填充整个空腔并均匀凝固。
第四步:压力施加。
当熔液注入完毕后,立即关闭注液口,并通过液压系统给模具施加一定的压力。
施加压力的目的是让熔液充分填充模具中的细小空隙,并加快凝固速度。
第五步:冷却和固化。
施加压力后,开始进行冷却。
通过冷却系统降低模具和熔液的温度,使熔液逐渐凝固并固化。
冷却时间的长短取决于材料的性质和产品的要求。
第六步:模具打开。
当熔液完全凝固后,打开模具,取出凝固成型的镁合金制品。
此时的制品已经具备了产品形状和尺寸的特征。
第七步:后处理。
取出的镁合金制品还需要进行后处理。
例如去除余温、修边、除去表面氧化、进行热处理等,以增强产品的性能和表面质量。
第八步:检验和质量控制。
对制品进行检验,包括外观检查、尺寸检查、力学性能测试等。
根据产品的使用要求,制定相应的质量控制标准,并做好相应记录和追踪。
以上是一般的镁合金压铸工艺流程,具体工艺流程会因产品形状、尺寸和要求的不同而有所调整。
通过良好的工艺流程控制和质量管理,能够制造出质量稳定、性能优良的镁合金制品。
- 1、下载文档前请自行甄别文档内容的完整性,平台不提供额外的编辑、内容补充、找答案等附加服务。
- 2、"仅部分预览"的文档,不可在线预览部分如存在完整性等问题,可反馈申请退款(可完整预览的文档不适用该条件!)。
- 3、如文档侵犯您的权益,请联系客服反馈,我们会尽快为您处理(人工客服工作时间:9:00-18:30)。
铸造 温度 ℃ 625~700 650~695 660~695
比热
热膨胀 热传导 系数 系数
电阻 Ωcm 14.1 12.5 N/A
导电 系数 Ms/m 6.6 N/A N/A
浦松比 mm/m 0.35 0.35 0.35
unit AZ91D AM60B AS41B
J/kg℃ m/m*K w/m*K 1.05 1.05 1.02 25.0 25.6 26.1 72 62 68
• 模具
分流子 母模
压铸模具 (cold chamber)
浇口套 公模
• 制品
压铸制品 (cold chamber)
溢流井
汤柄
溢料井
浇道
1.2 机械加工
• 工序
机械加工流程表
取件 放置定位 治具固定 刀具加工
清洗烘干
滤净
取出
治具放松
• 设备
加工机台基本数据 LxWxH : 2295x1400x2156mm 工作空间 : X/Y/Z – 510/360/250 刀具数量 : 10 pcs.
• 治具(一)
固定前
固定后
真空式夹具
固定前 反向夹具
固定后
• 治具(二)
固定前 立式夹具
固定后
治具基本结构说明
气动夹钳
真空吸盘
治具基座
刀具检出器
• 制品
机械加工图示
1.3 毛边研磨
• 工序
毛边研磨处理流程表
冲模下料 毛边清除 (人工) 喷砂 烘干
• 设备(一)
精密冲模
气动工具
• 设备(二)
2.3 合金与塑料性质比较
压铸合金与塑料之机械与物理性质比较表
物理性质 机械性质 熔点 ℃ 595 抗拉 强度 MPa 230 降伏 强度 MPa 160 154 比强度 扬氏 系数 GPa 45
材料名称
unit 镁合金
(AZ91D)
密度 g/cm3 1.81
热传导 伸长率 热膨胀 系数 系数 % 3
New Technology 镁合金技朮介绍
镁合金成型方式(Thixomolding) Magnesium die casting Magnesium processes Thixomolding®
Safe process; solid to solid Very good heat management Slow shot speed Expensive equipment Expensive raw material Long cycle t品
试验线
化成后
化成后
铬酸钙系
化成前
铬酸锰系
化成前
•工序
制品涂装流程表
底漆(I) 研磨补土 底漆(II) 研磨补土
检查包装
( 印刷 )
面漆
• 设备
2. 镁合金产品介绍
2.1 镁材料特性比较
常用鎂合金化學成份表
化學成份 合金種類
Al
8.3~9.7 5.5~6.5 3.5~5.0
硬度 BHN 75 62 75
扬氏 系数 GPa 45 45 45
潜热 KJ/Kg 373 373 373
unit AZ91D AM60B AS41B
常用镁合金之 物理特性
物理 性质 材料 名称
密度 g/cm3 1.81 1.79 1.77
凝固点 ℃ 470 540 565
熔点 ℃ 595 615 620
• 镁合金基本制程介绍 • 镁合金产品简介
1.镁合金基本制造流程
压铸工程 机械加工 毛边研磨 涂装工程 化成处理
a.压铸生产段 镁锭预热﹑熔解炉加热﹑保护气体调整﹑给汤及取料机械手设定﹑ 离型剂喷洒系统调整﹑模温机设定﹑机台生产条件设定﹑铸件生 产﹑铸件冷却装置﹑整缘冲剪毛头﹑自动输送设备﹑废料回收﹒ b.机械加工及毛边处理段 切削液选用﹑加工机(钻搪铣攻)修整﹑人工修饰﹑ 抛光研磨﹑防爆集尘﹑包装﹑半成品仓储﹒ c.表面化成处理段 溶剂脱脂→碱性脱脂→温水清洗→水洗→酸处理→ 纯水清洗→化成(铬酸)处理→纯水清洗→干燥﹒ d.涂装处理段 补土→干燥→补土修润→底漆→干燥→修润→ 面漆→干燥→包装→仓储→出货﹒
•3C制品(二)
• 3C制品(三)
•汽机车工业零组件
传动组件外盖、汽缸头盖、离合器、方向盘 、煞车踏板架 、仪表面板和座椅支架组合等
•自行车零组件
前叉、车后架、水壶架、曲柄
•手动工具、航天工业、 家电产品、医疗及运动器材
The End
Mn
0.15~0.50 0.24~0.6 0.35~0.7
Zn
0.35~1.0 0.22 max 0.12 max
Si
0.1 max 0.1 max 0.5~1.5
Cu
Ni
Fe
others
0.02 0.02 0.02
AZ91D AM60B AS41B
0.03 max 0.002 max 0.005 max 0.01 max 0.002 max 0.005 max 0.02 max 0.002 max 0.0035 max
• 工序
压铸制程制造流程表
镁锭预热 投料 熔解 给汤 压铸
闭模
离型剂涂布
取出
开模
冷却
• 设备(一)
压铸设备及周边设施 (cold chamber)
压铸机台 机械臂
cold chamber : 500t ~ 650t hot chamber : 150t
熔解炉 预热炉
• 设备(二)
冷热式机台说明
New Technology 镁合金技朮介绍 镁合金成型方式(热室)
Magnesium die casting Magnesium processes Hot chamber die casting
Short metal flow Good temperature management Low shot speed High maintenance costs Attention to gas heating Short cycle time
震动研磨机
圆盘式
卧式
干燥烤炉
• 制品(一)
冲模下料前后比较
冲模下料前后比较
研磨前
研磨后
• 制品(二)
研磨前后比较
研磨前后比较
研磨前后比较
研磨前后比较
1.4 化成处理
• 工序
化成处理流程表
脱脂 水洗 x 2 酸洗 水洗 x 2
纯水洗
水洗 x 2
化成
• 设备
化成槽 化成液
化成处理自动线(铬酸钙系)
1.1 压铸工程
• 镁锭
ASTM(美国材料试验所) B275合金命名规则:
主要合金 成份Al(铝)
AZ91D
次要合金 成份Zn(锌)
A:第一种标准成份 B:第一种标准成份 C:第一种标准成份 D:高纯度合金 E:高抗蚀性合金 X1:未登记之合金
主要合金成份 含量Al占9%
次要合金 成份含量Zn占1%
K m/m° K w/ m°
25.0
72
铝合金
(A380)
2.7
3
23.9
145
593
331
165
147
71
锌合金
(AG40A)
6.7
10
27.4
214
387
283
N/A
82
85
塑料 (PC+ABS)
1.07
16.5
76.5
0.28
260
39
16.5
102
2.1
•3C信息电子产品之外壳及零组件
笔记本电脑、数字相机、数字摄影机、MD、 LCD显示器、移动电话、PDA、TV、VCD、 DVD、PDP等之外壳及其结构零组件
單位:%
特性介绍: AZ91-机械性质及铸造性极佳 AM60-延性及冲击强度佳 AS41-高温强度及抗潜变能力优
2.2镁合金机械及物性说明
常用镁合金之 机械特性
机 械 性 质 材料 名 称
抗拉 降伏 压降伏 剪强度 疲劳 冲击 伸长率 强度 强度 强度 强度 强度 (51mm) MPa 230 220 215 MPa 160 120 140 MPa 165 130 140 MPa 140 N/A N/A MPa 70 70 N/A J 2.2 6.1 4.1 % 3 6~8 6
New Technology 镁合金技朮介绍 镁合金成型方式(冷室)
Magnesium die casting Magnesium processes Cold chamber die casting High shot speed Heat management takes attention Short cycle time Low maintanance costs Process flexibility Shot curve flexibility