河南省xx玻璃厂浮法玻璃熔窑燃气技改项目简介
浮法玻璃熔窑中燃烧控制系统的智能化设计

浮法玻璃熔窑中燃烧控制系统的智能化设计浮法玻璃熔窑是当今玻璃生产过程中最常用的方法之一,具有高效、节能、环保的特点。
而燃烧控制系统在浮法玻璃熔窑中的智能化设计是实现稳定燃烧、提高生产效率以及降低能源消耗的关键。
浮法玻璃熔窑的燃烧控制系统主要包括燃烧器、燃烧控制器以及监测仪器等组成部分。
通过自动控制系统对燃烧器进行管理,可以实现燃料的精确控制,确保熔窑内的火焰持续稳定,从而保持玻璃生产的连续性和稳定性。
智能化设计的燃烧控制系统应具备以下几个方面的功能。
首先,精确的燃料控制是智能化设计的核心。
通过传感器对燃烧过程进行实时监测,可以获取熔窑内的氧气浓度、燃烧温度、燃料流量等关键数据,进而根据设定的燃烧参数进行自动调节。
通过反馈控制的方式,使得燃烧器始终处于最佳工作状态,避免过量或不足的燃料供应,从而提高燃烧效率。
其次,智能化设计的燃烧控制系统应具备多种安全保护功能。
例如,当燃烧器工作异常或出现故障时,系统能够及时发出警报并采取相应的措施。
同时,针对燃烧器的自动点火、自动关火、自动调节等功能也应在系统中得以实现,确保燃烧过程的稳定和安全。
此外,智能化设计还应考虑到能源的节约与环保,通过优化燃烧参数,节省能源消耗。
例如,通过对燃烧过程中废气的回收利用、余热的利用等方式,可以有效降低生产过程中的能源浪费,减少二氧化碳等有害排放物的排放,实现可持续发展。
智能化设计的燃烧控制系统还应具备数据采集和分析功能。
通过对燃烧过程中各种参数的精确测量和保存,可以为后续的数据分析和优化提供依据。
对于燃烧过程中的异常情况,系统能够自动识别并报警,及时采取措施,避免生产事故的发生。
最后,智能化设计的燃烧控制系统应具备远程监控和操控的能力。
通过网络连接,系统能够实现对燃烧控制的远程监测和操作,方便管理人员对生产过程进行实时监控和调整,提高生产效率和生产质量。
综上所述,浮法玻璃熔窑中燃烧控制系统的智能化设计是提高生产效率、降低能源消耗和保证生产安全的关键。
石油焦粉燃烧技术

(1)从市场上购买成品粉时,其月效益为:
使用煤焦油:100吨×2930元/吨×30天=879万元
使用石油焦: 100吨×2250元/吨×30天=675万元
月 利 润: 879-675=204万元
(2)自建粉厂制粉时,其月效益为:
使用煤焦油: 100吨×2930元/吨×30天=879万元
服务项目:
一、提供玻璃窑炉干喷石油焦粉的技术改造、工程施工、技术咨询
二、协助玻璃企业建立不同规模的石油焦粉厂
三、为厂家节省燃料成本50%左右。
1、燃用重油与石油焦粉经济性比较分析
热值比较:〔常用标准值〕
重油热值大约10000大卡,石油焦粉热值大约8800大卡,重油与石油焦粉的热值比为;1比1.1~1.17之间(约1.15), 以此推算在消耗1吨重油的情况下, 需要消耗1.15吨石油焦粉才能达到1吨重油的热值。
石油焦粉系统全年总费用:石油焦粉5152万元+电耗154万元=5306万元
一条500t/d浮法玻璃生产线其采用石油焦粉燃料替代重油燃料
一年可节约燃料成本: 11217万元―5306万元=5911万元
年能耗比值:1―(5306÷11217)=52.7%效益将更加显著。
综上所述,给企业降低了生产成本,带来了巨大的经济效益,玻璃窑炉油改粉系统势在必行,一般油改粉系统工程改造周期60天,改造期间不影响重油及天然气系统正常工作,改造工程的设备投资费用,大约在设备运行50~60天内收回。以石油焦粉来替代重油燃烧,大大降低了企业的生产成本,该技术的全面突破,标致着我公司在玻璃窑炉燃料输送与喷吹燃烧系统领域中,技术处于国内领先水平。
2、燃用石油焦粉与煤焦油经济性比较分析
玻璃熔窑全氧燃烧技术的开发
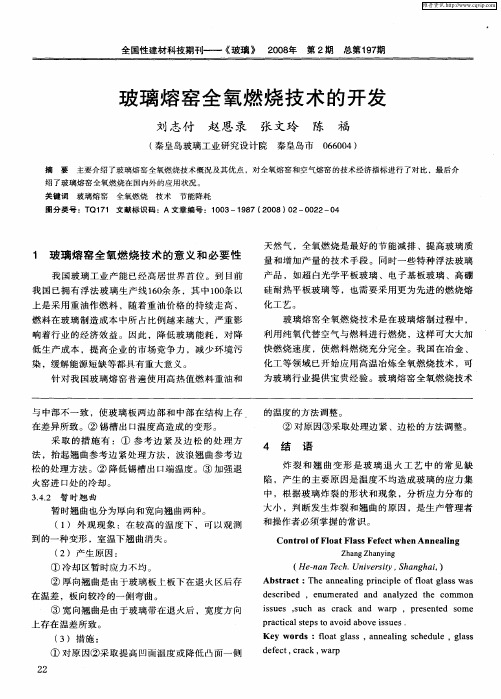
绍 了玻璃 熔 窑 全氧 燃 烧 在 国 内外 的应 用状 况 。
关键词 玻璃 熔 窑 全 氧燃 烧 技术 节能 降 耗
图分 类 号 :T 7 文 献标 识 码 :A文 章编 号 :1 0 Q1 1 0 3—1 8 ( 0 8) 2—0 2 — 4 97 2 0 0 0 2 0
1 玻璃 熔窑全 氧燃烧 技术 的意 义和必 要性
大 小 ,判 断 发生炸 裂和 翘 曲的原 因 ,是 生产管 理者 和操作 者必须掌 握 的常识 。
Co r fFl t a sFe e tw he nt ol oa s f c o Fl n Anne ln ai g
Zh n Zha yig a g n n
( )外 观 现象 :在较 高 的温 度下 ,可 以观测 1
我 国玻 璃工业 产 能 已经 高 居世界 首位 。到 目前
天然 气 ,全氧燃烧 是 最好 的节能减 排 、提高 玻璃质
量 和增加 产量 的技术 手段 。 同时 一些 特种浮 法玻璃
产 品 ,如 超 白光 学平 板玻璃 、电子基 板玻璃 、高硼 硅耐 热平 板玻璃 等 ,也 需要 采用更 为先 进 的燃烧熔
与 中部不 一致 ,使玻 璃 板两边 部 和中部 在结 构上存
的 温 度 的方 法 调 整 。
在差异 所致 。② 锡槽 出 口温度 高造 成 的变形 。 采 取 的 措施 有 :① 参 考 边 紧及 边 松 的处 理 方
法 ,抬起 翘 曲参 考边 紧处 理方 法 ,波浪 翘 曲参考 边
d s rbe , e u e a e a d n l z d he o m o e ci d n m r t d n a a y e t c m n is s ,u h s r c a w ap , p e e t d o e s ue s c a c a k nd r r s n e s m
浮法玻璃窖冷修技改项目施工方案
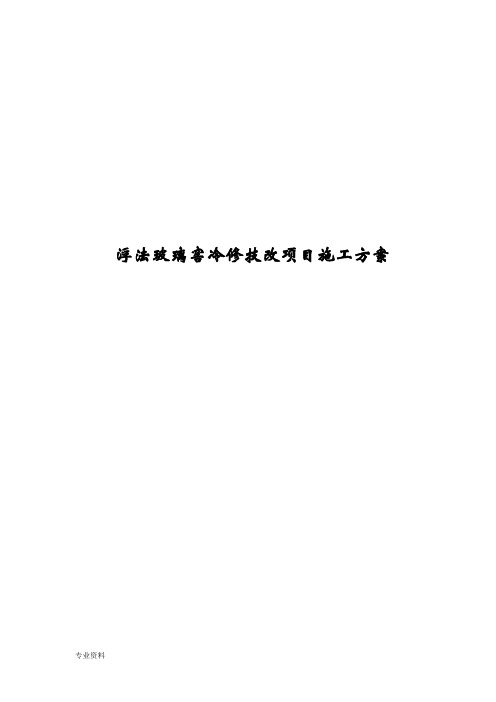
浮法玻璃窖冷修技改项目施工方案目录1、前言 (3)2、工程概况 (5)3、工程特点 (5)4、工程范围 (6)5、施工配合条件 (7)6、项目管理目标和指标 (7)7、工程部署及资源准备 (8)8、施工进度计划(见附页) (11)9、主要施工方法说明 (11)10、工程施工机具计划 (34)11、加工制作计划 (36)12、工程质量保证措施 (37)13、工程安全与职业健康及文明施工保证措施 (40)14、工程进度保证措施 (52)15、技术保证措施: (52)16、环境管理 (53)17.项目信息管理 (55)18、项目沟通管理 (57)19、项目结束阶段管理 (57)1、前言1.1、编制依据1.1.1、我司与xx玻璃集团股份有限公司签定的浮法玻璃生产线施工合同和技术规范内容。
1.1.2、业主提供的部分原图和冷修改造新图,合同或招标文件规定的及国家现行的标准和规范。
1.1.3、我公司以往新建和冷修浮法玻璃生产线施工经验。
1.1.4、我公司组织的技术人员对现场踏勘及与业主工程师交流的情况、相应的答疑文件;1.2、编制原则本方案编制将遵循以下两个原则:一是符合性原则;二是先进性原则。
1.2.1、符合性原则符合性原则包括两层含义,首先是整个方案的编制要符合合同文件的要求,按照业主的要约目标、要求来编制,尤其是要适应该项目工期紧、任务重、工序交叉多的特点;其次是要符合基建施工的程序和客观规律及xx浮法玻璃窑冷修工程的特点要求,并符合我公司多次施工浮法线的经验。
1.2.2、先进性原则先进性原则是要求在符合性原则的基础上,以本公司的技术、装备、员工素质为前提,采取科学的方法,合理的组织,优化的配置,完善的措施,实现先进的目标。
该工程重要的两个特征:施工技术要求高、工期紧张;如何利用公司的先进性资源确保满足技术要求和工期目标是本施工组织设计必须阐述的一个要点。
2、工程概况xx玻璃集团股份有限公司位于xx省xx市东凤镇同乐工业园,此次冷修技改项目是由秦皇岛玻璃工业设计研究院设计,业主自行监督管理的技改项目。
玻璃窑炉全氧燃烧项目简介

濮阳市华翔光源材料有限公司玻璃窑炉全氧燃烧项目简介1 企业简介濮阳市华翔光源材料有限公司位于河南省濮阳市文留镇濮阳工业园,紧靠中原油田腹地,文留镇是中原油田天然气主产区。
公司的前身是上海闵原集团下辖子公司扬州晨阑光源材料有限公司。
上海闵原集团公司下辖上海闵原电器有限公司、上海厚龙电器有限公司、上海精密机器有限公司、宜兴华珍公司、河南舞阳闵原电器有限公司、河南濮阳华珍电子有限公司、濮阳华翔光源材料有限公司,集团的主要产品有:跳泡、启辉器、节能灯芯柱、电光源特种玻璃及电光源相关设备,董事长蒋厚龙先生毕业于复旦大学电光源专业。
华翔公司于2005年至2007年先后收购原积玉玻璃制品有限公司、原华安玻璃制品有限公司,组建濮阳市华翔光源材料有限公司一厂、二厂、三厂。
华翔公司是一个朝气蓬勃的企业,占地面积150亩,现拥有7座玻璃窑炉,年产电光源特种玻璃管3.2万吨。
目前在职员工520人,其中高中级技术人员90名,80%的生产技术人员都是从事玻璃拉管行业10年以上,公司管理层有3人毕业于上海复旦大学电光源专业,与上海复旦大学电光源研究所一直保持着紧密合作关系,联合进行光源用特种玻璃管的各项技术工艺的改进,同时聘请该系有关专家出任濮阳市华翔光源有限公司的技术顾问。
公司主要产品是电光源用特种中铅、无铅玻璃管(公司专利申请号200810004409.5,此产品填补了省内空白),广泛用于节能灯行业(喇叭管、排气管、霓虹灯管、节能灯外管、彩色灯饰等)、电子指示显示行业(氖泡、跳泡、尖泡、二极管、电极等),并可根据用户要求提供玻璃管精切烧口、喇叭管火割、排气管切割、排气管烧口的后道加工服务;并有一支由资深光源行业技术工程师组成的售后服务小组。
公司现有7座玻璃窑炉,生产线28条,年产量近32000吨,公司采用先进的丹纳法生产工艺和公司自有专利技术(如可调温燃气火头,申请号200720070191.4;玻璃管用旋转管组件装置,申请号200820003284.X;两用型外端头玻璃管成型装置,申请号200820006426.8;两用型内端头玻璃管成型装置),玻璃管各类检测测量设备齐全,外型尺寸一致性好、产品料性稳定,产品得到了用户的一致好评,也一跃成为国内第二大、河南省独家的光源特种玻璃管生产厂家。
中国浮法玻璃的发展历程

中国浮法玻璃的发展(一)“洛阳浮法”技术的诞生“洛阳浮法”技术的研制,始于60年代初。
当时,英国皮尔金顿兄弟玻璃公司刚刚发表了经过约十年研制,发明并取得成功的国际上最新最先进的平板玻璃生产方法——浮法的问世。
同时,国际上一些学术刊物、杂志、论文和专利,都相继对有关浮法玻璃技术进行报道和简介。
但是这些报道都侧重于商品的性能和功能,而对浮法技术,不仅没有什么具体内容,相当多的都是不真实的,甚至进行误导。
而且当时的中国是处在以美国为首的世界发达国家的经济封锁的情况下,不要说参观工厂和购买技术是不可能的,就是想买一点浮法玻璃的样品,都难以实现。
因此,我国是在一无资料,二无情报,三无样品的情况下,根据物理化学的公共原理,“白手起家”着手进行研制的。
1960年开始时,曾由北京管庄建材科学研究院与上海耀华玻璃厂协作,进行过浮法工艺的初步探索。
后来在建材部主管领导的倡议和支持下,在建材研究院建筑玻璃研究室进行了实验阶段的研究。
通过静态单元试验、半连续工艺试验和连续性工艺试验,特别是对浮抛介质的选择,保护气体的成分和净化,玻璃成分的组成,以及加热元件和锡槽结构及耐火材料的选取等,都历经多次的试验,探索和筛选,直到1967年终于获得了一系列试验室阶段性成果。
接着在此基础上进入中间试验阶段,同时有些试验室阶段的工作,还继续同步进行。
1968年由建材研究院、玻璃设计院、湖南株洲玻璃厂三家合作,利用株洲玻璃厂尚未建成的玻璃球车间,改建为浮法玻璃中间试验线。
经过二年的努力,最后在1970年7月完成了中国浮法玻璃的中间试验。
经过长达6个月连续试验,终于取得了突破性的进展,其中最主要的成果是解决了浮法玻璃的成形方法——玻璃液的直接流入法,并生产出了中国的第一批6毫米浮法玻璃样品。
同时,在技术上对流槽的安装,槽体的构造,雾点的消除以及操作方法和工艺制度等多方面都取得了相当丰富的经验和成果。
紧接着在中间试验成功的基础上与河南洛阳玻璃厂合作,将洛阳玻璃厂建成投产不久的压延玻璃生产线改造为浮法玻璃工业性试验生产线,即进入工业性试验生产阶段,在秦皇岛玻璃研究院(建材研究院玻璃室的一部分)、株洲玻璃设计所(原北京玻璃设计院的一部分)、株洲玻璃厂、管庄建材研究院和洛阳玻璃厂等五个单位的协同合作下,扩大进行浮法玻璃的工业性试验,经过短短几个月的共同奋战,克服了一系列的困难后,终于在1971年9月胜利投产,并成功地拉出了原板宽近2米、厚6毫米的质量较好的浮法玻璃,并向市场提供了商品,取得了商业性的成果。
玻璃熔窑烟气余热发电简介101024
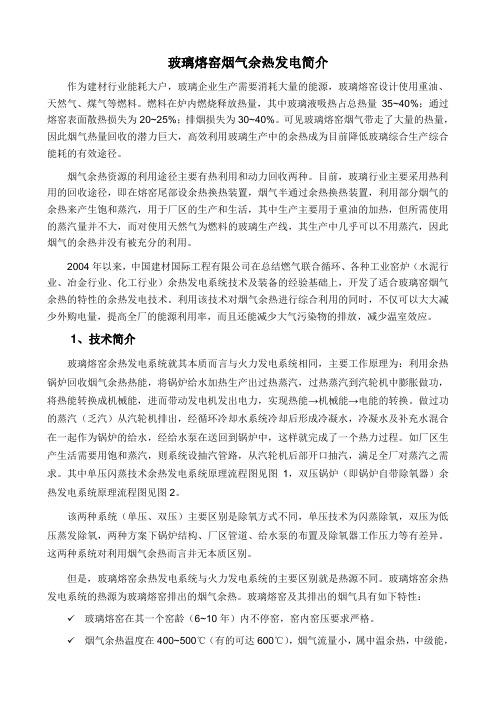
玻璃熔窑烟气余热发电简介作为建材行业能耗大户,玻璃企业生产需要消耗大量的能源,玻璃熔窑设计使用重油、天然气、煤气等燃料。
燃料在炉内燃烧释放热量,其中玻璃液吸热占总热量35~40%;通过熔窑表面散热损失为20~25%;排烟损失为30~40%。
可见玻璃熔窑烟气带走了大量的热量,因此烟气热量回收的潜力巨大,高效利用玻璃生产中的余热成为目前降低玻璃综合生产综合能耗的有效途径。
烟气余热资源的利用途径主要有热利用和动力回收两种。
目前,玻璃行业主要采用热利用的回收途径,即在熔窑尾部设余热换热装置,烟气半通过余热换热装置,利用部分烟气的余热来产生饱和蒸汽,用于厂区的生产和生活,其中生产主要用于重油的加热,但所需使用的蒸汽量并不大,而对使用天然气为燃料的玻璃生产线,其生产中几乎可以不用蒸汽,因此烟气的余热并没有被充分的利用。
2004年以来,中国建材国际工程有限公司在总结燃气联合循环、各种工业窑炉(水泥行业、冶金行业、化工行业)余热发电系统技术及装备的经验基础上,开发了适合玻璃窑烟气余热的特性的余热发电技术。
利用该技术对烟气余热进行综合利用的同时,不仅可以大大减少外购电量,提高全厂的能源利用率,而且还能减少大气污染物的排放,减少温室效应。
1、技术简介玻璃熔窑余热发电系统就其本质而言与火力发电系统相同,主要工作原理为:利用余热锅炉回收烟气余热热能,将锅炉给水加热生产出过热蒸汽,过热蒸汽到汽轮机中膨胀做功,将热能转换成机械能,进而带动发电机发出电力,实现热能→机械能→电能的转换。
做过功的蒸汽(乏汽)从汽轮机排出,经循环冷却水系统冷却后形成冷凝水,冷凝水及补充水混合在一起作为锅炉的给水,经给水泵在送回到锅炉中,这样就完成了一个热力过程。
如厂区生产生活需要用饱和蒸汽,则系统设抽汽管路,从汽轮机后部开口抽汽,满足全厂对蒸汽之需求。
其中单压闪蒸技术余热发电系统原理流程图见图1,双压锅炉(即锅炉自带除氧器)余热发电系统原理流程图见图2。
玻璃熔窑全氧燃烧技术及发展方向
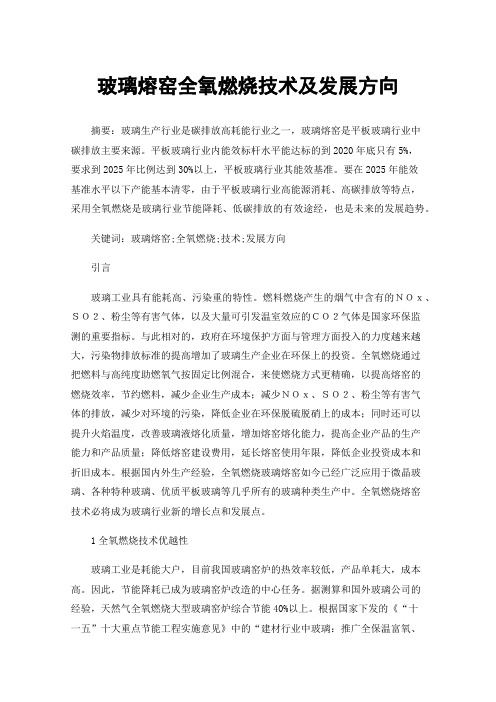
玻璃熔窑全氧燃烧技术及发展方向摘要:玻璃生产行业是碳排放高耗能行业之一,玻璃熔窑是平板玻璃行业中碳排放主要来源。
平板玻璃行业内能效标杆水平能达标的到2020年底只有5%,要求到2025年比例达到30%以上,平板玻璃行业其能效基准。
要在2025年能效基准水平以下产能基本清零,由于平板玻璃行业高能源消耗、高碳排放等特点,采用全氧燃烧是玻璃行业节能降耗、低碳排放的有效途经,也是未来的发展趋势。
关键词:玻璃熔窑;全氧燃烧;技术;发展方向引言玻璃工业具有能耗高、污染重的特性。
燃料燃烧产生的烟气中含有的NOx、SO2、粉尘等有害气体,以及大量可引发温室效应的CO2气体是国家环保监测的重要指标。
与此相对的,政府在环境保护方面与管理方面投入的力度越来越大,污染物排放标准的提高增加了玻璃生产企业在环保上的投资。
全氧燃烧通过把燃料与高纯度助燃氧气按固定比例混合,来使燃烧方式更精确,以提高熔窑的燃烧效率,节约燃料,减少企业生产成本;减少NOx、SO2、粉尘等有害气体的排放,减少对环境的污染,降低企业在环保脱硫脱硝上的成本;同时还可以提升火焰温度,改善玻璃液熔化质量,增加熔窑熔化能力,提高企业产品的生产能力和产品质量;降低熔窑建设费用,延长熔窑使用年限,降低企业投资成本和折旧成本。
根据国内外生产经验,全氧燃烧玻璃熔窑如今已经广泛应用于微晶玻璃、各种特种玻璃、优质平板玻璃等几乎所有的玻璃种类生产中。
全氧燃烧熔窑技术必将成为玻璃行业新的增长点和发展点。
1全氧燃烧技术优越性玻璃工业是耗能大户,目前我国玻璃窑炉的热效率较低,产品单耗大,成本高。
因此,节能降耗已成为玻璃窑炉改造的中心任务。
据测算和国外玻璃公司的经验,天然气全氧燃烧大型玻璃窑炉综合节能40%以上。
根据国家下发的《“十一五”十大重点节能工程实施意见》中的“建材行业中玻璃:推广全保温富氧、全氧燃烧浮法玻璃熔窑,降低烟道散热损失”精神,优化全氧超白压延玻璃生产线熔窑设计是必要的。
浮法玻璃熔窑节能_燃烧技术及保窑
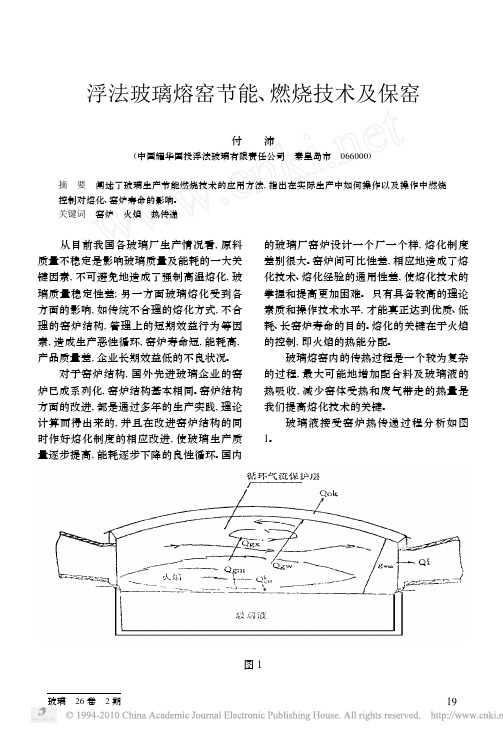
浮法玻璃熔窑节能、燃烧技术及保窑付 沛(中国耀华国投浮法玻璃有限责任公司 秦皇岛市 066000)摘 要 阐述了玻璃生产节能燃烧技术的应用方法,指出在实际生产中如何操作以及操作中燃烧控制对熔化、窑炉寿命的影响。
关键词 窑炉 火焰 热传递 从目前我国各玻璃厂生产情况看,原料质量不稳定是影响玻璃质量及能耗的一大关键因素,不可避免地造成了强制高温熔化,玻璃质量稳定性差;另一方面玻璃熔化受到各方面的影响,如传统不合理的熔化方式,不合理的窑炉结构,管理上的短期效益行为等因素,造成生产恶性循环,窑炉寿命短,能耗高,产品质量差,企业长期效益低的不良状况。
对于窑炉结构,国外先进玻璃企业的窑炉已成系列化,窑炉结构基本相同。
窑炉结构方面的改进,都是通过多年的生产实践,理论计算而得出来的,并且在改进窑炉结构的同时作好熔化制度的相应改进,使玻璃生产质量逐步提高,能耗逐步下降的良性循环。
国内的玻璃厂窑炉设计一个厂一个样,熔化制度差别很大。
窑炉间可比性差,相应地造成了熔化技术、熔化经验的通用性差,使熔化技术的掌握和提高更加困难。
只有具备较高的理论素质和操作技术水平,才能真正达到优质、低耗、长窑炉寿命的目的。
熔化的关键在于火焰的控制,即火焰的热能分配。
玻璃熔窑内的传热过程是一个较为复杂的过程,最大可能地增加配合料及玻璃液的热吸收,减少窑体受热和废气带走的热量是我们提高熔化技术的关键。
玻璃液接受窑炉热传递过程分析如图1。
图1 玻璃液接受的总热量为:Q m=Εg m C o[(T g100)4-T m100)4]F m+Εwm C o[(T w100)4-T m100)4]F m+Αgm k(t g-t m)F m(kcal h)式中:Q m——玻璃液吸收总热量;Q gm——火焰以辐射方式传给的热量;Q gm k——火焰以对流方式传给的热量;Q wm——窑壁以辐射方式传给的热量;Εgm——火焰对玻璃液的相对黑度;Εwm——窑壁对玻璃液的相对黑度;F m——火焰下玻璃液的受热面积;T g——火焰温度;T m——玻璃液温度;T w——窑壁温度;Αgm k——气体对玻璃液的对流给热系数;C o——火焰辐射系数。
玻璃熔窑全氧燃烧技术及发展方向

“十四五”期间,对我国玻璃行业来说,面临着如何将“玻璃熔窑全氧燃烧技术”成果进一步产业化并为行业尽早实现节能减排和碳达峰碳中和,寻找可靠技术措施的重大工程技术问题。
玻璃熔窑全氧燃烧技术最显著的特点一是节能减排,二是提高玻璃质量,目前只有使用重油、天然气等高热值燃料,生产优质玻璃的企业才有动力和需求采用全氧燃烧技术。
通过近年的科研设计和生产实践,玻璃熔窑全氧燃烧技术已经在光伏玻璃、玻璃纤维、玻璃器皿、微晶玻璃等生产领域中广泛应用,其优异的提高玻璃质量、节能减排效果得到了充分验证,但广泛实施浮法玻璃全氧燃烧技术仍然面临着一些重大工程技术和经济问题,总的来说主要需要在以下几个方面开展技术创新:1优化全氧熔窑三维仿真模拟体系通过研究全氧燃烧玻璃熔窑火焰空间和玻璃液流场的三维数学模型,开发界面友好、操作方便、参数设置容易的全氧燃烧浮法玻璃熔窑三维仿真系统,使参与玻璃熔窑设计和仿真的工程技术人员只要输入熔窑结构、燃气布置和相关边界条件等参数,玻璃熔窑三维仿真系统将自动根据使用者提供的设计要求,完成CFD建模、求解和后处理三个步骤。
图1为全氧燃烧数学模拟火焰空间温度分布图。
图1 全氧燃烧数学模拟火焰空间温度分布图进一步形成玻璃原料COD值的快速测定、玻璃的Redox控制、熔体性能、澄清新工艺、火焰空间的数值模拟等理论与关键技术,为全氧燃烧条件下排除玻璃液中的微气泡,保证优质玻璃的熔制提供工艺指导。
2全氧浮法熔窑耐火材料国产化大型全氧浮法熔窑池宽超过11 m,比国内最大的全氧玻壳、玻璃纤维窑池宽30%以上。
到目前为止,国内已经建成了600 t/d、800 t/d规模的全氧燃烧平板玻璃生产线,主要耐火材料也都是国内配套,但要使窑炉达到高质量、长寿命,对大型全氧熔窑的结构安全、关键部位耐火材料的国产化还需要深入研究。
通过总结成功经验,克服存在的不足,持续改进、不断推进全氧玻璃熔窑关键耐火材料的国产化进程。
全氧窑的长宽比是一项重要指标。
浮法玻璃厂主要设备安装技术规范

浮法玻璃生产线主要设备安装技术规范编制单位:******有限公司编制人:编制日期:年月日浮法玻璃生产线主要设备安装技术规范一、工程概况1、工艺组成及主在设备浮法玻璃生产线主要由熔窑、锡槽、退火窑、冷端四大工段组成,机械设备安装主要有:风机、闸板、窑头给料机、水平搅拌器、深层水包车、拉边机、锡槽吊挂水包、退火窑全套设备、冷端全套设备。
二、施工准备(1)、工程施工前,必须具备安装设备的技术条件,施工人员认真熟悉图纸,掌握技术数据。
(2)、工程施工前,对临建设施、运输道路、水源、电源、照明、消防设施、主要材料和机具及劳动力等,做好充分准备,作出合理安排。
(3)、工程施工前,有关的基础地坪、沟道等工程应已完工,其混凝土强度不应低于设计强度的75%,安装施工地点及附近的建筑材料、泥土、杂物等应清除干净。
(4)、当气象条件不适应设备安装的要求时,应采取措施后方可进行施工。
三、设备施工程序及工艺一般规定1、开箱检查和保管(1)、设备开箱时,应在建设单位有关人员、监理工程师参加下,按下列项目进行检查,并应作出记录:①、箱号、箱数包装情况;②、设备的名称、型号和规格数量;③、装箱清单、设备技术文件、资料及专用工具;④、设备有无缺损件、表面有无损坏和锈蚀等;(2)、设备及其零部件和专用工具,均应妥善保管,不得使其变形,损坏、锈蚀、错乱或丢失。
2、设备基础验收设备基础的位置、几何尺寸和质量要求,经检验应符合现行国家标准《钢筋混凝土工程施工及验收规范》的规定,并应有验收资料或记录。
3、主要工序施工要点:(1)、基础复检清理及划线;①、设备安装前应按施工图纸或规范的要求进行复检。
复检时,用水准仪验收土建移交标高点,做出标高线,做为设备安装的基准。
对设备基础表面和地脚螺栓预留孔中的油污、碎石、泥土、积水等均应清除干净;预留地脚螺栓的螺丝和螺母应保护完好;放置垫块部位和表面应凿平。
②、依据施工图和核对后的设备尺寸、规范要求,拉线检查基础纵横中心及预留孔(预埋件)位置,符合设计和规范要求后,用墨线弹出设备安装中心线及预留孔(预埋件)中心线,并在附近构筑物上作出设备安装中心永久标志。
浮法玻璃熔窑节能技术及途径.
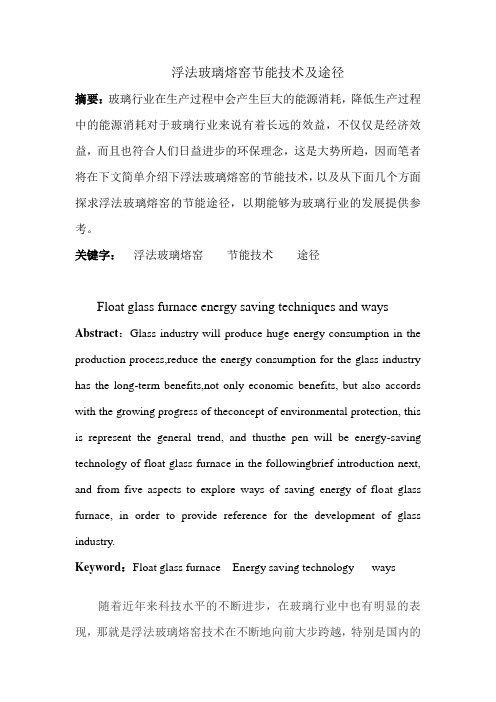
浮法玻璃熔窑节能技术及途径摘要:玻璃行业在生产过程中会产生巨大的能源消耗,降低生产过程中的能源消耗对于玻璃行业来说有着长远的效益,不仅仅是经济效益,而且也符合人们日益进步的环保理念,这是大势所趋,因而笔者将在下文简单介绍下浮法玻璃熔窑的节能技术,以及从下面几个方面探求浮法玻璃熔窑的节能途径,以期能够为玻璃行业的发展提供参考。
关键字:浮法玻璃熔窑节能技术途径Float glass furnace energy saving techniques and ways Abstract:Glass industry will produce huge energy consumption in the production process,reduce the energy consumption for the glass industry has the long-term benefits,not only economic benefits, but also accords with the growing progress of theconcept of environmental protection, this is represent the general trend, and thusthe pen will be energy-saving technology of float glass furnace in the followingbrief introduction next, and from five aspects to explore ways of saving energy of float glass furnace, in order to provide reference for the development of glass industry.Keyword:Float glass furnace Energy saving technology ways 随着近年来科技水平的不断进步,在玻璃行业中也有明显的表现,那就是浮法玻璃熔窑技术在不断地向前大步跨越,特别是国内的保温材料和耐火材料都在原基础上取得了巨大的进步,有进步虽然可喜,但是尚不足以与国外同领域的技术相比肩,或许通过以下数字大家能够更直观地看出差距所在,国外较先进的浮法玻璃熔窑技术最高产生55%的热效率,而我国最高产生40%。
浮法玻璃熔窑天然气和重油燃烧系统的比较
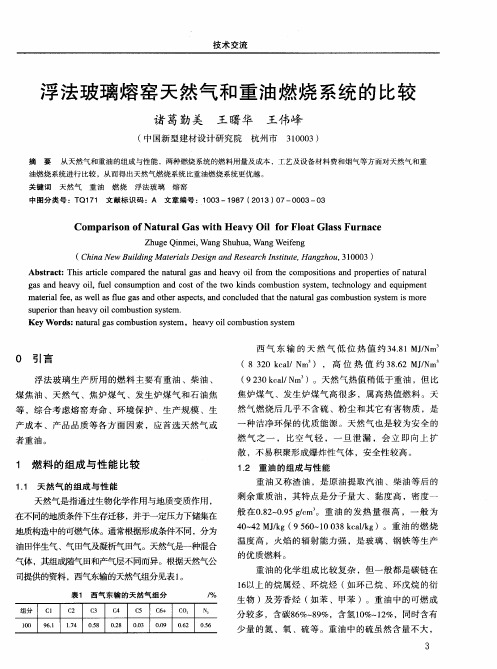
ma t e r i a l f e e , a s we l l a s lu f e g a s a n d o t he r a s pe c t s ,a n d c o n c l ud e d t h a t he t n a ur t a l g a s c o mb u s t i on s y s t e m i s mo r e
产成 本 、产 品 品质等 各方 面 因素 ,应首 选天 然气 或
者重 油 。
种 洁净 环保 的优质 能 源 。天 然气 也是 较 为安全 的
燃 气 之 一 , 比空气 轻 ,一 旦 泄 漏 ,会 立 即 向上 扩 散 ,不 易积聚形成 爆炸性气 体 ,安 全性较高 。
1 燃 料 的组成 与性 能 比较
西 气东 输 的天然 气低 位 热值 约3 4 . 8 1 MJ / N m
0 引 言
浮法玻 璃 生产所 用 的燃料 主要 有重 油 、柴油 、 煤 焦油 、天 然气 、焦 炉煤 气 、发生 炉煤 气 和石油 焦
(8 3 2 0 k e a l /N m ),高 位 热 值 约 3 8 . 6 2 MJ / N m
油 田伴生气 、气 田气及凝析气 田气。天然气是一种混合
温 度 高 ,火 焰 的辐射 能力 强 ,是玻璃 、钢 铁等 生产
的优质燃料 。
气体 ,其组成随气 田和产气层不 同而异 。根据天然气公 司提供的资料 ,西气东输 的天然气组分见表 1 。
表1 西气 东 输 的 天然 气 组 分
油燃 烧 系统 进行 比较 ,从而 得 出天然 气燃 烧 系统 比重 油燃 烧 系统更 优越 。
关键词
天然 气
重油
燃烧
科技成果——浮法玻璃炉窑全氧助燃装备技术
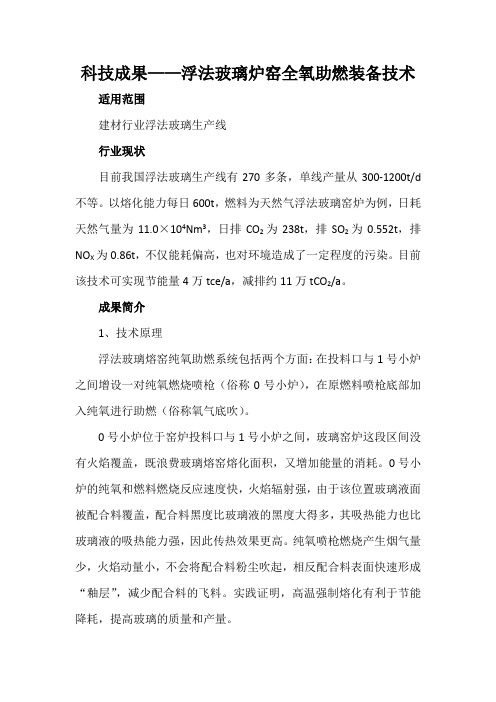
科技成果——浮法玻璃炉窑全氧助燃装备技术适用范围建材行业浮法玻璃生产线行业现状目前我国浮法玻璃生产线有270多条,单线产量从300-1200t/d 不等。
以熔化能力每日600t,燃料为天然气浮法玻璃窑炉为例,日耗天然气量为11.0×104Nm3,日排CO2为238t,排SO2为0.552t,排NO X为0.86t,不仅能耗偏高,也对环境造成了一定程度的污染。
目前该技术可实现节能量4万tce/a,减排约11万tCO2/a。
成果简介1、技术原理浮法玻璃熔窑纯氧助燃系统包括两个方面:在投料口与1号小炉之间增设一对纯氧燃烧喷枪(俗称0号小炉),在原燃料喷枪底部加入纯氧进行助燃(俗称氧气底吹)。
0号小炉位于窑炉投料口与1号小炉之间,玻璃窑炉这段区间没有火焰覆盖,既浪费玻璃熔窑熔化面积,又增加能量的消耗。
0号小炉的纯氧和燃料燃烧反应速度快,火焰辐射强,由于该位置玻璃液面被配合料覆盖,配合料黑度比玻璃液的黑度大得多,其吸热能力也比玻璃液的吸热能力强,因此传热效果更高。
纯氧喷枪燃烧产生烟气量少,火焰动量小,不会将配合料粉尘吹起,相反配合料表面快速形成“釉层”,减少配合料的飞料。
实践证明,高温强制熔化有利于节能降耗,提高玻璃的质量和产量。
在原燃料喷枪底部通入氧气,氧气从燃料喷枪底部加入,解决传统燃烧方式该位置燃烧缺氧的问题。
高纯度氧气燃烧速度快,温度高,辐射能力强,有利于玻璃熔化、澄清和均化,因此可以减少燃料上部空气量,从而降低空间火焰温度,使温度呈梯度分布,起到保护窑炉火焰空间胸墙、大碹作用,大大延长窑炉的使用寿命,同时也大幅降低尾气中NO X含量。
燃料喷枪底部的氧气还可以燃烧掉对面燃料喷枪未燃尽燃料,避免燃料带入玻璃窑炉蓄热室,烧坏格子体,从而延长窑炉格子体使用寿命。
2、关键技术(1)解决了全氧喷枪系统火焰长短和刚度调整问题,实现在不同窑体的使用;(2)通过研发满足不同要求的配套喷嘴砖,解决了喷嘴砖材质、更换和耐碱液冲刷的问题。
玻璃熔化窑炉节能技术改造项目可行性研究报告
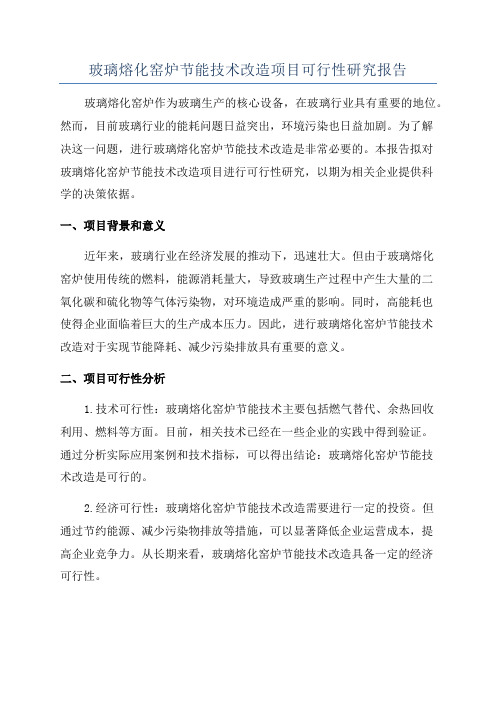
玻璃熔化窑炉节能技术改造项目可行性研究报告玻璃熔化窑炉作为玻璃生产的核心设备,在玻璃行业具有重要的地位。
然而,目前玻璃行业的能耗问题日益突出,环境污染也日益加剧。
为了解决这一问题,进行玻璃熔化窑炉节能技术改造是非常必要的。
本报告拟对玻璃熔化窑炉节能技术改造项目进行可行性研究,以期为相关企业提供科学的决策依据。
一、项目背景和意义近年来,玻璃行业在经济发展的推动下,迅速壮大。
但由于玻璃熔化窑炉使用传统的燃料,能源消耗量大,导致玻璃生产过程中产生大量的二氧化碳和硫化物等气体污染物,对环境造成严重的影响。
同时,高能耗也使得企业面临着巨大的生产成本压力。
因此,进行玻璃熔化窑炉节能技术改造对于实现节能降耗、减少污染排放具有重要的意义。
二、项目可行性分析1.技术可行性:玻璃熔化窑炉节能技术主要包括燃气替代、余热回收利用、燃料等方面。
目前,相关技术已经在一些企业的实践中得到验证。
通过分析实际应用案例和技术指标,可以得出结论:玻璃熔化窑炉节能技术改造是可行的。
2.经济可行性:玻璃熔化窑炉节能技术改造需要进行一定的投资。
但通过节约能源、减少污染物排放等措施,可以显著降低企业运营成本,提高企业竞争力。
从长期来看,玻璃熔化窑炉节能技术改造具备一定的经济可行性。
3.社会可行性:玻璃熔化窑炉节能技术改造可以减少排放的二氧化碳等有害气体,改善环境质量,保护生态系统,对于实现可持续发展具有积极意义。
此外,项目的实施还可以提高企业形象,增强社会认可度。
三、项目实施方案1.技术改造方案:选择合适的燃气替代、余热回收利用、燃料等技术,在真实的工业环境中进行试验和调试。
通过技术改造,使玻璃熔化窑炉能够实现节能、减排的目标。
2.经济资金方案:制定详细的投资预算,分析项目的投资回报率、内部收益率等指标。
同时,寻找合适的融资方式,如银行贷款、政府补贴等,确保项目进行顺利。
3.环境影响评价:对项目实施过程中可能产生的环境影响进行评估,制定相应的环境保护措施,确保项目符合环保要求。
玻璃窑炉技术改造工程方案

玻璃窑炉技术改造工程方案一、项目背景玻璃制造行业是国民经济中的重要组成部分,玻璃产品应用广泛,包括建筑玻璃、家用玻璃、汽车玻璃等。
而玻璃制造过程中所需的玻璃窑炉技术直接影响着生产效率和产品质量。
近年来,随着环保意识的提高和能源成本的上升,玻璃制造企业都面临着如何提高生产效率、降低能耗和排放的问题。
因此,进行玻璃窑炉技术改造成为许多玻璃制造企业的重要课题。
二、现状分析当前我国玻璃制造企业的玻璃窑炉技术主要存在以下问题:1. 能耗大,环境污染严重。
传统玻璃窑炉采用燃煤或者重油作为燃料,燃烧不充分导致排放大量废气和废渣,对环境造成严重污染。
同时,能源消耗大也直接影响了企业的生产成本。
2. 生产效率低。
传统玻璃窑炉采用手工操作或者简单的自动控制系统,无法实现智能化生产,生产效率低下。
3. 产品质量不稳定。
由于传统玻璃窑炉的控制能力有限,难以保证生产中产品的稳定质量。
综上所述,传统玻璃窑炉技术面临的问题亟待解决,需要进行技术改造来提高生产效率、降低能耗和排放、提升产品质量。
三、技术改造方案基于以上现状分析,针对玻璃窑炉技术的改造,提出如下技术方案:1. 优化燃烧系统。
采用高效、清洁的天然气燃料代替传统的煤炭或者重油,减少排放物的产生,提高能源利用率。
并且引入先进的燃烧控制技术,实现燃烧过程的精准控制,减少燃料的浪费,降低能耗。
2. 智能化控制系统。
引入先进的自动控制系统,实现对整个生产过程的智能化控制和监测,包括温度、压力、流量等参数的实时监控和调节。
通过数据采集和分析,实现生产过程的智能优化,提高生产效率。
3. 热回收技术。
利用余热回收技术,将窑炉烟气中的热能进行回收利用,用于加热水或者发电,提高能源利用效率。
4. 其他辅助设施改造。
对于玻璃窑炉周边的辅助设施,如气体净化系统、废气处理设备等也进行改造升级,保证整个生产过程的环保和安全。
四、项目实施方案1. 技术改造方案确定后,需要进行详细的项目实施方案制定。
浮法玻璃生产线主传动位置技改

浮法玻璃生产线主传动位置技改身份证:32081919740821xxxx前言:浮法玻璃主传动装备是玻璃生产核心设备之一,安装在退火窑C区位置,公司浮法玻璃一线600吨熔窑退火段距离是132米(249根轨道)。
它分A、B、C、RET、F五区,主传动设备安装在退火窑前端60米左右距离,它是选用30KW三相永磁同步电机作为动力,因为退火窑传动速度运行要稳定,所以采用进口丹佛斯FC300变频器带动。
改板时速度响应要快,输出力矩要均匀,不然玻璃厚度、宽度、切割精度达不到质量要求,对生产造成很大损失。
为了满足生产工艺需要,正常采用两套主传动设备互为备用,速度相差5%,如果1#这台主运行设备传动有问题,那么2#这台主传动设备通过超级离合自动切换,确保退火窑轨道始终运行。
当然两台主传动设备电源由两台不间断电源UPS供电,防止因停电事故造成影响!原状:公司浮法玻璃生产1线,自投产1年以来,经常玻璃板切割尺寸不准,有时玻璃板的厚度、宽度也受影响。
每次发生时间都不长,几分钟时间,维修人员到场都基本正常了,当时一部份人怀疑横切机有问题,也有一部分人怀疑岗位工操作错误所致,一时无处理进展。
甚至认为电气干扰所致:因为拉引区三台电机是由三台西门子440变频器控制的,它采用端子操作,命令源信号采用模拟电压类型(0-10V),速度随电压变化而变化。
它的模拟电压信号是由冷端PLC模拟输出卡(AO4*12BIT)发送的,冷端PLC是采用西门子S7-300类型,CPU采用:315-2DP,它有一只FM350计数卡,是用来采集退火传动速度信号。
退火窑出口处安装一只三洋TRD-J600-RZ光电编码器,用来传送每圈600个脉冲信号给FM350计数卡,通过PLC计算出主传动速度。
分析似乎也有可能,逐一处理,并没有实质解决。
聘请许多专家到场,也只是按以上分析给与处理建议,问题陷入僵局。
给生产带来不少损失!原因:通过以上现象,我们仔细查找原因。
浮法玻璃熔窑局部增氧助燃技术浅析
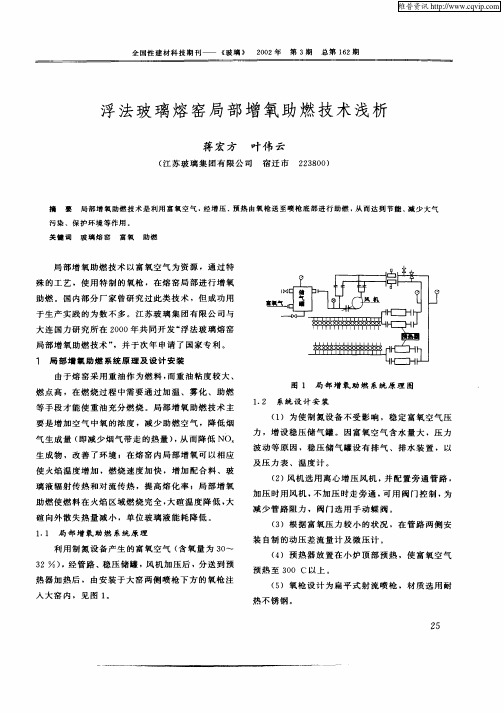
力 、流量 ) 。各 种数 据 统 计见 表 1 、表 2 。
表 1 数 据 统 计
、 \ 区 间
‘ l m A m
项
目 、\
~…
…
’ 一
逐 注 富 氧 段 一 期 二 期
7月 1 ~ 1 4 9 7月 2 ~ 3 O 0
富 氧 调 度段 一 期 二 期
7月 3 ~ 8月 4 1 8月 5 9 ~
及 压 力 表 、温 度计 。
使火 焰 温度 增 加 ,燃烧 速 度 加快 ,增加 配 合料 、玻
璃 液 辐 射传 热 和对 流传 热 ,提 高熔 化率 ;局部 增 氧
( ) 机选 用 离心 增 压风 机 , 配 置旁 通 管路 , 2 风 并 加压 时 用 风机 , 加压 时走 旁 通 , 用 阀 门控 制 , 不 可 为 减少 管 路 阻力 ,阀 门选 用 手动 蝶 阀 。 ( )根据 富 氧压 力 较小 的状况 ,在 管路 两 侧 安 3
第 3期
总 第 1 2期 6
2 调 试 阶 段
步 进 行 ” 的原则 ,在 近半 年 的 时 间 内 ,通 过对 参 数 记 录 、 析 、 整 , 定合 适 的运 行 参 数 ( 分 调 确 温度 、压
由 于局 部增 氧 助燃 技术 在 大 型工 业 熔 窑使 用 尚
属首 次 ,为确 保 生 产不 受 影 响 ,采用 “ 由小 到大 稳
要是 增 加空 气 中 氧 的浓度 ,减少 助燃 空 气 ,降低 烟
气生成量 ( 即减少 烟 气带 走 的热 量 ) 从 而降低 NO ,
生成 物 ,改 善 了环 境 ;在 熔 窑 内局 部增 氧 可 以相 应
( )为使 制 氮设 备 不受 影 响 ,稳 定 富 氧空 气 压 1 力 ,增 设稳 压 储 气罐 。因 富氧 空气 含 水 量 大 ,压 力 波 动等 原 因 ,稳 压储 气 罐设 有 排 气 、排 水装 置 , 以
浮法玻璃工厂全氧燃烧熔窑制氧装备的选择
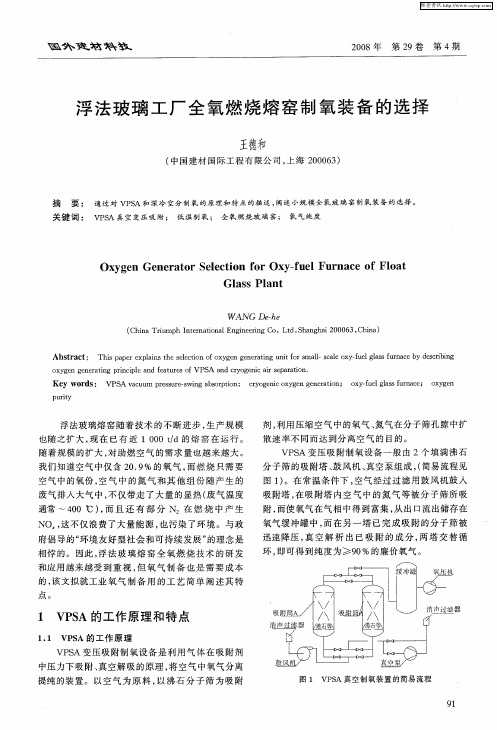
浮法 玻璃熔 窑 随着技 术 的不 断进 步 , 产规 模 生
也 随之扩 大 , 在 已有 近 10 0t 现 0 / 熔 窑 在 运行 。 d的 随着规 模 的扩大 , 助 燃空 气 的需 求量 也越 来越 大 。 对 我 们知 道空气 中仅 含 2 . %的氧 气 , 燃 烧 只需 要 09 而
Absr c : Thsp p re pan h e cino x g n g n rt gu i rs l c l o yf e gasfr aeb eciig ta t i a e x list esl t fo y e e eai nt o mal ae x —u l ls un c yd sr n e o n f —s b
维普资讯
20 0 8年
1 2 V S 的 特 点 . P A
第2 9卷
第 4期
工作 频繁 , 使该 工艺 对 切换 阀 门的质 量要 求非 常 致 高 ,阀门质量 的好 坏将 直 接影 响到 出氧能力 。
VP A是 2 S 0世 纪 5 0年代末 才 工 业 化应 用 的 制 氧方法 , 为一 种 新 塑 的制 氧方 法 ,变 压 吸 附法 具 作
剂 , 用压 缩空 气 中 的氧气 、 利 氮气 在分 子筛 孔隙 中扩
散 速 率不 同而 达到 分离 空气 的 目的。 VP A变 压吸 附制 氧设 备 一 般 由 2个 填 满沸 石 S
分 子 筛 的吸 附塔 、 风 机 、 鼓 真空泵 组成 ,简 易流程 见 ( 图 1 。在 常温条 件 下 , 气 经过 过 滤用 鼓 风 机鼓 入 ) 空 吸附塔 , 吸 附塔 内空 气 中 的 氮气 等 被 分 子筛 所 吸 在
Gl s a a s Pl nt
- 1、下载文档前请自行甄别文档内容的完整性,平台不提供额外的编辑、内容补充、找答案等附加服务。
- 2、"仅部分预览"的文档,不可在线预览部分如存在完整性等问题,可反馈申请退款(可完整预览的文档不适用该条件!)。
- 3、如文档侵犯您的权益,请联系客服反馈,我们会尽快为您处理(人工客服工作时间:9:00-18:30)。
河南省XX玻璃厂技改项目简介
二○一七年八月十五日
一、项目申报单位简介
河南省XX玻璃厂地处古都洛阳,是一个大型综合玻璃生产企业,现拥有两条日熔化量450吨/天规模浮法玻璃生产线,以及多条玻璃深加工生产线。
产品多次荣获省优、部优、国优,曾荣获全国质量效益先进企业称号,生产的青宫牌浮法玻璃2004年被评为河南省免检产品并保持至今。
并于2002年10月16日通过ISO9001:2000国际质量管理体系认证。
玻璃生产21年来,产品在全国30多个省、市、自治区均有销售网络,得到市场的普遍认可。
河南省XX玻璃厂始建于1951年,于1986年10月开始平板生产玻璃,现拥有两条日熔化400吨的浮法玻璃生产线,可产4~12毫米(以4~6毫米为主),无色、茶色、宝石蓝各种规格的平板玻璃,执行国家GB11614-99标准,产品质量接近世界先进水平。
2001年至今,年平均玻璃产量超过500万重箱,成为全国知名的玻璃生产厂家和重要的玻璃生产基地。
XX玻璃厂以质量求生存,以科技谋发展,向管理要效益,取得了不断的进步。
1993年7月,省统计局授予XX玻璃厂为河南省1992年度“全省大型企业综合经济效益百佳企业”,1994年12月,经国务院发展研究中心和《管理世界》中国企业评价中心综合评价,XX玻璃厂在1994年全国500家最大工业企业及行业评价排名中位于河南省最佳经济效益工业企业第10位,全国工业企业非金属矿物制品第12位。
1995年7月XX玻璃厂获“河南省大中型利税百强企业”称号,同年11月9日,国家经济贸易委员会、国家统计局公布1995年度中国工业企业综合评价最优500家,XX玻璃厂综合得分89.45分,总排位352位,在建材工业中排23位。
1999年被国家质量管理协会命名为《全国质量效益型先进企业》;2001年浮法翡翠绿玻璃被评为部优科技成果一等奖;2002年被河南省质量技术监督局授予《河南省重点保护产品》称号,并顺利通过ISO9001:2000国际质量管理体系认证;2003年获国家质量检验合格产品、河南省建材行业信得过产品称号。
二、项目主要内容
玻璃工厂是耗能大户,一座大型浮法玻璃熔窑一年要烧掉数万吨的燃料油。
随着燃油价格的不断高涨,燃料已占到玻璃成本的一半以上,致使玻璃制造总成本大幅增长,多数以重油为燃料的玻璃工厂面临亏损。
本项目以低热值的煤制气替代重油,用于熔制平板玻璃。
一方面通过用低热值、廉价的煤制气取代高热值、昂贵的重油,大大降低玻璃制造成本;另一方面,通过高低温两段蓄热式结构将排烟温度
降低400℃以上,减少排烟热损失,提高热效率,从而实现低热值能源替代石油产品和提高热效率双重节能目的。
三、技术先进性
(1)用低热值的煤制气取代昂贵的重油和天然气,实现降低能耗和能源替换双重节能目的,大幅度降低玻璃熔窑的燃料成本;
(2)采用两段式煤气发生炉结构,提高碳转化率的同时,进行脱焦、脱轻油、除尘和脱硫处理,以获得洁净的煤制气,实现煤炭的清洁燃烧和利用;
(3)采用高温、低温两段式蓄热结构,主要解决芒硝和粉尘的沉降与收集,又可使排烟温度降低到200℃以下,实现烟气余热的高效利用;
(4)快速、智能三通阀控制烟气、空气和煤气的换向,使窑压和窑温波动只有原来的1/5~1/7,产品质量和产量均增加;稳定的窑温和窑压使窑池所受冲刷减轻,熔窑寿命延长。
(5)特殊设计的蓄热室烧嘴代替小炉,实现弥漫式燃烧,延长了关键部位的寿命,节省了维护费用;
(6)能耗降低后,燃料消耗减少,相应的CO2、NO X、SO X排放减少。
四、投资估算及资金来源
项目总投资9500.5万元。
各项投资费用包括:窑炉耐火材料3385.2万元,窑炉钢材、泥料、运输、施工等1930万元,电气、设备、给排水等960.3万元,厂房改造1425万元,新建煤气站1800万元。
资金来源:设备及技术6500万元由北京XX技术有限公司提供,其他资金由中国XX华北集团公司(天津)提供。
五、经济效益分析
本项目500t/d浮法玻璃线实施改造后可年节约燃料费用5745.7万元,项目总投资9500.5万元,20个月可以收回投资,收益显著。
实施改造前日耗重油88.5吨,重油单价2900元/吨,重油费用约9372.1万元/年。
改造后单耗降低,年耗原煤56052吨,按620元/吨计算,约3475.2万元;其它各项费用约650.6万元;另年产焦油及轻油2496吨/年,外销后可增加收益约
499.4万元;三项共计3626.4万元,可节约5745.7万元。
六、节能效益分析
改造后不再使用我国紧缺的石油燃料,而采用储量丰富的煤作为燃料,每年可减少使用重油约3.23万吨,为缓解燃油市场供应压力做出一定贡献。
改造前玻璃单耗折合燃煤1838kcal/kg,改造后约1470.55kcal/kg,每年可节约燃料20%;考虑产质量提高减少二次熔化耗能,二项合计共折算标准煤1.32万吨。
每年可为市场提供焦油及轻油共5020吨,支援国家建设。
七、环保情况
1.煤气化部分
本项目采用储煤场地面硬化、四周建围墙、上部加挡风抑尘网等防尘措施,可使粉尘控制效率达85%~95%,从而实现原煤储运过程粉尘污染的有效控制。
煤气化炉排出的灰渣通过水浴后以实态形式存在,且是制作高档空心砖或红砖的优质原料。
上、下两段煤气混合后经间冷器、电捕轻油器等均可收集部分灰尘,最终煤气中灰尘的含量≤25mg/Nm3。
来自煤气化工序含H2S约2.0g/Nm3的煤气经栲胶脱硫系统脱硫后,H2S含量在50mg/Nm3以下,供玻璃窑炉使用。
因燃料在使用前就经过了净化,所以烟气中硫化物的含量明显低于原来燃重油的烟气。
粗煤气净化过程中产生的污水全部用于生产水蒸气,水蒸气用于煤气化流程;不够部分用原水补充,可以做到煤制气部分没有外排污水。
2.熔窑部分
SO2排放≤40mg/Nm3,烟尘排放≤10mg/Nm3。
3.总体排放
SO2排放≤90mg/Nm3,烟尘排放≤25mg/Nm3。
4.改造前后对比
改造前SO2排放≤850mg/Nm3,减少排放90%以上;烟尘排放≤50mg/Nm3,减少排放50%以上;Nox排放减少40%以上。
八、前期工作情况
针对浮法玻璃熔窑的特点,自2006年3月以来,XX组织相关专家进行了详尽的行业调研,并对各种燃重油和天然气的浮法玻璃熔窑进行了反复、详细的热平衡计算。
结果发现,现有浮法玻璃熔窑的烟气排放温度高达600℃,烟气携带的大量物理显热未得到充分利用,致使热效率普遍不高。
根据理论计算及实施经验,如果将玻璃熔窑的排烟温度降低到200℃以下,可减少20%以上的热损失。
2017年,河南省XX玻璃厂与XX公司合作后,XX公司针对XX玻璃厂浮法一、二线进行实地考察,现已完成该项目的热工计算及工艺理论分析并通过了可行性研究,确定了项目投资估算及资金来源。
目前省XX玻璃厂正在积极与环保部门进行协调,力求尽快达成一致意见。