高线工艺及设备选用
高线生产简介

高速线材生产设备
二、轧机
高线厂15#~28#均为旋臂式轧机,15#~18#轧机布置 形式为平立交替式,传动方式为单独传动。19#~28#布置形 式为顶角45度,传动方式为集体传动。各架次轧机规格如下:
架次 规格 15#~18# φ285 19#~23# φ228 24#~28# φ170
(3)加热质量好。完全消除了粘钢、翻炉的限制,很大程度上消除了 钢坯黑印,坯料下表面也不会造成划伤
(4)能耗低。由于采用蓄热式,废气排放时经过蓄热式,蓄热体将高 温废气的热量留下给换向后的空气和煤气预热,大大降低了能耗损失。
高速线材生产设备
一、加热炉
高速线材生产设备
二、轧机
高线厂1#~14#均为短应线轧机,轧机布置形式为平立 交替式。短应力线轧机和闭口式轧机相比具有投资少,刚度 大、更换方便的特点。各架次轧机规格如下:
(1)尽量实现钢坯热送。
(2)避免强制加热,加热能力不足时可适当待温。
(3)轧制节奏允许时加大步距,减少钢坯在炉内停 留时间。
高速线材生产工艺
二、加热
4、钢坯除鳞 国内线材生产线钢坯高 压水除鳞是近几年才投入使 用的,因为以前国内线材产 品大多为建筑用材,对表面 质量要求不严格,而且线材 粗轧都有几架箱型孔,有较 好的去除氧化铁皮的效果。 随着线材产品的不断升级, 对线材产品表面质量的要求 不断提高,国内新投产的生 产线都配备了高压水除鳞设 备。
高速线材生产工艺
二、加热
1、原料
线材的原料为小方坯,一般为150*150或 160*160的连铸小方坯,单支重量一般在2~2.5吨。 由于一部分冷墩钢和硬线拉丝用线材需要有较高的 致密度,所以有些钢厂也开始采用初轧坯来做高线 的原料。
高线
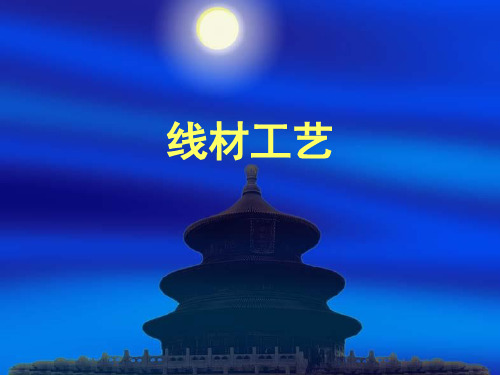
工艺流程
各区域主要设备及工艺特点
加热炉:目前加热炉一般采用侧进侧出步进 式煤气加热炉.
基本组成
复杂的热工设备,由炉膛与炉衬、燃 料系统、供风系统、排烟系统、冷却 系统、余热利用装置、装出料设备、 检测及调节装置、电子计算机控制系 统等构成 。
加热目的
①提高塑性,降低变形抗力,便于轧热到1200℃时,变形抗力下降到29Mpa, 只相当于室温下变形抗力的1/20; ②消除铸坯中某些组织缺陷与应力; ③为钢的组织性能的改善创建转变的条件;
线材生产线简介
线材生产按其流程特点基本上划分为3 线材生产按其流程特点基本上划分为3大工 可细分为6个工序),即原料加热、 ),即原料加热 序(可细分为6个工序),即原料加热、轧制 控冷、精整成品库。 控冷、精整成品库。轧制工序的区域包括从 加热炉出口直至吐丝机区域。 加热炉出口直至吐丝机区域。轧制区中最主 要的设备是轧线上的主轧机( 要的设备是轧线上的主轧机(包括传动装 ),以及一些辅助设备 飞剪、活套等) 以及一些辅助设备( 置),以及一些辅助设备(飞剪、活套等). 采用仿摩根5 45°顶交精轧机, 采用仿摩根5代45°顶交精轧机,水冷加风冷 的斯太尔摩冷却工艺。 的斯太尔摩冷却工艺。
各区域主要设备及工艺特点简介
精轧机:精轧机组为集体传动,10架轧机交替与水 平面成45°和135°设置,即相临机架互相垂直,与 平立交替布置相当,轧件不需扭转,采用WC辊环。 控制方式为:精确的传动比、配辊及辊缝设定实现 微张力轧制。作用以小的压下使轧件逐渐减径延伸, 得到表面质量和尺寸精度良好的成品。 生产过程中不是所有机架都会用到,根据规格不同, 投入使用的机架数不同。
Q235热轧圆盘条主要工艺参数 Q235热轧圆盘条主要工艺参数
高线生产的主要设备、选用
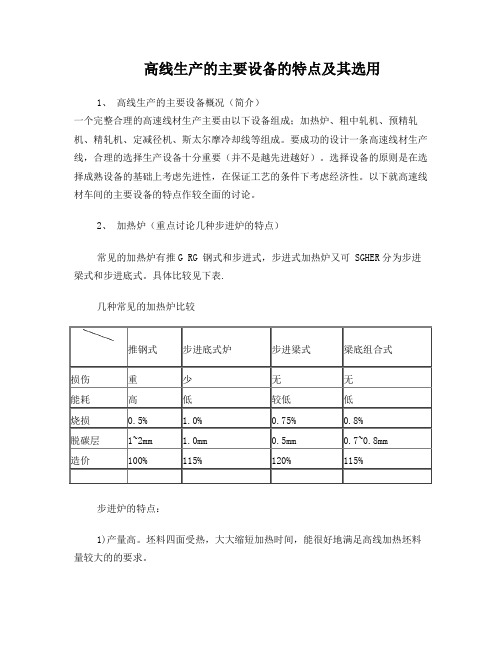
高线生产的主要设备的特点及其选用
1、高线生产的主要设备概况(简介)
一个完整合理的高速线材生产主要由以下设备组成;加热炉、粗中轧机、预精轧机、精轧机、定减径机、斯太尔摩冷却线等组成。
要成功的设计一条高速线材生产线,合理的选择生产设备十分重要(并不是越先进越好)。
选择设备的原则是在选择成熟设备的基础上考虑先进性,在保证工艺的条件下考虑经济性。
以下就高速线材车间的主要设备的特点作较全面的讨论。
2、加热炉(重点讨论几种步进炉的特点)
常见的加热炉有推G RG 钢式和步进式,步进式加热炉又可 SGHER分为步进梁式和步进底式。
具体比较见下表.
几种常见的加热炉比较
推钢式步进底式炉步进梁式梁底组合式
损伤重少无无
能耗高低较低低
烧损0.5% 1.0% 0.75% 0.8%
脱碳层1~2mm 1.0mm 0.5mm 0.7~0.8mm
造价100% 115% 120% 115% 步进炉的特点:
1)产量高。
坯料四面受热,大大缩短加热时间,能很好地满足高线加热坯料量较大的的要求。
青钢60万t高线工艺技术装备及特点
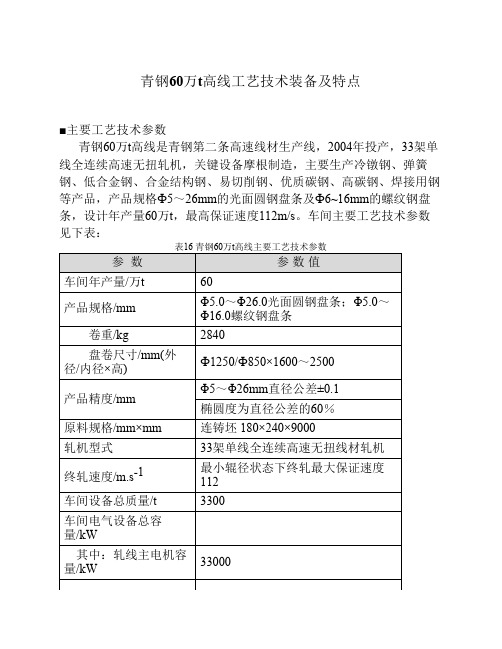
2)散卷冷却运输线:带有佳灵系统的斯太尔摩大风量辊式延迟冷却 型。总长约110.6m,11段冷却,冷却速度0.3~17℃/s,冷却风机共16 台,风压2.94kPa、每台风量154000m3/h。
3)集卷站:由鼻锥、带盘卷托板的集卷筒、旋转双芯棒和挂卷小车 等组成,均为液压传动。最大盘卷重量2840kg,最大盘卷高度约3.4m。
控制精度:
±0.10mm
(3)剪机
整个轧线共设有7台剪机,其中3台飞剪机分别设置在粗轧机组
(二)第七机架后、中轧机组第13机架后、精轧机组前,用于剪切轧件 头部和尾部,并可起事故碎断作用; 4台卡断剪,分别设置在4#轧机
前、20#轧机前、精轧机组前和减径定径机组前。
(4)测径仪 在减定径机组前后各设置一台,用于测量和显示进减定径机出减
条,设计年产量60万t,最高保证速度112m/s。车间主要工艺技术参数
见下表:
表16 青钢60万t高线主要工艺技术参数
参数
参数值
车间年产量/万t
60
产品规格/mm
Φ5.0~Φ26.0光面圆钢盘条;Φ5.0~ Φ16.0螺纹钢盘条
卷重/kg
2840
盘卷尺寸/mm(外 径/内径×高)
Ф1250/Ф850×1600~2500
4) 单轨钩式运输机:横钩布置,运输线长度约480m,小车数量60 个,小车运行速度18m/min。
5)自动压紧打捆机:卧式,最大压紧力400kN,压紧后最大高度 3440mm,捆线Ф6.3~Ф7.3mm,液压压紧和打捆、捆扎4道。
6)卸卷站:由卸卷小车和收集台架组成;双卸卷位置,每工位存放2卷。
采用脱头轧;
(2)采用180×240mm的矩形坯作原料,加大了最终产品的压缩 比,又避免第一机架因轧速过低而产生的烫辊问题;
韶钢国产新高线品种钢生产工艺
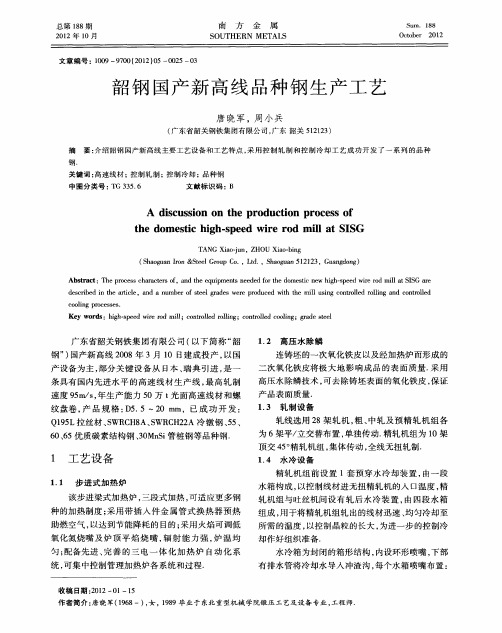
收 稿 日期 :0 2— 1— 5 2 1 0 1
却作 好 组织 准备 . 水 冷 箱为 封 闭的箱 形结 构 , 内设 环形 喷嘴 , 下部 有 排水 管将 冷却 水 导入 冲渣 沟 , 每个水 箱 喷嘴 布置 :
作 者 简 介 : 晓 军 (9 8一) 女 ,18 唐 16 , 99毕 业 于 东北 重 型 机 械 学 院 锻 压 工 艺及 设 备 专业 , 程 师 工
总第 18期 8
21 0 2年 1 O月
南
方
金
属
S m. 1 8 u 8
S OUTHERN ETAL M S
0co e 2 1 tb r 0 2
文 章 编 号 :10 0 9—90 2 1 )5— 0 5— 3 70{0 2 0 0 2 0
韶 钢 国产 新 高 线 品种 钢 生 产 工 艺
精 轧 机 组前 设 置 l套 预穿 水 冷 却 装 置 , 由一 段 水 箱构 成 , 以控 制线 材进 无扭 精轧 机 的人 口温 度 , 精 轧 机组 与 吐丝机 间设 有 轧后 水 冷装 置 , 由四段 水 箱
组成 , 用于将 精 轧机 组轧 出的线材 迅 速 、 匀冷 却 至 均
所 需 的温度 , 以控制 晶粒 的 长大 , 为进 一步 的控 制 冷
唐 晓军 , 小 兵 周
( 东省韶关 钢铁集团有限公司 , 东 韶关 522 ) 广 广 11 3
摘
要: 介绍韶 钢国产新高线主要工艺设备 和工艺特点 , 用控 制轧制 和控 制冷却 工艺成 功开发 了一 系列 的品种 采
钢.
关键词 : 速线 材 ; 高 控制轧制 ; 控制冷却 ;品种钢
青特钢二三高线工艺设备简介

轧 速度 , 配合 T MB双模 块 轧 机 时 , 最 大轧 制 速度 可 达1 4 0 m / s ( 设 计 最 大 轧制 速 度 可 达 1 7 0 m / s ) , 大 幅
尺度大 , 总压下量大 , 故采用脱头辊道 。轧线设计
( 青 岛特殊钢铁有限公司 , 山东 青 岛 2 6 6 o o o )
摘
要: 介绍 了青岛特殊钢铁二 三高线的生产工艺 , 重 点介绍采用 的达涅利双模块轧机 、 双 管吐丝机和轮廓仪 等新工艺装
备特点 , 生产线可稳定生产 5 . 0 ~ 7 . 0 m i l l 的帘线钢 、 冷镦 钢等线材产品。 关键词 : 高速线材 ; 双模块轧机 ; 双管吐丝机 ; 轮廓仪
中图分类号 : T G3 3 8 文献标识码 : B 文章编 号: 1 0 0 4 — 4 6 2 0 ( 2 0 1 6 ) 0 6 — 0 1 0 1 — 0 1
1 前
言
青 岛特 殊 钢 铁 有 限公 司根 据 国家 环保 搬 迁 政 策要求 , 在黄岛西海岸新区建设两条新的高速线材
齿 隙 的止 推轴 承 , 可有 效 降低轧 制 载荷 对设 备 的变
形, 提 升 线 材 产 品 的加 工精 度 , 对于 5 . 0 m m和 5 . 5
低 了主 电机功率 , 节能降耗 , 也为后期生产 中减低
电单 耗 和降低 吨钢生产成 本奠定 了坚 实基础 n 。
m m高精度 帘线钢 用母材有 重要 意义 。
青 特钢 双模块 T MB采用 一椭 三 圆的孔 型系统 ,
3 新技 术及设 备
3 . 1 D WB 精 轧机/ T MB双模 块轧机
高速线材和大盘卷生产线工艺及设备特点
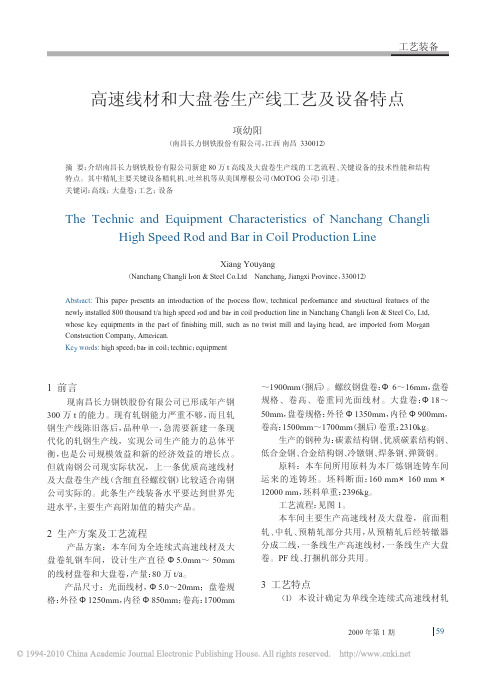
1前言现南昌长力钢铁股份有限公司已形成年产钢300万t的能力。
现有轧钢能力严重不够,而且轧钢生产线陈旧落后,品种单一,急需要新建一条现代化的轧钢生产线,实现公司生产能力的总体平衡,也是公司规模效益和新的经济效益的增长点。
但就南钢公司现实际状况,上一条优质高速线材及大盘卷生产线(含细直径螺纹钢)比较适合南钢公司实际的。
此条生产线装备水平要达到世界先进水平,主要生产高附加值的精尖产品。
2生产方案及工艺流程产品方案:本车间为全连续式高速线材及大盘卷轧钢车间,设计生产直径Ф5.0mm~50mm 的线材盘卷和大盘卷,产量:80万t/a。
产品尺寸:光面线材,Ф5.0~20mm;盘卷规格:外径Ф1250mm,内径Ф850mm;卷高:1700mm ~1900mm(捆后)。
螺纹钢盘卷:Ф6~16mm,盘卷规格、卷高、卷重同光面线材。
大盘卷:Ф18~50mm,盘卷规格:外径Ф1350mm,内径Ф900mm,卷高:1500mm~1700mm(捆后)卷重:2310kg。
生产的钢种为:碳素结构钢、优质碳素结构钢、低合金钢、合金结构钢、冷镦钢、焊条钢、弹簧钢。
原料:本车间所用原料为本厂炼钢连铸车间运来的连铸坯。
坯料断面:160mm×160mm×12000mm,坯料单重:2396kg。
工艺流程:见图1。
本车间主要生产高速线材及大盘卷,前面粗轧、中轧、预精轧部分共用,从预精轧后经转辙器分成二线,一条线生产高速线材,一条线生产大盘卷。
PF线、打捆机部分共用。
3工艺特点(1)本设计确定为单线全连续式高速线材轧高速线材和大盘卷生产线工艺及设备特点项幼阳(南昌长力钢铁股份有限公司,江西南昌330012)摘要:介绍南昌长力钢铁股份有限公司新建80万t高线及大盘卷生产线的工艺流程、关键设备的技术性能和结构特点。
其中精轧主要关键设备精轧机、吐丝机等从美国摩根公司(MOTOG公司)引进。
关键词:高线;大盘卷;工艺;设备The Technic and Equipment Characteristics of Nanchang Changli High Speed Rod and Bar in Coil Production LineXiang Youyang(Nanchang Changli Iron&Steel Co.Ltd Nanchang,Jiangxi Province,330012)Abstract:This paper presents an introduction of the process flow,technical performance and structural features of the newly installed800thousand t/a high speed rod and bar in coil production line in Nanchang Changli Iron&Steel Co,Ltd, whose key equipments in the part of finishing mill,such as no twist mill and laying head,are imported from Morgan Construction Company,American.Key words:high speed;bar in coil;technic;equipment机,粗、中、预精轧机为短应力线轧机,Ф5.0~7.5mm线材的保证速度为112m/s。
高线的工艺流程
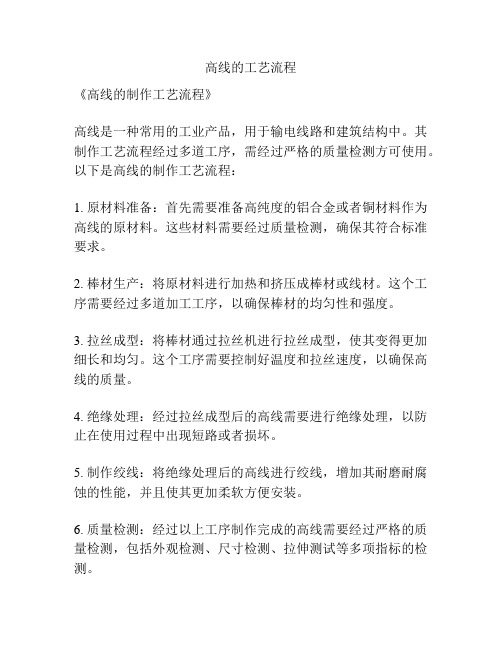
高线的工艺流程
《高线的制作工艺流程》
高线是一种常用的工业产品,用于输电线路和建筑结构中。
其制作工艺流程经过多道工序,需经过严格的质量检测方可使用。
以下是高线的制作工艺流程:
1. 原材料准备:首先需要准备高纯度的铝合金或者铜材料作为高线的原材料。
这些材料需要经过质量检测,确保其符合标准要求。
2. 棒材生产:将原材料进行加热和挤压成棒材或线材。
这个工序需要经过多道加工工序,以确保棒材的均匀性和强度。
3. 拉丝成型:将棒材通过拉丝机进行拉丝成型,使其变得更加细长和均匀。
这个工序需要控制好温度和拉丝速度,以确保高线的质量。
4. 绝缘处理:经过拉丝成型后的高线需要进行绝缘处理,以防止在使用过程中出现短路或者损坏。
5. 制作绞线:将绝缘处理后的高线进行绞线,增加其耐磨耐腐蚀的性能,并且使其更加柔软方便安装。
6. 质量检测:经过以上工序制作完成的高线需要经过严格的质量检测,包括外观检测、尺寸检测、拉伸测试等多项指标的检测。
7. 包装出厂:质量合格的高线进行包装和标识,做好出厂准备。
以上是高线的制作工艺流程,每一道工序都需要严格控制和检测,以确保高线的质量和可靠性。
制作出的高线产品要经过市场和用户的验证,得到认可后才能广泛应用。
大盘卷高速线材生产线工艺与设备简介

2020/1/25
18
吐丝机技术参数表
功能 位置 平均卷径 散卷直径范围 吐丝锥倾角 运行速度(标准) 吐丝管规格 更换吐丝管时间 润滑方式 润滑系统压力 吐丝盘旋转方向 吐丝头速度振幅 吐丝头振动频率 2总020速/1/2比5
主要设备性能
使线材形成散卷并输送到LCC风冷线 LCC风冷线前
Ф 1080mm Ф 1040mm~Ф 1100mm 10° 125m/s
Time
2020/1/25
10
8
6
water pressure of inline control 4
2
750 0
200
400
600
800
1000
1200
bille t le nght [m]
1400
1600
1800
0 2000
2020/1/25
31
控温轧制技术——低温轧制
1300
Roughing mill (8 passes)
1
大盘卷高速线材生产线概述
• 高速线材轧制线由2架CL线材预精轧机组、6架WRB线材精轧机组和4架FRS 线材减定径机组组成。轧制线采用S形大回环布置,其上装备有2个大容量的水 平活套、3个夹送辊和3个分钢道岔。
• S形大回环的布置形式使得高速线材可实现比较灵活的生产方式。 • LCC®(散卷冷却运输线)带有16台风机和保温罩,可以根据轧制规格和品种
辊身宽度
72mm
62mm
安装机架
24/25/26/30/31
27/28/29/32/33
辊环更换时间
6min
导卫更换时间
5min
传动
5000KW交流电机集中传动
高线生产工艺及常规培料规格

高线生产工艺及常规培料规格概述:线材一般是指直径为5~16mm的热轧圆钢或相当该断面的异型钢,因以盘卷状态交货,统称为线材或盘条。
国外线材规格已扩大到Φ50mm。
常见线材多为圆断面,异型断面线材有椭圆形、方形及螺纹形等,但生产数量很少。
线材品种按化学成分分类,一般分为低碳线材(称软线)、中高碳线材(硬线),还有低合金与合金钢线材、不锈钢线材及特殊钢线材(轴承、工具、精密等)几大类。
量大面广的品种属碳素钢线材,占线材总量的80~90%。
定义:高线生产是先将连铸坯送入步进式加热炉进行加热,进入高架式机组的粗轧、中轧、预精轧、精轧道次进行轧制(包括飞剪切头、尾),中间穿水冷却,经吐丝机形成线圈,经风冷辊道运输机冷却和集卷,P&F线输送冷却,压紧自动打包,称重、标牌后入库。
轧制中产生的切头、尾及中间冷条废钢经处理后回收至炼钢转炉使用,产生的氧化铁皮回收至烧结工序中配加循环使用。
一般将轧制速度大于40m/s的线材轧机称为高速线材轧机。
高速线材轧机的生产工艺特点:连续、高速、无扭和控冷。
其中高速轧制是最主要的工艺特点(此外,单线、微张力、组合结构、碳化钨辊环和自动化)。
流程:钢坯验收→编组→排钢→加热→出钢→粗轧→1#飞剪→中轧→2#飞剪→ 预精轧→预水冷→3#飞剪→精轧→穿水冷却→吐丝→风冷→集卷→检验→切头尾→打包→称重→标识→入库。
主要工艺参数:水电加热炉:加热炉步进机构分为步进梁和步进机械。
步进梁包括固定梁和活动梁,并采用步进梁交叉技术,即在装料端设固定梁4根,出料端设固定梁5根,炉内通长设置活动梁4根,9根梁分段并交叉布置,能实现梁与钢坯接触位置的不停倒换,有效消除“黑印”现象。
步进机械为双层框架式结构,上层框架为平移框架,下层框架为升降框架,在升降框架的上部和下部各安装有5组10个轮子完成升降和平移动作。
在平移框架和升降框架上各安装有2组8个防止跑偏的导轮。
步进机械采用全液压传动,平移框架和升降框架由钢梁制成。
高速线材工艺技术及设备
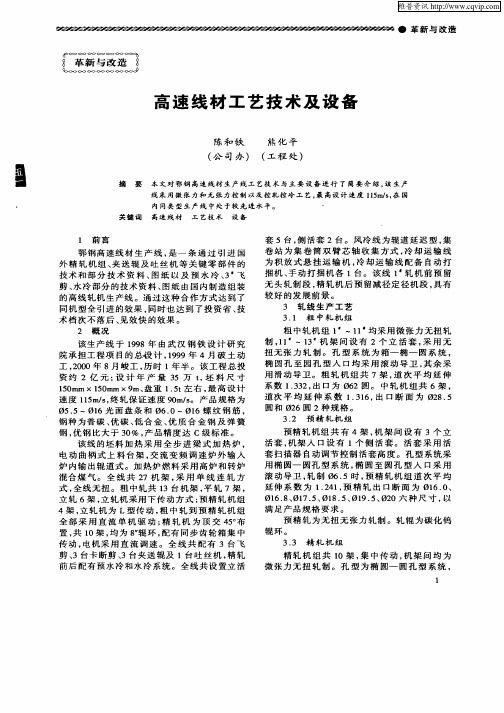
该 生 产 线 于 19 9 8年 由 武 汉 钢 铁 设 计 研 究 院 承 担 工 程 项 目的 总设 计 ,9 9年 4月 破 土 动 19 工 ,0 0年 8月 峻 工 , 时 1年半 。 该 工 程 总 投 20 历 资 约 2亿 元 ; 计 年 产 量 3 设 5万 t 坯 料 尺 寸 , 10 m×10 m×9 盘 重 1 5 左 右 , 高 设 计 5r a 5r a m、 .t 最 速 度 15rs 终 轧 保 证 速 度 9 m s 产 品 规格 为 1r , d 0 /。 0 . 5 5~01 6光 面 盘 条 和 0 . 6 0~0 6螺 纹 钢 筋 , 1 钢 种 为 普 碳 、 碳 、 合 金 、 质 合 金 钢 及 弹 簧 优 低 优 钢 , 钢 比大 于 3 % , 品 精 度 达 c级 标 准 。 优 0 产 该线的坯料加 热采用 全 步进 梁式 加 热炉 , 电 动 曲 柄 式 上 料 台架 , 流 变 频 调 速 炉 外 输 人 交 炉 内输 出辊 道 式 。加 热 炉 燃 料 采 用 高 炉 和 转 炉 混合 煤 气 。 全 线 共 2 7机 架 , 用 单 线 连 轧 方 采 式 , 线 无扭 。 粗 中 轧共 1 全 3台 机 架 , 轧 7架 , 平 立 轧 6架 , 轧 机 采 用 下 传 动 方 式 ; 精 轧 机 组 立 预 4架 , 轧 机 为 L型 传 动 , 中 轧 到 预 精 轧 机 组 立 粗 全部 采用 直 流单 机 驱动 ; 轧 机 为顶 交 4。 精 5 布 置, 1 共 0架 , 为 8辊 环 , 有 同 步 齿 轮 箱 集 中 均 ” 配 传动 , 电机 采 用 直 流 调 速 。 全 线 共 配 有 3台 飞
包钢棒材高线初步技术方案及主体设备价格
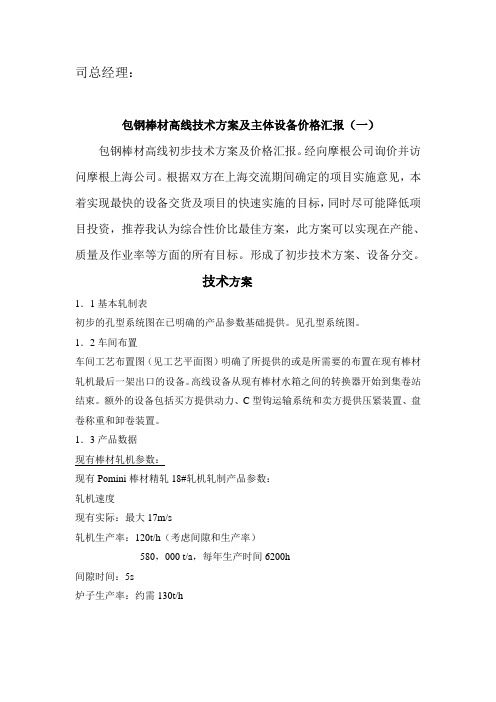
司总经理:包钢棒材高线技术方案及主体设备价格汇报(一)包钢棒材高线初步技术方案及价格汇报。
经向摩根公司询价并访问摩根上海公司。
根据双方在上海交流期间确定的项目实施意见,本着实现最快的设备交货及项目的快速实施的目标,同时尽可能降低项目投资,推荐我认为综合性价比最佳方案,此方案可以实现在产能、质量及作业率等方面的所有目标。
形成了初步技术方案、设备分交。
技术方案1.1基本轧制表初步的孔型系统图在已明确的产品参数基础提供。
见孔型系统图。
1.2车间布置车间工艺布置图(见工艺平面图)明确了所提供的或是所需要的布置在现有棒材轧机最后一架出口的设备。
高线设备从现有棒材水箱之间的转换器开始到集卷站结束。
额外的设备包括买方提供动力、C型钩运输系统和卖方提供压紧装置、盘卷称重和卸卷装置。
1.3产品数据现有棒材轧机参数:现有Pomini棒材精轧18#轧机轧制产品参数:轧机速度现有实际:最大17m/s轧机生产率:120t/h(考虑间隙和生产率)580,000 t/a,每年生产时间6200h间隙时间:5s炉子生产率:约需130t/h新高线工艺参数:坯料尺寸:150×150×11000mm,额定重量1900kg;轧机速度--保证值(带无扭轧机):105 m/s;--保证值(带定减径轧机):112 m/s;--设计:120 m/s;轧机能力:120 t/h 100%效率107.9 t/h (考虑间隙和生产率)800000 t/a,年工作时间6200h;坯料间隙:5s;加热炉能力:约130 t/h (新建加热炉,非最终能力);产品范围:光面线材:5.5㎜~25㎜(20㎜),以0.5㎜递增;钢级:高碳钢、低合金钢、弹簧钢、轴承钢、焊条钢、冷镦钢、轮胎钢帘线--设计等级:C1080用于选择设备和电机的设计入口温度和钢级--1#轧机入口:950~1150℃,参照钢级--无扭轧机(工艺温度):C1080 900~950℃弹簧钢950~1000℃冷镦钢850~870℃--定减径轧机(工艺温度):C1080 900~950℃弹簧钢1000~1050℃冷镦钢800~840℃盘卷尺寸/重量--盘卷:1250/1200mm(外径)×900/850mm(内径),额定重量1850kg 1.4 中间参数高线精轧机材对棒材来料断面尺寸、速度和公差的要求。
高线生产的主要设备、选用
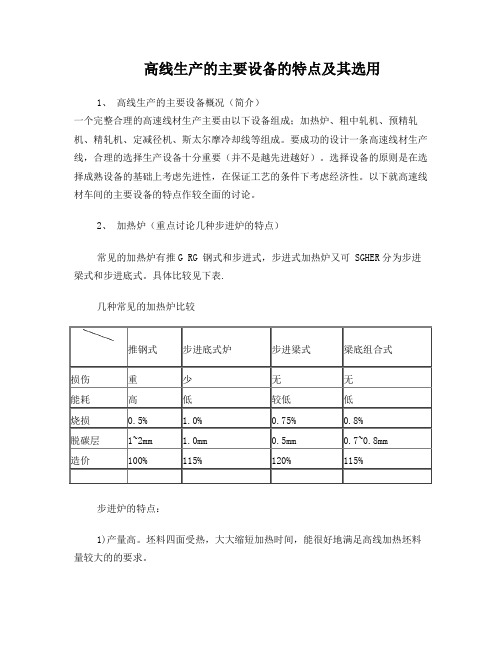
高线生产的主要设备的特点及其选用1、高线生产的主要设备概况(简介)一个完整合理的高速线材生产主要由以下设备组成;加热炉、粗中轧机、预精轧机、精轧机、定减径机、斯太尔摩冷却线等组成。
要成功的设计一条高速线材生产线,合理的选择生产设备十分重要(并不是越先进越好)。
选择设备的原则是在选择成熟设备的基础上考虑先进性,在保证工艺的条件下考虑经济性。
以下就高速线材车间的主要设备的特点作较全面的讨论。
2、加热炉(重点讨论几种步进炉的特点)常见的加热炉有推G RG 钢式和步进式,步进式加热炉又可 SGHER分为步进梁式和步进底式。
具体比较见下表.几种常见的加热炉比较推钢式步进底式炉步进梁式梁底组合式损伤重少无无能耗高低较低低烧损0.5% 1.0% 0.75% 0.8%脱碳层1~2mm 1.0mm 0.5mm 0.7~0.8mm造价100% 115% 120% 115% 步进炉的特点:1)产量高。
坯料四面受热,大大缩短加热时间,能很好地满足高线加热坯料量较大的的要求。
2)加热质量好。
钢坯在加热炉内散开布置,加热温度均匀,不会出现一般推钢式加热炉炉底处水管产生的黑印;钢坯与步进梁无摩擦,避免钢坯底面划伤;加热时间短,减少钢坯氧化量及脱碳层;坯料芯部和底部温差小,全长加热均匀。
3)操作灵活。
操作不受钢坯外形的限制,炉长不受推钢长度限制,变换品种容易;步进梁可作“踏步”动作,使钢坯温度均匀;空炉出炉简单,时间短,劳动强度低。
进出料方式:出料采用侧出料,进料有侧进料(密封性好);端出料(料好排)。
3、粗中轧机粗轧机类型很多,有摆锻式、三辊行星式、紧凑式、平立交替式、水平二辊式等形式。
(主要讲平立交替式和水平二辊式)。
摆锻式、三辊行星式已基本不用,紧凑式主要用于老厂的改造场地的限制,故重点讨论平立交替式和水平二辊式。
平立交替式:可实现轧件无扭轧制,特别适合高级线材的生产,另外可实行无孔型轧制。
现已有平立可转换轧机,可实现多线生产,但造价较高。
高线生产工艺工程及常用坯料规格的统计分析
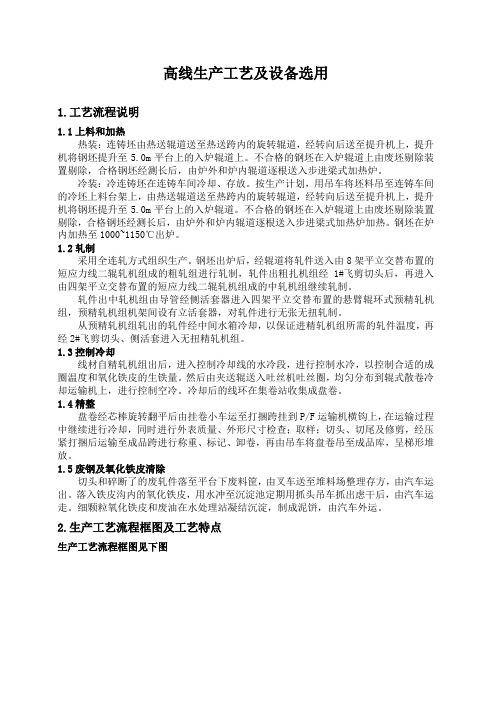
高线生产工艺及设备选用1.工艺流程说明1.1上料和加热热装:连铸坯由热送辊道送至热送跨内的旋转辊道,经转向后送至提升机上,提升机将钢坯提升至5.0m平台上的入炉辊道上。
不合格的钢坯在入炉辊道上由废坯剔除装置剔除,合格钢坯经测长后,由炉外和炉内辊道逐根送入步进梁式加热炉。
冷装:冷连铸坯在连铸车间冷却、存放。
按生产计划,用吊车将坯料吊至连铸车间的冷坯上料台架上,由热送辊道送至热跨内的旋转辊道,经转向后送至提升机上,提升机将钢坯提升至5.0m平台上的入炉辊道。
不合格的钢坯在入炉辊道上由废坯剔除装置剔除,合格钢坯经测长后,由炉外和炉内辊道逐根送入步进梁式加热炉加热。
钢坯在炉内加热至1000~1150℃出炉。
1.2轧制采用全连轧方式组织生产。
钢坯出炉后,经辊道将轧件送入由8架平立交替布置的短应力线二辊轧机组成的粗轧组进行轧制,轧件出粗扎机组经1#飞剪切头后,再进入由四架平立交替布置的短应力线二辊轧机组成的中轧机组继续轧制。
轧件出中轧机组由导管经侧活套器进入四架平立交替布置的悬臂辊环式预精轧机组,预精轧机组机架间设有立活套器,对轧件进行无张无扭轧制。
从预精轧机组轧出的轧件经中间水箱冷却,以保证进精轧机组所需的轧件温度,再经2#飞剪切头、侧活套进入无扭精轧机组。
1.3控制冷却线材自精轧机组出后,进入控制冷却线的水冷段,进行控制水冷,以控制合适的成圈温度和氧化铁皮的生铁量。
然后由夹送辊送入吐丝机吐丝圈,均匀分布到辊式散卷冷却运输机上,进行控制空冷。
冷却后的线环在集卷站收集成盘卷。
1.4精整盘卷经芯棒旋转翻平后由挂卷小车运至打捆跨挂到P/F运输机横钩上,在运输过程中继续进行冷却,同时进行外表质量、外形尺寸检查;取样;切头、切尾及修剪,经压紧打捆后运输至成品跨进行称重、标记、卸卷,再由吊车将盘卷吊至成品库,呈梯形堆放。
1.5废钢及氧化铁皮清除切头和碎断了的废轧件落至平台下废料筐,由叉车送至堆料场整理存方,由汽车运出。
高线生产工艺流程
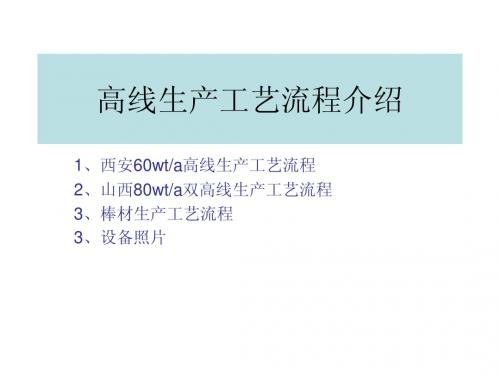
1、西安60wt/a高线生产工艺流程 2、山西80wt/a双高线生产工艺流程 3、棒材生产工艺流程 3、设备照片
上料台架
2#飞剪切头
散卷冷却
钢坯辊道
预精轧机组轧制 6HV 水箱冷却
集 卷
称重台
挂 卷
加热炉加热
3#飞剪切头
悬挂输送
钢坯出炉
精轧机组轧制10
检查取样
高压水除鳞
水箱冷却
钢坯精整理 合格冷连铸坯
冷床 合格热连铸坯
连铸机
缓冲台架 上料台架 称重、测长 加热 除磷 粗轧 飞剪切头、尾 一中轧 飞剪切头、尾 二中轧 中间水冷 飞剪切头、尾 精轧 定径 测径 涡流探伤 控制水冷 飞剪分段 冷床冷却 冷剪或冷锯定尺 检查、分类 计数 打捆 称重、标志 图1.3 棒材生产 工艺流程
外车间热处理
收集
精整
棒材入库
高线主要工艺设备介绍
• • 一、主轧机组 全线采用29架轧机,期中粗轧机组为7架,均为闭口式二辊轧机,全水平布置,直流电机单独传动;中轧机组6架, 均为短应力线轧机,平—立交替布置,直流电机单独传动;预精轧机为6架,2台短应力线轧机,4台紧凑式悬臂式 轧机,平—立交替布置,直流电机单独传动;精轧机为10架45°顶交型轧机,由一台交流电机传动。 二、集卷转运 1、集卷站: (1)型式:升降式集卷系统(带有布圈器) (2)组成:由集卷筒(电动布料器,电动操作分离支)液压马达和液压缸驱动的托板升降和开闭。 (3)作用;位于空冷线末端,使线材散卷集成盘卷,立式线架进行接卷后下降通过轮式输送机运输 (4)性能参数: 盘卷尺寸:外径1250mm,内径850mm。集卷最大高度~2500mm,盘卷最高温度450℃。 2、立式运输系统 (1)型式:轮式输送系统,由成套三合一减速机驱动皮带轮上的立式线架,对乘集在线架上的线卷进行输送。 (2)组成:由18组轮式输送机,4套转台,8个爪盘 (3)作用:运输系统负责把线卷从集卷站以立式姿态送到翻转机,然后再通过转运小车输送到现有的P﹠F系统。 3、 倾翻装置 (1)型式:液压倾翻,倾翻角度90° (2)组成:翻转基座框架、轮子部件、翻转、锁位和松开臂的液压缸和阀体。 (3)作用:负载的爪盘被翻转到水平位置 4、转运小车 (1)型式:电机拖动链条传动,液压升降式 (2)组成:底座轨道、带有升降台的小车、驱动系统(齿轮电机、复式链、液压缸和阀台) (3)作用:用来从爪盘上卸下线卷,通过配有升降台和小车横梁的小车从爪盘上抬起并且送到吊钩上
高线设计参数(典型)

3.8.4高速线材生产线3.8.4.1产品方案设计规模:45万吨/年产品:Φ5.5~20mm光面盘条Φ6.0~16mm螺纹盘条主要钢种:低合金钢、碳素结构钢、优质碳素结构钢、标准件用钢、冷镦及冷挤压钢、焊条钢、焊网钢。
产品大纲详见表3.8-8。
表3.8-8 高线产品大纲1)盘条直径及盘卷重量线材产品以压紧打捆状态交货。
盘条直径:Φ5.5~20mm盘重:~2465kg2)盘卷尺寸盘卷外径:Φ1250mm盘卷内径:Φ850mm盘卷高度:≤2200mm(打捆后)3.8.4.3原料及金属平衡连铸方坯年需要量为46.5万t。
1)断面边长:165mm×165mm2)定尺长度:12000mm生产线的综合成材率为96.8%,金属平衡见表3.8-9。
表3.8-9 高线金属平衡表图3.8-3高线工艺流程框图3.8.4.5轧机组成轧机由粗轧机组(8架)、中轧机组(8架)、精轧机组(8架)和减定径机组(4架)共28架轧机组成。
粗轧机组、中轧机组前6架(1H~14V)采用平-立交替布置的短应力线轧机,其立式轧机采用上传动型式。
中轧机组的后2架采用V型顶交45º悬臂辊环轧机,精轧机组采用V型顶交45º悬臂辊环轧机,减定径机组采用V型顶交45°悬臂辊环轧机。
轧机基本参数见表3.8-10。
表3.8-10 轧机基本参数表3.8.4.6主要工艺设备组成1)冷坯上料台架数量:1套台面存放钢坯数量:30根2)步进式加热炉数量:1座冷装额定加热能力:150t/h 3)无头轧制焊机数量:1套4)1号飞剪数量:1台型式:曲柄式工作制度:启停工作制5)2号飞剪数量:1台型式:回转式工作制度:连续工作制6)预水冷装置数量:1套7)精轧后水冷装置数量:1套8)减定径后水冷装置数量:1套9)高速飞剪数量:1套10)夹送辊和吐丝机数量:1套吐丝机机型:卧式吐丝机11)散卷冷却运输线数量:1套12)集卷站数量:1套13)立式卷芯架及P/F运输线数量:1套14)打捆机数量:2台15)称重装置数量:1台16)卸卷站数量:1台(双工位)3.8.4.7工艺平面布置主厂房由钢坯跨、加热炉跨、主轧跨、成品跨、轧辊间组成。
高线设备配置
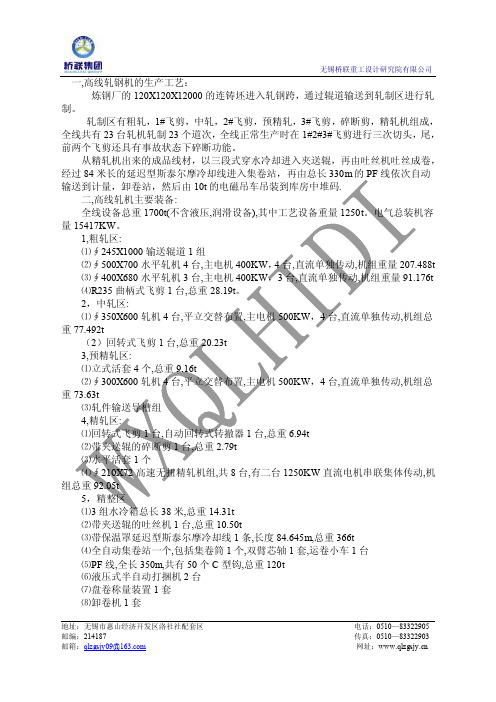
一,高线轧钢机的生产工艺:炼钢厂的120X120X12000的连铸坯进入轧钢跨,通过辊道输送到轧制区进行轧制。
轧制区有粗轧,1#飞剪,中轧,2#飞剪,预精轧,3#飞剪,碎断剪,精轧机组成,全线共有23台轧机轧制23个道次,全线正常生产时在1#2#3#飞剪进行三次切头,尾,前两个飞剪还具有事故状态下碎断功能。
从精轧机出来的成品线材,以三段式穿水冷却进入夹送辊,再由吐丝机吐丝成卷,经过84米长的延迟型斯泰尔摩冷却线进入集卷站,再由总长330m的PF线依次自动输送到计量,卸卷站,然后由10t的电磁吊车吊装到库房中堆码.二,高线轧机主要装备:全线设备总重1700t(不含液压,润滑设备),其中工艺设备重量1250t。
电气总装机容量15417KW。
1,粗轧区:⑴∮245X1000输送辊道1组⑵∮500X700水平轧机4台,主电机400KW,4台,直流单独传动,机组重量207.488t⑶∮400X680水平轧机3台,主电机400KW,3台,直流单独传动,机组重量91.176t⑷R235曲柄式飞剪1台,总重28.19t。
2,中轧区:⑴∮350X600轧机4台,平立交替布置,主电机500KW,4台,直流单独传动,机组总重77.492t(2)回转式飞剪1台,总重20.23t3,预精轧区:⑴立式活套4个,总重9.16t⑵∮300X600轧机4台,平立交替布置,主电机500KW,4台,直流单独传动,机组总重73.63t⑶轧件输送导槽组4,精轧区:⑴回转式飞剪1台,自动回转式转撤器1台,总重6.94t⑵带夹送辊的碎断剪1台,总重2.79t⑶水平活套1个⑷∮210X72高速无扭精轧机组,共8台,有二台1250KW直流电机串联集体传动,机组总重92.05t5,精整区⑴3组水冷箱总长38米,总重14.31t⑵带夹送辊的吐丝机1台,总重10.50t⑶带保温罩延迟型斯泰尔摩冷却线1条,长度84.645m,总重366t⑷全自动集卷站一个,包括集卷筒1个,双臂芯轴1套,运卷小车1台⑸PF线,全长350m,共有50个C型钩,总重120t⑹液压式半自动打捆机2台⑺盘卷称量装置1套⑻卸卷机1套地址:无锡市惠山经济开发区洛社社配套区电话:0510—83322905邮编:214187 传真:0510—833229036,液压与润滑设备:⑴粗轧与中轧液压,润滑站各一套⑵预精轧及中轧液压,润滑站各一套⑶集卷,打捆,称量卸卷,加热液压站各一套7,水处理⑴旋流沉渣池1座,平流池2座⑵净循环水处理系统1套⑶浊循环水处理系统1套地址:无锡市惠山经济开发区洛社配套区电话:0510—83322905地址:无锡市惠山经济开发区洛社配套区电话:0510—83322905。
高线的工艺流程

高线的工艺流程高线工艺流程高线,是一种用于电力传输和分配的铜或铝合金导线。
它的优点是能够承受高电流和高温,具有较低的电阻,因此可以减少能源损耗。
下面是一个高线的典型工艺流程。
第一步:原材料准备高线的主要原材料是电解铜或铝合金。
在生产过程中,需要将这些原材料按照一定比例混合并加热熔化,以便得到纯度较高的金属液。
第二步:连铸将金属液倒入连铸机的铸模中,使其冷却凝固形成长条状的连铸坯。
在连铸过程中,需要控制好温度和冷却速度,以确保连铸坯的质量。
第三步:轧制将连铸坯放入轧机中进行轧制。
轧制是高线生产过程中最关键的环节之一。
轧机可以将连铸坯逐渐拉长,并逐步减小断面,最终得到所需的高线尺寸。
轧制过程中需要加热和冷却轧机,使得金属连铸坯能够良好地变形。
第四步:拉拔将轧制后的高线放入拉拔机中进行拉拔。
拉拔是为了进一步改善高线的力学性能。
拉拔机通过逐渐减小模具的孔径,使高线在拉伸过程中变细变长。
这样可以使高线的晶粒细化,提高材料强度和延展性。
第五步:退火拉拔后的高线可能会出现应力和变硬的情况,因此需要进行退火处理。
退火是将高线加热至一定温度并保持一段时间,然后缓慢冷却的过程。
通过退火,可以消除高线的内部应力,改善其力学性能和电导率。
第六步:表面处理为了提高高线的腐蚀抗性和电导率,还需要对其表面进行处理。
常用的表面处理方法有镀锌、镀铝和镀锡等。
这些处理能够形成一层保护膜,增加高线的耐腐蚀性能,并提高其导电性能。
第七步:检验和包装经过上述工艺流程后,高线需要进行检验以确保质量符合要求。
常用的检验方法有外观检查、尺寸检测和性能测试等。
合格的高线经过检验后,会进行包装,以保护其表面免受损坏,并方便运输和储存。
以上是一个典型的高线工艺流程。
随着科技的不断进步,高线的生产工艺也在不断改进和发展。
工艺流程的优化可以提高生产效率和产品质量,为电力行业的发展做出贡献。
- 1、下载文档前请自行甄别文档内容的完整性,平台不提供额外的编辑、内容补充、找答案等附加服务。
- 2、"仅部分预览"的文档,不可在线预览部分如存在完整性等问题,可反馈申请退款(可完整预览的文档不适用该条件!)。
- 3、如文档侵犯您的权益,请联系客服反馈,我们会尽快为您处理(人工客服工作时间:9:00-18:30)。
高线生产工艺及设备选用1.工艺流程说明1.1上料和加热热装:连铸坯由热送辊道送至热送跨内的旋转辊道,经转向后送至提升机上,提升机将钢坯提升至5.0m平台上的入炉辊道上。
不合格的钢坯在入炉辊道上由废坯剔除装置剔除,合格钢坯经测长后,由炉外和炉内辊道逐根送入步进梁式加热炉。
冷装:冷连铸坯在连铸车间冷却、存放。
按生产计划,用吊车将坯料吊至连铸车间的冷坯上料台架上,由热送辊道送至热跨内的旋转辊道,经转向后送至提升机上,提升机将钢坯提升至5.0m平台上的入炉辊道。
不合格的钢坯在入炉辊道上由废坯剔除装置剔除,合格钢坯经测长后,由炉外和炉内辊道逐根送入步进梁式加热炉加热。
钢坯在炉内加热至1000~1150℃出炉。
1.2轧制采用全连轧方式组织生产。
钢坯出炉后,经辊道将轧件送入由8架平立交替布置的短应力线二辊轧机组成的粗轧组进行轧制,轧件出粗扎机组经1#飞剪切头后,再进入由四架平立交替布置的短应力线二辊轧机组成的中轧机组继续轧制。
轧件出中轧机组由导管经侧活套器进入四架平立交替布置的悬臂辊环式预精轧机组,预精轧机组机架间设有立活套器,对轧件进行无张无扭轧制。
从预精轧机组轧出的轧件经中间水箱冷却,以保证进精轧机组所需的轧件温度,再经2#飞剪切头、侧活套进入无扭精轧机组。
1.3控制冷却线材自精轧机组出后,进入控制冷却线的水冷段,进行控制水冷,以控制合适的成圈温度和氧化铁皮的生铁量。
然后由夹送辊送入吐丝机吐丝圈,均匀分布到辊式散卷冷却运输机上,进行控制空冷。
冷却后的线环在集卷站收集成盘卷。
1.4精整盘卷经芯棒旋转翻平后由挂卷小车运至打捆跨挂到P/F运输机横钩上,在运输过程中继续进行冷却,同时进行外表质量、外形尺寸检查;取样;切头、切尾及修剪,经压紧打捆后运输至成品跨进行称重、标记、卸卷,再由吊车将盘卷吊至成品库,呈梯形堆放。
1.5废钢及氧化铁皮清除切头和碎断了的废轧件落至平台下废料筐,由叉车送至堆料场整理存方,由汽车运出。
落入铁皮沟内的氧化铁皮,用水冲至沉淀池定期用抓头吊车抓出虑干后,由汽车运走。
细颗粒氧化铁皮和废油在水处理站凝结沉淀,制成泥饼,由汽车外运。
2.生产工艺流程框图及工艺特点生产工艺流程框图见下图热连铸坯辊道输送,旋转热坯提升机提升热坯提升机提升 辊道输送,旋转 合格冷连铸坯 水平二辊式粗轧机组飞剪切头,事故碎断预精轧机组轧制4道中轧机组轧制4道中间水箱水冷飞剪切头,事故碎断45°精轧机组轧制水冷段控制冷却吐丝机布线圈散卷运送控制风冷集 卷出炉辊道步进式加热炉加热检查,取样 打 捆 称重,挂牌 卸 卷入库,发货 斯太尔摩冷却翻卷,挂卷2.1高线轧机生产的主要工艺特点通常高线轧机的工艺特点可以概括为连续、高速、无扭和控冷。
其中高速轧制是最主要的工艺特点。
①高速线材轧机的高速轧制在工艺上保证高速的主要条件是原料质量、轧件精度、轧件温度。
高精度、高质量的轧件是保证不产生轧制故障的最根本条件。
通常应保证进入精轧机的轧件偏差不大于正负0.3mm。
当成品精度小于正负0.15mm是,进口精轧的轧件偏差不应大于成品尺寸偏差的2倍。
轧件偏差值是指轧件全长(包括头尾),特别是头部的最大偏差。
头部不良引起的故障多。
要保证轧件精度,必须严格控制钢坯尺寸精度。
钢坯尺寸的波动会影响轧件尺寸及机座间的张力,特别对粗轧前几道次影响较大。
为此近几年粗轧机组都采用单独传动,以便及时灵活地调节轧制速度,保证微张力轧制。
轧件温度也是影响高速轧制的重要因素,要保证轧件精度,必须保证轧件温度均匀稳定,所以要求加热温度均匀、控冷设施灵敏。
②控轧及轧后控制冷却控制冷却是分阶段控制自精轧机轧出的成品轧件的冷却速度,尽量降低轧件的二次氧化量,可根据钢的化学成分和使用性能要求,是散卷状态下的轧件从高温奥氏体组织转换成与所要求性能相对应的常温晶像组织。
它已是高线轧机不可分割的组成部分。
③高速轧机的高质量控制车间设计的质量控制上需要各工序都具备生产高速线材的能力:a.保证原料质量。
要求原料段具有原料检测、检查与清理修磨得手段,使投入的原料具有生产优质线材的条件b.采用步进式加热炉,以保证灵活的加热制度c.在单线生产时粗轧采用平立机组,减少轧件刮伤d.尽可能使用滚动导卫及硬面轧辊,保证轧件表面质量。
3.高线生产的主要设备概况一个完整合理的高速线材生产主要由以下设备组成;加热炉、粗中轧机、预精轧机、精轧机、、斯太尔摩冷却线等组成。
要成功的设计一条高速线材生产线,合理的选择生产设备十分重要。
选择设备的原则是在选择成熟设备的基础上考虑先进性,在保证工艺的条件下考虑经济性。
以下就高速线材车间的主要设备的特点作较全面的论述。
3.1加热炉在高速线材生产中常见的加热炉有推钢式和步进式,步进式加热炉又可分为步进梁式和步进底式。
具体比较见下表。
几种常见的加热炉比较推钢式步进底式炉步进梁式梁底组合式损伤重少无无能耗高低较低低烧损0.5% 1.0% 0.75% 0.8%脱碳层1~2mm 1.0mm 0.5mm 0.7~0.8mm造价100% 115% 120% 115%步进式加热炉的特点:①产量高。
坯料四面受热,大大缩短加热时间,能很好地满足高线加热坯料量较大的的要求。
②加热质量好。
钢坯在加热炉内散开布置,加热温度均匀,不会出现一般推钢式加热炉炉底处水管产生的黑印;钢坯与步进梁无摩擦,避免钢坯底面划伤;加热时间短,减少钢坯氧化量及脱碳层;坯料芯部和底部温差小,全长加热均匀。
③操作灵活。
操作不受钢坯外形的限制,炉长不受推钢长度限制,变换品种容易;步进梁可作“踏步”动作,使钢坯温度均匀;空炉出炉简单,时间短,劳动强度低。
进出料方式:出料采用侧出料,进料有侧进料(密封性好);端出料(料好排)。
综上所述,目前高速线材生产所用的加热炉是步进式加热炉。
3.2粗中轧、精轧及预精轧机3.2.1 粗轧机类型很多,有摆锻式、三辊行星式、紧凑式、平立交替式、水平二辊式等形式。
由于摆锻式、三辊行星式已基本不用,紧凑式主要用于老厂的改造场地的限制,所以重点总结平立交替式和水平二辊式。
平立交替式:可实现轧件无扭轧制,特别适合高级线材的生产,另外可实行无孔型轧制。
现已有平立可转换轧机,可实现多线生产,但造价较高。
以前用于高级钢的生产,现也普遍应用于碳结钢生产。
水平二辊式:这种形式的粗轧机应用较普遍,尤其适用于以碳素结构钢低合金钢为主的多线轧制。
其主要形式是闭口机架、短应力线轧机和预应力轧机。
3.2.2 预精轧机当前多采用平立交替布置,具有悬臂式轧辊的予精轧机,其主要优点有以下几个:①由于机架平立交替布置,实现了活套轧制,可以消除粗轧和中轧轧制时不可避免产生的堆、拉钢现象而造成的轧件尺寸不均匀,从而使精轧机组得到尺寸稳定且均匀的轧件,这对获得高精度的线材创造了极为有利的条件。
②机架间设有活套从而实现了无张力轧制,消除了由于堆拉钢而造成的轧件头、尾尺寸差,减少了切头、切尾,提高了成材率。
③本机组采用悬臂轴,碳化钨辊环,硬度高,每孔轧出量可成倍提高,更换辊环方便,提高了作业率。
④到预精轧轧件的断面较小,为保证轧件断面形状正确、尺寸精确和工艺稳定,道次变形小,悬臂式轧辊的予精轧机完全完足要求,其以设备重量轻、占地小。
因此,采用平立交替布置的悬臂式予精轧机组是合理的,不仅提高了轧机作业率,更重要的是保证了产品质量,提高了金属收得率,降低了生产成本。
3.2.3精轧机组是高速线材轧机最重要的、最关键的设备之一。
当今世界主要有四种流行机组:摩根、阿希洛、德马克、达涅利。
几种机型的主要特点如下表所示:序号结构和参数主导机型摩根型德马克达涅利阿希洛1 工作机座布置形式侧交45,后为顶交45侧交45,后改为15/75。
平立交替顶交452 辊环直径φ8 “×5+φ6”×5 φ210×10 φ210×2+φ165×8φ210×103 辊缝调整机构偏心套式调整机构偏心套式调整机构偏心套式调整机构带液压平衡的摆臂式4 机架中心距800~750mm 800mm 750及650mm 920mm5 传动装置利用伞齿轮改利用伞齿轮仅利用伞齿轮利用伞齿轮变传动方向且变速改变传动方向变速由圆柱齿轮完成改变传动方向且变速改变传动方向且变速一般采用摩根第六代v型超重型轧机,它主要有以下几个优点:①采用顶交45°机型,传动轴至地面设备机组距离短小,设备重心低,倾动力矩小。
机组稳定性好,震动小,噪音低,重量小、刚性大。
②操作视野开阔,便于操作管理。
③主电机功率大,为进一步提高精轧操作速度和实现低温轧制创造了条件。
④机架承载能力大,提高了轧制精度,最高轧制速度可达140m/s,成品范围大,生产率极高,是目前无扭精轧机的主导机型。
3.3斯太尔摩冷却线和高线轧辊的使用特点和条件3.3.1斯太尔摩冷却控制冷却线是高速线材生产的主要技术之一。
为避免当线材盘卷在800℃~1050℃高温下自然冷却时,因盘卷内外温差大而导致表面严重氧化、盘卷内部不符合要求、机械性能低、拉拔性能差等问题,为此目前新建的高线都选择了斯太尔摩冷却线,斯太尔摩冷却线有三种形式:标准型、缓慢型、延迟型,具体比较见下表:三种斯太尔摩冷却线的比较类型标准型延迟型缓慢型设备特点链式或辊式运输机,风冷,造价低有绝热面板,侧墙,顶盖的运输机,造价低,产量较大有绝热面板,侧墙、顶盖、电热烧嘴的运输机,造价高,产量低冷却速度 4.44~10C/s 1.11~10C/s 0.28~10C/s 最小运输速度0.254m/s 0.051m/s 0.051m/s低碳钢和低合金钢有一定的软化退火效果,不适合于生产低碳、低合金钢比标准型软化效果好、低合金钢的抗拉强度可降低3~4Kg/mm有较好的软化效果、低碳钢和低合金钢最合适中碳钢和高碳钢冷镦处理介于空冷和铅浴处理之间、适用于中、高碳钢生产比标准型好,用于紧固件的中碳钢生产,抗拉强度可减少10~15%有利于冷镦加工比延迟型好,比较接近铅浴淬火处理水平合金钢适用于一般生产要求,比延迟型综合性能差软化退火比标准型好,有利于提高综合机械性能,减少二次氧化铁皮,提高表面质量软化退火效果最好,综合机械性能最好综上:延迟性斯太尔摹冷却线可以较灵活的控制冷却工艺,根据钢种的用途和性能要求,进行最佳的工艺配合,特别适用于要求轧后缓慢冷却的低合金与合金类钢种,因而在新品种开发领域有着广阔的前景。
此外,采用斯太尔摹冷却工艺生产和开发的各种线材氧化铁皮少,在组织和性能上能较好的满足用户需求,使线材在后续加工中可省略热处理与酸洗工序,降低加工成本。
3.3.2高线轧辊的使用特点和条件轧辊最主要的出发点是保证线材的表面质量。
耐磨性是轧辊最主要的指标。
粗轧:压下量大,轧制条件恶劣,以强度、韧性为主。