注射剂生产车间工程设计[001]
大容量注射剂生产工艺流程图

目录1.大容量注射剂生产区概况2.需要验证的关键工序及工艺验证3.工艺流程的实施4.操作过程及工艺条件5.技术安全、工艺卫生及劳动保护6.物料平衡及技经指标7.设备一览表8.岗位定员9.附件(含设备操作、清洁规程)10.变更记录1.大容量注射剂生产区概况本生产区面积904㎡,其中1万级净化区域167㎡,10万级净化区域174㎡。
大容量注射剂车间采用10万级和1万级(局部百级)空气净化洁净级别,10万级区域设置缓冲、更衣、洗涤、洁具、称量、配碳、浓配、洗瓶等,1万级区域设置缓冲、更衣更鞋、稀配、化验、灌装、加塞、轧盖、洗涤、存放、洁具等功能间,所有隔断采用无粉尘产生的静电喷涂彩钢板,结合处采用圆角处理,不易产生积灰;人员经过三次更衣和二次更鞋后进入洁净区操作,物料进入洁净区均采用传递窗或气闸进行传递,人流、物流的进入相对分开,保证了洁净区空气洁净度要求;生产设备均采用优质不锈钢材料制造,采用洗瓶、灌装、压塞、轧盖联动线生产,其中洗瓶出口、灌装、加塞采用百级层流保护,灭菌器采用水浴式灭菌器。
1.1 大容量注射剂生产工艺流程图(见后页)1.2 大容量注射剂生产区工艺布局布置图(见后页)1.3 大容量注射剂生产区工艺设备布置图(见后页)1.4 大容量注射剂生产区送回风口平面布置图(见后页)以上项目按验证文件规定,均已在规定周期内进行相关的验证,验证方案及报告见相应文件。
大容量注射剂生产工艺流程图3.工艺流程的实施3.1 批生产指令的签发3.1.1 批生产指令由车间技术负责人根据生产计划表起草,并依据产品工艺规程于生产前一个工作日制定。
3.1.2 批生产指令应经QA质监员审核并签字,由车间主任签字批准后生效。
3.2 生产批记录的发放3.2.1 除配制工序和包装工序外,工序相应的生产批记录于生产当日由车间工艺质监员发放给各工序负责人,并于工序结束当日填写完整返回车间工艺质监员处汇总。
3.2.2 配制工序和包装工序的生产批记录于生产前一天由车间工艺质监员随同批生产指令或批包装指令一同发放,并于工序结束当日填写完整返回车间工艺质监员处汇总。
(完整版)冻干粉针制剂灌装车间设计
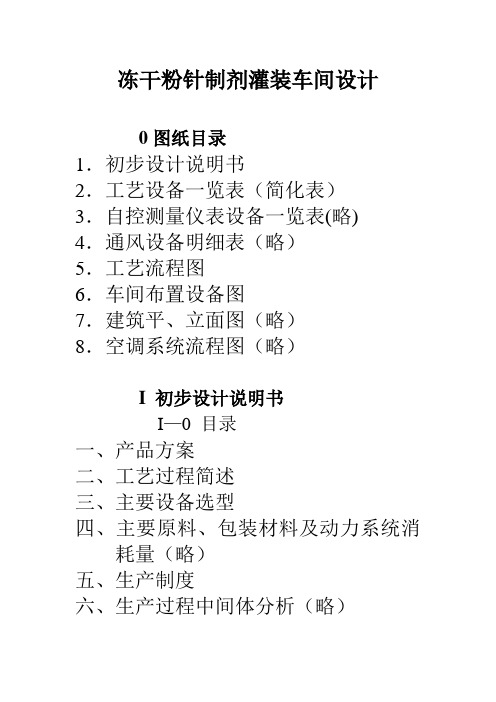
冻干粉针制剂灌装车间设计0图纸目录1.初步设计说明书2.工艺设备一览表(简化表)3.自控测量仪表设备一览表(略) 4.通风设备明细表(略)5.工艺流程图6.车间布置设备图7.建筑平、立面图(略)8.空调系统流程图(略)I 初步设计说明书I—0 目录一、产品方案二、工艺过程简述三、主要设备选型四、主要原料、包装材料及动力系统消耗量(略)五、生产制度六、生产过程中间体分析(略)七、仪表及自动控制(略)八、技术安全、防火及空气净化(略)九、车间配电(略)十、车间维修十一、车间布置十二、土建(略)十三、岗位定员(略)十四、存在问题及建议十五、主要技术经济指标(略)附表:1.工艺设备一览表2.自控仪表一览表(略)3.通风设备明细表(略)附图:1.工艺流程图2.车间设备布置图3.建筑平、立面图(略)4.空调系统流程图(略)I—1 产品方案(一)产品名称和性质冻干粉针剂D,是一种常用的注射剂型,遇水溶解。
(二)产品规格5ml,采用7ml瓶存储。
(三)产品包装方式无菌药用西林瓶包装,6瓶每盒。
I—2 工艺过程简述(一)胶塞的处理传统处理工艺:胶塞酸洗——自来水冲洗——胶塞洗涤机蒸汽煮,常水冲洗(搅拌)——注射用水冲洗,硅油搅拌,沥干——送胶塞干燥消毒机干燥消毒——由无菌室驱除,冷至室温备用现今有一步化的免洗胶塞,可省略以上步骤,取出灭菌后即可使用。
(二)药液的配制采用封闭液体循环配制机组,原辅料投入后在密闭的配制罐和管路系统中自动完成浓配、稀配、砂蕊过滤器粗滤、微孔滤膜过滤器精滤。
(三)西林瓶的处理西林瓶经过拨盘进入转笼。
随着转笼的转动,由超声波清洗后,用针管插入式高压水、汽循环冲洗瓶内壁,喷淋装置洗瓶子外壁,从而达到清洗效果。
转笼转一周后由拨盘推动的西林瓶将清洗好的瓶子呈散装形式自动进入隧道灭菌烘箱之中,并设有超声波元件损坏时由报警装置报警。
在网带式隧遭灭菌烘箱智能系统的监控下,瓶子随网带的输送依次进入隧道灭菌箱的预热区,高温灭菌区(温度≥350℃,灭菌时间≥5min)和低温冷却区。
10级-制药工程课程设计题目:年产1000万只庆大霉素注射液车间设计等 (1)

10级-制药工程课程设计题目:年产1000万只庆大霉素注射液车间设计等1.年产1000万只庆大霉素注射液车间设计2.年产1000万只肝素钠注射液车间设计3. 1.0亿支/年头孢类粉针剂车间设计4. 2.0亿片/年头孢类片剂车间设计5. 2.0亿粒/年头孢类胶囊剂车间设计6. 1.0亿支/年双黄连口服液车间设计7. 1.0亿粒/年双黄连胶囊剂车间设计8.5000万袋/年(5g/袋)双黄连颗粒剂车间设计9.10.0亿丸/年六味地黄丸车间设计10.2.0亿片/年(金嗓子)喉片片剂车间设计11.1.0亿支/年透明质酸钠(1ml)针剂凝胶剂车间设计12.1.0亿支/年青霉素钠粉针剂车间设计13.1.0亿支/年青霉素胶囊剂车间设计14.年产1000吨庆大霉素发酵车间设计15.年产1000吨林可霉素发酵车间设计16.年产1000吨红霉素发酵车间设计17.年产1000吨庆大霉素提炼车间设计18.年产1000吨林可霉素提炼车间设计19.年产1000吨红霉素提炼车间设计20.年产1000吨红霉素制水车间设计21.年产1000吨青霉素发酵车间设计22.年产1000吨头孢霉素发酵车间设计23.500吨/年产粗香菇多糖提取综合车间设计24.500吨/年产粗灰树花多糖提取综合车间设计25.250吨/年产肝素钠提取综合车间设计26.2000kg/年产肝素钠提取综合车间设计27.250吨/年产低分子肝素钠提取综合车间设计28.2000kg/年产低分子肝素钠提取综合车间设计29.250吨/年产透明质酸提取综合车间设计30.2000kg/年产透明质酸提取综合车间设计31.2.0亿片/年雷尼替丁片剂车间设计32.2.0亿片/年红霉素片剂车间设计33.5000g/年产香菇多糖提取综合车间设计34.5000g/年产灰树花多糖提取综合车间设计35.1000kg/年产溶菌酶提取综合车间设计36.50000kg/年产卵磷脂提取综合车间设计37.1000kg/年产卵磷脂提取综合车间设计38.50000kg/年产番茄红素提取综合车间设计39.1000kg/年产番茄红素提取综合车间设计40.50000kg/年产胡萝卜素提取综合车间设计41.1000kg/年产胡萝卜素提取综合车间设计42.年产1000万只禽流感疫苗车间设计43.年产1000万只狂犬疫苗车间设计44.2.0亿片/年VC银翘片片剂车间设计45.2.0亿粒/年藿香正气软胶囊车间设计46.2.0亿粒/年速效感冒胶囊车间设计47.2.0亿片/年吗丁啉片剂车间设计48.2.0亿粒/年异丙肌苷胶囊车间设计49.2.0亿粒/年环孢素A胶囊车间设计50.2.0亿粒/年他可莫司(Tacrolimus,FK506)胶囊车间设计51.1.0亿片/年VC银翘片片剂车间设计52.1.0亿粒/年藿香正气软胶囊车间设计53.1.0亿粒/年速效感冒胶囊车间设计54.1.0亿片/年吗丁啉片剂车间设计55.1.0亿片/年西咪替丁片剂车间设计56.1.0亿粒/年异丙肌苷胶囊车间设计57.1.0亿粒/年异丙肌苷胶囊车间设计58.1.0亿粒/年环孢素A胶囊车间设计59.1.0亿粒/年他可莫司(Tacrolimus,FK506)胶囊车间设计60.年产1000吨葡萄酒发酵车间设计61.年产10000吨葡萄酒发酵车间设计62.年产1000吨葡萄皮色素提取车间设计63.年产200吨庆大霉素发酵车间设计64.年产200吨林可霉素发酵车间设计65.年产200吨林可霉素提炼车间设计66.年产200吨青霉素发酵车间设计67.年产200吨头孢霉素发酵车间设计68.20t/h纯化水车间设计69.20t/h制药注射用水车间设计70.25吨/年产白藜芦醇(粗品)提取综合车间设计71.5000g/年产紫杉醇提取综合车间设计72.5000Kg/年产紫杉醇(粗品)提取综合车间设计73.5000g /年产白藜芦醇提取综合车间设计74.2000吨/年产乳链菌素发酵车间设计75.120吨/年产纳豆激酶生产车间设计注意:上述题目实际为制药工厂设计和制药工程课程设计二门课的作业!每人(可根据兴趣)选定一个题目后自己自动变为二个题目!变换方法:年产2000万只庆大霉素注射剂车间设计——年产2000万只庆大霉素注射剂可行性研究报告100kg/年产胰岛素生产车间设计——100kg/年产胰岛素可行性研究报告年产8000万只狂犬疫苗车间设计——年产8000万只狂犬疫苗可行性研究报告后者均为制药工厂设计课的作业的题目!交作业:每人一个文件夹:标题(目)+姓名;按班收齐上交!!!。
(完整版)冻干粉针制剂灌装车间设计
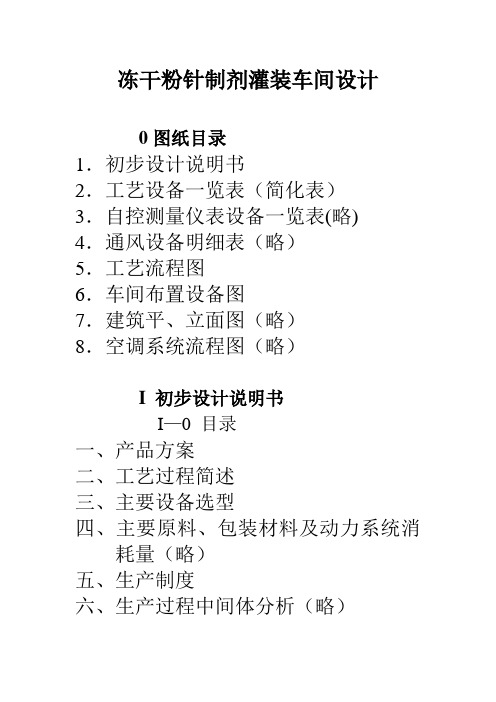
冻干粉针制剂灌装车间设计0图纸目录1.初步设计说明书2.工艺设备一览表(简化表)3.自控测量仪表设备一览表(略) 4.通风设备明细表(略)5.工艺流程图6.车间布置设备图7.建筑平、立面图(略)8.空调系统流程图(略)I 初步设计说明书I—0 目录一、产品方案二、工艺过程简述三、主要设备选型四、主要原料、包装材料及动力系统消耗量(略)五、生产制度六、生产过程中间体分析(略)七、仪表及自动控制(略)八、技术安全、防火及空气净化(略)九、车间配电(略)十、车间维修十一、车间布置十二、土建(略)十三、岗位定员(略)十四、存在问题及建议十五、主要技术经济指标(略)附表:1.工艺设备一览表2.自控仪表一览表(略)3.通风设备明细表(略)附图:1.工艺流程图2.车间设备布置图3.建筑平、立面图(略)4.空调系统流程图(略)I—1 产品方案(一)产品名称和性质冻干粉针剂D,是一种常用的注射剂型,遇水溶解。
(二)产品规格5ml,采用7ml瓶存储。
(三)产品包装方式无菌药用西林瓶包装,6瓶每盒。
I—2 工艺过程简述(一)胶塞的处理传统处理工艺:胶塞酸洗——自来水冲洗——胶塞洗涤机蒸汽煮,常水冲洗(搅拌)——注射用水冲洗,硅油搅拌,沥干——送胶塞干燥消毒机干燥消毒——由无菌室驱除,冷至室温备用现今有一步化的免洗胶塞,可省略以上步骤,取出灭菌后即可使用。
(二)药液的配制采用封闭液体循环配制机组,原辅料投入后在密闭的配制罐和管路系统中自动完成浓配、稀配、砂蕊过滤器粗滤、微孔滤膜过滤器精滤。
(三)西林瓶的处理西林瓶经过拨盘进入转笼。
随着转笼的转动,由超声波清洗后,用针管插入式高压水、汽循环冲洗瓶内壁,喷淋装置洗瓶子外壁,从而达到清洗效果。
转笼转一周后由拨盘推动的西林瓶将清洗好的瓶子呈散装形式自动进入隧道灭菌烘箱之中,并设有超声波元件损坏时由报警装置报警。
在网带式隧遭灭菌烘箱智能系统的监控下,瓶子随网带的输送依次进入隧道灭菌箱的预热区,高温灭菌区(温度≥350℃,灭菌时间≥5min)和低温冷却区。
年产2亿支2ml水针剂生产车间工艺设计

制药工程课程设计设计题目:年产2亿支2ml水针剂生产车间工艺设计专业班级:姓名:学号:小组成员:指导老师:设计时间:摘要本文是对年产2亿支2ml,200mg利巴韦林水针剂生产车间工艺设计的详细说明。
一方面,根据任务要求,对工艺流程进行了说明,并绘制了工艺管道流程图,完成了物料衡算和设备选型。
另一方面,按照GMP的要求,设计工艺平面布置,并绘制了平面压差分布图和洗瓶工序的管道布置图。
本设计严格遵守GMP规定,符合安全、环保、技术经济等方面的要求。
关键词:水针剂平面布置联动机组洁净区GMP目录一、工艺概述水针剂的生产步骤主要包括原辅料的准备、配制、灌封、灭菌、质检、包装等环节。
本设计的原料是药用利巴韦林(2ml,200mg),辅料是注射用水。
选择中性玻璃安瓿作为注射液的容器。
水针剂的洁净区划分:注射用水的制备、理瓶、检漏灭菌、灯检、印字包装在一般生产区;原料的配制、粗滤、安瓿的粗洗、精洗在C级洁净区;原料液的精滤、安瓿干燥灭菌、冷却、灌装、封口位于B级洁净区。
(一)工艺流程框图1.1 工艺流程框图(二)工艺用水制备水针剂生产需要大量的纯化水及注射用水。
本工艺中以自来水为原水,首先进行预处理,包括机械过滤、活性碳过滤、保安过滤,然后经过二级渗透处理得到纯化水,纯化水再经紫外线杀菌、微孔过滤后至用水点。
纯化水经过多效蒸馏操作得到蒸馏水,蒸馏水保温循环贮存,蒸馏水经过0.45μm微孔膜过滤即可送至注射用水的用水点。
1、纯化水制备目前在制药企业生产中,纯化水的制备一般有以下四种工艺流程:1)原水→ 预处理→ 阳离子交换→ 阴离子交换→ 混床→ 纯化水2)原水→ 预处理→ 电渗析→ 阳离子交换→ 阴离子交换→ 混床→ 纯化水3)原水→ 预处理→ 一级高压泵→ 一级反渗透→ 二级高压泵→二级反渗透→ 纯化水4)原水→ 预处理→高压泵→反渗透→ 一级混床→ 二级混床→纯化水其中全离子交换用于符合饮用水标准的原水,常用于原水含盐量<500 mg/L;电渗析+离子交换常用于原水含盐量>500 mg/L,使用电渗析,可减少树脂频繁再生,减少离子交换负担,使树脂制水周期延长,减少再生时酸、碱用量和排污量;反渗透+离子交换以反渗透直接作为二级混床的前处理,此时为了减轻混床再生时碱液用量,需在混床前设置脱气塔以脱去CO2。
注射剂的制备
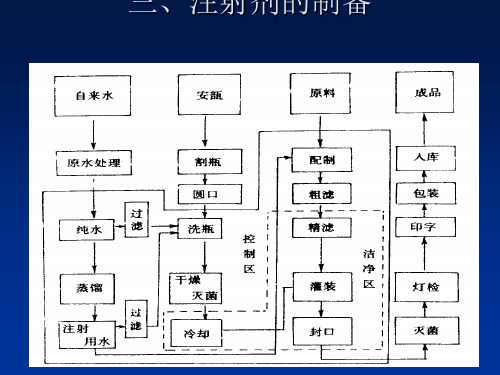
一、注射剂车间的设计与生产管理
注射剂生产车间按生产工艺及产品质量要求可分一般 生产区、控制区、洁净区。
一般生产区指无空气洁净度要求的生产或辅助房间。 控制区指对空气洁净度或菌落数有一定要求的生产或
辅助房间,一般定为>10万级或10万级。 洁净区指有较高洁净度或菌落数要求的生产房间。一
(二) 安瓿的质量要求与注射剂稳定性的关系
若玻璃容器含有过多的游离碱将增高注 射的pH值。
玻璃容器若不耐水腐蚀,则在盛装注射 用水有时产生“脱片”现象。
不耐碱或不耐侵蚀的容器,在装入磺胺 嘧啶钠等碱性较大的或枸椽酸钠、碳酸 氢钠、乳酸钠、氯化钙等钙钠盐类的注 射液时往往灭菌后或长期贮存时发生 “小白点”、“脱片”甚至产生混浊现 象。
注射剂从配制到灭菌,必须在规定时间内完成 (一般12小时)。
凡能耐热的产品,宜采用115℃30分钟灭菌。
(二) 检漏
检漏用一种灭菌检漏两用灭菌器。灭菌后,稍开 锅门,从进水管,放进冷水淋洗安瓿使温度降低, 然后关紧锅门并抽气,灭菌器内压力逐渐降低。
如有漏气安瓿,则安瓿内空气也被抽出。当真空 度 达 到 85.3 ~ 90.6kPa(640 ~ 680mmHg) 后 , 停 止抽气。
我国对澄明度检查的要求:取供试品,在 黑色背景、20W照明荧光灯光源下,用目 检视,应符合卫生部关于澄明度检查判断 标准的规定。
国内生产的BY-1型澄明度检测仪可以用 于澄明度检查,并可调节照度,使用方便。
(二)热原检查
热原检查目前各国药典法定的方法仍为 家兔法。选用家兔作试验动物,是因为 家兔对热原的反应和人是相同的。
如耐热性能差则在熔封或加热灭菌后往 往发生爆裂、漏气等现象。
玻璃安瓿的清洁度不良,特别是粘着于 瓶壁的麻点或玻屑等不易洗净,而在灌 封及热压灭菌后往往脱落而成废品。
注射液生产环境要求

注射液生产环境要求
注射液生产环境的要求比较严格,需要遵守药品生产质量管理规范(GMP)。
以下是一些重要的环境要求:
1. 车间环境需要经过专业消毒,洁净级别高的区域必须要防止交叉污染。
不同级别的洁净区域应设立不同的区域标识。
2. 温度和湿度也需要严格把控。
灭菌器和清洁区内的温度应控制在18℃~24℃,湿度控制在50%~60%。
3. 注射剂生产过程中,空气中的尘埃颗粒过大会引发感染,因此洁净区的尘埃粒子、菌落数、霉菌数量等应符合相关规定。
4. 注射剂生产还需要严格控制噪声、照明、工艺设备及工装系统等,以确保生产环境的洁净度。
总的来说,为了确保注射液的质量和安全,制药企业必须采取一系列严格的措施来确保生产环境符合相关的规定和标准。
磺胺间甲氧嘧啶钠注射液生产工艺规程-大容量

磺胺间甲氧嘧啶钠注射液生产工艺规程(大容量)目录1 产品概述2 处方和依据3 工艺流程图4 制剂工艺过程及工艺条件5 原辅材料质量标准和检查方法6 中间产品质量标准和检查方法7 成品质量标准和检查方法8 包装规格、包装材料质量标准9 说明书、产品文字说明和标志10 工艺要求11 设备一览表和主要设备生产能力12 技术安全与劳动保护13 劳动组织14 技术经济指标计算15 原辅料消耗定额16 包装材料消耗定额17 动力消耗定额18 综合利用与环境保护目的:制定本标准的目的是规范磺胺间甲氧嘧啶钠注射液生产过程,对一定数量的成品所需的起始原辅料和包装材料,以及工艺、加工说明、技术参数、注意事项等进一步标准化。
适用范围:适用于磺胺间甲氧嘧啶钠注射液生产全过程。
责任人:质量部部长、生产部部长、车间主任。
内容:1产品概述:本品为磺胺间甲氧嘧啶钠的灭菌水溶液。
含磺胺间甲氧嘧啶钠(C11H11N4NaO3S)应为标示量的96.0%~104.0%1.1产品特点:1.1.1性状:本品为无色至微黄色的澄明液体。
1.1.2作用与用途:磺胺类药。
用于各种敏感菌引起的呼吸道、消化道、泌尿道感染及球虫病、猪弓形虫病等。
局部灌注可治疗乳腺炎和子宫内膜炎。
1.1.3用法用量:静脉注射一次量每1Kg体重家畜0.5ml,一日1~2次,连用2-3日。
1.1.4规格:100ml:10g(磺胺间甲氧嘧啶钠)1.1.5贮藏:遮光、密闭保存。
1.1.6停药期:28日1.1.7有效期:二年1.1.8批准文号:2 处方和依据:2.1处方:(1000ml)磺胺间甲氧嘧啶钠100g 硫代硫酸钠 1 g注射用水 至1000ml10000级区100000级区4 制剂工艺过程及工艺条件: 4.1总述:4.1.1按生产指令单领取磺胺间甲氧嘧啶钠原料,在浓配灌中加入计算量70%的注射用水, 再加入计算量的硫代硫酸钠搅拌使溶解;然后加磺胺间甲氧嘧啶钠原料搅拌至完全溶解,粗滤至稀配灌中,加注射用水近全量,调节PH在规定范围内(9.7-10.8),补加注射用水至足量;用孔径为0.45um、0.22um的过滤器(使用前后经过完整性测试合格)精滤,检查澄明度、含量合格后,将药液输送到至灌封岗位,灌装压盖,100℃30分钟灭菌,灯检、贴签包装成规定规格即可。
注射剂车间的设计严格按GMP规定设计

注射剂车间的设计严格按GMP规定设计一. 注射剂车间的设计要求(一)位置选择(二)房间布局制备注射剂至少要备有下列各室,即射用水制备室、洗涤配滤室、灌封室、灭菌室、质检室和包装室等。
房间的布局要考虑生产艺的衔接,必须避免重复往返并防止原材料、半成品交叉污染与混杂,人物要分流。
人的走应有更衣室和卫生设施,保证进入室内人员的清洁卫生;物的走向可设计机械传送线,也可人工传送,但室间应设计有传递橱,并应该有足够的缓冲间。
注射剂生产车间按生产工艺及产品质量要求可分一般生产区、控制区、洁净区。
一般生产区指无空气洁净度要求的生产或辅助房间。
控制区指对空气洁净度或菌落数有一定要求的生产或辅助房间,一般定为>10万级或10万级。
洁净区指有较高洁净度或菌落数要求的生产房间,一般定为l万级或100级。
控制要求温度18℃~28℃,相对湿度50%~60%。
洁净区要求温度18℃一24℃,,相对湿度45%~65%。
(三)内部结构二、无菌操作室的空调系统无菌操作室的空调系统可对进入室内的空气给予过滤、去湿、加热等处理,使之成为无尘、无菌、清洁新鲜的空气,且使室内保持适宜的温度和湿度。
为提高洁净度可采用层流洁净空气技术。
三、空气的净化空气中大量生物和非生物微粒,设法去除这些微粒使空气符合规定的过程称为空气净化…空气净化是保证生产环境洁净和无菌的主要手段洁净室的标准。
(一)洁净室的标准净化空气中所残留的粒大小及数量是洁净度划分的依据。
各项要求见表4-4。
(二)层流洁净空气技术层流是指空气流线平行,具有一定的均匀的断面速度,气流水平的称水平层流,气流垂直向下的称垂直层流。
1.层流净化的优点微粒流体连续稳定地向个方向运动,一切粒子保持在层流运动中子粒子不易相碰而聚结,沉降。
2.水平层流净室的构造与工作原理3.垂直层流洁净室4. 层流洁净工作台层流净化室和净化台我国均有定型产品’,其净化效果均可达到lOO级洁净度的要求。
5. 层流净化技术在注射剂生产中的应用近年来在注射剂生产中,层流净化技术已广泛应用,按照国家卫生部GMP规定,100级洁净标准适用于生产无菌而又不能在最后容器中进行灭菌的药品的配液(指灌封前不需无菌滤过)及灌封;能在最后容器中灭菌的大体积(≥ 50m1)注射用药品的滤过、灌封;粉针剂的分装、压塞;无菌制剂、粉针剂原料药的精制烘干、分装。
注射剂生产车间工程设计

打针剂临盆车间工程设计最终灭菌小容量打针剂车间GMP设计(1)最终灭菌小容量打针剂临盆进程包含原辅料的预备.配制.灌封.灭菌.质检.包装等步调,按工艺装备的不合型式可分为单机临盆工艺和联念头组临盆工艺两种,其流程及情况区域划分(见图 A B).关于水针各单机装备和联念头组装备的具体内容详见前.(2)按照GMP的划定最终灭菌小容量打针剂临盆情况分为三个区域:一般临盆区.10万级干净区.1万级干净区.一般临盆区包含安瓿外清处理.半成品的灭菌检漏.异物检讨.印包等;10万级干净区包含物料称量.浓配.质检.安瓿的洗烘.工作服的洗涤等;1万级干净区包含稀配.灌封,且灌封机自带局部100级层流.干净级别高的区域相对于干净级别低的区域要保持5~10Pa的正压差.如工艺无特别请求,一般干净区温度为18~26℃,相对湿度为45%~65%.各工序需装配紫外线灯.(3)车间设计要贯彻人.物流离开的原则.人员在进入各个级此外临盆车间时,要先更衣,不合级此外临盆区需有响应级此外更衣净化措施.临盆区要严厉按照临盆工艺流程安插,各个级别雷同的临盆区相对分散,干净级别不合的房间互相接洽中设立传递窗或缓冲间,使物料传递路线尽量短捷.顺畅.物流路线的一条线是原辅料,物料经由外清处理,进行浓配.稀配;另一条线是安瓿瓶,安瓿经由外清处理后,进入洗灌封联动线清洗.烘干.两条线汇聚于灌封工序.灌封后的安瓿再经由灭菌.检漏.擦瓶.异物检讨,最后外包成全部临盆进程.具体进出水针车间的人流.物流路线(见图)所示.(4)帮助用房的合理设置是制剂车间GMP没计的一个重要环节.厂房内设置与临盆范围相顺应的原.辅材料,半成品.成品存放区域,且尽可能接近与其接洽的临盆区域,削减运输进程中的混淆与污染.存放区域内应安插待验区.及格品区和不及格品区;贮料称量室,并且要有利于包含空调风管在内的公用管线的安插.(5)水针临盆车间内地面一般做耐清洗的环氧自流坪地面,隔墙采取轻质彩钢板,墙与墙.墙与地面.墙与吊顶之间接缝处采取圆弧角处理,不得留有逝世角.(6)水针临盆车间须要排热.排湿房间有浓配间.稀配间.对象清洗间.灭菌间.洗瓶间.洁具室等,灭菌检漏需斟酌通风.公用工程包含给排水.供气.供热.强弱电.制冷通风.采暖等专业设汁应相符GMP原则.车间设计举例图车间设计举例图是水针临盆联念头组工艺车间安插图采取浓配加稀配的配料方法,具体安插(见图).水针单机临盆工艺车间安插图(见图),整体计划为一拖二型,即共用瓶子的粗.精洗工序,再分成两套灌封体系,合适多品种小批量临盆.配料采取一次配制的方法.具体安插如图7.2—3所示.最终灭菌大容量打针剂(大输液)车间相干链结:大输液设置装备摆设体系工艺流程图大输液临盆车间设计一般性要点:★★★最终灭菌大容量打针剂工艺流程★★★(1)控制大输液的临盆工艺是车间设计的症结,盛装输液的容器有玻璃瓶.聚乙烯塑料瓶.复合膜等,包装容器不合其临盆工艺也有差别,复合膜.玻璃瓶.塑料容器的输液工艺流程及情况区域划分分离(见图 A B C).无论何种包装容器其临盆进程一般包含原辅料的预备.浓配.稀配.包材处理(瓶外洗.粗洗.精洗等).灌封.灭菌.灯检.包装等工序.(2)设计时要分区明白,按照GMP划定,由大输液临盆工艺流程及情况区域划分示意图可知,大输液临盆分为一般临盆区.10万级干净区.1万级及局部100级干净区.一般临盆区包含瓶外洗.粒子处理.灭菌.灯检.包装等;10万级干净区包含原辅料称配.浓配.瓶粗洗.轧盖等;1万级干净区包含瓶精洗.稀配.灌封,个中瓶精洗后到灌封工序的吐露部分需百级层流呵护.临盆相接洽的功效区要互相接近,以达到物流顺畅.管线短捷,如物料流向:原辅料称配一浓配一稀配一灌封工序尽量接近.车间设计时合理安插人.物流,要尽量防止人.物流的交叉.人流路线包含人员经由不合的更衣进入一般临盆区.10万级干净区.l万级干净区,进出车间的物流一般有以下几条:瓶子或粒子的进入.原辅料的进入.外包材的进入以及成品的出口.进出输液车间的人流.物流路线(见图)所示.(3)闇练控制工艺临盆装备是设计好输液车间的症结,输液包装容器不合其临盆工艺不合,导致其临盆装备亦不合.即使是统一包装容器的输液,其临盆线也有不合的选择,如玻璃瓶装输液的洗瓶工序有分粗洗.精洗的滚筒式洗瓶机和集粗.精洗于一体的箱式洗瓶机.工艺装备的差别,车间安插必定不合,今朝的输液临盆均采取联动线,为我国较为经常应用的玻璃瓶输液临盆线.(4)合理安插好帮助用房.帮助用房是大输液车间临盆质量包管和GMP认证的重要内容,帮助用房的安插是否得当是车间设计成败的症结.一般大输液临盆车间的帮助用房包含万级对象清洗存放间.l0万级对象清洗存放间.化验室.洗瓶水配制间.不及格晶存放间.洁具室等.大输液车间一般性技巧请求:(1)大输液车间控制区包含l0万级干净区.1万级干净区,1万级情况下的局部100级层流,控制区温度为18~26℃,相对湿度为45%~65%.各工序需装配紫外线灯.(2)干净临盆区一般高度为2.7m阁下较为合适,上部吊顶内安插包含风管在内的各类管线加上斟酌维修须要,吊顶内部高度需为2.5m.(3)大输液临盆车间内地面一般做耐清洗的环氧自流坪地面,隔墙采取轻质彩钢板与墙.墙与地面.墙与吊顶之间接缝处采取圆弧角处理,不得留有逝世角.(4)干净临盆区需用干净地漏,百级区不得设置地漏.(5)浓配间.稀配间.对象清洗间.灭菌间.洗瓶间.洁具室需排热.排湿.在塑料颗粒制瓶和制盖的进程中均产生较多热量,除采取低温水体系冷却外,空调体系应斟酌响应的负荷,塑料颗粒的上料体系必须斟酌除尘措施.洗瓶水配制间要斟酌防腐与通风.(6)纯化水和打针用水管道设计时请求65℃回路轮回,管道装配坡度一般为0.1%一0.3%(1‰一3‰),不锈钢材质.支管盲段长度不该超出轮回主管管径的6倍.(7)不合情况区域要保持5~lOPa的压差,1万级干净区对10万级干净区保持5~lOPa的正压,10万级干净区对一般临盆区保持5~lOPa的正压.车间设计举例玻璃瓶装大输液车间安插图(见图),选用粗精洗合一的箱式洗瓶机,具体安插见图.塑料瓶装大输液车间(见图).选用塑料瓶二步法成型工艺,具体安插见图.无菌分装粉针剂车间GMP设计针剂车间设计一般性要点:(1)粉针剂的临盆工序包含:原辅料的擦洗消毒.西林瓶粗洗.精洗.灭菌湿润.胶塞处理及灭菌.铝盖洗涤及灭菌.分装.轧盖.灯检.包装等步调,按GMP划定其临盆Z域空气干净度级别分为100级.1万级和10万级.个中无菌分装.西林瓶出地道烘箱.胶塞出灭菌柜及其存放等工序须要局部100级层流呵护,原辅料的擦洗消毒.瓶塞精洗.瓶塞湿润灭菌为1万级,瓶塞粗洗.轧盖为10万级情况.其工艺流程图及情况区域划分见图7(2)车间设计要做到人.物流离开的原则,按照工艺流向及临盆工序的相干性,有机地将不合干净请求的功效区安插在一路,使物料流短捷.顺畅.粉针剂车间的物流根本上有以下几种:原辅料.西林瓶.胶塞.铝盖.外包材及成品出车间.进入车间的人员必须经由不合程度的更衣分离进入1万级和10万级干净区.进出粉针剂车间人.物流路线(见图)所示.(3)车间设置净化空折衷舒适性空调体系能有用控制温.湿度;并能确保造就室的温.湿度请求;若无特别工艺请求,控制区温度为18~26℃,相对湿度为45%~65%.各工序需装配紫外线灯灭菌.(4)车间内须要排热.排湿的工序一般有洗瓶区地道烘箱灭菌间.洗胶塞铝盖间.胶塞灭菌间.对象清洗间.洁具室等.(5)级别不合干净区之间保持5一lOPa的正压差每个房间应有测压装配.假如是临盆青霉素或其他高致敏性药品,分装室应保持相对负压.粉针剂车间设计举例无菌分装粉针剂车间工艺安插图(见图).该工艺选用联动线临盆,瓶子的灭菌装备为远红外地道烘箱,瓶子出地道烘箱后即受到局部100级的层流呵护.胶塞处理选用胶塞清洗灭菌一体化装备,出胶塞及胶塞的存放设置100级层流呵护.铝盖的处理另设一套人流畅道,以防止人.物流之间有大的交叉.具体安插如图所示干粉针剂车间GMP设计冻干粉针剂车间设计一般性要点:(1)冻于粉针剂的临盆工序包含:洗瓶及湿润灭菌.胶塞处理及灭菌.铝盖洗涤及灭菌.分装加半塞.冻于.轧盖.包装等.按GMP划定其临盆区域空气干净度级别分为100级.1万级和10万级.个中料液的无菌过滤.分装加半塞.冻干.净瓶塞存放为100级或1万级情况下的局部100级即为无菌功课区,配料.瓶塞精洗.瓶塞湿润灭菌为1万级,瓶塞粗洗.轧盖为10万级情况.其工艺流程图及情况区域划分见图4—u.(2)车间设汁力图计划合理,遵守人.物流离开的原则,不交叉返流.进入车间的人员必须经由不合程度的净化程序分离进入100级.1万级和l0万级干净区.进入100级区的人员必须穿戴无菌工作服,洗涤灭菌后的无菌工作服在100级层流呵护下整顿.无菌功课区的气压要高于其也区域,应尽量把无菌功课区安插在车间的中间区域,如许有利于气压从较高的房间流向较低的房间.(3)帮助用房的安插要合理,干净对象间.容器具清洗间宜设在无菌功课区外,非无菌工艺功课的岗亭不克不及安插在无菌功课区内.物料或其他物品进入无菌功课区时,应没置供物料.物品消毒或灭菌用的灭菌室或灭菌装备.洗涤后的容器具应经由消毒或灭菌处理方能进入无菌功课区.(4)车间设置净化空折衷舒适性空调体系可有用控制温.湿度;并能确保造就室的温.湿度请求;控制区温度为18~26℃,相对湿度为45%~65%.各工序需装配紫外线灯.(5)如有活菌造就如生物疫苗成品冻干车间,则请求将干净区严厉区分为活菌区与逝世菌区,并控制.处理好活菌区的空气排放及带有活菌的污水.(6)按照GMP的规矩请求安插纯水及打针用水的管道.车间设计举例生物疫苗成品冻干车间安插图(见图),空调体系活菌隔离措施依据室内干净级别和工作区域内是否与活菌接触,冻于临盆车间设置三套空调体系,具体介绍如下.(1)10万级净化空调体系.它重要解决二更间.造就基的配制.造就基的灭菌以及无菌衣服的洗涤,体系回风,与活菌区保持5~10Pa的正压.(2)一万级净化空调体系.该区域为活菌区,它重要解决接种.菌种造就.菌体收集.高压灭活.瓶塞的洗涤灭菌.对象清洗存放.三更.缓冲的空调净化.该区域保持相对负压,空气全新风运行,排风体系的空气需经高效过滤器过滤,以防止活菌外逸.(3)一万级净化空调体系和百级净化空调体系.重要解决净瓶塞的存放.配液.灌装加半塞.冻干.压塞和化验.该区域为逝世菌区,体系回风.除空调体系外,该车间在建筑密封性.纯化水.打针用水的管道安插.污物排放等方面的设计上也要有防止交叉污染的措施.该车间具体安插见图.。
年产1亿支2ml水针剂生产车间工艺设计毕业论文
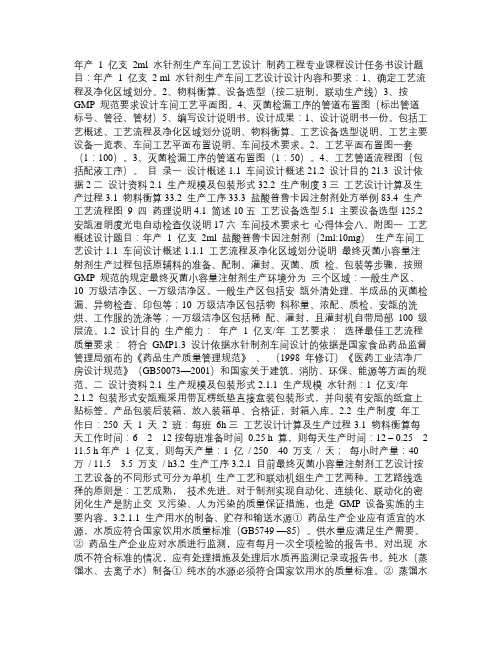
年产1 亿支2ml 水针剂生产车间工艺设计制药工程专业课程设计任务书设计题目:年产1 亿支2 ml 水针剂生产车间工艺设计设计内容和要求:1、确定工艺流程及净化区域划分。
2、物料衡算、设备选型(按二班制。
联动生产线)3、按GMP 规范要求设计车间工艺平面图。
4、灭菌检漏工序的管道布置图(标出管道标号、管径、管材)5、编写设计说明书。
设计成果:1、设计说明书一份。
包括工艺概述、工艺流程及净化区域划分说明、物料衡算、工艺设备选型说明、工艺主要设备一览表、车间工艺平面布置说明、车间技术要求。
2、工艺平面布置图一套(1:100)。
3、灭菌检漏工序的管道布置图(1:50)。
4、工艺管道流程图(包括配液工序)。
目录一设计概述1.1 车间设计概述21.2 设计目的21.3 设计依据2二设计资料2.1 生产规模及包装形式32.2 生产制度3三工艺设计计算及生产过程3.1 物料衡算33.2 生产工序33.3 盐酸普鲁卡因注射剂处方举例83.4 生产工艺流程图9 四药理说明4.1 简述10五工艺设备选型5.1 主要设备选型125.2 安瓿澄明度光电自动检查仪说明17六车间技术要求七心得体会八、附图一工艺概述设计题目:年产1 亿支2ml 盐酸普鲁卡因注射剂(2ml:10mg)生产车间工艺设计1.1 车间设计概述1.1.1 工艺流程及净化区域划分说明最终灭菌小容量注射剂生产过程包括原辅料的准备、配制、灌封、灭菌、质检、包装等步骤,按照GMP 规范的规定最终灭菌小容量注射剂生产环境分为三个区域:一般生产区、10 万级洁净区、一万级洁净区。
一般生产区包括安瓿外清处理、半成品的灭菌检漏、异物检查、印包等;10 万级洁净区包括物料称量、浓配、质检、安瓿的洗烘、工作服的洗涤等;一万级洁净区包括稀配、灌封,且灌封机自带局部100 级层流。
1.2 设计目的生产能力:年产1 亿支/年工艺要求:选择最佳工艺流程质量要求:符合GMP1.3 设计依据水针制剂车间设计的依据是国家食品药品监督管理局颁布的《药品生产质量管理规范》、(1998 年修订)《医药工业洁净厂房设计规范》(GB50073—2001)和国家关于建筑、消防、环保、能源等方面的规范。
注射剂车间纯化水系统URS

文件编号:URS-GC-001-A 注射剂车间纯化水系统用户需求江苏复旦复华药业有限公司目录1.审批 (2)2.概述 (3)3.标准 (3)4.生产和安全要求 (4)5.工艺技术与GMP要求 (5)6.约定 (15)7.培训及服务 (16)8.缩略语 (20)变更说明上海复旦复华药业有限公司由于现有的产能制约了企业的快速发展,加上现址地方已有新的规划,因此为了扩大再生产,拟在江苏海门经济技术开发区投资建设一座新厂房。
新基地生产以领先的高新技术,国内著名的品牌产品,规模化、系列化、多样化为发展方向,生产多样化的产品以及为未来进行战略储备,建成为华东地区乃至全国先进的医药生产企业。
其中拟建设的冻干车间在注射剂车间楼的第二层。
该文件旨在从项目和系统的角度阐述用户的需求,主要包括相关法规符合度和用户的具体需求,这份文件是构建起项目和系统的文件体系的基础,同时也是系统设计和验证的可接受标准的依据。
1)本用户需求标准(URS)是为了规定制药用水设备的技术要求,为该系统的招标提供技术依据,并作为后续验证工作的基础。
2)本项目设备供货范围包含纯化水机,并包含与设备配套的洁净管道工程及其相关各项文件、自控、验证服务。
3)本文件作为承包商编制工程施工、调试和服务技术条款的基础,承包商应根据本文件需求逐条做出响应,提供其技术要求是否满足本文件需求标准,如有偏差和不符合项应列出,并详细说明或提供解决方案。
4)乙方应有已通过FDA、欧盟GMP或WHO GMP认证的工程施工业绩。
5)甲方的建议、检查和确认并不能减轻乙方对其工作内容所应负的所有责任。
6)乙方必须提供完善的二次设计方案。
8)乙方必须有完善的验证服务团队和售后服务机构,并提供验证能力证明。
8)满足新版GMP验证需求,供应商需提供完善的文件系统。
同时,需展示已施工案例项目的文件编写情况。
本URS适用于新建注射剂车间项目的纯化水系统设备,包括设计、制造、测试、运输以及安装完成后的调试、培训。
小容量注射剂生产工艺

小容量打针剂出产工艺规程通那么目录1.小容量打针剂出产工艺流程图、小容量打针剂车间概况〔附图〕2.需要验证的关键工序及工艺验证〔列表〕3.操作过程及工艺条件4.技术安然、工艺卫生及劳动庇护5.物料平衡及技经指标6.设备一览表7.岗位定员8.附件目录〔岗位操作、清洁规程〕1.可灭菌小容量打针剂的出产流程图100000级区域小容量打针剂车间概况〔附图〕说明:由质监科按洁净厂房监控制度SMP-ZL-014对洁净区进行监控,由工程设备科负责维修,车间应按照实际使用情况提出相应的建议,包管洁净厂房在使用中符合GMP的规定。
2.需要验证的关键工序及工艺验证〔列表〕说明:每年需按验证办理制度SMP-ZL-012对上述关键工序及工艺进行验证〔再验证或回忆性验证〕。
假设系统、设备设施发生变动那么必需进行相应的验证。
验证由厂验证小组负责。
车间应按照情况及时提出相应的申请。
3.操作过程及工艺条件3.1 工艺用水:3.1.1 操作过程:3.1.1.1 原水为符合国家饮用水的尺度自来水。
3.1.1.2 纯化水由原水经石英砂过滤→精滤〔PE棒〕→阴床→阳床→混床→紫外灯灭菌→进入贮罐。
3.1.1.3 打针用水由纯化水经多效蒸馏水机颠末蒸馏而得。
3.1.2 工艺条件:3.1.2.1 原水应符合国家饮用水尺度。
3.1.2.2 原水的预处置的进水流量应≤3m3/h。
3.1.2.3 温床的流量为3m3/h。
3.1.2~pa~MPa之间。
3.1.2.5 纯化水的电导率应≤2us/cm,离子查抄符合«中国药典»2005版二部“纯化水〞的尺度。
打针用水的电导率≤2us/cm,离子查抄符合«中国药典»2005版二部“打针用水〞的尺度。
3.2 理瓶工序3 本公司可灭菌小容量打针剂所选用直接接触药品的容器为低硼硅玻璃安瓿,执行国家药品监督办理局国家药用包装容器〔材料〕尺度〔试行〕YBB00332002,以下均可简称安瓿。
注射剂口服固体制剂生产车间工程设计
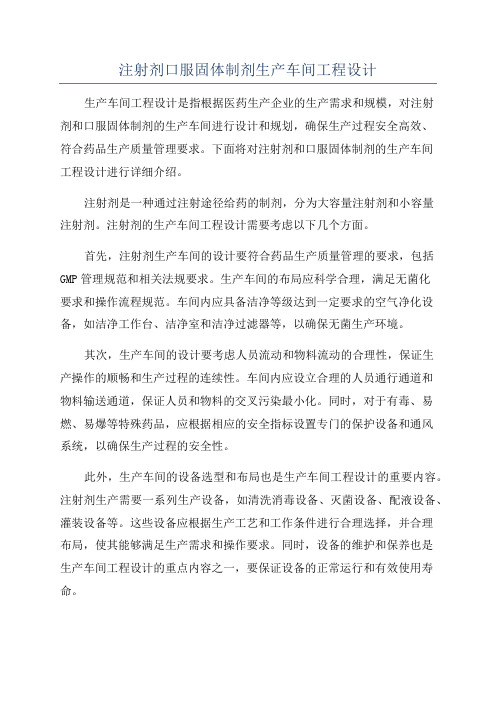
注射剂口服固体制剂生产车间工程设计生产车间工程设计是指根据医药生产企业的生产需求和规模,对注射剂和口服固体制剂的生产车间进行设计和规划,确保生产过程安全高效、符合药品生产质量管理要求。
下面将对注射剂和口服固体制剂的生产车间工程设计进行详细介绍。
注射剂是一种通过注射途径给药的制剂,分为大容量注射剂和小容量注射剂。
注射剂的生产车间工程设计需要考虑以下几个方面。
首先,注射剂生产车间的设计要符合药品生产质量管理的要求,包括GMP管理规范和相关法规要求。
生产车间的布局应科学合理,满足无菌化要求和操作流程规范。
车间内应具备洁净等级达到一定要求的空气净化设备,如洁净工作台、洁净室和洁净过滤器等,以确保无菌生产环境。
其次,生产车间的设计要考虑人员流动和物料流动的合理性,保证生产操作的顺畅和生产过程的连续性。
车间内应设立合理的人员通行通道和物料输送通道,保证人员和物料的交叉污染最小化。
同时,对于有毒、易燃、易爆等特殊药品,应根据相应的安全指标设置专门的保护设备和通风系统,以确保生产过程的安全性。
此外,生产车间的设备选型和布局也是生产车间工程设计的重要内容。
注射剂生产需要一系列生产设备,如清洗消毒设备、灭菌设备、配液设备、灌装设备等。
这些设备应根据生产工艺和工作条件进行合理选择,并合理布局,使其能够满足生产需求和操作要求。
同时,设备的维护和保养也是生产车间工程设计的重点内容之一,要保证设备的正常运行和有效使用寿命。
对于口服固体制剂的生产车间工程设计也有类似的要求。
口服固体制剂生产车间不需要无菌条件,但同样需要考虑GMP管理规范和相关法规要求。
车间内应设置洁净工作台、清洁区和污染区,以确保制剂过程的卫生和安全。
对于涉及到粉剂的制剂,应设置粉尘防护措施,减少粉尘的扩散和污染。
此外,生产车间的环境温度、湿度和空气流通情况也需要进行合理设计和控制。
环境温度和湿度对于药品生产有一定的影响,应根据生产工艺和药品特性进行相应的温湿度控制。
无菌冻干粉针车间工艺设计

无菌冻干粉针车间工艺设计摘要:外用重组人酸性成纤维细胞生长因子(以下简称rhAFGF),该产品是将人酸性成纤维细胞生长因子(rhAFGF)重组质粒转化大肠杆菌,使其高效表达人酸性成纤维细胞生长因子,经高度纯化制成的冻干制剂,含适宜稳定剂,不含防腐剂和抗生素。
主要用于治疗烧伤、创伤、慢性难愈创面等疾病,使损伤组织修复和再生。
该产品的特殊性在于成品包含一支冻干品、一支稀释剂均为无菌制剂,其冻干品属于冻干粉针注射剂,稀释剂属于水针注射剂。
故其对厂房、设备设施具有一定的特殊要求。
基于此本文以此为例,对车间的标准化设计进行阐述,以期为更多类似的车间设计提供助益。
关键词:无菌制剂;冻干粉针剂;注射剂;车间工艺设计该产品的生产车间为无菌制剂车间,冻干品的生产采用真空冷冻干燥技术,该技术可以有效满足生物制品生产时对于温度的要求,原料、辅料经过配制后经灌装、半压塞进入冻干机冻干、压塞后出箱轧盖。
稀释剂属于水针注射剂,即药液灌装后不进行冻干,全压塞后进行轧盖。
将该产品的冻干品及稀释剂在同一车间生产为企业节约了硬件的投入成本及场地的空间成本,这就对厂房的设计,设备的选型提出了更高的要求。
1、生产流程概述冻干品:按处方的比例将甘露醇、磷酸二氢钠、磷酸氢二钠投入1号罐,搅拌溶解,定容。
检测结果合格后将该罐中的药液适量,用压缩空气转移至2号罐,按照处方投入rhAFGF原液和人血白蛋白,定容成半成品。
然后经2道0.22µm PVDF过滤后,在B级背景下的A级层流下灌装,灌装后经半加塞,由自动进出料进入冷冻干燥机冻干,冻干后全压塞,推出冷冻干燥箱进入轧盖区铝盖轧封,在一般生产区域,目检后,贴标。
稀释剂:按处方的比例将磷酸二氢钠、磷酸氢二钠投入3号罐溶解定容,经2道0.22µm PVDF过滤后,在B级背景下的A级层流下灌装,灌装后经全加塞,由自动进出料进入轧盖区铝盖轧封,在一般生产区域,目检后,贴标。
从以上生产流程可以看出,稀释剂与冻干品的生产流程区别在于冻干品灌装时半加塞后进冻干机,稀释剂灌装时全加塞后不进冻干机,车间的布局设计参见图一(由于篇幅限制,本文只截取了关键的灌装区域),该车间即达到即生产冻干品有生产稀释剂的要求。
注射剂生产工艺流程与厂方设计布局

2.2注射剂生产工艺流程简介图1:注射剂生产流程图由图1,注射剂生产流程图可以看出:注射剂生产流程[4]主要包含以下工序:原料领料工序,要求领料人员进行原料品种、批号的复核。
原料经过拆外包工序,由一般区经传递窗消毒和灭菌后,传递至十万级暂存称量间存放。
称量工序,要求操作人员准确对衡器进行校验,进行称量时要求双人二次复核品种、批号和质量并做好标识。
配液工序要求操作人员应完全遵守并按照生产指令和生产工艺卡片执行配液的各项操作,依此保证生产出合格的中间品(半成品)。
半成品经取样交质保部检测,检测标准依据《兽药典》[5]半成品检验检测合格后,药液被送入灌装工序。
内包材领料工序,要求领料人员复核瓶子外观和规格。
经过拆外包后,由一般区经传递窗传至十万级洗瓶间,由洗瓶机进行洗瓶。
西林瓶经超声清洗后进行烘干灭菌工序,按照生产工艺要求和实际生产需要进行洗瓶,根据生产要求,合理控制洗瓶数量,待灭菌冷凉瓶后,由十万级经传递窗转移至万级灌装间进入灌封工序。
灌封工序为灌装和加塞操作,其主要要求是最大限度保证装量均匀度。
灌装加塞后由传送带送至十万级扎盖间,进行扎盖工序后,进行最终灭菌工序,按照每种产品的灭菌工艺要求灭菌。
灯检工序要求按生产操作规程进行灯检,应明确标识待灯检品的品种、批号,灯检后的合格与不合格品,杜绝混批事故出现。
灯检合格后,进行贴签。
外包装材料领料工序,其主要要求准确复核标签规格和批准文号。
依据生产指令进行打印标签和合格证,经复核无误后进行贴签。
贴签工序要求按统一整齐美观标准进行贴签。
包装后进行装箱,装箱要求产品按顺序摆放并放置合格证。
包装完毕后进行入库。
3.生产车间介绍3.1车间平面布局图2:注射剂车间平面布局图由图2,注射剂车间平面布局图可以看出:注射剂车间包含非洁净区的普通区和洁净区的十万级区和万级区[6]。
非洁净区(普通区)与洁净区的十万级区间人流通道设有缓冲间,物流通道设有传递窗,洁净区内不同洁净级别间,十万级区与万级区间同样设有缓冲间和传递窗。
开题报告-年产8千万支克矽平注射剂(规格80mg-2ml)车间工艺设计

重点:生产克矽平注射剂产品的合理生产工艺路线的选择、设备选型、物料 衡算。
难点:1、选择工艺路线(选择工艺路线,关系到后面工艺流程的选择和车 间平面布置) 2、物料衡算(要查阅相关的数据,引用物料的物理和化学参数)。 3、设备选型(设备的尺寸大小关系到设备的摆放和车间的布置)。
参考设计材料,包含项目源代码,屏幕录像指导、项目运行截图、项目设计说明书、任务书、报告书以及文献参考翻译 等,完整的设计文件及源代码,资料请联系 68661508(bshhty)索要
更多相关参考论文设计文档【WORD 可编辑】资源请访问 /lzj781219
研究意义:通过此次设计,了解了设计的一般程序,初步掌握了一定的设计 方法,对一些制药工艺和制药设备有了更深层的学习,能够较深刻的体会到现实 生产与理论计算的差别,进一步熟悉克矽平注射液市场前景及其整个生产工艺过 程。提高我国克矽平注射剂的产量和质量,加强对克矽平注射剂生产车间设计的 研究,对我国医药的发展和职业病防治有着重要意义,而且有利于制药工程专业 学生的工程设计能力的培养与训练。 二、 设计(论文)主要研究的内容、预期目标:(技术方案、路线)
一、 设计(论文)依据及研究意义: 设计依据:克矽平((聚 2 一乙烯基吡啶氮一氧化物,P204))为治疗和预防
矽肺病用药,是一种分子结构中具有带强负电性氧原子的高分子药物,常见剂型 为注射剂和喷雾剂。适用于各期矽肺病患者,对于早期和急性矽肺疗效较好,可 作为长期治疗药物。本品应用历史悠久,治疗效果显著,市场表现良好。
更多相关参考论文设计文档【WORD 可编辑】资源请访问 /lzj781219
本科生毕业设计(论文)开题报告
设计(论文)题目
- 1、下载文档前请自行甄别文档内容的完整性,平台不提供额外的编辑、内容补充、找答案等附加服务。
- 2、"仅部分预览"的文档,不可在线预览部分如存在完整性等问题,可反馈申请退款(可完整预览的文档不适用该条件!)。
- 3、如文档侵犯您的权益,请联系客服反馈,我们会尽快为您处理(人工客服工作时间:9:00-18:30)。
注射剂生产车间工程设计最终灭菌小容量注射剂车间GMP设计(1)最终灭菌小容量注射剂生产过程包括原辅料的准备、配制、灌封、灭菌、质检、包装等步骤,按工艺设备的不同型式可分为单机生产工艺和联动机组生产工艺两种,其流程及环境区域划分(见图A B)。
关于水针各单机设备和联动机组设备的具体内容详见前。
(2)按照GMP的规定最终灭菌小容量注射剂生产环境分为三个区域:一般生产区、10万级洁净区、1万级洁净区。
一般生产区包括安瓿外清处理、半成品的灭菌检漏、异物检查、印包等;10万级洁净区包括物料称量、浓配、质检、安瓿的洗烘、工作服的洗涤等;1万级洁净区包括稀配、灌封,且灌封机自带局部100级层流。
洁净级别高的区域相对于洁净级别低的区域要保持5~10Pa的正压差。
如工艺无特殊要求,一般洁净区温度为18~26℃,相对湿度为45%~65%。
各工序需安装紫外线灯。
(3)车间设计要贯彻人、物流分开的原则。
人员在进入各个级别的生产车间时,要先更衣,不同级别的生产区需有相应级别的更衣净化措施。
生产区要严格按照生产工艺流程布置,各个级别相同的生产区相对集中,洁净级别不同的房间相互联系中设立传递窗或缓冲间,使物料传递路线尽量短捷、顺畅。
物流路线的一条线是原辅料,物料经过外清处理,进行浓配、稀配;另一条线是安瓿瓶,安瓿经过外清处理后,进入洗灌封联动线清洗、烘干.两条线汇聚于灌封工序。
灌封后的安瓿再经过灭菌、检漏、擦瓶、异物检查,最后外包成整个生产过程。
具体进出水针车间的人流、物流路线(见图)所示。
(4)辅助用房的合理设置是制剂车间GMP没计的一个重要环节。
厂房内设置与生产规模相适应的原、辅材料,半成品、成品存放区域,且尽可能靠近与其联系的生产区域,减少运输过程中的混杂与污染。
存放区域内应安排待验区、合格品区和不合格品区;贮料称量室,并且要有利于包括空调风管在内的公用管线的布置。
(5)水针生产车间内地面一般做耐清洗的环氧自流坪地面,隔墙采用轻质彩钢板,墙与墙、墙与地面、墙与吊顶之间接缝处采用圆弧角处理,不得留有死角。
(6)水针生产车间需要排热、排湿房间有浓配间、稀配间、工具清洗间、灭菌间、洗瓶间、洁具室等,灭菌检漏需考虑通风。
公用工程包括给排水、供气、供热、强弱电、制冷通风、采暖等专业设汁应符合GMP原则。
车间设计举例图车间设计举例图是水针生产联动机组工艺车间布置图采用浓配加稀配的配料方式,具体布置(见图)。
水针单机生产工艺车间布置图(见图),整体布局为一拖二型,即共用瓶子的粗、精洗工序,再分成两套灌封系统,适合多品种小批量生产。
配料采用一次配制的方式。
具体布置如图7.2—3所示。
最终灭菌大容量注射剂(大输液)车间相关链结:大输液配置系统工艺流程图大输液生产车间设计一般性要点:★★★最终灭菌大容量注射剂工艺流程★★★(1)掌握大输液的生产工艺是车间设计的关键,盛装输液的容器有玻璃瓶、聚乙烯塑料瓶、复合膜等,包装容器不同其生产工艺也有差异,复合膜、玻璃瓶、塑料容器的输液工艺流程及环境区域划分分别(见图 A B C)。
无论何种包装容器其生产过程一般包括原辅料的准备、浓配、稀配、包材处理(瓶外洗、粗洗、精洗等)、灌封、灭菌、灯检、包装等工序。
(2)设计时要分区明确,按照GMP规定,由大输液生产工艺流程及环境区域划分示意图可知,大输液生产分为一般生产区、10万级洁净区、1万级及局部100级洁净区。
一般生产区包括瓶外洗、粒子处理、灭菌、灯检、包装等;10万级洁净区包括原辅料称配、浓配、瓶粗洗、轧盖等;1万级洁净区包括瓶精洗、稀配、灌封,其中瓶精洗后到灌封工序的暴露部分需百级层流保护。
生产相联系的功能区要相互靠近,以达到物流顺畅、管线短捷,如物料流向:原辅料称配一浓配一稀配一灌封工序尽量靠近。
车间设计时合理布置人、物流,要尽量避免人、物流的交叉。
人流路线包括人员经过不同的更衣进入一般生产区、10万级洁净区、l万级洁净区,进出车间的物流一般有以下几条:瓶子或粒子的进入、原辅料的进入、外包材的进入以及成品的出口。
进出输液车间的人流、物流路线(见图)所示。
(3)熟练掌握工艺生产设备是设计好输液车间的关键,输液包装容器不同其生产工艺不同,导致其生产设备亦不同。
即使是同一包装容器的输液,其生产线也有不同的选择,如玻璃瓶装输液的洗瓶工序有分粗洗、精洗的滚筒式洗瓶机和集粗、精洗于一体的箱式洗瓶机。
工艺设备的差异,车间布置必然不同,目前的输液生产均采用联动线,为我国较为常用的玻璃瓶输液生产线。
(4)合理布置好辅助用房。
辅助用房是大输液车间生产质量保证和GMP认证的重要内容,辅助用房的布置是否得当是车间设计成败的关键。
一般大输液生产车间的辅助用房包括万级工具清洗存放间、l0万级工具清洗存放间、化验室、洗瓶水配制间、不合格晶存放间、洁具室等。
大输液车间一般性技术要求:(1)大输液车间控制区包括l0万级洁净区、1万级洁净区,1万级环境下的局部100级层流,控制区温度为18~26℃,相对湿度为45%~65%。
各工序需安装紫外线灯。
(2)洁净生产区一般高度为2.7m左右较为合适,上部吊顶内布置包括风管在内的各种管线加上考虑维修需要,吊顶内部高度需为2.5m。
(3)大输液生产车间内地面一般做耐清洗的环氧自流坪地面,隔墙采用轻质彩钢板与墙、墙与地面、墙与吊顶之间接缝处采用圆弧角处理,不得留有死角。
(4)洁净生产区需用洁净地漏,百级区不得设置地漏。
(5)浓配间、稀配间、工具清洗间、灭菌间、洗瓶间、洁具室需排热、排湿。
在塑料颗粒制瓶和制盖的过程中均产生较多热量,除采用低温水系统冷却外,空调系统应考虑相应的负荷,塑料颗粒的上料系统必须考虑除尘措施。
洗瓶水配制间要考虑防腐与通风。
(6)纯化水和注射用水管道设计时要求65℃回路循环,管道安装坡度一般为0.1%一0.3%(1‰一3‰),不锈钢材质。
支管盲段长度不应超过循环主管管径的6倍。
(7)不同环境区域要保持5~lOPa的压差,1万级洁净区对10万级洁净区保持5~lOPa的正压,10万级洁净区对一般生产区保持5~lOPa的正压。
车间设计举例玻璃瓶装大输液车间布置图(见图),选用粗精洗合一的箱式洗瓶机,具体布置见图。
塑料瓶装大输液车间(见图)。
选用塑料瓶二步法成型工艺,具体布置见图。
无菌分装粉针剂车间GMP设计针剂车间设计一般性要点:(1)粉针剂的生产工序包括:原辅料的擦洗消毒、西林瓶粗洗、精洗、灭菌干燥、胶塞处理及灭菌、铝盖洗涤及灭菌、分装、轧盖、灯检、包装等步骤,按GMP规定其生产Z 域空气洁净度级别分为100级、1万级和10万级。
其中无菌分装、西林瓶出隧道烘箱、胶塞出灭菌柜及其存放等工序需要局部100级层流保护,原辅料的擦洗消毒、瓶塞精洗、瓶塞干燥灭菌为1万级,瓶塞粗洗、轧盖为10万级环境。
其工艺流程图及环境区域划分见图7 (2)车间设计要做到人、物流分开的原则,按照工艺流向及生产工序的相关性,有机地将不同洁净要求的功能区布置在一起,使物料流短捷、顺畅。
粉针剂车间的物流基本上有以下几种:原辅料、西林瓶、胶塞、铝盖、外包材及成品出车间。
进入车间的人员必须经过不同程度的更衣分别进入1万级和10万级洁净区。
进出粉针剂车间人、物流路线(见图)所示。
(3)车间设置净化空调和舒适性空调系统能有效控制温、湿度;并能确保培养室的温、湿度要求;若无特殊工艺要求,控制区温度为18~26℃,相对湿度为45%~65%。
各工序需安装紫外线灯灭菌。
(4)车间内需要排热、排湿的工序一般有洗瓶区隧道烘箱灭菌间、洗胶塞铝盖间、胶塞灭菌间、工具清洗间、洁具室等。
(5)级别不同洁净区之间保持5一lOPa的正压差每个房间应有测压装置。
如果是生产青霉素或其他高致敏性药品,分装室应保持相对负压。
粉针剂车间设计举例无菌分装粉针剂车间工艺布置图(见图)。
该工艺选用联动线生产,瓶子的灭菌设备为远红外隧道烘箱,瓶子出隧道烘箱后即受到局部100级的层流保护。
胶塞处理选用胶塞清洗灭菌一体化设备,出胶塞及胶塞的存放设置100级层流保护。
铝盖的处理另设一套人流通道,以避免人、物流之间有大的交叉。
具体布置如图所示干粉针剂车间GMP设计冻干粉针剂车间设计一般性要点:(1)冻于粉针剂的生产工序包括:洗瓶及干燥灭菌、胶塞处理及灭菌、铝盖洗涤及灭菌、分装加半塞、冻于、轧盖、包装等。
按GMP规定其生产区域空气洁净度级别分为100级、1万级和10万级。
其中料液的无菌过滤、分装加半塞、冻干、净瓶塞存放为100级或1万级环境下的局部100级即为无菌作业区,配料、瓶塞精洗、瓶塞干燥灭菌为1万级,瓶塞粗洗、轧盖为10万级环境。
其工艺流程图及环境区域划分见图4—u。
(2)车间设汁力求布局合理,遵循人、物流分开的原则,不交叉返流。
进入车间的人员必须经过不同程度的净化程序分别进入100级、1万级和l0万级洁净区.进入100级区的人员必须穿戴无菌工作服,洗涤灭菌后的无菌工作服在100级层流保护下整理。
无菌作业区的气压要高于其也区域,应尽量把无菌作业区布置在车间的中心区域,这样有利于气压从较高的房间流向较低的房间。
(3)辅助用房的布置要合理,清洁工具间、容器具清洗间宜设在无菌作业区外,非无菌工艺作业的岗位不能布置在无菌作业区内。
物料或其他物品进入无菌作业区时,应没置供物料、物品消毒或灭菌用的灭菌室或灭菌设备。
洗涤后的容器具应经过消毒或灭菌处理方能进入无菌作业区。
(4)车间设置净化空调和舒适性空调系统可有效控制温、湿度;并能确保培养室的温、湿度要求;控制区温度为18~26℃,相对湿度为45%~65%。
各工序需安装紫外线灯。
(5)若有活菌培养如生物疫苗制品冻干车间,则要求将洁净区严格区分为活菌区与死菌区,并控制、处理好活菌区的空气排放及带有活菌的污水。
(6)按照GMP的规则要求布置纯水及注射用水的管道。
车间设计举例生物疫苗制品冻干车间布置图(见图),空调系统活菌隔离措施根据室内洁净级别和工作区域内是否与活菌接触,冻于生产车间设置三套空调系统,具体介绍如下。
(1)10万级净化空调系统。
它主要解决二更间、培养基的配制、培养基的灭菌以及无菌衣服的洗涤,系统回风,与活菌区保持5~10Pa的正压。
(2)一万级净化空调系统。
该区域为活菌区,它主要解决接种、菌种培养、菌体收集、高压灭活、瓶塞的洗涤灭菌、工具清洗存放、三更、缓冲的空调净化。
该区域保持相对负压,空气全新风运行,排风系统的空气需经高效过滤器过滤,以防止活菌外逸。
(3)一万级净化空调系统和百级净化空调系统。
主要解决净瓶塞的存放、配液、灌装加半塞、冻干、压塞和化验。
该区域为死菌区,系统回风。
除空调系统外,该车间在建筑密封性、纯化水、注射用水的管道布置、污物排放等方面的设计上也要有防止交叉污染的措施。
该车间具体布置见图。