焊接通用要求
起重机械焊接工艺通用要求

起重机械焊接工艺通用要求1 范围本标准规定了起重机械焊接工艺在编制过程中的术语、定义、编制原则、编制内容、认可和修订等的通用要求。
本标准适用于纳入特种设备目录的起重机械采用(在此是否要给定材料)制造焊接工艺的编制,对于特殊材料焊接时的工艺要求可参照本标准。
2 规范性引用标准下列文件中的条款通过本标准的引用而成为本标准的条款。
凡是注日期的引用文件,其随后的所有修订单或修订版均不适用本标准。
凡不注日期的引用文件,其最新版本适用本标准。
TSG Z6002-2010 特种设备焊接操作人员考核细则GB6067.1-2010GB/T985.1-2008 气焊、焊条电弧焊、气体保护焊和高能束焊的推荐坡口GB/T985.2-2008 埋弧焊的推荐坡口GB/T3375-1994 焊接术语GB/T3811-2008GB/T5117-1995 碳钢焊条GB/T5118-1995 低合金钢焊条GB/T5293-1999 埋弧焊用碳钢焊丝焊剂GB/T8110-1995 气保焊用碳钢低合金钢焊丝GB/T10045-2001 碳钢药芯焊丝GB/T13304-1991 钢分类GB/T14957-94 熔化焊焊丝GB/T19866-2005 焊接工艺规程及评定的一般原则GB/T19867.1-2005 电弧焊焊接工艺规程3 术语和定义GB/T3375-1994确定的术语和定义适用于本标准。
3.1 结构焊4 焊接工艺编制原则编制时应当遵循以下基本原则:a)遵守国家安全技术规范和相应标准;b)根据起重机械的要求,适应本单位管理要求;c)具有科学性、合理性、可操作性;d)积极采用新材料、新方法、新技术;e)工艺的编制应当由具备一定工作经验和专业技术水平的人员编写。
5 通用要求5.1 应对以下信息进行收集:a)国家对产品质量、焊接标准规范的要求;b)本单位现有的质量保证体系的要求;c)本单位现有的资源情况,例如焊机;d)对本单位及周边环境影响情况;e)对焊接工艺执行情况;f)持续改进焊接工艺的信息情况。
焊接作业指导书

LOGO标志名称焊接作业指导书在此输入你的公司名称20XX年X月X日焊接作业指导书篇一:电子焊接作业指导书目的:使焊点光滑饱满,产品性能稳定、可靠,符合客户的要求。
适用范围:SMT 人员、手工焊接及检验人员。
内容:一. 印刷锡膏:1. 首先将网板固定在丝印台上,取一块光板调整网板的漏锡孔,使各个焊盘完全显露出来,让焊盘和网板的漏孔完全吻合,其偏移范围不能超过±0.2mm。
另外一定要注意网板的平整度,因为网板的翘曲直接影响锡膏的厚度、图形的完整。
2. 锡膏的选用应使用免清洗型(TUMARA)锡膏,具体锡膏的保存及使用规范请参考《印刷锡膏工艺》,此类锡膏的粒度一般在25-35um,四号粉颗粒,印刷出来不会有坍塌,支撑度高,回流前持续时间长。
3. 进行首块印刷时,丝印机的速度不要太快,用力要均匀,刮力的角度45°为宜。
首块印出后,一定要严格检查所有的焊盘以及锡膏图形,是否有漏印、图形偏移、图形不完整、锡膏厚度不均匀等现象。
发现缺陷后立即纠正过来,再印刷第二块直至调整符合要求为止。
二.自动贴片:1.要求各装配位号元器件的类型、型号、标称值和极性等特征标记要符合产品的装配图和物料清单要求,不能贴错位置和用错料。
2.贴片机的压力要适当,贴片压力过小,元器件焊端或引脚浮在锡膏表面,锡膏粘不住元器件,在传递和回流焊时容易产生位置移动,另外由于Z 轴高度过高,贴片时组件从高处扔下,会造成贴片位置偏移。
贴片压力过大,锡膏挤出量过多,容易造成锡膏粘连,回流焊时容易产生桥接,同时也会由于滑动造成贴片位置偏移,严重时还会损坏元器件。
贴装好的元器件要完好无损。
3.贴装元器件焊端或引脚不小于1/2 厚度要浸入焊膏。
对于一般元器件贴片时的锡膏挤出量(长度)应小于0.2mm,对于窄间距元器件贴片时的锡膏挤出量(长度)应小于0.1mm。
4.元器件的端头或引脚均和焊盘图形对齐、居中。
由于回流焊时有自定位效应,因此元器件贴装位置允许有一定的偏差。
焊接与切割作业安全通用要求

3、金属墙壁:靠近金属间壁、墙壁、天花板、屋顶等处另一侧易受传热或辐射而引燃的易燃物。
《焊接与切割安全》(GB9448—1999)第6.4.2条
强制
3
焊接和割切审批要求
操作者只有在规定的安全条件得到满足;并得到现场管理及监督者准许的前提下,才可实施焊接或切割操作。在获得准许的条件没有变化时,操作者可以连续地实施焊接或切割。
强制
13
消除火灾隐患
焊接或切割作业只能在无火灾隐患的条件下实施:
1、有条件时,首先要将工件移至指定的安全区进行焊接;
2、工件不可移时,应将火灾隐患周围所有可移动物移至安全位置;
3、工件及火源无法转移时,要采取措施限制火源以免发生火灾。
《焊接与切割安全》(GB9448—1999)第6.3条
强制
14
灭火设备配备
焊接和切割区域必须予以明确标明,并且应有必要的警告标志。
《焊接与切割安全》(GB9448—1999)第4.1.2条
强制
6
职业危害警告标志设置
在焊接及切割作业所产生的烟尘、气体、弧光、火花、电击、热、辐射及噪声可能导致危害的地方,应通过使用适当的警告标志使人们对这些危害有清楚的了解。
《焊接与切割安全》(GB9448—1999)第9条
焊接与切割作业安全通用要求
序号
项目名称
标准要求
依据条款
效力
1
设置现场管理和安全监督人员
焊接或切割现场应设置现场管理和安全监督人员。
《焊接与切割安全》(GB9448—1999)第3.2.2条
强制
2
设置火灾警戒人员
电(气)焊作业标准化规定

电(气)焊作业标准化规定1范围本规定适用于工程的电焊、气焊作业施工。
2引用标准本规定根据GB9448—88 《焊接与切割安全》、GBl0235--88《弧焊变压器防触电装置》、GB8197--87《防护屏安全要求》、 SDZ019—85《焊接通用技术》等国家行业有关规程、规范,结合工程施工实际情况进行制定。
3基本要求3.1通用要求3.1.1凡从事焊接和气割的工作人员,需经过专业培训考核取得操作证,持证上岗。
3.1.2作业人员应熟知本规定,作业时不得擅离职守,进入岗位应按规定穿戴劳动防护用品。
3.1.3焊工应穿帆布工作服,戴工作帽,上衣不准扎在裤子里。
口袋须有遮盖,脚面应有鞋罩,以免焊接时被烧伤。
3.1.4焊接和气割的场所,应配有消防设施,并应保证其处于完好状态。
焊工应熟练掌握其使用方法,能够正确使用。
3.1.5作业现场要设置明显的安全警示标志。
3.2电焊基本要求3.2.1电焊工应配有下列防护用品:3.2.1.1镶有滤光镜的手把面罩或套头面罩。
3.2.1.2电焊手套。
3.2.1.3橡胶绝缘鞋。
3.2.1.4清除焊渣用的白光眼镜(防护镜)。
3.2.2焊钳和焊枪应符合国家标准;焊钳和焊枪要有良好的绝缘性能和隔热能力。
不得使用有缺陷的焊钳、焊枪。
3.2.3焊接电缆应具有较好的绝缘性能和抗机械损伤能力、耐油、耐热和耐腐蚀等性能。
3.2.4焊接电缆宜用整根的,如需用短线接长时,接头不应超过2个。
3.2.5电缆横穿道路时应采用保护套,避免碾压磨损等。
3.2.6焊接电缆的绝缘每半年应检查一次。
3.2.7电焊机各项指标必须符合国家标准。
3.2.8焊机应安装空载自动断电保护装置。
3.2.9电焊机应每半年进行一次例行维修保养。
3.3气割、气焊安全规定3.3.1焊炬或割炬使用前应检查射吸能力是否良好。
3.3.2根据焊、切割材料的种类、厚度正确选用焊炬、割炬及焊咀、割咀。
3.3.3每个氧气瓶必须设两个防振橡胶圈,放置牢固。
焊接质量检验通用要求

1、总则1.1、目的:规范先歌工厂PCB'A 制程及手工焊接质量检验合格判定通用要求,此要求可通过与对应检验允收标准的配合使用更好地一致地满足客户要求,给客户满意度提供标准上的保证;1.2、适用范围:适用于先歌工厂PCB'A 制程及手工焊接质量检验使用,分频器制造及其它相关部门可选择性的参考使用;2、焊点通用要求合格的焊点必须呈现润湿特征,焊料良好地附着在被焊金属表面。
润湿的焊点,其焊缝外形特征是呈凹形的弯液面,判定依据是润湿时焊料与焊盘,焊料与引线 / 焊端之间的界面接触角较小或接近于零度。
通常焊料合金的范围很宽,可以表现出从很低甚至接近0度的接触角直到接近90度的接触角。
如果焊接面有部分面积没有被焊料合金润湿,则一般认定为不润湿状态,这时的特征是接触角大于90°。
如图1之A 、B 所示,焊点润湿角都不超过90度,合格;但C 、D 所示接触角虽然超过90度,属于例外情况,也是合格的,原因是焊点轮廓由于设计要求延伸到焊接区域外部边缘和阻焊膜。
图1:几种典型润湿角度修 订 记 录2.1、焊点外观合格性总体要求润湿角度合格●连接处的焊料中间厚边上薄,焊缝形状为凹型。
●焊缝表面总体光滑且焊料在被焊件上充分润湿;焊接件的轮廓清晰。
●焊点润湿角(焊料与元器件之间,以及焊料与PCB 之间)不超过90°注:例外情况:焊料量较大致使其不得不延伸到可焊区域外或阻焊膜处时,接触角大于90°(图1C 、D );2.2、典型焊点缺陷 2.2.1、基体金属暴露元器件引线、导体、焊盘表面的暴露的金属基体,原则上缺口和伤痕等不能超过引线直径的10%,导线宽度的20%。
某些PCB 和导体的表面处理涂层有不同的润湿特征,可能仅仅在规定区域呈现焊料润湿。
在这种情况下,应该考虑暴露的金属基体和表面处理涂层的特殊情况,只要其焊接仍然具有主要润湿特征,也应该可以表明是合格的。
合格的插件引脚或焊盘基体金属暴露合格● 导体的厚度面上暴露基体金属 ● 引线头(引线端面)上暴露基体金属 ● 有机可焊保护涂层焊盘上暴露金属 ●不要求有焊缝的地方暴露金属2.2.2、针孔、吹孔(爆孔)、孔洞等吹孔孔洞合格●焊点满足所有其它要求的前提下,存在的吹孔,针孔,孔洞等。
手工焊接要求和验收标准
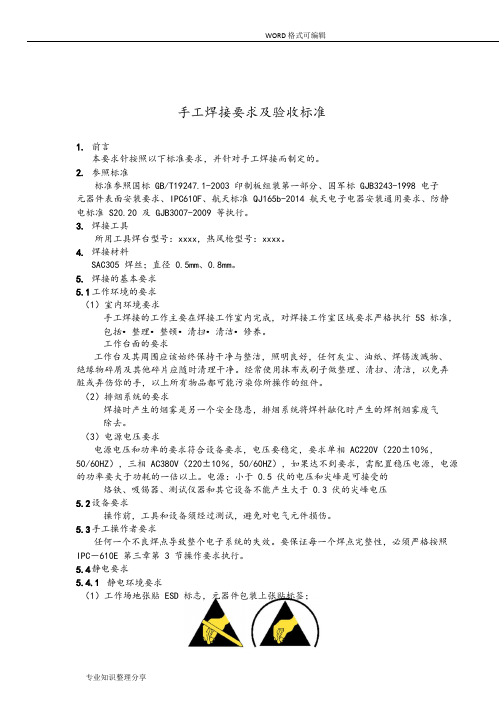
WORD格式可编辑手工焊接要求及验收标准1.前言本要求针按照以下标准要求,并针对手工焊接而制定的。
2.参照标准标准参照国标 GB/T19247.1-2003 印制板组装第一部分、国军标 GJB3243-1998 电子元器件表面安装要求、IPC610F、航天标准 QJ165b-2014 航天电子电器安装通用要求、防静电标准 S20.20 及 GJB3007-2009 等执行。
3.焊接工具所用工具焊台型号:xxxx,热风枪型号:xxxx。
4.焊接材料SAC305 焊丝;直径 0.5mm、0.8mm。
5.焊接的基本要求5.1工作环境的要求(1)室内环境要求手工焊接的工作主要在焊接工作室内完成,对焊接工作室区域要求严格执行 5S 标准,包括•整理•整顿•清扫•清洁•修养。
工作台面的要求工作台及其周围应该始终保持干净与整洁,照明良好,任何灰尘、油纸、焊锡泼溅物、绝缘物碎屑及其他碎片应随时清理干净。
经常使用抹布或刷子做整理、清扫、清洁,以免弄脏或弄伤你的手,以上所有物品都可能污染你所操作的组件。
(2)排烟系统的要求焊接时产生的烟雾是另一个安全隐患,排烟系统将焊料融化时产生的焊剂烟雾废气除去。
(3)电源电压要求电源电压和功率的要求符合设备要求,电压要稳定,要求单相 AC220V(220±10%,50/60HZ),三相 AC380V(220±10%,50/60HZ),如果达不到要求,需配置稳压电源,电源的功率要大于功耗的一倍以上。
电源:小于 0.5 伏的电压和尖峰是可接受的烙铁、吸锡器、测试仪器和其它设备不能产生大于 0.3 伏的尖峰电压5.2设备要求操作前,工具和设备须经过测试,避免对电气元件损伤。
5.3手工操作者要求任何一个不良焊点导致整个电子系统的失效。
要保证每一个焊点完整性,必须严格按照IPC-610E 第三章第 3 节操作要求执行。
5.4静电要求5.4.1静电环境要求(1)工作场地张贴 ESD 标志,元器件包装上张贴标签;(2)防静电桌(3)准备物品图 1 防静电标识图2防静电桌准备防静电箱、粉色聚乙烯包装袋、铝箔防静电袋、离子发生器,防静电地板、防静电指环或手套、防静电的 PCB 搁架、印制板套件。
焊接工艺评定规则

焊接工艺评定规则目次1. 总则2. 引用的标准、法规3. 焊接工艺评定的程序及要求4. 焊接工艺评定失败的处理5. 焊接工艺评定的保存6. 附录《焊接工艺评定》管理规则1. 总则1.1 根据〈蒸气锅炉安全技术监察规程〉(以下简称“蒸规”)及其附录Ⅰ的要求,本规则规定了在安装、改造、维修施工中,制作“焊接工艺评定”时所应遵守的程序和各部门、各职能人员的职责。
1.2 本规则同时规定了“焊接工艺评定”完成后的保管和应用。
1.3 “焊接工艺评定”是评定本单位是否具有焊出合格接头的能力;同时也验证施工中制定的焊接工艺是否正确。
因此,评定试件应由本单位熟练焊工焊接。
不允许借用其他单位的焊工,更不允许借用其他单位的焊接工艺评定。
1.4 “指导书”、“评定报告”、“施焊记录”填写时应字迹工整、清楚,需要修改的地方,修改人应签上时间、姓名和数量。
不许随意涂改。
2. 引用的标准、法规下列文件中的条款通过本管理规则的引用而成为本规则的条款。
凡是不注日期的引用文件,其最新版本适用于本规则。
《蒸气锅炉安全技术监察规程》JB/T 3375 《锅炉用材料入厂验收规则》JB/T 4730.1~4730.3 《承压设备无损检测》第一部分通用要求第二部分射线检测第三部分超声检测JB/T 2636 《锅炉受压元件焊接接头金相和断口检验方法》GB 228 《金属拉伸试验方法》GB /T229 《金属夏比冲击试验方法》GB 232 《金属弯曲试验方法》3. 焊接工艺评定的程序及要求3.1在编制施工方案时,应根据图纸及〈蒸规〉和附录Ⅰ的要求,首先审查已作过的“焊接工艺评定”是否能在母材和焊材的分类、母材和熔敷金属厚度、焊接方法、予热、焊后热处理等方面完全覆盖。
如不能则应重新制作“焊接工艺评定”。
3.2首先由焊接技术人员编写“焊接工艺指导书”。
指导书是评定工作的依据,应该根据本单位人员、设备的具体条件编写。
3.2.1编写指导书时,在母材的选择上,在同类钢号中应尽量选择有冲击值的母材。
五种常见作业安全通用要求

3
不准私拉乱接电气设备;
4
不准使用绝缘损坏的电气设备;
5
不准私用电热设备和灯泡取暖;6来自不准擅自用水冲洗电气设备;
7
不准用铜丝、铁丝替代保险丝;
8
不准擅自移动电气平安标志、围栏等平安设施;
9
不准使用检修中机器的电气设备;
10
不准在地下电缆附近随意打桩、动土。
五种作业的通用要求
起重作业安全要求
五种作业的通用要求
7 使用气瓶要谨慎,不要碰撞、抛掷,氧气瓶的防止回火器等平安防护装置必须齐全有效。
8
9 使用中的气瓶应垂直存放,与明火等热源的距离不少于10米,氧气瓶与乙醛瓶的平安距离 1 应不小于5米。 0 不应在潮湿或雨雪天气等环境下进行焊接作业,以防发生触电事故。
五种作业的通用要求
焊接、切割作业平安要求
预防对策措施
6 被吊物菱角处与捆绑钢丝绳间未加衬垫时不吊; 7 货物超载不吊; 8 结构或零部件有影响平安工作的缺陷或损伤时不吊; 9 工作场地昏暗,无法看清场地时不吊;
10 露天作业遇有六级以上大风及大雾等恶劣天气时不吊。
五种作业的通用要求
焊接、切割作业安全要求
五种作业的通用要求
焊接、切割作业平安要求
焊接就是通过加热或者加压,或者两种并用,并且使 用或不用填充材料,使工件到达结合的方法。 切割就是使一个物件〔部件、零件、机件〕分开,变成两 个或多个的工艺过程。
4
作业场所应设置防护挡板,防止焊花四溅或对其他人员的电弧辐射伤害。动火设备和运 行设备应有效隔离,如管道上用盲板,加封头塞头,或拆掉一节管子的防范方法。
5 在有易燃易爆物品场所进行作业时,必须对周围环境采取清理、遮挡等平安措施。
焊接设备的安全要求模版
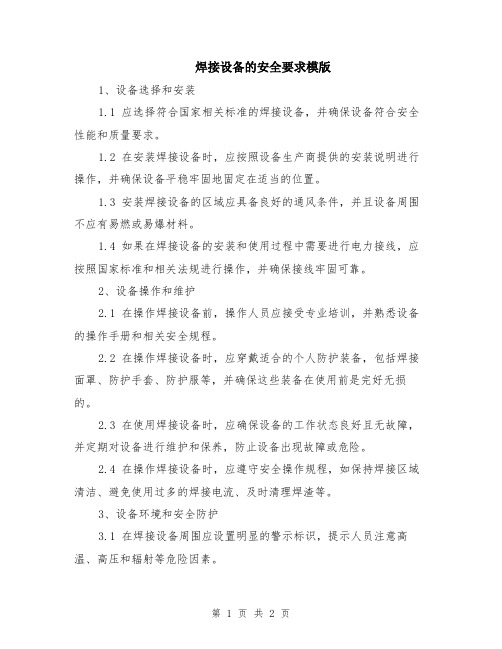
焊接设备的安全要求模版1、设备选择和安装1.1 应选择符合国家相关标准的焊接设备,并确保设备符合安全性能和质量要求。
1.2 在安装焊接设备时,应按照设备生产商提供的安装说明进行操作,并确保设备平稳牢固地固定在适当的位置。
1.3 安装焊接设备的区域应具备良好的通风条件,并且设备周围不应有易燃或易爆材料。
1.4 如果在焊接设备的安装和使用过程中需要进行电力接线,应按照国家标准和相关法规进行操作,并确保接线牢固可靠。
2、设备操作和维护2.1 在操作焊接设备前,操作人员应接受专业培训,并熟悉设备的操作手册和相关安全规程。
2.2 在操作焊接设备时,应穿戴适合的个人防护装备,包括焊接面罩、防护手套、防护服等,并确保这些装备在使用前是完好无损的。
2.3 在使用焊接设备时,应确保设备的工作状态良好且无故障,并定期对设备进行维护和保养,防止设备出现故障或危险。
2.4 在操作焊接设备时,应遵守安全操作规程,如保持焊接区域清洁、避免使用过多的焊接电流、及时清理焊渣等。
3、设备环境和安全防护3.1 在焊接设备周围应设置明显的警示标识,提示人员注意高温、高压和辐射等危险因素。
3.2 在焊接设备使用区域应确保良好的照明条件,以便操作人员能清楚地看到焊接区域和设备控制面板等。
3.3 当设备需要长时间连续工作时,应设立适当的休息时间,避免过度使用设备导致设备过热或故障。
3.4 在进行特殊焊接作业时,如高空焊接或水下焊接等,应根据实际情况采取相应的安全防护措施,以确保操作人员的人身安全。
4、紧急情况处理4.1 在焊接设备使用过程中,如发生火灾、漏电或设备故障等紧急情况,操作人员应立即停止使用设备,并按照紧急处理流程采取相应的措施。
4.2 焊接设备使用区域应配备相应的紧急疏散通道和应急设备,以便在紧急情况下能及时疏散人员并进行救援。
4.3 为了快速应对紧急情况,操作人员应定期进行应急演练,以熟悉应急流程和掌握相应的应急技能。
4.4 在紧急情况处理后,应对焊接设备进行检查和维修,并确保设备能够正常工作。
手工焊接要求及验收标准
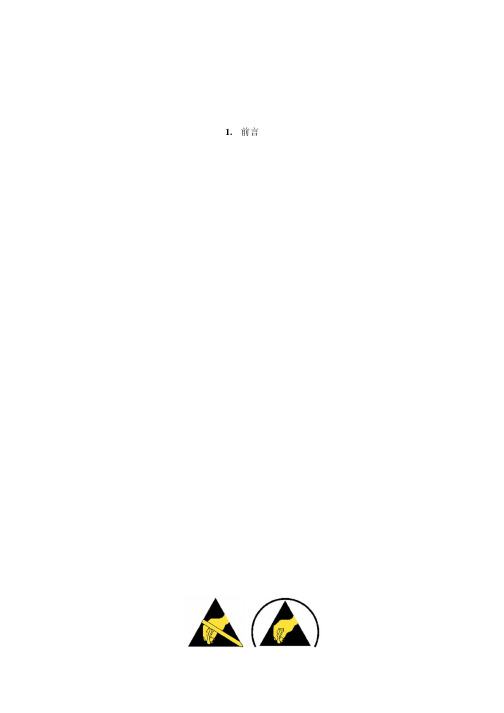
1.前言手工焊接要求及验收标准本要求针按照以下标准要求,并针对手工焊接而制定的。
2.参照标准标准参照国标GB/T19247.1-2003 印制板组装第一部分、国军标GJB3243-1998 电子元器件表面安装要求、IPC610F、航天标准QJ165b-2014 航天电子电器安装通用要求、防静电标准S20.20 及GJB3007-2009 等执行。
3.焊接工具所用工具焊台型号:xxxx,热风枪型号:xxxx。
4.焊接材料SAC305 焊丝;直径0.5mm、0.8mm。
5.焊接的基本要求5.1工作环境的要求(1)室内环境要求● 手工焊接的工作主要在焊接工作室内完成,对焊接工作室区域要求严格执行5S 标准,包括•整理•整顿•清扫•清洁•修养。
● 工作台面的要求工作台及其周围应该始终保持干净与整洁,照明良好,任何灰尘、油纸、焊锡泼溅物、绝缘物碎屑及其他碎片应随时清理干净。
经常使用抹布或刷子做整理、清扫、清洁,以免弄脏或弄伤你的手,以上所有物品都可能污染你所操作的组件。
(2)排烟系统的要求● 焊接时产生的烟雾是另一个安全隐患,排烟系统将焊料融化时产生的焊剂烟雾废气除去。
(3)电源电压要求电源电压和功率的要求符合设备要求,电压要稳定,要求单相AC220V(220±10%,50/60HZ),三相AC380V(220±10%,50/60HZ),如果达不到要求,需配置稳压电源,电源的功率要大于功耗的一倍以上。
电源:小于0.5 伏的电压和尖峰是可接受的● 烙铁、吸锡器、测试仪器和其它设备不能产生大于0.3 伏的尖峰电压5.2设备要求● 操作前,工具和设备须经过测试,避免对电气元件损伤。
5.3手工操作者要求任何一个不良焊点导致整个电子系统的失效。
要保证每一个焊点完整性,必须严格按照IPC-610E 第三章第3 节操作要求执行。
5.4静电要求5.4.1静电环境要求(1)工作场地张贴ESD 标志,元器件包装上张贴标签;(2)防静电桌(3)准备物品图 1 防静电标识图 2 防静电桌准备防静电箱、粉色聚乙烯包装袋、铝箔防静电袋、离子发生器,防静电地板、防静 电指环或手套、防静电的 PCB 搁架、印制板套件。
手工焊接要求及验收标准
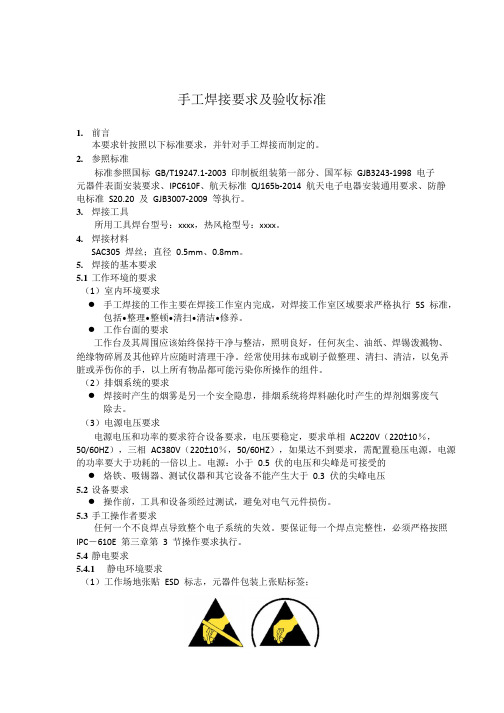
手工焊接要求及验收标准1.前言本要求针按照以下标准要求,并针对手工焊接而制定的。
2.参照标准标准参照国标GB/T19247.1-2003 印制板组装第一部分、国军标GJB3243-1998 电子元器件表面安装要求、IPC610F、航天标准QJ165b-2014 航天电子电器安装通用要求、防静电标准S20.20 及GJB3007-2009 等执行。
3.焊接工具所用工具焊台型号:xxxx,热风枪型号:xxxx。
4.焊接材料SAC305 焊丝;直径0.5mm、0.8mm。
5.焊接的基本要求5.1工作环境的要求(1)室内环境要求● 手工焊接的工作主要在焊接工作室内完成,对焊接工作室区域要求严格执行5S 标准,包括•整理•整顿•清扫•清洁•修养。
● 工作台面的要求工作台及其周围应该始终保持干净与整洁,照明良好,任何灰尘、油纸、焊锡泼溅物、绝缘物碎屑及其他碎片应随时清理干净。
经常使用抹布或刷子做整理、清扫、清洁,以免弄脏或弄伤你的手,以上所有物品都可能污染你所操作的组件。
(2)排烟系统的要求● 焊接时产生的烟雾是另一个安全隐患,排烟系统将焊料融化时产生的焊剂烟雾废气除去。
(3)电源电压要求电源电压和功率的要求符合设备要求,电压要稳定,要求单相AC220V(220±10%,50/60HZ),三相AC380V(220±10%,50/60HZ),如果达不到要求,需配置稳压电源,电源的功率要大于功耗的一倍以上。
电源:小于0.5 伏的电压和尖峰是可接受的● 烙铁、吸锡器、测试仪器和其它设备不能产生大于0.3 伏的尖峰电压5.2设备要求● 操作前,工具和设备须经过测试,避免对电气元件损伤。
5.3手工操作者要求任何一个不良焊点导致整个电子系统的失效。
要保证每一个焊点完整性,必须严格按照IPC-610E 第三章第3 节操作要求执行。
5.4静电要求5.4.1静电环境要求(1)工作场地张贴ESD 标志,元器件包装上张贴标签;(2)防静电桌(3)准备物品图 1 防静电标识图2防静电桌准备防静电箱、粉色聚乙烯包装袋、铝箔防静电袋、离子发生器,防静电地板、防静电指环或手套、防静电的PCB 搁架、印制板套件。
铝合金焊接现场场地及环境通用要求

铝合金焊接现场及环境通用要求1.目的为更好的控制焊接现场各因素对焊接的影响,满足铝合金产品焊接工艺要求,保证产品焊接质量。
2.适用范围应用于铝合金产品生产制造的焊接现场。
3.归口部门工艺技术部4.职责操作人员需按照此作业指导书进行操作。
5.总体要求5.1场地要求焊接场地应具有独立封闭的铝合金焊接、加工的专用场地,避免钢铝混杂;5.2环境要求应具有整体排烟、供暖和除湿装置,环境温度≥16℃,空气湿度≤60%,风速≤1m/s;针对四方机车车辆股份有限公司对环境的要求,在加工四方的产品时,按如下相关要求执行:环境温度≥8℃,空气湿度≤80%,风速≤1m/s;6.其他要求6.1焊接现场应有温湿度检测仪,并做好温、湿度记录;6.2焊接现场配备加热炉,已备随时对焊材进行烘干处理;6.3焊接区域各相邻工序之间应配备遮光屏;6.4车间应具备220V-380V和各种电源的接口、稳压装置;6.5应确保焊接电源电缆、焊接地线接线状态良好,不应存在破损现象;6.6焊接现场用电线应整理有序,焊接地线卡子应就近与被焊工件固定在一起;6.7具备满足焊接生产的坡口加工设备和预热设备;6.8生产焊接产品所用的工装、平台及定位拐角、卡具;6.9 5T以上的起重装置;6.10配备两套以上的防火消防器材;6.11能够满足产品要求的焊接打磨工具和测量工具。
7.车间温湿度的控制与调节:7.1温湿度控制仪安装位置:手工焊和自动焊区必须挂置温湿度控制仪,温湿度控制仪应安置在空气流通、不受阳光照射的地方;在自动焊区,温湿度控制仪安装在自动焊设备上;在手工焊区,温湿度控制仪安装在立柱上,距离≤25m;挂置高度约1.5米。
7.2检查频次:检查次数为每班次至少两次,由专人负责检查并填写检查记录;现场焊接监督人员跟踪记录的真实性并根据作业环境的变化适时增加检查频次。
7.3四季温湿度控制措施:环境条件按开工工作环境控制。
车间窗户须封闭、员工进出车间应随手关门;8.室外作业环境的控制:当需要在室外进行焊接作业时,除环境条件满足上述要求外,应在焊接现场周围增加挡风板。
焊接与切割作业安全通用要求

《焊接与切割安全》(GB9448—1999)第11.2.4条
强制
3
电缆完整
构成焊接回路的电缆外皮必须完整、绝缘良好(绝缘电阻大于1 MΩ)。用于高频、高压振荡器设备的电缆,必须具有相应的绝缘性能。
《焊接与切割安全》(GB9448—1999)第11.4.2条
《个体防护装备选用规范》(GB/T-11651)第6.1条
推荐
11
头罩或护目镜选用
作业人员在观察电弧时,必须使用带有滤光镜的头罩或手持面罩,或佩戴安全镜、护目镜或其他合适的眼镜;
《焊接与切割安全》(GB9448—1999)第4.2条
强制
12
防护手套佩戴
所有焊工和切割工必须佩戴耐火的防护手套。
《焊接与切割安全》(GB9448—1999)第4.2条
《溶解乙炔气瓶安全监察规程》第六十三条第1项
强制
9
乙炔和氧气瓶同运规定
移动作业时,应采用专用小车搬运,如需乙炔瓶和氧气瓶放在同一小车上搬运,必须用非燃材料隔板隔开。
《溶解乙炔气瓶安全监察规程》第六十四条第7项
强制
10
气瓶上端禁放物品
气瓶在使用时,其上端禁止放置物品,以免损坏安全装置或妨碍阀门的迅速关闭。使用结束后,气瓶阀必须关紧。
强制
4
电缆接线
焊机的电缆应使用整根导线,尽量不带连接接头。需要接长导线时,接头处要连接牢固、绝缘良好。
《焊接与切割安全》(GB9448—1999)第11.4.3条
强制
5
对电缆采取保护措施
构成焊接回路的电缆禁止搭在气瓶等易燃品上,禁止与油脂等易燃物质接触。在经过通道、马路时,必须采取保护措施(如:使用保护套)。
焊接与切割作业安全通用要求
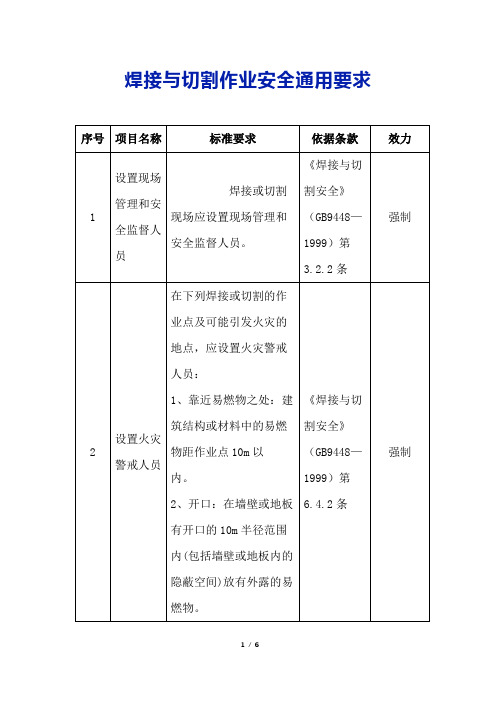
3、金属墙壁:靠近金属间壁、墙壁、天花板、屋顶等处另一侧易受传热或辐射而引燃的易燃物。
《焊接与切割安全》(GB9448—1999)第6.4.2条
强制
3
焊接和割切审批要求
操作者只有在规定的安全条件得到满足;并得到现场管理及监督者准许的前提下,才可实施焊接或切割操作。在获得准许的条件没有变化时,操作者可以连续地实施焊接或切割。
《个体防护装备选用规范》(GB/T-11651)第6.1条
推荐
11
头罩或护目镜选用
作业人员在观察电弧时,必须使用带有滤光镜的头罩或手持面罩,或佩戴安全镜、护目镜或其他合适的眼镜;
《焊接与切割安全》(GB9448—1999)第4.2条
强制
12
防护手套佩戴
所有焊工和切割工必须佩戴耐火的防护手套。
《焊接与切割安全》(GB9448—1999)第4.2条
强制
13
消除火灾隐患
焊接或切割作业只能在无火灾隐患的条件下实施:
1、有条件时,首先要将工件移至指定的安全区进行焊接;
2、工件不可移时,应将火灾隐患周围所有可移动物移至安全位置;
3、工件及火源无法转移时,要采取措施限制火源以免发生火灾。
《焊接与切割安全》(GB9448—1999)第6.3条
强制
14
灭火设备配备
焊接与切割作业安全通用要求
序号
项目名称
标准要求
依据条款效力1来自设置现场管理和安全监督人员
焊接或切割现场应设置现场管理和安全监督人员。
《焊接与切割安全》(GB9448—1999)第3.2.2条
强制
2
焊接(电焊)与切割作业安全要求

《焊接与切割安全》(GB9448—1999)第6.4.1条
强制
氧燃气焊接及切割安全
序号
项目名称
标准要求
依据条款
效力
1
氧气与可燃物的隔离
氧气瓶、气瓶阀、接头、减压器、软管及设备必须与油、润滑脂及其他可燃物或爆炸物相隔离。严禁用沾有油污的手、或带有油迹的手套去触碰氧气瓶或氧气设备。
强制
4
电缆接线
焊机的电缆应使用整根导线,尽量不带连接接头。需要接长导线时,接头处要连接牢固、绝缘良好。
《焊接与切割安全》(GB9448—1999)第11.4.3条
强制
5
对电缆采取保护措施
构成焊接回路的电缆禁止搭在气瓶等易燃品上,禁止与油脂等易燃物质接触。在经过通道、马路时,必须采取保护措施(如:使用保护套)。
强制
3
焊接和割切审批要求
操作者只有在规定的安全条件得到满足;并得到现场管理及监督者准许的前提下,才可实施焊接或切割操作。在获得准许的条件没有变化时,操作者可以连续地实施焊接或切割。
《焊接与切割安全》(GB9448—1999)第3.2.3条第二款
强制
4
在指定区域进行作业
焊接及切割应在为减少火灾隐患而设计、建造(或特殊指定)的区域内进行。因特殊原因需要在非指定的区域内进行焊接或切割操作时,必须经检查、核准。
1、靠近易燃物之处:建筑结构或材料中的易燃物距作业点10m以内。
2、开口:在墙壁或地板有开口的10m半径范围内(包括墙壁或地板内的隐蔽空间)放有外露的易燃物。
3、金属墙壁:靠近金属间壁、墙壁、天花板、屋顶等处另一侧易受传热或辐射而引燃的易燃物。
《焊接与切割安全》(GB9448—1999)第6.4.2条
手工焊接要求及验收标准

范文范例指导学习手工焊接要求及验收标准1.前言本要求针按照以下标准要求,并针对手工焊接而制定的。
2.参照标准标准参照国标 GB/T19247.1-2003 印制板组装第一部分、国军标 GJB3243-1998 电子元器件表面安装要求、IPC610F、航天标准 QJ165b-2014 航天电子电器安装通用要求、防静电标准 S20.20 及 GJB3007-2009 等执行。
3.焊接工具所用工具焊台型号:xxxx,热风枪型号:xxxx。
4.焊接材料SAC305 焊丝;直径 0.5mm、0.8mm。
5.焊接的基本要求5.1工作环境的要求(1)室内环境要求手工焊接的工作主要在焊接工作室内完成,对焊接工作室区域要求严格执行 5S 标准,包括•整理•整顿•清扫•清洁•修养。
工作台面的要求工作台及其周围应该始终保持干净与整洁,照明良好,任何灰尘、油纸、焊锡泼溅物、绝缘物碎屑及其他碎片应随时清理干净。
经常使用抹布或刷子做整理、清扫、清洁,以免弄脏或弄伤你的手,以上所有物品都可能污染你所操作的组件。
(2)排烟系统的要求焊接时产生的烟雾是另一个安全隐患,排烟系统将焊料融化时产生的焊剂烟雾废气除去。
(3)电源电压要求电源电压和功率的要求符合设备要求,电压要稳定,要求单相 AC220V(220±10%,50/60HZ),三相 AC380V(220±10%,50/60HZ),如果达不到要求,需配置稳压电源,电源的功率要大于功耗的一倍以上。
电源:小于 0.5 伏的电压和尖峰是可接受的烙铁、吸锡器、测试仪器和其它设备不能产生大于 0.3 伏的尖峰电压5.2设备要求操作前,工具和设备须经过测试,避免对电气元件损伤。
5.3手工操作者要求任何一个不良焊点导致整个电子系统的失效。
要保证每一个焊点完整性,必须严格按照IPC-610E 第三章第 3 节操作要求执行。
5.4静电要求5.4.1静电环境要求(1)工作场地张贴 ESD 标志,元器件包装上张贴标签;(2)防静电桌(3)准备物品图 1 防静电标识图 2 防静电桌准备防静电箱、粉色聚乙烯包装袋、铝箔防静电袋、离子发生器,防静电地板、防静 电指环或手套、防静电的 PCB 搁架、印制板套件。
IPC J-STD-001焊接的电气和电子组件要求

IPC J-STD-001焊接的电气和电子组件要求招生对象---------------------------------工程部、品质部、研发部、SMT、客服等部门经理、课长、主管、工程师、技术员. 从事电子行业的培训人员, 焊接人员, 工程技术人员及参与制定公司检验标准及参与检验的相关人员。
【主办单位】中国电子标准协会【咨询热线】0 7 5 5 – 2 6 5 0 6 7 5 7 137****2936李生【报名邮箱】martin# (请将#换成@)课程内容---------------------------------课程目的:IPC J-STD-001E焊接的电气和电子组件要求已经成为全球电子组装制造业的权威手册,本标准描述了制造高质量有铅和无铅互连元件的材料、方法和验证要求。
标准强调流程控制并且针对电子连接的各个方面设定了行业通用的要求。
IPC J-STD-001E标准共12章。
全文72页,38幅彩色插图,其中14幅为新增和更新插图,内容涵盖总则、适用文件、材料、元器件和设备要求、焊接和组装通用要求、导线和接线柱连接、通孔安装和端子、元器件的表面贴装、清洗工艺要求、PCB要求、涂覆和灌封、产品保证、返工和维修。
IPC J-STD-001E标准是由业界开发并接受认可的,可追溯的标准化模式的培训课程,以加强对标准的正确理解和适当运用。
通过这个培训课程将帮助员工提升专业技能。
IPC J-STD-001E标准CIS(认证专家)培训,针对生产线作业员,工程技术员、检验员、工艺工程师、生产/工程/质保行政人员及其他相关人员以及买家。
授课时间总共为四十小时(五天)IPC J-STD-001 IPC 认证专家(CIS) 课程大纲模块课程内容备注1欢迎/介绍。
IPC政策和程序IPC J-STD-001E 概述IPC政策/培训目标/证书的期限等。
001E的一般要求和引用文件,材料,元器件和设备要求,焊接和组装的通用要求,清洗工艺要求,考试。
- 1、下载文档前请自行甄别文档内容的完整性,平台不提供额外的编辑、内容补充、找答案等附加服务。
- 2、"仅部分预览"的文档,不可在线预览部分如存在完整性等问题,可反馈申请退款(可完整预览的文档不适用该条件!)。
- 3、如文档侵犯您的权益,请联系客服反馈,我们会尽快为您处理(人工客服工作时间:9:00-18:30)。
焊接通用要求
Welding procedure together with the relevant procedure qualification and non-destructive testing procedure shall be provided for pressure vessels.
Heat treatment procedure may be indicated in the welding procedure or submitted as separate documents.
Welding procedure and welder’s qualification shall be according to ASME code.
Welding shall be performed by qualified welders using qualified procedures and test and inspection shall be performed by qualified inspectors using qualified procedures, according to applicable ASME code.
The identification of the welders must be applicable for the following critical piping:
∙HP steam pipe (from(SH) outlet to ST HP stop valve);
∙Low temperature reheat steam pipe (from ST HP exhaust to (RH) inlet);
∙High temperature reheat steam pipe (from (RH) outlet to ST RSV).
The welding material shall be similar to the mother material according to applicable code.
Welding plant and ancillary equipment shall be in accordance with the appropriate parts of BS 638 or equivalent international standard.
The area of the temporary welded attachments shall be examined according to applicable code if the parts will be used as removed.
The material composition to be welded shall be according to applicable material code.
Preheat condition for shop and field welding shall be in accordance with applicable code.
NDT of castings, wrought products and welding shall be carried out in accordance with the applicable material code/standard or British Standard. NDE procedure for the owner’s witness ite ms shall be submitted for approval.
SNT-TC-1A shall be applied for NDE operator/inspector qualification. NDE operator shall be Level I, and inspector shall be Level II.
During the detailed design stage, the boiler manufacturer shall submit for approval the welding procedure specification (WPS) and procedure qualification records (PQR’s) and heat treatment procedure for the critical components which are listed below.(卖方负责自己供货范围内焊缝)
HP steam pipe (from (SH) outlet to ST HP stop valve);
Low temperature reheat steam pipe (from ST HP exhaust to (RH) inlet);
High temperature reheat steam pipe (from (RH) outlet to ST RSV).
Special consideration for field welding of any P-92 materials shall be taken. Field welding of this material shall be limited as much as possible.
Welding field procedures shall be according to ASME Code (without stamp).
焊接材料的选择应根据钢的化学成分、力学性能、使用工况条件和焊接工艺评定的结果选用。
焊接材料(焊丝、焊条、焊剂、钨棒、氩气、氧气和乙炔等)的质量应符合ASME标准。
焊接工程中使用的进口焊接材料应符合设计要求和工艺技术要求。
无焊接工艺评定(PQR)和焊接工艺规程(WPS)不能开始焊接生产,编制《焊接工艺规程》及其它焊接技术和生产用文件。
其它项目的焊接工艺评定可以转移到本项目,工艺评定必须覆盖本项目钢材的所有材质、规格、焊接位置及其它,当设计要求和母材有冲击韧性要求时,工艺评定应做冲击试验。
焊接坡口形式、对接间隙及坡口内、外边缘20mm附近无裂皮、重皮、坡口破损和毛刺等,按照ASME标准要求执行。
焊缝尺寸必须符合设计要求和相应的规范、标准要求。
焊缝表面应成型美观,波纹均匀,焊缝边缘应圆滑过渡到母材,焊缝及焊缝附近的飞溅物必须清理干净,严禁油漆掩盖飞溅及焊渣。
外观检查参照ASME 要求。
焊接接头的热处理按照ASME相关要求执行。
受压件焊接接头无损检验标准按照ASME相关标准执行。
焊接接头的光谱分析按照ASME的规定执行。
焊接接头的硬度检验:可取样的焊接接头采用台式硬度仪,按照ASME规定执行,其余焊接接头采用便携里氏硬度仪,按照ASME的规定执行。
硬度检验在焊后热处理完成后进行。
金相检验按照ASME执行。
焊接设备、热处理设备、无损检测设备、工器具及仪表应定期检查,需要计量的部分应定期校验。
焊接环境、焊接人员资质按照ASME规定执行。