运营管理-史蒂文森stevenson(各章课后习题答案)
《运营管理》课后习题答案

Chapter 02 — Competitiveness, Strategy, and Productivity3. (1) (2) (3) (4) (5)(6)(7)Week Output WorkerCost@$12x40OverheadCost @1。
5MaterialCost@$6TotalCostMFP(2)÷(6)1 30,000 2,880 4,320 2,700 9,900 3。
032 33,600 3,360 5,040 2,820 11,220 2。
993 32,200 3,360 5,040 2,760 11,160 2。
894 35,400 3,840 5,760 2,880 12,480 2.84*refer to solved problem #2Multifactor productivity dropped steadily from a high of 3。
03 to about 2.84.4。
a。
Before:80 ÷ 5 = 16 carts per worker per hour.After:84 ÷ 4 = 21 carts per worker per hour。
b。
Before:($10 x 5 = $50)+ $40 = $90;hence 80 ÷ $90 = 。
89 carts/$1。
After: ($10 x 4 = $40)+ $50 = $90;hence 84 ÷ $90 = .93 carts/$1。
c. Labor productivity increased by 31.25% ((21-16)/16).Multifactor productivity increased by 4。
5% ((。
93—。
89)/.89).*Machine ProductivityBefore: 80 ÷ 40 = 2 carts/$1.After:84 ÷ 50 = 1.68 carts/$1。
运营管理课后习题答案

学习-----好资料Chapter 02 - Competitiveness, Strategy, and Productivity3. (1) (2) (3) (4) (5) (6) (7)Overhead Material Total MFP WorkerCost Week Cost @1.5 Cost@ Output Cost@$6 (6) ?(2)$12x401 9,900 3.03 30,000 2,700 4,320 2,88011,220 3,360 2 5,040 2.99 2,820 33,6003,360 11,160 32,200 5,040 3 2.89 2,76035,40012,4803,8402,8802.8445,760*refer to solved problem #2Multifactor productivity dropped steadily from a high of 3.03 to about 2.84.4. a. Before: 80 ? 5 = 16 carts per worker per hour.After: 84 ? 4 = 21 carts per worker per hour.b. Before: ($10 x 5 = $50) + $40 = $90; hence 80 ÷$90 = .89 carts/$1. After: ($10 x 4 = $40) + $50 = $90; hence 84 ÷$90 = .93 carts/$1.c. Labor productivity increased by 31.25% ((21-16)/16). Multifactor productivity increased by 4.5% ((.93-.89)/.89).*Machine ProductivityBefore: 80 ÷40 = 2 carts/$1.After: 84 ÷50 = 1.68 carts/$1.Productivity increased by -16% ((1.68-2)/2)Chapter 03 - Product and Service Design6.Steps for Making Cash Withdrawal from an ATM1. Insert Card: Magnetic Strip Should be Facing Down2. Watch Screen for InstructionsSelect Transaction Options: 3.1) DepositWithdrawal 2)Transfer 3)4) Other4. Enter Information:1) PIN Number更多精品文档.学习-----好资料2) Select a Transaction and Account3) Enter Amount of Transaction5. Deposit/Withdrawal:1) Deposit—place in an envelope (which you'll find near or in the A TM) andinsert it into the deposit slot2) Withdrawal—lift the “Withdrawal Door,”being careful to remove all cash6. Remove card and receipt (which serves as the transaction record)8.Chapter 04 - Strategic Capacity Planning for Products and ServicesActual output?Efficiency?80% 2. Effective capacity Actual output = .8 (Effective capacity)Effective capacity = .5 (Design capacity)Actual output = (.5)(.8)(Effective capacity)Actual output = (.4)(Design capacity)Actual output = 8 jobsUtilization = .4Actual output?Utilization Design capacityActual output8??20 jobsDesign Capacity?4Effective .capacitya. Given: 10 hrs. or 600 min. of operating time per day. 10.250 days x 600 min. = 150,000 min. per year operating time.更多精品文档.学习-----好资料Total processing time by machineProduct A B C32,000 48,000 64,000 136,000 48,000 2 48,00024,000 36,000 3 30,00030,000 460,000 60,000122,000Total 186,000 208,000186,000?1.24N??2 machine A150,000208,000?1.?N38?2 machineB150,000122,000?.81?1 machine?N C150,000You would have to buy two “A”machines at a total cost of $80,000, or two “B”machines at a total cost of $60,000, or one “C”machine at $80,000.b.Total cost for each type of machine:A (2): 186,000 min ?60 = 3,100 hrs. x $10 = $31,000 + $80,000 = $111,000B (2) : 208,000 ? 60 = 3,466.67 hrs. x $11 = $38,133 + $60,000 = $98,133C(1): 122,000 ? 60 = 2,033.33 hrs. x $12 = $24,400 + $80,000 = $104,400Buy 2 Bs —these have the lowest total cost.Chapter 05 - Process Selection and Facility Layout3. 2435i更多精品文档.学习-----好资料Desired output = 4Operating time = 56 minutesOperating time56 minutes per hour??14 minutes per CT?unitDesired output4 units per hourTask # of Following tasksPositional Weight23 A 420 3 B18 2 C25 D 318 E 229 4 F24 3 G14 H 15Ia. First rule: most followers. Second rule: largest positional weight.更多精品文档.学习-----好资料First rule: Largest positional weight.b.Total time45 80.36%Efficiency c. CTx no. of stations564.cl.a.dabhgef2. Minimum Ct = 1.3 minutesTask Following tasks4 a3 b3 c2 d3 e2 f1 gh更多精品文档.学习-----好资料6 time).?(idlepercent54 percent???11.Idle 3. ).34(1NxCT420 min./day OTday/to 323)copiers??323.1 (rounds Output? 4.cycle/CT1.3 min.4.6timeTotal ? CT.6,Total time3??2. minutes?41. b.2N Assign a, b, c, d, and e to station 1: 2.3 minutes [no idle time] 2.Assign f, g, and h to station 2: 2.3 minutes420OTday182.6 copiers?/??Output 3. 2.3CT4.420 min./day day/?91.30 copiersMaximum Ct is 4.6. Output?cycle min./4.67. 4 1 5738更多精品文档.学习-----好资料6 2Chapter 06 - Work Design and Measurement3.Element PR OT NT AF STjob.476 .90 .46 1.15 .414 1.85 1.505 1.280 1.15 2 1.4721.10 .83 .913 3 1.15 1.0501.00 1.16 41.160 1.15 1.334Total 4.3328. A = 24 + 10 + 14 = 48 minutes per 4 hours48?.20A?240NT?6(.95)?5.70min.1?7.125min?ST5.70x.1?.209. a. Element PR OT NT A ST1 1.10 1.19 1.309 1.15 1.5052 1.15 .83 .955 1.15 1.098.588 1.05 1.15 .56 .6763b.x?.8322??2(.034)zs??034?.s?observations~68?n?67.12????.01(.83)ax????002.z?01?.A22zs2(.034)????n???46.24, round to 47 e = .01 minutes c. ????e.01????更多精品文档.学习-----好资料Chapter 07- Location Planning and Analysis1. Factor Local bank Steel millFood warehousePublic school1. forConvenience H ML M–H H –customers2. ofAttractiveness ML H –M H building3. rawto Nearness M L H L materials4. ofLarge amounts L HL L powerL H L 5. L Pollution controls6. andcost Labor L M L L availability7. TransportationM M–H M–L H costs8. ConstructionMM–HMHcosts更多精品文档.学习-----好资料Location (a) Location (b)A B C Weight 4. FactorC A B10/918/9 1. 10/9 2/9 5 9 5 Business Services7/9 1/9 7/9 7 6 2. 7 6/9 Community Services7/9 3 8/9 3. 8 1/9 3/9 7 Real Estate Cost2/9 4. 10/9 5 5 12/9 10/96 Construction Costs8/9 4/9 4 7/9 5. 8 7 1/9 Cost of Living4/95 5/9 5/9 1/9 55 6. Taxes7 6 8 1/9 6/9 7. 7/9 8/9 Transportation1.0 444553/9 55/9 54/939TotalEach factor has a weight of 1/7.39 44 45 a. Composite Scores 77 7B orC is the best and A is least desirable.b. Business Services and Construction Costs both have a weight of 2/9; the other factors each have a weight of 1/9.5 x + 2 x + 2 x = 1 x = 1/9A B C Composite Scores c. 54/955/9 53/9B is the best followed byC and then A.x yLocation 5.A7 32 B 86 C 41D 46 4 ETotals 25 20?y ?x ii??2025 = 4.0= = 5.0= = x = yn5n5Hence, the center of gravity is at (5,4) and therefore the optimal location.Chapter 08 - Management of Quality更多精品文档.好资料学习----- Checksheet 1.FrequencyWork Type12 Lube and Oil7 Brakes6 Tires4 Battery1 Transmission30TotalPareto127641Trans.BatteryBrakesLube & Oil Tires2??3 ??.???2???????????1????????????0break lunch breakThe run charts seems to show a pattern of errors possibly linked to break times or the end of the shift. Perhaps workers are becoming fatigued. If so, perhaps two 10 minute breaks in the morning and again in the afternoon instead of one 20 minute break could reduce some errors. Also, errors are occurring during the last few minutes before noon and the end of the shift, and those periods should also be given management's attention. 更多精品文档.学习-----好资料4PersonCordOtherChapter 9 - Quality Control更多精品文档.学习-----好资料Sample Mean Range4.=? 0.58(1.87) AR = 79.96 ±Mean Chart: X ±2.6 179.48 2 1.08±= 79.96 2.3 80.14 21.2 UCL = 81.04, LCL = 78.883 80.14?1.7 79.60 4 = 2.11(1.87) = 3.95 Range Chart: UCL = DR 4?2.0 5 80.02 = 0(1.87) = 0LCL = DR 3[Both charts suggest the process is in control: Neither has any 1.4680.38points outside the limits.])1?pp(2p?Control Limits = n = 200 6. n)99040096(..25 2.0096??0096p?.?200 )13(2000138.?.0096?Thus, UCL is .0234 and LCL becomes 0.Since n = 200, the fraction represented by each data point ishalf the amount shown. E.g., 1 defective = .005, 2 defectives= .01, etc.Sample 10 is too large.110409.857?8c?3c?7.857?.?7c7. Control limits: 14UCL is 16.266, LCL becomes 0.All values are within the limits.Let USL = Upper Specification Limit, LSL = Lower Specification Limit, 14.X = Process standard deviation= Process mean, ?For process H:1.??LSL1514X93.??)32(3)(.3?USL?X16?15??1.043?(3)(.32)???.0493 min.938,1.?C pk.93?1.0, not capable更多精品文档.学习-----好资料For process K:30??LSL33X0.??1))(13?(333??X36.5USL17.??1)3()(13?0?1.min{1.0,1.17}C?pk C not process is acceptable < is 1.33, since 1.0 1.33, the Assuming the minimum pk capable.For process T:516.X?LSL18.5?671.??)4(3?3)(0. L?X20.1?1833??1.)43?(3)(0.331.33}?1.C?min{1.67,pk Since 1.33 = 1.33, the process is capable.Chapter 10 - Aggregate Planning and Master SchedulingNo backlogs are allowed7. a.TotalJun. May Apr. Period Mar. Aug. July Sep.350 51 50 60 40 55 44 50 Forecast Output280 40 40 Regular 40 40 40 40 4051 3 8 8 8 8 Overtime 8 819 2 3 12 0 0 0 2 Subcontract0 0 4 3 Output - Forecast 3 ––4 0Inventory0 0 Beginning 3 0 4 0 00 3 0 0 Ending 4 0 07 0 0 1.5 1.5 0 2 Average 20 0 0 Backlog 0 0 0 0 0Costs:22,400 Regular 3,200 3,200 3,200 3,200 3,200 3,200 3,200 6,120 960 960 Overtime 960 360 960 960 9602,660 0 280 Subcontract 280 0 420 0 1,68070 0 0 15 Inventory 0 20 15 2031,2504,4405,8403,575 4,175Total4,4404,1804,600Level strategyb.更多精品文档.学习-----好资料Period Mar. Apr. May Jun. July Aug. Sep.Total350 51 40 55 60 Forecast 50 50 44Output280 Regular 40 40 40 40 40 40 4056 8 8 8 8 Overtime 8 8 8 Subcontract Output - Forecast Inventory Beginning Ending 8 Average 18 Backlog Costs: Regular Overtime Subcontract80 Inventory Backlog Total8.Period Forecast Output920 150 160 150 Regular 150 160 15050 0 10 Overtime 10 10 10 1020 10 Subcontract 0 0 0 0 100 0 10 0 –Output- Forecast 10 0Inventory0 Beginning 10 0 0 10 00 0 0 10 10 0 Ending20 0 0 0 10 Average 5 50 0 0 0 Backlog 0 0 0Costs: 46,000 Regular 7,500 7,500 7,500 8,000 8,000 7,5003,750 0 750 Overtime 750 750 750 7501,600 0 800 0 0 800 Subcontract 080 20 Inventory 40 200 Backlog 0 0 0 0 051,4308,3409,0508,2708,250Total9,0708,750Chapter 11 - MRP and ERP1. a. F: 2G: 1H: 1A: L: 1 x 2 = 2 J: 2 x 2 = 4 1 x 4 = 4D: J: 1 x 2 = 2 1 x 2 = 2 D: 2 x 4 = 8Totals: F = 2; G = 1; H = 1; J = 6; D = 10; L = 2; A = 4b.Stapler更多精品文档Base AssemblyTop Assembly学习-----好资料Beg. 4. 1 2 3 4 Day 5 6 7 Master Inv. Schedule 200 Quantity更多精品文档.学习-----好资料4 1 3 2 Week 10.70 40Material 80 602 3 Week 1 4Labor hr. 280 240 320 160Mach. hr. 210240 180120a. Capacity utilizationWeek 1 23 493.3% 106.7% 80% Labor 53.3%105%60%Machine 120% 90%b. Capacity utilization exceeds 100% for both labor and machine in week 2, and formachine alone in week 4.Production could be shifted to earlier or later weeks in which capacity isunderutilized. Shifting to an earlier week would result in added carrying costs;shifting to later weeks would mean backorder costs.Another option would be to work overtime. Labor cost would increase due toovertime premium, a probable decrease in productivity, and possible increase inaccidents.Chapter 12 - Inventory Management更多精品文档.-----好资料学习The following table contains figures on the monthly volume and unit costs for a 2. random sample of 16 items for a list of 2,000 inventory items.B 8,000 P05 16 500C30300P0910a. See table.b. To allocate control efforts.c. It might be important for some reason other than dollar usage, such as cost of a stockout, usage highly correlated to an A item, etc.3. D = 1,215 bags/yr.S = $10H = $752DS2(1,215)10 a. bags Q 18H75b. Q/2 = 18/2 = 9 bagsD1,215 bags c.orders5 ??67.Q18 bags/orders DS?/2HTC?Q d.Q181,215(75)?(10)?675??675?$1,350218e. Assuming that holding cost per bag increases by $9/bag/year更多精品文档.学习-----好资料)215)(102(1,?17 bagsQ =842151,17?71TC714.71?$1,428.(84)?(10)?714?172 $1,350] = $78.71 –Increase by [$1,428.71D = 40/day x 260 days/yr. = 10,400 packages4.H = $30 S = $6060400)22DS(10,oxes Q?b??203.96?204 a. 030H DQSTC?H? b.Q2400,20410?82$6,118.,)?3060?3,058.82?30()?(602042Yes c. 40020010,?(30TC60))?(d. 2002002 = 3,000 + 3,120 = $6,120TC 200 6,118.82 (only $1.18 higher than with EOQ, so 200 is acceptable.)6,120 –H = $2/month 7.S = $556) –D = 100/month (months 1112)–D = 150/month (months 7255100)2DS2(16?Q.Q D:??74 a.0102H55)2(150?Q83D:?90.022The EOQ model requires this.b.10 = $45 (revised ordering cost) Discount of $10/order is equivalent to S –c.$148.32–16 TC74 =更多精品文档.学习-----好资料10050*?$140)?(45TC?)(250502100100?TC?(45)$145(2)? 1001002100150?TC?$180(2)?(45)1501502=$181.667–12 TC 9115050185?$?(TC?45)(2)50502150100?.5*TC)?(45)?$167(2 1001002150150?195TC)?(45)?$(21501502p = 50/ton/day 10.u = 20 tons/day D= 20 tons/day x 200 days/yr. = 4,000 tons/yr.200 days/yr.S = $100H = $5/ton per yr.50100,4000)2DSp2( a. bags] [10,328 ?516.40 tonsQ??020?u550Hp?4.Q516b. ? bags]I [approx.6,196.8.u(p?)?(30)?30984 tons max50PI48309.max tons [approx. 3,098 bags] Average is92.:?154224516.QRun length =c. days ??10.3350P000,D4 Runs per year =d. 8] .7.75 ?[approx?4Q516. = 258.2 Q?e.ID max SH?TC =Q2 TC = $1,549.00 orig.774.50= $ TC rev.$774.50Savings would be更多精品文档.-----好资料学习Q P H 15. Range495 $5.00 $2.00 D = 4,900 seats/yr. 0–999497 NF 4.95 1.98 H = .4P 1,000–3,999500 NF 1.96 S = $50 4,000–5,999 4.90503 NF1.946,000+ 4.85with TC for all lower price breaks:Compare TC4954,900495 ($50) + $5.00(4,900) = $25,490($2) + TC = 495495 24,9001,000 ($50) + $4.95(4,900) = $25,490($1.98) + TC = 1,0001,000 24,9004,000 ($50) + $4.90(4,900) = $27,991= ($1.96) + TC4,0004,000 24,9006,000 ($50) + $4.85(4,900) = $29,626= ($1.94) + TC6,0006,0002Hence, one would be indifferent between 495 or 1,000 unitsTC????6,000503 500 1,000 4,000 495 497Quantity= 30 gal./day d 22.= 170 gal. ROPLT = 4 days,= 50 gal?ss = Z LTdZ = 1.34 Risk = 9% = 37.31 ?Solving, LTdss=1.88 x 37.31 = 70.14 gal. Z = 1.88, 3%Chapter 13 - JIT and Lean Operations= ?DT(1 + X) 1. N N = C D = 80 pieces per hour80(1.25) (1.35)= 75 min. = 1.25 hr. T = 3= 45 45 =C= .35X更多精品文档.学习-----好资料4. The smallest daily quantity evenly divisible into all four quantities is 3. Therefore, use three cycles.Product Daily quantityUnits per cycle21/3 = 7 21 A12/3 = 4 12 B3/3 = 1 3 C15/3 = 515D5.a. Cycle 1 2 3 4b. Cycle 1 2A 6 6 5 5 A 11 116 6 3 3 3 B B 32 2 C 1 1 1 1 C8 8 4 D 4 5 5 D2 2 E 4 42 E 2c. 4 cycles = lower inventory, more flexibility2 cycles = fewer changeovers7. Net available time = 480 –75 = 405. Takt time = 405/300 units per day = 1.35 minutes. Chapter 15 - Scheduling6. a. FCFS: A–B–C–DSPT: D–C–B–AEDD: C –B–D–ACR: A –C–D–BFCFS: Job time Flow time Due date Daystardy (days) (days) (days) Job20 14 A 14 016 10 B 24 8C 7 31 15 166 D 17 37 201064437更多精品文档.学习-----好资料SPT: Job time Flow time Due date Days Job (days) (days) (days) tardy0 6 17 D 60 13 15 C 77 16 B 23 1020 A 37 14 17243779Job time Flow time Due date EDD: DaysJob (days) (days) (days) tardyC 7 7 15 01 B 10 16 176 D 17 6 23201437 A172484Critical RatioProcessing Time(Days)Due Date Critical Ratio Calculation Job(20 –14 A 20 0) / 14 = 1.43(16 10 –16 B 0) /10 = 1.60(15 –7 15 0) / 7 = 2.14 C(17 –17D0) / 6 = 2.83 6Job A has the lowest critical ratio, therefore it is scheduled first and completed on day 14. After the completion of Job A, the revised critical ratios are:Processing Time(Days)Due DateJob Critical Ratio Calculation–– A –(16 16 10 B –14) /10 = 0.20(15 15 7 C –14) / 7 = 0.14(17 176–14) / 6 = 0.50 DJob C has the lowest critical ratio, therefore it is scheduled next and completed on day 21. After the completion of Job C, the revised critical ratios are:Processing Time(Days)Due DateJob Critical Ratio Calculation––– A(16 10 –B 21) /10 = 16 –0.50–C ––(17 –D21) / 6 = 617–0.67更多精品文档.学习-----好资料Job D has the lowest critical ratio therefore it is scheduled next and completed on day 27.The critical ratio sequence is A–C–D–B and the makespan is 37 days.9937b. FCFS SPT EDD CRtime Flow24.75 21.00 26.50 19.75 ?timeAverage flow jobsof Number tardy Days?nesst ardi Average job jobsNumber of 9.25 11.0 6.00 6.00 time ?Flow?the center Average number of jobsat Makespan 2.672.272.86 2.14SPT is superior.c.9.Time (hr.) Sequence of assignment:Order Step 1 Step 2last (or 7th) 1.40 A 1.20 .80 [C]first B 0.90 1.30 .90 [B]2nd 1.20 0.80 [A] C 2.003rd 1.30 [G] 1.70 D 1.504th 1.80 E 1.60 1.60 [E]6th 1.75 1.50 [D] 2.20 F5th1.40G1.301.75[F]Thus, the sequence is b-a-g-e-f-d-c. 更多精品文档.。
《运营管理》课后习题答案
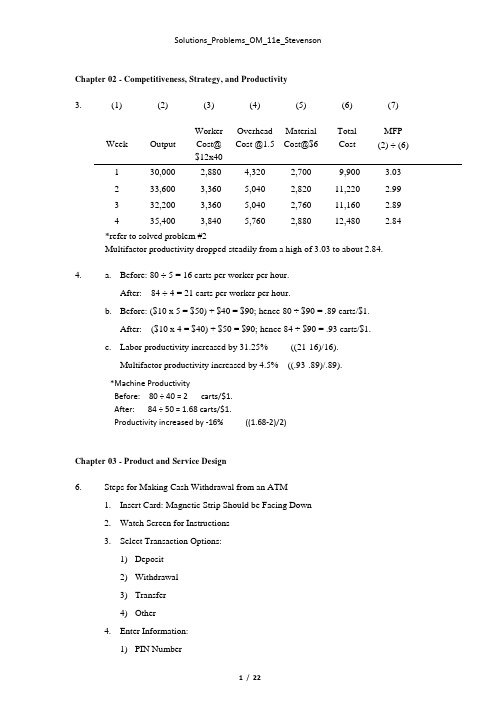
Chapter 02 - Competitiveness, Strategy, and Productivity3. (1) (2) (3) (4) (5) (6) (7)Week Output WorkerCost@$12x40Overhead********MaterialCost@$6TotalCostMFP(2) ÷ (6)1 30,000 2,880 4,320 2,700 9,900 3.032 33,600 3,360 5,040 2,820 11,220 2.993 32,200 3,360 5,040 2,760 11,160 2.894 35,400 3,840 5,760 2,880 12,480 2.84*refer to solved problem #2Multifactor productivity dropped steadily from a high of 3.03 to about 2.84.4. a. Before: 80 ÷ 5 = 16 carts per worker per hour.After: 84 ÷ 4 = 21 carts per worker per hour.b. Before: ($10 x 5 = $50) + $40 = $90; hence 80 ÷ $90 = .89 carts/$1.After: ($10 x 4 = $40) + $50 = $90; hence 84 ÷ $90 = .93 carts/$1.c. Labor productivity increased by 31.25% ((21-16)/16).Multifactor productivity increased by 4.5% ((.93-.89)/.89).*Machine ProductivityBefore: 80 ÷ 40 = 2 carts/$1.After: 84 ÷ 50 = 1.68 carts/$1.Productivity increased by -16% ((1.68-2)/2)Chapter 03 - Product and Service Design6. Steps for Making Cash Withdrawal from an ATM1. Insert Card: Magnetic Strip Should be Facing Down2. Watch Screen for Instructions3. Select Transaction Options:1) Deposit2) Withdrawal3) Transfer4) Other4. Enter Information:1) PIN Number2) Select a Transaction and Account3) Enter Amount of Transaction5. Deposit/Withdrawal: 1) Deposit —place in an envelop e (which you’ll find near or in the ATM) andinsert it into the deposit slot2) Withdrawal —lift the “Withdrawal Door,” being careful to remove all cash6. Remove card and receipt (which serves as the transaction record)8.Chapter 04 - Strategic Capacity Planning for Products and Services2. %80capacityEffective outputActual Efficiency ==Actual output = .8 (Effective capacity) Effective capacity = .5 (Design capacity) Actual output = (.5)(.8)(Effective capacity) Actual output = (.4)(Design capacity) Actual output = 8 jobs Utilization = .4capacityDesign outputActual =n Utilizatiojobs 204.8capacity Effective output Actual Capacity Design ===10. a. Given: 10 hrs. or 600 min. of operating time per day.250 days x 600 min. = 150,000 min. per year operating time.Total processing time by machineProductABC 1 48,000 64,000 32,000 2 48,000 48,000 36,000 3 30,000 36,000 24,000 460,000 60,000 30,000 Total 186,000208,000122,000machine181.000,150000,122machine 238.1000,150000,208machine224.1000,150000,186≈==≈==≈==C B A N N NYou would have to buy two “A” machines at a total cost of $80,000, or two “B” machines at a total cost of $60,000, or one “C” machine at $80,000.b.Total cost for each type of machine:A (2): 186,000 min ÷ 60 = 3,100 hrs. x $10 = $31,000 + $80,000 = $111,000B (2) : 208,000 ÷ 60 = 3,466.67 hrs. x $11 = $38,133 + $60,000 = $98,133 C(1): 122,000 ÷ 60 = 2,033.33 hrs. x $12 = $24,400 + $80,000 = $104,400Buy 2 Bs —these have the lowest total cost.Chapter 05 - Process Selection and Facility Layout3.Desired output = 4Operating time = 56 minutesunit per minutes 14hourper units 4hourper minutes 65output Desired time Operating CT ===Task # of Following tasksPositional WeightA 4 23B 3 20C 2 18D 3 25E 2 18F 4 29G 3 24H 1 14 I5a. First rule: most followers. Second rule: largest positional weight.Assembly Line Balancing Table (CT = 14)b. First rule: Largest positional weight.Assembly Line Balancing Table (CT = 14)c. %36.805645stations of no. x CT time Total Efficiency ===4. a. l.2. Minimum Ct = 1.3 minutesTask Following tasksa 4b 3c 3d 2e 3f 2g 1h3. percent 54.11)3.1(46.CT x N time)(idle percent Idle ==∑=4. 420 min./day 323.1 ( 323)/1.3 min./OT Output rounds to copiers day CT cycle=== b. 1. inutes m 3.224.6N time Total CT ,6.4 time Total ==== 2. Assign a, b, c, d, and e to station 1: 2.3 minutes [no idle time]Assign f, g, and h to station 2: 2.3 minutes3. 420182.6 copiers /2.3OT Output day CT ===4.420 min./dayMaximum Ct is 4.6. Output 91.30 copiers /4.6 min./day cycle==7.Chapter 06 - Work Design and Measurement3. Element PR OT NT AF job ST1 .90.46.414 1.15 .4762 .85 1.505 1.280 1.15 1.4723 1.10.83.913 1.15 1.05041.00 1.16 1.160 1.15 1.334Total4.3328. A = 24 + 10 + 14 = 48 minutes per 4 hours.min 125.720.11x70.5ST .min 70.5)95(.6NT 20.24048A =-=====9. a. Element PR OT NT A ST1 1.10 1.19 1.309 1.15 1.5052 1.15 .83 .955 1.15 1.09831.05.56.588 1.15 .676b.01.A 00.2z 034.s 83.x ==== 222(.034)67.12~68.01(.83)zs n observations ax ⎛⎫⎛⎫===⎪ ⎪⎝⎭⎝⎭c. e = .01 minutes 47 to round ,24.4601.)034(.2e zs n 22=⎪⎭⎫⎝⎛=⎪⎭⎫ ⎝⎛=Chapter 07- Location Planning and Analysis1. Factor Local bank Steel mill Food warehouse Public school1. Convenience forcustomers H L M–H M–H2. Attractiveness ofbuilding H L M M–H3. Nearness to rawmaterials L H L M4. Large amounts ofpower L H L L5. Pollution controls L H L L6. Labor cost andavailability L M L L7. Transportationcosts L M–H M–H M8. Constructioncosts M H M M–HLocation (a) Location (b)4. Factor A B C Weight A B C1. Business Services 9 5 5 2/9 18/9 10/9 10/92. Community Services 7 6 7 1/9 7/9 6/9 7/93. Real Estate Cost 3 8 7 1/9 3/9 8/9 7/94. Construction Costs 5 6 5 2/9 10/9 12/9 10/95. Cost of Living 4 7 8 1/9 4/9 7/9 8/96. Taxes 5 5 5 1/9 5/9 5/9 4/97. Transportation 6 7 8 1/9 6/9 7/9 8/9Total 39 44 45 1.0 53/9 55/9 54/9 Each factor has a weight of 1/7.a. Composite Scores 39 44 45 7 7 7B orC is the best and A is least desirable.b. Business Services and Construction Costs both have a weight of 2/9; the other factors eachhave a weight of 1/9.5 x + 2 x + 2 x = 1 x = 1/9c. Composite ScoresA B C 53/9 55/9 54/9B is the best followed byC and then A.5.Locationx yA 3 7B 8 2C 4 6D 4 1E 6 4Totals 25 20-x =∑x i= 25 = 5.0 -y =∑y i= 20 = 4.0 n 5 n 5Hence, the center of gravity is at (5,4) and therefore the optimal location.Chapter 08 - Management of Quality1. ChecksheetWork Type FrequencyLube and Oil 12Brakes 7Tires 6Battery 4Transmission 1Total 30ParetoLube & Oil Brakes Tires Battery Trans.2 .The run charts seems to show a pattern of errors possibly linked to break times or the end of the shift. Perhaps workers are becoming fatigued. If so, perhaps two 10 minute breaks in the morning and again in the afternoon instead of one 20 minute break could reduce some errors. Also, errors are occurring during the last few minutes before noon and the end of the shift, and those periods should also be given management’s attention.4break lunch break3 2 1 0• • •• • • ••• • • ••••••• ••• •• • •• • •••Chapter 9 - Quality Control4. Sample Mean Range179.48 2.6 Mean Chart: =X ± A 2-R = 79.96 ± 0.58(1.87) 2 80.14 2.3 = 79.96 ± 1.083 80.14 1.2UCL = 81.04, LCL = 78.884 79.60 1.7 Range Chart: UCL = D 4-R = 2.11(1.87) = 3.95 5 80.02 2.0LCL = D 3-R = 0(1.87) = 0680.381.4[Both charts suggest the process is in control: Neither has any points outside the limits.]6. n = 200 Control Limits = np p p )1(2-±Thus, UCL is .0234 and LCL becomes 0.Since n = 200, the fraction represented by each data point is half the amount shown. E.g., 1 defective = .005, 2 defectives = .01, etc.Sample 10 is too large.7. 857.714110c ==Control limits: 409.8857.7c 3c ±=± UCL is 16.266, LCL becomes 0.All values are within the limits.14. Let USL = Upper Specification Limit, LSL = Lower Specification Limit,X = Process mean, σ = Process standard deviationFor process H:}{capablenot ,0.193.93.04.1 ,938.min 04.1)32)(.3(1516393.)32)(.3(1.14153<===-=σ-=-=σ-pk C X USL LSL X 0096.)200(1325==p 0138.0096.200)9904(.0096.20096.±=±=For process K:.1}17.1,0.1min{17.1)1)(3(335.3630.1)1)(3(30333===-=σ-=-=σ- C X USL LSL X pk Assuming the minimum acceptable pk C is 1.33, since 1.0 < 1.33, the process is not capable.For process T:33.1}33.1,67.1min{33.1)4.0)(3(5.181.20367.1)4.0)(3(5.165.183===-=σ-=-=σ- C X USL LSL X pk Since 1.33 = 1.33, the process is capable.Chapter 10 - Aggregate Planning and Master Scheduling7. a.No backlogs are allowedPeriodForecast Output Regular Overtime Subcontract Output - Forecast Inventory Beginning Ending Average Backlog Costs: Regular Overtime Subcontract Inventory Totalb. Level strategyPeriodForecastOutputRegularOvertimeSubcontractOutput - ForecastInventoryBeginningEndingAverageBacklogCosts:RegularOvertimeSubcontractInventoryBacklogTotal8.PeriodForecastOutputRegularOvertimeSubcontractOutput- ForecastInventoryBeginningEndingAverageBacklogCosts:RegularOvertimeSubcontractInventoryBacklogTotalChapter 11 - MRP and ERP1. a. F: 2 G: 1 H: 1J: 2 x 2 = 4 L: 1 x 2 = 2 A: 1 x 4 = 4D: 2 x 4 = 8 J: 1 x 2 = 2 D: 1 x 2 = 2Totals: F = 2; G = 1; H = 1; J = 6; D = 10; L = 2; A = 44. Master Schedule10. Week 1 2 3 4Material 40 80 60 70Week 1 2 3 4Labor hr. 160 320 240 280Mach. hr. 120 240 180 210a. Capacity utilizationWeek 1 2 3 4Labor 53.3% 106.7% 80% 93.3%Machine 60% 120% 90% 105%b. C apacity utilization exceeds 100% for both labor and machine in week 2, and formachine alone in week 4.Production could be shifted to earlier or later weeks in which capacity isunderutilized. Shifting to an earlier week would result in added carrying costs;shifting to later weeks would mean backorder costs.Another option would be to work overtime. Labor cost would increase due toovertime premium, a probable decrease in productivity, and possible increase inaccidents.Chapter 12 - Inventory Management2. The following table contains figures on the monthly volume and unit costs for a random sample of 16 items for a list of 2,000 inventory items.a. See table.b. To allocate control efforts.c. It might be important for some reason other than dollar usage, such as cost of astockout, usage highly correlated to an A item, etc.3. D = 1,215 bags/yr. S = $10 H = $75a. bags HDS Q 187510)215,1(22===b. Q/2 = 18/2 = 9 bagsc.orders ordersbags bags Q D 5.67/ 18 215,1== d . S QD H 2/Q TC +=350,1$675675)10(18215,1)75(218=+=+=e. Assuming that holding cost per bag increases by $9/bag/yearQ ==84)10)(215,1(217 bags71.428,1$71.714714)10(17215,1)84(217=+=+=TCIncrease by [$1,428.71 – $1,350] = $78.714.D = 40/day x 260 days/yr. = 10,400 packagesS = $60 H = $30a. oxes b 20496.2033060)400,10(2H DS 2Q 0====b. S QD H 2Q TC +=82.118,6$82.058,3060,3)60(204400,10)30(2204=+=+=c. Yesd. )60(200400,10)30(2200TC 200+=TC 200 = 3,000 + 3,120 = $6,1206,120 – 6,118.82 (only $1.18 higher than with EOQ, so 200 is acceptable.)7.H = $2/month S = $55D 1 = 100/month (months 1–6)D 2 = 150/month (months 7–12)a. 16.74255)100(2Q :D H DS2Q 010===83.90255)150(2Q :D 02==b. The EOQ model requires this.c. Discount of $10/order is equivalent to S – 10 = $45 (revised ordering cost)1–6 TC74 = $148.32180$)45(150100)2(2150TC 145$)45(100100)2(2100TC *140$)45(50100)2(250TC 15010050=+==+==+=7–12 TC 91 =$181.66195$)45(150150)2(2150TC *5.167$)45(100150)2(2100TC 185$)45(50150)2(250TC 15010050=+==+==+=10. p = 50/ton/day u = 20 tons/day200 days/yr.S = $100 H = $5/ton per yr.a. bags] [10,328 tons 40.5162050505100)000,4(2u p p H DS 2Q 0=-=-=b. ]bags 8.196,6 .approx [ tons 84.309)30(504.516)u p (P Q I max ==-=Average is92.154248.309:2I max =tons [approx. 3,098 bags] c. Run length =days 33.10504.516P Q == d. Runs per year = 8] approx .[ 7.754.516000,4QD == e. Q ' = 258.2TC =S QD H 2I max + TC orig. = $1,549.00 TC rev. = $ 774.50Savings would be $774.50D= 20 tons/day x 200 days/yr. = 4,000 tons/yr.15. RangeP H Q D = 4,900 seats/yr. 0–999 $5.00 $2.00 495 H = .4P 1,000–3,999 4.95 1.98 497 NF S = $50 4,000–5,999 4.90 1.96 500 NF 6,000+ 4.85 1.94503 NFCompare TC 495 with TC for all lower price breaks:TC 495 =495 ($2) + 4,900($50) + $5.00(4,900) = $25,490 2 495 TC 1,000 = 1,000 ($1.98) + 4,900($50) + $4.95(4,900) = $25,4902 1,000 TC 4,000 = 4,000 ($1.96) + 4,900($50) + $4.90(4,900) = $27,9912 4,000 TC 6,000 = 6,000 ($1.94) + 4,900($50) + $4.85(4,900) = $29,6262 6,000Hence, one would be indifferent between 495 or 1,000 units 22. d = 30 gal./day ROP = 170 gal. LT = 4 days,ss = Z σd LT = 50 galRisk = 9% Z = 1.34 Solving, σd LT = 37.31 3% Z = 1.88, ss=1.88 x 37.31 = 70.14 gal.Chapter 13 - JIT and Lean Operations1. N = ?N = DT(1 + X)D = 80 pieces per hourC T = 75 min. = 1.25 hr. = 80(1.25) (1.35)= 3C = 45 45X = .35QuantityTC4. The smallest daily quantity evenly divisible into all four quantities is 3. Therefore, usethree cycles.Product Daily quantity Units per cycleA 21 21/3 = 7B 12 12/3 = 4C 3 3/3 = 1D 15 15/3 = 55.a. Cycle 1 2 3 4A 6 6 5 5B 3 3 3 3C 1 1 1 1D 4 4 5 5E 2 2 2 2 b. Cycle 1 2A 11 11B 6 6C 2 2D 8 8E 4 4c. 4 cycles = lower inventory, more flexibility2 cycles = fewer changeovers7. Net available time = 480 – 75 = 405. Takt time = 405/300 units per day = 1.35 minutes. Chapter 15 - Scheduling6. a. FCFS: A–B–C–DSPT: D–C–B–AEDD: C–B–D–ACR: A–C–D–BFCFS: Job time Flow time Due date DaysJob (days) (days) (days) tardyA 14 14 20 0B 10 24 16 8C 7 31 15 16D 6 37 17 2037 106 44SPT: Job time Flow time Due date Days Job (days) (days) (days) tardyD 6 6 17 0C 7 13 15 0B 10 23 16 7A 14 37 20 1737 79 24EDD:Job D has the lowest critical ratio therefore it is scheduled next and completed on day 27.b.ardi Flow time Average flow time Number of jobsDays tardy Average job t ness Number of jobs Flow timeAverage number of jobs at the center Makespan==∑=FCFS SPT EDD CR26.50 19.75 21.00 24.75 11.0 6.00 6.00 9.25 2.86 2.142.272.67c. SPT is superior.9.Thus, the sequence is b-a-g-e-f-d-c.。
《运营管理》课后习题标准答案
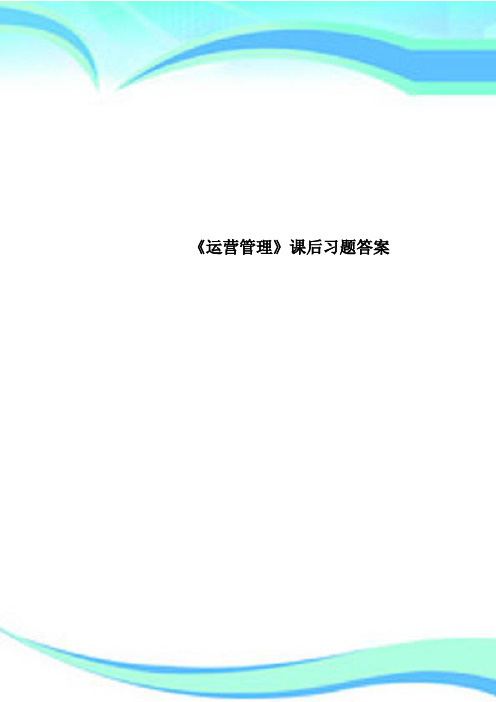
《运营管理》课后习题答案————————————————————————————————作者:————————————————————————————————日期:2Chapter 02 - Competitiveness, Strategy, and Productivity3. (1) (2) (3) (4) (5) (6) (7)Week Output WorkerCost@$12x40Overhead********MaterialCost@$6TotalCostMFP(2) ÷ (6)1 30,000 2,880 4,320 2,700 9,900 3.032 33,600 3,360 5,040 2,820 11,220 2.993 32,200 3,360 5,040 2,760 11,160 2.894 35,400 3,840 5,760 2,880 12,480 2.84*refer to solved problem #2Multifactor productivity dropped steadily from a high of 3.03 to about 2.84.4. a. Before: 80 ÷ 5 = 16 carts per worker per hour.After: 84 ÷ 4 = 21 carts per worker per hour.b. Before: ($10 x 5 = $50) + $40 = $90; hence 80 ÷ $90 = .89 carts/$1.After: ($10 x 4 = $40) + $50 = $90; hence 84 ÷ $90 = .93 carts/$1.c. Labor productivity increased by 31.25% ((21-16)/16).Multifactor productivity increased by 4.5% ((.93-.89)/.89).*Machine ProductivityBefore: 80 ÷ 40 = 2 carts/$1.After: 84 ÷ 50 = 1.68 carts/$1.Productivity increased by -16% ((1.68-2)/2)Chapter 03 - Product and Service Design6. Steps for Making Cash Withdrawal from an ATM1. Insert Card: Magnetic Strip Should be Facing Down2. Watch Screen for Instructions3. Select Transaction Options:1) Deposit2) Withdrawal3) Transfer4) Other4. Enter Information:1) PIN Number2) Select a Transaction and Account3) Enter Amount of Transaction5. Deposit/Withdrawal: 1) Deposit —place in an envelope (which you’ll find near or in the ATM) andinsert it into the deposit slot2) Withdrawal —lift the “Withdrawal Door,” being careful to remove all cash6. Remove card and receipt (which serves as the transaction record)8.TechnicalRequirements IngredientsHandlingPreparationCustomer RequirementsTaste √√ Appearance√ √√Texture/consistency√√Chapter 04 - Strategic Capacity Planning for Products and Services2. %80capacityEffective outputActual Efficiency ==Actual output = .8 (Effective capacity) Effective capacity = .5 (Design capacity) Actual output = (.5)(.8)(Effective capacity) Actual output = (.4)(Design capacity) Actual output = 8 jobs Utilization = .4capacityDesign outputActual =n Utilizatiojobs 204.8capacity Effective output Actual Capacity Design ===10. a. Given: 10 hrs. or 600 min. of operating time per day.250 days x 600 min. = 150,000 min. per year operating time.Total processing time by machineProductABC 1 48,000 64,000 32,000 2 48,000 48,000 36,000 3 30,000 36,000 24,000 460,000 60,000 30,000 Total 186,000208,000122,000machine181.000,150000,122machine 238.1000,150000,208machine224.1000,150000,186≈==≈==≈==C B A N N NYou would have to buy two “A” machines at a total cost of $80,000, or two “B” machines at a total cost of $60,000, or one “C” machine at $80,000.b.Total cost for each type of machine:A (2): 186,000 min ÷ 60 = 3,100 hrs. x $10 = $31,000 + $80,000 = $111,000B (2) : 208,000 ÷ 60 = 3,466.67 hrs. x $11 = $38,133 + $60,000 = $98,133 C(1): 122,000 ÷ 60 = 2,033.33 hrs. x $12 = $24,400 + $80,000 = $104,400Buy 2 Bs —these have the lowest total cost.Chapter 05 - Process Selection and Facility Layout3.3 adf752 b4 c4 e9 h5 i6 gDesired output = 4Operating time = 56 minutesunit per minutes 14hourper units 4hourper minutes 65output Desired time Operating CT ===Task # of Following tasksPositional WeightA 4 23B 3 20C 2 18D 3 25E 2 18F 4 29G 3 24H 1 14 I5a. First rule: most followers. Second rule: largest positional weight.Assembly Line Balancing Table (CT = 14)Work StationTask Task TimeTime RemainingFeasible tasksRemainingIF 5 9 A,D,G A 3 6 B,G G6 – – II D7 7 B, E B 2 5 C C4 1 – III E 4 10 H H9 1 – IV I59–b. First rule: Largest positional weight.Assembly Line Balancing Table (CT = 14)Work StationTask Task TimeTime RemainingFeasible tasks RemainingIF 5 9 A,D,G D7 2 – II G 6 8 A, E A 3 5 B,E B2 3 – III C 4 10 E E4 6 – IV H 95 I I5–c. %36.805645stations of no. x CT time Total Efficiency ===4. a. l.2. Minimum Ct = 1.3 minutesTask Following tasksa 4b 3c 3d 2e 3f 2g 1habd cfeghWork StationEligible Assign Time RemainingIdle TimeIa A 1.1 b,c,e, (tie)B 0.7C 0.4E 0.3 0.3 II d D 0.0 0.0 IIIf,g F 0.5G 0.2 0.2 IVh H 0.1 0.10.63. percent 54.11)3.1(46.CT x N time)(idle percent Idle ==∑=4. 420 min./day 323.1 ( 323)/1.3 min./OT Output rounds to copiers day CT cycle=== b. 1. inutes m 3.224.6N time Total CT ,6.4 time Total ==== 2. Assign a, b, c, d, and e to station 1: 2.3 minutes [no idle time]Assign f, g, and h to station 2: 2.3 minutes3. 420182.6 copiers /2.3OT Output day CT ===4.420 min./dayMaximum Ct is 4.6. Output 91.30 copiers /4.6 min./day cycle==7. 1 5 4 3 8 762Chapter 06 - Work Design and Measurement3. Element PR OT NT AF job ST1 .90.46.414 1.15 .4762 .85 1.505 1.280 1.15 1.4723 1.10.83.913 1.15 1.05041.00 1.16 1.160 1.15 1.334Total4.3328. A = 24 + 10 + 14 = 48 minutes per 4 hours.min 125.720.11x70.5ST .min 70.5)95(.6NT 20.24048A =-=====9. a. Element PR OT NT A ST1 1.10 1.19 1.309 1.15 1.5052 1.15 .83 .955 1.15 1.09831.05.56.588 1.15 .676b.01.A 00.2z 034.s 83.x ==== 222(.034)67.12~68.01(.83)zs n observations ax ⎛⎫⎛⎫===⎪ ⎪⎝⎭⎝⎭c. e = .01 minutes 47 to round ,24.4601.)034(.2e zs n 22=⎪⎭⎫⎝⎛=⎪⎭⎫ ⎝⎛=Chapter 07- Location Planning and Analysis1. Factor Local bank Steel mill Food warehouse Public school1. Convenience forcustomers H L M–H M–H2. Attractiveness ofbuilding H L M M–H3. Nearness to rawmaterials L H L M4. Large amounts ofpower L H L L5. Pollution controls L H L L6. Labor cost andavailability L M L L7. Transportationcosts L M–H M–H M8. Constructioncosts M H M M–HLocation (a) Location (b)4. Factor A B C Weight A B C1. Business Services 9 5 5 2/9 18/9 10/9 10/92. Community Services 7 6 7 1/9 7/9 6/9 7/93. Real Estate Cost 3 8 7 1/9 3/9 8/9 7/94. Construction Costs 5 6 5 2/9 10/9 12/9 10/95. Cost of Living 4 7 8 1/9 4/9 7/9 8/96. Taxes 5 5 5 1/9 5/9 5/9 4/97. Transportation 6 7 8 1/9 6/9 7/9 8/9Total 39 44 45 1.0 53/9 55/9 54/9 Each factor has a weight of 1/7.a. Composite Scores 39 44 45 7 7 7B orC is the best and A is least desirable.b. Business Services and Construction Costs both have a weight of 2/9; the other factors eachhave a weight of 1/9.5 x + 2 x + 2 x = 1 x = 1/9c. Composite ScoresA B C 53/9 55/9 54/9B is the best followed byC and then A.5.Locationx yA 3 7B 8 2C 4 6D 4 1E 6 4Totals 25 20-x =∑x i= 25 = 5.0 -y =∑y i= 20 = 4.0 n 5 n 5Hence, the center of gravity is at (5,4) and therefore the optimal location.Chapter 08 - Management of Quality1. ChecksheetWork Type FrequencyLube and Oil 12Brakes 7Tires 6Battery 4Transmission 1Total 30Pareto127641 Lube & Oil Brakes Tires Battery Trans.2 .The run charts seems to show a pattern of errors possibly linked to break times or the end of the shift. Perhaps workers are becoming fatigued. If so, perhaps two 10 minute breaks in the morning and again in the afternoon instead of one 20 minute break could reduce some errors. Also, errors are occurring during the last few minutes before noon and the end of the shift, and those periods should also be given management’s attention.4Power Per LamMissDidn’Not OutletDefectBurn LoosLampOtheCordbreak lunch3 2•• •• •• • ••• • ••• •••• ••• •• • •• • •••Chapter 9 - Quality Control4. Sample Mean Range179.48 2.6 Mean Chart: =X ± A 2-R = 79.96 ± 0.58(1.87) 2 80.14 2.3 = 79.96 ± 1.083 80.14 1.2UCL = 81.04, LCL = 78.884 79.60 1.7 Range Chart: UCL = D 4-R = 2.11(1.87) = 3.95 5 80.02 2.0LCL = D 3-R = 0(1.87) = 0680.381.4[Both charts suggest the process is in control: Neither has any points outside the limits.]6. n = 200 Control Limits = np p p )1(2-±Thus, UCL is .0234 and LCL becomes 0.Since n = 200, the fraction represented by each data point is half the amount shown. E.g., 1 defective = .005, 2 defectives = .01, etc.Sample 10 is too large.7. 857.714110c ==Control limits: 409.8857.7c 3c ±=± UCL is 16.266, LCL becomes 0.All values are within the limits.14. Let USL = Upper Specification Limit, LSL = Lower Specification Limit,X = Process mean, σ = Process standard deviationFor process H:}{capablenot ,0.193.93.04.1 ,938.min 04.1)32)(.3(1516393.)32)(.3(1.14153<===-=σ-=-=σ-pk C X USL LSL X 0096.)200(1325==p 0138.0096.200)9904(.0096.20096.±=±=For process K:.1}17.1,0.1min{17.1)1)(3(335.3630.1)1)(3(30333===-=σ-=-=σ- C X USL LSL X pk Assuming the minimum acceptable pk C is 1.33, since 1.0 < 1.33, the process is not capable.For process T:33.1}33.1,67.1min{33.1)4.0)(3(5.181.20367.1)4.0)(3(5.165.183===-=σ-=-=σ- C X USL LSL X pk Since 1.33 = 1.33, the process is capable.Chapter 10 - Aggregate Planning and Master Scheduling7. a.No backlogs are allowedPeriod Mar. Apr. May Jun. July Aug. Sep. TotalForecast 50 44 55 60 50 40 51 350 Output Regular 40 40 40 40 40 40 40 280 Overtime 8 8 8 8 8 3 8 51 Subcontract 2 0 3 12 2 0 0 19 Output - Forecast 0 4 –4 0 0 3 –3 Inventory Beginning 0 0 4 0 0 0 3 Ending 0 4 0 0 0 3 0 Average 0 2 2 0 0 1.5 1.5 7 Backlog 0 0 0 0 0 0 0 0 Costs: Regular 3,200 3,200 3,200 3,200 3,200 3,200 3,200 22,400 Overtime 960 960 960 960 960 360 960 6,120 Subcontract 280 0 420 1,680280 0 0 2,660 Inventory 0 20 20 0 0 15 15 70 Total4,4404,1804,6005,8404,4403,575 4,17531,250b. Level strategyPeriod Mar. Apr. May Jun. July Aug. Sep. Total Forecast 50 44 55 60 50 40 51 350 OutputRegular 40 40 40 40 40 40 40 280 Overtime 8 8 8 8 8 8 8 56 Subcontract 2 2 2 2 2 2 2 14 Output - Forecast 0 6 –5 –10 0 10 –1InventoryBeginning 0 0 6 1 0 0 1Ending 0 6 1 0 0 1 0Average 0 3 3.5 .5 0 .5 .5 8 Backlog 0 0 0 9 9 0 0 18 Costs:Regular 3,200 3,200 3,200 3,200 3,200 3,200 3,200 22,400 Overtime 960 960 960 960 960 960 960 6,720 Subcontract 280 280 280 280 280 280 280 1,960 Inventory 30 35 5 0 5 5 80 Backlog 180 180 360 Total 4,440 4,470 4,475 4,625 4,620 4,445 4,445 31,520 8.Period 1 2 3 4 5 6 TotalForecast 160 150 160 180 170 140 960OutputRegular 150 150 150 150 160 160 920Overtime 10 10 0 10 10 10 50Subcontract 0 0 10 10 0 0 20Output- Forecast 0 10 0 –10 0 0InventoryBeginning 0 0 10 10 0 0Ending 0 10 10 0 0 0Average 0 5 10 5 0 0 20Backlog 0 0 0 0 0 0 0Costs:Regular 7,500 7,500 7,500 7,500 8,000 8,000 46,000Overtime 750 750 0 750 750 750 3,750Subcontract 0 0 800 800 0 0 1,600Inventory 20 40 20 80Backlog 0 0 0 0 0 0Total 8,250 8,270 8,340 9,070 9,050 8,750 51,430Chapter 11 - MRP and ERP1. a. F: 2 G: 1 H: 1J: 2 x 2 = 4 L: 1 x 2 = 2 A: 1 x 4 = 4D: 2 x 4 = 8 J: 1 x 2 = 2 D: 1 x 2 = 2Totals: F = 2; G = 1; H = 1; J = 6; D = 10; L = 2; A = 4b.4. Master Schedule Day Beg. Inv. 1 2 3 4 5 6 7 Quantity100 150 200 TableBeg. Inv. 1 2 3 4 5 6 7 Gross requirements 100 150 200 Scheduled receipts Projected on hand Net requirements 100 150 200 Planned-order receipts 100 150 200 Planned-order releases 100 150 200Wood Sections Beg. Inv. 1 2 3 4 5 6 7 Gross requirements 200300 400 Scheduled receipts 100 Projected on hand 100100 Net requirements 100 300 400 Planned-order receipts 100 300 400 Planned-order releases400 400Braces Beg. Inv. 1 2 3 4 5 6 7 Gross requirements 300 450 600 Scheduled receipts Projected on hand 60 60 60 60 Net requirements 240 450 600 Planned-order receipts 240 450 600Planned-order releases 240 450 600StaplerTopBaseCoveSpri SlideBase Strik RubberSlidSpriLegs Beg.Inv.1 2 3 4 5 6 7Gross requirements 400 600 800Scheduled receiptsProjected on hand 120 120 120 120 88 88 71 Net requirements 280 600 800Planned-order receipts 308 660 880Planned-order releases 968 88010. Week 1 2 3 4Material 40 80 60 70Week 1 2 3 4Labor hr. 160 320 240 280Mach. hr. 120 240 180 210a. Capacity utilizationWeek 1 2 3 4Labor 53.3% 106.7% 80% 93.3%Machine 60% 120% 90% 105%b. C apacity utilization exceeds 100% for both labor and machine in week 2, and formachine alone in week 4.Production could be shifted to earlier or later weeks in which capacity isunderutilized. Shifting to an earlier week would result in added carrying costs;shifting to later weeks would mean backorder costs.Another option would be to work overtime. Labor cost would increase due toovertime premium, a probable decrease in productivity, and possible increase inaccidents.Chapter 12 - Inventory Management2. The following table contains figures on the monthly volume and unit costs for a random sample of 16 items for a list of 2,000 inventory items. DollarItemUnit Cost UsageUsageCategoryK34 10 200 2,000 C K35 25 600 15,000 A K36 36 150 5,400 B M10 16 25 400 C M20 20 80 1,600 C Z45 80 250 16,000 A F14 20 300 6,000 B F95 30 800 24,000 A F99 20 60 1,200 C D45 10 550 5,500 B D48 12 90 1,080 C D52 15 110 1,650 C D57 40 120 4,800 B N08 30 40 1,200 C P05 16 500 8,000 BP091030300Ca. See table.b. To allocate control efforts.c. It might be important for some reason other than dollar usage, such as cost of astockout, usage highly correlated to an A item, etc.3. D = 1,215 bags/yr. S = $10 H = $75a. bags HDS Q 187510)215,1(22===b. Q/2 = 18/2 = 9 bagsc.orders ordersbags bags Q D 5.67/ 18 215,1== d . S QD H 2/Q TC +=350,1$675675)10(18215,1)75(218=+=+=e. Assuming that holding cost per bag increases by $9/bag/yearQ ==84)10)(215,1(217 bags71.428,1$71.714714)10(17215,1)84(217=+=+=TCIncrease by [$1,428.71 – $1,350] = $78.714.D = 40/day x 260 days/yr. = 10,400 packagesS = $60 H = $30a. oxes b 20496.2033060)400,10(2H DS 2Q 0====b. S QD H 2Q TC +=82.118,6$82.058,3060,3)60(204400,10)30(2204=+=+=c. Yesd. )60(200400,10)30(2200TC 200+=TC 200 = 3,000 + 3,120 = $6,1206,120 – 6,118.82 (only $1.18 higher than with EOQ, so 200 is acceptable.)7.H = $2/month S = $55D 1 = 100/month (months 1–6)D 2 = 150/month (months 7–12)a. 16.74255)100(2Q :D H DS2Q 010===83.90255)150(2Q :D 02==b. The EOQ model requires this.c. Discount of $10/order is equivalent to S – 10 = $45 (revised ordering cost)1–6 TC74 = $148.32180$)45(150100)2(2150TC 145$)45(100100)2(2100TC *140$)45(50100)2(250TC 15010050=+==+==+=7–12 TC 91 =$181.66195$)45(150150)2(2150TC *5.167$)45(100150)2(2100TC 185$)45(50150)2(250TC 15010050=+==+==+=10. p = 50/ton/day u = 20 tons/day200 days/yr. S = $100 H = $5/ton per yr.a. bags] [10,328 tons 40.5162050505100)000,4(2u p p H DS 2Q 0=-=-=b. ]bags 8.196,6 .approx [ tons 84.309)30(504.516)u p (P Q I max ==-=Average is92.154248.309:2I max =tons [approx. 3,098 bags] c. Run length =days 33.10504.516P Q == d. Runs per year = 8] approx .[ 7.754.516000,4QD == e. Q ' = 258.2TC =S QD H 2I max + TC orig. = $1,549.00 TC rev. = $ 774.50Savings would be $774.50D= 20 tons/day x 20015. RangeP H Q D = 4,900 seats/yr. 0–999 $5.00 $2.00 495 H = .4P 1,000–3,999 4.95 1.98 497 NF S = $50 4,000–5,999 4.90 1.96 500 NF 6,000+4.851.94503 NFCompare TC 495 with TC for all lower price breaks:TC 495 =495 ($2) + 4,900($50) + $5.00(4,900) = $25,490 2 495 TC 1,000 = 1,000 ($1.98) + 4,900($50) + $4.95(4,900) = $25,4902 1,000 TC 4,000 = 4,000 ($1.96) + 4,900($50) + $4.90(4,900) = $27,9912 4,000 TC 6,000 = 6,000 ($1.94) + 4,900($50) + $4.85(4,900) = $29,6262 6,000Hence, one would be indifferent between 495 or 1,000 units 22. d = 30 gal./day ROP = 170 gal. LT = 4 days,ss = Z σd LT = 50 galRisk = 9% Z = 1.34 Solving, σd LT = 37.31 3% Z = 1.88, ss=1.88 x 37.31 = 70.14 gal.Chapter 13 - JIT and Lean Operations1. N = ?N = DT(1 + X)D = 80 pieces per hourC T = 75 min. = 1.25 hr. = 80(1.25) (1.35)= 3C = 45 45X = .35• •• •495 497 500 5031,0004,000 6,000QuantityTC4. The smallest daily quantity evenly divisible into all four quantities is 3. Therefore, usethree cycles.Product Daily quantity Units per cycleA 21 21/3 = 7B 12 12/3 = 4C 3 3/3 = 1D 15 15/3 = 55.a. Cycle 1 2 3 4A 6 6 5 5B 3 3 3 3C 1 1 1 1D 4 4 5 5E 2 2 2 2 b. Cycle 1 2A 11 11B 6 6C 2 2D 8 8E 4 4c. 4 cycles = lower inventory, more flexibility2 cycles = fewer changeovers7. Net available time = 480 – 75 = 405. Takt time = 405/300 units per day = 1.35 minutes. Chapter 15 - Scheduling6. a. FCFS: A–B–C–DSPT: D–C–B–AEDD: C–B–D–ACR: A–C–D–BFCFS: Job time Flow time Due date DaysJob (days) (days) (days) tardyA 14 14 20 0B 10 24 16 8C 7 31 15 16D 6 37 17 2037 106 44SPT: Job time Flow time Due date Days Job (days) (days) (days) tardyD 6 6 17 0C 7 13 15 0B 10 23 16 7A 14 37 20 1737 79 24EDD: Job time Flow time Due date DaysJob (days) (days) (days) tardyC 7 7 15 0B 10 17 16 1D 6 23 17 6A 14 37 20 1784 24Critical RatioJob Processing Time(Days) Due Date Critical Ratio CalculationA 14 20 (20 – 0) / 14 = 1.43B 10 16 (16 – 0) /10 = 1.60C 7 15 (15 – 0) / 7 = 2.14D 6 17 (17 – 0) / 6 = 2.83Job A has the lowest critical ratio, therefore it is scheduled first and completed on day 14. After the completion of Job A, the revised critical ratios are:Job Processing Time(Days) Due Date Critical Ratio CalculationA –––B 10 16 (16 – 14) /10 = 0.20C 7 15 (15 – 14) / 7 = 0.14D 6 17 (17 – 14) / 6 = 0.50Job C has the lowest critical ratio, therefore it is scheduled next and completed on day 21. After the completion of Job C, the revised critical ratios are:Job Processing Time(Days) Due Date Critical Ratio CalculationA –––B 10 16 (16 – 21) /10 = –0.50C –––D 6 17 (17 – 21) / 6 = –0.67Job D has the lowest critical ratio therefore it is scheduled next and completed on day 27. The critical ratio sequence is A –C –D –B and the makespan is 37 days. Critical Ratio sequenceProcessing Time(Days)Flow time Due Date TardinessA 14 14 20 0 C 7 21 15 6 D 6 27 17 10 B1037 16 21 ∑9937b.ardi Flow time Average flow time Number of jobsDays tardy Average job t ness Number of jobs Flow timeAverage number of jobs at the center Makespan==∑=FCFS SPT EDD CR26.50 19.75 21.00 24.75 11.0 6.00 6.00 9.25 2.86 2.142.272.67c. SPT is superior.9.Time (hr.) Sequence of assignment:Order Step 1 Step 2A 1.20 1.40 .80 [C] last (or 7th)B 0.90 1.30 .90 [B] firstC 2.00 0.80 1.20 [A] 2ndD 1.70 1.50 1.30 [G] 3rdE 1.60 1.80 1.60 [E] 4thF 2.20 1.75 1.50 [D] 6th G1.301.401.75[F]5thThus, the sequence is b-a-g-e-f-d-c.。
运营管理作业答案
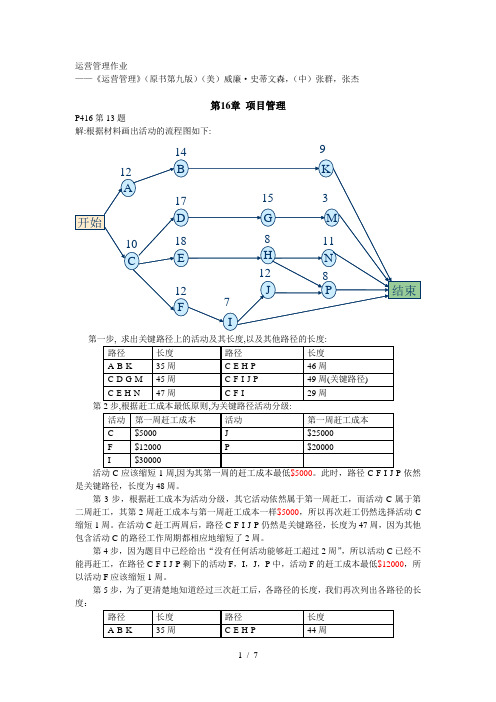
运营管理作业 ——《运营管理》(原书第九版)(美)威廉·史蒂文森,(中)张群,张杰第16章 项目管理P416第13题解:根据材料画出活动的流程图如下:9第2步,根据赶工成本最低原则,为关键路径活动分级:依然是关键路径,长度为48周。
第3步,根据赶工成本为活动分级,其它活动依然属于第一周赶工,而活动C 属于第二周赶工,其第2周赶工成本与第一周赶工成本一样$5000,所以再次赶工仍然选择活动C 缩短1周。
在活动C 赶工两周后,路径C-F-I-J-P 仍然是关键路径,长度为47周,因为其他包含活动C 的路径工作周期都相应地缩短了2周。
第4步,因为题目中已经给出“没有任何活动能够赶工超过2周”,所以活动C 已经不能再赶工,在路径C-F-I-J-P 剩下的活动F ,I ,J ,P 中,活动F 的赶工成本最低$12000,所以活动F 应该缩短1周。
第5步,为了更清楚地知道经过三次赶工后,各路径的长度,我们再次列出各路径的长度:由上表可见,经过三次赶工后,路径C-F-I-J-P仍然是关系路径,长度为46周,活动F 的第二周赶工成本为$15000,比剩下的活动I,J,P的第一周赶工成本更低,所以第四次赶工继续缩短活动F的加工时间1周。
接下来,路径C-E-H-N和路径C-F-I-J-P的长度都是45周,因此它们都是关键的。
第6步,在两条关键路径上根据赶工成本最低原则为活动分级(注意剔除已经不能再赶工的活动):的P,第五次赶工成本为$16000+$20000=$36000。
因此,成本最小的项目缩短5周的赶工进度安排是:活动C缩短2周;活动F缩短2周,活动E和活动P各缩短1周,总的赶工成本为2×$5000+2×$12000+$16000+$20000=$70000。
P416第14题解:问题a第1步,求出关键路径上的活动及其长度,以及其他路径的长度:第2步,根据赶工成本最低原则,为关键路径活动分级,并求出各活动每缩短1周所需花费的成第3步,开始缩短项目,一次一周,每次缩短之后检查一遍当前关键路径.于是:①将活动7-11减少1周,成本相应增加$15000,关键路径长度现在变为34周;②将活动1-2减少1周,成本相应增加$18000,关键路径长度现在变为33周;③现在有两条关键路径,进一步的改进必须是同时缩短两条路径,即:路径$5000,关键路径长度现在变为32周;⑤现在有三条关键路径,进一步的改进必须是同时缩短三条路径,即路径1-2,2-5,5-7,7-11,11-13;路径1-4,4-6,6-10, 10-12,12-13和路径1-3,3-8,8-11,11-13。
《运营管理》课后习题标准答案
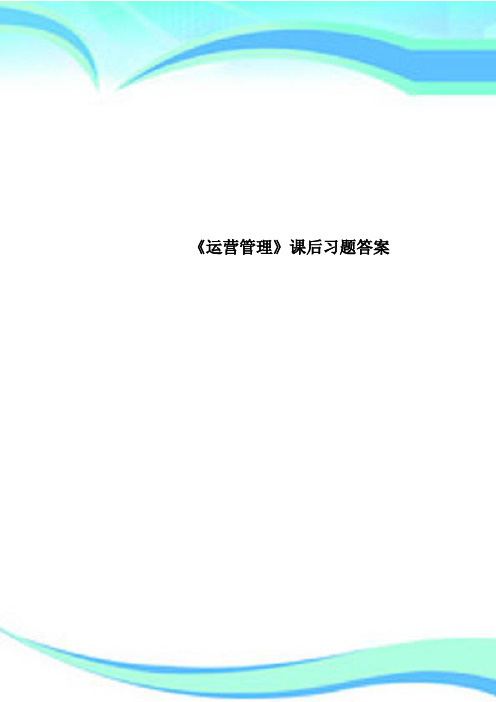
《运营管理》课后习题答案————————————————————————————————作者:————————————————————————————————日期:2Chapter 02 - Competitiveness, Strategy, and Productivity3. (1) (2) (3) (4) (5) (6) (7)Week Output WorkerCost@$12x40Overhead********MaterialCost@$6TotalCostMFP(2) ÷ (6)1 30,000 2,880 4,320 2,700 9,900 3.032 33,600 3,360 5,040 2,820 11,220 2.993 32,200 3,360 5,040 2,760 11,160 2.894 35,400 3,840 5,760 2,880 12,480 2.84*refer to solved problem #2Multifactor productivity dropped steadily from a high of 3.03 to about 2.84.4. a. Before: 80 ÷ 5 = 16 carts per worker per hour.After: 84 ÷ 4 = 21 carts per worker per hour.b. Before: ($10 x 5 = $50) + $40 = $90; hence 80 ÷ $90 = .89 carts/$1.After: ($10 x 4 = $40) + $50 = $90; hence 84 ÷ $90 = .93 carts/$1.c. Labor productivity increased by 31.25% ((21-16)/16).Multifactor productivity increased by 4.5% ((.93-.89)/.89).*Machine ProductivityBefore: 80 ÷ 40 = 2 carts/$1.After: 84 ÷ 50 = 1.68 carts/$1.Productivity increased by -16% ((1.68-2)/2)Chapter 03 - Product and Service Design6. Steps for Making Cash Withdrawal from an ATM1. Insert Card: Magnetic Strip Should be Facing Down2. Watch Screen for Instructions3. Select Transaction Options:1) Deposit2) Withdrawal3) Transfer4) Other4. Enter Information:1) PIN Number2) Select a Transaction and Account3) Enter Amount of Transaction5. Deposit/Withdrawal: 1) Deposit —place in an envelope (which you’ll find near or in the ATM) andinsert it into the deposit slot2) Withdrawal —lift the “Withdrawal Door,” being careful to remove all cash6. Remove card and receipt (which serves as the transaction record)8.TechnicalRequirements IngredientsHandlingPreparationCustomer RequirementsTaste √√ Appearance√ √√Texture/consistency√√Chapter 04 - Strategic Capacity Planning for Products and Services2. %80capacityEffective outputActual Efficiency ==Actual output = .8 (Effective capacity) Effective capacity = .5 (Design capacity) Actual output = (.5)(.8)(Effective capacity) Actual output = (.4)(Design capacity) Actual output = 8 jobs Utilization = .4capacityDesign outputActual =n Utilizatiojobs 204.8capacity Effective output Actual Capacity Design ===10. a. Given: 10 hrs. or 600 min. of operating time per day.250 days x 600 min. = 150,000 min. per year operating time.Total processing time by machineProductABC 1 48,000 64,000 32,000 2 48,000 48,000 36,000 3 30,000 36,000 24,000 460,000 60,000 30,000 Total 186,000208,000122,000machine181.000,150000,122machine 238.1000,150000,208machine224.1000,150000,186≈==≈==≈==C B A N N NYou would have to buy two “A” machines at a total cost of $80,000, or two “B” machines at a total cost of $60,000, or one “C” machine at $80,000.b.Total cost for each type of machine:A (2): 186,000 min ÷ 60 = 3,100 hrs. x $10 = $31,000 + $80,000 = $111,000B (2) : 208,000 ÷ 60 = 3,466.67 hrs. x $11 = $38,133 + $60,000 = $98,133 C(1): 122,000 ÷ 60 = 2,033.33 hrs. x $12 = $24,400 + $80,000 = $104,400Buy 2 Bs —these have the lowest total cost.Chapter 05 - Process Selection and Facility Layout3.3 adf752 b4 c4 e9 h5 i6 gDesired output = 4Operating time = 56 minutesunit per minutes 14hourper units 4hourper minutes 65output Desired time Operating CT ===Task # of Following tasksPositional WeightA 4 23B 3 20C 2 18D 3 25E 2 18F 4 29G 3 24H 1 14 I5a. First rule: most followers. Second rule: largest positional weight.Assembly Line Balancing Table (CT = 14)Work StationTask Task TimeTime RemainingFeasible tasksRemainingIF 5 9 A,D,G A 3 6 B,G G6 – – II D7 7 B, E B 2 5 C C4 1 – III E 4 10 H H9 1 – IV I59–b. First rule: Largest positional weight.Assembly Line Balancing Table (CT = 14)Work StationTask Task TimeTime RemainingFeasible tasks RemainingIF 5 9 A,D,G D7 2 – II G 6 8 A, E A 3 5 B,E B2 3 – III C 4 10 E E4 6 – IV H 95 I I5–c. %36.805645stations of no. x CT time Total Efficiency ===4. a. l.2. Minimum Ct = 1.3 minutesTask Following tasksa 4b 3c 3d 2e 3f 2g 1habd cfeghWork StationEligible Assign Time RemainingIdle TimeIa A 1.1 b,c,e, (tie)B 0.7C 0.4E 0.3 0.3 II d D 0.0 0.0 IIIf,g F 0.5G 0.2 0.2 IVh H 0.1 0.10.63. percent 54.11)3.1(46.CT x N time)(idle percent Idle ==∑=4. 420 min./day 323.1 ( 323)/1.3 min./OT Output rounds to copiers day CT cycle=== b. 1. inutes m 3.224.6N time Total CT ,6.4 time Total ==== 2. Assign a, b, c, d, and e to station 1: 2.3 minutes [no idle time]Assign f, g, and h to station 2: 2.3 minutes3. 420182.6 copiers /2.3OT Output day CT ===4.420 min./dayMaximum Ct is 4.6. Output 91.30 copiers /4.6 min./day cycle==7. 1 5 4 3 8 762Chapter 06 - Work Design and Measurement3. Element PR OT NT AF job ST1 .90.46.414 1.15 .4762 .85 1.505 1.280 1.15 1.4723 1.10.83.913 1.15 1.05041.00 1.16 1.160 1.15 1.334Total4.3328. A = 24 + 10 + 14 = 48 minutes per 4 hours.min 125.720.11x70.5ST .min 70.5)95(.6NT 20.24048A =-=====9. a. Element PR OT NT A ST1 1.10 1.19 1.309 1.15 1.5052 1.15 .83 .955 1.15 1.09831.05.56.588 1.15 .676b.01.A 00.2z 034.s 83.x ==== 222(.034)67.12~68.01(.83)zs n observations ax ⎛⎫⎛⎫===⎪ ⎪⎝⎭⎝⎭c. e = .01 minutes 47 to round ,24.4601.)034(.2e zs n 22=⎪⎭⎫⎝⎛=⎪⎭⎫ ⎝⎛=Chapter 07- Location Planning and Analysis1. Factor Local bank Steel mill Food warehouse Public school1. Convenience forcustomers H L M–H M–H2. Attractiveness ofbuilding H L M M–H3. Nearness to rawmaterials L H L M4. Large amounts ofpower L H L L5. Pollution controls L H L L6. Labor cost andavailability L M L L7. Transportationcosts L M–H M–H M8. Constructioncosts M H M M–HLocation (a) Location (b)4. Factor A B C Weight A B C1. Business Services 9 5 5 2/9 18/9 10/9 10/92. Community Services 7 6 7 1/9 7/9 6/9 7/93. Real Estate Cost 3 8 7 1/9 3/9 8/9 7/94. Construction Costs 5 6 5 2/9 10/9 12/9 10/95. Cost of Living 4 7 8 1/9 4/9 7/9 8/96. Taxes 5 5 5 1/9 5/9 5/9 4/97. Transportation 6 7 8 1/9 6/9 7/9 8/9Total 39 44 45 1.0 53/9 55/9 54/9 Each factor has a weight of 1/7.a. Composite Scores 39 44 45 7 7 7B orC is the best and A is least desirable.b. Business Services and Construction Costs both have a weight of 2/9; the other factors eachhave a weight of 1/9.5 x + 2 x + 2 x = 1 x = 1/9c. Composite ScoresA B C 53/9 55/9 54/9B is the best followed byC and then A.5.Locationx yA 3 7B 8 2C 4 6D 4 1E 6 4Totals 25 20-x =∑x i= 25 = 5.0 -y =∑y i= 20 = 4.0 n 5 n 5Hence, the center of gravity is at (5,4) and therefore the optimal location.Chapter 08 - Management of Quality1. ChecksheetWork Type FrequencyLube and Oil 12Brakes 7Tires 6Battery 4Transmission 1Total 30Pareto127641 Lube & Oil Brakes Tires Battery Trans.2 .The run charts seems to show a pattern of errors possibly linked to break times or the end of the shift. Perhaps workers are becoming fatigued. If so, perhaps two 10 minute breaks in the morning and again in the afternoon instead of one 20 minute break could reduce some errors. Also, errors are occurring during the last few minutes before noon and the end of the shift, and those periods should also be given management’s attention.4Power Per LamMissDidn’Not OutletDefectBurn LoosLampOtheCordbreak lunch3 2•• •• •• • ••• • ••• •••• ••• •• • •• • •••Chapter 9 - Quality Control4. Sample Mean Range179.48 2.6 Mean Chart: =X ± A 2-R = 79.96 ± 0.58(1.87) 2 80.14 2.3 = 79.96 ± 1.083 80.14 1.2UCL = 81.04, LCL = 78.884 79.60 1.7 Range Chart: UCL = D 4-R = 2.11(1.87) = 3.95 5 80.02 2.0LCL = D 3-R = 0(1.87) = 0680.381.4[Both charts suggest the process is in control: Neither has any points outside the limits.]6. n = 200 Control Limits = np p p )1(2-±Thus, UCL is .0234 and LCL becomes 0.Since n = 200, the fraction represented by each data point is half the amount shown. E.g., 1 defective = .005, 2 defectives = .01, etc.Sample 10 is too large.7. 857.714110c ==Control limits: 409.8857.7c 3c ±=± UCL is 16.266, LCL becomes 0.All values are within the limits.14. Let USL = Upper Specification Limit, LSL = Lower Specification Limit,X = Process mean, σ = Process standard deviationFor process H:}{capablenot ,0.193.93.04.1 ,938.min 04.1)32)(.3(1516393.)32)(.3(1.14153<===-=σ-=-=σ-pk C X USL LSL X 0096.)200(1325==p 0138.0096.200)9904(.0096.20096.±=±=For process K:.1}17.1,0.1min{17.1)1)(3(335.3630.1)1)(3(30333===-=σ-=-=σ- C X USL LSL X pk Assuming the minimum acceptable pk C is 1.33, since 1.0 < 1.33, the process is not capable.For process T:33.1}33.1,67.1min{33.1)4.0)(3(5.181.20367.1)4.0)(3(5.165.183===-=σ-=-=σ- C X USL LSL X pk Since 1.33 = 1.33, the process is capable.Chapter 10 - Aggregate Planning and Master Scheduling7. a.No backlogs are allowedPeriod Mar. Apr. May Jun. July Aug. Sep. TotalForecast 50 44 55 60 50 40 51 350 Output Regular 40 40 40 40 40 40 40 280 Overtime 8 8 8 8 8 3 8 51 Subcontract 2 0 3 12 2 0 0 19 Output - Forecast 0 4 –4 0 0 3 –3 Inventory Beginning 0 0 4 0 0 0 3 Ending 0 4 0 0 0 3 0 Average 0 2 2 0 0 1.5 1.5 7 Backlog 0 0 0 0 0 0 0 0 Costs: Regular 3,200 3,200 3,200 3,200 3,200 3,200 3,200 22,400 Overtime 960 960 960 960 960 360 960 6,120 Subcontract 280 0 420 1,680280 0 0 2,660 Inventory 0 20 20 0 0 15 15 70 Total4,4404,1804,6005,8404,4403,575 4,17531,250b. Level strategyPeriod Mar. Apr. May Jun. July Aug. Sep. Total Forecast 50 44 55 60 50 40 51 350 OutputRegular 40 40 40 40 40 40 40 280 Overtime 8 8 8 8 8 8 8 56 Subcontract 2 2 2 2 2 2 2 14 Output - Forecast 0 6 –5 –10 0 10 –1InventoryBeginning 0 0 6 1 0 0 1Ending 0 6 1 0 0 1 0Average 0 3 3.5 .5 0 .5 .5 8 Backlog 0 0 0 9 9 0 0 18 Costs:Regular 3,200 3,200 3,200 3,200 3,200 3,200 3,200 22,400 Overtime 960 960 960 960 960 960 960 6,720 Subcontract 280 280 280 280 280 280 280 1,960 Inventory 30 35 5 0 5 5 80 Backlog 180 180 360 Total 4,440 4,470 4,475 4,625 4,620 4,445 4,445 31,520 8.Period 1 2 3 4 5 6 TotalForecast 160 150 160 180 170 140 960OutputRegular 150 150 150 150 160 160 920Overtime 10 10 0 10 10 10 50Subcontract 0 0 10 10 0 0 20Output- Forecast 0 10 0 –10 0 0InventoryBeginning 0 0 10 10 0 0Ending 0 10 10 0 0 0Average 0 5 10 5 0 0 20Backlog 0 0 0 0 0 0 0Costs:Regular 7,500 7,500 7,500 7,500 8,000 8,000 46,000Overtime 750 750 0 750 750 750 3,750Subcontract 0 0 800 800 0 0 1,600Inventory 20 40 20 80Backlog 0 0 0 0 0 0Total 8,250 8,270 8,340 9,070 9,050 8,750 51,430Chapter 11 - MRP and ERP1. a. F: 2 G: 1 H: 1J: 2 x 2 = 4 L: 1 x 2 = 2 A: 1 x 4 = 4D: 2 x 4 = 8 J: 1 x 2 = 2 D: 1 x 2 = 2Totals: F = 2; G = 1; H = 1; J = 6; D = 10; L = 2; A = 4b.4. Master Schedule Day Beg. Inv. 1 2 3 4 5 6 7 Quantity100 150 200 TableBeg. Inv. 1 2 3 4 5 6 7 Gross requirements 100 150 200 Scheduled receipts Projected on hand Net requirements 100 150 200 Planned-order receipts 100 150 200 Planned-order releases 100 150 200Wood Sections Beg. Inv. 1 2 3 4 5 6 7 Gross requirements 200300 400 Scheduled receipts 100 Projected on hand 100100 Net requirements 100 300 400 Planned-order receipts 100 300 400 Planned-order releases400 400Braces Beg. Inv. 1 2 3 4 5 6 7 Gross requirements 300 450 600 Scheduled receipts Projected on hand 60 60 60 60 Net requirements 240 450 600 Planned-order receipts 240 450 600Planned-order releases 240 450 600StaplerTopBaseCoveSpri SlideBase Strik RubberSlidSpriLegs Beg.Inv.1 2 3 4 5 6 7Gross requirements 400 600 800Scheduled receiptsProjected on hand 120 120 120 120 88 88 71 Net requirements 280 600 800Planned-order receipts 308 660 880Planned-order releases 968 88010. Week 1 2 3 4Material 40 80 60 70Week 1 2 3 4Labor hr. 160 320 240 280Mach. hr. 120 240 180 210a. Capacity utilizationWeek 1 2 3 4Labor 53.3% 106.7% 80% 93.3%Machine 60% 120% 90% 105%b. C apacity utilization exceeds 100% for both labor and machine in week 2, and formachine alone in week 4.Production could be shifted to earlier or later weeks in which capacity isunderutilized. Shifting to an earlier week would result in added carrying costs;shifting to later weeks would mean backorder costs.Another option would be to work overtime. Labor cost would increase due toovertime premium, a probable decrease in productivity, and possible increase inaccidents.Chapter 12 - Inventory Management2. The following table contains figures on the monthly volume and unit costs for a random sample of 16 items for a list of 2,000 inventory items. DollarItemUnit Cost UsageUsageCategoryK34 10 200 2,000 C K35 25 600 15,000 A K36 36 150 5,400 B M10 16 25 400 C M20 20 80 1,600 C Z45 80 250 16,000 A F14 20 300 6,000 B F95 30 800 24,000 A F99 20 60 1,200 C D45 10 550 5,500 B D48 12 90 1,080 C D52 15 110 1,650 C D57 40 120 4,800 B N08 30 40 1,200 C P05 16 500 8,000 BP091030300Ca. See table.b. To allocate control efforts.c. It might be important for some reason other than dollar usage, such as cost of astockout, usage highly correlated to an A item, etc.3. D = 1,215 bags/yr. S = $10 H = $75a. bags HDS Q 187510)215,1(22===b. Q/2 = 18/2 = 9 bagsc.orders ordersbags bags Q D 5.67/ 18 215,1== d . S QD H 2/Q TC +=350,1$675675)10(18215,1)75(218=+=+=e. Assuming that holding cost per bag increases by $9/bag/yearQ ==84)10)(215,1(217 bags71.428,1$71.714714)10(17215,1)84(217=+=+=TCIncrease by [$1,428.71 – $1,350] = $78.714.D = 40/day x 260 days/yr. = 10,400 packagesS = $60 H = $30a. oxes b 20496.2033060)400,10(2H DS 2Q 0====b. S QD H 2Q TC +=82.118,6$82.058,3060,3)60(204400,10)30(2204=+=+=c. Yesd. )60(200400,10)30(2200TC 200+=TC 200 = 3,000 + 3,120 = $6,1206,120 – 6,118.82 (only $1.18 higher than with EOQ, so 200 is acceptable.)7.H = $2/month S = $55D 1 = 100/month (months 1–6)D 2 = 150/month (months 7–12)a. 16.74255)100(2Q :D H DS2Q 010===83.90255)150(2Q :D 02==b. The EOQ model requires this.c. Discount of $10/order is equivalent to S – 10 = $45 (revised ordering cost)1–6 TC74 = $148.32180$)45(150100)2(2150TC 145$)45(100100)2(2100TC *140$)45(50100)2(250TC 15010050=+==+==+=7–12 TC 91 =$181.66195$)45(150150)2(2150TC *5.167$)45(100150)2(2100TC 185$)45(50150)2(250TC 15010050=+==+==+=10. p = 50/ton/day u = 20 tons/day200 days/yr. S = $100 H = $5/ton per yr.a. bags] [10,328 tons 40.5162050505100)000,4(2u p p H DS 2Q 0=-=-=b. ]bags 8.196,6 .approx [ tons 84.309)30(504.516)u p (P Q I max ==-=Average is92.154248.309:2I max =tons [approx. 3,098 bags] c. Run length =days 33.10504.516P Q == d. Runs per year = 8] approx .[ 7.754.516000,4QD == e. Q ' = 258.2TC =S QD H 2I max + TC orig. = $1,549.00 TC rev. = $ 774.50Savings would be $774.50D= 20 tons/day x 20015. RangeP H Q D = 4,900 seats/yr. 0–999 $5.00 $2.00 495 H = .4P 1,000–3,999 4.95 1.98 497 NF S = $50 4,000–5,999 4.90 1.96 500 NF 6,000+4.851.94503 NFCompare TC 495 with TC for all lower price breaks:TC 495 =495 ($2) + 4,900($50) + $5.00(4,900) = $25,490 2 495 TC 1,000 = 1,000 ($1.98) + 4,900($50) + $4.95(4,900) = $25,4902 1,000 TC 4,000 = 4,000 ($1.96) + 4,900($50) + $4.90(4,900) = $27,9912 4,000 TC 6,000 = 6,000 ($1.94) + 4,900($50) + $4.85(4,900) = $29,6262 6,000Hence, one would be indifferent between 495 or 1,000 units 22. d = 30 gal./day ROP = 170 gal. LT = 4 days,ss = Z σd LT = 50 galRisk = 9% Z = 1.34 Solving, σd LT = 37.31 3% Z = 1.88, ss=1.88 x 37.31 = 70.14 gal.Chapter 13 - JIT and Lean Operations1. N = ?N = DT(1 + X)D = 80 pieces per hourC T = 75 min. = 1.25 hr. = 80(1.25) (1.35)= 3C = 45 45X = .35• •• •495 497 500 5031,0004,000 6,000QuantityTC4. The smallest daily quantity evenly divisible into all four quantities is 3. Therefore, usethree cycles.Product Daily quantity Units per cycleA 21 21/3 = 7B 12 12/3 = 4C 3 3/3 = 1D 15 15/3 = 55.a. Cycle 1 2 3 4A 6 6 5 5B 3 3 3 3C 1 1 1 1D 4 4 5 5E 2 2 2 2 b. Cycle 1 2A 11 11B 6 6C 2 2D 8 8E 4 4c. 4 cycles = lower inventory, more flexibility2 cycles = fewer changeovers7. Net available time = 480 – 75 = 405. Takt time = 405/300 units per day = 1.35 minutes. Chapter 15 - Scheduling6. a. FCFS: A–B–C–DSPT: D–C–B–AEDD: C–B–D–ACR: A–C–D–BFCFS: Job time Flow time Due date DaysJob (days) (days) (days) tardyA 14 14 20 0B 10 24 16 8C 7 31 15 16D 6 37 17 2037 106 44SPT: Job time Flow time Due date Days Job (days) (days) (days) tardyD 6 6 17 0C 7 13 15 0B 10 23 16 7A 14 37 20 1737 79 24EDD: Job time Flow time Due date DaysJob (days) (days) (days) tardyC 7 7 15 0B 10 17 16 1D 6 23 17 6A 14 37 20 1784 24Critical RatioJob Processing Time(Days) Due Date Critical Ratio CalculationA 14 20 (20 – 0) / 14 = 1.43B 10 16 (16 – 0) /10 = 1.60C 7 15 (15 – 0) / 7 = 2.14D 6 17 (17 – 0) / 6 = 2.83Job A has the lowest critical ratio, therefore it is scheduled first and completed on day 14. After the completion of Job A, the revised critical ratios are:Job Processing Time(Days) Due Date Critical Ratio CalculationA –––B 10 16 (16 – 14) /10 = 0.20C 7 15 (15 – 14) / 7 = 0.14D 6 17 (17 – 14) / 6 = 0.50Job C has the lowest critical ratio, therefore it is scheduled next and completed on day 21. After the completion of Job C, the revised critical ratios are:Job Processing Time(Days) Due Date Critical Ratio CalculationA –––B 10 16 (16 – 21) /10 = –0.50C –––D 6 17 (17 – 21) / 6 = –0.67Job D has the lowest critical ratio therefore it is scheduled next and completed on day 27. The critical ratio sequence is A –C –D –B and the makespan is 37 days. Critical Ratio sequenceProcessing Time(Days)Flow time Due Date TardinessA 14 14 20 0 C 7 21 15 6 D 6 27 17 10 B1037 16 21 ∑9937b.ardi Flow time Average flow time Number of jobsDays tardy Average job t ness Number of jobs Flow timeAverage number of jobs at the center Makespan==∑=FCFS SPT EDD CR26.50 19.75 21.00 24.75 11.0 6.00 6.00 9.25 2.86 2.142.272.67c. SPT is superior.9.Time (hr.) Sequence of assignment:Order Step 1 Step 2A 1.20 1.40 .80 [C] last (or 7th)B 0.90 1.30 .90 [B] firstC 2.00 0.80 1.20 [A] 2ndD 1.70 1.50 1.30 [G] 3rdE 1.60 1.80 1.60 [E] 4thF 2.20 1.75 1.50 [D] 6th G1.301.401.75[F]5thThus, the sequence is b-a-g-e-f-d-c.。
《运营管理》课程习题及答案_修订版(1).pdf

3、对多品种小批量生产一般采用(
)布置。
A、流水线 B、按功能 C、固定位置 D、生产单元
4、运营战略属于( ) A.公司级战略 B. 事业部级战略
C. 职能级战略
D. 作业层战略
5、从市场定位开始入手,而这种市场定位是根据企业对其选择的目标市场的理 解以及竞争对手的市场行为而得出来的匹配是() A.市场驱动的匹配 B. 运营能力驱动的匹配 C. 实践领域的匹配 D. 可持续性
A.单件生产
B.小批生产
C. 大批生产
D. 工程项目
3、汽车装配应采用( )
A.流水线布置
B. 定位布置
C.对象专业化布置 D. 以上都不是
4、计算机辅助设计是指利用计算机帮助( )
A.产品设计
B.决策制定
C. 质量控制
D. 流程控制
5、以下哪项与成组技术紧密相关( )
A.数控机床
B. 机器人 C. 单元制造
二、多项选择题
1、一般来说,企业的战略可以划分的层次有(
A.公司发展战略
B. 公司总体战略
D.公司经营战略
E. 职能级战略
) C. 公司营销战略
2、影响运营战略制定的因素有(
)
A.市场需求及其变化
B. 技术进步 C. 企业整体经营目标
D.供应市场
E. 各部门职能战略
3、企业根据自身条件可以确定的竞争重点包括(
7、企业经营活动中的最主要部分是( )
A.产品研发
B. 产品设计
C. 生产运营活动
D. 生产系统的选择
8、下列哪项不是生产运作管理的目标 A、质量 B 、成本 C、价格 D 、柔性
()
9、按照生产要素密集程度和顾客接触程度划分,医院是:
《运营管理》威廉.史蒂文森著,张群、张杰、马风才译,机械工业出版社(第11版课后习题答案)

23 0.96 0.01749
材料/磅 多要素生产率
1
30000 6
450
9900 3.03
2
33600 7
470
11220 2.99
3
32200 7
460
11160 2.89
4
35400 8
480
12480 2.84
第4题 工人
买设备前 买设备后
美元/小时 生产率
每小时产量 劳动成本 机器成本 劳动 多要素
5
80
10
40
16
0.89
第1题
庆典 婚宴
工人
套餐 8 6
生产率
300
37.5 低
240
40 高
为什
第2题 周
小组人数 铺放码数 生产率
1
4
96
24
2
3
72
24
3
4
92
23
4
2
50
25
5
3
69
23
6
2
52
26
人数与生产率?
第3题 周工作
40H
工资 12﹩/H
材料成本 6﹩/磅
单价 140
管理费 周劳动成 本1.5倍
周
产量 工人
2
3.5
400 6.30
28
2
3.6
400 6.71
第9题 雇员
周工作/ 人
工时费/H
合约数
材料费 管理费
3
40
25
360 1000 9000
3
生产率 1.938462
2小题 生产率
日接待顾 客
运营管理》-课后习题答案
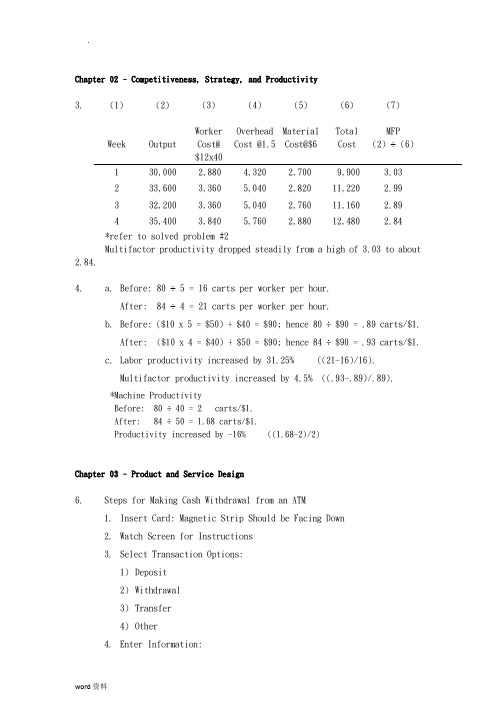
Chapter 02 - Competitiveness, Strategy, and Productivity3. (1) (2) (3) (4) (5) (6) (7)Week Output WorkerCost@$12x40OverheadCost @1.5MaterialCost@$6TotalCostMFP(2) ÷ (6)1 30,000 2,880 4,320 2,700 9,900 3.032 33,600 3,360 5,040 2,820 11,220 2.993 32,200 3,360 5,040 2,760 11,160 2.894 35,400 3,840 5,760 2,880 12,480 2.84*refer to solved problem #2Multifactor productivity dropped steadily from a high of 3.03 to about 2.84.4. a. Before: 80 ÷ 5 = 16 carts per worker per hour.After: 84 ÷ 4 = 21 carts per worker per hour.b. Before: ($10 x 5 = $50) + $40 = $90; hence 80 ÷ $90 = .89 carts/$1.After: ($10 x 4 = $40) + $50 = $90; hence 84 ÷ $90 = .93 carts/$1.c. Labor productivity increased by 31.25% ((21-16)/16).Multifactor productivity increased by 4.5% ((.93-.89)/.89).*Machine ProductivityBefore: 80 ÷ 40 = 2 carts/$1.After: 84 ÷ 50 = 1.68 carts/$1.Productivity increased by -16% ((1.68-2)/2)Chapter 03 - Product and Service Design6. Steps for Making Cash Withdrawal from an ATM1. Insert Card: Magnetic Strip Should be Facing Down2. Watch Screen for Instructions3. Select Transaction Options:1) Deposit2) Withdrawal3) Transfer4) Other4. Enter Information:1) PIN Number2) Select a Transaction and Account3) Enter Amount of Transaction5. Deposit/Withdrawal:1) Deposit —place in an envelope (which you’ll find near or in theATM) and insert it into the deposit slot2) Withdrawal —lift the “Withdrawal Door,” being careful to remove all cash 6. Remove card and receipt (which serves as the transaction record)8.Chapter 04 - Strategic Capacity Planning for Products and Services2. %80capacityEffective outputActual Efficiency ==Actual output = .8 (Effective capacity) Effective capacity = .5 (Design capacity) Actual output = (.5)(.8)(Effective capacity) Actual output = (.4)(Design capacity) Actual output = 8 jobs Utilization = .4capacityDesign outputActual =n Utilizatiojobs 204.8capacity Effective output Actual Capacity Design ===10. a. Given: 10 hrs. or 600 min. of operating time per day. 250 days x 600 min. = 150,000 min. per year operating time.Total processing time by machineProductA B C 1 48,000 64,000 32,000 2 48,000 48,000 36,000 3 30,000 36,000 24,000 460,00060,00030,000Total 186,000 208,000 122,000machine181.000,150000,122machine 238.1000,150000,208machine224.1000,150000,186≈==≈==≈==C B A N N NYou would have to buy two “A” machines at a total cost of $80,000, or two “B” machines at a total cost of $60,000, or one “C” machine at $80,000.b. Total cost for each type of machine:A (2): 186,000 min ÷ 60 = 3,100 hrs. x $10 = $31,000 + $80,000 = $111,000B (2) : 208,000 ÷ 60 = 3,466.67 hrs. x $11 = $38,133 + $60,000 = $98,133 C(1): 122,000 ÷ 60 = 2,033.33 hrs. x $12 = $24,400 + $80,000 = $104,400Buy 2 Bs —these have the lowest total cost.Chapter 05 - Process Selection and Facility Layout3.Desired output = 4Operating time = 56 minutesunit per minutes 14hourper units 4hourper minutes 65output Desired time Operating CT ===Task # of Following tasks PositionalWeightA 4 23B 3 20C 2 18D 3 25E 2 18F 4 29G 3 24H 1 14 I5a. First rule: most followers. Second rule: largest positional weight.Assembly Line Balancing Table (CT = 14)b. First rule: Largest positional weight.Assembly Line Balancing Table (CT = 14)c. %36.805645stations of no. x CT time Total Efficiency ===4. a. l.2. Minimum Ct = 1.3 minutesTask Following tasksa 4b 3c 3d 2e3f 2g 1h3. percent 54.11)3.1(46.CT x N time)(idle percent Idle ==∑=4. 420 min./day 323.1 ( 323)/1.3 min./OT Output rounds to copiers day CT cycle=== b. 1. inutes m 3.224.6N time Total CT ,6.4 time Total ==== 2. Assign a, b, c, d, and e to station 1: 2.3 minutes [no idle time]Assign f, g, and h to station 2: 2.3 minutes3. 420182.6 copiers /2.3OT Output day CT ===4.420 min./dayMaximum Ct is 4.6. Output 91.30 copiers /4.6 min./day cycle==7.Chapter 06 - Work Design and Measurement3.Element PR OT NT AF job ST1 .90 .46 .414 1.15 .4762 .85 1.505 1.280 1.15 1.4723 1.10 .83 .913 1.15 1.050 41.00 1.16 1.160 1.15 1.334Total4.3328. A = 24 + 10 + 14 = 48 minutes per 4 hours.min 125.720.11x70.5ST .min 70.5)95(.6NT 20.24048A =-=====9. a. Element PR OT NT A ST1 1.10 1.19 1.309 1.15 1.5052 1.15 .83 .955 1.15 1.09831.05 .56 .588 1.15 .676b.01.A 00.2z 034.s 83.x ==== 222(.034)67.12~68.01(.83)zs n observations ax ⎛⎫⎛⎫===⎪ ⎪⎝⎭⎝⎭ c. e = .01 minutes 47 to round ,24.4601.)034(.2e zs n 22=⎪⎭⎫⎝⎛=⎪⎭⎫ ⎝⎛=Chapter 07- Location Planning and Analysis1.Factor Local bank Steel mill Food warehouse Public school 1. Convenience forcustomers H L M –H M –H 2. Attractivenessof building H L M M –H 3. Nearness to rawmaterials L H L M 4. Large amountsof power L H L L 5. Pollutioncontrols L H L L 6. Labor cost andavailability L M L L 7. Transportationcosts L M –H M –H M8. Constructioncosts M H M M –HLocation (a) Location (b)4. Factor A B C WeightA B C1.Business Services 9 5 5 2/9 18/9 10/9 10/92.Community Services 7 6 7 1/9 7/9 6/9 7/93.Real Estate Cost 3 8 7 1/9 3/9 8/9 7/94.Construction Costs 5 6 5 2/9 10/9 12/9 10/95.Cost of Living 4 7 8 1/9 4/9 7/9 8/96.Taxes 5 5 5 1/9 5/9 5/9 4/97.Transportation 6 7 8 1/9 6/9 7/9 8/9 Total 39 44 45 1.0 53/9 55/9 54/9 Each factor has a weight of 1/7.a . Composite Scores39 44 457 7 7B orC is the best and A is least desirable.b . Business Services and Construction Costs both have a weight of 2/9; the other factors each have a weight of 1/9.5 x + 2 x + 2 x = 1 x = 1/9c . Composite ScoresA B C53/9 55/9 54/9B is the best followed byC and then A.5.Locationx yA 3 7B 8 2C 4 6D 4 1E 6 4Totals 25 20-x =∑x i= 25 = 5.0 -y =∑y i= 20 = 4.0 n 5 n 5Hence, the center of gravity is at (5,4) and therefore the optimallocation.Chapter 08 - Management of Quality1. ChecksheetWork Type FrequencyLube and Oil 12Brakes 7Tires 6Battery 4Transmission 1Total 30ParetoLube & Oil Brakes Tires Battery Trans.2 .The run charts seems to show a pattern of errors possibly linked to break times or the end of the shift. Perhaps workers are becoming fatigued. If so, perhaps two 10 minute breaks in the morning and again in the afternoon instead of one 20 minute break could reduce some errors. Also, errors are occurring during the last few minutes before noon and the end of the shift, and those periods should also be given management’s attention.4break lunch break3 2 1 0∙ ∙ ∙∙ ∙ ∙ ∙∙∙ ∙ ∙ ∙∙∙∙∙∙∙ ∙∙∙ ∙∙ ∙ ∙∙ ∙ ∙∙∙Chapter 9 - Quality Control4. Sample Mean Range179.48 2.6 Mean Chart: =X ± A 2-R = 79.96 ± 0.58(1.87) 2 80.14 2.3 = 79.96 ± 1.083 80.14 1.2UCL = 81.04, LCL = 78.884 79.60 1.7 Range Chart: UCL = D 4-R = 2.11(1.87) = 3.95 5 80.02 2.0LCL = D 3-R = 0(1.87) = 0680.381.4[Both charts suggest the process is in control: Neither has any points outside the limits.]6. n = 200 Control Limits = np p p )1(2-±Thus, UCL is .0234 and LCL becomes 0.Since n = 200, the fraction represented by each data point is half the amount shown. E.g., 1 defective = .005, 2 defectives = .01, etc. Sample 10 is too large.7. 857.714110c ==Control limits: 409.8857.7c 3c ±=± UCL is 16.266, LCL becomes 0.All values are within the limits.14. Let USL = Upper Specification Limit, LSL = Lower Specification Limit,X = Process mean, σ = Process standard deviationFor process H:0096.)200(1325==p 0138.0096.200)9904(.0096.20096.±=±=}{capablenot ,0.193.93.04.1 ,938.min 04.1)32)(.3(1516393.)32)(.3(1.14153<===-=σ-=-=σ-pk C X USL LSL XFor process K:.1}17.1,0.1min{17.1)1)(3(335.3630.1)1)(3(30333===-=σ-=-=σ- C X USL LSL X pk Assuming the minimum acceptable pk C is 1.33, since 1.0 < 1.33, the process is not capable.For process T: 33.1}33.1,67.1min{33.1)4.0)(3(5.181.20367.1)4.0)(3(5.165.183===-=σ-=-=σ- C X USL LSL X pk Since 1.33 = 1.33, the process is capable.Chapter 10 - Aggregate Planning and Master Scheduling7. a. No backlogs are allowedPeriodForecast Output Regular Overtime Subcontract Inventory Beginning Ending Average Backlog Costs:RegularOvertimeSubcontractInventoryTotalb. Level strategyPeriodForecastOutputRegularOvertimeSubcontractInventoryBeginningEndingAverageBacklogCosts:RegularOvertimeSubcontractInventoryBacklogTotal8.PeriodForecastOutputRegularOvertimeSubcontractInventoryBeginningEndingAverageBacklogCosts:RegularOvertimeSubcontractInventoryBacklogTotalChapter 11 - MRP and ERP1. a. F: 2G: 1 H: 1 J: 2 x 2 = 4 L: 1 x 2 = 2 A: 1 x 4 = 4 D: 2 x 4 = 8 J: 1 x 2 = 2 D: 1 x 2 = 2Totals: F = 2; G = 1; H = 1; J = 6; D = 10; L = 2; A = 44. Master Schedule10. Week 1 2 3 4Material 40 80 60 70Week 1 2 3 4Labor hr. 160 320 240 280Mach. hr. 120 240 180 210a. Capacity utilizationWeek 1 2 3 4Labor 53.3% 106.7% 80% 93.3%Machine 60% 120% 90% 105%b. Capacity utilization exceeds 100% for both labor and machine in week2, and for machine alone in week 4.Production could be shifted to earlier or later weeks in which capacityis underutilized. Shifting to an earlier week would result in addedcarrying costs; shifting to later weeks would mean backorder costs.Another option would be to work overtime. Labor cost would increase dueto overtime premium, a probable decrease in productivity, and possibleincrease in accidents.Chapter 12 - Inventory Management2. The following table contains figures on the monthly volume and unit costs for a random sample of 16 items for a list of 2,000 inventory items.a. See table.b. To allocate control efforts.c. It might be important for some reason other than dollar usage, suchas cost of a stockout, usage highly correlated to an A item, etc.3. D = 1,215 bags/yr. S = $10 H = $75a. bags HDS Q 187510)215,1(22===b. Q/2 = 18/2 = 9 bagsc.orders ordersbags bags Q D 5.67/ 18 215,1== d . S QD H 2/Q TC +=350,1$675675)10(18215,1)75(218=+=+=e. Assuming that holding cost per bag increases by $9/bag/yearQ ==84)10)(215,1(217 bags71.428,1$71.714714)10(17215,1)84(217=+=+=TC Increase by [$1,428.71 – $1,350] = $78.714. D = 40/day x 260 days/yr. = 10,400 packagesS = $60 H = $30a. oxes b 20496.2033060)400,10(2H DS 2Q 0====b. S QD H 2Q TC +=82.118,6$82.058,3060,3)60(204400,10)30(2204=+=+=c. Yesd. )60(200400,10)30(2200TC 200+=TC 200 = 3,000 + 3,120 = $6,1206,120 – 6,118.82 (only $1.18 higher than with EOQ, so 200 isacceptable.)7. H = $2/month S = $55D 1 = 100/month (months 1–6)D 2 = 150/month (months 7–12)a. 16.74255)100(2Q :D H DS2Q 010===83.90255)150(2Q :D 02==b. The EOQ model requires this.c. Discount of $10/order is equivalent to S – 10 = $45 (revised ordering cost)1–6 TC74 = $148.32180$)45(150100)2(2150TC 145$)45(100100)2(2100TC *140$)45(50100)2(250TC 15010050=+==+==+=7–12 TC 91 = $181.66195$)45(150150)2(2150TC *5.167$)45(100150)2(2100TC 185$)45(50150)2(250TC 15010050=+==+==+=10. p = 50/ton/day u = 20 tons/day200 days/yr.S = $100H = $5/ton per yr.a. bags] [10,328 tons 40.5162050505100)000,4(2u p p H DS 2Q 0=-=-=b. ]bags 8.196,6 .approx [ tons 84.309)30(504.516)u p (P Q I max ==-=Average is92.154248.309:2I max =tons [approx. 3,098 bags] c. Run length =days 33.10504.516P Q == d. Runs per year = 8] approx .[ 7.754.516000,4QD ==e. Q ' = 258.2D= 20 tons/day x 200 days/yr. = 4,000 tons/yr.TC =S QDH 2I max + TC orig. = $1,549.00 TC rev. = $ 774.50Savings would be$774.5015.RangePHQD = 4,900 seats/yr. 0–999 $5.00 $2.00 495 H = .4P 1,000–3,9994.95 1.98 497 NFS = $50 4,000–5,9994.90 1.96 500 NF6,000+ 4.85 1.94 503 NFCompare TC 495 with TC for all lower price breaks:TC 495 = 495 ($2) + 4,900($50) + $5.00(4,900) = $25,4902 495TC 1,000 = 1,000 ($1.98) + 4,900($50) + $4.95(4,900) = $25,4902 1,000 TC 4,000 = 4,000 ($1.96) + 4,900($50) + $4.90(4,900) = $27,9912 4,000 TC 6,000 = 6,000 ($1.94) + 4,900($50) + $4.85(4,900) = $29,6262 6,000Hence, one would be indifferent between 495 or 1,000 units22. d = 30 gal./day ROP = 170 gal.QuantityTCLT = 4 days,ss = Zσd LT = 50 galRisk = 9% Z = 1.34 Solving, σd LT = 37.313% Z = 1.88, ss=1.88 x 37.31 = 70.14 gal. Chapter 13 - JIT and Lean Operations1. N = ?N = DT(1 + X)D = 80 pieces per hour CT = 75 min. = 1.25 hr.= 80(1.25)(1.35) = 3C = 45 45X = .354. The smallest daily quantity evenly divisible into all four quantities is3. Therefore, use three cycles.Product Daily quantity Units per cycleA 21 21/3 = 7B 12 12/3 = 4C 3 3/3 = 1D 15 15/3 = 55.a. Cycle 1 2 3 4A 6 6 5 5B 3 3 3 3C 1 1 1 1D 4 4 5 5E 2 2 2 2 b. Cycle 1 2A 11 11B 6 6C 2 2D 8 8E 4 4c. 4 cycles = lower inventory, more flexibility2 cycles = fewer changeovers7. Net available time = 480 –75 = 405. Takt time = 405/300 units per day = 1.35 minutes.Chapter 15 - Scheduling6. a. FCFS: A–B–C–DSPT: D–C–B–AEDD: C–B–D–ACR: A–C–D–BFCFS: Job time Flow time Due date DaysJob (days) (days) (days) tardyA 14 14 20 0B 10 24 16 8C 7 31 15 16D 6 37 17 2037 106 44SPT: Job time Flow time Due date DaysJob (days) (days) (days) tardyD 6 6 17 0C 7 13 15 0B 10 23 16 7A 14 37 20 1737 79 24EDD:Critical Ratiocompleted on day 14. After the completion of Job A, the revised critical ratios are:completed on day 21. After the completion of Job C, the revised critical ratios are:Job D has the lowest critical ratio therefore it is scheduled next and completed on day 27.The critical ratio sequence is A –C –D –B and the makespan is 37 days.b.ardi Flow time Average flow time Number of jobsDays tardy Average job t ness Number of jobs Flow timeAverage number of jobs at the center Makespan==∑=FCFS SPT EDD CR26.50 19.75 21.00 24.75 11.0 6.00 6.00 9.252.86 2.14 2.27 2.67c. SPT is superior.9.Thus, the sequence is b-a-g-e-f-d-c.。
《运营管理》课程习题和答案解析_修订版
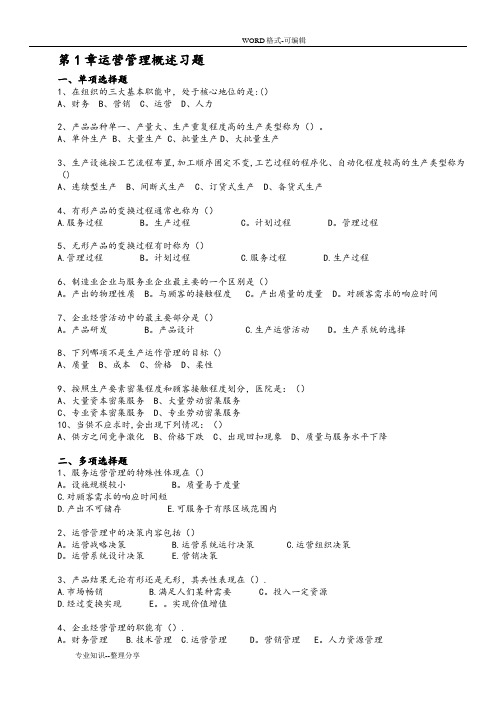
第1章运营管理概述习题一、单项选择题1、在组织的三大基本职能中,处于核心地位的是:()A、财务B、营销C、运营D、人力2、产品品种单一、产量大、生产重复程度高的生产类型称为()。
A、单件生产B、大量生产C、批量生产D、大批量生产3、生产设施按工艺流程布置,加工顺序固定不变,工艺过程的程序化、自动化程度较高的生产类型称为()A、连续型生产B、间断式生产C、订货式生产D、备货式生产4、有形产品的变换过程通常也称为()A.服务过程 B。
生产过程 C。
计划过程 D。
管理过程5、无形产品的变换过程有时称为()A.管理过程 B。
计划过程 C.服务过程 D.生产过程6、制造业企业与服务业企业最主要的一个区别是()A。
产出的物理性质 B。
与顾客的接触程度 C。
产出质量的度量 D。
对顾客需求的响应时间7、企业经营活动中的最主要部分是()A。
产品研发 B。
产品设计 C.生产运营活动 D。
生产系统的选择8、下列哪项不是生产运作管理的目标()A、质量B、成本C、价格D、柔性9、按照生产要素密集程度和顾客接触程度划分,医院是:()A、大量资本密集服务B、大量劳动密集服务C、专业资本密集服务D、专业劳动密集服务10、当供不应求时,会出现下列情况:()A、供方之间竞争激化B、价格下跌C、出现回扣现象D、质量与服务水平下降二、多项选择题1、服务运营管理的特殊性体现在()A。
设施规模较小 B。
质量易于度量C.对顾客需求的响应时间短D.产出不可储存E.可服务于有限区域范围内2、运营管理中的决策内容包括()A。
运营战略决策 B.运营系统运行决策 C.运营组织决策D。
运营系统设计决策 E.营销决策3、产品结果无论有形还是无形,其共性表现在().A.市场畅销B.满足人们某种需要 C。
投入一定资源D.经过变换实现 E。
实现价值增值4、企业经营管理的职能有().A。
财务管理 B.技术管理 C.运营管理 D。
营销管理 E。
人力资源管理5、运营管理的计划职能具体包括以下方面内容()A.目标 B。
《运营管理》课后习题答案

Chapter 02 - Competitiveness, Strategy, and Productivity3. (1) (2) (3) (4) (5) (6) (7)Week Output WorkerCost@$12x40Overhead********MaterialCost@$6TotalCostMFP(2) ÷ (6)1 30,000 2,880 4,320 2,700 9,900 3.032 33,600 3,360 5,040 2,820 11,220 2.993 32,200 3,360 5,040 2,760 11,160 2.894 35,400 3,840 5,760 2,880 12,480 2.84*refer to solved problem #2Multifactor productivity dropped steadily from a high of 3.03 to about 2.84.4. a. Before: 80 ÷ 5 = 16 carts per worker per hour.After: 84 ÷ 4 = 21 carts per worker per hour.b. Before: ($10 x 5 = $50) + $40 = $90; hence 80 ÷ $90 = .89 carts/$1.After: ($10 x 4 = $40) + $50 = $90; hence 84 ÷ $90 = .93 carts/$1.c. Labor productivity increased by 31.25% ((21-16)/16).Multifactor productivity increased by 4.5% ((.93-.89)/.89).*Machine ProductivityBefore: 80 ÷ 40 = 2 carts/$1.After: 84 ÷ 50 = 1.68 carts/$1.Productivity increased by -16% ((1.68-2)/2)Chapter 03 - Product and Service Design6. Steps for Making Cash Withdrawal from an ATM1. Insert Card: Magnetic Strip Should be Facing Down2. Watch Screen for Instructions3. Select Transaction Options:1) Deposit2) Withdrawal3) Transfer4) Other4. Enter Information:1) PIN Number2) Select a Transaction and Account3) Enter Amount of Transaction5. Deposit/Withdrawal:1) Deposit —place in an envelope (which you’ll fin d near or in theATM) and insert it into the deposit slot2) Withdrawal —lift the “Withdrawal Door,” being careful to remove all cash 6. Remove card and receipt (which serves as the transaction record)8.Chapter 04 - Strategic Capacity Planning for Products and Services2. %80capacityEffective outputActual Efficiency ==Actual output = .8 (Effective capacity) Effective capacity = .5 (Design capacity) Actual output = (.5)(.8)(Effective capacity) Actual output = (.4)(Design capacity) Actual output = 8 jobs Utilization = .4capacityDesign outputActual =n Utilizatiojobs 204.8capacity Effective output Actual Capacity Design ===10. a. Given: 10 hrs. or 600 min. of operating time per day. 250 days x 600 min. = 150,000 min. per year operating time.Total processing time by machineProductA B C 1 48,000 64,000 32,000 2 48,000 48,000 36,000 3 30,000 36,000 24,000 460,00060,00030,000Total 186,000 208,000 122,000machine181.000,150000,122machine 238.1000,150000,208machine224.1000,150000,186≈==≈==≈==C B A N N NYou would have to buy two “A” machines at a total cost of $80,000, or two “B” machines at a total cost of $60,000, or one “C” machine at $80,000.b. Total cost for each type of machine:A (2): 186,000 min ÷ 60 = 3,100 hrs. x $10 = $31,000 + $80,000 = $111,000B (2) : 208,000 ÷ 60 = 3,466.67 hrs. x $11 = $38,133 + $60,000 = $98,133 C(1): 122,000 ÷ 60 = 2,033.33 hrs. x $12 = $24,400 + $80,000 = $104,400Buy 2 Bs —these have the lowest total cost.Chapter 05 - Process Selection and Facility Layout3.Desired output = 4Operating time = 56 minutesunit per minutes 14hourper units 4hourper minutes 65output Desired time Operating CT ===Task # of Following tasks PositionalWeight A 4 23 B 3 20 C 2 18 D 3 25 E 2 18 F 4 29 G 3 24 H 1 14 I5a. First rule: most followers. Second rule: largest positionalweight.Assembly Line Balancing Table (CT = 14)b. First rule: Largest positional weight.Assembly Line Balancing Table (CT = 14)c. %36.805645stations of no. x CT time Total Efficiency ===4. a. l.2. Minimum Ct = 1.3 minutesTask Following tasksa 4b 3c 3d2e 3f 2g 1h3. percent 54.11)3.1(46.CT x N time)(idle percent Idle ==∑=4. 420 min./day 323.1 ( 323)/1.3 min./OT Output rounds to copiers day CT cycle=== b. 1. inutes m 3.224.6N time Total CT ,6.4 time Total ==== 2. Assign a, b, c, d, and e to station 1: 2.3 minutes [no idle time]Assign f, g, and h to station 2: 2.3 minutes3. 420182.6 copiers /2.3OT Output day CT ===4.420 min./dayMaximum Ct is 4.6. Output 91.30 copiers /4.6 min./day cycle==7.Chapter 06 - Work Design and Measurement3.Element PR OT NT AF job ST1 .90 .46 .414 1.15 .4762 .85 1.505 1.280 1.15 1.4723 1.10 .83 .913 1.15 1.050 41.00 1.16 1.160 1.15 1.334Total4.3328. A = 24 + 10 + 14 = 48 minutes per 4 hours.min 125.720.11x70.5ST .min 70.5)95(.6NT 20.24048A =-=====9. a. Element PR OT NT A ST1 1.10 1.19 1.309 1.15 1.5052 1.15 .83 .955 1.15 1.09831.05 .56 .588 1.15 .676b.01.A 00.2z 034.s 83.x ==== 222(.034)67.12~68.01(.83)zs n observations ax ⎛⎫⎛⎫===⎪ ⎪⎝⎭⎝⎭ c. e = .01 minutes 47 to round ,24.4601.)034(.2e zs n 22=⎪⎭⎫⎝⎛=⎪⎭⎫ ⎝⎛=Chapter 07- Location Planning and Analysis1. Factor Local bank Steel mill Food warehouse Public school1. Convenience forcustomers H L M–H M–H2. Attractivenessof building H L M M–H3. Nearness to rawmaterials L H L M4. Large amountsof power L H L L5. Pollutioncontrols L H L L6. Labor cost andavailability L M L L7. Transportationcosts L M–H M–H M8. Constructioncosts M H M M–HLocation (a) Location (b)4. Factor A B C WeightA B C1.Business Services 9 5 5 2/9 18/9 10/9 10/92.Community Services 7 6 7 1/9 7/9 6/9 7/93.Real Estate Cost 3 8 7 1/9 3/9 8/9 7/94.Construction Costs 5 6 5 2/9 10/9 12/9 10/95.Cost of Living 4 7 8 1/9 4/9 7/9 8/96.Taxes 5 5 5 1/9 5/9 5/9 4/97.Transportation 6 7 8 1/9 6/9 7/9 8/9 Total 39 44 45 1.0 53/9 55/9 54/9 Each factor has a weight of 1/7.a . Composite Scores39 44 457 7 7B orC is the best and A is least desirable.b . Business Services and Construction Costs both have a weight of 2/9; the other factors each have a weight of 1/9.5 x + 2 x + 2 x = 1 x = 1/9c . Composite ScoresA B C53/9 55/9 54/9B is the best followed byC and then A.5.Locationx yA 3 7B 8 2C 4 6D 4 1E 6 4Totals 25 20-x =∑x i= 25 = 5.0 -y =∑y i= 20 = 4.0 n 5 n 5Hence, the center of gravity is at (5,4) and therefore the optimallocation.Chapter 08 - Management of Quality1. ChecksheetWork Type FrequencyLube and Oil 12Brakes 7Tires 6Battery 4Transmission 1Total 30ParetoLube & Oil Brakes Tires Battery Trans.2 .The run charts seems to show a pattern of errors possibly linked to break times or the end of the shift. Perhaps workers are becoming fatigued. If so, perhaps two 10 minute breaks in the morning and again in the afternoon instead of one 20 minute break could reduce some errors. Also, errors are occurring during the last few minutes before noon and the end of the shift, and those periods should also be given management’s attention.4break lunch break3 2 1 0• • •• • • ••• • • ••••••• ••• •• • •• • •••Chapter 9 - Quality Control4. Sample Mean Range179.48 2.6 Mean Chart: =X ± A 2-R = 79.96 ± 0.58(1.87) 2 80.14 2.3 = 79.96 ± 1.083 80.14 1.2UCL = 81.04, LCL = 78.884 79.60 1.7 Range Chart: UCL = D 4-R = 2.11(1.87) = 3.95 5 80.02 2.0LCL = D 3-R = 0(1.87) = 0680.381.4[Both charts suggest the process is in control: Neither has any points outside the limits.]6. n = 200 Control Limits = np p p )1(2-±Thus, UCL is .0234 and LCL becomes 0.Since n = 200, the fraction represented by each data point is half the amount shown. E.g., 1 defective = .005, 2 defectives = .01, etc. Sample 10 is too large.7. 857.714110c ==Control limits: 409.8857.7c 3c ±=± UCL is 16.266, LCL becomes 0.All values are within the limits.14. Let USL = Upper Specification Limit, LSL = Lower Specification Limit,X = Process mean, σ = Process standard deviationFor process H:0096.)200(1325==p 0138.0096.200)9904(.0096.20096.±=±=}{capablenot ,0.193.93.04.1 ,938.min 04.1)32)(.3(1516393.)32)(.3(1.14153<===-=σ-=-=σ-pk C X USL LSL XFor process K:.1}17.1,0.1min{17.1)1)(3(335.3630.1)1)(3(30333===-=σ-=-=σ- C X USL LSL X pk Assuming the minimum acceptable pk C is 1.33, since 1.0 < 1.33, the process is not capable.For process T: 33.1}33.1,67.1min{33.1)4.0)(3(5.181.20367.1)4.0)(3(5.165.183===-=σ-=-=σ- C X USL LSL X pk Since 1.33 = 1.33, the process is capable.Chapter 10 - Aggregate Planning and Master Scheduling7. a. No backlogs are allowedPeriodForecast Output Regular Overtime Subcontract Inventory Beginning Ending Average Backlog Costs:RegularOvertimeSubcontractInventoryTotalb. Level strategyPeriodForecastOutputRegularOvertimeSubcontractInventoryBeginningEndingAverageBacklogCosts:RegularOvertimeSubcontractInventoryBacklogTotal8.PeriodForecastOutputRegularOvertimeSubcontractInventoryBeginningEndingAverageBacklogCosts:RegularOvertimeSubcontractInventoryBacklogTotalChapter 11 - MRP and ERP1. a. F: 2G: 1 H: 1 J: 2 x 2 = 4 L: 1 x 2 = 2 A: 1 x 4 = 4 D: 2 x 4 = 8 J: 1 x 2 = 2 D: 1 x 2 = 2Totals: F = 2; G = 1; H = 1; J = 6; D = 10; L = 2; A = 44. Master Schedule10. Week 1 2 3 4Material 40 80 60 70Week 1 2 3 4Labor hr. 160 320 240 280Mach. hr. 120 240 180 210a. Capacity utilizationWeek 1 2 3 4Labor 53.3% 106.7% 80% 93.3%Machine 60% 120% 90% 105%b. Capacity utilization exceeds 100% for both labor and machine in week2, and for machine alone in week 4.Production could be shifted to earlier or later weeks in which capacityis underutilized. Shifting to an earlier week would result in addedcarrying costs; shifting to later weeks would mean backorder costs.Another option would be to work overtime. Labor cost would increase dueto overtime premium, a probable decrease in productivity, and possibleincrease in accidents.Chapter 12 - Inventory Management2.The following table contains figures on the monthly volume and unit costs for a random sample of 16 items for a list of 2,000 inventory items.a. See table.b. To allocate control efforts.c. It might be important for some reason other than dollar usage, suchas cost of a stockout, usage highly correlated to an A item, etc.3. D = 1,215 bags/yr. S = $10 H = $75a. bags HDS Q 187510)215,1(22===b. Q/2 = 18/2 = 9 bagsc.orders ordersbags bags Q D 5.67/ 18 215,1== d . S QD H 2/Q TC +=350,1$675675)10(18215,1)75(218=+=+=e. Assuming that holding cost per bag increases by $9/bag/yearQ ==84)10)(215,1(217 bags71.428,1$71.714714)10(17215,1)84(217=+=+=TC Increase by [$1,428.71 – $1,350] = $78.714. D = 40/day x 260 days/yr. = 10,400 packagesS = $60 H = $30a. oxes b 20496.2033060)400,10(2H DS 2Q 0====b. S QD H 2Q TC +=82.118,6$82.058,3060,3)60(204400,10)30(2204=+=+=c. Yesd. )60(200400,10)30(2200TC 200+=TC 200 = 3,000 + 3,120 = $6,1206,120 – 6,118.82 (only $1.18 higher than with EOQ, so 200 isacceptable.)7. H = $2/month S = $55D 1 = 100/month (months 1–6)D 2 = 150/month (months 7–12)a. 16.74255)100(2Q :D H DS2Q 010===83.90255)150(2Q :D 02==b. The EOQ model requires this.c. Discount of $10/order is equivalent to S – 10 = $45 (revised ordering cost)1–6 TC74 = $148.32180$)45(150100)2(2150TC 145$)45(100100)2(2100TC *140$)45(50100)2(250TC 15010050=+==+==+=7–12 TC 91 = $181.66195$)45(150150)2(2150TC *5.167$)45(100150)2(2100TC 185$)45(50150)2(250TC 15010050=+==+==+=10. p = 50/ton/day u = 20 tons/day200 days/yr.S = $100H = $5/ton per yr.a. bags] [10,328 tons 40.5162050505100)000,4(2u p p H DS 2Q 0=-=-=b. ]bags 8.196,6 .approx [ tons 84.309)30(504.516)u p (P Q I max ==-=Average is92.154248.309:2I max =tons [approx. 3,098 bags] c. Run length =days 33.10504.516P Q == d. Runs per year = 8] approx .[ 7.754.516000,4QD ==e. Q ' = 258.2D= 20 tons/day x 200 days/yr. = 4,000 tons/yr.TC =S QDH 2I max + TC orig. = $1,549.00 TC rev. = $ 774.50Savings would be$774.5015.RangePHQD = 4,900 seats/yr. 0–999 $5.00 $2.00 495 H = .4P 1,000–3,9994.95 1.98 497 NFS = $50 4,000–5,9994.90 1.96 500 NF6,000+ 4.85 1.94 503 NFCompare TC 495 with TC for all lower price breaks:TC 495 = 495 ($2) + 4,900($50) + $5.00(4,900) = $25,4902 495TC 1,000 = 1,000 ($1.98) + 4,900($50) + $4.95(4,900) = $25,4902 1,000 TC 4,000 = 4,000 ($1.96) + 4,900($50) + $4.90(4,900) = $27,9912 4,000 TC 6,000 = 6,000 ($1.94) + 4,900($50) + $4.85(4,900) = $29,6262 6,000Hence, one would be indifferent between 495 or 1,000 units22. d = 30 gal./day ROP = 170 gal.QuantityTCLT = 4 days,ss = Zσd LT = 50 galRisk = 9% Z = 1.34 Solving, σd LT = 37.313% Z = 1.88, ss=1.88 x 37.31 = 70.14 gal. Chapter 13 - JIT and Lean Operations1. N = ?N = DT(1 + X)D = 80 pieces per hour CT = 75 min. = 1.25 hr.= 80(1.25)(1.35) = 3C = 45 45X = .354. The smallest daily quantity evenly divisible into all four quantities is3. Therefore, use three cycles.Product Daily quantity Units per cycleA 21 21/3 = 7B 12 12/3 = 4C 3 3/3 = 1D 15 15/3 = 55.a. Cycle 1 2 3 4A 6 6 5 5B 3 3 3 3C 1 1 1 1D 4 4 5 5E 2 2 2 2 b. Cycle 1 2A 11 11B 6 6C 2 2D 8 8E 4 4c. 4 cycles = lower inventory, more flexibility2 cycles = fewer changeovers7. Net available time = 480 –75 = 405. Takt time = 405/300 units per day = 1.35 minutes.Chapter 15 - Scheduling6. a. FCFS: A–B–C–DSPT: D–C–B–AEDD: C–B–D–ACR: A–C–D–BFCFS: Job time Flow time Due date DaysJob (days) (days) (days) tardyA 14 14 20 0B 10 24 16 8C 7 31 15 16D 6 37 17 2037 106 44SPT: Job time Flow time Due date DaysJob (days) (days) (days) tardyD 6 6 17 0C 7 13 15 0B 10 23 16 7A 14 37 20 1737 79 24EDD:completed on day 14. After the completion of Job A, the revised critical ratios are:completed on day 21. After the completion of Job C, the revised criticalJob D has the lowest critical ratio therefore it is scheduled next and completed on day 27.b.ardi Flow time Average flow time Number of jobsDays tardy Average job t ness Number of jobs Flow timeAverage number of jobs at the center Makespan==∑=FCFS SPT EDD CR26.50 19.75 21.00 24.75 11.0 6.00 6.00 9.25 2.86 2.14 2.27 2.67c. SPT is superior.9.Thus, the sequence is b-a-g-e-f-d-c.。
运营管理》-课后习题答案
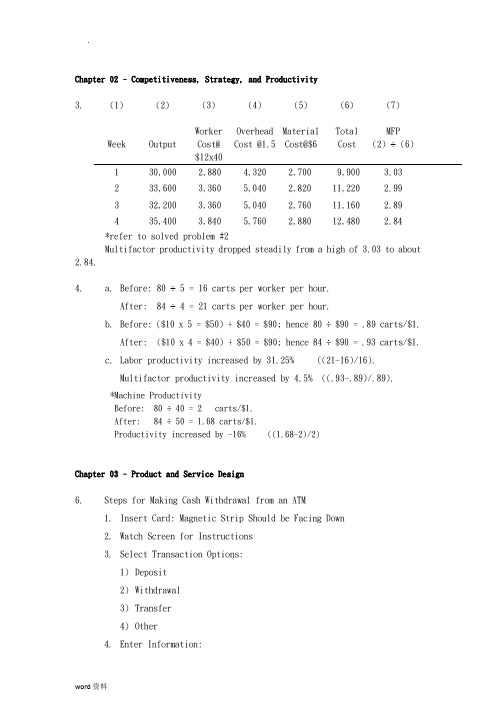
Chapter 02 - Competitiveness, Strategy, and Productivity3. (1) (2) (3) (4) (5) (6) (7)Week Output WorkerCost@$12x40OverheadCost @1.5MaterialCost@$6TotalCostMFP(2) ÷ (6)1 30,000 2,880 4,320 2,700 9,900 3.032 33,600 3,360 5,040 2,820 11,220 2.993 32,200 3,360 5,040 2,760 11,160 2.894 35,400 3,840 5,760 2,880 12,480 2.84*refer to solved problem #2Multifactor productivity dropped steadily from a high of 3.03 to about 2.84.4. a. Before: 80 ÷ 5 = 16 carts per worker per hour.After: 84 ÷ 4 = 21 carts per worker per hour.b. Before: ($10 x 5 = $50) + $40 = $90; hence 80 ÷ $90 = .89 carts/$1.After: ($10 x 4 = $40) + $50 = $90; hence 84 ÷ $90 = .93 carts/$1.c. Labor productivity increased by 31.25% ((21-16)/16).Multifactor productivity increased by 4.5% ((.93-.89)/.89).*Machine ProductivityBefore: 80 ÷ 40 = 2 carts/$1.After: 84 ÷ 50 = 1.68 carts/$1.Productivity increased by -16% ((1.68-2)/2)Chapter 03 - Product and Service Design6. Steps for Making Cash Withdrawal from an ATM1. Insert Card: Magnetic Strip Should be Facing Down2. Watch Screen for Instructions3. Select Transaction Options:1) Deposit2) Withdrawal3) Transfer4) Other4. Enter Information:1) PIN Number2) Select a Transaction and Account3) Enter Amount of Transaction5. Deposit/Withdrawal:1) Deposit —place in an envelope (which you’ll find near or in theATM) and insert it into the deposit slot2) Withdrawal —lift the “Withdrawal Door,” being careful to remove all cash 6. Remove card and receipt (which serves as the transaction record)8.Chapter 04 - Strategic Capacity Planning for Products and Services2. %80capacityEffective outputActual Efficiency ==Actual output = .8 (Effective capacity) Effective capacity = .5 (Design capacity) Actual output = (.5)(.8)(Effective capacity) Actual output = (.4)(Design capacity) Actual output = 8 jobs Utilization = .4capacityDesign outputActual =n Utilizatiojobs 204.8capacity Effective output Actual Capacity Design ===10. a. Given: 10 hrs. or 600 min. of operating time per day. 250 days x 600 min. = 150,000 min. per year operating time.Total processing time by machineProductA B C 1 48,000 64,000 32,000 2 48,000 48,000 36,000 3 30,000 36,000 24,000 460,00060,00030,000Total 186,000 208,000 122,000machine181.000,150000,122machine 238.1000,150000,208machine224.1000,150000,186≈==≈==≈==C B A N N NYou would have to buy two “A” machines at a total cost of $80,000, or two “B” machines at a total cost of $60,000, or one “C” machine at $80,000.b. Total cost for each type of machine:A (2): 186,000 min ÷ 60 = 3,100 hrs. x $10 = $31,000 + $80,000 = $111,000B (2) : 208,000 ÷ 60 = 3,466.67 hrs. x $11 = $38,133 + $60,000 = $98,133 C(1): 122,000 ÷ 60 = 2,033.33 hrs. x $12 = $24,400 + $80,000 = $104,400Buy 2 Bs —these have the lowest total cost.Chapter 05 - Process Selection and Facility Layout3.Desired output = 4Operating time = 56 minutesunit per minutes 14hourper units 4hourper minutes 65output Desired time Operating CT ===Task # of Following tasks PositionalWeightA 4 23B 3 20C 2 18D 3 25E 2 18F 4 29G 3 24H 1 14 I5a. First rule: most followers. Second rule: largest positional weight.Assembly Line Balancing Table (CT = 14)b. First rule: Largest positional weight.Assembly Line Balancing Table (CT = 14)c. %36.805645stations of no. x CT time Total Efficiency ===4. a. l.2. Minimum Ct = 1.3 minutesTask Following tasksa 4b 3c 3d 2e3f 2g 1h3. percent 54.11)3.1(46.CT x N time)(idle percent Idle ==∑=4. 420 min./day 323.1 ( 323)/1.3 min./OT Output rounds to copiers day CT cycle=== b. 1. inutes m 3.224.6N time Total CT ,6.4 time Total ==== 2. Assign a, b, c, d, and e to station 1: 2.3 minutes [no idle time]Assign f, g, and h to station 2: 2.3 minutes3. 420182.6 copiers /2.3OT Output day CT ===4.420 min./dayMaximum Ct is 4.6. Output 91.30 copiers /4.6 min./day cycle==7.Chapter 06 - Work Design and Measurement3.Element PR OT NT AF job ST1 .90 .46 .414 1.15 .4762 .85 1.505 1.280 1.15 1.4723 1.10 .83 .913 1.15 1.050 41.00 1.16 1.160 1.15 1.334Total4.3328. A = 24 + 10 + 14 = 48 minutes per 4 hours.min 125.720.11x70.5ST .min 70.5)95(.6NT 20.24048A =-=====9. a. Element PR OT NT A ST1 1.10 1.19 1.309 1.15 1.5052 1.15 .83 .955 1.15 1.09831.05 .56 .588 1.15 .676b.01.A 00.2z 034.s 83.x ==== 222(.034)67.12~68.01(.83)zs n observations ax ⎛⎫⎛⎫===⎪ ⎪⎝⎭⎝⎭ c. e = .01 minutes 47 to round ,24.4601.)034(.2e zs n 22=⎪⎭⎫⎝⎛=⎪⎭⎫ ⎝⎛=Chapter 07- Location Planning and Analysis1.Factor Local bank Steel mill Food warehouse Public school 1. Convenience forcustomers H L M –H M –H 2. Attractivenessof building H L M M –H 3. Nearness to rawmaterials L H L M 4. Large amountsof power L H L L 5. Pollutioncontrols L H L L 6. Labor cost andavailability L M L L 7. Transportationcosts L M –H M –H M8. Constructioncosts M H M M –HLocation (a) Location (b)4. Factor A B C WeightA B C1.Business Services 9 5 5 2/9 18/9 10/9 10/92.Community Services 7 6 7 1/9 7/9 6/9 7/93.Real Estate Cost 3 8 7 1/9 3/9 8/9 7/94.Construction Costs 5 6 5 2/9 10/9 12/9 10/95.Cost of Living 4 7 8 1/9 4/9 7/9 8/96.Taxes 5 5 5 1/9 5/9 5/9 4/97.Transportation 6 7 8 1/9 6/9 7/9 8/9 Total 39 44 45 1.0 53/9 55/9 54/9 Each factor has a weight of 1/7.a . Composite Scores39 44 457 7 7B orC is the best and A is least desirable.b . Business Services and Construction Costs both have a weight of 2/9; the other factors each have a weight of 1/9.5 x + 2 x + 2 x = 1 x = 1/9c . Composite ScoresA B C53/9 55/9 54/9B is the best followed byC and then A.5.Locationx yA 3 7B 8 2C 4 6D 4 1E 6 4Totals 25 20-x =∑x i= 25 = 5.0 -y =∑y i= 20 = 4.0 n 5 n 5Hence, the center of gravity is at (5,4) and therefore the optimallocation.Chapter 08 - Management of Quality1. ChecksheetWork Type FrequencyLube and Oil 12Brakes 7Tires 6Battery 4Transmission 1Total 30ParetoLube & Oil Brakes Tires Battery Trans.2 .The run charts seems to show a pattern of errors possibly linked to break times or the end of the shift. Perhaps workers are becoming fatigued. If so, perhaps two 10 minute breaks in the morning and again in the afternoon instead of one 20 minute break could reduce some errors. Also, errors are occurring during the last few minutes before noon and the end of the shift, and those periods should also be given management’s attention.4break lunch break3 2 1 0∙ ∙ ∙∙ ∙ ∙ ∙∙∙ ∙ ∙ ∙∙∙∙∙∙∙ ∙∙∙ ∙∙ ∙ ∙∙ ∙ ∙∙∙Chapter 9 - Quality Control4. Sample Mean Range179.48 2.6 Mean Chart: =X ± A 2-R = 79.96 ± 0.58(1.87) 2 80.14 2.3 = 79.96 ± 1.083 80.14 1.2UCL = 81.04, LCL = 78.884 79.60 1.7 Range Chart: UCL = D 4-R = 2.11(1.87) = 3.95 5 80.02 2.0LCL = D 3-R = 0(1.87) = 0680.381.4[Both charts suggest the process is in control: Neither has any points outside the limits.]6. n = 200 Control Limits = np p p )1(2-±Thus, UCL is .0234 and LCL becomes 0.Since n = 200, the fraction represented by each data point is half the amount shown. E.g., 1 defective = .005, 2 defectives = .01, etc. Sample 10 is too large.7. 857.714110c ==Control limits: 409.8857.7c 3c ±=± UCL is 16.266, LCL becomes 0.All values are within the limits.14. Let USL = Upper Specification Limit, LSL = Lower Specification Limit,X = Process mean, σ = Process standard deviationFor process H:0096.)200(1325==p 0138.0096.200)9904(.0096.20096.±=±=}{capablenot ,0.193.93.04.1 ,938.min 04.1)32)(.3(1516393.)32)(.3(1.14153<===-=σ-=-=σ-pk C X USL LSL XFor process K:.1}17.1,0.1min{17.1)1)(3(335.3630.1)1)(3(30333===-=σ-=-=σ- C X USL LSL X pk Assuming the minimum acceptable pk C is 1.33, since 1.0 < 1.33, the process is not capable.For process T: 33.1}33.1,67.1min{33.1)4.0)(3(5.181.20367.1)4.0)(3(5.165.183===-=σ-=-=σ- C X USL LSL X pk Since 1.33 = 1.33, the process is capable.Chapter 10 - Aggregate Planning and Master Scheduling7. a. No backlogs are allowedPeriodForecast Output Regular Overtime Subcontract Inventory Beginning Ending Average Backlog Costs:RegularOvertimeSubcontractInventoryTotalb. Level strategyPeriodForecastOutputRegularOvertimeSubcontractInventoryBeginningEndingAverageBacklogCosts:RegularOvertimeSubcontractInventoryBacklogTotal8.PeriodForecastOutputRegularOvertimeSubcontractInventoryBeginningEndingAverageBacklogCosts:RegularOvertimeSubcontractInventoryBacklogTotalChapter 11 - MRP and ERP1. a. F: 2G: 1 H: 1 J: 2 x 2 = 4 L: 1 x 2 = 2 A: 1 x 4 = 4 D: 2 x 4 = 8 J: 1 x 2 = 2 D: 1 x 2 = 2Totals: F = 2; G = 1; H = 1; J = 6; D = 10; L = 2; A = 44. Master Schedule10. Week 1 2 3 4Material 40 80 60 70Week 1 2 3 4Labor hr. 160 320 240 280Mach. hr. 120 240 180 210a. Capacity utilizationWeek 1 2 3 4Labor 53.3% 106.7% 80% 93.3%Machine 60% 120% 90% 105%b. Capacity utilization exceeds 100% for both labor and machine in week2, and for machine alone in week 4.Production could be shifted to earlier or later weeks in which capacityis underutilized. Shifting to an earlier week would result in addedcarrying costs; shifting to later weeks would mean backorder costs.Another option would be to work overtime. Labor cost would increase dueto overtime premium, a probable decrease in productivity, and possibleincrease in accidents.Chapter 12 - Inventory Management2. The following table contains figures on the monthly volume and unit costs for a random sample of 16 items for a list of 2,000 inventory items.a. See table.b. To allocate control efforts.c. It might be important for some reason other than dollar usage, suchas cost of a stockout, usage highly correlated to an A item, etc.3. D = 1,215 bags/yr. S = $10 H = $75a. bags HDS Q 187510)215,1(22===b. Q/2 = 18/2 = 9 bagsc.orders ordersbags bags Q D 5.67/ 18 215,1== d . S QD H 2/Q TC +=350,1$675675)10(18215,1)75(218=+=+=e. Assuming that holding cost per bag increases by $9/bag/yearQ ==84)10)(215,1(217 bags71.428,1$71.714714)10(17215,1)84(217=+=+=TC Increase by [$1,428.71 – $1,350] = $78.714. D = 40/day x 260 days/yr. = 10,400 packagesS = $60 H = $30a. oxes b 20496.2033060)400,10(2H DS 2Q 0====b. S QD H 2Q TC +=82.118,6$82.058,3060,3)60(204400,10)30(2204=+=+=c. Yesd. )60(200400,10)30(2200TC 200+=TC 200 = 3,000 + 3,120 = $6,1206,120 – 6,118.82 (only $1.18 higher than with EOQ, so 200 isacceptable.)7. H = $2/month S = $55D 1 = 100/month (months 1–6)D 2 = 150/month (months 7–12)a. 16.74255)100(2Q :D H DS2Q 010===83.90255)150(2Q :D 02==b. The EOQ model requires this.c. Discount of $10/order is equivalent to S – 10 = $45 (revised ordering cost)1–6 TC74 = $148.32180$)45(150100)2(2150TC 145$)45(100100)2(2100TC *140$)45(50100)2(250TC 15010050=+==+==+=7–12 TC 91 = $181.66195$)45(150150)2(2150TC *5.167$)45(100150)2(2100TC 185$)45(50150)2(250TC 15010050=+==+==+=10. p = 50/ton/day u = 20 tons/day200 days/yr.S = $100H = $5/ton per yr.a. bags] [10,328 tons 40.5162050505100)000,4(2u p p H DS 2Q 0=-=-=b. ]bags 8.196,6 .approx [ tons 84.309)30(504.516)u p (P Q I max ==-=Average is92.154248.309:2I max =tons [approx. 3,098 bags] c. Run length =days 33.10504.516P Q == d. Runs per year = 8] approx .[ 7.754.516000,4QD ==e. Q ' = 258.2D= 20 tons/day x 200 days/yr. = 4,000 tons/yr.TC =S QDH 2I max + TC orig. = $1,549.00 TC rev. = $ 774.50Savings would be$774.5015.RangePHQD = 4,900 seats/yr. 0–999 $5.00 $2.00 495 H = .4P 1,000–3,9994.95 1.98 497 NFS = $50 4,000–5,9994.90 1.96 500 NF6,000+ 4.85 1.94 503 NFCompare TC 495 with TC for all lower price breaks:TC 495 = 495 ($2) + 4,900($50) + $5.00(4,900) = $25,4902 495TC 1,000 = 1,000 ($1.98) + 4,900($50) + $4.95(4,900) = $25,4902 1,000 TC 4,000 = 4,000 ($1.96) + 4,900($50) + $4.90(4,900) = $27,9912 4,000 TC 6,000 = 6,000 ($1.94) + 4,900($50) + $4.85(4,900) = $29,6262 6,000Hence, one would be indifferent between 495 or 1,000 units22. d = 30 gal./day ROP = 170 gal.QuantityTCLT = 4 days,ss = Zσd LT = 50 galRisk = 9% Z = 1.34 Solving, σd LT = 37.313% Z = 1.88, ss=1.88 x 37.31 = 70.14 gal. Chapter 13 - JIT and Lean Operations1. N = ?N = DT(1 + X)D = 80 pieces per hour CT = 75 min. = 1.25 hr.= 80(1.25)(1.35) = 3C = 45 45X = .354. The smallest daily quantity evenly divisible into all four quantities is3. Therefore, use three cycles.Product Daily quantity Units per cycleA 21 21/3 = 7B 12 12/3 = 4C 3 3/3 = 1D 15 15/3 = 55.a. Cycle 1 2 3 4A 6 6 5 5B 3 3 3 3C 1 1 1 1D 4 4 5 5E 2 2 2 2 b. Cycle 1 2A 11 11B 6 6C 2 2D 8 8E 4 4c. 4 cycles = lower inventory, more flexibility2 cycles = fewer changeovers7. Net available time = 480 –75 = 405. Takt time = 405/300 units per day = 1.35 minutes.Chapter 15 - Scheduling6. a. FCFS: A–B–C–DSPT: D–C–B–AEDD: C–B–D–ACR: A–C–D–BFCFS: Job time Flow time Due date DaysJob (days) (days) (days) tardyA 14 14 20 0B 10 24 16 8C 7 31 15 16D 6 37 17 2037 106 44SPT: Job time Flow time Due date DaysJob (days) (days) (days) tardyD 6 6 17 0C 7 13 15 0B 10 23 16 7A 14 37 20 1737 79 24EDD:Critical Ratiocompleted on day 14. After the completion of Job A, the revised critical ratios are:completed on day 21. After the completion of Job C, the revised critical ratios are:Job D has the lowest critical ratio therefore it is scheduled next and completed on day 27.The critical ratio sequence is A –C –D –B and the makespan is 37 days.b.ardi Flow time Average flow time Number of jobsDays tardy Average job t ness Number of jobs Flow timeAverage number of jobs at the center Makespan==∑=FCFS SPT EDD CR26.50 19.75 21.00 24.75 11.0 6.00 6.00 9.252.86 2.14 2.27 2.67c. SPT is superior.9.Thus, the sequence is b-a-g-e-f-d-c.。
运营管理-史蒂文森stevenson(各章课后习题答案)

最大节拍18分钟第1题1最小节拍2.4分钟2450/2.4=187.5450/18=25产量范围25-187.5318/2.4=7.5 取整 8个工作地4450/125=3.6分钟5450/9=50 450/15=30第2题产量33.33/时 时间60分钟 节拍60/33.33=1.8分钟 工作地6/1.8=3.33 取整4个工作地作业时间闲置时间闲置时间百分比1a 1.40.416.67%2b,e 1.30.5 1.2/(1.8*4)=1/63d,c,f 1.804g,h 1.50.3第3题工作时间56分钟 产量4 节拍14分钟 作业总时长45分 工作地45/14=3.21取整4个工作地作业时间闲置时间闲置时间百分比1f,a,g14019.64%2d,b,c13111/(14*4)=0.19643e,h1314i59第4题图-PPT总时长4.6/最小节拍1.3=3.54 取整4个工作地工作地作业时间闲置时间闲置时间百分比1a,b,c,e10.311.54%2d 1.300.6/(1.3*4)=0.11543f,g 1.10.2420/1.3=323个4h 1.20.1若只能使用2个工作地 则最小节拍为2.3分钟 该节拍可行工作地作业时间闲置时间闲置时比0%1a,b,c,e,d 2.30420/2.3=182.6个2f,g,h 2.30420/4.6=91.3个第5题图-PPT,工作时间8*60=480分 日产量240单位 节拍480/240=2分钟工作地作业时间闲置时间闲置时比 1.4/6=23.33% 1a,b,c,f202d,e 1.60.43g11第6题图-PPT,总时长4/节拍1.5=2.67 取整3个工作地工作地作业时间闲置时间闲置时比0.5/4.5=11.11% 1a,b,c 1.20.32d,e,f,g,h 1.40.13i,j,k,l 1.40.1第7题图-PPT,总时长193 7*60*60/500=50.4秒 193/50.4=3.83取整4个工作地可采纳以50秒为生产节拍,工作地闲置时间可利用,理论上的最小节拍。
最新《运营管理》课后习题答案

Chapter 02 - Competitiveness, Strategy, and Productivity3. (1) (2) (3) (4) (5) (6) (7)Week Output WorkerCost@$12x40OverheadCost @1.5MaterialCost@$6TotalCostMFP(2) ÷ (6)1 30,000 2,880 4,320 2,700 9,900 3.032 33,600 3,360 5,040 2,820 11,220 2.993 32,200 3,360 5,040 2,760 11,160 2.894 35,400 3,840 5,760 2,880 12,480 2.84*refer to solved problem #2Multifactor productivity dropped steadily from a high of 3.03 to about 2.84.4. a. Before: 80 ÷ 5 = 16 carts per worker per hour.After: 84 ÷ 4 = 21 carts per worker per hour.b. Before: ($10 x 5 = $50) + $40 = $90; hence 80 ÷ $90 = .89 carts/$1.After: ($10 x 4 = $40) + $50 = $90; hence 84 ÷ $90 = .93 carts/$1.c. Labor productivity increased by 31.25% ((21-16)/16).Multifactor productivity increased by 4.5% ((.93-.89)/.89).*Machine ProductivityBefore: 80 ÷ 40 = 2 carts/$1.After: 84 ÷ 50 = 1.68 carts/$1.Productivity increased by -16% ((1.68-2)/2)Chapter 03 - Product and Service Design6. Steps for Making Cash Withdrawal from an ATM1. Insert Card: Magnetic Strip Should be Facing Down2. Watch Screen for Instructions3. Select Transaction Options:1) Deposit2) Withdrawal3) Transfer4) Other4. Enter Information:1) PIN Number2) Select a Transaction and Account3) Enter Amount of Transaction5. Deposit/Withdrawal: 1) Deposit —place in an envelope (which you’ll find near or in the ATM) andinsert it into the deposit slot2) Withdrawal —lift the “Withdrawal Door,” being careful to remove all cash6. Remove card and receipt (which serves as the transaction record)8.Chapter 04 - Strategic Capacity Planning for Products and Services2. %80capacityEffective outputActual Efficiency ==Actual output = .8 (Effective capacity) Effective capacity = .5 (Design capacity) Actual output = (.5)(.8)(Effective capacity) Actual output = (.4)(Design capacity) Actual output = 8 jobs Utilization = .4capacityDesign outputActual =n Utilizatiojobs 204.8capacity Effective output Actual Capacity Design ===10. a. Given: 10 hrs. or 600 min. of operating time per day.250 days x 600 min. = 150,000 min. per year operating time.Total processing time by machineProductABC 1 48,000 64,000 32,000 2 48,000 48,000 36,000 3 30,000 36,000 24,000 460,000 60,000 30,000 Total 186,000208,000122,000machine181.000,150000,122machine 238.1000,150000,208machine224.1000,150000,186≈==≈==≈==C B A N N NYou would have to buy two “A” machines at a total cost of $80,000, or two “B” machines at a total cost of $60,000, or one “C” machine at $80,000.b.Total cost for each type of machine:A (2): 186,000 min ÷ 60 = 3,100 hrs. x $10 = $31,000 + $80,000 = $111,000B (2) : 208,000 ÷ 60 = 3,466.67 hrs. x $11 = $38,133 + $60,000 = $98,133 C(1): 122,000 ÷ 60 = 2,033.33 hrs. x $12 = $24,400 + $80,000 = $104,400Buy 2 Bs —these have the lowest total cost.Chapter 05 - Process Selection and Facility Layout3.Desired output = 4Operating time = 56 minutesunit per minutes 14hourper units 4hourper minutes 65output Desired time Operating CT ===Task # of Following tasksPositional WeightA 4 23B 3 20C 2 18D 3 25E 2 18F 4 29G 3 24H 1 14 I5a. First rule: most followers. Second rule: largest positional weight.Assembly Line Balancing Table (CT = 14)b. First rule: Largest positional weight.Assembly Line Balancing Table (CT = 14)c. %36.805645stations of no. x CT time Total Efficiency ===4. a. l.2. Minimum Ct = 1.3 minutesTask Following tasksa 4b 3c 3d 2e 3f 2g 1h3. percent 54.11)3.1(46.CT x N time)(idle percent Idle ==∑=4. 420 min./day 323.1 ( 323)/1.3 min./OT Output rounds to copiers day CT cycle=== b. 1. inutes m 3.224.6N time Total CT ,6.4 time Total ==== 2. Assign a, b, c, d, and e to station 1: 2.3 minutes [no idle time]Assign f, g, and h to station 2: 2.3 minutes3. 420182.6 copiers /2.3OT Output day CT ===4.420 min./dayMaximum Ct is 4.6. Output 91.30 copiers /4.6 min./day cycle==7.Chapter 06 - Work Design and Measurement3. Element PR OT NT AF job ST1 .90.46.414 1.15 .4762 .85 1.505 1.280 1.15 1.4723 1.10.83.913 1.15 1.05041.00 1.16 1.160 1.15 1.334Total4.3328. A = 24 + 10 + 14 = 48 minutes per 4 hours.min 125.720.11x70.5ST .min 70.5)95(.6NT 20.24048A =-=====9. a. Element PR OT NT A ST1 1.10 1.19 1.309 1.15 1.5052 1.15 .83 .955 1.15 1.09831.05.56.588 1.15 .676b.01.A 00.2z 034.s 83.x ==== 222(.034)67.12~68.01(.83)zs n observations ax ⎛⎫⎛⎫===⎪ ⎪⎝⎭⎝⎭ c. e = .01 minutes 47 to round ,24.4601.)034(.2e zs n 22=⎪⎭⎫⎝⎛=⎪⎭⎫ ⎝⎛=Chapter 07- Location Planning and Analysis1. Factor Local bank Steel mill Food warehouse Public school1. Convenience forcustomers H L M–H M–H2. Attractiveness ofbuilding H L M M–H3. Nearness to rawmaterials L H L M4. Large amounts ofpower L H L L5. Pollution controls L H L L6. Labor cost andavailability L M L L7. Transportationcosts L M–H M–H M8. Constructioncosts M H M M–HLocation (a) Location (b)4. Factor A B C Weight A B C1. Business Services 9 5 5 2/9 18/9 10/9 10/92. Community Services 7 6 7 1/9 7/9 6/9 7/93. Real Estate Cost 3 8 7 1/9 3/9 8/9 7/94. Construction Costs 5 6 5 2/9 10/9 12/9 10/95. Cost of Living 4 7 8 1/9 4/9 7/9 8/96. Taxes 5 5 5 1/9 5/9 5/9 4/97. Transportation 6 7 8 1/9 6/9 7/9 8/9Total 39 44 45 1.0 53/9 55/9 54/9 Each factor has a weight of 1/7.a. Composite Scores 39 44 45 7 7 7B orC is the best and A is least desirable.b. Business Services and Construction Costs both have a weight of 2/9; the other factors eachhave a weight of 1/9.5 x + 2 x + 2 x = 1 ⇒ x = 1/9c. Composite ScoresA B C 53/9 55/9 54/9B is the best followed byC and then A.5.Locationx yA 3 7B 8 2C 4 6D 4 1E 6 4Totals 25 20-x =∑x i= 25 = 5.0 -y =∑y i= 20 = 4.0 n 5 n 5Hence, the center of gravity is at (5,4) and therefore the optimal location.Chapter 08 - Management of Quality1. ChecksheetWork Type FrequencyLube and Oil 12 Brakes 7 Tires 6 Battery 4 Transmission1Total30Pareto2 .The run charts seems to show a pattern of errors possibly linked to break times or the end of the shift. Perhaps workers are becoming fatigued. If so, perhaps two 10 minute breaks in the morning and again in the afternoon instead of one 20 minute break could reduce some errors. Also, errors are occurring during the last few minutes before noon and the end of the shift, and those periods should also be given management’s attention.Lube & Oil BrakesTiresBatteryTrans.break lunch break3 2 1 0• • •• • • ••• • • ••••••• ••• •• • •• • •••4Chapter 9 - Quality Control4. Sample Mean Range179.48 2.6 Mean Chart: =X ± A 2-R = 79.96 ± 0.58(1.87) 2 80.14 2.3 = 79.96 ± 1.083 80.14 1.2UCL = 81.04, LCL = 78.884 79.60 1.7 Range Chart: UCL = D 4-R = 2.11(1.87) = 3.95 5 80.02 2.0LCL = D 3-R = 0(1.87) = 0680.381.4[Both charts suggest the process is in control: Neither has any points outside the limits.]6. n = 200 Control Limits = np p p )1(2-±Thus, UCL is .0234 and LCL becomes 0.Since n = 200, the fraction represented by each data point is half the amount shown. E.g., 1 defective = .005, 2 defectives = .01, etc.Sample 10 is too large.7. 857.714110c ==Control limits: 409.8857.7c 3c ±=± UCL is 16.266, LCL becomes 0.All values are within the limits.14. Let USL = Upper Specification Limit, LSL = Lower Specification Limit,X = Process mean, σ = Process standard deviationFor process H:}{capablenot ,0.193.93.04.1 ,938.min 04.1)32)(.3(1516393.)32)(.3(1.14153<===-=σ-=-=σ-pk C X USL LSL X0096.)200(1325==p 0138.0096.200)9904(.0096.20096.±=±=For process K:.1}17.1,0.1min{17.1)1)(3(335.3630.1)1)(3(30333===-=σ-=-=σ- C X USL LSL X pk Assuming the minimum acceptable pk C is 1.33, since 1.0 < 1.33, the process is not capable.For process T:33.1}33.1,67.1min{33.1)4.0)(3(5.181.20367.1)4.0)(3(5.165.183===-=σ-=-=σ- C X USL LSL X pk Since 1.33 = 1.33, the process is capable.Chapter 10 - Aggregate Planning and Master Scheduling7. a.No backlogs are allowedPeriodForecast Output Regular Overtime Subcontract Output - Forecast Inventory Beginning Ending Average Backlog Costs: Regular Overtime Subcontract Inventory Totalb.Level strategyPeriodForecastOutputRegularOvertimeSubcontractOutput - ForecastInventoryBeginningEndingAverageBacklogCosts:RegularOvertimeSubcontractInventoryBacklogTotal8.PeriodForecastOutputRegularOvertimeSubcontractOutput- ForecastInventoryBeginningEndingAverageBacklogCosts:RegularOvertimeSubcontractInventoryBacklogTotalChapter 11 - MRP and ERP1. a. F: 2 G: 1 H: 1J: 2 x 2 = 4 L: 1 x 2 = 2 A: 1 x 4 = 4D: 2 x 4 = 8 J: 1 x 2 = 2 D: 1 x 2 = 2Totals: F = 2; G = 1; H = 1; J = 6; D = 10; L = 2; A = 4b.4.MasterSchedule10. Week 1 2 3 4Material 40 80 60 70Week 1 2 3 4Labor hr. 160 320 240 280Mach. hr. 120 240 180 210a. Capacity utilizationWeek 1 2 3 4Labor 53.3% 106.7% 80% 93.3%Machine 60% 120% 90% 105%b. C apacity utilization exceeds 100% for both labor and machine in week 2, and formachine alone in week 4.Production could be shifted to earlier or later weeks in which capacity isunderutilized. Shifting to an earlier week would result in added carrying costs;shifting to later weeks would mean backorder costs.Another option would be to work overtime. Labor cost would increase due toovertime premium, a probable decrease in productivity, and possible increase inaccidents.Chapter 12 - Inventory Management2. The following table contains figures on the monthly volume and unit costs for a random sample of 16 items for a list of 2,000 inventory items.a. See table.b. To allocate control efforts.c. It might be important for some reason other than dollar usage, such as cost of astockout, usage highly correlated to an A item, etc.3. D = 1,215 bags/yr. S = $10 H = $75a. bags HDS Q 187510)215,1(22===b. Q/2 = 18/2 = 9 bagsc.orders ordersbags bags Q D 5.67/ 18 215,1== d . S QD H 2/Q TC +=350,1$675675)10(18215,1)75(218=+=+=e. Assuming that holding cost per bag increases by $9/bag/yearQ ==84)10)(215,1(217 bags71.428,1$71.714714)10(17215,1)84(217=+=+=TCIncrease by [$1,428.71 – $1,350] = $78.714.D = 40/day x 260 days/yr. = 10,400 packagesS = $60 H = $30a. oxes b 20496.2033060)400,10(2H DS 2Q 0====b. S QD H 2Q TC +=82.118,6$82.058,3060,3)60(204400,10)30(2204=+=+=c. Yesd. )60(200400,10)30(2200TC 200+=TC 200 = 3,000 + 3,120 = $6,1206,120 – 6,118.82 (only $1.18 higher than with EOQ, so 200 is acceptable.)7.H = $2/month S = $55D 1 = 100/month (months 1–6)D 2 = 150/month (months 7–12)a. 16.74255)100(2Q :D H DS2Q 010===83.90255)150(2Q :D 02==b. The EOQ model requires this.c. Discount of $10/order is equivalent to S – 10 = $45 (revised ordering cost)1–6 TC74 = $148.32180$)45(150100)2(2150TC 145$)45(100100)2(2100TC *140$)45(50100)2(250TC 15010050=+==+==+=7–12 TC 91 =$181.66195$)45(150150)2(2150TC *5.167$)45(100150)2(2100TC 185$)45(50150)2(250TC 15010050=+==+==+=10. p = 50/ton/day u = 20 tons/day200 days/yr.S = $100 H = $5/ton per yr.a. bags] [10,328 tons 40.5162050505100)000,4(2u p p H DS 2Q 0=-=-=b. ]bags 8.196,6 .approx [ tons 84.309)30(504.516)u p (P Q I max ==-=Average is92.154248.309:2I max =tons [approx. 3,098 bags] c. Run length =days 33.10504.516P Q == d. Runs per year = 8] approx .[ 7.754.516000,4QD == e. Q ' = 258.2TC =S QD H 2I max + TC orig. = $1,549.00 TC rev. = $ 774.50Savings would be $774.50D= 20 tons/day x 200 days/yr. = 4,000 tons/yr.15. RangeP H Q D = 4,900 seats/yr. 0–999 $5.00 $2.00 495 H = .4P 1,000–3,999 4.95 1.98 497 NF S = $50 4,000–5,999 4.90 1.96 500 NF 6,000+ 4.85 1.94503 NFCompare TC 495 with TC for all lower price breaks:TC 495 =495 ($2) + 4,900($50) + $5.00(4,900) = $25,490 2 495 TC 1,000 = 1,000 ($1.98) + 4,900($50) + $4.95(4,900) = $25,4902 1,000 TC 4,000 = 4,000 ($1.96) + 4,900($50) + $4.90(4,900) = $27,9912 4,000 TC 6,000 = 6,000 ($1.94) + 4,900($50) + $4.85(4,900) = $29,6262 6,000Hence, one would be indifferent between 495 or 1,000 units 22. d = 30 gal./day ROP = 170 gal. LT = 4 days,ss = Z σd LT = 50 galRisk = 9% Z = 1.34 Solving, σd LT = 37.31 3% Z = 1.88, ss=1.88 x 37.31 = 70.14 gal.Chapter 13 - JIT and Lean Operations1. N = ?N = DT(1 + X)D = 80 pieces per hourC T = 75 min. = 1.25 hr. = 80(1.25) (1.35)= 3C = 45 45X = .35QuantityTC4. The smallest daily quantity evenly divisible into all four quantities is 3. Therefore, usethree cycles.Product Daily quantity Units per cycleA 21 21/3 = 7B 12 12/3 = 4C 3 3/3 = 1D 15 15/3 = 55.a. Cycle 1 2 3 4A 6 6 5 5B 3 3 3 3C 1 1 1 1D 4 4 5 5E 2 2 2 2 b. Cycle 1 2A 11 11B 6 6C 2 2D 8 8E 4 4c. 4 cycles = lower inventory, more flexibility2 cycles = fewer changeovers7. Net available time = 480 – 75 = 405. Takt time = 405/300 units per day = 1.35 minutes. Chapter 15 - Scheduling6. a. FCFS: A–B–C–DSPT: D–C–B–AEDD: C–B–D–ACR: A–C–D–BFCFS: Job time Flow time Due date DaysJob (days) (days) (days) tardyA 14 14 20 0B 10 24 16 8C 7 31 15 16D 6 37 17 2037 106 44SPT: Job time Flow time Due date Days Job (days) (days) (days) tardyD 6 6 17 0C 7 13 15 0B 10 23 16 7A 14 37 20 1737 79 24EDD:Job D has the lowest critical ratio therefore it is scheduled next and completed on day 27.b.ardi Flow time Average flow time Number of jobsDays tardy Average job t ness Number of jobs Flow timeAverage number of jobs at the center Makespan==∑=FCFS SPT EDD CR26.50 19.75 21.00 24.75 11.0 6.00 6.00 9.25 2.86 2.142.272.67c. SPT is superior.9.Thus, the sequence is b-a-g-e-f-d-c.。
运营管理》-课后习题答案
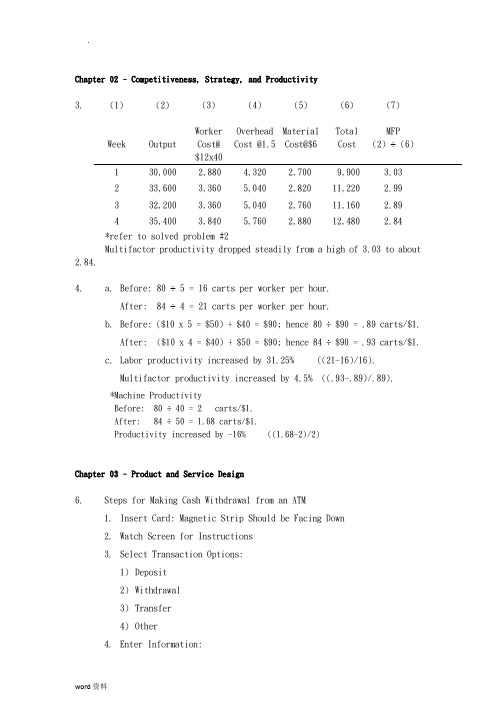
Chapter 02 - Competitiveness, Strategy, and Productivity3. (1) (2) (3) (4) (5) (6) (7)Week Output WorkerCost@$12x40OverheadCost @1.5MaterialCost@$6TotalCostMFP(2) ÷ (6)1 30,000 2,880 4,320 2,700 9,900 3.032 33,600 3,360 5,040 2,820 11,220 2.993 32,200 3,360 5,040 2,760 11,160 2.894 35,400 3,840 5,760 2,880 12,480 2.84*refer to solved problem #2Multifactor productivity dropped steadily from a high of 3.03 to about 2.84.4. a. Before: 80 ÷ 5 = 16 carts per worker per hour.After: 84 ÷ 4 = 21 carts per worker per hour.b. Before: ($10 x 5 = $50) + $40 = $90; hence 80 ÷ $90 = .89 carts/$1.After: ($10 x 4 = $40) + $50 = $90; hence 84 ÷ $90 = .93 carts/$1.c. Labor productivity increased by 31.25% ((21-16)/16).Multifactor productivity increased by 4.5% ((.93-.89)/.89).*Machine ProductivityBefore: 80 ÷ 40 = 2 carts/$1.After: 84 ÷ 50 = 1.68 carts/$1.Productivity increased by -16% ((1.68-2)/2)Chapter 03 - Product and Service Design6. Steps for Making Cash Withdrawal from an ATM1. Insert Card: Magnetic Strip Should be Facing Down2. Watch Screen for Instructions3. Select Transaction Options:1) Deposit2) Withdrawal3) Transfer4) Other4. Enter Information:1) PIN Number2) Select a Transaction and Account3) Enter Amount of Transaction5. Deposit/Withdrawal:1) Deposit —place in an envelope (which you’ll find near or in theATM) and insert it into the deposit slot2) Withdrawal —lift the “Withdrawal Door,” being careful to remove all cash 6. Remove card and receipt (which serves as the transaction record)8.Chapter 04 - Strategic Capacity Planning for Products and Services2. %80capacityEffective outputActual Efficiency ==Actual output = .8 (Effective capacity) Effective capacity = .5 (Design capacity) Actual output = (.5)(.8)(Effective capacity) Actual output = (.4)(Design capacity) Actual output = 8 jobs Utilization = .4capacityDesign outputActual =n Utilizatiojobs 204.8capacity Effective output Actual Capacity Design ===10. a. Given: 10 hrs. or 600 min. of operating time per day. 250 days x 600 min. = 150,000 min. per year operating time.Total processing time by machineProductA B C 1 48,000 64,000 32,000 2 48,000 48,000 36,000 3 30,000 36,000 24,000 460,00060,00030,000Total 186,000 208,000 122,000machine181.000,150000,122machine 238.1000,150000,208machine224.1000,150000,186≈==≈==≈==C B A N N NYou would have to buy two “A” machines at a total cost of $80,000, or two “B” machines at a total cost of $60,000, or one “C” machine at $80,000.b. Total cost for each type of machine:A (2): 186,000 min ÷ 60 = 3,100 hrs. x $10 = $31,000 + $80,000 = $111,000B (2) : 208,000 ÷ 60 = 3,466.67 hrs. x $11 = $38,133 + $60,000 = $98,133 C(1): 122,000 ÷ 60 = 2,033.33 hrs. x $12 = $24,400 + $80,000 = $104,400Buy 2 Bs —these have the lowest total cost.Chapter 05 - Process Selection and Facility Layout3.Desired output = 4Operating time = 56 minutesunit per minutes 14hourper units 4hourper minutes 65output Desired time Operating CT ===Task # of Following tasks PositionalWeightA 4 23B 3 20C 2 18D 3 25E 2 18F 4 29G 3 24H 1 14 I5a. First rule: most followers. Second rule: largest positional weight.Assembly Line Balancing Table (CT = 14)b. First rule: Largest positional weight.Assembly Line Balancing Table (CT = 14)c. %36.805645stations of no. x CT time Total Efficiency ===4. a. l.2. Minimum Ct = 1.3 minutesTask Following tasksa 4b 3c 3d 2e3f 2g 1h3. percent 54.11)3.1(46.CT x N time)(idle percent Idle ==∑=4. 420 min./day 323.1 ( 323)/1.3 min./OT Output rounds to copiers day CT cycle=== b. 1. inutes m 3.224.6N time Total CT ,6.4 time Total ==== 2. Assign a, b, c, d, and e to station 1: 2.3 minutes [no idle time]Assign f, g, and h to station 2: 2.3 minutes3. 420182.6 copiers /2.3OT Output day CT ===4.420 min./dayMaximum Ct is 4.6. Output 91.30 copiers /4.6 min./day cycle==7.Chapter 06 - Work Design and Measurement3.Element PR OT NT AF job ST1 .90 .46 .414 1.15 .4762 .85 1.505 1.280 1.15 1.4723 1.10 .83 .913 1.15 1.050 41.00 1.16 1.160 1.15 1.334Total4.3328. A = 24 + 10 + 14 = 48 minutes per 4 hours.min 125.720.11x70.5ST .min 70.5)95(.6NT 20.24048A =-=====9. a. Element PR OT NT A ST1 1.10 1.19 1.309 1.15 1.5052 1.15 .83 .955 1.15 1.09831.05 .56 .588 1.15 .676b.01.A 00.2z 034.s 83.x ==== 222(.034)67.12~68.01(.83)zs n observations ax ⎛⎫⎛⎫===⎪ ⎪⎝⎭⎝⎭ c. e = .01 minutes 47 to round ,24.4601.)034(.2e zs n 22=⎪⎭⎫⎝⎛=⎪⎭⎫ ⎝⎛=Chapter 07- Location Planning and Analysis1.Factor Local bank Steel mill Food warehouse Public school 1. Convenience forcustomers H L M –H M –H 2. Attractivenessof building H L M M –H 3. Nearness to rawmaterials L H L M 4. Large amountsof power L H L L 5. Pollutioncontrols L H L L 6. Labor cost andavailability L M L L 7. Transportationcosts L M –H M –H M8. Constructioncosts M H M M –HLocation (a) Location (b)4. Factor A B C WeightA B C1.Business Services 9 5 5 2/9 18/9 10/9 10/92.Community Services 7 6 7 1/9 7/9 6/9 7/93.Real Estate Cost 3 8 7 1/9 3/9 8/9 7/94.Construction Costs 5 6 5 2/9 10/9 12/9 10/95.Cost of Living 4 7 8 1/9 4/9 7/9 8/96.Taxes 5 5 5 1/9 5/9 5/9 4/97.Transportation 6 7 8 1/9 6/9 7/9 8/9 Total 39 44 45 1.0 53/9 55/9 54/9 Each factor has a weight of 1/7.a . Composite Scores39 44 457 7 7B orC is the best and A is least desirable.b . Business Services and Construction Costs both have a weight of 2/9; the other factors each have a weight of 1/9.5 x + 2 x + 2 x = 1 x = 1/9c . Composite ScoresA B C53/9 55/9 54/9B is the best followed byC and then A.5.Locationx yA 3 7B 8 2C 4 6D 4 1E 6 4Totals 25 20-x =∑x i= 25 = 5.0 -y =∑y i= 20 = 4.0 n 5 n 5Hence, the center of gravity is at (5,4) and therefore the optimallocation.Chapter 08 - Management of Quality1. ChecksheetWork Type FrequencyLube and Oil 12Brakes 7Tires 6Battery 4Transmission 1Total 30ParetoLube & Oil Brakes Tires Battery Trans.2 .The run charts seems to show a pattern of errors possibly linked to break times or the end of the shift. Perhaps workers are becoming fatigued. If so, perhaps two 10 minute breaks in the morning and again in the afternoon instead of one 20 minute break could reduce some errors. Also, errors are occurring during the last few minutes before noon and the end of the shift, and those periods should also be given management’s attention.4break lunch break3 2 1 0∙ ∙ ∙∙ ∙ ∙ ∙∙∙ ∙ ∙ ∙∙∙∙∙∙∙ ∙∙∙ ∙∙ ∙ ∙∙ ∙ ∙∙∙Chapter 9 - Quality Control4. Sample Mean Range179.48 2.6 Mean Chart: =X ± A 2-R = 79.96 ± 0.58(1.87) 2 80.14 2.3 = 79.96 ± 1.083 80.14 1.2UCL = 81.04, LCL = 78.884 79.60 1.7 Range Chart: UCL = D 4-R = 2.11(1.87) = 3.95 5 80.02 2.0LCL = D 3-R = 0(1.87) = 0680.381.4[Both charts suggest the process is in control: Neither has any points outside the limits.]6. n = 200 Control Limits = np p p )1(2-±Thus, UCL is .0234 and LCL becomes 0.Since n = 200, the fraction represented by each data point is half the amount shown. E.g., 1 defective = .005, 2 defectives = .01, etc. Sample 10 is too large.7. 857.714110c ==Control limits: 409.8857.7c 3c ±=± UCL is 16.266, LCL becomes 0.All values are within the limits.14. Let USL = Upper Specification Limit, LSL = Lower Specification Limit,X = Process mean, σ = Process standard deviationFor process H:0096.)200(1325==p 0138.0096.200)9904(.0096.20096.±=±=}{capablenot ,0.193.93.04.1 ,938.min 04.1)32)(.3(1516393.)32)(.3(1.14153<===-=σ-=-=σ-pk C X USL LSL XFor process K:.1}17.1,0.1min{17.1)1)(3(335.3630.1)1)(3(30333===-=σ-=-=σ- C X USL LSL X pk Assuming the minimum acceptable pk C is 1.33, since 1.0 < 1.33, the process is not capable.For process T: 33.1}33.1,67.1min{33.1)4.0)(3(5.181.20367.1)4.0)(3(5.165.183===-=σ-=-=σ- C X USL LSL X pk Since 1.33 = 1.33, the process is capable.Chapter 10 - Aggregate Planning and Master Scheduling7. a. No backlogs are allowedPeriodForecast Output Regular Overtime Subcontract Inventory Beginning Ending Average Backlog Costs:RegularOvertimeSubcontractInventoryTotalb. Level strategyPeriodForecastOutputRegularOvertimeSubcontractInventoryBeginningEndingAverageBacklogCosts:RegularOvertimeSubcontractInventoryBacklogTotal8.PeriodForecastOutputRegularOvertimeSubcontractInventoryBeginningEndingAverageBacklogCosts:RegularOvertimeSubcontractInventoryBacklogTotalChapter 11 - MRP and ERP1. a. F: 2G: 1 H: 1 J: 2 x 2 = 4 L: 1 x 2 = 2 A: 1 x 4 = 4 D: 2 x 4 = 8 J: 1 x 2 = 2 D: 1 x 2 = 2Totals: F = 2; G = 1; H = 1; J = 6; D = 10; L = 2; A = 44. Master Schedule10. Week 1 2 3 4Material 40 80 60 70Week 1 2 3 4Labor hr. 160 320 240 280Mach. hr. 120 240 180 210a. Capacity utilizationWeek 1 2 3 4Labor 53.3% 106.7% 80% 93.3%Machine 60% 120% 90% 105%b. Capacity utilization exceeds 100% for both labor and machine in week2, and for machine alone in week 4.Production could be shifted to earlier or later weeks in which capacityis underutilized. Shifting to an earlier week would result in addedcarrying costs; shifting to later weeks would mean backorder costs.Another option would be to work overtime. Labor cost would increase dueto overtime premium, a probable decrease in productivity, and possibleincrease in accidents.Chapter 12 - Inventory Management2. The following table contains figures on the monthly volume and unit costs for a random sample of 16 items for a list of 2,000 inventory items.a. See table.b. To allocate control efforts.c. It might be important for some reason other than dollar usage, suchas cost of a stockout, usage highly correlated to an A item, etc.3. D = 1,215 bags/yr. S = $10 H = $75a. bags HDS Q 187510)215,1(22===b. Q/2 = 18/2 = 9 bagsc.orders ordersbags bags Q D 5.67/ 18 215,1== d . S QD H 2/Q TC +=350,1$675675)10(18215,1)75(218=+=+=e. Assuming that holding cost per bag increases by $9/bag/yearQ ==84)10)(215,1(217 bags71.428,1$71.714714)10(17215,1)84(217=+=+=TC Increase by [$1,428.71 – $1,350] = $78.714. D = 40/day x 260 days/yr. = 10,400 packagesS = $60 H = $30a. oxes b 20496.2033060)400,10(2H DS 2Q 0====b. S QD H 2Q TC +=82.118,6$82.058,3060,3)60(204400,10)30(2204=+=+=c. Yesd. )60(200400,10)30(2200TC 200+=TC 200 = 3,000 + 3,120 = $6,1206,120 – 6,118.82 (only $1.18 higher than with EOQ, so 200 isacceptable.)7. H = $2/month S = $55D 1 = 100/month (months 1–6)D 2 = 150/month (months 7–12)a. 16.74255)100(2Q :D H DS2Q 010===83.90255)150(2Q :D 02==b. The EOQ model requires this.c. Discount of $10/order is equivalent to S – 10 = $45 (revised ordering cost)1–6 TC74 = $148.32180$)45(150100)2(2150TC 145$)45(100100)2(2100TC *140$)45(50100)2(250TC 15010050=+==+==+=7–12 TC 91 = $181.66195$)45(150150)2(2150TC *5.167$)45(100150)2(2100TC 185$)45(50150)2(250TC 15010050=+==+==+=10. p = 50/ton/day u = 20 tons/day200 days/yr.S = $100H = $5/ton per yr.a. bags] [10,328 tons 40.5162050505100)000,4(2u p p H DS 2Q 0=-=-=b. ]bags 8.196,6 .approx [ tons 84.309)30(504.516)u p (P Q I max ==-=Average is92.154248.309:2I max =tons [approx. 3,098 bags] c. Run length =days 33.10504.516P Q == d. Runs per year = 8] approx .[ 7.754.516000,4QD ==e. Q ' = 258.2D= 20 tons/day x 200 days/yr. = 4,000 tons/yr.TC =S QDH 2I max + TC orig. = $1,549.00 TC rev. = $ 774.50Savings would be$774.5015.RangePHQD = 4,900 seats/yr. 0–999 $5.00 $2.00 495 H = .4P 1,000–3,9994.95 1.98 497 NFS = $50 4,000–5,9994.90 1.96 500 NF6,000+ 4.85 1.94 503 NFCompare TC 495 with TC for all lower price breaks:TC 495 = 495 ($2) + 4,900($50) + $5.00(4,900) = $25,4902 495TC 1,000 = 1,000 ($1.98) + 4,900($50) + $4.95(4,900) = $25,4902 1,000 TC 4,000 = 4,000 ($1.96) + 4,900($50) + $4.90(4,900) = $27,9912 4,000 TC 6,000 = 6,000 ($1.94) + 4,900($50) + $4.85(4,900) = $29,6262 6,000Hence, one would be indifferent between 495 or 1,000 units22. d = 30 gal./day ROP = 170 gal.QuantityTCLT = 4 days,ss = Zσd LT = 50 galRisk = 9% Z = 1.34 Solving, σd LT = 37.313% Z = 1.88, ss=1.88 x 37.31 = 70.14 gal. Chapter 13 - JIT and Lean Operations1. N = ?N = DT(1 + X)D = 80 pieces per hour CT = 75 min. = 1.25 hr.= 80(1.25)(1.35) = 3C = 45 45X = .354. The smallest daily quantity evenly divisible into all four quantities is3. Therefore, use three cycles.Product Daily quantity Units per cycleA 21 21/3 = 7B 12 12/3 = 4C 3 3/3 = 1D 15 15/3 = 55.a. Cycle 1 2 3 4A 6 6 5 5B 3 3 3 3C 1 1 1 1D 4 4 5 5E 2 2 2 2 b. Cycle 1 2A 11 11B 6 6C 2 2D 8 8E 4 4c. 4 cycles = lower inventory, more flexibility2 cycles = fewer changeovers7. Net available time = 480 –75 = 405. Takt time = 405/300 units per day = 1.35 minutes.Chapter 15 - Scheduling6. a. FCFS: A–B–C–DSPT: D–C–B–AEDD: C–B–D–ACR: A–C–D–BFCFS: Job time Flow time Due date DaysJob (days) (days) (days) tardyA 14 14 20 0B 10 24 16 8C 7 31 15 16D 6 37 17 2037 106 44SPT: Job time Flow time Due date DaysJob (days) (days) (days) tardyD 6 6 17 0C 7 13 15 0B 10 23 16 7A 14 37 20 1737 79 24EDD:Critical Ratiocompleted on day 14. After the completion of Job A, the revised critical ratios are:completed on day 21. After the completion of Job C, the revised critical ratios are:Job D has the lowest critical ratio therefore it is scheduled next and completed on day 27.The critical ratio sequence is A –C –D –B and the makespan is 37 days.b.ardi Flow time Average flow time Number of jobsDays tardy Average job t ness Number of jobs Flow timeAverage number of jobs at the center Makespan==∑=FCFS SPT EDD CR26.50 19.75 21.00 24.75 11.0 6.00 6.00 9.252.86 2.14 2.27 2.67c. SPT is superior.9.Thus, the sequence is b-a-g-e-f-d-c.。
《运营管理》课后习题答案

《运营管理》课后习题答案Chapter 02 - Competitiveness, Strategy, and Productivity3. (1) (2) (3) (4) (5) (6) (7)Week Output WorkerCost@$12x40Overhead********MaterialCost@$6TotalCostMFP(2) ÷ (6)1 30,000 2,880 4,320 2,700 9,900 3.032 33,600 3,360 5,040 2,820 11,220 2.993 32,200 3,360 5,040 2,760 11,160 2.894 35,400 3,840 5,760 2,880 12,480 2.84*refer to solved problem #2Multifactor productivity dropped steadily from a high of 3.03 to about 2.84.4. a. Before: 80 ÷ 5 = 16 carts per worker per hour.After: 84 ÷ 4 = 21 carts per worker per hour.b. Before: ($10 x 5 = $50) + $40 = $90; hence 80 ÷ $90 = .89 carts/$1.After: ($10 x 4 = $40) + $50 = $90; hence 84 ÷ $90 = .93 carts/$1.c. Labor productivity increased by 31.25% ((21-16)/16).Multifactor productivity increased by 4.5% ((.93-.89)/.89).*Machine ProductivityBefore: 80 ÷ 40 = 2 carts/$1.After: 84 ÷ 50 = 1.68 carts/$1.Productivity increased by -16% ((1.68-2)/2)Chapter 03 - Product and Service Design6. Steps for Making Cash Withdrawal from an ATM1. Insert Card: Magnetic Strip Should be Facing Down2. Watch Screen for Instructions3. Select Transaction Options:1) Deposit2) Withdrawal3) Transfer4) Other4. Enter Information:1) PIN Number2) Select a Transaction and Account3) Enter Amount of Transaction5. Deposit/Withdrawal: 1) Deposit —place in an envelope (which you’ll find near or in the ATM) andinsert it into the deposit slot2) Withdrawal —lift the ―Withdrawal Door,‖ being careful to remove all cash6. Remove card and receipt (which serves as the transaction record)8.Chapter 04 - Strategic Capacity Planning for Products and Services2. %80capacityEffective outputActual Efficiency ==Actual output = .8 (Effective capacity) Effective capacity = .5 (Design capacity) Actual output = (.5)(.8)(Effective capacity) Actual output = (.4)(Design capacity) Actual output = 8 jobs Utilization = .4capacityDesign outputActual =n Utilizatiojobs 204.8capacity Effective output Actual Capacity Design ===10. a. Given: 10 hrs. or 600 min. of operating time per day.250 days x 600 min. = 150,000 min. per year operating time.Total processing time by machineProductABC 1 48,000 64,000 32,000 2 48,000 48,000 36,000 3 30,000 36,000 24,000 460,000 60,000 30,000 Total 186,000208,000122,000machine181.000,150000,122machine 238.1000,150000,208machine224.1000,150000,186≈==≈==≈==C B A N N NYou would have to buy two ―A‖ machines at a total cost of $80,000, or two ―B‖ machines at a total cost of $60,000, or one ―C‖ machine at $80,000.b.Total cost for each type of machine:A (2): 186,000 min ÷ 60 = 3,100 hrs. x $10 = $31,000 + $80,000 = $111,000B (2) : 208,000 ÷ 60 = 3,466.67 hrs. x $11 = $38,133 + $60,000 = $98,133 C(1): 122,000 ÷ 60 = 2,033.33 hrs. x $12 = $24,400 + $80,000 = $104,400Buy 2 Bs —these have the lowest total cost.Chapter 05 - Process Selection and Facility Layout3.Desired output = 4Operating time = 56 minutesunit per minutes 14hourper units 4hourper minutes 65output Desired time Operating CT ===Task # of Following tasksPositional WeightA 4 23B 3 20C 2 18D 3 25E 2 18F 4 29G 3 24H 1 14 I5a. First rule: most followers. Second rule: largest positional weight.Assembly Line Balancing Table (CT = 14)b. First rule: Largest positional weight.Assembly Line Balancing Table (CT = 14)c. %36.805645stations of no. x CT time Total Efficiency === 4. a. l.2. Minimum Ct = 1.3 minutesTask Following tasksa 4b 3c 3d 2e 3f 2g 1h3. percent 54.11)3.1(46.CT x N time)(idle percent Idle ==∑=4. 420 min./day 323.1 ( 323)/1.3 min./OT Output rounds to copiers day CT cycle=== b. 1. inutes m 3.224.6N time Total CT ,6.4 time Total ==== 2. Assign a, b, c, d, and e to station 1: 2.3 minutes [no idle time]Assign f, g, and h to station 2: 2.3 minutes3. 420182.6 copiers /2.3OT Output day CT ===4.420 min./dayMaximum Ct is 4.6. Output 91.30 copiers /4.6 min./day cycle ==7.Chapter 06 - Work Design and Measurement 3.Element PR OT NT AF job ST1 .90.46.414 1.15 .4762 .85 1.505 1.280 1.15 1.4723 1.10.83.913 1.15 1.05041.00 1.16 1.160 1.15 1.334Total4.3328. A = 24 + 10 + 14 = 48 minutes per 4 hours .min 125.720.11x70.5ST .min 70.5)95(.6NT 20.24048A =-=====9. a. Element PR OT NT A ST1 1.10 1.19 1.309 1.15 1.5052 1.15 .83 .955 1.15 1.09831.05.56.588 1.15 .676b.01.A 00.2z 034.s 83.x ==== 222(.034)67.12~68.01(.83)zs n observations ax ??===c. e = .01 minutes 47 to round ,24.4601.)034(.2e zs n 22=??=??? ??=Chapter 07- Location Planning and Analysis1. Factor Local bank Steel mill Food warehouse Public school 1. Convenience forcustomers H L M–H M–H2. Attractiveness ofbuilding H L M M–H3. Nearness to rawmaterials L H L M4. Large amounts ofpower L H L L5. Pollution controls L H L L6. Labor cost andavailability L M L L7. Transportationcosts L M–H M–H M8. Constructioncosts M H M M–HLocation (a) Location (b)4. Factor A B C Weight A B C1. Business Services 9 5 5 2/9 18/9 10/9 10/92. Community Services 7 6 7 1/9 7/9 6/9 7/93. Real Estate Cost 3 8 7 1/9 3/9 8/9 7/94. Construction Costs 5 6 5 2/9 10/9 12/9 10/95. Cost of Living 4 7 8 1/9 4/9 7/9 8/96. Taxes 5 5 5 1/9 5/9 5/9 4/97. Transportation 6 7 8 1/9 6/9 7/9 8/9Total 39 44 45 1.0 53/9 55/9 54/9 Each factor has a weight of 1/7.a. Composite Scores 39 44 45 7 7 7B orC is the best and A is least desirable.b. Business Services and Construction Costs both have a weight of 2/9; the other factors eachhave a weight of 1/9.5 x + 2 x + 2 x = 1 x = 1/9c. Composite ScoresA B C 53/9 55/9 54/9B is the best followed byC and then A.5.Locationx yA 3 7B 8 2C 4 6D 4 1E 6 4Totals 25 20-x =∑x i= 25 = 5.0 -y =∑y i= 20 = 4.0 n 5 n 5Hence, the center of gravity is at (5,4) and therefore the optimal location.Chapter 08 - Management of Quality1. ChecksheetWork Type FrequencyLube and Oil 12Brakes 7Tires 6Battery 4Transmission 1Total 30ParetoLube & Oil Brakes Tires Battery Trans.2 .The run charts seems to show a pattern of errors possibly linked to break times or the end of the shift. Perhaps workers are becoming fatigued. If so, perhaps two 10 minute breaks in the morning and again in the afternoon instead of one 20 minute break could reduce some errors. Also, errors are occurring during the last few minutes before noon and the end of the shift, and those periods should also be given management’s attention.4break lunch break3 2 1 0Chapter 9 - Quality Control4. Sample Mean Range179.48 2.6 Mean Chart: =X ± A 2-R = 79.96 ± 0.58(1.87) 2 80.14 2.3 = 79.96 ± 1.083 80.14 1.2UCL = 81.04, LCL = 78.884 79.60 1.7 Range Chart: UCL = D 4-R = 2.11(1.87) = 3.95 5 80.02 2.0LCL = D 3-R = 0(1.87) = 0680.381.4[Both charts suggest the process is in control: Neither has any points outside the limits.]6. n = 200 Control Limits = np p p )1(2-±Thus, UCL is .0234 and LCL becomes 0.Since n = 200, the fraction represented by each data point is half the amount shown. E.g., 1 defective = .005, 2 defectives = .01, etc.Sample 10 is too large.7. 857.714110c ==Control limits: 409.8857.7c 3c ±=± UCL is 16.266, LCL becomes 0.All values are within the limits.14. Let USL = Upper Specification Limit, LSL = Lower Specification Limit,X = Process mean, σ = Process standard deviationFor process H:}{capablenot ,0.193.93.04.1 ,938.min 04.1)32)(.3(1516393.)32)(.3(1.14153<===-=σ-=-=σ-pk C X USL LSL X 0096.)200(1325==p 0138.0096.200)9904(.0096.20096.±=±=For process K:.1}17.1,0.1min{17.1)1)(3(335.3630.1)1)(3(30333===-=σ-=-=σ- C X USL LSL X pk Assuming the minimum acceptable pk C is 1.33, since 1.0 < 1.33, the process is not capable.For process T:33.1}33.1,67.1min{33.1)4.0)(3(5.181.20367.1)4.0)(3(5.165.183===-=σ-=-=σ- C X USL LSL X pk Since 1.33 = 1.33, the process is capable.Chapter 10 - Aggregate Planning and Master Scheduling7. a. No backlogs are allowedPeriodForecast Output Regular Overtime Subcontract Output - Forecast Inventory Beginning Ending Average Backlog Costs: Regular Overtime Subcontract Inventory Totalb. Level strategyPeriodForecastOutputRegularOvertimeSubcontract Output - Forecast Inventory Beginning Ending Average Backlog Costs:Regular Overtime Subcontract Inventory BacklogTotal8.PeriodForecastOutputRegularOvertimeSubcontractOutput- ForecastInventoryBeginningEndingAverageBacklogCosts:RegularOvertimeSubcontractInventoryBacklogTotalChapter 11 - MRP and ERP1. a. F: 2 G: 1 H: 1J: 2 x 2 = 4 L: 1 x 2 = 2 A: 1 x 4 = 4D: 2 x 4 = 8 J: 1 x 2 = 2 D: 1 x 2 = 2Totals: F = 2; G = 1; H = 1; J = 6; D = 10; L = 2; A = 44. Master Schedule10. Week 1 2 3 4Material 40 80 60 70Week 1 2 3 4Labor hr. 160 320 240 280Mach. hr. 120 240 180 210a. Capacity utilizationWeek 1 2 3 4Labor 53.3% 106.7% 80% 93.3%Machine 60% 120% 90% 105%b. C apacity utilization exceeds 100% for both labor and machine in week 2, and formachine alone in week 4.Production could be shifted to earlier or later weeks in which capacity isunderutilized. Shifting to an earlier week would result in added carrying costs;shifting to later weeks would mean backorder costs.Another option would be to work overtime. Labor cost would increase due toovertime premium, a probable decrease in productivity, and possible increase inaccidents.Chapter 12 - Inventory Management2.The following table contains figures on the monthly volume and unit costs for a random sample of 16 items for a list of 2,000 inventory items.a. See table.b. To allocate control efforts.c. It might be important for some reason other than dollar usage, such as cost of astockout, usage highly correlated to an A item, etc.3. D = 1,215 bags/yr. S = $10 H = $75a. bags HDS Q 187510)215,1(22===b. Q/2 = 18/2 = 9 bagsc.orders ordersbags bags Q D 5.67/ 18 215,1== d . S QD H 2/Q TC +=350,1$675675)10(18215,1)75(218=+=+=e. Assuming that holding cost per bag increases by $9/bag/yearQ ==84)10)(215,1(217 bags71.428,1$71.714714)10(17215,1)84(217=+=+=TCIncrease by [$1,428.71 – $1,350] = $78.714.D = 40/day x 260 days/yr. = 10,400 packagesS = $60 H = $30a. oxes b 20496.2033060)400,10(2H DS 2Q 0====b. S QD H 2Q TC +=82.118,6$82.058,3060,3)60(204400,10)30(2204=+=+=c. Yesd. )60(200400,10)30(2200TC 200+=TC 200 = 3,000 + 3,120 = $6,1206,120 – 6,118.82 (only $1.18 higher than with EOQ, so 200 is acceptable.)7.H = $2/month S = $55D 1 = 100/month (months 1–6)D 2 = 150/month (months 7–12)a. 16.74255)100(2Q :D H DS2Q 010===83.90255)150(2Q :D 02==b. The EOQ model requires this.c. Discount of $10/order is equivalent to S – 10 = $45 (revised ordering cost)1–6 TC74 = $148.32180$)45(150100)2(2150TC 145$)45(100100)2(2100TC *140$)45(50100)2(250TC 15010050=+==+==+=7–12 TC 91 =$181.66195$)45(150150)2(2150TC *5.167$)45(100150)2(2100TC 185$)45(50150)2(250TC 15010050=+==+==+=10. p = 50/ton/day u = 20 tons/day200 days/yr.S = $100 H = $5/ton per yr.a. bags] [10,328 tons 40.5162050505100)000,4(2u p pH DS 2Q 0=-=-=b. ]bags 8.196,6 .approx [ tons 84.309)30(504.516)u p (P Q I m ax ==-=Average is92.154248.309:2I m ax =tons [approx. 3,098 bags] c. Run length =days 33.10504.516P Q == d. Runs per year = 8] approx.[ 7.754.516000,4QD == e. Q ' = 258.2TC =S QD H 2I max + TC orig. = $1,549.00 TC rev. = $ 774.50Savings would be $774.50D= 20 tons/day x 200 days/yr. = 4,000 tons/yr.15. RangeP H Q D = 4,900 seats/yr. 0–999 $5.00 $2.00 495 H = .4P 1,000–3,999 4.95 1.98 497 NF S = $50 4,000–5,999 4.90 1.96 500 NF 6,000+ 4.85 1.94503 NFCompare TC 495 with TC for all lower price breaks:TC 495 = 495 ($2) + 4,900($50) + $5.00(4,900) = $25,4902 495 TC 1,000 = 1,000 ($1.98) + 4,900($50) + $4.95(4,900) = $25,4902 1,000 TC 4,000 = 4,000 ($1.96) + 4,900($50) + $4.90(4,900) = $27,9912 4,000 TC 6,000 = 6,000 ($1.94) + 4,900($50) + $4.85(4,900) = $29,6262 6,000Hence, one would be indifferent between 495 or 1,000 units22. d = 30 gal./day ROP = 170 gal. LT = 4 days,ss = Z σd LT = 50 galRisk = 9% Z = 1.34 Solving, σd LT = 37.31 3% Z = 1.88, ss=1.88 x 37.31 = 70.14 gal.Chapter 13 - JIT and Lean Operations 1. N = ?N = DT(1 + X)D = 80 pieces per hourC T = 75 min. = 1.25 hr. = 80(1.25) (1.35) = 3C = 45 45X = .35QuantityTC。
- 1、下载文档前请自行甄别文档内容的完整性,平台不提供额外的编辑、内容补充、找答案等附加服务。
- 2、"仅部分预览"的文档,不可在线预览部分如存在完整性等问题,可反馈申请退款(可完整预览的文档不适用该条件!)。
- 3、如文档侵犯您的权益,请联系客服反馈,我们会尽快为您处理(人工客服工作时间:9:00-18:30)。
50
0
闲置时比
0.5/4.5= 11.11%
闲置时比
7/200=3. 5%
第8题
图-PPT, 节拍 400/200= 2分钟 总时长 8.5/2=4. 25取整5 个工作地
工作地
1 2 3 4 5
作业
a,b c,d e,f,i g,j,h k,m
时间 闲置时间
1.9
0.1
1.9
0.1
2
0
1.5
0.5
1.4
0.1
1.4
0.1
图-PPT, 总时长 193 7*60*60/ 500=50.4 秒 193/50.4 =3.83取 整4个工 作地 可采纳以 50秒为生 产节拍, 工作地闲 置时间可 利用,理 论上的最 小节拍。
工作地
1 2 3 4
作业
时间 闲置时间
d
50
0
a
45
5
b,e,f
48
2
c,g,h,i,j
行程数 成本 总成本
10
800 14150
20 1400
40 2400
55 2750
80 3200
90 3600
第15、16 、17、18 题略
效率 83.33%
1-16.67%
效率 80.36%
1-19.64%
效率 88.46%
1-11.54%
8 4 6
C2
工作地 1 2 3 4
作业 a b,e d,c,f g,h
时间 闲置时间
1.4
0.4
1.3
0.5
1.8
0
1.5
0.3
闲置时间 百分比
16.67% 1.2/(1.8 *4)=1/6
工作时间 56分钟 产量4 节拍14分 钟 作业 总时长45 分 工作 地 45/14=3. 21取整4 个
工作地 作业 1 f,a,g
时间 闲置时间
14
0
闲置时间 百分比
19.64%
2 d,b,c
3 e,h 4i
13
1
13
1
5
9
第4题
图-PPT
总时长 4.6/最小 节拍 1.3=3.54 取整4个工 作地
工作地 作业 1 a,b,c,e
时间
闲置时间
1
0.3
2d
1.3
0
3 f,g
1.1
0.2
4h 若只能使 用2个工 作地 则 最小节拍 为2.3分 钟 该节 拍可行 工作地 作业
第1题 第2题 第3题
1
最小节拍 2.4分钟
2
450/2.4=1 87.5
18/2.4=7.
3 5 取整
8个工作地
4
450/125=3 .6分钟
5
450/9=50 450/15=30
最大节拍18分钟
450/18=2 5
产量范围 25-187.5
产量 33.33/时 时间60分 钟 节拍 60/33.33 =1.8分钟 工作地 6/1.8=3. 33 取整4 个
1.2
0.8
闲置时比
1.5/10=1 5%
第9题
1
6
4
2
5
3
答案不唯 一 经列交换 或行交换 可得其它 答案
第10题 第11题
答案略 1 3 6
5
4
8
7
2
第13题
3
1
9
7
5
2
第12题
5
1
4
6 第14题 A1
B4
3
2
7
8
D3
第14题
位置 A-C A-D C-D B-D A-B B-C
距离
部门 80 1--2 70 1--3 60 2--3 50 3--4 40 1--4 40 2--4
1.2
0.1
时间 闲置时间
1 a,b,c,e,d
2.3
0
2 f,g,h
2.3
0
第5题
图-PPT, 工作时间 8*60=480 分日 产量240 单位 节拍 480/240= 2分钟
工作地 作业 1 a,b,c,f
时间
闲置时间
ቤተ መጻሕፍቲ ባይዱ
2
0
11/(14*4 )=0.1964
闲置时间 百分比
11.54% 0.6/(1.3 *4)=0.11 54 420/1.3= 323个
闲置时比
0%
420/2.3=
182.6个
420/4.6=
91.3个
闲置时比
1.4/6=23 .33%
第6题
2 d,e 3g
图-PPT, 总时长4/ 节拍 1.5=2.67 取整3个 工作地
1.6
0.4
1
1
第7题
工作地
1 2 3
作业
时间 闲置时间
a,b,c d,e,f,g,h i,j,k,l
1.2
0.3